U.S. patent application number 16/467439 was filed with the patent office on 2019-10-03 for lubricating composition comprising glycerol monoethers.
The applicant listed for this patent is CENTRE NATIONAL DE LA RECHERCHE SCIENTIFIQUE, TOTAL MARKETING SERVICES. Invention is credited to Nicolas CHAMPAGNE, Gwendoline GRAVE, Francoise QUIGNARD, Nathalie TANCHOUX.
Application Number | 20190300809 16/467439 |
Document ID | / |
Family ID | 57909744 |
Filed Date | 2019-10-03 |


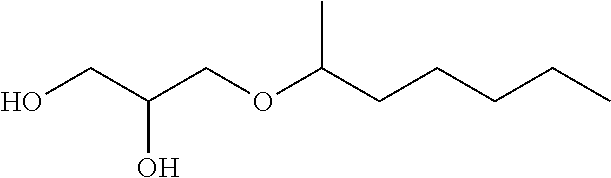

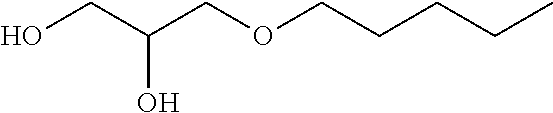
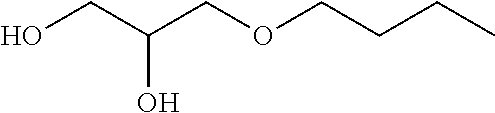


United States Patent
Application |
20190300809 |
Kind Code |
A1 |
CHAMPAGNE; Nicolas ; et
al. |
October 3, 2019 |
LUBRICATING COMPOSITION COMPRISING GLYCEROL MONOETHERS
Abstract
Disclosed is a lubricating composition including: at least one
base oil; and at least one glycerol monoether characterised in that
one of the alcohol functions of the glycerol forms an ether
function with a linear or branched, alkyl or alkylene R group
including 6 or 7 carbon atoms, the composition being an engine
lubricant.
Inventors: |
CHAMPAGNE; Nicolas;
(Caluire, FR) ; GRAVE; Gwendoline; (Toulouse,
FR) ; QUIGNARD; Francoise; (Montpellier, FR) ;
TANCHOUX; Nathalie; (Grabels, FR) |
|
Applicant: |
Name |
City |
State |
Country |
Type |
TOTAL MARKETING SERVICES
CENTRE NATIONAL DE LA RECHERCHE SCIENTIFIQUE |
Puteaux
Paris |
|
FR
FR |
|
|
Family ID: |
57909744 |
Appl. No.: |
16/467439 |
Filed: |
December 6, 2017 |
PCT Filed: |
December 6, 2017 |
PCT NO: |
PCT/EP2017/081746 |
371 Date: |
June 6, 2019 |
Current U.S.
Class: |
1/1 |
Current CPC
Class: |
C10N 2020/071 20200501;
C10N 2030/54 20200501; C10M 2207/046 20130101; C10N 2040/25
20130101; C10M 129/16 20130101; C10M 2203/003 20130101; C10M
2209/084 20130101; C10M 2215/064 20130101; C10N 2030/06 20130101;
C10M 169/04 20130101; C10M 2205/04 20130101; C10M 2203/1025
20130101; C10N 2020/069 20200501; C10M 2205/0285 20130101; C10M
2203/1025 20130101; C10N 2020/02 20130101; C10M 2205/04 20130101;
C10M 2205/06 20130101; C10N 2060/02 20130101; C10M 2203/1025
20130101; C10N 2020/02 20130101; C10M 2205/04 20130101; C10M
2205/06 20130101; C10N 2060/02 20130101 |
International
Class: |
C10M 129/16 20060101
C10M129/16; C10M 169/04 20060101 C10M169/04 |
Foreign Application Data
Date |
Code |
Application Number |
Dec 7, 2016 |
FR |
1662075 |
Claims
1-9. (canceled)
10. A lubricating composition comprising: at least one base oil;
and at least one glycerol mono-ether, characterized in that one of
the alcohol functions of glycerol forms an ether function with a
linear or branched alkyl or alkylene group R comprising 6 or 7
carbon atoms, the composition being an engine lubricant.
11. The lubricating composition of claim 10 comprising: at least
one base oil; and at least one glycerol mono-ether of formula (I)
or (II), taken alone or as a mixture ##STR00008## in which R
represents a linear or branched alkyl or alkylene group comprising
6 or 7 carbon atoms.
