U.S. patent application number 16/347785 was filed with the patent office on 2019-10-31 for process for producing lighter distillates.
The applicant listed for this patent is HINDUSTAN PETROLEUM CORPORATION LTD. Invention is credited to Sriganesh Gandham, Venkateswarlu Choudary Nettem, Venkata Chalapathi Rao Peddy, Satyanarayana Murty Pudi, Kanuparthy Naga Raja, Bhavesh Sharma.
Application Number | 20190330543 16/347785 |
Document ID | / |
Family ID | 62075548 |
Filed Date | 2019-10-31 |


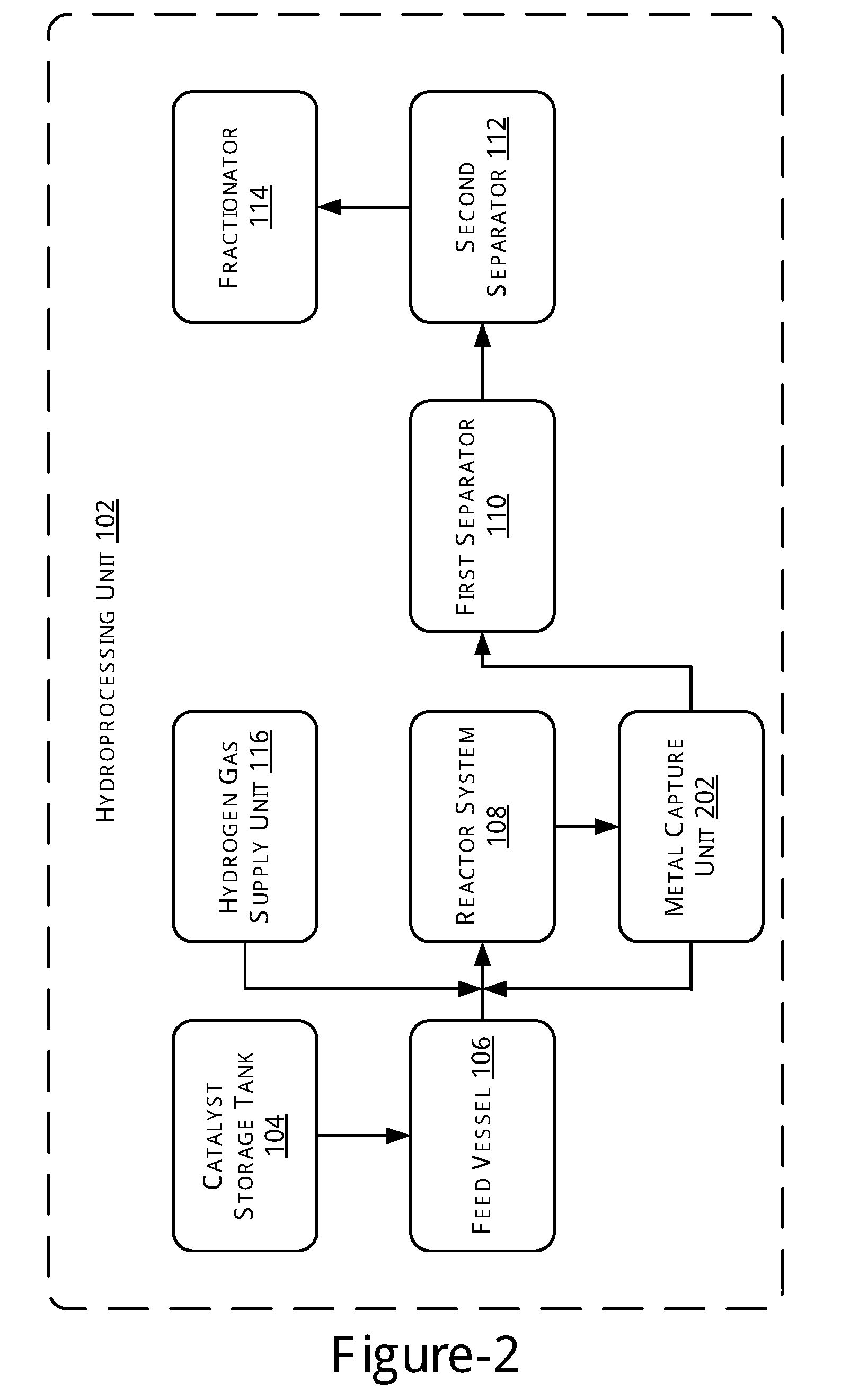
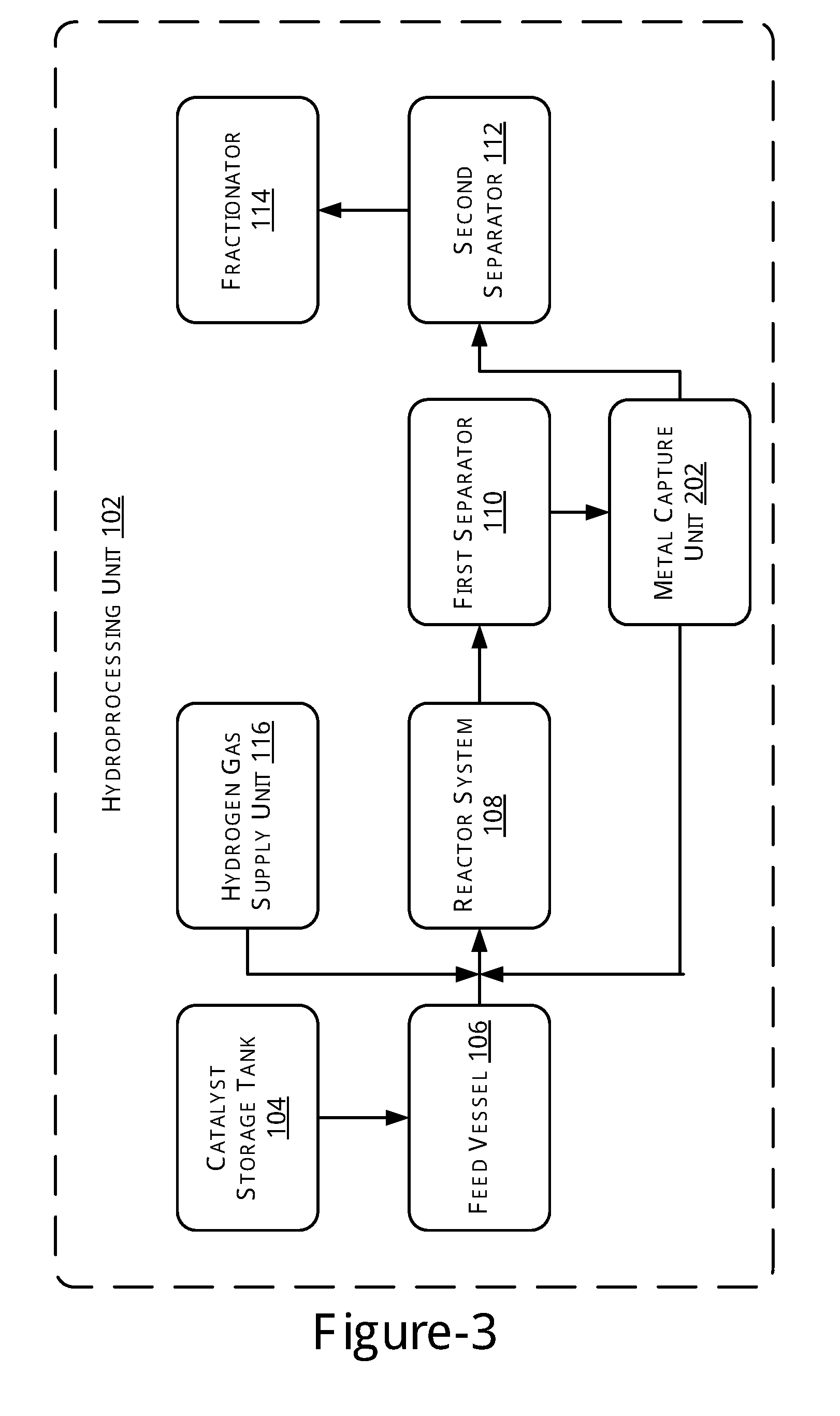
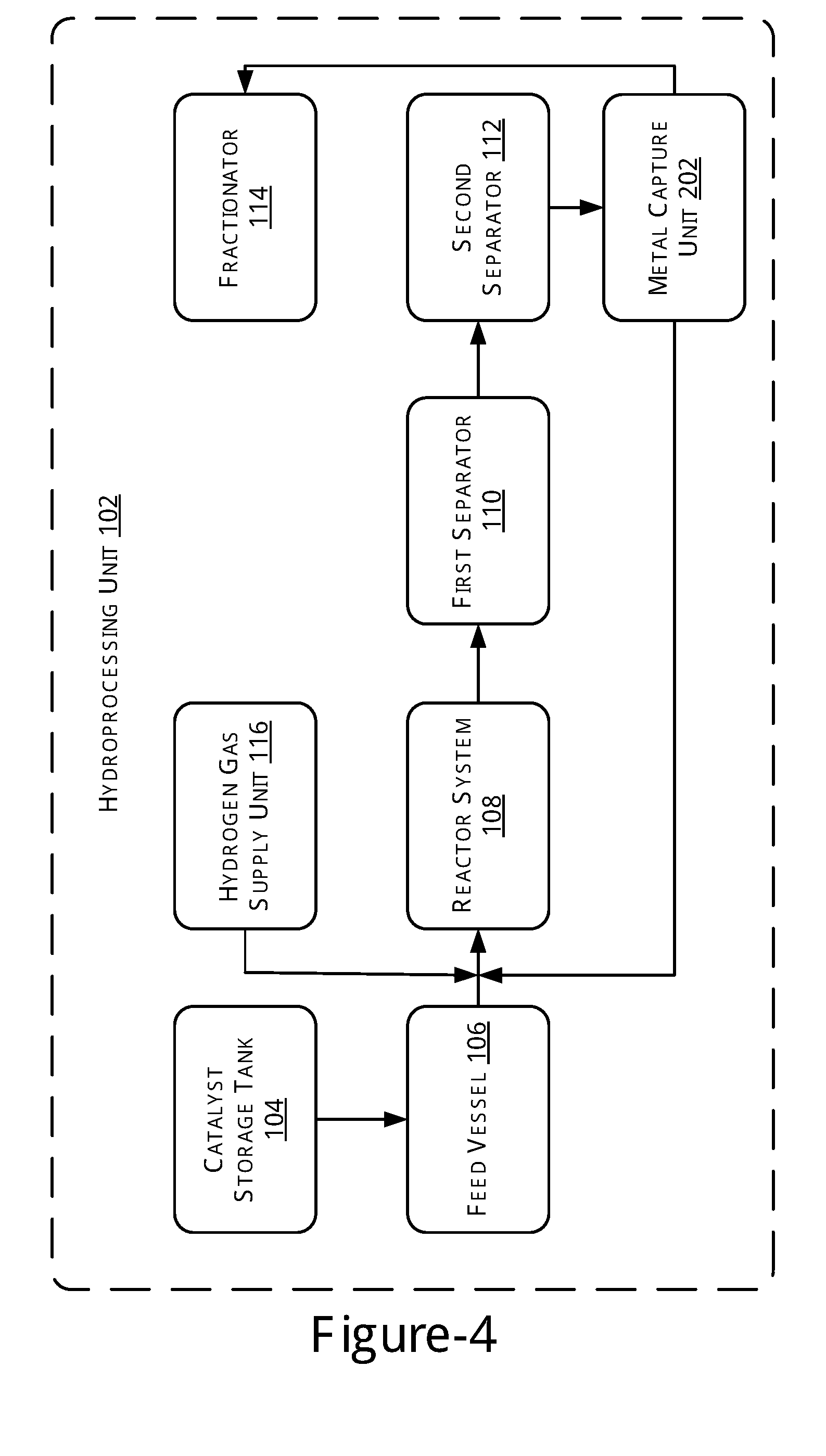
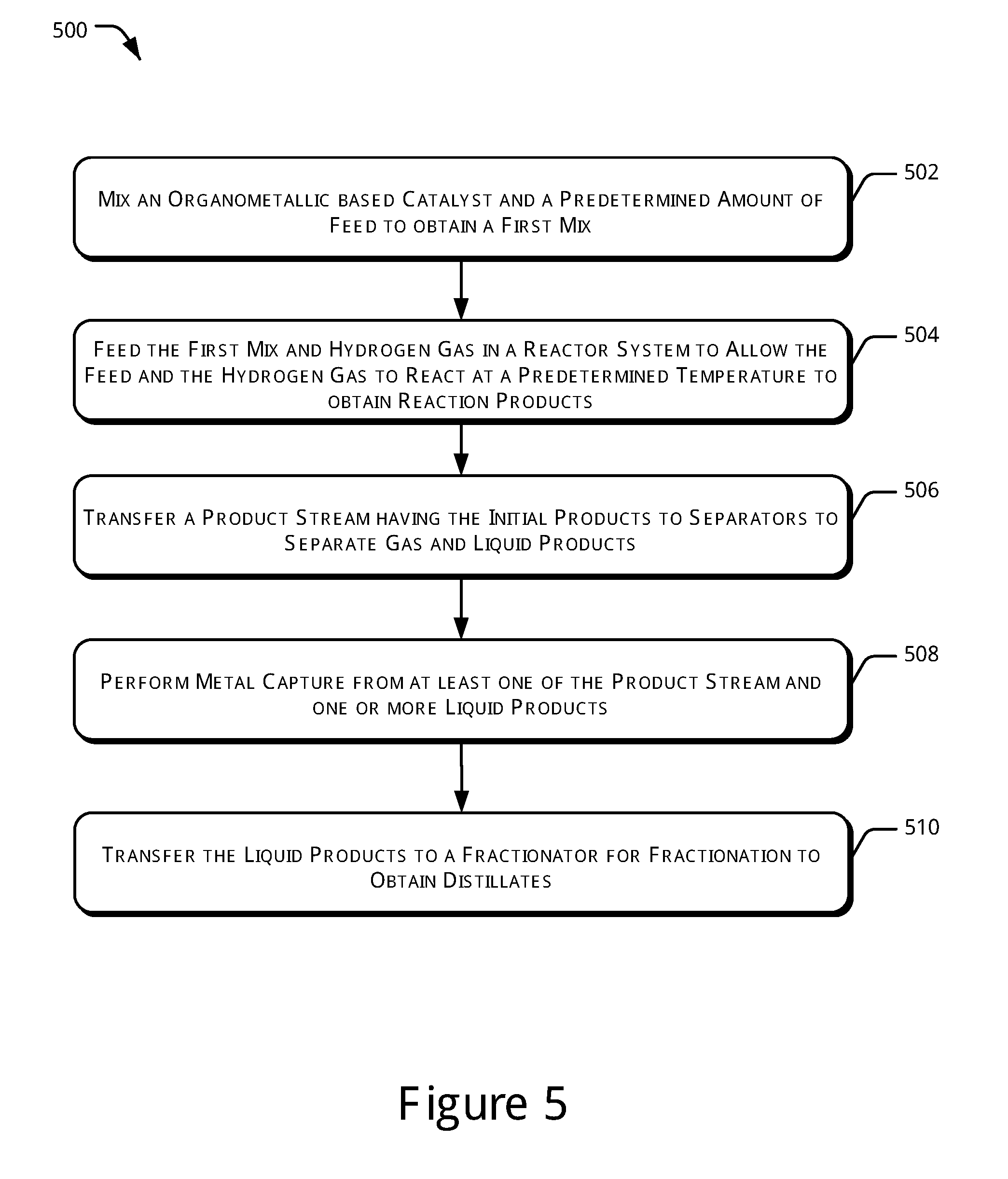
United States Patent
Application |
20190330543 |
Kind Code |
A1 |
Raja; Kanuparthy Naga ; et
al. |
October 31, 2019 |
PROCESS FOR PRODUCING LIGHTER DISTILLATES
Abstract
The present subject matter relates to a process of producing
lighter distillates. The hydrocarbons in the presence of
organometallic catalyst are reacted with hydrogen leading to
hydrotreating and/or hydrocracking reactions. The metals present in
product are subsequently captured the metal capture unit.
Inventors: |
