U.S. patent application number 16/314584 was filed with the patent office on 2019-10-17 for rotary cylinder piston compressor pump and compressor with rotary cylinder piston compressor pump.
The applicant listed for this patent is GREE GREEN REFRIGERATION TECHNOLOGY CENTER CO., LTD. OF ZHUHAI. Invention is credited to Liying Deng, Zhongcheng Du, Yusheng Hu, Hui Huang, Jia Xu.
Application Number | 20190316586 16/314584 |
Document ID | / |
Family ID | 57114560 |
Filed Date | 2019-10-17 |
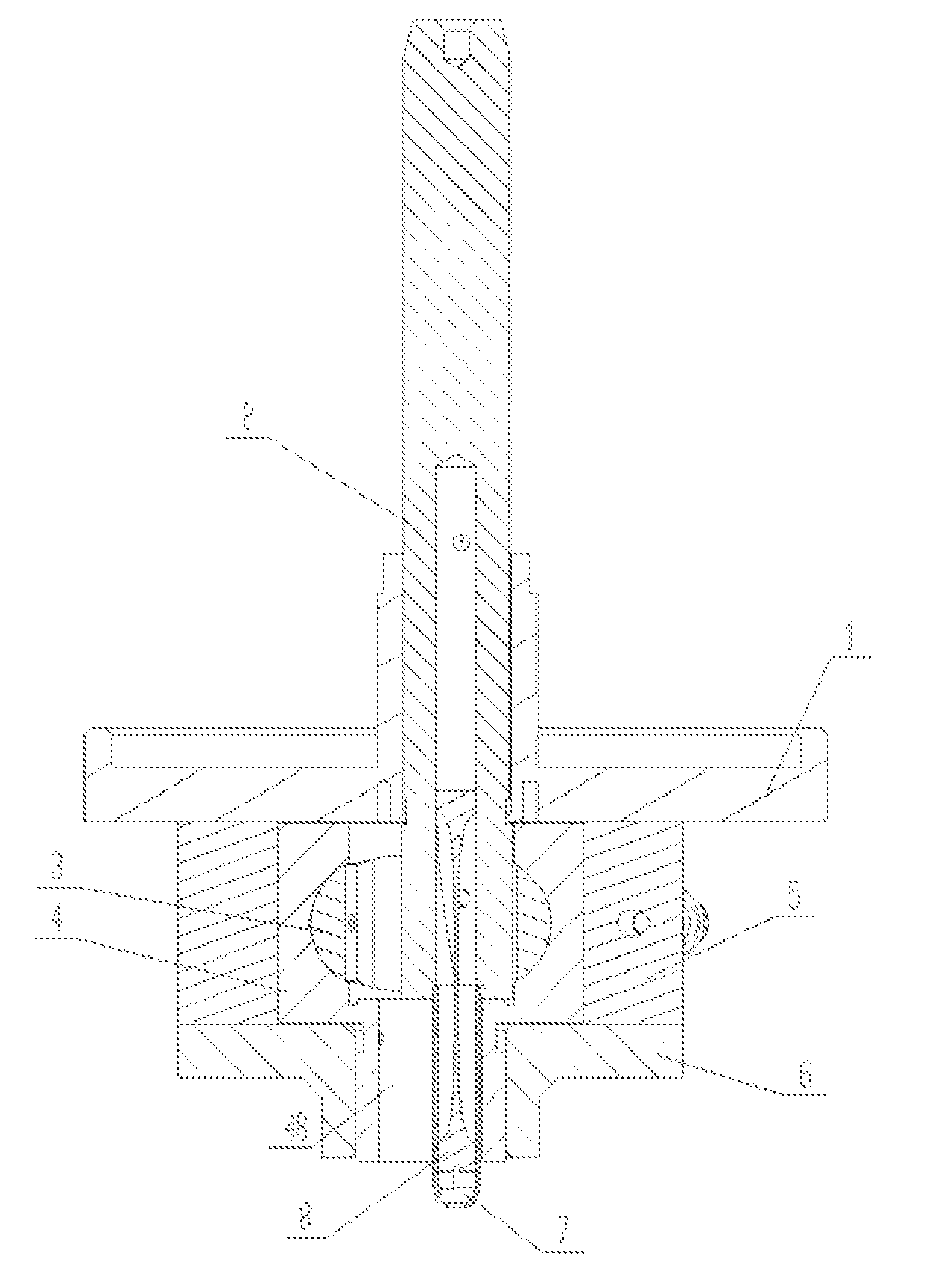
