U.S. patent application number 16/074346 was filed with the patent office on 2019-08-22 for electrochemical deposition of elements in aqueous media.
This patent application is currently assigned to LumiShield Technologies Incorporated. The applicant listed for this patent is LumiShield Technologies Incorporated. Invention is credited to Hunaid B. NULWALA, John D. WATKINS, Xu ZHOU.
Application Number | 20190256994 16/074346 |
Document ID | / |
Family ID | 55442889 |
Filed Date | 2019-08-22 |




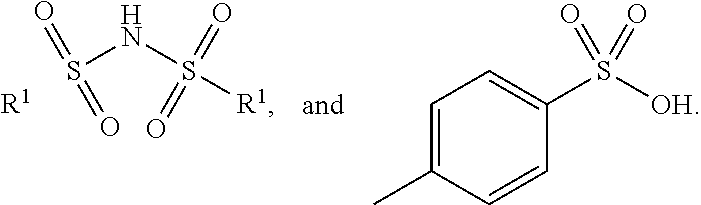




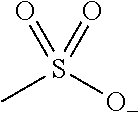
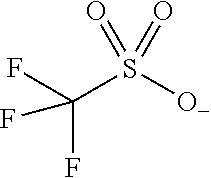
View All Diagrams
United States Patent
Application |
20190256994 |
Kind Code |
A1 |
NULWALA; Hunaid B. ; et
al. |
August 22, 2019 |
Electrochemical Deposition of Elements in Aqueous Media
Abstract
The disclosure relates to a method for the electrodeposition of
at least one metal onto a surface of a conductive substrate. In
some embodiments, the electrodeposition is conducted at a
temperature from about 10.degree. C. to about 70.degree. C., about
0.5 atm to about 5 atm, in an atmosphere comprising oxygen. In some
embodiments, the method comprises electrodepositing the at least
one metal via electrochemical reduction of a metal complex
dissolved in a substantially aqueous medium.
Inventors: |
NULWALA; Hunaid B.;
(Pittsburgh, PA) ; WATKINS; John D.; (Pittsburgh,
PA) ; ZHOU; Xu; (Pittsburgh, PA) |
|
Applicant: |
Name |
City |
State |
Country |
Type |
LumiShield Technologies Incorporated |
Pittsburgh |
PA |
US |
|
|
Assignee: |
LumiShield Technologies
Incorporated
Pittsburgh
PA
|
Family ID: |
55442889 |
Appl. No.: |
16/074346 |
Filed: |
February 16, 2016 |
PCT Filed: |
February 16, 2016 |
PCT NO: |
PCT/US2016/018050 |
371 Date: |
July 31, 2018 |
Current U.S.
Class: |
1/1 |
Current CPC
Class: |
C25D 3/56 20130101; C25D
9/08 20130101; C25D 3/54 20130101; C23C 28/321 20130101; C25D 3/44
20130101 |
International
Class: |
C25D 3/44 20060101
C25D003/44; C25D 9/08 20060101 C25D009/08; C25D 3/54 20060101
C25D003/54; C23C 28/00 20060101 C23C028/00; C25D 3/56 20060101
C25D003/56 |
Claims
1.-23. (canceled)
24. A method for electrodeposition of at least one reactive metal
onto a surface of a conductive substrate at a temperature from
about 10.degree. C. to about 70.degree. C., about 0.5 atm (50.66
kPa) to about 5 atm (506.62 kPa), in an atmosphere comprising
oxygen, the method comprising electrodepositing the at least one
reactive metal via electrochemical reduction of a metal complex
dissolved in a substantially aqueous medium the metal complex
comprising a metal center and ligands; wherein: the reactive metal
comprises at least one of aluminum, titanium, manganese, gallium,
vanadium, zirconium, and niobium; and the ligands are at least one
of sulfonate ligands and sulfonimide ligands.
25. The method of claim 24, wherein the at least one sulfonate
ligand is a ligand of a formula SO.sub.3R.sup.1, wherein R.sup.1 is
halo; substituted or unsubstituted C.sub.6-C.sub.18-aryl;
substituted or unsubstituted C.sub.1-C.sub.6-alkyl; and substituted
or unsubstituted C.sub.6-C.sub.18-aryl-C.sub.1-C.sub.6-alkyl.
26. The method of claim 24, wherein the at least one sulfonimide
ligand is a ligand of a formula N(SO.sub.2R.sup.1), wherein R.sup.1
is halo; substituted or unsubstituted C.sub.6-C.sub.18-aryl;
substituted or unsubstituted C.sub.1-C.sub.6-alkyl; and substituted
or unsubstituted C.sub.6-C.sub.18-aryl-C.sub.1-C.sub.6-alkyl.
27. The method of claim 24, wherein the at least one sulfonate
ligand comprises a sulfonate ligand of a formulae: ##STR00015##
28. The method of claim 24, wherein the at least one sulfonimide
ligand comprises a sulfonimide ligand of a formula:
##STR00016##
29. The method of claim 24, wherein the metal complex is at least
one metal complex of a formula Al(SO.sub.3R.sup.1).sub.n, wherein
R.sup.1 is halo; substituted or unsubstituted
C.sub.6-C.sub.18-aryl; substituted or unsubstituted
C.sub.1-C.sub.6-alkyl; n is an integer from 2 to 8; and
Al[N(SO.sub.3R.sup.1).sub.2].sub.n, wherein R.sup.1 is halo;
substituted or unsubstituted C.sub.6-C.sub.18-aryl; substituted or
unsubstituted C.sub.1-C.sub.6-alkyl; substituted or unsubstituted
C.sub.6-C.sub.18-aryl-C.sub.1-C.sub.6-alkyl; and n is an integer
from 1 to 4.
30. The method of claim 24, wherein the substantially aqueous
medium comprises an electrolyte.
31. The method of claim 30, wherein the electrolyte comprises at
least one of a halide electrolyte; a perchlorate electrolyte; an
amidosulfonate electrolyte; hexafluorosilicate electrolyte; a
tetrafluoroborate electrolyte; methanesulfonate electrolyte; and a
carboxylate electrolyte.
32. The method of claim 31, wherein the electrolyte comprises at
least one of compounds of a formula R.sup.3CO.sub.2--, wherein
R.sup.3 is substituted or unsubstituted C.sub.6-C.sub.18-aryl; or
substituted or unsubstituted C.sub.1-C.sub.6-alkyl.
33. The method of claim 31, wherein the electrolyte comprises at
least one of polycarboxylates; and lactones.
34. The method of claim 24, wherein the pH of the substantially
aqueous medium is buffered at a pH from about 1 to about 7.
35. The method of claim 24, wherein the substantially aqueous
medium comprises a water-miscible organic solvent.
36. The method of claim 35, wherein the water-miscible organic
solvent comprises at least one of an C.sub.1-C.sub.6-alkanol, a
C.sub.2-C.sub.10-polyol, a (poly)alkylene glycol ether, a
C.sub.2-C.sub.10-carboxylic acid; a C.sub.2-C.sub.10-ketone; a
C.sub.2-C.sub.10-aldehyde; a pyrrolidone; a
C.sub.2-C.sub.10-nitrile; a phthalate; a
C.sub.2-C.sub.10-dialkylamine; a C.sub.2-C.sub.10-dialkylformamide;
a C.sub.2-C.sub.10-dialkyl sulfoxide; a
C.sub.4-C.sub.10-heterocycloalkane; an aminoalcohol; and a
C4-C10-heteroarylene.
37. The method of claim 36, wherein the C.sub.1-C.sub.6-alkanol
comprises ethanol.
38. The method of claim 24, wherein the electrodepositing comprises
electrodepositing at least one layer of the at least one metal onto
the surface of the substrate.
39. The method of claim 24, wherein the electrodepositing comprises
electrodepositing at least a first layer and a second layer of the
at least one metal onto the surface of the substrate.
40. The method of claim 39, wherein the first layer comprises a
different at least one metal relative to the second layer.
41. A method for electrodeposition of at least one metal onto a
surface of a conductive substrate at a temperature from about
10.degree. C. to about 70.degree. C., about 0.5 atm (50.66 kPa) to
about 5 atm (506.62 kPa), in an atmosphere comprising oxygen, the
method comprising electrodepositing the at least one metal via
electrochemical reduction of a metal complex dissolved in a
substantially aqueous medium; wherein: the metal complex comprises
a metal center and ligands, wherein at least one of the ligands is
an electron withdrawing ligand and the ligands are sufficiently
electron withdrawing such that the reduction potential of the metal
in the metal complex is decreased below the over-potential for the
evolution of hydrogen gas due to water splitting; and the at least
one metal is at least one of reactive and non-reactive metals; or
the ligands are at least one of sulfonate ligands and sulfonimide
ligands.
42. A method for electrodeposition of at least one reactive metal
onto a surface of a conductive substrate at a temperature from
about 10.degree. C. to about 70.degree. C., about 0.5 atm (50.66
kPa) to about 5 atm (506.62 kPa), in an atmosphere comprising
oxygen, the method comprising electrodepositing the at least one
reactive metal via electrochemical reduction of a metal complex
dissolved in a substantially aqueous medium; wherein: the reactive
metal comprises at least one of aluminum, titanium, manganese,
gallium, vanadium, zirconium, and niobium; and the metal complex
comprises a metal center and ligands, wherein at least one of the
ligands is an electron withdrawing ligand, and are sufficiently
electron withdrawing such that the reduction potential of the metal
in the metal complex is decreased below the over-potential for the
evolution of hydrogen gas due to water splitting.
