U.S. patent application number 16/162903 was filed with the patent office on 2019-04-18 for method of treating a steel.
The applicant listed for this patent is SAFRAN LANDING SYSTEMS. Invention is credited to Nicolas BINOT, Valentine DENEUX.
Application Number | 20190112680 16/162903 |
Document ID | / |
Family ID | 61132537 |
Filed Date | 2019-04-18 |


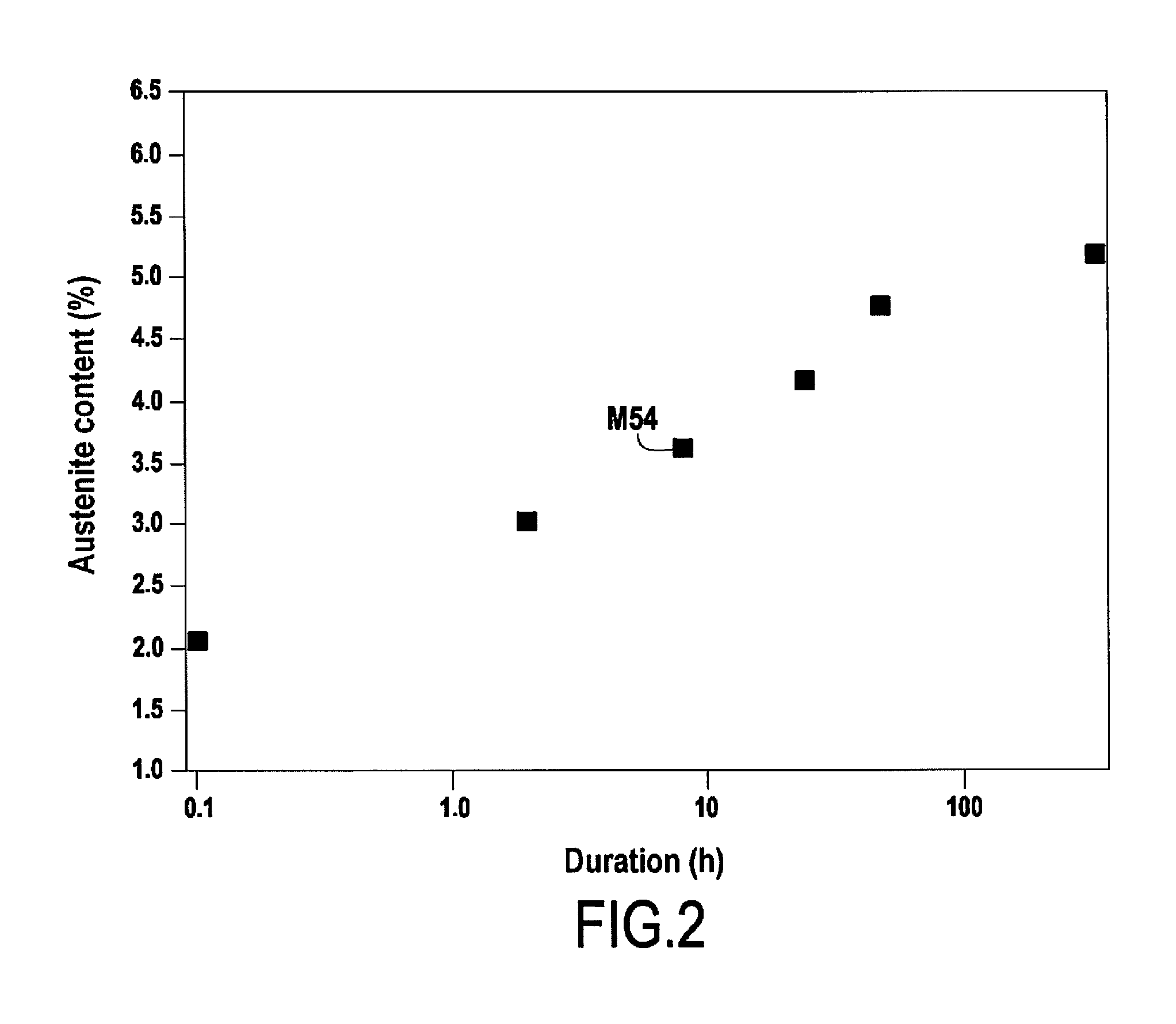
United States Patent
Application |
20190112680 |
Kind Code |
A1 |
DENEUX; Valentine ; et
al. |
April 18, 2019 |
METHOD OF TREATING A STEEL
Abstract
A method of treating a steel including, in percentages by
weight: 0.2% to 0.33% carbon, 4% to 8% cobalt, 7% to 11% nickel,
0.8% to 3% chromium, 0.5% to 2.5% molybdenum, 0.5% to 5.9%
tungsten, 0.05% to 0.2% vanadium, and not more than 0.02% titanium,
the balance being constituted by iron and inevitable impurities,
the method including subjecting the steel to solutionizing heat
treatment at a temperature from 950.degree. C. to 1100.degree. C.;
then subjecting the steel to quenching treatment; then placing the
steel in a cryogenic enclosure; cooling the inside of the cryogenic
chamber in which the steel is present to a treatment temperature
less than or equal to -73.degree. C.; and subjecting the steel to
cryogenic treatment while the treatment temperature is maintained
inside the enclosure, the time duration between the end of the
quenching treatment and the beginning of the cryogenic treatment
being less than or equal to 4 hours.
Inventors: |
DENEUX; Valentine;
(LASSEUBE, FR) ; BINOT; Nicolas; (ARAUX,
FR) |
|
Applicant: |
Name |
City |
State |
Country |
Type |
SAFRAN LANDING SYSTEMS |
VELIZY-VILLACOUBLAY |
|
FR |
|
|
Family ID: |
61132537 |
Appl. No.: |
16/162903 |
Filed: |
October 17, 2018 |
Current U.S.
Class: |
1/1 |
Current CPC
Class: |
C21D 1/18 20130101; C22C
38/44 20130101; C21D 6/02 20130101; C22C 38/46 20130101; C21D 6/007