Raja; Kanuparthy Naga;
(Hoskote, Karnataka, Bangalore, IN) ; Sharma;
Bhavesh; (Hoskote, Karnataka, Bangalore, IN) ; Pudi;
Satyanarayana Murty; (Hoskote, Karnataka, Bangalore, IN)
; Peddy; Venkata Chalapathi Rao; (Hoskote, Karnataka,
Bangalore, IN) ; Nettem; Venkateswarlu Choudary;
(Hoskote, Karnataka, Bangalore, IN) ; Gandham;
Sriganesh; (Hoskote, Karnataka, Bangalore, IN) |
|
Applicant: |
Name |
City |
State |
Country |
Type |
HINDUSTAN PETROLEUM CORPORATION LTD |
Mumbai |
|
IN |
|
|
Family ID: |
62075548 |
Appl. No.: |
16/347785 |
Filed: |
November 7, 2017 |
PCT Filed: |
November 7, 2017 |
PCT NO: |
PCT/IN2017/050514 |
371 Date: |
May 6, 2019 |
Current U.S.
Class: |
1/1 |
Current CPC
Class: |
C10G 47/02 20130101;
C10G 45/08 20130101; C10G 2300/4093 20130101; C10G 2400/04
20130101; C10G 2300/706 20130101; C10G 2400/06 20130101; C10G 31/10
20130101; C10G 47/00 20130101; C10G 49/02 20130101; C10G 2300/301
20130101; C10G 45/02 20130101; C10G 25/00 20130101; C10G 45/16
20130101; C10G 45/10 20130101; C10G 2400/02 20130101; C10G 47/14
20130101; C10G 2300/1055 20130101; C10G 45/04 20130101 |
International
Class: |
C10G 45/16 20060101
C10G045/16; C10G 45/10 20060101 C10G045/10; C10G 45/08 20060101
C10G045/08; C10G 47/14 20060101 C10G047/14 |
Foreign Application Data
Date |
Code |
Application Number |
Nov 7, 2016 |
IN |
201621038025 |
Claims
1. A process for hydroprocessing of hydrocarbons, said process
comprising the following steps: i. mixing the hydrocarbon feed and
an organometallic catalyst to obtain a combined feed; ii.
hydroprocessing said combined feed under hydrogen atmosphere in a
reactor at a temperature in the range of 100.degree. C. to
450.degree. C. and at a pressure in the range of 10 bar to 250 bar
to obtain a product stream; iii. transferring said product stream
to a metal capture unit to separate the metals from the product
stream; iv. sending relatively metal free product stream obtained
in step (iii) to first separator for the separation of gas and
liquid products; v. transferring the liquid product stream
separated out in step (iv) to second separator for further
separation of gas and liquid products; and vi. sending the liquid
products separated out in step (v) to a fractionator for obtaining
various fractions of the hydroprocessed product.
