U.S. patent application number 16/383102 was filed with the patent office on 2019-10-17 for building foundation repair product.
The applicant listed for this patent is DONALD BARTON. Invention is credited to DONALD BARTON.
Application Number | 20190316314 16/383102 |
Document ID | / |
Family ID | 68161394 |
Filed Date | 2019-10-17 |


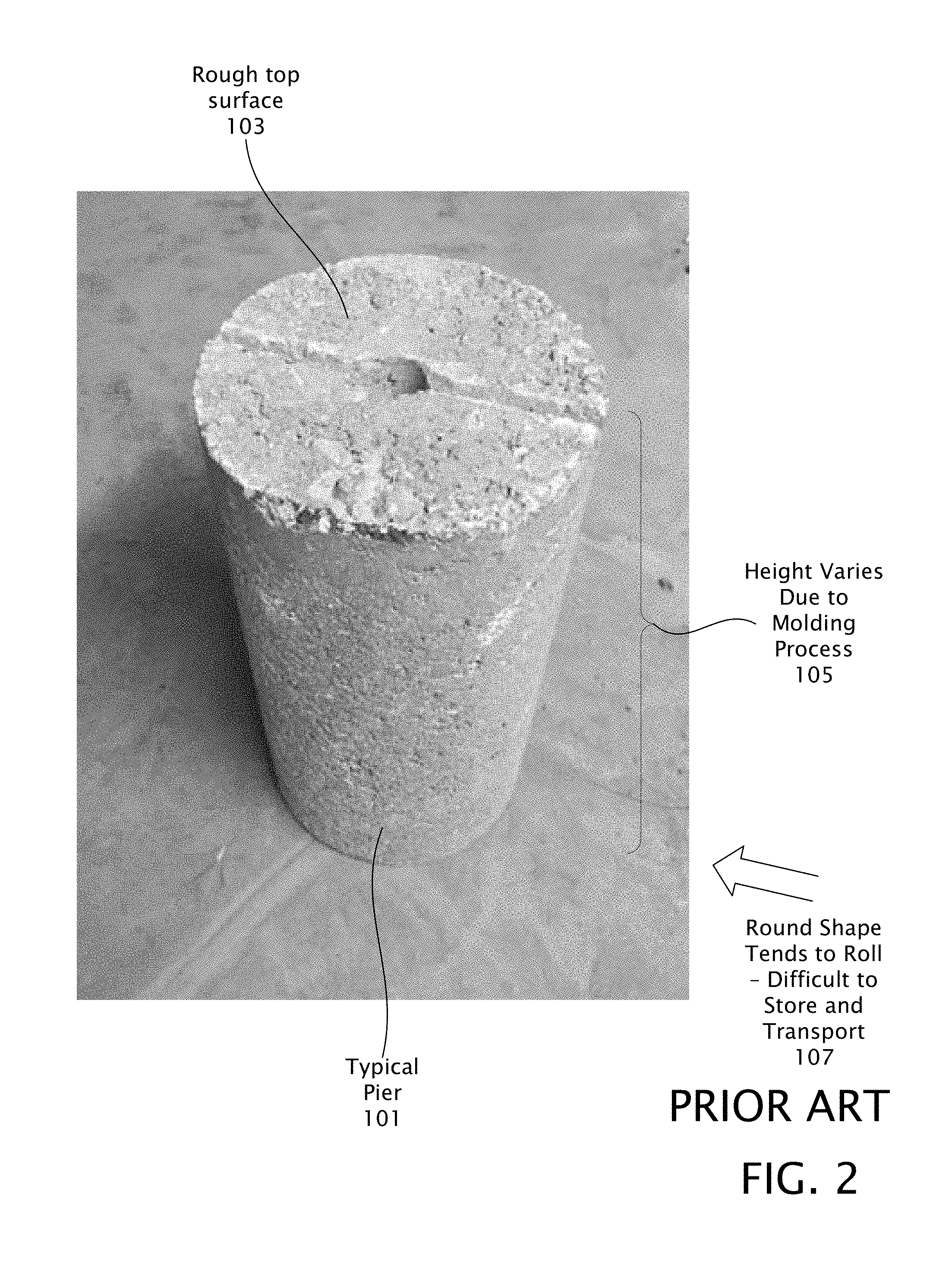




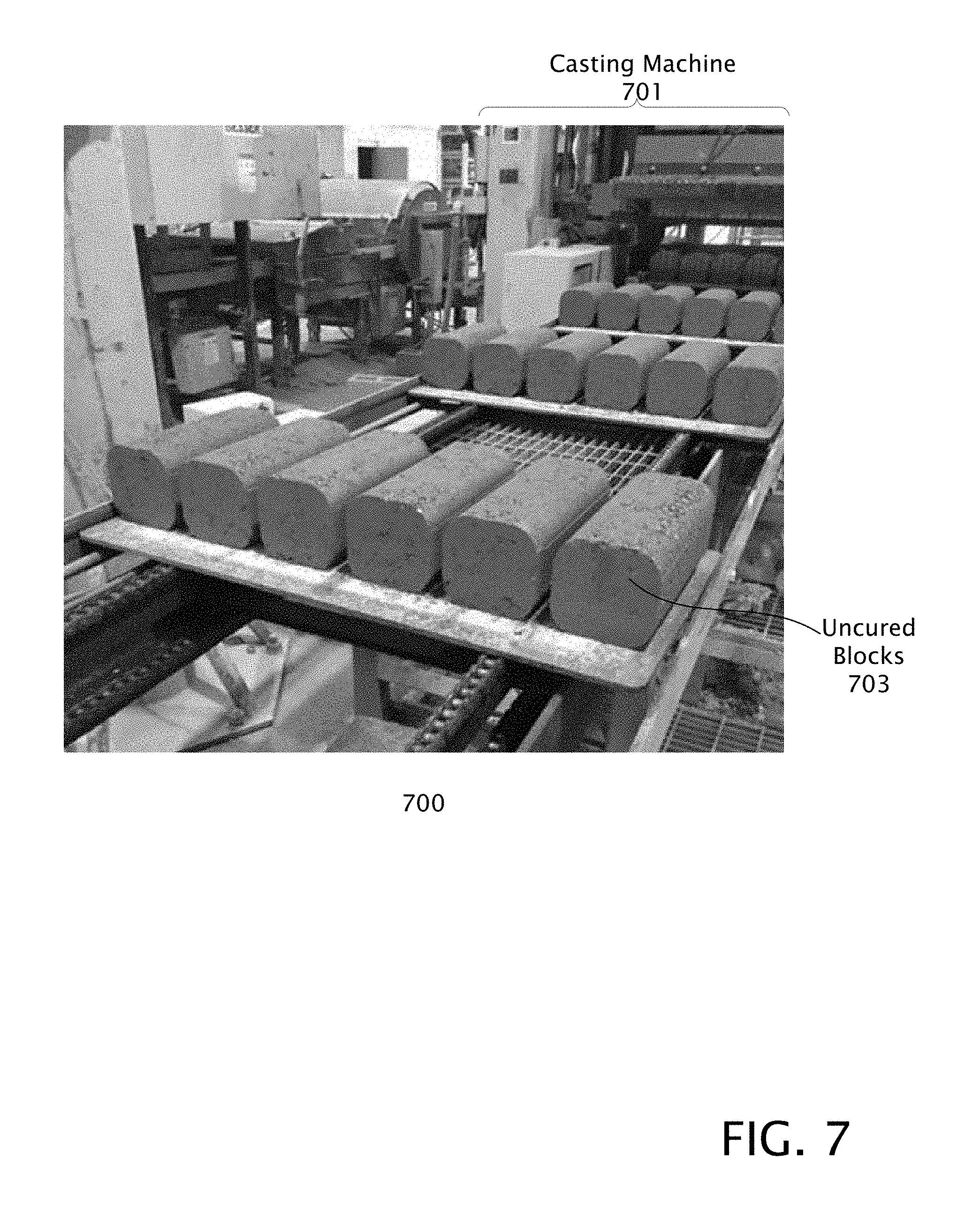



United States Patent
Application |
20190316314 |
Kind Code |
A1 |
BARTON; DONALD |
October 17, 2019 |
BUILDING FOUNDATION REPAIR PRODUCT
Abstract
The present example provides a building foundation repair
product that is a horizontally cast concrete product. Horizontal
casting, unlike the typical vertical casting produces smooth end
surfaces that aid in installing the building foundation repair
product as the end surfaces are defined by the mold. Also, the
building foundation repair product has been designed with flat
surfaces that make up its sides. The flat surfaces advantageously
tend to prevent the product from rolling when used at a job site,
and allows the a building foundation repair product to be easily
palletized for shipping, as they tend to be stable when stacked on
the pallet.
