U.S. patent application number 15/814657 was filed with the patent office on 2019-05-16 for laser-hardened fillet-rolled crankshaft.
This patent application is currently assigned to FORD GLOBAL TECHNOLOGIES, LLC. The applicant listed for this patent is FORD GLOBAL TECHNOLOGIES, LLC. Invention is credited to Nathaniel Hansen, Michael A. Kopmanis, Roger L. Moyer, Phillip Schroeder.
Application Number | 20190143398 15/814657 |
Document ID | / |
Family ID | 66335426 |
Filed Date | 2019-05-16 |
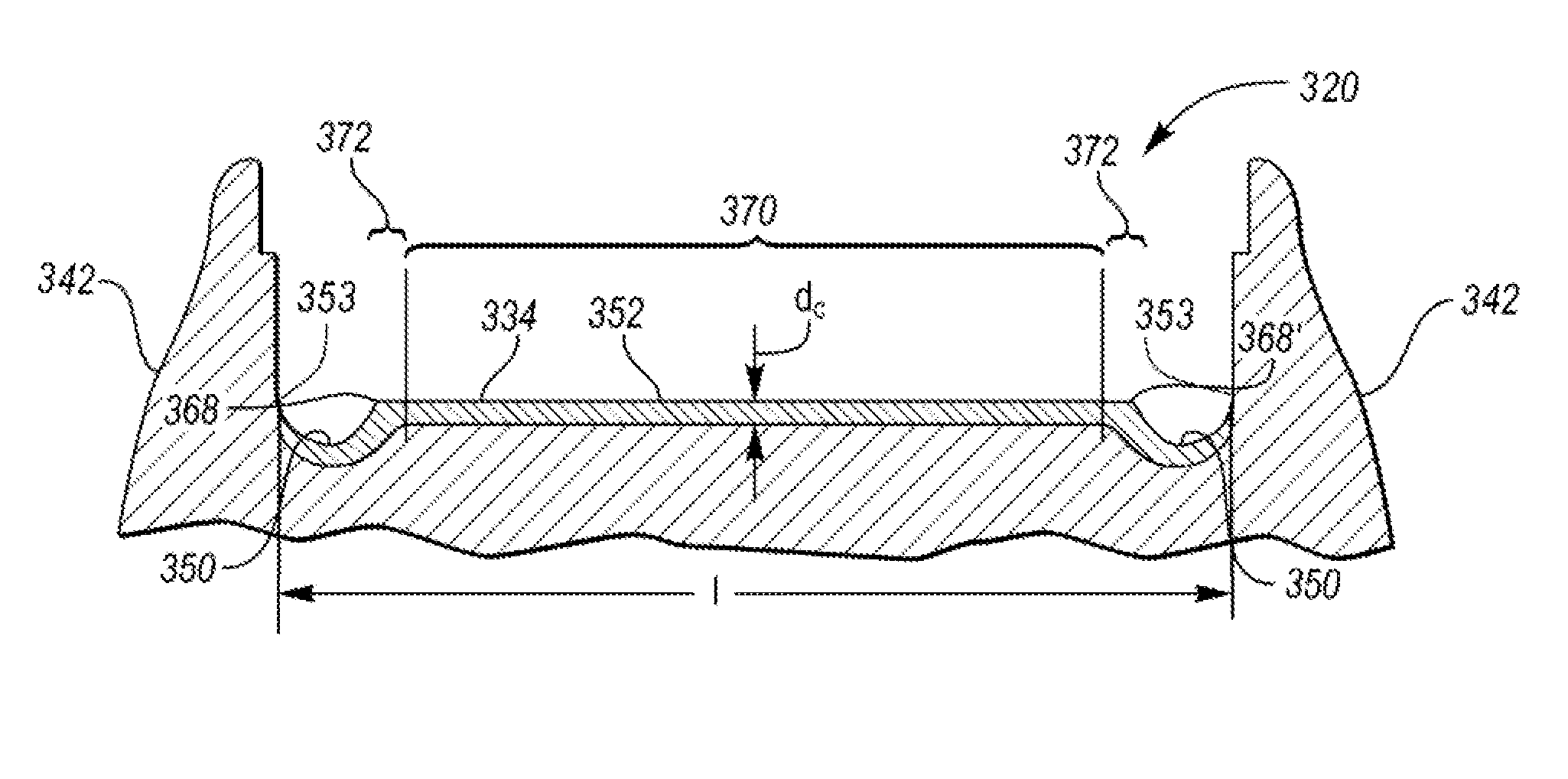
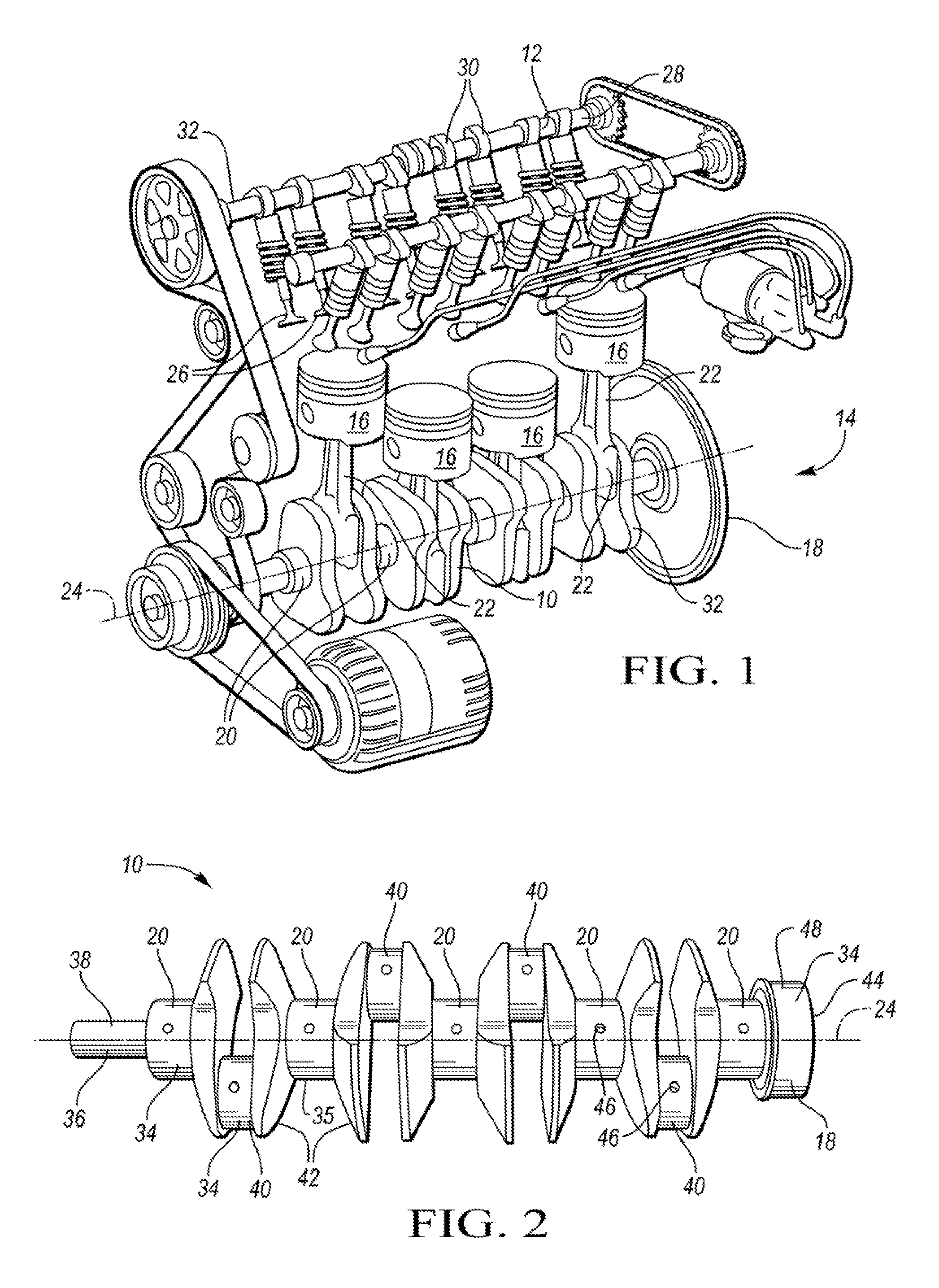

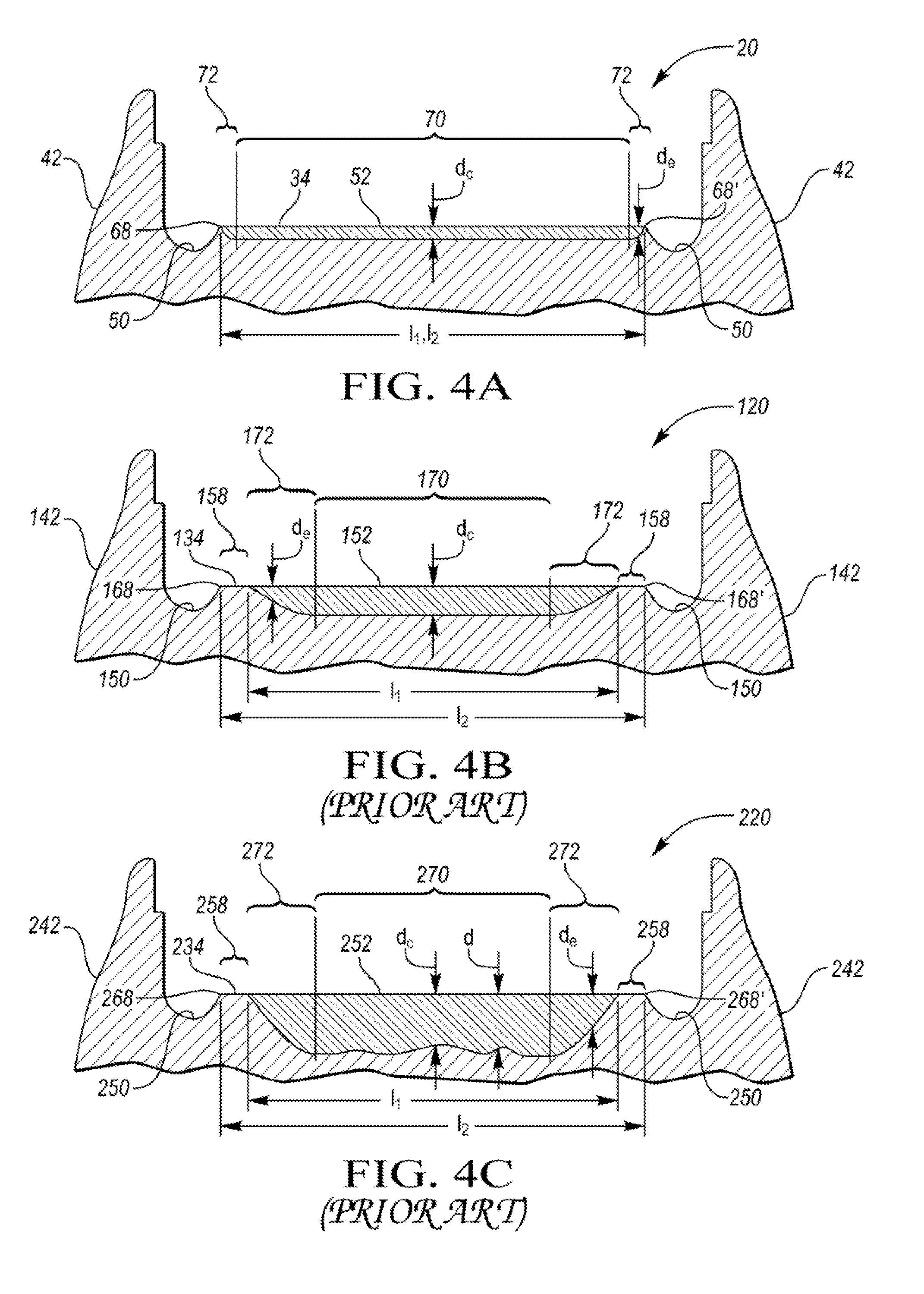

United States Patent
Application |
20190143398 |
Kind Code |
A1 |
Hansen; Nathaniel ; et
al. |
May 16, 2019 |
LASER-HARDENED FILLET-ROLLED CRANKSHAFT
Abstract
An automotive shaft fillet treating method including laser
hardening a green machined fillet surface to a uniform depth d to
induce compressive stresses into the surface, the surface extending
the entire length l between outer edges of two undercut regions of
the fillet, and applying additional compressive stress to the laser
hardened surface via fillet rolling such that the uniform depth d
is maintained along the entire length l during a subsequent
grinding operation.
Inventors: |
Hansen; Nathaniel; (Canton,
MI) ; Schroeder; Phillip; (Continental, OH) ;