2. The process as claimed in claim 1, wherein said hydrocarbon feed
comprises of hydrocarbons boiling above 60.degree. C., ranging from
Naphtha to Vacuum Gas Oil.
3. The process as claimed in claim 1, wherein said catalyst
comprises at least one metal or a metallic compound of said metal
selected from the group consisting of chromium, manganese, iron,
cobalt, nickel, zirconium, niobium, molybdenum, tungsten,
ruthenium, rhodium, tin, and tantalum.
4. The process as claimed in claim 1, wherein the amount of said
catalyst is in the range of 0.001 wt % to 10 wt % of said
hydrocarbon feed.
5. The process as claimed in claim 1, wherein in the process step
(ii), hydroprocessing is carried out for a time period in the range
of 15 minutes to 4 hours.
6. The process as claimed in claim 1, wherein in the process step
(ii), the said reactor system can be selected from a group
consisting of continuous stirred tank reactor, ebullated bed
reactor, slurry bubble column reactor or combinations thereof.
7. The process as claimed in claim 1, wherein the metal capture
unit is placed at the downstream of first separator.
8. The process as claimed in claim 1, wherein the metal capture
unit is placed at the downstream of second separator.
9. The process as claimed in claim 1, wherein a portion of captured
metal stream is recycled back to the reactor system while the
remaining portion is sent for metal recovery.
10. The process as claimed in claim 1, wherein the metal capture
unit is one of a centrifuge unit and an adsorption unit.
Description
TECHNICAL FIELD
[0001] The present subject matter relates to hydroprocessing and,
in particular, to a process for hydroprocessing distillates in the
range of naphtha to vacuum gas oils in slurry phase.
BACKGROUND
[0002] Hydroprocessing is widely used to improve quality of
products obtained during crude oil refining. For instance,
hydrotreating is carried out to remove Sulfur and Nitrogen from
hydrocarbon feedstock in treating units. Similarly, hydrocracking
is carried out to convert heavy hydrocarbons into lighter and more
valuable hydrocarbons. Hydrotreating and hydrocracking reactions
are generally carried out in fixed bed reactors. Solid catalysts of
different shapes are loaded into the fixed bed reactors to form
number of beds separated by a quench system to carry out the
reactions for Hydroprocessing.
BRIEF DESCRIPTION OF DRAWINGS
[0003] The detailed description is described with reference to the
accompanying figures. In the figures, the left-most digit(s) of a
reference number identifies the figure in which the reference
number first appears. The same numbers are used throughout the
drawings to reference like features and components.
[0004] FIG. 1 illustrates a block diagram of a hydroprocessing
unit, in accordance with an example of the present subject
matter.
[0005] FIG. 2 illustrates a block diagram of a hydroprocessing
unit, in accordance with another example of the present subject
matter.
[0006] FIG. 3 illustrates a block diagram of a hydroprocessing
unit, in accordance with yet another example of the present subject
matter.
[0007] FIG. 4 illustrates a block diagram of a hydroprocessing
unit, in accordance with yet another example of the present subject
matter.
[0008] FIG. 5 illustrates a method for producing lighter
distillates in a hydroprocessing unit, in accordance with yet
another example of the present subject matter.
DETAILED DESCRIPTION
[0009] In conventional hydroprocessing fixed bed reactors, solid
catalysts are arranged to form fixed beds. During operation,
hydrocarbon feed is allowed to flow through the catalyst beds. As
the feed reaches the pores of the catalyst, reaction takes place
between the hydrocarbons and hydrogen gas in presence of the active
metals in the catalysts. The after-products of the reaction
subsequently flow out and exit the reactor for further downstream
processing. As the fixed bed reactors require the feed to flow
across the catalyst surface and catalyst pores before reaching the
active metals for reaction, the feed usually faces resistance from
the catalyst surface and the catalyst pores. Further, due to the
regular reactions occurring over the catalyst, coke formation may
take place, owing to which the pores may get blocked. The feed may
thus not be able to freely access the active metals on the
catalyst. Further, flow maldistribution of the feed may occur due
to dead zones and channeling within the fixed bed reactors, thus,
limiting the extent of reaction, thereby affecting the efficiency
of hydroprocessing.
[0010] The present subject matter describes a process of producing
lighter distillates. In one example, the process includes
hydroprocessing of hydrocarbons in the range of naphtha to vacuum
gas oils in slurry phase. In one example implementation, the
lighter distillates are produced by performing hydrotreating and/or
hydrocracking reactions in a hydroprocessing unit. The
hydroprocessing unit is to carry out hydroprocessing reactions in a
slurry phase with active catalysts in dispersed mode. In one
implementation, the active catalyst may be an organometallic based
catalyst comprising a metal selected from a predetermined group of
metals.
[0011] In one embodiment of the present subject matter, the
organometallic based catalyst may comprise a metal selected from
the group consisting of titanium, molybdenum, vanadium, chromium,
manganese, iron, cobalt, nickel, zirconium, tungsten, ruthenium,
rhodium, tin, tantalum, rhenium, and iridium. In one
implementation, the amount of metal in the catalyst used for
hydroprocessing of the hydrocarbons may be in the range of 0.001%
to 10% by weight.
[0012] In one example, the hydroprocessing unit includes a reactor
system, a feed vessel for providing feed to the reactor system, a
catalyst storage tank for providing a catalyst to the feed vessel,
separators for separation of gaseous and liquid products obtained
from the reactor system, and a fractionator for separation of
different fractions of the product. In one implementation, the
reactor system can be selected from a group consisting of
continuous stirred tank reactor, ebullated bed reactor, slurry
bubble column reactor or combinations thereof. In one another
implementation, the reactor system comprises of reactors in a
configuration selected from the group consisting of series,
parallel and series-parallel.
