U.S. patent application number 16/121578 was filed with the patent office on 2019-03-07 for sorption heat transfer module.
The applicant listed for this patent is Mahle International GmbH. Invention is credited to Roland Burk, Lars Ludwig.
Application Number | 20190072302 16/121578 |
Document ID | / |
Family ID | 65364055 |
Filed Date | 2019-03-07 |
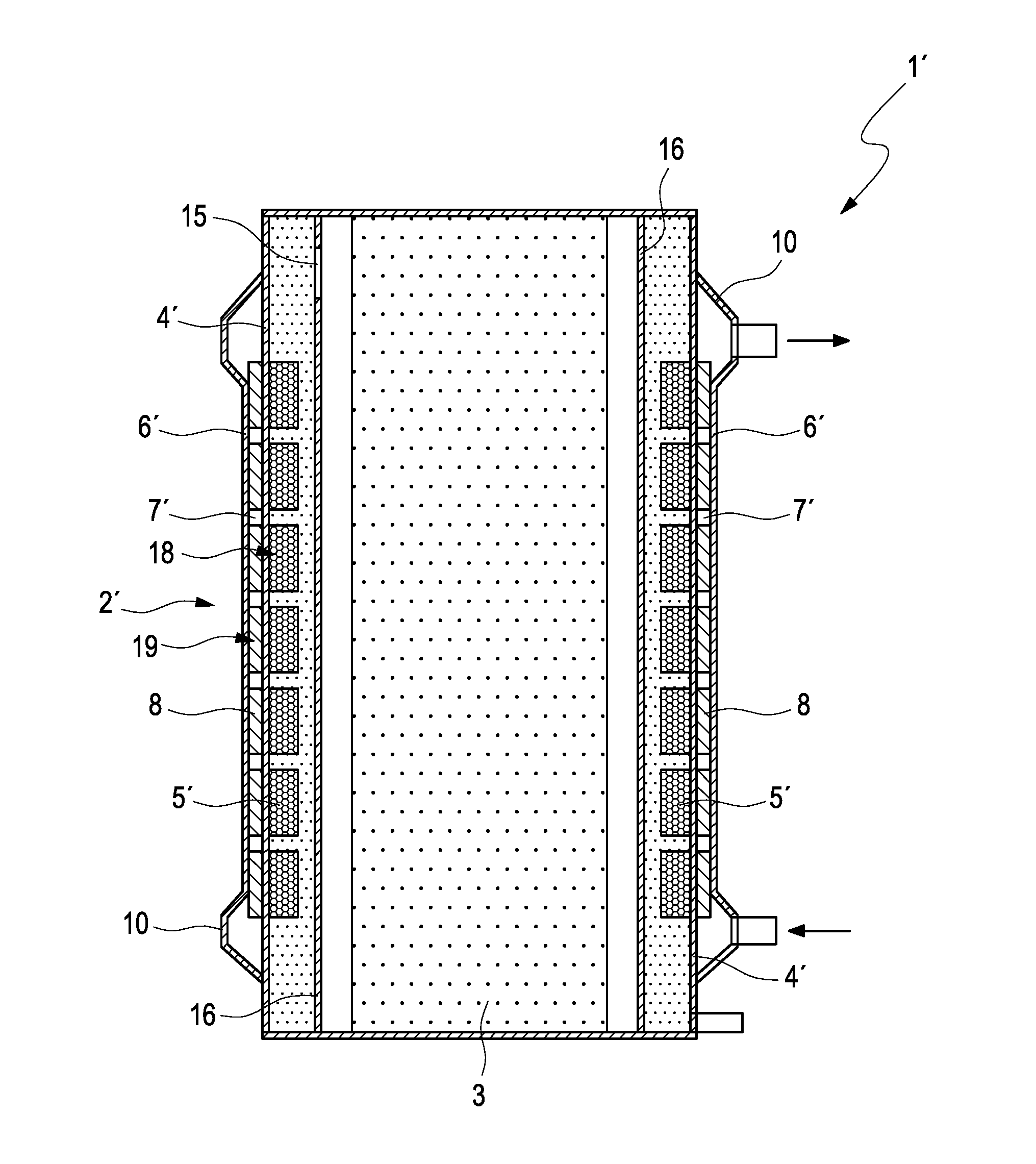



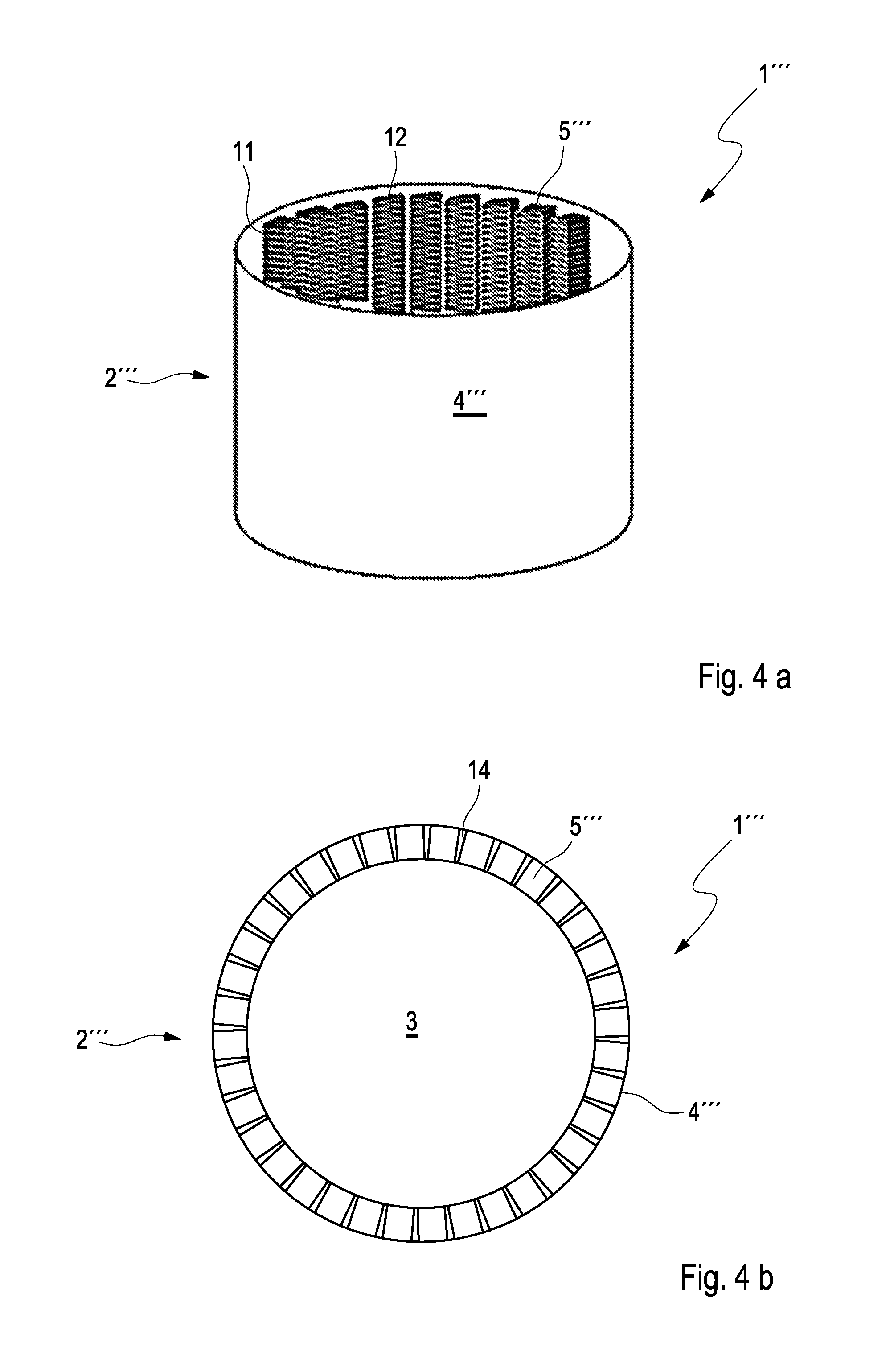
United States Patent
Application |
20190072302 |
Kind Code |
A1 |
Burk; Roland ; et
al. |
March 7, 2019 |
SORPTION HEAT TRANSFER MODULE
Abstract
A sorption heat transfer module may include a thermally
activatable housing enclosing a sorption zone through which a
working medium is flowable. The thermally activatable housing may
include a gas-tight inner wall composed of a corrosion-protected
material, an internal surface of which is adjoined by a capillary
structure. The capillary structure may include at least one
corrugated fin package connected in a firmly bonded manner to the
internal surface of the inner wall.
Inventors: |
Burk; Roland; (Stuttgart,
DE) ; Ludwig; Lars; (Altbach, DE) |
|
Applicant: |
Name |
City |
State |
Country |
Type |
Mahle International GmbH |
Stuttgart |
|
DE |
|
|
Family ID: |
65364055 |
Appl. No.: |
16/121578 |
Filed: |
September 4, 2018 |
Current U.S.
Class: |
1/1 |
Current CPC
Class: |
F25B 35/04 20130101;
Y02A 30/27 20180101; F25B 2500/01 20130101 |
International
Class: |
F25B 35/04 20060101
F25B035/04 |
Foreign Application Data
Date |
Code |
Application Number |
Sep 5, 2017 |
DE |
102017215617.1 |
Aug 1, 2018 |
DE |
102018212820.0 |
Claims
1. A sorption heat transfer module comprising: a thermally
activatable housing enclosing a sorption zone through which a
working medium is flowable; the thermally activatable housing
including a gas-tight inner wall composed of a corrosion-protected
material, an internal surface of which is adjoined by a capillary
structure including at least one corrugated fin package connected
in a firmly bonded manner to the internal surface of the inner
wall.
2. The sorption heat transfer module according to claim 1, wherein
the thermally activatable housing further includes an outer wall
enclosing the inner wall and together with the inner wall forms an
annular channel though which a heat transfer agent is axial
flowable.
3. The sorption heat transfer module according to claim 2, wherein
the inner wall and the outer wall are each configured
cylindrically, the inner wall arranged coaxially and concentrically
in the outer wall, the annular channel is arranged radially between
the inner wall and the outer wall.
4. The sorption heat transfer module according to claim 3, wherein
the annular channel smaller dimensions in a radial direction than
the capillary structure.
5. The sorption heat transfer module according to claim 2, wherein
the annular channel includes at least one of an inlet-side annular
beading and an outlet-side annular beading.
