U.S. patent application number 16/424136 was filed with the patent office on 2019-09-26 for method and system for implementing high-speed electrical interfaces between semiconductor dies in optical communication systems.
The applicant listed for this patent is Luxtera, Inc.. Invention is credited to Sherif Abdalla, John Andrew Guckenberger, Daniel Kucharski, Thierry Pinguet.
Application Number | 20190293883 16/424136 |
Document ID | / |
Family ID | 44476542 |
Filed Date | 2019-09-26 |
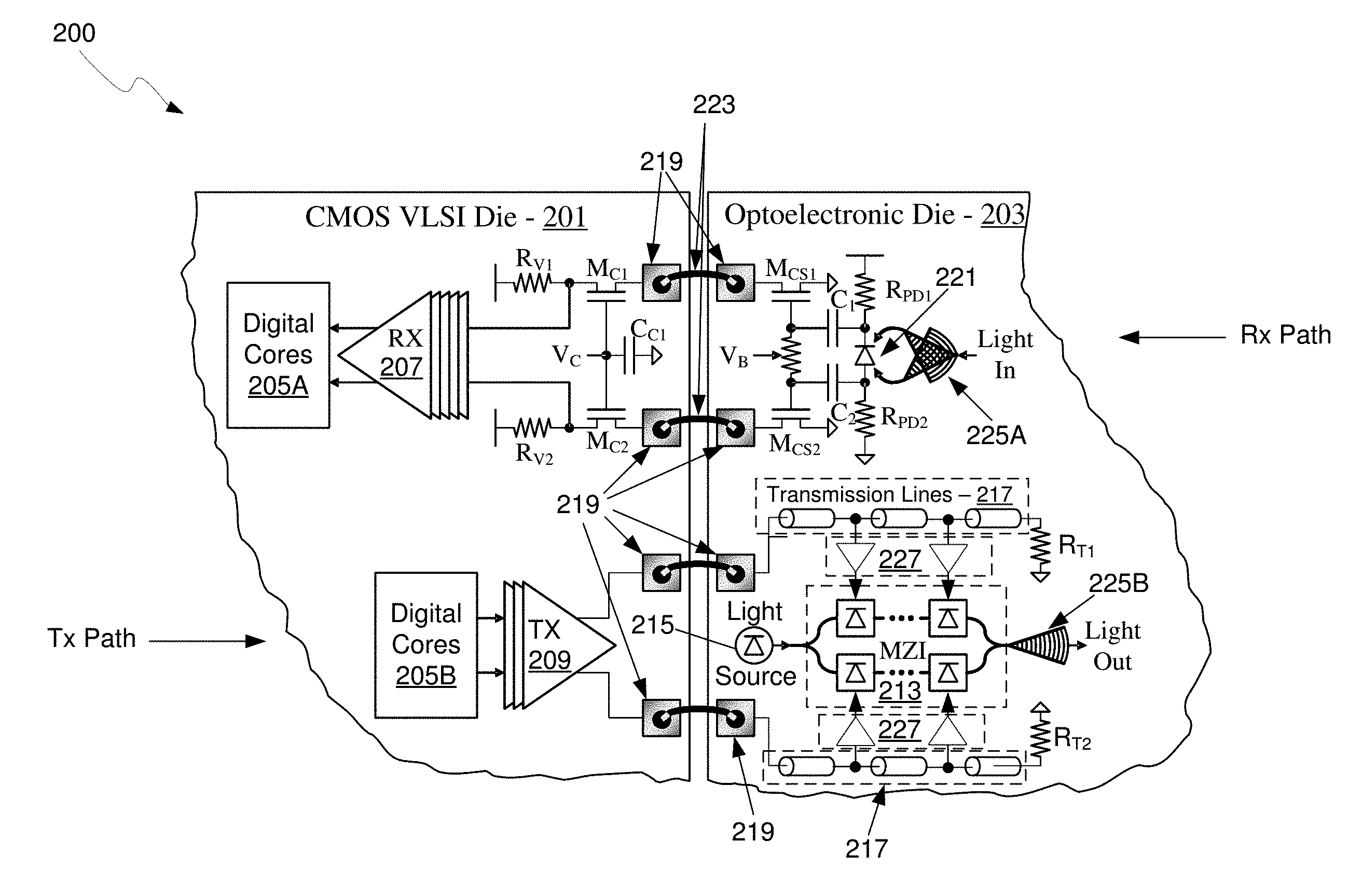

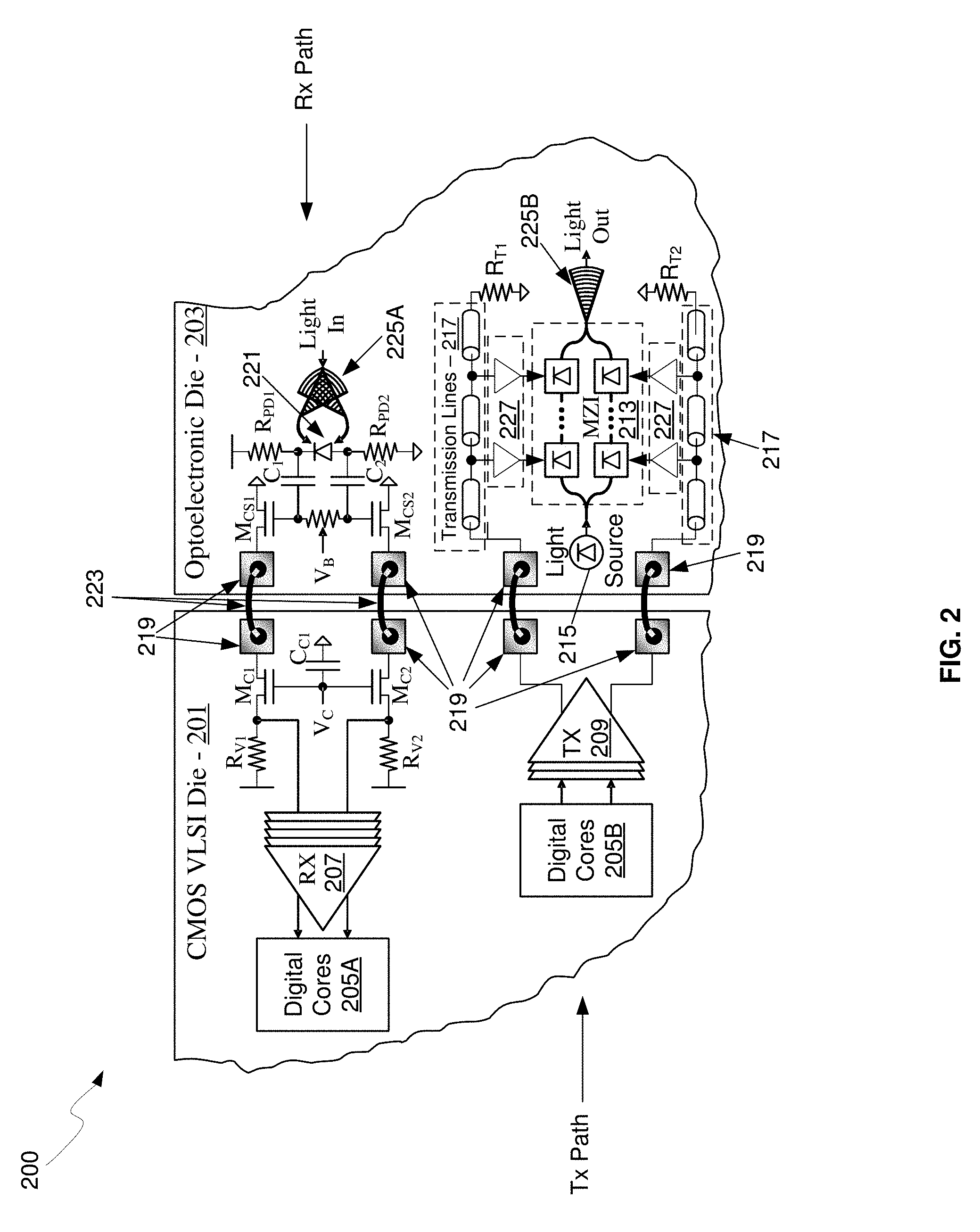
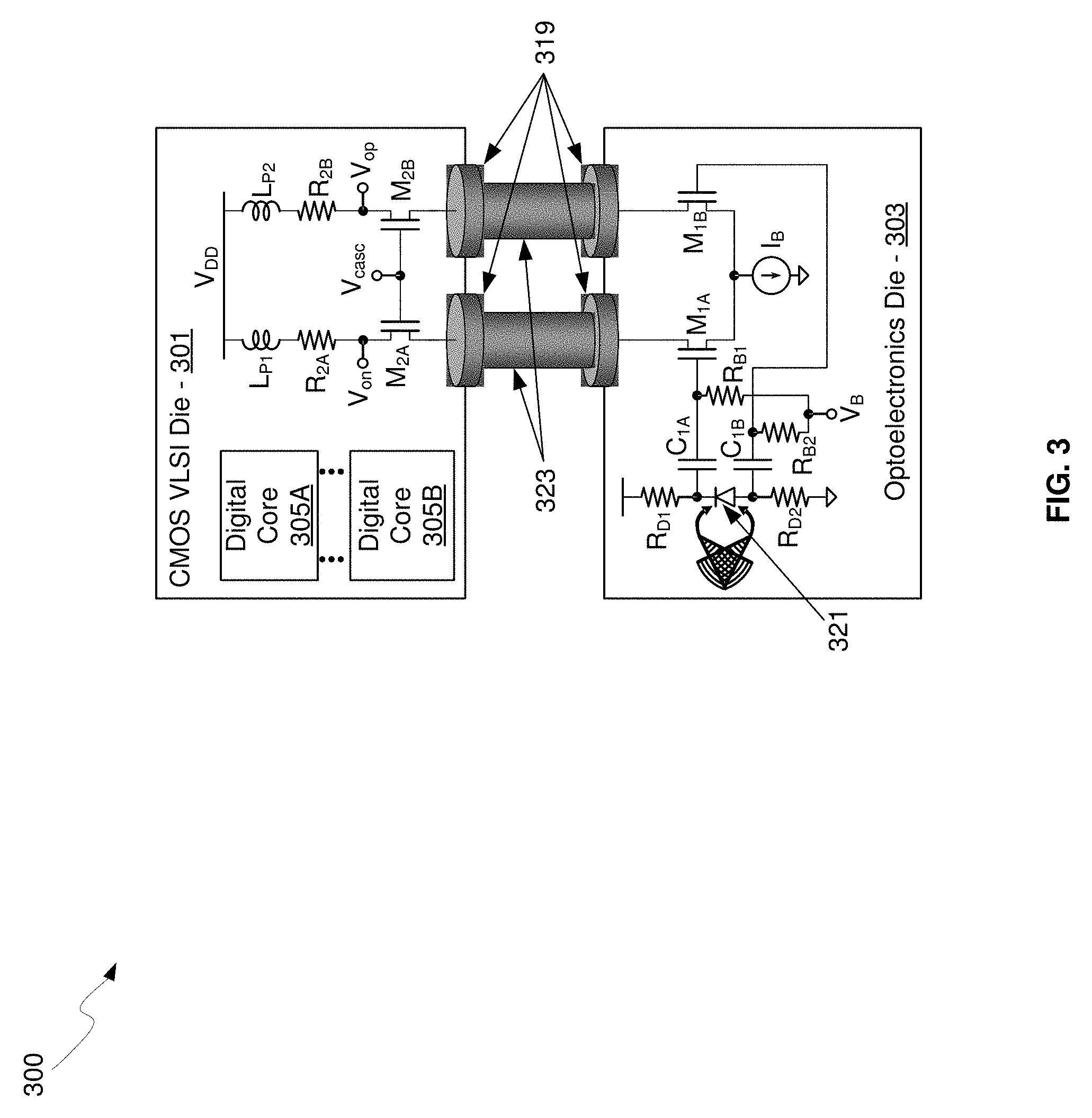
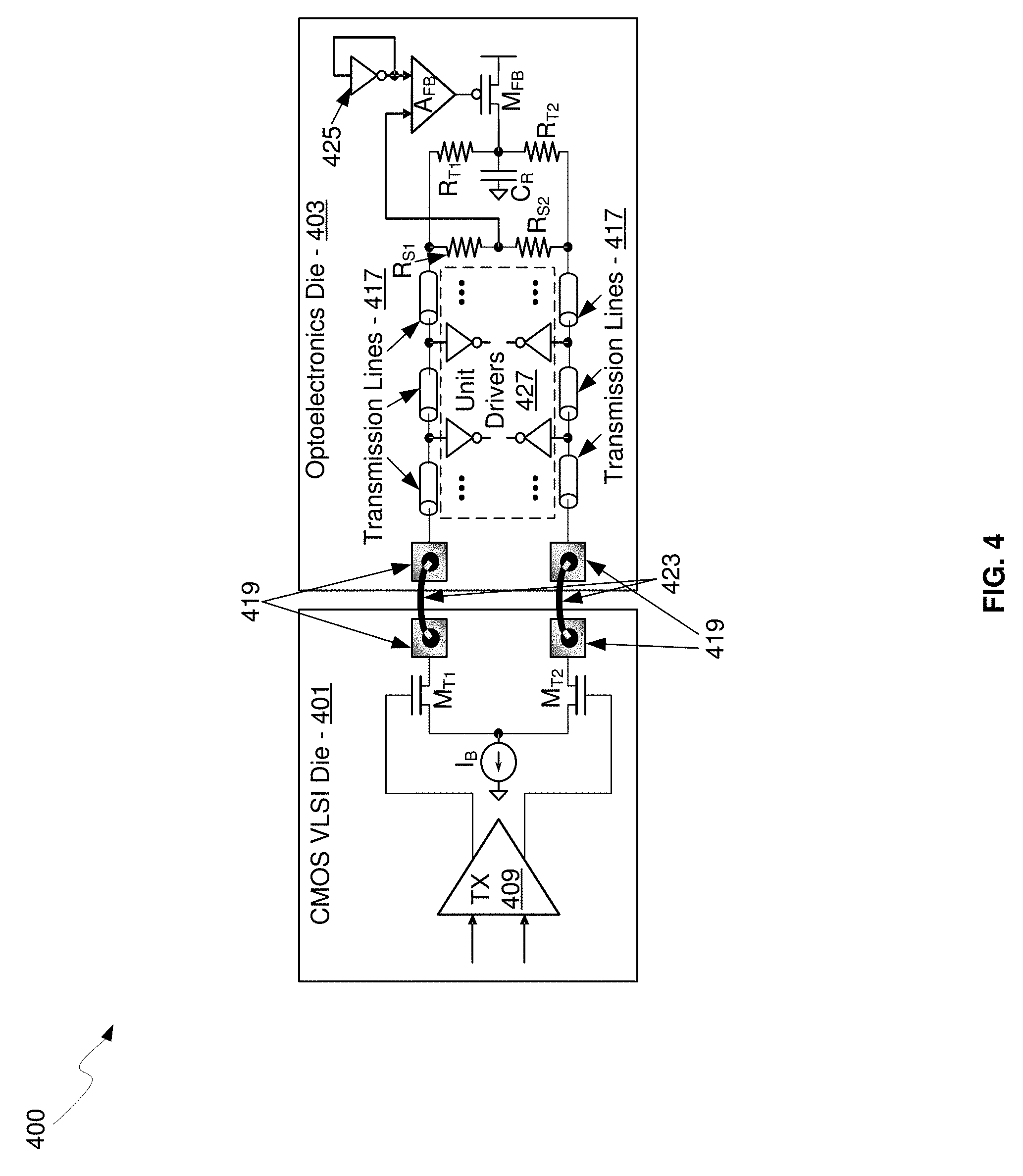
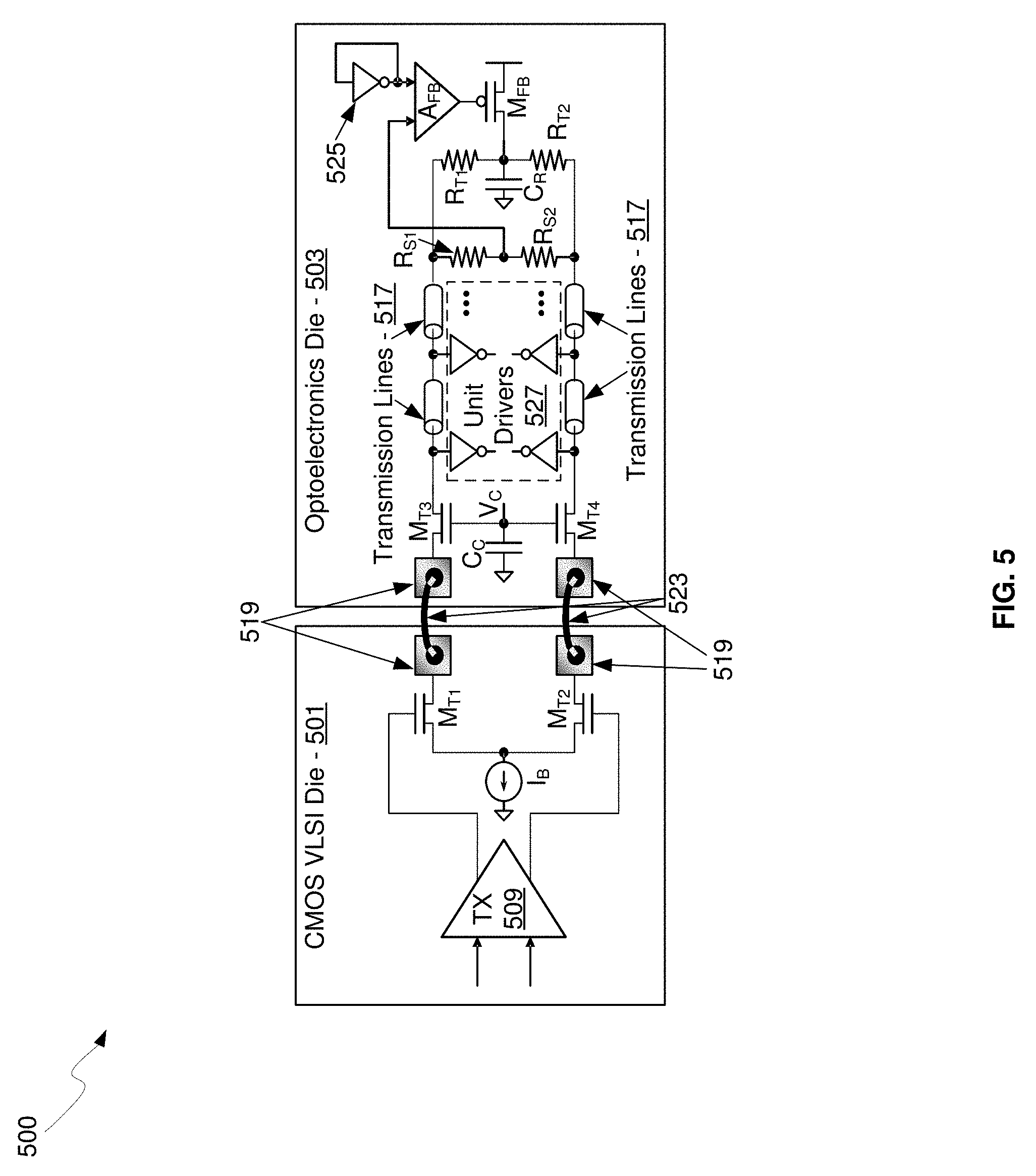
United States Patent
Application |
20190293883 |
Kind Code |
A1 |
Kucharski; Daniel ; et
al. |
September 26, 2019 |
Method And System For Implementing High-Speed Electrical Interfaces