12. The lubricating composition according to claim 10 wherein R
represents a linear or branched alkyl or alkylene group comprising
6 carbon atoms.
13. The lubricating composition according to claim 10 comprising
from 0.01% to 5% by weight, of glycerol mono-ether.
14. A method of lubricating an engine comprising the implementation
of a lubricating composition according to claim 10.
15. The method according to claim 14 wherein the engine is a motor
engine.
16. The method for reducing the friction in an engine comprising
the implementation of a lubricating composition according to claim
10.
17. The method for reducing the fuel consumption of an engine
comprising the implementation of a lubricating composition
according to claim 10.
18. The method for reducing friction in an engine comprising the
implementation of a glycerol mono-ether as defined in claim 10 in a
lubricating composition of an engine.
19. The method for reducing the fuel consumption of an engine
comprising the implementation of a glycerol mono-ether as defined
in claim 10 in a lubricating composition of an engine.
20. The lubricating composition according to claim 11 comprising
from 0.01 to 2% by weight of glycerol mono-ether of formula (I) or
(II) taken alone or as a mixture.
21. The lubricating composition according to claim 10, comprising
from 0.1 to 1.5% by weight of glycerol mono-ether characterized in
that one of the alcohol functions of glycerol forms an ether
function with a linear or branched alkyl or alkylene group R,
wherein R represents a linear or branched alkyl or alkylene group
comprising 6 carbon atoms.
Description
[0001] The invention relates to the field of friction modifiers,
and, in particular, organic friction modifiers. More particularly,
the invention relates to a lubricating composition comprising a
friction modifier selected from glycerol monoethers. The invention
also relates to the use of this lubricating composition for
lubricating an engine.
[0002] One of the major objectives of the present automotive
industry is the reduction of the fuel consumption of engines,
especially motor vehicle engines, and thus the improvement of fuel
economy vehicles. Reducing friction in an engine is an effective
way to achieve fuel economy. Thus, much research has been done on
friction modifiers.
[0003] Four major groups stand out among friction modifiers:
nanoparticles, polymers, organomolybdenum compounds and organic
molecules.
[0004] Although nanoparticles and polymers are little used today,
this is not the case for organomolybdenum compounds, which
represent the most important family of friction modifiers. The
best-known and most widely used inorganic friction modifier is
molybdenum dithiocarbamate (MoDTC). These inorganic friction
modifiers, although very effective, have certain drawbacks. In
fact, they may induce some fouling and corrosion of engine parts.
In addition, they are only active at high temperatures and may
damage some type of amorphous carbon (DLC) surface.
[0005] In addition, from an ecological point of view, it is
necessary to reduce the content of sulfur or phosphorus elements of
the lubricating compositions used.
[0006] Thus, organic friction modifiers are studied and
conventionally used. It has been found that glycerol esters are
effective, and, in particular, glycerol mono-oleate is the most
commonly used commercially. It has the advantage of not containing
ash, phosphorus or sulfur and being produced from renewable raw
materials. However, its properties as a friction modifier are lower
than those of molybdenum dithiocarbamate.
[0007] The use of glycerol ethers as a friction modifier is also
known. Thus, the application JPS5925890 describes the use of
glycerol ethers comprising an alkyl chain comprising from 4 to 28
carbon atoms. JP2000273481 also discloses the use of glycerol
ethers comprising an alkyl chain comprising more than 14 carbons as
friction modifiers.
[0008] There is therefore an interest in proposing new friction
modifiers to improve efficiency.
[0009] Thus, an object of the present invention is to provide a
friction modifier and a lubricating composition comprising this
friction modifier that overcome all or some of the aforementioned
drawbacks.
[0010] Another object of the present invention is to provide an
organic friction modifier derived from renewable raw materials and
which does not have the drawbacks of MoDTC and which is effective
at low temperature.
[0011] Yet another object of the present invention is to provide a
lubricating composition for reducing friction and thus reducing the
fuel consumption of the engine, preferably of a motor vehicle.
[0012] The present invention thus relates to a lubricating
composition comprising: [0013] at least one base oil; and [0014] at
least one glycerol mono-ether, characterized in that one of the
alcohol functions of glycerol forms an ether function with a linear
or branched alkyl or alkylene group R comprising from 5 to 8 carbon
atoms, preferably from 6 to 7 carbon atoms, preferably 6 carbon
atoms.