43. A method for electrodeposition of at least one reactive metal
onto a surface of a conductive substrate at a temperature from
about 10.degree. C. to about 70.degree. C., about 0.5 atm (50.66
kPa) to about 5 atm (506.62 kPa), in an atmosphere comprising
oxygen, the method comprising electrodepositing the at least one
reactive metal via electrochemical reduction of a metal complex
dissolved in a medium that is at least about 50% aqueous, the metal
complex comprising a metal center and ligands; wherein: the
reactive metal comprises at least one of aluminum, titanium,
manganese, gallium, vanadium, zirconium, and niobium; and the
ligands are at least one of sulfonate ligands and sulfonimide
ligands.
44. The method of claim 43, wherein the medium is at least about
60% aqueous.
45. The method of claim 44, wherein the medium is at least about
70% aqueous.
46. The method of claim 45, wherein the medium is at least about
80% aqueous.
47. The method of claim 46, wherein the medium is at least about
90% aqueous.
48. The method of claim 47, wherein the medium is at least about
99% aqueous.
49. The method of claim 24, wherein the reactive metal is aluminum,
and the medium consists essentially of water.
Description
BACKGROUND
[0001] Electrodeposition of metals, including aluminum, at ambient
temperatures has been widely investigated owing to a variety of
potential applications that include uses in corrosion-resistant
applications, decorative coatings, performance coatings, surface
aluminum alloys, electro-refining processes, and aluminum-ion
batteries. Due to the large reduction potential of some metals,
these materials have been exclusively used in non-aqueous media.
For example, baths that have been developed for aluminum
electrodeposition fall into three categories. These categories are
inorganic molten salts, ionic liquids, and molecular organic
solvents. Inorganic molten salt baths require a relatively high
temperature (e.g., >140.degree. C.). And in some instances, such
baths are prone to the volatilization of corrosive gases. For
example, AlCl.sub.3--NaCl--KCl baths suffer from the volatilization
of corrosive AlCl.sub.3 gas. In addition, baths that have been
developed for aluminum electrodeposition have high energy
consumption and material limitations of the substrate and
apparatus.
[0002] Ionic liquid and organic solvent baths both allow
electrodeposition of a metal, such as aluminum, at lower
temperatures. For example, aluminum plating from room temperature
ionic liquids has been the subject of a number of studies over the
past few years. Still, an industrial process for aluminum
electrodeposition from ionic liquids does not been realized, even
though a manufacturing pilot plant was developed by Nisshin Steel
Co., Ltd. The plant was not considered economically viable due to
cost associated with materials and the need to perform plating in
an inert atmosphere, free of humidity.
[0003] Commercial aluminum electroplating processes from organic
solvents has been deployed with limited success. As of now, only
two processes, namely, the Siemens Galvano Aluminium (SIGAL)
process and Room-temperature Electroplated Aluminium (REAL) process
have been deployed. The SIGAL process is currently licensed to
AlumiPlate, Inc. and yields high quality aluminum. However,
organoaluminum processes are self-ignitable and extremely sensitive
to atmospheric water.
SUMMARY
[0004] Disclosed herein is a method for the electrodeposition of at
least one metal onto a surface of a conductive substrate. The
electrodeposition is performed at a temperature from about
10.degree. C. to about 70.degree. C. and, in some instances, at a
pressure of about 0.5 atm to about 5 atm, in an atmosphere
comprising oxygen. The method of the various embodiments described
herein comprises electrodepositing the at least one metal via
electrochemical reduction of a metal complex dissolved in a
substantially aqueous medium.
DESCRIPTION OF THE FIGURES
[0005] The drawings illustrate generally, by way of example, but
not by way of limitation, various embodiments discussed in the
present document.
[0006] FIG. 1 is a plot of a series for metal reductions versus
that of proton reduction.
[0007] FIG. 2 is cyclic voltammograms for aluminum complexes at 1 M
concentration in water (i) Al(Tf.sub.2N).sub.3; and (ii) AlCl.sub.3
on a 3 mm glassy carbon working electrode vs. a Ag/AgCl (3M NaCl)
reference electrode and an aluminum counter electrode and a 50
mVs.sup.-1 scan rate.
[0008] FIG. 3 is cyclic voltammograms for aluminum complexes in
water (i) 6 M p-TSA; (ii) 0.5 M Al(p-TSA).sub.6 (pH 0.24); (iii)
0.5 M Al(p-TSA).sub.4; (iv) 0.5 M Al(p-TSA).sub.6 with pH adjusted
to 1.35 with NH.sub.4OH; and (v) 1 M AlCl.sub.3 on a 3 mm glassy
carbon working electrode vs. a Ag/AgCl (3 M NaCl) reference
electrode and an aluminum counter electrode and a 50 mVs.sup.-1
scan rate.
[0009] FIG. 4 is cyclic voltammograms for aluminum complexes in
water (i) 1 M Al(MS).sub.3 (pH 2.47); (ii) 3 M Al(MS).sub.1 (pH
3.15); and (iii) 1 M AlCl.sub.3 on a 3 mm glassy carbon working
electrode vs. a Ag/AgCl (3 M NaCl) reference electrode and an
aluminum counter electrode and a 50 mVs.sup.-1 scan rate.
[0010] FIG. 5 is a scanning electron microscopy
(SEM)/energy-dispersive X-ray (EDX) spectroscopy image of 20 AWG
copper wire plated to a thickness in excess of 10 .mu.m with
aluminum.
DESCRIPTION
Introduction
[0011] Many commercially important elements from the periodic table
cannot be easily electrodeposited from aqueous solutions because
their reduction potentials can be much larger than the
electrochemical window for water (e.g., the over-potential for the
evolution of hydrogen gas due to water splitting). The various
embodiments described herein provide an approach whereby the
reduction potential of metals is "tuned" in a way that they are
amendable to electrodeposition from aqueous solutions. In one
embodiment, the reduction potential of the metal is tuned by
selecting ligands that change the reduction potential of the metals
such that the metal can be electrodeposited from an aqueous
solution without, e.g., hydrogen gas generation. In other
embodiments, the ligands are chosen in such a way that they affect
the reduction potential of the metal center, thermodynamically,
such that the reduction of the metal center occurs prior to the
hydrogen evolution overpotential.
[0012] Some embodiments described herein, therefore, are directed
to a method for the electrodeposition of at least one metal onto a
surface of a conductive substrate. In some embodiments, the
electrodeposition is conducted at a temperature from about
10.degree. C. to about 70.degree. C. (e.g., about 10.degree. C. to
about 25.degree. C.; about 10.degree. C. to about 40.degree. C.;
about 15.degree. C. to about 50.degree. C.; about 25.degree. C. to
about 50.degree. C.; or about 30.degree. C. to about 50.degree.
C.), about 0.5 atm to about 5 atm (e.g., about 0.5 atm to about 2
atm; 0.5 atm to about 1 atm; 1 atm to about 3 atm; 2 atm to about 5
atm or about 2 atm to about 3 atm), in an atmosphere comprising
oxygen (e.g., in an atmosphere comprising about 1 to about 100%
oxygen; about 5 to about 50% oxygen; about 10 to about 30% oxygen;
about 15 to about 30% oxygen; about 20 to about 80% oxygen or about
25 to about 75% oxygen, the balance of the atmosphere comprising
gases including nitrogen, carbon dioxide, carbon monoxide, water
vapor, etc.). In some embodiments, the method comprises
electrodepositing the at least one metal via electrochemical
reduction of a metal complex dissolved in a substantially aqueous
medium. It should be understood that the method of the various
embodiments described herein can also be conducted under conditions
wherein the medium also contains at least some amount of dissolved
oxygen (e.g., dissolved oxygen in the water present in the
medium).
Metals
[0013] The metals that can be electrodeposited using the
electrodeposition methods described herein are not limited.
Electron withdrawing approach is applicable to at least the metals
in Groups 2, 4, 5, 7, and 13. Metals useful in the methods
described herein include metals having in general a Pauling
electronegativity below 1.9 (e.g., about 1.3 to about 1.6; about
1.7 to about 1.9; and about 1.6 to about 1.9). Generally speaking,
such metals would be considered nearly impossible to plate in water
at high efficiency; or such metals would encounter problems with
hydrogen embrittlement.
[0014] The electromotive series for the process
M.sup.n++ne.sup.-.fwdarw.M, illustrated in FIG. 1 shows an example
of a series for metal reductions versus that of proton reduction.
Metals with a negative reduction are considered more difficult to
reduce than protons in the presence of an acid source and are able
to do so based on the high overpotential for proton reduction.
