U.S. patent application number 16/222822 was filed with the patent office on 2019-06-27 for locomotive control system.
The applicant listed for this patent is General Electric Company. Invention is credited to Munishwar Ahuja, Shankar Chandrasekaran, Subhas Chandra Das, Ajith Kuttannair Kumar, Rupam Mukherjee.
Application Number | 20190193760 16/222822 |
Document ID | / |
Family ID | 66949260 |
Filed Date | 2019-06-27 |

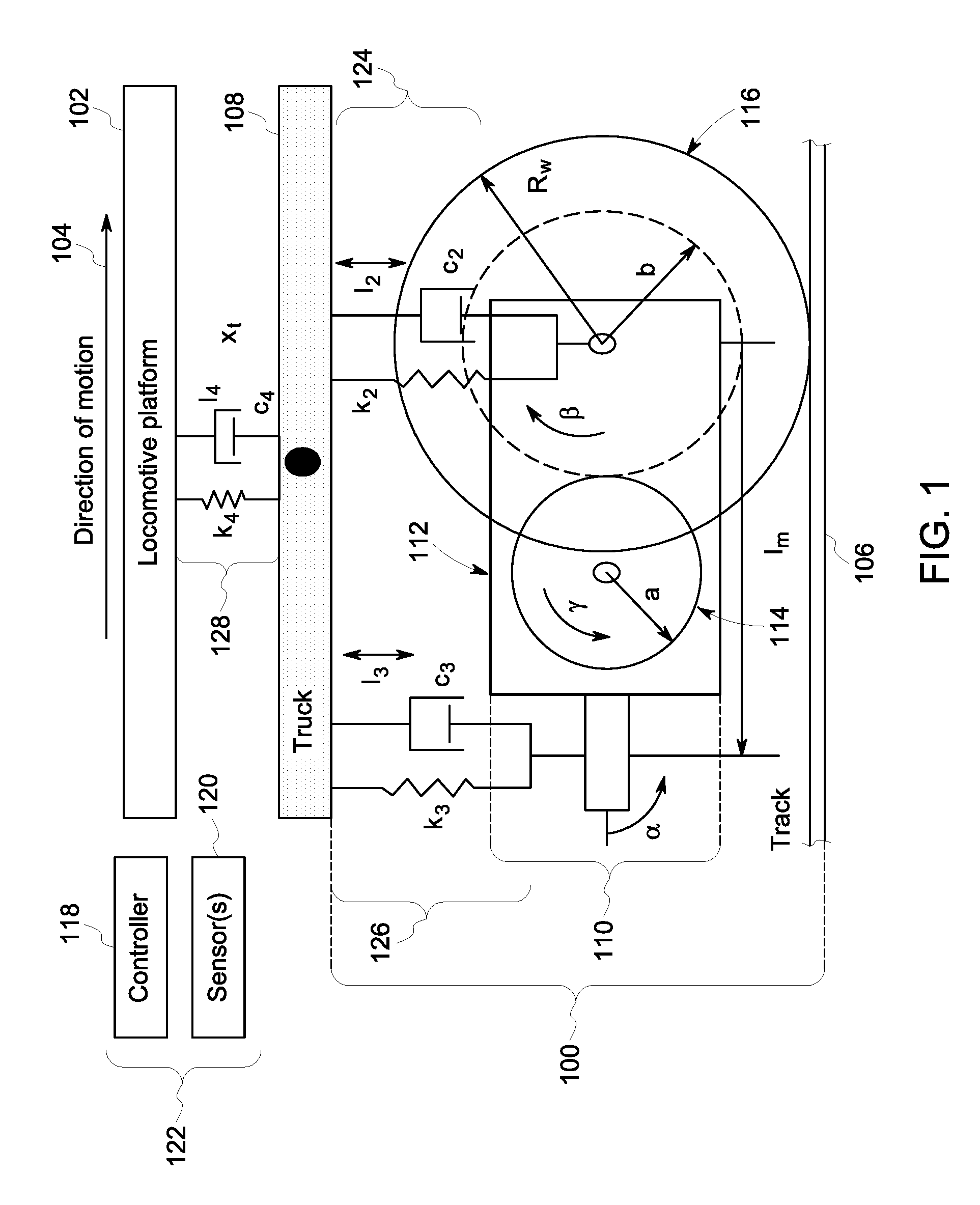

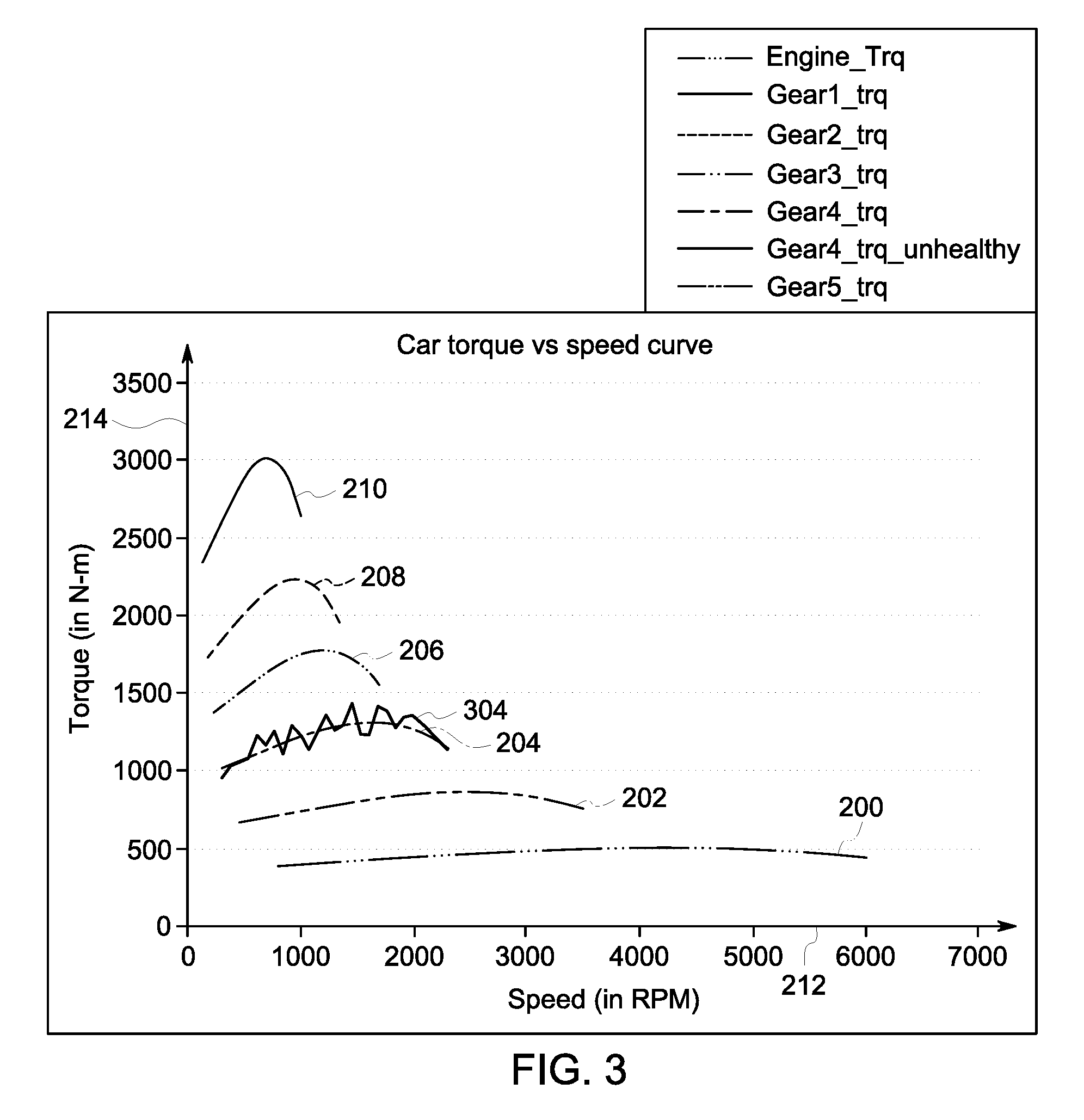
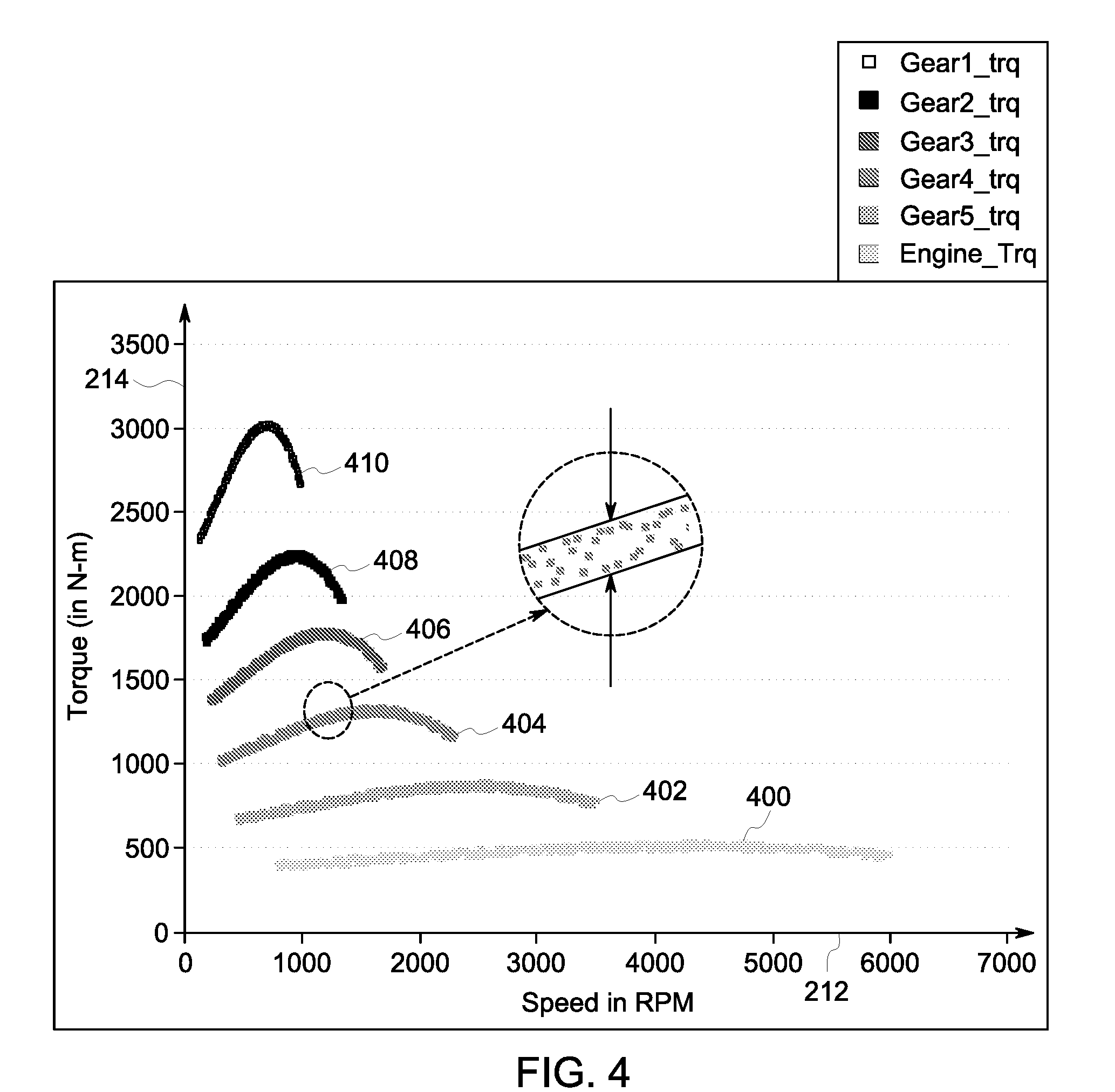
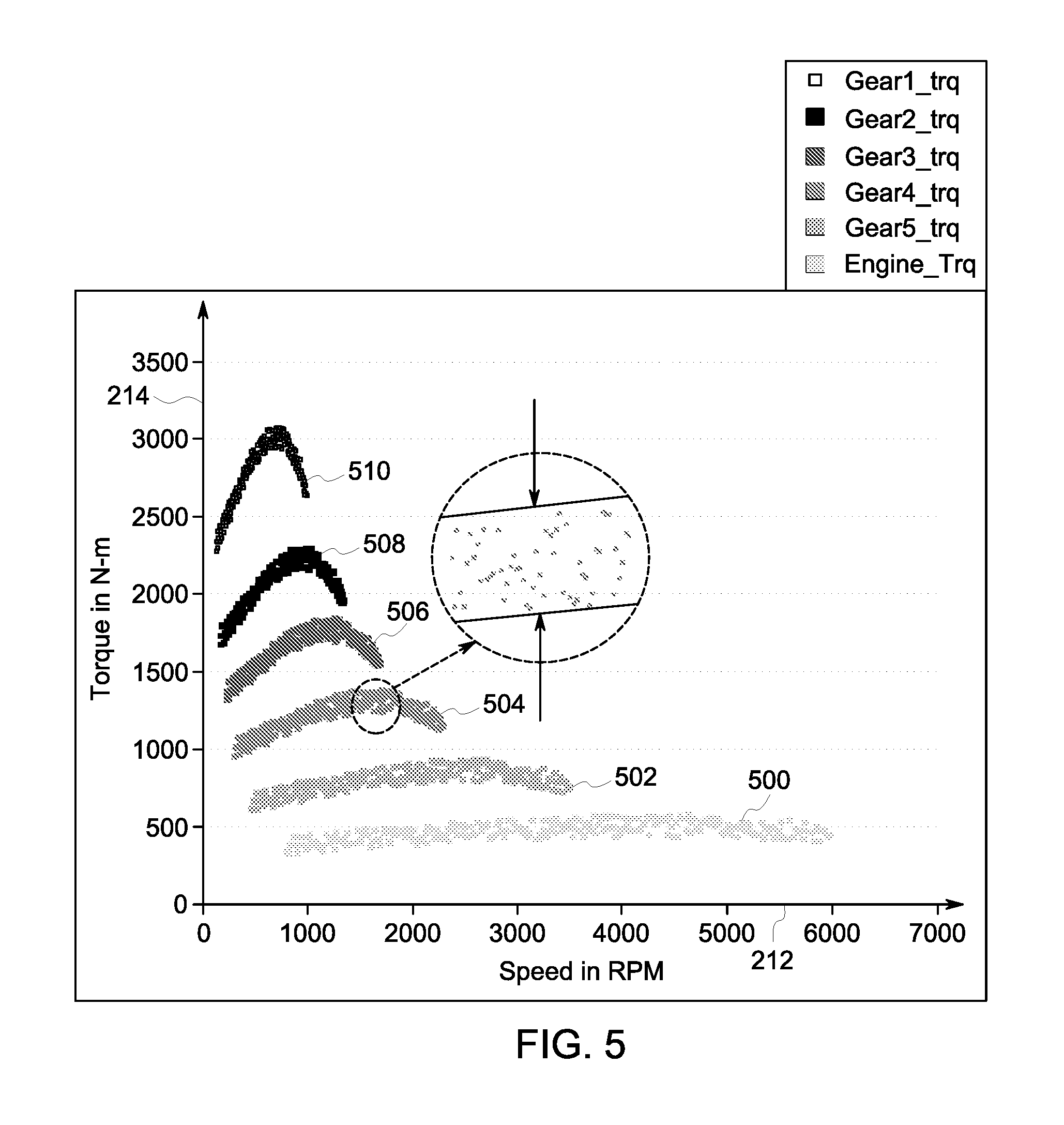





View All Diagrams
United States Patent
Application |
20190193760 |
Kind Code |
A1 |
Kumar; Ajith Kuttannair ; et
al. |
June 27, 2019 |
LOCOMOTIVE CONTROL SYSTEM
Abstract
A locomotive control system measures actuating parameters of a
locomotive propulsion system and monitors the actuating parameters
according to a forcing function of operation of the propulsion
system. A degraded component of the locomotive is identified by
comparing actuating parameters generated according to the forcing
function with actuating parameters expressed as a function of speed
of another locomotive propulsion system, examining changes in the
generated actuating parameters over time, examining oscillations in
movement of the locomotive during gear shifting, comparing wheel
speed decreases during another forcing function, and/or comparing a
magnitude of a spectrum of the actuating parameters of with one or
more designated magnitudes.
