U.S. patent application number 16/176835 was filed with the patent office on 2019-05-02 for multicomponent latent-crimping staple fiber and method therefor.
The applicant listed for this patent is Fiber Innovation Technology, Inc.. Invention is credited to Jeffrey S. DUGAN.
Application Number | 20190127891 16/176835 |
Document ID | / |
Family ID | 66243533 |
Filed Date | 2019-05-02 |




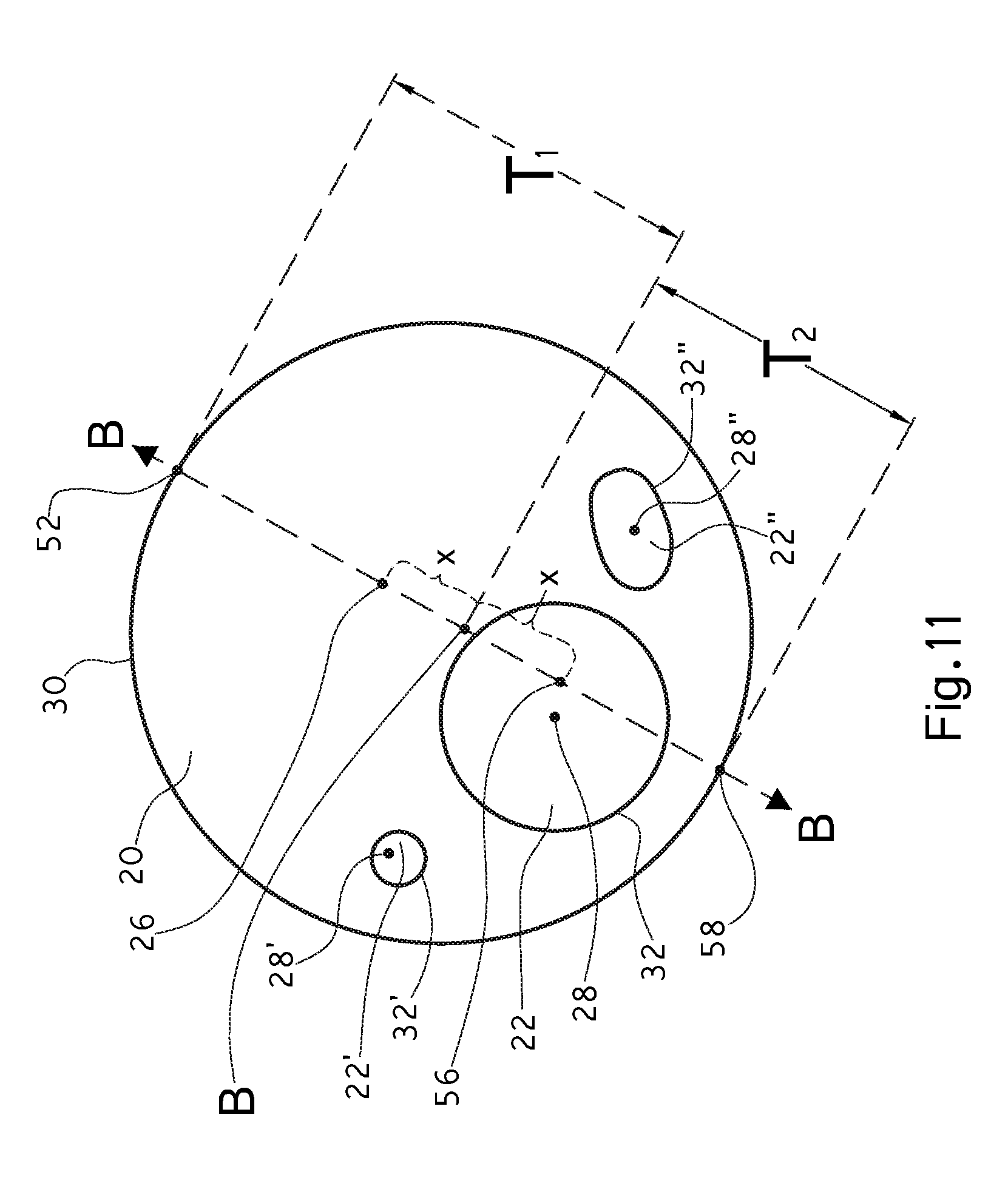
United States Patent
Application |
20190127891 |
Kind Code |
A1 |
DUGAN; Jeffrey S. |
May 2, 2019 |
MULTICOMPONENT LATENT-CRIMPING STAPLE FIBER AND METHOD THEREFOR
Abstract
A multicomponent latent-crimping staple fiber, or a
non-mechanically-crimped staple fiber contains a first component
and a second component which each have their own differing lengths
and a shrinkage differential therebetween and eccentric
cross-sectional centers of mass. The staple fibers herein have a
tenacity after crimping of at least 90% as compared to the tenacity
prior to crimping. Processes for making such a fiber are also
described.
Inventors: |
DUGAN; Jeffrey S.; (Erwin,
TN) |
|
Applicant: |
Name |
City |
State |
Country |
Type |
Fiber Innovation Technology, Inc. |
Johnson City |
TN |
US |
|
|
Family ID: |
66243533 |
Appl. No.: |
16/176835 |
Filed: |
October 31, 2018 |
Related U.S. Patent Documents
|
|
|
|
|
|
Application
Number |
Filing Date |
Patent Number |
|
|
62579190 |
Oct 31, 2017 |
|
|
|
Current U.S.
Class: |
1/1 |
Current CPC
Class: |
D02G 1/18 20130101; D01F
8/12 20130101; D01D 5/22 20130101; D01F 8/06 20130101; D01D 5/32
20130101; D01F 8/16 20130101; D01F 8/14 20130101 |
International
Class: |
D01F 8/12 20060101
D01F008/12; D01F 8/16 20060101 D01F008/16; D01F 8/14 20060101
D01F008/14; D01F 8/06 20060101 D01F008/06; D02G 1/18 20060101
D02G001/18 |
Claims
1. A multicomponent latent-crimping staple fiber comprising: A. a
first component comprising: i. a first length; and ii. a first
cross-sectional center of mass; and B. a second component
comprising: i. a second length; and ii. a second cross-sectional
center of mass, wherein the shrinkage differential between the
first length and the second length is at least 0.01%, and wherein
the first cross-sectional center of mass and the second
cross-sectional center of mass are eccentric, wherein the first
component and the second component are extruded and combined to
form a multicomponent latent-crimping fiber, wherein the
multicomponent latent-crimping fiber is cut to form a
multicomponent latent-crimping staple fiber, wherein the
multicomponent latent-crimping staple fiber is crimped either
before, during, or after cutting, and wherein the multicomponent
latent-crimping staple fiber has a tenacity of at least about 90%
as compared to the tenacity of the multicomponent latent-crimping
fiber prior to crimping.
2. The multicomponent latent-crimping staple fiber according to
claim 1, wherein the first component comprises a polymer selected
from the group consisting of a polyamide, a sulfur-containing
polymer, an aromatic polyester, an aliphatic polyester, a
polyolefin, and a combination thereof.
3. The multicomponent latent-crimping staple fiber according to
claim 1, wherein the second component comprises a polymer selected
from the group consisting of a polyamide, a sulfur-containing
polymer, an aromatic polyester, an aliphatic polyester, a
polyolefin, and a combination thereof.
4. The multicomponent latent-crimping staple fiber according to
claim 1, wherein the multicomponent latent-crimping staple fiber is
selected from a heat-crimped fiber, a humidity-crimped fiber, a
water-crimped fiber, a light-crimped fiber, and a combination
thereof.
5. The multicomponent latent-crimping staple fiber according to
claim 1, wherein the multicomponent latent-crimping fiber is
extruded and drawn to optimize tenacity
6. The multicomponent latent-crimping staple fiber according to
claim 1, wherein the tenacity is the tenacity at break.
7. The multicomponent latent-crimping staple fiber according to
claim 1, wherein the tenacity is the tenacity at 7% elongation.
8. (canceled)
9. The multicomponent latent-crimping staple fiber according to
claim 1, wherein the first component comprises nylon, wherein the
second component comprises nylon, wherein the tenacity at break
prior to crimping is at least 5.5 g/denier, wherein the tenacity at
7% elongation prior to crimping is at least 1.3 g/denier, wherein
the tenacity at break after crimping is at least 90% of the
tenacity at break prior to crimping, and wherein the tenacity at 7%
elongation after crimping is at least 90% of the tenacity at 7%
elongation prior to crimping.
10. A fabric comprising the multicomponent latent-crimping staple
fiber according to claim 1.
11.-14. (canceled)
15. A non-mechanically-crimped staple fiber comprising: A. a first
component comprising: i. a first length; and ii. a first
cross-sectional center of mass; and B. a second component
comprising: i. a second length; and ii. a second cross-sectional
center of mass, wherein the shrinkage differential between the
first length and the second length is at least 0.01%, and wherein
the first cross-sectional center of mass and the second
cross-sectional center of mass are eccentric, wherein the first
component and the second component are extruded to form a
non-mechanically-crimped fiber, wherein the
non-mechanically-crimped fiber is cut to form a
non-mechanically-crimped staple fiber, wherein the
non-mechanically-crimped fiber is crimped either before, during, or
after cutting, and wherein the non-mechanically-crimped staple
fiber has a tenacity of at least about 90% as compared to the
tenacity of the non-mechanically-crimped fiber prior to
crimping.
16. The non-mechanically-crimped staple fiber according to claim
15, wherein the first component comprises a polymer selected from
the group consisting of a polyamide, a sulfur-containing polymer,
an aromatic polyester, an aliphatic polyester, a polyolefin, and a
combination thereof.
17. The non-mechanically-crimped staple fiber according to claim
15, wherein the second component comprises a polymer selected from
the group consisting of a polyamide, a sulfur-containing polymer,
an aromatic polyester, an aliphatic polyester, a polyolefin, and a
combination thereof.
18. The non-mechanically-crimped staple fiber according to claim
15, wherein the multicomponent latent-crimping staple fiber is
selected from a heat-crimped fiber, a humidity-crimped fiber, a
water-crimped fiber, a light-crimped fiber, and a combination
thereof.
19. The non-mechanically-crimped staple fiber according to claim
15, wherein the multicomponent latent-crimping fiber is extruded
and drawn to optimize tenacity
20. The non-mechanically-crimped staple fiber according to claim
15, wherein the tenacity is the tenacity at break.
21. The non-mechanically-crimped staple fiber according to claim
15, wherein the tenacity is the tenacity at 7% elongation.
