U.S. patent application number 15/771847 was filed with the patent office on 2019-02-28 for copper alloy material.
This patent application is currently assigned to MITSUBISHI MATERIALS CORPORATION. The applicant listed for this patent is MITSUBISHI MATERIALS CORPORATION. Invention is credited to Kanta DAIRAKU, Toshio SAKAMOTO, Shoichiro YANO.
Application Number | 20190062874 15/771847 |
Document ID | / |
Family ID | 58695049 |
Filed Date | 2019-02-28 |

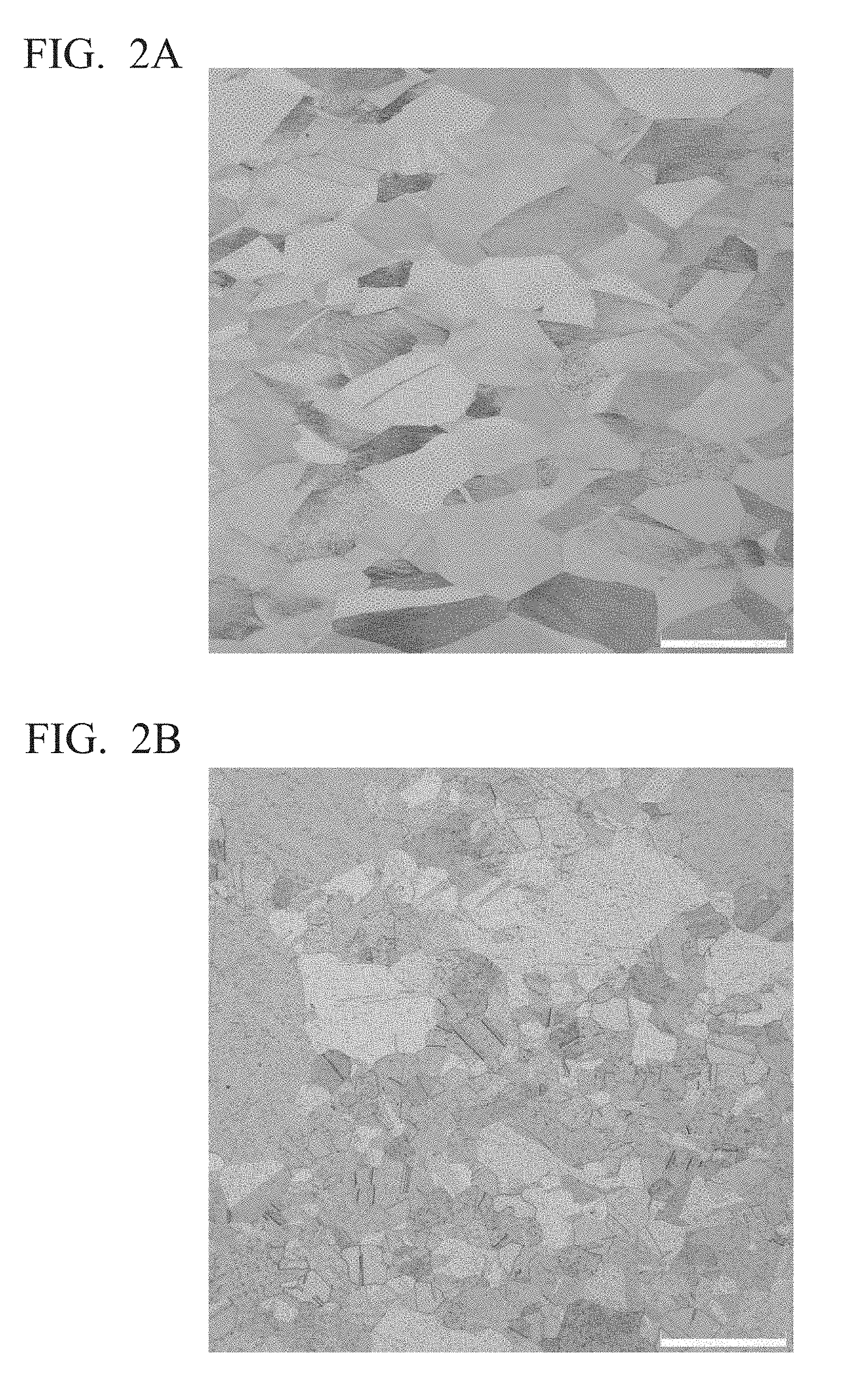
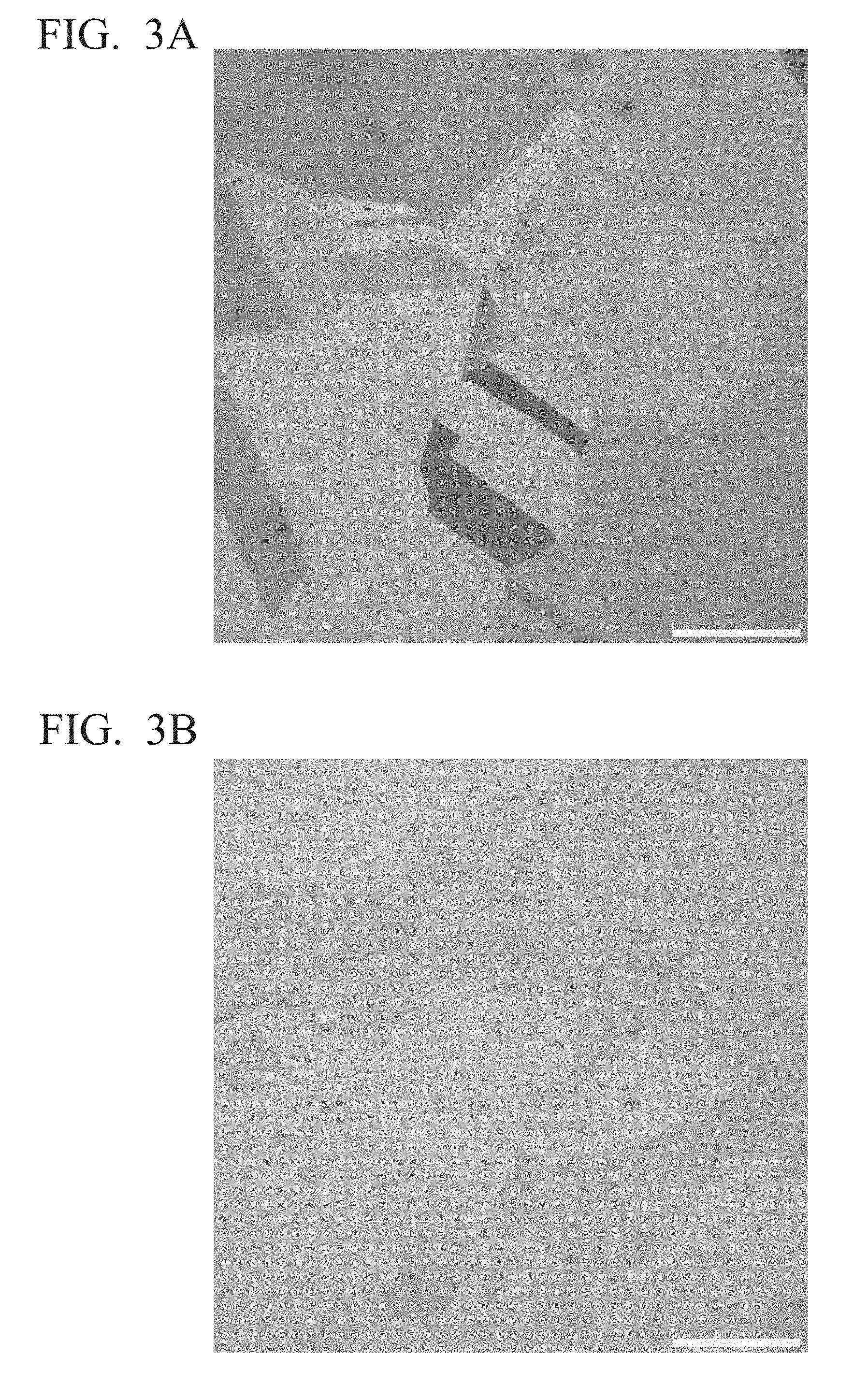