Moyer; Roger L.; (McCutchenville, OH) ; Kopmanis;
Michael A.; (Monroe, MI) |
|
Applicant: |
Name |
City |
State |
Country |
Type |
FORD GLOBAL TECHNOLOGIES, LLC |
Dearborn |
MI |
US |
|
|
Assignee: |
FORD GLOBAL TECHNOLOGIES,
LLC
Dearborn
MI
|
Family ID: |
66335426 |
Appl. No.: |
15/814657 |
Filed: |
November 16, 2017 |
Current U.S.
Class: |
29/888.08 |
Current CPC
Class: |
C21D 7/08 20130101; B24B
39/04 20130101; B24B 39/045 20130101; B23K 26/352 20151001; C21D
1/09 20130101; B24B 19/12 20130101; C21D 1/58 20130101; B24B 5/42
20130101; C21D 1/20 20130101; C21D 9/30 20130101; C21D 1/10
20130101; C21D 1/42 20130101; C21D 1/52 20130101; B21H 7/185
20130101; C21D 1/08 20130101 |
International
Class: |
B21H 7/18 20060101
B21H007/18; B24B 39/04 20060101 B24B039/04; C21D 9/30 20060101
C21D009/30; C21D 1/58 20060101 C21D001/58; C21D 1/08 20060101
C21D001/08; C21D 1/42 20060101 C21D001/42 |
Claims
1. An automotive shaft fillet treating method comprising: laser
hardening a green machined fillet surface to a uniform depth d to
induce compressive stresses into the surface, the surface extending
the entire length l between outer edges of two undercut regions of
the fillet; and applying additional compressive stress to the laser
hardened surface via fillet rolling such that the uniform depth d
is maintained along the entire length l during a subsequent
grinding operation.