[0015] Preferably, in the composition according to the invention,
the group R comprises 6 or 7 carbon atoms.
[0016] Preferably, the composition according to the invention is an
engine lubricant.
[0017] Advantageously, the R group of the glycerol monoether
according to the invention forms an ether bond with any oxygen atom
of glycerol, whether it is bonded to one of the two primary carbons
or to the secondary carbon of glycerol.
[0018] Advantageously according to the invention, the glycerol
mono-ether is chosen from glycerol monoethers of formula (I) or
(II), taken alone or as a mixture:
##STR00001##
[0019] in which R represents a linear or branched alkyl or alkylene
group comprising from 5 to 8 carbon atoms, preferably from 6 to 7
carbon atoms, preferably 6 carbon atoms.
[0020] Preferably, in the compounds of formula (I) or (II), R
represents a linear or branched alkyl or alkylene group comprising
6 or 7 carbon atoms.
[0021] Preferably, the glycerol mono-ether according to the
invention is chosen from the compounds of formula (I).
[0022] Preferably, the glycerol mono-ether according to the
invention is chosen from the compounds of formula (II).
[0023] Preferably, the glycerol mono-ether according to the
invention is a mixture of at least one compound of formula (I) and
at least one compound of formula (II).
[0024] Advantageously, the lubricating composition according to the
invention comprises from 0.01% to 5% by weight of glycerol
mono-ether according to the invention relative to the total weight
of the lubricating composition. Preferably, the lubricating
composition comprises from 0.01% to 2% by weight, preferably from
0.1% to 1.5% by weight of glycerol mono-ether as defined above,
relative to the total weight of the lubricating composition.
[0025] The glycerol monoethers according to the invention may be
obtained by any technique known to those skilled in the art. In
particular, a preferred synthetic route for the preparation of
glycerol monoethers of the invention consists in the reaction
between glycerol and an alcohol ROH, wherein R has the definition
given above.
[0026] The etherification reaction between glycerol and an alcohol
is preferably carried out in the presence of an acid catalyst,
preferably an acid heterogeneous catalyst or a homogeneous acid
catalyst.
[0027] Preferably, the acidic heterogeneous catalysts are chosen
from zeolites, resins or oxides of alumina.
[0028] Among the resins, may be mentioned perfluorinated polymer
resins such as Nafion.RTM. NR50, cation exchange resins such as
Dowex 50wx8, or among ion exchange resins with acidic properties
such as Amberlyst.RTM. 15 and 36.
[0029] Among the zeolites, particular mention may be made of
mordenites, ZMS-5 zeolites of the MFI type, BEA zeolites or
faujasites. Preferably, the acidic heterogeneous catalyst is a
zeolite, preferably a mordenite type zeolite, preferably a
mordenite with a Si/Al ratio of 11.
[0030] Preferably, the homogeneous acidic catalysts are chosen from
phosphoric acid, para-toluenesulfonic acid (APTS) and triflic acid.
Preferably, the acidic homogeneous catalyst is para-toluenesulfonic
acid (APTS).
[0031] Advantageously according to the invention and in order to
favor the synthesis of the glycerol mono-ether, the amount of
acidic homogeneous catalyst involved in the reaction is between 1%
and 10 mol% relative to the glycerol content, preferably it is
between 1% and 2.5 mol%. Advantageously, the amount of
heterogeneous catalyst involved in the reaction is between 1 and 5
mol% relative to the glycerol content, preferably it is 3.5
mol%.
[0032] The alcohol/glycerol molar ratio is optimized in order to
obtain the best possible yield of glycerol mono-ether while
limiting the secondary reactions of glycerol oligomer formation.
Preferably, the alcohol/glycerol molar ratio is between 1/6 and
3/1, preferably it is 1/1.
[0033] The etherification reaction may also, in another embodiment,
be carried out from the di-ether resulting from the reaction of the
alcohol on itself.
[0034] The etherification reaction of glycerol may be carried out
in any type of reactor known to those skilled in the art.
Advantageously, it is conducted in an autoclave.
[0035] The conditions of temperature, pressure and the
etherification reaction time of the glycerol can be determined in
the usual manner by those skilled in the art. Advantageously, the
reaction is carried out at a temperature of between 80 and
200.degree. C., preferably between 130 and 160.degree. C., for
example it may be carried out at 150.degree. C.
[0036] Advantageously according to the invention, the reaction is
carried out for at least 5 hours, preferably for 5 to 48 hours. The
reaction time may be 24 hours or 48 hours.