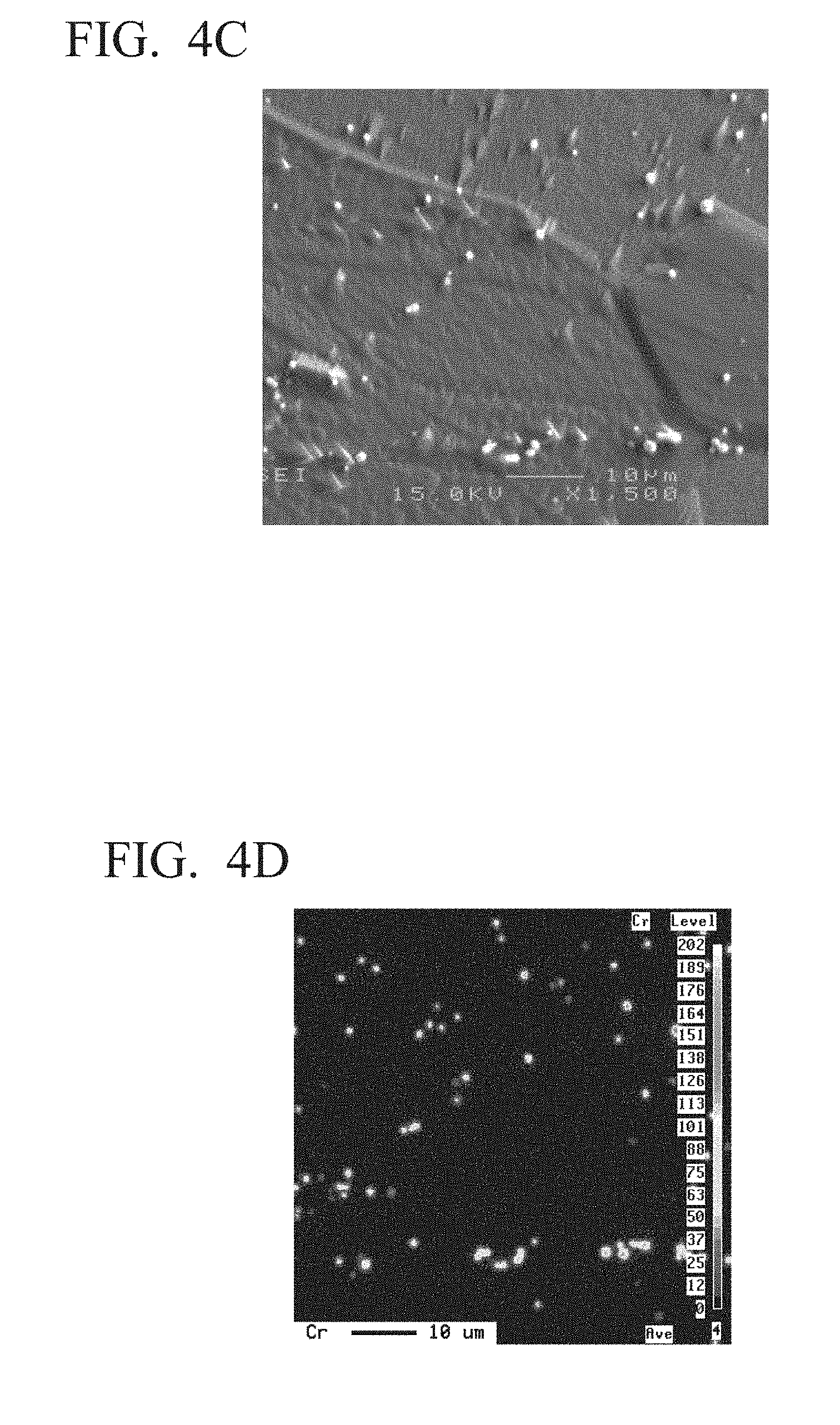
United States Patent
Application |
20190062874 |
Kind Code |
A1 |
YANO; Shoichiro ; et
al. |
February 28, 2019 |
COPPER ALLOY MATERIAL
Abstract
A copper alloy material has a composition including: 0.3 mass %
or more and less than 0.5 mass % of Cr; 0.01 mass % or more and
0.15 mass % or less of Zr; and a Cu balance including inevitable
impurities, wherein an average of crystal grain sizes is in a range
of 0.1 mm or more and 2.0 mm or less, and a standard deviation of
the crystal grain sizes is 0.6 or less.