6. The sorption heat transfer module according to claim 1, further
comprising a heat-conducting structure adjoining an external
surface of the inner wall, which is connected in a firmly bonded
manner to the inner wall.
7. The sorption heat transfer module according to claim 3, further
comprising a heat-conducting structure adjoining an external
surface of the inner wall, which is connected in a firmly bonded
manner to the inner wall, wherein the heat-conducting structure is
arranged in the annular channel.
8. The sorption heat transfer module according to claim 7, wherein
the heat-conducting structure extends in an annular manner in the
annular channel.
9. The sorption heat transfer module according to claim 7, wherein
the heat-conducting structure extends from the inner wall in the
annular channel and over at least 80% of a radial channel width of
the annular channel.
10. The sorption heat transfer module according to claim 7, further
comprising a thermally insulating layer arranged in the annular
channel radially between the heat-conducting structure and the
outer wall.
11. The sorption heat transfer module according to claim 10,
wherein the thermally insulating layer abuts radially inwards
against the heat-conducting structure and radially outwards against
the outer wall.
12. The sorption heat transfer module according to claim 6, wherein
the heat-conducting structure has smaller dimensions in a radial
direction than the capillary structure.
13. The sorption heat transfer module according to claim 1,
wherein: the at least one corrugated fin package includes a
plurality of corrugated fin packages; and at least one of i) at
least one tip and ii) at least one front face of each of the
plurality of corrugated fin packages is connected in a firmly
bonded manner to the inner wall.
14. The sorption heat transfer module according to claim 13,
wherein the plurality of corrugated fin packages includes a
plurality of through-openings in a rolling plane, which allow an
axial passage of the working medium between the inner wall and the
plurality of corrugated fin packages arranged thereon.
15. The sorption heat transfer module according to claim 14,
wherein at least two of the plurality of through openings are
arranged between two axially adjacent corrugated fin packages of
the plurality of corrugated fin packages capillary structure
arranged offset with respect to one another in a circumferential
direction.
16. The sorption heat transfer module according to claim 13,
wherein at least two axially adjacent corrugated fin packages of
the plurality of corrugated fin packages are connected in a firmly
bonded manner on a front side and are arranged offset with respect
to one another in a circumferential direction.
17. The sorption heat transfer module according to claim 13,
wherein the plurality of corrugated fin packages are connected in a
firmly bonded manner on a front side and are disposed spaced apart
from one another in a circumferential direction such that a
plurality of wedge-shaped axial flow channels are formed between
each of the plurality of corrugated fin packages.
18. The sorption heat transfer module according to claim 1, wherein
the at least one corrugated fin package includes a plurality of
corrugated fin packages are arranged spaced apart from one another
in a circumferential direction and an axial direction on the inner
wall.
19. The sorption heat transfer module according to claim 1, wherein
the at least one corrugated fin package has at least one of i) a
fin density of 200 Ri/dm to 400 Ri/dm, and ii) a width of 10 mm to
30 mm.
20. The sorption heat transfer module according to claim 1,
wherein: at least one of i) the inner wall is composed of a
corrosion-protected steel material and ii) the capillary structure
is composed of a copper material; and the working medium is an
alcoholic fluid.
21. The sorption heat transfer module according to claim 1, wherein
the thermally activatable housing is cylindrical.
22. The sorption heat transfer module according to claim 1, wherein
the thermally activatable housing further includes a dividing wall
with at least one through opening which extends between the
capillary structure and the sorption zone.
Description
CROSS-REFERENCE TO RELATED APPLICATIONS
[0001] This application claims priority to German Patent
Application No. DE 10 2017 215 617.1, filed on Sep. 5, 2017 and
German Patent Application No. DE 10 2018 212 820.0, filed on Aug.
1, 2018, the contents of both of which are incorporated herein by
reference in their entirety.
TECHNICAL FIELD
[0002] The present invention relates to a sorption heat transfer
module.
BACKGROUND
[0003] Thermally driven sorption refrigeration systems have a high
energy saving potential since inexpensive waste and excess heat is
as used as drive energy and as a result, the pressure on the
electrical networks can be reduced, particularly in hot time and
climate zones with a high refrigeration requirement. These
installations can also be used as heat pumps which by means of
burner heat raise additional environmental heat to a temperature
level sufficient for heating purposes, with the result that the
fuel requirement can be reduced.
[0004] Of particular interest here are adsorption systems in which
porous solids are used and which have no moving parts which are
therefore liable to wear in the working medium area. The greatest
obstacle to the introduction of these systems on the market can be
attributed to the relatively low power densities hitherto achieved
and the still too-high power costs.
[0005] The published German Patent Application DE 10 2011 079 586
A1 describes such a sorption module whose housing design is however
still very complex and is a source of some loss mechanisms. A
disadvantage is the complex design with a fairly large number of
joints to be sealed hermetically.
[0006] A further development for the solution of these problems is
disclosed with the published German Patent Application DE 10 2014
223 040 A1 in which a housing wall is configured as a heat transfer
structure, with the result that the number of passive housing walls
is reduced. As a result, some loss effects are reduced. Due to a
largely cylindrical formation of the housing structure, support
means for receiving pressure differential forces can be dispensed
with, which brings with it cost advantages.