22. The non-mechanically-crimped staple fiber according to claim
15, wherein the first component is nylon 6, 6, with a relative
viscosity of from about 30 to about 60, wherein the second
component is nylon 6, 6, with a relative viscosity of from about 50
to about 130, and wherein the relative viscosity of the second
component is at least 20 higher than the relative viscosity of the
first component.
23. The non-mechanically-crimped staple fiber according to claim
15, wherein the tenacity at 7% elongation is at least 1.3 g/denier
prior to non-mechanically crimping, and wherein the tenacity at 7%
elongation after non-mechanically-crimping is at least 70% of the
tenacity at 7% elongation prior to non-mechanically crimping.
24. The non-mechanically-crimped staple fiber according to claim
15, wherein the tenacity at break is at least 5.5 prior to
non-mechanically crimping, and wherein the tenacity at break after
non-mechanically-crimping is at least 70% of the tenacity at break
prior to non-mechanically crimping.
25. The non-mechanically-crimped staple fiber according to claim
15, wherein the first component, the second component, or both the
first component and the second component comprises a polyphenylene
sulfide.
26. The non-mechanically-crimped staple fiber according to claim
15, wherein the first component comprises nylon, wherein the second
component comprises nylon, wherein the tenacity at break prior to
crimping is at least 5.5 g/denier, wherein the tenacity at 7%
elongation prior to crimping is at least 1.3 g/denier, wherein the
tenacity at break after crimping is at least 90% of the tenacity at
break prior to crimping, and wherein the tenacity at 7% elongation
after crimping is at least 90% of the tenacity at 7% elongation
prior to crimping.
27. A fabric comprising the non-mechanically-crimped staple fiber
according to claim 15.
28. A garment comprising the non-mechanically-crimped staple fiber
according to claim 15.
Description
CROSS-REFERENCE TO RELATED APPLICATIONS
[0001] This application claims the benefit of U.S. Provisional
Application No. 62/579,190 filed Oct. 31, 2017, the disclosure of
which is incorporated by reference in its entirety.
FIELD OF THE INVENTION
[0002] The present invention relates to artificial (a.k.a.,
synthetic or man-made) fibers. More specifically, the present
invention relates to self-crimping or latent-crimping artificial
fibers.
BACKGROUND
[0003] Artificial fibers are typically spun, drawn, and textured
prior to being spun into a yarn. Often such artificial fibers are
textured by crimping prior to use as crimping provides benefits
such as improved skin feel, softness, stretch, fluffiness, etc. to
the fibers. Crimping may also be required in order to card/spin the
fibers into a yarn. Traditionally, crimping is achieved via a
mechanical crimping tool or machine (e.g., a stuffer-box crimper)
which physically compresses some parts of the fiber so as to
achieve a wavy pattern in the fiber. Such crimps typically form
such a wavy pattern by forming a sharp bend in the fiber at various
intervals. However, it has now been found that such sharp bends and
deformation of the fiber results in reduced fiber strength.
[0004] Multicomponent, latent-crimp artificial fibers formed from
polymers are known. Such artificial fibers tend to be synthetic
fibers formed of man-made polymers such as polyethylene,
polypropylene, polyurethanes, polyesters, etc., and the
latent-crimping is typically formed by using, for example, polymers
of different viscosities, different melt temperatures, different
thicknesses, different fiber shapes, etc. which then form crimps or
in some cases, a continuous curl(s) in the case of many
latent-crimping fibers, when the fibers are exposed to heat,
humidity, mechanical stretching, etc. Such artificial fibers are
typically long fibers, such as tow fibers, continuous filament
yarns, etc. The typical goal of such latent-crimp fibers is to
increase fiber bulk without having to mechanically crimp the fibers
thereby avoiding a processing step, and/or avoiding a step which
limits the throughput speed. Other times there may be a desire to
cause the fiber to curl after a fabric is formed, so as to develop
bulk in the fabric.
[0005] Such multicomponent, latent-crimp artificial fibers may be
used in, for example non-woven fabrics, spun-bound fabrics, and the
like as well as yarns, and woven fabrics. These may then be further
processed into a variety of products ranging from garments to
carpeting, diapers, drapes, personal care items, industrial
components, tires, linens, etc.
[0006] While bulk and fluffiness are typically an important
characteristic of artificial fibers, depending on the intended use,
additional characteristics such as hydrophobicity, hydrophilicity,
tenacity, acid resistance, colorability, stain resistance,
durability to laundering, abrasion resistance, etc. may also be
desirable. However, current multicomponent, latent-crimp fibers do
not have very high tenacity. Furthermore, typical latent-crimp
fibers do not consist of exclusively polyamide fibers but may
instead include a selection of many polymers.
[0007] In certain specialized fabric applications such as military
apparel, protective apparel, workwear, etc., fibers may require
both high tenacity as well as abrasion resistance. Abrasion
resistance, at least in polyamides, is typically correlated with
tenacity, and is understood to be caused by a high tenacity, or
more precisely, caused by the same molecular morphology within the
fiber that results in a high tenacity. However, current
multicomponent latent-crimp artificial fibers may suffer problems
such as low tenacity, expensive equipment requirements, complex
processing steps, etc. Without intending to be limited by theory,
it is believed that previous processes have not sought to optimize
the tenacity of the fibers using various techniques, formulas, etc.
while also forming a latent-crimping fiber. We further believe that
such a process has not been optimized in the production of a staple
fiber process.
[0008] Continuous filament processes typically do not use
stuffer-box crimping because the continuous filament processes
typically need to run at speeds above those at which stuffer-box
crimping can effectively operate. So continuous filament processes
typically rely on latent crimping or use hot air and agitation in a
process common in carpet yarns, known as "bulked continuous
filament" (BCF) processes. In some continuous filament processes, a
mechanical texturizing process also imparts discrete bends into the
fibers.
[0009] In contrast, staple fiber processes typically do not use
latent crimping because they are slow enough to accommodate
stuffer-box crimping which is technically easier and standard in
the industry. Staple fibers will typically be carded and thus
require crimping less for softness than for their ability to hold
together in and after the carding process because of the crimping.
Other existing staple fibers require mechanical crimping, which has
now been found to result in a loss of tenacity as compared to the
original fiber. Similarly, existing commercial nylon staple fibers
and yarns made therefrom, such as those that are "micro-kinked"
(e.g., "Type 420" high tenacity nylon 6, 6 by Invista) are
high-tenacity staple fibers that are reportedly neither
latent-crimped nor fully-mechanically-crimped. Allegedly these
micro-kinked fibers are produced via an expensive and unwieldy
process which is responsible for imparting the micro-kinks.
However, because these fibers are not crimped nor curled in the
conventional sense, they cannot be carded by themselves without
loading the card. Instead, the micro-kinked fibers must be blended
with, for example, cotton so that the naturally crimped cotton
fibers will carry the fibers through the card. And even so, even
these fibers do require a minimum amount of crimp, imparted in a
reportedly expensive and unwieldy "micro-kinking" process.
[0010] Accordingly, there remains a need for staple fibers having a
latent crimp that possess improved tenacity, lower production
costs, reduced complexity, and/or that can be made with standard
staple fiber production equipment and simpler, less expensive, and
less labor-intensive production processes. The need also exists for
high-tenacity polyamide fibers such as nylon, that possess a latent
crimp. The need also exists for a high-tenacity staple fiber which
is suitable for carding and does not require blending with other
crimped fibers.
SUMMARY OF THE INVENTION
[0011] In an embodiment of the present invention, a multicomponent
latent-crimping staple fiber contains a first component and a
second component. The first component has a first length and a
first cross-sectional center of mass. The second component has a
second length and a second cross-sectional center of mass. The
shrinkage differential between the first length and the second
length is at least 0.01%, based on the lower shrinkage rate polymer
component. The first cross-sectional center of mass and the second
cross-sectional center of mass are eccentric. Furthermore, the
first component and the second component are extruded to form a
multicomponent latent-crimping fiber, and the multicomponent
latent-crimping fiber is cut to form a multicomponent
latent-crimping staple fiber. The multicomponent latent-crimping
staple fiber is crimped either before, during, or after cutting,
and the multicomponent latent-crimping staple fiber has a tenacity
of at least about 90% as compared to the tenacity of the
multicomponent latent-crimping fiber prior to crimping.
[0012] In an embodiment of the present invention, a method for
forming a staple fiber contains the steps of melting a first
component, melting a second component, combining the first
component with the second component, extruding the first component
and the second component from an extrusion die to form a fiber,
drawing the fiber to form a drawn fiber, non-mechanically crimping
the drawn fiber to form a crimped fiber, and cutting the fiber to
form a staple fiber. In this process, the extruding step may occur
before the combining step, after the combining step, or
simultaneously with the combining step. In addition, the cutting
step may be occur before or after the non-mechanically crimping
step.
[0013] In an embodiment of the present invention, a
non-mechanically-crimped staple fiber contains a first component
and a second component. The first component has a first length and
a first cross-sectional center of mass. The second component has a
second length and a second cross-sectional center of mass. The
shrinkage differential between the first length and the second
length is at least 0.01%, based on the lower shrinkage rate polymer
component and the first cross-sectional center of mass and the
second cross-sectional center of mass are eccentric. The first
component and the second component are extruded to form a
non-mechanically-crimped fiber. The non-mechanically-crimped fiber
is cut to form a non-mechanically-crimped staple fiber, where the
non-mechanically-crimped fiber is crimped either before, during, or
after cutting. The non-mechanically-crimped staple fiber has a
tenacity of at least about 90% as compared to the tenacity of the
non-mechanically-crimped fiber prior to crimping.
[0014] Without intending to be limited by theory it is believed
that the present invention may provide, for example, a
multicomponent or non-mechanically-crimped staple fiber which is
cardable without mechanical crimping, a multicomponent or
non-mechanically-crimped staple fiber which has a higher tenacity
than a comparable mechanically-crimped fiber, a process with
improved speed, a process with reduced complexity, a process which
allows high tenacity staple fibers to be made with standard
equipment, a process that avoids the expense and complexity of
micro-kinking, a less labor-intensive process, and/or a
multicomponent or non-mechanically-crimped staple fiber which is
more easily blended with other fibers. It is further believed that
these fibers, multicomponent staple fibers,
non-mechanically-crimped staple fibers, etc. are especially
suitable for use in fabrics which require a high tenacity, such as
protective garments and work clothes.
