U.S. patent application number 16/336816 was filed with the patent office on 2019-07-11 for contamination-preventing agent composition and contamination preventing method.
The applicant listed for this patent is MAINTECH CO., LTD.. Invention is credited to Daisuke KOBAYASHI, Hiraku SAWADA, Hiroshi SEKIYA, Kazuyuki YUSA.
Application Number | 20190211504 16/336816 |
Document ID | / |
Family ID | 58043260 |
Filed Date | 2019-07-11 |

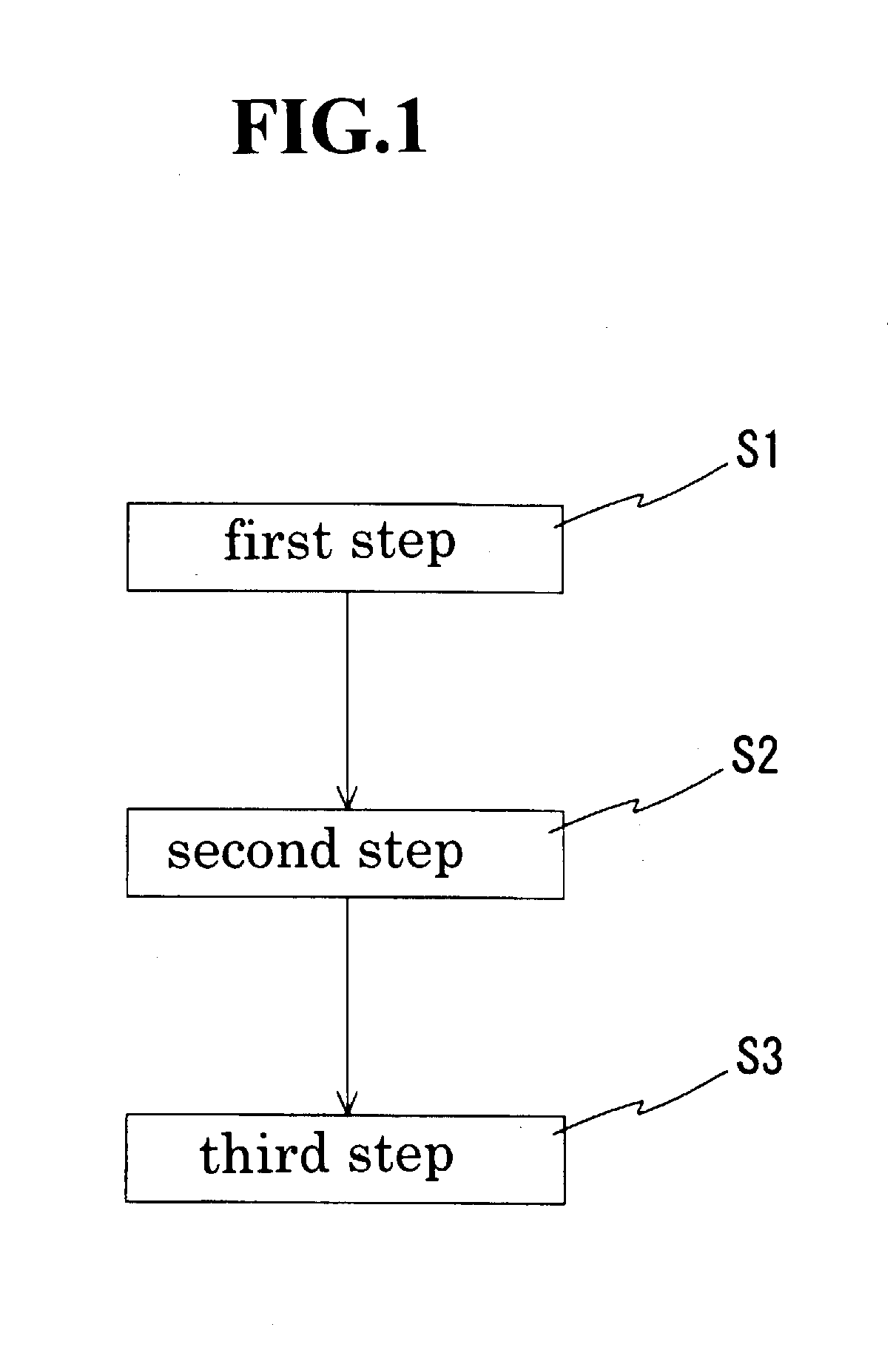


United States Patent
Application |
20190211504 |
Kind Code |
A1 |
SEKIYA; Hiroshi ; et
al. |
July 11, 2019 |
CONTAMINATION-PREVENTING AGENT COMPOSITION AND CONTAMINATION
PREVENTING METHOD
Abstract
To provide a contamination-preventing agent composition and a
contamination preventing method which even if the composition is
imparted only to a dryer on the upstream side, a sufficient amount
of the composition can be imparted to a dryer on the downstream
side via a wet paper, and pitch contamination of a plurality of
dryers can be prevented sufficiently as a whole. The present
invention is a contamination-preventing agent composition imparted
to dryers D1 to D8 in a dry part D of a paper machine and
comprising an emulsion, a re-transfer agent and water, wherein the
re-transfer agent has a cloud point of 55.degree. C. or higher and
an HLB value of 8 to 15, and preferably a contamination-preventing
agent composition wherein the dynamic surface tension value at a
lifetime of 100 ms by a maximum bubble pressure method is 65 mN/m
or less.
Inventors: |
SEKIYA; Hiroshi; (Tokyo,
JP) ; KOBAYASHI; Daisuke; (Tokyo, JP) ;
SAWADA; Hiraku; (Fuji-shi, Shizuoka, JP) ; YUSA;
Kazuyuki; (Fuji-shi, Shizuoka, JP) |
|
Applicant: |
Name |
City |
State |
Country |
Type |
MAINTECH CO., LTD. |
Tokyo |
|
JP |
|
|
Family ID: |
58043260 |
Appl. No.: |
16/336816 |
Filed: |
September 29, 2016 |
PCT Filed: |
September 29, 2016 |
PCT NO: |
PCT/JP2016/004406 |
371 Date: |
March 26, 2019 |
Current U.S.
