U.S. patent application number 16/090201 was filed with the patent office on 2019-04-18 for stacked-plate heat exchanger.
This patent application is currently assigned to Mahle International GmbH. The applicant listed for this patent is Mahle International GmbH. Invention is credited to Klaus Irmler, Michael Schmidt.
Application Number | 20190113285 16/090201 |
Document ID | / |
Family ID | 58455054 |
Filed Date | 2019-04-18 |
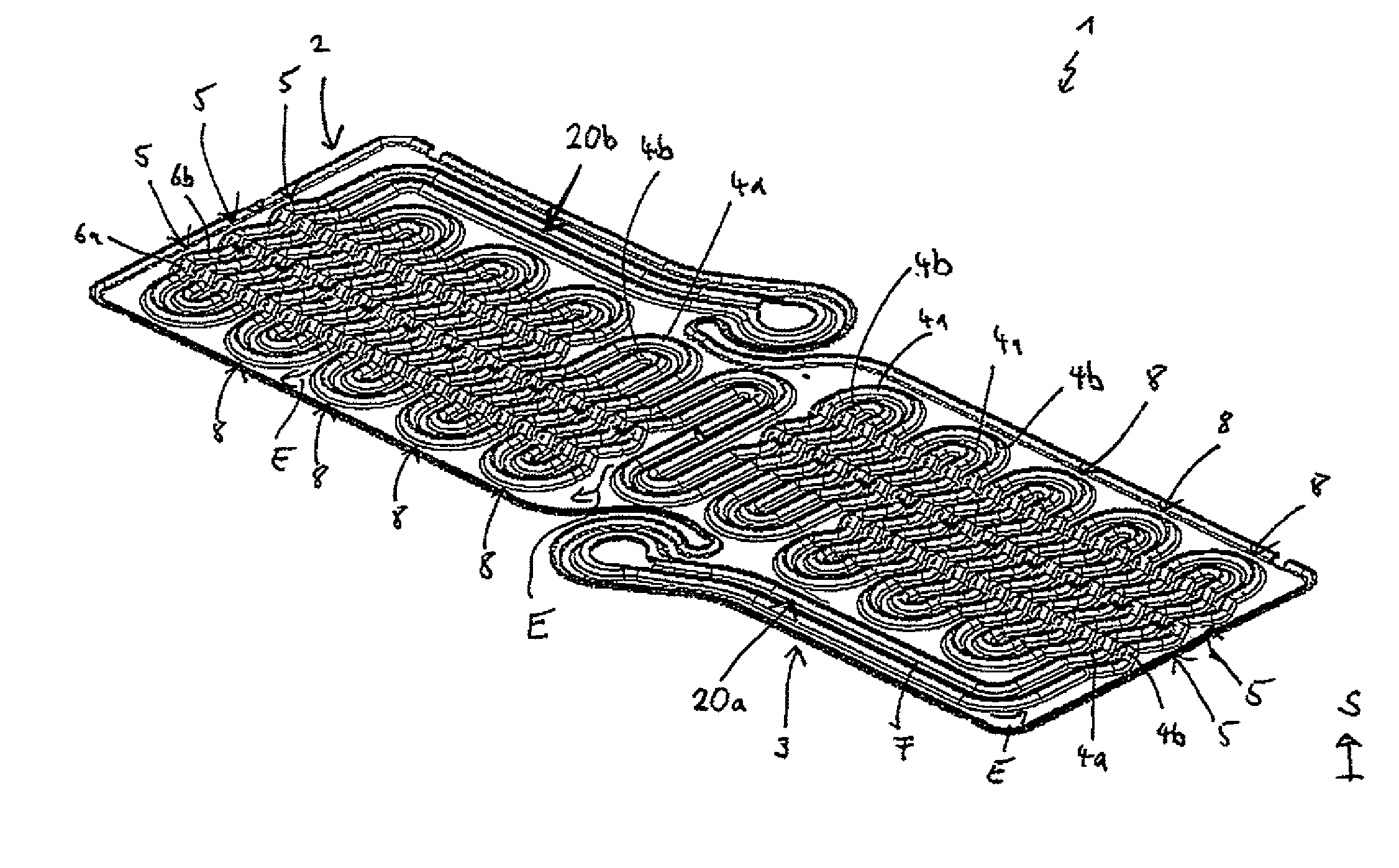



United States Patent
Application |
20190113285 |
Kind Code |
A1 |
Irmler; Klaus ; et
al. |
April 18, 2019 |
STACKED-PLATE HEAT EXCHANGER
Abstract
A stacked-plate heat exchanger may include a plurality of
stacked plates stacked on top of each other along a stacking
direction. A channel structure, through which a fluid may be
flowable, may be formed in at least one stacked plate. From a top
view of the at least one stacked plate, the channel structure may
have at least one fluid channel along the stacking direction that
may have at least one channel section with a zigzag-like
geometry.