Inventors: |
YANO; Shoichiro; (Iwaki-shi,
JP) ; DAIRAKU; Kanta; (Iwaki-shi, JP) ;
SAKAMOTO; Toshio; (Kitamoto-shi, JP) |
|
Applicant: |
Name |
City |
State |
Country |
Type |
MITSUBISHI MATERIALS CORPORATION |
Tokyo |
|
JP |
|
|
Assignee: |
MITSUBISHI MATERIALS
CORPORATION
Tokyo
JP
|
Family ID: |
58695049 |
Appl. No.: |
15/771847 |
Filed: |
October 11, 2016 |
PCT Filed: |
October 11, 2016 |
PCT NO: |
PCT/JP2016/080125 |
371 Date: |
April 27, 2018 |
Current U.S.
Class: |
1/1 |
Current CPC
Class: |
C22F 1/08 20130101; B22C
9/061 20130101; C22C 9/00 20130101; C22C 9/01 20130101 |
International
Class: |
C22C 9/01 20060101
C22C009/01; C22F 1/08 20060101 C22F001/08 |
Foreign Application Data
Date |
Code |
Application Number |
Nov 9, 2015 |
JP |
2015-219852 |
Claims
1. A copper alloy material having a composition including: 0.3 mass
% or more and less than 0.5 mass % of Cr; 0.01 mass % or more and
0.15 mass % or less of Zr; and a Cu balance including inevitable
impurities, wherein an average of crystal grain sizes is in a range
of 0.1 mm or more and 2.0 mm or less, and a standard deviation of
the crystal grain sizes is 0.6 or less.
2. The copper alloy material according to claim 1, wherein an area
ratio of crystallized Cr in cross section observation is 0.5% or
less.
3. The copper alloy material according to claim 1, wherein, after
performing a heat treatment at 1000.degree. C. for 1 hour
retention, an average of crystal grain sizes is in a range of 0.1
mm or more and 3.0 mm or less, and a standard deviation of the
crystal grain sizes is 1.5 or less.
4. The copper alloy material according to claim 1, wherein the
composition of the copper alloy material further includes Al in a
range of 0.1 mass % or more and 2.0 mass % or less.
5. The copper alloy material according to claim 1, wherein the
composition of the copper alloy material further includes one or
more elements selected from Fe, Co, Sn, Zn, P, Si and Mg in a range
of 0.005 mass % or more and 0.1 mass % or less as a total.
Description
CROSS-REFERENCE TO RELATED PATENT APPLICATIONS
[0001] This application is a U.S. National Phase Application under
35 U.S.C. .sctn. 371 of International Patent Application No.
PCT/JP2016/080125 filed on Oct. 11, 2016 and claims the benefit of
Japanese Patent Application No. 2015-219852, filed on Nov. 9, 2015,
all of which are incorporated herein by reference in their
entireties. The International Application was published in Japanese
on May 18, 2017 as International Publication No. WO/2017/081972
under PCT Article 21(2).
FIELD OF THE INVENTION
[0002] The present invention relates to a copper alloy material
suitable for a part used in a high temperature environment such as
a molding material for casting and a welding part such as a contact
tip.
BACKGROUND OF THE INVENTION
[0003] Conventionally, Cu--Cr--Zr-based alloys such as C18150 are
used as a material for casting mold materials and welding members
which are used at high temperatures, since they have excellent heat
resistance and electrical conductivity as shown in Japanese
Examined Patent Application, Second Publication No. S62-097748 and
Japanese Unexamined Patent Application, First Publication No.
H05-339688.
[0004] These Cu--Cr--Zr-based alloy are usually produced by a
production process, in which a cast made of Cu--Cr--Zr-based alloy
is subjected to a plastic working; a solution treatment, for
example in a condition of 950-1050.degree. C. of a retention
temperature and 0.5-1.5 hours of a retention time, and an aging
treatment, for example in a condition of 400-500.degree. C. of a
retention temperature and 2-4 hours of a retention time, are
performed on the plastically worked material; and then the material
subjected to the solution and aging treatments is finished into a
predetermined shape by machine working in the end.
[0005] In the above-described methods, Cr and Zr are dissolved in
the matrix of Cu by the solution treatment and fine precipitates of
Cr and Zr are dispersed by the aging treatment to improve strength
and conductivity.
Technical Problem
[0006] Although the above-described Cu--Cr--Zr-based alloy has
excellent heat resistance, when it is exposed to a use environment
with a peak temperature of 500.degree. C. or more, occasionally,
re-solution of precipitate starts for the strength and the
conductivity to be reduced and for coarsening of the crystal grain
to occur.
[0007] When coarsening of the crystal grains occurs, the
propagation speed of the crack increases and the service life of
the product may be shortened. In addition, there has been a problem
that mechanical properties such as strength and elongation are
remarkably deteriorated due to local occurrence of coarsening of
crystal grains.
[0008] The present invention has been made in view of the
above-described circumstances. An object of the present invention
to provide a copper alloy material which is stable in
characteristics and excellent in service life even when it is used
in a high temperature environment of 500.degree. C. or more.