[0037] Advantageously according to the invention, the method
comprises a purification step. This purification step may comprise
the following steps: liquid-liquid extraction and/or fractional
distillation under reduced pressure. The liquid-liquid extraction
is conducted in the presence of a pair of solvents, which may be
determined in the usual manner by those skilled in the art.
[0038] Preferably, the acetonitrile/heptane pair may be used.
[0039] Advantageously, at least one liquid-liquid extraction is
conducted, preferably at least two. Even more preferably, three
liquid-liquid extractions are carried out.
[0040] In a preferred manner according to the invention, during the
distillation step, the initial alcohol and the glycerol mono-ether
are separated.
[0041] Advantageously, the process according to the invention makes
it possible to selectively obtain glycerol monoethers.
[0042] The lubricating composition according to the invention
comprises at least one base oil.
[0043] The base oil(s) used in the lubricating compositions
according to the invention may be chosen from a wide range. The
base oil of the lubricating composition used according to the
invention may, in particular, be chosen from mineral, synthetic or
natural oils, bio-sourced, animal, plant, known to those skilled in
the art.
[0044] The base oil(s) according to the invention may be oils of
mineral or synthetic origin, chosen from oils of groups I to V
according to the classes defined in the API classification (or
their equivalents according to the ATIEL classification) (Table A),
alone or in mixtures.
TABLE-US-00001 TABLE A Saturated Viscosity index content Sulfur
content (VI) Group I Mineral oils <90% >0.03% 80 .ltoreq. VI
< 120 Group II Hydrocracked .gtoreq.90% .ltoreq.0.03% 80
.ltoreq. VI < 120 oils Group III Hydrocracked .gtoreq.90%
.ltoreq.0.03% .gtoreq.120 or hydro-isomerized oils Group IV
Polyalphaolefines (PAO) Group V Esters and other bases not included
in groups I to IV
[0045] The mineral base oils useful according to the invention
include all types of bases obtained by atmospheric and vacuum
distillation of crude oil, followed by refining operations such as
solvent extraction, desalphating, solvent dewaxing, hydrotreatment,
hydrocracking, hydroisomerization and hydrofinishing.
[0046] Mixtures of synthetic and mineral oils may also be used.
[0047] There is generally no limitation on the use of different
lubricating bases for producing the lubricating compositions used
according to the invention, except that they must have properties,
in particular viscosity, viscosity index, sulfur, oxidation
resistance, adapted for use for engines or for vehicle
transmissions.
[0048] The lubricating composition according to the invention may
comprise from 50 to 99% of at least one base oil, preferably from
60 to 99%, advantageously from 70 to 99% by weight, relative to the
total weight of lubricating composition.
[0049] The lubricating composition according to the invention may
also comprise numerous additives.
[0050] The preferred additives for the lubricating composition used
according to the invention are chosen from detergents, antiwear
additives, extreme pressure additives, viscosity index improvers,
dispersants, antioxidants, pour point improvers, anti-foam agents,
and inorganic friction modifiers and mixtures thereof.
[0051] The lubricating composition according to the invention may
also comprise at least one detergent additive.
[0052] The detergent additives generally make it possible to reduce
the formation of deposits on the surface of the metal parts by
dissolving the secondary oxidation and combustion products.
[0053] The detergent additives that may be used in the lubricating
composition according to the invention are generally known to those
skilled in the art. The detergent additives may be anionic
compounds comprising a long lipophilic hydrocarbon chain and a
hydrophilic head. The associated cation may be a metal cation of an
alkali metal or alkaline earth metal.
[0054] The detergent additives are preferably chosen from the
alkali metal or alkaline earth metal salts of carboxylic acids, the
sulphonates, the salicylates, the naphthenates and the phenate
salts. The alkali and alkaline earth metals are preferably calcium,
magnesium, sodium or barium.
[0055] These metal salts generally comprise the metal in
stoichiometric amount or in excess, therefore in an amount greater
than the stoichiometric amount. These are then overbased detergent
additives; the excess metal bringing the overbased character to the
detergent additive is then generally in the form of an
oil-insoluble metal salt, for example a carbonate, a hydroxide, an
oxalate, an acetate, a glutamate, preferably a carbonate.
[0056] Advantageously, the lubricating composition according to the
invention may comprise from 2 to 4% by weight of detergent additive
relative to the total mass of the lubricating composition.
[0057] Anti-wear additives and extreme pressure additives protect
friction surfaces by forming a protective film adsorbed on these
surfaces.