These metals may have a reduced cathodic plating efficiency as a
result of competitive hydronium ion reduction or an increased risk
of hydrogen embrittlement. According to the various embodiments
described herein, by addition of a suitable electron withdrawing
ligand, any metal on this electromotive series may benefit from the
reduction potential being made more positive by the inductive
effect of the ligand thus creating a situation of increased
efficiency for the plating process as compared with the hydrogen
reduction overpotential. Examples of metals that are in the
"electromotive series" include gold, platinum, iridium, palladium,
silver, mercury, osmium, ruthenium, copper, bismuth, antimony,
tungsten, lead, tin, molybdenum, nickel, cobalt, indium, cadmium,
iron, chromium, zinc, niobium, manganese, vanadium, aluminum,
beryllium, titanium, magnesium, calcium, strontium, barium, and
potassium. See, e.g., EP0175901, which is incorporated by reference
as if fully set forth herein.
[0015] In some embodiments, suitable metals for use in the various
methods described herein include metals that have a reduction
potential from about 0 V to about -2.4 V.
[0016] In some embodiments, the metals that can be electrodeposited
using the electrodeposition methods described herein can be
"reactive" or "non-reactive" metals. The term "reactive," as used
herein, generally refers to metals that are reactive to, among
other things, oxygen and water. Reactive metals include
self-passivating metals. Self-passivating metals contain elements
which can react with oxygen to form surface oxides (e.g., such as
the oxides of, but not limited to, Cr, Al, Ti, etc.). These surface
oxide layers are relatively inert and prevent further corrosion of
the underlying metal.
[0017] Examples of reactive metals include aluminum, titanium,
manganese, gallium, vanadium, zinc, zirconium, and niobium.
Examples of non-reactive metals include tin, gold, copper, silver,
rhodium, and platinum.
[0018] Additional metals that can be electrodeposited using the
electrodeposition methods described herein include molybdenum,
tungsten, iridium, gallium, indium, strontium, scandium, yttrium,
magnesium, manganese, chromium, lead, tin, nickel, cobalt, iron,
zinc, niobium, vanadium, titanium, beryllium, and calcium.
Metal Complex
[0019] The metal complexes of the various embodiments described
herein comprise a metal center and ligands associated with the
metal center. In some embodiments, at least one of the ligands
associated with the metal center is an electron withdrawing
ligand.
[0020] Metal complexes of the various embodiments described herein
include metal complexes of the formula:
(M.sub.1L.sub.aL.sub.b).sub.p(M.sub.2L.sub.aL.sub.b).sub.d
wherein M.sub.1 and M.sub.2 each, independently represents a metal
center; L is an electron withdrawing ligand; p is from 0 to 5; and
d is from 0 to 5; a is from 1 to 8 (e.g., from 1 to 4; from 0.5 to
1.5; from 2 to 8; 2 to 6; and 4 to 6); and b is from 1 to 8 (e.g.,
from 1 to 4; from 0.5 to 1.5; from 2 to 8; 2 to 6; and 4 to 6). The
metal complexes contemplated herein, therefore, can include metal
complexes comprising more than one metal species and can even
include up to ten different metal species when p and d are each 5.
In addition, each of the metal complexes can have the same or
different ligands around the metal center. Thus, for example, one
can have two different metal complexes (e.g., when p is 1 and d is
1), the first being Cr(SO.sub.3R.sup.1).sub.a; and the second being
Mo(SO.sub.3R.sup.1).sub.a. This combination of metal complexes can
be used to electrodeposit a CrMo alloy on a surface of a
substrate.
[0021] As used herein, the term "metal center" generally refers to
a metal cation of a metal from Groups 2, 4, 5, 7, and 13. But it
should be understood that metal cations from Groups 2, 4, 5, 7, and
13 can be alloy plated using the methods described herein with
metal cations from Groups 3, 6, 8, 9, 10, 11, and 12.
[0022] Some examples of "metal centers" include a cation of
aluminum (e.g., Al.sup.+3), titanium (e.g., Ti.sup.2+, Ti.sup.3+,
and Ti.sup.+4), manganese (e.g., Mn.sup.2+ and Mn.sup.3+), gallium
(e.g., Ga.sup.+3), vanadium (e.g., V.sup.+2, V.sup.3+, and
V.sup.+4), zinc (e.g., Zn.sup.2+), zirconium (e.g., Zr.sup.4+),
niobium (e.g., Nb.sup.+3 and Nb.sup.+5), tin (e.g., Sn.sup.+2 and
Sn.sup.+4), gold (e.g., Au.sup.+1 and Au.sup.+3), copper (e.g.,
Cu.sup.+1 and Cu.sup.+3), silver (e.g., Ag.sup.+1), rhodium (e.g.,
Rh.sup.+2 and Rh.sup.+4), platinum (e.g., Pt.sup.+2 and Pt.sup.+4),
chromium (e.g., Cr.sup.+2, Cr.sup.+3, and Cr.sup.+6), tungsten
(e.g., W.sup.+4 and W.sup.+5), and iridium (e.g., Ir.sup.+1 and
Ir.sup.+4).
[0023] As defined herein, the term "electron withdrawing ligand"
generally refers to a ligand or combination of one or more ligands
(e.g., two to three; two to six; three to six; or four to six
ligands) associated with the metal center, wherein the ligand or
ligands are sufficiently electron withdrawing such that the
reduction potential of the metal center in the metal complex is
decreased below the over-potential for the evolution of hydrogen
gas due to water splitting. The term "over-potential for the
evolution of hydrogen gas due to water splitting" refers, in some
instances, to a potential more negative than -1.4 V versus Ag/AgCl,
where one generally observes significant hydrogen generation.
[0024] In some embodiments, electron withdrawing ligands can be
ligands wherein the conjugate acid of the ligand has a pKa of from
about 2 to about -5 (e.g., about -1.5 to about -4; about -2 to
about -3; about -2 to about -4; about -1 to about -3; and about 2
to about -2).
[0025] In some embodiments, the ligands that are useful in the
methods described herein include sulfonate ligands, sulfonimide
ligands, carboxylate ligands; and .beta.-diketonate ligands.
[0026] Examples of sulfonate ligands include sulfonate ligands of
the formula .sup.-OSO.sub.2R.sup.1, wherein R.sup.1 is halo;
substituted or unsubstituted C.sub.6-C.sub.18-aryl; substituted or
unsubstituted C.sub.1-C.sub.6-alkyl; substituted or unsubstituted
C.sub.6-C.sub.18-aryl-C.sub.1-C.sub.6-alkyl.
[0027] Examples of sulfonimide ligands include ligands of the
formula .sup.-N(SO.sub.3R.sup.1), wherein R.sup.1 is wherein
R.sup.1 is halo; substituted or unsubstituted
C.sub.6-C.sub.18-aryl; substituted or unsubstituted
C.sub.1-C.sub.6-alkyl; substituted or unsubstituted
C.sub.6-C.sub.18-aryl-C.sub.1-C.sub.6-alkyl.
[0028] Examples of carboxylate ligands include ligands of the
formula R.sup.1C(O)O.sup.-, wherein R.sup.1 is wherein R.sup.1 is
halo; substituted or unsubstituted C.sub.6-C.sub.18-aryl;
substituted or unsubstituted C.sub.1-C.sub.6-alkyl; substituted or
unsubstituted C.sub.6-C.sub.18-aryl-C.sub.1-C.sub.6-alkyl. Other
examples of carboxylate ligands include ligands of the formula
.sup.-O(O)C--R.sup.2--C(O)O.sup.- wherein R.sup.2 is
(C.sub.1-C.sub.6)-alkylenyl or
(C.sub.3-C.sub.6)-cycloalkylenyl.
[0029] In some embodiments, the ligands can be ligands such as the
ones described in Scheme I, herein.
##STR00001##
[0030] Specific examples of sulfonate ligands include sulfonate
ligands of the formulae:
##STR00002##
[0031] Specific examples of sulfonimide ligands include sulfonimide
ligand of the formula:
##STR00003##
wherein each R.sup.1 is independently F or CF.sub.3. In some
embodiments, each R.sup.1 is the same and can be F or CF.sub.3.
[0032] Examples of .beta.-diketonate ligands includes ligands of
the formula:
##STR00004##
where R.sup.3, R.sup.4, and R.sup.5 may be substituted or
unsubstituted C.sub.6-C.sub.18-aryl; substituted or unsubstituted
C.sub.1-C.sub.6-alkyl; or substituted or unsubstituted
C.sub.6-C.sub.18-aryl-C.sub.1-C.sub.6-alkyl, with the understanding
that all resonance structures of the two .beta.-diketonate ligands
picture above, are also included.
[0033] In some embodiments, .alpha.-diketonate ligands can have the
formula R.sup.6C(.dbd.O)CHCHC(.dbd.O)R.sup.7, wherein R.sup.6 and
R.sup.7 may be selected from alkoxy groups (e.g., methoxy, ethoxy,
propoxy, hexyloxy, octyloxy, and the like), aryloxy groups (e.g.,
phenoxy, biphenyloxy, anthracenyloxy, naphthyloxy, pyrenyloxy, and
the like), and arylalkyloxy groups (e.g., benzyloxy, naphthyloxy,
and the like).
[0034] In one embodiment, the ligand is acetylacetonate, also known
as an "acac" ligand.
[0035] Some of the ligands described herein are shown in their
deprotonated form (e.g., in the form of their conjugate base).
