U.S. patent application number 16/316743 was filed with the patent office on 2019-05-23 for artificial turf comprising an agglomerate infill.
This patent application is currently assigned to Polytex Sportbelage Produktions-GmbH. The applicant listed for this patent is Polytex Sportbelage Produktions-GmbH. Invention is credited to Ivo LOHR, Ulrich NEUHOFF, Stephan SICK.
Application Number | 20190153679 16/316743 |
Document ID | / |
Family ID | 56511351 |
Filed Date | 2019-05-23 |
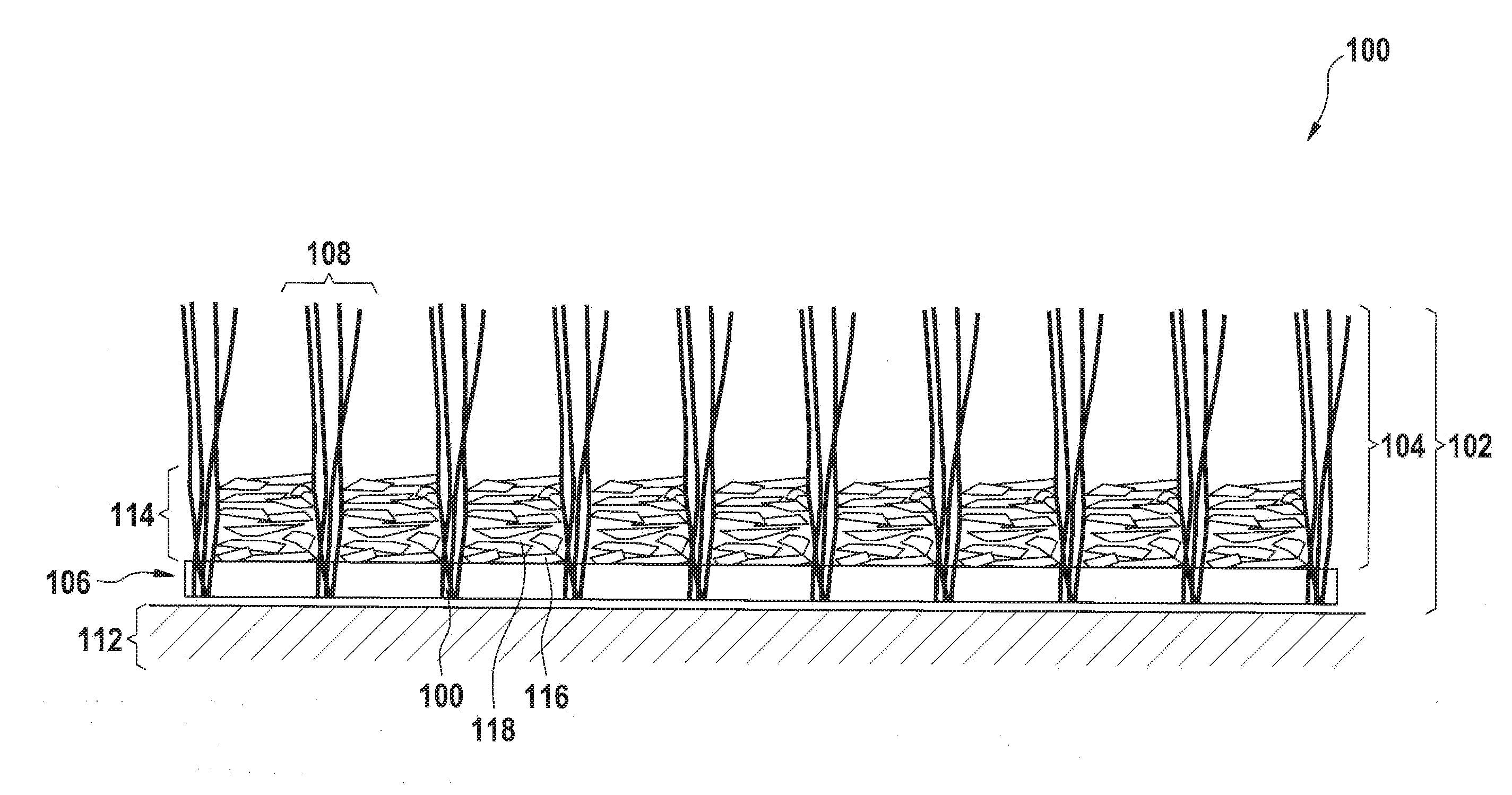

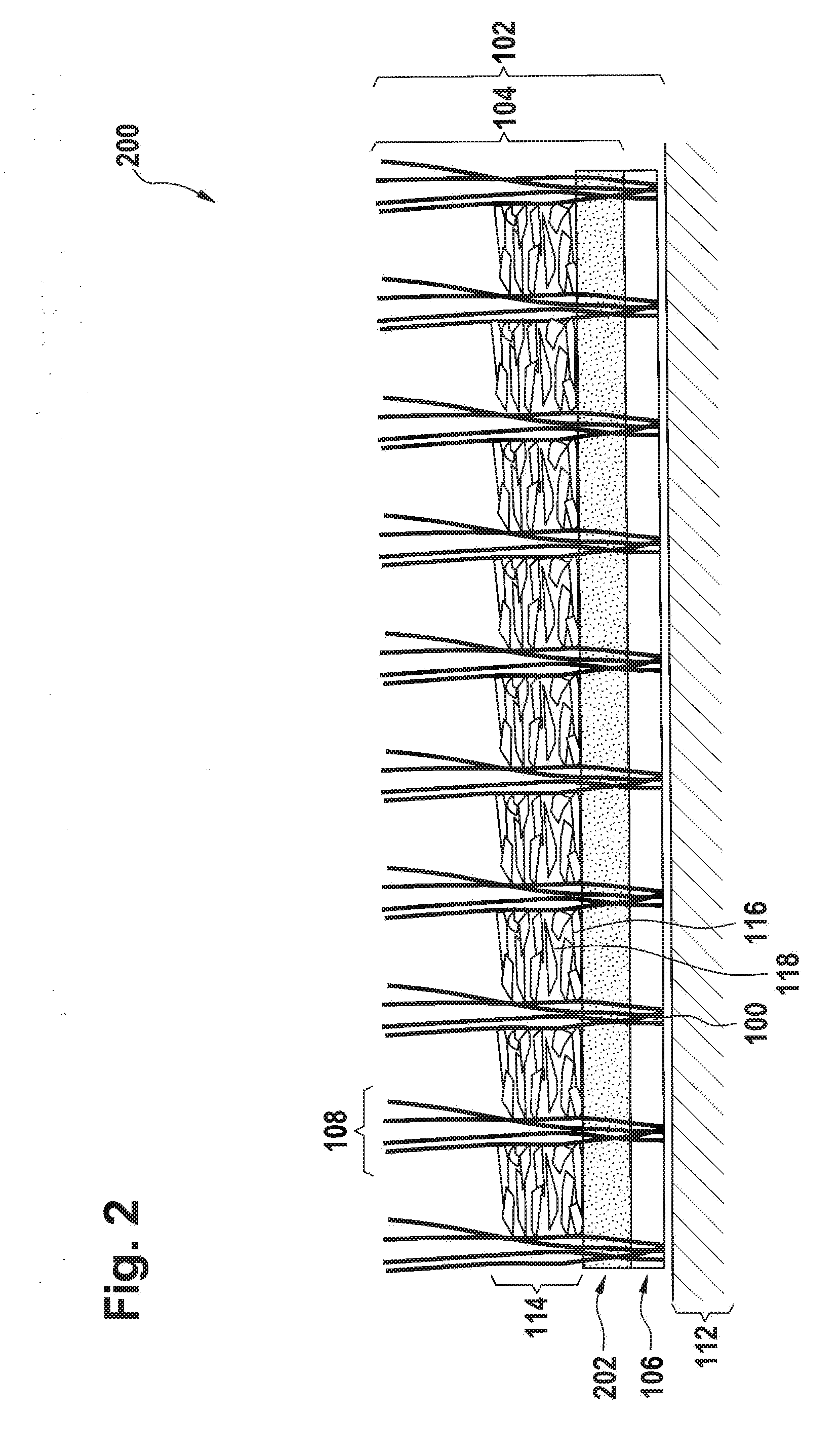



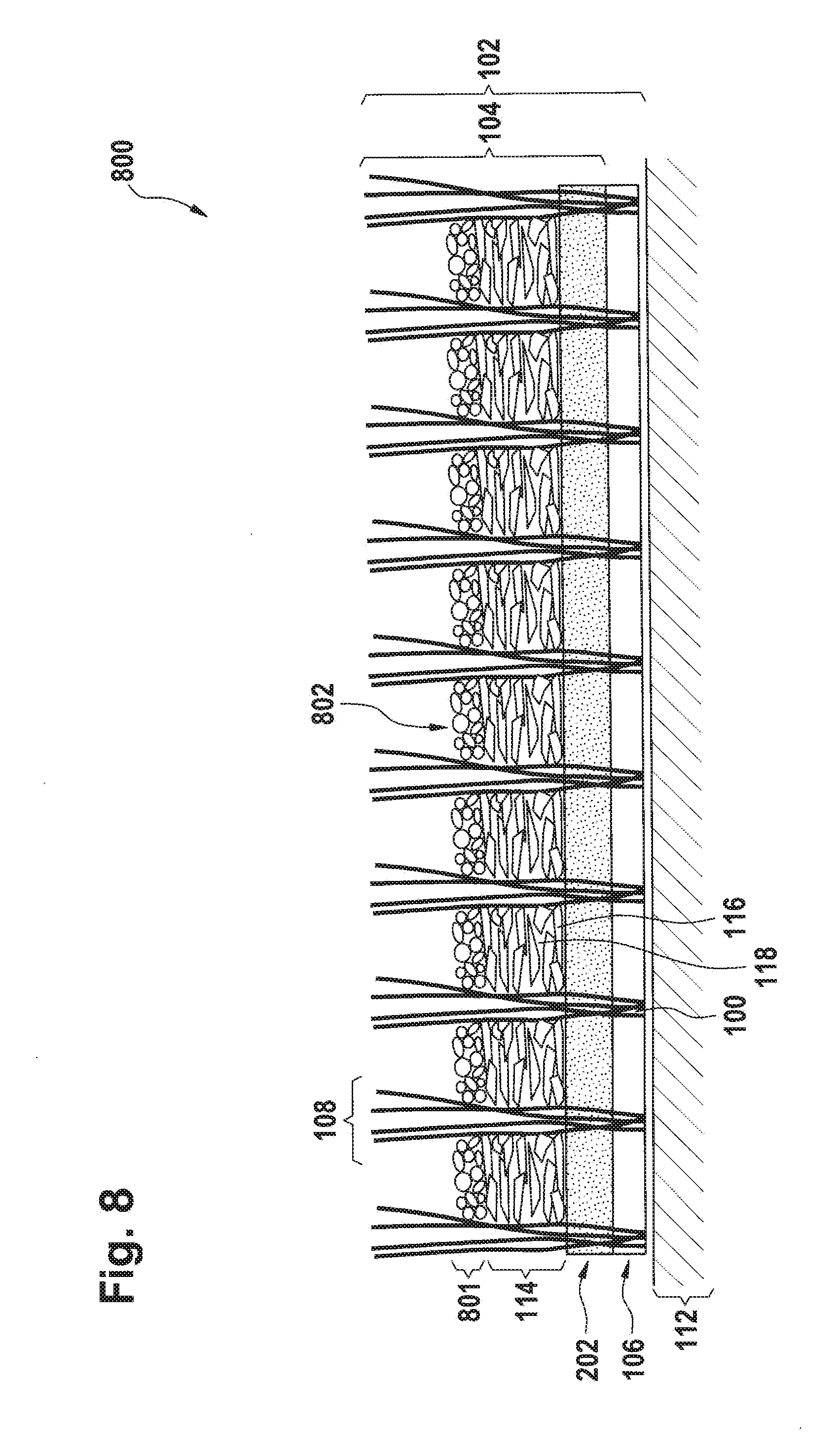

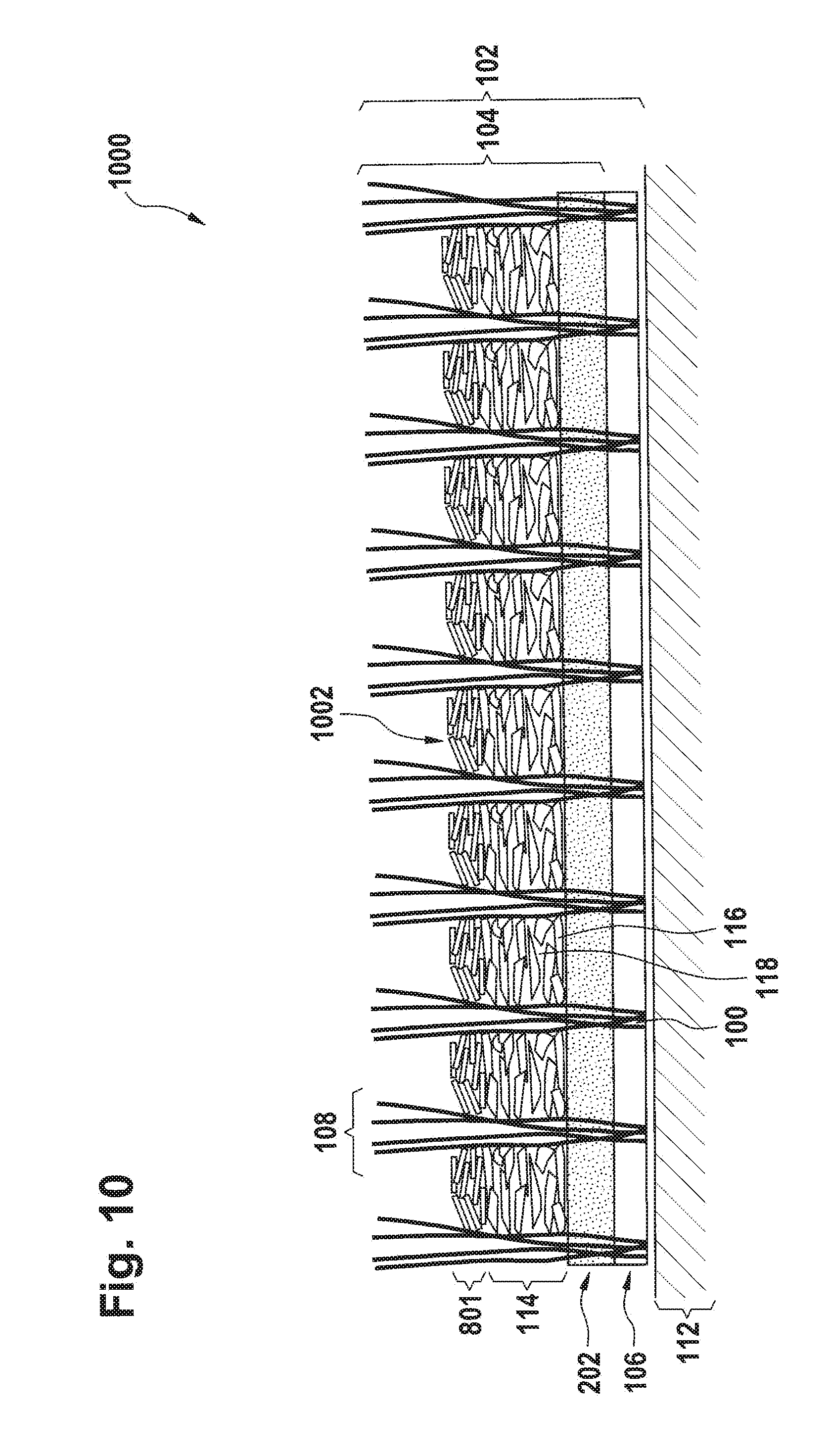
United States Patent
Application |
20190153679 |
Kind Code |
A1 |
NEUHOFF; Ulrich ; et
al. |
May 23, 2019 |
ARTIFICIAL TURF COMPRISING AN AGGLOMERATE INFILL
Abstract
An artificial turf surface includes an artificial turf carpet
with a pile, wherein the artificial turf carpet includes a backing.