20130101; C22C 38/50 20130101; C21D 6/04 20130101; C22C 38/52
20130101; C21D 6/004 20130101 |
International
Class: |
C21D 6/00 20060101
C21D006/00; C21D 6/04 20060101 C21D006/04; C21D 1/18 20060101
C21D001/18 |
Foreign Application Data
Date |
Code |
Application Number |
Oct 18, 2017 |
FR |
1759760 |
Claims
1. A method of treating a steel comprising, in percentages by
weight: 0.2% to 0.33% carbon, 4% to 8% cobalt, 7% to 11% nickel,
0.8% to 3% chromium, 0.5% to 2. 5% molybdenum, 0.5% to 5.9%
tungsten, 0.05% to 0.2% vanadium, and not more than 0.02% titanium,
the balance being constituted by iron and inevitable impurities,
the method comprising: subjecting the steel to solutionizing heat
treatment at a temperature lying in the range 950.degree. C. to
1100.degree. C.; subjecting the steel to quenching treatment,
performed after the solutionizing heat treatment; placing the steel
in a cryogenic enclosure after the quenching treatment; cooling the
inside of the cryogenic chamber in which the steel is present, the
cooling being taken down to a treatment temperature less than or
equal to -73.degree. C.; and subjecting the steel to cryogenic
treatment while the treatment temperature is maintained inside the
enclosure, the time duration between the end of the quenching
treatment and the beginning of the cryogenic treatment being less
than or equal to 4 hours.
2. The method according to claim 1, wherein the time duration
between the end of the quenching treatment and the beginning of the
cryogenic treatment is less than or equal to 2 hours.
3. The method according to claim 2, wherein the time duration
between the end of the quenching treatment and the beginning of the
cryogenic treatment is less than or equal to 1 hour.
4. The method according to claim 1, wherein the duration of the
cryogenic treatment is greater than or equal to 1 hour.
