U.S. patent application number 16/326781 was filed with the patent office on 2019-06-13 for yieldable bearing block.
The applicant listed for this patent is FCI Holdings Delaware, Inc.. Invention is credited to Dakota Faulkner, Lumin Ma, John C. Stankus.
Application Number | 20190178083 16/326781 |
Document ID | / |
Family ID | 61691095 |
Filed Date | 2019-06-13 |

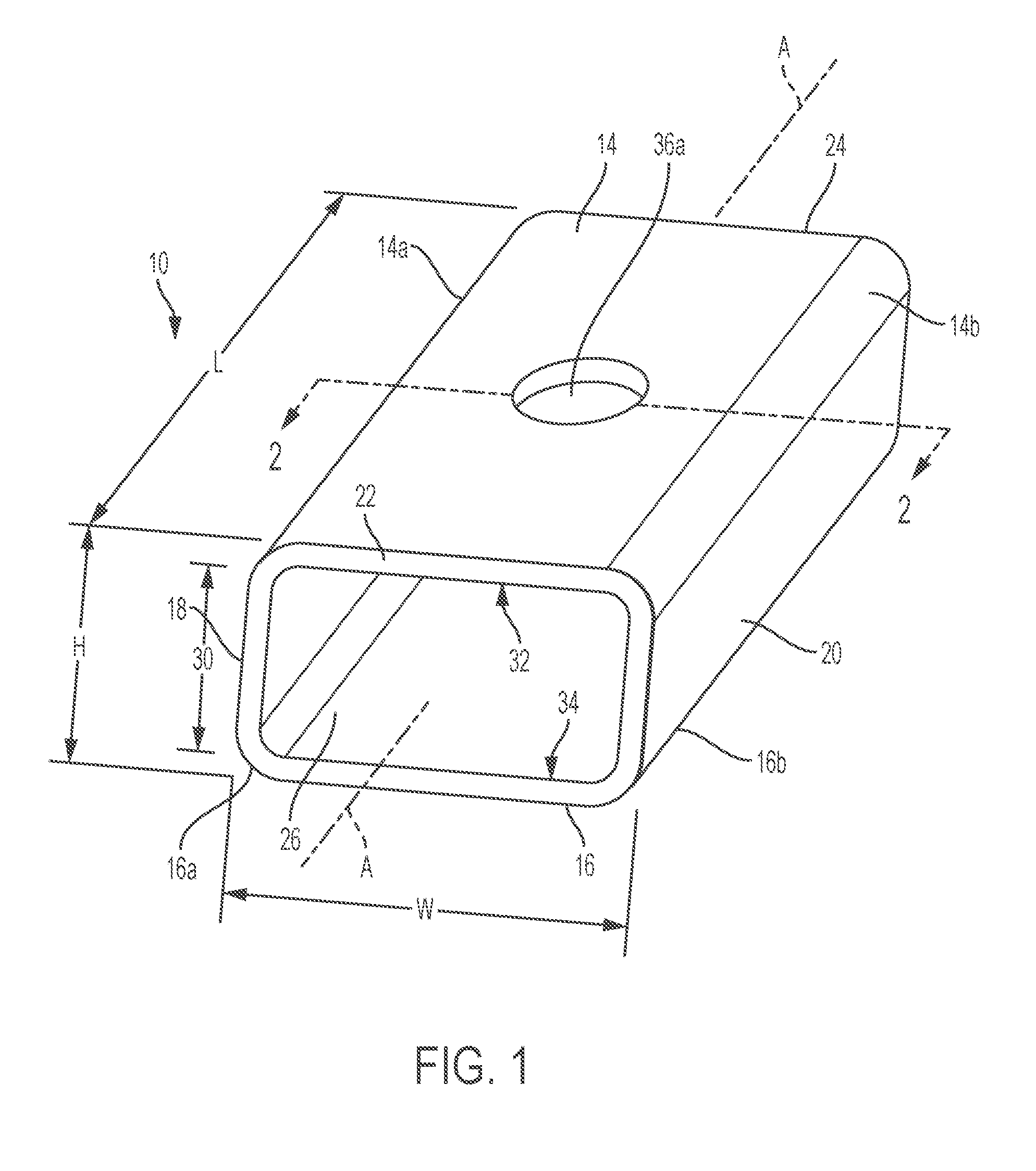


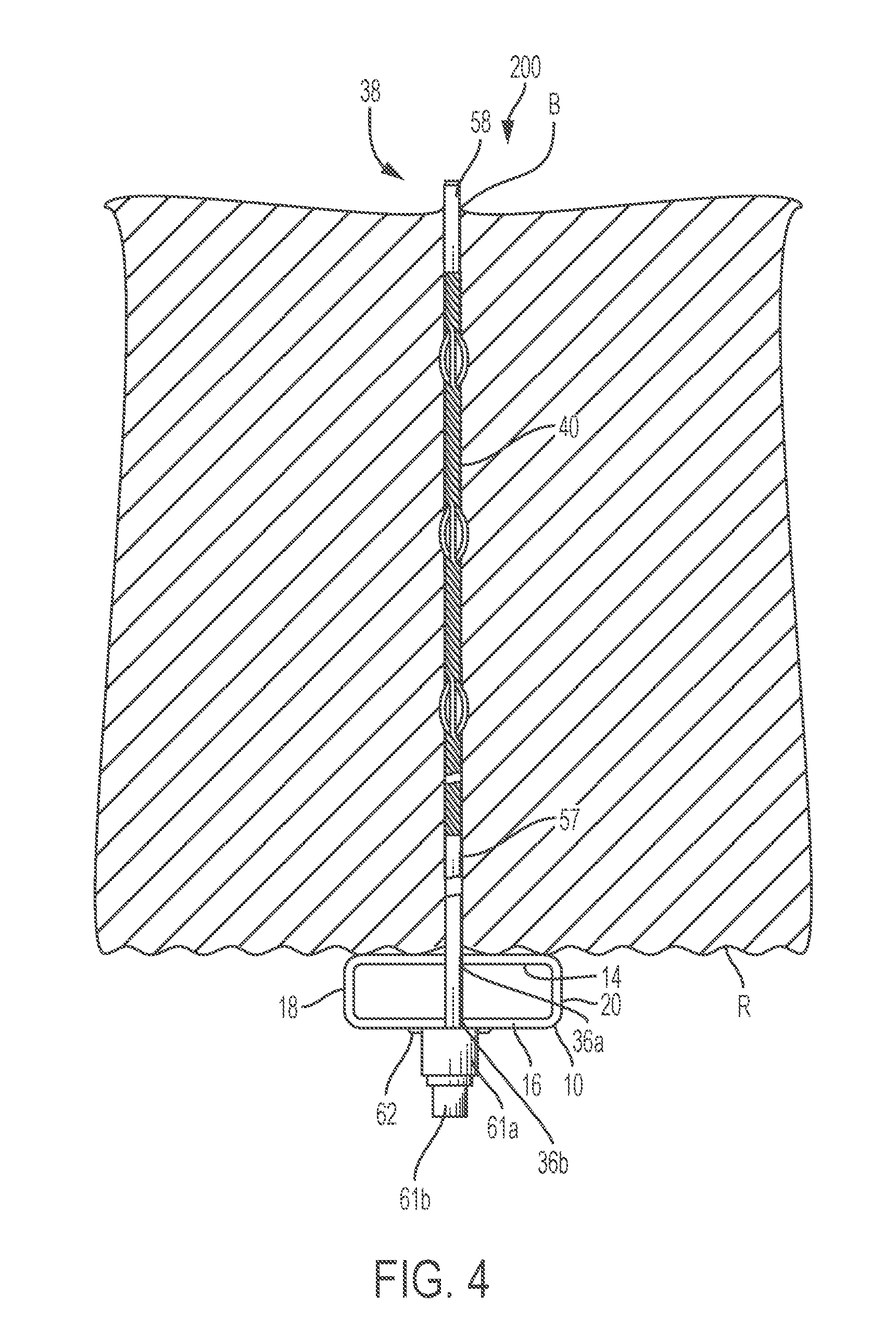