SUMMARY OF THE INVENTION
Solution to Problem
[0009] To solve the above-described technical problem, an aspect of
the present invention is directed to a copper alloy material having
a composition including: 0.3 mass % or more and less than 0.5 mass
% of Cr; 0.01 mass % or more and 0.15 mass % or less of Zr; and a
Cu balance including inevitable impurities, wherein an average of
crystal grain sizes is in a range of 0.1 mm or more and 2.0 mm or
less, and a standard deviation of the crystal grain sizes is 0.6 or
less (hereinafter, referred as "a copper alloy material of the
present invention").
[0010] In the copper alloy material as configured above, the
composition includes 0.3 mass % or more and less than 0.5 mass % of
Cr; 0.01 mass % or more and 0.15 mass % or less of Zr; and a Cu
balance including inevitable impurities. Thus, by precipitating
fine precipitates by the aging treatment, strength (hardness) and
conductivity can be improved. In addition, crystallized Cr is
reduced since the Cr content is set to a relatively low level at
0.3 mass % or more and less than 0.5 mass %. Thus, occurrence of
unevenly-sized re-crystallized grains because of accumulation of
local strain due to these crystallized Cr can be suppressed.
Therefore, local coarsening of crystal grains can be suppressed
even in a case of being used under high temperature condition.
[0011] In addition, the average of the crystal grain sizes is set
in the range of 0.1 mm or more and 2.0 mm or less in the copper
alloy material of the present invention. Thus, accumulation of
strain is relatively low for the copper alloy material to be
re-crystallized. In addition, the standard deviation of the crystal
grain sizes is set to 0.6 or less. Thus, the crystal grain sizes
are uniform, accumulation of local strain is less. Accordingly,
local coarsening of crystal grains can be suppressed even in a case
of being used under high temperature condition.
[0012] In the copper alloy material of the present invention, it is
preferable that an area ratio of crystallized Cr in cross section
observation is 0.5% or less.
[0013] In this case, since the area ratio of the crystallized Cr in
cross section observation is set to 0.5% or less, accumulation of
local strain is less. Accordingly, local coarsening of crystal
grains can be reliably suppressed even in a case of being used
under high temperature condition.
[0014] In the copper alloy material of the present invention, it is
preferable that after performing a heat treatment at 1000.degree.
C. for 1 hour retention, an average of crystal grain sizes is in a
range of 0.1 mm or more and 3.0 mm or less, and a standard
deviation of the crystal grain sizes is 1.5 or less.
[0015] In this case, even after performing the heat treatment at
1000.degree. C. for 1 hour retention, crystal grains are not
coarsened and the crystal grain sizes are kept relatively uniform.
Accordingly, mechanical properties and conductivity are stable even
in a case of being used under high temperature condition at
500.degree. C. or more.
[0016] In the copper alloy material of the present invention, the
composition of the copper alloy material may further include Al in
a range of 0.1 mass % or more and 2.0 mass % or less.
[0017] In this case, since the composition of the copper alloy
material further includes Al in a range of 0.1 mass % or more and
2.0 mass % or less, conductivity can be adjusted to about 30-60%
IACS. The copper alloy material having such a conductivity is
particularly suitable as a casting mold material for
electromagnetic stirring applications.
[0018] In the copper alloy material of the present invention, the
composition of the copper alloy material may further include one or
more elements selected from Fe, Co, Sn, Zn, P, Si and Mg in a range
of 0.005 mass % or more and 0.1 mass % or less as a total.
[0019] In this case, since the composition of the copper alloy
material further includes one or more elements selected from Fe,
Co, Sn, Zn, P, Si and Mg in the above-described range, coarsening
of crystal grain sizes can be suppressed more reliably because of
the grain boundary pinning effect by a compound including these
elements.
Advantageous Effects of Invention
[0020] According to the present invention, it is possible to
provide a copper alloy material having stable characteristics and
excellent service life even when it is used in a high temperature
environment of 500.degree. C. or more.
BRIEF DESCRIPTION OF THE DRAWINGS
[0021] FIG. 1 is a flowchart of a method of manufacturing a copper
alloy material that is an embodiment of the present invention.
[0022] FIG. 2A is a structural observation photograph of Example 1
of the present invention.
[0023] FIG. 2B is a structural observation photograph of
Comparative Example 4.
[0024] FIG. 3A is a structure observation photograph of Example 1
of the present invention after performing the heat treatment at
1000.degree. C. for 1 hour retention time.
[0025] FIG. 3B is a structure observation photograph of Comparative
Example 4 after performing the heat treatment at 1000.degree. C.
for 1 hour retention time.
[0026] FIG. 4A is an observation photograph of crystallized Cr and
an SEM image in Example 1 of the present invention.
[0027] FIG. 4B is an EPMA (Cr) image in Example 1 of the present
invention.
[0028] FIG. 4C is an observation photograph of crystallized Cr and
an SEM image in Comparative Example 4.
[0029] FIG. 4D is an EPMA (Cr) image in Comparative Example 4.
DETAILED DESCRIPTION OF THE INVENTION
[0030] Hereinafter, a copper alloy material is an embodiment of the
present invention will be described.
[0031] The copper alloy material of the present embodiment is a
material for a part used in a high temperature environment such as
a molding material for casting and a welding part.
[0032] The copper alloy material according to the present
embodiment has a composition including: 0.3 mass % or more and less
than 0.5 mass % of Cr; 0.01 mass % or more and 0.15 mass % or less
of Zr; and a Cu balance including inevitable impurities. In the
copper alloy material of the present embodiment, Al may be
contained in the range of 0.1 mass % or more and 2.0 mass % or
less, if necessary. Further, one or more elements selected from Fe,
Co, Sn, Zn, P, Si and Mg may be contained in a total amount of
0.005 mass % or more and 0.1 mass % or less.
