U.S. patent application number 15/830062 was filed with the patent office on 2019-06-06 for methods of forming a porous thermal barrier coating.
The applicant listed for this patent is GENERAL ELECTRIC COMPANY. Invention is credited to Theodore Robert Grossman, Joshua Lee Margolies.
Application Number | 20190169730 15/830062 |
Document ID | / |
Family ID | 64572135 |
Filed Date | 2019-06-06 |




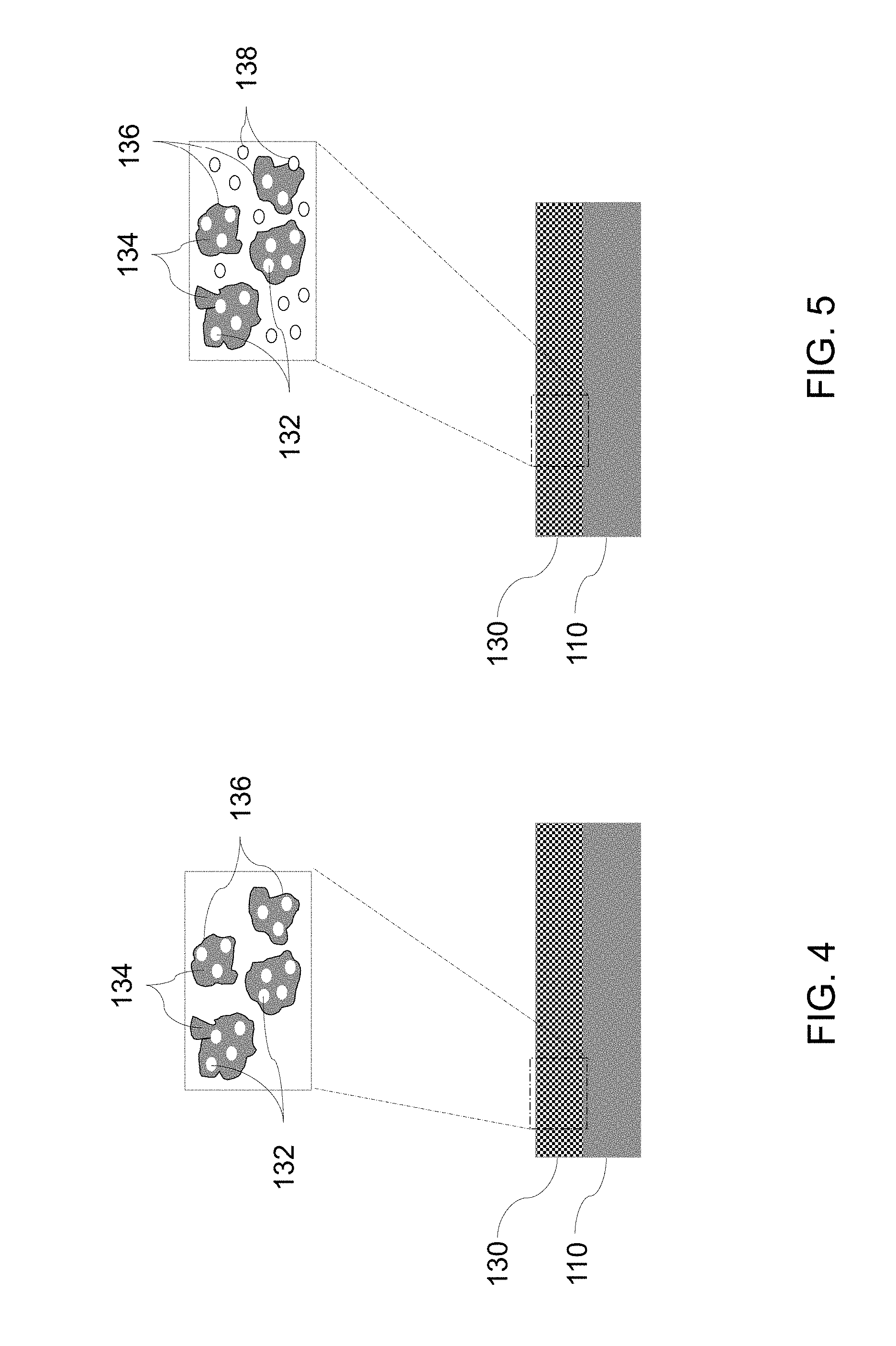

United States Patent
Application |
20190169730 |
Kind Code |
A1 |
Grossman; Theodore Robert ;
et al. |
June 6, 2019 |
METHODS OF FORMING A POROUS THERMAL BARRIER COATING
Abstract
A method for controlling the porosity parameter of porous
thermal barrier coatings is presented. The method includes
disposing a feedstock material on a substrate to form a porous
thermal barrier coating. The feedstock material includes a
gas-forming additive and a thermal barrier coating material. The
disposing step further includes controlling the porosity parameter
of the porous thermal barrier coating by controlling a feedstock
material feed rate, an amount of the gas-forming additive in the
feedstock material, a temperature of the disposed feedstock
material on the substrate, or combinations thereof.
Inventors: |
Grossman; Theodore Robert;
(Cincinnati, OH) ; Margolies; Joshua Lee;
(Niskayuna, NY) |
|
Applicant: |
Name |
City |
State |
Country |
Type |
GENERAL ELECTRIC COMPANY |
Schenectady |
NY |
US |
|
|
Family ID: |
64572135 |
Appl. No.: |
15/830062 |
Filed: |
December 4, 2017 |
Current U.S.
Class: |
1/1 |
Current CPC
Class: |
C23C 4/02 20130101; C23C
4/134 20160101; C23C 4/11 20160101; C23C 4/18 20130101 |
International
Class: |
C23C 4/134 20060101
C23C004/134 |
Claims
1. A method of forming a porous thermal barrier coating,
comprising: disposing a feedstock material on a substrate to form
the porous thermal barrier coating, wherein the feedstock material
comprises a gas-forming additive and a thermal barrier coating
material, and wherein the disposing comprises controlling a
porosity parameter of the porous thermal barrier coating by
controlling a feedstock material feed rate, an amount of the
gas-forming additive in the feedstock material, a temperature of
the disposed feedstock material on the substrate, or combinations
thereof.