Inventors: |
Irmler; Klaus; (Tuebingen,
DE) ; Schmidt; Michael; (Bietigheim-Bissingen,
DE) |
|
Applicant: |
Name |
City |
State |
Country |
Type |
Mahle International GmbH |
Stuttgart |
|
DE |
|
|
Assignee: |
Mahle International GmbH
Stuttgart
DE
|
Family ID: |
58455054 |
Appl. No.: |
16/090201 |
Filed: |
March 30, 2017 |
PCT Filed: |
March 30, 2017 |
PCT NO: |
PCT/EP2017/057536 |
371 Date: |
September 28, 2018 |
Current U.S.
Class: |
1/1 |
Current CPC
Class: |
F28D 9/0025 20130101;
F28D 9/0031 20130101; F28F 3/048 20130101; F28D 9/0043 20130101;
F28F 3/08 20130101; F28F 3/046 20130101 |
International
Class: |
F28D 9/00 20060101
F28D009/00; F28F 3/04 20060101 F28F003/04 |
Foreign Application Data
Date |
Code |
Application Number |
Mar 31, 2016 |
DE |
10 2016 205 353.1 |
Claims
1. A stacked-plate heat exchanger comprising: a plurality of
stacked plates stacked on top of each other along a stacking
direction; wherein a channel structure, through which a fluid is
flowable, is formed in at least one stacked plate; wherein, from a
top view of the at least one stacked plate, the channel structure
has at least one fluid channel along the stacking direction that
has at least one channel section with a zigzag-like geometry.
2. The stacked-plate heat exchanger according to claim 1, wherein
the at least one channel section has a first partial section and a
second partial section forming an angle between 90.degree. and
165.degree..
3. The stacked-plate heat exchanger according to claim 1, wherein
the first and the second partial sections are respectively formed
substantially rectilinear and continue into one another via a
curved formed transition section.
4. The stacked-plate heat exchanger according to claim 1, wherein
the at least one fluid channel is formed in a meander-like manner
and has a plurality of channel sections each with a zigzag-like
geometry.
5. The stacked-plate heat exchanger according to claim 1, wherein
at least one fluid channel has a plurality of U-shaped channel
sections, wherein at least one channel section with the zigzag-like
geometry is provided between at least two U-shaped channel sections
adjacent along an extent direction of the fluid channel.
6. The stacked-plate heat exchanger according to claim 5, wherein
two channel sections with the zigzag-like geometry and following
one another along the extent direction are provided between the at
least two U-shaped channel sections.
7. The stacked-plate heat exchanger according to claim 1, wherein
the at least one fluid channel includes at least two fluid channels
extending substantially parallel to and at a distance from one
another.
8. The stacked-plate heat exchanger according to claim 7, wherein,
between the at least two fluid channels, at least one connecting
channel is formed in a region of the at least one channel section,
the at least one connecting channel fluidically connecting the at
least two fluid channels to one another.