Class: |
1/1 |
Current CPC
Class: |
D21H 21/02 20130101;
D21H 17/06 20130101; D21H 17/33 20130101; D21F 5/00 20130101; D21F
5/022 20130101; D21F 1/32 20130101; D21F 5/04 20130101; D21H 17/14
20130101 |
International
Class: |
D21F 5/02 20060101
D21F005/02; D21F 5/04 20060101 D21F005/04; D21F 1/32 20060101
D21F001/32 |
Claims
1. A contamination-preventing agent composition imparted to a dryer
in a dry part of a paper machine and comprising an emulsion, a
re-transfer agent and water, wherein said re-transfer agent has a
cloud point of 55.degree. C. or higher and an HLB value of 8 to
15.
2. The contamination-preventing agent composition according to
claim 1, wherein the dynamic surface tension value at a lifetime of
100 ms by a maximum bubble pressure method is 65 mN/m or less.
3. The contamination-preventing agent composition according to
claim 1, wherein said dryer is made of cast iron, and the contact
angle to the cast iron is 70.degree. or less.
4. The contamination-preventing agent composition according to
claim 1, wherein said re-transfer agent is at least one selected
from the group consisting of polyoxyalkylene alkyl ether,
polyoxyalkylene fatty acid ester, polyoxyalkylene sorbitan fatty
acid ester and polyoxyalkylene sorbitol fatty acid ester.
5. The contamination-preventing agent composition according to
claim 1, wherein said emulsion is composed of a non-silicone oil,
water and an emulsifier, and said non-silicone oil is at least one
selected from the group consisting of polybutenes, synthetic ester
oils, mineral oils, vegetable oils and liquid paraffins.
6. The contamination-preventing agent composition according to
claim 5, wherein the compounding ratio of said re-transfer agent
with respect to 10% by mass of said non-silicone oil is 0.1% by
mass to 10% by mass.
7. The contamination-preventing agent composition according to
claim 1, wherein the compounding ratio of said re-transfer agent is
0.01% by mass to 10% by mass.
8. The contamination-preventing agent composition according to
claim 1, wherein a coating film is formed by being imparted to said
dryer, and a part of said coating film is re-emulsified when the
coating film comes in contact with a wet paper.
9. A contamination preventing method, comprising a first step of
imparting the contamination-preventing agent composition according
to claim 1 to a dryer on the upstream side to form a coating film,
a second step of bringing a wet paper into contact with the coating
film to re-emulsify a part of the coating film and transfer the
re-emulsified emulsion to the wet paper, and a third step of
bringing said wet paper carrying said emulsion into contact with a
dryer on the downstream side to impart said emulsion to the dryer
on the downstream side.
Description
TECHNICAL FIELD
[0001] The present invention relates to a contamination-preventing
agent composition and a contamination preventing method, and more
particularly to a contamination-preventing agent composition and a
contamination preventing method capable of preventing pitch
contamination of a plurality of dryers in a dry part of a paper
machine.
BACKGROUND ART
[0002] A paper making process in a paper machine generally has a
wire part in which a liquid in which pulp is dispersed in water is
placed on a mesh (wire) for papermaking and excess water is
naturally dropped to obtain a wet paper, a press part for
transferring moisture in the wet paper to a felt by passing the wet
paper between a pair of press rolls and pressing it by the press
rolls via the felt, thereby dewatering the wet paper, a dry part
for drying the paper by contacting the wet paper which has passed
through the press part with a plurality of heated driers, to obtain
a paper, and a reel part for winding the paper on a bar called a
spool.
[0003] In the above-mentioned dry part, there is a problem that the
pitch sticks to the surface of a dryer. If the pitch sticks to the
dryer, a wet paper is contaminated, and the yield thereof is
significantly reduced.
[0004] On the other hand, a silicone-based contamination-preventing
agent composition and a non-silicone contamination-preventing agent
composition are known as a contamination-preventing agent
composition for preventing pitch contamination in a dry part of a
paper making process.
[0005] For example, as the silicone-based contamination-preventing
agent composition, a contamination-preventing agent composition
containing a polysiloxane compound having a predetermined chemical
structural formula and having from 0.5 to 5 amino-modified groups
per molecule of the polysiloxane compound is known (see, e.g.,
Patent Document 1).
[0006] Further, as the non-silicone contamination-preventing agent
composition, a contamination-preventing agent composition
containing a non-silicone oil and an emulsifier for emulsifying the
non-silicone oil, wherein the emulsifier is a neutralized product
of a fatty acid and an amine compound is known (see, e.g., Patent
Document 2).
[0007] However, with these contamination-preventing agent
compositions, although it is possible to prevent the pitch
contamination of a dryer on the upstream side to which the
contamination-preventing agent composition is imparted, it is
impossible to sufficiently prevent the pitch contamination of a
dryer on the downstream side only by itself. For this reason, it is
necessary to impart a contamination-preventing agent composition to
each of a plurality of dryers.
[0008] In the present specification, "dryer on the upstream side"
means a dryer positioned upstream with respect to traveling of a
wet paper, and "dryer on the downstream side" means a dryer
positioned downstream with respect to traveling of a wet paper.
[0009] In contrast, there is known a contamination-preventing agent
composition containing a low molecular polysiloxane compound having
a predetermined chemical structural formula and a polymer
polysiloxane compound having a predetermined chemical structural
formula, wherein the kinematic viscosity of the low molecular
polysiloxane compound at 25.degree. C. is 10 to 300 mm.sup.2/s, the
kinematic viscosity of the polymer polysiloxane compound at
25.degree. C. is 40 to 90,000 mm.sup.2/s, the number of modified
groups per molecule of the low molecular polysiloxane compound is
from 0.1 to 3.0, the number of modified groups per molecule of the
polymer polysiloxane compound is 1.0 to 10, and the repeating
number m of the polysiloxane unit in the low molecular polysiloxane
compound and the repeating number n of the polysiloxane unit in the
polymer polysiloxane compound satisfy the relationship of 2
m.ltoreq.n (see, e.g., Patent Document 3).
[0010] In such a contamination-preventing agent composition, the
polymer polysiloxane compound forms a coating film on a dryer on
the upstream side, while the low molecular polysiloxane compound
transfers to a wet paper and is carried by the wet paper, and the
low-molecular polysiloxane compound is re-transferred to a dryer on
the downstream side to which the wet paper is guided, hence, pitch
contamination of a plurality of dryers can be prevented as a
whole.