Between Semiconductor Dies In Optical Communication Systems
Abstract
A method and system for implementing high-speed electrical
interfaces between semiconductor dies in optical communication
systems are disclosed and may include communicating electrical
signals between a first die and a second die via coupling pads
which may be located in low impedance points in Tx and Rx paths.
The electrical signals may be communicated via one or more
current-mode, controlled impedance, and/or capacitively-coupled
interfaces. The current-mode interface may include a cascode
amplifier stage split between source and drain terminals of
transistors on the dies. The controlled-impedance interfaces may
include transmission line drivers on a first die and transmission
lines on a second die. The capacitively-coupled interfaces may
include capacitors formed by contact pads on the dies. The coupling
pads may be connected via one or more of: wire bonds, metal
pillars, solder balls, or conductive resin. The dies may comprise
CMOS and may be coupled in a flip-chip configuration.
Inventors: |
Kucharski; Daniel; (San
Marcos, CA) ; Guckenberger; John Andrew; (San Diego,
CA) ; Pinguet; Thierry; (Arlington, WA) ;
Abdalla; Sherif; (Carlsbad, CA) |
|
Applicant: |
Name |
City |
State |
Country |
Type |
Luxtera, Inc. |
Carlsbad |
CA |
US |
|
|
Family ID: |
44476542 |
Appl. No.: |
16/424136 |
Filed: |
May 28, 2019 |
Related U.S. Patent Documents
|
|
|
|
|
|
Application
Number |
Filing Date |
Patent Number |
|
|
16110587 |
Aug 23, 2018 |
10302880 |
|
|
16424136 |
|
|
|
|
15716103 |
Sep 26, 2017 |
10061094 |
|
|
16110587 |
|
|
|
|
13033439 |
Feb 23, 2011 |
9772460 |
|
|
15716103 |
|
|
|
|
61338690 |
Feb 23, 2010 |
|
|
|
Current U.S.