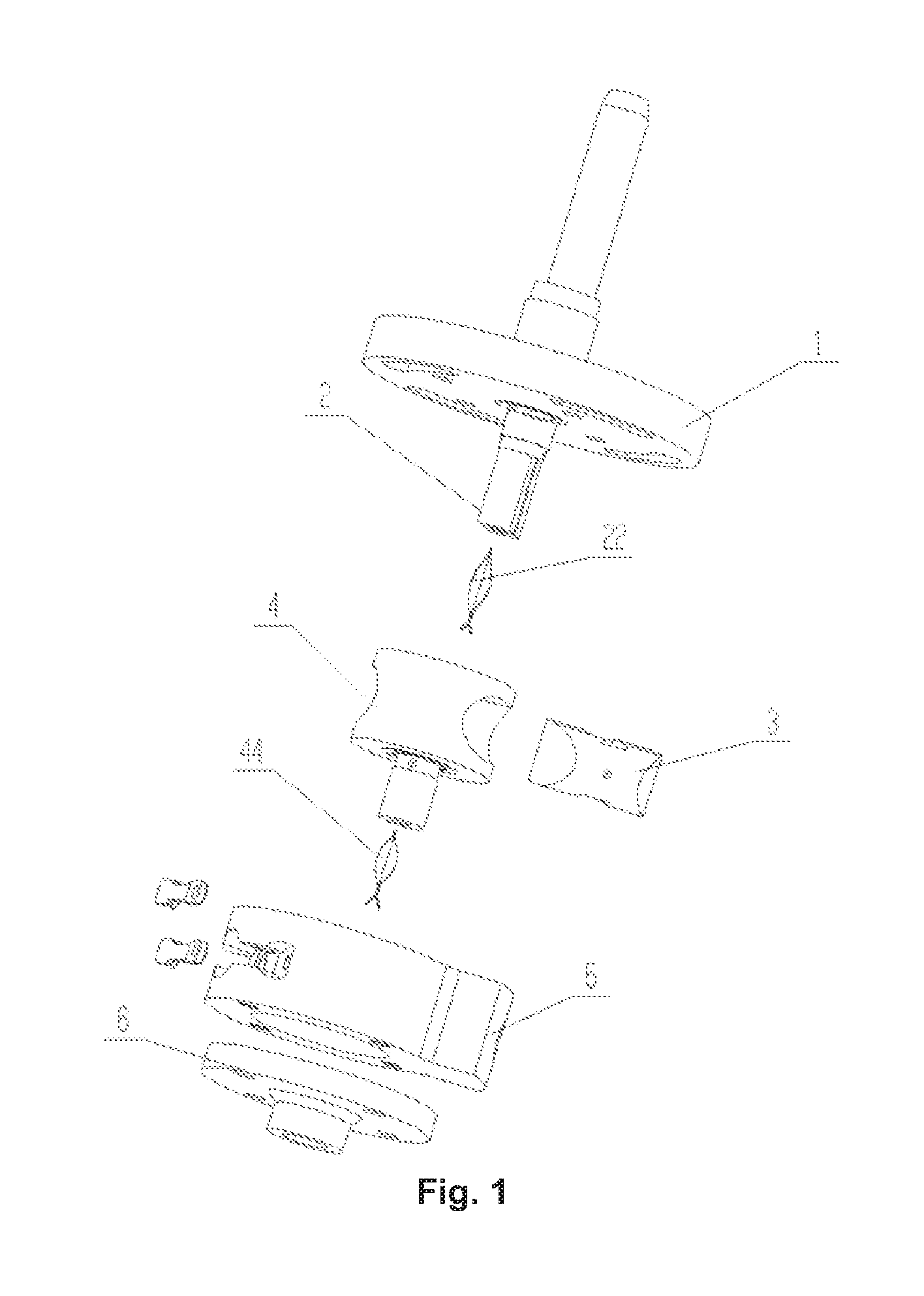


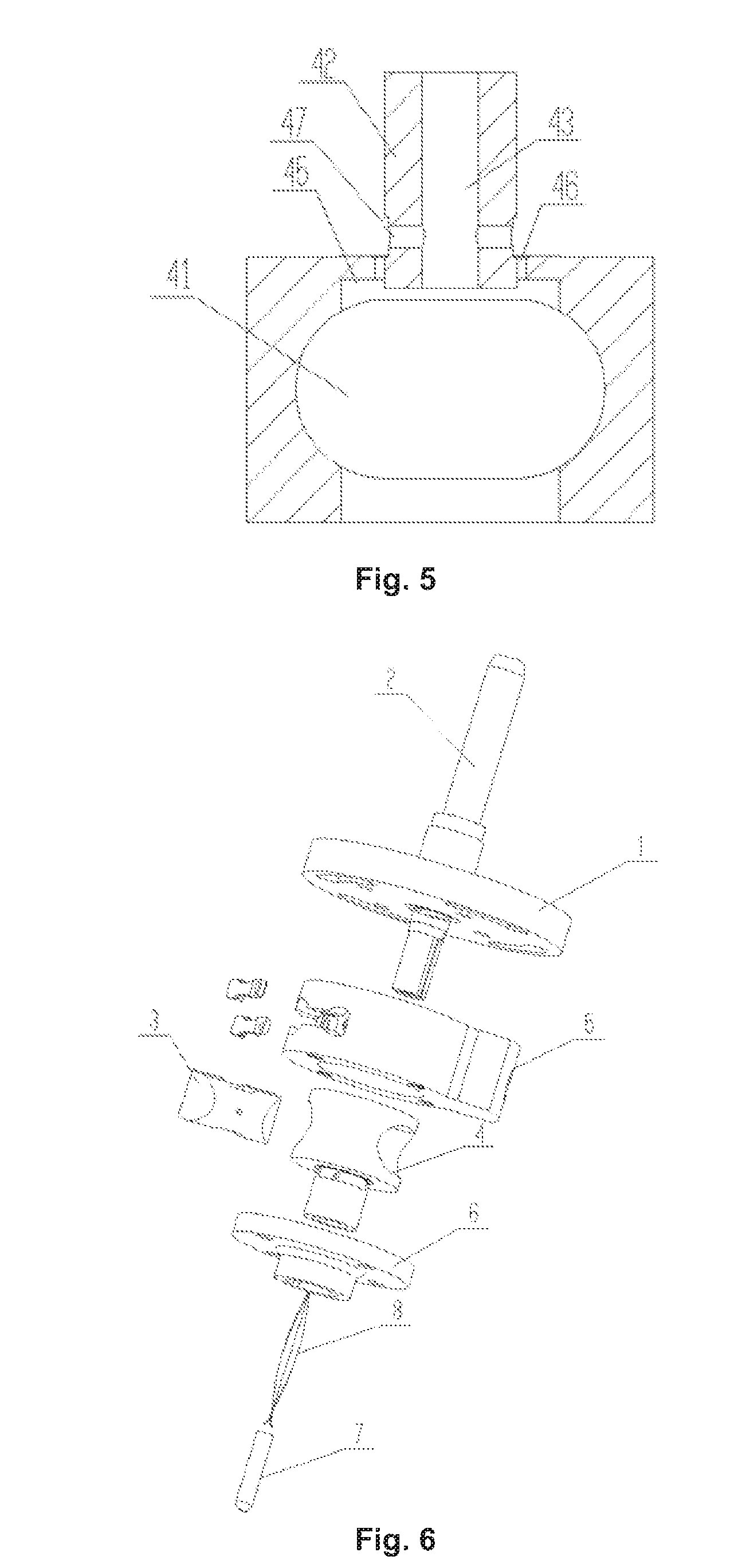
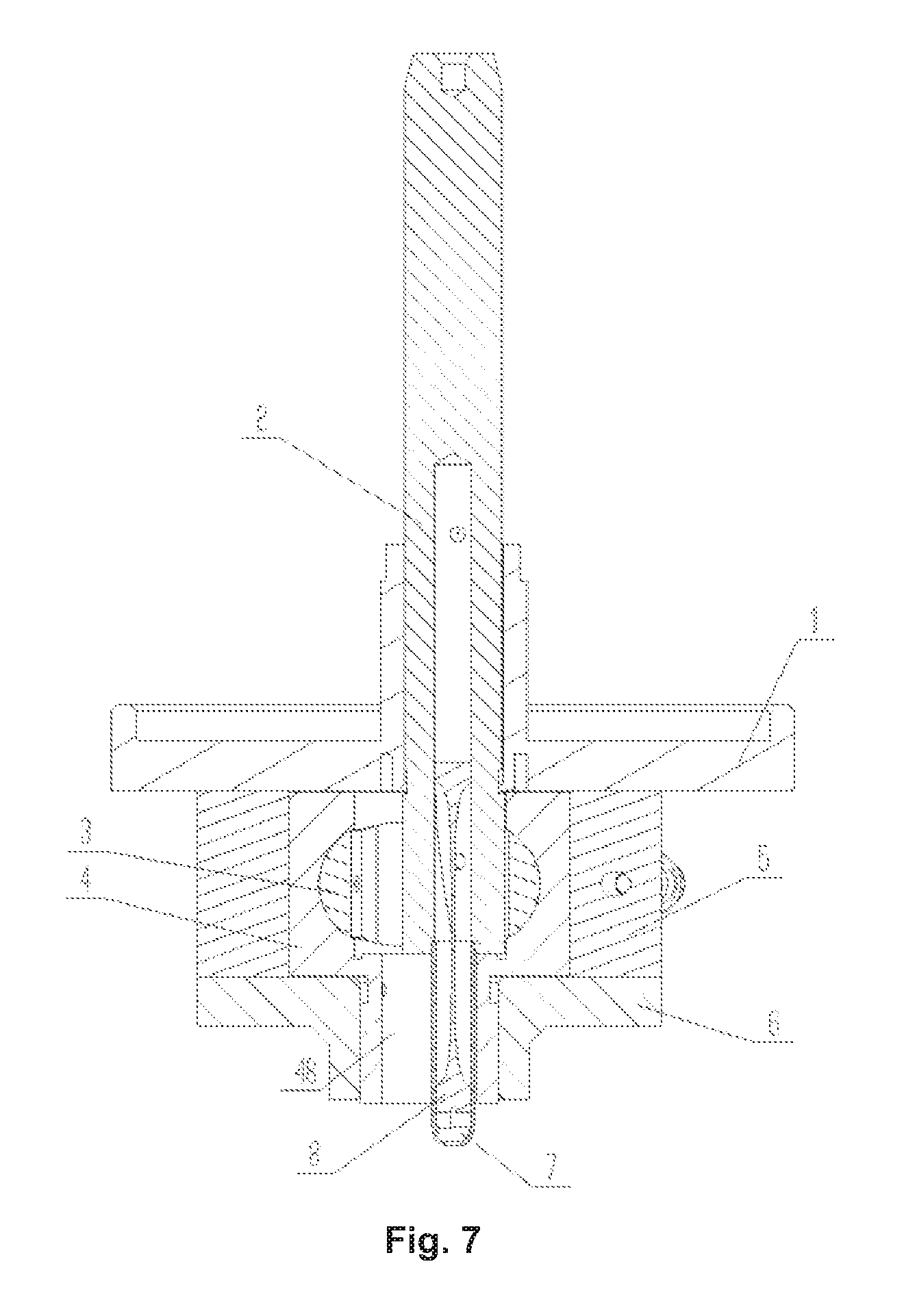
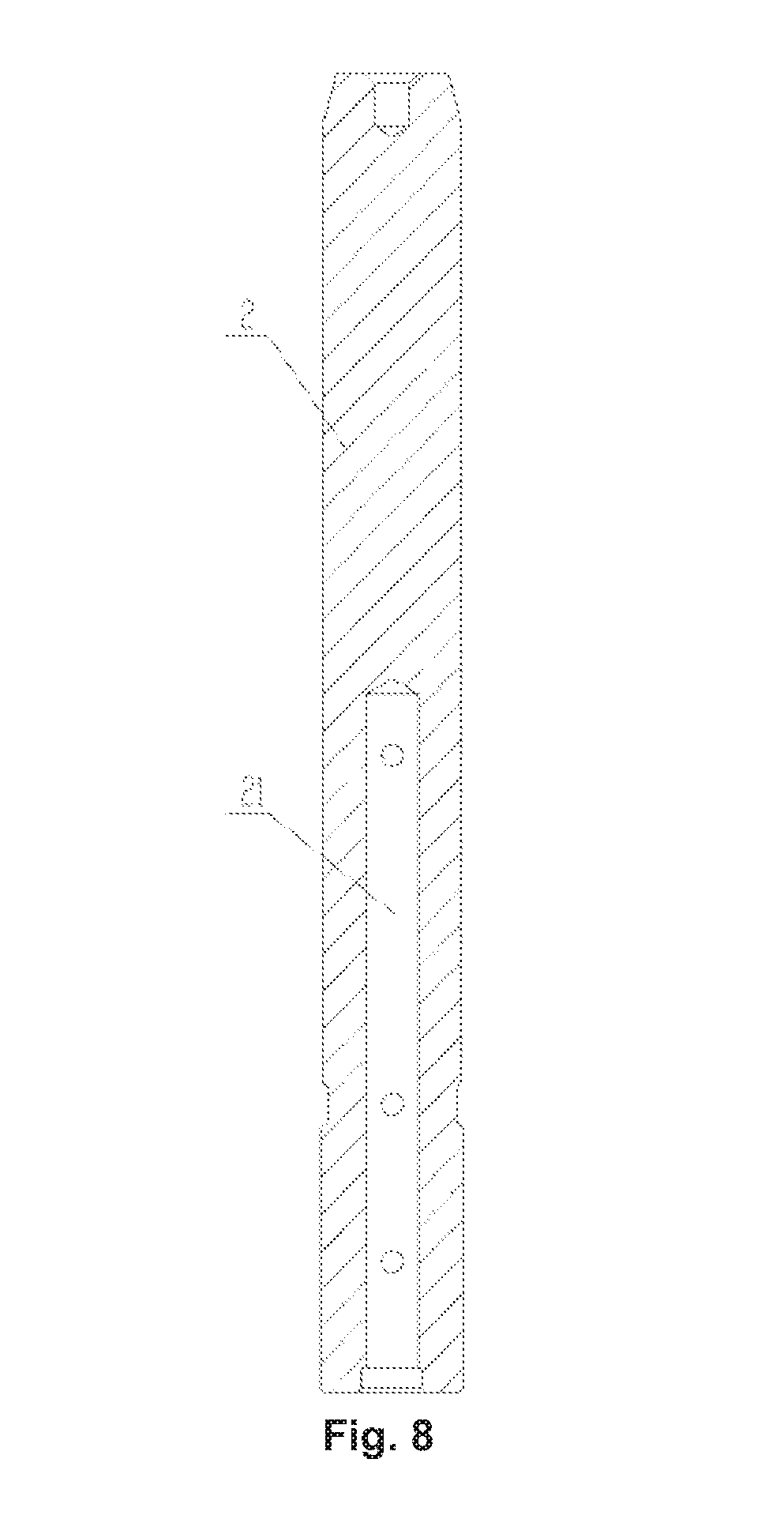

United States Patent
Application |
20190316586 |
Kind Code |
A1 |
Huang; Hui ; et al. |
October 17, 2019 |
ROTARY CYLINDER PISTON COMPRESSOR PUMP AND COMPRESSOR WITH ROTARY
CYLINDER PISTON COMPRESSOR PUMP
Abstract
A rotary cylinder piston compressor pump is provided, including
a rotating shaft (2), a piston (3) and a cylinder (4). A rotating