CITATION LIST
Patent Literature
[0011] PTL 1: Japanese Patent No. 4868628
[0012] PTL 2: Japanese Patent No. 4828001
[0013] PTL 3: Japanese Patent No. 4868629
SUMMARY OF INVENTION
Technical Problem
[0014] However, with the contamination-preventing agent composition
in the above Patent Document 3, it is possible to prevent pitch
contamination of a plurality of dryers as a whole, but particularly
in a dryer on the downstream side, it cannot be said that pitch
contamination can be sufficiently prevented.
[0015] That is, with the contamination-preventing agent composition
in the above Patent Document 3, the polymer polysiloxane compound
to form a coating film is not transferred to the wet paper, and
only the low molecular polysiloxane compound is transferred to the
wet paper, hence, there is a disadvantage that the amount of
re-transfer to the wet paper (hereinafter referred to as "pick-up
amount.") is small, and sufficient amount cannot be imparted to a
dryer on the downstream side.
[0016] In addition, since the coating film composed of the
low-molecular polysiloxane compound is extremely weak and easily
re-transferred, there is also a disadvantage that even if it is
imparted to a dryer on the downstream side, it is re-transferred
again and it is hard to remain on the dryer.
[0017] The present invention has been made in view of the above
circumstances, and has an object of providing a
contamination-preventing agent composition and a contamination
preventing method which even if the composition is imparted only to
a dryer on the upstream side, a sufficient amount of the
composition can be imparted to a dryer on the downstream side via a
wet paper, and pitch contamination of a plurality of dryers can be
prevented sufficiently as a whole.
Solution to Problems
[0018] The present inventors have intensively studied to solve the
above-described problem and resultantly found that the
above-described problem can be solved by allowing the
contamination-preventing agent composition to have a constitution
containing a re-transfer agent having predetermined physical
properties, leading to completion of the present invention.
[0019] The present invention is (1) a contamination-preventing
agent composition imparted to a dryer in a dry part of a paper
machine and comprising an emulsion, a re-transfer agent and water,
wherein the re-transfer agent has a cloud point of 55.degree. C. or
higher and an HLB value of 8 to 15.
[0020] The present invention is (2) the contamination-preventing
agent composition according to (1), wherein the dynamic surface
tension value at a lifetime of 100 ms by a maximum bubble pressure
method is 65 mN/m or less.
[0021] The present invention is (3) the contamination-preventing
agent composition according to (1) or (2), wherein the dryer is
made of cast iron, and the contact angle to the cast iron is
70.degree. or less.
[0022] The present invention is (4) the contamination-preventing
agent composition according to any one of (1) to (3), wherein the
re-transfer agent is at least one selected from the group
consisting of polyoxyalkylene alkyl ether, polyoxyalkylene fatty
acid ester, polyoxyalkylene sorbitan fatty acid ester and
polyoxyalkylene sorbitol fatty acid ester.
[0023] The present invention is (5) the contamination-preventing
agent composition according to any one of (1) to (4), wherein the
emulsion is composed of a non-silicone oil, water and an
emulsifier, and the non-silicone oil is at least one selected from
the group consisting of polybutenes, synthetic ester oils, mineral
oils, vegetable oils and liquid paraffins.
[0024] The present invention is (6) the contamination-preventing
agent composition according to (5), wherein the compounding ratio
of the re-transfer agent with respect to 10% by mass of the
non-silicone oil is 0.1% by mass to 10% by mass.
[0025] The present invention is (7) the contamination-preventing
agent composition according to any one of (1) to (6), wherein the
compounding ratio of the re-transfer agent is 0.01% by mass to 10%
by mass.
[0026] The present invention is (8) the contamination-preventing
agent composition according to any one of (1) to (7), wherein a
coating film is formed by being imparted to the dryer, and a part
of the coating film is re-emulsified when the coating film comes in
contact with a wet paper.
[0027] The present invention is (9) a contamination preventing
method, comprising a first step of imparting the
contamination-preventing agent composition according to any one of
claims (1) to (7) to a dryer on the upstream side to form a coating
film, a second step of bringing a wet paper into contact with the
coating film to re-emulsify a part of the coating film and transfer
the re-emulsified emulsion to the wet paper, and a third step of
bringing the wet paper carrying the emulsion into contact with a
dryer on the downstream side to impart the emulsion to the
downstream dryer.
Advantageous Effects of Invention
[0028] With the contamination-preventing agent composition of the
present invention, moisture is removed by drying of the emulsion to
form a coating film, and then a moisture-containing wet paper comes
into contact with the film, whereby a part of the coating film is
re-emulsified.
[0029] At this time, since the coating film contains a re-transfer
agent for promoting re-transfer, the re-emulsified
contamination-preventing agent composition will promptly
re-transfer to the wet paper.
[0030] Here, by using a re-transfer agent having a cloud point of
55.degree. C. or higher, when the contamination-preventing agent
composition containing a re-transfer agent forms a coating film on
a dryer, re-transfer of the contamination-preventing agent
composition to the wet paper can be promoted without losing the
active performance of the re-transfer agent even during heating
with the dryer. The temperature of the dryer is generally
55.degree. C. or higher.
[0031] By using a re-transfer agent having an HLB value of 8 to 15,
it is possible to effectively activate the interface between water
and the coating film and promote re-emulsification.
[0032] It is preferable that the compounding ratio of the
re-transfer agent is 0.01% by mass to 10% by mass based on the
total amount.
[0033] For these reasons, by using a re-transfer agent having a
cloud point of 55.degree. C. or higher and an HLB value of 8-15,
the pick-up amount of the emulsion obtained by re-emulsification of
the coating film onto the wet paper can be improved.
[0034] Therefore, for example, if a contamination-preventing agent
composition is given to a dryer at the most upstream side with
respect to traveling of the wet paper, it is possible to impart a
sufficient amount even to a dryer on the downstream side via the
wet paper.
[0035] As a result, it is possible to prevent pitch contamination
as a whole for a plurality of dryers.
[0036] For the contamination-preventing agent composition of the
present invention, the speed of movement to the interface between
the coating film and the wet paper can be made faster by setting
the dynamic surface tension value at a lifetime of 100 ms according
to the maximum bubble pressure method to 65 mN/m or less.
[0037] That is, in the paper machine, it is a very short time from
imparting of the contamination-preventing agent composition to a
dryer until the dryer comes into contact with a wet paper, and by
setting the dynamic surface tension value within the above range,
it becomes possible to promptly exert the function of the
re-transfer agent of re-emulsifying the coating film.
