U.S. patent application number 15/806352 was filed with the patent office on 2019-05-09 for method and system for operating a phase-leg of a three-level active neutral point clamped converter.
The applicant listed for this patent is GENERAL ELECTRIC COMPANY. Invention is credited to Jiangbiao He, Sachin Madhusoodhanan, Di Pan, Di Zhang.
Application Number | 20190140557 15/806352 |
Document ID | / |
Family ID | 63491533 |
Filed Date | 2019-05-09 |




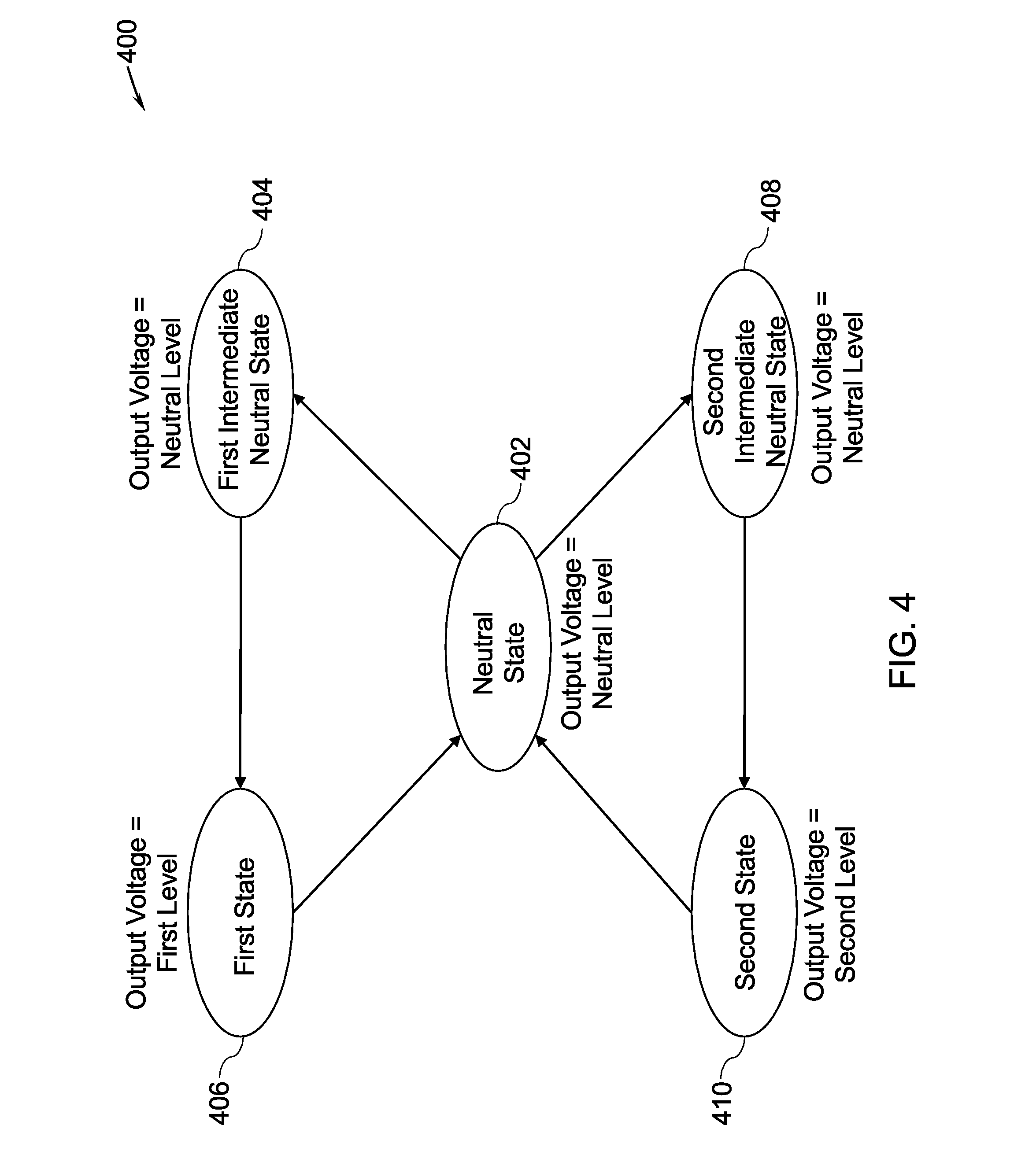




United States Patent
Application |
20190140557 |
Kind Code |
A1 |
Zhang; Di ; et al. |
May 9, 2019 |
METHOD AND SYSTEM FOR OPERATING A PHASE-LEG OF A THREE-LEVEL ACTIVE
NEUTRAL POINT CLAMPED CONVERTER
Abstract
A method for operating a phase-leg of a three-level active
neutral point clamped (3L-ANPC) converter is presented. The
phase-leg includes an output terminal, a plurality of input
terminals, and a plurality of switches disposed therebetween. The
method includes operating the phase-leg in a neutral state to
generate an output voltage having a neutral level. The method
further includes transitioning the phase-leg to a first
intermediate neutral state from the neutral state. Moreover, the
method includes transitioning the phase-leg from the first
intermediate neutral state to a first state to generate the output
voltage having a first level. A modulator for operating the
phase-leg of the 3L-ANPC converter is also presented. Moreover, a
3L-ANPC converter including the modulator is presented.
Inventors: |
Zhang; Di; (Niskayuna,
NY) ; He; Jiangbiao; (Niskayuna, NY) ;
Madhusoodhanan; Sachin; (San Jose, CA) ; Pan; Di;
(Niskayuna, NY) |
|
Applicant: |
Name |
City |
State |
Country |
Type |
GENERAL ELECTRIC COMPANY |
Schenectady |
NY |
US |
|
|
Family ID: |
63491533 |
Appl. No.: |
15/806352 |
Filed: |
November 8, 2017 |
Current U.S.
Class: |
1/1 |
Current CPC
Class: |
H02M 7/5395 20130101;
H02M 7/48 20130101; H02M 7/483 20130101; H02M 7/487 20130101 |
International
Class: |
H02M 7/5395 20060101
H02M007/5395 |
Goverment Interests
STATEMENT REGARDING FEDERALLY SPONSORED RESEARCH AND
DEVELOPMENT
[0001] This invention was made with Government support under
contract number NNC15CA29C awarded by the National Aeronautics and
Space Administration (NASA). The Government has certain rights in
the invention.
Claims
1. A method for operating a phase-leg of a three-level active
neutral point clamped converter, the phase-leg comprising an output
terminal, a plurality of input terminals, and a plurality of
switches disposed between the plurality of input terminals and the
output terminal, the method comprising: operating the phase-leg in
a neutral state to generate an output voltage having a neutral
level by operating a second switch, a third switch, a fifth switch,
and a sixth switch of the plurality of switches in a conducting
state and operating a first switch and a fourth switch of the
plurality of switches in a non-conducting state; transitioning the
phase-leg to a first intermediate neutral state from the neutral
state by operating the second switch and the fifth switch in the
conducting state and operating the first switch, the third switch,
the fourth switch, and the sixth switch in the non-conducting
state; and transitioning the phase-leg from the first intermediate
neutral state to a first state to generate the output voltage
having a first level by operating the first switch, the third
switch, and the fifth switch in the conducting state and operating
the second switch, the fourth switch, and the sixth switch in the
non-conducting state.