shaft hole (21) is provided in the rotating shaft (2). An oil
guiding channel communicated with the rotating shaft hole (21) is
provided in the cylinder (4). A recess (45) is formed in the inner
end face of the cylinder (4). An oil path sealed relative to a
compression cavity of the cylinder (4) is formed between the recess
(45) and the piston (3). The oil path is communicated with an oil
path between the piston (3) and the rotating shaft (2) and is
communicated with the oil guiding channel by means of an oil
returning channel. Also provided is a compressor including the
compressor pump.
Inventors: |
Huang; Hui; (Guangdong,
CN) ; Hu; Yusheng; (Guangdong, CN) ; Deng;
Liying; (Guangdong, CN) ; Du; Zhongcheng;
(Guangdong, CN) ; Xu; Jia; (Guangdong,
CN) |
|
Applicant: |
Name |
City |
State |
Country |
Type |
GREE GREEN REFRIGERATION TECHNOLOGY CENTER CO., LTD. OF
ZHUHAI |
Guangdong |
|
CN |
|
|
Family ID: |
57114560 |
Appl. No.: |
16/314584 |
Filed: |
February 17, 2017 |
PCT Filed: |
February 17, 2017 |
PCT NO: |
PCT/CN2017/073923 |
371 Date: |
December 31, 2018 |
Current U.S.