Inventors: |
BARTON; DONALD; (Houston,
TX) |
|
Applicant: |
Name |
City |
State |
Country |
Type |
BARTON; DONALD |
Houston |
TX |
US |
|
|
Family ID: |
68161394 |
Appl. No.: |
16/383102 |
Filed: |
April 12, 2019 |
Related U.S. Patent Documents
|
|
|
|
|
|
Application
Number |
Filing Date |
Patent Number |
|
|
62657726 |
Apr 14, 2018 |
|
|
|
Current U.S.
Class: |
1/1 |
Current CPC
Class: |
E02D 5/30 20130101; E02D
5/665 20130101; E02D 37/00 20130101 |
International
Class: |
E02D 37/00 20060101
E02D037/00; E02D 5/66 20060101 E02D005/66; E02D 5/30 20060101
E02D005/30 |
Claims
1. A building foundation repair product formed by a process
comprising: filling a horizontally oriented mold for forming a
right irregular cylinder with rounded square bases with concrete,
from a side; striking off excess cement from the mold; compacting
the cement; forming a radius; and replacing a radius forming rod
with a division plate.
2. The building foundation repair product formed by a process of
claim 1, in which compacting is provided by vibrating.
3. The building foundation repair product formed by a process of
claim 1, further comprising forming rod apertures in the foundation
repair product.
4. The building foundation repair product formed by a process of
claim 1, further comprising curing the foundation repair
product.
5. The building foundation repair product formed by a process of
claim 1, further comprising lifting the mold into position.
6. A building foundation repair product comprising: a concrete
block shaped in the form of a right irregular cylinder with rounded
square bases.
7. The building foundation repair product of claim 6 in which a
length from a top rounded square base to a bottom rounded square
base is twelve inches.
8. The building foundation repair product of claim 6 in which a
distance between parallel flat surfaces is five and a half
inches.
9. The building foundation repair product of claim 6 in which each
corner of a plurality of rounded corners has a one and a half inch
radius.
10. The building foundation repair product of claim 6 further
comprising a longitudinal circular cylindrical aperture centered in
the top and bottom rounded square bases.
11. The building foundation repair product of claim 6 in which the
rounded square bases include a top rounded square base and a bottom
rounded square base each formed by concrete in contact with a mold
surface.
Description
CROSS-REFERENCE TO RELATED APPLICATION
[0001] This application claims the benefit of U.S. Provisional
Patent Application No. 62/657,726 filed Apr. 14, 2018, the contents
of which are hereby incorporated by reference.
TECHNICAL FIELD
[0002] This description relates generally to masonry building
products and more specifically to building foundation repair.
BACKGROUND
[0003] Buildings are prone to settling as they age and the
underlying soil compacts or otherwise changes over time. Settling
can cause cracks in walls and floors, as well a degradation of a
level surface. In colder climates buildings tend to have more
substantial footings due to the freezing and thawing that
necessitates a deeper footing to extend below the frost line. In
warmer areas not prone top freezing the building may merely be
constructed on a concrete slab poured in place. Both types of
foundation are prone to settling. In slab construction a remedy for
a sinking or cracked foundation may be to excavate under the slab
and attempt to raise it back to its original level by various
methods. Accordingly a building foundation repair product would be
useful in supporting damaged building foundations and slabs would
be desirable.
SUMMARY
[0004] The following presents a simplified summary of the
disclosure in order to provide a basic understanding to the reader.
This summary is not an extensive overview of the disclosure and it
does not identify key/critical elements of the invention or
delineate the scope of the invention. Its sole purpose is to
present some concepts disclosed herein in a simplified form as a
prelude to the more detailed description that is presented
later.