2. The method according to claim 1, wherein the controlling the
porosity parameter of the porous thermal barrier coating comprises
controlling the temperature of the disposed feedstock material on
the substrate using an auxiliary heat source.
3. The method according to claim 1, wherein the disposed feedstock
material on the substrate is heated to a temperature greater than a
temperature that the substrate can withstand. Amend to claim 1 and
include.
4. The method according to claim 3, wherein the disposed feedstock
material on the substrate is heated to a temperature in a range
from about 1000.degree. C. to about 1500.degree. C.
5. The method according to claim 1, wherein the controlling the
porosity parameter of the porous thermal barrier coating comprises
controlling the amount of the gas-forming additive in the feedstock
material in a range from about 0.1 wt % to about 10 wt %.
6. The method according to claim 1, wherein the controlling the
porosity parameter of the porous thermal barrier coating comprises
controlling the feedstock material feed rate in a range from about
2.5 gm/min to about 100 gm/min.
7. The method according to claim 1, wherein the gas-forming
additive comprises graphite, carbides, oxycarbides, nitrides, or
combinations thereof.
8. The method according to claim 1, wherein the gas-forming
additive comprises elemental carbon.
9. The method according to claim 1, wherein the thermal barrier
coating material comprises yttria-stabilized zirconia.
10. The method according to claim 1, wherein the feedstock material
is disposed on the substrate using an air plasma spray process.
11. The method according to claim 1, wherein the porosity parameter
comprises an average pore size, an average pore volume, a pore size
distribution, a pore microstructure, or combinations thereof.
12. The method according to claim 1, wherein the porous thermal
barrier coating comprises a plurality of pores such that at least
some pores of the plurality of pores are intragranular.
13. The method according to claim 1, wherein the controlling the
porosity parameter of the porous thermal barrier coating comprises
controlling an average pore size of a plurality of pores in the
porous thermal barrier coating in a range from about 0.1 microns to
about 25 microns.
14. The method according to claim 1, wherein the controlling the
porosity parameter of the porous thermal barrier coating comprises
controlling an average pore volume of a plurality of pores in the
porous thermal barrier coating in a range from about 5 volume % to
about 10 volume %.
15. The method according to claim 1, wherein the controlling the
porosity parameter of the thermal barrier coating further comprises
forming a graded porosity across a thickness of the thermal barrier
coating.
16. A method of forming a porous thermal barrier coating,
comprising: disposing a feedstock material using an air plasma
spray process on a substrate to form the porous thermal barrier
coating, wherein the feedstock material comprises a gas-forming
additive and a thermal barrier coating material, and wherein the
disposing comprises controlling a porosity parameter of the porous
thermal barrier coating by controlling a temperature of the
disposed feedstock material on the substrate using an auxiliary
heat source.
17. The method according to claim 16, wherein the disposed
feedstock material on the substrate is heated to a temperature in a
range from about 1000.degree. C. to about 1500.degree. C.
18. The method according to claim 16, wherein the gas-forming
additive comprises elemental carbon.
19. The method according to claim 16, wherein the thermal barrier
coating material comprises yttria-stabilized zirconia.
20. A method of forming a porous thermal barrier coating comprising
a graded porosity, the method comprising: disposing a feedstock
material on a substrate to form the porous thermal barrier coating,
wherein the feedstock material comprises a gas-forming additive and
a thermal barrier coating material, and wherein the disposing
comprises forming the graded porosity in the thermal barrier
coating by controlling: an amount of the gas-forming additive in
the feedstock material, a temperature of the disposed feedstock
material on the substrate using an auxiliary heat source, or a
combination thereof.
Description
BACKGROUND
[0001] The disclosure relates generally to methods for forming
porous thermal barrier coatings. More particularly, the disclosure
relates to controlling a porosity parameter of porous thermal
barrier coatings.
[0002] Thermal barrier coatings are typically used in articles that
operate at or are exposed to high temperatures. Aviation turbines
and land-based turbines, for example, may include one or more
components protected by the thermal barrier coatings. Examples of
materials used for thermal barrier coatings include rare
earth-stabilized zirconia materials such as yttrium-stabilized
zirconia (YSZ). Rare earth stabilized zirconia materials have a
thermal conductivity of about 2.2 W/m-K when evaluated as a dense
sintered compact. The YSZ is widely used as a thermal barrier
coating material in gas turbines, in part, because of its high
temperature capability, low thermal conductivity, and relative ease
of deposition. In recent years, there has been a growing demand for
further improvements in the thermal barrier properties to decrease
the overall weight, thickness, and amount of materials used to form
thermal barrier coatings.
[0003] The thermal conductivity of thermal barrier coatings may
also be reduced by increasing the porosity of the coatings.
Conventionally thermal barrier coatings may be formed using
suitable deposition techniques, such as, for example, by air plasma
spraying (APS) or by electron beam physical vapor deposition
(EPVD). Thermal barrier coatings deposited by the APS process may
typically have a microstructure characterized by irregular fattened
grains surrounded by inhomogeneous porosity. Thermal barrier
coatings deposited by the EBPVD process may yield a columnar,
strain-tolerant grain structure that may be able to expand and
contract without causing stresses that lead to spallation. However,
the EBPVD process may be more capital intensive than the APS
process. Therefore, there is a need for improved coating processes
that enable control over the porosity of the thermal barrier
coatings, thereby controlling the thermal conductivity of the
thermal barrier coatings.