Inventors: |
Kumar; Ajith Kuttannair;
(Erie, PA) ; Chandrasekaran; Shankar; (Erie,
PA) ; Das; Subhas Chandra; (Bangalore, IN) ;
Mukherjee; Rupam; (Bangalore, IN) ; Ahuja;
Munishwar; (Bangalore, IN) |
|
Applicant: |
Name |
City |
State |
Country |
Type |
General Electric Company |
Schenectady |
NY |
US |
|
|
Family ID: |
66949260 |
Appl. No.: |
16/222822 |
Filed: |
December 17, 2018 |
Related U.S. Patent Documents
|
|
|
|
|
|
Application
Number |
Filing Date |
Patent Number |
|
|
62608730 |
Dec 21, 2017 |
|
|
|
Current U.S.
Class: |
1/1 |
Current CPC
Class: |
B61C 5/00 20130101; B61L
3/006 20130101; B61L 3/008 20130101; B61L 15/0072 20130101; B61L
3/002 20130101; B61L 15/0081 20130101; B61C 17/12 20130101 |
International
Class: |
B61L 3/00 20060101
B61L003/00; B61L 15/00 20060101 B61L015/00 |
Claims
1. A locomotive control system comprising: a locomotive having a
propulsion system and one or more sensors located onboard the
locomotive, the one or more sensors configured to measure one or
more actuating parameters generated by the propulsion system while
the locomotive is stationary, idling, or during changes in movement
of the locomotive; and one or more processors communicatively
coupled with the one or more sensors, the one or more processors
configured to control operation of the propulsion system according
to a forcing function and to monitor the one or more actuating
parameters while the propulsion system is operating according to
the forcing function, wherein the one or more processors are
configured to identify a degraded component of the locomotive by
one or more of: comparing the actuating parameters that are
monitored with speed actuating parameters expressed as a function
of speed of at least one other propulsion system associated with at
least one other locomotive, examining changes in the actuating
parameters that are monitored over time, examining oscillations in
changes in movement of the locomotive during shifting of gears
between different torques or between different transmission torques
during operation of the propulsion system according to the forcing
function, comparing decreases in wheel speed of the locomotive
during operation of the propulsion system according to the forcing
function with designated wheel speeds associated with at least one
other locomotive, or comparing a magnitude of one or more
frequencies in a frequency domain spectrum of the actuating
parameters of the locomotive with one or more designated magnitudes
while the locomotive is one or more of moving, idling, or
stationary.
2. The locomotive control system of claim 1, wherein the forcing
function is one or more of a designated forcing function that
predefines the actuating parameters of the propulsion system of the
locomotive, a naturally occurring forcing function that identifies
operational conditions of the propulsion system that are not
automatically implemented, or a combination of the designated
forcing function and the naturally occurring forcing function.
3. The locomotive control system of claim 1, wherein the forcing
function defines one or more of motor torques of the propulsion
system, a terrain over which the locomotive travels, a gradient of
a route on which the locomotive travels, a speed bump of the
locomotive, a stiff gradient of the locomotive, a coasting
operation of the locomotive, or a combination of forces that one or
more of assist motion or oppose motion of the locomotive.
4. The locomotive control system of claim 1, wherein the actuating
parameters include one or more of torque generated by the
propulsion system, power generated by the propulsion system, force
generated by the propulsion system, tractive effort generated by
the propulsion system, speed of the locomotive, or an opposing
force to generated torque of the propulsion system.
5. The locomotive control system of claim 1, wherein the propulsion
system is one or more of a motor or a prime mover other than an
engine of the locomotive.
6. The locomotive control system of claim 1, wherein the forcing
function designates one or more of: engine torques as a function of
engine speeds that are generated by an engine of the locomotive,
application of one or more brakes of the locomotive, or shifting of
gears in a transmission of the locomotive.
7. The locomotive control system of claim 1, wherein the one or
more processors are configured to monitor torques generated by the
propulsion system during operation of the locomotive according to
operational conditions designated by the forcing function, wherein
the one or more processors are configured to identify the degraded
component of the locomotive by one or more of: comparing torques
that are generated by the propulsion system during operation
according to the forcing function as the actuating parameters, with
the forcing function designating torques as a function of the speed
of the other propulsion system that is associated with the at least
one other locomotive, or examining the changes in the actuating
parameters that are generated by the propulsion system during
operation according to the forcing function over time, wherein the
degraded component of the locomotive is determined responsive to a
variance in the actuating parameters that are generated by the
propulsion system exceeding one or more designated thresholds.
8. The locomotive control system of claim 1, wherein the one or
more processors are configured to identify the degraded component
of the locomotive by examining the oscillations in the changes in
movement of the locomotive during shifting of gears and determining
that the oscillations exceed one or more thresholds.
9. The locomotive control system of claim 1, wherein the one or
more processors are configured to identify the degraded component
of the locomotive by comparing the magnitude of the one or more
frequencies in the frequency domain spectrum of the actuating
parameters of the locomotive with one or more designated
magnitudes.
10. A locomotive control system comprising: a locomotive having one
or more motors configured to generate torque to propel the
locomotive; one or more sensors configured to measure a response of
the locomotive to the torque that is generated by the one or more
motors, the one or more sensors configured to generate sensor data
representative of the response that is measured; and a hardware
controller configured to direct the one or more motors of the
locomotive to generate the torque according to a designated torque
profile, the controller also configured to receive the sensor data
and to determine a frequency spectrum of the response of the
locomotive, the controller also configured to compare one or more
parts of the frequency spectrum with a threshold to determine that
a component of the locomotive is degraded and to automatically
change movement of the locomotive responsive to determining that
the component is degraded.
11. The locomotive control system of claim 10, wherein the
designated torque profile is a pseudo random binary sequence of
torques to be generated by the one or more motors.
12. The locomotive control system of claim 10, wherein the one or
more sensors are configured to measure one or more of speeds or
accelerations of the locomotive as the response of the locomotive
to the torque that is generated by the one or more motors.
13. The locomotive control system of claim 10, wherein the one or
more sensors are configured to measure rotor speeds of the one or
more motors as the response of the locomotive to the torque that is
generated by the one or more motors.
14. A locomotive control system comprising: an engine configured to
be disposed onboard a locomotive and to receive a supply of fuel
for cylinders of the engine; a power electronics circuit configured
to be coupled with the engine and to conduct electric current to
one or more motors of the locomotive for propelling the locomotive;
one or more sensors configured to monitor direct current link
voltages in the power electronics circuit coupled with the engine;
and one or more processors configured to be communicatively coupled
with the one or more sensors, the one or more processors also
configured to change the supply of fuel to at least one of the
cylinders of the engine, to determine a magnitude of a frequency in
a frequency spectrum of the direct current link voltages that are
monitored, and to determine whether the at least one cylinder that
receives the supply of fuel that is changed is damaged or degraded
based on the magnitude of the frequency that is determined.
15. The locomotive control system of claim 14, wherein the one or
more processors are configured to change the supply of fuel to the
at least one cylinder by reducing fuel supplied to the least one
cylinder.
16. The locomotive control system of claim 14, wherein the one or
more processors are configured to change the supply of fuel to the
at least one cylinder by cutting out the at least one cylinder.
17. The locomotive control system of claim 14, wherein the one or
more processors are configured to change the supply of fuel to the
at least one cylinder by stopping injection of the fuel to a first
cylinder of the cylinders while other cylinders of the cylinders in
the engine continue being injected with the fuel.
18. The locomotive control system of claim 14, wherein the
frequency in the frequency spectrum is at one half of a frequency
of a speed at which the engine operates.
19. The locomotive control system of claim 14, wherein the one or
more processors are configured to sequentially change the supply of
fuel to other cylinders in the plural cylinders, monitor the direct
current link voltages, determine the magnitude of the frequency,
and determine whether each of the other cylinders receiving the
sequentially changed supply of fuel is damaged or degraded based on
the magnitude of the frequency.
20. The locomotive control system of claim 14, wherein the one or
more processors are configured to change the supply of the fuel to
the at least one cylinder by increasing fuel supplied to the at
least one cylinder relative to one or more other cylinders of the
engine.
Description
CROSS-REFERENCE TO RELATED APPLICATIONS
[0001] This application claims priority to U.S. Provisional
Application No. 62/608,730, which was filed on 21 Dec. 2017, and
the entire disclosure of which is incorporated herein by
reference.
FIELD
[0002] Embodiments of the inventive subject matter described herein
relate to systems that control vehicles such as locomotives based
on evaluated health of the vehicles and/or components of the
vehicles.
BACKGROUND
[0003] A variety of different types of vehicles, (e.g.,
locomotives, other off-highway vehicles, trucks, cars, sport
utility vehicles, marine vessels, etc.) have various power
assemblies that include axle or wheel components and many
interconnected components and assemblies that are subjected to
degradation due to infancy, age, operational stresses, etc. This is
true for the many different types of vehicles and the operating
method of the vehicles (e.g., autonomous or driverless vehicles,
semi-autonomous vehicles, or driver-operated vehicles).