The artificial turf carpet further includes artificial grass
fibers. The artificial grass fibers are tufted into the backing.
The artificial grass fibers form the pile. The artificial grass
fibers are secured to the backing. The artificial turf surface
further includes an artificial turf infill distributed within the
pile, wherein the artificial turf infill includes irregularly
shaped grains, wherein the grains include an agglomerate including
at least one type of non-elastomeric thermoplastic. At least a
portion of the grains have fibrous extensions.
Inventors: |
NEUHOFF; Ulrich; (Duisburg,
DE) ; SICK; Stephan; (Willich-Neersen, DE) ;
LOHR; Ivo; (Kempen, DE) |
|
Applicant: |
Name |
City |
State |
Country |
Type |
Polytex Sportbelage Produktions-GmbH |
Grefrath |
|
DE |
|
|
Assignee: |
Polytex Sportbelage
Produktions-GmbH
Grefrath
DE
|
Family ID: |
56511351 |
Appl. No.: |
16/316743 |
Filed: |
July 18, 2017 |
PCT Filed: |
July 18, 2017 |
PCT NO: |
PCT/EP2017/068145 |
371 Date: |
January 10, 2019 |
Current U.S.
Class: |
1/1 |
Current CPC
Class: |
E01C 13/08 20130101;
D05C 17/026 20130101 |
International
Class: |
E01C 13/08 20060101
E01C013/08; D05C 17/02 20060101 D05C017/02 |
Foreign Application Data
Date |
Code |
Application Number |
Jul 18, 2016 |
EP |
16180026.3 |
Claims
1. An artificial turf surface comprising: an artificial turf carpet
with a pile, wherein the artificial turf carpet comprises a
backing; wherein the artificial turf carpet further comprises
artificial grass fibers, wherein the artificial grass fibers are
tufted into the backing, wherein the artificial grass fibers form
the pile, wherein the artificial grass fibers are secured to the
backing; and artificial turf infill distributed within the pile,
wherein the artificial turf infill comprises irregularly shaped
grains, wherein the irregularly shaped grains comprise an
agglomerate, wherein the agglomerate comprises at least one type of
non-elastomeric thermoplastic, wherein at least a portion of the
grains have fibrous extensions.
2. The artificial turf surface of claim 1, wherein at least 50%, at
least 60%, at least 70%, at least 80%, at least 90%, or at least
95% of the irregularly shaped grains have a curved profile.
3. The artificial turf surface of claim 1, wherien at least 40%,
50%, 60%, 70%, 80%, or 90% of the grains have the fibrous
extensions.
4. The artificial turf surface of claim 1, wherein in at least 50%,
70%, or 90% of the portion of the grains the fibrous extensions
comprise at least 30% of the weight of the grains.
5. The artificial turf surface of claim 1, wherein the at least one
types of non-elastomeric thermoplastic comprise recycled artificial
turf fibers.
6. The artificial turf surface of claim 1, wherein the irregularly
shaped grains have a longitudinally stretched out and curved volume
expansion with ratios of length to diameter/cross-section within
1:2 to 1:50.
7. The artificial turf surface of claim 1, wherein the irregularly
shaped grains have a longitudinally stretched out and curved volume
expansion with ratios of length to diameter/cross-section within
any one of the following: 1:4 to 1:50, 1:8 to 1:50, 1:16 to 1:50,
and 1:32 to 1:50.
8. The artificial turf surface of claim 1, wherein the irregularly
shaped grains have a sieve size between 0.2 mm and 12 mm.
9. The artificial turf surface of claim 1, wherein irregularly
shaped grains have a thickness between 0.05 mm and 2 mm.
10. The artificial turf surface of claim 1, wherein the at least
one type of non-elastomeric thermoplastic comprise any one of the
following: a least one thermoplastic polymer, a polyolefm, waste
plastic, fibrous waste plastic, pre-consumer yarn, post-consumer
yarn recovered synthetic sports fields, artificial turf fiber,
recovered waste plastic, poly ethylene, polypropylene, a
polyethylene and polypropylene mixture, LLDPE, HDPE, LDPE, MDPE,
PP, PE, a polyolefin, and combinations thereof.
11. The artificial turf surface of claim 1, wherein the at least
one type of non-elastomeric thermoplastic comprise any one of the
following: recycled packaging material, poly ethylene food
packaging, polyethylene food packaging, and combinations
thereof.
12. The artificial turf surface of claim 1, wherein the fibrous
extensions of the irregularly shaped grains interlock with any one
of the following: the artificial grass fibers, the fibrous
extensions of other irregularly shaped grains, and combinations
thereof.
13. The artificial turf surface of claim 1, wherein at least a
portion of the fibrous extensions are branched and/or hook
shaped.
14. The artificial turf surface of claim 1, wherein the artificial
turf surface further comprises a sand layer between the backing and
the artificial turf infill.
15. The artificial turf surface of claim 1, wherein the artificial
turf surface further comprises a top infill layer, wherein the
irregularly shaped grains are between the backing and the top
infill layer.
16. The artificial turf surface of claim 15, wherein the top infill
layer comprises regularly shaped granules.
17. The artificial turf surface of claim 16, wherein the regularly
shaped granules comprise any one of the following: a least one
thermoplastic polymer, a polyolefin, waste plastic, fibrous waste
plastic, pre-consumer yarn, post-consumer yarn recovered synthetic
sports fields, artificial turf fiber, recovered waste plastic,
recycled packaging material, polyethylene food packaging, poly
ethylene, polypropylene, a polyethylene and polypropylene mixture,
LLDPE, HDPE, LDPE, MDPE, PP, PE, and a polyolefin, and combinations
thereof.
18. The artificial turf surface of claim 16, wherein the regularly
shaped granules comprise any one of the following: an elastomeric
compound, rubber, crumb rubber, EPDM, and combinations thereof.
19. The artificial turf surface of claim 16, wherein the regularly
shaped granules comprises at least 50%, 70%, 90%, or 95% of the top
infill layer by weight.
20. The artificial turf surface of claim 15, wherein the top infill
comprises elongated granules.
21. The artificial turf surface of claim 20, wherein the top infill
comprises at least 40%, 50%, 60%, 70%, 80%, 90%, or 95% of the
elongated granules by weight.
22. The artificial turf surface of claim 20, wherein the wherein
the elongated granules are formed from any one of the following: an
elastomeric compound, shavings from at least one block of an
elastomeric compound, rubber, crumb rubber, EPDM, and combinations
thereof.
23. The artificial turf surface of claim 1, wherein the artificial
turf surface further comprises a sand layer between the backing and
the artificial turf infill, wherein the artificial turf surface
further comprises a top infill layer, wherein the irregularly
shaped grains are between the backing and the top infill layer,
wherein the top infill comprises irregularly shaped granulate,
wherein the irregularly shaped granulate comprises shavings from at
least one block of an elastomeric compound.
24. The artificial turf surface of claim 1, wherein the agglomerate
at least comprises 80%, 90%, 95%, or 99% by weight the at least one
type of non-elastomeric thermoplastic.
25. A method of manufacturing an artificial turf system, wherein
the method comprises: providing an artificial turf carpet with a
pile, wherein the artificial turf carpet comprises a backing;
wherein the artificial turf carpet further comprises artificial
grass fibers, wherein the artificial grass fibers are tufted into
the backing, wherein the artificial grass fibers form the pile
surface, wherein the artificial grass fibers are secured to the
backing; and forming an agglomerate comprising at least one type of
non-elastomeric plastic to form irregularly shaped grains to
provide an infill for the artificial turf carpet.