[0005] The present example provides a building foundation repair
product that is a horizontally cast concrete product. Horizontal
casting, unlike the typical vertical casting produces smooth end
surfaces that aid in installing the building foundation repair
product as the end surfaces are defined by the mold. Also, the
building foundation repair product has been designed with flat
surfaces that make up its sides. The flat surfaces advantageously
tend to prevent the product from rolling when used at a job site,
and allows the a building foundation repair product to be easily
palletized for shipping, as they tend to be stable when stacked on
the pallet.
[0006] Many of the attendant features will be more readily
appreciated as the same becomes better understood by reference to
the following detailed description considered in connection with
the accompanying drawings.
DESCRIPTION OF THE DRAWINGS
[0007] The present description will be better understood from the
following detailed description read in light of the accompanying
drawings, wherein:
[0008] FIG. 1 shows a method of installing piers to repair a
cracked foundation.
[0009] FIG. 2 shows a typical pier used in foundation repair.
[0010] FIG. 3 shows an improved building foundation repair
product.
[0011] FIG. 4 shows an inclined view of the improved building
foundation repair product.
[0012] FIG. 5 shows a plan view of the improved building foundation
repair product.
[0013] FIG. 6 shows a pallet of improved building foundation repair
products prepared for shipping.
[0014] FIG. 7 shows uncured horizontally cast improved building
foundation repair products exiting the casting machine.
[0015] FIG. 8 shows details of the mold mechanism for casting
improved building foundation repair products.
[0016] FIG. 9 shows the mold for casting improved building
foundation repair products.
[0017] FIG. 10 is a flow diagram showing a process for
manufacturing the improved building foundation repair product.
[0018] Like reference numerals are used to designate like parts in
the accompanying drawings.
DETAILED DESCRIPTION
[0019] The detailed description provided below in connection with
the appended drawings is intended as a description of the present
examples and is not intended to represent the only forms in which
the present example may be constructed or utilized. The description
sets forth the functions of the example and the sequence of steps
for constructing and operating the example. However, the same or
equivalent functions and sequences may be accomplished by different
examples.
[0020] The examples below describe a building foundation repair
product (or equivalently a "block" or "pier"). Although the present
examples are described and illustrated herein as being implemented
in a house foundation repair system, the system described is
provided as an example and not a limitation. As those skilled in
the art will appreciate, the present examples are suitable for
application in a variety of different types of foundation leveling
systems.
[0021] As utilized herein a rounded square shape, may be generated
by separating four quarters of a circle and connecting their loose
ends with straight lines, or by separating the four sides of a
square and connecting them with quarter-circles. The rounded square
can be scaled up or down quite easily. Another way to describe a
rounded square is as a square simply having rounded corners.
[0022] As utilized herein generally a prism is a shape having flat
sides connecting two parallel bases. The bases are polygons (either
regular or irregular). If the bases are not parallel, then the
shape is not a prism. Each side of a prism is a parallelogram. A
prism with square bases is a square prism.
[0023] In addition to the attributes of a prism, and as utilized
herein a square prism is a three dimensional solid object whose
bases are squares. In a square prism, the opposite sides and angles
are congruent. A cube is a special case of a square prism as the
lines connecting the faces are the same length as the lines making
up the square bases.
[0024] As utilized herein a cylinder shape has one curved side
coupling two parallel bases. The bases are curved shapes (either
regular or irregular). If the bases are not parallel, then the
shape is not a cylinder. A cylinder with round bases is a circular
cylinder.
[0025] Prisms and cylinders may be right (the bases are
perpendicular to the sides), or oblique (the bases are not
perpendicular to the sides). Bases may be regular or irregular. A
regular shape is one having equal edge lengths, and/or equal
angles. Both prisms and cylinders have bases that are coupled
together by the sides. Both prisms and cylinders have cross
sections that are identical to the bases. A cylinder has one side,
and a prism may have an infinite number of sides.
[0026] The term cement as used herein is a binding material,
typically used in construction that sets, hardens, and adheres to
other materials, thus binding them together. Cement is seldom used
without adding other substances that it binds together. Typically
cement binds sand and gravel (aggregate) in various forms together.
Cement mixed with fine aggregate is termed mortar that may be used
in setting masonry bricks. When cement is mixed with sand and
gravel concrete that may be formed or cast in various shapes is
produced. Mortar and concrete are typically mixed with water when
being prepared for use. Cement may be of the non-hydraulic, or
hydraulic type (Portland cement). Portland cement, that is widely
used, typically contains calcium carbonate (lime) that has been
heated to form calcium oxide (quicklime) and other additives such
as gypsum. Cement may also be mixed with other substances such as
pigment and the like.