Class: |
1/1 |
Current CPC
Class: |
G02B 6/4274 20130101;
G02B 6/4286 20130101 |
International
Class: |
G02B 6/42 20060101
G02B006/42 |
Claims
1. (canceled)
2. A method for processing signals, the method comprising: in a
communication system, communicating electrical signals between a
first die and a second die via coupling pads on said first die and
said second die, wherein said coupling pads are located at low
impedance points between two transistors in said communication
system, wherein a first of said two transistors is integrated in
said first die and a second of said two transistors is integrated
in said second die.
3. The method according to claim 2, comprising communicating said
electrical signals via one or more current-mode interfaces.
4. The method according to claim 3, wherein said one or more
current-mode interfaces comprise a cascode amplifier stage split
between a source terminal of said first of said two transistors
integrated in said first die and a drain terminal of said second of
said two transistors integrated in said second die.
5. The method according to claim 3, wherein said one or more
current-mode interfaces comprise a cascode amplifier stage split
between a source terminal of said first of said two transistors
integrated in said second die and a drain terminal of said second
of said two transistors integrated in-said first die.
6. The method according to claim 2, comprising communicating said
electrical signals via one or more controlled-impedance
interfaces.
7. The method according to claim 6, wherein said one or more
controlled-impedance interfaces comprise one or more transmission
line drivers on said first die and one or more transmission lines
on said second die of said communication system.
8. The method according to claim 2, comprising communicating said
electrical signals via one or more capacitively-coupled
interfaces.
9. The method according to claim 8, wherein said
capacitively-coupled interfaces comprise capacitors formed by one
or more of said coupling pads on said first die and one or more of
said coupling pads on said second die.
10. The method according to claim 2, comprising communicating said
electrical signals via one or more inductively-coupled
interfaces.
11. The method according to claim 2, wherein said coupling pads are
connected via one or more of: wire bonds, metal pillars, solder
balls, or conductive resin.
12. The method according to claim 2, wherein said first die and
said second die are coupled in a flip-chip configuration.
13. The method according to claim 2, wherein said first die
comprises a complimentary metal-oxide-semiconductor (CMOS) die.
14. The method according to claim 2, wherein said second die
comprises an optoelectronics die.
15. A system for processing signals, the system comprising: a
communication system comprising a first die and a second die, said
first die and said second die comprising circuitry that is operable
to communicate electrical signals between said first die and said
second die via coupling pads on said first die and said second die,
wherein said coupling pads are located at low impedance points
between two transistors in said communication system, wherein a
first of said two transistors is integrated in said first die and a
second of said two transistors is integrated in said second
die.
16. The system according to claim 15, wherein said circuitry is
operable to communicate said electrical signals via one or more
current-mode interfaces.
17. The system according to claim 16, wherein said one or more
current-mode interfaces comprise a cascode amplifier stage split
between a source terminal of said first of said two transistors
integrated in said first die and a drain terminal of said second of
said two transistors integrated in said second die.
18. The system according to claim 16, wherein said one or more
current-mode interfaces comprise a cascode amplifier stage split
between a source terminal of said first of said two transistors
integrated in said second die and a drain terminal of said second
of said two transistors integrated in said first die.
19. The system according to claim 15, wherein said circuitry is
operable to communicate said electrical signals via one or more
controlled-impedance interfaces.
20. The system according to claim 19, wherein said one or more
controlled-impedance interfaces comprise one or more transmission
line drivers on said first die and one or more transmission lines
on said second die of said communication system.
21. The system according to claim, 15, wherein said circuitry is
operable to communicate said electrical signals via one or more
capacitively-coupled interfaces.
22. The system according to claim 21, wherein said
capacitively-coupled interfaces comprise capacitors formed by one
or more of said coupling pads on said first die and one or more of
said coupling pads on said second die.
23. The system according to claim 15, wherein said circuitry is
operable to communicate said electrical signals via one or more
inductively-coupled interfaces.
24. The system according to claim 15, wherein said coupling pads
are connected via one or more of: wire bonds, metal pillars, solder
balls, or conductive resin.
25. The system according to claim 15, wherein said first die and
said second die are coupled in a flip-chip configuration.
26. The system according to claim 15, wherein said first die
comprises an electronics complimentary metal-oxide-semiconductor
(CMOS) die.
27. The system according to claim 15, wherein said second die
comprises an optoelectronics CMOS die.
Description
CROSS-REFERENCE TO RELATED APPLICATIONS/INCORPORATION BY
REFERENCE
[0001] This application is a continuation of U.S. application Ser.
No. 16/110,587 filed on Aug. 23, 2018, which is a continuation of
U.S. application Ser. No. 15/716,103 filed on Sep. 26, 2017, now
U.S. Pat. No. 10,061,094, which is a continuation of U.S. patent
application Ser. No. 13/033,439 filed on Feb. 23, 2011, now U.S.
Pat. No. 9,772,460, which makes reference to and claims priority to
U.S. Provisional Application Ser. No. 61/338,690 filed on Feb. 23,
2010, each of which is hereby incorporated herein by reference in
its entirety.
FEDERALLY SPONSORED RESEARCH OR DEVELOPMENT
[0002] [Not Applicable]
MICROFICHE/COPYRIGHT REFERENCE
[0003] [Not Applicable]
FIELD OF THE INVENTION
[0004] Certain embodiments of the invention relate to signal
processing. More specifically, certain embodiments of the invention
relate to a method and system for implementing high-speed
electrical interfaces between semiconductor dies in optical
communication systems.
BACKGROUND OF THE INVENTION
[0005] As data networks scale to meet ever-increasing bandwidth
requirements, the shortcomings of copper data channels are becoming
apparent. Signal attenuation and crosstalk due to radiated
electromagnetic energy are the main impediments encountered by
designers of such systems. They can be mitigated to some extent
with equalization, coding, and shielding, but these techniques
require considerable power, complexity, and cable bulk penalties
while offering only modest improvements in reach and very limited
scalability. Free of such channel limitations, optical
communication has been recognized as the successor to copper
links.
[0006] Optical communication systems have been widely adopted for
applications ranging from internet backbone, local area networks,
data centers, supercomputing, to high-definition video. Due to
superior bandwidth and low loss, optical fibers are the medium of
choice for transporting high-speed binary data.
[0007] Further limitations and disadvantages of conventional and
traditional approaches will become apparent to one of skill in the
art, through comparison of such systems with the present invention
as set forth in the remainder of the present application with
reference to the drawings.
BRIEF SUMMARY OF THE INVENTION
[0008] A system and/or method for implementing high-speed
electrical interfaces between semiconductor dies in optical
communication systems, substantially as shown in and/or described
in connection with at least one of the figures, as set forth more
completely in the claims.
[0009] Various advantages, aspects and novel features of the
present invention, as well as details of an illustrated embodiment
thereof, will be more fully understood from the following
description and drawings.
BRIEF DESCRIPTION OF SEVERAL VIEWS OF THE DRAWINGS
[0010] FIG. 1 is a block diagram of a photonically enabled CMOS
optical communication system, in accordance with an embodiment of
the invention.
[0011] FIG. 2 is a block diagram of split receiver and transmitter
electrical interfaces, in accordance with an embodiment of the
invention.
[0012] FIG. 3 is a block diagram of a flip-chip-type
photonically-enabled CMOS optical receiver system, in accordance
with an embodiment of the invention.
[0013] FIG. 4. is a block diagram illustrating a
controlled-impedance split-transmitter interface, in accordance
with an embodiment of the invention.
[0014] FIG. 5. is a block diagram illustrating a low-impedance
split-transmitter cascode interface, in accordance with an
embodiment of the invention.