[0013] During operation, a predetermined amount of the
organometallic based catalyst may be mixed with a predetermined
amount of the hydrocarbon feed present in the feed vessel. The mix
of organometallic based catalyst and the hydrocarbon feed may then
be provided along with Hydrogen gas to the reactor system at a
predetermined pressure. The hydrocarbon feed and the Hydrogen gas
is then allowed to react in presence of the active metals in the
catalysts at a predetermined temperature and pressure, for a
predetermined time period. The products, thus obtained are
processed by the separators to separate gaseous and liquid products
and further remove dissolved gases from the liquid products.
Subsequently, the liquid products are provided to the fractionator
for fractionation to obtain different products. Further, metal
capture units can be used to capture and re-use the metal from the
catalyst, as will be described in detail with reference to the
figures.
[0014] The present subject matter thus provides a process of
producing lighter distillates in the range of naphtha to vacuum gas
oils in slurry phase. The distillates are produced in a
hydroprocessing unit that facilitates hydroprocessing of
hydrocarbon feedstocks in a slurry phase with active catalysts in
dispersed mode. Hydroprocessing the feedstock in a slurry phase
instead of a fixed bed reactor helps in providing efficient
reaction between the hydrocarbon feedstock and the hydrogen gas in
the presence of the active metal in the active catalyst. As the
active catalyst is dispersed in the liquid hydrocarbon feedstock to
form a slurry, the feedstock is efficiently able to come in contact
with the metal.
[0015] The present subject matter is further described with
reference to FIGS. 1 to 5. It should be noted that the description
and figures merely illustrate principles of the present subject
matter. Various arrangements may be devised that, although not
explicitly described or shown herein, encompass the principles of
the present subject matter. Moreover, all statements herein
reciting principles, aspects, and examples of the present subject
matter, as well as specific examples thereof, are intended to
encompass equivalents thereof.
[0016] FIG. 1 illustrates a block diagram of a hydroprocessing unit
102, in accordance with an example of the present subject matter.
In one example, the hydroprocessing unit 102 includes a catalyst
storage tank 104, a feed vessel 106, a reactor system 108, a first
separator 110, a second separator 112, and a fractionator 114.
Although, the hydroprocessing unit 102 may include various other
intermediate sub-units that may be utilized for hydroprocessing,
however, for the sake of brevity and not as a limitation, only the
aforementioned sub-units are described and shown in the figure.
[0017] The reactor system 108 is in fluid connection with the feed
vessel 106 and the first separator 110. In one implementation, the
first separator 110 is a high-pressure separator and the second
separator 112 is a low-pressure separator. Further, a hydrogen gas
supply unit 116 may be connected to the reactor system 108 for
providing the hydrogen for hydroprocessing.
[0018] As previously described, the hydroprocessing unit 102 may be
implemented for performing hydrotreating and/or hydrocracking
reactions of hydrocarbon feedstock ranging from naphtha to vacuum
gas oil. For example, the hydrocarbon feed comprises of
hydrocarbons boiling above 60.degree. C. In one implementation, the
hydroprocessing unit 102 may use an organometallic based catalyst
comprising a metal selected from the group consisting of titanium,
molybdenum, vanadium, chromium, manganese, iron, cobalt, nickel,
zirconium, tungsten, ruthenium, rhodium, tin, tantalum, rhenium,
and iridium. In one implementation, the amount of metal in the
catalyst used for hydrotreating the hydrocarbons may be in the
range of 0.001% to 10% by weight. Further, the metal content in the
catalyst may range from 1% to 35%.
[0019] Further, the hydroprocessing unit 102 may be operated at a
temperature in the range of 100.degree. C. to 450.degree. C.
depending on the feed and the catalyst. The hydroprocessing unit
102 may be operated at a pressure in the range of 10 bar to 250 bar
depending on the feed and the catalyst.
[0020] In operation, initially, a predetermined amount of an
organometallic based catalyst is obtained from the catalyst storage
tank 104 and mixed with a predetermined amount of feed obtained
from the feed vessel 106. In one implementation, the catalyst and
the feed may be mixed in one of a static line mixer (not shown in
the figure) or a mixing tank (not shown in the figure) before the
mix enters into the reactor system 108. The mix of catalyst and the
feed may then be transferred to the reactor system 108. Further,
the hydrogen gas may be fed to the reactor system 108 at a
predetermined pressure. The feed and the hydrogen gas subsequently
react in the presence of the catalyst at a predetermined
temperature for a predetermined time period. For example, the
reaction may be carried out under hydrogen atmosphere at a
temperature in the range of 100.degree. C. to 450.degree. C. and at
a pressure in the range of 10 bar to 250 bar for a time ranging
from 15 minutes to 4 hours.
[0021] As a result of the high temperature reaction conditions, the
organometallic catalyst decomposes to release the active metal. The
metal in the reactant mixture acts as the catalyst for
hydroprocessing resulting in the cracking of heavy hydrocarbons
into lighter distillates.
[0022] A product stream having the products obtained as a result of
the reaction is subsequently transferred to the first separator 110
to separate gas products and liquid products. The separation
happens by virtue of Thermodynamic flash at predetermined
temperature and pressure maintained within the first separator 110.
In one example, the first separator is operated in a temperature
range of 200 to 250 deg C. and in a Pressure range of 180-200
bar.
[0023] In one example, the gas products may include dry gas and
LPG. Dry gas may be routed to hydrogen recovery section for
hydrogen separation. The recovered hydrogen may be recycled back to
the reaction zone. The liquid products are further transferred to
the second separator 112 to remove dissolved gases from the liquid
products. The gases, thus obtained, are then removed from the
second separator 112 for further treatment, while the liquid
products are moved to the fractionator 114. The separation in the
second separator 112 happens by virtue of Thermodynamic flash at
predetermined temperature and pressure maintained within the second
separator 112. In one example, the second separator 112 is operated
in a temperature range of 25 to 30 deg C. and in a Pressure range
of 1-2 bar.
