U.S. patent application number 16/104564 was filed with the patent office on 2019-05-23 for plasma processing apparatus and method for forming semiconductor device structure.
This patent application is currently assigned to Taiwan Semiconductor Manufacturing Co., Ltd.. The applicant listed for this patent is Taiwan Semiconductor Manufacturing Co., Ltd.. Invention is credited to Chih-Hao CHEN, Po-Ju CHEN, Yi-Wei CHIU, Chun-Hsing WU, Fang-Yi WU.
Application Number | 20190157048 16/104564 |
Document ID | / |
Family ID | 66533298 |
Filed Date | 2019-05-23 |
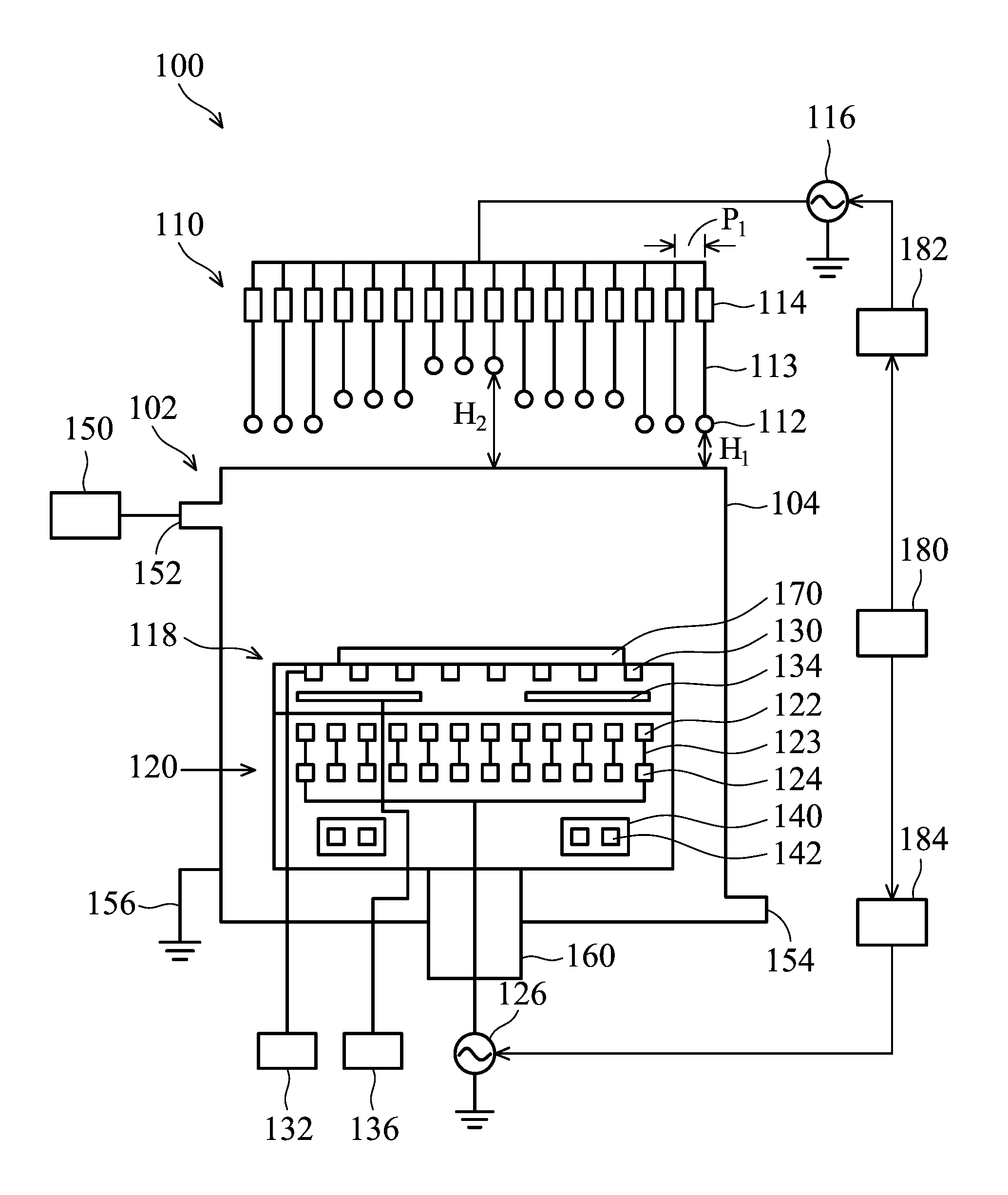



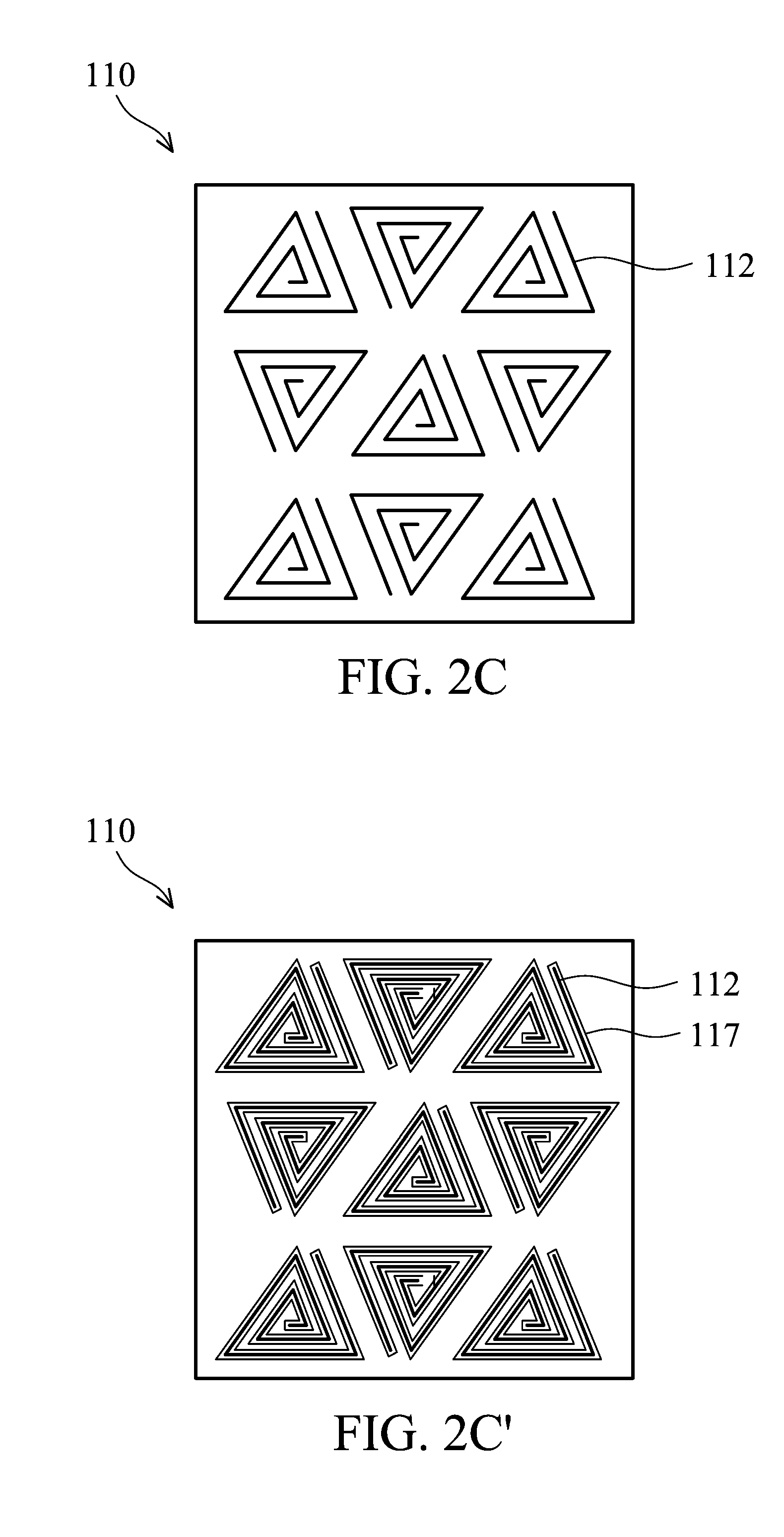

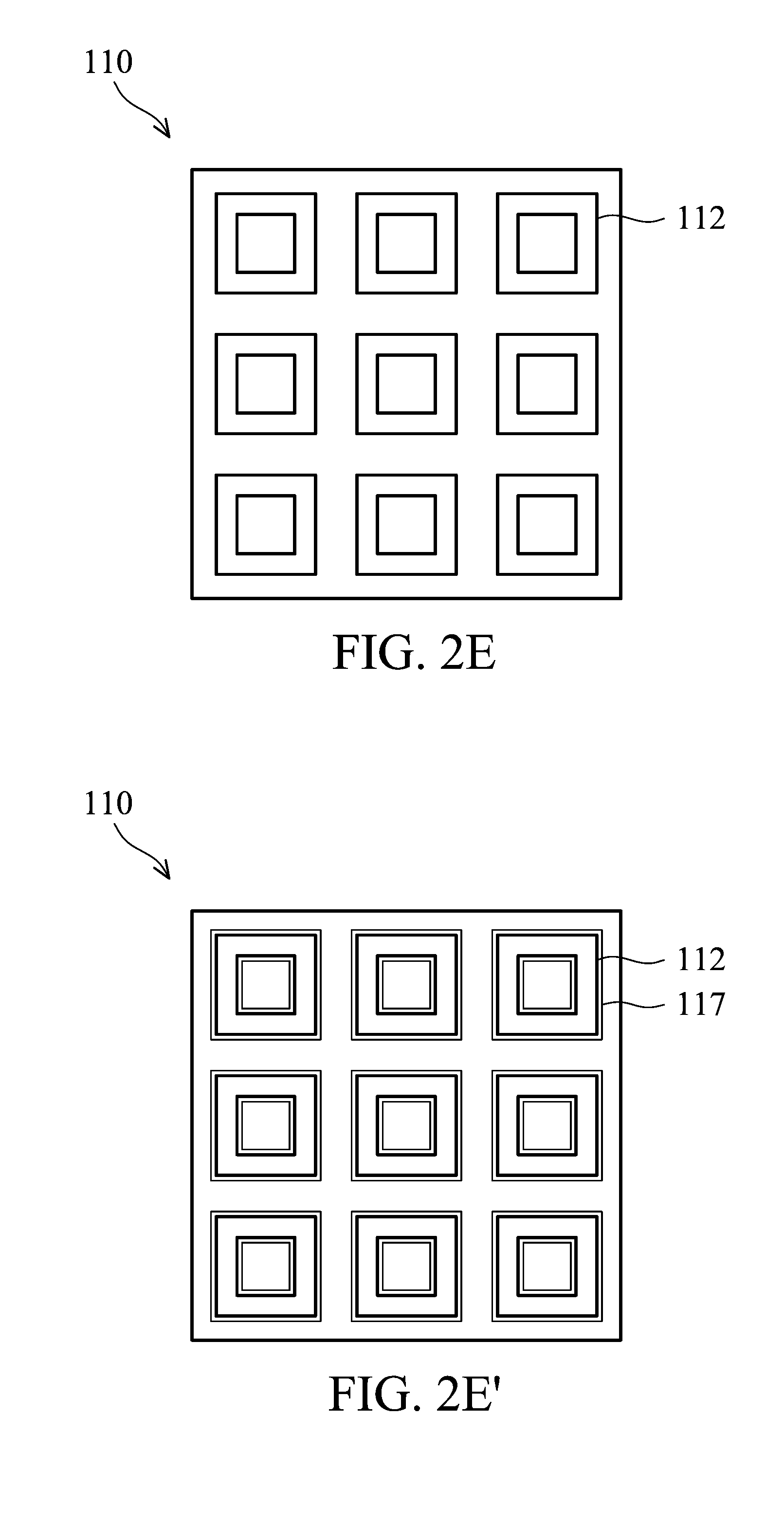