Class: |
1/1 |
Current CPC
Class: |
F04C 2240/60 20130101;
F04C 2210/22 20130101; F04C 18/00 20130101; F04C 15/0088 20130101;
F04C 2240/603 20130101; F04C 29/023 20130101; F04C 2/344 20130101;
F04C 15/06 20130101; F04C 15/0057 20130101 |
International
Class: |
F04C 29/02 20060101
F04C029/02; F04C 18/00 20060101 F04C018/00 |
Foreign Application Data
Date |
Code |
Application Number |
Jul 29, 2016 |
CN |
201610614674.X |
Claims
1. A rotary cylinder piston compressor pump, comprising a rotating
shaft (2), a piston (3) and a cylinder (4), a rotating shaft hole
(21) being provided in the rotating shaft (2), and an oil guiding
channel communicated with the rotating shaft hole (21) being
provided in the cylinder (4), wherein a recess (45) is formed in an
inner end face of the cylinder (4), an oil path sealed relative to
a compression cavity of the cylinder (4) is formed between the
recess (45) and the piston (3), and the oil path is communicated
with an oil path between the piston (3) and the rotating shaft (2)
and is communicated with the oil guiding channel by means of an oil
returning channel.
2. The rotary cylinder piston compressor pump as claimed in claim
1, wherein the oil returning channel comprises a cylinder oil hole
(46) provided on the cylinder (4), and the cylinder oil hole (46)
penetrates through a bottom of the recess (45) and an outer surface
of the cylinder (4).
3. The rotary cylinder piston compressor pump as claimed in claim
2, wherein the cylinder (4) comprises a cylinder short shaft (42),
the oil returning channel further comprises a cylinder short shaft
hole (47) provided on the cylinder short shaft (42), the cylinder
short shaft hole (47) is communicated with the cylinder oil hole
(46), and the cylinder short shaft hole (47) penetrates through an
inner surface and an outer surface of the cylinder short shaft
(42).
4. The rotary cylinder piston compressor pump as claimed in claim
1, wherein an intersection area of the rotating shaft hole (21) and
the oil guiding channel is not less than 20% of a cross-sectional
area of the rotating shaft hole (21).
5. The rotary cylinder piston compressor pump as claimed in claim
1, wherein the cylinder (4) comprises a cylinder short shaft (42),
and the oil guiding channel is a cylinder hole (43) provided in the
cylinder short shaft (42).
6. The rotary cylinder piston compressor pump as claimed in claim
1, wherein the oil guiding channel is an oil guiding pipe (7); the
cylinder (4) comprises a cylinder short shaft (42), the cylinder
short shaft (42) is provided with a through hole structure (48) for
providing a moving space for movement of the oil guiding pipe (7),
and the oil guiding pipe (7) is disposed in the through hole
structure (48); and one end of the oil guiding pipe (7) is mounted
on the rotating shaft (2), an outlet end of the oil guiding pipe
(7) is butted with the rotating shaft hole (21), and an oil guiding
sheet (8) is disposed in the oil guiding pipe (7).
7. The rotary cylinder piston compressor pump as claimed in claim
1, wherein a rotating shaft hole oil guiding sheet (22) is disposed
in the rotating shaft hole (21).
8. The rotary cylinder piston compressor pump as claimed in claim
1, wherein a piston oil hole (31) penetrating through an inner
surface and an outer surface of the piston (3) is provided on a
side wall of the piston (3).
9. The rotary cylinder piston compressor pump as claimed in claim
1, wherein an inlet end of the rotating shaft hole (21) is a
tapered structure flared outward.
10. The rotary cylinder piston compressor pump as claimed in claim
4, wherein the cylinder (4) comprises a cylinder short shaft (42),
and the oil guiding channel is a cylinder hole (43) provided in the
cylinder short shaft (42).
11. The rotary cylinder piston compressor pump as claimed in claim
4, wherein the oil guiding channel is an oil guiding pipe (7); the
cylinder (4) comprises a cylinder short shaft (42), the cylinder
short shaft (42) is provided with a through hole structure (48) for
providing a moving space for movement of the oil guiding pipe (7),
and the oil guiding pipe (7) is disposed in the through hole
structure (48); and one end of the oil guiding pipe (7) is mounted
on the rotating shaft (2), an outlet end of the oil guiding pipe
(7) is butted with the rotating shaft hole (21), and an oil guiding
sheet (8) is disposed in the oil guiding pipe (7).
12. A compressor, comprising a rotary cylinder piston compressor
pump, the rotary cylinder piston compressor pump comprising a
rotating shaft (2), a piston (3) and a cylinder (4), a rotating
shaft hole (21) being provided in the rotating shaft (2), and an
oil guiding channel communicated with the rotating shaft hole (21)
being provided in the cylinder (4), wherein a recess (45) is formed
in an inner end face of the cylinder (4), an oil path sealed
relative to a compression cavity of the cylinder (4) is formed
between the recess (45) and the piston (3), and the oil path is
communicated with an oil path between the piston (3) and the
rotating shaft (2) and is communicated with the oil guiding channel
by means of an oil returning channel.
Description
[0001] The present application claims benefit of Chinese Patent
Application No. 201610614674.X, filed to the China Patent Office on
Jul. 29, 2016, entitled "Rotary Cylinder Piston Compressor Pump and
Compressor with the Rotary Cylinder Piston Compressor Pump", the
contents of which are hereby incorporated in its entirety by this
reference.
TECHNICAL FIELD
[0002] The present disclosure relates to a technical field of
compressors, and more particularly to a rotary cylinder piston
compressor pump and a compressor with the rotary cylinder piston
compressor pump.
BACKGROUND
[0003] A rotary cylinder piston compressor belongs to a
refrigeration piston compressor of a brand new structure, which
essentially adopts a cross slider structure principle. Referring to
FIG. 10, O1 is the center of a rotating shaft, O2 is the center of
a cylinder, e is a center-to-center distance (i.e., eccentric
amount of the compressor), and a square is the center of mass of a
piston. When the rotating shaft rotates, the piston is driven to
move in a circular motion, and the distance between the piston and
the center of the cylinder is in the range of 0 to e. The rotating
shaft is eccentrically assembled with the cylinder, and the
rotating shaft drives the cylinder to rotate through the piston.