[0024] The fractionator 114 may perform fractionation to separate
product fractions from the liquid product based on their boiling
point range to obtain various fractions of the product. In one
example, the products obtained from fractionator may be mixtures of
Naphtha, Kerosene, Diesel, and Vacuum Gas Oil. The operating
conditions of the fractionator can be appropriately selected
depending on the products to be obtained, as will be
understood.
[0025] In the above described process, the metal from the catalyst
remains in the liquid product streams that are taken out from the
different separators. The present subject matter provides for metal
capture, such as using adsorption or centrifugation, for separating
out the metals from the hydroprocessed products. The metals
adsorbed on the adsorbents may be further put to re-use as a
catalyst in the reactor leading to a reduction in the requirement
of make-up catalyst. Further, the amount of metal discarded as
waste is substantially reduced. Various example schemes for metal
capture will now be described.
[0026] FIG. 2 illustrates a block diagram of the hydroprocessing
unit 102, in accordance with another example of the present subject
matter. As illustrated, the hydroprocessing unit 102 in accordance
with the current embodiment further includes a metal capture unit
202 coupled to the reactor system 108. The metal capture unit 202
is provided to remove metals from the products obtained from the
reactor system 108.
[0027] In operation, initially, a predetermined amount of a
catalyst is obtained from the catalyst storage tank 104 and mixed
with a predetermined amount of feed obtained from the feed vessel
106. The mix of catalyst and the feed may then be transferred to
the reactor system 108. Further, the hydrogen gas may be
transferred to the reactor system 108 at a predetermined pressure.
The feed and the hydrogen gas may then be allowed to react in the
presence of the catalyst at a predetermined temperature for a
predetermined time period.
[0028] A product stream having the products obtained as a result of
the reaction is subsequently transferred to the metal capture unit
202. The metal capture unit 202 may implement a separation process
for separating metals from the product stream. In one
implementation, the separation process may be one of an adsorption
process and a centrifugal process.
[0029] For the separation process being a centrifugal process, the
metal capture unit 202 may be implemented as a centrifuge. The
metal capture unit 202 may thus perform the separation process such
that the product stream is separated into a lighter portion stream
and a heavier portion stream. The heavier portion stream that
includes the metals may be transferred back to the reactor system
108 while the lighter portion stream is transferred to the first
separator 110 for the separation of gas and liquid products.
[0030] For the separation process being an adsorption process, the
metal capture unit 202 may be implemented as an adsorption unit
employing an adsorption bed with active adsorbents. As the product
stream is received by the metal capture unit 202, the metals are
adsorbed on the adsorbents. The adsorption may occur as a result of
one or both of physical adsorption and chemical adsorption.
[0031] A relatively metal free hydrocarbon product stream, thus
obtained, is transferred to the first separator 110. A metal loaded
stream of adsorbents obtained owing to the adsorption may be
transferred to the reactor system 108 as an additional catalyst for
the reactions. In one example, a portion of the metal loaded stream
of adsorbents may be recycled to the reactor while the other
portion may be sent for metal recovery. The ratio of the metal
loaded stream recycled may depend on the extent of adsorption which
occurs and can be changed suitably as will be understood.
[0032] In the metal recovery process, the metal from the metal
loaded adsorbents may be leached away, for example, by contact with
a hydrocarbon. In one example, the leaching may be performed using
fresh diesel. The recovered metal may be again used in the reaction
or may be used as reclaimed metal.
[0033] After the reaction, the product stream from the reactor 108
may be sent to a filtration system (not shown in diagram) to remove
spent adsorbents, i.e., metal loaded adsorbents, before
transferring to metal capture unit 202, which is filled with fresh
adsorbents. Alternatively, the metal loaded adsorbents may be
regenerated to reclaim metals without being transferred to the
reactor system 108.
[0034] The adsorbent employed in the metal capture unit may employ
any commercial adsorbent that can adsorb the metals and can be
selected from a group consisting of activated carbon derived from
hard woods, soft woods and rice husks, functionalized activated
carbon obtained from refinery residues like delayed coker pitch,
slurry hydrocracking pitch and Bituminous tar, lignite coal,
ion-exchange resins, carbon nanotubes, graphene, carbon black,
functionalized carbon obtained after carbonization of rubber tires
and coconut coir, zeolites, alumino-silicates, silica light, ZSM-5,
modernite, carbon molecular sieves and clays such as bentonite and
kaolin.
[0035] On receiving the product stream after metal capture, which
is either the relatively metal free hydrocarbon product stream or
the lighter portion stream, the first separator 110 processes the
product stream to separate gas products and liquid products. The
liquid products are further transferred to the second separator 112
to remove dissolved gases from the liquid products. The gases, thus
obtained, are then removed from the second separator 112 for
further treatment, while the liquid products are moved to the
fractionator 114. The fractionator 114 may perform fractionation to
separate product fractions from the liquid product based on their
boiling point range to obtain various distillates. The operating
conditions of the various units, such as reactor, separators, and
fractionator, may be similar to those described earlier.
[0036] FIG. 3, illustrates a block diagram of the hydroprocessing
unit 102, in accordance with yet another example of the present
subject matter. As illustrated, the hydroprocessing unit 102 in
accordance with the current embodiment, further includes the metal
capture unit 202 coupled to the first separator 110 and the reactor
system 108. In said embodiment, the metal capture unit 202 is
provided to remove metals from the liquid products obtained from
the first separator 110.
[0037] Thus, in this scheme, metal capture is conducted after the
separation of the lighter fractions from the hydroprocessed
products. Metal removal thus happens from the heavier portion left
behind after the separation of lighters. The operating conditions
of the various units, such as reactor, separators, and
fractionator, may be similar to those described earlier.
[0038] FIG. 4 illustrates a block diagram of the hydroprocessing
unit 102, in accordance with yet another example of the present
subject matter. As illustrated, the hydroprocessing unit 102 in
accordance with the current embodiment, further includes the metal
capture unit 202 coupled to the second separator 112, the reactor
system 108, and the fractionator 114. In said embodiment, the metal
capture unit 202 is provided to remove metals from the liquid
products obtained from the second separator 112.