9. The stacked-plate heat exchanger according to claim 8, wherein
the at least one connecting channel includes a plurality of
connecting channels arranged at a distance from one another along
an extent direction of the at least two fluid channels.
10. The stacked-plate heat exchanger according to claim 9, wherein
the plurality of connecting channels fluidically connect all of the
at least two fluid channels to one another.
11. The stacked-plate heat exchanger according to claim 1, wherein
one of: the channel structure is formed to be flowed through by
water, and the at least one fluid channel has a cross-sectional
area between 2 mm.sup.2 and 8 mm.sup.2 in a cross-section of the at
least one stacked plate perpendicular to an extent direction of the
at least one fluid channel; the channel structure is formed to be
flowed through by ethanol, and the cross-sectional area of the at
least one fluid channel is between 3 mm.sup.2 and 15 mm.sup.2 in
the cross-section of the at least one stacked plate; the channel
structure is formed to be flowed through by, and the
cross-sectional area of the at least one fluid channel is between 6
mm.sup.2 and 20 mm.sup.2 in the cross-section of the at least one
stacked plate; or the channel structure is formed to be flowed
through by hydrofluorocarbons, and the cross-sectional area of the
at least one fluid channel is between 15 mm.sup.2 and 40 mm.sup.2
in the cross-section of the at least one stacked plate.
12. The stacked-plate heat exchanger according to claim 1, wherein
the channel structure includes at least one of corrugation-like
elevations and depressions in the at least one stacked plate.
13. The stacked-plate heat exchanger according to claim 1, wherein
at least two stacked plates each has a channel structure.
14. The stacked-plate heat exchanger according to claim 7, further
comprising a shared fluid inlet for distributing the fluid to the
at least two fluid channels, and a shared fluid outlet for
directing the fluid out after flowing through the at least two
fluid channels.
15. The stacked-plate heat exchanger according to claim 1, wherein
the at least one fluid channel and the at least one channel section
are configured such that the fluid is substantially entirely in
liquid phase when in the at least one channel section.
16. The stacked-plate heat exchanger according to claim 1, wherein
the at least one fluid channel includes at least one other channel
section different from the at least channel section with a
zigzag-like geometry that does not have a zigzag-like geometry.
17. The stacked-plate heat exchanger according to claim 16, wherein
the at least one other channel has a rectilinear geometry.
18. The stacked-plate heat exchanger according to claim 7, wherein
the at least two fluid channels include three fluid channels.
19. A stacked-plate heat exchanger comprising: a plurality of
stacked plates stacked on top of each other along a stacking
direction; wherein at least one of the stacked plates includes a
channel structure through which a fluid is flowable; and wherein
the channel structure includes at least two fluid channels along
the stacking direction extending substantially parallel to and at a
distance from one another, and at least one connecting channel
fluidically connecting the at least two fluid channels to one
another, the at least two fluid channels each having at least one
channel section with a zigzag-like geometry.
20. The stacked-plate heat exchanger according to claim 19, wherein
the at least one channel section has a first partial section and a
second partial section forming an angle between 90.degree. and
165.degree..
Description
CROSS REFERENCE TO RELATED APPLICATIONS
[0001] This application claims priority to International Patent
Application No. PCT/EP2017/057536, filed on Mar. 30, 2017, and
German Patent Application No. DE 10 2016 205 353.1, filed on Mar.
31, 2016, the contents of both of which are hereby incorporated by
reference in their entirety.
TECHNICAL FIELD
[0002] The invention relates to a stacked-plate heat exchanger.
BACKGROUND
[0003] Stacked-plate heat exchangers come into use as so-called
exhaust gas evaporators in the exhaust gas aftertreatment of
internal combustion engines. Such an exhaust gas evaporator enables
a recovery of thermal energy from the exhaust gases which are
discharged from the internal combustion engine. In an exhaust gas
evaporator, heat is extracted from the exhaust gas and is fed to a
coolant or refrigerant, the so-called working medium, which is
typically evaporated here.