26. The method of claim 25, wherein at least 50%, at least 60%, at
least 70%, at least 80%, at least 90%, or at least 95% of the
irregularly shaped grains have a curved profile.
27. The method of claim 25, wherien at least 40%, 50%, 60%, 70%,
80%, or 90% of the grains have the fibrous extensions.
28. The method of claim 25, wherein in at least 50%, 70%, or 90% of
the portion of the grains the fibrous extensions comprise at least
30% of the weight of the grains.
29. The method of claim 25, wherein the agglomeration of the at
least one type of non-elastomeric thermoplastic into the
agglomerate and the forming of the irregularly shaped grains from
the agglomerate is performed using an agglomerator.
30. The method of claim 29, wherein the agglomerator is a friction
agglomerator.
31. The method of claim 25, wherein forming of the irregularly
shaped grains is performed using an extruder.
32. The method of claim 30, wherein the extruder comprises any one
of the following: an underwater pelletizing system, a watering
pelletizing system, a strand pelletizing system, and hot-cut
pelletizing system.
33. The method of claim 31, wherein the extruder comprises an
extrusion die plate, wherein any one of the following: the
extrusion die plate has at least one orifice for extruding the
agglomerate, wherein the at least one orifice has a first portion
and an opposing portion, wherein the first portion is rough,
wherein the opposing portion is smooth to form irregularly shaped
grains that have a curved profile; the extruder die plate comprises
multiple orifices, and the multiple orifices have at least two
distinct sizes and/or the orifices are irregularly shaped; and
combinations thereof.
34. The method of claim 31, wherein the extruder comprise a cutting
system for cutting the irregularly shaped grains, wherein the
cutting system is configured for producing irregularly shaped
grains with varying lengths.
35. The method of claim 25, wherein the method further comprises
mixing at least one additive into the agglomerate before forming
the irregularly shaped grains.
36. The method of claim 35, wherein the at least one additive
comprises any one of the following: a dye, a colorant, a
UV-stabilizer, a flame retardant, a binding agent, a blowing agent,
an anti-seize agent, a lubricant, a filler, a compatibilizer, and
combinations thereof.
37. The method of claim 25, wherein the method further comprises
recycling used artificial turf to provide the at least one type of
non-elastomeric thermoplastic.
38. A method of manufacturing an artificial turf surface, wherein
the method comprises the method of claim 25, wherein the method
further comprises: installing the artificial turf carpet; and
distributing the irregularly shaped grains within the pile to form
an artificial turf surface.
39. The use of an agglomerate as infill for artificial turf,
wherein the agglomerate comprises irregularly shaped grains formed
from at least one type of non-elastomeric thermoplastic, and
wherein at least a portion of the grains have fibrous
extensions.
40. The use of an agglomerate as infill for artificial turf of
claim 38, wherein at least 50%, at least 60%, at least 70%, at
least 80%, at least 90%, or at least 95% of the irregularly shaped
grains have a curved profile.
Description
FIELD OF THE INVENTION
[0001] The invention relates to artificial turf, in particular to
artificial turfs with infill and also infill for artificial
turf.
BACKGROUND AND RELATED ART
[0002] Artificial turfs are known as a carpet structure resembling
natural grass. The structure consists of a fabric to which fibers
are tufted and fixed at the bottom side of the fabric. The fibers
are monofilamented or twisted yarns of polyethylene or other
thermoplastic materials. The fabrics are woven goods made of
polypropylene and the fixing material which glues the fibers to the
fabric are mixtures of SBR latices and fillers such as calcium
carbonate or polyurethane-based adhesives.
[0003] Artificial turfs are used as sports fields whereas the
carpets are laid onto a substructure of rubber granules acting as a
shock damping layer or onto a substructure that comprises an
elastic layer (e-layer). The carpet structure is filled with sand
and rubber granules in order to keep the structure in place so that
the carpet does not slip and the fibers stay in an upright
position. The filling material is also referred to as infill or
infill material. Typically in use is SBR-rubber or EPDM-rubber,
both elastomeric materials in irregularly granulated form. The
SBR-rubber is commonly sourced from used tires.
[0004] An advantage of using artificial turf is that it eliminates
the need to care for a grass playing or landscaping surface, like
regular mowing, scarifying, fertilizing and watering. Watering can
be e.g. difficult due to regional restrictions for water usage. In
other climatic zones the re-growing of grass and re-formation of a
closed grass cover is slow compared to the damaging of the natural
grass surface by playing and/or exercising on the field. Artificial
turf fields though they do not require a similar attention and
effort to be maintained, may require some maintenance such as
having to be cleaned from dirt and debris and having to be brushed
regularly. This may be done to help fibers stand-up after being
stepped down during the play or exercise. Throughout the typical
usage time of 5-15 years it may be beneficial if an artificial turf
sports field can withstand high mechanical wear, can resist UV, can
withstand thermal cycling or thermal ageing, can resist
inter-actions with chemicals and various environmental conditions.
It is therefore beneficial if the artificial turf has a long usable
life, is durable, and keeps its playing and surface characteristics
as well as appearance throughout its usage time.
[0005] The infill of synthetic turfs plays a predominant role
concerning the mechanical properties of the complete turf
structure. These properties determine the damping of a bouncing
ball and running or jumping athletes. It is also desirable that the
uppermost structure of a turf would not cause injuries of the
athletes, such as burns, scratches, skin abrasions, etc. Filling a
synthetic turf only with sand would have an unpleasant effect of
energy-sapping, comparable to running on dry sand on a beach. To
avoid such uncomfortable attitudes infill systems are commonly in
use. At least two layers built up such infill systems, whereas the
sand layer is laid first on top of the carpet topping (the opposite
side of the backing) and a second layer or elastomeric material
laid onto the sand. The elastomeric material normally consists of
ground rubber, whereas the particles are coarser than the sand
grains. The thickness of an infill system is such that only a small
proportion of the grass fibers exceed the infill layer in height.
The complete structure then resembles freshly mowed natural
grass.
[0006] The FIFA (Federation Internationale de Football Associaton)
has set up quality standards in their `Quality Concept for Football
Turf, Handbook of Requirements, January 2012 Edition.` In this
handbook, the standards are described as well as the test methods.
For synthetic turf infill systems, the following holds: [0007]
force reduction: 60%-70% [0008] vertical deformation: 4 mm-10 mm
[0009] rotational resistance: 30 Nm-45 Nm all of which in dry and
wet condition and after simulated wear.
[0010] According to the FIFA standards the tests are carried out
with a so-called advanced artificial athlete--Triple A, a Lisport
wear tester and a rotational resistance tester. Artificial turf or
artificial grass is surface that is made up of fibers which is used
to replace grass. The structure of the artificial turf is designed
such that the artificial turf has an appearance which resembles
grass. Typically, artificial turf is used as a surface for sports
such as soccer, American football, rugby, tennis, golf, for playing
fields, or exercise fields. Furthermore, artificial turf is
frequently used for landscaping applications.
[0011] Artificial turf may be manufactured using techniques for
manufacturing carpets. For example, artificial turf fibers which
have the appearance of grass blades may be tufted or attached to a
backing. Often times artificial turf infill is placed between the
artificial turf fibers. Artificial turf infill is a granular
material that covers the bottom portion of the artificial turf
fibers. The use of artificial turf infill may have a number of
advantages. For example, artificial turf infill may help the
artificial turf fibers stand up straight. Artificial turf infill
may also absorb impact from walking or running and provide an
experience similar to being on real turf. The artificial turf
infill may also help to keep the artificial turf carpet flat and in
place by weighting it down.
[0012] United States patent application US 2010/0151158 discloses a
method for recycling synthetic turf that includes agglomerating a
plurality of synthetic turf fragments and extruding the
agglomerated material. The method produces a recycled material for
use as infill in a synthetic turf. The agglomerate is extruded and
may be in a spherical, cylindrical, oval, or football shaped. The
pellets may also be of an irregular shape. The irregular shape may
be used to aid tight packing of the granules.