[0039] Thus, in this scheme, metal capture is conducted after the
further separation of the lighter fractions from the hydroprocessed
products. Metal removal is done here after most of the volatile or
lighter fractions have been separated out from the heavier portion
left behind. The operating conditions of the various units, such as
reactor, separators, and fractionator, may be similar to those
described earlier.
[0040] FIG. 5 illustrates a method 500 for producing lighter
distillates in a hydroprocessing unit, in accordance with yet
another example of the present subject matter.
[0041] The order in which the method 500 is described is not
intended to be construed as a limitation, and any number of the
described method blocks may be combined in any order to implement
the aforementioned methods, or an alternative method. Further, the
method may be performed in a hydroprocessing unit, such as the
hydroprocessing unit 102.
[0042] At block 502, an organometallic based catalyst and a
predetermined amount of feed are mixed to obtain a first mix. In
one example, the organometallic based catalyst comprising a metal
selected from the group consisting of titanium, molybdenum,
vanadium, chromium, manganese, iron, cobalt, nickel, zirconium,
tungsten, ruthenium, rhodium, tin, tantalum, rhenium, and iridium.
Further, the feed may be a hydrocarbon feed. The catalyst and the
feed may be mixed in one of a static line mixer (not shown in the
figure) or a mixing tank (not shown in the figure).
[0043] At block 504, the first mix and hydrogen gas are fed in a
reactor system. The hydrogen may be mixed with the first mix before
entering into the reactor system. The hydrogen gas and the feed are
allowed to react in the presence of the catalyst at a predetermined
temperature to obtain reaction products. In one example, the
temperature may be maintained in the range of 100.degree. C. to
450.degree. C.
[0044] At block 506, a product stream having the reaction products
is transferred to separators to obtain gaseous and liquid products.
In one example, the liquid products are further processed to
separate gas dissolved in the liquid products.
[0045] At block 508, metal may be captured from at least one of the
product stream and one or more liquid product streams, for example,
as per the schemes described in FIGS. 2-4 earlier.
[0046] At block 510, the liquid products are transferred to a
fractionator for fractionation. In one example, the fractionator
may perform fractionation to separate product fractions from the
liquid product to obtain lighter distillates including Naphtha,
Kerosene, Diesel, and Vacuum Gas Oil.
EXAMPLES
[0047] The present subject matter will now be illustrated with
working examples, which are intended to illustrate the working of
disclosure and not intended to be taken restrictively to imply any
limitations on the scope of the present disclosure. Unless defined
otherwise, all technical and scientific terms used herein have the
same meaning as commonly understood to one of ordinary skill in the
art to which this disclosure belongs. It is to be understood that
this disclosure is not limited to the particular methods and
experimental conditions described, as such methods and conditions
may vary depending on the process and inputs used as will be easily
understood by a person skilled in the art.
Example 1: Slurry Phase Diesel Hydrotreating with No Catalyst
[0048] The example 1 illustrates the slurry phase hydrotreating of
sour diesel in the presence of hydrogen without catalyst. In said
example, 300 ml of sour diesel was taken in a batch reactor. The
reactor was purged with nitrogen to remove any air trapped inside
and later it was pressurized with Hydrogen to attain a pressure of
40 bar. The reaction mixture was heated to 340.degree. C., under
continuous stirring at 500 rpm. The reaction temperature was
maintained for 1 hour. After 1 hour, chilled water was circulated
to bring down the temperature to 30.degree. C. The gaseous products
were collected in a gas bomb. The liquid sample was collected and
analyzed in Micro Distillation Unit as per ASTM D-7345. Density
measurement and Sulphur analysis was also conducted for both the
feed diesel as well as the products. The results of the experiment
of example 1 are summarized in Tables 1 and 2, as shown herein:
TABLE-US-00001 TABLE 1 Results for Sulphur content and density for
the feed diesel and the product Property Feed Product Density at
15.degree. C. 0.85505 g/m.sup.3 0.85476 g/m.sup.3 Sulphur content
1.65 wt % 1.53 wt %
TABLE-US-00002 TABLE 2 Results for micro distillation for the feed
and product Feed Product Initial Boiling Point (IBP) 228.5.degree.
C. 230.4.degree. C. 95% 377.8.degree. C. 380.4.degree. C.
[0049] As illustrated, there is a small reduction in the Sulphur
content of the product as is observed from the Sulphur
analysis.
Example 2: Slurry Phase Diesel Hydrotreating at 40 Bar Pressure of
Hydrogen with Iron-Based Catalyst
[0050] The example 2 illustrates the slurry phase hydrotreating of
sour diesel in the presence of hydrogen using SCAT-106* as a
catalyst precursor which is an Iron-based organometallic catalyst.
In said example, 300 ml of sour diesel and 1000 ppm of SCAT-106*
were taken in a batch reactor. The reactor was purged with nitrogen
to remove any air trapped inside and later it was pressurized with
Hydrogen to attain a pressure of 40 bar. The reaction mixture was
heated to 340.degree. C., under continuous stirring at 500 rpm.
Heating was continued for 1 hour. After 1 hour, the reaction was
quenched by circulating chilled water to bring down the temperature
to 30.degree. C. The gaseous products were collected in a gas bomb.
The liquid sample was collected and analyzed in Micro Distillation
Unit as per ASTM D-7345. Density measurement and Sulphur content
analysis were also conducted for both the feed diesel as well as
the products. The results of the experiment of example 2 are
summarized in Tables 3 and 4, as shown herein:
TABLE-US-00003 TABLE 3 Results for Sulphur content and density for
the feed diesel and the product Property Feed Product Density at
15.degree. C. 0.85505 g/m.sup.3 0.84828 g/m.sup.3 Sulphur content
1.65 wt % 1.46 wt %
TABLE-US-00004 TABLE 4 Results for micro distillation for the feed
and product Feed Product IBP 228.5.degree. C. 226.2.degree. C. 95%
377.8.degree. C. 379.3.degree. C.
[0051] As illustrated, the Sulphur removal is more with the
addition of catalyst as compared to the reaction without the use of
a catalyst.