[0004] Such a stacked-plate heat exchanger is known for example
from DE 10 2009 012 493 A1.
[0005] In order to achieve as high an efficiency as possible in the
heat recovery, an optimized geometry of the channel structure in
which the working medium is directed through the evaporator or
respectively stacked-plate heat exchanger is of central
importance.
SUMMARY
[0006] It is an object of the present invention to provide an
improved embodiment for a stacked-plate heat exchanger, which in
particular has an improved efficiency.
[0007] This problem is solved by the subject of the independent
claims. Preferred embodiments are the subject of the dependent
claims.
[0008] Accordingly, it is a basic idea of the invention to provide
the channel structure, formed in the stacked-plate heat exchanger,
which is to be flowed through by a fluid--the working medium of the
heat exchanger--partially with a zigzag-like channel geometry. The
changes to the flow direction of the working medium, entailed
thereby, when flowing through the zigzag-like channel geometry, are
accompanied by an increased heat exchange between the working
medium and the exhaust gas which is directed through the
stacked-plate heat exchanger. Therefore, such a zigzag-like channel
geometry is suitable in a region of the channel structure in which
the working medium is present in liquid phase. This is because in
this region, at low speeds of flow of the working medium, the heat
transmission to the working medium is itself reduced. The
zigzag-like channel geometry essential to the invention can at
least compensate this reduced heat transmission with working medium
present in liquid phase, and therefore leads, as a result, to an
improved efficiency of the heat exchanger.
[0009] In the regions of the channel structure in which the working
medium is two-phase, therefore is also present in gaseous form, the
heat transmission is also sufficiently high without a zigzag-like
geometry, so that there the said zigzag-like channel geometry can
be dispensed with. Therefore, in these regions of the channel
structure, an unnecessary pressure loss in the working medium,
which always accompanies the zigzag geometry, is avoided.
[0010] A stacked-plate heat exchanger according to the invention
comprises a plurality of stacked plates which are stacked on top of
each other along a stacking direction. A channel structure, which
is to be flowed through by a fluid, is formed in at least one
stacked plate. The channel structure, when the stacked plate is
viewed from above, comprises at least one fluid channel along the
stacking direction, said fluid channel having at least one channel
section with a zigzag-like geometry.
[0011] In a preferred embodiment, the at least one channel section
with a zigzag-like geometry has a first partial section, which
continues into a second partial section. The two partial sections
form together an angle of between 90.degree. and 165.degree..
Experimental investigations have shown that with the said angle
range a particularly high heat exchange can be achieved between the
working medium and the exhaust gas.
[0012] In an advantageous further development, the first and the
second partial section are configured so as to be substantially
rectilinear along the stacking direction, when viewed from above,
and continue into one another by means of a curved formed
transition section. By means of such a geometry, an undesired
pressure loss in the working medium when flowing through the fluid
channel can be kept low.
[0013] Particularly preferably, the at least one fluid channel of
the channel structure is formed in a meander-like manner and has a
plurality of channel sections with a zigzag-like geometry. Such a
geometry permits the arrangement of the fluid channel on a stacked
plate with relatively small surface dimensions. Therefore, the
stacked-plate heat exchanger can be realized with particularly
compact exterior dimensions.
[0014] In a further preferred embodiment, at least one fluid
channel has a plurality of U-shaped channel sections.
[0015] In this variant, at least one channel section with a
zigzag-like geometry is provided between at least two adjacent
U-shaped channel sections along an extent direction of the at least
one fluid channel. This variant also permits a high heat exchange
with, at the same time, a small installation space requirement.
[0016] Because it is likewise able to be realized in a particularly
compact construction, a variant may be considered to be
particularly preferred in which, between the at least two U-shaped
channel sections following one another along the extent direction
of the at least one fluid channel, two channel sections with a
zigzag-like geometry are provided following one another along the
extent direction.