[0027] FIG. 1 shows a system for installing piers 207, 209 to
repair a cracked 203 foundation 201. Building foundations 201,
especially slab type construction, are typically subject to
settling and shifting over time. This can lead to cracks 203 in
walls, slabs, and other damage to a building. A typical technique
for repairing this type of damage to a slab foundation is to
excavate 205 around a foundation 201 perimeter at periodic
intervals, with the excavation 205 extending under the foundation
201 so that one or more support piers 207, 209 may be driven into
the ground to support the foundation 201. A concrete cylinder 209
(conventional building foundation repair product) is typically
placed under the foundation (here shown installed on top of a
previously installed pier 207). A hydraulic jack or equivalent 211
may be inserted in the gap 214 between the bottom surface of the
foundation and the top of the concrete cylinder or pier 207.
[0028] When the jack 211 is pumped, expanding it, the cylinder 207,
209 is typically driven into the earth (or as shown here further
driving the second pier 207 further into the ground). The process
is repeated adding additional cylinders until they can no longer be
driven into the earth, and a stable support for the foundation has
been created. At this point the foundation is leveled and a final
remaining gap between the foundation and cylinder 213 is filled
with shims (typically stainless steel or the like-not shown). The
excavation 205 is filled in and the foundation 201 is now level so
that the structure may now be repaired.
[0029] It is worth pointing out that the piers, 207, 209 as
typically used are cylindrical. As far as is known this is a carry
over from when round wooden pilings or posts driven into the earth
such as this in order to support a structure such as a building,
dock, or the like. There is apparently no particular reason for the
round shape, other than historical tradition, as the round shape
can create some, until this time unsolved, problems for this
leveling methos.
[0030] FIG. 2 shows a typical pier, or equivalently pile 101 used
in foundation repair. Some of the drawbacks to these piers 101
include, the round shape 107 being difficult to handle and package
(they roll) 107, the finish surface 103 on the top/bottoms is
uneven and coarse (which can lead to failure), and the varying
heights of the units inherent in their manufacturing process.
[0031] Manufacturers of round cylinder foundation repair piers 101
typically invariably cast them vertically in the shape of a
generally circular cylinder, in cylindrical forms, as this is
typically the easiest way to cast a cylinder. Vertical casting
often results in rough concrete debris remaining on the side
forming the top base of the piers 101. The end user typically must
clean each unit with a hammer and chisel to insure no protrusions,
that could lead to failure, during the hydraulic push into the
ground at up to 10,000 psi. The pressure points tend to concentrate
the force which can crack the pier. Vertical casting has been done
for many years in spite of the difficulties encountered by
foundation repairmen with obtaining a smooth top and bottom surface
that can take the pressure produced by a jack driving the pier into
the ground.
[0032] The length of the piers 105 tends to vary during the forming
process. Screeding off the top surface after the mold has been
filled does not lend itself to constant height pier as the screed
may not be pressed level with the top of the form, either by
insufficient application of pressure, or by aggregate protruding
above the form and being resistant to the screed pushing it down
into the form, which also leads to the above mentioned rough
surfaces 103.
[0033] Typical round piles 101 are difficult to package and
transport. The round shape of cylinders is difficult to handle from
the point of manufacture to the final installation, as they tend to
roll due to the round shape. In packing they may be set upright on
their bases, but if care is not always taken to set them, on end,
on level ground they can easily roll. In spite of the above
mentioned difficulties piers have been made as described above
until this time to repair cracked or uneven foundations.
[0034] By realizing the drawbacks above, this discovery of the
problem is the invention that has led to the development of an
improved building foundation repair product. Cylindrical piers 101
have been used throughout the industry for years without
improvement. In fact, other methods of foundation leveling that
have been developed have taught away from improvement of the piers,
as such things as helical piers, steel piers and the like have been
use as alternatives to the cylindrical concrete piers. However,
improved concrete piers are apparently not be available.
