U.S. patent application number 15/167392 was filed with the patent office on 2019-02-21 for perovskite based charge transport layers for thin film optoelecronic devices and methods of making.
The applicant listed for this patent is The Florida State University Research Foundation, Inc.. Invention is credited to Biwu Ma, Yu Tian.
Application Number | 20190058135 15/167392 |
Document ID | / |
Family ID | 59021605 |
Filed Date | 2019-02-21 |
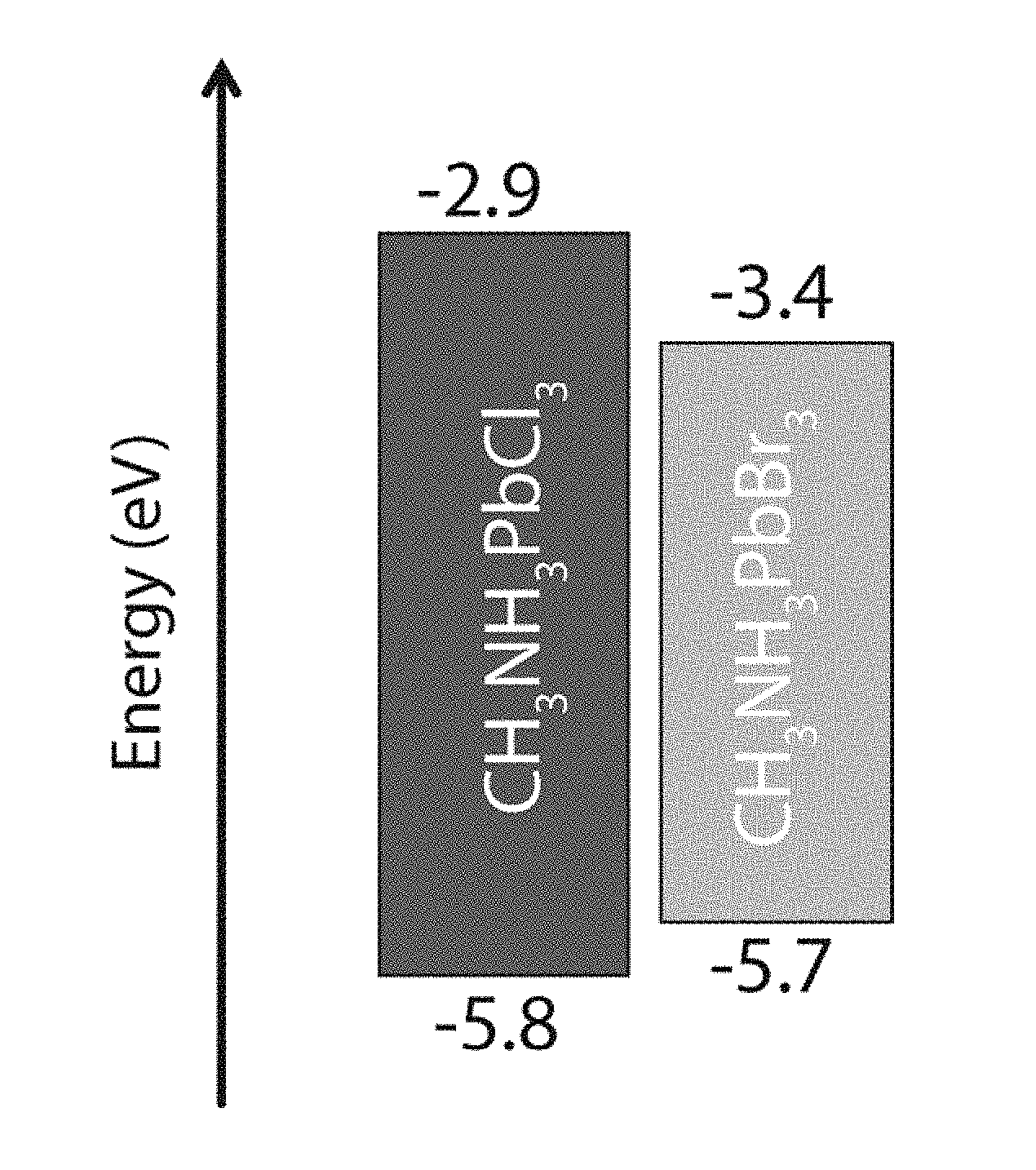
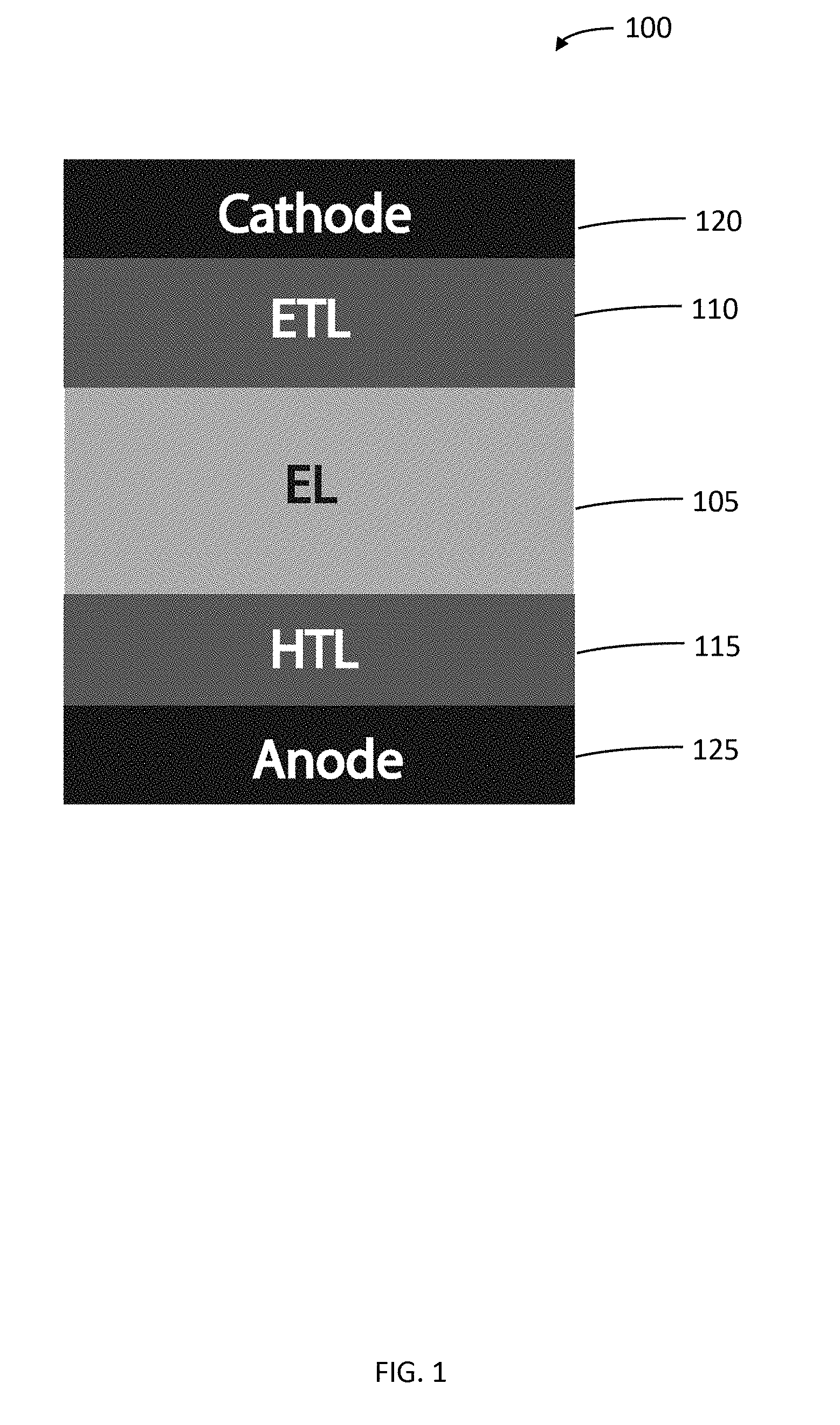
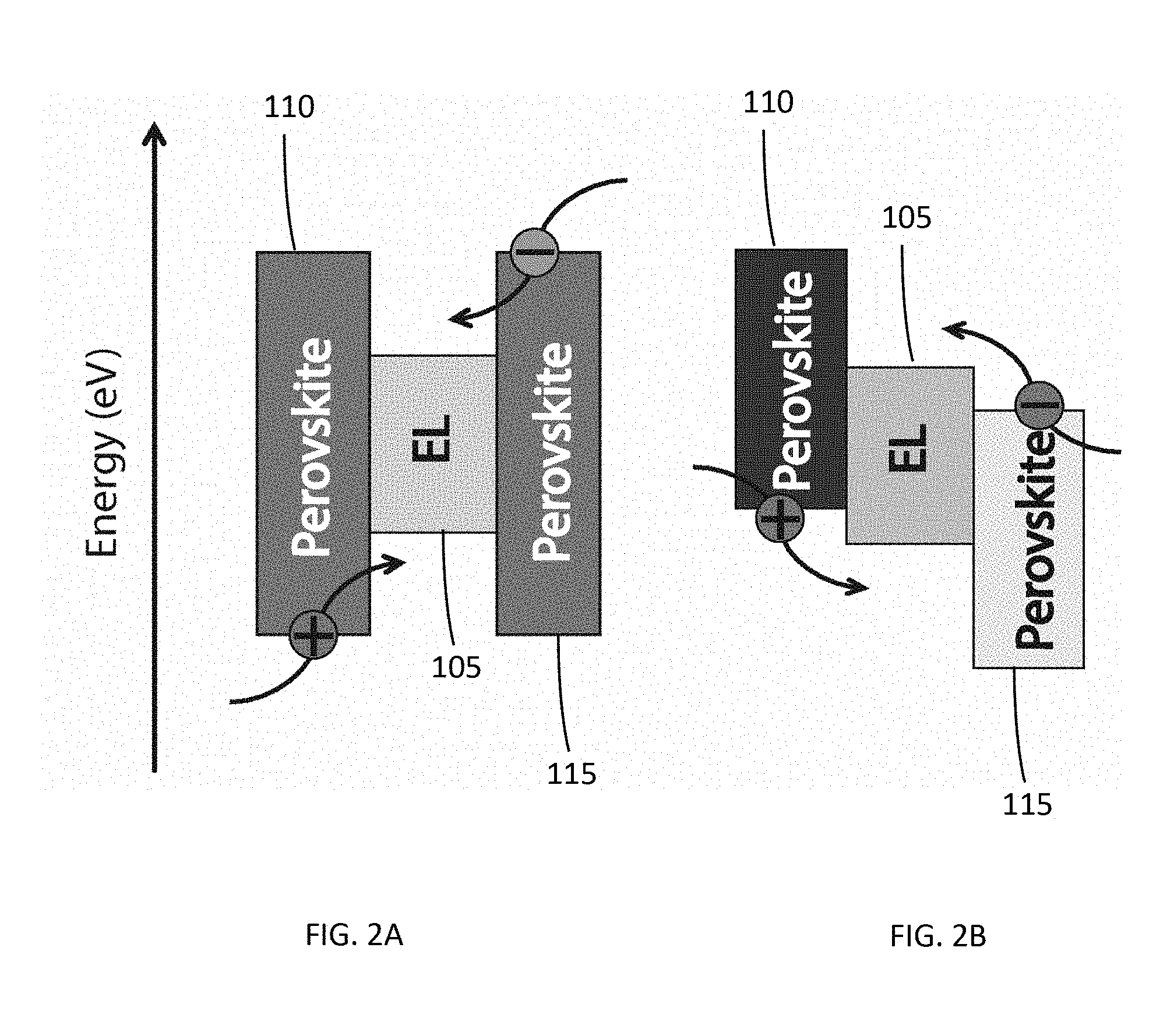


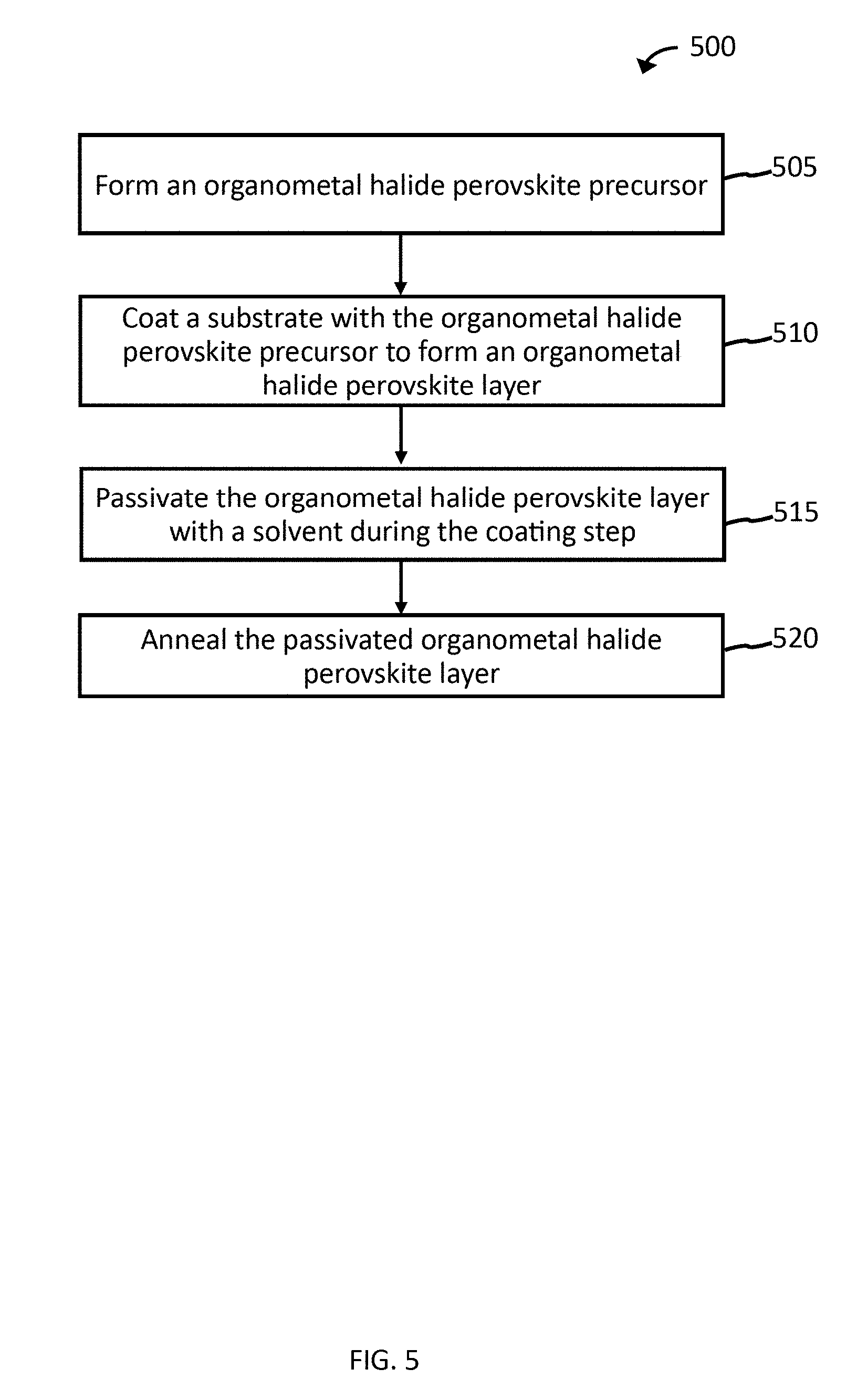

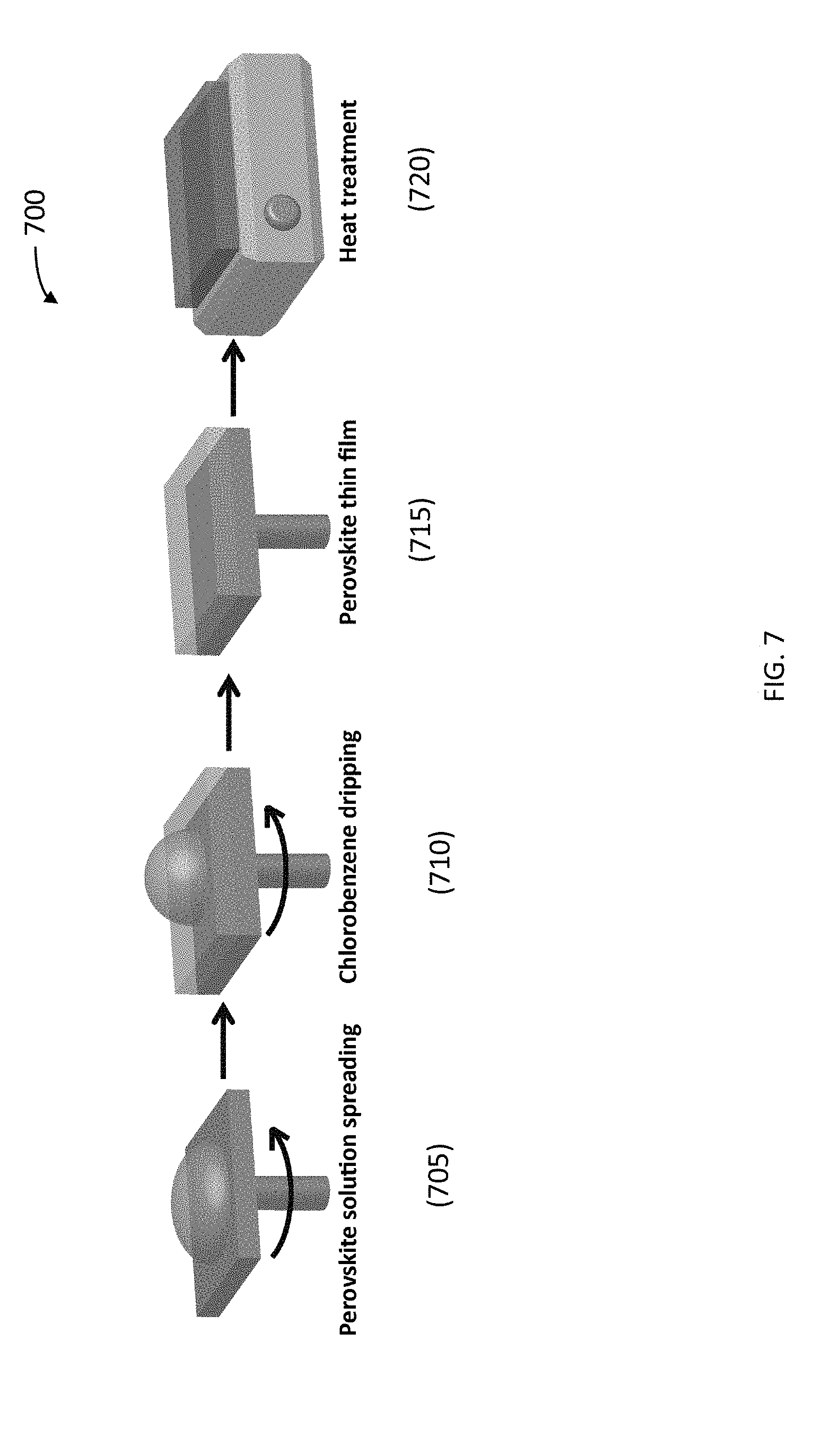
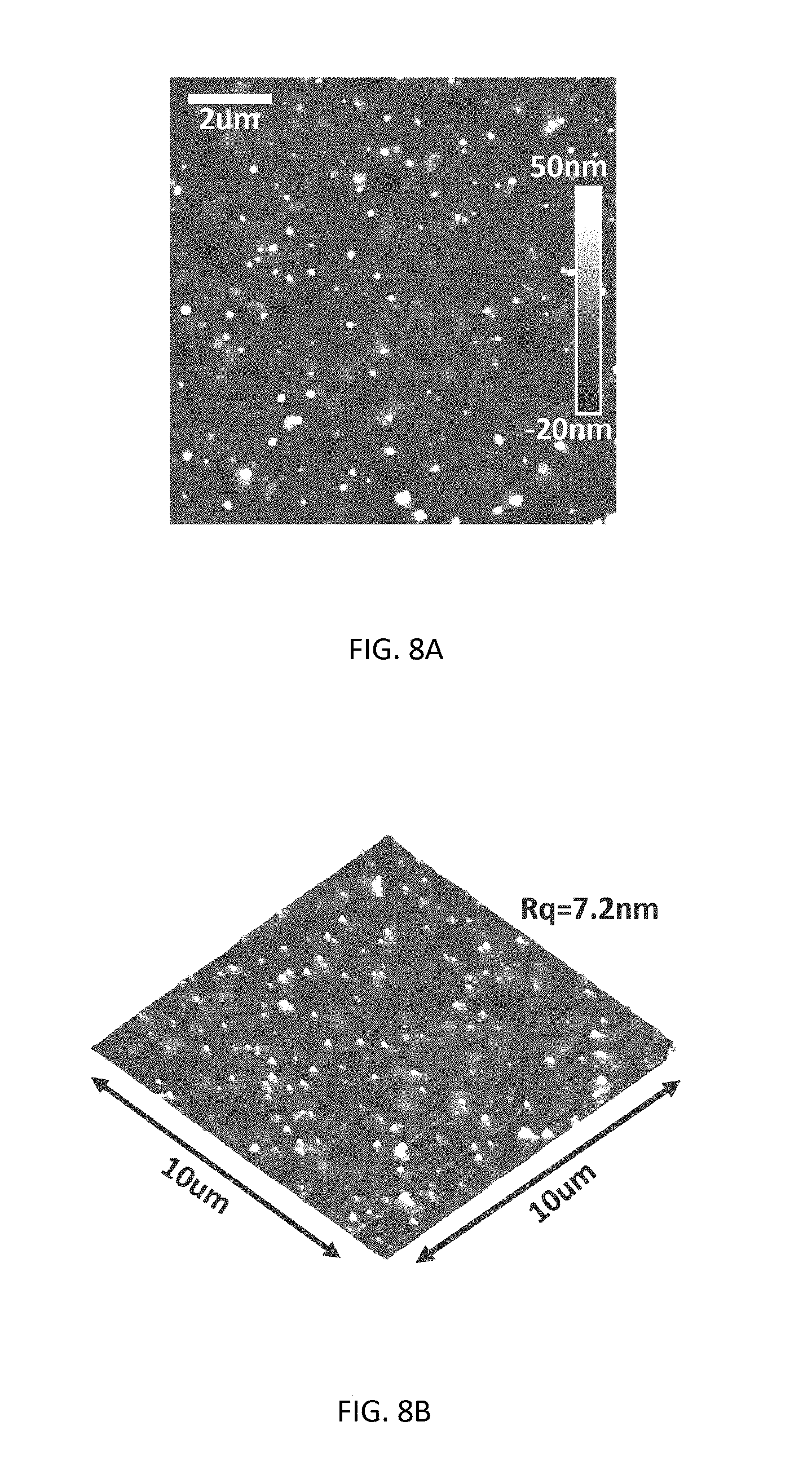
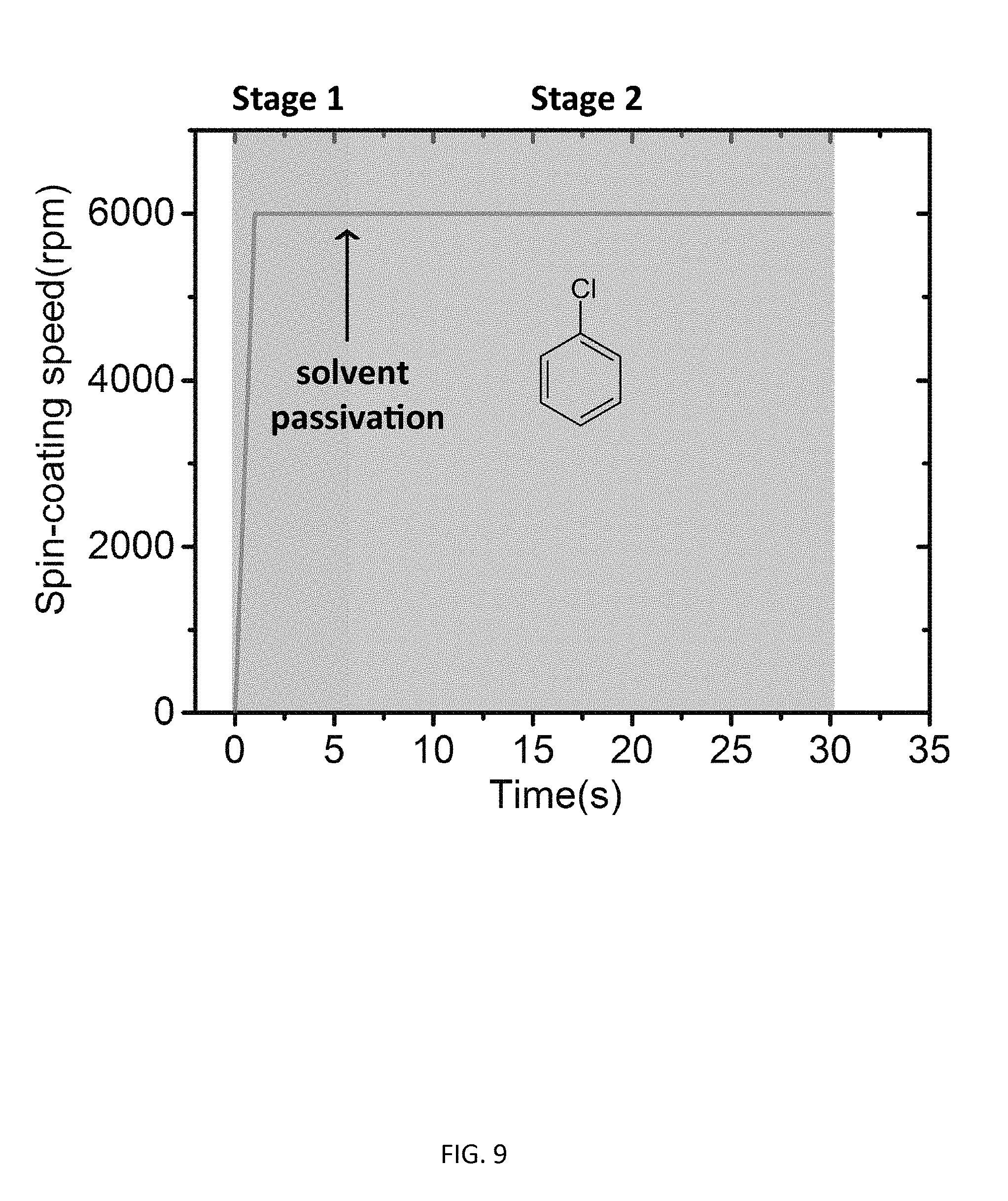
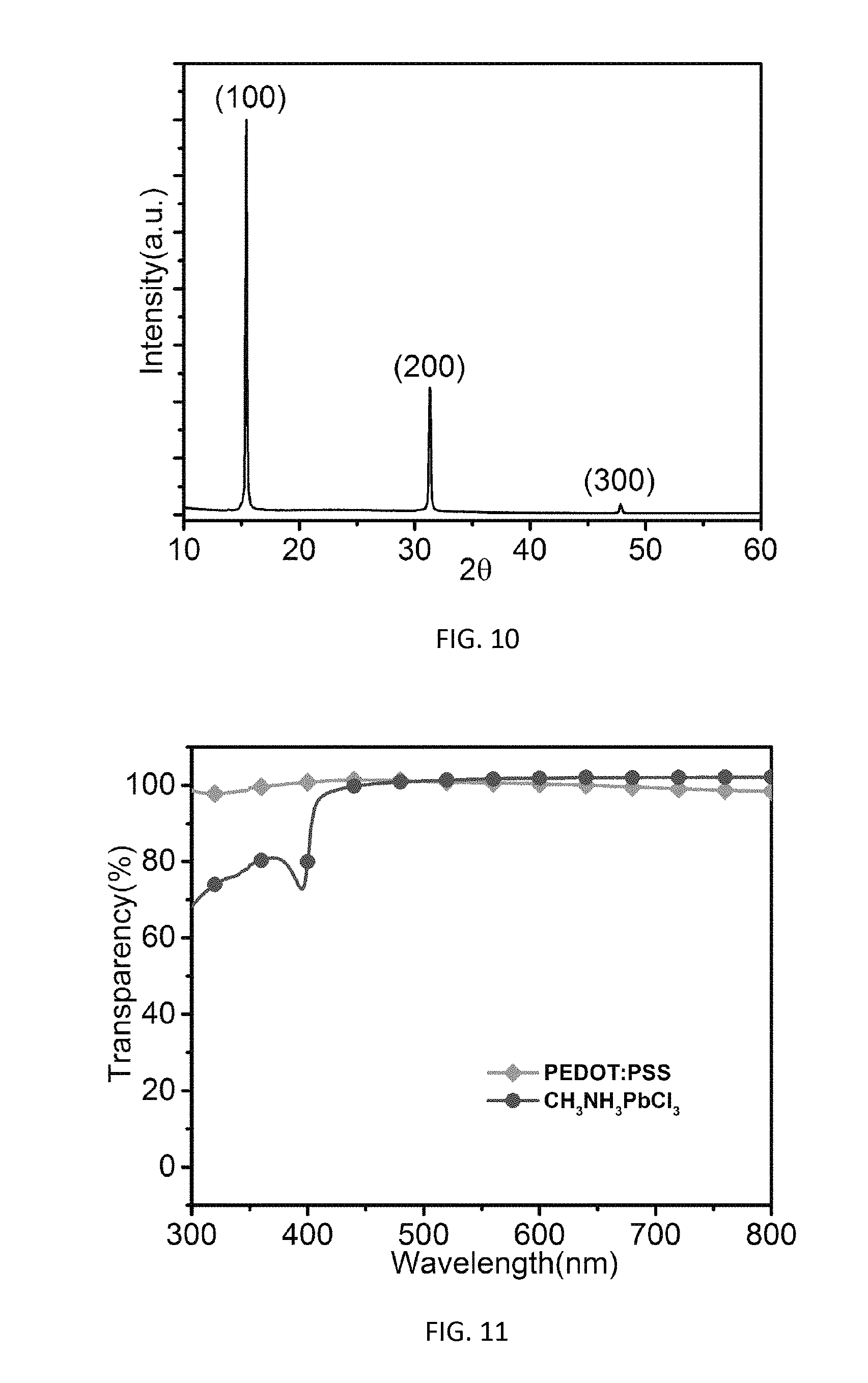
View All Diagrams
United States Patent
Application |
20190058135 |
Kind Code |