BRIEF DESCRIPTION
[0004] One embodiment of the disclosure is directed to a method of
forming a porous thermal barrier coating by disposing a feedstock
material on a substrate. The feedstock material includes a
gas-forming additive and a thermal barrier coating material. The
disposing step further includes controlling a porosity parameter of
the porous thermal barrier coating by controlling the feedstock
material feed rate, an amount of the gas-forming additive in the
feedstock material, the temperature of the disposed feedstock
material on the substrate, or combinations thereof.
[0005] Another embodiment of the disclosure is directed to a method
of forming a porous thermal barrier coating by disposing a
feedstock material using an air plasma spray process on a
substrate. The feedstock material includes a gas-forming additive
and a thermal barrier coating material. The disposing step further
includes controlling a porosity parameter of the porous thermal
barrier coating by controlling the temperature of the disposed
feedstock material on the substrate using an auxiliary heat
source.
[0006] Another embodiment of the disclosure is directed to a method
of forming a porous thermal barrier coating including a graded
porosity. The method includes disposing a feedstock material on a
substrate to form the porous thermal barrier coating, wherein the
feedstock material includes a gas-forming additive and a thermal
barrier coating material. The disposing includes forming the graded
porosity in the thermal barrier coating by controlling an amount of
the gas-forming additive in the feedstock material, a temperature
of the disposed feedstock material on the substrate using an
auxiliary heat source, or a combination thereof.
DRAWINGS
[0007] These and other features, aspects, and advantages of the
present disclosure will become better understood when the following
detailed description is read with reference to the accompanying
drawings, in which like characters represent like parts throughout
the drawings, wherein:
[0008] FIG. 1 illustrates a method of forming a porous thermal
barrier coating, in accordance with an embodiment of the
disclosure;
[0009] FIG. 2 illustrates a method of forming a porous thermal
barrier coating, in accordance with an embodiment of the
disclosure.
[0010] FIG. 3 illustrates a method of forming a porous thermal
barrier coating, in accordance with an embodiment of the
disclosure.
[0011] FIG. 4 illustrates a sectional view of a schematic of a
porous thermal barrier coating, in accordance with an embodiment of
the disclosure;
[0012] FIG. 5 illustrates another sectional view of a schematic of
a porous thermal barrier coating, in accordance with an embodiment
of the disclosure; and
[0013] FIG. 6 illustrates a scanning electron microscope (SEM)
photomicrograph of a porous thermal barrier coating, in accordance
with an embodiment of the disclosure.
DETAILED DESCRIPTION
[0014] Approximating language, as used herein throughout the
specification and claims, may be applied to modify any quantitative
representation that could permissibly vary without resulting in a
change in the basic function to which it is related. Accordingly, a
value modified by a term such as "about" is not to be limited to
the precise value specified. In some instances, the approximating
language may correspond to the precision of an instrument for
measuring the value. Here and throughout the specification and
claims, range limitations may be combined and/or interchanged, such
ranges are identified and include all the sub-ranges contained
therein unless context or language indicates otherwise.
[0015] In the following specification and the claims, the singular
forms "a", "an" and "the" include plural referents unless the
context clearly dictates otherwise. As used herein, the term "or"
is not meant to be exclusive and refers to at least one of the
referenced components being present and includes instances in which
a combination of the referenced components may be present, unless
the context clearly dictates otherwise.
[0016] As used herein, the terms "may" and "may be" indicate a
possibility of an occurrence within a set of circumstances; a
possession of a specified property, characteristic or function;
and/or qualify another verb by expressing one or more of an
ability, capability, or possibility associated with the qualified
verb. Accordingly, usage of "may" and "may be" indicates that a
modified term is apparently appropriate, capable, or suitable for
an indicated capacity, function, or usage, while taking into
account that in some circumstances, the modified term may sometimes
not be appropriate, capable, or suitable.
[0017] As used herein, the term "coating" refers to a material
disposed on at least a portion of an underlying surface in a
continuous or discontinuous manner. Further, the term "coating"
does not necessarily mean a uniform thickness of the disposed
material, and the disposed material may have a uniform or a
variable thickness. The term "coating" may refer to a single layer
of the coating material or may refer to a plurality of layers of
the coating material. The coating material may be the same or
different in the plurality of layers.
[0018] As used herein, the term "disposed on" refers to layers or
coatings disposed directly in contact with each other or indirectly
by having intervening layers there between, unless otherwise
specifically indicated.
[0019] One embodiment of the disclosure is directed to a method of
forming a porous thermal barrier coating. The method includes
disposing a feedstock material on a substrate to form the porous
thermal barrier coating, wherein the feedstock material includes a
gas-forming additive and a thermal barrier coating material. The
disposing step includes controlling a porosity parameter of the
porous thermal barrier coating by controlling a feedstock material
feed rate, an amount of the gas-forming additive in the feedstock
material, a temperature of the disposed feedstock material on the
substrate, or combinations thereof.
[0020] FIG. 1 illustrates a method 10 in accordance with some
embodiments of the present disclosure. The method 10 includes
providing a substrate 110, at step 11, disposing a feedstock
material 121 on the substrate 110 to form a disposed feedstock
material 120, at step 12, and forming a porous thermal barrier
coating 130 on the substrate 110, at step 13.
[0021] It should be noted that although in FIG. 1, the substrate
110 is shown has having a planar profile for ease of illustration,
the substrate 110 may have any suitable geometry or profile, for
example, a complex geometry, a non-planar profile, or a combination
of both. As used herein, the term "complex geometry" refers to
shapes not easily or consistently identifiable or reproducible,
such as, not being square, circular, or rectangular. In some
embodiments, the substrate 110 may be a part of a component exposed
to a high temperature environment, for example, a turbine engine.
In some embodiments, the turbine engine may be an aircraft engine.
Alternatively, the turbine engine may be any other type of engine
used in industrial applications. Non-limiting examples of such
turbine engines include a land-based turbine engine employed in a
power plant, a turbine engine used in a marine vessel, or a turbine
engine used in an oil rig. Non-limiting examples of turbine engine
components include turbine airfoils such as blades and vanes,
turbine shrouds, turbine nozzles, buckets, combustor components
such as liners and deflectors, heat shields, augmentor hardware of
gas turbine engines, and other similar turbine components known to
those skilled in the art.