SUMMARY
[0013] The invention provides for an artificial turf surface, a
method, and the use of an agglomerate as infill for artificial
turf. Embodiments are given in the dependent claims.
[0014] Examples may provide for an artificial turf infill that is
at least partially made from an agglomerate comprising one or more
non-elastomeric thermoplastics. The agglomerate is formed into
irregularly shaped grains. A "grain" as used herein encompasses a
small part or portion of a material that is hard.
[0015] Normally, non-elastomeric thermoplastics would be too hard
and rigid to use as an artificial turf infill. However, forming
them into grains that have fibrous extensions makes them flexible.
When the grains are distributed in the pile of the artificial turf,
the grains have a tendency to pack loosely because of the fibrous
extensions. This produces voids or free space between the grains
which makes the resultant infill more elastic although it has been
manufactured from non-elastomeric thermoplastics.
[0016] In various examples, the agglomerate may be formed my one or
more non-elastomeric thermoplastics and an additional additives
such as a pigment powder.
[0017] In some examples, the artificial turf infill that is at
least partially made from an agglomerate of at least two
non-elastomeric thermoplastics.
[0018] In other examples, material used to form the artificial turf
infill is provided as an agglomerate. An extrusion process or an
agglomeration process is then used to form the material into the
grains with fibrous extensions.
[0019] In one aspect, the invention provides for an artificial turf
surface comprising an artificial turf carpet with a pile. The
artificial turf carpet comprises a backing. The artificial turf
carpet further comprises artificial grass fibers. The artificial
grass fibers are tufted into the backing. The artificial turf grass
fibers form the pile. The artificial grass fibers are secured to
the backing.
[0020] The artificial turf surface further comprises an artificial
turf infill which is distributed within the pile. The artificial
turf infill may also be described as being distributed between the
artificial grass fibers. The artificial turf infill comprises
irregularly shaped grains. The grains comprise an agglomerate
comprising at least one type of non-elastomeric thermoplastic.
Alternatively the grains can be described as comprising an
agglomerate comprising at least one type of non-elastomeric
thermoplastic. At least a portion of the grains have fibrous
extensions.
[0021] In some examples all or a majority of the grains have the
fibrous extensions. In other examples at least 40% 50%, 60%, 70%,
80%, or 90% of the grains have the fibrous extensions. A fibrous
extension as used herein encompasses a region of the grain that is
substantially narrower than another portion of the grain. The
material of the grain may be rigid, but the fibrous extension is
narrow enough that the fibrous extension is able to flex or
bend.
[0022] The use of the irregularly shaped grains as the artificial
turf infill may have several benefits. One potential benefit is
that the non-elastomeric thermoplastics can be used. Normally the
artificial turf infill is made up of an elastomeric material or
material which is easily pushed aside so that the artificial turf
surface has lifelike properties such as mimicking the give of a
real turf surface which has dirt or sand within it. The irregularly
shaped grains have the benefit that there may be air pockets and
the packing ratio of the artificial turf infill is reduced. This
allows the hard non-elastomeric thermoplastics to be used and still
have the properties which realistically mimic a real turf
surface.
[0023] In another embodiment, at least 50%, at least 60%, at least
70%, at least 80%, at least 90%, or at least 95% of the irregularly
shaped grains have a curved profile. Increasing the proportion of
irregularly shaped grains with a curved profile may have the effect
of increasing the amount of cavities or voids formed within the
artificial turf infill. This may in turn provide for better shock
absorption by the artificial turf infill.
[0024] In another embodiment, at least 40%, 50%, 60%, 70%, 80%, or
90% of the grains have the fibrous extensions. This embodiment may
be beneficial because increasing the number or amount of fibrous
extensions may provide for better shock absorption by the
grains.
[0025] In another embodiment, in at least 50%, 70%, or 90% of the
portion of the grains the fibrous extensions comprise at least 30%
of the weight of the grains. This embodiment may be beneficial
because increasing the number or amount of fibrous extensions may
provide for better shock absorption by the grains.
[0026] In another embodiment, the at least one type of
non-elastomeric thermoplastic is viscoelastic at temperatures below
100.degree. C.
[0027] In another embodiment, the at least one type of
non-elastomeric thermoplastic comprise recycled artificial turf
fibers. Recycled artificial turf fibers are equivalent to
artificial grass fibers. The recycled artificial turf fibers are
artificial turf fibers which have been removed from a previously
installed artificial turf surface. The use of the non-elastomeric
thermoplastics from recycled artificial turf fibers may have the
benefit that the reuse of the thermoplastic reduces the amount of
waste which is deposited in landfills. It may also have the benefit
that the recycled artificial turf fibers may have additives which
would be useful for the artificial turf infill. For instance, the
recycled artificial turf fibers may be colored green. Having the
artificial turf infill a green color may be beneficial in making
the artificial turf surface more lifelike looking. It may also have
the benefit that the recycled artificial turf fibers have other
additives such as UV protection which will increase the longevity
of the artificial turf infill.
[0028] In another embodiment, the irregularly shaped grains have a
longitudinally stretched out and curved volume expansion with
ratios of length to diameter/cross sectioned within 1:2 to
1:50.
[0029] In another embodiment, the irregularly shaped grains have a
longitudinally stretched out and curved volume expansion with
ratios of length to diameter/cross-section within any one of the
following: 1:4 to 1:50, 1:8 to 1:50, 1:16 to 1:50, and 1:32 to
1:50. This embodiment may be beneficial because as the irregualry
shaped grains become narrower with respect to their length the
irregularly shaped grains may become more flexible.
[0030] In another embodiment, the irregularly shaped grains have a
sieve size between 0.2 mm and 12 mm. In this embodiment the
irregularly shaped grains have been selected such that they pass
through a first sieve with an opening of 12 mm or less. The
irregularly shaped grains are further selected such that they are
captured by a sieve with openings of 0.2 mm or greater. The opening
of the first sieve remains greater than the opening of the second
sieve.
[0031] In another embodiment the irregularly shaped grains have a
sieve size below 12 mm. In this embodiment the irregularly shaped
grains have been selected such that they pass through a sieve with
an opening of 12 mm or less.
[0032] In another embodiment, the irregularly shaped grains have a
thickness between 0.5 mm and 2 mm.
[0033] In another embodiment, the at least one type of
non-elastomeric thermoplastic comprise any one of the following: at
least one thermoplastic polymer, a polyolefin, waste plastic,
fibrous waste plastic, pre-consumer yarn, post-consumer yarn
recovered from synthetic sports fields, artificial turf fiber,
recovered waste plastic, recycled packaging material, poly ethylene
food packaging, poly ethylene, polypropylene, a poly ethylene and
poly propylene mixture, LLDPE, HDPE, LDPE, MDPE, PP, PE, a
polyolefin, and combinations thereof. This embodiment may be
beneficial because thermoplastic which would normally be disposed
of may be used for manufacturing a high quality artificial turf
surface.
[0034] In another embodiment, the artificial turf surface further
comprises a sand layer between the backing and the artificial turf
infill. The use of the sand layer between the backing and the
artificial turf infill may further serve to improve the replication
of natural turf surface properties by the artificial turf surface.
The use of the sand layer may also reduce the amount of artificial
turf infill which is required to be used.
[0035] In another embodiment, the majority of the irregularly
shaped grains have a curved profile. The curved profile may be in a
cross-sectional view of the irregularly shaped grain. Having a
curved profile may be beneficial because it may reduce how closely
the irregularly shaped grains can be packed next to each other.
Having them less dense may be beneficial because the artificial
turf infill will have a more springy or elastic profile although
the agglomerate is made of a non-elastomeric thermoplastic.
[0036] In another embodiment, the fibrous extensions of the
irregularly shaped grains interlock with any one of the following:
the artificial grass fibers, the fibrous extensions of other
irregularly shaped grains, and combinations thereof. This
embodiment may be beneficial because the interlocking of the
fibrous extensions may serve to hold the irregularly shaped grains
in the same position with respect to each other, and also possibly
to help hold their position relative to the artificial grass
fibers. This may for example have the benefit of reducing the
splash effect when a ball hits an artificial turf surface. Splash
is when the impact of a ball or other object causes artificial turf
infill to fly up above the surface of the artificial turf surface.