BRIEF DESCRIPTION OF THE DRAWINGS
[0015] FIG. 1 shows a cross-sectional view of an embodiment of a
fiber of the present invention having a dumbbell-shaped
cross-section;
[0016] FIG. 2 shows a cross-sectional view of an embodiment of a
fiber of the present invention having a circular-shaped
cross-section;
[0017] FIG. 3 shows a cross-sectional view of as embodiment of a
fiber of the present invention having a circular-shaped
cross-section;
[0018] FIG. 4 shows a cross-sectional view of an embodiment of a
fiber of the present invention having a snowman-shaped
cross-section;
[0019] FIG. 5 shows a cross-section view of an embodiment of a
fiber of the present invention having a bowtie-shaped
cross-section;
[0020] FIG. 6 shows a cross-sectional view of an embodiment of a
fiber of the present invention having a trilobal-shaped
cross-section;
[0021] FIG. 7 shows a cross-sectional view of an embodiment of a
fiber of the present invention having an oval-shaped
cross-section;
[0022] FIG. 8 shows a cross-sectional view of an embodiment of a
fiber of the present invention having an oval-shaped
cross-section;
[0023] FIG. 9 shows a cross-sectional view of an embodiment of a
fiber of the present invention having a circular-shaped
cross-section and multiple components therein;
[0024] FIG. 10 shows a perspective view of an embodiment of a fiber
of the present invention; and
[0025] FIG. 11 shows a simplified view of an embodiment of a fiber
showing the aggregate center of mass.
[0026] The figures herein are for illustrative purposes only and
are not necessarily drawn to scale.
DESCRIPTION OF THE PREFERRED EMBODIMENTS
[0027] Unless otherwise specifically provided, all tests herein are
conducted at standard conditions which include a room and testing
temperature of 25.degree. C., sea level (1 atm.) pressure, pH 7,
35% relative humidity, and all measurements are made in metric
units. Furthermore, all percentages, ratios, etc. herein are by
weight, unless specifically indicated otherwise.
[0028] As used herein, the term "shrinkage differential", .DELTA.S,
indicates the percent difference in length of the polymer component
occupying the inner surface of the helix formed by the curled fiber
and the polymer component occupying the outer surface of the helix
formed by the curled fiber, divided by the length of the polymer
component occupying the outer inner surface of the helix formed by
the curled fiber. As one skilled in the art understands, when these
are extruded/combined, these polymers have the same length.
However, upon being non-mechanically-crimped, either by heat,
humidity, etc. as described herein, one polymer component will
shrink more than the other polymer component, thereby causing the
entire fiber to curl and form a helix. Without intending to be
limited by theory, it is believed that in such a situation, the
polymer component which shrinks more will be on the inside/inner
part of the helix while the polymer component which shrinks less
will necessarily be on the outside/outer part of the helix.
[0029] As used herein, the term "mechanical crimping" and
variations thereof such as "mechanically-crimped", refers to
crimping caused by the physical compression of at least a portion
of the fiber, typically with a gear-like roller, zig-zag or wavy
teeth, a machine such as a stuffer-box crimper, and other
mechanical methods and equipment known in the fiber and textile
art. In some cases, a bulked continuous filament (BCF) process may
also include mechanical crimping therein so as to bulk up the
filament and make it fatter, fluffier, etc.
[0030] As used herein, the term "latent-crimping" indicates that
the fiber is designed and formed in a manner such that it may be
crimped without the use of mechanical crimping. Such
latent-crimping is known in the art and may be caused by, for
example, applying heat, humidity, water, etc. to the fiber which
causes the (properly-configured) fiber to curl or crimp.
[0031] As used herein, the term "eccentric" indicates that the
(first, second, etc.) cross-sectional centers of mass are not at
the same point.
[0032] As used herein the term "yarn" typically indicates a
collection or a plurality of continuous filaments and/or staple
fibers held together as a bundle, roughly in parallel. The yarn
typically has a substantially continuous length, such as a length
greater than about 25 cm, and more typically a length of from about
1 meter to even about 10,000,000 meters or more.
[0033] As used herein, it is understood herein that Nomex.TM. by
DuPont is generally representative of meta-aramid polymer fibers,
while Kevlar.TM. by DuPont is generally representative of
para-aramid polymer fibers.
[0034] An embodiment of the present invention relates to a
multicomponent latent-crimping staple fiber containing a first
component and a second component. The first component has a first
length and a first cross-sectional center of mass. The second
component has a second length and a second cross-sectional center
of mass. The shrinkage differential, .DELTA.S, is the percentage
difference of the first length and the second length, as described
herein, and is at least 0.01%. For an explanation about the
shrinkage differential and the calculation thereof, please see FIG.
10 and the discussion therefor. Also, the first cross-sectional
center of mass and the second cross-sectional center of mass are
eccentric.
[0035] It is further understood that in a multicomponent fiber, the
components are typically arranged in the fiber such that they
define a specific spatial arrangement within the fiber's cross
section. Furthermore, this specific spatial arrangement typically
does not vary significantly along the entire length of the fiber.
As a result, any discussion of centers of mass of the components in
such a multi-component fiber defines a specific cross-sectional
arrangement, and not a specific feature that involves changes in
the fiber's cross section along its length.
[0036] Another embodiment of the present invention relates to a
non-mechanically-crimped staple fiber containing a first component
and a second component. The first component has a first length and
a first cross-sectional center of mass. The second component has a
second length and a second cross-sectional center of mass. The
shrinkage differential between the first length and the second
length is at least 0.01%, based on the lower shrinkage rate polymer
component. Also, the first cross-sectional center of mass and the
second cross-sectional center of mass are eccentric.
[0037] Another embodiment of the present invention relates to a
method of forming a staple fiber by the steps of melting a first
component, melting a second component, combining the first
component with the second component, extruding the first component
and the second component from an extrusion die to form a fiber,
drawing the fiber to form a drawn fiber, non-mechanically crimping
the drawn fiber to form a crimped fiber, and cutting the crimped
fiber to form a staple fiber. In this process, the extruding step
may occur before the combining step, after the combining step, or
simultaneously with the combining step. As used herein, the
"combining step" indicates where different molten polymer streams
and/or fibers/streams extruded from the spinnerets are combined
together to form a single fiber. If the combining step occurs when
the polymer streams are molten, then this typically occurs
immediately before, or simultaneously with, the extruding step.
[0038] Another embodiment of the present invention relates to a
method of forming a staple fiber by the steps of melting a first
component, melting a second component, combining the first
component with the second component, extruding the first component
and the second component from an extrusion die to form a fiber,
drawing the fiber to form a drawn fiber, cutting the drawn fiber to
form a cut fiber, and non-mechanically crimping the cut fiber to
form a crimped fiber. In this process, the extruding step may occur
before the combining step, after the combining step, or
simultaneously with the combining step.
[0039] Another embodiment of the present invention relates to a
method for forming a continuous web or a sliver by the steps of
melting a first component, melting a second component, combining
the first component with the second component, extruding the first
component and the second component from an extrusion die to form a
fiber, drawing the fiber to form a drawn fiber, non-mechanically
crimping the drawn fiber to form a crimped fiber, cutting the
crimped fiber to form a staple fiber, optionally blending with one
or more other fibers, and carding the staple fiber to form a
continuous web or sliver.
[0040] In an embodiment of the method of the present invention, the
combining step takes place immediately prior to the extrusion step.
In such a case the combining step is conducted when the polymers
are molten polymer streams.
[0041] In another embodiment of the method herein, the combining
step and the extruding step are simultaneous. In such a case the
combining step is conducted when the polymers are molten polymer
streams. The extrusion dies, spinnerets, etc. useful in such a
method are well-known in the art.
[0042] In an embodiment herein the combining step occurs after; or
immediately after the extruding step so as to avoid or minimize the
possibility of the blending of the first component and the second
component into a single homogenous mixture. The multicomponent
fiber useful herein is a fiber having a plurality of components;
typically a first component, a second component, a third component,
etc. In an embodiment herein the components contain a polymer; or a
plurality of polymers. In an embodiment herein, the first component
includes a polymer; or a polymer selected from the group consisting
of a polyamide, a sulfur-containing polymer, an aromatic polyester,
an aliphatic polyester, a polyolefin, and a combination thereof; or
a polyamide, a polyphenylene sulfide, a polyarylene terephthalate,
a polyarylene isopthalate, a polylactic acid, a
polyhydroxyalkanoate an aliphatic polyester, a polypropylene, a
polyethylene, a polymethylpentene, and a combination thereof; or
nylon, polyphenylene sulfide, polyethylene terephthalate,
polylactic acid, poly propylene, and a combination thereof; or
nylon 6, 6, polyphenylene sulfide, and a combination thereof. As
used herein with respect to the polymers, the term "a combination
thereof" specifically includes copolymers, homopolymers, and blends
thereof.
[0043] In an embodiment herein, the second component includes a
polymer; or a polymer selected from the group consisting of a
polyamide, a sulfur-containing polymer, an aromatic polyester, an
aliphatic polyester, a polyolefin, and a combination thereof; or a
polyamide, a polyphenylene sulfide, an aromatic polyester, an
aliphatic polyester, a polyolefin, and a combination thereof; or
nylon, polyphenylene sulfide, an aromatic polyester, an aliphatic
polyester, a polyolefin, and a combination thereof; or nylon 6,
nylon 6,6, polyphenylene sulfide, and a combination thereof.
[0044] In an embodiment herein, the first component contains; or
is, nylon 66 and the second component contains; or is, nylon
66.
[0045] In an embodiment of the present invention the first
component and second component may be chemically the same, in an
alternate embodiment, they are chemically different. In an
embodiment herein, the weight ratio of the first component to the
second component in the fiber; or staple fiber; or multicomponent
latent-crimping staple fiber; or non-mechanically-crimped staple
fiber, is from about 10:90 to about 90:10; or from about 30:70 to
70:30; or from about 40:60 to about 60:40.
[0046] In an embodiment herein, a plurality of components; or the
first component; the second component; the third component, etc.
contain a polyamide having a relatively high molecular weight, as
indicated by having a relative viscosity of about 50 to about 300;
or about 55 to about 250; or about 60 to about 200 as measured
according to the Brookfield Method described in ASTM D789,
D4878.
[0047] In an embodiment herein, the first component has a first
molecular weight, as indicated by having a relative viscosity of
from about 50 to about 300; or about 55 to about 250; or about 60
to about 200.
[0048] In an embodiment herein, the second component has a second
molecular weight, as indicated by having a relative viscosity of
from about 5 to about 200; or from about 10 to about 175; or from
about 20 to about 140.
[0049] In an embodiment herein, the first molecular weight and the
second molecular weight have relative viscosities that respectively
differ by at least 10.
[0050] One skilled in the art understands that polyesters generally
measure molecular weight via inherent viscosity, polyamides
generally measure molecular weight via relative viscosity, and that
other polymers generally use melt flow index to indicate relative
differences in molecular weight. Molecular weight is also measured
by the actual atomic weight of the polymer, such as via, for
example, the number molecular weight. In an embodiment herein, the
molecular weight of the polymer in the first component and the
polymer in the molecular weight of the second component differ by
at least 5 percent as compared to the polymer having the higher
molecular weight.