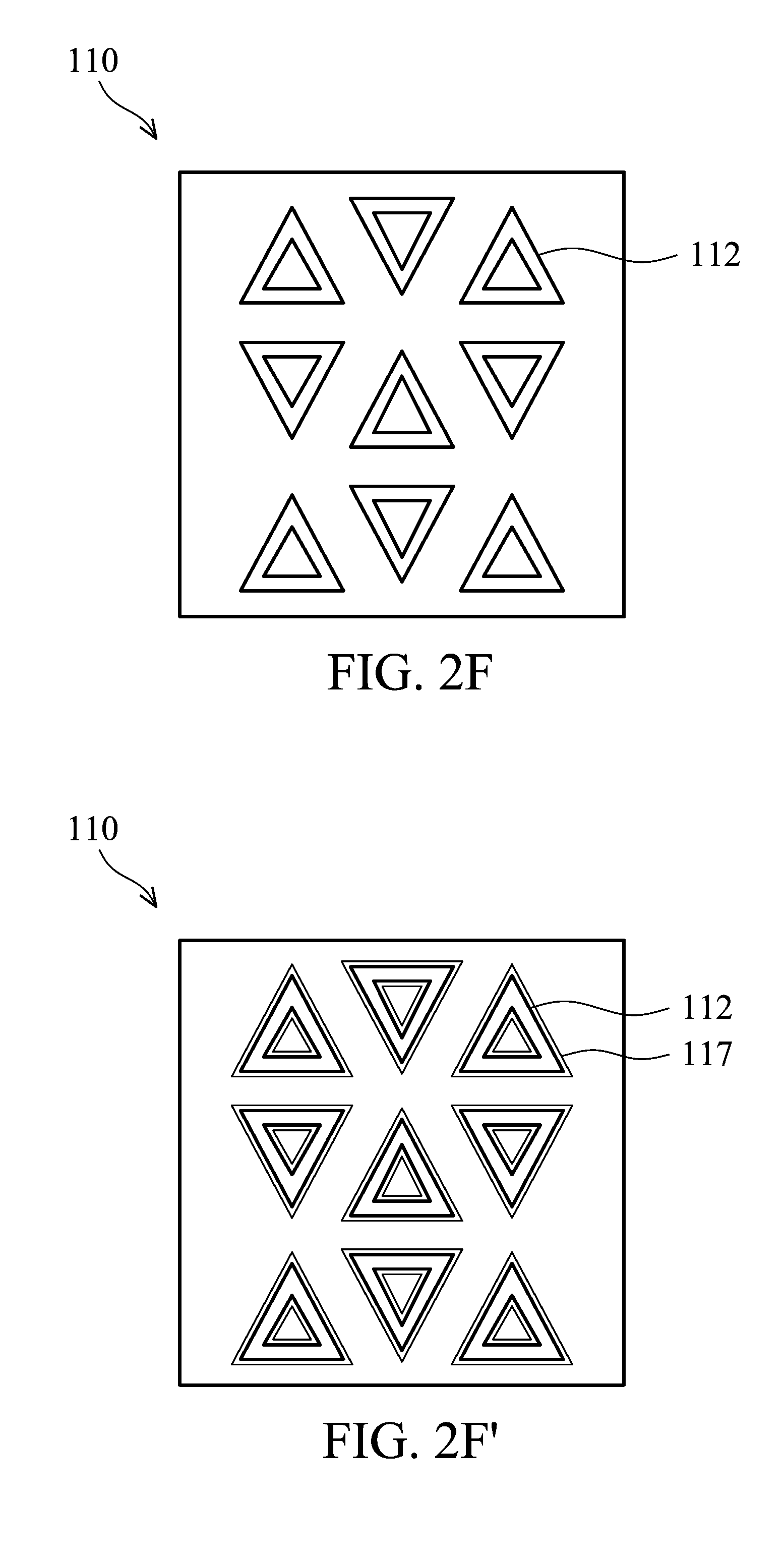

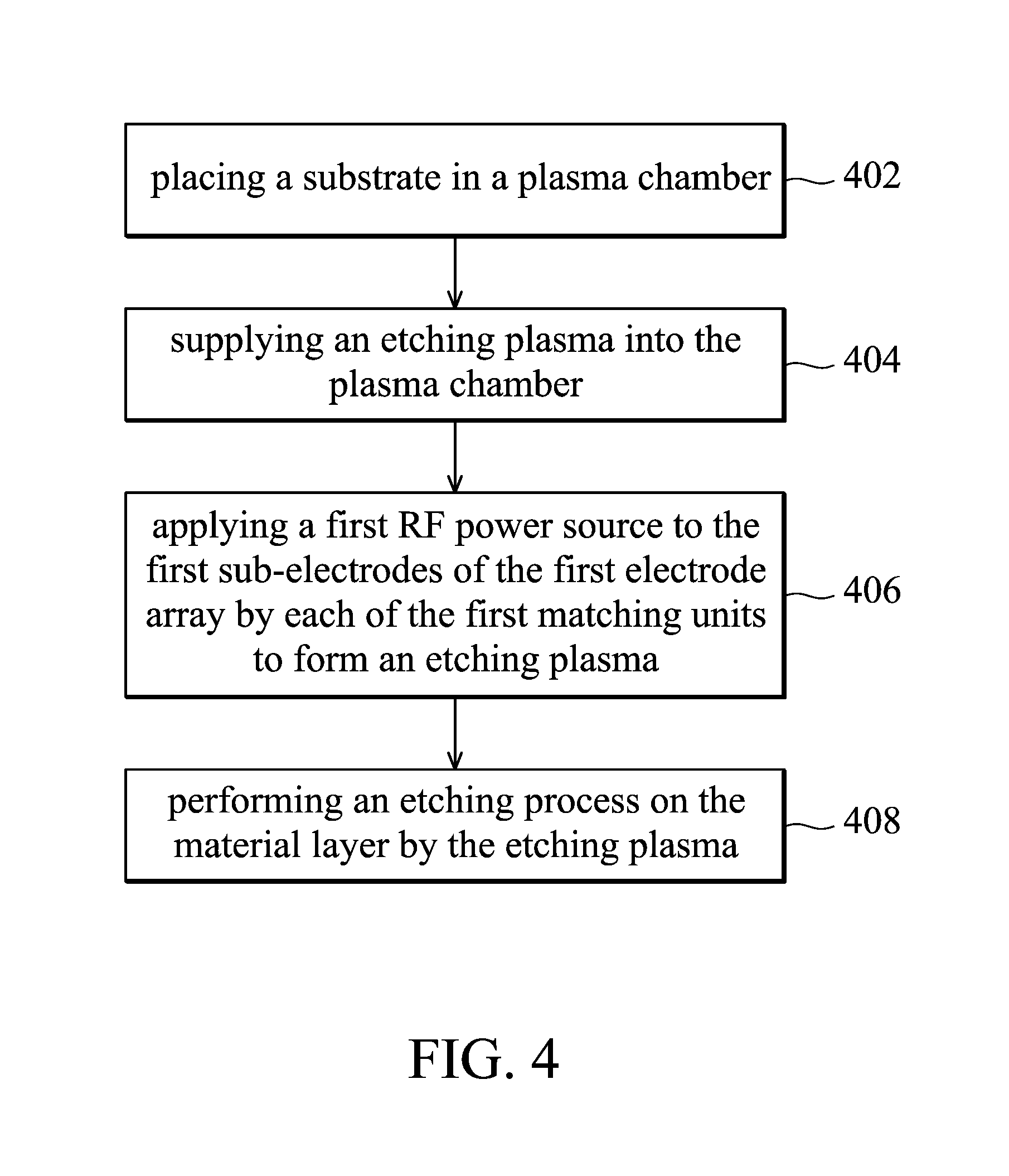
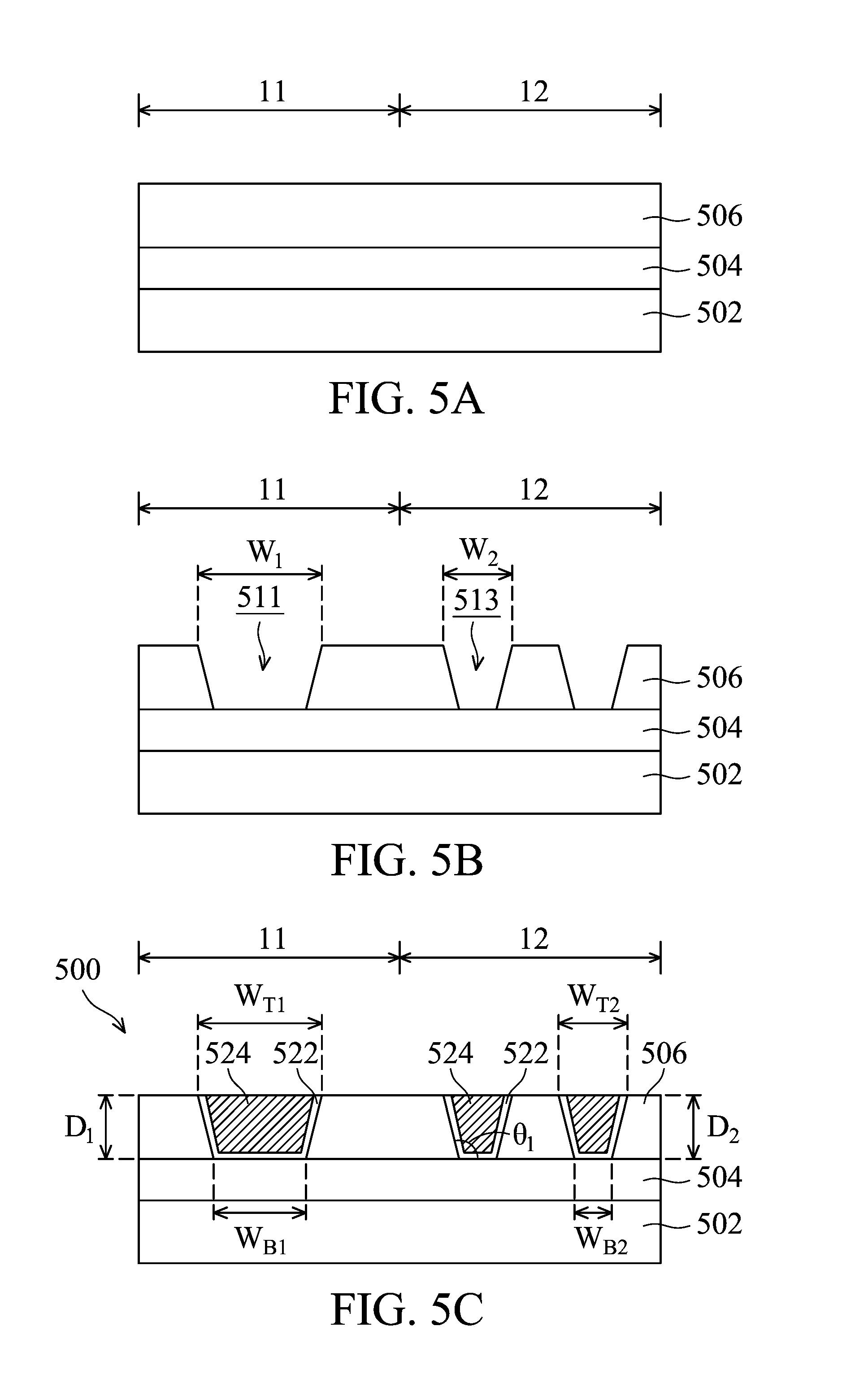
View All Diagrams
United States Patent
Application |
20190157048 |
Kind Code |
A1 |
CHEN; Po-Ju ; et
al. |
May 23, 2019 |
PLASMA PROCESSING APPARATUS AND METHOD FOR FORMING SEMICONDUCTOR
DEVICE STRUCTURE
Abstract
A plasma processing apparatus is provided. The plasma processing
apparatus includes a plasma chamber including a housing, and a
first electrode array disposed above and outside the housing. The
first electrode array includes a plurality of first sub-electrodes.
The plasma processing apparatus also includes a number of first
matching units outside of the housing, and each of the first
matching units is electrically connected to each of the first
sub-electrodes.
Inventors: |
CHEN; Po-Ju; (Hsinchu City,
TW) ; WU; Chun-Hsing; (Zhubei City, TW) ; WU;
Fang-Yi; (Kaohsiung City, TW) ; CHIU; Yi-Wei;
(Kaohsiung City, TW) ; CHEN; Chih-Hao; (Hsinchu
City, TW) |
|
Applicant: |
Name |
City |
State |
Country |
Type |
Taiwan Semiconductor Manufacturing Co., Ltd. |
Hsinchu |
|
TW |
|
|
Assignee: |
Taiwan Semiconductor Manufacturing
Co., Ltd.
Hsinchu
TW
|
Family ID: |
66533298 |
Appl. No.: |
16/104564 |
Filed: |
August 17, 2018 |
Related U.S. Patent Documents
|
|
|
|
|
|
Application
Number |
Filing Date |
Patent Number |
|
|
62587751 |
Nov 17, 2017 |
|
|
|
Current U.S.