It resembles the splash of an object hitting a puddle of water.
[0037] In another embodiment, at least a portion of the fibrous
extensions are branched. The branching of the fibrous extensions
may be beneficial because it may make the fibrous extensions more
flexible. The branching may also produce hook like structures that
enable the irregularly shaped grains to better interlock either
with themselves or artificial grass fibers.
[0038] In another embodiment, the artificial turf surface further
comprises a top infill layer. The irregularly shaped grains are
between the backing and the top infill layer.
[0039] In another embodiment, the top infill layer comprises
regularly shaped granules. The regularly shaped granules may for
example have round, oval, a rounded, or bead shaped appearance. The
use of the regularly shaped granules may be beneficial because it
may have the effect of reducing the friction between an object
sliding on the artificial turf surface and the irregularly shaped
grains.
[0040] In another embodiment, the regularly shaped granules
comprises at least 50%, 70%, 90%, or 95% of the top infill layer by
weight. This embodiment may be beneficial because as the amount of
the regularly shaped granules increases in the top infill layer the
friction between an object sliding on the artificial turf surface
is further reduced.
[0041] In another embodiment, the top infill layer consists of the
regularly shaped granules.
[0042] For example, the regularly shaped grains could be made from
an agglomerate that is similar or has an equivalent composition to
the irregularly shaped grains. In other examples the regularly
shaped granules could be made from a elastomeric compound such as
crumb rubber or other materials conventionally used as artificial
turf infill. For example, the elastomeric granulates used for
artificial turf infill could be placed on the surface artificial
turf infill formed by the irregularly shaped grains. This may
reduce the amount of elastomeric granulates that are used. As a
smaller amount of the elastomeric granulate is used, it may reduce
the splash effect when a ball or other object impacts the
artificial turf surface.
[0043] In another embodiment, the regularly shaped granules
comprise any one of the following: a least one thermoplastic
polymer, a polyolefin, waste plastic, fibrous waste plastic,
pre-consumer yarn, post-consumer yarn recovered synthetic sports
fields, artificial turf fiber, recovered waste plastic, recycled
packaging material, poly ethylene food packaging, EPDM, LLDPE,
HDPE, LDPE, MDPE, PP, PE, a polyolefin, an elastomeric compound,
rubber, crumb rubber, and combinations thereof.
[0044] In another embodiment, the top infill comprises elongated
granules. In some examples, the elongated granules may comprise an
elastic or flexible material. The use of the elongated granulates
in the top infill may have several advantages. First, the elongated
shape may help the top infill to remain above or covering the
infill made from the irregularly shaped grains. The elongated shape
may, in some examples, result in less friction between a person or
object sliding on the artificial turf. The use of the elongated
granules may also reduce the splash effect when a ball or other
object impacts the artificial turf surface.
[0045] In another embodiment, the elongated granulate are formed
from any one of the following: an elastomeric compound, shavings
from a block of an elastomeric compound, rubber, crumb rubber,
EPDM, and combinations thereof.
[0046] In another embodiment the elongated granulate are shavings
formed from a block of an elastomeric compound. The use of the
shavings from an elastomeric compound may make the artificial turf
surface appear more realistic. The use of shavings from an
elastomeric compound may also make the shaving have a fiber like
structure that helps to keep them in place and reduce the splash
effect.
[0047] In another embodiment, the top infill comprises at least
40%, 50%, 60%, 70%, 80%, 90%, or 95% of the elongated granules by
weight. This embodiment may be beneficial because it may provide
for an artificial turf surface that is less likely to damage or
irritate the skin of a player when sliding on the playing surface.
The reduction of the splash effect may also increase with a larger
proportion of the elongated granules in the top infill.
[0048] In another embodiment, the top infill consists of the
elongated granules. This embodiment may have the benefit of further
reducing the splash effect.
[0049] In another embodiment, the artificial turf surface further
comprises a sand layer between the backing and the artificial turf
infill. The artificial turf surface further comprises a top infill
layer, wherein the irregularly shaped grains are between the
backing and the top infill layer. The top infill comprises
irregularly shaped granulate. The irregularly shaped granulate
comprises shavings from a block of an elastomeric compound. This
embodiment may be beneficial because the irregularly shaped
granulate may provide shock absorbency and also may reduce the
friction between an object sliding on the artificial turf surface
and the irregularly shaped grains.
[0050] In another aspect, the invention provides for a method of
manufacturing an artificial turf system. An artificial turf system
as used herein encompasses the components which are supplied to
manufacture an artificial turf surface.
[0051] The method comprises providing an artificial turf carpet
with a pile. The artificial turf carpet comprises a backing. The
artificial turf carpet further comprises artificial grass fibers.
The artificial grass fibers are tufted into the backing. The
artificial grass fibers form the pile surface. The artificial grass
fibers are secured to the backing.
[0052] The method further comprises agglomerating the at least one
type of non-elastomeric plastic into an agglomerate for forming
irregularly shaped grains to provide an infill for the artificial
turf carpet.
[0053] In another embodiment, the agglomeration of the at least one
type of non-elastomeric thermoplastic into the agglomerate and the
forming of the irregularly shaped grains form the agglomerate is
performed using an agglomerator. An agglomerator as used herein is
a device which applies heat and pressure to agglomerate multiple
thermoplastics into a single structure. The agglomerator may also
cut or break the agglomeration into the irregularly shaped
grains.
[0054] The use of an agglomerator may be beneficial because it may
provide for an inexpensive means of manufacturing irregularly
shaped grains.
[0055] In another embodiment, the agglomerator is a friction
agglomerator. The friction agglomerator may have one or more moving
portions which use friction to generate the heat necessary to form
the agglomerate.
[0056] In another embodiment, the agglomerator is a disc
agglomerator. The disc agglomerator may have one or more rotating
discs which receive the heated non-elastomeric thermoplastic and
agglomerate them into the agglomerate and form the irregularly
shaped grains at the same time.
[0057] In another embodiment, the forming of the irregularly shaped
grains from the agglomerate is performed using an extruder. The use
of an extruder may be beneficial because the properties of the
irregularly shaped grains may be precisely controlled. An extruder
as used herein encompasses a device which heats the at least one
type of non-elastomeric thermoplastic and then forces them through
an orifice to extrude them. There may also be a device which cuts
the extruded agglomerate into the irregularly shaped grains. The
material extruded from the extruder may be referred to as an
extrudate. However, the extrudate is the agglomerate.
[0058] In another embodiment, the extruder comprises any one of the
following: an underwater pelletizing system, a water ring
pelletizing system, a strand pelletizing system, and a hot-cut
pelletizing system.
[0059] In another embodiment, the extruder optionally comprises a
pelletizer or granulation system to additionally form the shape of
the irregularly shaped trains.
[0060] In another embodiment, the forming of the irregularly shaped
grains is performed using an extruder. The use of an extruder may
be beneficial because it may allow for precise control of the
properties of the irregularly shaped grains such as the length, the
amount of curvature of the grain, and the relative size
distribution.
[0061] In another embodiment, the extruder comprises an extrusion
die plate. The extrusion die plate has at least one orifice for
extruding the agglomerate. The at least one orifice has a first
portion and an opposing portion. The first portion is rough. The
opposing portion is smooth to form irregularly shaped grains that
have a curved profile. The first portion, which is rough, causes a
breaking or slowing effect as the agglomerate is extruded. This
causes the resulting irregularly shaped grain to have a curved
profile. This may be beneficial in that it may cause the
irregularly shaped grains to pack less densely. This may cause them
to have a more elastic behavior although they are made from a
non-elastomeric thermoplastic.
[0062] In another embodiment, the extruder comprises multiple
orifices. The multiple orifices have at least two distinct sizes.