[0004] Degradation of these components with time may not be easily
recognizable. To recognize the incipient damage from degradation,
tear down of specific parts or of the entire vehicle may be
required, followed by manual inspection, inspection with
specialized equipment, and/or specific tests. These inspection
methods incur high cost in terms of labor, equipment cost,
downtime, etc. Degradation of vehicle components or assemblies can
negatively impact operation of the vehicle and/or other components
and assemblies when the level of degradation reaches a severe
level, which can result in breakdown of any component or assembly,
derating the vehicle performance, or rendering the vehicle
completely inoperable.
[0005] Severe degradation, wear or breakdown of components or
assemblies leading to breakdown of the vehicle can result in
significant costs in terms of labor, downtime, and replacement
parts. While some known systems and methods such as periodic
inspection or operator detections of anomalies, which can vary from
person to person) can attempt to predict when repair or replacement
of components is needed. But, these approaches lack accuracy in
predictions and/or result in the identification of the need for
repair or replacement at too late of a time.
BRIEF DESCRIPTION
[0006] In one embodiment, a locomotive control system is provided.
The control system includes a locomotive having a propulsion system
and one or more sensors located onboard the locomotive. The one or
more sensors configured to measure one or more actuating parameters
of the propulsion system while the locomotive is stationary,
idling, or during changes in movement of the locomotive. The
control system also includes one or more processors communicatively
coupled with the one or more sensors. The one or more processors
are configured to monitor the one or more actuating parameters
according to a forcing function that represents operation of the
propulsion system of the locomotive. The one or more processors
also are configured to identify a degraded component of the
locomotive by one or more of (a) comparing actuating parameters
that are generated by the propulsion system according to the
forcing function with (speed) actuating parameters expressed as a
function of speed of another propulsion system associated with at
least one other locomotive, (b) examining changes in the actuating
parameters that are generated by the propulsion system according to
the forcing function over time, (c) examining oscillations in the
changes in movement of the locomotive during shifting of gears
between different torques or between different transmission torques
of the forcing function, (d) comparing decreases in wheel speed of
the locomotive during operation according to the forcing function
with designated wheel speeds associated with at least one other
locomotive, and/or (e) comparing a magnitude of one or more
frequencies in a frequency domain spectrum of the actuating
parameters of the locomotive with one or more designated magnitudes
while the locomotive is one or more of moving, idling, or
stationary.
[0007] In one embodiment, a locomotive control system is provided
that includes a locomotive having one or more motors configured to
generate torque to propel the locomotive and one or more sensors
configured to measure a response of the locomotive to the torque
that is generated by the one or more motors. The one or more
sensors are configured to generate sensor data representative of
the response that is measured. The control system also includes a
hardware controller configured to direct the one or more motors of
the locomotive to generate the torque according to a designated
torque profile. The controller also is configured to receive the
sensor data and to determine a frequency spectrum of the response
of the locomotive. The controller is configured to compare one or
more parts of the frequency spectrum with a threshold to (a)
determine that a component of the locomotive is degraded and to (b)
automatically change movement of the locomotive responsive to
determining that the component is degraded.
[0008] In one embodiment, a locomotive control system includes an
engine configured to be disposed onboard a locomotive and to
receive a supply of fuel for cylinders of the engine, a power
electronics circuit configured to be coupled with the engine and to
conduct electric current to one or more motors of the locomotive
for propelling the locomotive, one or more sensors configured to
monitor direct current link voltages in the power electronics
circuit coupled with the engine, and one or more processors
configured to be communicatively coupled with the one or more
sensors. The one or more processors also are configured to change
the supply of fuel to at least one of the cylinders of the engine,
to determine a magnitude of a frequency in a frequency spectrum of
the direct current link voltages that are monitored, and to
determine whether the at least one cylinder that receives the
supply of fuel that is changed is damaged or degraded based on the
magnitude of the frequency that is determined.
BRIEF DESCRIPTION OF THE DRAWINGS
[0009] Reference is now made briefly to the accompanying drawings,
in which:
[0010] FIG. 1 schematically illustrates an example of a wheel and
axle combination of a vehicle;
[0011] FIG. 2 illustrates several examples of torque and speed
relationships for a healthy vehicle as measured by the sensors
shown in FIG. 1;
[0012] FIG. 3 illustrates one example of a comparison between
torque and speed relationships as measured by the sensors shown in
FIG. 1;
[0013] FIGS. 4 and 5 illustrate other examples of comparisons
between torque and speed relationships as measured by the sensors
shown in FIG. 1;
[0014] FIG. 6 illustrates engine or motor torques and transmission
torques of a vehicle as measured by the sensors shown in FIG.
1;
[0015] FIG. 7 illustrates moving speeds of vehicles as measured by
one or more of the sensors shown in FIG. 1;
[0016] FIG. 8 illustrates moving speeds of vehicles as measured by
one or more of the sensors shown in FIG. 1;
[0017] FIG. 9 illustrates braking efforts or forces of the vehicle
while braking according to one example;
[0018] FIG. 10 illustrates moving speeds of the vehicle and wheel
speeds of the wheel while braking according to one example;
[0019] FIG. 11 illustrates examples of torque references and
measured torques of the motor in the vehicle shown in FIG. 1;
[0020] FIG. 12 illustrates rotor speeds of the motor in the vehicle
shown in FIG. 1;
[0021] FIG. 13 illustrates one example of an engine speed spectrum
and a wheel speed spectrum;
[0022] FIG. 14 illustrates a flowchart of one embodiment a method
for evaluating vehicle health;
[0023] FIG. 15 illustrates another example of an engine speed
spectrum;
[0024] FIG. 16 illustrates one example of a forcing function;
[0025] FIG. 17 illustrates three examples of sensed changes in
length of the secondary suspension in the first wheel and axle
combination of the vehicle in response to implementation of the
forcing function shown in FIG. 16;
[0026] FIG. 18 illustrates one example of sensed changes in length
of a secondary suspension in another wheel and axle combination of
the same vehicle in response to implementation of the forcing
function shown in FIG. 16;
[0027] FIG. 19 schematically illustrates another embodiment of the
control system shown in FIG. 1;
[0028] FIG. 20 illustrates operation of the control system shown in
FIG. 19;
[0029] FIG. 21 illustrates one embodiment of a timing diagram for
examination of the cylinders of the engine.
[0030] FIG. 22 illustrates one example of a spatial representation
of a cylinder firing sequence of the engine shown in FIG. 19 when a
first cylinder of the engine is cut out and a twelfth cylinder of
the same engine is weak;
[0031] FIG. 23 illustrates one example of a magnitude of the DC
link voltage data spectrum at one half the frequency of the engine
speed when a healthy cylinder is cut out and no other cylinder of
the engine is weak;
[0032] FIG. 24 illustrates one example of a magnitude of the DC
link voltage data spectrum at one half the frequency of the engine
speed when a healthy cylinder is cut out and another cylinder of
the engine is weak;
[0033] FIG. 25 illustrates one example of a magnitude of the DC
link voltage data spectrum at one half the frequency of the engine
speed when a weak cylinder is cut out;
[0034] FIG. 26 illustrates examples of magnitudes of DC link
voltage spectra at one half of the engine speed frequency at
different fueling levels for a healthy cylinder;
[0035] FIG. 27 illustrates examples of magnitudes of DC link
voltage spectra at one half of the engine speed frequency at
different fueling levels for a weak or degraded cylinder; and
[0036] FIG. 28 illustrates a flowchart of one embodiment of a
method for identifying a weak cylinder in an engine.
DETAILED DESCRIPTION
[0037] Reference will be made below in detail to example
embodiments of the inventive subject matter, examples of which are
illustrated in the accompanying drawings. Wherever possible, the
same reference numerals used throughout the drawings refer to the
same or like parts. Although example embodiments of the inventive
subject matter are described with respect to rail vehicles,
embodiments of the inventive subject matter are also applicable for
use with other vehicles. For example, the vehicles may be
off-highway vehicles designed to perform an operation associated
with a particular industry, such as mining, construction, farming,
etc., and may include haul trucks, cranes, earth moving machines,
mining machines, farming equipment, tractors, material handling
equipment, earth moving equipment, etc. Optionally, the vehicles
may be on-road vehicles, such as automobiles, tractor-trailer rigs,
on-road dump trucks, etc. Moreover, yet other embodiments of the
inventive subject matter are applicable to purely electric vehicles
and machinery, such as battery powered vehicles. The inventive
subject matter can be applicable for marine vehicles also.
[0038] Components in vehicle power assemblies, such as wheel-axle
combinations, suspension systems, trucks, platforms, etc., can
degrade due to various reasons in a variety of different vehicles
(e.g., locomotives, other off-highway vehicles, trucks, cars, sport
utility vehicles, marine vessels, or the like). If the degradation
persists for a long duration, the degradation may lead to failure
of primary components in the power assemblies, and may further lead
to secondary damages. It can be difficult to identify underlying
issues with these components unless inspected or subjected to
specific tests. The inventive subject matter described herein uses
readings from existing sensor or sensors and/or processed
parameters from those sensors, which can be correlated to specific
components. Then, without physical inspection of the component, the
extent of damage (e.g., abnormality, degradation, or change) can be
identified. The inventive subject matter can account for the normal
wear and tear of a vehicle (e.g., a ten-year old car may not behave
or operate in the same way as new or younger car). While the
description herein focuses on locomotives, one or more embodiments
may pertain to other types of vehicles, such as automobiles,
trucks, marine vessels, mining vehicles, or the like.
[0039] The inventive subject matter described herein can provide
early signs of component or assembly degradation (to take
appropriate action) via various modes (examples on the on-board
computer or on a central database, which also can send the wireless
messages to the vehicle owner or other authorized person in case of
unmanned or driver-less vehicles). By noticing the degradation at
an early stage, well planned maintenance or immediate action can be
taken to avoid any severe damage, secondary damages, downtime and,
therefore, saving in related costs.
[0040] One embodiment of the inventive subject matter described
herein examines data from previously existing sensors or sensor
readings and correlates this data to specific components of the
vehicle. The sensors may be pre-existing in that the sensors (or
the data that is output by the sensors, or derived parameters from
one or more sensors or processed parameter from combinations of
those sensors) are used for one or more purposes other than
evaluation of the health of the vehicle or vehicle component. For
example, the sensor or sensor data may be used for control of the
vehicle. The systems and methods described herein can use this
sensor data to evaluate the health of the vehicle or vehicle
component without physical inspection of the component. The extent
of damage, abnormality, degradation, or other change in the
component can be identified from this sensor data.
[0041] Using one or more embodiments of the inventive subject
matter described herein, a forcing function of a known pattern is
generated for a vehicle axle, motor, or propulsion system (e.g.,
the torque generated by engine of car). During normal operation or
with predefined test cases, the performance can be monitored on a
continuous or defined interval basis. Measuring parameters (e.g.,
displacement, speed, acceleration, etc.) from existing sensors
(e.g., a speed sensor) or with special sensors (e.g., a three-axis
accelerometer) can allow for the health of various vehicle
components to be evaluated, or derived parameters from one or more
sensors or processed parameter from combinations of those sensors.
From the measured parameters, evaluating frequency responses,
natural frequency components, damping, rise times, settling times,
absolute/RMS/average magnitude, mean/standard deviation, or any
other such quantity can be determined to evaluate the extent of
degradation of vehicle components. An unhealthy or damaged
condition of a vehicle component can be evaluated by examining the
response of the components to identify deviations in the response
over time, by identifying the difference from a component response
from predefined or designated healthy responses, or by examining
the absolute response of the component. or deviation in specific
parameters within a specific type of vehicles.
[0042] FIG. 1 schematically illustrates an example of a wheel and
axle combination 100 of a locomotive having a locomotive control
system 122. The vehicle is represented by a vehicle platform 102
(e.g., "Locomotive Platform" in FIG. 1) and a truck 108, which can
represent part of a vehicle chassis. The vehicle is moving in a
direction of motion 104 along a route 106 ("Track" in FIG. 1).
While the vehicle and route are indicated in FIG. 1 as being a
locomotive and a track, respectively, not all embodiments of the
inventive subject matter described herein are limited to rail
vehicles. One or more embodiments can be used with automobiles,
off-highway vehicles, or the like.
[0043] A motor 110 having a stator 112 and a rotor 114 rotates an
axle joined to a wheel 116 or directly rotates the wheel 116 to
propel the vehicle along the route. The motor is coupled with the
truck by a primary suspension 124, such as one or more springs,
flexible bodies, or the like, as well as by another coupling 126,
such as a dog bone connection. The truck is coupled with the
platform by a secondary suspension 128, such as one or more
springs, flexible bodies, or the like. These suspensions can at
least partially absorb vibrations and shocks encountered during
movement of the vehicle and/or vibrations of vehicle
components.