Class: |
1/1 |
Current CPC
Class: |
H01L 21/67103 20130101;
H01J 37/32568 20130101; H01L 21/3065 20130101; H01J 37/32541
20130101; H01L 21/6831 20130101; H01L 21/768 20130101; H01L
29/66795 20130101; H01L 21/76816 20130101; H01J 37/32715 20130101;
H01L 21/67069 20130101; H01J 37/3255 20130101; H01J 37/32183
20130101; H01J 2237/334 20130101; H01L 21/31116 20130101; H01L
21/6833 20130101 |
International
Class: |
H01J 37/32 20060101
H01J037/32; H01L 21/67 20060101 H01L021/67; H01L 21/683 20060101
H01L021/683; H01L 21/3065 20060101 H01L021/3065 |
Claims
1. A plasma processing apparatus, comprising: a plasma chamber
comprising a housing and a wafer support; a first electrode array
disposed over the wafer support, wherein the first electrode array
comprises a plurality of first sub-electrodes; and a plurality of
first matching units connected to the first electrode array,
wherein each of the first matching units is electrically connected
to each of the first sub-electrodes.
2. The plasma processing apparatus as claimed in claim 1, further
comprising: a first RF power source connected to the plurality of
first sub-electrodes configured to provide energy to the plurality
of first sub-electrodes via the plurality of first matching
units.
3. The plasma processing apparatus as claimed in claim 1, further
comprising: a wafer support disposed in the plasma chamber; and a
second electrode array disposed in the wafer support, wherein the
second electrode array comprises a plurality of second sub-second
electrodes.
4. The plasma processing apparatus as claimed in claim 3, further
comprising: a plurality of second matching units connected to the
plurality of second sub-electrodes, wherein each of the second
matching units is electrically connected to one of the plurality of
second sub-electrodes.
5. The plasma processing apparatus as claimed in claim 4, further
comprising: a second RF power source connected to the plurality of
second sub-electrodes configured to provide energy to the plurality
of second sub-electrodes via the plurality of second matching
units.
6. The plasma processing apparatus as claimed in claim 3, wherein
each of the plurality of first sub-electrodes and the plurality of
second sub-electrodes comprises aluminum (Al), nickel (Ni),
chromium (Cr), tin (Sn), copper (Cu), platinum (Pt), gold (Au),
ceramic or piezoelectric material.
7. The plasma processing apparatus as claimed in claim 1, wherein
each of the first sub-electrodes has a distance which is measured
from a top surface of the housing to a bottom surface of each of
the plurality of first sub-electrodes, and the first sub-electrodes
have the same or different heights.
8. The plasma processing apparatus as claimed in claim 1, wherein
the first electrode array further comprises an insulating material
insulates the adjacent sidewalls of the plurality of first
sub-electrodes.
9. The plasma processing apparatus as claimed in claim 1, wherein
the plurality of first sub-electrodes is arranged in a spiral shape
when seen from a top-view.
10. The plasma processing apparatus as claimed in claim 1, further
comprising: a plurality of gas channels disposed in the wafer
support, wherein the gas channels are disposed above the second
electrode array; an electrostatic electrode disposed in the wafer
support; and a cooling plate disposed in the wafer support, wherein
the electrostatic electrode is between the gas channels and the
cooling plate.
11. A plasma processing apparatus, comprising: a plasma chamber
comprising a housing and a wafer support; a top electrode array
disposed over the wafer support, wherein the top electrode array
comprises a plurality of top sub-electrodes spaced apart from one
another; and a bottom electrode array disposed in the wafer
support, wherein the bottom electrode comprises a plurality of
bottom sub-electrodes spaced apart from one another.
12. The plasma processing apparatus as claimed in claim 11, further
comprising: a plurality of top matching units each electrically
connected to one of the plurality of top sub-electrodes; and a
first RF power source configured to provide energy to the top
sub-electrodes via the plurality of top matching units.
13. The plasma processing apparatus as claimed in claim 11, further
comprising: a plurality of gas channels disposed in the wafer
support, wherein the plurality of gas channels is positioned above
the bottom electrode array; and an electrostatic electrode disposed
in the wafer support, wherein the electrostatic electrode is
positioned above the bottom electrode array.
14. The plasma processing apparatus as claimed in claim 13, further
comprising: a plurality of bottom matching units each electrically
connected to one of the plurality of bottom sub-electrodes.
15. The plasma processing apparatus as claimed in claim 11, wherein
two adjacent ones of the plurality of top sub-electrodes are
separated from each other by a dielectric layer.
16. The plasma processing apparatus as claimed in claim 11, wherein
the top electrode array further comprises an insulating material
insulates the adjacent sidewalls of the top sub-electrodes.
17. A method for forming a semiconductor device structure,
comprising: placing in a plasma chamber a substrate including a
material layer thereon, wherein the plasma chamber comprises: a
housing; a first electrode array comprising a plurality of first
sub-electrodes; a plurality of first matching units each
electrically connected to one of the plurality of first
sub-electrodes; and a second electrode array disposed in the
housing, the second electrode array comprising a plurality of
second sub-electrodes; supplying an etching gas into the plasma
chamber; applying a first RF power source to the first
sub-electrodes of the first electrode array by each of the first
matching units to form an etching plasma from the etching gas,
adjusting a distance between each of the first sub-electrodes and
the substrate to generate a plasma density distribution across the
substrate; and performing an etching process on the material layer
using the etching plasma.
18. The method of claim 17, further comprising: applying a second
RF power source to the plurality of second sub-electrodes of the
second electrode array by a plurality of second matching units,
wherein the plurality of second sub-electrodes is configured to
increase the plasma density near the material layer.
19. The method of claim 18, further comprising: supplying a
cleaning gas into the plasma chamber; performing a cleaning process
on an edge region of the substrate by applying the first RF power
source to a portion of the plurality of first sub-electrodes which
is located at an edge region of the first electrode array to
increase the plasma density near the edge region of the
substrate.
20. The method of claim 17, wherein the etching plasma has
different plasma density in different regions above the substrate.
Description
CROSS REFERENCE TO RELATED APPLICATIONS
[0001] This Application claims the benefit of U.S. Provisional
Application No. 62/587,751, filed on Nov. 17, 2017, and entitled
"Plasma processing apparatus and method for forming semiconductor
device structure", the entirety of which is incorporated by
reference herein.
BACKGROUND
[0002] Semiconductor devices are used in a variety of electronic
applications, such as personal computers, cell phones, digital
cameras, and other electronic equipment. Semiconductor devices are
typically fabricated by sequentially depositing insulating or
dielectric layers, conductive layers, and semiconductive layers of
material over a semiconductor substrate, and patterning the various
material layers using lithography to form circuit components and
elements thereon. Many integrated circuits are typically
manufactured on a single semiconductor wafer, and individual dies
on the wafer are singulated by sawing between the integrated
circuits along a scribe line. The individual dies are typically
packaged separately, in multi-chip modules, for example, or in
other types of packaging.
[0003] A plasma processing (dry etching) process offers better
critical dimension control than conventional wet chemical etching
in the fabrication of semiconductor devices.
[0004] Although existing plasma processing apparatuses have
generally been adequate for their intended purpose, they have not
been entirely satisfactory in all respects.
BRIEF DESCRIPTION OF THE DRAWINGS
[0005] Aspects of the present disclosure are best understood from
the following detailed description when read with the accompanying
figures. It should be noted that, in accordance with the standard
practice in the industry, various features are not drawn to scale.
In fact, the dimensions of the various features may be arbitrarily
increased or reduced for clarity of discussion.
[0006] FIG. 1 shows a schematic view of a plasma processing
apparatus, in accordance with some embodiments of the
disclosure.
[0007] FIG. 2A shows a top-view of the first sub-electrodes, in
accordance with some embodiments of the disclosure.
[0008] FIG. 2A' shows a top-view of the first sub-electrodes, in
accordance with some embodiments of the disclosure.
[0009] FIGS. 2B and 2B' show top-views of the first sub-electrodes
in accordance with some embodiments of the disclosure.
[0010] FIGS. 2C and 2C' show top-views of the first sub-electrodes,
in accordance with some embodiments of the disclosure.
[0011] FIGS. 2D and 2D' show top-views of the first sub-electrodes,
in accordance with some embodiments of the disclosure.
[0012] FIGS. 2E and 2E' show top-views of the first sub-electrodes,
in accordance with some embodiments of the disclosure.
[0013] FIGS. 2F and 2F' show top-views of the first sub-electrodes,
in accordance with some embodiments of the disclosure.
[0014] FIGS. 3A-3C shows top-views of the second sub-electrodes, in
accordance with some embodiments of the disclosure.