[0033] In the copper alloy material of the present embodiment, the
average of crystal grain sizes is in a range of 0.1 mm or more and
2.0 mm or less, and the standard deviation of the crystal grain
sizes is 0.6 or less.
[0034] In addition, in the copper alloy material of the present
embodiment, the area ratio of crystallized Cr in cross section
observation is 0.5% or less.
[0035] The area ratio of the crystallized Cr is determined by
observing the structure of an arbitrary cross section of the copper
alloy material (for example, a cross section parallel to the
rolling direction) with microscopic etching, observing the
structure with SEM or the like, and analyzing it.
[0036] Furthermore, in the copper alloy material of the present
embodiment, after performing a heat treatment at 1000.degree. C.
for 1 hour retention, the average of crystal grain sizes is in a
range of 0.1 mm or more and 3.0 mm or less, and the standard
deviation of the crystal grain sizes is 1.5 or less.
[0037] The reasons why the composition of the copper alloy material
according to the present embodiment, the crystal structure and the
like are defined as described above will be described below.
[0038] (Cr: 0.3 Mass % or More and Less than 0.5 Mass %)
[0039] Cr is an element having an action effect that improves
strength (hardness) and electrical conductivity by finely
precipitating Cr-based precipitates in crystal grains of the parent
phase by means of an aging treatment.
[0040] Here, in a case where the content of Cr is less than 0.3
mass %, the precipitation amount during the aging treatment becomes
insufficient, and there is a concern that the strength (hardness)
improvement effect cannot be sufficiently obtained. In addition, in
a case where the content of Cr is 0.5 mass % or more, a relatively
large amount of crystallized Cr exist even after the solution
treatment; local strain is accumulated due to these crystallized
Cr; and sizes of recrystallized grains becomes uneven. When it is
used under a high temperature environment, it is possible that the
crystal grains are coarsened.
[0041] On the basis of what has been described above, in the
present embodiment, the content of Cr is set in a range of 0.3 mass
% or more and less than 0.5 mass %. Meanwhile, in order to reliably
exhibit the above-described action effect, the lower limit of the
content of Cr is preferably set to 0.35 mass % or more, and the
upper limit of the content of Cr is preferably set to 0.45 mass %
or less.
[0042] (Zr: 0.01 Mass % or More and 0.15 Mass % or Less)
[0043] Zr is an element having an action effect that improves
strength (hardness) and electrical conductivity by finely
precipitating Zr-based precipitates in the crystal grain boundaries
of the parent phase by means of the aging treatment.
[0044] Here, in a case where the content of Zr is less than 0.01
mass %, the precipitation amount during the aging treatment becomes
insufficient, and there is a concern that the strength (hardness)
improvement effect cannot be sufficiently obtained. In addition, in
a case where the content of Zr exceeds 0.15 mass %, there is a
concern that electrical conductivity and thermal conductivity may
decrease. In addition, even when more than 0.15 mass % of Zr is
included, there is a concern that an additional strength
improvement effect cannot be obtained.
[0045] On the basis of what has been described above, in the
present embodiment, the content of Zr is set in a range of 0.01
mass % or more and 0.15 mass % or less. Meanwhile, in order to
reliably exhibit the above-described action effect, the lower limit
of the content of Zr is preferably set to 0.05 mass % or more, and
the upper limit of the content of Zr is preferably set to 0.13 mass
% or less.
[0046] Al: 0.1 mass % or more and less than 2.0 mass %
[0047] Al is an element having an action effect that decreases
electrical conductivity by forming a solid solution in copper
alloys. Therefore, it is possible to adjust the electrical
conductivity of the copper alloy material to approximately 30% to
60% IACS by controlling the amount of Al added.
[0048] Here, in a case where the content of Al is less than 0.1
mass %, it becomes difficult to suppress the electrical
conductivity at a low level. In addition, in a case where the
content of Al is 2.0 mass % or more, there is a concern that the
electrical conductivity may significantly decrease and the thermal
conductivity may become insufficient.
[0049] On the basis of what has been described above, in the
present embodiment, the content of Al is set in a range of 0.1 mass
% or more and less than 2.0 mass % in the case of adding Al.
Meanwhile, in order to reliably exhibit the above-described action
effect, the lower limit of the content of Al is preferably set to
0.3 mass % or more, and the upper limit of the content of Al is
preferably set to 1.5 mass % or less. In the case where Al is not
intentionally added, Al may be included in the inevitable
impurities at less than 0.1 mass %.
[0050] (One or More Elements Selected from Fe, Co, Sn, Zn, P, Si
and Mg: Total of 0.005 Mass % or More and 0.1 Mass % or Less)
[0051] Elements of Fe, Co, Sn, Zn, P, Si and Mg are elements that
form fine compounds and exhibit a pinning effect to suppress
crystal growth.
[0052] Here, in a case where the total content of one or more
elements selected from Fe, Co, Sn, Zn, P, Si and Mg is less than
0.005 mass %, there is a concern that the above-described pinning
effect cannot be exhibited sufficiently. On the other hand, in a
case where the total content of one or more elements selected from
Fe, Co, Sn, Zn, P, Si and Mg exceeds 0.1 mass %, there is a concern
that the electrical conductivity and the thermal conductivity may
decrease.
[0053] On the basis of what has been described above, in the
present embodiment, the total content of one or more elements
selected from Fe, Co, Sn, Zn, P, Si and Mg is set in a range of
0.005 mass % or more and 0.1 mass % or less. Meanwhile, in order to
reliably exhibit the above-described action effect, the lower limit
of the total content of one or more elements selected from Fe, Co,
Sn, Zn, P, Si and Mg P is preferably set to 0.02 mass % or more,
and the upper limit of the total content of one or more elements
selected from Fe, Co, Sn, Zn, P, Si and Mg is preferably set to
0.07 mass % or less. In addition, when elements such as Fe, Co, Sn,
Zn, P, Si and Mg are not intentionally added, these elements may be
contained as impurities in a total amount of less than 0.005 mass
%.