5. The method according to claim 1, further comprising subjecting
the steel to tempering treatment performed after the cryogenic
treatment.
6. The method according to claim 1, wherein the treated steel
constitutes an aircraft landing gear part.
7. The method according to claim 1, wherein the steel constitutes a
part of weight greater than or equal to 10 kg.
8. The method according to claim 1, wherein, during the quenching
treatment, the steel is cooled to an end-of-quenching temperature
that is less than or equal to 71.degree. C.
Description
CROSS REFERENCE TO RELATED APPLICATIONS
[0001] This application claims priority to French Patent
Application No. 1759760, filed Oct. 18, 2017, the entire content of
which is incorporated herein by reference in its entirety.
FIELD
[0002] The present invention relates to a method of treating a
steel, the method including in particular cryogenic treatment, the
steel possibly being for making aircraft landing gear parts.
BACKGROUND
[0003] Patent U.S. Pat. No. 9,051,635 discloses a steel presenting
good mechanical properties associated with good stress-corrosion
resistance.
[0004] That steel comprising, in percentages by weight, 0.2% to
0.33% carbon, 4% to 8% cobalt, 7% to 11% nickel, 0.8% to 3%
chromium, 0.5% to 2.5% molybdenum, 0.5% to 5.9% tungsten, 0.05% to
0.2% vanadium, and not more than 0.02% titanium, the balance being
constituted by iron and inevitable impurities, is--in the
above-mentioned patent--treated by the following succession of
steps, without specifying the time durations between each of the
steps: steel solutionizing heat treatment, quenching treatment,
immersion in liquid nitrogen, and tempering treatment.
[0005] Such a steel constitutes a material that is of interest for
making aircraft landing gear parts, in particular.
[0006] Nevertheless, the inventors have observed that there remains
significant dispersion in mechanical properties within batches of
steel parts subjected to the treatment disclosed in patent U.S.
Pat. No. 9,051,635. It would be desirable to reduce the dispersion
of those mechanical properties in order to optimize design curves,
and consequently to improve the performance of parts made using
that steel, e.g. by making them lighter in weight, by increasing
their lifetime, or by increasing the stresses to which they can be
exposed.
[0007] Also, the immersion in liquid nitrogen that is performed in
Document U.S. Pat. No. 9,051,635 does not constitute a step that is
appropriate for treating steel on an industrial scale.
Consequently, it remains desirable to have methods of treating that
steel that are more compatible with treatment on an industrial
scale.
[0008] Also known is the publication by Wang et al. "Austenite
layer and precipitation in high Co--Ni maraging steel" (Micron 57
(2014) 112-116) which discloses treatment of a steel whereby, after
quenching, the steel is dipped in a cryogenic bath at -73.degree.
C.
SUMMARY
[0009] In a first aspect, the invention provides a method of
treating a steel comprising, in percentages by weight: 0.2% to
0.33% carbon, 4% to 8% cobalt, 7% to 11% nickel, 0.8% to 3%
chromium, 0.5% to 2.5% molybdenum, 0.5% to 5.9% tungsten, 0.05% to
0.2% vanadium, and not more than 0.02% titanium, the balance being
constituted by iron and inevitable impurities, the method
comprising at least:
[0010] subjecting the steel to solutionizing heat treatment at a
temperature lying in the range 950.degree. C. to 1100.degree.
C.;
[0011] subjecting the steel to quenching treatment, performed after
the solutionizing heat treatment;
[0012] placing the steel in a cryogenic enclosure after the
quenching treatment;
[0013] cooling the inside of the cryogenic chamber in which the
steel is present, the cooling being taken down to a treatment
temperature less than or equal to -73.degree. C.; and
[0014] subjecting the steel to cryogenic treatment while the
treatment temperature is maintained inside the enclosure, the time
duration between the end of the quenching treatment and the
beginning of the cryogenic treatment being less than or equal to 4
hours.