[0022] The substrate 110 may include a ceramic matrix composite or
a metallic superalloy. Non-limiting examples of suitable metallic
superalloys include iron-based superalloys, cobalt based
superalloys, nickel based superalloys, or combinations thereof.
[0023] The substrate 110 may be a pre-fabricated component of a
turbine engine, or, may be manufactured before the disposing step.
In some embodiments, the step 11, of providing the substrate may
include one or more preparatory steps, for example, cleaning,
polishing, disposing a bond coating, and the like. In some
embodiments, the substrate 110 may be coated with a bond coating
(not shown in Figures), at step 11. The bond coating may be formed
from a metallic oxidation-resistant material that protects the
underlying substrate 110 and enables the porous thermal barrier
coating 130 to more tenaciously adhere to substrate 110. Suitable
materials for the bond coating include M.sub.1CrAlY alloy powders,
where M.sub.1 represents a metal such as iron, nickel, platinum or
cobalt. Non-limiting examples of other suitable bond coat materials
include metal aluminides such as nickel aluminide, platinum
aluminide, or a combination thereof.
[0024] As mentioned earlier, the feedstock material 121 is disposed
on the substrate 110 to form a disposed feedstock material 120, at
step 12. As used herein, the term "feedstock material" refers to a
homogenous mixture of two or more materials forming a single phase,
or, alternatively, to a heterogenous mixture of two or more
materials forming more than one phase. The feedstock material 121
may be in a solid form, in a liquid form, or in a semi-solid form.
In certain embodiments, the feedstock material 121 is in the form
of a powder.
[0025] As stated earlier, the feedstock material 121 includes a
gas-forming additive and a thermal barrier coating material. In
certain embodiments, the feedstock material 121 includes a
homogeneous mixture of the gas-forming additive and the thermal
barrier coating material. In certain embodiments, the gas-forming
additive is pre-dissolved into the thermal barrier coating material
to form the feedstock material 121. Without being bound by any
theory, it is believed that by incorporating the gas-forming
additive in the feedstock material 121 at the time of fabrication
of the feedstock material 121 (for example, a feedstock powder), a
porosity parameter of the porous thermal barrier coating 130 may be
controlled. For example, by controlling one or more of the amount,
the size, or the distribution of the gas-forming additive in the
feedstock material 121.
[0026] As used herein, the term "gas-forming additive" refers to a
material which, at an elevated temperature, is capable of oxidizing
into a non-reactive and insoluble (with the thermal barrier coating
material) gas that is entrapped by the thermal barrier coating
material, thereby forming pores. Examples of suitable gas-forming
additives include, but are not limited to, graphite, carbides,
oxycarbides, nitrides, or combination thereof. In certain
embodiments, the gas forming additive includes elemental carbon. As
described in detail later, during or after the disposing step, the
gas forming additive forms a gas, for example, carbon monoxide,
carbon dioxide, nitrous oxide, or any suitable gas depending on the
composition of the gas-forming additive employed. The insoluble gas
is entrapped in the thermal barrier coating during the disposing or
the post-disposing steps, thereby forming pores. In some
embodiments, a substantial amount of the gas formed is entrapped in
the thermal barrier coating material. The term "substantial amount
of the gas" as used herein refers to at least 90 volume % of the
gas formed. This is in contrast to fugitive materials employed to
form porous coatings, wherein the coating materials are subjected
to elevated temperatures such that the fugitive materials decompose
or oxidize, and the resulting gases are expelled from the coatings,
thereby resulting in pores.
[0027] As used herein, the term "thermal barrier coating" refers to
a coating that includes a material capable of reducing heat flow to
the underlying substrate of the article, that is, form a thermal
barrier. The composition of the porous thermal barrier coating in
terms of the type and amount of the thermal barrier coating
materials may depend upon one or more factors, including the
composition of the adjacent bond coat layer (if present), the
coefficient of thermal expansion (CTE) characteristics desired for
the thermal barrier coating, and the thermal barrier properties
desired for the thermal barrier coating.
[0028] Non-limiting examples of suitable thermal barrier coating
materials include zirconias, pyrochlores, or combinations thereof.
In some embodiments, the thermal barrier material includes
chemically stabilized zirconias (for example, metal oxides blended
with zirconia), such as yttria-stabilized zirconias,
ceria-stabilized zirconias, calcia-stabilized zirconias,
scandia-stabilized zirconias, magnesia-stabilized zirconias,
india-stabilized zirconias, ytterbia-stabilized zirconias,
lanthana-stabilized zirconias, gadolinia-stabilized zirconias, as
well as mixtures of such stabilized zirconias.
[0029] In certain embodiments, the thermal barrier coating material
includes yttria-stabilized zirconias. Suitable yttria-stabilized
zirconias may include from about 1 wt % to about 20 wt % yttria
(based on the combined weight of yttria and zirconia), and more
typically from about 3 wt % to about 10 wt % yttria. An example
yttria-stabilized zirconia thermal barrier coating includes about 7
wt % yttria and about 93 wt % zirconia. These chemically stabilized
zirconias may further include one or more of a second metal (e.g.,
a lanthanide or actinide) oxide such as dysprosia, erbia, europia,
gadolinia, neodymia, praseodymia, urania, and hafnia to further
reduce thermal conductivity of the thermal barrier coating.