[0017] In an advantageous further development, the channel
structure comprises at least two fluid channels extending
substantially parallel to and at a distance from one another. In
this way, a high compressive strength can be ensured in the
individual fluid channels. For a variety of working media, such as
for instance cyclopentane, ethanol, acetone, it proves to be
advantageous if precisely three fluid channels are provided, which
extend substantially parallel to and at a distance from one
another.
[0018] In a further advantageous further development, at least one
connecting channel is formed between the at least two fluid
channels, which connecting channel is provided with a zigzag-like
geometry in the region of the channel section and fluidically
connects the at least two fluid channels with one another. This
enables a pressure equalization of the fluid pressure which is
present in the working medium in the individual fluid channels.
This, in turn, promotes a laterally particularly homogeneous heat
exchange between working medium or respective the fluid, and the
exhaust gas.
[0019] Particularly preferably, a plurality of connecting channels
is provided, which are arranged at a distance from one another
along the extent direction of the at least two fluid channels. In
this way, the desired pressure equalization can be guaranteed over
the entire extent of the fluid channels.
[0020] In a further advantageous further development, at least one
connecting channel, preferably respectively all connecting
channels, fluidically connects to one another all the fluid
channels which are present. This provision also promotes a pressure
equalization in the working medium or respectively fluid which is
advantageous for a homogeneous heat exchange.
[0021] In another preferred embodiment, the channel structure is
formed to be flowed through by water. For this, all the fluid
channels which are present have, together, in a cross-section of
the stacked plate perpendicularly to the extent direction of the
fluid channels, a cross-section area of between 2 mm.sup.2 and 8
mm.sup.2. Alternatively thereto, the channel structure is formed to
be flowed through by ethanol. For this, all the fluid channels
which are present have, together, in the cross-section of the
stacked plate perpendicularly to the extent direction of the fluid
channels, a cross-section area of between 3 mm.sup.2 and 15
mm.sup.2. It is also conceivable to use a mixture of ethanol and
water. Alternatively thereto, the channel structure can be formed
to be flowed through by cyclopentane. In this case, all the fluid
channels which are present have, together, in the cross-section of
the stacked plate perpendicularly to the extent direction of the
fluid channels, a cross-section area of between 6 mm.sup.2 and 20
mm.sup.2. Alternatively thereto, the use of acetone is also
conceivable. Alternatively thereto, the channel structure is formed
to be flowed through by hydrofluorocarbons (HFC). In this variant,
all the fluid channels which are present have, together, in a
cross-section of the stacked plate perpendicularly to the extent
direction of the fluid channels, a cross-section area of between 15
mm.sup.2 and 40 mm.sup.2. Depending on the choice of the working
medium, therefore, an individual design of the cross-section area
of the individual fluid channels takes place. In this way, an
efficient heat exchange is ensured, with, at the same time, little
pressure loss in the working medium. All the named substances can
also be used as a mixture with an oil.
[0022] A further preferred embodiment proves to be technically
particularly simple to realize and therefore to be produced at a
favourable cost, in which the channel structure is formed by
corrugation-like elevations or depressions present in the stacked
plate. This permits a realizing of the stacked plates with the
channel structure essential to the invention as shaped sheet metal
parts, in particular by means of deep drawing.
[0023] In a further preferred embodiment, a channel structure is
present in at least two stacked plates. The more stacked plates are
provided with a channel structure with the zigzag-like flow
geometry essential to the invention, the higher is the efficiency
which is able to be achieved with the stacked-plate heat exchanger,
in particular if the latter is used as an exhaust gas evaporator in
interaction with an internal combustion engine.
[0024] Expediently, the stacked-plate heat exchanger can have a
shared fluid inlet for distributing the fluid to the at least two,
preferably three, fluid channels, and a shared fluid outlet for
directing the fluid out after flowing through the respective fluid
channels. This provision simplifies the structure of the
stacked-plate heat exchanger, in particular when several separate
fluid channels are provided.