2. The method of claim 1, wherein the plurality of input terminals
comprises a first input terminal, a second input terminal, and a
neutral input terminal, wherein the first switch, the second
switch, the third switch, and the fourth switch of the plurality of
switches are operatively coupled in series, and wherein the first
switch is operatively coupled to the first input terminal, the
fourth switch is operatively coupled to the second input terminal,
an interconnection point of the second switch and the third switch
is operatively coupled to the neutral input terminal, the fifth
switch is operatively coupled between an interconnection point of
the first switch and the second switch and the output terminal, and
the sixth switch is operatively coupled between an interconnection
point of the third switch and the fourth switch and the output
terminal.
3. The method of claim 1, wherein the first level comprises a
positive voltage level.
4. The method of claim 1, wherein transitioning the phase-leg to
the first intermediate neutral state from the neutral state
comprises transitioning the third switch and the sixth switch to
the non-conducting state.
5. The method of claim 1, wherein transitioning the phase-leg from
the first intermediate neutral state to the first state comprises
transitioning the first switch and the third switch to the
conducting state and transitioning the second switch to the
non-conducting state.
6. The method of claim 1, further comprising transitioning the
phase-leg from the first state to the neutral state.
7. The method of claim 6, wherein transitioning the phase-leg from
the first state to the neutral state comprises: transitioning the
phase-leg from the first state to the first intermediate neutral
state; and transitioning the phase-leg from first intermediate
neutral state to the neutral state.
8. The method of claim 6, wherein transitioning the phase-leg from
the first state to the neutral state comprises transitioning the
phase-leg directly to the neutral state from the first state.
9. The method of claim 6, further comprising transitioning the
phase-leg from the neutral state to a second intermediate neutral
state, wherein transitioning the phase-leg from the neutral state
to the second intermediate neutral state comprises operating the
third switch and the sixth switch in the conducting state and
operating the first switch, the second switch, the fourth switch,
and the fifth switch in the non-conducting state.
10. The method of claim 9, wherein transitioning the phase-leg from
the neutral state to the second intermediate neutral state
comprises transitioning the second switch and the fifth switch to
the non-conducting state.
11. The method of claim 9, further comprising transitioning the
phase-leg from the second intermediate neutral state to a second
state to generate the output voltage having a second level, wherein
transitioning the phase-leg from the second intermediate neutral
state to the second state comprises operating the second switch,
the fourth switch, and the sixth switch in the conducting state and
operating the first switch, the third switch, and the fifth switch
in the non-conducting state.
12. The method of claim 11, wherein transitioning the phase-leg
from the second intermediate neutral state to the second state
comprises transitioning the second switch and the fourth switch to
the conducting state and transitioning the third switch to the
non-conducting state.
13. The method of claim 11, wherein the second level comprises a
negative voltage level.
14. The method of claim 11, further comprising transitioning the
phase-leg from the second state to the neutral state.
15. The method of claim 14, wherein transitioning the phase-leg
from the second state to the neutral state comprises: transitioning
the phase-leg from the second state to the second intermediate
neutral state; and transitioning the phase-leg from second
intermediate neutral state to the neutral state.
16. The method of claim 14, wherein transitioning the phase-leg
from the second state to the neutral state comprises transitioning
the phase-leg directly to the neutral state from the second
state.
17. A modulator for operating a phase-leg of a three-level active
neutral point clamped converter, the phase-leg comprising an output
terminal, a plurality of input terminals, and a plurality of
switches disposed between the plurality of input terminals and the
output terminal, the modulator comprising: a controller operatively
coupled to the plurality of switches and configured to: operate the
phase-leg in a neutral state to generate an output voltage having a
neutral level by operating a second switch, a third switch, a fifth
switch, and a sixth switch of the plurality of switches in a
conducting state and operating a first switch and a fourth switch
of the plurality of switches in a non-conducting state; transition
the phase-leg to a first intermediate neutral state from the
neutral state by operating the second switch and the fifth switch
in the conducting state and operating the first switch, the third
switch, the fourth switch, and the sixth switch in the
non-conducting state; and transition the phase-leg from the first
intermediate neutral state to a first state to generate the output
voltage having a first level by operating the first switch, the
third switch, and the fifth switch in the conducting state and
operating the second switch, the fourth switch, and the sixth
switch in the non-conducting state.
18. The modulator of claim 17, wherein the controller is further
configured to: transition the phase-leg from the first state to the
neutral state; transition the phase-leg from the neutral state to a
second intermediate neutral state by operating the third switch and
the sixth switch in the conducting state and operating the first
switch, the second switch, the fourth switch, and the fifth switch
in the non-conducting state; transition the phase-leg from the
second intermediate neutral state to a second state to generate the
output voltage having a second level by operating the second
switch, the fourth switch, and the sixth switch in the conducting
state and operating the first switch, the third switch, and the
fifth switch in the non-conducting state, wherein the second level
comprises a negative voltage level; and transition the phase-leg
from the second state to the neutral state.
19. The modulator of claim 18, wherein the controller is configured
to: transition the second switch and the fifth switch to the
non-conducting state to transition the phase-leg from the neutral
state to the second intermediate neutral state; and transition the
second switch and the fourth switch to the conducting state and
transition the third switch to the non-conducting state to
transition the phase-leg from the second intermediate neutral state
to the second state.
20. A three-level active neutral point clamped converter,
comprising: one or more phase-legs, wherein at least one phase-leg
of the one or more phase-legs comprises: an output terminal; a
plurality of input terminals comprising a first input terminal, a
second input terminal, and a neutral input terminal; a plurality of
switches disposed between the plurality of input terminals and the
output terminal, wherein the plurality of switches comprises a
first switch, a second switch, a third switch, a fourth switch, a
fifth switch, and a sixth switch, wherein the first switch, the
second switch, the third switch, and the fourth switch of the
plurality of switches are operatively coupled in series, and
wherein the first switch is operatively coupled to the first input
terminal, the fourth switch is operatively coupled to the second
input terminal, an interconnection point of the second switch and
the third switch is operatively coupled to the neutral input
terminal, the fifth switch is operatively coupled between an
interconnection point of the first switch and the second switch and
the output terminal, and the sixth switch is operatively coupled
between an interconnection point of the third switch and the fourth
switch and the output terminal; a modulator operatively coupled to
the plurality of switches of the one or more phase-legs and
configured to: operate the at least one phase-leg of the one or
more phase-legs in a neutral state to generate an output voltage
having a neutral level by operating the second switch, the third
switch, the fifth switch, and the sixth switch of the plurality of
switches in a conducting state and operating the first switch and
the fourth switch of the plurality of switches in a non-conducting
state; transition the at least one phase-leg of the one or more
phase-legs to a first intermediate neutral state from the neutral
state by operating the second switch and the fifth switch in the
conducting state and operating the first switch, the third switch,
the fourth switch, and the sixth switch in the non-conducting
state; and transition the at least one phase-leg of the one or more
phase-legs from the first intermediate neutral state to a first
state to generate the output voltage having a first level by
operating the first switch, the third switch, and the fifth switch
in the conducting state and operating the second switch, the fourth
switch, and the sixth switch in the non-conducting state.
Description
BACKGROUND
[0002] Embodiments of the present specification relate generally to
a three-level active neutral point clamped converter, and more
specifically to a modulator and a method for operating a phase-leg
of the three-level active neutral point clamped converter.
[0003] Typically, three-level active neutral point clamped
(3L-ANPC) converters are employed to convert a direct current (DC)
power to an alternating current (AC) power having a three-level
output. The 3L-ANPC converters are widely used in AC drives and
flexible AC transmission systems. These 3L-ANPC converters employ a
plurality of switches to aid in the power conversion. Also,
traditionally, 3L-ANPC converters that employ silicon carbide (SiC)
switches such as SiC metal-oxide-semiconductor field-effect
transistors (MOSFET) are used when it is desirable to withstand a
high voltage and/or high power.