Due to the eccentric relationship between the rotating shaft and
the cylinder, the rotating shaft and the cylinder rotate around the
respective axes during operation, and the piston reciprocates
relative to the cylinder to achieve gas compression.
[0004] Specifically, the rotating shaft of the rotary cylinder
piston compressor is eccentrically assembled with the cylinder, the
rotating shaft drives the cylinder to rotate through the piston,
and oil is pumped through a short shaft hole in a cylinder short
shaft to a rotating shaft hole in the rotating shaft of the
cylinder. Due to the eccentric relationship between the rotating
shaft and the cylinder, the rotating shaft and the cylinder rotate
around the respective axes during operation. On the one hand, the
contact between the lower end surface of the rotating shaft and the
end surface of the cylinder ensures the oil supply of the rotating
shaft, but brings adverse influence on the circulation of an oil
groove oil channel on the side surface of the rotating shaft, which
is not conducive to the lubrication the kinematic pair of the
rotating shaft and the piston under heavy working conditions. On
the other hand, an intersection area of the inner hole of the
rotating shaft and the inner hole of the cylinder rotating shaft
has a great influence on the oil supply of the rotating shaft.
[0005] In view of the above problems, there is a need for a rotary
cylinder piston compressor pump and a compressor with the rotary
cylinder piston compressor pump, which can solve the problem in the
conventional art of large circulation resistance of an oil groove
oil channel on the side surface of a rotating shaft.
SUMMARY
[0006] An objective of the present disclosure is to provide a
rotary cylinder piston compressor pump, which can solve the problem
in the conventional art of large circulation resistance of an oil
groove oil channel on the side surface of a rotating shaft.
[0007] Another objective of the present disclosure is to provide a
compressor adopting the rotary cylinder piston compressor pump as
described above.
[0008] In order to achieve the objectives, the present disclosure
adopts the following technical solutions.
[0009] A rotary cylinder piston compressor pump includes a rotating
shaft, a piston and a cylinder, wherein a rotating shaft hole is
provided in the rotating shaft, an oil guiding channel communicated
with the rotating shaft hole is provided in the cylinder, a recess
is formed in the inner end face of the cylinder, an oil path sealed
relative to a compression cavity of the cylinder is formed between
the recess and the piston, and the oil path is communicated with an
oil path between the piston and the rotating shaft and is
communicated with the oil guiding channel by means of an oil
returning channel.
[0010] As a preferred solution of the above rotary cylinder piston
compressor pump, the oil returning channel includes a cylinder oil
hole provided on the cylinder, and the cylinder oil hole penetrates
through the bottom of the recess and the outer surface of the
cylinder.
[0011] As a preferred solution of the above rotary cylinder piston
compressor pump, the oil returning channel further includes a
cylinder short shaft hole provided on a cylinder short shaft, the
cylinder short shaft hole is communicated with the cylinder oil
hole, and the cylinder short shaft hole penetrates through the
inner surface and the outer surface of the cylinder short
shaft.
[0012] As a preferred solution of the above rotary cylinder piston
compressor pump, an intersection area of the rotating shaft hole
and the oil guiding channel is not less than 20% of a
cross-sectional area of the rotating shaft hole.
[0013] As a preferred solution of the above rotary cylinder piston
compressor pump, the cylinder includes a cylinder short shaft, and
the oil guiding channel is a cylinder hole provided in the cylinder
short shaft.
[0014] As a preferred solution of the above rotary cylinder piston
compressor pump, the oil guiding channel is an oil guiding
pipe;
[0015] the cylinder includes a cylinder short shaft, the cylinder
short shaft is provided with a through hole structure for providing
a moving space for movement of the oil guiding pipe, and the oil
guiding pipe is disposed in the through hole structure; and one end
of the oil guiding pipe is mounted on the rotating shaft, the
outlet end of the oil guiding pipe is butted with the rotating
shaft hole, and an oil guiding sheet is disposed in the oil guiding
pipe.
[0016] As a preferred solution of the above rotary cylinder piston
compressor pump, a rotating shaft hole oil guiding sheet is
disposed in the rotating shaft hole.
[0017] As a preferred solution of the above rotary cylinder piston
compressor pump, a piston oil hole penetrating through the inner
surface and the outer surface of the piston is provided on the side
wall of the piston.
[0018] As a preferred solution of the above rotary cylinder piston
compressor pump, the inlet end of the rotating shaft hole is a
tapered structure flared outward.
[0019] A compressor may include the rotary cylinder piston
compressor pump as described above.
[0020] The present disclosure has the beneficial effects as
follows. By providing the recess and the oil returning channel, the
oil discharging resistance of an oil hole in the side surface of
the rotating shaft is effectively reduced, the oil discharging
quantity of the oil hole of the rotating shaft is increased, and
therefore, the problem of abnormal abrasion caused by insufficient
lubrication between the side surface of the rotating shaft and the
piston under a heavy working condition is effectively solved.