[0044] One or more sensors 120 can measure various parameters of
the wheel and axle combination during movement of the vehicle. The
parameters are shown in FIG. 1 and described herein. Parameters l2
and l3 represent linear displacements of the wheel and axle
combination, and the motor, respectively, from the vehicle platform
and/or truck. Parameters .alpha. and .beta. represent angular
displacements of the rotor and wheel, respectively.
[0045] While the vehicle is stationary, any one or any combination
of these parameters causes a finite angular displacement .gamma..
This displacement .gamma. represents relative displacement of the
rotor with respect to the stator of the motor (e.g., a traction
motor). One or more of the changes of these parameters with respect
to time (e.g., the velocities {dot over (l)}2, {dot over (l)}3,
{dot over (.alpha.)}, and {dot over (.beta.)} will cause a
rotational angular rotor velocity {dot over (.gamma.)}:
[0046] While the vehicle is moving (e.g., at a constant speed), the
velocities {dot over (l)}2, {dot over (l)}3, and {dot over
(.alpha.)} should be zero, and the velocities {dot over (.gamma.)}
and {dot over (.beta.)} should be constant. Hardware, software,
operator inputs, external factors may cause one or more of the
velocities {dot over (l)}2, {dot over (l)}3, and {dot over
(.alpha.)} to have a value other than zero. If {dot over (.beta.)}
is constant, then the velocity {dot over (.gamma.)} may no longer
have a zero value. If the velocities {dot over (l)}2, {dot over
(l)}3, and {dot over (.alpha.)} are oscillatory in nature and the
velocity {dot over (.beta.)} is constant, then the rotor velocity
{dot over (.gamma.)} will be oscillatory.
[0047] In one embodiment of the inventive subject matter, a
locomotive control system 122 of the vehicle has a controller 118
and the sensors 120 that measure motor phase voltage and phase
current of electric energy supplied to the motor, and rotor speed
(e.g., {dot over (.gamma.)}) as feedbacks for motor control. The
controller can be formed from hardware circuitry that includes
and/or is connected with one or more processors (e.g., one or more
microprocessors, field programmable gate arrays, and/or integrated
circuits) that perform operations described herein. The sensors can
include a voltage and/or current sensor that measures the phase
voltage and current supplied to the motor, as well as the rotor
speed. The controller optionally can also measure the speed at
which the wheel rotates (e.g., for speed control of the vehicle),
but due to various constraints, it may not be feasible to measure
the actual speed of the wheel. Instead, the controller can monitor
the rotor speed and then scale the rotor speed to estimate the
wheel speed.
[0048] If oscillation is present in the rotor speed (e.g., due to
external factors), disturbance or noise will also appear in the
estimated wheel speed that is monitored by the controller. If the
wheel speed does not have disturbances, but the rotor speed that is
monitored by the controller does have noise (e.g., due to
disturbances caused by changes in the velocities {dot over (l)}2,
{dot over (l)}3, and {dot over (.alpha.)}), then the wheel speed
that is monitored by the controller will have a scaled component of
this noise.
[0049] The controller may take corrective action if the disturbance
in wheel speed is detected (e.g., due to wheel slip or excessive
acceleration). But, if noise in the wheel speed is caused by
oscillation in the rotor speed (and the noise is not identified as
caused by the rotor speed oscillation), then the controller may
incorrectly implement the corrective action. This can degrade
performance of the vehicle, such as by reducing or losing adhesion
of the wheel to the route, causing motor torque to pulsate, and/or
vibration of the actuating parameter having a frequency of
variation that matches the system spring-mass frequency.
[0050] An actuating parameter of a vehicle is work or other energy
that is output by a propulsion system of the vehicle. Examples of
actuating parameters are provided herein, and include motor torque,
power, speed, pulling force, tractive effort generated by the
propulsion system, (e) speed of the locomotive, and/or (f) an
opposing force to generated torque of the propulsion system.
[0051] In one embodiment, the frequency or range of frequencies of
the wheel and axle combination frequencies may need to be
identified for the controller to suppress or reduce the wheel and
axle combination frequencies that interfere with the speed sensor.
While these frequencies can be identified by the controller and
sensors measuring the displacements and velocities described above
while the vehicle operates at various known or designated speeds
and motor torque combinations, this can be a time consuming and
costly endeavor.
[0052] FIG. 1 is just an example of a single wheel axle of a
locomotive. But the inventive subject matter described herein can
be extended for any other type truck/axle/platform arrangement, and
may be used for any other vehicle having (a) one or more axles
under same truck and/or platform, (b) the spring damper with each
axle may have none, single or multiple or combination of those
spring damper arrangement, (c) a motor-axle transmission of a
direct drive or geared (single or multi-stage gear) type, (d)
propulsion components other than a wheel-axle system.
[0053] Instead, in at least one embodiment of the inventive subject
matter described herein, the controller may direct a vehicle
propulsion system (e.g., an engine in a vehicle having
engine-driven axles, or an electrical propulsion system in case a
vehicle having electrical motor driven axles) to generate
incremental torque pulses. These torque pulses can have different
designated pulse widths and can be applied by the propulsion system
on an axle in a particular or designated sequence. The controller
can select a combination of torque pulse widths and sequences can
be a pseudo random binary sequence (PRBS) or another type of
sequence.
[0054] In a vehicle having axles and/or wheels directly driven from
the propulsion system, the controller can direct the propulsion
system to apply the torque pulse sequence, and for motor driven
system, the motor can apply the torque pulse sequence on top of
(superimposed on) the actual torque generated to propel the
vehicle. With the total torque (torque pulses plus propulsion
torque) applied by an actuator of the propulsion system (e.g., an
engine or motor or any similar system), the controller acquires
data from the sensor(s). The controller compares the gain of the
speed or torque for different frequency components, and can
identify which frequency components have greater gain(s). These
frequency components can then be attenuated by the controller
applying one or more filters, such as a Kalman filter or another
filter that attenuates noise in the measured rotor speeds). This
can help eliminate or reduce noise from the motor or speeds of the
propulsion system or torques measured by the sensors.
[0055] During normal operation (e.g., operation of a vehicle having
healthy components), the controller can monitor the torques
generated by the propulsion system or generated motor torques and
speeds on a continuous basis, defined interval basis, or other
repeating basis. The torques and speeds can be monitored based on
data generated by the sensors. The sensors can measure displacement
or other movement, speeds (engine, wheel, motor, gear, etc.),
acceleration, etc. The controller can then calculate the frequency
response, the natural frequency component, dampening, rise time,
settling time, absolute magnitude, root mean square value of the
magnitude, average magnitude, mean, standard deviation, or other
calculation of the engine or motor or wheel torques and/or speeds
as one or more derived quantities. The derived quantities can be
used to estimate or quantify degradation of the engine, axle,
wheel, and/or interconnecting gears (e.g., the transmission). This
method can be extended to vehicles with any other actuating
parameter (in place of torque), such as power, speed, pulling force
or any similar.
[0056] For example, the controller can compare one or more of the
derived quantities with derived quantities of a vehicle known to be
healthy to identify differences (if any). As another example, the
controller can compare one or more of the derived quantities with
derived quantities of a set or fleet of vehicles to identify
differences (if any). As another example, the controller can
monitor the derived quantities of the same vehicle over time to
track changes over time or the controller can monitor the derived
quantities of the combination of a set of vehicles and of same
vehicle over time to track changes in any components.
[0057] In one embodiment, the controller can generate and/or look
out for one or more forcing functions of known patterns for an axle
or motor of the vehicle. In one example, this forcing function is a
relationship between a speed at which the propulsion system
operates and resultant torque. Three variations on the forcing
functions can exist. First, a forcing function can be a designated
forcing function that designates or predefines operating settings
or outputs of the propulsion system. With a designated forcing
function, the controller of the vehicle can direct the propulsion
system to operate at designated settings or outputs dictated or
defined by the forcing function. Second, a forcing function can be
a naturally occurring or uncontrolled forcing function, where the
controller of the vehicle monitors operations of the propulsion
system to determine when these operates match or coincide with
designated settings or outputs dictated or defined by the forcing
function. This type of forcing function is not created by the
controller, but is identified by the controller when the vehicle
operates in a defined, designated way. For example, the controller
can monitor the torque generated by a motor to determine when the
torque is within predefined limits (e.g., fifty to sixty percent of
a maximum torque that can be generated by the motor) during travel.
The controller can examine sensor data (or processed sensor data)
that is obtained or indicative of sensed information during the
same time period that the torque was within these predefined
limits. Third, a forcing function can be a combination forcing
function, which is a union or mix of the first and second types of
forcing function. This third forcing function can involve the
controller monitoring operations of the vehicle to determine when
the operations of the propulsion system match, coincide with, or
otherwise fall within a defined range and, responsive to this
occurring, the controller can change movement of the vehicle (such
as by directing the propulsion system to operate in a predefined or
designated manner). For example, the controller can monitor the
torque generated by a motor to determine when the torque is at 50%
of the maximum torque that the motor can generate. Responsive to
identifying this torque output, the controller can direct the motor
to generate a 1 hertz torque waveform superimposed on the 50%
torque output as the forcing function.
[0058] FIG. 2 illustrates several examples of torque and speed
relationships 200, 202, 204, 206, 208, 210 for a healthy vehicle as
measured by the sensors shown in FIG. 2. The torque and speed
relationships are shown alongside a horizontal axis 212
representative of operating speed of the propulsion system and a
vertical axis 214 representative of torque. The first relationship
202 shows the relationship between torque and speed for the
propulsion system of the vehicle, and can be referred to as the
propulsion system relationship. The second through fifth
relationships 202, 204, 206, 208, 210 show the relationships
between the gear torques and the speed for first through fifth
gears of the transmission of the healthy vehicle, respectively.
[0059] Each of the torque and speed relationships can be determined
from the controller using a forcing function of a known pattern.
The pattern can be torque that changes during normal operation of
the vehicle, torque that changes in steps (e.g., step responses),
torque that changes according to sine pulses, etc. The controller
can use the forcing function regardless of the type or weight of
the load carried by the vehicle (e.g., light load, heavy load, no
load, etc.).
[0060] FIG. 3 illustrates one example of a comparison between
torque and speed relationships as measured by the sensors shown in
FIG. 2. As shown in FIG. 3, the controller monitors a torque and
propulsion system speed relationship 304 for a vehicle while the
vehicle operates in fourth gear. The controller compares this
relationship 304 with the relationship 204 of a healthy vehicle
(the same or different vehicle) and identifies differences between
the relationships 204, 304. These differences can indicate to the
controller that there is a component of the vehicle used while the
vehicle operates in fourth gear that is degrading or otherwise in
need of repair or replacement.
[0061] FIGS. 4 and 5 illustrate other examples of comparisons
between torque and speed relationships as measured by the sensors
shown in FIG. 2. The controller can obtain the measured torques and
speeds from the sensors onboard the same vehicle over time. The
torque and speed relationships 400, 402, 404, 406, 408, 410 shown
in FIG. 4 represent the relationships between the gear torques and
the propulsion system speed for the engine (relationship 400) and
for first through fifth gears of the transmission of the vehicle
(relationships 402, 404, 406, 408, 410, respectively). The torque
and speed relationships 500, 502, 504, 506, 508, 510 shown in FIG.
5 represent the relationships between the gear torques and the
speed for the propulsion system (relationship 500) and for first
through fifth gears of the transmission of the vehicle
(relationships 502, 504, 506, 508, 510, respectively). The
relationships shown in FIGS. 4 and 5 may be obtained from data of
the same vehicle (e.g., at different times), or from different
vehicles.
[0062] The controller can examine the sensor data points forming
the relationships shown in FIGS. 4 and 5 and determine that there
is a wider range of measured torques in the relationships shown in
FIG. 5. For example, the data points making up the relationships
shown in FIG. 5 extend over a wider range of torques for each or
several of the propulsion system speeds. This can indicate that the
propulsion system (e.g., the wheel and axle combination, and motor)
of the vehicle associated with the relationships shown in FIG. 5
may have degraded from an earlier time associated with the
relationships shown in FIG. 4, or that the vehicle associated with
the relationships shown in FIG. 5 has a more degraded propulsion
system than the vehicle associated with the relationships shown in
FIG. 4.
[0063] FIG. 6 illustrates engine or motor torques 600 and
transmission torques 602 of a vehicle as measured by the sensors
shown in FIG. 1. The motor/engine torques and transmission torques
are shown alongside a horizontal axis 604 representative of time
and vertical axes 606, 608 representative of magnitudes of
generated torque. The transmission torques decrease in steps at
different times. Each step decrease indicates that the vehicle has
shifted gears to a higher gear. The motor/engine torques similarly
have step changes at corresponding times, also indicating a change
in gears of the vehicle.