[0004] As will be appreciated, SiC MOSFETs switch faster in
comparison to other switches such as insulated gate bipolar
transistors (IGBTs), thereby resulting in lower switching losses.
However, the faster switching of the SiC MOSFETs also leads to
higher voltage stress across the SiC MOSFETs of the traditional
3L-ANPC converters due to a commutation loop inductance. Typically,
in the traditional 3L-ANPC converters that employ SiC MOSFETs,
large commutation loops or both the large commutation loops and
small commutation loops are formed. Formation of the large
commutation loops results in an increased loop inductance in the
traditional 3L-ANPC converters. This increase in the loop
inductance results in an increase in the voltage stress across the
SiC MOSFETs, thereby resulting in a reduced lifetime of the SiC
MOSFETs in the traditional 3L-ANPC converters.
[0005] Moreover, the SiC MOSFETs typically leverage a MOSFET body
diode as an anti-parallel diode to reduce cost and space. Further,
in the traditional 3L-ANPC converters, the MOSFET body diodes in
some SiC MOSFETs are operated to conduct current for extended
periods of time. However, such body diodes cannot conduct high
current for extended periods of time due to thermal and reliability
constraints, thereby leading to poor reliability of the traditional
3L-ANPC converters.
BRIEF DESCRIPTION
[0006] In accordance with certain aspects of the present
specification, a method for operating a phase-leg of a three-level
active neutral point clamped (3L-ANPC) converter is presented. The
phase-leg includes an output terminal, a plurality of input
terminals, and a plurality of switches disposed therebetween. The
method includes operating the phase-leg in a neutral state to
generate an output voltage having a neutral level by operating a
second switch, a third switch, a fifth switch, and a sixth switch
of the plurality of switches in a conducting state and operating a
first switch and a fourth switch of the plurality of switches in a
non-conducting state. The method further includes transitioning the
phase-leg to a first intermediate neutral state from the neutral
state by operating the second switch and the fifth switch in the
conducting state and operating the first switch, the third switch,
the fourth switch, and the sixth switch in the non-conducting
state. Moreover, the method includes transitioning the phase-leg
from the first intermediate neutral state to a first state to
generate the output voltage having a first level by operating the
first switch, the third switch, and the fifth switch in the
conducting state and operating the second switch, the fourth
switch, and the sixth switch in the non-conducting state.
[0007] In accordance with another aspect of the present
specification, a modulator for operating a phase-leg of a 3L-ANPC
converter is presented. The phase-leg includes an output terminal,
a plurality of input terminals, and a plurality of switches
disposed therebetween. The modulator includes a controller
operatively coupled to the plurality of switches. The controller is
and configured to operate the phase-leg in a neutral state to
generate an output voltage having a neutral level by operating a
second switch, a third switch, a fifth switch, and a sixth switch
of the plurality of switches in a conducting state and operating a
first switch and a fourth switch of the plurality of switches in a
non-conducting state. The controller is further configured to
transition the phase-leg to a first intermediate neutral state from
the neutral state by operating the second switch and the fifth
switch in the conducting state and operating the first switch, the
third switch, the fourth switch, and the sixth switch in the
non-conducting state. Furthermore, the controller is configured to
transition the phase-leg from the first intermediate neutral state
to a first state to generate the output voltage having a first
level by operating the first switch, the third switch, and the
fifth switch in the conducting state and operating the second
switch, the fourth switch, and the sixth switch in the
non-conducting state.
[0008] In accordance with another aspect of the present
specification, a 3L-ANPC converter is presented. The 3L-ANPC
converter includes one or more phase-legs. At least one phase-leg
of the one or more phase-legs includes an output terminal, and a
plurality of input terminals such as a first input terminal, a
second input terminal, and a neutral input terminal. Furthermore,
the phase-leg includes plurality of switches disposed between the
plurality of input terminals and the output terminal. The plurality
of switches includes a first switch, a second switch, a third
switch, a fourth switch, a fifth switch, and a sixth switch, where
the first switch, the second switch, the third switch, and the
fourth switch of the plurality of switches are operatively coupled
in series, and where the first switch is operatively coupled to the
first input terminal, the fourth switch is operatively coupled to
the second input terminal, an interconnection point of the second
switch and the third switch is operatively coupled to the neutral
input terminal, the fifth switch is operatively coupled between an
interconnection point of the first switch and the second switch and
the output terminal, and the sixth switch is operatively coupled
between an interconnection point of the third switch and the fourth
switch and the output terminal. The 3L-ANPC converter further
includes a modulator operatively coupled to the plurality of
switches of the one or more phase-legs. The modulator is configured
to operate the phase-leg in a neutral state to generate an output
voltage having a neutral level by operating the second switch, the
third switch, the fifth switch, and the sixth switch of the
plurality of switches in a conducting state and operating the first
switch and the fourth switch of the plurality of switches in a
non-conducting state. The modulator is further configured to
transition the phase-leg to a first intermediate neutral state from
the neutral state by operating the second switch and the fifth
switch in the conducting state and operating the first switch, the
third switch, the fourth switch, and the sixth switch in the
non-conducting state. Moreover, the modulator is configured to
transition the phase-leg from the first intermediate neutral state
to a first state to generate the output voltage having a first
level by operating the first switch, the third switch, and the
fifth switch in the conducting state and operating the second
switch, the fourth switch, and the sixth switch in the
non-conducting state.
DRAWINGS
[0009] These and other features and aspects of embodiments of the
present specification will become better understood when the
following detailed description is read with references to the
accompanying drawings in which like characters represent like parts
throughout the drawings, wherein:
[0010] FIG. 1 is a block diagram of a three-level active neutral
point clamped (3L-ANPC) converter, in accordance with aspects of
the present specification;
[0011] FIG. 2 is a schematic diagram of a phase-leg of the 3L-ANPC
converter of FIG. 1, in accordance with aspects of the present
specification;
[0012] FIG. 3 is a graphical representation of an example signal
representing an output voltage of the phase-leg of FIG. 2, in
accordance with aspects of the present specification;
[0013] FIG. 4 is a state diagram depicting transitions of an
operating state of the phase-leg of FIG. 2 to generate the output
voltage of FIG. 3, in accordance with aspects of the present
specification;
[0014] FIG. 5 is a flow-diagram of an example method of operating
the phase-leg of FIG. 2 to generate a signal corresponding to a
first cycle of the output voltage of FIG. 3, in accordance with
aspects of the present specification;
[0015] FIG. 6 is a flow-diagram of an example method of operating
the phase-leg of FIG. 2 to generate a signal corresponding to a
second cycle of the output voltage of FIG. 3, in accordance with
aspects of the present specification; and
[0016] FIGS. 7A, 7B, 7C, 7D, and 7E respectively represent
schematic diagrams that depict an operating state of switches of
the phase-leg of FIG. 2 in a neutral state, a first intermediate
state, a first state, a second intermediate state, and a second
state, in accordance with aspects of the present specification.
DETAILED DESCRIPTION
[0017] As will be described in detail hereinafter, various
embodiments of an exemplary system and method for operating a
phase-leg of a three-level active neutral point clamped (3L-ANPC)
converter are presented. Use of these systems and methods results
in improved life-time of the 3L-ANPC converter. In particular, the
systems and methods allow a flow of an electrical current through
body diodes of switches of the 3L-ANPC converter for a reduced
duration of time in comparison to traditional 3L-ANPC converters
resulting in improved life-time of the switches. Moreover, these
systems and methods lead to formation of small commutation loops
within the phase-leg, thereby reducing an overall loop inductance
of the phase-leg of the 3L-ANPC converter. Such a reduction in the
overall loop inductance reduces voltage stress across the switches
of the 3L-ANPC converter. Consequently, the life-time and the
reliability of the 3L-ANPC converter may be improved.