[0054] (Other Inevitable Impurities: 0.05 Mass % or Less)
[0055] Meanwhile, examples of the inevitable impurities other than
Cr, Zr, Al, Fe, Co, Sn, Zn, P, Si, and Mg described above include
B, Ag, Ca, Te, Mn, Ni, Sr, Ba, Sc, Y, Ti, Hf, V, Nb, Ta, Mo, W, Re,
Ru, Os, Se, Rh, Ir, Pd, Pt, Au, Cd, Ga, In, Li, Ge, As, Sb, Tl, Pb,
Be, N, H, Hg, Tc, Na, K, Rb, Cs, Po, Bi, lanthanoids, O, S, C and
the like. Since there is a concern that these inevitable impurities
may decrease the electrical conductivity and the thermal
conductivity, the total amount thereof is preferably set to 0.05
mass % or less.
[0056] (Average Crystal Grain Size: 0.1 mm or More and 2.0 mm or
Less/Standard Deviation of Grain Size: 0.6 or Less)
[0057] In the case of having a fine crystal structure with an
average crystal grain size of less than 0.1 mm, the driving force
in recrystallization increases and there is a possibility that high
strain is introduced locally. Therefore, when used under a high
temperature environment, the crystal grains may be coarsened. On
the other hand, when the average crystal grain size exceeds 2.0 mm,
workability becomes insufficient and it is difficult to use
industrially. Specifically, since the grain boundary strength
decreases, the tensile strength and elongation are lowered and the
crack propagation speed also increases, which makes it difficult to
use it industrially.
[0058] In addition, when the standard deviation of the crystal
grain size exceeds 0.6, the deviation of the crystal grain sizes
becomes large and strain is locally accumulated. Thus, when used
under a high temperature environment, the crystal grains become
coarse. In addition, the mechanical properties may be
deteriorated.
[0059] On the basis of what has been described above, in the
present embodiment, the average crystal grain size is set in the
range of 0.1 mm or more and 2.0 mm or less, and the standard
deviation of the crystal grain size is set to be 0.6 or less. The
lower limit of the average crystal grain size is preferably 0.15 mm
or more, and the upper limit of the average crystal grain size is
preferably 1.0 mm or less. In addition, it is preferable to set the
upper limit of the standard deviation of crystal grain size to 0.5
or less.
[0060] (Area Ratio of Cr Crystallized Material in Section
Observation: 0.5% or Less)
[0061] When the area ratio of the crystallized Cr exceeds 0.5%, the
strain is locally accumulated, so that the size of the
recrystallized grains is difficult to be uniform. Thus, when used
in a high temperature environment, there is a possibility that
crystal grains becomes coarse.
[0062] From the above, in the present embodiment, the area ratio of
the crystallized Cr in the cross sectional observation is set to be
0.5% or less. The upper limit of the area ratio of the crystallized
Cr is preferably 0.3% or less.
[0063] (Average Crystal Grain Size after Heat Treatment Maintained
at 1000.degree. C. for 1 Hour: 0.1 mm or More and 3.0 mm or
Less/Standard Deviation of Grain Size: 1.5 or Less)
[0064] By setting the average crystal grain size after the heat
treatment maintained at 1000.degree. C. for 1 hour within the above
range, coarsening of crystal grains when used in a high temperature
environment is reliably suppressed. In addition, by setting the
standard deviation after heat treatment held at 1000.degree. C. for
1 to 1.5 hours or less, occurrence of unevenly sized crystal grains
when used under a high temperature environment is reliably
suppressed.
[0065] From the above description, in the present embodiment, the
average crystal grain size after the heat treatment maintained at
1000.degree. C. for 1 hour is set in the range of 0.1 mm to 3.0 mm,
the standard deviation of the crystal grain size is 1.5 or less.
The lower limit of the average crystal grain size is preferably 0.2
mm or more, and the upper limit of the average crystal grain size
is preferably 0.5 mm or less. In addition, it is preferable to set
the upper limit of the standard deviation of crystal grain size to
1.3 or less.
[0066] Next, a method for manufacturing the casting mold material
according to the embodiment of the present invention will be
described with reference to a flowchart of FIG. 1.
[0067] (Melting and Casting Step S01)
[0068] First, a copper raw material made of oxygen-free copper
having a copper purity of 99.99 mass % or higher is loaded into a
carbon crucible and is melted using a vacuum melting furnace,
thereby obtaining molten copper. Next, the above-described additive
elements are added to the obtained molten metal so as to obtain a
predetermined concentration, and components are formulated, thereby
obtaining a molten copper alloy.
[0069] Here, as raw materials of Cr, and Zr which are the additive
elements, Cr, and Zr having a high purity are used, and, for
example, Cr having a purity of 99.99 mass % or higher is used as a
raw material of Cr, and Zr having a purity of 99.95 mass % or
higher is used as a raw material of Zr. In addition, Al, Fe, Co,
Sn, Zn, P, Si and Mg are added thereto as necessary. Meanwhile, as
raw materials of Al, Fe, Co, Sn, Zn, P, Si and Mg, parent alloys
with Cu may also be used.
[0070] In addition, the component-formulated molten copper alloy is
injected into a die, thereby obtaining an ingot.
[0071] (Homogenization Treatment Step S02)
[0072] Next, a thermal treatment is carried out in order for the
homogenization of the obtained ingot.
[0073] Specifically, a homogenization treatment is carried out on
the ingot in the atmosphere under conditions of 950.degree. C. or
higher and 1,050.degree. C. or lower for one hour or longer.
[0074] (Hot Working Step S03)
[0075] Next, hot rolling with a working percentage of 50% or higher
and 99% or lower is carried out on the ingot in a temperature range
of 900.degree. C. or higher and 1,000.degree. C. or lower, thereby
obtaining a rolled material. Meanwhile, the method of the hot
working may be hot forging. After this hot working, the rolled
material is immediately cooled by means of water cooling.