2. The method of claim 1, wherein the surface includes the
undercuts, crests, end regions, and a central region of the
fillet.
3. The method of claim 1, wherein a hardened depth d of the surface
is about 1.0 mm.
4. The method of claim 1, wherein the surface includes about 80 to
100% fillet contact area.
5. The method of claim 1, wherein the shaft is a crankshaft or a
camshaft.
6. The method of claim 1, wherein the fillet rolling is performed
at about 5 to 15 kN.
7. The method of claim 1, wherein the fillet is a main journal, a
pin journal, or a post.
8. The method of claim 7, wherein the subsequent grinding operation
includes remanufacturing.
9. A method of treating a fillet, the method comprising: laser
hardening an undercut-to-undercut surface of a green fillet to a
uniform depth d to induce compressive stresses uniformly into the
surface; and applying additional compressive stress to the laser
hardened surface via fillet rolling such that the uniform depth d
is maintained along the entire surface.
10. The method of claim 9, wherein the surface includes the
undercuts, crests, end regions, and a central region of the
fillet.
11. The method of claim 9, wherein the uniform depth d of the
surface is about 1.0 mm.
12. The method of claim 9, wherein the surface includes about 80 to
100% of fillet contact area.
13. The method of claim 9, wherein the shaft is a crankshaft or a
camshaft.
14. The method of claim 9, wherein the fillet rolling is performed
at about 5 to 15 kN.
15. The method of claim 9, wherein the fillet is a main journal, a
pin journal, or a post.
16. The method of claim 9, wherein the uniform depth d is
maintained along the entire surface during subsequent
operation(s).
17. A shaft fillet comprising: an undercut-to-undercut surface area
defined by and between outer edges of two undercut regions of the
fillet, an entirety of the surface area being laser hardened to a
uniform depth d to form a layer containing hardened portions
configured to receive additional compressive stress via fillet
rolling without fracture.
18. The fillet of claim 17, wherein the depth d is about 1.0
mm.
19. The fillet of claim 17, wherein the fillet is a main journal, a
pin journal, or a post.
20. The fillet of claim 17, wherein the surface area includes the
undercuts, crests, end regions, and a central region of the fillet.
Description
TECHNICAL FIELD
[0001] The disclosure relates to crankshaft manufacturing including
laser hardening of journal surfaces of a crankshaft or a camshaft
and subsequent fillet rolling of the surfaces.
BACKGROUND
[0002] Crankshaft and camshaft manufacturing includes hardening of
a portion of their surfaces to increase their mechanical
properties. Typically, induction hardening is used to achieve the
hardening. Yet, the inherent nature of the induction process
results in numerous disadvantages such as deeper case depths than
is necessary and inherent distortion. Alternative methods have been
developed, but they are not well suited for high volume production
due to batch processing requirements.
SUMMARY
[0003] An automotive shaft fillet treating method is disclosed. The
method includes laser hardening a green machined fillet surface to
a uniform depth d to induce compressive stresses into the surface.
The surface extends the entire length l between outer edges of two
undercut regions of the fillet. The method also includes applying
additional compressive stress to the laser hardened surface via
fillet rolling such that the uniform depth d is maintained along
the entire length l during a subsequent grinding operation. The
surface may include the undercuts, crests, end regions, and a
central region of the fillet. The hardened depth d of the surface
may be about 1.0 mm. The surface may include about 80 to 100%
fillet contact area. The shaft may be a crankshaft or a camshaft.
The fillet rolling may be performed at about 5 to 15 kN. The fillet
may be a main journal, a pin journal, or a post. The subsequent
grinding operation may include remanufacturing.
[0004] In an alternative embodiment, a method of treating a fillet
is disclosed. The method includes laser hardening an
undercut-to-undercut surface of a green fillet to a uniform depth d
to induce compressive stresses uniformly into the surface. The
method further includes applying additional compressive stress to
the laser hardened surface via fillet rolling such that the uniform
depth d is maintained along the entire surface. The surface may
include the undercuts, crests, end regions, and a central region of
the fillet. The uniform depth d of the surface may be about 1.0 mm.
The surface may include about 80 to 100% of fillet contact area.
The shaft may be a crankshaft or a camshaft. The fillet rolling may
be performed at about 5 to 15 kN. The fillet may be a main journal,
a pin journal, or a post. The uniform depth d may be maintained
along the entire surface during subsequent operation(s).
[0005] In a yet alternative embodiment, a shaft fillet is
disclosed. The shaft includes an undercut-to-undercut surface area
defined by and between outer edges of two undercut regions of the
fillet, an entirety of the surface area being laser hardened to a
uniform depth d to form a layer containing hardened portions
configured to receive additional compressive stress via fillet
rolling without fracture. The depth d may be about 1.0 mm. The
fillet may be a main journal, a pin journal, or a post. The surface
area may include the undercuts, crests, end regions, and a central
region of the fillet.
BRIEF DESCRIPTION OF THE DRAWINGS
[0006] FIG. 1 depicts a schematic view of an example vehicle
combustion engine including a crankshaft and a camshaft in
accordance with one or more embodiments;
[0007] FIG. 2 depicts a perspective view of a laser hardened
crankshaft;
[0008] FIG. 3 depicts a perspective view of a laser hardened
camshaft;
[0009] FIG. 4A depicts a schematic cross-sectional view of a laser
hardened main journal of the crankshaft depicted in FIG. 2, the
journal surface area having a case depth of less than about 1
mm;
[0010] FIG. 4B depicts a schematic cross-sectional view of a laser
hardened main journal of a prior art crankshaft, the journal
surface area having a case depth of about 1.2 mm;
[0011] FIG. 4C depicts a schematic cross-sectional view of an
induction hardened main journal of a prior art crankshaft, the
journal surface area having a case depth of about 2.5 mm;
[0012] FIG. 5 depicts a perspective view of a laser hardened
portion of a crankshaft depicted in FIG. 2;
[0013] FIG. 6 depicts a perspective view of an induction hardened
portion of a prior art crankshaft having induction hardened
surfaces; and
[0014] FIG. 7 depicts a schematic cross-sectional view of a laser
hardened main journal, prepared for fillet rolling, of the
crankshaft depicted in FIG. 2, the laser hardened surface extending
the entire length between two outer edges of two undercut
region.
DETAILED DESCRIPTION
[0015] Embodiments of the present disclosure are described herein.
It is to be understood, however, that the disclosed embodiments are
merely examples, and other embodiments may take various and
alternative forms. The figures are not necessarily to scale; some
features could be exaggerated or minimized to show details of
particular components. Therefore, specific structural and
functional details disclosed herein are not to be interpreted as
limiting, but merely as a representative basis for teaching one
skilled in the art to variously employ the present invention. As
those of ordinary skill in the art will understand, various
features illustrated and described with reference to any one of the
figures may be combined with features illustrated in one or more
other figures to produce embodiments that are not explicitly
illustrated or described. The combinations of features illustrated
provide representative embodiments for typical applications.
Various combinations and modifications of the features consistent
with the teachings of this disclosure, however, could be desired
for particular applications or implementations.