[0058] There is a wide variety of anti-wear additives. In a
preferred manner for the lubricating composition according to the
invention, the anti-wear additives are chosen from phosphosulfur
additives such as metal alkylthiophosphates, in particular zinc
alkylthiophosphates, and more specifically zinc
dialkyldithiophosphates or ZnDTPs. The preferred compounds have the
formula Zn((SP(S)(OR.sup.11)(OR.sup.12.sub.2)), in which R.sup.11
and R.sup.12, which may be identical or different, independently
represent an alkyl group, preferably an alkyl group comprising from
1 to 18 carbon atoms.
[0059] Amine phosphates are also anti-wear additives which may be
used in the lubricating composition according to the invention.
However, the phosphorus provided by these additives may act as a
poison of the catalytic systems of automobiles because these
additives are ash generators. These effects may be minimized by
partially substituting amine phosphates with non-phosphorus
additives, such as, for example, polysulfides, especially
sulfur-containing olefins. Advantageously, the lubricating
composition according to the invention may comprise from 0.01 to 6%
by weight, preferably from 0.05 to 4% by weight, more preferably
from 0.1 to 2% by weight relative to the total weight of the
lubricating composition, anti-wear additives and extreme pressure
additives.
[0060] The lubricating composition of the present invention may
also comprise at least one viscosity index improving additive. As
examples of additives improving the viscosity index, mention may be
made of polymeric esters, homopolymers or copolymers, hydrogenated
or non-hydrogenated, of styrene, butadiene and isoprene, in
particular polyacrylates, polymethacrylates (PMA) or alternatively
olefin copolymers, especially ethylene/propylene copolymers.
[0061] Advantageously, the lubricating composition according to the
invention may also comprise at least one dispersing agent.
[0062] The dispersing agent may be chosen from Mannich bases,
succinimides and their derivatives.
[0063] Also advantageously, the lubricating composition according
to the invention may comprise from 0.2 to 10% by weight of
dispersing agent relative to the total mass of the lubricating
composition.
[0064] Advantageously, the lubricating composition according to the
invention may comprise at least one antioxidant additive.
[0065] The antioxidant additive generally serves to retard the
degradation of the lubricating composition in service. This
degradation may notably result in the formation of deposits, the
presence of sludge or an increase in the viscosity of the
lubricating composition.
[0066] Antioxidant additives act in particular as radical
inhibitors or destroyers of hydroperoxides. Among the antioxidant
additives commonly used, mention may be made of antioxidant
additives of the phenolic type, antioxidant additives of the amine
type, antioxidant phosphosulfur additives. Some of these
antioxidant additives, for example phosphosulfur antioxidant
additives, may be ash generators. Phenolic antioxidant additives
may be ash-free or may be in the form of neutral or basic metal
salts. The antioxidant additives may especially be chosen from
sterically hindered phenols, sterically hindered phenol esters, and
sterically hindered phenols comprising a thioether bridge,
diphenylamines, diphenylamines substituted with at least one
C.sub.1-C.sub.12 alkyl group, and N,N'-dialkyl-aryl diamines and
mixtures thereof.
[0067] Preferably, according to the invention, the sterically
hindered phenols are chosen from compounds comprising a phenol
group in which at least one vicinal carbon of the carbon bearing
the alcohol function is substituted by at least one
C.sub.1-C.sub.10 alkyl group, preferably a C.sub.1-C.sub.6alkyl
group, preferably a C.sub.4 alkyl group, preferably by the
ter-butyl group.
[0068] Amino compounds are another class of antioxidant additives
that may be used, optionally in combination with phenolic
antioxidant additives. Examples of amine compounds are aromatic
amines, for example aromatic amines of formula
NR.sup.13R.sup.14R.sup.15 in which R.sup.13 represents an
optionally substituted aliphatic or aromatic group, R.sup.14
represents an optionally substituted aromatic group, R.sup.15
represents a hydrogen atom, an alkyl group, an aryl group or a
group of formula R.sup.16S(O).sub.2R.sup.17 in which R.sup.16
represents an alkylene group or an alkenylene group, R.sup.17
represents an alkyl group, an alkenyl group or an aryl group and z
represents 0, 1 or 2.
[0069] Sulfurized alkyl phenols or their alkali and alkaline earth
metal salts may also be used as antioxidant additives.