[0018] In the effort to provide a concise description of these
embodiments, all features of an actual implementation may not be
described in the specification. It should be appreciated that in
the development of any such actual implementation, as in any
engineering or design project, numerous implementation-specific
decisions may be made to achieve the developer's specific goals
such as compliance with system-related and business-related
constraints.
[0019] When describing elements of the various embodiments of the
present specification, the articles "a", "an", "the" and "said" are
intended to mean that there are one or more of the elements. The
terms "comprising", "including" and "having" are intended to be
inclusive and mean that there may be additional elements other than
the listed elements.
[0020] As used herein, the terms "may" and "may be" indicate a
possibility of an occurrence within a set of circumstances; a
possession of a specified property, characteristic or function;
and/or qualify another verb by expressing one or more of an
ability, capability, or possibility associated with the qualified
verb. Accordingly, usage of "may" and "may be" indicates that a
modified term is apparently appropriate, capable, or suitable for
an indicated capacity, function, or usage, while taking into
account that in some circumstances, the modified term may sometimes
not be appropriate, capable, or suitable.
[0021] FIG. 1 is a block diagram of a three-level active neutral
point clamped (3L-ANPC) converter 100, in accordance with aspects
of the present specification. By way of a non-limiting example, the
3L-ANPC converter 100 may be an inverter that facilitates
conversion of a direct current (DC) power to an alternating current
(AC) power. In a presently contemplated configuration, the 3L-ANPC
converter 100 includes an input port 102, an output port 104, and
one or more phase-legs 106, 108, 110 disposed between the input
port 102 and the output port 104. Additionally, the 3L-ANPC
converter 100 may also include a modulator 112 that is operatively
coupled to the one or more phase-legs 106, 108, 110. The term
"power" as used herein may be representative of a voltage, a
current, or both the voltage and current.
[0022] It may be noted that use of the three phase-legs 106-110 in
the 3L-ANPC converter 100 aids in generating a three-phase output
at the output port 104. Although the 3L-ANPC converter 100 of FIG.
1 is shown as having the three phase-legs 106-110, use of a 3L-ANPC
converter having less than three phase-legs or greater than three
phase-legs is also contemplated. For example, a 3L-ANPC converter
with one phase-leg may produce a single-phase output voltage. By
way of another non-limiting example, a 3L-ANPC converter with two
phase-legs may produce a two-phase output voltage.
[0023] The input port 102 includes a positive input terminal 114, a
neutral input terminal 116, and a negative input terminal 118.
These terminals 114, 116, 118 may be hereinafter collectively
referred to as input terminals 114-118. The positive input terminal
114 may be maintained at a positive voltage, the negative input
terminal 118 may be maintained at a negative voltage, and the
neutral input terminal 116 may be maintained at a neutral voltage.
In some embodiments, the positive voltage and the negative voltage
may be non-zero potentials while the neutral voltage may be a zero
potential or substantially close to a zero potential. In certain
embodiments, the neutral voltage may also be a non-zero potential.
The input terminals 114-118 of the input port 102 are electrically
coupled to input terminals (see FIG. 2) of each of the phase-legs
106-110.
[0024] In the example of FIG. 1, a three-phase output voltage may
be available at the output port 104 of the 3L-ANCP converter 100.
The output port 104 includes output terminals 120, 122, 124 to
supply the three-phase output voltage to any target electronic
device (not shown) coupled to the 3L-ANCP converter 100. More
particularly, a single-phase voltage may be supplied via each of
the output terminals 120, 122, 124. These terminals 120, 122, 124
may be hereinafter collectively referred to as output terminals
120-124. In some embodiments, output terminals 120-124 of the
output port 104 are electrically coupled to an output terminal (see
FIG. 2) of each of the phase-legs 106-110. The output voltage at
each of the output terminals 120-124 includes three levels such as
a first level, a second level, and a neutral level. By way of
example, the first level may be a positive voltage level, while the
second level may be a negative voltage level. By way of another
example, while the first level may be the negative voltage level,
the second level may be the positive voltage level. Moreover, the
neutral level may be a zero voltage or substantially close to a
zero voltage. In certain embodiments, the neutral level may be a
non-zero voltage.
[0025] The phase-legs 106, 108, 110 are electrically coupled to the
input port 102 and the output port 104. Each of the phase-legs 106,
108, 110 is configured to convert the DC power received from the
input port 102 to an AC power and supply the generated AC power to
the output port 104 as a phase voltage and a phase current. More
particularly, the phase-legs 106, 108, 110 are configured to
provide the generated AC power to the corresponding output terminal
120, 122, 124. In some embodiments, one or more of the phase-legs
106-110 may include a plurality of switches (see FIG. 2) to
facilitate conversion of the DC power to the AC power. The
phase-legs 106-110 will be described in greater detail with
reference to FIG. 2.
[0026] The modulator 112 is operatively coupled to the phase-legs
106-110. In the embodiment of FIG. 1, the modulator 112 is shown as
a part of the 3L-ANPC converter 100. In certain embodiments, the
modulator 112 may be disposed outside the 3L-ANPC converter
100.
[0027] In some embodiments, the modulator 112 may include a
controller 126 configured to control operations of the phase-legs
106-110 to facilitate the conversion of the DC power to the AC
power by the phase-legs 106-110. The controller 126 may include
hardware elements such as a specially programmed general purpose
computer, an electronic processor such as a microprocessor, a
digital signal processor, and/or a microcontroller. Further, the
controller 126 may include input/output ports and a storage medium,
such as an electronic memory. Various examples of the
microprocessor include, but are not limited to, a reduced
instruction set computing (RISC) architecture type microprocessor
or a complex instruction set computing (CISC) architecture type
microprocessor. Further, the microprocessor may be a single-core
type or multi-core type. Alternatively, the controller 126 may be
implemented using hardware elements such as circuit boards with
processors, logic gates, or as software running on a processor such
as a personal computer (PC), or a microcontroller.
[0028] The controller 126 may be operatively coupled to the
phase-legs 106-110. More particularly, the controller 126 may be
operatively coupled to the switches (see FIG. 2) of the phase-legs
106-110 and configured to control switching of the switches to
facilitate conversion of the DC power to the AC power. The
controller 126 may be configured to operate the phase-legs 106-110
such that loop inductances of the phase-legs 106-110 are reduced,
consequently resulting in a reduction in the voltage stress on the
switches of the phase-legs 106-110. Implementing the design of the
3L-ANPC converter 100 as described hereinabove results in improved
life and reliability of the 3L-ANPC converter 100. The operation of
the controller 126 will be described in greater detail with
reference to FIGS. 2-7.
[0029] Referring now to FIG. 2, a schematic diagram 200 of one
embodiment of a phase-leg such as the phase-leg 106 of the 3L-ANPC
converter 100 of FIG. 1, in accordance with aspects of the present
specification, is presented. In some embodiments, the other
phase-legs 108 and 110 may also have a configuration similar to the
configuration of the phase-leg 200 depicted in FIG. 2. Also, FIG. 2
will be described with reference to the components of FIG. 1.
[0030] In some embodiments, the phase-leg 200 may include a
plurality of input terminals such as a first input terminal 202, a
second input terminal 204, and a neutral input terminal 206. The
phase-leg 200 may also include a plurality of switches and an
output terminal 208. The plurality of switches includes a first
switch 210, a second switch 212, a third switch 214, a fourth
switch 216, a fifth switch 218, and a sixth switch 220. The first
switch 210, second switch 212, third switch 214, fourth switch 216,
fifth switch 218, and sixth switch 220 are hereinafter collectively
referred to as switches 210-220.