[0016] Except where expressly indicated, all numerical quantities
in this description indicating dimensions or material properties
are to be understood as modified by the word "about" in describing
the broadest scope of the present disclosure.
[0017] The first definition of an acronym or other abbreviation
applies to all subsequent uses herein of the same abbreviation and
applies mutatis mutandis to normal grammatical variations of the
initially defined abbreviation. Unless expressly stated to the
contrary, measurement of a property is determined by the same
technique as previously or later referenced for the same
property.
[0018] Crankshafts and camshafts are fundamental features in an
automotive engine. FIG. 1 depicts a schematic view of an exemplary
crankshaft 10 and camshaft 12 as internal portions of a combustion
engine 14. A crankshaft 10 is a mechanical part able to perform a
conversion between reciprocating motion and rotational motion. In
an internal combustion engine 14 of a vehicle, a crankshaft 10
translates reciprocating motion of the pistons 16 into rotational
motion which enables the wheels to drive a vehicle forward. The
crankshaft 10 may be any crankshaft 10 within the cylinder block or
in the cylinder head. The crankshaft 10 is connected to a flywheel
18, an engine block (not depicted) using bearings on a number of
main journals 20, and to the pistons 16 via their respective rods
22 so that all pistons 16 of an engine 14 are attached to the
crankshaft 10. The crankshaft 10 regulates the movement of pistons
16 as it moves the pistons 16 up and down inside the cylinders (not
depicted). The crankshaft 10 has a linear axis 24 about which it
rotates, typically with several bearing journals 20 riding on
replaceable bearings held in the engine block (not depicted).
[0019] FIG. 1 further illustrates an exemplary camshaft 12. The
camshaft 12 may be any camshaft 12 within the cylinder block or in
the cylinder head. A camshaft 12 is used to operate valves 26 of
internal combustion engines with pistons 16. It consists of a
cylindrical rod 28 running the length of the cylinder bank (not
depicted) and a number of lobes 30 protruding from it, one for each
valve 26. The lobes 30 force the valves 26 open by pressing on the
valve 26 as they rotate. The camshaft 12 is linked to the
crankshaft 10. As the crankshaft 10 rotates, the camshaft 12
rotates along with it in a synchronized movement.
[0020] Crankshafts 10 and camshafts 12 can be monolithic or
assembled from several pieces. Typically, these shafts 32 are
forged from a steel bar through roll forging or casting in iron.
The manufacturing process includes a number of steps, typically up
to 25 operations including rough machining of the crankshaft,
hardening, grinding or turning, and polishing. Most steel shafts 32
have induction hardened journal surfaces to increase their
mechanical properties. Some high volume automotive and most high
performance shafts use a more costly nitride process. Carburization
and flame hardening are other exemplary methods of hardening. Yet,
all of these technologies present a number of disadvantages, some
of which are discussed below.
[0021] Induction hardening process has inherent drawbacks with
respect to journal surface area coverage as induction hardening
causes pattern proliferation and overheating of certain regions due
to the nature of the inductive field. Difficulty of managing the
physics of an induction field lie in applying it to desired regions
while avoiding undesired regions. The current flow around oil holes
during the induction hardening process typically causes bulging and
necking conditions. Additionally, axial locating of inductors is
often problematic. Coils and recipes must be designed to prevent
both metallurgical damage in the chamfer area and pattern
infringement into undercuts. These factors typically result in
compromises with respect to hardness, surface coverage, and width
of the surface hardening pattern. To obtain a higher percentage of
surface coverage, a change in the journal design to a tangential
journal design has been proposed. Yet, the design change still
results in additional manufacturing compromises related to grinding
and polishing.
[0022] Additionally, the typical case hardening methods induce
distortion of the shaft. For example, induction hardening causes 50
to 70 .mu.m distortion or more in the shaft axis. Therefore, it is
customary that the amount of material removed in the finishing
operation and process positioning errors be accounted for and added
to the desired finish case depth. This requires that the hardening
case depth be increased which may be accomplished by increasing
heat time and/or power supply current. High frequency induction
hardening typically produces a case depth of about 1.5 mm to 3 mm
which represents an adequate case depth and enables remanufacturing
without subsequent retreating. Yet, the product requires grinding
after treating. Thus, the typical case depth before grinding is
about 1.5 mm to 3 mm, but the case depth of an induction-hardened
crankshaft or camshaft in a finished state is not less than 0.5 mm.
Shallower case depths are difficult to achieve with the induction
process due to the level of manageable field strength and quench
control.
[0023] Furthermore, the finishing process results in a relative
increase in residual tensile stresses. To avoid tensile stresses,
lower productivity grind cycles must be employed. To measure
absolute stress, costly and time-consuming X-Ray diffraction must
be utilized. Despite these efforts, the grind-harden sequence
always results in some loss of desirable compressive stress.
Compressive residual stress in the journal surfaces helps prevent
cracks from forming and is generally good for fatigue
properties.
[0024] The typical hardening methods present additional drawbacks.
For example, coils are used for induction hardening. These copper
coils have to be changed any time a new geometry on a journal is
introduced. Coils are perishable tooling and must be regularly
replaced or reworked from cycling damage. Such change is very
costly and time consuming. Furthermore, a quench fluid and high
electromagnetic field used during induction hardening present
environmental and health challenges.
[0025] Nitriding has a number of disadvantages as well. For
example, it is a relatively time consuming process, taking at least
8 hours. Additionally, the resulting depth of the hardened surface
is relatively shallow, about 0.01 mm to 0.015 mm after a minimum of
an 8-hour-long process, and the shaft has to be retreated if it is
ever reground for service. While deeper depths can be obtained via
nitriding, substantially longer time is required to achieve the
depths deeper than 0.015 mm. The maximum case depth is limited to
about 0.5 mm, and time to achieve this depth is about 120 hours
which renders this method impractical for high volume applications.
Nitriding also produces an undesirable white layer on the surface
of the shaft, requiring removal by polishing of the surface after
processing.
[0026] Additionally still, crankshaft fatigue strength in journals
has traditionally been improved by increasing journal compressive
stress via rolling or the above-mentioned induction
hardening/nitriding. Yet, a combination of both methods is
traditionally not used because the induction hardened martensitic
microstructure is brittle, even in a tempered state, prone to
cracking, especially when subsequent mechanical fillet rolling
loads are applied.
[0027] If both fillet rolling and induction hardening is employed,
high fracture rates are observed. Further still, straightening
capabilities after the rolling process, which is normally performed
in the fillet rolling machine after soft rolling, is generally
omitted, and higher grind stock levels must be employed to
accommodate heat treat shaft distortion. The potential fracture
zones coincide with peak stress areas within the crankshaft when in
operation, which may lead to crankshaft or engine fatigue failure.
To prevent such event, all of such crankshafts require checking
with magnetic particle inspection (MPI), which presents a labor and
time intensive process with subjective results and only 80%
effectiveness due to the required human element.
[0028] Therefore, it would be desirable to provide a method of
shaft surface hardening which would overcome one or more
limitations of the previously devised manufacturing methods. It
would be desirable to provide a low-distortion hardening method
which would increase the overall hardened journal surface area,
allow for wider surface hardening pattern of journal surfaces, and
eliminate necking as well as the need to grind out the distortions
which occur during the induction hardening process. Additionally,
it would be desirable to develop a hardening method which would
eliminate the soft zone around the oil hole on a journal.