Contemplated herein are also the ligands in their conjugate acid
form such as, for example:
##STR00005##
In addition, contemplated herein are ligands that can be in
equilibrium between their conjugate acid and conjugate base forms,
such as, for example:
##STR00006##
[0036] Various ratios of metal to ligand are contemplated for use
in the methods described herein. For example, the ratio of metal to
ligand can be from about 1:50 to about 1:1 (e.g., from about 1:50
to about 1:25; about 1:30 to about 1:15; about 1:15 to about 1:5;
about 1:10 to about 1:1; and about 1:10 to about 1:5).
[0037] The terms "halo," "halogen," or "halide" group, as used
herein, by themselves or as part of another substituent, mean,
unless otherwise stated, a fluorine, chlorine, bromine, or iodine
atom.
[0038] The term "aryl," as used herein, refers to substituted or
unsubstituted cyclic aromatic hydrocarbons that do not contain
heteroatoms in the ring. Thus aryl groups include, but are not
limited to, phenyl, azulenyl, heptalenyl, biphenyl, indacenyl,
fluorenyl, phenanthrenyl, triphenylenyl, pyrenyl, naphthacenyl,
chrysenyl, biphenylenyl, anthracenyl, and naphthyl groups. In some
embodiments, aryl groups contain about 6 to about 18 carbons
(C.sub.6-C.sub.18; e.g., C.sub.6-C.sub.12; C.sub.6-C.sub.10; and
C.sub.12-C.sub.18) in the ring portions of the groups.
Representative substituted aryl groups can be mono-substituted or
substituted more than once, such as, but not limited to, 2-, 3-,
4-, 5-, or 6-substituted phenyl or 2-8 substituted naphthyl
groups.
[0039] The term "alkyl," as used herein, refers to substituted or
unsubstituted straight chain and branched alkyl groups and
cycloalkyl groups having from 1 to 50 carbon atoms
(C.sub.1-C.sub.50; e.g., C.sub.10-C.sub.30, C.sub.12-C.sub.18;
C.sub.1-C.sub.20, C.sub.1-C.sub.10; C.sub.1-C.sub.8;
C.sub.1-C.sub.6, and C.sub.1-C.sub.3). Examples of straight chain
alkyl groups include those with from 1 to 8 carbon atoms
(C.sub.1-C.sub.8) such as methyl, ethyl, n-propyl, n-butyl,
n-pentyl, n-hexyl, n-heptyl, n-octyl groups. Examples of branched
alkyl groups include, but are not limited to, isopropyl, iso-butyl,
sec-butyl, t-butyl, neopentyl, isopentyl, 2,2-dimethylpropyl, and
isostearyl groups. Examples of cycloalkyl groups include
cyclopropyl, cyclobutyl, cyclopentyl, and cyclohexyl groups.
[0040] The term "substituted" as used herein refers to a group
(e.g., alkyl and aryl) or molecule in which one or more hydrogen
atoms contained thereon are replaced by one or more "substituents."
The term "substituent" as used herein refers to a group that can be
or is substituted onto a molecule or onto a group. Examples of
substituents include, but are not limited to, a halogen (e.g., F,
Cl, Br, and I); an oxygen atom in groups such as hydroxyl groups,
alkoxy groups, aryloxy groups, aralkyloxy groups, oxo(carbonyl)
groups, carboxyl groups including carboxylic acids, carboxylates,
and carboxylate esters; a sulfur atom in groups such as thiol
groups, alkyl and aryl sulfide groups, sulfoxide groups, sulfone
groups, sulfonyl groups, and sulfonamide groups; a nitrogen atom in
groups such as amines, hydroxylamines, nitriles, nitro groups,
N-oxides, hydrazides, azides, and enamines; and other heteroatoms
in various other groups. Non-limiting examples of substituents that
can be bonded to a substituted carbon (or other) atom include F,
Cl, Br, I, OR, OC(O)N(R).sub.2, CN, NO, NO.sub.2, ONO.sub.2, azido,
CF.sub.3, OCF.sub.3, R, O (oxo), S (thiono), C(O), S(O),
methylenedioxy, ethylenedioxy, N(R).sub.2, SR, SOR, SO.sub.2R,
SO.sub.2N(R).sub.2, SO.sub.3R, C(O)R, C(O)C(O)R, C(O)CH.sub.2C(O)R,
C(S)R, C(O)OR, OC(O)R, C(O)N(R).sub.2, OC(O)N(R).sub.2,
C(S)N(R).sub.2, (CH.sub.2).sub.0-2N(R)C(O)R,
(CH.sub.2).sub.0-2N(R)N(R).sub.2, N(R)N(R)C(O)R, N(R)N(R)C(O)OR,
N(R)N(R)CON(R).sub.2, N(R)SO.sub.2R, N(R)SO.sub.2N(R).sub.2,
N(R)C(O)OR, N(R)C(O)R, N(R)C(S)R, N(R)C(O)N(R).sub.2,
N(R)C(S)N(R).sub.2, N(COR)COR, N(OR)R, C(.dbd.NH)N(R).sub.2,
C(O)N(OR)R, or C(.dbd.NOR)R, wherein R can be, for example,
hydrogen, alkyl, acyl, cycloalkyl, aryl, aralkyl, heterocyclyl,
heteroaryl, or heteroarylalkyl.
[0041] The term "acyl" as used herein refers to a group containing
a carbonyl moiety wherein the group is bonded via the carbonyl
carbon atom. The carbonyl carbon atom is also bonded to another
carbon atom, which can be part of a substituted or unsubstituted
alkyl, aryl, aralkyl cycloalkyl, cycloalkylalkyl, heterocyclyl,
heterocyclylalkyl, heteroaryl, heteroarylalkyl group or the like.
In the special case wherein the carbonyl carbon atom is bonded to a
hydrogen, the group is a "formyl" group, an acyl group as the term
is defined herein. An acyl group can include 0 to about 12-40,
6-10, 1-5 or 2-5 additional carbon atoms bonded to the carbonyl
group. An acryloyl group is an example of an acyl group. An acyl
group can also include heteroatoms within the meaning here. A
nicotinoyl group (pyridyl-3-carbonyl) is an example of an acyl
group within the meaning herein. Other examples include acetyl,
benzoyl, phenylacetyl, pyridylacetyl, cinnamoyl, and acryloyl
groups and the like. When the group containing the carbon atom that
is bonded to the carbonyl carbon atom contains a halogen, the group
is termed a "haloacyl" group. An example is a trifluoroacetyl
group.
[0042] The term "aralkyl," "arylalkyl," and "aryl-alkyl" as used
herein refers to alkyl groups as defined herein in which a hydrogen
or carbon bond of an alkyl group is replaced with a bond to an aryl
group as defined herein. Representative aralkyl groups include
benzyl and phenylethyl groups.
[0043] The term "heteroaralkyl" and "heteroarylalkyl" as used
herein refers to alkyl groups as defined herein in which a hydrogen
or carbon bond of an alkyl group is replaced with a bond to a
heteroaryl group as defined herein.
[0044] The term "heterocyclyl" as used herein refers to substituted
or unsubstituted aromatic and non-aromatic ring compounds
containing 3 or more ring members, of which, one or more is a
heteroatom such as, but not limited to, N, O, and S. Thus, a
heterocyclyl can be a cycloheteroalkyl, or a heteroaryl, or if
polycyclic, any combination thereof. In some embodiments,
heterocyclyl groups include 3 to about 20 ring members, whereas
other such groups have 3 to about 15 ring members. In some
embodiments, heterocyclyl groups include heterocyclyl groups that
include 3 to 8 carbon atoms (C.sub.3-C.sub.8), 3 to 6 carbon atoms
(C.sub.3-C.sub.6) or 6 to 8 carbon atoms (C.sub.6-C.sub.8). A
heterocyclyl group designated as a C.sub.2-heterocyclyl can be a
5-ring with two carbon atoms and three heteroatoms, a 6-ring with
two carbon atoms and four heteroatoms and so forth. Likewise a
C.sub.4-heterocyclyl can be a 5-ring with one heteroatom, a 6-ring
with two heteroatoms, and so forth. The number of carbon atoms plus
the number of heteroatoms equals the total number of ring atoms. A
heterocyclyl ring can also include one or more double bonds. A
heteroaryl ring is an embodiment of a heterocyclyl group. The
phrase "heterocyclyl group" includes fused ring species including
those that include fused aromatic and non-aromatic groups.
Representative heterocyclyl groups include, but are not limited to
piperidynyl, piperazinyl, morpholinyl, furanyl, pyrrolidinyl,
pyridinyl, pyrazinyl, pyrimidinyl, triazinyl, thiophenyl,
tetrahydrofuranyl, pyrrolyl, oxazolyl, imidazolyl, triazolyl,
tetrazolyl, benzoxazolinyl, and benzimidazolinyl groups.
[0045] The term "alkoxy" as used herein refers to an oxygen atom
connected to an alkyl group, including a cycloalkyl group, as are
defined herein. Examples of linear alkoxy groups include but are
not limited to methoxy, ethoxy, propoxy, butoxy, pentyloxy,
hexyloxy, and the like. Examples of branched alkoxy include but are
not limited to isopropoxy, sec-butoxy, tert-butoxy, isopentyloxy,
isohexyloxy, and the like. Examples of cyclic alkoxy include but
are not limited to cyclopropyloxy, cyclobutyloxy, cyclopentyloxy,
cyclohexyloxy, and the like. An alkoxy group can include one to
about 12-20 or about 12-40 carbon atoms bonded to the oxygen atom,
and can further include double or triple bonds, and can also
include heteroatoms. For example, an allyloxy group is an alkoxy
group within the meaning herein. A methoxyethoxy group is also an
alkoxy group within the meaning herein, as is a methylenedioxy
group in a context where two adjacent atoms of a structure are
substituted therewith.