[0076] (Solution Treatment Step S04)
[0077] Next, a heating treatment is carried out on the rolled
material obtained in the hot working step S03 under conditions of
920.degree. C. or higher and 1,050.degree. C. or lower for 0.5
hours or longer and five hours or shorter, thereby carrying out a
solution treatment. The heating treatment is carried out, for
example, in the atmosphere or an inert gas atmosphere, and as
cooling after the heating, water cooling is carried out.
[0078] (Aging Treatment Step S05)
[0079] Next, after the solution treatment step S04, an aging
treatment is carried out, and precipitates such as Cr-based
precipitates and Zr-based precipitates are finely precipitated,
thereby obtaining a first aging treatment material.
[0080] Here, the first aging treatment is carried out under
conditions of, for example, 400.degree. C. or higher and
530.degree. C. or lower for 0.5 hours or longer and five hours or
shorter.
[0081] Meanwhile, the thermal treatment method during the aging
treatment is not particularly limited, but the thermal treatment is
preferably carried out in an inert gas atmosphere. In addition, the
cooling method after the heating treatment is not particularly
limited, but water cooling is preferably carried out.
[0082] By means of the above-described steps, the copper alloy
material that is the present embodiment is manufactured.
[0083] According to the copper alloy material of the present
invention provided with the above-described constitution, since the
casting mold material is provided with a composition including 0.3
mass % or more and less than 0.5 mass % of Cr, 0.01 mass % or more
and 0.15 mass % or less of Zr, and a Cu balance including
inevitable impurities, fine precipitates can be precipitated by
performing the solution and aging treatments. Thus, strength and
electrical conductivity can be improved.
[0084] In addition, since the Cr content is set to a relatively low
content of 0.3 mass % or more and less than 0.5 mass %,
crystallized Cr hardly exists after the solution treatment.
Specifically, the area ratio of crystallized Cr in cross section
observation is 0.5% or less. Therefore, occurrence of unevenly
sized recrystallized grains by accumulation of local strain due to
the crystallized Cr can be suppressed. Accordingly, local
coarsening of crystal grains can be reliably suppressed even when
it is used under a high temperature environment.
[0085] In the present embodiment, the average crystal grain size is
set in the range of 0.1 mm or more and 2.0 mm or less, and the
standard deviation of the crystal grain size is set to 0.6 or less,
so that there is less accumulation of local strain. Accordingly,
local coarsening of crystal grains can be reliably suppressed even
when it is used under a high temperature environment.
[0086] Furthermore, the average crystal grain size after the heat
treatment maintained at 1000.degree. C. for 1 hour is set in the
range of 0.1 mm or more and 3.0 mm or less, and the standard
deviation of the crystal grain size is set to 1.5 or less. Thus,
even after heat treatment at 1000.degree. C. for 1 hour retention,
crystal grains are not coarsened locally and even when used under a
high temperature environment of 500.degree. C. or more, mechanical
properties and conductivity are stable.
[0087] Further, in this embodiment, when Al is contained in the
range of 0.1 mass % or more and 2.0 mass % or less, the
conductivity can be adjusted to about 30 to 60% IACS.
[0088] As a result, it is possible to obtain a copper alloy
material particularly suitable as a casting mold material for
electromagnetic stirring applications.
[0089] In addition, in the present embodiment, when the copper
alloy material further includes one or more elements selected from
Fe, Co, Sn, Zn, P, Si and Mg in a range of 0.005 mass % or more and
0.1 mass % or less as a total, coarsening of crystal grains can be
more reliably suppressed by the pinning effect of a compound
containing these elements.
[0090] Hitherto, the embodiment of the present invention has been
described, but the present invention is not limited thereto and can
be appropriately modified in the scope of the technical concept of
the invention.
Examples
[0091] Hereinafter, the results of confirmation tests carried out
in order to confirm the effects of the present invention will be
described.
[0092] A copper raw material made of oxygen-free copper having a
copper purity of 99.99 mass % or higher was prepared, was loaded
into a carbon crucible, and was melted using a vacuum melting
furnace (with a degree of vacuum of 10.sup.-2 Pa or lower), thereby
obtaining molten copper. A variety of additive elements were added
to the obtained molten copper so as to formulate a component
composition shown in Table 1, the component composition was
maintained for five minutes, and then the molten copper alloy was
injected into a cast iron die, thereby obtaining an ingot. The
sizes of the ingot were set to a width of approximately 80 mm, a
thickness of approximately 50 mm, and a length of approximately 130
mm.
[0093] Meanwhile, as a raw material of Cr which was an additive
element, Cr having a purity of 99.99 mass % or higher was used, and
as a raw material of Zr, Zr having a purity of 99.95 mass % or
higher was used.
[0094] Next, a homogenization treatment was carried out in the
atmosphere under conditions of 1,000.degree. C. for one hour, and
then hot rolling was carried out. The rolling reduction in the hot
rolling was set to 80%, thereby obtaining a hot-rolled material
having a width of approximately 100 mm, a thickness of
approximately 10 mm, and a length of approximately 520 mm.
[0095] A solution treatment was carried out on this hot-rolled
material under conditions of 1,000.degree. C. for 1.5 hours, and
then cooled at the cooling rates shown in Table 2.
[0096] Next, a aging treatment was carried out under conditions of
500 (.+-.15).degree. C. for three hours. By following
above-described procedures, the copper alloy materials were
obtained.
[0097] For the obtained copper alloy material, the structure of the
copper alloy material after the aging treatment was observed, and
the standard deviation of the average crystal grain size and
crystal grain size was measured.
[0098] In addition, the average crystal grain size and the standard
deviation of the crystal grain diameter after the heat treatment
for 1 hour at 1000.degree. C. retention were measured for this
copper alloy material.