[0025] Further important features and advantages of the invention
will emerge from the subclaims, from the drawings and from the
associated figure description with the aid of the drawings.
[0026] It shall be understood that the features mentioned above and
to be explained further below are able to be used not only in the
respectively indicated combination, but also in other combinations
or in isolation, without departing from the scope of the present
invention.
[0027] Preferred example embodiments of the invention are
illustrated in the drawings and are explained further in the
following description, wherein the same reference numbers refer to
identical or similar or functionally identical components.
BRIEF DESCRIPTION OF THE DRAWINGS
[0028] There are shown, respectively diagrammatically:
[0029] FIG. 1 an individual stacked plate of the stacked-plate heat
exchanger with the channel structure according to the invention, in
a perspective view,
[0030] FIG. 2 a detail illustration of the channel structure of
FIG. 1 in a top view onto the stacked plate,
[0031] FIG. 3 a variant of the stacked plate of FIGS. 1 and 2, with
a channel structure which comprises three fluid channels, in a
cross-section,
[0032] FIG. 4 the stacked-plate heat exchanger with several stacked
plates stacked on top of each other, in a perspective
illustration.
DETAILED DESCRIPTION
[0033] FIG. 1 illustrates by way of example an individual stacked
plate 2 of a stacked-plate heat exchanger 1 according to the
invention, in a perspective illustration.
[0034] In the stacked plate 2 shown in FIG. 1, a channel structure
3 is formed which is to be flowed through by a fluid F. The channel
structure 3 comprises two fluid channels 4a, 4b which, when the
stacked plate 2 is viewed from above, extend along the stacking
direction S substantially parallel to and at a distance from one
another. The channel structure 3 with the fluid channels 4a, 4b is
formed by corrugation-like elevations or depressions 10 formed in
the stacked plate 2. Each stacked plate 2 is covered in stacking
direction S on both sides with two cover plates 11a, 11b lying
opposite one another, as can be seen from FIG. 3 which shows the
stacked plate 2 in a sectional illustration. Accordingly, the two
cover plates 11a, 11b delimit the channel structures 3 formed in
the stacked plate 2 in and contrary to the stacking direction S
(cf. FIG. 2). The two cover plates 11a, 11b can be soldered to the
respective stacked plate 2.
[0035] For the formation of the stacked-plate heat exchanger 1,
several stacked plates 2 with respective cover plates 11a, 11b can
be stacked on top of each other. This is shown in FIG. 4, which
shows the stacked-plate heat exchanger 1 in a perspective partial
illustration. The individual stacked plates 2 with the cover plates
11a, 1b are arranged at a distance from one another in the stacking
direction S, wherein adjacent cover plates 11a, 11b in stacking
direction S rest against one another by means of a respective rib
structure 12, which is not illustrated in closer detail in FIG. 4.
The intermediate spaces 13 formed in the region of the rib
structures 12 between adjacent cover plates 11a, 11b can be flowed
through by an exhaust gas 14, which is in heat exchange with the
fluid F flowing through the channel structures 3 of the stacked
plates 2.
[0036] Observing FIG. 1 again now, it will be seen that the two
fluid channels 4a, 4b of the channel structure 3 are formed
respectively in a meander-like manner. Each of the two fluid
channels 4a, 4b has channel sections 5 with respectively a
zigzag-like geometry. The stacked-plate heat exchanger 1 can have,
in addition, a shared fluid inlet for distributing the fluid F to
the two fluid channels 4a, 4b, and a shared fluid outlet for
directing the fluid F out after flowing through the two fluid
channels 4a, 4b.