A1 |
Ma; Biwu ; et al. |
February 21, 2019 |
PEROVSKITE BASED CHARGE TRANSPORT LAYERS FOR THIN FILM
OPTOELECRONIC DEVICES AND METHODS OF MAKING
Abstract
A new type of charge transport layer based on organometal halide
perovskite for highly efficient organic light emitting diodes
(OLEDs) is demonstrated. By solution processing of halide
perovskite precursors, smooth essentially pure perovskite thin
films may be prepared with high transparency and conductivity.
Solution processed multilayer OLED with this perovskite-based hole
transport layer outperforms a device with a PEDOT:PSS layer.
Inventors: |
Ma; Biwu; (Tallahassee,
FL) ; Tian; Yu; (Tallahassee, FL) |
|
Applicant: |
Name |
City |
State |
Country |
Type |
The Florida State University Research Foundation, Inc. |
Tallahassee |
FL |
US |
|
|
Family ID: |
59021605 |
Appl. No.: |
15/167392 |
Filed: |
May 27, 2016 |
Current U.S.
Class: |
1/1 |
Current CPC
Class: |
H01L 51/56 20130101;
H01L 51/0037 20130101; H01L 51/5012 20130101; H01L 51/005 20130101;
Y02E 10/549 20130101; H01L 51/0028 20130101; H01L 51/0042 20130101;
H01L 51/0003 20130101; H01L 51/4213 20130101; H01L 51/0085
20130101; H01L 51/5016 20130101; H01L 51/5072 20130101; H01L
51/5056 20130101 |
International
Class: |
H01L 51/00 20060101
H01L051/00; H01L 51/50 20060101 H01L051/50; H01L 51/42 20060101
H01L051/42; H01L 51/56 20060101 H01L051/56 |
Claims
1. A method for forming a charge transport layer of a thin film
optoelectronic device, comprising: forming an organometal halide
perovskite precursor; coating a substrate with the organometal
halide perovskite precursor to form an organometal halide
perovskite layer; passivating the organometal halide perovskite
layer with a solvent during the coating step; and annealing the
passivated organometal halide perovskite layer.
2. The method of claim 1, wherein the organometal halide perovskite
precursor comprises a mixture of AX and BX.sub.2, where A is a
cation, B is a metal, and X is a halide ion.
3. The method of claim 2, wherein A comprises methylammonium
(CH.sub.3NH.sub.3), formamidinium (NH.sub.2CHNH.sub.2), cesium
(Cs), or mixtures thereof.