[0099] Further, cross-section observation was performed on the
material after the solution treatment, and the area ratio of
crystallized Cr was measured.
[0100] FIGS. 2A and 2B show the structure observation pictures of
the copper alloy materials of Example 1 of the present invention
and Comparative Example 4, respectively, after the above-described
aging treatment and before the heat treatment at 1000.degree. C.
for 1 hour retention.
[0101] Similarly, FIG. 3A and FIG. 3B show the structure
observation pictures of the copper alloy materials of Example 1 of
the present invention and Comparative Example 4, respectively,
after the above-described aging treatment and the heat treatment at
1000.degree. C. for 1 hour retention.
[0102] (Composition Analysis)
[0103] The component composition of the obtained copper alloy
material was measured by ICP-MS analysis. The measurement results
are shown in Table 1.
[0104] (Average Crystal Grain Size and Standard Deviation of Grain
Size)
[0105] A sample of 10 mm.times.15 mm from the central portion of
the plate width was cut out from the obtained thickness of the
copper alloy material and the surface in the rolling direction (RD
direction) was polished and then micro etching was performed.
[0106] This sample was observed and the average crystal grain size
was measured by the intercept method prescribed in JIS H 0501.
[0107] (Area Ratio of Cr Crystallization)
[0108] A sample of 10 mm.times.15 mm from the central portion of
the plate width was cut out from the thickness of the copper alloy
material and the surface in the rolling direction (RD direction)
was polished and then micro etching was performed.
[0109] This sample was observed by SEM, and in a SEM-EPMA image of
1500 times magnification (field of view of approximately 70
.mu.m.times.70 .mu.m), a region where the Cr concentration was
higher than that of the parent phase was judged to be "crystallized
Cr", and ratios of crystallized Cr were determined by the following
formula.
Area ratio=(area occupied by crystallized Cr)/(70 .mu.m.times.70
.mu.m)
[0110] FIGS. 4A to 4D show SEM-EPMA images of Example 1 of the
present invention and Comparative Example 4.
[0111] (Tensile Strength)
[0112] JIS Z 2241 No. 2 test piece was taken with the rolling
direction as the pulling direction and subjected to the test using
a 100 kN tensile tester.
TABLE-US-00001 TABLE 1 Composition (mass %) Cr Zr Al Fe Co Sn Zn P
Si Mg Cu Examples of 1 0.35 0.14 -- -- -- -- -- -- -- -- balance
the present 2 0.35 0.14 0.02 -- -- 0.02 0.02 -- -- -- balance
invention 3 0.39 0.14 0.93 -- -- -- -- -- -- -- balance 4 0.45 0.08
-- 0.01 -- -- -- 0.01 -- -- balance 5 0.45 0.07 -- -- -- -- -- --
0.02 0.01 balance 6 0.50 0.02 1.90 -- 0.07 -- -- 0.02 -- -- balance
Comparative 1 0.20 0.10 -- -- -- -- -- -- -- -- balance Examples 2
0.70 0.14 -- -- -- -- -- -- -- -- balance 3 0.70 0.02 -- -- -- --
-- -- 0.01 -- balance 4 0.90 0.08 -- -- -- -- -- -- -- 0.20
balance
TABLE-US-00002 TABLE 2 After heat treatment at Area ratio After
aging treatment 1000.degree. C. for 1 hour of Cooling Average
Average crystallized rate after crystal crystal Cr after solution
grain Tensile grain Tensile solution treatment size Standard
strength size Standard strength treatment (.degree. C./min) (mm)
deviation (MPa) (mm) deviation (MPa) (%) Examples of 1 1000 0.144
0.58 433 0.243 1.21 413 0.3 the present 2 1000 0.162 0.55 430 0.451
1.25 407 0.3 invention 3 1000 0.169 0.56 423 0.331 1.34 420 0.3 4
1000 0.110 0.49 417 0.207 1.29 419 0.5 5 1000 0.161 0.52 433 0.303
1.30 401 0.4 6 27 0.142 0.55 427 0.213 1.45 389 0.5 Comparative 1 9
0.120 0.62 383 0.270 1.53 357 0.7 Examples 2 1000 0.078 0.70 432
0.292 1.56 339 1.8 3 1000 0.081 0.65 422 0.346 1.52 331 1.8 4 1000
0.096 0.68 434 0.261 1.63 353 2.0
[0113] FIGS. 2A and 3A, in Examples 1 to 6 of the present
invention, local grain coarsening was suppressed even after being
placed in a high-temperature environment.
[0114] On the other hand, as shown in FIGS. 2B and 3B, in
Comparative Examples 1 to 4, the crystal grains coarsened locally
after being placed in a high-temperature environment.
[0115] In Comparative Example 1 in which the Cr content was less
than the range of the scope of the present invention and the
standard deviation of the crystal grain size was more than the
range of the scope of the present invention, the tensile strength
after the aging heat treatment and after the heat treatment at
1000.degree. C. for 1 hour was insufficient.
[0116] In Comparative Example 2-4 in which the content of Cr was
more than the range of the scope of the present invention and the
average crystal grain size was less than the scope of the present
invention and the standard deviation of crystal grain size was more
than the range of the scope of the present invention, the tensile
strength greatly decreased after the heat treatment at 1000.degree.
C. for 1 hour.
[0117] In contrast, in Examples 1-6 of the present invention, the
tensile strength after aging heat treatment was high and the
tensile strength did not decrease greatly after the heat treatment
at 1000.degree. C. for 1 hour.
[0118] From the above-described results, according to the example
of the present invention, it is confirmed that a copper alloy
material having stable properties and excellent service life even
when it is used under a high temperature environment of 500.degree.
C. or more was provided.
INDUSTRIAL APPLICABILITY
[0119] It is possible to suppress property deterioration of a part
made of the Cu--Cr--Zr-based alloy in a high temperature
environment and prolong the service life of the casting molding
material, the welding part and the like.
* * * * *