[0015] FIG. 4 shows a flow-chart of a method for forming a
semiconductor device structure, in accordance with some
embodiments.
[0016] FIGS. 5A-5C show cross-sectional views of various stages of
forming a semiconductor device structure, in accordance with some
embodiments of the disclosure.
[0017] FIGS. 6A-6C show cross-sectional views of various stages of
forming a semiconductor device structure, in accordance with some
embodiments of the disclosure.
[0018] FIGS. 7A-7E show cross-sectional views of various stages of
forming a semiconductor device structure, in accordance with some
embodiments of the disclosure.
DETAILED DESCRIPTION
[0019] The following disclosure provides many different
embodiments, or examples, for implementing different features of
the subject matter provided. Specific examples of components and
arrangements are described below to simplify the present
disclosure. These are, of course, merely examples and are not
intended to be limiting. For example, the formation of a first
feature over or on a second feature in the description that follows
may include embodiments in which the first and second features are
formed in direct contact, and may also include embodiments in which
additional features may be formed between the first and second
features, such that the first and second features may not be in
direct contact. In addition, the present disclosure may repeat
reference numerals and/or letters in the various examples. This
repetition is for the purpose of simplicity and clarity and does
not in itself dictate a relationship between the various
embodiments and/or configurations discussed.
[0020] Some variations of the embodiments are described. Throughout
the various views and illustrative embodiments, like reference
numbers are used to designate like elements. It should be
understood that additional operations can be provided before,
during, and after the method, and some of the operations described
can be replaced or eliminated for other embodiments of the
method.
[0021] The fins may be patterned using any suitable method. For
example, the fins may be patterned using one or more
photolithography processes, including double-patterning or
multi-patterning processes. Generally, double-patterning or
multi-patterning processes combine photolithography and
self-aligned processes, allowing patterns to be created that have,
for example, pitches smaller than what is otherwise obtainable
using a single, direct photolithography process. For example, in
one embodiment, a sacrificial layer is formed over a substrate and
patterned using a photolithography process. Spacers are formed
alongside the patterned sacrificial layer using a self-alignment
process. The sacrificial layer is then removed, and the remaining
spacers may then be used to pattern the fins.
[0022] Embodiments for a plasma processing apparatus are provided.
FIG. 1 shows a schematic view of a plasma processing apparatus 100,
in accordance with some embodiments of the disclosure. The plasma
processing apparatus 100 includes a plasma chamber 102, a first
electrode array 110 (or top electrode array) and a second electrode
array 120 (or bottom electrode array). The plasma chamber 102
includes a housing 104 (or wall portions). The housing 104 is
configured to maintain a vacuum environment during processing. The
housing 104 is grounded through a ground 156.
[0023] The housing 104 includes a gas inlet 152 and a gas outlet
154. The gas inlet 152 is connected to the plasma chamber 102. A
gas supply 150 is coupled to the plasma chamber 102. The gas from
the gas supply 150 is supplied to the plasma chamber 102 through
the gas inlet 152. The gas supply 150 may supply a single gas or a
gas mixture of more than one gas. The gas outlet 154 is connected
to the plasma chamber 102. The chemical byproducts and unwanted
reagents from the plasma chamber 102 are evacuated via gas outlet
154.
[0024] The first electrode array 110 is disposed above and outside
the housing 104. The first electrode array 110 includes a number of
first sub-electrodes 112 (or top sub-electrodes). In some
embodiments, the first sub-electrodes 112 are made of
low-resistivity material. In some embodiments, the first
sub-electrodes 112 are made of conductive materials, such as
aluminum (Al), nickel (Ni), chromium (Cr), tin (Sn), copper (Cu),
platinum (Pt), gold (Au), ceramic or piezoelectric material.
[0025] A number of first matching units 114 are outside the housing
104. The first matching units 114 are used to perform an impedance
matching function. Each of the first matching units 114 are
electrically connected to corresponding first sub-electrodes 112 by
a number of first conductive lines 113. The first conductive lines
113 may have different lengths. Therefore, the first sub-electrodes
112 have different heights H.sub.1, H.sub.2. The heights H.sub.1,
H.sub.2 is measured from the top surface of the housing 104 to the
bottom surface of each of the first sub-electrodes 112. The plasma
density in the plasma chamber 102 can be controlled by adjusting
the height H.sub.1, H.sub.2 of each of the first sub-electrodes
112. In some embodiments, a first portion of the first
sub-electrodes 112 in the edge region of the first electrode array
110 has a first height H.sub.1, and a second portion of the first
sub-electrodes 112 in the middle region of the first electrode
array 110 has a second height H.sub.2. The second height H.sub.2 is
greater than the first height H.sub.1. When the first portion of
the first sub-electrodes 112 is closer to the housing 104 than the
second portion of the first sub-electrodes 112, a first plasma
density of a first region which is directly below the first portion
of the first sub-electrodes 112 will be higher than a second plasma
density of a second region which is directly below the second
portion of the first sub-electrodes 112. In some embodiments, the
first height H.sub.1 is in a range from about 0.1 cm to about 20
cm. There is a first pitch P.sub.1 between two adjacent first
sub-electrodes 112. In some embodiments, the first pitch P.sub.1 is
in a range from about 0.05 mm to about 10 mm.
[0026] A first RF power source 116 is electrically connected to the
number of the first matching units 114. The first RF power source
116 is configured to provide a RF power (or RF energy) to each of
the first sub-electrodes 112 via each of the first matching units
114. The first RF power source 116 is configured to supply an RF
power for plasma generation to the first sub-electrodes 112 through
the first matching units 114. The first matching units 114 are
disposed on the transmission path between the first RF power source
116 and the first sub-electrodes 112, and the first matching units
114 are configured to perform an impedance matching function. More
specifically, through the help of the number of the first matching
units 114, the first RF power source 116 can provide different
levels of RF power to the first sub-electrodes 112 to form a
desired plasma density distribution in the different regions of the
plasma chamber 102.
[0027] The first sub-electrodes 112 are separately controlled by a
number of first matching units 114. In some embodiments, the first
RF power generated from the first RF power source 116 applies a
high-frequency in a range from about 1 MHz to about 100 MHz.
[0028] A wafer support 118 is disposed in the plasma chamber 102.
The wafer support 118 is configured to support a wafer or substrate
170. The second electrode array 120 (or bottom electrode array) is
disposed in the wafer support 118 in the plasma chamber 102. A
number of gas channels 130 are disposed in the wafer support 118.
The gas channels 130 are connected to a gas supply 132. The gas
channels 130 are configured to transfer the heat to provide uniform
temperature distribution. The heat may be generated from the
electrostatic electrode 134 or from the etching process. An
electrostatic electrode 134 is disposed in the wafer support 118
and is configured to hold the substrate 170 by an electrostatic
attracting force. The electrostatic electrode 134 is connected to a
chuck power 136.
[0029] The second electrode array 120 includes a number of second
sub-electrodes 122 (or bottom sub-electrodes). A number of second
matching units 124 are electrically connected to corresponding the
second sub-electrodes 122. Each of the second matching units 124
are electrically connected to corresponding second sub-electrodes
122 by a number of second conductive lines 123. In some
embodiments, the second sub-electrodes 122 are made of
low-resistivity material. In some embodiments, the second
sub-electrodes 122 are made of conductive materials, such as
aluminum (Al), nickel (Ni), chromium (Cr), tin (Sn), copper (Cu),
platinum (Pt), gold (Au), ceramic or piezoelectric material.
[0030] A second RF power source 126 is disposed outside the housing
104 and the plasma chamber 102. The second RF power source 126 is
configured to provide a RF power (or RF energy) to each of the
second sub-electrodes 122 via each of the second matching units
124. More specifically, the second RF power source 126 is
configured to provide different RF powers to the second
sub-electrodes 122 through the number of the second matching units
124 to form a desired plasma density distribution in the different
regions of the plasma chamber 102. The second sub-electrodes 122
are separately controlled by a number of second matching units
124.
[0031] A cooling plate 140 is disposed in the wafer support 118 to
form a built-in cooling mechanism, and a cooling fluid 142 are
disposed in the cooling plate 140. The cooling plate 140 is
configured to cool the temperature of the substrate 170. A moving
mechanism 160 is below the wafer support 118 and enables the wafer
support 118 assembly to move up or down.