[0007] A disadvantage of the proposed cylindrical module concept
however is the quality of the thermal connection of the phase
change structures to a fluid heat transfer medium and the
comparatively large thermal mass, which has a harmful effect on the
power density and the efficiency of the sorption module.
Furthermore, there is the problem that depending on the
installation position of the cylinder module, it can occur that
condensate bound in the capillary structure can be displaced in the
entire structure due to gravitational and acceleration effects. For
example, condensed working medium can accumulate in low-lying
regions, with the result that conversely high-lying regions of the
capillary structure dry out too rapidly during the evaporation
phase.
[0008] Another weak point of the said embodiment of the housing
jacket carrying this capillary structure is the difficulty of
applying the internal capillary structure with very good thermal
contact. For this a metal firmly bonded connection preferably by
soldering should be strived for, which is made difficult by the
protective oxide layer of stainless steel.
[0009] A third weak point of the last-mentioned module design is
the heat transfer coefficient k on the side of the heat transfer
agent, which serves to remove or supply the condensation heat and
the heat of evaporation with the smallest possible driving
temperature difference.
SUMMARY
[0010] The present invention is concerned with the problem of
providing an improved cylindrical sorption module with thermally
activatable housing. This problem is solved according to the
invention by the subject matter of the independent claim(s).
Advantageous embodiments are the subject matter of the dependent
claim(s).
[0011] The present invention is based on the general idea that a
housing with suitable structures simultaneously provides a heat
transfer surface in order to transfer condensation heat and/or
evaporation heat with very good heat transfer to a or from a fluid
heat transfer medium. By multiple usage of components and
structures, a substantial contribution can thus be made to
increasing the volumetric power density, the efficiency and also to
reducing the manufacturing costs. The first two optimization
criteria in this case require a structure combination by means of
which a total heat transfer coefficient from the heat transfer
medium to the phase change structure and from there to the
saturation temperature of the working medium vapour of overall 1500
W/m.sup.2*K is exceeded. The individual thermal resistances of the
heat transfer path must therefore be minimized under the boundary
condition of minimal production costs for material and joining
processes.
[0012] For this purpose a sorption heat transfer module having a
thermally activatable housing is provided which encloses a sorption
zone through which a working medium can flow, and in which the
housing according to the invention comprises a gastight inner wall
made of a corrosion-protected material, the internal surface of
which is adjoined by a capillary structure which consists of at
least one corrugated fin package which is connected in a firmly
bonded manner to the internal surface of the inner wall. This
results in an extremely efficient phase change structure which is
particularly easy to manufacture and at the same time very well
connected, which provides a sorption heat transfer module having a
high efficiency. The term "gas-tight" should not be understood to
be absolute in the present connection but relative, i.e. related to
the present case of application. In other words, the gas-tight
inner wall is substantially tight for the gases which usually occur
in such a sorption heat module whereas tightness e.g. with respect
to hydrogen gas is not required.
[0013] In a preferred embodiment of the sorption heat transfer
module according to the invention, it is provided that the
thermally activatable housing comprises an outer wall which
encloses the gas-tight inner wall and together with the inner wall
forms an annular channel for a heat transfer agent through which
axial flow can take place. Via this annular channel, a heat
transfer agent can flow particularly simply and specifically
through the sorption heat transfer module according to the
invention and the condensation heat can be efficiently removed.
[0014] A particularly compact design can be achieved if the inner
wall and the outer wall are each configured cylindrically, if the
inner wall is arranged coaxially and concentrically in the outer
wall and if the annular channel is arranged radially between inner
wall and outer wall.
[0015] This compact design can be assisted by the fact that the
annular channel has smaller dimensions in the radial direction than
the capillary structure.
[0016] Expediently it can be provided that the annular channel has
respectively one inlet-side and/or outlet-side annular beading. The
inlet-side annular beading can serve as a distribution box whilst
the outlet-side annular beading can serve as a collecting box.
[0017] The solution according to the invention consists in
particular in using corrosion-protected steel such as, for example,
stainless steel, zinc-plated, nickel-plated or particularly
preferably tin-plated steel (tin sheet) as material for a gas-tight
housing wall. Additionally preferred is a cylindrical housing
geometry fabricated from longitudinally welded or optionally formed
steel tubes. The capillary structure is preferably made of
optionally tin-plated copper strip as phase change structure for
condensation, capillary binding of condensed working medium,
preferably methanol and re-evaporation of the condensate, wherein
closed corrugated fin annular packages are provided for soldering
to the inner wall of the corrosion-protected housing. In a first
embodiment of the sorption heat transfer module according to the
invention, the application of the corrugated fin packages is
provided here in such a manner that the tips of these corrugated
fin packages are soldered to an internal surface of the inner wall.
In a particularly preferred second embodiment of the sorption heat
transfer module according to the invention, the application of the
corrugated fin packages is additionally provided in such a manner
that the front faces of the corrugated fin packages are soldered to
the internal surface of the inner wall.
[0018] Accordingly, in a production process firstly a soft-soldered
assembly can be created consisting of a gas-tight cylinder with
internally soldered-on capillary structures and externally
soldered-on corrugated fins and in a second step this assembly can
be completed by an outer wall which with the gas-tight inner wall
forms an annular channel through which axial flow can take place so
that the inner assembly can be thermally activated by flow with a
heat transfer agent.