DETAILED DESCRIPTION OF THE INVENTION
[0015] Certain aspects of the invention may be found in a method
and system for implementing high-speed electrical interfaces
between semiconductor dies in optical communication systems.
Exemplary aspects of the invention may comprise communicating
electrical signals between an electronics die and an
optoelectronics die via coupling pads on the electronics die and
the optoelectronics die in an optical communication system. The
coupling pads may be located at low impedance points in one or more
transmit paths and/or one or more receive paths in the optical
communication system. The electrical signals may be communicated
via one or more current-mode interfaces that may comprise a cascode
amplifier stage split between source terminals of transistors on
the electronics die and drain terminals of transistors on the
optoelectronics die. The electrical signals may be communicated via
one or more controlled-impedance interfaces that may comprise one
or more transmission line drivers on a first die and one or more
transmission lines on a second die of the optical communication
system. The electrical signals may be communicated via one or more
capacitively-coupled interfaces that may comprise capacitors formed
by one or more of the contact pads on the electronics die and one
or more of the contact pads on the optoelectronics die. The
electrical signals may be communicated via one or more
inductively-coupled interfaces. The coupling pads may be connected
via one or more of: wire bonds, metal pillars, solder balls, or
conductive resin. The electronics die and the optoelectronics die
may comprise CMOS dies. The electronics die and the optoelectronics
die may be coupled in a flip-chip configuration.
[0016] FIG. 1 is a block diagram of a photonically-enabled CMOS
optical communication system, in accordance with an embodiment of
the invention. Referring to FIG. 1, there is shown optoelectronic
devices comprising optical modulators 105A-105D, photodiodes
111A-111D, monitor photodiodes 113A-113H, and optical devices
comprising taps 103A-103K, optical terminations 115A-115D, and
grating couplers 117A-117H. There are also shown electrical devices
and circuits comprising amplifiers 107A-107D, analog and digital
control circuits 109, and control sections 112A-112D. The
amplifiers 107A-107D may comprise transimpedance and limiting
amplifiers (TIA/LAs), for example. Optical signals are communicated
between optical and optoelectronic devices via optical waveguides
fabricated in the chip or chips comprising the devices.
[0017] The optical modulators 105A-105D comprise Mach-Zehnder or
ring modulators, for example, and enable the modulation of the CW
laser input signal. The optical modulators 105A-105D comprise
high-speed and low-speed phase modulation sections and are
controlled by the control sections 112A-112D. The high-speed phase
modulation section of the optical modulators 105A-105D may modulate
a CW light source signal with a data signal. The low-speed phase
modulation section of the optical modulators 105A-105D may
compensate for slowly varying phase factors such as those induced
by mismatch between the waveguides, waveguide temperature, or
waveguide stress and is referred to as the passive phase, or the
passive biasing of the MZI.
[0018] The phase modulators may have a dual role: to compensate for
the passive biasing of the MZI and to apply the additional phase
modulation used to modulate the light intensity at the output port
of the MZI according to a data stream. The former phase tuning and
the latter phase modulation may be applied by separate, specialized
devices, since the former is a low speed, slowly varying
contribution, while the latter is typically a high speed signal.
These devices are then respectively referred to as the LSPM and the
HSPM. Examples for LSPM are thermal phase modulators (TPM), where a
waveguide portion is locally heated up to modify the index of
refraction of its constituting materials, or forward biased PIN
junctions (PINPM) where current injection into the PIN junction
modifies the carrier density, and thus the index of refraction of
the semiconductor material. An example of an HSPM is a reversed
biased PIN junction, where the index of refraction is also
modulated via the carrier density, but which allows much faster
operation, albeit at a lower phase modulation efficiency per
waveguide length.
[0019] The outputs of the modulators may be optically coupled via
waveguides to the grating couplers 117E-117H. The taps 103D-103K
comprise four-port optical couplers, for example, and are utilized
to sample the optical signals generated by the optical modulators
105A-105D, with the sampled signals being measured by the monitor
photodiodes 113A-113H. The unused branches of the taps 103D-103K
are terminated by optical terminations 115A-115D to avoid back
reflections of unwanted signals.
[0020] The grating couplers 117A-117H comprise optical gratings
that enable coupling of light into and out of the chip or chips
comprising the optical gratings 117A-117H. The grating couplers
117A-117D may be utilized to couple light received from optical
fibers into a photonically-enabled CMOS chip, and the grating
couplers 117E-117H may be utilized to couple light from the
photonically-enabled CMOS chip into optical fibers. The grating
couplers 117A-117H may comprise single polarization grating
couplers (SPGC) and/or polarization splitting grating couplers
(PSGC). In instances where a PSGC is utilized, two input, or
output, waveguides may be utilized.
[0021] The optical fibers may be epoxied, for example, to the
photonically-enabled CMOS chip, and may be aligned at an angle from
normal to the surface of the chip to optimize coupling efficiency.
In an embodiment of the invention, the optical fibers may comprise
single-mode fiber (SMF) and/or polarization-maintaining fiber
(PMF).
[0022] In another exemplary embodiment, optical signals may be
communicated directly into the surface of the photonically-enabled
CMOS chip without optical fibers by directing a light source on an
optical coupling device in the chip, such as the light source
interface 135 and/or the optical fiber interface 139. This may be
accomplished with directed laser sources and/or optical sources on
another chip flip-chip bonded to the photonically-enabled CMOS
chip.
[0023] The photodiodes 111A-111D may convert optical signals
received from the grating couplers 117A-117D into electrical
signals that are communicated to the amplifiers 107A-107D for
processing. The photodiodes 111A-111D may comprise high-speed
heterojunction photodiodes, for example, and may comprise germanium
(Ge) in the collector and base regions for absorption in the 1.55
.mu.m optical wavelength range, and may be integrated on a CMOS
silicon-on-insulator (SOI) wafer. In another embodiment of the
invention, the photodiodes 111A-111D may instead comprise
phototransistors.
[0024] The analog and digital control circuits 109 may control gain
levels or other parameters in the operation of the amplifiers
107A-107D, which may then communicate electrical signals to other
circuitry, such as in a deep sub-micron CMOS chip with for further
digital signal processing, for example. In an embodiment of the
invention, the plurality of optical, optoelectronic, and electronic
devices in the photonically-enabled CMOS optical communication
system 100 may be integrated in different chips depending on the
speed and other device requirements. For example, complex,
high-speed digital processing may be performed on electronic
devices in a deep sub-micron CMOS chip that is communicatively
coupled to a photonically-enabled CMOS chip comprising optical,
electrical, and optoelectronic devices.
[0025] The control sections 112A-112D comprise electronic circuitry
that enable modulation of the CW laser signal received from the
splitters 103A-103C. The optical modulators 105A-105D require
high-speed electrical signals to modulate the refractive index in
respective branches of a Mach-Zehnder interferometer (MZI), for
example. In an embodiment of the invention, the control sections
112A-112D may include sink and/or source driver electronics that
may enable a bidirectional link utilizing a single laser.
[0026] The chips comprising the photonically-enabled CMOS optical
communication system 100 may comprise semiconductor-on-insulator
(SOI), bulk silicon, silicon-on-sapphire, indium phosphide,
indium-gallium-nitride, indium-gallium-arsenide, gallium arsenide,
or an organic polymer, for example.