This embodiment may be beneficial because the size distribution of
the irregularly shaped grains and their relative frequency can be
precisely controlled.
[0063] In another embodiment, the multiple orifices may have an
irregular shape or profile. The use of the irregular shape or
profile may have the benefit of producing grains of agglomerate
that are irregularly shaped.
[0064] In another embodiment, the extruder comprises a cutting
system for cutting irregularly shaped grains.
[0065] In another embodiment, the cutting system of the extruder is
configured for producing irregularly shaped grains with varying
lengths. This may for instance be achieved by controlling how often
the cutting system cuts off extrudate (the agglomerate) that is
being extruded. By varying the times between when the agglomerate
is cut or choosing a distribution of times the relative size
distribution of the irregularly shaped grains can be
controlled.
[0066] In another embodiment, the method further comprises mixing
at least one additive into the agglomerate before forming the
irregularly shaped grains. This may be beneficial in adding various
properties to the irregularly shaped grains such as flame
retardants, UV protection, or dyes to color to change the
appearance of the artificial turf infill.
[0067] In another embodiment, the at least one additive comprises
any one of the following: a colorant or dye, a UV stabilizer, a
flame retardant, a filler, a blowing agent, an anti-seize agents, a
lubricant, compatibilizer, a binding agent, and combinations
thereof.
[0068] In another embodiment, the method further comprises
recycling used artificial turf to provide the at least one of the
at least one type of non-elastomeric thermoplastic. This may be
beneficial in that it may reduce the environmental impact of
installing a new artificial turf surface. It may also have the
benefit that the thermoplastic recovered from the used artificial
turf may have additives such as colorants or UV stabilizers or
flame retardants that are already present. This may reduce the cost
of manufacturing a new artificial turf surface.
[0069] In another embodiment the agglomerate at least comprises
80%, 90%, 95%, or 99% by weight the at least one type of
non-elastomeric thermoplastic. In other words the agglomerate is at
least 80%, 90%, 95%, or 99% (by weight) made from the at least one
non-elastomeric thermoplastic. Increasing the amount of the
non-elastomeric thermoplastic may have the benefit of increasing
the mechanical stability of the fibrous extensions. If other
materials such as sand or elastomeric materials are mixed into the
agglomerate the irregularly shaped grains may be structurally
compromised.
[0070] In another embodiment the agglomerate consists of the at
least one type of non-elastomeric thermoplastic. This embodiment
may be beneficial because the agglomerate is completely made from
the at least one type of non-elastomeric thermoplastic. Although
the agglomerate is made from the non-elastomeric thermoplastic it
is flexible due to the fibrous extensions. The fibrous extensions
are less likely to break apart when formed entirely from the at
least one type of non-elastomeric thermoplastic.
[0071] In another embodiment the irregularly shaped grains consist
of the agglomerate. This may provide for better structural
integrity of the irregularly shaped grains.
[0072] In another aspect, the invention provides for a method of
manufacturing an artificial turf surface. The method comprises a
method of manufacturing an artificial turf system according to an
embodiment. The method further comprises installing the artificial
turf carpet. The method further comprises distributing the
irregularly shaped grains within the pile and between the
artificial grass fibers to form the artificial turf.
[0073] In another embodiment, the method of manufacturing the
artificial turf surface comprises distributing a sand layer within
the pile before distributing the irregularly shaped grains.
[0074] In another aspect, the invention provides for use of an
agglomerate as infill for artificial turf. The agglomerate
comprises irregularly shaped grains formed for at least one type of
non-elastomeric thermoplastic. At least a portion of the grains may
have fibrous extensions.
[0075] It is understood that one or more of the aforementioned
embodiments of the invention may be combined as long as the
combined embodiments are not mutually exclusive.
BRIEF DESCRIPTION OF THE DRAWINGS
[0076] In the following embodiments of the invention are explained
in greater detail, by way of example only, making reference to the
drawings in which:
[0077] FIG. 1 illustrates an example of an artificial turf
surface;
[0078] FIG. 2 illustrates a further example of an artificial turf
surface;
[0079] FIG. 3 illustrates an examples of an irregularly shaped
grains;
[0080] FIG. 4 illustrates an example of an agglomerator;
[0081] FIG. 5 illustrates an example of an extruder;
[0082] FIG. 6 illustrates an example of an extrusion die plate;
[0083] FIG. 7 illustrates an example of an artificial turf
system;
[0084] FIG. 8 illustrates a further example of an artificial turf
surface;
[0085] FIG. 9 illustrates a further example of an extrusion die
plate; and
[0086] FIG. 10 illustrates a further example of an artificial turf
surface.
DETAILED DESCRIPTION
[0087] Like numbered elements in these figures are either
equivalent elements or perform the same function. Elements which
have been discussed previously will not necessarily be discussed in
later figures if the function is equivalent.
[0088] FIG. 1 shows an example of an artificial turf surface 100.
The artificial turf surface 100 is formed by an artificial turf
carpet 102 that has a pile 104. The artificial turf carpet 102
comprises a backing 106. Into the backing there are artificial
grass fibers 108 that are tufted 110 into the backing 106. The pile
104 is formed from the artificial grass fibers 108. The artificial
grass fibers 108 may for instance be formed from a thermoplastic
yarn or artificial grass. The backing 106 may be placed onto a base
layer 112. The base layer may take different forms in different
examples. In one example the base layer is simply the ground. The
artificial turf carpet 102 may simply be placed on the ground. In
other examples the base layer 112 may have different components for
providing drainage, and absorption of shock from athletes or other
users of the artificial turf surface 100.
[0089] Within the pile 104 and between the artificial grass fibers
108 is spread an artificial turf infill 114. In this case the
infill 114 comprises irregularly shaped grains 116. The irregularly
shaped grains are formed from an agglomerate comprising at least
one type of non-elastomeric thermoplastic. The non-elastomeric
thermoplastics may also be thermoplastic polymers. The use of the
irregularly shaped grains causes voids 118 between a number of the
irregularly shaped grains 116. These voids provide give and
elasticity to the irregularly shaped grains 116 that are made of
what is considered normally a rigid thermoplastic. This enables a
material which would normally be unsuitable for making artificial
turf infill function well. The artificial turf infill 114 may
provide for helping the artificial grass fibers 108 to stay rigid
and in the correct position. They may also provide for shock
absorption or other physical properties which help the artificial
turf surface 100 more approximate the properties of a real turf
surface.
[0090] FIG. 2 shows a further example of an artificial turf surface
200. The artificial turf surface 200 is similar to the artificial
turf surface 100 shown in FIG. 1. However, in this example there is
additionally a layer of sand between the backing and the infill
114. The example shown in FIG. 2 may further approximate the
properties of real turf more accurately. The use of the infill 114
with the irregularly shaped grains 116 may provide a more lifelike
and elastic surface than when sand 202 is used alone.
[0091] FIG. 3 shows a photograph of a number of irregularly shaped
grains 116. The irregularly shaped grains comprise at least one
non-elastomeric polymer. The photograph shows that at least some of
the irregularly shaped grains comprise fibrous extensions 302. Not
all of the fibrous structure of the extensions is visible in the
photograph. Some of the grains also show fibrous extensions 302
with a branched structure 304. Some of the fibrous extensions 302
also have a hook like structure 306. The branched structure 304 or
hook like structure 306 may help the irregularly shaped grains
interlock with themselves and/or artificial grass fibers.
thermoplastics.
[0092] The irregularly shaped grains in FIG. 3 were tested as
artificial turf infill. Although made from rigid thermoplastics
they exhibited shock absorbency. Recycled SBR rubber infill was
compared to irregularly shaped grain infill of two different sizes.