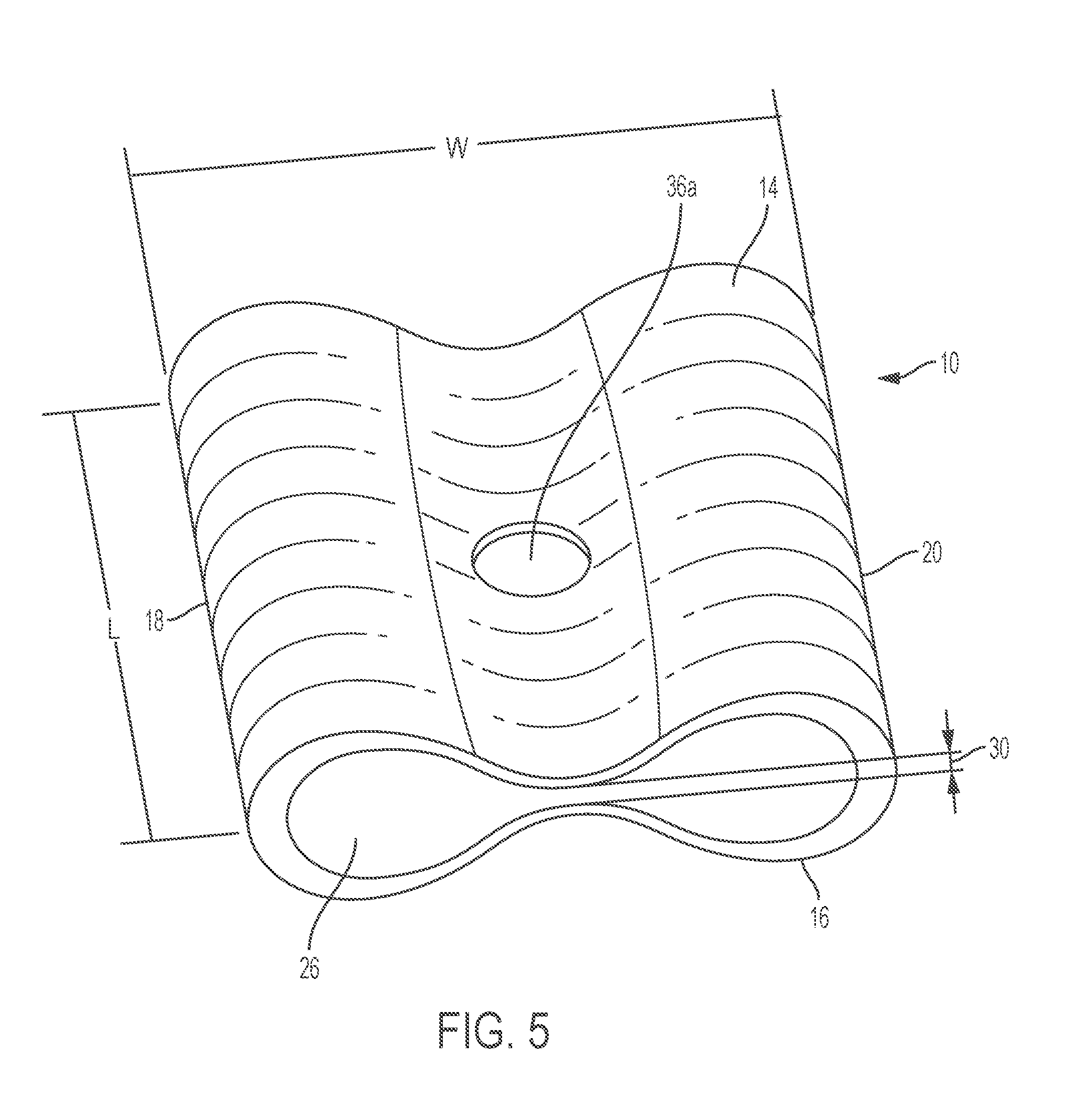

United States Patent
Application |
20190178083 |
Kind Code |
A1 |
Stankus; John C. ; et
al. |
June 13, 2019 |
Yieldable Bearing Block
Abstract
A mine roof bolting system including a bearing member having a
first member, a second member spaced apart from the first member,
and apertures defined through each of the first and second members,
and a mine roof bolt extending through the apertures. When a load
is applied to the mine roof bolting system, the bearing member
yields or deforms. Also, a method for providing a roof support in
an underground mine including providing the bearing member and
inserting a mine roof bolt through the apertures of the bearing
member and into a borehole in a mine roof, wherein the bearing
member yields upon application of a load in excess of a
predetermined load.