[0051] In an embodiment herein, the term "optimized tenacity" and
variants thereof indicates that for an aromatic polyester the
aromatic polyester has a minimum inherent viscosity of about 0.6;
or at least about 0.7, for at least one of the first component or
the second component. One skilled in the art understands that the
other component could have a lower inherent viscosity.
[0052] In an embodiment herein the term "optimized tenacity" and
variants thereof indicates that for a polyolefin, the polyolefin
has a melt flow index of about 25 or less; or about 18 or less, for
at least one of the polymers in the first component or the second
component.
[0053] In an embodiment herein, the term "optimized tenacity" and
variants thereof indicates for a nylon or a polyphenylene sulfide,
the nylon or the polyphenylene sulfide has a maximum Melt Flow
Index of about 180; or a maximum Melt Flow Index of about 130.
[0054] In all instances, the term "optimized tenacity" and variants
thereof may additionally include not just formulation-related
details, but also process-related steps such as drawing.
[0055] One skilled in the art understands that using MFI to
designate relative polymer viscosities is further complicated by
the fact that the standard MFI test, ASTM D1238, uses different
test conditions for different classes of polymers. For example, for
polyphenylene sulfide, the test conditions are 316.degree. C. and a
5 kg weight, for polypropylene the test conditions are 230.degree.
C. and a 2.16 kg weight, and for high density polyethylene it is
190.degree. C. and a 2.16 kg weight.
[0056] In an embodiment herein, a plurality of components; or the
first component; the second component; the third component, etc.
contain a polymer; or a nylon; or nylon 6,6 having a relative
viscosity of from about 40 to about 60. In an embodiment herein, a
plurality of components; or the first component; or the second
component; the third component, etc. contain a polymer; or nylon;
or nylon 6,6 having a relative viscosity of from about 70 to about
90. In an embodiment herein, the first component contains nylon 6,
6 having a relative viscosity of from about 40 to about 60, and the
second component contains nylon 6, 6 having a relative viscosity of
from about 70 to about 90.
[0057] In an embodiment herein the relative viscosity of the first
component and the relative viscosity of the second component are
different; or differ by at least about 10; or differ by at least
about 15; or differ by at least about 20; or differ by at least
about 30.
[0058] For the ease of understanding, only a first component and a
second component are specifically described herein. However, one
skilled in the art understands that many, many other components may
also be used herein, such as three components, four components,
five components, etc. as desired.
[0059] In an embodiment herein, the other component each
independently includes a polymer; or a polymer selected from the
group consisting of a polyamide, a sulfur-containing polymer, an
aromatic polyester, an aliphatic polyester, a polyolefin, and a
combination thereof; or a polyamide, a polyphenylene sulfide, an
aromatic polyester, an aliphatic polyester, a polyolefin, and a
combination thereof; or nylon, polyphenylene sulfide, an aromatic
polyester, an aliphatic polyester, a polyolefin, and a combination
thereof.
[0060] In an embodiment herein, the chemical composition of the
first component and the second component are different. Without
intending to be limited by theory, it is believed that one method
to create different degrees of shrinkage (a.k.a., shrinkage rates)
is to use different polymers for the first component and the second
component.
[0061] In an embodiment herein the chemical composition of the
first component and the second component are the same, and any
difference in the degree of shrinkage is due to a different factor,
such as the molecular weight.
[0062] The method and formula for calculating the shrinkage
differential is discussed herein with respect to FIG. 10.
[0063] In an embodiment herein, the shrinkage differential is
greater than or equal to about 0.01%; or from about 0.01% to about
20%; or at least about 0.3%; or from about 0.3% to about 5%, based
on the lower shrinkage rate polymer component.
[0064] One skilled in the art understands that each individual
fiber herein inherently possesses a cross-section and therefore
also possesses a cross-sectional shape as described herein. The
cross-section is defined as a view or cut perpendicular to the long
axis of the fiber(s). The cross-sectional shape, which therefore
corresponds to the cross-section is the shape formed by the fiber
if it is cut, either in reality or virtually, at the
cross-section.
[0065] In an embodiment herein, a plurality of different
components; or at least about 2 different components; or each
different component, possesses a different cross-sectional shape.
Without intending to be limited by theory, it is believed that if
components possess different cross-sectional shapes then they will
typically possess different cross-sectional centers of mass, which
in turn may result in them more easily forming crimps in the fiber
when subjected to non-mechanical crimping; or heat crimping; or
humidity-crimping; or moisture/water crimping; or heat
crimping.
[0066] In an embodiment herein, the fiber; or staple fiber; or
multicomponent latent-crimping staple fiber; or
non-mechanically-crimped staple fiber, is crimped by a
non-mechanical method as described herein.
[0067] A fiber cross-section of an embodiment of the present
invention is seen, for example, in FIG. 1. In the embodiment of
FIG. 1, a fiber, 10, is cut perpendicular to the long axis and
shows a double-lobed cross-section, commonly-referred to as a
dumbbell-shaped cross-section. A first component, 20, is connected
to a second component, 22, at the polymer interface, 24, where the
first component, 20, and second component, 22, have been fused
together during, for example a co-extrusion process in which the
first component and the second component are combined together at
the time of extrusion.
[0068] One skilled in the art understands that such a co-extrusion
process is not necessarily required herein, and that the first
component and the second component may be combined before
extrusion; or immediately before extrusion, from an extrusion die,
after extrusion; or immediately after extrusion, from an extrusion
die, or simultaneously during extrusion from the extrusion die. One
skilled in the art understands that in the present invention the
first component and the second component may be brought together
immediately before, during, or after the first component and the
second component move through and are extruded from a single or
separate extrusion die(s). In an embodiment herein, the first
component and the second component are extruded through separate
extruders, after which the polymer streams may be brought into
contact before, during, simultaneously with, or immediately after,
passing through an extrusion die.
[0069] Regardless of when the first component and the second
component are combined, they typically become permanently fused
together; or become permanently fused together before they
solidify, so as to form a single fiber. Such a fiber is generally
known as a bicomponent fiber if there are only two components, or a
multicomponent fiber if there are two or more components.
[0070] The fiber herein is non-mechanically crimped (i.e., without
employing mechanical crimping resulting in physical compression of
the fiber). Thus, the crimping may be caused by a factor, typically
an externally-applied factor, such as heat, humidity, water, light,
and combination thereof; or heat, humidity, water, and a
combination hereof; or heat, humidity and a combination hereof; or
heat. Thus, the fiber may be categorized as a heat-crimped fiber, a
humidity-crimped fiber, a water-crimped fiber, a light-crimped
fiber, etc.
[0071] In an embodiment herein, the non-mechanical crimping is
caused by heat. Without intending to be limited by theory, it is
believed that heat is more flexible in that heat can cause crimping
in just about any combination of different polymers, even, for
example, if the polymers are chemically the same but differ only in
molecular weight. In contrast, moisture only causes crimping for a
few specific polymer pairs. Furthermore, it is believed that
moisture-activated curling is reversible, so it may not generally
be useful to have a fiber that curls and is cardable only when wet,
or in humid conditions, but not when dry.
[0072] In an embodiment herein, the crimping is caused by a
difference in the shrinkage rate of the first component and the
second component. Without intending to be limited by theory it is
believed that this is caused by the difference in relaxation of the
different polymers that have been stretched out in the prior
processing to increase their tenacity. In some cases there is
sufficient ambient thermal energy to allow sufficient shrinkage by
merely releasing the tension on the fibers; however, one skilled in
the art understands that in other cases, some additional heating is
beneficial to achieve this effect.
[0073] One skilled in the art understands that fibers that crimp in
response to moisture use differences in swelling caused by
spontaneous moisture uptake. Without intending to be limited by
theory it is believed that this requires a substantial difference
in chemical nature between the two polymers (such as between nylon
and polypropylene) but is not typically dependent on differences in
molecular weight. Furthermore, it is believed that this will not
typically occur in polymers with the same chemical formula (such as
two different nylons) regardless of molecular weights.
[0074] The crimping degree useful herein may range from about 1
curl per 2.54 cm to about 100 curls per 2.54 cm; or from about 2
curls per 2.54 cm to about 50 curls per 2.54 cm; or from about 2
curls per 2.54 cm to about 24 curls per 2.54 cm. The crimping
degree is typically measured by eye for curled fibers. For the
crimped; or non-mechanically-crimped fibers herein, the number of
curl peaks and valleys is counted (i.e., the center of one peak,
through one valley to the center of the next peak defines 360
degrees of rotation of the fiber seen from the end) rather than
"v-shaped" peaks and valleys. Preferably this is conducted
according to ASTM D3937, where the word "curls" is substituted for
"crimps", as some definitions of "crimps" require the fiber to be
"bent" in a sudden (i.e., sharp) angle change, rather than a
gradual change which is more representative of the present
invention.
[0075] Tenacity is an industry-standard test which measures the
strength of a fiber, for example, until break or under a standard
elongation of, for example, 7%. DIN 53816 is a standard test method
with an automated Favimat machine available from TexTechno H. Stein
GmbH & Co. KG, of Moenchengladbach, Germany, which provides
instructions to run the test therewith. In the tenacity test,
multiple fibers (10 to 20) are typically tested and the results
averaged to produce an average tenacity. Tenacity is the force
divided by the fiber denier or decitex (linear density, or grams
per 9000 m in the case of denier, or grams per 10000 m in the case
of decitex). Most typically, tenacity is measured at the break
point of the fiber, but for fibers to be blended with cotton in
spun yarns, it is important to measure the tenacity at 7%
elongation of the fiber (typically long before the break point)
because the cotton fibers will typically break at 7% elongation so
it is important to know how much strength the non-cotton fiber will
provide at the point at which the cotton no longer contributes to
the strength of the yarn.
[0076] In an embodiment herein, the fiber; or the staple fiber; or
the multicomponent latent-crimping staple fiber; or the
non-mechanically-crimped staple fiber, has a tenacity at break of
greater than or equal to about 5 g/denier; or greater than or equal
to about 6 g/denier; or greater than or equal to about 6.3
g/denier.
[0077] In an embodiment herein the fiber; or the staple fiber; or
the multicomponent latent-crimping staple fiber; or the
non-mechanically-crimped staple fiber, has a tenacity at 7%
elongation of greater than or equal to about 0.5 g/denier; or
greater than or equal to about 1.1 g/denier; greater than or equal
to about 1.3 g/denier; or greater than or equal to about 1.4
g/denier; or greater than or equal to about 2 g/denier; or greater
than or equal to about 2.2 g/denier.