[0030] As used herein, the term "porous thermal barrier coating"
refers to a coating including a plurality of pores. The term
"porosity parameter of the porous thermal barrier coating" as used
herein refers to one or more of pore size, pore size distribution,
number of pores, or pore microstructure of the plurality of pores,
in the porous thermal barrier coating 130. The pore size provides
an indication of the median or average size of the pores in the
porous thermal barrier coating 130. The pore size distribution
provides a quantitative description of the range of pore sizes
present across the length, breadth and thickness of the porous
thermal barrier coating 130. Pore volume is the percentage of
volume occupied by the plurality of pores in the total volume
occupied by the porous thermal barrier coating 130, and is also
referred to as the "total porosity" of the porous thermal barrier
coating 130. By varying one of more of the aforementioned porosity
parameters, the total porosity of the plurality of pores in the
porous thermal barrier coating 130 may be controlled. One or more
of the pore size, the pore shape, the number of pores, the pore
size distribution, or the pore microstructure in the porous thermal
barrier coating 130 may be controlled using the methods described
in the present disclosure.
[0031] In some embodiments, an average pore size of the plurality
of pores in the porous thermal barrier coating 130 is in a range
from about 0.1 microns to about 25 microns. In some embodiments, an
average pore size of the plurality of pores in the porous thermal
barrier coating 130 is in a range from about 0.25 microns to about
5 microns. The plurality of pores in the porous thermal barrier
coating 130 may be characterized any suitable shape. In certain
embodiments, the shape of the pores in the porous thermal barrier
coating may be substantially spherical. In some embodiments,
spheroidal porosity in the porous thermal barrier coating 130 may
provide a strain tolerant microstructure, thereby allowing the
thermal barrier coating to operate under the gas turbine operating
conditions for much longer periods.
[0032] Referring again to FIG. 1, at step 12, the feedstock
material 121 is disposed on the substrate 110 using a suitable
apparatus 115. The feedstock material 121 may be disposed on a bond
coating (if present) or on the substrate 110 directly by any of a
variety of techniques, including vapor disposition, such as
physical vapor deposition (PVD), electron beam physical vapor
deposition (EBPVD); plasma spray, such as air plasma spray (APS),
suspension plasma spray (SPS), and vacuum plasma spray (VPS); other
thermal spray deposition methods such as high velocity oxy-fuel
(HVOF) spray, detonation, or wire spray; chemical vapor deposition
(CVD), sol-gel method, or combinations of two or more of the
afore-mentioned techniques.
[0033] The particular technique used for disposing, depositing or
otherwise forming the porous thermal barrier coating 130 may depend
on one or more of the composition of the porous thermal barrier
coating 130, the thickness, and the physical structure desired for
the porous thermal barrier coating 130. In certain embodiments, the
feedstock material 121 is disposed using plasma spray techniques,
in particular, APS technique. As mentioned earlier, the gas-forming
additive and the thermal barrier coating material is co-deposited
as a feedstock material 121 on the substrate 110 or the bond
coating (if present). In some embodiments, co-depositing may be
achieved by blending, mixing or otherwise combining the gas-forming
additive and the thermal barrier coating material together (for
example, as powders) to provide a mixture that is then deposited
onto substrate/bond coating. The blending or mixing of the
gas-forming additive and the thermal barrier coating material may
be effected prior to providing the feedstock material to the
deposition apparatus 115 (for example, an APS gun), or may be
effected in the deposition apparatus 115 itself, therein forming
the feedstock material. In certain embodiments, the gas-forming
additive is mixed and dissolved in the thermal barrier coating
material prior to providing the feedstock material 121 to the
deposition apparatus 115. The term "disposed feedstock material" as
used herein refers to an as-deposited feedstock material, i.e.,
feedstock material that has not been subjected to additional steps
(e.g., heating), or, alternately to a feedstock material that has
been subjected to additional steps (e.g., heating via an auxiliary
heat source) after the disposing step. The term "disposed feedstock
material" as used herein is differentiated from a "porous thermal
barrier coating" such that in the "disposed feedstock material" the
thermal barrier coating material is in a partially or completely
molten state, and the pores may still not be entrapped within the
coating.
[0034] The disposing step 12 further includes controlling the
feedstock material 121 feed rate, an amount of the gas-forming
additive in the feedstock material 121, or the temperature of the
disposed feedstock material 120 on the substrate 110 to form a
porous thermal barrier coating 130. By controlling one or more of
these parameters, the porosity parameter (and therefore, a total
porosity) of the porous thermal barrier coating 130 is controlled.
Without being bound by any theory, it is believed that, in the
absence of this controlling step, an uncontrolled, non-spheroidal,
or randomly distributed porosity in the porous thermal barrier
coating 130 may result.
[0035] In some embodiments, the porosity parameter of the porous
thermal barrier coating 130 is controlled by controlling one or
both a feedstock material 121 feed rate and an amount of the
gas-forming additive in the feedstock material 121. The term "feed
rate" as used herein refers to rate of deposition of the feedstock
material 121 on the substrate 110, using a suitable deposition
apparatus 115. In embodiments, wherein the feedstock material is
deposited using the APS process, the term "feed rate" refers to the
spray rate of the feedstock material 121. In some embodiments, the
porosity parameter of porous thermal barrier coating 130 is
controlled by controlling an amount of the gas-forming additive in
the feedstock material 121 in a range from about 0.1 wt % to about
10 wt %. In some embodiments, the porosity parameter of porous
thermal barrier coating 130 is controlled by controlling an amount
of the gas-forming additive in the feedstock material 121 in a
range from about 0.5 wt % to about 5 wt %. In some embodiments, as
described in detail later, the amount of gas-forming additive in
the feedstock material 121 may be varied over the duration of the
disposing step such that the disposed feedstock material 120
includes a graded content of the gas-forming additive, thereby
forming a graded porosity in the resultant porous thermal barrier
coating 130. In such embodiments, the term "amount of gas-forming
additive" refers to an average amount of gas-forming additive in
the feedstock material 121 over the entire duration of the
disposing step.
[0036] In some embodiments, the porosity parameter of porous
thermal barrier coating 130 is controlled by controlling the
feedstock material 121 feed rate in a range from about 2.5 gm/min
to about 100 gm/min. In some embodiments, the porosity parameter of
porous thermal barrier coating 130 is controlled by controlling the
feedstock material 121 feed rate in a range from about 20 gm/min to
about 50 gm/min. The feed rate may be controlled by using a valve
or any other suitable method. This is in contrast to methods used
to form porous thermal barrier coatings, wherein the feed rate or
the amount of the gas-forming additive in the feedstock material
are not controlled, which may result in uncontrolled and random
porosity.