[0031] Although not depicted in FIG. 2, the first input terminal
202, the second input terminal 204, and the neutral input terminal
206 of the phase-leg 200 may be respectively operatively coupled to
the positive input terminal 114, the negative input terminal 118,
the neutral input terminal 116 of the 3L-ANPC converter 100 of FIG.
1. Also, the output terminal 208 of the phase-leg 200 may be
operatively coupled to the output terminal 124 of the 3L-ANPC
converter 100 of FIG. 1. Furthermore, a gate terminal of each of
the switches 210-220 may be operatively coupled to the modulator
112 of the 3L-ANPC converter 100. More particularly, the gate
terminal of each of the switches 210-220 may be operatively coupled
to the controller 126 of the modulator 112.
[0032] One embodiment of the phase-leg 200 having six switches
210-220 is depicted in FIG. 2. However, the phase-leg 200 having
greater than six or fewer than six switches is also contemplated.
Moreover, the switches 210-220 depicted in FIG. 2 are silicon
carbide (SiC) metal-oxide-semiconductor field-effect transistors
(MOSFETs), where each switch may include a MOSFET element and a
body diode. It may be noted that, the phase-leg 200 having other
types of switches is also envisioned. Other non-limiting examples
of the switches 210-220 include transistors, gate commutated
thyristors, field effect transistors, insulated gate bipolar
transistors (IGBT), gate turn-off thyristors, static induction
transistors, static induction thyristors, or combinations thereof.
Furthermore, materials used to form the switches 210-220 may
include, but are not limited to, silicon (Si), germanium (Ge), SiC,
gallium nitride (GaN), or combinations thereof.
[0033] As will be appreciated, an SiC switch module typically
includes two switches. Therefore, in some embodiments, three such
SiC modules may be used to form the phase-leg 200 of FIG. 2. By way
of example, the switches 210 and 212 may belong to a first SiC
switch module (not shown), the switches 214 and 216 may belong to a
second SiC switch module (not shown), and the switches 218 and 220
may belong to a third SiC switch module (not shown). It may be
noted that other types of SiC switch modules may also be used
without limiting the scope of the present specification.
[0034] As depicted in FIG. 2, the first switch 210, the second
switch 212, the third switch 214, and the fourth switch 216 are
operatively coupled in series. More particularly, the switches
210-216 are coupled in series such that a source terminal of the
first switch 210 is connected to a drain terminal of the second
switch 212, a source terminal of the second switch 212 is connected
to a drain terminal of the third switch 214, and a source terminal
of the third switch 214 is connected to a drain terminal of the
fourth switch 216. Further, the first switch 210 is operatively
coupled to the first input terminal 202 and the fourth switch 216
is operatively coupled to the second input terminal 204. More
particularly, as depicted in FIG. 2, a drain terminal of the first
switch 210 is connected to the first input terminal 202, while a
source terminal of the fourth switch 216 is connected to the second
input terminal 204.
[0035] Furthermore, reference numeral 226 represents an
interconnection point of the second switch 212 and the third switch
214. The interconnection point 226 is operatively coupled to the
neutral input terminal 206. Also, reference numeral 228 represents
an interconnection point of the first switch 210 and the second
switch 212. The fifth switch 218 is operatively coupled between the
interconnection point 228 and the output terminal 208. More
particularly, in the example of FIG. 2, a drain terminal of the
fifth switch 218 is connected to the interconnection point 228 and
a source terminal of the fifth switch 218 is connected to the
output terminal 208. Moreover, reference numeral 230 represents an
interconnection point of the third switch 214 and the fourth switch
216. The sixth switch 220 is operatively coupled between the
interconnection point 230 and the output terminal 208. In
particular, a source terminal of the sixth switch 220 is connected
to the interconnection point 230 and a drain terminal of the sixth
switch 220 is connected to the output terminal 208.
[0036] Moreover, in some embodiments, the phase-leg 200 may also
include capacitors 222 and 224. The capacitor 222 is connected
between the first input terminal 202 and the neutral input terminal
206. Also, the capacitor 224 is connected between the second input
terminal 204 and the neutral input terminal 206.
[0037] The controller 126 may be configured to operate the
phase-leg 200 in one or more operating states including, but not
limited to, a neutral state, a first intermediate neutral state, a
first state, a second intermediate neutral state, or a second state
(see FIG. 4). In some embodiments, the phase-leg 200, when operated
in any of the neutral state, the first intermediate neutral state,
or the second intermediate neutral state, may be configured to
generate an output voltage having the neutral level at the output
terminal 208. Moreover, the phase-leg 200, when operated in the
first state, may be configured to generate the output voltage
having the first level at the output terminal 208. In a similar
fashion, the phase-leg 200, when operated in the second state, may
be configured to generate the output voltage having the second
level at the output terminal 208. A signal representative of an
example output voltage of the phase-leg 200 is depicted in FIG.
3.
[0038] To transition the phase-leg 200 between the neutral state,
the first intermediate neutral state, the first state, the second
intermediate neutral state, and the second state, the controller
126 may be configured to selectively operate one or more of the
switches 210-220 in a conducting state and operate the remaining
switches in a non-conducting state. As will be appreciated, the
switches operated in the conducting state allow an electrical
current to pass through, while the switches operated in the
non-conducting state block a flow of the electrical current
therethrough. The controller 126 is configured to operate any
switch in the conducting state or the non-conducting state by
applying a control signal to the gate terminal of that switch
210-220.
[0039] In the embodiment of FIG. 2, the switches 210-220 are
N-channel SiC MOSFETs. Accordingly, to operate any of the switches
210-220 in the conducting state, it is desirable to supply a
control signal having a higher magnitude (H) to a corresponding
gate terminal. It may be noted that the control signal having the
higher magnitude is representative of a control signal having a
magnitude that is greater than a magnitude of a signal provided to
a corresponding source terminal. Similarly, to operate any of the
switches 210-220 in the non-conducting state, it is desirable to
supply a control signal having a lower magnitude (L) to the
corresponding gate terminal. It may be noted that the control
signal having the lower magnitude is representative of a control
signal having a magnitude that is lower than a magnitude of a
signal provided to a corresponding source terminal. Moreover, it
may be noted that if P-channel SiC MOSFETs are used as the switches
210-220, the levels of the control signals may be interchanged.
[0040] Accordingly, to operate any of the switches 210-220 in the
conducting state, the controller 126 may be configured to supply a
control signal having the higher magnitude to the gate terminals of
the respective switches. Similarly, to operate any of the switches
210-220 in the non-conducting state, the controller 126 may be
configured to supply a control signal having the lower magnitude
(L) to the gate terminals of the respective switches.
[0041] During operation of the phase-leg 200, commutation loops are
created when one or more switches 210-220 are transitioned from the
conducting state to the non-conducting state or vice-versa. An
inductance of such a commutation loop is referred to as a loop
inductance.
[0042] Typically, in traditional 3L-ANPC converters, large
commutation loops or both the large commutation loops and small
commutation loops are formed in any phase-leg. As will be
appreciated, the loop inductance increases with an increase in a
length of the commutation loop. Consequently, the traditional
3L-ANPC converters exhibit increased loop inductance.
Disadvantageously, the increased loop inductance adversely impacts
switching speed of switches of the traditional 3L-ANPC converters
and also increases voltage stress on the switches of the
traditional 3L-ANPC converters.