[0078] In an embodiment herein, the fiber; or the staple fiber; or
the multicomponent latent-crimping staple fiber; or the
non-mechanically-crimped staple fiber, or the multicomponent
latent-crimping staple fiber; or the non-mechanically-crimped
staple fiber, has a tenacity at break of greater than or equal to
about 5 g/denier; or greater than or equal to about 6 g/denier; or
greater than or equal to about 6.3 g/denier and further also has a
tenacity at 7% elongation of greater than or equal to about 0.5
g/denier; or greater than or equal to about 1.1 g/denier; greater
than or equal to about 1.3 g/denier; or greater than or equal to
about 1.4 g/denier; or greater than or equal to about 2 g/denier;
or greater than or equal to about 2.2 g/denier.
[0079] In an embodiment herein the fiber; or the staple fiber; or
the multicomponent latent-crimping staple fiber; or the
non-mechanically-crimped staple fiber, or the multicomponent
latent-crimping staple fiber; or the non-mechanically-crimped
staple fiber, has a crimp index of from about 0.99 to about 0.1; or
from about 0.95 to about 0.5. As used herein, crimp index is
measured by the difference between the stretched length and the
unstretched (i.e., relaxed) length, according to the formula:
crimp index=100*(L.sub.0-L.sub.c)/(L.sub.0).
where L.sub.0 is the stretched length in cm and L.sub.c is the
unstretched or original length in cm (as measured before pulling
the fiber out straight).
[0080] Without intending to be limited by theory, it is believed
that mechanical crimping of fibers, especially mechanical crimping
of fibers which compresses the fiber in the direction perpendicular
to the longest axis of the fiber creates a localized bend point in
the fiber, which concentrates the bending forces at the specific
points where the bend is located. The focusing of the deformation,
and even fiber/polymer damage, to a specific point in turn
increases the stress at that point which leads to reduced tenacity
and weakness of the fiber. In contrast, a non-mechanically-crimped
fiber does not possess impaired plasticity as the deformation is
substantially continuous and gradually distributed along the entire
length, which in turn distributes the stresses more evenly. Thus,
for example, it has been found that depending on the actual test,
the mechanical crimping can result in a significant tenacity
reduction of over 10%, with some fibers even resulting in a
tenacity reduction of over 40%, as compared to the uncrimped fiber.
Accordingly, it has been found that the use of standard
high-tenacity staple fiber production methods to produce a
high-tenacity staple fiber that is then mechanically crimped
results in fibers that lack the tenacity required for high
durability fabrics, such as those required in military, law
enforcement, and workwear uses. Instead, as noted above,
specialized equipment and/or processing is required to impart
micro-kinks into a high-tenacity fiber in order to impart
cardability sufficient for blending with cotton fibers without
sacrificing tenacity significantly. However, such a specialized
process increases the cost and decreases the availability of such
fibers and yarns, fabrics, etc. made therefrom. Furthermore, the
Applicant's testing shows that such a process still does not result
in a fiber that is sufficiently well-crimped to enable carding
without blending with other crimped fibers, such as cotton.
[0081] In contrast, it is believed that the fibers that are
non-mechanically-crimped and are instead crimped via applying, for
example, heat, humidity, water, etc. do not suffer from such a
reduced tenacity because they avoid the physical damage and/or the
focused stresses of a localized bend point caused by mechanical
crimping tools and the associated fiber compression process.
Therefore, it is believed that the multicomponent latent-crimping
staple fibers and the non-mechanically-crimped staple fibers of the
present invention may possess significantly higher tenacity than
comparable mechanically-crimped fibers; or comparable
mechanically-crimped staple fibers. Furthermore, it is believed
that the multicomponent latent-crimping staple fibers and the
non-mechanically-crimped staple fibers of the present invention may
more evenly distribute the stresses imparted on the fiber, and
therefore may possess improved and/or higher tenacities.
[0082] Without intending to be limited by theory, it is also
believed that the multicomponent latent-crimping staple fibers and
the non-mechanically-crimped staple fibers of the present invention
may possess significantly higher tenacity than comparable
mechanically-crimped fibers; or comparable mechanically-crimped
staple fibers because they do not undergo any physical damage or
other significant molecular rearrangement due to the stresses
caused by the bending at the points where mechanical crimpers
pinch/compress and therefore potentially weaken the fiber.
[0083] In an embodiment herein, the fiber; or the staple fiber; or
the multicomponent latent-crimping staple fiber; or the
non-mechanically-crimped staple fiber, herein has a tenacity at
break prior to crimping and a tenacity at break after crimping. In
an embodiment herein the tenacity at break after crimping is
greater than or equal to about 90%; or greater than or equal to
about 92%; or greater than or equal to about 94%; or greater than
or equal to about 95%, to less than or equal to about 120%; or less
than or equal to about 100%; or less than or equal to about 99%; or
less than or equal to about 98%; or less than or equal to about 97%
of the tenacity at break prior to crimping according to ASTM D3822.
We note that due to measurement inconsistencies, and/or differences
between specific fibers and locations, or actual increase of fiber
strength after non-mechanical crimping, it is possible that the
tenacity at break after crimping could actually appear to increase,
or could in fact increase above 100% of the tenacity at break prior
to crimping. The tenacity at break after crimping is calculated as
a percentage according to the following equation: [(tenacity at
break prior to crimping-tenacity at break after
crimping).times.100]/[tenacity at break prior to crimping].
[0084] In an embodiment herein, the fiber; or the staple fiber; or
the multicomponent latent-crimping staple fiber; or the
non-mechanically-crimped staple fiber, herein has a tenacity at 7%
elongation prior to crimping and a tenacity at 7% elongation after
crimping. In an embodiment herein the tenacity at 7% elongation
after crimping is greater than or equal to about 60%; or greater
than or equal to about 65%; or greater than or equal to about 68%;
or greater than or equal to about 70%; or greater than or equal to
about 85%; or greater than or equal to about 90%, to less than or
equal to 120%; or less than or equal to about 100%; or less than or
equal to about 99%; or less than or equal to about 98%; or less
than or equal to about 97% of the tenacity at 7% elongation prior
to crimping according to ASTM D3822. Similarly, as noted above for
tenacity at break, the tenacity at 7% elongation after crimping may
be greater than 100% of the tenacity at 7% elongation prior to
crimping. The tenacity at 7% elongation after crimping is
calculated as a percentage according to the following equation:
[(tenacity at 7% elongation prior to crimping-tenacity at 7%
elongation after crimping).times.100]/[tenacity at 7% elongation
prior to crimping].
[0085] In an embodiment herein, the fiber; or the staple fiber; or
the multicomponent latent-crimping staple fiber; or the
non-mechanically-crimped staple fiber, herein has a tenacity at
break prior to crimping and a tenacity at break after crimping as
well as a tenacity at 7% elongation prior to crimping and a
tenacity at 7% elongation after crimping. In an embodiment herein
the tenacity at break after crimping is at least about 90%; or at
least about 92%; or at least about 94%; or at least about 95%, to
less than or equal to about 120%; or about 100%; or to about 99%;
or to about 98%; or to about 97% of the tenacity at break prior to
crimping In an embodiment herein, the same fiber; or the same
staple fiber; or the same multicomponent latent-crimping staple
fiber; or the same non-mechanically-crimped staple fiber, has a
tenacity at 7% elongation after crimping that is at least about
60%; or at least about 65%; or at least about 68%; or at least
about 70%; or greater than or equal to about 85%; or greater than
or equal to about 90%, to less than or equal to about 120%; or
about 100%; or to about 99%; or to about 98%; or to about 97% of
the tenacity at 7% elongation prior to crimping.
[0086] In an embodiment herein, the fiber; or staple fiber; or
multicomponent latent-crimp staple fiber; or
non-mechanically-crimped staple fiber; or drawn fiber; or crimped
fiber herein contains a nylon as the first component and a nylon as
the second component. The fiber; or staple fiber; or multicomponent
latent-crimp staple fiber; or non-mechanically-crimped staple
fiber; or drawn fiber; or crimped fiber has a tenacity at break
before crimping of at least 5.5 g/denier; or at least 6 g/denier;
or at least 6.3 g/denier; or at least 6.5 g/denier, and has a
tenacity at 7% elongation prior to crimping of at least 1.3
g/denier; or at least 1.4 g/denier; or at least 1.5 g/denier; or at
least 1.6 g/denier. The tenacity at break after crimping is at
least, 85%; or 90%; or 93%, to less than or equal to about 120%; or
about 100%; or to about 99%; or to about 98%; or to about 97% of
the tenacity at break before crimping. Furthermore, the tenacity at
7% elongation after crimping is at least, 85%; or 90%; or 93%, to
less than or equal to about 120%; or about 100%; or to about 99%;
or to about 98%; or to about 97% of the tenacity at 7% elongation
before crimping.
[0087] In the embodiment of FIG. 1 the cross-section of the first
component, 20, and the cross-section of the second component, 22,
are essentially mirror-images of each other. The first component,
20, contains a first cross-sectional center of mass, 26, while the
second component, 22, contains a second cross-sectional center of
mass, 28. As can be seen in FIG. 1, these points are eccentric as
they are in different locations. Thus it is clear that the first
component and the second component are not coaxial (i.e., they are
eccentric).
[0088] In fact, in FIG. 1, the first cross-sectional center of mass
is on one side of the juncture, 24, while the second
cross-sectional center of mass, 28, is on the other side of the
juncture. One skilled in the art understands that even for
irregular shapes, the center of mass may be easily calculated
using, for example a CAD program or other program known in the
art.
[0089] In an embodiment herein each of the components possesses a
cross-sectional shape, which is the shape of the cross-section when
taken perpendicular to the longest axis of the fiber. Thus, as seen
in FIG. 1, the first cross-sectional shape, 30, is a light
bulb-like shape, and the second cross-sectional shape, 32, is the
same cross-sectional shape, merely a mirror image of the first
cross-sectional shape, 30. When combined together these form a
dumbbell-shaped cross-section.
[0090] Fibers having additional cross-sectional shapes are also
useful herein including, for example, side-by-side non-concentric
circles, snowmen, offset cross-sectional shapes, side-by-side
trilobal fibers or other multilobal fibers, side-by-side ribbon
cross section fibers, side-by-side hollow fibers, etc. may also be
useful herein. In an embodiment herein after non-mechanical
crimping the components; or the first component and the second
component, form a spiral along the length of the fiber; however, it
is recognized that for each individual cross-sectional shape at any
point on the length of the fiber, the specific first
cross-sectional center of mass and the second cross-sectional
center of mass are eccentric. Furthermore, it is understood that
any winding or crimping may not be; or typically is not, inherent
in the cross section when the cross section is first formed. The
person having ordinary skill in the art understands that this
typically only occurs after the two components shrink at different
rates, thereby forming the fiber into a helical curl in which the
two components wind around each other in a spiral.