[0070] Another class of antioxidant additives is copper compounds,
for example copper thio- or dithio-phosphates, copper and
carboxylic acid salts, dithiocarbamates, sulphonates, phenates,
copper acetylacetonates. Copper salts I and II, succinic acid or
anhydride salts may also be used.
[0071] The lubricating composition according to the invention may
contain all types of antioxidant additives known to those skilled
in the art.
[0072] Advantageously, the lubricating composition comprises at
least one ash-free antioxidant additive.
[0073] Also advantageously, the lubricating composition according
to the invention comprises from 0.5 to 2% by weight relative to the
total weight of the composition, of at least one antioxidant
additive.
[0074] Also advantageously, the lubricating composition according
to the invention may also comprise at least one pour point
depressant additive.
[0075] By slowing the formation of paraffin crystals, pour point
depressant additives generally improve the cold behavior of the
lubricating composition according to the invention.
[0076] As examples of pour point depressant additives, mention may
be made of alkyl polymethacrylates, polyacrylates, polyarylamides,
polyalkylphenols, polyalkylnaphthalenes and alkylated
polystyrenes.
[0077] The lubricating composition may also comprise an anti-foam
additive chosen from silicones and their derivatives, such as
polysiloxanes and their derivatives. Such an anti-foam additive may
be Bluesil 47V12500.RTM. marketed by Bluestar Silicones. The
antifoam additive of the lubricating composition according to the
invention may also be chosen from acrylics, such as PC1244.RTM.
marketed by Mosanto.
[0078] Advantageously, the lubricating composition according to the
invention may comprise at least one additional friction-modifying
additive, such as an inorganic friction modifier. The inorganic
friction modifier additive may be selected from a compound
providing metal elements and an ash free compound. Among the
compounds providing metal elements, mention may be made of
transition metal complexes such as Mo, Sb, Sn, Fe, Cu and Zn, the
ligands of which may be hydrocarbon compounds comprising oxygen,
nitrogen, sulfur or phosphorus.
[0079] In particular, mention may be made of organomolybdenum
compounds which represent the most important family of friction
modifiers. Molybdenum dithiocarbamate (MoDTC) is the best known
compound in this family.
[0080] Advantageously, the lubricating composition according to the
invention may comprise from 0.01 to 5% by weight or from 0.01 to 2%
by weight, preferably from 0.1 to 1.5% by weight or 0.1 at 2% by
weight relative to the total weight of the lubricating composition,
of the additional friction modifier additive.
[0081] The invention also relates to the use of a lubricating
composition according to the invention for lubricating an engine,
preferably a motor vehicle engine.
[0082] The invention also relates to the use of a lubricating
composition according to the invention for reducing the friction in
an engine, preferably a motor vehicle engine.
[0083] The invention also relates to the use of the lubricating
composition according to the invention for reducing the fuel
consumption of an engine, preferably of a motor vehicle engine.
[0084] Preferably, the reduction of friction in an engine or the
reduction of the fuel consumption of an engine is measured with
respect to the friction or fuel consumption measured with respect
to a reference composition.
[0085] Advantageously, the reference composition does not comprise
glycerol mono-ether, characterized in that one of the alcohol
functions of glycerol forms an ether function with an alkyl or
alkylene R group comprising 6 or 7 carbon atoms.
[0086] Advantageously, the invention also relates to the use of the
lubricating composition according to the invention for reducing the
fuel consumption at the start and during the operating phase of the
engine.
[0087] The invention also relates to the use of a glycerol
mono-ether as defined above in a lubricating composition for
reducing the friction in an engine or for reducing the fuel
consumption of an engine, preferably a motor vehicle engine.
[0088] Preferably, the use of a glycerol mono-ether of formula
according to the invention as defined above allows a reduction in
fuel consumption at startup and during the operating phase of the
engine.
[0089] The invention also relates to a method of lubricating an
engine, preferably a motor vehicle engine comprising the
implementation of a lubricating composition according to the
invention.
[0090] The invention also relates to a method for reducing the fuel
consumption of an engine, preferably a motor vehicle engine
comprising the implementation in the engine of a lubricating
composition according to the invention.
[0091] The various aspects of the invention are illustrated by the
following examples, but are not limited thereto.
EXAMPLES
[0092] Compounds Used:
[0093] The different glycerol monoethers tested are described in
Table I below. The synthetic route requires that the glycerol and
fatty alcohol used is soluble one in the other. However, any fatty
alcohol comprising 8 or more carbon atoms is not soluble in
glycerol, wherein the corresponding glycerol ethers can not be
synthesized according to the described synthetic route.