[0037] In some embodiments, the porosity parameter of porous
thermal barrier coating 130 is controlled by controlling the
temperature of the disposed feedstock material 120 on the substrate
110. The temperature of the disposed feedstock material 120 on the
substrate 110 may be controlled by controlling one or more of the
temperature of the feedstock material 121 before depositing (e.g.,
by pre-heating the feedstock material), temperature of deposition
(e.g., the spray temperature if using APS for deposition or by
using an auxiliary heat source during deposition); or the
temperature of the substrate 110 on which the feedstock material is
being deposited. In certain embodiments, the temperature of the
disposed feedstock material 120 on the substrate 110 is controlled
by a combination of pre-heating the substrate and by maintaining
the disposed feedstock material temperature.
[0038] In some embodiments, the disposed feedstock material 120 on
the substrate 110 is heated to a temperature greater than a
temperature that the substrate 110 can withstand. As used herein,
the term "temperature that the substrate can withstand" refers to a
temperature beyond which the substrate may start to deform, melt,
or change form. In some embodiments, the disposed feedstock
material may be heated to a temperature similar to a turbine engine
operating temperature. Depositing and heating the feedstock
material to a temperature similar to the engine operating
temperature may result in reduced coating stresses of the
interface, while at that temperature, therefore, potentially
improving the lifetime of the thermal barrier coating in the
engine. In some embodiments, the disposed feedstock material 120 on
the substrate 110 is heated to a temperature in a range from about
1000.degree. C. to about 1500.degree. C. In certain embodiments,
the disposed feedstock material 120 on the substrate 110 is heated
to a temperature in a range from about 1150.degree. C. to about
1300.degree. C.
[0039] The disposed feedstock material 120 may be heated using an
auxiliary heat source. The term "auxiliary heat source" refers to a
heat source employed in addition to the primary apparatus used for
disposing the feedstock material 121. For example, when disposing
the feedstock material using an APS technique, the APS apparatus
may include a primary heat source that is distinct and separate
from the auxiliary heat source. Suitable auxiliary heat sources
include, but are not limited to, infrared (IR) sources, plasma
sources, inductors, or combinations thereof. In some embodiments,
the auxiliary heat source is a plasma source that is different from
the plasma source used for the APS process. In certain embodiments,
the auxiliary heat source includes an induction coil.
[0040] Another embodiment of the disclosure is directed to a method
of forming a porous thermal barrier coating using an auxiliary heat
source. The method includes disposing a feedstock material using an
air plasma spray process on a substrate to form the porous thermal
barrier coating, wherein the feedstock material includes a
gas-forming additive and a thermal barrier coating material, and
wherein the disposing step includes controlling a porosity
parameter of the porous thermal barrier coating by controlling a
temperature of the disposed feedstock material on the substrate
using the auxiliary heat source.
[0041] FIG. 2 illustrates a method 20 in accordance with an
embodiment of the present disclosure. The method 20 includes
providing a substrate 110, at step 14; disposing a feedstock
material using an APS apparatus 115 on the substrate 110 to form a
disposed feedstock material 120, at step 15; and forming a porous
thermal barrier coating 130 on the substrate 110, at step 16. The
method further includes, controlling a temperature of the disposed
feedstock material, at step 15, using an auxiliary heat source 125.
Non-limiting examples of suitable auxiliary heat sources are
described herein earlier. Further, it should be noted that although
FIG. 2 illustrates a single auxiliary heat source 125, one or more
heat sources 125 may be employed depending on the size and shape of
the substrate. Furthermore, one or more of the configuration of the
auxiliary heat source 125, the placement of the auxiliary heat
source 125, and the proximity of the auxiliary heat source 125 to
the substrate 110 may be varied depending on the degree of heating
required.
[0042] Referring now to FIGS. 1 and 2, in some embodiments, the
heating of the disposed feedstock material 120 is effected by one
or more of pre-heating the substrate 110, simultaneously disposing
and heating the feedstock material 121, or heating the disposed
feedstock material 120 after the disposing step 12,15. In certain
embodiments, the heating of the disposed feedstock material 120 is
effected by pre-heating the substrate 110 prior to the disposing
step 12,15. In some such instances, the substrate 110 may be
pre-heated to a first temperature using the auxiliary heat source
125 and the feedstock material 121 may be deposited on the
pre-heated substrate. The first temperature may be sufficient to
melt the thermal barrier coating material or maintain an already
molten thermal barrier coating material in the molten state, but
lower than the temperature that the substrate 110 can withstand. In
some embodiments, during the disposing step 12,15 the feedstock
material may be further heated to a second temperature using the
auxiliary heat source 125. The second temperature may be sufficient
to result in oxidation of the gas-forming additive thereby forming
a gas in the molten thermal barrier coating material, but greater
than the temperature that the substrate can withstand. For example,
for nickel or cobalt-based superalloys, the auxiliary heat source
may heat the disposed feedstock material 120 to a temperature
greater than the melting point of these superalloys, such that the
gases are formed.
[0043] The method may further include cooling the disposed
feedstock material 120 to form the porous thermal barrier coating
130, at step 13,16. In some embodiments, by employing a pre-heated
substrate, the gas-forming additive containing feedstock material
121 is deposited at a temperature such that the gas-forming
additive oxidizes and forms a gas. This gas may form while the
feedstock material is still molten causing the gas bubbles to form
pores. In some embodiments, the rate of cooling of the disposed
feedstock material 120 is such that these pores are entrapped
within the disposed feedstock material 120. As mentioned earlier,
the porosity of these entrapped pores may be controlled using the
methods described herein. In some embodiments, as described in
detail later, the auxiliary heat source 125 may be further
controlled such that the heating from the auxiliary heat source 125
may be effected to generate a graded porosity in the porous thermal
barrier coating 130.