[0015] In particular, the invention is remarkable in that the time
duration between the end of the quenching treatment and the
beginning of the cryogenic treatment is limited.
[0016] In recent studies, the inventors have observed that the
residual austenite content can vary a little within a batch of
parts made of the above-described steel that has been subjected to
cryogenic treatment. Nevertheless, this variation, even when small,
has a significant influence on the dispersion of mechanical
properties within the batch of treated parts. It has been possible
to identify the small variations in the residual austenite content
by using particular measurement techniques that are sufficiently
accurate (synchrotron X-ray diffraction and sigmameter). Once the
inventors had identified the origin of the dispersion in mechanical
properties, they studied the influence of conditions for reaching
the cryogenic treatment temperature, and they found that the time
duration between the end of quenching and the beginning of the
cryogenic treatment had an influence on the residual austenite
content. Thus, by limiting this duration, as described above, the
invention serves beneficially to obtain better control over the
residual austenite content obtained in the treated steel, and
consequently to reduce the dispersion in its mechanical properties.
Also, the inventors have observed that by limiting this duration,
it is beneficially possible to improve the stress-corrosion
resistance of the steel. By performing the cryogenic treatment in a
cryogenic enclosure that is cooled after being loaded with the
steel, it is beneficially possible to make the method compatible
with treatment on an industrial scale. Also, the invention causes
the cryogenic enclosure in which the steel is placed to cool
progressively, which also contributes to controlling the residual
austenite content compared with the situation in which the steel is
dipped directly into a cryogenic bar. Specifically, such dipping
results in an undesirable phenomenon of film boiling, which
prevents proper control over the cooling, and which has the
consequence of not enabling the residual austenite content to be
properly controlled.
[0017] In an embodiment, the time duration between the end of the
quenching treatment and the beginning of the cryogenic treatment is
less than or equal to 2 hours, an in an embodiment less than or
equal to 1 hour.
[0018] Imposing such a time duration between quenching and the
beginning of cryogenic treatment serves beneficially to further
reduce the dispersion in mechanical properties that is obtained for
the treated steel.
[0019] In an embodiment, the duration of the cryogenic treatment is
greater than or equal to 1 hour.
[0020] In an embodiment, the method further comprises subjecting
the steel to tempering treatment performed after the cryogenic
treatment.
[0021] In an embodiment, the treated steel constitutes an aircraft
landing gear part. By way of example, the part may be an axle, a
rocker beam, or a portion of the rocker beam, such as its pivot
axis.
[0022] In an embodiment, the steel constitutes a part of weight
greater than or equal to 10 kilograms (kg). The weight of the part
may be greater than or equal to 40 kg, e.g. greater than or equal
to 100 kg.
[0023] The invention is particularly beneficial when treating a
part of significant weight, and thus of considerable size, in so
far as the above-mentioned undesirable phenomenon of film boiling
occurs regardless of the size of the part, but is more marked with
increasing size of the part.
[0024] In an embodiment, during the quenching treatment, the steel
is cooled to an end-of-quenching temperature that is less than or
equal to 71.degree. C.
[0025] Using a low end-of-quenching temperature contributes
beneficially to still further reducing the residual austenite
content.
BRIEF DESCRIPTION OF THE DRAWINGS
[0026] Other characteristics and benefits of the invention appear
from the following description, given by way of nonlimiting example
and with reference to the accompanying figures, in which:
[0027] FIG. 1 is a diagram showing how the temperature imposed on
the steel varies in an example of the treatment method of an
embodiment of the invention; and
[0028] FIG. 2 shows the result of a comparative test revealing the
influence on the residual austenite content of the time duration
between the end of the quenching treatment and the beginning of the
cryogenic treatment.
DETAILED DESCRIPTION
[0029] In percentages by weight, the treated steel comprises: 0.2%
to 0.33% carbon, 4% to 8% cobalt, 7% to 11% nickel, 0.8% to 3%
chromium, 0.5% to 2.5% molybdenum, 0.5% to 5.9% tungsten, 0.05% to
0.2% vanadium, and no more than 0.02% titanium, the balance being
constituted by iron and inevitable impurities.