TABLE-US-00002 TABLE I Name Formula MEG C7P ##STR00002## MEG C7S
##STR00003## MEG C6P ##STR00004## MEG C5P ##STR00005## MEG C4P
##STR00006## MEG C3P ##STR00007##
[0094] The operating conditions used for the preparation of each of
the above glycerol monoethers are presented in the following Table
II:
TABLE-US-00003 TABLE II Efficiency in Name Reactor Catalyst
Temperature Period MEG (%) MEG B 2.5% mol 160.degree. C. 24 h 15
C7P APTS MEG ROR 2.5% mol 150.degree. C. 14 h 10 C7S APTS MEG R2L
1% mol 150.degree. C. 24 h 25 C6P APTS MEG ROR 2.5% mol 150.degree.
C. 7 h 33 C5P APTS MEG MP 1% mol 150.degree. C. 24 h 15 C4P APTS
MEG ROR 2.5% mol 140.degree. C. 5 h 8 C3P APTS
[0095] The reactors used are the following: [0096] B: Buchi glass
reactor immersed in an oil bath, [0097] ROR: Fast opening reactor
with a stirring propeller of 220 mL, [0098] MP: Multi-reactors
consisting of six autoclaves of 75 mL, [0099] R2L: 2L stainless
steel reactor with stirring blade.
[0100] The amount of catalyst is a molar amount relative to the
amount of glycerol used.
[0101] For the synthesis of each of the above glycerol monoethers:
[0102] the glycerol, the catalyst and the alcohol are mixed and
react together; [0103] then the mixture thus obtained is first
purified by decantation without solvent, then subjected to a
liquid-liquid extraction and finally subjected to fractional
distillation to recover the glycerol mono-ether.
[0104] The amount of glycerol monoethers obtained at the end of the
reaction is measured by gas chromatography.
[0105] TGA Measurements
[0106] Thermogravimetric analysis (TGA) gives the mass loss of a
sample as a function of temperature. The sample is heated according
to programmed temperature ramps. The mass losses are determined
using a scale that continuously measures the mass of the sample
during its rise in temperature. The results of these TGA
measurements on the various glycerol monoethers above are described
in Table III.
TABLE-US-00004 TABLE III % of weight loss Temperature (.degree. C.)
MEG C3P 100% 169.5.degree. C. MEG C4P 100% 186.6.degree. C. MEG C5P
100% 192.4.degree. C. MEG C6P 100% 216.1.degree. C. MEG C7P 100%
222.9.degree. C. MEG C7S 100% 195.1.degree. C.
[0107] Thus short glycerol monoethers (MEG C3P and MEG C4P) have a
loss of mass of 100% for lower temperatures, and especially less
than 190.degree. C. which makes them difficult to use in an engine
application or even incompatible with such an application.
[0108] Conversely, the glycerol monoethers according to the
invention (MEG CSP, MEG C6P, MEG C7P and MEG C7S) have a loss of
mass of 100% for higher temperatures, and, in particular, may be
greater than 200.degree. C. which makes them fully compatible with
use in a lubricating composition for a engine application.
[0109] Characterization Tests
[0110] In order to characterize the behavior of the compositions
according to the invention, two series of tests were performed.
[0111] The HFRR (High Frequency Reciprocating Rig) test is used to
evaluate the performance of fuels and lubricants in terms of
friction in the mixed/limit regime.
[0112] This test involves fixing a steel plane, on which the
lubricating composition to be tested is placed, in a heating block.
A steel ball subjected to a certain load is then brought into
contact with the lubricating composition and the steel plane before
being vibrated. The vibration frequency and the load applied to the
ball as well as the temperature at which the lubricating
composition is subjected are adjustable. This test makes it
possible to obtain a coefficient of friction curve as a function of
the duration of the test.
[0113] In practice, the test lasts 30 min, the ball travels back
and forth 2 mm at a frequency of 20 Hz, an average shear rate of 40
mm.s.sup.-1 (limit regime). At the stop point of the ball, the
speed is zero which places this test well in a limited and mixed
lubrication regime. A load of 200 g is applied on the ball, which
corresponds to a pressure of 800 MPa. The oil is heated to
100.degree. C.
[0114] The MTM test (Traction Machine or Mini Traction Machine)
makes it possible to evaluate the performance of lubricants in
terms of friction in the mixed/hydrodynamic regime. This test
consists in setting in relative motion a steel ball and a steel
plane, at different speeds, allowing definition of the % SSR (ratio
of the speed of slip/drive speed or Slide-to-Roll Ratio) which
corresponds at the slip speed/drive speed.