[0091] FIG. 2 shows a cross-sectional view of an embodiment of a
fiber, 10, herein having a circular-shaped cross-section. In this
embodiment, the first component, 20, and the second component, 22,
are in an eccentric core-sheath arrangement, where the first
cross-sectional center of mass, 26, is outside of the circle formed
by the juncture, 24, while the second cross-sectional center of
mass, 28, is inside of the circle formed by the juncture, 24.
[0092] In the embodiment of FIG. 2, the first cross-sectional
shape, 30, is a crescent-like shape, while the second
cross-sectional shape, 32, is a circle-like shape.
[0093] FIG. 3 shows a cross-sectional view of an embodiment of a
fiber, 10, herein, having a circular-shaped cross-section. The
first component, 20, and the second component, 22, have shapes
similar to a waning moon whose phases are separated by the
juncture, 24, which extends in an arc from almost opposite sides of
the cross-section. In this embodiment, the first cross-sectional
shape, 30, is larger than the second cross-sectional shape, 32. The
first cross-sectional center of mass, 26, is to the left side of
the juncture, 24, while the second cross-sectional center of mass,
28, is on the right side of the juncture.
[0094] FIG. 4 shows a cross-sectional view of an embodiment of a
fiber, 10, herein having a snowman-shaped cross-section. The first
component, 20, and the first cross-sectional center of mass, 26,
are both on the left side of the juncture, 24, while the second
component, 22, and the second cross-sectional center of mass, 28,
are both on the right side of the juncture, 24. The first
cross-sectional shape, 30, is in the shape of a crescent, while the
second cross-sectional shape, 32, is in the shape of a circle.
[0095] FIG. 5 shows a cross-sectional view of an embodiment of a
fiber, 10, herein having a bowtie-shaped cross-section. In this
embodiment, the first component, 20, and the first cross-sectional
center of mass, 26, are again both on the left side of the
juncture, 24, while the second component, 22, and the second
cross-sectional center of mass, 28, are both on the right side of
the juncture, 24. The first cross-sectional shape, 30, is in the
shape of a triangle, while the second cross-sectional shape, 32, is
in the shape of a triangle with a slightly indented tip.
[0096] FIG. 6 shows a cross-sectional view of an embodiment of a
fiber, 10, herein having a trilobal-shaped cross-section. In this
embodiment, the first component, 20, and the first cross-sectional
center of mass, 26 are both above the juncture, 24, while the
second component, 22, and the second cross-sectional center of
mass, 28, are below the juncture, 24. The first cross-sectional
shape, 30, is like an extended oval, while the second
cross-sectional shape, 32, protrudes in two lobes. In this
embodiment, the first component, 20, is overall smaller than the
second component, 22.
[0097] FIG. 7 shows a cross-sectional view of an embodiment of a
fiber, 10, herein having an oval-shaped cross-section. The first
component, 20, and the first cross-sectional center of mass, 30,
are both to the left of the juncture, 24, while the second
component, 22, and the second cross-sectional center of mass, 32,
are to the right side of the juncture, 24. In this case, the first
cross-sectional shape, 30, is a mirror image of the second
cross-sectional shape, 32.
[0098] FIG. 8 shows a cross-sectional view of an embodiment of a
fiber, 10, herein having an oval-shaped cross-section. FIG. 8 is
similar to FIG. 7, except that the juncture, 24, runs horizontally
instead of vertically. The first component, 20, and the first
cross-sectional center of mass, 30, are above the juncture, 24,
while the second component, 22, and the second cross-sectional
center of mass, 32, are below the juncture, 24. In this case, the
first cross-sectional shape, 30, is again a mirror image of the
second cross-sectional shape, 32.
[0099] FIG. 9 shows a cross-sectional view of an embodiment of a
fiber, 10, of the present invention having a circular-shaped
cross-section. In the embodiment of FIG. 9, there are multiple
components such as a second component, 22, a third component, 34,
and a fourth component, 36, etc. inside of the first component, 20.
It is recognized that in an embodiment herein, the second
component, the third component, the forth component, etc. could
each be the same composition and/or shape, or could all be
different as desired. In the embodiment of FIG. 9, the first
component, 20, is the largest by cross-sectional area and encloses
all of the second component, 20, the third component, 34, and the
fourth component, 36, as a sheath.
[0100] The second component, 20, is present as a circular-shaped
cross-sectional shape, 30, having a juncture, 24, and a second
cross-sectional center of mass, 28, therein.
[0101] The third component, 34, is present having an oval third
cross-sectional shape, 38, and a third cross-sectional center of
mass, 40, inside of the third cross-sectional shape, 38. The third
component, 34, contacts and is surrounded by the first component,
20, at the juncture, 24.
[0102] The fourth component, 36, is present having a circular
fourth cross-sectional shape, 42, and a fourth cross-sectional
center of mass, 44, inside of the fourth cross-sectional shape, 42.
The fourth component, 36, contacts and is surrounded by the first
component, 20, at the juncture, 24.
[0103] Thus, it can be seen in FIG. 9 that the proportions, sizes,
shapes, etc. of the various components may be varied considerably
and still fall within the scope of the present invention.
[0104] FIG. 10 shows a perspective view of an embodiment of a
fiber, 10, of the present invention, which in this case is shown so
that the curl can be seen. As noted herein, the curl of the fiber
is caused by the shrinkage differential, .DELTA.S, of the first
component and the second component. During the non-mechanical
crimping step the first component and the second component
typically both shrink, but to a different degree. This results in
the twisting of the 3D conformation of the fiber so that it will
typically form a curled fiber, 46. It is this curl which allows it
to be carded and further processed like a natural fiber. Also,
without intending to be limited by theory, it is believed that the
curled fiber, 46, possesses a very high tenacity as compared to
other comparable fibers which are subjected to a mechanical
crimping process.
[0105] In FIG. 10, for ease of explanation, the first component,
20, is arbitrarily-designated as the polymer having a lower
shrinkage rate, and is therefore on the outer perimeter of the
helix, 48, formed by the curled fiber, 46. Similarly, the second
component, 22, is therefore designated as the polymer having a
higher shrinkage rate, and is therefore on the inner perimeter of
the helix, 48. However, one skilled in the art understands that
depending on the actual composition of the first component and the
second component herein, these may be switched and/or different.
The point is that the polymer component having a lower shrinkage
rate will typically possess a longer length and will therefore be
on the outer perimeter of the helix, while the polymer component
having a higher shrinkage rate will typically be shorter and
therefore will be in the inner perimeter of the helix, as viewed
from the center, C, of the helix, 48.
[0106] In FIG. 10, the first length, L.sub.1, is defined as the
outside length of the (longer) first component for a single
360.degree. rotation of the curled fiber, 46. Similarly, the second
length, L.sub.2, is defined as is defined as the inside length of
the (shorter) second component for a single 360.degree. rotation of
the curled fiber, 46.
[0107] The shrinkage differential, .DELTA.S, is then defined as the
percent difference in length of the polymer component occupying the
inner surface of the helix, 48, formed by the curled fiber, 46, and
the polymer component occupying the outer surface of the helix, 48,
formed by the curled fiber, 46. The general formula for this
calculation is:
.DELTA.S=100*(L.sub.1-L.sub.2)/L.sub.1,
where L.sub.1 is the length of the longer polymer component
(corresponding to the first component in FIG. 10), and L.sub.2 is
the length of the shorter polymer component (corresponding to the
second component in FIG. 10). As noted herein, the longer polymer
component will typically be on the outer edge of the helix, while
the shorter polymer component will typically be on the inner edge
of the helix. While it is recognized that the above designations
are arbitrary, the Applicant believes that it is standard in the
art to place the longer length in the denominator. Accordingly,
this convention is used throughout the application and in all
calculations unless otherwise specifically noted.
[0108] If the first length, L.sub.1, and the second length,
L.sub.2, are directly measurable, then this is preferred. However,
in many cases it is recognized that it will be extremely difficult,
if not impossible to directly measure the first length, L.sub.1,
and the second length, L.sub.2. Accordingly, we also provide herein
the basis for calculating the first length and the second
length.
[0109] Referring to FIG. 10, the distance between corresponding
points on adjacent loops, 50, of the helix, 48, is defined as the
relaxed length, L.sub.r. The relaxed length, L.sub.r, is easily
calculated as the inverse of the number of curls per 2.54 cm. Thus,
10 curls per 2.54 cm would equal a relaxed length of 0.254 cm (or
2.54 mm). This measurement is made (or calculated) when the curled
fiber, 46, is relaxed.
[0110] As seen in FIG. 10, the nominal radius, R.sub.n, is measured
(or calculated) from the center, C, of the helix, 48,
radially-outward to the polymer interface, 24, which in FIG. 10 is
to the center of the curled fiber, 46. This measurement is made (or
calculated) when the curled fiber, 46, is relaxed.
[0111] In FIG. 10, the first component, 20, has a first thickness,
T.sub.1, which is measured (or calculated) from the center of the
polymer interface, 24, outward; or radially-outward (in the
direction away from the center, C, of the helix, 48), to the first
component edge, 52. The first component edge, 52, is the edge of
the fiber, 10, which contains the first component, 20, and which is
furthest from the center, C, of the helix, 48. This measurement is
made (or calculated) when the curled fiber, 46, is relaxed. Unless
otherwise specifically stated, the thicknesses herein are measured
(or calculated) in the direction perpendicular to an imaginary line
drawn to the center, C, of the helix, 48. Furthermore, in FIG. 10,
the line formed by the polymer interface, 24, is also perpendicular
to an imaginary line drawn to the center, C, of the helix, 48.
[0112] Similarly, the second component, 22, has a second thickness,
T.sub.2, which is measured (or calculated) from the polymer
interface, 24, inward; or radially-inward (in the direction towards
the center, C, of the helix, 48), from the second component edge,
54. The second component edge, 54, is the edge of the fiber, 10,
which contains the second component, 20, and which is closest to
the center, C, of the helix, 48. This measurement is made (or
calculated) when the curled fiber, 46, is relaxed.
[0113] In FIG. 10, the first radius, R.sub.1, is measured as the
(radial) distance from the center, C, to the first component edge,
52. This measurement is made (or calculated) when the curled fiber,
46, is relaxed. Alternatively, the first radius, R.sub.1, is
calculated as the nominal radius, R.sub.n, added to the first
thickness, T.sub.1 according to the formula:
R.sub.1=R.sub.n+T.sub.1.