[0032] A controller 180 is coupled to the plasma chamber 102. The
controller 180 sets the operational parameters of the plasma
chamber 102, including which RF power sources are turned on or
turned off, their voltages and power settings. The controller 180
is coupled to a first power controller 182 and a second power
controller 184. The first power controller 182 provides the control
signals to the first RF generator 116 to control the amount of
power from the first RF generator 116. The second power controller
184 provides the control signals to the second RF generator 126 to
control the amount of power from the second RF generator 126. In
some embodiments, the controller 180 sends instructions to the
first power controller 182 for the configuration of the power on
the first sub-electrodes 112, which includes setting switch to
connect the first sub-electrodes 112 to ground or to RF power. In
some other embodiments, the controller 180 sends instructions to
the first power controller 182 and the second power controller 184,
which includes switching to connect the first sub-electrodes 112 to
ground or to RF power, and switching to connect the second
sub-electrodes 122 to ground or to RF power.
[0033] The plasma is generated between the top surface of the
plasma chamber 102 and the wafer support 118. For example, the
first sub-electrodes 112 are independently or separately powered by
the first RF power source 116 through the number of the first
matching units 114 to produce inductively coupled plasma (ICP) in
the plasma chamber 102. In some embodiments, an electric field is
generated by the first RF power source 116 to excite the reaction
gas into the plasma chamber 102 while the etching gas or the
cleaning gas is supplied into the plasma chamber 102 via the gas
inlet 152. Afterwards, the reaction gas is excited into plasma by
the electric field. After generation the plasma, the material layer
506 (shown in FIG. 5B) is etched by the plasma.
[0034] In some embodiments, the etching gas is supplied by the gas
supply 150 into the plasma chamber 102. The etching gas includes
fluorine-containing gas that includes nitrogen trifluoride
(NF.sub.3), hexafluoroethane (C.sub.2F.sub.6), tetrafluoromethane
(CF.sub.4), fluoroform (CHF.sub.3), fluorine (F.sub.2), hydrogen
fluoride (HF), or a combination thereof. In some other embodiments,
the etching gas further includes another additive gas, such as
oxygen (O.sub.2) or ozone (O.sub.3).
[0035] In some embodiments, the cleaning gas is supplied by the gas
supply 150 into the plasma chamber 102. The cleaning gas includes
fluorine-containing gas, inert gas, or a combination thereof. The
fluorine-containing gas includes nitrogen trifluoride (NF.sub.3),
hexafluoroethane (C.sub.2F.sub.6), tetrafluoromethane (CF.sub.4),
fluoroform (CHF.sub.3), fluorine (F.sub.2), hydrogen fluoride (HF),
or a combination thereof. The inert gas includes argon (Ar), helium
(He), neon (Ne), krypton (Kr), xenon (Xe), or a combination
thereof.
[0036] FIG. 2A shows a top-view of the first sub-electrodes 112, in
accordance with some embodiments of the disclosure.
[0037] The first sub-electrodes 112 include a number of parts. In
some embodiments, the first sub-electrodes 112 include a first part
112a, a second part 112b, a third part 112c, a fourth part 112d, a
fifth part 112e, a sixth part 112f, a seventh part 112g, an eighth
part 112h and a ninth part 112i. These parts 112a, 112b, 112c,
112d, 112e, 112f, 112g, 112h, 112i are separate from each other and
arranged in a matrix. The first sub-electrodes 112 are separated
from each other by a dielectric layer 115 between two adjacent
first sub-electrodes 112. In some embodiments, each of the first
sub-electrodes 112 has a spiral shape when seen from a top-view. In
some embodiments, each of the parts of the first sub-electrodes 112
has a size in a range from about 0.1 cm.sup.2 to about 1
cm.sub.2.
[0038] FIG. 2A' shows a top-view of the first sub-electrodes 112,
in accordance with some embodiments of the disclosure. FIG. 2A' is
similar to FIG. 2A, the difference being that the adjacent
sidewalls of the parts 112a, 112b, 112c, 112d, 112e, 112f, 112g,
112h, 112i of the first sub-electrodes 112 in FIG. 2A' are
insulated by the insulating material 117.
[0039] FIGS. 2B and 2B' show top-views of the first sub-electrodes
112 in accordance with some embodiments of the disclosure. Each of
the first sub-electrodes 112 has a squared spiral shape when seen
from a top-view. FIG. 2B' is similar to FIG. 2B, with the
difference between them being the insulating material 117 that
covers the outer surface of each of the first sub-electrodes
112.
[0040] FIGS. 2C and 2C' show top-views of the first sub-electrodes
112, in accordance with some embodiments of the disclosure. Each of
the first sub-electrodes 112 has a triangular spiral shape when
seen from a top-view. FIG. 2C' is similar to FIG. 2C, the
difference between them being that an insulating material 117
covers the outer surface of each of the first sub-electrodes
112.
[0041] FIGS. 2D and 2D' show top-views of the first sub-electrodes
112, in accordance with some embodiments of the disclosure. Each of
the first sub-electrodes 112 has a concentric ring shape when seen
from a top-view. FIG. 2D' is similar to FIG. 2D, the difference
between is that an insulating material 117 is covering the outer
surface of each of the first sub-electrodes 112.
[0042] FIGS. 2E and 2E' show top-views of the first sub-electrodes
112, in accordance with some embodiments of the disclosure. Each of
the first sub-electrodes 112 has a rectangular concentric shape
when seen from a top-view. FIG. 2E' is similar to FIG. 2E, the
difference between is that an insulating material 117 covers the
outer surface of each of the first sub-electrodes 112.
[0043] FIGS. 2F and 2F' show top-views of the first sub-electrodes
112, in accordance with some embodiments of the disclosure. Each of
the first sub-electrodes 112 has a triangular concentric shape when
seen from a top-view. FIG. 2F' is similar to FIG. 2F, the
difference between them being that there is an insulating material
117 covering the outer surface of each of the first sub-electrodes
112.
[0044] It should be noted that the number of first sub-electrodes
112 is not limited to nine, and that the number of first
sub-electrodes 112 can be adjusted according to actual
application.
[0045] FIGS. 3A-3C show top-views of the second sub-electrodes 122,
in accordance with some embodiments of the disclosure. The second
sub-electrodes 122 include a number of parts. In some embodiments,
the second sub-electrodes 122 include a first part 122a, a second
part 122b, a third part 122c, a fourth part 122d, a fifth part
122e, a sixth part 122f, a seventh part 122g, an eighth part 122h
and a ninth part 122i. These parts 122a, 122b, 122c, 122d, 122e,
122f, 122g, 122h, 122i are separate from each other and arranged in
a matrix. The second sub-electrodes 122 are separated from each
other by a dielectric layer 125 between two adjacent second
sub-electrodes 122. In FIG. 3A, each of the second sub-electrodes
122 has a circular shape when seen from a top-view.
[0046] In FIG. 3B, each of the second sub-electrodes 122 has a
rectangular shape when seen from a top-view. In FIG. 3C, each of
the second sub-electrodes 122 has a triangular shape when seen from
a top-view.
[0047] FIG. 4 shows a flow-chart of a method for forming a
semiconductor device structure, in accordance with some
embodiments.
[0048] In operation 402, the substrate 170 as shown in FIG. 1 is
placed in the plasma chamber 102. In some embodiments, a material
layer 506 (as shown in FIG. 5A) is formed over the substrate
502.
[0049] In operation 404, an etching gas is supplied into the plasma
chamber 102. In some embodiments, the etching gas includes
fluorine-containing gas that includes nitrogen trifluoride
(NF.sub.3), hexafluoroethane (C.sub.2F.sub.6), tetrafluoromethane
(CF.sub.4), fluoroform (CHF.sub.3), fluorine (F.sub.2), hydrogen
fluoride (HF), or a combination thereof. In some other embodiments,
the etching gas further includes another additive gas, such as
oxygen (O.sub.2) or ozone (O.sub.3).
[0050] In operation 406, a first RF power source 116 is applied to
the first sub-electrodes 112 of the first electrode array 110 by
each of the first matching units 114 to produce an etching plasma.
Therefore, the process gas supplied in the plasma chamber 102 is
excited and dissociated to form a plasma. In some embodiments, the
etching plasma has different plasma densities in different regions
above the substrate 170 or 502 by applying a different levels of RF
power to every first sub-electrode 112. In some embodiments, the
density of the plasma in the central region is increased by
increasing the RF power of the corresponding first sub-electrode
112 in the central region.
[0051] In some other embodiments, a second RF power source 126 is
applied to the second sub-electrodes 122 of the second electrode
array 120. Therefore, an etchant or the etching plasma in the
plasma chamber 102 is guided onto a surface of the substrate
170.