[0027] As complexity and data throughput of optical communication
systems increase, it is often inefficient, difficult, or even
impossible to monolithically integrate all system subcomponents on
a single semiconductor die. This may be caused by diversity of
semiconductor technologies and materials used in constructing such
systems. Some of these technologies are either highly specialized
or are optimized for a fairly narrow range of applications. For
example, III-V semiconductors excel in light generation and
detection, SiGe HBT technologies work very well in high-speed
analog and mixed signal applications, and deep submicron CMOS
provides speed and density necessary for implementing complex
digital functions and signal processing on VLSI scale, with a wide
variety of existing digital cores readily available for
integration. Overlaps between these technologies exist in some
areas, but in many cases it may be more efficient to choose the
right technology for each function. This approach may enable
systems to be assembled from multiple semiconductor dies.
Electrical interfaces between these dies may create performance
bottlenecks or lead to inefficiencies, such as reduced transmission
speed, increased timing jitter, or additional power
consumption.
[0028] In an embodiment of the invention, high-speed electronic
devices and circuits may be integrated on a CMOS VLSI chip and
optical, optoelectronic, and electronic devices may be integrated
on a second photonically-enabled CMOS chip. The chips may be
configured adjacent to each other or may be configured face-to-face
in a flip-chip configuration. Coupling techniques may comprise wire
bonds, solder balls, metal pillars, conductive resin, and/or
proximity interconnects such as capacitively-coupled interfaces or
inductively-coupled interfaces. Capacitively-coupled interfaces may
comprise metal pads on adjacent chips comprising capacitors for
AC-coupling of signals, whereas inductively-coupled interfaces may
comprise inductor coils on adjacent chips with signals being
communicated between chips via inductive coupling between the
coils.
[0029] In operation, the photonically-enabled CMOS optical
communication system 100 may be operable to transmit and/or receive
and process optical signals. The grating couplers 117A-117D may be
operable to receive optical signals from optical fibers coupled to
a photonically-enabled CMOS chip, and may convert the optical mode
of the fiber into the much smaller mode of a Si waveguide
fabricated on the photonically-enabled CMOS SOI wafer. The grating
couplers 117A-117D may comprise a single-polarization or a
polarization-splitting type: in the first case, only a specific
polarization is coupled to a single Si waveguide, while in the
second case, two orthogonal polarizations are split into two output
waveguides.
[0030] In an exemplary embodiment of the invention, optical,
electrical, and optoelectronic devices may be integrated on chips
that may be optimized for a particular device. For example, optical
and optoelectronic, and some electronic devices may be integrated
on a photonically-enabled CMOS chip whereas high-speed electronic
devices may be integrated on an adjacent deep sub-micron CMOS chip.
The coupling of the two chips may then be configured to minimize
effects from parasitic impedances. For example, in a current-mode
interface, the interconnect may be configured between transistors
in a cascode configuration with one pair of transistors on one chip
an open-drain configuration and another pair of transistors on a
second chip in the cascode configuration.
[0031] In addition, in a controlled-impedance interface,
configurable impedance transmission lines may be utilized on a
photonically-enabled CMOS chip to match impedance with low input
impedance of Tx amplifiers in a deep sub-micron CMOS chip, which
also mitigates the effects of parasitic impedances resulting from
the interconnect between chips.
[0032] FIG. 2 is a block diagram of split receiver and transmitter
electrical interfaces, in accordance with an embodiment of the
invention. Referring to FIG. 2, there is shown a
photonically-enabled CMOS optical communication system 200
comprising a CMOS very-large-scale-integration (VLSI) die 201 and a
CMOS optoelectronics die 203. The Tx path in the lower half of the
dies comprises a controlled-impedance interface, whereas the Rx
path in the upper half of the dies comprises a current-mode
interface.
[0033] The CMOS optoelectronics die 203 comprises passive optical
structures, such as grating couplers 225A and 225B, waveguides,
splitters, and combiners. The CMOS optoelectronics die 203 also
comprises active optoelectronic elements such as the photodetector
221 for the purpose of detecting optical signals in receivers and
optical phase modulators. The phase modulators may be configured to
function as Mach-Zehnder interferometers, such as the MZI 213, for
the purpose of modulating optical signals in transmitters. The
optoelectronics die also comprises a common-source pair comprising
transistors M.sub.CS1 and M.sub.CS2, resistors R.sub.PD1,
R.sub.PD2, R.sub.T1, R.sub.T2 and RB, capacitors C.sub.1 and
C.sub.2, and other integrated circuit elements. The invention is
not limited to the number of optical, optoelectronic, and
electronic devices shown, as it comprises representative sections
of the chips. The CMOS optoelectronics die 203 also comprises
transmission lines 217, a light source 215, unit drivers 227,
coupling pads 219, and a bias voltage VB.
[0034] The CMOS VLSI die 201 comprises digital cores 205A and 205B,
receiver (Rx) gain stages 207, transmitter (Tx) gain stages 209,
CMOS transistors M.sub.C1 and M.sub.C2, capacitor C.sub.C1, bias
resistors R.sub.V1 and R.sub.V2, coupling pads 219, and a bias
voltage V.sub.C. The Rx gain stages 207 and the Tx gain stages 209
may comprise suitable gain control elements for communicating
signals to and from the digital cores 205A and 205B. The Tx gain
stages 209 may comprise transmission line drivers for communicating
electrical signals from the CMOS VLSI die 201 and the transmission
lines 217 on the optoelectronics die 203.
[0035] The digital cores 205A and 205B may comprise high-speed
digital processing cores, for example, that may be operable to
generate signals to be transmitted and/or process received signals.
The transistors M.sub.C1 and M.sub.C2 may comprise a cascode
configuration, such that the impedance seen at the coupling pads
219 may be low. In this manner, the interface between the CMOS VLSI
die 201 and the CMOS optoelectronics die 203 may be less sensitive
to parasitic impedances.
[0036] The coupling between the CMOS VLSI die 201 and the
optoelectronics die 203 is not limited to wire bonds, as
illustrated by the wire bonds 223 in FIG. 2. Accordingly, other
techniques may be utilized, such as solder balls, metal pillars,
conductive resin, and/or proximity interconnects, which may
comprise capacitively-coupled interfaces or inductively-coupled
interfaces, for example. Capacitively-coupled interfaces may
comprise the coupling pads 219 on adjacent chips comprising
capacitors for AC-coupling of signals, whereas inductively-coupled
interfaces may comprise inductor coils on adjacent chips with
signals being communicated between chips via inductive coupling
between the coils.
[0037] In operation, the optical receiver interface may utilize
transistors available on the CMOS optoelectronics die 203. In an
exemplary embodiment, the pair of NMOS transistors M.sub.CS1 and
M.sub.CS2 may be in a common-source configuration with the drain
terminals coupled to the coupling pads 219. The CMOS transistors
M.sub.CS1 and M.sub.CS2 may communicate modulated currents to
another pair of NMOS transistors M.sub.C1 and M.sub.C2 in cascode
configuration on the CMOS VLSI die 201. The input impedance looking
into source terminals of these cascode devices may be very low, and
they may accept the currents transmitted by the common-source
transistor pair without creating large voltage signals. Low
impedance may desensitize this type of interface to parasitic
inductance, capacitance, and resistance associated with pads, bond
wires, or other interconnect elements. The transmitted currents may
then be converted to a voltage signal on the CMOS VLSI die 201 by a
pair of resistors R.sub.V1 and R.sub.V2 connected to drain
terminals of the cascode transistors M.sub.C1 and M.sub.C2. The
voltage signal may be further amplified by subsequent voltage gain
stages, the Rx gain stages 207, until it reaches an amplitude
suitable for use by the digital cores 205A.