[0038] In the contamination-preventing agent composition of the
present invention, the dryer is made of cast iron, and the contact
angle to the cast iron is 70.degree. or less, accordingly, the
emulsion easily forms a coating film along the surface of the
drier.
[0039] In the contamination-preventing agent composition of the
present invention, the effect of re-emulsification can be exerted
surely when the re-transfer agent is at least one selected from the
group consisting of polyoxyalkylene alkyl ether, polyoxyalkylene
fatty acid ester, polyoxyalkylene sorbitan fatty acid ester and
polyoxyalkylene sorbitol fatty acid ester.
[0040] In the contamination-preventing agent composition of the
present invention, when the emulsion is composed of a non-silicone
oil, water and an emulsifier, the compounding ratio of the
re-transfer agent with respect to 10% by mass of the non-silicone
oil is 0.1% by mass to 10% by mass.
[0041] When the non-silicone oil is at least one selected from the
group consisting of polybutenes, synthetic ester oils, mineral
oils, vegetable oils and liquid paraffins, a coating film can be
easily formed on the dryer, re-emulsification is easily performed,
and pitch contamination can be surely prevented.
[0042] In the case where the contamination-preventing agent
composition of the present invention forms a coating film by being
imparted to a dryer and a part of the coating film is re-emulsified
with a re-transfer agent by contact of the coating film with a wet
paper, even if the composition is imparted only to a dryer on the
upstream side, a sufficient amount of the composition can be
imparted to a dryer on the downstream side via the wet paper, and
pitch contamination of a plurality of dryers can be prevented
sufficiently as a whole.
[0043] In the contamination preventing method of the present
invention, pitch contamination of a plurality of dryers can be
prevented sufficiently as a whole via a first step, a second step
and a third step by using the contamination-preventing agent
composition described above.
BRIEF DESCRIPTION OF DRAWINGS
[0044] FIG. 1 is a flowchart showing a contamination preventing
method using a contamination-preventing agent composition according
to the present embodiment.
[0045] FIG. 2 is an explanatory diagram for explaining a
contamination preventing method according to the present
embodiment.
[0046] FIG. 3 is a schematic diagram showing a dryer using a
contamination-preventing agent composition according to the present
embodiment.
DESCRIPTION OF EMBODIMENTS
[0047] Hereinafter, preferred embodiments of the present invention
will be described in detail with reference to the drawings as
necessary. The positional relationship such as up, down, left and
right are based on the positional relationship shown in the drawing
unless otherwise noted. Further, the dimensional ratios of the
drawings are not limited to the illustrated ratios.
[0048] The contamination-preventing agent composition according to
the present embodiment can prevent pitch contamination of a dryer
by being imparted to the dryer in a dry part of a paper
machine.
[0049] Specifically, even if the composition is imparted only to a
dryer on the upstream side, a sufficient amount can be imparted to
a dryer on the downstream side via a wet paper. As a result, pitch
contamination can be sufficiently prevented for a plurality of
dryers as a whole.
[0050] With the contamination-preventing agent composition, a
coating film is formed by being imparted to a drier, thereby
preventing pitch contamination of the dryer.
[0051] Thereafter, when the coating film comes into contact with
the wet paper, a part of the coating film is re-emulsified, and the
contamination-preventing agent composition is transferred to the
wet paper.
[0052] The transferred contamination-preventing agent composition
is carried by the wet paper and is imparted also to a dryer on the
downstream side.
[0053] Details of these will be described later.
[0054] As a result, according to the contamination-preventing agent
composition of the present embodiment, it is possible to
sufficiently prevent pitch contamination as a whole for a plurality
of dryers.
[0055] It is preferable for the contamination-preventing agent
composition that the dynamic surface tension value at a lifetime of
100 ms by a maximum bubble pressure method is 65 mN/m or less.
[0056] When the dynamic surface tension value of the
contamination-preventing agent composition exceeds 65 mN/m, the
speed at which the re-transfer agent moves to the interface between
the dryer and the emulsion tends to be delayed as compared with the
case where the dynamic surface tension value is within the above
range. In this case, emulsification does not occur instantaneously,
and the pick-up amount to the wet paper becomes insufficient.
[0057] The dynamic surface tension value is a value measured in an
environment of 25.degree. C. using an automatic dynamic surface
tension meter BP-D5 (manufactured by Kyowa Interface Science,
Inc.).
[0058] It is preferable for the contamination-preventing agent
composition that the contact angle to cast iron is 70.degree. or
less.
[0059] When the contact angle of the contamination-preventing agent
composition to cast iron exceeds 70.degree., there are drawbacks
that it takes more time to remove moisture by drying and it becomes
difficult to form a uniform coating as compared with the case where
the contact angle is within the above range.
[0060] The contact angle is a value measured in an environment of
25.degree. C. and 50% humidity using DropMaster DMs-401, Teflon
needle 18 G.
[0061] Here, the dryer is generally made of cast iron.
[0062] Therefore, when the contamination-preventing agent
composition is imparted to a dryer, the contamination-preventing
agent composition can form a coating film on the surface of the
dryer instantaneously by setting the contact angle to cast iron
within the above-described range.
[0063] Cast iron is formed by casting an alloy containing iron as a
main component and containing at least one selected from the group
consisting of nickel, chromium, carbon and silicon.
[0064] The cast iron used to measure the contact angle may be the
same as or different from the cast iron of a dryer. It is
preferable that both of them are cast irons having a ten-point
average roughness (Rz) of 0.16 .mu.m or less, a maximum height
(Rmax) of 0.21 .mu.m or less, and an arithmetic mean roughness (Ra)
of 0.04 .mu.m or less.
[0065] In the contamination-preventing agent composition according
to the present embodiment, the emulsion is composed of a
non-silicone oil, water and an emulsifier. That is, the
non-silicone oil is emulsified with an emulsifier using water as a
medium.
[0066] The non-silicone oils includes mineral oils such as gear
oil, dryer oil, turbine oil, spindle oil and the like, vegetable
oils such as coconut oil, linseed oil, castor oil, rapeseed oil,
corn oil and the like, liquid paraffin, isoparaffin,
polyisobutylene, polybutene, maleated polybutene, synthetic ester
oil, polyethylene wax, micro wax, 12-hydroxystearic acid and the
like. These may be used singly or in combination of two or
more.