Inventors: |
Stankus; John C.;
(Canonsburg, PA) ; Faulkner; Dakota; (New
Kensington, PA) ; Ma; Lumin; (Pittsburgh,
PA) |
|
Applicant: |
Name |
City |
State |
Country |
Type |
FCI Holdings Delaware, Inc. |
Wilmington |
|
DE |
|
|
Family ID: |
61691095 |
Appl. No.: |
16/326781 |
Filed: |
September 25, 2017 |
PCT Filed: |
September 25, 2017 |
PCT NO: |
PCT/US17/53192 |
371 Date: |
February 20, 2019 |
Related U.S. Patent Documents
|
|
|
|
|
|
Application
Number |
Filing Date |
Patent Number |
|
|
62399693 |
Sep 26, 2016 |
|
|
|
Current U.S.
Class: |
1/1 |
Current CPC
Class: |
E21D 20/00 20130101;
E21D 21/0086 20130101; F16B 31/02 20130101 |
International
Class: |
E21D 21/00 20060101
E21D021/00; E21D 20/00 20060101 E21D020/00 |
Claims
1. A mine roof bolting system comprising: a bearing member
including a first member, a second member spaced apart from the
first member, and apertures defined through each of the first and
second members; and a mine roof bolt extending through the
apertures, wherein when a load is applied to the mine roof bolting
system, the bearing member yields.
2. The mine roof bolting system of claim 1, wherein a gap is
provided between the first member and the second member and wherein
when a predetermined load is applied to the mine roof bolting
system, the gap is reduced.
3. The mine roof bolting system of claim 2, wherein the gap
provided between the first member and the second member is at least
1 inch.
4. The mine roof bolting system of claim 1, wherein the bearing
member comprises a rectangular steel tube.
5. The mine roof bolting system of claim 1, wherein the mine roof
bolt is a cable bolt, a solid bolt, an expandable bolt, or a hollow
bolt.
6. The mine roof bolting system of claim 1, further comprising a
bearing plate having a bearing surface for contacting rock strata,
a contact surface positioned opposite the bearing surface for
engaging the bearing member, and an aperture defined through the
bearing plate.
7. A mine roof bolting system comprising: a bearing member
comprising: a first member defining a first aperture; a second
member spaced apart from the first member and defining a second
aperture; and a web extending between the first member and the
second member and thereby defining a gap between the first member
and the second member; and a mine roof bolt extending through the
first and second apertures of the bearing member.
8. The mine roof bolting system of claim 7, wherein the mine roof
bolt is a cable bolt, a solid bolt, an expandable bolt, or a hollow
bolt.
9. The mine roof bolting system of claim 7, further comprising a
bearing plate comprising a bearing surface for contacting the mine
roof, a contact surface for contacting the bearing member, and an
aperture through which the mine roof bolt extends.
10. The mine roof bolting system of claim 7, wherein the first
member is substantially parallel to the second member.
11. The mine roof bolting system of claim 7, further comprising
another web extending between the first member and the second
member, the two webs being spaced apart by the gap.
12. The bearing member of claim 11, wherein, when taken together,
the first member, the second member, the first web, and the second
web define a central cavity.
13. A method for providing a roof support in an underground mine,
the method comprising the steps of: providing a bearing member
including a first member, a second member spaced apart from the
first member, and apertures defined through each of the first and
second members; and inserting a mine roof bolt through the
apertures of the bearing member and into a borehole in a mine roof,
wherein the bearing member yields upon application of a load in
excess of a predetermined load.
14. The method for providing a roof support of claim 13, wherein
the mine roof bolt is a cable bolt, a solid bolt, an expandable
bolt, or a hollow bolt.
15. The method for providing a roof support of claim 13, further
comprising positioning a bearing plate in between the mine roof and
the yieldable bearing member.
Description
CROSS-REFERENCE TO RELATED APPLICATION
[0001] This application claims priority to U.S. Provisional Patent
Application No. 62/399,693 filed Sep. 26, 2016, the disclosure of
which is hereby incorporated in its entirety by reference.