BRIEF DESCRIPTION OF THE DRAWINGS
[0021] FIG. 1 is a schematic diagram illustrating an exploded state
of a rotary cylinder piston compressor pump according to a first
specific embodiment of the present disclosure;
[0022] FIG. 2 is a schematic structure diagram of a rotary cylinder
piston corepressor pump according to a first embodiment of the
present disclosure;
[0023] FIG. 3 is a partial enlarged view of "part I" in FIG. 2;
[0024] FIG. 4 is a schematic structure diagram of a rotating shaft
according to a first embodiment of the present disclosure;
[0025] FIG. 5 is a schematic structure diagram of a cylinder
according to a first embodiment of the present disclosure;
[0026] FIG. 6 is a schematic diagram illustrating an exploded state
of a rotary cylinder piston compressor pump according to a second
embodiment of the present disclosure;
[0027] FIG. 7 is a schematic structure diagram of a rotary cylinder
piston compressor pump according to a second embodiment of the
present disclosure;
[0028] FIG. 8 is a schematic structure diagram of a rotating shaft
according to a second embodiment of the present disclosure;
[0029] FIG. 9 is a schematic structure diagram of a cylinder
according to a second embodiment of the present disclosure; and
[0030] FIG. 10 is a schematic structure diagram of a cross
slider.
[0031] 1: Upper flange; 2: rotating shaft; 3: piston; 4: cylinder;
5: cylinder sleeve; 6: lower flange; 7: oil guiding pipe; 8: oil
guiding sheet;
[0032] 21: rotating shaft hole; 22: rotating shaft hole oil guiding
sheet;
[0033] 31: piston oil hole;
[0034] 41: piston hole; 42: cylinder short shaft; 43: cylinder
hole; 44: cylinder hole oil guiding sheet; 45: recess; 46: cylinder
oil hole; 47: cylinder short shaft hole; 48: through hole
structure.
DETAILED DESCRIPTION OF THE EMBODIMENTS
[0035] The technical solutions of the present disclosure will be
further described below in conjunction with the accompanying
drawings and specific implementations.
First Embodiment
[0036] As shown in FIG. 1 to FIG. 5, the present embodiment
provides a rotary cylinder piston compressor pump. The rotary
cylinder piston compressor pump includes an upper flange 1, a
rotating shaft 2, a piston 3, a cylinder 4, a cylinder sleeve 5,
and a lower flange 6, wherein the piston 3 is mounted in a piston
hole 41 of the cylinder 4, a cylinder short shaft 42 of the
cylinder 4 is mounted on the lower flange 6, the cylinder sleeve 5
is mounted coaxially with the cylinder 4, the lower flange 6 is
fixed at the lower end of the cylinder sleeve 5, a piston bearing
surface of the rotating shaft 2 is fitted with a piston plane, the
upper flange 1 fixes the upper half of the rotating shaft 2, and
the upper flange 1 is fixed to the upper end of the cylinder sleeve
5 by screws.
[0037] Specifically, a rotating shaft hole 21 is provided in the
rotating shaft 2, and an oil guiding channel communicated with the
rotating shaft hole 21 is provided in the cylinder 4.
[0038] Referring to FIG. 2 and FIG. 5, a recess 45 is formed in the
inner end face of the cylinder 4, an oil path sealed relative to a
compression cavity of the cylinder 4 is formed between the recess
45 and the piston 3, the oil path is communicated with an oil path
between the piston 3 and the rotating shaft 2 and is communicated
with the oil guiding channel by means of an oil returning channel.
Specifically, referring to FIG. 5, the recess 45 is an annular oil
groove provided around the cylinder short shaft 42, and the
provision of the recess 45 does not affect the air tightness
between the cylinder short shaft 42 and the rotating shaft 2.
[0039] By providing the recess 45 and the oil returning channel,
the oil discharging resistance of an oil hole in the side surface
of the rotating shaft 2 is reduced, the oil discharging quantity of
the oil hole of the rotating shaft 2 is increased, and therefore,
the problem of abnormal abrasion caused by insufficient lubrication
between the side surface of the rotating shaft 2 and the piston 3
under a heavy working condition is effectively solved.
[0040] The oil returning channel includes a cylinder oil hole 46
provided on the cylinder 4, and the cylinder oil hole 46 penetrates
through the bottom of the recess 45 and the outer surface of the
cylinder 4.
[0041] The oil returning channel further includes a cylinder short
shaft hole 47 provided on the cylinder short shaft 42, the cylinder
short shaft hole 47 is communicated with the cylinder oil hole 46,
and the cylinder short shaft hole 47 penetrates through the inner
surface and the outer surface of the cylinder short shaft 42.
[0042] By providing the recess 45, the cylinder oil hole 46 and the
cylinder short shaft hole 47, the oil discharging resistance of the
oil hole in the side surface of the rotating shaft 2 is further
reduced, the oil discharging quantity of the oil hole of the
rotating shaft 2 is increased, and therefore, the problem of
abnormal abrasion caused by insufficient lubrication between the
side surface of the rotating shaft 2 and the piston 3 under a heavy
working condition is effectively solved.
[0043] An intersection area of the rotating shaft hole 21 and the
oil guiding channel is not less than 20% of a cross-sectional area
of the rotating shaft hole 21. By increasing the intersection area
of the rotating shaft hole 21 and the oil guiding channel, the oil
pumping amount of the rotating shaft 2 is able to be increased.
[0044] A specific means of increasing the intersection area of the
rotating shaft hole 21 and the oil guiding channel is to increase
the diameter of the rotating shaft hole 21 of the rotating shaft 2.
Preferably, the ratio of the inner diameter of the rotating shaft
hole 21 to the outer diameter of the rotating shaft 2 ranges from
0.3 to 0.6. Further preferably, the ratio of the inner diameter of
the rotating shaft hole 21 to the outer diameter of the rotating
shaft 2 is 0.35, 0.4 or 0.5. In the present embodiment, the inner
diameter of the rotating shaft hole 21 is 6 mm, and the outer
diameter of the rotating shaft 2 is 16.5 mm.