Additionally still, it would be desirable to provide a flexible
hardening method which would result in cost and time savings,
reduce cycle time, eliminate the need for finish grind stock from
the total case depth, eliminate copper coil tooling, and increase
environmental safety by eliminating quench fluid and high
electromagnetic field. It would also be desirable to further
increase fatigue strength, provide a more uniform case depth across
the journal surface, and simplify the case pattern inspection
process.
[0029] Laser hardening represents an alternative method of
hardening precision journal surfaces for enhanced wear properties.
Yet, the current laser methods have focused on replication of
induction patterns and case depths. The laser maximum case depth is
limited by metallurgical surface damage caused by overheating.
Thus, the laser-hardened case depth prior to grind on a typical
laser-hardened crankshaft is about 1.2 mm. Unlike
induction-hardened case depths, laser-hardened minimal case depths
can be achieved without risk. At maximum depth of about 1.2 mm,
overheating of the undercut regions dictates the width of the
hardening pattern with respect to crankshaft fatigue requirements
and limits the hardening pattern to up to about 85% of the journal
surface area.
[0030] It has now been surprisingly discovered that the minimum
case depth requirements may be reduced below 1.2 mm while
delivering satisfactory wear properties, enabling refurbishment or
regrinding of the components without retreatment, and maximizing
throughput with the laser hardening process. Additionally, since
the case depth of the laser hardening process affects processing
time, lowering the case depth requirements significantly reduces
cycle time by up to 50% or more.
[0031] According to one or more embodiments, a method is provided
which includes subjecting a shaft 10, 12 to laser hardening,
specifically, laser hardening one or more surface areas of a shaft
10, 12. FIGS. 2 and 3 depict non-limiting examples of a crankshaft
10 and a camshaft 12, respectively. Each shaft 10, 12 includes one
or more surfaces 34 to be hardened which form a band 35 around a
perimeter of the journal. FIG. 2 depicts an exemplary crankshaft 10
having a post 36 at the first end 38, main journals 20, and pin/rod
journals 40 connected to a plurality of counterweights or bearings
42 via undercut regions (not depicted), and a flywheel 18 at the
second end 44. The main journals 20, also called the main bearing
journals or fillets, include an oil hole 46 which serves for
distribution of lubricating oil to the bearings. The pin journals
40, also known as crankpins or crankpin fillets, also include an
oil hole 46. The crankshaft 10 further includes oil ducts
facilitating lubrication, which are not depicted. The crankshaft 10
may further include an oil seal 48 located on the flywheel 18. FIG.
3 depicts a non-limiting example of a camshaft 12 having a
cylindrical rod 28, a plurality of main journals 20, and a
plurality of lobes 30.
[0032] As is depicted in FIGS. 2 and 3, the one or more surfaces 34
to be hardened may include a surface on a main journal 20, a pin
journal 40, an oil seal 48, a lobe 30, or a running surface 62. The
number of main journals 20, pin journals 40, oil seals 48, lobes
30, and their respective surfaces to be hardened may differ and
depend on the desirable parameters of the shaft 32 which is being
manufactured. A running surface 62 may be any cylindrical or
shouldered surface or any surface in contact with a journal such as
a bushing surface 64 or a shouldered wall surface 66.
[0033] The method may include a step of generating a surface
hardening pattern from a 3-D model of the shaft 32 to be laser
hardened. The method may include a step of programming a
microprocessor unit (MPU) to generate the surface hardening
pattern. In one or more embodiments, the generated surface
hardening pattern may include a series of preselected points, a
portion of, or the entire surface geometry of the shaft 10, 12. The
surface hardening pattern may include one or more surfaces 34 on
one or more main journals 20, pin journals 40, lobes 30, oil seals
48, or running surfaces 62.
[0034] The method may include determining dimensions of the surface
area to be hardened. The method may include a step of adjusting a
spot size of the laser beam according to the dimensions of the
surface area to be hardened, specifically the depth and width of
the surface area to be hardened 34. The method may include a step
of directing a laser beam from the laser power unit to the surface
34 of the shaft 10, 12 to be laser hardened according to the
surface hardening pattern. The method may include adjusting one or
more parameters of the surface hardening pattern before and/or
during the laser hardening operation.
[0035] In one or more embodiments, the laser hardening may be
facilitated by at least one laser power unit. A plurality of laser
power units may be utilized. For example, one laser power unit may
be used for tempering the surfaces 34 to be hardened. Such laser
could be a lower power laser such as a 1.0 kW laser. The second
laser power unit could be a high power laser unit facilitating the
hardening. The high power unit could be, for example, a 6.0 kW
laser. A laser power unit having a different power may be used, for
example any laser having power ranging from 500 W to 50 kW may be
suitable. Alternatively, both tempering and hardening may be
facilitated by one laser power unit. Alternatively still, tempering
may be omitted because the laser microstructure is less than 100%
martensitic. The temperature to be achieved during the hardening
process should not exceed about 1260.degree. C. to prevent
overheating of the shaft material.
[0036] The method contemplates using different types of lasers as
the heat source for the hardening operation. Exemplary non-limiting
examples of suitable lasers include lasers having different types
of active gain media. The gain media may include liquid such as dye
lasers in which the chemical make-up of the dye determines the
operational wavelength. The liquids may be organic chemical solvent
such as methanol, ethanol, and ethylene glycol containing a dye
such as coumarin, rhodamine, and fluorescein. The gain media may
include gas such as CO.sub.2, Ar, Kr, and/or gas mixtures such as
He--Ne. The gain medium may be metal vapor such as Cu, HeCd, HeHg,
HeSe, HeAg, or Au. The gain media may include solids such as
crystals and glass, usually doped with an impurity such as Cr, Nd,
Er, or Ti ions. The solid crystals may include YAG (yttrium
aluminum garnet), YLF (yttrium lithium fluoride), LiSAF (lithium
strontium aluminum fluoride), or sapphire (aluminum oxide).
Non-limiting examples of solid-state gain media doped with an
impurity include Nd:YAG, Cr:sapphire, Cr:LiSAF, Er:YLF, Nd:glass,
or Er:glass. The gain medium may include semiconductors having a
uniform dopant distribution or a material with differing dopant
levels in which the movement of electrons causes laser action.
Non-limiting examples of semiconductor gain media may include
InGaAs, GaN, InGaN, and InGaAsP. The laser may be a high power
fiber laser created from active optical fibers doped with rare
earth ions and semiconductor diodes as the light source to pump the
active fibers.
[0037] The at least one laser power unit may be connected to the
MPU also known as a central processing unit capable of accepting
digital data as input, processing the data according to
instructions stored in its memory, and providing output. The MPU
may include mathematical modeling software which is capable of
processing input data. Exemplary input data may include information
about a 3-D model of a shaft 32 having surfaces 34 to be hardened;
parameters for new geometry such as hardening width, energy
balance, or the like; parameters relating to oil holes such as the
oil hole radius, offset from the center of a journal, or the
like.
[0038] The method implements laser hardening into the depth of less
than 1.2 mm, 1.0 mm, 0.8 mm, or 0.5 mm. At these depths as well as
at deeper case depths, distortion of the main journals 20 is only
minimal in comparison with induction hardening. The distortion of
the main journals 20 caused by laser hardening may be about 5 .mu.m
to 10 .mu.m. In comparison, an induction-hardened shaft may feature
about 50 .mu.m to 70 .mu.m distortion or more on the main journals.