[0044] Another embodiment of the disclosure is directed to a method
of forming a porous thermal barrier coating including a graded
porosity. The method includes disposing a feedstock material on a
substrate to form the porous thermal barrier coating, wherein the
feedstock material includes a gas-forming additive and a thermal
barrier coating material. The disposing includes forming the graded
porosity in the thermal barrier coating by controlling an amount of
the gas-forming additive in the feedstock material, a temperature
of the disposed feedstock material on the substrate using an
auxiliary heat source, or a combination thereof.
[0045] The term "graded porosity" as used herein refers to a
variation in the volume percentage of the porous thermal barrier
coating 130 occupied by the plurality of the pores, across a
thickness of the porous thermal barrier coating 130. For a specific
region of the porous thermal barrier coating 130, the volume
percentage occupied by the plurality of the pores may be referred
to as the "porosity" in that specific region. Further, the term
graded porosity encompasses a discrete variation in porosity, a
continuous variation in porosity, or a combination thereof. For
example, in some embodiments, the method may include forming a
graded porosity in the porous thermal barrier coatings 130 such
that the porosity continuously increases or decreases across a
thickness of the porous thermal barrier coating 130 from a region
disposed proximate to the substrate 110 (or the bond coating if
present) to a surface of the porous thermal barrier coating 130. In
some other embodiments, the feedstock material 121 may be disposed
on the substrate 110 (or the bond coating if present) in the form
of discrete layers such that there is a step change (increase or
decrease) of the porosity across the different layers of the
resulting porous thermal barrier coating 130. In certain
embodiments, the method includes forming a porous thermal barrier
coating 130 such that regions proximate to the substrate 110 (or
the bond coating if present) and the surface of the porous thermal
barrier coating 130 may be substantially free of porosity. The
intermediate region may have a graded porosity that may be discrete
or continuous. Further the porosity in the intermediate region may
increase or decrease depending on the desired properties of the
porous thermal barrier coating. Without being bound by any theory,
it is believed that a graded porosity across a thickness of the
porous thermal barrier coating 130 may provide desired performance
characteristics, depending on the end-use application. For example,
by minimizing the porosity in a layer/region proximate to the
surface of the porous thermal barrier coating, erosion or impact
resistance of the coating may be enhanced. In some other
applications, a porous surface of the thermal barrier coating may
be desired, for example, to improve sacrificial properties of the
coating.
[0046] The porosity of the porous thermal barrier coating 130 in
different regions/layers of the thermal barrier coating 130 may be
varied by varying one or both of a number of pores in the different
regions/layers and an average size of the plurality of pores in the
different regions/layers. In certain embodiments, a graded porosity
across a thickness of the porous thermal barrier coating is formed
by controlling an amount of the gas-forming additive in the
feedstock material, a temperature of the disposed feedstock
material on the substrate using an auxiliary heat source, or a
combination thereof.
[0047] Referring back to FIGS. 1 and 2, in some embodiments, a
graded porosity across a thickness of the porous thermal barrier
coating 130 may be formed, for example, by controlling an amount of
the gas-forming additive in the feedstock material 121. By varying
the amount of the gas-forming additive in the feedstock material
121, the amount of gas-forming additive in the disposed feedstock
material 120 over a duration of the disposing step 12, 15 may be
varied. Therefore, resulting in a graded content of the gas-forming
additive in disposed feedstock material 120. This graded content of
the gas-forming additive in the disposed feedstock material 120,
upon oxidation may result in a graded porosity. In some
embodiments, the amount of gas-forming additive in the feedstock
material 121 may be varied by providing a plurality of feeds to the
deposition apparatus 115 with varying gas-forming additive content,
and controlling the feed into the deposition apparatus 115.
[0048] With continued reference to FIG. 2, in some other
embodiments, a graded porosity across a thickness of the porous
thermal barrier coating 130 may be formed, for example, by
controlling the temperature of the disposed feedstock material 120.
In such embodiments, the auxiliary heat source 125 may be turned on
or off, during the duration of the disposing step 15 depending on
the desired gradation in porosity. For example, for layers/regions
where minimal porosity is desired, the auxiliary heat source 125
may be turned off, thereby minimizing the formation of gases in
those layers/regions.
[0049] Referring now to FIG. 3, a method 30 of forming a porous
thermal barrier coating 130 with a graded porosity is illustrated.
The method 30 includes providing a substrate 110, at step 31;
disposing a thermal barrier coating material 112 on the substrate
110, at step 32; disposing a feedstock material 121 on the thermal
barrier coating material 112 to form a plurality of layers of
disposed feedstock material (120',120''), at step 33; disposing the
thermal barrier coating material 112 on an outermost layer 120'' of
the disposed feedstock material 120'', at step 34, and forming a
porous thermal barrier coating 130 on the substrate 110, at step
35. The method further includes, controlling a temperature of the
disposed feedstock material 120', 120'', at step 33, using an
auxiliary heat source 125. Non-limiting examples of suitable
auxiliary heat sources are described herein earlier. In some
embodiments, the auxiliary heat source 125 may also be used in
steps 32 and 34 to dispose the thermal barrier coating material 112
on the substrate 110. It should be noted that although FIG. 3
illustrates two layers of disposed feedstock material (120',
120''), multiple layers of disposed feedstock material may be
present on the thermal barrier coating material 112 depending on
the total porosity requirement.
[0050] In some embodiments, the amount of gas-forming additive in
the disposed feedstock material 120' may be different than the
amount in the disposed feedstock material 120''. As mentioned
earlier, the amount of gas-forming additive in the disposed
feedstock material 120 may be varied by varying an amount of the
gas-forming additive in the feedstock material 121. This variation
in the amount of gas-forming additive in different layers may lead
to variation in the total porosity of each layer thereby producing
the porous thermal barrier coating 130 with a graded porosity.