[0115] The tests consist of a 120 min accumulation period where the
ball rotates at 100 mm.s.sup.-1 (hydrodynamic regime) with a % SSR
of 50%, for a load of 1.1 GPa and an oil temperature 100.degree.
C.
[0116] A friction modifier is considered effective if it lowers the
coefficient of friction. The different glycerol monoethers are
tested in a reference lubricating composition whose composition is
given in Table IV below.
TABLE-US-00005 TABLE IV Description Content (%) Base oil 1 Group
III (kinematic 59.4 viscosity measured at 100.degree. C. according
to ASTM D556 = 4 mm.sup.2/s), Base oil 2 Group IV (kinematic 20
viscosity measured at 100.degree. C. according to ASTM D556 = 6
mm.sup.2/s) Viscosity modifier Poly(isoprene-styrene- 6.6
hydrogenated) Pour point depressant polymer poly
(alkylmethacrylate) 0.2 Antioxidant Diphenylamine 1.5 Additive
package P6003 .RTM. marketed by the 12.3 company Infineum
[0117] Each glycerol mono-ether is added at a content of 1% by
weight relative to the total weight of the reference lubricating
composition. The various lubricating compositions tested are
described in Table V below.
TABLE-US-00006 TABLE V Composition 1 Composition 2 Composition 3
Composition 4 Composition 5 Composition 6 Composition 7 Reference
99 99 99 99 99 99 99 composition MEG C3P 1 MEG C4P 1 MEG C5P 1 MEG
C6P 1 MEG C7P 1 MEG C7S 1 Glycerol 1 mono- oleate
Example 1
HFRR Tests
[0118] Table VI below represents the coefficients of friction of
the reference composition and compositions 3, 4, 5 and 6; the
values were taken after 900 seconds of testing.
TABLE-US-00007 TABLE VI Reference lubricating composition
Composition 3 Composition 4 Composition 5 Composition 6 Coefficient
0.131 0.112 0.119 0.119 0.119 of friction at 900 seconds
[0119] Thus, all of the lubricating compositions according to the
invention (compositions 3 to 6) significantly lower the coefficient
of friction on this HFRR test under severe conditions.
Example 2
MTM Tests
[0120] As previously described, the MTM tests will probe the
performance of the friction modifiers under less severe conditions
than the HFRR test but are nevertheless representative of operating
points of certain driving members. Table VII below indicates the
values of the coefficients of friction of compositions 1, 2, 4, 5,
6 and 7; the values were taken after 6120 seconds of testing.
TABLE-US-00008 TABLE VII Coefficient of friction Composition 1
0.063 Composition 2 0.045 Composition 4 0.041 Composition 5 0.039
Composition 6 0.040 Composition 7 0.045
[0121] Thus, the lubricating compositions 4 to 6 according to the
invention significantly lower the coefficient of friction on this
MTM test in comparison with the comparative compositions 1 and 2
(comprising respectively a C.sub.3 and C.sub.4 glycerol mono-ether)
or comparative composition 7 (comprising glycerol
mono-oleate)).
Example 3
Engine Tests
[0122] In order to confirm the good results expressed on
tribological tests, the composition 3 and the composition 6 were
evaluated comparatively by the implementation of the motor test
described below:
[0123] During the test, the fluid temperature (water/oil) is
regulated. The engine is then positioned at a selected operating
point (rpm/torque) and the fuel consumption is then measured at
this point. A consumption map is thus produced by this means. The
test engine is a Renault R9M engine.
[0124] Table VIII shows the gains in terms of % fuel consumption
compared to the reference composition at a temperature (water/oil)
set at 90.degree. C. The threshold of significance of the test is
equal to 0.15%.
TABLE-US-00009 TABLE VIII Regime Couple Composition 6 Composition 3
2500 160 0.14 0.31 2000 160 0.24 0.44 1500 160 0.19 0.35 2500 90
0.37 0.61 2000 90 0.06 0.50 1500 90 0.28 0.60 2500 40 0.42 0.88
2000 40 0.58 0.82 1500 40 0.71 0.79 849 2 1.96 0.95 Average heat
0.49 0.62 gain
[0125] Thus the lubricating compositions according to the invention
significantly improve the fuel consumption, especially when
hot.
* * * * *