[0046] The term "aryloxy" and "heteroaryloxy" as used herein refers
to an oxygen atom connected to an aryl group or a heteroaryl group,
as the terms are defined herein. Examples of aryloxy groups include
but are not limited to phenoxy, naphthyloxy, and the like. Examples
of heteroaryloxy groups include but are not limited to pyridoxy and
the like.
[0047] The term "amine" as used herein refers to primary,
secondary, and tertiary amines having, e.g., the formula
N(group).sub.3 wherein each group can independently be H or non-H,
such as alkyl, aryl, and the like. Amines include but are not
limited to alkylamines, arylamines, arylalkylamines; dialkylamines,
diarylamines, diaralkylamines, heterocyclylamines and the like; and
ammonium ions.
[0048] The term "alkylenyl" as used herein refers to straight chain
and branched, saturated divalent groups having from 1 to 20 carbon
atoms, 10 to 20 carbon atoms, 12 to 18 carbon atoms, 1 to about 20
carbon atoms, 1 to 10 carbons, 1 to 8 carbon atoms or 1 to 6 carbon
atoms. Examples of straight chain alkylenyl groups include those
with from 1 to 6 carbon atoms such as --CH.sub.2--,
--CH.sub.2CH.sub.2--, --CH.sub.2CH.sub.2CH.sub.2--,
--CH.sub.2CH.sub.2CH.sub.2CH.sub.2--, and
--CH.sub.2CH.sub.2CH.sub.2CH.sub.2CH.sub.2--. Examples of branched
alkylenyl groups include --CH(CH.sub.3)CH.sub.2-- and
--CH.sub.2CH(CH.sub.3)CH.sub.2--.
[0049] The term "cycloalkylenyl" as used herein refers to cyclic
(mono- and polycyclic, including fused and non-fused polycyclic),
saturated carbon-only divalent groups having from 3 to 20 carbon
atoms, 10 to 20 carbon atoms, 12 to 18 carbon atoms, 3 to about 10
carbon atoms, 3 to 10 carbons, 3 to 8 carbon atoms or 3 to 6 carbon
atoms. Examples of cycloalkylenyl groups include:
##STR00007##
wherein the wavy lines represent the points of attachment to, e.g.,
the moieties --C(O)O.sup.-.
[0050] In some embodiments, the metal complex is at least one metal
complex of the formula Al(SO.sub.3R.sup.1).sub.n, wherein R.sup.1
is halo; substituted or unsubstituted C.sub.6-C.sub.18-aryl;
substituted or unsubstituted C.sub.1-C.sub.6-alkyl; substituted or
unsubstituted C.sub.6-C.sub.18-aryl-C.sub.1-C.sub.6-alkyl; n is an
integer from 2 to 8; and Al[N(SO.sub.3R.sup.1).sub.2].sub.n,
wherein R.sup.1 is halo; substituted or unsubstituted
C.sub.6-C.sub.18-aryl; substituted or unsubstituted
C.sub.1-C.sub.6-alkyl; substituted or unsubstituted
C.sub.6-C.sub.18-aryl-C.sub.1-C.sub.6-alkyl; and n is an integer
from 1 to 4.
[0051] Although not wishing to be bound by any specific theory, it
is believed that the metal complex can be additionally complexed
with any species present in the substantially aqueous medium that
is capable of complexing with the metal center. For example, in
some instances, the substantially aqueous medium is buffered with a
citrate buffer. It is possible that the metal center of the metal
complex can coordinate not only with electron withdrawing ligands,
but also with the citrate in the buffer.
Substantially Aqueous Medium
[0052] The various embodiments of the methods described herein
comprise electrodepositing the at least one metal via
electrochemical reduction of a metal complex dissolved in a
substantially aqueous medium.
[0053] In some embodiments, the substantially aqueous medium
comprises an electrolyte. Generally speaking, the electrolyte can
comprise any cationic species coupled with a corresponding anionic
counterion (e.g., some of the sulfonate ligands, sulfonimide
ligands, carboxylate ligands; and .beta.-diketonate ligands
described herein). Cationic species include, for example, a
sulfonium cation, an ammonium cation, a phosphonium cation, a
pyridinium cation, a bipyridinium cation, an amino pyridinium
cation, a pyridazinium cation, an oxazolium cation, a pyrazolium
cation, an imidazolium cation, a pyrimidinium cation, a triazolium
cation, a thiazolium cation, an acridinium cation, a quinolinium
cation, an isoquinolinium cation, an orange-acridinium cation, a
benzotriazolium cation, or a methimazolium cation. See, e.g.,
Published U.S. Appl. No. 2013/0310569, which is incorporated by
reference as if fully set forth herein.
[0054] An electrolyte can also comprise a cationic metal with a
more negative reduction potential than the metal center in the
metal complex of the various embodiments described herein. In other
embodiments, the electrolyte can comprise any suitable cation,
including .sup.+NR.sub.4, wherein each R is independently hydrogen
or C.sub.1-C.sub.6-alkyl; .sup.+PR.sub.4, wherein each R is
independently hydrogen or C.sub.1-C.sub.6-alkyl; imidazolium,
pyridinium, pyrrolidinium, piperidinium; and .sup.+SR.sub.3; in
combination with any suitable anion.
[0055] Examples of electrolytes include electrolytes comprising at
least one of a halide electrolyte (e.g., tetrabutylammonium
chloride, bromide, and iodide); a perchlorate electrolyte (e.g.,
lithium perchlorate, sodium perchlorate, and ammonium perchlorate);
an amidosulfonate electrolyte; hexafluorosilicate electrolyte
(e.g., hexafluorosilicic acid); a tetrafluoroborate electrolyte
(e.g., tetrabutylammonium tetrafluoroborate); a sulfonate
electrolyte (e.g., tin methanesulfonate); and a carboxylate
electrolyte.
[0056] Examples of carboxylate electrolytes include electrolytes
comprising at least one of compound of the formula
R.sup.3CO.sub.2.sup.-, wherein R.sup.3 is substituted or
unsubstituted C.sub.6-C.sub.18-aryl; substituted or unsubstituted
C.sub.1-C.sub.6-alkyl. Carboxylate electrolytes also include
polycarboxylates such as citrate (e.g., sodium citrate); and
lactones, such as ascorbate (e.g., sodium ascorbate).
[0057] But in some embodiments, the metal complex can also act as
an electrolyte.
[0058] In sum, it should be understood that: (i) the metal complex
can be the electrolyte (e.g., have a dual function as metal complex
for electrodeposition and as electrolyte); (ii) when a buffer is
used, the metal complex, in combination with the buffer, can be the
electrolyte; (iii) the metal complex, in combination with a
non-buffering electrolyte, can be the electrolyte; or (iv) the
metal complex, in combination with a non-buffering electrolyte and
an additional non-buffering salt (e.g., sodium chloride and
potassium chloride), can be the electrolyte.
[0059] In some embodiments the substantially aqueous medium has a
pH of from about 1 to about 7 (e.g., about 2 to about 4; about 3 to
about 6; about 2 to about 5; about 3 to about 7; or about 4 to
about 7). In other embodiments, the substantially aqueous medium is
buffered at a pH of between about 1 and about 7 (e.g., about 2 to
about 4; about 3 to about 6; about 2 to about 5; about 3 to about
7; or about 4 to about 7) using an appropriate buffer.
[0060] In some embodiments, the substantially aqueous medium
comprises a water-miscible organic solvent. The water-miscible
organic solvent comprises at least one of an
C.sub.1-C.sub.6-alkanol (ethanol, methanol, 1-propanol, and
2-propanol); a C.sub.2-C.sub.10-polyol (e.g., 1,2-butanediol,
1,3-butanediol, 1,4-butanediol, 1,3-propanediol, 1,5-propanediol,
ethylene glycol, propylene glycol, diethylene glycol, and
glycerol); a (poly)alkylene glycol ether (e.g, glyme and diglyme);
a C.sub.2-C.sub.10-carboxylic acid (e.g., ethanoic acid, acetic
acid, butyric acid, and propanoic acid); a C.sub.2-C.sub.10-ketone
(e.g., acetone, 2-butanone, cyclohexanone, and acetylacetone); a
C.sub.2-C.sub.10-aldehyde (e.g., acetaldehyde); a pyrrolidone
(e.g., N-Methyl-2-pyrrolidone); a C.sub.2-C.sub.10-nitrile (e.g.,
acetonitrile); a phthalate (e.g., di-n-butylphthalate); a
C.sub.2-C.sub.10-dialkylamine (e.g., diethylamine); a
C.sub.2-C.sub.10-dialkylformamide (e.g., dimethylformamide); a
C.sub.2-C.sub.10-dialkyl sulfoxide (dimethyl sulfoxide); a
C.sub.4-C.sub.10-heterocycloalkane (e.g., dioxane and
tetrahydrofuran); aminoalcohols (e.g., aminoethanol); and a
C.sub.4-C.sub.10-heteroarylene (e.g., pyridine).