Thus, in such embodiments, the porous thermal barrier coating 130
includes a plurality of layers (112, 120', 120'') such that the
porosity of each layer is different.
[0051] In some embodiments, the temperature of the disposed
feedstock material 120' may be different from a temperature of the
disposed feedstock material 120''. As mentioned earlier, the
temperature of the disposed feedstock material 120 may be varied by
controlling the auxiliary heat source 125. This variation of the
temperature in the different layers may lead to variation in the
total porosity of each layer, thereby producing the porous thermal
barrier coating 130 with a graded porosity. Thus, in such
embodiments, the porous thermal barrier coating 130 includes a
plurality of layers (112, 120', 120'') such that the porosity of
each layer is different.
[0052] FIGS. 4 and 5 illustrate a sectional view of a schematic of
a porous thermal barrier coating 130 including a plurality of pores
132, formed using the methods in accordance with some embodiments
of the disclosure. In some embodiments, controlling the porosity
parameter of the porous thermal barrier coating 130 includes
controlling an average pore size of a plurality of pores 132 in the
porous thermal barrier coating 130 in a range from about 0.1
microns to about 25 microns. In some embodiments, controlling the
porosity parameter of the porous thermal barrier coating 130
includes controlling an average pore size of a plurality of pores
132 in the porous thermal barrier coating 130 in a range from about
0.25 microns to about 5 microns. In some embodiments, controlling
the porosity parameter of the porous thermal barrier coating 130
includes controlling an average pore volume of a plurality of pores
132 in the porous thermal barrier coating 130 in a range from about
1 volume % to about 10 volume %. In some embodiments, controlling
the porosity parameter of the porous thermal barrier coating 130
includes controlling an average pore volume of a plurality of pores
132 in the porous thermal barrier coating 130 in a range from about
5 volume % to about 10 volume %.
[0053] In some embodiments, controlling the porosity parameter of
the porous thermal barrier coating 130 includes controlling the
pore microstructure of the plurality of pores 132 in the porous
thermal barrier coating 130. In some embodiments, the porous
thermal barrier coating 130 includes a plurality of pores 132 such
that at least some pores of the plurality of pores are
intragranular. The term "intragranular" as used herein means that
the pores are present inside the grains. In some embodiments, the
porous thermal barrier coating 130 includes a plurality of pores
132 such that at least some pores of the plurality of pores are
intergranular (present between the grains), or, present at the
grain boundaries. In certain embodiments, greater than 50% of the
plurality of pores are intragranular. In certain embodiments,
greater than 80% of the plurality of pores are intragranular.
[0054] FIG. 4 illustrates a schematic of a microstructure of the
porous thermal barrier coating 130 formed, in accordance with some
embodiments of the present disclosure. The microstructure of the
porous thermal barrier coating 130 as illustrated in FIG. 4 is
characterized by grains 134 having a plurality of grain boundaries
136. The microstructure further includes plurality of pores 132
present inside the grains 134 (intragranular pores).
[0055] FIG. 5 illustrates another schematic of a microstructure of
the porous thermal barrier coating 130 formed, in accordance with
some embodiments of the present disclosure. The microstructure of
the porous thermal barrier coating 130 as illustrated in FIG. 5 is
characterized by grains 134 having a plurality of grain boundaries
136. The microstructure further includes plurality of pores 132
present inside the grains 134 (intragranular pores) and plurality
of pores 138 at or between the grain boundaries 136 (intergranular
pores).
[0056] FIG. 6 illustrates a scanning electron microscopy (SEM)
photomicrograph of a porous thermal barrier coating 130 formed by
coating a mixture of YSZ and elemental carbon, using the APS
process. The microstructure of the porous thermal barrier coating
130 as illustrated in FIG. 6 is characterized by grains 134 having
a plurality of grain boundaries 136. The microstructure further
includes plurality of susbtantially spherical pores 132 present
inside the grains 134 (intragranular pores). The pores 132 are
generated by entrapped carbon-containing gas.
[0057] Without being bound by any theory, is believed that the
presence of gas-forming additive (e.g., elemental carbon) in the
feedstock material may result in additional porosity, because of
gases (e.g., carbon monoxide, carbon dioxide, and the like)
produced from the decomposition of the gas-forming additive at high
temperatures. These gases, because of being insoluble in the
thermal barrier coating material, may be trapped within the thermal
barrier coating material. The pressure exerted by the entrapped gas
on the surrounding thermal barrier material may inhibit pore
coarsening and redistribution in the microstructure, such that the
thermal barrier coating retains fine porosity and the
microstructure of the thermal barrier coating may be thermally
stabilized. The controlled porosity may further result in lower
thermal conductivity of the porous thermal barrier coating.
Therefore, in some such embodiments, the porous thermal barrier
coatings may provide enhanced thermal protection, because for the
same coating thickness, the temperature gradient across the coating
is higher. Alternatively, the turbine engine components can be
designed for thinner thermal barrier coatings and, where
applicable, lower cooling air flow rates. This may lead to
reduction in processing and material costs, and promote component
life and engine efficiency.
[0058] The foregoing examples are merely illustrative, serving to
exemplify only some of the features of the disclosure. Accordingly,
it is the Applicants' intention that the appended claims are not to
be limited by the choice of examples utilized to illustrate
features of the present disclosure. As used in the claims, the word
"comprises" and its grammatical variants logically also subtend and
include phrases of varying and differing extent such as for
example, but not limited thereto, "consisting essentially of" and
"consisting of." Where necessary, ranges have been supplied; those
ranges are inclusive of all sub-ranges there between. It is to be
expected that variations in these ranges will suggest themselves to
a practitioner having ordinary skill in the art and where not
already dedicated to the public, those variations should where
possible be construed to be covered by the appended claims. It is
also anticipated that advances in science and technology will make
equivalents and substitutions possible that are not now
contemplated by reason of the imprecision of language and these
variations should also be construed where possible to be covered by
the appended claims.
* * * * *