[0019] The term `corrugated fins" and fin packages made from these
are understood as continuously rollable zig-zag structures made of
thin-walled metal strip which can be formed very differently in
detail, for example with or without gills.
[0020] In a further preferred embodiment of the sorption heat
transfer module according to the invention, it is provided that a
heat-conducting structure adjoins an external surface of the
gas-tight inner wall, which is connected in a firmly bonded manner
to the inner wall and which preferably consists of at least one
corrugated fin package. This heat-conducting structure appreciably
increases the efficiency of the sorption heat transfer module and
can be produced in a modular manner similar to the capillary
structure. It is preferred here that a thermally insulating layer,
preferably a silicone foam mat, is inserted between the
heat-conducting structure and the outer wall in order to ensure
thermal insulation of the annular channel towards the outside and
to minimize the connected thermal mass. A silicone foam mat is
specifically available as prefabricated material in different
dimensions and is particularly easy to process. Particularly
preferably the annular channel has respectively one inlet-side
and/or outlet-side annular beading which is used for a homogeneous
distribution of the axially directed volume flow of a heat transfer
agent in the circumferential direction.
[0021] It is particularly advantageous here if the heat-conducting
structure is arranged here in the aforesaid annular channel. By
this means the heat can be efficiently transferred between the
fluidic heat transfer agent flowing in the annular channel and the
inner wall.
[0022] Advantageous here is a further development in which the
heat-conducting structure extends in an annular manner in the
annular channel. By this means a large volume of the annular space
can be used by the heat-conducting structure which improves the
efficiency of the heat transfer.
[0023] Another further development additionally or alternatively
proposes that the heat-conducting structure extends starting from
the inner wall in the annular channel over at least 80%, preferably
over at least 90% of a radial channel width of the annular channel.
This also improves the utilization of the space present in the
annular channel.
[0024] The efficiency of the heat transfer between the heat
transfer agent and the inner wall can also be improved whereby a
thermally insulating layer, preferably a silicone foam mat, is
arranged in the annular channel radially between the
heat-conducting structure and the outer wall. This reduces any heat
transfer between the heat-conducting structure and the outer wall
or between heat transfer agent and outer wall.
[0025] Particularly advantageous is a further development in which
the individual components are matched to one another so that the
thermally insulating layer abuts radially inwards against the
heat-conducting structure and radially outwards against the outer
wall. By this means the space provided in the annular channel is
maximally utilized radially by the heat-conducting structure
without there being any radial contact between the heat-conducting
structure and the outer wall.
[0026] The compact design can also be assisted if according to one
embodiment, the heat-conducting structure has smaller dimensions in
the radial direction than the capillary structure.
[0027] In an even further preferred embodiment of the sorption heat
transfer module according to the invention, it is provided that
tips or front faces of individual corrugated fin packages of the
capillary structure and/or heat-conducting structure are connected
in a firmly bonded manner to the inner wall and are preferably
located opposite the corrugated fin packages of the capillary
structure and the heat-conducting structure so that they overlap.
The firmly bonded connection of tips or front faces and preferred
opposite position of the two structures here ensures a particularly
good thermal contact via the inner wall. Preferably the corrugated
fin packages of the capillary structure which are connected in a
firmly bonded manner on the front side have through-openings in a
rolling plane, which allow an axial passage of the working medium
between the inner wall and the corrugated fin packages arranged
thereon. This results in the advantage that the individual
corrugated fin packages can easily be applied and at the same time
there is an axially assisted vapour flow with external gas flushing
effect. Particularly preferably here at least two of the through
openings are arranged between two axially adjacent corrugated fin
packages of the capillary structure offset with respect to one
another in the circumferential direction in order to enable a
flushing transport of undesirable non-condensable external gases in
the principal flow direction. Alternatively or additionally at
least two of the axially adjacent corrugated fin packages connected
in a firmly bonded manner on the front side are arranged offset
with respect to one another in the circumferential direction.
However, the corrugated fin packages of the capillary structure
connected in a firmly bonded manner on the front side can also be
arranged axially parallel and spaced apart from one another in the
circumferential direction, preferably arranged spaced apart from
one another in a contact-free manner, so that wedge-shaped axial
flow channels are formed between the individual corrugated fin
packages. As a result of the contact-free arrangement, a capillary
contact between individual corrugated fin packages is avoided,
whilst at the same time a tight occupancy of the phase change zone
is ensured and furthermore, external gases can be flushed out in an
axially parallel manner and can accumulate in a passive axial end
region of the phase change structure.
[0028] In yet another preferred embodiment of the sorption heat
transfer module according to the invention, it is provided that
individual corrugated fin packages of the capillary structure are
arranged spaced apart from one another in the circumferential
direction and axial direction on the gastight inner wall,
preferably at an axial distance between 1 mm and 4 mm, particularly
preferably at an axial distance between 2 mm and 3 mm. Specifically
with the choice of these distances, in practice displacement
effects of condensate due to gravity and accelerations can be
avoided and a particularly high flushing capacity for external
gases of the sorption heat transfer module can be established
without adversely affecting its efficiency.