[0043] The controller 126 of the modulator 112 may be configured to
operate the phase-leg 200 such that small commutation loops are
formed in the phase-leg 200. Consequently, the loop inductance of
the phase-leg 200 in one or more of the operating states is reduced
in comparison to the loop inductance experienced by the traditional
3L-ANPC converters. The reduction in the loop inductance in turn
reduces voltage stress on the switches 210-220 of the phase-leg
200. Moreover, the controller 126 may be configured to operate the
switches 210-220 such that the body diodes of the switches 210-220
do not conduct currents for extended periods of time. For example,
in the configuration of FIG. 2, the body diodes of some of the
switches 210-220 conduct current merely for a few microseconds.
Consequently, the body diodes of these switches 210-220 are
protected from adverse effects of flow of current therethrough.
Advantageously, such an operation of the phase-leg 200 results in
improved life and reliability of the phase-leg 200 and the 3L-ANPC
converter 100.
[0044] Furthermore, in accordance with the aspects of the present
specification, the phase-leg 200 is additionally operated in a
first intermediate state and a second intermediate state in
comparison to the phase-legs of the traditional 3L-ANPC converters.
Also, it may be noted that the phase-leg 200 is configured to be
operated in the first and second intermediate states for a short
duration, for example, a few microseconds. Typically, body diodes
in the switches 210-220 are not designed for carrying current for
long durations. In the traditional 3L-ANPC converters, body diodes
of some switches conduct current for long durations especially
while an output voltage having a neutral level is generated by the
traditional 3L-ANPC converters. In accordance with the aspects of
the present specification, when the phase-leg 200 is operated in a
first intermediate state or a second intermediate state for a short
duration, the switches 218, 220 also operate in the non-conducting
state for the short duration. Advantageously, operating the
phase-leg 200 in the first and second intermediate states for short
durations aids in reducing the time during which the body diodes of
the switches 218, 220 conduct current. Hence, the body diodes of
the switches 218, 220 are protected from adverse effects of current
flowing therethrough. Consequently, the reliability and useful life
of the 3L-ANPC converter 100 is improved in comparison to the
reliability and useful life of the traditional 3L-ANPC
converters.
[0045] FIG. 3 is a graphical representation 300 depicting an
example signal that represents an output voltage 302 of a phase-leg
such as the phase-leg 200, in accordance with aspects of the
present specification. FIG. 3 is described with reference to the
components of FIG. 2.
[0046] The output voltage 302 may be obtained at the output
terminal 208 of the phase-leg 200. Reference numeral 304 represents
an X-axis and the reference numeral 306 represents a Y-axis. The
X-axis 304 and the Y-axis 306 respectively represent time and an
amplitude of the output voltage 302. Further, reference numerals
308, 310, and 312 represent a first level, a second level, and a
neutral level, respectively, of the output voltage 302. Moreover,
reference numerals 314 and 316 respectively represent a first cycle
and a second cycle of the output voltage 302. For ease of
illustration, two cycles 314, 316 of the output voltage 302 are
represented in FIG. 3. It may be noted that output voltage 302 may
include more than two cycles. Further, in the example of FIG. 3,
the first cycle 314 is shown as a positive cycle while the second
cycle 316 is shown as a negative cycle. Use of the phase-leg 200 to
generate the output voltage 302 having any number of first cycles
314, any number of second cycles 316, or any combination or pattern
of the first and second cycles 314, 316 is also envisioned.
Moreover, use of the phase-leg 200 to generate the output voltage
302 having only the first cycles 314 or only the second cycles 316
is also envisioned.
[0047] In FIG. 3, T.sub.0 represents a total time corresponding to
a neutral state of the phase-leg 200. Also, T.sub.min represents a
minimum pulse duration corresponding to any of the first, second,
and third levels 308, 310, 312 of the output voltage 302, and
T.sub.s represents a time period of a single cycle such as the
first cycle 314 or the second cycle 316 of the output voltage 302
of the phase-leg 200.
[0048] FIG. 4 is a state diagram 400 depicting transitions of an
operating state of the phase-leg 200 of FIG. 2 to generate the
output voltage 302 of FIG. 3, in accordance with aspects of the
present specification. FIG. 4 is described in conjunction with
FIGS. 2 and 3. The operating states such as the neutral state, the
first intermediate neutral state, the first state, the second
intermediate neutral state, and the second state are represented by
reference numerals 402, 404, 406, 408, and 410, respectively. The
arrows are used to generally indicate a subsequent operating state
corresponding to a given operating state.
[0049] During operation of the phase-leg 200, at time t=0, if it is
assumed that the phase-leg 200 is operating in the neutral state
402 and the output voltage 302 having the first level 308 is
desired as depicted in the first cycle 314, the controller 126 is
configured to transition the phase-leg 200 to the first
intermediate neutral state 404 and subsequently to the first state
406. Further, the controller 126 is configured to maintain the
phase-leg 200 in the first state 406 for a first determined time
duration (see Table-2). The first determined time duration may be
computed by the controller 126 based on a desired frequency and
duty-cycle of the output voltage 302. Subsequent to the lapse of
the first determined time duration, the controller 126 is
configured to transition the phase-leg 200 back to the neutral
state 402. In one embodiment, as depicted in FIG. 4, the controller
126 may be configured to transition the phase-leg 200 directly to
the neutral state 402 from the first state 406. In an alternative
embodiment, the controller 126 may be configured to transition the
phase-leg 200 to the neutral state 402 from the first state 406 via
the first intermediate neutral state 404.
[0050] Moreover, to generate the output voltage 302 having the
second level 310, the controller 126 is configured to transition
the phase-leg 200 to second intermediate neutral state 408 and
subsequently to the second state 410. Further, the controller 126
may be configured to maintain the phase-leg 200 in the second state
410 for a second determined time duration. The second determined
time duration may be computed by the controller 126 based on a
desired frequency and duty-cycle of the output voltage 302.
Subsequent to the lapse of the second determined time duration, the
controller 126 may be configured to transition the phase-leg 200
back to the neutral state 402. In one embodiment, as depicted in
FIG. 4, the controller 126 may be configured to transition the
phase-leg 200 directly to the neutral state 402 from the second
state 410. Alternatively, the controller 126 may be configured to
transition the phase-leg 200 to the neutral state 402 from the
second state 410 via the second intermediate neutral state 408.
[0051] Table 1 illustrates levels of the output voltage 302
corresponding to the operating states 402-410. Also, Table 2
illustrates non-limiting examples of determined time durations
corresponding to the operating states 402-410.
TABLE-US-00001 TABLE 1 Operating state of the phase-leg 200 Level
of the output voltage 302 Neutral state 402 Neutral level 312 First
intermediate neutral state 404 Neutral level 312 First state 406
First level 308 Second intermediate neutral state 408 Neutral level
312 Second state 410 Second level 310
TABLE-US-00002 TABLE 2 First intermediate neutral state 404 OR
second First intermediate state 406 neutral OR second T.sub.0
Neutral state 402 state 408 state 410 0 < T.sub.0 < T.sub.min
0 T.sub.min T.sub.s-T.sub.min T.sub.min < T.sub.0 <
2T.sub.min 0 T.sub.0 T.sub.s-T.sub.0 2T.sub.min < T.sub.0 <
3T.sub.min T.sub.0 - T.sub.min T.sub.min T.sub.s-T.sub.0 3T.sub.min
< T.sub.0 < 4T.sub.min T.sub.0 - 2T.sub.min + T.sub.min
T.sub.min T.sub.s-T.sub.0 4T.sub.min < T.sub.0 T.sub.0/2 -
T.sub.min + T.sub.0/2 T.sub.min T.sub.s-T.sub.0
[0052] Column 1 of Table 2 represents example scenarios indicating
different ranges of the total time T.sub.0 corresponding to the
neutral state 402. Columns 2-4 of Table 2 represent time durations
of the operating states 402-410 that correspond to the value of
T.sub.0 in column 1. As noted hereinabove, the minimum pulse
duration T.sub.min represents a minimum time duration required for
any of the levels 308, 310, 312. Accordingly, if the total time
T.sub.0 for the neutral state 402 is less than the minimum pulse
duration T.sub.min (see, row 1 of Table 2), the time duration
corresponding to the first level 308 and hence the first state 406,
or the second level 310 and hence the second state 410 may be
adjusted to a value of (T.sub.s-T.sub.min). This adjustment may be
performed because the minimum pulse duration T.sub.min is required
to facilitate generation of the neutral level 312. The neutral
level 312 may be generated by operating the phase-leg 200 in the
neutral state 402, the first intermediate neutral state 404, and
the second intermediate neutral state 408.