[0064] FIGS. 7 and 8 illustrate moving speeds 700, 800 of vehicles
as measured by one or more of the sensors shown in FIG. 1. The
moving speeds can be measured as the vehicle changes gears as shown
in FIG. 6. For example, the moving speeds shown in FIG. 7 can be
measured for the vehicle that changes gears at the same times shown
in FIG. 6. The moving speeds shown in FIG. 8 can be measured for
the vehicle that changes gears at the same times shown in FIG. 6.
The moving speeds shown in FIGS. 7 and 8 are shown alongside the
horizontal axis 604 and a vertical axis 706 representative of
vehicle speeds.
[0065] The controller can examine the moving speeds and identify
oscillations 702, 802 in the speeds at or around the same times
that the vehicle shifts gears. The magnitude of the oscillations
can indicate whether the vehicle is healthy or in need of repair.
For example, the magnitude of the oscillations shown in FIG. 7 may
be examined by the controller and determine to not exceed one or
more thresholds, while the magnitude of the oscillations shown in
FIG. 8 may be examined by the controller and determine to exceed
one or more thresholds. The controller can determine that the
vehicle associated with the oscillations shown in FIG. 8 needs
repair and/or one or more components of the vehicle need
replacement.
[0066] FIGS. 9 and 10 illustrate braking efforts or forces 909,
moving speeds 1001 of the vehicle, and wheel speeds 1009 of the
wheel while braking according to one example. The braking efforts,
moving speeds, and wheel speeds can be measured by the sensors of
the control system as the vehicle brakes to slow down and stop from
a moving state. The braking efforts are shown alongside a
horizontal axis 905 representative of time and a vertical axis 907
representative of magnitudes of braking efforts. The moving and
wheel speeds are shown alongside the horizontal axis 905 and a
vertical axis 1007 representative of speeds.
[0067] Also shown in FIGS. 9 and 10 are designated braking efforts
901 and designated wheel speeds 1003. The controller can obtain the
braking efforts, moving speeds, and wheel speeds from the sensors
as the vehicle is engaging in the forcing function of braking. The
controller can compare the braking efforts to the designated
braking efforts and the wheel speeds to the designated wheel speeds
to determine if the brakes are degraded. In the illustrated
examples, because the braking effort oscillates, is not constant,
and varies from the designated braking effort, and/or because the
wheel speeds oscillate and/or vary from the designated wheel
speeds, the controller can determine that one or more components of
the brakes of the vehicle are degraded and need repair or
replacement.
[0068] FIG. 11 illustrates examples of torque references 900 and
measured torques 902 of the motor in the vehicle shown in FIG. 1.
FIG. 12 illustrates rotor speeds 1002 of the motor in the vehicle
shown in FIG. 1. The measured torques and rotor speeds can be
measured by the sensors shown in FIG. 1. The torque references
represent the sequence of torque pulses that the controller directs
the motor to generate, as described above. The torque references
and measured torques are shown in FIG. 11 alongside a horizontal
axis 904 representative of time and a vertical axis 906
representative of motor torques. The rotor speeds are shown
alongside the horizontal axis 904 and a vertical axis 1006
representative of rotational speeds of the motor.
[0069] The controller can select the sequence of torque reference
pulses from among several different sequences, with each sequence
associated with a different frequency range of interest that is to
be applied to a component of the vehicle under examination. The
controller can compare the applied frequencies and the frequencies
of sensor data of a measured parameter of the vehicle in the
frequency domain to determine the health of a vehicle component or
the vehicle itself. For example, the controller can compare the
frequencies of the torque applied by the motor (according to the
torque pulse sequence directed by the controller) with the
frequencies of the speed at which the motor operates.
[0070] FIG. 13 illustrates one example of an engine speed or drive
train spectrum 1100 and a wheel speed spectrum 1102. The engine
speed or drive train and wheel speed spectra are shown along a
horizontal axis 1104 representative of different frequencies and a
vertical axis 1106 representative of magnitudes of the engine speed
or drive train spectrum and the wheel speed spectrum. The
controller can generate or otherwise determine the engine speed or
drive train and wheel speed spectra based on parameters sensed by
the sensors shown in FIG. 1. The controller can examine the spectra
at one or more expected or designated frequencies to determine if
the magnitude of the spectra at the designated frequencies exceed a
predefined upper limit. For example, the wheel speed spectra can be
associated with a limit of zero decibels at a frequency of twenty
radians per second and the engine speed spectra can be associated
with a limit of forty decibels at a frequency of sixty radians per
second. The actuating parameter which is generated by the engine or
drive train can be extended to any other source (such as, motor or
any prime mover with single or multi-stage gear). The spectrum of
actuating quantity can be replaced with magnitude, RMS value,
average value or any other mathematical quantification.
[0071] The controller can examine the engine speed and wheel speed
spectra and determine if either spectrum exceeds a limit at an
associated frequency. If a spectrum exceeds the limit, then the
controller can determine that the corresponding vehicle component
is degrading or needs repair or replacement. For example, the
controller can determine that the wheel speed spectrum does not
exceed the limit of zero decibels at twenty radians per second, but
that the engine speed spectrum does exceed the limit of forty
decibels at sixty radians per second. The controller can then
determine that the motor has degraded and needs repair or
replacement. Responsive to determining that a component needs
repair or replacement, the controller can then generate one or more
signals that direct an output device to notify an operator of the
vehicle of the unhealthy component, and/or that direct another
system (e.g., an automated robotic system) to repair, replace, or
obtain a replacement of the unhealthy component. Optionally,
responsive to determining that a component needs repair or
replacement, the controller can change movement of the vehicle,
such as by automatically slowing or stopping movement of the
vehicle.
[0072] FIG. 14 illustrates a flowchart of one embodiment a method
1200 for evaluating vehicle health. The method 1200 can be
performed by the controller to determine whether one or more
vehicle components have degraded and need repair or replacement
without stopping operation of the vehicle or taking apart the
vehicle. The method 1200 also can identify degraded components
without requiring additional sensors be added to the vehicle.
[0073] At 1202, performance of one or more vehicle components are
monitored. For example, existing speed sensors can be used to
monitor parameters such as motor rotor speeds (which can be used to
determine estimated wheel speeds), the amount of torque generated
by a motor, etc.
[0074] At 1204, one or more quantities are derived from the
monitored parameters. For example, the frequency response of the
parameters, one or more frequency components of the parameters, or
the like, can be determined from the parameters. At 1206, the
derived quantity or quantities are evaluated. This evaluation can
include comparing the derived quantity with a designated value of
the quantity. This designated value can be indicative of a healthy
vehicle or healthy component of the vehicle. Optionally, the
evaluation can include comparing the derived quantity with a
derived quantity that is calculated from plural vehicles. For
example, the derived quantity can be compared with a root mean
square, average, median, or the like, of the same quantity but
measured for a fleet of vehicles. As another example, the derived
quantity can be monitored over time to see how the quantity changes
with respect to time.
[0075] At 1208, a determination is made as to whether the derived
quantity indicates an unhealthy (e.g., degraded) vehicle or vehicle
component. For example, if the derived quantity deviates from the
designated value, the same quantity determined for a group of
vehicles, or changes in a negative manner over time, then the
derived quantity can indicate a degraded component of the vehicle.
As another example, if the derived quantity exceeds or falls below
an associated limit or threshold, then the derived quantity can
indicate a degraded vehicle component. If the derived quantity
indicates a degraded component of a vehicle, then flow of the
method 1200 can proceed toward 1210. Otherwise, the method 1200 can
return toward 1202 or may terminate. At 1210, the vehicle is
repaired. For example, the component can be repaired or replaced in
response to determining that the derived quantity indicates that
the component has degraded.
[0076] One embodiment of the inventive subject matter described
herein provides a computerized system and method that identifies
early degradation in the health of various components of vehicles
by acquiring data from sensors with known forcing functions.
Measurements of the health of vehicle components can be determined
by measuring sensor outputs using on-board and/or off-board
computer systems with known forcing functions, and comparing the
sensor inputs with available baseline values. Based on and/or
responsive to measuring the health of one or more components, the
system or method can automatically repair and/or replace one or
more components.
[0077] The health of various components of axles, trucks,
platforms, etc., of vehicles is monitored with known operating
conditions and modes. The known operating conditions can be
designated speeds, motor torques, tractive efforts, engine speeds,
power generated, etc. The known operating modes include a motoring
mode, a braking mode, a coasting mode (where the vehicle is moving
without tractive effort or braking effort being generated), etc.
The known operating conditions or modes provide measures of a
forcing function of the vehicle. When a particular forcing function
is generated or reached (e.g., during normal operation as opposed
to a testing operation of the vehicle), various parameters such as
engine speed or displacement of any particular location on a
three-dimensional plane or corresponding acceleration are measured
using available sensors.
[0078] The sensor inputs are acquired (with on-board computer or
separate data acquisition system) and processed (e.g., using a fast
Fourier transform, calculating a root mean square value, average,
study of one or more patterns of sensor data, etc.). Deviation of
one or more of these processed parameters from a designated healthy
value, a previously calculated value, and/or values of a fleet of
vehicles is determined. Based on this deviation, a determination of
whether one or more components of the vehicle need to be repaired
or replaced, and a repair of the vehicle or replacement of a part
can be automatically performed.
[0079] In one embodiment, a complete physical model of the vehicle
or vehicle component can be derived. From this model, axle
combination dynamics, axle-to-axle interactions, or the like, can
be modeled on a very detailed level and the possible interaction of
these dynamics on sensor at various locations can be determined.
The forcing function can be various types, such as multiple pulses
of various frequency range, step function, sine or cosine function,
or any other pattern. With the forcing function, the sensors may be
of different types measuring different type of movement (rotational
or linear, displacement, velocity or acceleration, etc.)
[0080] Many vehicle components are not easily accessible or may not
be easily inspected, which can make it difficult to determine signs
of degradation. With the systems and methods described herein,
determination of early degradation of such components are possible,
and the repair or replacement can be optimally scheduled to save
cost and downtime.
[0081] Returning to the description of the wheel and axle
combination of the vehicle shown in FIG. 1, the movements of one or
more components of the vehicle can be monitored over time by the
controller to determine whether an absolute value of the magnitude
and/or frequency of any of these movements exceed designated
thresholds or limits while the vehicle operates within one or more
operating conditions. The controller can use a model of the wheel
and axle combination that represents each of the suspensions as a
separate spring damper. In the model, each component can be
associated with a natural frequency of movement that is actuated at
one or more operating points or conditions of the vehicle.
[0082] FIG. 15 illustrates another example of an engine speed
spectrum 1300. This engine speed spectrum can be generated or
determined by the controller examining rotor speeds sensed by one
or more of the sensors shown in FIG. 1. The controller can
transform the rotor speeds measured by the sensors from the time
domain to the frequency domain using a fast Fourier transform or
another transform. The spectrum shown in FIG. 15 is shown alongside
a horizontal axis 1302 representative of frequencies and a vertical
axis 1304 representative of magnitudes of the rotor speeds.
[0083] The controller can examine the engine speed spectrum 1300
and identify one or more peaks 1306, 1308, 1310 at one or more
associated frequencies. These peaks and the magnitudes of the peaks
can be the derived quantities referred to above and that are used
to evaluate the health of vehicle components. The controller may be
programmed or otherwise provided with certain designated
frequencies that are associated with natural frequencies of
movement of one or more of the suspensions. For example, the
primary suspension 124 shown in FIG. 1 may be associated with a
first designated frequency that is the same frequency at which the
first peak 1306 appears. The controller can determine from this
correspondence that the first peak 1306 indicates movement of the
primary suspension, and is not due to wear or degradation of the
wheel and axle combination. The second peak 1308 occurs at a
frequency that is not associated with any designated frequency of a
known component. Therefore, the controller can identify the
presence of the second peak 1308 as indicating degradation of some
component of the wheel and axle combination. The third peak 1310
occurs at a designated frequency associated with torsional
vibration of the wheel and/or axle.
[0084] For the first and third peaks that occur at designated
frequencies associated with components of the vehicle, the
controller can determine if the magnitude of these peaks exceeds
one or more designated threshold or limits associated with the
corresponding components. For example, the controller can compare
the first peak with one upper limit and can compare the third peak
with another upper limit. If the first peak exceeds the
corresponding limit, then the controller determines that the
primary suspension has degraded or is otherwise in need of repair
or replacement. If the third peak exceeds the corresponding limit,
then the controller determines that the wheel and/or axle has
degraded or is otherwise in need of repair or replacement.
[0085] In one embodiment, at least one of the sensors shown in FIG.
1 can be a displacement or distance sensor that measures how far a
suspension (e.g., the secondary suspension also shown in FIG. 1) is
compressed. The compression distance of a suspension can be
provided from the sensors to the controller as a parameter of the
wheel and axle combination, and can be examined to determine the
health or degradation state of the suspension.
[0086] FIG. 16 illustrates one example of a forcing function 1400.