Example 3: Slurry Phase Diesel Hydrotreating at 60 Bar Pressure of
Hydrogen with Molybdenum-Based Catalyst
[0052] The example 3 illustrates the slurry phase hydrotreating of
sour diesel in the presence of hydrogen using SOSCAT-9 as a
catalyst which is a Molybdenum-based organometallic catalyst. In
said example, 50 grams of sour diesel, 10000 ppm of SOSCAT-9 and
0.5 g of Dimethyl disulfide (for sulfiding of the catalyst) was
taken in a batch reactor. The reactor was purged with nitrogen to
remove any air trapped inside and later it was pressurized with
Hydrogen to attain a pressure of 60 bar. For pre-sulfidation of the
catalyst, the reactor with the reaction mixture was heated to a
temperature of about 320.degree. C. The reaction mixture was then
cooled down and the reactor was de-pressurized. The reaction
mixture was again heated to 340.degree. C., under continuous
stirring at 500 rpm after re-pressurizing the reactor to 60 bar
Hydrogen Pressure. Heating was continued for 1 hour. After 1 hour,
the reaction was quenched by circulating chilled water to bring
down the temperature to 30.degree. C. The gaseous products were
collected in a gas bomb. The liquid sample was collected and
analyzed in Micro Distillation Unit as per ASTM D-7345. Density
measurement and Sulphur content analysis were also conducted for
both the feed diesel as well as the products. The results of the
experiment of example 3 are summarized in Tables 5 and 6, as shown
herein:
TABLE-US-00005 TABLE 5 Results for Sulphur content and density for
the feed diesel and the product Property Feed Product Density at
15.degree. C. 0.85505 g/m.sup.3 0.8273 g/m.sup.3 Sulphur content
1.65 wt % 200 ppm
TABLE-US-00006 TABLE 6 Results for micro distillation for the feed
and product Feed Product IBP 228.5.degree. C. 115.6.degree. C. 95%
377.8.degree. C. 393.6.degree. C.
[0053] As illustrated, there is a substantial further reduction in
the Sulphur content of the product when the operation is conducted
at 60 bar with a Molybdenum based organometallic catalyst.
Example 4: Slurry Phase Diesel Hydrotreating of Partially
Hydrotreated Diesel
[0054] The example 4 illustrates the slurry phase hydrotreating of
partially hydrotreated diesel in the presence of hydrogen using
SOSCAT-9 as a catalyst which is a Molybdenum-based organometallic
catalyst. In said example, 50 grams of sour diesel, 10000 ppm of
SOSCAT-9 and 0.5 g of Dimethyl disulfide (for sulfiding of the
catalyst) was taken in a batch reactor. The reactor was purged with
nitrogen to remove any air trapped inside and later it was
pressurized with Hydrogen to attain a pressure of 60 bar.
Pre-sulfidation of the catalyst was conducted at 340.degree. C. The
reaction mixture was then cooled down and the reactor was
de-pressurized. The reaction mixture was again heated to
340.degree. C., under continuous stirring at 500 rpm after
re-pressurizing the reactor to 60 bar Hydrogen Pressure. Heating
was continued for 1 hour. After 1 hour, the reaction was quenched
by circulating chilled water to bring down the temperature to
30.degree. C. The gaseous products were collected in a gas bomb.
The liquid sample was collected and analyzed in Micro Distillation
Unit as per ASTM D-7345. Density measurement and Sulphur content
analysis were also conducted for both the feed diesel as well as
the products. The results of the experiment of example 4 are
summarized in Tables 7 and 8, as shown herein:
TABLE-US-00007 TABLE 7 Results for Sulphur content and density for
the feed diesel and the product Property Feed Product Density at
15.degree. C. 0.8242 g/m.sup.3 0.822 g/m.sup.3 Sulphur content 170
ppm 12.98 ppm
TABLE-US-00008 TABLE 8 Results for micro distillation for the feed
and product Feed Product 95% 383.degree. C. 382.8.degree. C.
[0055] As illustrated, there is a further reduction in the Sulphur
content of the product when the operation is conducted using a
Molybdenum based organometallic catalyst.
Example 5: Slurry Phase Diesel Hydrotreating of Diesel Along with
Adsorption for Metal Capture
[0056] The example 5 illustrates the slurry phase hydrotreating of
sour diesel in the presence of hydrogen using Iron-based
organometallic catalyst followed by adsorption operation with
Alumina powder. In said example, 250 grams of sour diesel and 50000
ppm of Iron-based organometallic catalyst was taken in a batch
reactor. The reactor was purged with nitrogen to remove any air
trapped inside and later it was pressurized with Hydrogen to attain
a pressure of 60 bar. The reaction mixture was then heated to
340.degree. C., under continuous stirring at 500 rpm. Heating was
continued for 1 hour. After 1 hour, the reaction was quenched by
circulating chilled water to bring down the temperature to
30.degree. C. The gaseous products were collected in a gas bomb.
The liquid sample was collected and analyzed for metals using
ICP-MS.
[0057] Alumina powder was then taken in a batch reactor followed by
addition of the liquid sample which was collected after reaction.
This was done for metal capture by adsorption, for example, as per
the process of FIG. 3 described earlier. For the metal capture, the
liquid sample with Alumina powder was heated to 340.degree. C.,
under continuous stirring at 500 rpm. Heating was continued for 1
hour. After 1 hour, the reaction was quenched by circulating
chilled water to bring down the temperature to 30.degree. C. The
liquid product was collected and analyzed for metals using ICP-MS.
The results of the experiment of example 5 are summarized in Table
9, as shown herein:
TABLE-US-00009 TABLE 9 Results for metal analysis Liquid Sample
Property Liquid Sample after metal capture Nickel + Vanadium +
67598.5 ppm 47669 ppm Iron + Molybdenum
[0058] As illustrated, there is a reduction in the metal content of
the product after carrying out adsorption following the
reaction.
[0059] While illustrative system and methods as described herein
embodying various characteristics of the present subject matter are
shown, it will be understood by those skilled in the art, that the
subject matter is not limited to these embodiments. Modifications
may be made by those skilled in the art, particularly in light of
the foregoing teachings. For example, each of the elements of the
aforementioned embodiments may be utilized alone or in combination
or sub combination with elements of the other embodiments. It will
also be appreciated and understood that modifications may be made
without departing from the true scope of the present subject
matter. The description is thus to be regarded as illustrative
instead of restrictive on the present subject matter.
* * * * *