Substrate
[0061] Embodiments described herein are directed to a method for
the electrodeposition of at least one metal onto a surface of a
conductive substrate.
[0062] As defined herein, the term "substrate" includes any
material with a resistivity of less than 1 .OMEGA.m (at 20.degree.
C.). Some metallic substrates will naturally have such a
resistivity. But the requisite resistivity can be achieved for
non-metallic substrates by methods known in the art. For example,
through doping, as is the case for semi-conductors comprising
primarily of silicon; or by pretreatment of the substrate with an
alternative coating technique to deposit a thin, adherent layer
with a surface resistivity of less than 1 .OMEGA.m, as is the case
for plastics, precoated with a metal such as copper.
[0063] Other substrates include, for example, plastics that are
doped with a carbon material (e.g., carbon nanotubes and graphene)
to the point where they are suitably conductive; and electron
conductive polymers such as polypyrrole and polythiophene.
Applications
[0064] In some embodiments, the methods described herein can be
used to electrodeposit at least one layer (e.g., at least two) of
the at least one (e.g., at least two) metal onto a surface of a
substrate. In some embodiments, each layer can comprise one or more
different metals. In other embodiments, when there are at least two
layers that are electrodeposited, a first layer comprises different
at least one metal relative to the second layer.
[0065] The electrodeposition methods described herein can therefore
be used to in a variety of different applications, including:
electrodesposition of corrosing resistant alloys; generating
biomedical coatings; generating automotive coatings; generating
catalysis coatings; growing refractory material over metallic
substrates (e.g., materials used in kilns, power plants, glass
smelters, steel manufacturing, etc., which would have use for
growing refractory materials on an aluminum oxide layer to generate
a ceramic coating with a metal backing); thermal barrier coatings
for, e.g., gas turbines; water infrastructure coatings, to imbue
the infrastructure with, among other things, resistance to
sulfates, alkaline conditions, and improved corrosion resistance
towards hot water; highway and aerospace infrastructure, to imbue
the infrastructure with improved corrosion against natural
elements, salts, and de-icing fluids); nano-patterning and
applications in electronics and lithography; generating metal
alloys; improve adhesion of, e.g., paint to a surface by creating
hydroxylic functionality on aluminum oxide layers; electro-coat
applications where, for example sharp edges on a metal surface are
first coated with a second metal and the coated metal is
subsequently cationic epoxy electrocoated); creating non-adhesives
substrates by co-depositing nickel-Teflon on a substrate;
generating primer coatings for e-coat applications, as well as
aerospace and automotive coatings; applications in galvanic
corrosions, where dissimilar metals may be in contact; metal
purification; optics and radiator absorbers; light to thermal
conversion devices; heat exchangers; creating coatings comprising
nano- or microparticles of diamond, Teflon.RTM., carbon black,
talc, where the nano- or microparticles are suspended in the
substantially aqueous medium and they would be included in the
plating.
[0066] The term "about" as used herein can allow for a degree of
variability in a value or range, for example, within 10%, within
5%, or within 1% of a stated value or of a stated limit of a
range.
[0067] The term "substantially" as used herein refers to a majority
of, or mostly, as in at least about 50%, 60%, 70%, 80%, 90%, 95%,
96%, 97%, 98%, 99%, 99.5%, 99.9%, 99.99%, or at least about 99.999%
or more.
[0068] Values expressed in a range format should be interpreted in
a flexible manner to include not only the numerical values
explicitly recited as the limits of the range, but also to include
all the individual numerical values or sub-ranges encompassed
within that range as if each numerical value and sub-range were
explicitly recited. For example, a range of "about 0.1% to about
5%" or "about 0.1% to 5%" should be interpreted to include not just
about 0.1% to about 5%, but also the individual values (e.g., 1%,
2%, 3%, and 4%) and the sub-ranges (e.g., 0.1% to 0.5%, 1.1% to
2.2%, 3.3% to 4.4%) within the indicated range. The statement
"about X to Y" has the same meaning as "about X to about Y," unless
indicated otherwise. Likewise, the statement "about X, Y, or about
Z" has the same meaning as "about X, about Y, or about Z," unless
indicated otherwise.
[0069] In this document, the terms "a," "an," or "the" are used to
include one or more than one unless the context clearly dictates
otherwise. The term "or" is used to refer to a nonexclusive "or"
unless otherwise indicated. In addition, it is to be understood
that the phraseology or terminology employed herein, and not
otherwise defined, is for the purpose of description only and not
of limitation. Any use of section headings is intended to aid
reading of the document and is not to be interpreted as limiting.
Further, information that is relevant to a section heading may
occur within or outside of that particular section. Furthermore,
all publications, patents, and patent documents referred to in this
document are incorporated by reference herein in their entirety, as
though individually incorporated by reference. In the event of
inconsistent usages between this document and those documents so
incorporated by reference, the usage in the incorporated reference
should be considered supplementary to that of this document; for
irreconcilable inconsistencies, the usage in this document
controls.
[0070] In the methods described herein, the steps can be carried
out in any order without departing from the principles of the
invention, except when a temporal or operational sequence is
explicitly recited. Furthermore, specified steps can be carried out
concurrently unless explicit claim language recites that they be
carried out separately. For example, a claimed step of doing X and
a claimed step of doing Y can be conducted simultaneously within a
single operation, and the resulting process will fall within the
literal scope of the claimed process.
EXAMPLES
[0071] The examples described herein are intended solely to be
illustrative, rather than predictive, and variations in the
manufacturing and testing procedures can yield different results.
All quantitative values in the Examples section are understood to
be approximate in view of the commonly known tolerances involved in
the procedures used. The foregoing detailed description and
examples have been given for clarity of understanding only. No
unnecessary limitations are to be understood therefrom.
Materials
[0072] Aluminum carbonate (Al.sub.2(CO.sub.3).sub.3, Alfa Aesar);
aluminum chloride (AlCl.sub.3, anhydrous, .gtoreq.98.0%, TCl);
bis(trifluoromethane)sulfonamide (Tf.sub.2NH, .gtoreq.95.0%,
Sigma-Aldrich); methanesulfonic acid (MsOH, 99%, Acros Organics);
p-toluenesulphonic acid (TsOH, monohydrate, 98.5+%, Alfa Aesar);
trifluoromethanesulfonic acid (TfOH, 99%, Oakwood Chemical);
trifluoroacetic acid (TFA, 99%, Alfa Aesar); polyvinyl alcohol
(PVA, average M.sub.w 13000-23000, 98% hydrolyzed, Sigma-Aldrich);
ammonium acetate (CH.sub.3CO.sub.2NH.sub.4, 97%, Alfa Aesar);
ammonium hydroxide solution (NH.sub.4OH, ACS reagent,
Sigma-Aldrich); and citric acid (97%, Alfa Aesar) were used without
further purification.
Example 1
Synthesis of 1 M Al(NTf.sub.2N).sub.3 Aqueous Solution
[0073] To a mixture of Al.sub.2(CO.sub.3).sub.3 (138 g, 0.59 mol, 1
eq) in H.sub.2O (600 mL), HTf.sub.2N aqueous solution (6 eq., 995
g, 3.54 mol; in 300 mL H.sub.2O) was added portion-wise under
magnetic stirring at room temperature. The turbid mixture foamed
and became warm. After 2 h, the mixture was heated at 60.degree. C.
overnight and afforded a transparent light yellow liquid. After the
mixture was cooled down to room temperature, additional H.sub.2O
was added to make the total volume of the mixture 1.2 L.
Example 2
General Procedures for Preparation Aluminum Complex Aqueous
Solutions for Cyclic Voltammetry (CV) Experiments
[0074] To prepare 2 mL aluminum complex aqueous solutions, a
mixture of Al.sub.2(CO.sub.3).sub.3 (0.23 g, 1 mmol) and H.sub.2O
(0.5 mL) was stirred at room temperature. Organic acid (6 or 12
mmol; 3 or 6 eq. to Al, see Table 1) was added slowly into the
mixture and yielded a turbid aqueous mixture. After stirring for
another 1 hour, the mixture was heated to approximately 60.degree.
C. overnight and give a clear liquid. After the mixture was cooled
to room temperature, H.sub.2O was added to adjust the solution to
certain molarity (0.5 or 1 M, see Table 1).