[0030] In an embodiment, and in percentages by weight, the treated
steel comprises: 0.25% to 0.31% carbon, 6.8% to 8% cobalt, 9.3% to
10.5% nickel, 0.8% to 2.6% chromium, 0.9% to 2.1% molybdenum, 0.7%
to 2% tungsten, 0.05% to 0.12% vanadium, and no more than 0.015%
titanium, the balance being constituted by iron and inevitable
impurities.
[0031] In an embodiment, and in percentages by weight, the treated
steel comprises: 0.29% to 0.31% carbon, 6.8% to 7.2% cobalt, 9.8%
to 10.2% nickel, 0.8% to 2.6% chromium, 0.9% to 2.1% molybdenum,
0.7% to 1.4% tungsten, 0.05% to 0.12% vanadium, and no more than
0.015% titanium, the balance being constituted by iron and
inevitable impurities.
[0032] The method begins with a temperature rise ramp (step E1) up
to a temperature Ts, lying in the range 950.degree. C. to
1100.degree. C.
[0033] Thereafter the temperature Ts is maintained in order to
subject the steel to solutionizing heat treatment (step E2). The
duration of the steel solutionizing heat treatment E2 may be
greater than or equal to 1 hour, e.g. lying in the range 1 hour to
2 hours.
[0034] The steel is then subjected to quenching treatment (step E3)
at the end of the solutionizing treatment E2. The quenching
treatment E3 consists in cooling the steel rapidly by immersing it
in a cooling fluid such as water or oil. During the quenching
treatment E3, the steel is cooled to an end-of-quenching
temperature Ta. In the example shown, this end-of-quenching
temperatures Ta is equal to ambient temperature (20.degree. C.),
but it would not go beyond the ambit of the invention for it to be
different from ambient temperature, e.g. higher than ambient
temperature. The end-of-quenching temperature Ta may be less than
or equal to 71.degree. C., and in an embodiment less than or equal
to 50.degree. C. In particular, the end-of-quenching temperature Ta
may lie in the range 16.degree. C. to 71.degree. C. At the end of
the quenching treatment E3, the steel is no longer being cooled by
exchanging heat with the above-mentioned cooling fluid used for
quenching. At that moment, the temperature of the steel is equal to
the end-of-quenching temperature Ta.
[0035] Where necessary, after quenching E3 and before placing the
steel in the cryogenic enclosure, a first intermediate step (step
E4) may be performed during which the steel is maintained in an
environment at ambient temperature Ta. In a variant, this first
intermediate step E4 may be omitted, and the steel may be placed
directly in the cryogenic enclosure after the quenching treatment
E3. Naturally, when it is performed, this first intermediate step
E4 is of limited duration so that the time duration between the end
of the quenching treatment E3 and the beginning of the cryogenic
treatment also remains limited, as mentioned above.
[0036] Once the steel has been placed in the cryogenic enclosure,
the inside of the enclosure is then cooled down (step E5).
[0037] This cooling comprises a temperature lowering ramp down to
the treatment temperature Tc, which is less than or equal to
-73.degree. C. The rate of cooling imposed during this temperature
lowering ramp may be greater than or equal to 0.5.degree. C. per
minute (C.degree./min), e.g. greater than or equal to 1.5.degree.
C./min, or indeed greater than or equal to 2.5.degree. C./min, or
indeed greater than or equal to 5.degree. C./min. This rate of
cooling may also be less than or equal to 4.degree. C./min. This
imposed rate of cooling may be substantially constant. It would not
go beyond the ambit of the invention for the rate of cooling to
vary during the cooling step E5, so the cooling step E5 could thus
comprise a first temperature drop at a first rate of cooling,
followed by a second temperature drop at a second rate of cooling
different from the first, e.g. slower than the first.