[0067] Among them, the non-silicone oil is preferably at least one
selected from the group consisting of polybutenes, synthetic ester
oils, mineral oils, vegetable oils and liquid paraffins from the
viewpoint of a film forming property and a pitch contamination
preventing property.
[0068] The emulsifier is not particularly limited, and known
nonionic surfactants, anionic surfactants, cationic surfactants,
amphoteric surfactants and the like are used.
[0069] Among these, the emulsifier is preferably an anionic
surfactant or a nonionic surfactant, from the viewpoint of storage
stability of the emulsion.
[0070] In the contamination-preventing agent composition according
to the present embodiment, the re-transfer agent includes
polyoxyalkylene alkyl ethers, polyoxyalkylene alkyl thioethers,
polyoxyalkylene fatty acid esters, polyoxyalkylene sorbitan fatty
acid esters, polyoxyalkylene sorbitol fatty acid esters, glycerin
mono-fatty acid esters and the like. These may be used singly or in
combination of two or more.
[0071] Among them, the re-transfer agent is preferably at least one
selected from the group consisting of polyoxyalkylene alkyl ethers,
polyoxyalkylene fatty acid esters, polyoxyalkylene sorbitan fatty
acid esters and polyoxyalkylene sorbitol fatty acid esters, from
the viewpoint of ease of re-emulsification.
[0072] The re-transfer agent preferably has a cloud point of
55.degree. C. or higher. When the cloud point is lower than
55.degree. C., the function as a re-transfer agent may possibly be
lost due to heat of a dryer as compared with the case where the
cloud point is within the above range.
[0073] When the re-transfer agent is water-soluble, the cloud point
is a temperature at which an aqueous solution containing 1% by mass
of the re-transfer agent is heated to become cloudy.
[0074] In contrast, when the re-transfer agent is water-insoluble,
the cloud point is a temperature at which a 25% (w/w) diethylene
glycol monobutyl ether aqueous solution containing 10% by mass of
the re-transfer agent is heated to become cloudy.
[0075] The re-transfer agent preferably has an HLB value of 8 to
15.
[0076] When the HLB value is less than 8 or exceeds 15, it is
impossible to sufficiently activate the interface between the
coating film made of the non-silicone oil described above and
water, as compared with the case where the HLB value is within the
above range.
[0077] The HLB value is a value measured by a known Griffin
method.
[0078] In the contamination-preventing agent composition, the
compounding ratio of the re-transfer agent is preferably 0.01% by
mass to 10% by mass with respect to the total amount of the
contamination-preventing agent composition.
[0079] When the compounding ratio of the re-transfer agent with
respect to the total amount of the contamination-preventing agent
composition is less than 0.01% by mass, there is a fear that the
re-transfer becomes insufficient and the pick-up amount to the
paper decreases, as compared with the case where the compounding
ratio of the re-transfer agent is within the above range, while
when the compounding ratio of the re-transfer agent with respect to
the total amount of the contamination-preventing agent composition
exceeds 10% by mass, the re-transfer agent itself bonds to the
pitch or the like, which may cause contamination, as compared with
the case where the compounding ratio of the re-transfer agent is
within the above range.
[0080] In the contamination-preventing agent composition, the
compounding ratio of the re-transfer agent with respect to 10% by
mass of the non-silicone oil is preferably 0.1% by mass to 10% by
mass.
[0081] When the compounding ratio of the re-transfer agent with
respect to 10% by mass of the non-silicone oil is less than 0.1% by
mass, there is a fear that the re-transfer agent cannot
sufficiently re-transfer the non-silicone oil, as compared with the
case where the compounding ratio of the re-transfer agent is within
the above range, while when the compounding ratio of the
re-transfer agent with respect to 10% by mass of the non-silicone
oil exceeds 10% by mass, there is a fear that the effect of
preventing adhesion of pitch contamination by the non-silicone oil
becomes insufficient, as compared with the case where the
compounding ratio of the re-transfer agent is within the above
range.
[0082] The contamination-preventing agent composition according to
the present embodiment is produced by stirring and mixing a
non-silicone oil, an emulsifier and water to obtain an emulsion and
stirring and mixing the emulsion, a re-transfer agent and
water.
[0083] In the above-described stirring and mixing, a hand mixer, a
homogenizer and the like are suitably used. In addition, they may
be dispersed by a dispersing machine such as a sand mill, a bead
mill, a ball mill or the like.
[0084] Next, the contamination preventing method using the
above-mentioned contamination-preventing agent composition will be
described.
[0085] FIG. 1 is a flowchart showing a contamination preventing
method using the contamination-preventing agent composition
according to the present embodiment.
[0086] As shown in FIG. 1, the contamination preventing method
according to the present embodiment has a first step S1 of
imparting the contamination-preventing agent composition a dryer on
the upstream side to form a coating film, a second step S2 of
bringing a wet paper into contact with the coating film to
re-emulsify a part of the coating film and transfer the
re-emulsified emulsion to the wet paper, and a third step S3 of
bringing the wet paper carrying the emulsion into contact with a
dryer on the downstream side to impart the emulsion to the
downstream dryer.
[0087] FIG. 2 is an explanatory diagram for explaining a
contamination preventing method according to the present
embodiment.
[0088] As shown in FIG. 2, in the contamination preventing method,
the contamination-preventing agent composition is first directly
imparted to a dryer 10 on the upstream side of a dry part in the
first step S1.
[0089] At this time, the dryer 10 is at a high temperature in order
to dry a wet paper W. For this reason, in the surface of the dryer
10, a part of water contained in the contamination-preventing agent
composition is evaporated, and a coating film 1 is formed of a
non-silicone oil. The coating film 1 contains also a re-transfer
agent.
[0090] Then, in the second step S2, when the traveling wet paper W
comes into contact with a dryer 10 on the upstream side, at the
same time as the wet paper W is dried, a part of the coating film 1
on the surface of the dryer 10 is re-emulsified by water contained
in the wet paper W. At this time, since the re-transfer agent is
contained in the emulsion 1a of the re-emulsified
contamination-preventing agent composition, the emulsion 1a is
transferred to the wet paper W.
[0091] The time from imparting the contamination-preventing agent
composition to a dryer until the wet paper comes into contact with
the dryer is extremely short, and is 40 ms to 160 ms.
[0092] Next, in the third step S3, the wet paper W travels while
holding the emulsion 1a and comes into contact with a dryer 11 on
the downstream side.