The first size of irregularly shaped grain infill had a
characteristic dimension of less than 2.5 mm. The second size had a
characteristic dimension greater than 2.5 mm. A sieve with a 2.5 mm
screen was used to separate the two. In the experiment the force
reduction of a soccer ball hitting the surface was measured for
three consecutive hits at the same location for each hit. The
results are summarized in the table below
TABLE-US-00001 SBR infill agglomerate agglomerate As benchmark
<2.5 mm >2.5 mm Force reduction 1st hit 32.8% 40.3% 36.6%
Force reduction 2.sup.nd hit 19.3% 9.8% 25.7% Force reduction
3.sup.rd hit 15.8% 6.1% 19.8%
[0093] In the above table it can be see that the agglomerate infill
made from the irregularly shaped grains has a shock absorbency that
is comparable to the SBR infill made from recycled black crumb
rubber. In fact, the larger grains (greater than 2.5 mm)
surprisingly showed shock absorbency that was greater than the SBR
infill material for all three impacts.
[0094] FIG. 4 shows an example of an agglomerator 400. The
agglomerator has a hopper 402 for receiving waste thermoplastic
404. A feeder 406 then feeds the waste thermoplastic 404 into a an
agglomerator 408 which comprises a rotating disc and a stationary
portion The agglomerator 408 may heat and compress the waste
thermoplastic 404. The rotating disc 408 may have veins or
gear-like surfaces which compress and cut the waste thermoplastic
404 into the irregularly shaped grains 116.
[0095] FIG. 5 shows an example of an extruder 500. The extruder
again has a hopper for receiving waste thermoplastic 404. The waste
thermoplastic is then fed by a feeder 406 which heats and forces
the waste thermoplastic through an orifice through an extrusion die
plate 504. A cutting system 506 then cuts agglomerate that is
extruded from the orifice 502 into the irregularly shaped grains
116. The rate at which the cutting system 508 cuts the agglomerate
will control the length of the irregularly shaped grains 116. The
rate of the cutting system 506 can be varied to produce a
distribution of lengths of irregularly shaped grains 116.
[0096] FIG. 6 shows an example of an extrusion die plate 504 with
an orifice 502. The orifice 502 has a first portion 600 and an
opposing portion 602. The first portion 600 is rough and the
opposing portion 602 is smooth. This modification will cause
material extruded from the orifice 502 to have a curvature to
it.
[0097] FIG. 7 shows a flowchart which illustrates a method of
manufacturing an artificial turf system. First in step 700 an
artificial turf carpet 102 such as shown in FIG. 1 or 2 is
provided. Next in step 702 irregularly shaped grains 116 are
manufactured using the machine such as is illustrated in FIG. 4 or
5. At least one type of non-elastomeric thermoplastic is either
provided as an agglomerate or formed with another material such as
a second elastomeric thermoplastic or a dye in power form. The
agglomerate is then forced into the irregularly shaped grains 116.
In some examples, the agglomeration process is used to form the
irregularly shaped grains. In other examples, an extruder or
agglomerator is used to form the agglomerate into the irregularly
shaped grains.
[0098] FIG. 8 shows a further example of an artificial turf surface
800. The artificial turf surface 800 is similar to the artificial
turf surface 200 shown in FIG. 2. However, in this example there is
additionally a top infill layer (801) that comprises regularly
shaped granules 802. The top infill layer (801) is on top of the
irregularly shaped grains 114. The use of the regularly shaped
granules 802 have the advantage of reducing the friction when
something slides on the surface of the artificial turf surface 800.
The regularly shaped granules 802 may be made of several different
materials. In one example the regularly shaped granules are made
from a agglomerate comprising at least one type of non-elastomeric
thermoplastic. In another example the regularly shaped granules are
made from an elastomer.
[0099] FIG. 9 illustrates another example of an extrusion die plate
(504) similar to that shown in FIG. 6. The extrusion die plate has
a number of orifices 502' for extruding the irregularly shaped
granules. The orifices have a variety of different sizes. The
relative sizes of the orifices can be used to generate a
distribution of grains with different sizes. The shape or profile
of the orifices can also be modified to aid in providing the grains
with an irregular shape.
[0100] FIG. 10 shows a further example of an artificial turf
surface 1000. The artificial turf surface 1000 is similar to the
artificial turf surface 800 shown in FIG. 8. However, in this
example the top infill layer comprises either elongated granules
1002 and/or irregularly shaped granulate 1002 on top of the
irregularly shaped grains 114. The use of the elongated granules
1002 and/or irregularly shaped granulate 1002 may have the
advantage of reducing the friction when something slides on the
surface of the artificial turf surface 1002. The elongated granules
1002 and/or irregularly shaped granulate 1002 may be made of
several different materials. In one example the elongated granules
1002 and/or irregularly shaped granulate 1002 may for example be
manufactured from an elastomeric compound or other flexible
material.
[0101] The following examples are several possible practical
examples of artificial turf surfaces that use the irregularly
shaped grains as artificial turf infill. Artificial turf infill
made from irregularly shaped grains is referred to as "polymer
agglomerate." All weights refer to the amount of material
distributed on the surface of an artificial turf carpet. The
polymer agglomerate is placed on top of the sand layer. The term
e-layer refers to a substructure made of a shock absorptive layer
of rubber granulate, matting, or other material under the
artificial turf carpet. [0102] Example 1 (artificial turf carpet
with a 40 mm high pile): [0103] Polymer agglomerate: 5 kg/m.sup.2
[0104] Sand: 15 kg/m.sup.2 [0105] e-layer: 25 mm [0106] Example 2
(artificial turf carpet with a 40 mm high pile): [0107] Polymer
agglomerate: 7.5 kg/m.sup.2 [0108] Sand: 12.5 kg/m.sup.2 [0109]
e-layer: 25 mm [0110] Example 3 (artificial turf carpet with a 40
mm high pile): [0111] Polymer agglomerate: 5 kg/m.sup.2 [0112]
Sand: 15 kg/m.sup.2 [0113] e-layer: 30 mm [0114] Example 4
(artificial turf carpet with a 40 mm high pile): [0115] Polymer
agglomerate: 5 kg/m.sup.2 [0116] Size distribution: 0-2.5 mm
(sorted by sieve size) [0117] Sand: 15 kg/m.sup.2 [0118] e-layer:
25 mm [0119] Example 5 (artificial turf carpet with a 40 mm or 60
mm high pile): [0120] Polymer agglomerate: 5 kg/m.sup.2 [0121] Size
distribution: 2.5-12.5 mm (sorted by sieve size) [0122] Sand: 15
kg/m.sup.2 [0123] e-layer: 25 mm
[0124] In the 5 above examples, the numerical values may be varied
by up to 10%, 20, or 30% to produce alternative examples.
[0125] In examples 1 through 3, so size distribution of the polymer
agglomerate is given. It is understood that any sieve size between
1 and 12.5 mm may be used to sort agglomerate for these two
examples.
[0126] In examples 4 and 5: Grains that pass through the 2.5 mm
sieve are used for example 4. The grains that are caught by the 2.5
mm sieve, but pass through a 12.5 mm sieve are used for example
5.
LIST OF REFERENCE NUMERALS
[0127] 100 artificial turf surface [0128] 102 artificial turf
carpet [0129] 104 pile [0130] 106 backing [0131] 108 artificial
grass fibers [0132] 110 tufting [0133] 112 base layer [0134] 114
infill [0135] 116 irregularly shaped grains [0136] 118 void [0137]
200 artificial turf surface [0138] 202 sand [0139] 302 fibrous
extensions [0140] 304 branched structure [0141] 306 hook like
structure [0142] 400 agglomerator [0143] 402 hopper [0144] 404
waste thermoplastic [0145] 408 agglomerator disk [0146] 500
extruder [0147] 502 orifice [0148] 502' orifice [0149] 504
extrusion die plate [0150] 506 cutting system [0151] 600 first
portion [0152] 602 opposing portion [0153] 700 provide an
artificial turf carpet with a pile, [0154] 702 form an agglomerate
comprising least one type of non-elastomeric thermoplastic into
irregularly shaped grains to provide an infill for the artificial
turf carpet [0155] 800 artificial turf surface [0156] 801 top
infill layer [0157] 802 regularly shaped granules [0158] 1000
artificial turf surface [0159] 1002 elongated granules or
irregularly shaped granulate
* * * * *