Therefore, the laser hardening process distortion levels even at
deeper depths are such that heat-related distortion is manageable.
The laser-hardened case depth can be reduced to less than about 1
mm also because accounting for grinding stock to compensate for
induction hardening distortions is no longer necessary. This in
turn enables significantly shorter cycle time. Increasing scan
speeds at the same or lower power levels can achieve hardening
shallower case depths in a shorter time.
[0039] The method may include hardening one or more surfaces 34 to
the case depth of about 0.05 mm to 1.1 mm, 0.15 mm to 0.8 mm, or
0.2 mm to 0.5 mm. For example, if the requirements of the final
product are 0.2 mm, hardening may be done to the depth of 0.6 mm to
0.7 mm. Laser hardening may save up to 50% of cycle time associated
with hardening of a shaft 32 that requires a hardening depth of
more than about 1.2 mm. Hardening shallower than about 0.5 mm
contributes to even shorter cycle time as less time is required for
scanning and applying heat to the surfaces 34. Unlike the prior art
shafts, the laser hardened shaft 32 of the present disclosure may
be reground and/or remanufactured without repeating the hardening
operation even if the case depth is only about 0.2 mm.
[0040] The shallow case depth of less than about 1 mm enables wider
laser hardening pattern than the patterns achievable while
implementing case depth deeper than about 1.2 mm. The pattern may
expand closer to the edges of the surfaces 34 or reach the very
edges of the surfaces 34. The wider pattern may include up to 100%
surface area of the one or more surfaces 34 to be laser hardened
such that the band 35 does not contain any unhardened portions 58.
The wider pattern includes more than 80%, 85%, 90%, 95%, or 99% of
the one or more surfaces 34 to be laser hardened and/or of the band
35. As can be seen in FIG. 4A, which depicts a profile of an
exemplary journal contact surface which is laser hardened 34 having
a shallow case depth of less than about 1 mm, the laser hardened
area extends from crest 68 to crest 68' which is defined by two
undercut regions 50.
[0041] In comparison, only up to 80% of a journal surface area 134
having a depth of about 1.2 mm may be laser hardened, as FIG. 4B
illustrates. Laser hardening a wider pattern to the depth of about
1.2 mm could jeopardize the journal strength as it could induce
conditions which generate risk to subsequent fillet rolling
operations and/or negatively impact the undercut regions 50 by
overheating. The laser hardened layer 152 depicted in FIG. 4B does
not reach the crests 168, 168'. And only up to 85% of a journal
surface area 234, depicted in FIG. 4C, having a case depth of about
2.5 mm and being hardened by an induction process may be hardened.
Just as the layer 152 in FIG. 4B, the laser hardened layer 252,
illustrated in FIG. 4C, is not wide enough to extend across the
entire distance between the crests 268 and 268' defined by the
undercut regions 250. Specifically, clamshell induction hardening
may achieve hardening of only up to 75% surface area and orbital
induction hardening up to 85% surface area. Thus, providing shallow
case depth laser hardening enables a significantly wider surface
hardening pattern. The unhardened areas are depicted in FIGS. 4B
and 4C as 158 and 258, respectively.
[0042] A perspective view of a journal 20 having near-100% journal
surface area laser-hardened is depicted in FIG. 5. As FIG. 5
illustrates, the laser-hardened journal 20 of a shaft 32 may
include a hardened surface area 52 directly adjacent to the edge 54
of the oil hole 46 and extending between crests 68, 68' defining
edges 56 of the undercut regions 50. The oil hole 46 and the
undercut regions 50 are free from metallurgical transformation. The
surface area of the oil hole 46 and the undercut regions 50 thus
remain completely unhardened.
[0043] In contrast, a clamshell induction-hardened journal 220 is
depicted in FIG. 6. The hardened surface area 252 on the journal
240 does not include the area adjacent to the oil hole 246 and the
area adjacent to the undercut regions 250. The journal 220 of FIG.
6 thus includes non-hardened areas 258 which remain soft. The
dimensions of the soft area 258 around the oil hole 246 may reach
up to 2-3 mm radially around the oil hole 246. The soft area 258
contributes to undesirable fatigue stress and lower bearing seizure
resistance. Additionally, induction hardening of the acute side of
the oil hole 246 presents other challenges such as difficulty in
preventing overheating of the cross sectional area of the oil hole
246. Such overheating induces damage which in turn affects fatigue
strength. Adjusting the induction hardening process to alleviate
overheating would in turn result in a compromised level of hardness
or soft spots 258. Additionally, traditional induction hardening
may affect the surface area of the oil hole 246 and/or the area of
the undercut regions 250 such that the areas 246 and/or 250 are
heat-affected and subjected to undesirable metallurgical
changes.
[0044] As can be further seen in FIG. 6, induction hardening causes
necking or narrowing of the induction pattern as the current flows
around the oil hole 246 and/or the undercut regions 250. The
absence of ferrous volume around the oil hole 246 and the undercut
regions 250 results in higher current flow, resulting in bulging of
the pattern at the oil hole 246 and around the undercut regions
250. To avoid necking, induction coil design and/or the amount of
current has to be adjusted as necking presents a fatigue stress
concern. Yet, when the coil design and/or current are reduced, the
area near the oil hole 246 and the undercut regions 250 results in
a narrower, necked, pattern. In contrast, due to the nature,
flexibility, and precision of laser hardening, the laser-hardened
journal 20 is free of necking, as FIG. 5 illustrates.
[0045] Referring back to FIGS. 4A-4C, it can be seen that the laser
hardened layer 52 in FIG. 4A features different dimensions and a
shape of the profile than the hardened layers 152 and 252 depicted
in FIGS. 4B and 4C, respectively. The laser hardened layer 52 in
FIG. 4A includes a central region 70 and end regions 72. The layer
52 has a length l.sub.1, the distance between crests 68 and 68' is
designated as length l.sub.2. l.sub.1 may equal l.sub.2 in at least
a portion of the layer 52 such as the very top portion at the
journal surface 34. As a result, the crest-to-crest contact surface
area does not contain any unhardened portions. Alternatively,
l.sub.1 may equal l.sub.2 throughout the entire depth of the layer
52, or at least in 50%, 60%, 70%, 80%, 90% or more of the depth of
the layer 52.
[0046] The layer 52 may be about 1 mm or less deep, as was
described above. The central region 70 may have a depth d.sub.c,
which may be substantially the same or constant throughout the
entire central region 70. The end regions 72 of the layer 52 may
have the same or different depth d.sub.e than the depth of the
central region 70 d.sub.c. The depth d.sub.c may equal or be
greater than d.sub.e. The depth d.sub.e of the end regions 72
depends on the shape of the end regions 72. The end regions 72 may
have a substantially square pattern or rounded shape. Other shapes
are contemplated. For example, if the shape of the end regions 72
is substantially square, the depth d.sub.e may be the same or
substantially similar as the depth d.sub.c. The depth of the layer
52 may thus be constant or substantially the same in about 70%,
72%, 74%, 76%, 78%, 80%, 84%, 86%, 88%, 90%, 92%, 94%, 96% or more
of the layer 52.