BACKGROUND OF THE INVENTION
Field of the Invention
[0002] The present invention relates to a mine roof bolting system,
and more particularly, a mine roof bolting system including a
bearing member that yields or deforms when subjected to a load.
Description of Related Art
[0003] The roof of a mine is conventionally supported by tensioning
the roof with mine bolts drilled in the mine roof that reinforce
the unsupported rock formation behind the roof. Other structures
may also be supported, such as walls or ribs of an underground
mine; thus use of the term "roof" herein is also applicable to
other such structures. The end of the mine bolt may be anchored
mechanically to the rock formation by engagement of an expansion
assembly on the end of the bolt with the rock formation.
Alternatively, the mine roof bolt may be adhesively bonded to the
rock formation with a resin bonding material inserted into the bore
hole into which the mine roof bolt is inserted. A combination of
mechanical anchoring and resin bonding can also be employed by
using both an expansion assembly and resin bonding material.
[0004] Cable bolts are used in the mining industry, and
particularly, hard rock mining as they provide several advantages
over conventional mine roof bolts, for example, ease of handling
and installation. Cable bolts are substantially easier to fit into
a borehole than the elongated rods of conventional rod bolt
systems. Regardless of the height limitations in a mine, cable
bolts may be adapted to boreholes of any length due to their
flexibility. Moreover, the strength capacity of cables typically
exceed that of conventional rod bolts.
[0005] With certain mining conditions, particularly those found in
hard rock mining, the rock formation in the mine roof is
susceptible to movement or rock burst as a result of mine-induced
seismicity, the excavation of perimeter rock, minor seismicities,
and the like. Under dynamic loading caused by rock bursts, the
conventional mine roof bolts described above are vulnerable to
failure.
SUMMARY OF THE INVENTION
[0006] The present invention includes a simple, low cost, and easy
to manufacture mine roof bolting system wherein at least a portion
of the system deforms to absorb some of the dynamic loading caused
by a rock burst or excessive load caused by squeezing ground.
[0007] The present invention is directed to a mine roof bolting
system comprising a bearing member having a first member, a second
member spaced apart from the first member, and apertures defined
through each of the first and second members; and a mine roof bolt
extending through the apertures. When a load is applied to the mine
roof bolting system, the bearing member yields.
[0008] The present invention is also directed to a mine roof
bolting system comprising a bearing member comprising a first
member defining a first aperture, a second member spaced apart from
the first member and defining a second aperture, and a web
extending between the first member and the second member and
thereby defining a gap between the first member and the second
member; and a mine roof bolt extending through the first and second
apertures of the bearing member.
[0009] The present invention is also directed to a method for
providing a roof support in an underground mine. The method
includes providing a bearing member as described above and
inserting a mine roof bolt through the apertures of the bearing
member and into a borehole in a mine roof. The bearing member is
adapted to yield upon application of a load in excess of a
predetermined load. The mine roof bolt may be a cable bolt, a solid
bolt, an expandable (inflatable) bolt, or a hollow bolt.
BRIEF DESCRIPTION OF THE DRAWINGS
[0010] The present invention will now be described in further
detail with reference to the accompanying figures, in which:
[0011] FIG. 1 is a perspective view of a yieldable bearing member
in accordance with the present invention;
[0012] FIG. 2 is a cross-section view of the yieldable bearing
member of FIG. 1 taken along line 2-2;
[0013] FIG. 3 is a front elevation view of a mine roof bolting
system including a bearing plate, the bearing member of FIG. 1, and
a mine roof bolt;
[0014] FIG. 4 is a front elevation view of a mine roof bolting
system including the bearing member of FIG. 1 and a mine roof
bolt;
[0015] FIG. 5 is a perspective view of the bearing member of FIG. 1
after the bearing member has yielded; and
[0016] FIG. 6 is a load deflection curve comparing yieldable
bearing members made in accordance with the present invention.