[0052] It should be noted that the first RF power source 116 and
the second RF power source 126 are controlled separately to obtain
stable plasma. The plasma in the housing 104 is controlled by the
first RF power source 116, and the bombardment is controlled by the
second RF power source 126. In some embodiments, only the first RF
power source 116 is operated. For example, when a photoresist layer
is removed, only the first RF power source 116 is operated. In some
other embodiments, the first RF power source 116 and the second RF
power source 126 are operated simultaneously using the controller
180. For example, when substrate 102 is made of silicon (Si), the
first RF power source 116 and the second RF power source 126 are
operated simultaneously in the etching process. The first RF power
source 116 is used to remove the silicon material and the second RF
power source 126 is used to remove the silicon oxide formed over
the silicon.
[0053] In operation 408, an etching process is performed on the
material layer 506 (shown in FIG. 5B) using the plasma. The etched
depth of the material layer 506 is controlled by the plasma density
of the plasma, and the plasma density is determined by separately
controlling each of the first sub-electrodes 112 and/or the second
sub-electrodes 122.
[0054] In some other embodiments, the first height H.sub.1 of each
of the first sub-electrodes 122 may be adjusted by adjusting the
length of the first conductive liner 113. The first height H.sub.1
is the distance between one of the first sub-electrodes 112 to the
top surface of the plasma chamber 102. When one of the first
sub-electrodes 112 is close to the plasma chamber 102, a higher
electric field directly below the one of the first sub-electrodes
112 is generated to form a higher plasma density. The plasma
densities in different regions of the plasma chamber 102 may be
different by controlling the first height H.sub.1.
[0055] Reference is now made to FIG. 1. In some instances,
contamination of the substrate 170 is more prominent on edge region
than on central region of the substrate 170. In those instances, a
cleaning process can be performed on the edge region of the
substrate 170. In some embodiments, a cleaning process is performed
after the etching process. In some other embodiments, a cleaning
process is performed between two etching processes. A cleaning gas
is supplied into the plasma chamber 102. Afterwards, a cleaning
process is performed on an edge region of the substrate 170 by
applying the first RF power source 116 to a portion of the first
sub-electrodes 112 which is located at an edge region of the first
electrode array 110. In some other embodiments, a cleaning process
is performed on an edge region of the substrate 170 by applying the
first RF power source 116 to a portion of the first sub-electrodes
112 and simultaneously applying the second RF power source 126 to a
portion of the second sub-electrodes 122. The portion of the first
sub-electrodes 112 is configured to increase the plasma density
near the edge region of the substrate.
[0056] It should be noted that the cleaning process is performed
in-situ after the etching process without transferring the
substrate 170 to another chamber. Therefore, the risk of the
substrate pollution is reduced. Furthermore, the size of edge
region of the first electrode array 110 may be tunable according to
the size of the first sub-electrodes 112.
[0057] FIGS. 5A-5C show cross-sectional views of various stages of
forming a semiconductor device structure 500, in accordance with
some embodiments of the disclosure.
[0058] As shown in FIG. 5A, a substrate 502 is provided. An etching
stop layer 504 is formed over the substrate 502. A material layer
506 is formed over the etching stop layer 504. The substrate 502
has a first region 11 and a second region 12.
[0059] Afterward, as shown in FIG. 5B, the material layer 506 is
etched by performing an etching process on the material layer 506
to form a first trench 511 in the first region 11 and a second
trench 513 in the second region, in accordance with some
embodiments of the disclosure. The first trench 511 has a first top
width W.sub.1, and the second trench 513 has a second top width
W.sub.2. The first top width W.sub.1 is greater than the second top
width W.sub.2.
[0060] For regions with different exposed areas (or etched areas),
it is difficult to control etch uniformity due to the loading
effect. Depending on the etching strategy, the loading effect is
the etch rate for a high pattern density area being either faster
or slower than it is for a low pattern density area. In other
words, the loading effect is that the etch rate in a large area is
mismatched to the etch rate in a small area. This means that the
loading effect may be affected by pattern density.
[0061] In order to reduce the loading effect, by applying different
first RF powers to the number of first sub-electrodes 112, the
regions in the plasma chamber 102 may be controlled to have
different plasma density. In some embodiments, the plasma density
of the etching gas in the first region 11 is different from the
plasma density of the etching gas in the second region 12. That is,
although the pattern density in the first region 11 is different
from that in the second region 12, the depth of the first trench
511 is substantially equal to the depth of the second trench 513 by
separately controlling the first sub-electrodes 112 and the second
sub-electrodes 122. In some embodiments, the density of the plasma
is affected by the layout and the controller, and the etched depth
and the critical dimension (CD) of the etched structure are
determined by the density of the plasma. According to feedback of
the etched depth, the critical dimension (CD) of the etched
structure, the layout and the controller are controlled to obtain
desirable etched profile.
[0062] Next, as shown in FIG. 5C, a diffusion barrier layer 522 is
deposited in the first trench 511 and the second trench 513, and
then a conductive layer 524 is formed on the diffusion barrier
layer 522, in accordance with some embodiments of the disclosure.
As a result, a first conductive structure 526 is constructed by the
first diffusion barrier layer 522 and the conductive layer 524 in
the first region 11. A second conductive structure 528 is
constructed by the diffusion barrier layer 522 and the conductive
layer 524 in the second region 12.
[0063] The first conductive structure 526 has a first depth D.sub.1
which is measured from a top surface of the conductive layer 524 to
a bottom surface of the diffusion barrier layer 522. The second
conductive structure 528 has a second depth D.sub.2 which is
measured from a top surface of the conductive layer 524 to a bottom
surface of the diffusion barrier layer 522. In some embodiments, a
depth ratio (D.sub.1/D.sub.2) of the first depth D.sub.1 to the
second depth D.sub.2 is in a range from about 0.8 to about 1.2.
[0064] In the first region 11, the first conductive structure 526
has a first top width W.sub.T1 and a first bottom width W.sub.B1.
In some embodiments, a width ratio (W.sub.T1/W.sub.B1) of the first
top width W.sub.T1 to the first bottom width W.sub.B1 is in a range
from about 0.8 to about 1.2. In the second region 12, the second
conductive structure 528 has a second top width W.sub.T2 and a
second bottom width W.sub.B2. In some embodiments, a width ratio
(W.sub.T/W.sub.B) of the second top width W.sub.T2 to the second
bottom width W.sub.B2 is in a range from about 0.8 to about 1.2. A
first angle .theta..sub.1 is between the bottom surface of the
diffusion barrier layer 522 and a sidewall surface of the
conductive layer 524. In some embodiments, the first angle
.theta..sub.1 is in a range from about 70 degrees to about 90
degrees.
[0065] FIGS. 6A-6C show cross-sectional views of various stages of
forming a semiconductor device structure 600, in accordance with
some embodiments of the disclosure.
[0066] As shown in FIG. 6A, a first dielectric layer 604 is formed
over a substrate 602, and a conductive layer 606 is formed in the
first dielectric layer 604. An etching stop layer 608 is formed
over the first dielectric layer 604, and a second dielectric layer
610 is formed over the etching stop layer 608.
[0067] Next, as shown in FIG. 6B, a first opening 611 is formed in
the first region 11 and a second opening 613 is formed in the
second region 12, in accordance with some embodiments of the
disclosure. The first opening 611 is a first trench-via cavity for
use as a dual damascene cavity. The second opening 613 is a second
trench-via cavity for use as a dual damascene cavity.
[0068] The first opening 611 and the second opening 613 are formed
by performing an etching process. The etching process is performed
in the plasma processing apparatus 100 in FIG. 1. It should be
noted that although the pattern density in the first region 11 is
different from that in the second region 12, and the depth of the
first opening 611 is substantially equal to the depth of the second
opening 613 by using a number of first sub-electrodes 112 and a
number of second sub-electrodes 122. The plasma density in the
first region 11 and the second region 12 can be controlled by
separately controlling each of the first sub-electrodes 112 and
each of the second sub-electrodes 122 via the first matching units
114 and the second matching units 124.
[0069] Subsequently, as shown in FIG. 6C, a diffusion barrier layer
622 is deposited in the first opening 611 and the second opening
613, and then a conductive layer 624 is formed on the diffusion
barrier layer 622, in accordance with some embodiments of the
disclosure. As a result, a first trench-via structure 626 is formed
in the first region 11 and a second trench-via structure 628 is
formed in the second region 12. The first trench-via structure 626
is electrically connected to the conductive layer 606 in the first
region 11, and the second trench-via structure 628 is electrically
connected to the conductive layer 606 in the second region 12.