[0047] Unlike the layer 52, the laser hardened layer 152 depicted
in FIG. 4B has a depth greater than 1 mm, specifically about 1.2
mm, as was referenced above. The end regions 172 do not have a
substantially square profile and feature a triangular shape or
rounded shape. Thus, the depth d.sub.e varies throughout the end
regions 172 and is not substantially the same as the depth d.sub.c
in the central region 170. The depth in the central region d.sub.c
is greater than the depth in the end regions d.sub.e. Due to the
varying depth of the end regions 172, the depth of the layer 152
may be the same in up to about 65% of the layer 152. The length
l.sub.1 of the hardened layer 152 is smaller than the distance
between crests 168 and 168' designated as length l.sub.2 such that
soft or unhardened portions 58 remain between the layer 152 and the
undercut regions 150.
[0048] Likewise, the profile of the induction-hardened surface 252
differs from the profile of the layer 52 as the layer 252 typically
displays irregularities such as protrusions or peaks 269 and a
central concave region 270. The depth of the layer 252 thus differs
throughout the layer 252. Specifically, the depth d.sub.c within
the central region 270 is smaller than the depth d outside of the
central region due to concavity which is inherent with the
induction process. Additionally, the end regions 272 are rounded,
may feature a shape of a triangle, or both and do not feature a
square pattern. The depth of the end regions 272 d.sub.e differs
throughout the end regions 272. The depth d.sub.e is smaller than
the depth d, and may be smaller or greater than d.sub.c. The depth
of the layer 252 may be about 2.5 mm to 3 mm or greater prior to
grinding, as was explained above. Due to the varying depth of the
end regions 172, the central region 270, and the irregularities in
the region outside of the central region 270, the depth of the
layer 252 may be substantially the same in only up to about 55% of
the layer 252. The length l.sub.1 of the layer 252 is smaller than
the distance between crests 268 and 268' designated as length
l.sub.2 such that unhardened portions 58 remain between the layer
252 and the undercut regions 250.
[0049] The journal profile may be straight or crown or
barrel-shaped, thus non-straight. Straightness relates to a profile
being uniformly level/straight with no defined barrel shape. The
crown profile may have a relatively large radius or a prescribed
level of barrel defined by about 1.5 .mu.m to 3 .mu.m radially. The
barrel-shape relates to a convex shape. An hourglass or concave
shape is not desirable as it may result in isolated peak loading of
the journals. The barrel-shape may be added to accommodate, for
example, cylinder block bulkhead deflections or a crankshaft
deflection due to firing loads which may effectively close the
crank pins, resulting in undesirable pin-loading of main journals
20. Whether the profile shape is straight or barrel-shaped,
consistent profile is required. While an induction process must use
a narrower pattern or abandon the fillet rolling and straightening
method, the laser method can harden a band 35 closer to the
undercuts 50, the unhardened area 58 is reduced, and subsequent
profile is more uniform when compared to the induction hardened
profile. The laser method also allows utilization of the fillet
rolling which results in straightening shafts more readily and
lowers grind stock levels while also providing near-100% hardened
journal area 52 while increasing the effective bearing width.
[0050] The difference between the profiles depicted in FIGS. 4A-4C
may be also expressed as the rate of change of the profile. The
rate of change may be defined as .mu.m of change in a length. Since
the irregularities in the profile such as the afore-mentioned peaks
269 and the concavity in the central region 270 may result in
journal failure, elimination of the irregularities and concavity is
a goal. A straighter profile, or a profile with lower rate of
change of the profile, provides more contact surface area to
provide bearing support which translates into an increased lifetime
of the journal. The induction-hardened layer 252 typically has the
rate of change of about 1 .mu.m in 2-3 mm. Utilizing the method
disclosed herein, a rate of change of 1 .mu.m in 2 mm or less may
be achieved. Laser hardening thus enables a higher degree of
control over straightness of the profile and/or profile uniformity
than induction hardening.
[0051] The rate of change and straightness of the laser
heat-treated surfaces on the main journals 20 of a crankshaft were
measured via an Adcole High-Speed Crankshaft Gage measuring machine
manufactured by the Adcole Corporation. The machine provides
robot-fed 100% crankshaft inspection having submicron accuracy and
presents a recognized standard in camshaft and crankshaft gauging.
The results are provided in Table 1 below. The induction hardened
surfaces on the main journals 220 of an induction-hardened
crankshaft were obtained using the same machine, results of which
are referenced in Table 2 below. Comparison of the data in both
tables shows that the average straightness achievable by the laser
heat treatment is nearly 50% better than straightness attainable
via an induction process.
TABLE-US-00001 TABLE 1 Straightness of main journal laser hardened
surfaces on a laser hardened crankshaft Main journal 1 Main journal
2 Main journal 3 Main journal 4 Average Crankshaft straightness
straightness straightness straightness straightness no. [.mu.m]
[.mu.m] [.mu.m] [.mu.m] [.mu.m] 1 1.4 1.9 1.9 1.3 1.6 2 1.2 1.8 1.7
1.7 1.6 3 1.2 1.8 1.4 1.5 1.5 4 1.0 1.9 1.6 1.8 1.6 5 1.1 1.5 1.5
2.0 1.5 6 1.4 1.2 0.7 1.2 1.1 7 1.6 1.5 0.8 1.5 1.4 8 0.9 1.2 0.9
2.0 1.3 9 1.1 1.3 1.1 1.8 1.3 10 1.4 1.9 1.0 1.5 1.5
TABLE-US-00002 TABLE 2 Straightness of main journal induction
hardened surfaces on an induction hardened crankshaft Main journal
1 Main journal 2 Main journal 3 Main journal 4 Average Crankshaft
straightness straightness straightness straightness straightness
no. [.mu.m] [.mu.m] [.mu.m] [.mu.m] [.mu.m] 1 1.6 2.3 2.4 2.1 2.1 2
2.1 2.7 3.2 2.5 2.6 3 2.1 2.6 3.5 2.2 2.6 4 1.9 2.9 2.7 2.6 2.5 5
2.7 2.9 3.5 2.6 2.9 6 2.1 2.4 3.6 3.1 2.8 7 1.6 2.2 2.1 1.8 1.9 8
1.8 2.0 2.4 2.0 2.1 9 2.0 2.2 2.3 2.1 2.2 10 1.9 2.1 2.4 2.0
2.1
[0052] Due to advantages mentioned above, laser hardening may be
applied when it is desirable to harden all of the journal surfaces
except the undercut region 50, the oil hole 46, or a combination
thereof. Thus, crankshafts 10 which require seal surface hardening
may be processed via laser hardening as well. The method may be
likewise applied to camshafts 12. One of the advantages of
laser-hardening camshaft 12 surfaces such as main/cam journals 20
or lobes 30 is limiting overheating of these surfaces which may
typically have a tendency to overheat due to a lack of heat sink.
Thus, a narrow hardening pattern typical for the cam journals 20
and lobes 30 could be widened up to about 80%, 90%, or 100% of cam
journal surface or lobe surface while preventing metallurgical
damage to the surfaces.
[0053] In one or more embodiments, the method may include
additional manufacturing steps after the shaft 32 is laser
hardened. In at least one embodiment, the method may include
polishing. Polishing may include any conventional method of
polishing of a metal surface of a laser hardened shaft 32. The
method may include removal of certain amount of material stock.