[0035] FIG. 3 shows an improved building foundation repair product
300. Since introduction of this product demand, and hence sales
have been strong, showing that the improved building foundation
repair product has satisfied a long felt unmet need in the
foundation repair industry. The improved building foundation repair
product is designed to solve the issues discussed above regarding
conventional piers while retaining the performance specifications
of piers typically used in foundation leveling. A manufacturing
method to make the improved building foundation repair product has
also been developed that enables the improvements in the improved
building foundation repair product. In short a horizontal molding
process applied to making the improved building foundation repair
product allows the above mentioned problems with respect to
conventional cylindrical piers to be solved.
[0036] Benefits of the new design provides flat top and bottom
bases 303 for ease of installation, not requiring extra steps to
clean, brush and chip debris. The flat top 304 and bottom 302 bases
significantly reduces potential of failure due to raised debris.
The height between the top and bottom bases is also uniform and
controlled by the mold. Height of unit is consistent 12'', or as
desired for a given application 309.
[0037] The improved building foundation repair product may be
stacked on its sides or ends without rolling. Units have flat sides
307 to prevent rolling. In fact any conceivable surface upon which
the improved building foundation repair product comes to rest upon
will not lead to rolling. The improved building foundation repair
product allows for safe packaging when palletized for shipment.
[0038] In alternative examples of the improved building foundation
repair product other shapes that prevent rolling may be produced
that are also cast horizontally and have smooth ends. For example
polygons such as rectangular, semicircular, hexagonal, or other
polygons will provide flat sides from a horizontal mold that tends
to prevent rolling.
[0039] The rounded corners 301 tend to prevent chipping and
strengthen the improved building foundation repair product. It is
also contemplated that in equivalent examples the rounded corners
301 along the long axis of the building foundation repair product
as described herein, may equivalently be replaced by a simple
beveled edge or the like. In general reducing edges along the long
axis of the building foundation repair product ("knocked down
edges"), make it less prone to damage, chipping, or the like. In
general round or generally curved edges tend to be utilized in the
building foundation repair product. The improved building
foundation repair product 300 may also include a longitudinal
aperture 305 formed therein, to accommodate an alignment rod (not
shown) which may be used during foundation repair.
[0040] FIG. 4 shows an inclined view of the improved building
foundation repair product 300. The improved building foundation
repair product 300 may be describes as having the shape of a right
(not oblique) irregular cylinder, with bases in the shape of a
rounded square 401. Top base 304 and bottom base area 302 are in
the shape of a rounded square and identical. An aperture 405 may be
disposed along a longitudinal axis of the improved building
foundation repair product. Typically the aperture 405 has the
outline of a circular cylinder.
[0041] As a cylinder type of shape there is one side that wraps
around the top 304 and bottom 302 bases. The one side includes four
flat surfaces areas (two of which are shown 307, 308), each
longitudinally adjoining a rounded corner area in four places. The
four rounded corner areas are identical. The four surface areas are
each rectangular and identical.
[0042] FIG. 5 shows a plan view of the improved building foundation
repair product 300. The plan view of the rounded square bottom base
302 is identical to the plan view of the rounded square top base
405 shown, and is left out for simplification. The plan view of the
left side 509, the right side 507, and the bottom side 505 are
identical to the plan view of the top side 520 (shown) and are
omitted for the sake of brevity.
[0043] The dimensions of the rounded square base area 304 of the
improved building foundation repair product 300 are 5.5 inches
between sides. Those skilled in the art will realize that this
dimension is exemplary and other equivalent dimensions may be
utilized. The flat side areas 307 of the rounded square base 501
are coupled by an exemplary 1.5 inch radius quarter circle shaped
surfaces.
[0044] Those skilled in the art will realize that the improved
building foundation repair product 300 may be cast in equivalent
examples having top and bottom bases that will also provide a flat
side to stop rolling. For example rectangular, hexaganol,
octogonal, compound shapes, shape that provide one or more flat
surfaces, or the like.
[0045] The height of the improved building foundation repair
product 300 is 12 inches. The dimensions provided are exemplary
only and not intended to be limiting.
[0046] The improved building foundation repair product 300 can be
produced with or without a center aperture 405 (which may be
provided to accommodate a reinforcement rod added during
instillation), typically 3/4'' in diameter. The use of a center
aperture 405 is a preference by some installers with no additional
or loss of strength. The defining characteristic of the unit is the
smooth top and bottom which can only be achieved by the new
manufacturing design using a mold having a top and bottom base in
fixed relation to each other.