The forcing function represents torque applied by a motor to a
first wheel and axle combination of the vehicle. FIG. 17
illustrates three examples of sensed changes in length 1500, 1502,
1504 of the secondary suspension in the first wheel and axle
combination of the vehicle in response to implementation of the
forcing function shown in FIG. 16. FIG. 18 illustrates one example
of sensed changes in length 1600 of a secondary suspension in
another wheel and axle combination of the same vehicle in response
to implementation of the forcing function shown in FIG. 16.
[0087] The forcing function and the changes in length of the
secondary suspensions shown in FIGS. 16 through 18 are shown
alongside horizontal axes 1406 representative of time. The forcing
function also is shown alongside a vertical axis 1408
representative of torque generated by motors that rotate the axles
in the first and second wheel and axle combinations. The sensed
changes in length shown in FIG. 17 are shown alongside a vertical
axis 1508 representative of how far the secondary suspension for
the first wheel and axle combination is compressed. The sensed
changes in length shown in FIG. 18 are shown alongside a vertical
axis 1608 representative of how far the secondary suspension for
the first wheel and axle combination is compressed.
[0088] The forcing function shown in FIG. 16 indicates that the
controller directed the motors to increase the torque generated by
the motors at a time t.sub.0. The controller can monitor the
changes in secondary suspension lengths monitored by the sensors
and as shown in FIGS. 17 and 18. The first changes in length 1500
shown in FIG. 17 can be examined by the controller to identify
degradation in the secondary suspension of the first wheel and axle
combination. For example, the first changes in length increase
following the increase in torque generated by the motor at the time
t.sub.0, but the first changes in length remain at or below an
upper threshold or limit 1510. The controller can then determine
that the secondary suspension of the first wheel and axle
combination is not damaged or degraded to the state where repair or
replacement is needed.
[0089] In another example, however, the different, second changes
in length 1502 indicate how the secondary suspension in the first
wheel and axle combination is compressed following generation of
the torque according to the forcing function. The controller can
examine the second changes in length and determine that these
changes in length increase to a rounded peak and then decrease to
the upper threshold or limit following generation of the torque at
the time t.sub.0. Or, the third changes in length 1504 can indicate
how the secondary suspension in the first wheel and axle
combination is compressed following generation of the torque
according to the forcing function. The controller can examine the
third changes in length and determine that these changes in length
increase to a plateau above the upper threshold or limit, and then
decrease to the upper threshold or limit following generation of
the torque at the time t.sub.0.
[0090] The controller can examine the third changes in length 1504
and determine that the increase of the changes in length of the
secondary suspension above the threshold or limit indicate that the
secondary suspension is degraded, and can determine that the
secondary suspension is severely degraded due to the changes in
length increasing to a maximum (e.g., the plateau) before
decreasing. But, the controller can examine the second changes in
length 1502 and determine that the increase of the changes in
length of the secondary suspension above the threshold or limit
indicate that the secondary suspension is degraded, but not as
degraded as the third changes in length 1504 would otherwise
indicate due to the second changes in length 1502 not increasing to
the maximum plateau.
[0091] The controller can examine the changes in length 1600 of the
secondary suspension in the second wheel and axle combination and
determine that the way in which the changes in length 1600 vary
after the time t.sub.0 that the torque is generated indicates
degradation of the secondary suspension. For example, even though
the changes in length 1600 do not increase to a maximum plateau and
does not increase above the threshold 1510, the variations in the
secondary suspension (for a wheel and axle combination other than
the wheel and axle combination having the motor that applied the
torque) can indicate degradation in the secondary suspension of the
other wheel and axle combination.
[0092] One or more additional embodiments of the inventive subject
matter described herein can be used to evaluate the health or
predict the failure of one or more cylinders in an engine. A
computerized system that is onboard a vehicle can have a first
computing unit (e.g., processor or group of processors) that
operates as a supervisory control of the vehicle (e.g., to
automatically control one or more functions of the vehicle) and one
or more additional second computing units operating to execute an
engine cylinder failure detection algorithm. The first computing
unit can be referred to herein as a supervisory controller and the
second computing unit(s) can be referred to herein as monitoring
controllers. Each unit and/or controller can be formed from
hardware circuitry that includes and/or is connected with one or
more processors (e.g., one or more microprocessors, field
programmable gate arrays, and/or integrated circuits) that perform
the associated functions or operations described herein.
[0093] The supervisory controller checks for allowable system
conditions (e.g., vehicle speed, motor torque, a designated sample
time, etc.) to enable execution of the engine cylinder failure
detection algorithm by the monitoring controller(s). Upon execution
of this algorithm, the monitoring controller obtains a signal
(e.g., a direct current link voltage of the rectified output of
alternator driven by the engine), which can have the signature of a
single or multiple engine cylinder failure. The monitoring
controller can perform a data validity check, and evaluate
0.5.times. engine frequency components from the frequency spectrum
of the direct current link voltage (or any other multiple of engine
frequency or engine speed or other parameters). If specific
frequency component magnitudes are higher than a predefined
threshold, then engine unbalance is detected, and one or more
cylinders of the engine can be identified as needing repair. In one
embodiment, repair of the engine can then be automatically
implemented.
[0094] FIG. 19 schematically illustrates another embodiment of the
control system 122 shown in FIG. 1. The control system includes the
controller 118 shown in FIG. 1 and two sensors 1700, 1702 of the
sensors 120 shown in FIG. 1. Also shown in FIG. 19 are an engine
1704, an alternator (or generator) 1706 coupled with the engine,
and power electronics or circuitry 1708 that conducts electric
current generated by the alternator to the motors 110 of the
vehicle. The sensor 1700 represents a speed sensor that measures
how rapidly the engine operates and the sensor 1702 represents a
direct current link sensor that measures the electric current
conducted from the alternator and/or through the power electronics
to the motor(s) of the vehicle.
[0095] FIG. 20 illustrates operation of the control system 122
shown in FIG. 19. The controller 118 can include a supervisory
control unit 1800, several computing units 1802, 1804, 1806, and an
engine control unit 1808. Each of the units 1800, 1802, 1804, 1806,
1808 can represent the same or separate hardware circuitry that
includes and/or is connected with one or more of the same or
different processors. The units 1800, 1802, 1804, 1806, 1808
perform the functions or operations described herein. While three
computing units 1802, 1804, 1806 are shown, optionally, there may
be a single computing unit, two computing units, or more than three
computing units. The control system can be entirely disposed
onboard a vehicle, or one or more components (e.g., the computing
units) can be disposed off-board the vehicle.
[0096] In operation, the supervisory control unit receives sensor
data 1810 from the sensors to determine whether the operational
conditions of the engine and/or motor are acceptable (e.g., within
designated limits). For example, the supervisory control unit can
monitor the speed of the engine to determine whether the sensor
data is within predefined limits. Optionally, the supervisory
control unit can receive other sensor data to determine if the
sensor data is within acceptable limits, such as the torque created
by one or more motors, the sample time (e.g., whether there is
sufficient time to acquire and evaluate sensor data), or other
sensor data. If the sensor data indicates acceptable operating
conditions, then the supervisory control unit can communicate a
trigger signal 1812 to one or more of the computing units to
initiate an algorithm or process for evaluating cylinders of the
engine. The supervisory control unit also can communicate the same
or a similar trigger signal to the engine control unit to inform
the engine control unit when the cylinders are to be evaluated.
Otherwise, the supervisory control unit does not communicate the
trigger signal.
[0097] Responsive to receiving the trigger signal, the computing
unit(s) obtain or capture sensor data 1814 from the DC link sensor.
This sensor data can represent direct current link voltage sensed
from the power electronics. The sensor data from the DC link sensor
can indicate failure of one or more cylinders of the engine, as
described herein. For example, the computing unit(s) in receipt of
the DC link sensor data can examine spectrum analysis by evaluating
the frequency components of the DC link voltage at one or more
frequencies, such as at one half of the frequency at which the
engine is operating (e.g., half the speed of the engine operating
speed). If the magnitude of the DC link voltage at the one or more
frequencies (e.g., 0.5 of the engine frequency component) exceeds
one or more previously defined thresholds or upper limits, then the
DC link voltage can indicate degradation, damage, or failure of one
or more cylinders in the engine. The thresholds or limits can
include the magnitude of one half the engine frequency component
when the same cylinder is cut out and no other cylinder is faulty
(as previously measured), the magnitude of one half the engine
frequency component when no cylinder is cut out and no other
cylinder is faulty (as previously measured), and/or the magnitude
of one half the engine frequency component when the same cylinder
was last examined. The computing unit(s) that detected the cylinder
failure can communicate a failure signal 1816 to the supervisory
control unit. In one embodiment, a different computing unit can be
dedicated to examining the frequency component(s) from a different
cylinder.
[0098] To identify which cylinder of the engine has failed, the
engine control unit can sequentially cut out individual cylinders
of the engine and can communicate a cut-out signal 1818 to the
supervisory control unit that indicates which cylinder of the
cylinders in the engine is or will be cut-out. A cylinder can be
cut-out by not injecting fuel into the cylinder and thereby
preventing combustion within that cylinder, while other cylinders
(that are not cut out) continue to receive fuel and combust
fuel-and-air mixtures in the cylinders. The supervisory control
unit then communicates the trigger signal to one of more of the
computing units, as described above. The computing units perform
the spectrum analysis described above with each cylinder being cut
out at different times to determine which cylinder has failed.
[0099] FIG. 21 illustrates one embodiment of a timing diagram for
examination of the cylinders of the engine. The timing diagram
defines a sequence of several time periods shown alongside (e.g.,
above) a common timeline 1900. The sequence includes a cylinder
cut-out pattern 1902 that indicates when each cylinder of the
engine is cut out. For example, the raised portions of the cylinder
cut-out pattern indicate that a cylinder is cut out, with the
identity of the cylinder indicated by CC1, CC2, and so on. In the
illustrated embodiment, the engine includes twelve cylinders, but
optionally can include fewer or more cylinders.
[0100] A trigger pattern 1904 of the sequence indicates when the
trigger signal is sent from the supervisory control unit to the
computing unit(s) to begin examination of the data from the DC link
sensor. The raised portions of the trigger pattern indicate when
the trigger signal is sent to a different computing unit, with the
notations SCT1, SCT2, and so on, indicating which computing unit
receives the trigger signal.
[0101] A data acquisition pattern 1906 of the sequence indicates
when a computing unit acquires data from the DC link sensor while a
cylinder is cut out. The data acquisition pattern includes shorter
shapes that extend over part of the timeline to indicate when the
DC link sensor data is obtained by the computing unit. The
notations DA1-1, DA1-7, DA2-8, and so on, indicate which computing
unit is obtaining the DC link sensor data and which cylinder is cut
out. For example, DA3-9 indicates that the third computing unit is
acquiring DC link sensor data while the ninth cylinder of the
engine is cut out.
[0102] A spectrum analysis pattern 1908 of the sequence indicates
when a computing unit is analyzing the spectrum of the DC link
sensor data, as described above. The spectrum analysis pattern
includes elongated shapes that extend over part of the timeline to
indicate when the computing unit is examining the spectrum of the
DC link sensor data acquired while a cylinder is cut out. The
notations SA1-1, SA1-7, SA2-8, and so on, indicate which computing
unit is examining the spectrum of the DC link sensor data and which
cylinder is cut out. For example, SA3-9 indicates that the third
computing unit is examining the spectrum of the DC link sensor data
while the ninth cylinder of the engine is cut out.
[0103] As shown by the sequence in FIG. 21, different cylinders are
cut out at different times, but the acquisition of sensor data and
analysis of the sensor data can be performed during overlapping
time periods by different computing units.
[0104] The analysis of the sensor data spectrum can be performed in
a variety of manners to determine whether a cylinder of an engine
is degraded, faulty, or otherwise not working, and/or to identify
which cylinder of the engine is degraded, faulty, or otherwise not
working. In one embodiment, the computing unit examines the
magnitude at one-half of the frequency of the engine speed in the
spectrum of DC link voltages measured by the DC link sensor. The
magnitude of the spectrum at this frequency is the vector sum of
the magnitude caused by a potentially weak, damaged, or otherwise
degraded cylinder and the magnitude caused by the cylinder that has
been cut out.
[0105] FIG. 22 illustrates one example of a spatial representation
2000 of a cylinder firing sequence of the engine shown in FIG. 19
when a first cylinder of the engine is cut out and a twelfth
cylinder of the same engine is weak (e.g., faulty, damaged, or
degraded). The spatial representation includes several axes 2002
that radially extend from a common location and that each represent
magnitudes of the frequency response of the DC link sensor data for
a different cylinder. A vector 2004 represents the magnitude of the
frequency in the DC link spectrum at one half the engine speed when
the first cylinder ("cyl1" in FIG. 22) is cut out and the twelfth
cylinder ("cyl12" in FIG. 22) is weak. The vector 2004 is the
combination of a vector 2006 along the axis associated with the
magnitude of the spectrum at one half of the engine frequency for
the first cylinder and another vector 2008 along the axis
associated with the magnitude of the spectrum at one half of the
engine frequency for the twelfth cylinder.