[0053] Advantageously, operating the phase-leg 200 in the first
intermediate neutral state 404 while transitioning from the neutral
state 402 to the first state 406 or vice-versa and operating the
phase-leg 200 in the second intermediate neutral state 404 while
transitioning from the neutral state 402 to the second state 410,
or vice-versa, result in small commutation loops in the phase-leg
200 due to corresponding switching of the switches 210-220 as
described hereinabove. Consequent to operating the phase-leg 200
with such small commutation loops, the overall loop inductance of
the phase-leg 200 at any given point of time is reduced. This
reduction in the overall loop inductance reduces voltage stress
across the switches 210-220 of the phase-leg 200. Consequently, the
life-time and the reliability of the switches 210-220 and the
3L-ANPC converter 100 may be improved.
[0054] FIG. 5 is a flow-diagram 500 of an example method of
operating a phase-leg 200 to generate a signal such as a first
cycle of an output voltage at an output terminal of the phase-leg
200, in accordance with aspects of the present specification. In
particular, FIG. 5 represents a method of operating the phase-leg
200 (see FIG. 2) to generate the first cycle 314 (see FIG. 3) of
the output voltage 302 (see FIG. 3) at the output terminal 208 (see
FIG. 2) of the phase-leg 200. FIG. 5 is described with respect to
operation of the phase-leg 200. It may be noted that the phase-legs
106, 108, 110 of FIG. 1 may also be operated in a similar fashion
with an appropriate phase difference. FIG. 5 is described in
conjunction with FIGS. 1-4.
[0055] At step 502, the phase-leg 200 is operated in the neutral
state 402 to generate the output voltage 302 having the neutral
level 312. To operate the phase-leg 200 in the neutral state 402,
the controller 126 is configured to operate the second switch 212,
the third switch 214, the fifth switch 218, and the sixth switch
220 in a conducting state and the first switch 210 and the fourth
switch 216 in a non-conducting state (see FIG. 7A). In the neutral
state 402, the phase-leg 200 generates the output voltage having
the neutral level 312. It may be noted that in the neutral state
402, since the switches 212, 214, 220, and 218 are operated in the
conducting state, the body diodes of these switches 212, 214, 220,
and 218 do not conduct any current. Therefore, the life-time and
reliability of the switches 212, 214, 220, and 218 and hence, the
life-time and reliability of the 3L-ANPC converter 100 may be
improved.
[0056] Further, at step 504, the phase-leg 200 is transitioned to
the first intermediate neutral state 404 from the neutral state
402. Accordingly, the controller 126 is configured to transition
the third switch 214 and the sixth switch 220 to the non-conducting
state. Hence, in the first intermediate neutral state 404, while
the second switch 212 and the fifth switch 218 are operated in the
conducting state, the first switch 210, the third switch 214, the
fourth switch 216, and the sixth switch 220 are operated in the
non-conducting state (see FIG. 7B). In the first intermediate
neutral state 404, the phase-leg 200 continues to generate the
output voltage having the neutral level 312.
[0057] Furthermore, at step 506, the phase-leg 200 is transitioned
from the first intermediate neutral state 404 to the first state
406 to generate the output voltage 302 having the first level 308.
To effect this transition of the phase-leg 200, the controller 126
is configured to transition the first switch 210 and the third
switch 214 to the conducting state and transition the second switch
212 to the non-conducting state. Accordingly, in the first state
406, while the first switch 210, the third switch 214, and the
fifth switch 218 are operated in the conducting state, the second
switch 212, the fourth switch 216, and the sixth switch 220 are
operated in the non-conducting state (see FIG. 7C).
[0058] As noted hereinabove with reference to step 504, to
transition the phase-leg 200 from the neutral state 402 to the
first intermediate neutral state 404, the switches 212 and 218 are
operated in the conducting state, while the switches 214 and 220
are transitioned to the non-conducting state. This transition of
the switches 214, 220 results in reduced voltage stress across the
switches 214 and 220 in comparison to voltage stress experienced by
switches in the traditional 3L-ANPC converters. Moreover, the
phase-leg 200 may be operated in the first intermediate neutral
state 404 for a short period of time such as for a few
microseconds, after which the switches 214 and 220 are transitioned
to the conducting state to transition the phase-leg 200 to the
first state 406. Accordingly, the body diodes of the switches 214,
220 need to conduct a current during that short duration
corresponding to the first intermediate neutral state 404, thereby
resulting in an increased life-time of the switches 214, 220 in
comparison to the switches of the traditional 3L-ANPC
converters.
[0059] Moreover, at step 508, the phase-leg 200 is transitioned
from the first state 406 to the neutral state 402 to generate the
output voltage 302 having the neutral level 312. As previously
noted, in the neutral state 402, the controller 126 is configured
to operate the second switch 212, the third switch 214, the fifth
switch 218, and the sixth switch 220 in a conducting state and the
first switch 210 and the fourth switch 216 in a non-conducting
state.
[0060] In some embodiments, the controller 126 may be configured to
transition the phase-leg 200 directly to the neutral state 402 from
the first state 406. To transition the phase-leg 200 directly to
the neutral state 402 from the first state 406, the controller 126
is configured to transition the second switch 212 and the sixth
switch 220 to the conducting state and transition the first switch
210 to the non-conducting state.
[0061] In certain other embodiments, the controller 126 may be
configured to transition the phase-leg 200 to the neutral state 402
from the first state 406 via the first intermediate neutral state
404. In this example, the controller 126 is configured to first
transition the phase-leg 200 from the first state 406 to the first
intermediate neutral state 404 and subsequently transition the
phase-leg 200 from the first intermediate neutral state 404 to the
neutral state 402. Accordingly, the controller 126 is configured to
first transition the second switch 212 to the conducting state and
transition the first switch 210 and the third switch 214 to the
non-conducting state to facilitate transition of the phase-leg 200
from the first state 406 to the first intermediate neutral state
404. Further, the controller 126 is configured to transition the
third switch 214 and the sixth switch 220 to the conducting state
to transition the phase-leg 200 from the first intermediate neutral
state 404 to the neutral state 402.
[0062] FIG. 6 is a flow-diagram 600 of an example method of
operating a phase-leg 200 to generate a signal such as a second
cycle of an output voltage at an output terminal of the phase-leg
200, in accordance with aspects of the present specification. In
particular, FIG. 6 represents a method of operating the phase-leg
200 (see FIG. 2) to generate the second cycle 316 (see FIG. 3) of
the output voltage 302 (see FIG. 3) at the output terminal 208 (see
FIG. 2) of the phase-leg 200. FIG. 6 is described with respect to
operation of the phase-leg 200. It may be noted that the phase-legs
106, 108, 110 of FIG. 1 may also be operated in a similar fashion
with an appropriate phase difference. FIG. 5 is described in
conjunction with FIGS. 1-4.