[0045] Referring to FIG. 2, in the present embodiment, the cylinder
4 includes a cylinder short shaft 42, and the oil guiding channel
is a cylinder hole 43 provided in the cylinder short shaft 42. The
cylinder hole 43 is provided with a cylinder hole oil guiding sheet
44. The cylinder hole oil guiding sheet 44 rotates in synchronism
with the cylinder 4 and pumps oil into the rotating shaft hole 21
by a centrifugal force. Preferably, an intersection area of the
rotating shaft hole 21 and the cylinder hole 43 is not less than
one-third or one-fifth of the cross-sectional area of the rotating
shaft hole 21.
[0046] Referring to FIG. 1 and FIG. 2, in order to further increase
the oil pumping amount of the rotating shaft 2, a rotating shaft
hole oil guiding sheet 22 is disposed in the rotating shaft hole
21. The rotating shaft hole oil guiding sheet 22 has the same
structure as the conventional cylinder hole oil guiding sheet 44
disposed in the cylinder hole 43, and has a spiral blade type
structure.
[0047] A piston oil hole 31 penetrating through the inner surface
and the outer surface of the piston 3 is provided on the side wall
of the piston 3. The piston oil hole 31 can lubricate the outer
wall surface of the piston 3 and the inner wall surface of the
cylinder 4 while reducing the oil loss caused by the reciprocating
motion of the rotating shaft 2 in the piston hole.
[0048] The inlet end of the rotating shaft hole 21 is a tapered
structure flared outward. By arranging the end portion of the
rotating shaft hole 21 into a tapered structure, an intersection
area of the rotating shaft hole 21 and the oil guiding channel can
be effectively increased under the premise of the same hole
diameter of the rotating shaft hole 21.
[0049] In order to further explain the above rotary cylinder piston
compressor pump, the present embodiment also provides the working
process of the above pump:
[0050] A motor drives the rotating shaft 2 to rotate, and the
piston supporting surface of the rotating shaft 2 drives the piston
3 to rotate, but the piston 3 only reciprocates relative to the
rotating shaft 2; the non-circular (or circular) side of the piston
further drives the cylinder 4 to rotate, at this time, the piston 3
only reciprocates relative to the cylinder 4, and the reciprocating
direction of the piston 3 to the cylinder 4 is perpendicular to the
reciprocating direction of the piston 3 to the rotating shaft 2;
during the reciprocating motion, the entire pump structure
completes the process of suction, compression and exhaust.
[0051] The present embodiment also provides a compressor, which
includes the rotary cylinder piston compressor pump as described
above.
Second Embodiment
[0052] As shown in FIG. 6 to FIG. 9, in the present embodiment,
another structural form of an oil guiding channel is provided.
Referring to FIG. 6 and FIG. 7, the oil guiding channel is an oil
guiding pipe 7. The cylinder 4 includes a cylinder short shaft 42,
the cylinder short shaft 42 is provided with a through hole
structure 48 for providing a moving space for movement of the oil
guiding pipe 7, and the oil guiding pipe 7 is disposed in the
through hole structure 48. One end of the oil guiding pipe 7 is
mounted on the rotating shaft 2, the outlet end of the oil guiding
pipe 7 is butted with the rotating shaft hole 21, and an oil
guiding sheet 8 is disposed in the oil guiding pipe 7. The
structure of the oil guiding sheet is the same as that of the
rotating shaft oil guiding sheet 22 mentioned in the first
embodiment.
[0053] In order to provide a moving space for the oil guiding pipe
7, the inner diameter of the cylinder short shaft 42 is larger than
the inner diameter of the cylinder short shaft 42 in the first
embodiment, and the corresponding inner diameter of a bearing on a
lower flange 6 is also increased. Specifically, the ratio of the
inner diameter of the through hole structure 48 to the outer
diameter of the cylinder short shaft 42 ranges from 0.6 to 0.8.
Preferably, the ratio of the inner diameter of the through hole
structure 48 to the outer diameter of the cylinder short shaft 42
is 0.65, 0.7 or 0.75. In the present embodiment, the inner diameter
of the through hole structure 48 is 14 mm, and the outer diameter
of the cylinder short shaft 42 is 20 mm.
[0054] One end of the oil guiding pipe 7 is inserted into the
rotating shaft hole 21, and the end portion of the rotating shaft
hole 21 is arranged in a tapered structure. When the oil guiding
pipe 7 is assembled into the rotating shaft hole 21, the tapered
structure can play a guiding role, which is convenient for assembly
of the oil guiding pipe 7. Referring to FIG. 8, the lower end of
the rotating shaft hole 21 is a stepped hole for inserting the oil
guiding pipe 7. By using the oil guiding pipe 7 as the oil guiding
channel, the intersection area of the rotating shaft hole 21 and
the oil guiding channel can be made the same as the cross-sectional
area of the rotating shaft hole 21, whereby the oil pumping effect
of the rotating shaft 2 can be remarkably improved.
[0055] It is to be noted that in this embodiment, other structures
are the same as that of the first embodiment except that the
structural form of the oil guiding channel is different from that
of the first embodiment.
[0056] The technical principles of the present disclosure have been
described above in connection with specific embodiments. The
descriptions are only intended to explain the principles of the
present disclosure and are not to be construed as limiting the
scope of protection of the present disclosure. Based on the
explanation herein, those skilled in the art can associate other
specific implementations of the present disclosure without making
creative works. These modes fall within the scope of protection of
the present disclosure.
* * * * *