TABLE-US-00001 TABLE 1 Organic acid used (ligand) Reduction
Compound in to Al Aluminum onset Compound abbreviation synthesis
ratio Molarity/M pH potential/V Aluminum chloride AlCl.sub.3 N/A
3:1 1 2.04 -1.67 Aluminum Al(Tf.sub.2N).sub.3 Tf.sub.2NH 3:1 1 1.91
-1.10 bis(trifluoromethane)sulfonimide Al(Tf.sub.2N).sub.1 1:1 1
3.30 -1.20 Aluminum methanesulfonate Al(MS).sub.3 MsOH 3:1 1 2.47
-0.84 Al(MS).sub.6 6:1 1 1.00 -1.11 Al(MS).sub.1 1:1 3 3.15 -1.12
Aluminum p- Al(OTs).sub.3 TsOH 3:1 1 2.36 -1.13 toluenesulphonate
Al(OTs).sub.6 6:1 0.5 0.24 -0.93 Al(OTs).sub.6 6:1 0.5 1.35 -1.17
Aluminum Al(OTf).sub.6 TfOH 6:1 1 2.82 -1.35
trifluoromethanesulfonate Aluminum trifluoroacetate Al(TFA).sub.3
TFA 3:1 0.5 3.17 -1.10 Al(TFA).sub.6 6:1 0.5 0.78 only gas
evolution Al(TFA).sub.6 6:1 0.5 1.18 -1.07 Al(TFA).sub.6 6:1 0.5
3.34 -1.32
TABLE-US-00002 TABLE 2 pKa in Ligand Structure water
bis(trifluoromethane) sulfonamide(Tf.sub.2N) ##STR00008## Too
negative to measure p-Toluenesulfonate (p-TSA) ##STR00009## -2.14
Methanesulfonate (MSO) ##STR00010## -1.61 Triflate (TfO)
##STR00011## -3.43 Trifluoroacetate (TFA) ##STR00012## 0.52
Example 3
Hull Cell Experiments
Aluminum Plating Experiment 1
[0075] An example of the aluminum plating process used 0.3 M
Al(Tf.sub.2N).sub.3 in water with an additional electrolyte of 1 M
ammonium acetate. An additive of 0.5 wt % PVA was added. A hull
cell plating was conducted using 100 mL of the solution at 0.5 A
for 30 mins giving a powdery deposit at the high current density
end, no plating at the low current density end and a smooth,
reflective, metallic coating between 40 A/dm.sup.2 and 150
A/dm.sup.2. The pH of the plating solution was buffered between 4.8
and 5.0, and a temperature of 40.degree. C. The solution is found
to contain some dark colored precipitate and a large amount of
foaming, post electrolysis. A dark, metallic deposit of smooth
reflective aluminum is shown by scanning electron microscopy (SEM)
and energy-dispersive X-ray (EDX) spectroscopy analysis. See, e.g.,
FIG. 5.
Aluminum Plating Experiment 2
[0076] An additional example of the aluminum plating process used
0.3 M Al(Tf.sub.2N).sub.3 in water with an additional electrolyte
of 1 M ammonium citrate which was titrated from 1M citric acid with
NH.sub.4OH. An additive of 0.5 wt % PVA was added. A hull cell
plating was conducted using 100 mL of the solution at 0.5 A for 30
mins giving a thicker and darker deposit at the high current
density end (above 40 A/dm.sup.2), no plating at the low current
density end (below 40 A/dm2). The coating was thickest at the high
current density end and appeared shiny and metallic. The pH of the
plating solution was buffered between 2.8 and 3.2, and a
temperature of 40.degree. C. The solution is found to contain less
dark colored precipitate but no foaming was seen in this case, post
electrolysis. A thin, dark, metallic deposit of smooth reflective
aluminum is shown by SEM and EDX analysis, with a clear deposition
gradient from high to low current density.
Example 4
Small Scale Electroplating of High Purity Aluminum from
Al(OMs)/NH.sub.4 Citrate on a Curved Geometry
[0077] Using a 10 mL test aliquot of 0.5 M Al(OMs) and 1 M ammonium
citrate with aluminum to ligand ratio of 1:1, a 20 AWG copper wire
was successfully plated to a thickness in excess of 10 .mu.m. The
procedure used a two electrode system with a copper wire (20 AWG, 6
mm length) as the cathode substrate and an aluminum
counter/reference electrode. Chronopotentiometry was carried out at
-20 mA (-120 mAcm.sup.-2) for 3 hours (FIG. 5). The temperature of
the bath was controlled and maintained at 54.degree. C.
throughout.
Example 5
[0078] A range of aluminum salts with various ligand structures
have been developed (see Table 2). The ligands are generally
considered as mono-dentate, with the exception of Tf.sub.2N which
is more likely a bidentate ligand. Each ligand is considered as
electron withdrawing in nature to varying degrees. While not being
bound by any specific theory, it is believed that this electron
withdrawing character is likely to shift the reduction potential of
aluminum (or any other metal described herein) with the most
strongly electron withdrawing substituents leading to a shift
towards less negative potentials. FIG. 2 shows the comparative
electron withdrawing character of each substituent as estimated
from the pKa of the acid. Generally speaking, stronger acids are
more able to stabilize the deprotonated form of the acid leading to
lower pKas.
[0079] In order to test the effect of various electron withdrawing
substituents on the standard reduction potential of aluminum
complexes a series of cyclic voltammetry experiments were carried
out. Each salt was synthesized in situ by combination of various
acids with aluminum carbonate in water to make a 1 M solution of
each salt. In order to limit ligand substitution and complexation,
no other electrolyte was added into the solution. Each cyclic
voltammogram was collected vs. Ag/AgCl (3 M NaCl) and used an
aluminum counter electrode. The working electrode was chosen as
glassy carbon to limit the hydrogen evolution reaction which would
ordinarily obscure the aluminum reduction for some salts.
[0080] As a control case 1 M AlCl.sub.3 was used to gauge the
effectiveness of the electron withdrawing substituents. It was
expected that for aluminum chloride it is likely that the
electroactive species is of an aqueous aluminum hydroxide complex
(Al[H.sub.2O].sub.5OH), which forms rapidly upon AlCl.sub.3
exposure to excess water. This aluminum complex was initially
compared to Al(Tf.sub.2N).sub.3 (FIG. 2) and it was found that the
electron withdrawing Tf.sub.2N ligands had a significant effect on
the cathodic reduction process. The onset potential was shifted
from about -1.65 V to about -1.1 V. While not being bound by any
particular theory, it is believed that this shift in reduction
potential shows that the aluminum species may be in a different
form from the AlCl.sub.3 case and does not simply become a water
hydroxide complex. This might suggest that the ligand structure
might be substantially retained in water and remains stable in
solution for months. This development in aqueous aluminum
complexation and comparative ease of electroreduction allows for
greater competition of aluminum reduction with hydronium reduction
on metal substrates, thus opening an aqueous aluminum plating
procedure. Further evidence that aluminum electroplating is
possible in this system comes from the presence of a nucleation
loop in a reverse scan. This suggests a nucleation event occurs on
the cathodic wave, likely the surface adsorption of a reduced
aluminum species.
[0081] Additional salts (see Table 2) have been tested in a similar
procedure with some salts showing similar promise for aluminum
reduction. Other ligands were tested in a 1:1, 1:3 and 1:6 ratio of
aluminum to ligand to test the effect of a 6 coordinate complex vs.
a 1 or 3 coordinate complex. In the case of a hexa-coordinate
aluminum species, an additional effect was that excess acid caused
the pH to be reduced significantly.
[0082] When p-TSA is used as the ligand in both a 1:4 and 1:6 ratio
with Al.sup.3+ a systematic shift is seen towards more positive
reduction potentials. As the solution becomes more acidic, it would
be expected that hydronium reduction would become more prevalent at
more positive potentials. In the case of 6 M unbound p-TSA (FIG. 3
scan (i)) a solvent reduction wave is visualized with a low onset
and no mass transport limiting peak. When the same amount of p-TSA
is used in a 1:6 molar ratio with aluminum a similar onset is seen
(FIG. 3 scan (ii)) but now a peak emerges which, when compared with
Al(Tf.sub.2N).sub.3 may be attributed to an Al.sup.3+ reduction
event from a p-TSA rich complex. In a 1:4 ratio with aluminum (FIG.
3 scan (iii)), a more negative onset and peak is seen as well as
larger resistance. This discrepancy may be explained in part by pH
shift since it would be expected that the excess acid would lead to
a dramatic reduction in solution pH. Indeed, the pH of the 1:6
solution is about 0.24 and may explain the early onset of hydronium
reduction. When the pH of this solution was adjusted by addition of
ammonium hydroxide to pH 1.35 the redox behavior is identical to
that of the 1:4 solution (FIG. 3, scans (iii) and (iv)). This
behavior shows that the redox process is the same in both cases and
that the aluminum coordination is likely by 1-4 p-TSA, is stable in
acidic media and has a lower reduction potential than
Al(H.sub.2O)OH.sup.2+.
[0083] Methanesulfonate (MS) is a comparable ligand to p-TSA,
showing highly electron withdrawing character but is sterically
much smaller, which may be expected to facilitate a hexa-coordinate
aluminum species. It is found that both the 1:1 and 6:1 ligand to
aluminum ratio cases have very similar onsets for aluminum
reduction of ca. -1.1V. However the 3:1 case shows an onset of only
-0.84 V. This suggests that a maximized effect for electron
withdrawing ligands is found for this ratio with lower coordination
(1:1) being very similar in onset to other tested ligands and 6:1
having an excess of acid and ligands. The 3:1 case also has a pH of
only 2.47 suggesting that a lot of the expected free protons are
lost upon reaction with the carbonate and the ligands are likely
coordinated rather than the aluminum complex leading to a high
hydronium ion concentration.
[0084] Triflate (TfO) showed very little evidence of ligation to
aluminum with a 6:1 ratio of acid showing a highly acidic
environment with a pH of 0. This suggests that the majority of the
acid remains free and is not involved in the anticipated carbonate
displacement reaction and leads to almost no aluminum ligation.