[0114] The second radius, R.sub.2, is measured as the (radial)
distance from the center, C, to the second component edge, 54. This
measurement is made (or calculated) when the curled fiber, 46, is
relaxed. Alternatively, the second radius, R.sub.2, is calculated
as the second thickness, T.sub.2, subtracted from the nominal
radius, R.sub.n, according to the formula:
R.sub.2=R.sub.n-T.sub.2.
[0115] The first length, L.sub.1, is defined as the length of the
(outer, longer) first component edge of the first component, 20,
for a single 360.degree. rotation of the curled fiber, 46. This
measurement is made (or calculated) when the curled fiber, 46, is
relaxed. The first length is calculated by the following
formula:
L.sub.1=[(L.sub.r).sup.2+(2.pi.R.sub.1).sup.2].sup.1/2.
[0116] Similarly, the second length, L.sub.2, is defined as the
length of the (inner, shorter) second component edge, 54, of the
second component, 22, for a single 360.degree. rotation of the
curled fiber, 46. This measurement is made (or calculated) when the
curled fiber, 46, is relaxed. The second length is calculated by
the following formula:
L.sub.2=[(L.sub.r).sup.2+(2.pi.R.sub.2).sup.2].sup.1/2.
[0117] In embodiment such as shown in FIG. 2 where the center of
the polymer interface is not obvious then T.sub.1, and T.sub.2, are
measured (or calculated) from a point, A, which is equidistant from
the first cross-sectional center of mass, 26, and the second
cross-sectional center of mass, 28, along imaginary line A-A
connecting the first cross-sectional center of mass, 26, and the
second cross-sectional center of mass, 28. Specifically, point A is
a distance, x, away from the first cross-sectional center of mass,
26. Point A is also the same distance, x, away from the second
cross-sectional center of mass, 28.
[0118] Assuming, for the sake of convenience, that in FIG. 2 the
first component, 20, has a lower shrinkage rate than the second
component, 22, then the first component, 20, would be towards the
outer edge of the helix (see FIG. 10 at 48) relative to the center,
C, of the helix, 48, while the second component, 22, having a
higher shrinkage rate would be towards the inner edge of the helix
(see FIG. 10 at 48), relative to the center, C, of the helix, 48.
Therefore, in the embodiment of FIG. 2, the first thickness,
T.sub.1, is measured (or calculated) as the distance between point
A, and the first component edge, 52. Similarly, the second
thickness, T.sub.2, is measured (or calculated) as the distance
between point A, and the second component edge, 54.
[0119] FIG. 11 shows a simplified view of an embodiment of a fiber,
10, herein. While the overall cross-sectional shapes are similar to
that of FIG. 9, for the ease of calculation and understanding in
this embodiment, the first component, 20, with a first
cross-sectional shape, 30, surrounds three second components, 22,
22', and 22'', that are all identical in composition, molecular
weight, etc. Each of the second components, 22, 22', and 22'', has
its own respective second cross-sectional center of mass, 28, 28',
and 28'' and own respective second cross-sectional shape, 32, 32',
and 32''. Since these second components, 22, 22', and 22'', are
identical in composition, we may easily find an aggregate center of
mass, 56, mathematically.
[0120] Assuming for the sake of this embodiment that the first
component has a lower shrinkage rate and is therefore on the outer
edge of the helix (see FIG. 10 at 48), as measured from the center
(see FIG. 10 at C) as compared to the second component, then an
imaginary line B-B may be drawn connecting the first
cross-sectional center of mass, 26 and the aggregate center of
mass, 56. Point B is located on line B-B and is equidistant, x,
from the first cross-sectional center of mass, 26 and the aggregate
center of mass, 56. The imaginary line, B-B exits the first
component, 20, at the first component edge, 52. For the purposes of
this embodiment, the aggregated second component edge, 58, is
effectively the point at which the line B-B exits the fiber,
opposite of the first component edge, 52. Therefore first
thickness, T.sub.1 is measured (or calculated) as the distance
between point B and the first component edge, 52. The second
thickness, T.sub.2 is measured (or calculated) as the distance
between point B and the aggregated second component edge, 58. The
respective lengths are therefore measured (or calculated)
accordingly to calculate the shrinkage differential, .DELTA.S.
[0121] Without intending to be limited by theory, it is believed
that the combination of different shrinkage rates and the eccentric
cross-sectional centers of mass of the first component and the
second component ensures that the fiber will crimp and form curls,
typically resulting in a helix, when subjected to non-mechanical
crimping such as heat, humidity, water, etc. as is appropriate. In
an embodiment herein, the curling/crimping in this invention is
driven exclusively by heat, specifically by heating the fiber to a
temperature near or above the glass transition temperature,
T.sub.g, of the component having the lower Tg, which allows the
differential shrinkage in the components
[0122] The fiber; or staple fiber, herein may be formed by standard
staple fiber processes, using standard bicomponent equipment known
in the art.
[0123] In an embodiment herein, two or more thermoplastic polymers
are extruded and brought into an eccentric cross-sectional
relationship in a spinneret capillary. After exiting the spinneret
capillary, the molten polymers are cooled (typically in a crossflow
of chilled air), solidify and are stretched/drawn along the length
of the fiber. These fibers are subsequently drawn further, by
passing the fibers across a set of rollers and subsequently across
another set of rollers running at a faster speed than the first set
of rolls. Typically, heat is applied during this drawing phase to
facilitate the orientation of polymer chains parallel to the long
axis of the fiber.
[0124] In the typical prior art process, after drawing, it is
typical to form crimps in the fibers in a stuffer-box crimping
process. The stretched and crimped fibers may then be heated to dry
off any water from the application of processing finishes, or to
partially heat-set the fibers or pre-shrink them. The fibers are
then cut to a length suitable for downstream processing such as
carding and spun yarn formation.
[0125] In contrast, in the present invention the stuffer-box
crimping step is bypassed, and in the last heating step, the fiber
develops its curl from the shrinkage differential prior to cutting.
It is also conceivable that the fiber could be cut prior to heating
and then crimped/developing the curl.
[0126] Similarly, the continuous web or sliver herein may also be
formed using standard continuous web or sliver processes, using
standard equipment known in the art. Typically the first component
is melted, typically simultaneously while the second component is
melted. The first component is added to the second component either
prior to, afterwards, or simultaneously during the extrusion of the
first component and the second component through an extrusion die
to form a fiber. As used herein, the term "extrusion", or
"extruding" includes the melting of the polymers prior to forming
the fiber cross section and pushing the molten fiber out of the
spinneret capillary.
[0127] In the present invention, the term "sliver formation"
indicates the step that occurs when the extruded, stretched,
crimped or curled, and cut fiber has been carded and a card
web/carded web is formed into a sliver.
[0128] The fiber is subjected to a drawing process which stretches
out the fiber so as to align the polymer chains along the long axis
of the fiber to form a drawn fiber. More specifically, the drawing
process increases the ratio of polymer orientation in the direction
of the (long) fiber axis and may also increase the crystallinity of
the fiber by creating crystalline regions in the fiber interspersed
with amorphous regions. Without intending to be limited by theory,
it is believed that as the degree of drawing increases, the fiber
contains an, increasing percentage of crystalline regions as
compared to amorphous regions. Drawing may, for example, increase
the molecular orientation of the fibers, change the appearance of
the fibers, increase the tenacity of the fibers, increase the
rigidity of the fibers, or change the feel and/or surface
properties of the fibers. One skilled in the art understands that
if crystallinity develops or increases, it can reduce overall fiber
shrinkage and drawing also reduces fiber elongation, etc. The
drawing processes useful herein include cold-drawing processes,
partially-oriented yarn processes, hot-drawing processes,
air-drawing processes and a combination thereof; or cold-drawing
processes, hot-drawing processes and a combination thereof; or
hot-drawing processes.
[0129] In an embodiment herein, the fiber, the multicomponent
latent-crimping staple fiber, the staple fiber, etc. herein is
drawn to an essentially maximum degree; or the maximum extent
possible. In this context, the term "maximum" means that the fiber
is drawn to the maximum draw ratio that the fiber can endure
without breaking, minus a small margin of safety; or about a 30%
margin of safety to about a 1% margin of safety; or about a 20%
margin of safety to about a 1% margin of safety; or about a 10%
margin of safety to about a 1% margin of safety. This maximum
degree also is generally accompanied by a fiber elongation at break
of less than or equal to about 50%; or from about 50% to about 0%;
or less than or equal to about 45%; or from about 45% to about 0%;
or less than or equal to about 35%; or from about 35% to about 0%.
Without intending to be limited by theory, it is believed that in
some embodiments simply stretching the fiber to a "maximum" draw
ratio is not sufficient to optimize the fiber's strength; instead a
combination of polymer orientation prior to drawing (set by fiber
extrusion temperatures and speeds), drawing speeds and
temperatures, the amount of draw distributed among two or more draw
zones, and where heat is applied (e.g., on metal rolls, in a water
bath between rolls, or in a steam chest between rolls, or
combinations) may be required to develop the maximum practical
strength in the fiber.
[0130] In an embodiment of the present invention, the process is
optimized for the particular fiber's maximum tenacity via
non-mechanical crimping; or heat-crimping, rather than via
mechanical crimping. Without intending to be limited by theory, it
is believed that such a process is not currently known or used in
the art, as the prior processes may draw the fiber, but are not
actually intended to maximize or otherwise optimize the tenacity.
As noted in prior art processes, the curl is typically merely
intended to bulk up the fiber.
[0131] In an embodiment herein, the drawing process is
cold-drawing. In an embodiment herein the first component is a
nylon and the drawing process is cold-drawing. In an embodiment
herein, the first component is a nylon, the second component is a
nylon, and the drawing process is cold-drawing. In an embodiment
herein the drawing process is hot-drawing. In an embodiment herein
the first component is a nylon and the drawing process is
hot-drawing. In an embodiment herein, the first component is a
nylon, the second component is a nylon, and the drawing process is
hot-drawing. Without intending to be limited by theory, it is
believed that certain high tenacity nylon fibers may benefit from
hot-drawing so as to significantly increase the fiber's
tenacity.
[0132] The drawn fiber herein is then typically non-mechanically
crimped via subjecting the drawn fiber to an external condition
such as heat, moisture, humidity, light, and a combination thereof;
or heat, humidity and a combination hereof; or heat. to form a
crimped fiber. As noted herein, the crimping process creates waves
or curls in the drawn fiber such as the kinks found in natural
fibers such as cotton and wool. However, one skilled in the art
understands that natural fibers such as cotton and wool may have
dramatically differing degrees of bending or curling along their
length. In an embodiment herein, the crimping in the fibers of the
present invention contain a "curl" that is a smooth and regular
shape and is substantially the same at all points along the fiber.