[0038] As mentioned above, an aspect of the invention limits the
time duration between the end of the quenching treatment E3,
corresponding to the moment when the end-of-quenching temperature
Ta is reached, and the beginning of the cryogenic treatment E6,
corresponding to the moment when the treatment temperature Tc is
reached. This duration corresponds to the time duration after the
end of quenching E3 during which the steel is at a temperature
higher than the treatment temperature Tc. Limiting this duration
serves to limit the residual austenite content. FIG. 2 shows a
result of a comparative test performed on a Ferrium.RTM. M54 steel
while using an end-of-quenching temperature Ta of 20.degree. C. and
a treatment temperature Tc of -73.degree. C. In that test, the time
duration between the end of the quenching treatment and the
beginning of the cryogenic treatment was varied. It can be seen
that the longer that time duration, the greater the increase in the
residual austenite content in the steel. The inventors have also
carried out a comparative test in order to determine the influence
on the stress-corrosion resistance of the steel of the time
duration between the end of the quenching treatment and the
beginning of the cryogenic treatment. In that test, the
stress-corrosion resistance of the steel was measured as follows:
an initial crack was made in the test piece, which was wetted with
a solution of NaCl, and then a constant stress was imposed on the
sample, and at the end of 1000 hours (h), the K1SCC was determined.
At the end of 1000 h, the test piece was broken in static manner,
thereby enabling its K1SCC to be determined from the size of the
initial crack and the value of the load. K1SCC is a parameter known
to the person skilled in the art for quantifying stress-corrosion
resistance. The test that was performed showed that the
stress-corrosion resistance of the steel was significantly better
when the steel had been subjected to treatment in which the time
duration between the end of the quenching treatment and the
beginning of the cryogenic treatment was limited to 2 hours,
compared with the situation not in the invention when the duration
was 8 hours.
[0039] The installation suitable for performing the method is
itself known. Such an installation comprises a cryogenic enclosure
connected to a tank of cooling fluid together with a control system
configured to control the rate at which the cooling fluid is
introduced into the inside of the enclosure, and the rate at which
it is discharged out therefrom. The cooling fluid may be introduced
into the inside of the enclosure while in the gaseous state. Under
such circumstances, the cooling fluid may be vaporized outside the
enclosure and then the cooling fluid in the gaseous state as
generated in that way can be introduced into the inside of the
enclosure through at least one injection port. As a result of
controlling the introduction and discharge flow rates, it is
possible to obtain the desired rate of cooling, which contributes
to obtaining the desired duration between the end of quenching E3
and the beginning of the cryogenic treatment E6. This control over
the introduction and discharge flow rates also makes it possible to
maintain the treatment temperatures Tc during the cryogenic
treatment. As an example of a cryogenic installation that is
suitable, mention may be made of the liquid nitrogen type fluid
Linde Gas VF TES installation.
[0040] There is then a temperature stabilization dwell, during
which the treatment temperatures Tc is maintained in order to
perform the cryogenic treatment of the steel (step E6). The
duration of the cryogenic treatment E6 is predetermined, and may be
greater than or equal to 1 hour, e.g. lying in the range 1 to 2
hours.
[0041] Once the cryogenic treatment E6 has been performed, the
temperature may be raised progressively up to ambient temperature
Ta (step E7).
[0042] If so desired, it is then possible to perform a second
intermediate step E8 during which the steel is maintained in an
environment at ambient temperature Ta.
[0043] Thereafter, a temperature raising ramp may be performed
(step E9) up to a tempering temperature Tr, e.g. lying in the range
465.degree. C. to 550.degree. C.
[0044] A temperature stabilization dwell at the tempering
temperature Tr is then carried out in order to perform the
tempering heat treatment (step E10). The duration of the tempering
heat treatment may be greater than or equal to 4 hours, for example
it may lie in the range 4 hours to 32 hours.
[0045] The steel may then be cooled, e.g. by maintaining it in an
environment at ambient temperature.
[0046] The term "lying in the range . . . to . . . " should be
understood as including the bounds.
* * * * *