[0106] FIG. 23 illustrates one example of a magnitude 2100 of the
DC link voltage data spectrum at one half the frequency of the
engine speed when a healthy (not weak) cylinder is cut out and no
other cylinder of the engine is weak. FIG. 24 illustrates one
example of a magnitude 2200 of the DC link voltage data spectrum at
one half the frequency of the engine speed when a healthy cylinder
is cut out and another cylinder of the engine is weak. FIG. 25
illustrates one example of a magnitude 2300 of the DC link voltage
data spectrum at one half the frequency of the engine speed when a
weak cylinder is cut out. The magnitudes shown in FIGS. 23 through
25 are shown alongside a horizontal axis 2102 representative of
frequencies of the DC link sensor data spectrum and a vertical axis
2104 representative of magnitudes of the frequency in the DC link
sensor data spectrum at a frequency that is one half of the engine
frequency (or speed). Also shown in FIGS. 23 through 25 is a
designated threshold or limit 2106, which indicates a faulty or
weak cylinder.
[0107] The computing unit examining the sensor data spectrum can
examine the magnitude shown in FIG. 25 and determine that the
cylinder from which the sensor data is obtained is not a weak
cylinder because this magnitude does not exceed the designated
threshold. But, the computing unit examining the sensor data
spectrum can examine the magnitude shown in FIG. 26 and determine
that the cylinder is a weak cylinder because this magnitude does
exceed the designated threshold. The computing unit examining the
sensor data spectrum can examine the magnitude shown in FIG. 27 and
determine that the cylinder is the cylinder that was cut out
because the magnitude far exceeds the designated threshold (e.g.,
by more than the magnitude shown in FIG. 26 and associated with the
weak cylinder). The magnitudes of the spectra that are examined by
the computing units can be the derived quantities used to evaluate
vehicle component health, as described above.
[0108] The Table below illustrates examples of different magnitudes
of the DC link sensor data spectrum at a frequency that is one half
of the frequency of the engine speed when the twelfth cylinder
("CC12" in the Table) is weak and when different cylinders are cut
out. The magnitudes are expressed as percentages of the threshold
described above. The phase angles of the vectors (e.g., the vector
2006 shown in FIG. 20) for the corresponding magnitudes also are
shown in the Table.
TABLE-US-00001 0.5x freq magnitude with different cylinders cutout
with Cyl12 is a weak cylinder Cylinder # cutout CC CC CC CC CC CC
CC CC CC CC CC CC 1 2 3 4 5 6 7 8 9 10 11 12 Mag (%) 125.1 117.9
100.6 88.9 73.2 70.0 78.4 88.9 108.1 117.9 128.2 100 Phase 29.1
47.3 80.3 103.0 148.5 180.0 231.0 257.0 293.5 312.7 -17.4 0.0
Angle(in .degree.)
[0109] Alternatively or additionally, the computing unit(s) can
determine which cylinder is weak by individually fueling each
cylinder until the magnitude of the frequency in the DC link
voltage spectrum at one half of the engine speed frequency
disappears or is reduced to zero. For example, each cylinder can be
individually over-fueled (injected with more fuel than the other
cylinders) or under-fueled (injected with less fuel than the other
cylinders) in a sequence by controlling the fuel injectors
associated with the cylinders. The magnitude of the frequency in
the DC voltage link spectrum at one half of the engine speed
frequency is examined and, when the magnitude at the frequency at
one half of the engine speed frequency disappears or reduces to
zero, the cylinder that is over- or under-fueled while the
magnitude disappears is identified by the computing unit as a weak
cylinder. The magnitudes of the spectra that are examined by the
computing units can be the derived quantities used to evaluate
vehicle component health, as described above.
[0110] Alternatively or additionally, the computing unit(s) can
determine which cylinder is weak by individually fueling each
cylinder in a step-wise manner and comparing the magnitude of the
frequency in the DC link voltage spectrum at one half of the engine
speed frequency at each fueling step with a designated range of
magnitudes associated with a healthy cylinder. For example, a first
cylinder may be injected with 10% of the amount of fuel that is
otherwise provided to this cylinder during normal operating
conditions (when the cylinders are not being tested as described
herein). The magnitude of the frequency in the DC link voltage
spectrum at one half of the engine speed frequency is examined.
Then, this same cylinder is injected with another amount of fuel
(e.g., 20% of the amount otherwise provided) and the magnitude is
examined. Then, this same cylinder is injected with another amount
of fuel (e.g., 30% of the amount otherwise provided) and the
magnitude is examined, and so on. This process can be repeated for
one or more, or all, other cylinders in the engine. The magnitudes
of the spectra that are examined by the computing units can be the
derived quantities used to evaluate vehicle component health, as
described above.
[0111] FIG. 26 illustrates examples of magnitudes 2400, 2402, 2404
of DC link voltage spectra at one half of the engine speed
frequency at different fueling levels for a healthy cylinder. The
magnitudes 2400, 2402, 2404 are shown alongside a horizontal axis
2406 representative of different fueling levels of the cylinder
(e.g., 10%, 20%, etc.) and alongside a vertical axis 2408
representative of the magnitudes of the frequency of the DC link
voltage spectra at one half of the engine speed frequency. Also
shown in FIG. 26 are designated ranges 2410, 2412, 2414 of
magnitudes at corresponding fueling levels. The ranges of
magnitudes indicate acceptable ranges of the magnitude of the DC
link voltage spectra at the one half of the engine speed frequency.
If the magnitude for a fuel level falls within the corresponding
range, then that magnitude indicates that the cylinder is healthy.
As shown in FIG. 26, the magnitudes all fall within the ranges,
thereby indicating to the computing unit(s) that the cylinder under
examination is healthy. The ranges of magnitudes can be determined
from measurements performed when the cylinders are known to be
healthy at the different fuel levels.
[0112] FIG. 27 illustrates examples of magnitudes 2500, 2502, 2504
of DC link voltage spectra at one half of the engine speed
frequency at different fueling levels for a weak or degraded
cylinder. The magnitudes 2500, 2502, 2504 are shown alongside the
horizontal axis 2406 and the vertical axis 2408. As shown in FIG.
27, the magnitude 2500 at the fueling level of 10% is within the
associated range 2410, but the magnitudes 2502, 2504 associated
with the fueling levels of 30% and 110%, respectively, fall outside
the associated ranges 2412, 2414. This can indicate to the
computing unit(s) that the cylinder under examination is not
healthy and may be weak or degraded.
[0113] FIG. 28 illustrates a flowchart of one embodiment of a
method 2600 for identifying a weak cylinder in an engine. The
method 2600 can represent the operations performed by the control
system in examining the cylinders of an engine. At 2602, the engine
operates by directing fuel-and-air mixtures into the cylinders of
the engine. At 2604, a determination is made as to whether the
operating conditions of the engine are acceptable for examination
of the cylinders. If the operating conditions are acceptable, then
flow of the method 2600 can proceed toward 2606. Otherwise, flow of
the method 2600 can return toward 2602 until the conditions are
acceptable, or the method 2600 can terminate.
[0114] At 2606, a value of a variable i is set to one and a value
of a variable n is set to the number of cylinders in the engine.
Optionally, these values can be set at another point in the method
2600. Optionally, the variable i is set to another value. At 2608,
the cylinder is cut off. For example, injection of fuel to the
i.sup.th cylinder may be temporarily suspended or stopped. At 2610,
the DC link voltage of the power electronics of the vehicle is
monitored while the i.sup.th cylinder is cut out. At 2612, a
determination is made as to whether the DC link voltage indicates
that one or more of the cylinders is weak. For example, the
magnitude of the frequency of a spectrum of the DC link voltage can
be examined and/or compared to one or more thresholds to determine
if any cylinder is weak, as described above. Optionally, the amount
of fueling to the cylinder can be changed and the DC link voltage
spectrum can be examined, as described above. The fueling amount
can be changed by increasing or decreasing the amount of fuel
supplied to the cylinder, also as described above. If the DC link
voltage indicates that a cylinder is weak, then flow of the method
2600 can proceed toward 2614. Otherwise, flow of the method 2600
can continue toward 2616.
[0115] At 2614, the i.sup.th cylinder is identified as a weak
cylinder. One or more remedial actions can be performed, such as
automatically decreasing operation of the engine (e.g., decreasing
the speed of the engine), automatically stopping operation of the
engine, changing an amount of fuel supplied to the weak cylinder,
or the like. Flow of the method 2600 can proceed toward 2616 or can
terminate (e.g., at 2618).
[0116] At 2616, a determination is made as to whether the current
value of i is equal to n, the number of cylinders in the engine. If
the value of i is equal to the number of cylinders in the engine,
then flow of the method 2600 can terminate at 2618, or can return
toward 2602. If the value of i is not equal to the number of
cylinders in the engine (e.g., i is less than n), then flow of the
method 2600 can proceed toward 2620. At 2620, the value of i is
incrementally increased (e.g., by one), and flow of the method 2600
can return toward 2608.
[0117] In one embodiment, a locomotive control system is provided.
The control system includes a locomotive having a propulsion system
and one or more sensors located onboard the locomotive. The one or
more sensors configured to measure one or more actuating parameters
of the propulsion system while the locomotive is stationary,
idling, or during changes in movement of the locomotive. The
control system also includes one or more processors communicatively
coupled with the one or more sensors. The one or more processors
are configured to monitor the one or more actuating parameters
according to a forcing function that represents operation of the
propulsion system of the locomotive. The one or more processors
also are configured to identify a degraded component of the
locomotive by one or more of (a) comparing actuating parameters
that are generated by the propulsion system according to the
forcing function with (speed) actuating parameters expressed as a
function of speed of another propulsion system associated with at
least one other locomotive, (b) examining changes in the actuating
parameters that are generated by the propulsion system according to
the forcing function over time, (c) examining oscillations in the
changes in movement of the locomotive during shifting of gears
between different torques or between different transmission torques
of the forcing function, (d) comparing decreases in wheel speed of
the locomotive during operation according to the forcing function
with designated wheel speeds associated with at least one other
locomotive, and/or (e) comparing a magnitude of one or more
frequencies in a frequency domain spectrum of the actuating
parameters of the locomotive with one or more designated magnitudes
while the locomotive is one or more of moving, idling, or
stationary.
[0118] In one embodiment, a locomotive control system includes a
locomotive having a propulsion system and one or more sensors
located onboard the locomotive. The one or more sensors are
configured to measure one or more actuating parameters generated by
the propulsion system while the locomotive is stationary, idling,
or during changes in movement of the locomotive. The system also
includes one or more processors communicatively coupled with the
one or more sensors. The one or more processors are configured to
control operation of the propulsion system according to a forcing
function and to monitor the one or more actuating parameters while
the propulsion system is operating according to the forcing
function. The one or more processors are configured to identify a
degraded component of the locomotive by one or more of (a)
comparing the actuating parameters that are monitored with speed
actuating parameters expressed as a function of speed of at least
one other propulsion system associated with at least one other
locomotive, (b) examining changes in the actuating parameters that
are monitored over time, (c) examining oscillations in changes in
movement of the locomotive during shifting of gears between
different torques or between different transmission torques during
operation of the propulsion system according to the forcing
function, (d) comparing decreases in wheel speed of the locomotive
during operation of the propulsion system according to the forcing
function with designated wheel speeds associated with at least one
other locomotive, and/or (e) comparing a magnitude of one or more
frequencies in a frequency domain spectrum of the actuating
parameters of the locomotive with one or more designated magnitudes
while the locomotive is one or more of moving, idling, or
stationary.
[0119] Optionally, the forcing function is one or more of (a) a
designated forcing function that predefines the actuating
parameters of the propulsion system of the locomotive, (b) a
naturally occurring forcing function that identifies operational
conditions of the propulsion system that are not automatically
implemented, and/or (c) a combination of the designated forcing
function and the naturally occurring forcing function. The forcing
function optionally can define one or more of (a) motor torques of
the propulsion system, (b) a terrain over which the locomotive
travels, (c) a gradient of a route on which the locomotive travels,
(d) a speed bump of the locomotive, (e) a stiff gradient of the
locomotive, (f) a coasting operation of the locomotive, and/or (g)
a combination of forces that one or more of assist motion or oppose
motion of the locomotive.
[0120] The actuating parameters may include one or more of (a)
torque generated by the propulsion system, (b) power generated by
the propulsion system, (c) force generated by the propulsion
system, (d) tractive effort generated by the propulsion system, (e)
speed of the locomotive, and/or (f) an opposing force to generated
torque of the propulsion system. The propulsion system can be one
or more of (a) a motor and/or (b) a prime mover other than an
engine of the locomotive.