[0047] FIG. 6 shows a pallet of a plurality of improved building
foundation repair products 300 prepared for shipping 600. The
improved building foundation repair products 300 stack neatly on a
typical pallet 601, to which they may be securely strapped.
[0048] FIG. 7 shows production 700 of uncured horizontally cast
improved building foundation repair products 703 exiting the
casting machine 701. Horizontal casting in a mold that has top and
bottom surfaces as part of the mold enable the previously described
attributes to be obtained. A casting machine 701 such as the
exemplary Besser Ultrapac Concrete Products Machine may be used
with a custom made mold to produce improved building foundation
repair products at an exemplary rate of 36 improved building
foundation repair products per minute. Besser Ultrapac Concrete
Products Machiene is manufactured by Besser Inc. located at 801
Johnson Street, Alpena Mich.
[0049] A wide variety of sizes and types of machines may be
utilized to mold the improved building foundation repair products.
For example the improved building foundation repair products could
be molded one at a time by hand if desired. However, automated
equipment such as the exemplary casting machine tends to
efficiently and consistently produce the improved building
foundation repair products.
[0050] The concrete is transferred to the casting machine where it
is fed into the mold which has been previously set up in the
machine. The configuration of the mold in general determines the
size and style of the products produced, as the casting machine
tends to be general purpose in nature. Interchangable molds allows
the manufacturer to make a wide range of concrete products using
the same equipment in the same facility. Depending upon the demand
for products the mold may be changed after several hours, days or
weeks.
[0051] Once placed into the mold the concrete is typically
compacted and consolidated by a combination of pressure and
controlled vibration. Vibration may be customized for each improved
building foundation repair product being produced ensuring high
quality products with maximum compaction, uniformity and strength.
At the end of the molding cycle the improved building foundation
repair products are expelled from the mold onto a pallet or board
depending upon the factory set up.
[0052] As the products leave the casting machine a rotating brush
or a short blast of air can be used to remove loose pieces of
concrete. At this point the products are referred to as "green",
and then cured in a conventional manner prior to shipping.
[0053] FIG. 8 shows a simplified top view 800 the mold mechanism
for casting improved building foundation repair products. The mold
is designed with sliding split division plates 814 that move
forward and back to create the radius detail on the bottom side of
the improved building foundation repair product as a number of them
are being manufactured. This manufacturing design is unique to this
mold. Molding the product horizontally allows for both ends of the
unit to be flat-as fixed by the mold dimensions. Concrete is added
from the side (rather than the top) and a compacting head acts to
smooth the side where the concrete fills the mold. Horizontal
casting improves performance of the improved building foundation
repair product and eliminates the need for field clean up of the
ends. Subsequent field testing of the product has provided very
positive feedback. ASTM strength testing of the building foundation
repair product has also been encouraging.
[0054] The core rods 812 form the apertures in the improved
building foundation repair product.
[0055] The block produced by horizontal molding has ends that
contact the mold and produce smooth ends, as opposed to a vertical
casting process that leaves the ends rough.
[0056] FIG. 9 shows the mold 900 for horizontally casting improved
building foundation repair products. This mold allows six improved
building foundation repair products to be produced at a time. The
number produced is exemplary, and molds for producing different
numbers of improved building foundation repair products may
equivalently created. However all molds have surfaces that define
the top and bottom bases of the improved building foundation repair
products that are in fixed relation to each other, so that smooth
ends may be produced.
[0057] FIG. 10 is a flow diagram showing a process for
manufacturing the improved building foundation repair product 1000.
At building foundation repair product 1002 the mold is lifted in
position. The mold is filled with cement having an optional
smoothing agent added at 1004. The excess material is struck off at
1006 A head compacts the material in the mold 1008. The radius is
pulled out, and replaced with a division plate 1009 At block 1010
apertures through the block are formed with a rod. And finally the
building foundation repair product is cured.
[0058] Those skilled in the art will realize that the process
sequences described above may be equivalently performed in any
order to achieve a desired result. Also, sub-processes may
typically be omitted as desired without taking away from the
overall functionality of the processes described above.
* * * * *