[0029] In yet another preferred embodiment of the sorption heat
transfer module according to the invention, it is provided that the
corrugated fin packages of the capillary structure have a fin
density between 200 Ri/dm and 400 Ri/dm, and/or a width of the
corrugated fin packages of the capillary structure lies between 10
mm and 30 mm, preferably between 15 mm and 25 mm. With the choice
of these dimensions, in practice a particularly high efficiency of
the sorption heat transfer module can be demonstrated.
[0030] In yet another preferred embodiment of the sorption heat
transfer module according to the invention, it is provided that the
gas-tight inner wall is made of a corrosion-protected steel
material, in particular a zinc-plated, nickel-plated or tin-plated
steel, and/or the capillary structure and/or the heat-conducting
structure is made of a copper material, in particular a tin-plated
copper strip, which is preferably soft soldered to the gas-tight
inner wall and the working medium is an alcoholic fluid, in
particular methanol or ethanol. The said combination of materials
is due to the alcoholic working media such as methanol or ethanol.
If water is used as working medium, aluminium-based materials can
also be used. However, the preferred materials have the advantage
that these can be soft-soldered cost-effectively.
[0031] In yet another preferred embodiment of the sorption heat
transfer module according to the invention, it is provided that the
thermally activatable housing is designed to be cylindrical and is
preferably made of longitudinally welded, particularly preferably
formed steel tubes. A cylindrical design has a high differential
compressive strength and merely requires forming steps which can be
implemented cost-effectively.
[0032] In yet another preferred embodiment of the sorption heat
transfer module according to the invention, it is provided that the
thermally activatable housing has a dividing wall provided with at
least one through opening which extends between the capillary
structure and the sorption zone. The dividing wall is used here for
thermal separation of the two different temperature-controlled
zones of the sorption heat transfer module, wherein transport of
the vaporous working medium between the zones takes place via the
at least one through opening.
[0033] Further important features and advantages of the invention
are obtained from the subclaims, from the drawings and from the
relevant description of the figures with reference to the
drawings.
[0034] It is understood that the features mentioned previously and
to be explained further hereinafter can be used not only in the
respectively given combination but also in other combinations or
alone without departing from the scope of the present
invention.
[0035] A preferred exemplary embodiment of the invention is shown
in the drawings and will be explained in detail in the following
description, wherein the same reference numbers relate to the same
or similar or functionally the same components.
BRIEF DESCRIPTION OF THE DRAWINGS
[0036] In the figures, in each case schematically:
[0037] FIG. 1a shows a radial section through a first sorption heat
transfer module according to the invention with thermally
activatable housing;
[0038] FIG. 1b shows a detailed view of the thermally activatable
housing of the sorption heat transfer module from FIG. 1a;
[0039] FIG. 2 shows an axial section through a further sorption
heat transfer module according to the invention with thermally
activatable housing and a dividing wall between phase change
structure and sorption zone;
[0040] FIG. 3a shows a perspective view of yet another sorption
heat transfer module according to the invention with corrugated
fins soldered on the front side;
[0041] FIG. 3b shows a plan view of the sorption heat transfer
module from FIG. 3a;
[0042] FIG. 4a shows a perspective view of yet another sorption
heat transfer module according to the invention with corrugated
fins soldered on the front side and
[0043] FIG. 4b shows a plan view of the sorption heat transfer
module from FIG. 4a.
DETAILED DESCRIPTION
[0044] FIG. 1a shows a radial section through a first sorption heat
transfer module 1 according to the invention with thermally
activatable housing 2. This housing 2 encloses a sorption zone 3,
which according to the known prior art comprises a plurality of
flat tubes which with adsorption shaped bodies are applied to the
flat tubes by means of adhesive bonding with good thermal contact.
Furthermore, according to the prior art, the inner region can
contain further installations for extending the functionality
and/or for reducing the loss effects during operation of the
sorption heat transfer module 1 which however are not the subject
of the present invention.
[0045] In this first embodiment as a phase change structure, an
annular corrugated fin package 5 rolled from tin-plated copper
strip is applied by soft soldering with good thermal contact to the
internal surface of a gas-tight inner wall 4 which here consists of
tin plate. This corrugated fin package 5 here represents a
capillary structure 18. The width of the at least one annular
corrugated fin package 5 is dimensioned so that with a preferred
fin density between 200 Ri/dm and 400 Ri/dm, the capillary force is
sufficient to hold condensed working medium in a fixed position
against gravity and optionally predictable acceleration forces. The
width of a corrugated fin package 5 lies between 10 mm and 30 mm,
preferably between 15 mm and 25 mm.
[0046] The housing 2 also comprises an outer wall 6 which together
with the gas-tight inner wall 4 forms an annular channel 7 which
has a fluidic, i.e. liquid and/or gaseous heat transfer agent
flowing through it in the axial direction. In order to increase the
thermal conductivity, a heat-conducting structure 19 in the form of
another corrugated fin package 8 is provided, which is
soft-soldered to the inner wall 4. For thermal insulation the outer
wall 6 is separated from the heat-conducting structure 19 by an
insulating layer 9.
[0047] In the axial direction of this inner wall 4, which is
designed to be cylindrical here merely as an example, a plurality
of such annular closed corrugated fin packages 5 are arranged
axially at a distance from one another in such a manner that no
capillary bridges are formed between the annular packages 5. This
is achieved by axial spacings between 1 and 4 mm. Particularly
preferred spacings lie in the range between 2 mm and 3 mm.