[0121] The forcing function can designate one or more of (a) engine
torques as a function of engine speeds that are generated by an
engine of the locomotive, (b) application of one or more brakes of
the locomotive, and/or (c) shifting of gears in a transmission of
the locomotive. The one or more processors can be configured to
monitor torques generated by the propulsion system during operation
of the locomotive according to operational conditions designated by
the forcing function. The one or more processors can be configured
to identify the degraded component of the locomotive by one or more
of (a) comparing torques that are generated by the propulsion
system during operation according to the forcing function as the
actuating parameters (with the forcing function designating torques
as a function of the speed of the other propulsion system that is
associated with the at least one other locomotive) and/or (b)
examining the changes in the actuating parameters that are
generated by the propulsion system during operation according to
the forcing function over time (where the degraded component of the
locomotive is determined responsive to a variance in the actuating
parameters that are generated by the propulsion system exceeding
one or more designated thresholds).
[0122] Optionally, the one or more processors can be configured to
identify the degraded component of the locomotive by examining the
oscillations in the changes in movement of the locomotive during
shifting of gears and determining that the oscillations exceed one
or more thresholds. The one or more processors can be configured to
identify the degraded component of the locomotive by comparing the
magnitude of the one or more frequencies in the frequency domain
spectrum of the actuating parameters of the locomotive with one or
more designated magnitudes.
[0123] In one embodiment, a locomotive control system is provided
that includes a locomotive having one or more motors configured to
generate torque to propel the locomotive and one or more sensors
configured to measure a response of the locomotive to the torque
that is generated by the one or more motors. The one or more
sensors are configured to generate sensor data representative of
the response that is measured. The control system also includes a
hardware controller configured to direct the one or more motors of
the locomotive to generate the torque according to a designated
torque profile. The controller also is configured to receive the
sensor data and to determine a frequency spectrum of the response
of the locomotive. The controller is configured to compare one or
more parts of the frequency spectrum with a threshold to (a)
determine that a component of the locomotive is degraded and to (b)
automatically change movement of the locomotive responsive to
determining that the component is degraded.
[0124] Optionally, the designated torque profile can be a pseudo
random binary sequence of torques to be generated by the one or
more motors. The one or more sensors can be configured to measure
one or more of speeds or accelerations of the locomotive. The one
or more sensors can be configured to measure rotor speeds of the
one or more motors.
[0125] In one embodiment, a locomotive control system includes an
engine configured to be disposed onboard a locomotive and to
receive a supply of fuel for cylinders of the engine, a power
electronics circuit configured to be coupled with the engine and to
conduct electric current to one or more motors of the locomotive
for propelling the locomotive, one or more sensors configured to
monitor direct current link voltages in the power electronics
circuit coupled with the engine, and one or more processors
configured to be communicatively coupled with the one or more
sensors. The one or more processors also are configured to change
the supply of fuel to at least one of the cylinders of the engine,
to determine a magnitude of a frequency in a frequency spectrum of
the direct current link voltages that are monitored, and to
determine whether the at least one cylinder that receives the
supply of fuel that is changed is damaged or degraded based on the
magnitude of the frequency that is determined.
[0126] Optionally, the one or more processors can be configured to
change the supply of fuel to the at least one cylinder by reducing
fuel supplied to the least one cylinder. The one or more processors
can be configured to change the supply of fuel to the at least one
cylinder by cutting out the at least one cylinder. The one or more
processors can be configured to change the supply of fuel to the at
least one cylinder by stopping injection of the fuel to a first
cylinder of the cylinders while other cylinders of the cylinders in
the engine continue being injected with the fuel.
[0127] The frequency in the frequency spectrum can be at one half
of a frequency of a speed at which the engine operates.
[0128] The one or more processors can be configured to sequentially
change the supply of fuel to other cylinders in the plural
cylinders, monitor the direct current link voltages, determine the
magnitude of the frequency, and determine whether each of the other
cylinders receiving the sequentially changed supply of fuel is
damaged or degraded based on the magnitude of the frequency.
[0129] Optionally, the one or more processors are configured to
change the supply of the fuel to the at least one cylinder by
increasing fuel supplied to the at least one cylinder relative to
one or more other cylinders of the engine.
[0130] In an embodiment, a system (e.g., vehicle system, or vehicle
controls system) includes a vehicle and one or more processors. The
vehicle has a propulsion system and one or more sensors located
onboard the vehicle. The one or more sensors are configured to
measure one or more actuating parameters generated by the
propulsion system while the vehicle is stationary, idling, or
during changes in movement of the vehicle. The one or more
processors are communicatively coupled with the one or more
sensors, and are configured to monitor the one or more actuating
parameters according to a forcing function that represents
operation of the propulsion system of the vehicle. The one or more
processors are configured to identify a degraded component of the
vehicle by one or more of: comparing the actuating parameters that
are generated by the propulsion system and monitored according to
the forcing function with speed actuating parameters expressed as a
function of speed of at least one other propulsion system
associated with at least one other vehicle; examining changes in
the actuating parameters that are generated by the propulsion
system and monitored according to the forcing function over time;
examining oscillations in changes in movement of the vehicle during
shifting of gears between different torques or between different
transmission torques of the forcing function; comparing decreases
in wheel speed of the vehicle during operation according to the
forcing function with designated wheel speeds associated with at
least one other vehicle; and/or comparing a magnitude of one or
more frequencies in a frequency domain spectrum of the actuating
parameters of the vehicle with one or more designated magnitudes
while the vehicle is one or more of moving, idling, or
stationary.
[0131] In another embodiment, the forcing function is one or more
of a designated forcing function that predefines the actuating
parameters of the propulsion system of the vehicle, a naturally
occurring forcing function that identifies operational conditions
of the propulsion system that are not automatically implemented, or
a combination of the designated forcing function and the naturally
occurring forcing function.
[0132] In another embodiment, the forcing function defines one or
more of motor torques of the propulsion system, a terrain over
which the vehicle travels, a gradient of a route on which the
vehicle travels, a speed bump of the vehicle, a stiff gradient of
the vehicle, a coasting operation of the vehicle, or a combination
of forces that one or more of assist motion or oppose motion of the
vehicle.
[0133] In another embodiment, the actuating parameters include one
or more of torque generated by the propulsion system, power
generated by the propulsion system, force generated by the
propulsion system, tractive effort generated by the propulsion
system, speed of the vehicle, or an opposing force to generated
torque of the propulsion system.
[0134] In another embodiment, the propulsion system is one or more
of a motor or a prime mover other than an engine of the
vehicle.
[0135] In another embodiment, the forcing function designates one
or more of: engine torques as a function of engine speeds that are
generated by an engine of the vehicle, application of one or more
brakes of the vehicle, or shifting of gears in a transmission of
the vehicle.
[0136] In another embodiment, the one or more processors are
configured to monitor torques generated by the propulsion system
during operation of the vehicle according to operational conditions
designated by the forcing function. The one or more processors are
configured to identify the degraded component of the vehicle by one
or more of: comparing torques that are generated by the propulsion
system during operation according to the forcing function as the
actuating parameters, with the forcing function designating torques
as a function of the speed of the other propulsion system that is
associated with the at least one other vehicle; and/or examining
the changes in the actuating parameters that are generated by the
propulsion system during operation according to the forcing
function over time, wherein the degraded component of the vehicle
is determined responsive to a variance in the actuating parameters
that are generated by the propulsion system exceeding one or more
designated thresholds.
[0137] In another embodiment, the one or more processors are
configured to identify the degraded component of the vehicle by
examining the oscillations in the changes in movement of the
vehicle during shifting of gears and determining that the
oscillations exceed one or more thresholds.
[0138] In another embodiment, the one or more processors are
configured to identify the degraded component of the vehicle by
comparing the magnitude of the one or more frequencies in the
frequency domain spectrum of the actuating parameters of the
vehicle with one or more designated magnitudes.
[0139] In another embodiment, a vehicle control system includes a
vehicle, one or more sensors, and a hardware controller (e.g.,
electrical circuit with a processor). The vehicle has one or more
motors configured to generate torque to propel the vehicle. The one
or more sensors are configured to measure a response of the vehicle
to the torque that is generated by the one or more motors, the one
or more sensors configured to generate sensor data representative
of the response that is measured. The hardware controller is
configured to direct the one or more motors of the vehicle to
generate the torque according to a designated torque profile. The
controller also is configured to receive the sensor data and to
determine a frequency spectrum of the response of the vehicle. The
controller also is configured to compare one or more parts of the
frequency spectrum with a threshold to determine that a component
of the vehicle is degraded and to automatically change movement of
the vehicle responsive to determining that the component is
degraded.
[0140] In another embodiment, the designated torque profile is a
pseudo random binary sequence of torques to be generated by the one
or more motors.
[0141] In another embodiment, the one or more sensors are
configured to measure one or more of speeds or accelerations of the
vehicle as the response of the vehicle to the torque that is
generated by the one or more motors.
[0142] In another embodiment, the one or more sensors are
configured to measure rotor speeds of the one or more motors.
[0143] In another embodiment, a vehicle control system includes an
engine, a power electronics circuit, one or more sensors, and one
or more processors. The engine is configured to be disposed onboard
a vehicle and to receive a supply of fuel for cylinders of the
engine. The power electronics circuit is configured to be coupled
with the engine and to conduct electric current to one or more
motors of the vehicle for propelling the vehicle. The one or more
sensors are configured to monitor direct current link voltages in
the power electronics circuit coupled with the engine. The one or
more processors are configured: to be communicatively coupled with
the one or more sensors; to change the supply of fuel to at least
one of the cylinders of the engine; to determine a magnitude of a
frequency in a frequency spectrum of the direct current link
voltages that are monitored; and to determine whether the at least
one cylinder that receives the supply of fuel that is changed is
damaged or degraded based on the magnitude of the frequency that is
determined.
[0144] In another embodiment, the one or more processors are
configured to change the supply of fuel to the at least one
cylinder by reducing fuel supplied to the least one cylinder.
[0145] In another embodiment, the one or more processors are
configured to change the supply of fuel to the at least one
cylinder by cutting out the at least one cylinder.
[0146] In another embodiment, the one or more processors are
configured to change the supply of fuel to the at least one
cylinder by stopping injection of the fuel to a first cylinder of
the cylinders while other cylinders of the cylinders in the engine
continue being injected with the fuel.
[0147] In another embodiment, the frequency in the frequency
spectrum is at one half of a frequency of a speed at which the
engine operates.
[0148] In another embodiment, the one or more processors are
configured to sequentially change the supply of fuel to other
cylinders in the plural cylinders, monitor the direct current link
voltages, determine the magnitude of the frequency, and determine
whether each of the other cylinders receiving the sequentially
changed supply of fuel is damaged or degraded based on the
magnitude of the frequency.
[0149] In another embodiment, the one or more processors are
configured to change the supply of the fuel to the at least one
cylinder by increasing fuel supplied to the at least one cylinder
relative to one or more other cylinders of the engine.
[0150] It is to be understood that the above description is
intended to be illustrative, and not restrictive. For example, the
above-described embodiments (and/or aspects thereof) may be used in
combination with each other. In addition, many modifications may be
made to adapt a particular situation or material to the teachings
of the inventive subject matter without departing from its scope.
While the dimensions and types of materials described herein are
intended to define the parameters of the inventive subject matter,
they are by no means limiting and are exemplary embodiments. Many
other embodiments will be apparent to those of skill in the art
upon reviewing the above description. As used herein, the terms
"including" and "in which" are used as the plain-English
equivalents of the respective terms "comprising" and "wherein."
Moreover, terms such as "first," "second," "third," "upper,"
"lower," "bottom," "top," etc. are used merely as labels, and are
not intended to impose numerical or positional requirements on
their objects.
[0151] This written description uses examples to disclose several
embodiments of the inventive subject matter, including the best
mode, and also to enable one of ordinary skill in the art to
practice the embodiments of inventive subject matter, including
making and using any devices or systems and performing any
incorporated methods.
[0152] As used herein, an element or step recited in the singular
and proceeded with the word "a" or "an" should be understood as not
excluding plural of said elements or steps, unless such exclusion
is explicitly stated. Furthermore, references to "one embodiment"
of the inventive subject matter are not intended to be interpreted
as excluding the existence of additional embodiments that also
incorporate the recited features. Moreover, unless explicitly
stated to the contrary, embodiments "comprising," "including," or
"having" an element or a plurality of elements having a particular
property may include additional such elements not having that
property.
[0153] Since certain changes may be made in the above-described
system and method without departing from the spirit and scope of
the inventive subject matter herein involved, it is intended that
all the subject matter of the above description or shown in the
accompanying drawings shall be interpreted merely as examples
illustrating the inventive concept herein and shall not be
construed as limiting the inventive subject matter.
* * * * *