This allows the crimped fiber to be more easily spun into a yarn
and/or further processed using standard equipment and
processes.
[0133] Typically, the crimped fiber is then cut to form a staple
fiber. Staple fibers herein are typically from about 3 mm to about
25 cm in length; or from about 18 mm to about 15 cm in length; or
from about 2.54 cm to about 8 cm in length. The staple fibers may
then be carded and then spun with a filament and/or with other
staple fibers to form a yarn.
[0134] Traditionally, carding is a mechanical process where staple
fibers are transported to the carding process in a bale, which may
optionally first go through an "opener" or an "opening" process.
The opened fibers then are carded on a carding machine or "card",
which forms a web from the fibers. Other fibers may be introduced
and blended prior to carding. With natural fibers, this carding
process breaks up clumped up fibers and aligns individual fibers
for subsequent processing. At the end of the carding process, the
result is a sliver, a rope a tow, a yarn.
[0135] In an embodiment herein, cotton fibers are blended with the
fiber; or staple fiber; or multicomponent latent-crimp staple
fiber; or non-mechanically-crimped staple fiber; or drawn fiber; or
crimped fiber of the invention, at the carding stage or
subsequently in the yarn spinning process. Successful carding
results in a fiber web in which the fibers hold together with each
other such that the web does not collapse under its own weight or
under gentle pulling, which is required to form the sliver. The
flat card web is bunched together into a cylindrical "sliver,"
which is coiled into a can. The sliver is then further processed
into a roving, which has better fiber orientation than the sliver,
a narrower diameter and fewer fibers in the diameter than the
sliver. The roving is spooled onto a spindle and then further spun
into a yarn, which has a still narrower diameter, and fewer fibers
in the diameter, but greater strength. The yarn may comprise staple
fibers only, or it may be formed by wrapping staple fibers around a
core filament yarn. During the yarn spinning process, other staple
fibers may optionally be introduced and blended together.
[0136] It is recognized that the fiber; or staple fiber; or
multicomponent latent-crimp staple fiber; or
non-mechanically-crimped staple fiber; or drawn fiber; or crimped
fiber, or continuous web; or sliver, herein may further contain an
additive intended to modify one or more properties such as, for
example, hydrophilicity, hydrophobicity, surface feel, color,
infrared absorption, infrared reflection, florescence, UV
absorption, UV reflection, tenacity, etc.
[0137] It is recognized that the additives that can help achieve
these properties may be additives added to the fiber polymer(s)
prior to or during extrusion, and/or components of fiber finishes
added to the surface of the fiber, typically in the drawing stage
prior to crimping/curling, or after crimping/curling and prior to
cutting.
[0138] Accordingly, it is believed that it is now possible to use a
low-cost, simple conventional staple fiber process and equipment to
form a high-tenacity fiber; or staple fiber; or multicomponent
latent-crimp staple fiber; or non-mechanically-crimped staple
fiber; or drawn fiber; or crimped fiber, that can be successfully
carded without blending with naturally- or mechanically-crimped
fibers. Furthermore, the fiber; or staple fiber; or multicomponent
latent-crimp staple fiber; or non-mechanically-crimped staple
fiber; or drawn fiber; or crimped fiber, can also be carded and/or
mixed with or into blends of other crimped fibers such as the
micro-kinked nylon 6,6 staple fibers and others known in the
art.
[0139] In an embodiment herein, the fiber; or staple fiber; or
multicomponent latent-crimp staple fiber; or
non-mechanically-crimped staple fiber; or drawn fiber; or crimped
fiber, can also be carded and/or mixed with or into a natural
fiber, a synthetic fiber, or a combination thereof; an animal
fiber, a plant fiber, a synthetic fiber, or a combination thereof;
or alpaca, angora, cashmere, cotton, lambswool, silk, wool,
acetate, bamboo, lyocell, ramie, rayon, viscose, acrylic, a
para-aramid polymer (e.g., Kevlar.TM.), a meta-aramid polymer
(e.g., Nomex.TM.), nylon, polyester, spandex, rayon, and a,
combination thereof; or cotton, silk, wool, acetate, rayon,
acrylic, a para-aramid polymer (e.g., Kevlar.TM.), a meta-aramid
polymer (e.g., Nomex.TM.), nylon, polyester, spandex, and a
combination thereof; or cotton, silk, wool, rayon, a para-aramid
polymer, a meta-aramid polymer, nylon, polyester, and a combination
thereof.
[0140] In another embodiment, the fiber; or staple fiber; or
multicomponent latent-crimp staple fiber; or
non-mechanically-crimped staple fiber; or drawn fiber; or crimped
fiber, or continuous web, herein may be further processed into for
example a non-woven fabric, a sliver, a yarn, a knit fabric, and a
woven fabric. These may then be further processed into a variety of
products ranging from garments to carpeting, diapers, drapes,
personal care items, industrial components, tires, linens, etc.
[0141] In an embodiment of the present invention, the increased
fiber tenacity results in increased abrasion resistance for a woven
fabric, such as a military garment or cloth, a protective garment
or cloth, an emergency garment or cloth, or a workwear garment or
cloth.
Example 1
[0142] "Type 420" high tenacity nylon 6,6 staple fibers available
around the world from Invista (www.invista.com) are commonly
accepted as having tenacities suitable for use in military apparel
and workwear. This fiber's properties are described below in Table
1. This fiber has no measurable crimps per 2.54 cm and can be
carded successfully only by blending it with mechanically- or
naturally-crimped fibers, such as cotton. When only "Type 420"
fibers are introduced into an industrial carding machine, the
fibers load the card, preventing successful continuous formation of
a fiber web that can be formed into a sliver for subsequent
processing into yarn.
[0143] Fiber A is a drawn, high tenacity nylon 6,6 fiber made using
high molecular weight nylon having a relative viscosity of 83. on a
standard staple fiber extrusion line as described above. The
tenacity at break and the tenacity at 7% elongation were measured
after drawing and prior to crimping. Fiber A was then crimped using
a standard stuffer-box mechanical crimper to crimp the fibers in a
zig-zag crimp. The mechanically-crimped Fiber A was suitable for
carding without blending with other crimped fibers, successfully
forms a sliver, and is successfully subsequently processed into a
yarn.
[0144] This fiber's properties are described below in Table 1.
[0145] Fiber B is a bicomponent nylon 6, 6, fiber produced in a
side-by-side bowtie configuration as seen in FIG. 5. The first
component is a nylon 6, 6 polymer with a relative viscosity of 83.
The second component is a nylon 6, 6, polymer with a relative
viscosity of 43. The tenacity at break and the tenacity at 7%
elongation were measured. Fiber B was then run through a
conventional staple drying oven to heat the fibers which heat
crimped Fiber B into helixes having about 4 curls/cm (10 curls/2.54
cm). The heat-crimped Fiber B was suitable for carding without
blending with other crimped fibers, successfully forms a sliver,
and is successfully subsequently processed into a yarn.
[0146] The extrusion and drawing processes used to produce Fiber A,
Fiber B, were optimized for high tenacity at break.
TABLE-US-00001 TABLE 1 Fiber A after Fiber A prior mechanical Fiber
B prior Fiber B after Type 420 to crimping crimping to crimping
heat crimping Tenacity @ 6.6 6.5 5.8 6.4 6.3 break (g/denier)
Tenacity @ 7% 1.4 1.47 0.85 2.5 2.5 elongation (g/denier) Crimping
0 crimps 0 crimps 10 crimps 0 curls 10 curls degree (/2.54 cm)
[0147] As can be seen in Table 1, Fiber A possesses a significant
lower tenacity according to either the tenacity at break test or
the tenacity at 7% elongation test after being subjected to
mechanical crimping. While Fiber A possessed similar tenacity at
break and tenacity at 7% elongation as compared to Type 420 prior
to mechanical crimping, the tenacities are significantly reduced
after mechanical crimping. Therefore the Applicant believes that a
similar reduction would occur to the Type 420 fibers if they were
subjected to a normal mechanically-crimping process.
[0148] Fiber A's tenacity at break after mechanical crimping is
only 89% of the tenacity prior to crimping. Fiber A's tenacity at
7% elongation after mechanical crimping is only 58% of the tenacity
at 7% elongation prior to crimping.
[0149] In contrast, Fiber B shows that the tenacity at break after
heat crimping is 98% of the tenacity at break prior to heat
crimping. Fiber B also shows that the tenacity at 7% elongation
after heat crimping is 100% (i.e., no loss of tenacity whatsoever)
as compared to the tenacity at 7% elongation test before heat
crimping.
[0150] Accordingly, the non-mechanical crimping employed in the
production of Fiber B is significantly better at maintaining the
tenacity at break and the tenacity at 7% elongation, as compared to
mechanical crimping.
Example 2
[0151] Fiber C is as a 2.5 denier per filament, round homopolymer
fiber made using polyphenylene sulfide with a melt index of 170.
After drawing but before crimping, Fiber C's tenacity at break is
4.8 g/denier. After mechanical crimping, Fiber C's tenacity at
break is 4.2 g/denier. This shows that Fiber C's tenacity at break
is significantly reduced by the mechanical crimping.
[0152] Fiber D is a 2.5 denier per filament round eccentric
sheath/core bicomponent fiber according to the invention herein,
similar to that seen in FIG. 2, except that the polymer ratio is
50:50. The first component, forming the sheath, is a polyphenylene
sulfide with a melt flow index of 170. The second component,
forming the eccentric core, is a polyphenylene sulfide with a melt
flow index of 100. After drawing, but before heat-crimping, Fiber D
has a tenacity at break of 5.0 g/denier. After heat-crimping, Fiber
D's tenacity at break is 4.8 g/denier. This shows that even after
heat-crimping, Fiber D's tenacity at break was only slightly
reduced and is still 96% of the tenacity at break prior to
heat-crimping.
Example 3
[0153] A fiber of the present invention is made from two different
nylons. The tenacity at break before crimping is 6 grams/denier and
has a tenacity at 7% elongation of 1.4 grams per denier before
crimping. Both the tenacity at break and tenacity at 7% elongation
after non-mechanically crimping are 90 percent of the respective
tenacity at break prior to crimping and tenacity at 7% elongation
prior to crimping.
[0154] It should be understood that the above only illustrates and
describes examples whereby the present invention may be carried
out, and that modifications and/or alterations may be made thereto
without departing from the spirit of the invention.
[0155] It should also be understood that certain features of the
invention, which are, for clarity, described in the context of
separate embodiments, may also be provided in combination in a
single embodiment. Conversely, various features of the invention
which are, for brevity, described in the context of a single
embodiment, may also be provided separately, or in any suitable
subcombination.
* * * * *