DESCRIPTION OF THE INVENTION
[0017] The following description is provided to enable those
skilled in the art to make and use the described embodiments
contemplated for carrying out the invention. For purposes of the
description hereinafter, the terms "upper", "lower", "vertical",
"horizontal", "top", "bottom", "lateral", "longitudinal", and
derivatives thereof relate to the invention as it is oriented in
the drawing figures. It is to be understood that the specific
devices illustrated in the attached drawings, and described in the
following specification, are simply exemplary embodiments of the
invention. Hence, specific dimension and other physical
characteristics related to the embodiments disclosed herein are not
to be understood as limiting.
[0018] FIGS. 1 and 2 illustrate a yieldable bearing member made in
accordance with the present invention. The yieldable bearing member
10, also referred to herein as a yieldable bearing block, generally
includes a first member 14, also referred to as a top member, a
second member 16, also referred to as a bottom member, and at least
one web 18, 20 extending between the top member 14 and the bottom
member 16.
[0019] The top member 14 may be spaced apart from the bottom member
16 and may be substantially parallel to the bottom member 16. The
top member 14 and the bottom member may each be in the form of a
plate which may take any suitable shape including, but not limited
to a rectangle, a square, a trapezoid, a parallelogram, a polygon,
and a circle. The web 18, 20 may extend from a first side 14a of
the top member 14 to a first side 16a of the bottom member 16. A
second web 18, 20 may extend from a second side 14b of the top
member 14 to a second side 16b of the bottom member 16. First sides
14a, 16a and second sides 14b, 16b each may include curved portions
connecting the top member 14 and the bottom member 16. The top
member 14, the bottom member 16, and the two webs 18, 20 may
combine to define a central cavity 26 such that the yieldable
bearing block 10 has a tubular configuration. The central cavity 26
extends along a central axis A from a first end 22 to a second end
24 of the yieldable bearing block 10 such that a gap 30 is formed
between an interior surface 32 of the top member 14 and an interior
surface 34 of the bottom member 16. The central cavity 26 may be
open, or alternatively, may include a compressible material such as
wood, plastic, hard rubber, aerated cement, or the like, to modify
the loading/deformation properties of the yieldable bearing block
10.
[0020] In one embodiment, the webs 18, 20 may extend from
respective sides 14a, 14b of the top member 14 to respective sides
16a, 16b of the bottom member 16 such that the webs 18, 20 are at
right angles to the top member 14 and the bottom member 16. The top
member 14 and the bottom member may have the same size and shape
and two webs 18, 20 may be provided as shown in FIGS. 1 and 2. The
top member 14, the bottom member 16, and the webs 18, 20 combine to
define a central cavity 26 having a square or rectangular
cross-section.
[0021] In another embodiment, the size and/or shape of top member
14 and the bottom member 16 may be different or the top member 14
may be offset from the bottom member 16 such that the webs 18, 20
are angled with respect to the top member 14 and the bottom member
16. Two webs 18, 20 may be provided such that the top member 14,
the bottom member 16, and the webs 18, 20 combine to define a
central cavity 26 having a cross-section that is a trapezoid or a
parallelogram.
[0022] In a further embodiment, at least one of the top member 14,
the bottom member 16, and the webs may be curved. Two webs 18, 20
may be provided such that the top member 14, the bottom member 16,
and the webs 18, 20 combine to define a central cavity 26 having a
cross-section that is a circle, an ellipse, or a truncated circle
having two flat sides and two curved sides.
[0023] The yieldable bearing block 10 may have a length L measured
along the central axis A from the first end 22 to the second end
24, a width W measured perpendicular to the central axis A between
opposing webs 18, 20, and a height H measured perpendicular to the
central axis A between the top member 14 and the bottom member 16.
With particular reference to FIG. 2, an exterior surface 28 of the
yieldable bearing block 10 and the central cavity 26 define a wall
thickness 14' of the top member 14, a wall thickness 16' of the
bottom member 16, and wall thicknesses 18' and 20' of the webs 18
and 20, respectively. The wall thickness 14', 16', 18', 20' of each
wall 14, 16, 18, 20 may be equal to each other such that the
yieldable bearing block 10 has a uniform wall thickness T or may be
different from each other in order to provide different portions of
the yieldable bearing block 10 with different mechanical
properties. For example, the yieldable bearing block 10 may have a
uniform wall thickness T of 5/16 inch or 3/8 inch. As is further
discussed hereinafter, the length L, width W, height H, and wall
thickness T of the yieldable bearing block 10 can be manufactured
to provide specific yield and tensile properties for various
underground mining conditions, for example, hard rock mining.