[0093] Then, since the side of the wet paper W to which the
emulsion 1a has been transferred comes into contact with the dryer
11 on the downstream side, a part of the emulsion 1a is
re-transferred to the dryer 11 on the downstream side.
[0094] Then, by separation of the wet paper W, the re-transferred
emulsion 1a is heated again by the dryer 11 on the downstream side
to form a coating film.
[0095] On the other hand, the emulsion 1a which has not been
re-transferred to the dryer 11 on the downstream side is
transferred to a dryer on the further downstream side of by the wet
paper W, and re-transferred to the dryer in a like manner.
[0096] By repeating the imparting of the emulsion 1a of the
contamination-preventing agent composition to a dryer on the
downstream side as described above, it becomes possible to impart
the emulsion 1a of the contamination-preventing agent composition
to a plurality of dryers.
[0097] In the contamination preventing method, a
contamination-preventing agent composition is continuously imparted
to a dryer 10 on the upstream side, so that an emulsion of the
contamination-preventing agent composition is imparted continuously
also to a drier 11 on the downstream side via the wet paper W.
[0098] In the contamination preventing method according to the
present embodiment, since the contamination-preventing agent
composition described above is used, it is possible to increase the
pick-up amount of the contamination-preventing agent composition to
the wet paper W.
[0099] Further, through the first step S1, the second step S2 and
the third step S3 described above, it is possible to prevent pitch
contamination as a whole for the plurality of dryers.
[0100] Next, the spraying position of the contamination-preventing
agent composition according to the present embodiment will be
described.
[0101] FIG. 3 is a schematic diagram showing a dryer using the
contamination-preventing agent composition according to the present
embodiment.
[0102] As shown in FIG. 3, the contamination-preventing agent
composition is used in a dry part D.
[0103] The dry part D includes a wet paper W, a plurality of
cylindrical dryers D1, D2, D3, D4, D5, D6, D7 and D8 (hereinafter
referred to as "D1 to D8") for heating and drying the wet paper W,
canvases K1, K2 for pressing the wet paper against the dryers D1
through D8, a canvas roll KR for guiding the canvases K1, K2, a
breaker stack roll B for gently adjusting the smoothness and paper
thickness of the dried wet paper W, and a calender roll C for
adjusting the smoothness and paper thickness of the dried wet paper
W.
[0104] In the dry part D, the wet paper W is pressed against the
surfaces of the dryers D1 to D8 by the canvases K1 and K2. As a
result, the wet paper W adheres to the dryers D1 to D8 and is
simultaneously heated and dried.
[0105] Thereafter, the wet paper W is sandwiched by the breaker
stack roll B, and then the wet paper W is densified by the calender
roll C.
[0106] The contamination-preventing agent composition is imparted
to the dryer D 1 on the most upstream side of the dry part D at the
position of the arrow A.
[0107] The method of imparting the contamination-preventing agent
composition is not particularly limited, and for example, a shower
method using a spray nozzle or the like, a spray method, and the
like are used.
[0108] After the contamination-preventing agent composition is
imparted at the position of the arrow A of the dryer D 1, the dryer
D 1 is rotated to guide the wet paper W and the emulsion of the
contamination-preventing agent composition is transferred to the
wet paper W.
[0109] Then, the emulsion of the contamination-preventing agent
composition is carried by the wet paper W and re-transferred to a
dryer D3 on the downstream side to which the wet paper is guided,
and re-transferred to a dryer D5 on the further downstream side and
re-transferred to a dryer D7 on the further downstream side.
[0110] On the other hand, the contamination-preventing agent
composition imparted at the position of the arrow A of the dryer D2
is re-transfers to a dryer D4 on the downstream side to which the
wet paper is guided, and re-transferred to a dryer D6 on the
further downstream side and re-transferred to a dryer D8 on the
further downstream side.
[0111] By repeating the re-transfer as described above, the
contamination-preventing agent composition or the emulsion thereof
is imparted to the dryers D1 to D8 as a whole and pitch
contamination can be prevented.
[0112] At this time, the spray amount of the
contamination-preventing agent composition is preferably 0.02
mg/m.sup.2 to 2.0 mg/m.sup.2 in terms of the nonvolatile component
amount per passage area of the wet paper.
[0113] When the spray amount is less than 0.02 mg/m.sup.2, the
contamination-preventing agent composition does not sufficiently
adhere to the surface of a dryer and pitch contamination cannot be
sufficiently prevented in some cases, as compared with the case
where the spray amount is within the above-described range. In
contrast, when the spray amount is over 2.0 mg/m.sup.2, there is a
possibility that the contamination-preventing agent composition
itself causes contamination, as compared with the case where the
spray amount is within the above-described range.
[0114] Although preferred embodiments of the present invention have
been described above, the present invention is not limited to the
above-described embodiments.
[0115] The contamination-preventing agent composition according to
the present embodiment is composed of an emulsion, a re-transfer
agent and water, and may contain additives such as a chelating
agent, a pH adjusting agent, a preservative, a dispersing agent, a
viscosity adjusting agent, a solid lubricant, a wetting agent, a
dusting-preventing agent, a release agent, an adhesive, a surface
modification agent, a cleaning agent, a paper strength enhancer, a
sizing agent, a retention aid, a water repellent, an oil repellent,
an anti-lubricant, a softener and the like.
[0116] According to the present embodiment, the
contamination-preventing agent composition is imparted to a dryer,
but it may be imparted not only to a dryer but also to a canvas, a
canvas roll, a calender roll, a breaker stack roll and the
like.
[0117] In the contamination-preventing agent composition according
to the present embodiment, the dryer is made of cast iron, but it
may be made of another material.
EXAMPLES
[0118] Hereinafter, the present invention will be described more
specifically based on Examples and Comparative Examples, but the
present invention is not limited to the following Examples.
Example 1
[0119] To an emulsion containing 10 parts by mass of liquid
paraffin (non-silicone oil), 0.1 part by mass of polycarboxylic
acid amine (emulsifier, anionic surfactant), 0.1 part by mass of
stearic acid amine (emulsifier, anionic surfactant) and 88.8 parts
by mass of purified water was added 1.0 part by mass of
polyoxyalkylene alkyl ether (re-transfer agent, cloud point:
62.degree. C., HLB: 8.1) and they were mixed by stirring to prepare
a sample A of a contamination-preventing agent composition.