[0037] FIG. 2 is a detail illustration of FIG. 1 in the region of
channel sections 5 with a respectively zigzag-like geometry. As can
be seen from FIG. 2, a channel section 5 with a zigzag-like
geometry, present in the channel structure 3, has a first partial
section 6a which continues into a second partial section 6b by
means of a transition section 7. The first and the second partial
section 6a, 6b are respectively configured to be substantially
rectilinear, the transition section 7, on the other hand, is formed
so as to be curved. The two partial sections 6a, 6b are preferably
arranged at an angle of between 90.degree. and 165.degree. to one
another.
[0038] As FIG. 1 shows, the two fluid channels 4a, 4b respectively
comprise not only channel sections 5 with a zigzag-like geometry,
but respectively also have a plurality of U-shaped channel sections
8. Between two U-shaped channel sections 8 adjacent along an extent
direction E of the fluid channels 4a, 4b, the channel sections 5
are formed with a zigzag-like geometry.
[0039] The channel sections 5 with a zigzag-like geometry are
arranged in the stacked-plate heat exchanger 1 such that in the
channel sections 5 the fluid F is present entirely in liquid phase.
In addition, the two fluid channels 4a, 4b can respectively have
two channel sections 20a, 20b that are different from the channel
sections 5 with a zigzag-like geometry, in which the fluid channels
4a, 4b do not have a zigzag-like geometry, but rather can be formed
so as to be rectilinear or differently.
[0040] As FIG. 2 demonstrates, connecting channels 9 are formed
between the two fluid channels 4a, 4b running at a distance from
one another, in the region of the channel sections 5 with a
zigzag-like geometry. The connecting channels 9 fluidically connect
the fluid channels 4a, 4b to one another and are arranged, for
this, at a distance from one another along the extent direction E
of the fluid channels 4a, 4b.
[0041] FIG. 3 shows a variant of the example of FIG. 1. In the
example of FIG. 3, as already mentioned above, a stacked plate 2 of
the stacked-plate heat exchanger 1 is illustrated in a
cross-section perpendicularly to the extent direction E. In the
variant according to FIG. 3, the channel structure 3 comprises a
first, a second and a third fluid channel 4a, 4b, 4c, therefore
three fluid channels 4a, 4b, 4c.
[0042] As FIG. 3 demonstrates, the first fluid channel 4a in the
cross-section of FIG. 3 has a cross-sectional area A.sub.1, the
second fluid channel 4b has a cross-sectional area A.sub.2, and the
third fluid channel 4c has a cross-sectional area A.sub.3. The
total A of the individual cross-sectional areas in the case of the
three fluid channels 4a, 4b, 4c which are present results as
A=A.sub.1+A.sub.2+A.sub.3.
[0043] Preferably, the cross-sectional area A is adapted to the
working medium flowing through the channel structure 3, therefore
to the fluid which is used. In this way, an efficient heat exchange
can be ensured with, at the same time, a small pressure loss in the
working medium/fluid.
[0044] If the channel structure 3 is to be flowed through by
fluid/working medium, a range of values of between 2 mm.sup.2 and 8
mm.sup.2 is recommended for the cross-sectional area A defined
above.
[0045] If the channel structure 3 is to be flowed through by
ethanol as fluid/working medium, then a range of values of between
3 mm.sup.2 and 15 mm.sup.2 proves to be advantageous for the
cross-sectional area A defined above. The use of a mixture of
ethanol and water is also conceivable.
[0046] If the channel structure 3 is to be flowed through by
cyclopentane as fluid/working medium, then a range of values of
between 6 mm.sup.2 and 20 mm.sup.2 is recommended for the
cross-sectional area A defined above. Acetone can be used as an
alternative substance to cyclopentane.
[0047] If the channel structure 3 is to be flowed through by
hydrofluorocarbons (HFC) as fluid/working medium, then a range of
values of between 15 mm.sup.2 and 40 mm.sup.2 is recommended for
the cross-sectional area A defined above.
[0048] In further variants, a mixture of one of the previously
mentioned substances with an oil is also possible.
* * * * *