[0054] Additionally still, the above-described method may provide a
consistent, near-100% hardened journal surface area while ensuring
no infringement into the undercut fatigue zone 50 which otherwise
poses reliability risk. The method also presents an additional
advantage over induction hardened tangential fillet designs.
[0055] In one or more embodiments, the laser process described
above may utilize fillet rolling, which enables straightening of
the shaft 32 before grinding such that the grind stock may be
reduced. Thus, utilization of the laser technique and fillet
rolling offers up to 100% hardened journal surface and roll
straightening. On the other hand, to achieve a maximum achievable
hardening pattern with induction hardening, additional grind stock
must be added due to greater distortion. Additionally, as was
stated above, an induction hardened journals with undercuts in
combination with fillet rolling may lead to crankshaft failure such
as a cracked crankshaft and low fillet rolling tool life.
[0056] Fillet rolling or deep rolling is a radially symmetrical
deformation process which may be used for surface finish, hardness,
and/or residual stress control. Fillet rolling may be used to
strengthen journal fillets. In one or more embodiments, a method of
treating a shaft fillet via laser hardening and subsequent fillet
rolling is disclosed. The method includes laser hardening a fillet
surface, depicted in FIG. 7, to a depth d to induce compressive
stresses into the surface. The surface may be a green fillet
surface. The surface may be a green machined surface. The depth d
may equal the depth d.sub.c as depicted in FIG. 4A. Unlike in FIG.
4A, the laser-hardened surface or layer 352 does not extend just
crest-to-crest 368-368', but the laser-hardened surface or layer
352 extends the entire length l between outer edges 353 of two
undercut regions 350 of the journal 320. The laser-hardened surface
352 is thus inclusive of both undercuts 350, both crests 368', both
end regions 372, and the central region 370. The surface may
include about 80 to 100% fillet contact area. The surface 352 may
include about 70, 80, 85, 90, 95, 98, 100% of the journal area.
[0057] The depth d or d.sub.c, as depicted in FIG. 7 may be
uniform, substantially the same or constant in the entire layer
352. Alternatively, the depth may vary such that the depth at the
outer edges 353 may be smaller than the depth in the central region
370, at the end regions 372, at the lowest point of the undercut
region 350, or a combination thereof. The layer 352 substantially
follows the shape of the central region 370, the end regions 352,
and the undercut region 350. The depth of the layer 352 may thus be
constant or substantially the same in about 70%, 72%, 74%, 76%,
78%, 80%, 84%, 86%, 88%, 90%, 92%, 94%, 96% or more of the layer
352. The depth d.sub.c in FIG. 7 may be about 0.8 mm to 1.0 mm. The
depth d.sub.c in FIG. 7 may also be about 1.25-1.5 mm.
[0058] The method further includes fillet rolling or deep rolling
to apply additional compressive stress to the laser-hardened
surface 352. The fillet rolling is performed in such a way that the
depth d or d.sub.c, as depicted in FIG. 7, is maintained along the
entire length l. The depth d may be maintained during a subsequent
operation such as grinding or remanufacturing.
[0059] The fillet rolling may follow immediately after
laser-hardening of the journal surface. Alternatively, the fillet
rolling may follow after another operation such as polishing.
[0060] The combined laser hardening and fillet rolling enables a
more uniform case depth across the journal surface and simplifies
the case pattern inspection process because the entire width or
length l between journal collars or the outer edges 353 of the
undercut regions 350 may be hardened.
[0061] Without limiting the disclosure to a single theory, the
combined method yield success because the laser hardening does not
generate a fully martensitic structure as the phase transformation
in the journals is captured via air quenching instead. Yet, the
laser hardening provides sufficient increase in
hardness/compression strength to meet the desired levels for
bearing journal seizure resistance. Thus, the microstructure
produced by the laser hardening process in the fillet areas enables
increased fillet rolling loads which may be applied onto the
laser-treated surface of the journal in comparison with fillets
which were unhardened and subsequently rolled or hardened by
traditional methods such as induction hardening and subsequently
rolled.
[0062] Typically, unhardened or induction-hardened fillet rolling
loads are limited by material displacement or roller penetration,
which when exceeded, may result in skidding or failure of the
roller. For example, induction-hardened fillets, having martensitic
microstructure, being rolled may be very susceptible to fracture
and distortion at the load of about 10 to 12 kN.
[0063] But laser-hardening of the fillet area provides a
sufficiently strong, hardened, but not brittle surface or layer
having a mixed microstructure, which is not subject to fracture,
but which reduces material displacement. The combination of these
properties allows increase of fillet rolling loads. Thus, while the
fillet rolling load is specific to a specific application and
depends on various factors such as fatigue requirements, parent
material type, roller radius, roller size, and angle, example
fillet rolling loads for the herein-disclosed laser-hardened
fillets/journals may be about 5 to 15 kN, 8 to 14 kN, or 10 to 12
kN. The fillet rolling may be performed at the loads of, for
example, about 10 to 15 kN or 11 to 15 kN.
[0064] The higher rolling loads result in higher level of
compression. The greater compressive stress applied via fillet
rolling onto the fillet laser-hardened areas results in improved
fatigue strength. The improved fatigue strength, in turn, helps
avoid a change in the base material alloy, which may prevent
increase in raw material cost and productivity loss due to
machinability.
[0065] The method also enables a wider case pattern, yielding
greater hardened journal bearing surface area, as case depth may
remain uniform through the journal 370 from one outer edge 353 of
the first undercut region 350 to the outer edge 353 of the second
undercut region 350. As a result, there may be no loss in
length/width l of the treated area after subsequent operation or
operations such as grinding, regrinding, remanufacturing, and/or
undersize grinding as the pattern transition remains outside of the
ground zone. This presents an advantage for both initial and
subsequent remanufacture grinding operations.
[0066] Additional advantages of the disclosed method thus lie in
achieving higher fillet compressive stress levels while preserving
the ability to straighten without fracture and avoiding additional
grind stock on journals to accommodate distortion. Risk of fracture
is greatly reduced, compared to rolled fillets which were
previously hardened by traditional hardening methods described
above. As a result, 100% MPI is not required for the laser-hardened
fillet-rolled journals. Additionally, the case hardened pattern may
be expanded to 100% coverage of the journal, increasing overall
engine bearing load bearing capacity and seizure resistance. The
process also simplifies the manufacturing process for applying case
hardening pattern as the pattern no longer must be confined between
fillet edges or end regions 372. Since 100% of journal surface may
be hardened as migration into fillet zones is no longer a concern,
there is a greater level of seizure resistance.
[0067] The method of laser-hardening and subsequent fillet rolling
is applicable to a crankshaft, camshaft, main journals, pins
journals, posts, any portion that requires fillet rolling, or a
combination thereof. While automotive shafts and journals are
mentioned, the method likewise applies to other engine applications
such as shafts and journals for compact utility tractors,
motorcycles, and small engine harden/utility applications.
[0068] While exemplary embodiments are described above, it is not
intended that these embodiments describe all possible forms of the
disclosure. Rather, the words used in the specification are words
of description rather than limitation, and it is understood that
various changes may be made without departing from the spirit and
scope of the disclosure. Additionally, the features of various
implementing embodiments may be combined to form further
embodiments of the disclosure.
* * * * *