[0120] The dynamic surface tension value at 100 ms of the sample A
was 45 mN/m and the contact angle to cast iron was 50.degree..
Example 2
[0121] A sample B of a contamination-preventing agent composition
was prepared in the same manner as in Example 1 except that 1.0
part by mass of another polyoxyalkylene alkyl ether (re-transfer
agent, cloud point: 79.degree. C., HLB: 14.7) was used instead of
the polyoxyalkylene alkyl ether.
[0122] The dynamic surface tension value at 100 ms of the sample B
was 49 mN/m and the contact angle to cast iron was 54.degree..
Example 3
[0123] A sample C of a contamination-preventing agent composition
was prepared in the same manner as in Example 1 except that 1.0
part by mass of polyoxyalkylene sorbitan fatty acid ester
(re-transfer agent, cloud point: 60.degree. C. or higher, HLB:
14.9) was used instead of the polyoxyalkylene alkyl ether.
[0124] The dynamic surface tension value at 100 ms of the sample C
was 62 mN/m and the contact angle to cast iron was 68.degree..
Example 4
[0125] A sample D of a contamination-preventing agent composition
was prepared in the same manner as in Example 1 except that 10
parts by mass of castor oil (vegetable oil, non-silicone oil) was
used instead of liquid paraffin.
[0126] The dynamic surface tension value at 100 ms of the sample D
was 52 mN/m and the contact angle to cast iron was 60.degree..
Example 5
[0127] A sample E of a contamination-preventing agent composition
was prepared in the same manner as in Example 1 except that 10
parts by mass of castor oil (vegetable oil, non-silicone oil) was
used instead of liquid paraffin and 1 part by mass of
polyoxyalkylene fatty acid ester (re-transfer agent, cloud point:
60.degree. C. or higher, HLB: 13.6) was used instead of the
polyoxyalkylene alkyl ether.
[0128] The dynamic surface tension value at 100 ms of the sample E
was 43 mN/m and the contact angle to cast iron was 52.degree..
Example 6
[0129] A sample F of a contamination-preventing agent composition
was prepared in the same manner as in Example 1 except that 10
parts by mass of ester synthetic oil (non-silicone oil) was used
instead of liquid paraffin.
[0130] The dynamic surface tension value at 100 ms of the sample F
was 50 mN/m and the contact angle to cast iron was 62.degree..
Example 7
[0131] A sample G of a contamination-preventing agent composition
was prepared in the same manner as in Example 1 except that 10
parts by mass of ester synthetic oil (non-silicone oil) was used
instead of liquid paraffin and 1 part by mass of polyoxyalkylene
sorbitol fatty acid ester (re-transfer agent, cloud point:
80.degree. C. or higher, HLB: 13.8) was used instead of the
polyoxyalkylene alkyl ether.
[0132] The dynamic surface tension value at 100 ms of the sample G
was 42 mN/m and the contact angle to cast iron was 50.degree..
Comparative Example 1
[0133] A sample H of a contamination-preventing agent composition
was prepared in the same manner as in Example 1 except that the
polyoxyalkylene alkyl ether was not used.
[0134] The dynamic surface tension value at 100 ms of the sample H
was 72 mN/m and the contact angle to cast iron was 102.degree..
Comparative Example 2
[0135] A sample I of a contamination-preventing agent composition
was prepared in the same manner as in Example 1 except that 1.0
part by mass of another polyoxyalkylene alkyl ether (cloud point:
53.degree. C., HLB: 6.5) was used instead of the polyoxyalkylene
alkyl ether.
[0136] The dynamic surface tension value at 100 ms of the sample I
was 66 mN/m and the contact angle to cast iron was 85.degree..
Comparative Example 3
[0137] A sample J of a contamination-preventing agent composition
was prepared in the same manner as in Example 1 except that 1.0
part by mass of another polyoxyalkylene alkyl ether (cloud point:
52.degree. C., HLB: 8.0) was used instead of the polyoxyalkylene
alkyl ether.
[0138] The dynamic surface tension value at 100 ms of the sample J
was 66 mN/m and the contact angle to cast iron was 76.degree..
Comparative Example 4
[0139] A sample K of a contamination-preventing agent composition
was prepared in the same manner as in Example 1 except that 1.0
part by mass of another polyoxyalkylene alkyl ether (cloud point:
62.degree. C., HLB: 7.8) was used instead of the polyoxyalkylene
alkyl ether.
[0140] The dynamic surface tension value at 100 ms of the sample K
was 66 mN/m and the contact angle to cast iron was 79.degree..
Comparative Example 5
[0141] A sample L of a contamination-preventing agent composition
was prepared in the same manner as in Example 1 except that 1.0
part by mass of another polyoxyalkylene alkyl ether (cloud point:
100.degree. C. or higher, HLB: 16.0) was used instead of the
polyoxyalkylene alkyl ether.
[0142] The dynamic surface tension value at 100 ms of the sample L
was 67 mN/m and the contact angle to cast iron was 85.degree..
Comparative Example 6
[0143] A sample M of a contamination-preventing agent composition
was prepared in the same manner as in Example 1 except that 10
parts by mass of castor oil (vegetable oil, non-silicone oil) was
used instead of liquid paraffin and the polyoxyalkylene alkyl ether
was not used.
[0144] The dynamic surface tension value at 100 ms of the sample M
was 69 mN/m and the contact angle to cast iron was 82.degree..
Comparative Example 7
[0145] A sample N of a contamination-preventing agent composition
was prepared in the same manner as in Example 1 except that 10
parts by mass of castor oil (vegetable oil, non-silicone oil) was
used instead of liquid paraffin and 1.0 part by mass of another
polyoxyalkylene alkyl ester (cloud point: 53.degree. C., HLB: 6.5)
was used instead of the polyoxyalkylene alkyl ether.
[0146] The dynamic surface tension value at 100 ms of the sample N
was 68 mN/m and the contact angle to cast iron was 78.degree..
Comparative Example 8
[0147] A sample O of a contamination-preventing agent composition
was prepared in the same manner as in Example 1 except that 10
parts by mass of castor oil (vegetable oil, non-silicone oil) was
used instead of liquid paraffin and 1.0 part by mass of another
polyoxyalkylene alkyl ester (cloud point: 100.degree. C. or higher,
HLB: 16.0) was used instead of the polyoxyalkylene alkyl ether.