[0070] In the first region 11, the first trench-via structure 626
has a third top width W.sub.T3 and a third bottom width W.sub.B3.
In some embodiments, a width ratio (W.sub.T3/W.sub.B3) of the third
top width W.sub.T3 to the third bottom width W.sub.B3 is in a range
from about 0.8 to about 1.2. In the second region 12, the second
trench-via structure 628 has a fourth top width W.sub.T4 and a
fourth bottom width W.sub.B4. In some embodiments, a width ratio
(W.sub.T4/W.sub.B4) of the fourth top width W.sub.T4 to the fourth
bottom width W.sub.B4 is in a range from about 0.8 to about 1.2. A
second angle .theta..sub.2 is between the bottom surface of the
diffusion barrier layer 622 and a sidewall surface of the
conductive layer 624. In some embodiments, the second angle
.theta..sub.2 is in a range from about 70 degrees to about 90
degrees.
[0071] FIGS. 7A-7C show cross-sectional views of various stages of
forming a semiconductor device structure 700, in accordance with
some embodiments of the disclosure.
[0072] As shown in FIG. 7A, a substrate 702 is provided. The
substrate 702 includes a first region 11 and a second region 12.
Afterwards, a dielectric layer 704 and a mask layer 706 are formed
over the substrate 702, and a photoresist layer 708 is formed over
the mask layer 706. The photoresist layer 708 is patterned by a
patterning process.
[0073] Next, as shown in FIG. 7B, after the photoresist layer 708
is patterned, the dielectric layer 704 and the mask layer 706 are
patterned by using the patterned photoresist layer 708 as a mask,
in accordance with some embodiments. As a result, a patterned
dielectric layer 704 and a patterned mask layer 706 are obtained.
Afterwards, the patterned photoresist layer 708 is removed.
[0074] Afterwards, an etching process is performed on the substrate
702 to form a number of fin structures 710a, 710b by using the
patterned dielectric layer 704 and the patterned mask layer 706 as
a mask. The fin structures 710a, 710b include first fin structures
710a in the first region 11 and second fin structures 710b in the
second region 12. In some embodiments, each of the fin structures
710a, 710b has a width that gradually increases from the top
portion to the bottom portion. In other words, each of the fin
structures 710a, 710b has a tapered fin width which is gradually
tapered from the bottom portion to the top portion. A first pitch
P.sub.1 is between two adjacent fin structures 710a in the first
region 11, and a second pitch P.sub.2 is between two adjacent fin
structures 710b in the second region 12. The second pitch P.sub.2
is greater than the first pitch P.sub.1.
[0075] Each of the first fin structures 710a has a fifth top width
W.sub.T5 and a fifth bottom width W.sub.B5. In some embodiments, a
width ratio (W.sub.T5/W.sub.B5) of the fifth top width W.sub.T5 to
the fifth bottom width W.sub.B5 is in a range from about 0.8 to
about 1.2. A third angle .theta..sub.3 is between the bottom
surface of the first fin structure 710a and a sidewall surface of
the first fin structure 710a. In some embodiments, the third angle
.theta..sub.3 is in a range from about 70 degrees to about 90
degrees.
[0076] Afterwards, as shown in FIG. 7C, after the fin structures
710a, 710b are formed, the isolation layer 712 is formed to cover
the fin structures 710a, 710b over the substrate 702, in accordance
with some embodiments.
[0077] Next, as shown in FIG. 7D, the isolation layer 712 is
thinned or planarized to expose the top surface of the patterned
mask layer 706. In some embodiments, the insulating layer 712 is
thinned by a chemical mechanical polishing (CMP) process.
Afterwards, a portion of the insulating layer 712 is removed to
form an isolation structure 714, in accordance with some
embodiments.
[0078] Afterwards, as shown in FIG. 7E, a gate dielectric layer 716
is formed on the fin structures 710a, 710b, the isolation
structures 714a, 714b, and a gate electrode layer 718 is formed on
the gate dielectric layer 716, in accordance with some embodiments.
A gate structure 720 is constructed by the gate dielectric layer
716 and the gate electrode layer 718.
[0079] The disclosure provides a plasma processing apparatus. The
first RF power source 116 is configured to provide different RF
powers to the first sub-electrodes 112 to form a desired plasma
density distribution in the plasma chamber 102. In addition, the
second RF power source 126 is configured to provide different RF
powers to the second sub-electrodes 122 to form a desired plasma
density distribution in the plasma chamber 102.
[0080] The methods for forming the semiconductor device structures
500, 600,700 include using the plasma processing apparatus 100. In
some embodiments, the substrate 502 with the material layer 506 (as
shown in FIG. 5A) is positioned in the plasma chamber 102. A
processing gas is supplied into the plasma chamber 102, and then
the first RF power source 116 is applied to the first
sub-electrodes 112 by the first matching units 114 to form a
plasma. The material layer 506 is etched by using the plasma. In
some other embodiments, in addition to applying the first RF power
source 116 to the first sub-electrodes 112, the second RF power
source 126 is simultaneously applied to the second sub-electrodes
122 by the second matching units 124.
[0081] The plasma density in the plasma chamber 102 can be
controlled by adjusting the first height H.sub.1 of each of the
first sub-electrodes 112. Furthermore, the cleaning process is
performed in-situ after the etching process without transferring
the substrate 170 to another chamber. Therefore, the risk of
substrate pollution is reduced.
[0082] Embodiments for a plasma processing apparatus and method for
formation a semiconductor device structure are provided. The plasma
processing apparatus includes a plasma chamber including a housing,
a first electrode array disposed outside the housing, and a number
of first matching units outside the housing. The first electrode
array includes a number of first sub-electrodes. The first
sub-electrodes may be separately controlled by a number of first
matching units. The plasma processing apparatus further includes a
wafer support disposed in the plasma chamber. A second electrode
array is disposed in the wafer support, and the second electrode
array includes a number of second sub-second electrodes. The second
sub-second electrodes may be separately controlled by a number of
second matching units.
[0083] The first RF power source is configured to provide different
RF powers to the first sub-electrodes to form a desired plasma
density distribution in the different regions of the plasma
chamber. The second RF power source is configured to provide
different RF powers to the second sub-electrodes to form a desired
plasma density distribution in the different regions of the plasma
chamber. As a result, the etched depths or etched widths of the
trench in different regions are controlled well by using the first
sub-electrodes and the second sub-electrodes. Therefore, the
quality and yield of the semiconductor device structure is
improved.
[0084] In some embodiments, a plasma processing apparatus is
provided. The plasma processing apparatus includes a plasma chamber
including a housing, and a first electrode array disposed above and
outside the housing. The first electrode array includes a plurality
of first sub-electrodes. The plasma processing apparatus also
includes a number of first matching units outside of the housing,
and each of the first matching units is electrically connected to
each of the first sub-electrodes.
[0085] In some embodiments, a plasma processing apparatus is
provided. The plasma processing apparatus includes a plasma chamber
including a housing and a wafer support. The plasma processing
apparatus includes a top electrode array disposed above and outside
the housing, and the top electrode array includes a plurality of
top sub-electrodes. The top sub-electrodes are separate from each
other. The plasma processing apparatus further includes a bottom
electrode array disposed in the wafer support, and the bottom
electrode includes a plurality of bottom sub-electrodes. The bottom
sub-electrodes are separate from each other.
[0086] In some embodiments, a method for forming a semiconductor
device structure is provided. The method includes placing a
substrate with a material layer above the substrate in a plasma
chamber. The plasma chamber includes a housing, a first electrode
array disposed above and outside the housing, the first electrode
array includes a plurality of first sub-electrodes, a number of
first matching units electrically connected to each of the first
sub-electrodes and a second electrode array disposed in the
housing. The method includes supplying an etching plasma into the
plasma chamber and applying a first RF power source to the first
sub-electrodes of the first electrode array by each of the first
matching units to form an etching plasma. The etching plasma has
different plasma density in different regions above the substrate.
The method includes performing an etching process on the material
layer by the etching plasma.
[0087] The foregoing outlines features of several embodiments so
that those skilled in the art may better understand the aspects of
the present disclosure. Those skilled in the art should appreciate
that they may readily use the present disclosure as a basis for
designing or modifying other processes and structures for carrying
out the same purposes and/or achieving the same advantages of the
embodiments introduced herein. Those skilled in the art should also
realize that such equivalent constructions do not depart from the
spirit and scope of the present disclosure, and that they may make
various changes, substitutions, and alterations herein without
departing from the spirit and scope of the present disclosure.
* * * * *