[0038] The bias voltage VB may be operable to bias the
common-source pair comprising M.sub.CS1 and M.sub.CS2 and the
resistors R.sub.PD1 and R.sub.PD2 may be operable to bias the
photodiode 221. An electrical signal may be generated by the
photodiode 221 in response to an input light signal. The generated
signal may be AC-coupled via the capacitors C.sub.1 and C.sub.2 to
the gate terminals of the transistors M.sub.CS1 and M.sub.CS2 for
communication to the CMOS VLSI die 201 via the cascode circuit
comprising M.sub.C1 and M.sub.C2.
[0039] The transmission lines 217 may comprise tunable impedances
for matching to prior gain stages, such as the Tx gain stages 209,
and may also provide a low impedance for reduced sensitivity to
parasitic impedances in the coupling between the CMOS VLSI die 201
and the optoelectronics die 203. The signals received from the CMOS
VLSI die 201 may be communicated to the unit drivers 227, which may
be operable to modulate CW optical signals in the MZI 213 received
from the light source 215.
[0040] FIG. 3 is a block diagram of a flip-chip-type
photonically-enabled CMOS optical receiver system, in accordance
with an embodiment of the invention. Referring to FIG. 3, there is
shown a photonically-enabled CMOS optical communication system 300
comprising a CMOS VLSI die 301, an optoelectronics die 303, and
metal pillars 323. The CMOS VLSI die 301 comprises a plurality of
digital cores shown as the digital cores 305A and 305B, transistors
M.sub.2A and M.sub.2B, resistors R.sub.2A and R.sub.2B, inductors
L.sub.P1 and L.sub.P2, and coupling pads 319. There is also shown
control voltage V.sub.casc, supply voltage V.sub.DD, and output
voltages V.sub.on and V.sub.op.
[0041] The optoelectronics die 303 comprises a photodiode 321,
photodiode bias resistors R.sub.D1 and R.sub.D2, coupling
capacitors C.sub.1A and C.sub.1B, bias resistors R.sub.B1 and
R.sub.B2, a current source I.sub.B, and transistors M.sub.1A and
M.sub.1B. The transistors M.sub.1A, M.sub.2A, M.sub.1B, and
M.sub.2B comprise a differential cascode circuit for amplifying a
signal generated by the photodiode 321. The metal pillars 323 may
provide electrical interconnection as well as structural support
between the CMOS VLSI die 301 and the optoelectronics die 303. The
die may be configured in a face-to-face die attachment via metal
pillars 323 instead of side-by-side dies connected with bond wires,
for example, but the principle of operation and the advantages of
low-impedance interfaces are the same.
[0042] In operation, the transistors M.sub.1A and M.sub.1B on the
optoelectronics die 303 comprise a differential pair whose drains
may be coupled to the metal pillars 323 that may communicate
differential currents to the CMOS VLSI die 323. The cascode
transistors M.sub.2A and M.sub.2B may receive the communicated
currents that may be converted to a differential voltage signal via
the resistors R.sub.2A and R.sub.2B and bandwidth-enhancing
inductors L.sub.P1 and L.sub.P2. The optoelectronics die 303
comprises passive and active circuit elements to provide bias
voltage for the integrated photodetector, to convert photocurrent
to a voltage signal, and to couple the photo-generated signal to
the gates of transistors M.sub.1A and M.sub.1B.
[0043] FIG. 4. is a block diagram illustrating a
controlled-impedance split-transmitter interface, in accordance
with an embodiment of the invention. Referring to FIG. 4, there is
shown a photonically-enabled CMOS optical communication system 400
CMOS VLSI die 401, an optoelectronics die 403, and wire bonds
423.
[0044] In an exemplary embodiment, the CMOS optical communication
system 400 comprises transmission lines 417 as a break point
between the CMOS VLSI die 401 and the optoelectronics die 403,
which may thus comprise a controlled-impedance interface. The
resulting impedance may be relatively low, such as
Z.sub.0=50.OMEGA., thereby providing an insensitivity to parasitic
inductance, capacitance, and resistance associated with pads, bond
wires, or other interconnect elements.
[0045] The CMOS VLSI die may contain digital cores, such as the
digital cores 205A, 205B, 305A, and 305B, described with respect to
FIGS. 2 and 3, where the transmitted signal originates, as well as
analog signal conditioning circuitry such as transmission line
drivers. The CMOS VLSI die 401 also comprises Tx gain stages 409, a
current source I.sub.B, transistors M.sub.T1 and M.sub.T2, and
coupling pads 419.
[0046] The optoelectronics die 403 comprises transmission lines
417, which may provide proper electrical to optical velocity
matching for MZI operation. The optoelectronics die 403 also
comprises distributed amplifier stages implemented with
transistors, as illustrated schematically by the unit drivers 427.
These distributed amplifiers may provide large signals to optical
phase modulators in the MZI.
[0047] The optoelectronics die 403 also comprises sense resistors
R.sub.S1 and R.sub.S2, termination resistors R.sub.T1 and R.sub.T2,
a capacitor C.sub.R, and a common-mode feedback circuit comprising
a feedback gain stage AFB, a feedback control transistor M.sub.FB,
and a replica reference inverter 425. The common-mode feedback
circuit may be operable to convert limited-swing current-mode logic
(CML) signals to full-swing CMOS signals by matching the common
mode voltage on the transmission lines 417 to the transition
threshold of the unit drivers 427.
[0048] In operation, signals for transmission may be generated in
one or more digital cores in the CMOS VLSI die 401 and communicated
to the gate terminals of the transistors M.sub.T1 and M.sub.T2
comprising a differential pair. The signal amplified by the
differential pair may be communicated to the optoelectronics die
403 via the coupling pads 419, which may be coupled between die
using the wire bonds 423.
[0049] The coupling between the CMOS VLSI die 401 and the
optoelectronics die 403 is not limited to wire bonds, as
illustrated by the wire bonds 423 in FIG. 4. Accordingly, other
techniques may be utilized, such as solder balls, metal pillars,
conductive resin, and/or proximity interconnects, which may
comprise capacitively-coupled interfaces or inductively-coupled
interfaces, for example. Capacitively-coupled interfaces may
comprise the coupling pads 419 on adjacent chips comprising
capacitors for AC-coupling of signals, whereas inductively-coupled
interfaces may comprise inductor coils on adjacent chips with
signals being communicated between chips via inductive coupling
between the coils.
[0050] The transmission lines 417 may provide tunable impedances
for matching to prior gain stages, such as the differential pair
M.sub.T1 and M.sub.T2, and may also provide a low impedance for
reduced sensitivity to parasitic impedances in the coupling between
the CMOS VLSI die 401 and the optoelectronics die 403. The signals
received from the CMOS VLSI die 401 may be communicated to the unit
drivers 427, which may be operable to modulate optical signals in a
MZI modulator, such as the MZI 213, described with respect to FIG.
2.
[0051] FIG. 5. is a block diagram illustrating a low-impedance
split-transmitter cascode interface, in accordance with an
embodiment of the invention. Referring to FIG. 5, there is shown a
photonically-enabled CMOS optical communication system 500
comprising a CMOS VLSI die 501, an optoelectronics die 503, and
wire bonds 523.