[0148] The dynamic surface tension value at 100 ms of the sample O
was 68 mN/m and the contact angle to cast iron was 80.degree..
Comparative Example 9
[0149] A sample P of a contamination-preventing agent composition
was prepared in the same manner as in Example 1 except that 10
parts by mass of ester synthetic oil (non-silicone oil) was used
instead of liquid paraffin and the polyoxyalkylene alkyl ether was
not used.
[0150] The dynamic surface tension value at 100 ms of the sample P
was 70 mN/m and the contact angle to cast iron was 90.degree..
Comparative Example 10
[0151] A sample Q of a contamination-preventing agent composition
was prepared in the same manner as in Example 1 except that 10
parts by mass of ester synthetic oil (non-silicone oil) was used
instead of liquid paraffin and 1.0 part by mass of another
polyoxyalkylene alkyl ester (cloud point: 53.degree. C., HLB: 6.5)
was used instead of the polyoxyalkylene alkyl ether.
[0152] The dynamic surface tension value at 100 ms of the sample Q
was 66 mN/m and the contact angle to cast iron was 73.degree..
Comparative Example 11
[0153] A sample R of a contamination-preventing agent composition
was prepared in the same manner as in Example 1 except that 10
parts by mass of ester synthetic oil (non-silicone oil) was used
instead of liquid paraffin and 1.0 part by mass of another
polyoxyalkylene alkyl ester (cloud point: 100.degree. C. or higher,
HLB: 16.0) was used instead of the polyoxyalkylene alkyl ether.
[0154] The dynamic surface tension value at 100 ms of the sample R
was 67 mN/m and the contact angle to cast iron was 75.degree..
(Evaluation Method)
1. Contamination Preventing Test
[0155] Each 0.2 g of the samples obtained in Examples 1 to 7 and
Comparative Examples 1 to 11 were sprayed onto a 5.times.25 cm
square stainless steel plate and dried with heating at 80.degree.
C.
[0156] Next, a 5.times.25 cm square broad-leaf tree bleached kraft
pulp (LBKP) was adjusted to a water content of 60%, which was
brought into contact with the sample on the stainless steel plate
for 10 seconds at a contact pressure of 30 g/cm.sup.2. In this way,
a part of the sample was transferred to LBKP.
[0157] Next, another stainless steel plate was prepared, and the
above-mentioned LBKP was brought into contact with this at a
contact pressure of 30 g/cm.sup.2 for 10 seconds, and the sample
was re-transferred from the LBKP to the another stainless steel
plate.
[0158] Then, onto the another stainless steel plate, a
heat-resistant tape (trade name: No. 5413, manufactured by 3M Japan
Co., Ltd.) was pasted so as to sandwich the re-transferred sample,
and the sample was heated at 80.degree. C.
[0159] Then, the magnitude of the force when peeling the
heat-resistant tape was measured. The smaller the value, the easier
the pitch is peeled (pitch is hard to adhere), meaning the high
contamination preventing effect. As a blank, measurements were also
made on samples not sprayed on the stainless steel plate.
[0160] The obtained results are shown in Table 1.
2. Actual Machine Evaluation
[0161] The samples of Examples 1, 5 and 7 and Comparative Examples
1, 2, 5, 6, 7, 9 and 10 were sprayed at a rate of 5 cc/min to the
dryer D1 at the position of the arrow A shown in FIG. 3, and the
dryer was operated for 60 minutes.
[0162] Further, doctor blades (dryer contamination-removing
apparatus) not shown were placed so as to come into contact with
the dryers D1, D3, D5 and D7, respectively.
[0163] For each dryer, the presence or absence of the pitch
accumulated on the doctor blade was visually observed.
[0164] The obtained results are shown in Table 1.
TABLE-US-00001 TABLE 1 Peeling force Presence or absence of pitch
(N) D1 D3 D5 D7 Example 1 1.57 Absent absent present -- Example 2
1.60 -- -- -- -- Example 3 1.79 -- -- -- -- Example 4 1.14 -- -- --
-- Example 5 1.09 absent absent absent absent Example 6 1.02 -- --
-- -- Example 7 0.89 absent absent absent absent Comparative 2.63
absent present present -- Example 1 Comparative 2.44 absent present
present -- Example 2 Comparative 2.54 -- -- -- -- Example 3
Comparative 2.59 -- -- -- -- Example 4 Comparative 2.38 absent
present present -- Example 5 Comparative 1.98 absent present
present present Example 6 Comparative 2.05 absent present present
present Example 7 Comparative 2.12 -- -- -- -- Example 8
Comparative 1.85 absent present present present Example 9
Comparative 1.87 absent present present present Example 10
Comparative 1.97 -- -- -- -- Example 11 blank 2.84 -- -- -- --
[0165] From the results in Table 1, the samples of Examples 1 to 7
showed lower tape peeling force as compared with the samples of
Comparative Examples 1 to 11 and the blank sample. In particular,
it was found that the samples of Examples 4 to 7 had extremely low
tape peeling force and the effect remarkably appeared. From this,
it was found that the contamination-preventing agent composition of
the present invention has a pitch adhesion preventing effect.
[0166] Further, in the test on an actual machine, the samples of
Examples 5 and 7 manifested a sufficient contamination preventing
effect even for a dryer on the downstream side. On the other hand,
any of the samples of Comparative Examples 5 to 7 and 9 and 10 were
able to prevent the pitch contamination of the dryer D1, but could
not prevent the pitch contamination of the downstream dryer.
INDUSTRIAL APPLICABILITY
[0167] The contamination-preventing agent composition of the
present invention is used by being imparted to a dryer in a dry
part at the time of paper making. According to the
contamination-preventing agent composition of the present
invention, it is possible to prevent pitch contamination of a
plurality of dryers as a whole, so that the yield in the production
of paper can be greatly improved.
REFERENCE SIGNS LIST
[0168] 1 . . . coating film, [0169] 1a . . . emulsion, [0170] 10,
11 . . . dryer, [0171] B . . . breaker stack roll, [0172] C . . .
calender roll, [0173] D . . . dry part, [0174] D1, D2, D3, D4, D5,
D6, D7, D8 . . . dryer, [0175] K1, K2 . . . canvas, [0176] KR . . .
canvas roll, [0177] S1 . . . first step, [0178] S2 . . . second
step, [0179] S3 . . . third step, [0180] W . . . wet paper
* * * * *