[0048] FIG. 1b shows a detailed view 17 of the thermally
activatable housing 2 of the sorption heat transfer module 1 from
FIG. 1a. It can be identified therein that the external surface of
the inner wall 4 has a fin structure which is also connected to
this inner wall 4 by soft soldering with very good thermal contact.
Together with the outer wall 6 the finned annular channel 7 is
thereby formed through which a heat transfer agent can be guided in
the axial direction with a very good heat transfer coefficient.
Furthermore, it can be seen that the outer wall 6 is not thermally
connected to the corrugated fin package 8 of the heat-conducting
structure 19 and is even spaced apart from the heat-conducting
structure 19 so that the thermal contact remains as small as
possible. An annular gap remaining between fin structure and outer
jacket can be filled by an insulating layer 9 such as a silicone
foam mat. The desired thermal decoupling with respect to the outer
wall 6 serves the purpose that the sensible heat is minimized
during thermal cycling of the sorption heat transfer module 1 by
reducing the connected thermal mass. In this first embodiment of a
sorption heat transfer module 1 according to the invention, the
corrugated fin packages 5 and 8 which are closed over the
circumference of the housing 2 are soft-soldered via their tips 11
to the gas-tight inner wall 4, whilst a front face 12 of the
individual corrugated fin packages 5 and 8 points in the axial
direction.
[0049] It can be further deduced from FIGS. 1a and 1b that the
inner wall 4 and the outer wall 6 are each cylindrically
configured, that the inner wall 4 is arranged coaxially and
concentrically in the outer wall 6 and that the annular channel 7
is arranged radially between the inner wall 4 and the outer wall 6.
It is further shown in FIG. 1b that the annular channel 7 has
smaller dimensions in the radial direction than the capillary
structure 18. In addition, as explained previously it is provided
that an external surface of the inner wall 4 is adjoined by said
heat-conducting structure 19, which is connected in a firmly bonded
manner to the inner wall 4 and which preferably consists of at
least one corrugated fin package 8. It can be seen here that the
heat-conducting structure 19 is arranged in the annular channel 7.
In addition, it is provided that the heat-conducting structure 19
extends in an annular form in the annular channel 7. Furthermore,
starting from the inner wall 4 the heat-conducting structure 19 can
extend in the annular channel 7 over 80% or over 85% or over 90% or
over 95% or more than 95% of a radial channel width 20 of the
annular channel 7. Particularly advantageously said thermally
insulating layer 9, preferably a silicone foam mat, can be arranged
in the annular channel 7 radially between the heat-conducting
structure 19 and the outer wall 6. The radial dimensions of annular
channel 7, heat-conducting structure 19 and insulating layer 9 are
matched to one another here so that the insulating layer 9 abuts
radially inwards against the heat-conducting structure 19 and
radially outwards against the outer wall 6. Finally it is provided
here that the heat-conducting structure 19 has smaller dimensions
in the radial direction than the capillary structure 18 whereas the
capillary structure 18 has larger dimensions in the radial
direction than the annular channel 7.
[0050] FIG. 2 shows an axial section through another sorption heat
transfer module 1' according to the invention with thermally
activatable housing 2' which simultaneously contains or forms the
phase change structure. The central, non-differentiated sorption
zone 3 and the structure of the thermally activatable housing 2'
with two annular distribution chambers for heat transfer agent can
substantially be identified. One of these distribution chambers is
formed by a cylindrical outer wall 6' together with a gas-tight
inner wall 4' and forms a finned annular channel 7' through which
flow can take place in the axial direction. Furthermore, seven
annular corrugated fin packages 5' can be identified in this
diagram as a condensate-storing phase change structure which is
soldered to the internal surface of the inner wall 4' with good
thermal contact.
[0051] The entire gas chamber between the central sorption zone 3
operated at higher temperature levels and the external phase change
zone which can be activated via the temperature-controllable inner
wall 4' is here divided into two partial chambers by another
cylindrical dividing wall 16. This dividing wall 16 is provided
with a through opening 15, via which the vaporous working medium is
transported between the two zones. The intermediate cylinder is
used for thermal separation of the two differently
temperature-controlled zones of the sorption heat transfer module
1'. The annular channel 7' has respectively one inlet-side and one
outlet-side annular beading 10, which is used for a homogeneous
distribution of the axially directed volume flow in the
circumferential direction.
[0052] FIG. 3a show a perspective view of yet another sorption heat
transfer module 1'' according to the invention with corrugated fins
5'' soldered on the front side, which are attached to an inner wall
4'' of a housing 2'' in several axial positions spaced apart from
one another. In this second embodiment of a sorption heat transfer
module according to the invention, it can be seen that the
corrugated fin packages 5'' are turned through 90.degree. there,
i.e. are soldered with their front faces 12 to the internal surface
of the inner wall 4''. Furthermore, these corrugated fin packages
5'' preferably have no gills or other inner openings in order to
reduce the harmful influence of a condensate displacement due to
gravity and acceleration effects. In this perspective view it can
be seen that here also a plurality of corrugated fin packages 5''
are arranged axially spaced apart above one another in order to
form a larger area of the housing 2'' as phase change zone. Since
in this second embodiment, the capillary retaining effect of the
corrugated fin packages 5'' in particular when the sorption heat
transfer module 1'' is installed in a vertical position has a
lesser importance due to the gill-less structure, the fin density
can be brought to lower values.