[0052] In an exemplary embodiment, the CMOS optical communication
system 500 comprises transmission lines 517 on the optoelectronics
die 503 as in the controlled-impedance interface shown in FIG. 4,
but also comprises a break point between the CMOS VLSI die 501 and
the optoelectronics die 503 utilizing a splitting of the interface
circuits in a differential cascode amplifier stage comprising the
transistors M.sub.T1-M.sub.T4, as in the current-mode die
interface, described with respect to FIGS. 2 and 3. This further
lowers interface impedance compared to a directly-driven
transmission line, resulting in a lower voltage swing and even less
sensitivity to interconnect inductance and capacitance.
[0053] The interface comprises an open-drain differential driver on
the CMOS VLSI die 501 and cascode-configured transistors on the
optoelectronics die 503. The open-drain differential driver
comprises a pair of NMOS transistors M.sub.T1/M.sub.T2 and the
cascode transistors comprise the transistors M.sub.T3/M.sub.T4 with
the drain terminals of M.sub.T1/M.sub.T2 and the source terminals
of M.sub.T3/M.sub.T4 connected to the coupling pads 519 for
launching differential current signals into terminated transmission
lines 517 on the optoelectronics die 503. The optoelectronics die
503 also comprises a common-mode feedback loop, which matches the
common-mode voltage on the transmission lines 517 to the switching
threshold of the distributed amplifier stages comprising the unit
drivers 527.
[0054] The CMOS VLSI die 501 may contain digital cores, such as the
digital cores 205A, 205B, 305A, and 305B, described with respect to
FIGS. 2 and 3, where the transmitted signal originates, as well as
analog signal conditioning circuitry such as transmission line
drivers. The CMOS VLSI die 501 also comprises Tx gain stages 509, a
current source I.sub.B, transistors M.sub.T1 and M.sub.T2, and
coupling pads 519.
[0055] The optoelectronics die 503 comprises cascode transistors
M.sub.T3 and M.sub.T4, capacitors Cc, and transmission lines 517,
which may provide proper electrical to optical velocity matching
for MZI operation. The optoelectronics die 503 also comprises
distributed amplifier stages implemented with transistors, as
illustrated schematically by the unit drivers 527. These
distributed amplifiers may provide large signals to optical phase
modulators in the MZI.
[0056] The optoelectronics die 503 also comprises sense resistors
R.sub.S1 and R.sub.S2, termination resistors R.sub.T1 and R.sub.T2,
a capacitor C.sub.R, and a common-mode feedback circuit comprising
a feedback gain stage AFB, a feedback control transistor M.sub.FB,
and a replica reference inverter 525. The common-mode feedback
circuit may be operable to convert limited-swing current-mode logic
(CML) signals to full-swing CMOS signals.
[0057] Additionally, transistors on the optoelectronics die 503 may
be used to implement analog and control functions associated with
the optoelectronic devices. For example, this may include low-noise
voltage regulators for integrated photodetectors and calibration or
real-time control loops for the MZIs to compensate for the effect
of process and temperature variations. Retaining these functions on
the optoelectronics die 503 reduces the total number of
interconnects between the two dies and keeps sensitive analog and
control nets local and isolated from possible sources of crosstalk.
Digital state machines and low-speed serial communication
interfaces for digital control and monitoring can also be
implemented on the optoelectronics die 503 as needed.
[0058] In operation, signals for transmission may be generated in
one or more digital cores in the CMOS VLSI die 501 and communicated
to the gate terminals of the transistors M.sub.T1 and M.sub.T2
comprising a differential pair. The signal amplified by the
differential pair may be communicated to the optoelectronics die
503 via the coupling pads 519, which may be coupled between die
using the wire bonds 523.
[0059] The coupling between the CMOS VLSI die 501 and the
optoelectronics die 503 is not limited to wire bonds, as
illustrated by the wire bonds 523 in FIG. 5. Accordingly, other
techniques may be utilized, such as solder balls, metal pillars,
conductive resin, and/or proximity interconnects, which may
comprise capacitively-coupled interfaces or inductively-coupled
interfaces, for example. Capacitively-coupled interfaces may
comprise the coupling pads 519 on adjacent chips comprising
capacitors for AC-coupling of signals, whereas inductively-coupled
interfaces may comprise inductor coils on adjacent chips with
signals being communicated between chips via inductive coupling
between the coils.
[0060] The transmission lines 517 may provide tunable impedances
for matching to prior gain stages, such as the differential pair
M.sub.T1 and M.sub.T2. The low impedance at the source terminals of
the cascode transistors M.sub.T3 and M.sub.T4 provide reduced
sensitivity to parasitic impedances in the coupling between the
CMOS VLSI die 501 and the optoelectronics die 503. The signals
received from the CMOS VLSI die 501 may be communicated to the unit
drivers 527, which may be operable to modulate optical signals in a
MZI modulator, such as the MZI 213, described with respect to FIG.
2.
[0061] In an embodiment of the invention, a method and system are
disclosed for communicating electrical signals between an
electronics die 201, 301, 401, and 501 and an optoelectronics die
203, 303, 403, and 503 via coupling pads 219, 319, 419, and 519 on
the electronics die 201, 301, 401, and 501 and the optoelectronics
die 203, 303, 403, and 503 in an optical communication system 200,
300, 400, and 500. The coupling pads 219, 319, 419, and 519 may be
located in low impedance points in one or more transmit paths
and/or one or more receive paths in the photonically-enabled CMOS
optical communication system 200, 300, 400, and 500.
[0062] The electrical signals may be communicated via one or more
current-mode interfaces that may comprise a cascode amplifier stage
split between source terminals of transistors M.sub.C1, M.sub.C2,
M.sub.T1, M.sub.T2, M.sub.2A, and M.sub.2B on the electronics die
201, 301, 401, and 501 and drain terminals of transistors
M.sub.CS1, M.sub.CS2, M.sub.T3, M.sub.T4, M.sub.1A, and M.sub.1B on
the optoelectronics die 203, 303, 403, and 503. The electrical
signals may be communicated via one or more controlled-impedance
interfaces that may comprise one or more transmission line drivers
209 and 409 on a first die and one or more transmission lines 217,
417, and 517 on a second die of the optical communication system
200, 300, 400, and 500. The electrical signals may be communicated
via one or more capacitively-coupled interfaces that may comprise
capacitors formed by one or more of the contact pads 219, 319, 419,
and 519 on the electronics die 201, 301, 401, and 501 and one or
more of the contact pads on the optoelectronics die 203, 303, 403,
and 503. The electrical signals may be communicated via one or more
inductively-coupled interfaces. The coupling pads 219, 319, 419,
and 519 may be connected via one or more of: wire bonds 223, 423,
and 523, metal pillars 319, solder balls, or conductive resin. The
electronics die 201, 301, 401, and 501 and the optoelectronics die
203, 303, 403, and 503 may be coupled in a flip-chip
configuration.
[0063] While the invention has been described with reference to
certain embodiments, it will be understood by those skilled in the
art that various changes may be made and equivalents may be
substituted without departing from the scope of the present
invention. In addition, many modifications may be made to adapt a
particular situation or material to the teachings of the present
invention without departing from its scope. Therefore, it is
intended that the present invention not be limited to the
particular embodiments disclosed, but that the present invention
will include all embodiments falling within the scope of the
appended claims.
* * * * *