[0063] At step 602, the phase-leg 200 is operated in the neutral
state 402 to generate the output voltage 302 having the neutral
level 312. Further, at step 604, the phase-leg 200 may be
transitioned from the neutral state 402 to the second intermediate
neutral state 408. To transition the phase-leg 200 from the neutral
state 402 to the second intermediate neutral state 408, the
controller 126 may be configured to transition the second switch
212 and the fifth switch 218 to the non-conducting state.
Accordingly, in the second intermediate neutral state 408, the
third switch 214 and the sixth switch 220 are operated in the
conducting state, whereas the first switch 210, the second switch
212, the fourth switch 216, and the fifth switch 218 are operated
in the non-conducting state (see FIG. 7D). Consequently, in the
second intermediate neutral state 408, the phase-leg 200 generates
the output voltage having the neutral level 312.
[0064] Moreover, at step 606, the phase-leg 200 is transitioned
from the second intermediate neutral state 408 to the second state
410 to generate the output voltage having the second level 310.
Accordingly, the controller 126 may be configured to transition the
second switch 212 and the fourth switch 216 to the conducting state
and transition the third switch 214 to the non-conducting state.
Hence, in the second state 410, the second switch 212, the fourth
switch 216, and the sixth switch 220 are operated in the conducting
state, whereas the first switch 210, the third switch 214, and the
fifth switch 218 are operated in the non-conducting state (see FIG.
7E).
[0065] As noted hereinabove with reference to step 604, to
transition the phase-leg 200 from the neutral state 402 to the
second intermediate neutral state 408, the switches 214 and 220 are
operated in the conducting state, while the switches 212 and 218
are transitioned to the non-conducting state. This transition of
the switches 212, 218 results in reduced voltage stress across the
switches 212, 218 in comparison to voltage stress experienced by
switches in the traditional 3L-ANPC converters. In addition, the
phase-leg 200 may be operated in the second intermediate neutral
state 408 for a short period of time such as for a few
microseconds, after which the switches 212 and 218 are transitioned
to the conducting state to transition the phase-leg 200 to the
second state 410. Accordingly, the body diodes of the switches 212,
218 need to conduct a current during that short duration
corresponding to the second intermediate neutral state 408, thereby
resulting in an increased life-time of the switches 212, 218 in
comparison to the switches of the traditional 3L-ANPC
converters.
[0066] Additionally, at step 608, the phase-leg 200 is transitioned
from the second state 410 to the neutral state 402. As previously
noted, in the neutral state 402, the controller 126 is configured
to operate the second switch 212, the third switch 214, the fifth
switch 218, and the sixth switch 220 in a conducting state and the
first switch 210 and the fourth switch 216 in a non-conducting
state (see FIG. 7A).
[0067] In some embodiments, the controller 126 may be configured to
transition the phase-leg 200 directly to the neutral state 402 from
the second state 410. To transition the phase-leg 200 from the
second state 410 to the neutral state 402, the controller 126 is
configured to transition the third switch 214 and the fifth switch
218 to the conducting state and transition the fourth switch 216 to
the non-conducting state.
[0068] In certain other embodiments, the controller 126 may be
configured to transition the phase-leg 200 to the neutral state 402
from the second state 410 via the second intermediate neutral state
408. In this example, the controller 126 is configured to first
transition the phase-leg 200 from the second state 410 to the
second intermediate neutral state 408 and subsequently transition
the phase-leg 200 from the second intermediate neutral state 408 to
the neutral state 402. Accordingly, the controller 126 is
configured to first transition the second switch 212 and the fourth
switch 216 to the non-conducting state and transition the third
switch 214 to the conducting state to facilitate the transition of
the phase-leg 200 from the second state 410 to the second
intermediate neutral state 408. Further, the controller 126 is
configured to transition the second switch 212 and the fifth switch
218 to the conducting state to transition the phase-leg 200 from
the second intermediate neutral state 408 to the neutral state
402.
[0069] Moreover, in some embodiments, the method of FIG. 6 may be
executed after the execution of the method of FIG. 5 to generate
the output voltage 302 as depicted in FIG. 3. Also, in certain
embodiments, the methods of FIG. 5 and FIG. 6 may be alternatively
repeated to generate the output voltage including alternate first
and second cycles 314, 316. Additionally, in certain other
embodiments, the methods of FIG. 5 and FIG. 6 may be executed in a
predetermined pattern to generate the output voltage having the
predetermined pattern of the first and second cycles 314, 316.
[0070] FIGS. 7A, 7B, 7C, 7D, and 7E respectively represent
schematic diagrams 702, 704, 706, 708, 710 that depict operating
state the switches 210-220 of the phase-leg 200 of FIG. 2. In
particular, FIGS. 7A-7E respectively represent the operating state
of the switches 210-222 in the neutral state 402, the first
intermediate state 404, and the first state 406, the second
intermediate state 408, and the second state 410 (see FIG. 4) of
the phase-leg 200, in accordance with aspects of the present
specification. It may be noted that in FIGS. 7A-7E, only the
switches that operate in the conducting state are marked with an
encompassing square. Table 3 summarizes the operating state of the
switches 210-220 corresponding to the operating states 402-408.
TABLE-US-00003 TABLE 3 Operating state of Operating state of
switches 210-220 the phase-leg 200 Conducting state Non-conducting
state Neutral state 402 Switches 212, 214, 218, Switches 210, 216
(see FIG. 7A) 220 First intermediate Switches 212, 218 Switches
210, 214, 216, neutral state 404 220 (see FIG. 7B) First state 406
Switches 210, 214, 218 Switches 212, 216, 220 (see FIG. 7C) Second
intermediate Switches 214, 220 Switches 210, 212, 216, neutral
state 408 218 (see FIG. 7D) Second state 410 Switches 212, 216, 220
Switches 210, 214, 218 (see FIG. 7E)
[0071] The systems and methods for operating the phase-leg(s)
106-110 of the 3L-ANPC converter described hereinabove facilitate
an operation of the 3L-ANPC converter with reduced loop inductances
in comparison to the traditional 3L-ANPC converters. Moreover, in
the 3L-ANPC converter of the present specification, some of the
switches are operated such that the corresponding body diodes do
not conduct current for long periods of time, thereby protecting
the body diodes. Consequently, switching losses, voltage stresses,
and an effect of the current through the body diodes corresponding
to one or more of the switches are greatly reduced, thereby leading
to a highly reliable operation of the 3L-ANPC converter.
Furthermore, the reduction in the overall switching losses leads to
enhanced efficiency of the 3L-ANPC converter of the present
specification in comparison to the traditional 3L-ANPC
converters.
[0072] It is to be understood that not necessarily all such objects
or advantages described above may be achieved in accordance with
any particular embodiment. Thus, for example, those skilled in the
art will recognize that the systems and techniques described herein
may be embodied or carried out in a manner that achieves or
improves one advantage or group of advantages as taught herein
without necessarily achieving other objects or advantages as may be
taught or suggested herein.
[0073] While the technology has been described in detail in
connection with only a limited number of embodiments, it should be
readily understood that the specification is not limited to such
disclosed embodiments. Rather, the technology can be modified to
incorporate any number of variations, alterations, substitutions or
equivalent arrangements not heretofore described, but which are
commensurate with the spirit and scope of the claims. Additionally,
while various embodiments of the technology have been described, it
is to be understood that aspects of the specification may include
only some of the described embodiments. Accordingly, the
specification is not to be limited by the foregoing description,
but is only limited by the scope of the appended claims.
* * * * *