This hypothesis is corroborated by the relatively negative
reduction potential compared to other ligands of -1.35 V.
[0085] The final ligand Trifluoroacetate (TFA) was different from
the others by way of a coordinating acetate anion rather than a
sulfonate. For the case of a 1:3 complex for aluminum to TFA, a
similar character was seen to that of both p-TSA and TfO with an
onset potential of ca -1.10 V and a resistive peak being found,
suggesting very few charge carriers being available. With a 1:6
ratio of aluminum to TFA a much lower onset potential was found
although it is highly likely that the majority of this process was
proton reduction with no clear aluminum onset being detectable.
When the pH was adjusted for the 1:6 solution to make it most
similar to that of the 1:3 a much higher onset potential was found.
This suggests a different reductive aluminum species as compared to
the 1:3 case, although the reduction was also not similar in
character to that of Al(H.sub.2O).sub.5OH and thus it must be
determined that TFA is able to at least partially coordinate to the
aluminum center and affect its electronegativity.
[0086] In summary, Al(MS).sub.3 shows the lowest recorded potential
for Al.sup.3+ reduction below that for hydronium reduction with an
onset of about -0.84 V and a peak at about -1.3 V. See, e.g., FIG.
4. Hydrogen generation is obvious at the higher limit of this
voltage range but an appreciable current for aluminum reduction is
established prior to the evolution of gas. Other ligands p-TSA and
Tf.sub.2N show a comparable lowered reduction potential although
slightly more negative than MS. It is unclear what the coordination
for the p-TSA ligand is to aluminum, and is likely to be able to
coordinate at least three p-TSA ligands. This coordination is
sufficient to substantially lower the reduction potential of
Al.sup.3+ and is visible proceeding hydronium reduction at pHs as
low as 1.35. TfO however, seems to be unstable in the presence of
NH.sub.4.sup.+ and is likely not strongly coordinating, with a
redox process most similar to that of the water hydrated aluminum
species. TFA appears to be an intermediate case whereby a lower
coordination number may be possible in conjunction with some
hydration. A slightly improved reduction potential is recorded,
although not sufficient to compete with either Tf.sub.2N or
p-TSA.
[0087] It will be apparent to those skilled in the art that the
specific structures, features, details, configurations, etc., that
are disclosed herein are simply examples that can be modified
and/or combined in numerous embodiments. All such variations and
combinations are contemplated by the inventor as being within the
bounds of this disclosure. Thus, the scope of the disclosure should
not be limited to the specific illustrative structures described
herein, but rather extends at least to the structures described by
the language of the claims, and the equivalents of those
structures. To the extent that there is a conflict or discrepancy
between this specification as written and the disclosure in any
document incorporated by reference herein, this specification as
written will control.
[0088] The present invention provides for the following exemplary
embodiments, the numbering of which is not to be construed as
designating levels of importance:
[0089] Embodiment 1 relates to a method for the electrodeposition
of at least one metal onto a surface of a conductive substrate at a
temperature from about 10.degree. C. to about 70.degree. C., about
0.5 atm to about 5 atm, in an atmosphere comprising oxygen, the
method comprising electrodepositing the at least one metal via
electrochemical reduction of a metal complex dissolved in a
substantially aqueous medium.
[0090] Embodiment 2 relates to the method of Embodiment 1, wherein
the metal comprises at least one of reactive and non-reactive
metals.
[0091] Embodiment 3 relates to the method of Embodiment 2, wherein
the reactive metal comprises at least one of aluminum, titanium,
manganese, gallium, vanadium, zinc, zirconium, and niobium.
[0092] Embodiment 4 relates to the method of Embodiment 2, wherein
the non-reactive metal comprises at least one of tin, gold, copper,
silver, rhodium, and platinum.
[0093] Embodiment 5 relates to the method of Embodiments 1-4,
wherein the metal complex comprises a metal center and ligands,
wherein at least one of the ligands is an electron withdrawing
ligand
[0094] Embodiment 6 relates to the method of Embodiment 5, wherein
the ligands are sufficiently electron withdrawing such that the
reduction potential of the metal in the metal complex is decreased
below the over-potential for the evolution of hydrogen gas due to
water splitting.
[0095] Embodiment 7 relates to the method of Embodiments 5-6,
wherein the ligands are at least one of sulfonate ligands and
sulfonimide ligands.
[0096] Embodiment 8 relates to the method of Embodiment 7, wherein
the at least one sulfonate ligands is a ligand of the formula
SO.sub.3R.sup.1, wherein R.sup.1 is halo; substituted or
unsubstituted C.sub.6-C.sub.18-aryl; substituted or unsubstituted
C.sub.1-C.sub.6-alkyl; substituted or unsubstituted
C.sub.6-C.sub.18-aryl-C.sub.1-C.sub.6-alkyl.
[0097] Embodiment 9 relates to the method of Embodiment 7, wherein
the at least one sulfonimide ligand is a ligand of the formula
N(SO.sub.3R.sup.1), wherein R.sup.1 is wherein R.sup.1 is halo;
substituted or unsubstituted C.sub.6-C.sub.18-aryl; substituted or
unsubstituted C.sub.1-C.sub.6-alkyl; substituted or unsubstituted
C.sub.6-C.sub.18-aryl-C.sub.1-C.sub.6-alkyl.
[0098] Embodiment 10 relates to the method of Embodiment 7-9,
wherein the at least one sulfonate ligand comprises a sulfonate
ligand of the formulae:
##STR00013##
[0099] Embodiment 11 relates to the method of Embodiment 7, wherein
the at least one sulfonimide ligand comprises a sulfonimide ligand
of the formula:
##STR00014##
[0100] Embodiment 12 relates to the method of Embodiments 1-11,
wherein the metal complex is at least one metal complex of the
formula Al(SO.sub.3R.sup.1).sub.n, wherein R.sup.1 is halo;
substituted or unsubstituted C.sub.6-C.sub.18-aryl; substituted or
unsubstituted C.sub.1-C.sub.6-alkyl; substituted or unsubstituted
C.sub.6-C.sub.18-aryl-C.sub.1-C.sub.6-alkyl; n is an integer from 2
to 8; and Al[N(SO.sub.3R.sup.1).sub.2].sub.n, wherein R.sup.1 is
halo; substituted or unsubstituted C.sub.6-C.sub.18-aryl;
substituted or unsubstituted C.sub.1-C.sub.6-alkyl; substituted or
unsubstituted C.sub.6-C.sub.18-aryl-C.sub.1-C.sub.6-alkyl; and n is
an integer from 1 to 4.
[0101] Embodiment 13 relates to the method of Embodiments 1-12,
wherein the substantially aqueous medium comprises an
electrolyte.
[0102] Embodiment 14 relates to the method of Embodiment 13,
wherein the electrolyte comprises at least one of a halide
electrolyte; a perchlorate electrolyte; an amidosulfonate
electrolyte; hexafluorosilicate electrolyte; a tetrafluoroborate
electrolyte; methanesulfonate electrolyte; and a carboxylate
electrolyte.
[0103] Embodiment 15 relates to the method of Embodiments 13-14,
wherein the electrolyte comprises at least one of compounds of the
formula R.sup.3CO.sub.2.sup.-, wherein R.sup.3 is substituted or
unsubstituted C.sub.6-C.sub.18-aryl; or substituted or
unsubstituted C.sub.1-C.sub.6-alkyl;
[0104] Embodiment 16 relates to the method of Embodiments 13-15,
wherein the electrolyte comprises at least one of polycarboxylates;
and lactones.
[0105] Embodiment 17 relates to the method of Embodiments 1-16,
wherein the pH of the substantially aqueous medium is buffered at a
pH of about 1 and about 7.
[0106] Embodiment 18 relates to the method of Embodiments 1-17,
wherein the substantially aqueous medium comprises a water-miscible
organic solvent.
[0107] Embodiment 19 relates to the method of Embodiment 18,
wherein the water-miscible organic solvent comprises at least one
of an C.sub.1-C.sub.6-alkanol, a C.sub.2-C.sub.10-polyol, a
(poly)alkylene glycol ether, a C.sub.2-C.sub.10-carboxylic acid; a
C.sub.2-C.sub.10-ketone; a C.sub.2-C.sub.10-aldehyde; a
pyrrolidone; a C.sub.2-C.sub.10-nitrile; a phthalate; a
C.sub.2-C.sub.10-dialkylamine; a C.sub.2-C.sub.10-dialkylformamide;
a C.sub.2-C.sub.10-dialkyl sulfoxide; a
C.sub.4-C.sub.10-heterocycloalkane; an aminoalcohol; and a
C.sub.4-C.sub.10-heteroarylene.
[0108] Embodiment 20 relates to the method of Embodiment 19,
wherein the C.sub.1-C.sub.6-alkanol comprises ethanol.
[0109] Embodiment 21 relates to the method of Embodiments 1-,
wherein the electrodepositing comprises electrodepositing at least
one layer of the at least one metal onto a surface of the
substrate.
[0110] Embodiment 22 relates to the method of Embodiments 1-21,
wherein the electrodepositing comprises electrodepositing at least
two layers of the at least one metal onto a surface of the
substrate.
[0111] Embodiment 23 relates to the method of Embodiment 22,
wherein the first layer comprises different at least one metal
relative to the second layer.
* * * * *