[0024] Apertures 36a, 36b for receiving a fastening mechanism, such
as a mine roof bolt 38, are defined in the top member 14 and the
bottom member 16 of the yieldable bearing block 10. The apertures
36a, 36b may be positioned substantially at each of the centers of
the top member 14 and the bottom member 16. The apertures 36a, 36b
may be dimensioned to receive an elongated body 40 of a mine roof
bolt 38 (FIGS. 3 and 4). For example, the apertures 36a, 36b may be
dimensioned to receive a mine roof bolt 38 having a diameter of 0.6
inch or 0.7 inch.
[0025] The yieldable bearing block 10 may be produced from any
yieldable material having high strength, for example, steel or
aluminum. The material may have a minimum yield strength of 46 ksi
and a minimum tensile strength of 58 ksi. One such material is
rectangular steel tube, for example, a rectangular tube made of
ASTM A500-B steel.
[0026] The yieldable bearing block 10 can be used as part of a mine
roof bolting system, such as a mine roof bolting system 100, shown
in FIG. 3, including the yieldable bearing block 10, a bearing
plate 42, and a mine roof bolt 38, or a mine roof bolting system
200, shown in FIG. 4, including the yieldable bearing block 10 and
a mine roof bolt 38.
[0027] Referring to FIG. 5, the yieldable bearing block 10 is
designed to yield, or deform, such that the gap 30 of the yieldable
bearing block 10 is reduced when a predetermined load, for example,
15 tons or more or 20 tons or more, is applied to the mine roof
bolting system 100 or the mine roof bolting system 200.
[0028] Referring to FIG. 3, the mine roof bolting system 100
includes the yieldable bearing block 10, the bearing plate 42, and
the mine roof bolt 38. The bearing plate 42 may generally include a
planar body 44 having a bearing surface 46 for engaging the mine
roof R and a contact surface 48 for engaging the top member 14 of
the yieldable bearing block 10. The bearing plate 42 may be made of
commercial grade steel. An aperture 50 may be positioned
substantially at the center of the planar body 44. The bearing
plate 42 may optionally include one or more rib members 52
surrounding the aperture 50 and positioned between the aperture 50
and a peripheral edge 54 of the bearing plate 42. It should be
appreciated that other bearing plates known in the art may be used
in the system 100.
[0029] The mine roof bolting system 100 may be installed in a mine
roof R to provide support to a rock formation. The mine roof bolt
38 is inserted through the apertures 36 of the yieldable bearing
block 10 and the aperture 50 of the bearing plate 42 and into a
borehole B. The mine roof bolt 38 may be a solid bolt, such as a
solid rebar bolt or smooth bar bolt, a cable bolt, an expandable
(inflatable) bolt, a hollow bolt, or any other mine roof bolt
designed for supporting rock strata as is known in the art. A drive
end 60 of the mine roof bolt 38 may include a drive head that does
not tension the bolt or may include a tensioning system. Suitable
tensioning systems include an externally threaded bolt with a
tensioning nut optionally having a shear pin or breakout portion or
the like threaded thereon, a barrel and wedge assembly on a cable
bolt or other drive heads as are known in the art for installing
mine roof bolts.
[0030] By way of example, the mine roof bolt 38 may be a cable bolt
formed of a selected length of a flexible multi-strand steel cable
56 having an anchor end portion 58 and a drive end portion 60
including a barrel and wedge assembly 61a and a drive nut 61b.
Between the anchor end portion 58 and the drive end portion 60, the
cable 56 is flexible and extends a length as determined by the
length of the borehole B in the rock formation. A stiffening tube
57 may enclose the flexible multi-strand steel cable 56 at a
proximal end thereof, adjacent the barrel and wedge assembly 61a. A
washer 62 may optionally be placed between the bottom member 16 of
the yieldable bearing block 10 and the barrel and wedge assembly
61a such that the yieldable bearing block 10 does not directly
contact the barrel and wedge assembly 61a.