[0053] Preferably the corrugated fin packages 5'' which are
soldered on annularly on the inside have spaced-apart openings in
the circumferential direction which enable a small axially parallel
gas transport. These serve the purpose that non-condensable
external gases which accumulate there are flushed away in the
axially parallel direction and can accumulate in an axial end
region in order to be sucked away there in concentrated form as
required according to the prior art.
[0054] FIG. 3b shows a radial section through the sorption heat
transfer module 1'' from FIG. 3a in which two easy-to-implement
possibilities for achieving such rinsing channels are shown. For
example, before forming into a corrugated fin, the metal strip can
have through openings 13 in the form of recesses at the edge to be
soldered subsequently, which have the result that at certain
spacings the solder edge is set back so far that no soldering
occurs there. Particularly preferably the length of the edge
setback in the longitudinal direction of the strip is selected so
that at least a corrugation hill and/or corrugation valley of the
corrugated fin is not soldered on as is shown schematically in the
upper half of FIG. 3b.
[0055] The lower half of FIG. 3b shows a division of each
corrugated fin package 5'' into a plurality of separate, in the
present case, eight partial packages between which axial gas
transport is possible. Advantageously through openings 13' in the
form of interruptions of two corrugated fin packages 5'' arranged
one above the other, are arranged offset with respect to one
another in order to enable rinsing transport of undesirable
non-condensable external gases in the principal direction of
flow.
[0056] The through openings 13, 13' for axial gas transport serve
the purpose that non-condensable gases accumulating between the
corrugated fin packages 5'' cannot accumulate there in harmful
concentration but are transported following the principal direction
of flow in the direction of that axial end of the housing 2'' which
has a displacement chamber and/or a blow-off or extraction opening
through which these harmful gases can be removed from the housing
2'' as required.
[0057] The structure applied to the outside of the gas-tight inner
wall 4'' to improve the heat transfer on the heat transfer agent
side can be designed in a similar manner to the first embodiment of
FIG. 1. There also the fin structure can consist of a plurality of
annular layers, whose soldered connecting surfaces preferably
overlap with the annular phase change structures soldered on the
inside.
[0058] FIG. 4a shows a perspective view of yet another sorption
heat transfer module 1''' according to the invention with
corrugated fins soldered on the front side. There the individual
corrugated fin packages 5''' are soldered on the inner wall 4''' of
the sorption heat transfer module 1''' axially parallel to the
front face 12. The corrugated fin packages 5''' are connected in a
firmly bonded manner to the inner wall 4''', for example by soft
soldering. The outer finned structure for the axial flow through
the housing 2''' is not shown here.
[0059] FIG. 4b shows a radial section through the sorption heat
transfer module 1''' of FIG. 4a. It can be seen that wedge-shaped
axial flow channels 14 are formed between the individual corrugated
fin packages 5''' which enable an axial transport, for example of a
methanol vapour to be condensed and contribute towards a flushing
of non-condensable external gases onto an axial end of the gas
chamber. Preferably the corrugated fin packages 5''' are positioned
here so that on the one hand the highest possible surface density
of the cylinder is achieved but on the other hand the corrugated
fin packages 5''' do not touch each other. As a result of this
particularly preferred arrangement of the corrugated fin packages
5''', a displacement of condensate due to gravity and acceleration
in the horizontal and vertical position of the sorption module is
particularly effectively prevented.
[0060] According to the depicted fundamental embodiments of a
front-side or tip-side application of the corrugated fin packages 5
. . . 5''', the thermally activatable housing implemented according
to the invention affords manifold advantages compared to known
solutions. Thus, the very high attainable heat transfer coefficient
between fluid temperature and saturated vapour temperature of the
working medium only requires very small driving temperature
differences for the removal of condensation heat and supply of
evaporation heat and thereby increases the efficiency and the power
density of the sorption heat transfer module. In addition, the
optionally tin-plated semi-finished product materials such as for
example tin plate for the gas-tight inner wall and optionally
tin-plated copper strip for fabricating the phase change structure
in the form of corrugated fin packages having a high fin density
and thus attainable capillary condensate retaining function and the
surface-enlarging fin system of the annular channel for fluidic
flow enable a very cost-effective and thermally very good
conducting joining process of the three required structure
components. In particular, the particularly preferred second
embodiment of a sorption heat transfer module according to the
invention in FIGS. 3 and 4 makes it easy to vary the receiving
capacity of the phase change structure by varying the strip width.
In addition, the fin orientation of this embodiment avoids flow-off
effects of stored condensate since no passage paths are provided
due to a smooth gill-less fin design. This fin orientation is
therefore suitable both for horizontal and for vertical module
installation. This particularly preferred second embodiment
additionally has the advantage of easier applicability of the
individual corrugated fin packages and axially assisted vapour flow
with external gas flushing effect.
[0061] The axial flow through the housing 2 . . . 2''' is however
not necessarily advantageous. The material combination based on
steel materials is due to the favoured alcohol working media
(methanol, ethanol). When using water as working medium,
aluminium-based materials can also be used but these cannot be
soft-soldered cost-effectively. In general purely cylindrical
designs can also be avoided but these have a lower differential
compressive strength and require more complex forming methods
and/or thicker wall thicknesses such as, for example, internal
high-pressure forming.
* * * * *