[0031] When the mine roof bolting system 100 experiences loading
due to a shift in the surrounding rock strata, the yieldable
bearing block 10 yields, or deforms, such that the gap 30 of the
yieldable bearing block 10 is reduced. As the yieldable bearing
block 10 yields, the mine roof bolting system 100 absorbs some of
the dynamic load such that the mine roof system 100 can support a
greater load than a comparable system not including the yieldable
bearing block 10.
[0032] Referring to FIG. 4, the mine roof bolting system 200
includes the yieldable bearing block 10 and a mine roof bolt 38.
The mine roof bolting system 200 is substantially the same as the
mine roof bolting system 100, but does not include the bearing
plate 42. Instead, the top member 14 of the yieldable bearing block
10 directly engages the mine roof R such that the yieldable bearing
block 10 serves a dual function, acting as both the yieldable
bearing block 10 and the bearing plate 42. For example, in the mine
roof bolting system 200, the yieldable bearing block 10 may be at
least 36 square inches.
[0033] When the mine roof system 200 experiences loading due to
natural forces of the mine, the yieldable bearing block 10 yields,
or deforms, such that the gap 30 of the yieldable bearing block 10
is reduced. As the yieldable bearing block 10 yields, the mine roof
bolting system 100 absorbs some of the dynamic load such that mine
roof system 200 can support a greater load than a comparable system
not including the yieldable bearing block 10.
[0034] The following tests were conducted to demonstrate the
general principles of the present invention. The invention should
not be considered to be limited to the specific tests presented
herein.
Examples
[0035] Ten yieldable bearing blocks 10 having a rectangular
cross-section and various lengths L, widths W, heights H, and wall
thicknesses T, were tested to determine a maximum load and a
maximum yield (i.e., maximum deflection) that each of the ten
yieldable bearing blocks 10 could withstand prior to failure. A
load was applied to the top member 14 of the yieldable bearing
blocks 10 using a rod having a 1.75 inch diameter to simulate the
housing of a mine roof bolt having a 0.6 inch diameter. The maximum
load and deflection achieved before the gap between the top member
14 and the bottom member 16 is at least partially closed as the top
member 14 and the bottom member 16 move toward one another under
the load as shown in FIG. 5 was measured. The results of the tests
are shown below in Table 1.
TABLE-US-00001 TABLE 1 Test results showing maximum load and
deflection Tube size Sample (W .times. H .times. T) length Max load
Max deflection Test # (inch) (inch) (ton) (inch) 1 4 .times. 3
.times. 3/8 4.5 24 1.95 2 4.0 22 1.88 3 3.5 20 1.76 4 4 .times. 2
.times. 5/16 4.5 21 1.21 5 4.0 20 1.16 6 3.5 18 1.11 7 3 .times. 2
.times. 5/16 4.5 34 1.22 8 4.0 33 1.20 9 3.5 31 1.12 10 3.0 24
1.06
[0036] Load deflection curves comparing the results of the
yieldable bearing blocks of Tests 9 and 10 having a length of 3.5
inches and a length of 3 inches, respectively, are shown in FIG. 6.
The results shown in FIG. 6 demonstrate that a load up to a
predetermined load (e.g., about 25 tons for Test 9 at a length of 3
inches and about 20 tons for Test 10 at a length of 3.5 inches) can
be applied before maximum deflection is achieved. A mine roof
support system incorporating the yieldable bearing block of the
present invention can withstand an added load (e.g., 20-25 tons as
shown in Tests 9 and 10), allowing the system to yield upon
application of the load.
[0037] The yieldable bearing block provided herein provides an easy
to manufacture and low cost system for increasing the load for
which a mine roof bolting system can support. The systems disclosed
herein are particularly advantageous in hard rock mining under
which dynamic loading is caused by squeezing and rock bursts.
[0038] While embodiments of the yieldable bearing block are shown
in the accompanying figures and described hereinabove in detail,
other embodiments will be apparent to, and readily made by, those
skilled in the art without departing from the scope and spirit of
the invention. Accordingly, the foregoing description is intended
to be illustrative rather than restrictive. The disclosure
described hereinabove is defined by the appended claims and all
changes to the disclosure that fall within the meaning and the
range of equivalency of the claims are to be embraced within its
scope.
* * * * *