4. The method of claim 2, wherein B comprises lead (Pb), tin (Sn),
germanium (Ge), or mixtures thereof.
5. The method of claim 2, wherein X comprises fluoride (F.sup.-),
chloride (Cl.sup.-), bromide (Br.sup.-), iodide (I.sup.-), astatide
(At.sup.-), or mixtures thereof.
6. The method of claim 2, wherein forming the organometal halide
perovskite precursor comprises mixing AX and BX.sub.2 in a solvent
mixture of approximately 7 parts by volume dimethylformamide and
approximately 3 parts by volume dimethylsulfoxide.
7. The method of claim 6, wherein the resulting solvent mixture
comprises approximately 0.64M AX and approximately 0.4 M
BX.sub.2.
8. The method of claim 1, wherein the organometal halide perovskite
layer comprises methylammonium lead chloride
(CH.sub.3NH.sub.3PbCl.sub.3), formamidinium lead chloride
(NH.sub.2CHNH.sub.2PbCl.sub.3), cesium lead chloride
(CsPbCl.sub.3), or mixtures thereof.
9. The method of claim 1, wherein coating the substrate comprises
spin coating the organometal halide perovskite precursor onto the
substrate.
10. The method of claim 9, wherein a duration of the spin coating
step comprises approximately 30 seconds, and the passivating
solvent is added after approximately 6 seconds.
11. The method of claim 1, wherein passivating the organometal
halide perovskite layer comprises adding a low polarity organic
solvent during the coating step.
12. The method of claim 11, wherein the low polarity organic
solvent comprises chloroform, chlorobenzene, toluene, or mixtures
thereof.
13. The method of claim 1, wherein annealing the passivated
organometal halide perovskite layer comprises heating to
approximately 100.degree. C. for 10 minutes.
14. A method for forming a charge transport layer of a thin film
optoelectronic device, comprising: forming an organometal halide
perovskite precursor by dissolving methylammonium chloride
(CH.sub.3NH.sub.3Cl) and lead chloride (PbCl.sub.2) in a mixture of
dimethylformamide and dimethylsulfoxide; coating a substrate with
the organometal halide perovskite precursor to form a layer of
methylammonium lead chloride (CH.sub.3NH.sub.3PbCl.sub.3) on the
substrate; passivating the methylammonium lead chloride layer by
adding a low polarity organic solvent during the coating step; and
annealing the passivated methylammonium lead chloride layer.
15. The method of claim 14, wherein the organometal halide
perovskite precursor comprises approximately 0.64 M methylammonium
chloride and approximately 0.4 M lead chloride.
16. The method of claim 14, wherein the low polarity organic
solvent comprises chloroform, chlorobenzene, toluene, or mixtures
thereof.
17. An optoelectronic device, comprising: a first charge transport
layer; a photoactive layer; and a second charge transport layer;
wherein one or both of the first and second charge transport layers
comprise methylammonium lead chloride (CH.sub.3NH.sub.3PbCl.sub.3)
deposited from a mixture of methylammonium chloride
(CH.sub.3NH.sub.3Cl) and lead chloride (PbCl.sub.2) in a solution
of dimethylformamide and dimethylsulfoxide, passivated with a low
polarity organic solvent, and thermally annealed.
18. The device of claim 17, wherein the mixture comprises
approximately 0.64M methylammonium chloride and approximately 0.4 M
lead chloride.
19. The device of claim 17, wherein the photoactive layer comprises
a light emitting layer.
20. The device of claim 17, wherein the photoactive layer comprises
a light harvesting layer.
Description
BACKGROUND OF THE INVENTION
1. Field of the Invention
[0001] This invention relates, generally, to thin film
optoelectronic devices. More specifically, it relates to charge
transport layers based on halide perovskite materials.
2. Brief Description of the Prior Art
[0002] Thin film optoelectronic devices have experienced tremendous
development over the last decades. Light emitting diodes (LEDs)
based on organics, polymers, and quantum dots have achieved high
efficiencies and long lifetimes suitable for applications in full
color displays and solid-state lighting. Organic/polymeric
photovoltaic cells (PVs) have been established as a highly
promising low-cost solar energy conversion technology with power
conversion efficiencies improved from about 1% to more than 10%.
All these thin film optoelectronic devices are configured in a
typical layered structure, with the photoactive (either light
emitting or light harvesting) layer sandwiched between charge
transport layers in contact with two electrodes. The charge
transport layers, i.e. hole transport layer (HTL) and electron
transport layer (ETL), play critical roles in determining the
device performance.
[0003] To overcome complicated synthesis and purification, low
stability and conductivity, and high cost associated with known
solution processed charge transport layers based on organic
molecules, polymers, and metal oxides, it is desirable to start
with abundant common materials and use a process in which thin
films can be prepared by high throughput solution processing with
high conductivity to significantly improve device performance.
However, no such processes have yet been satisfactorily
demonstrated.
[0004] Accordingly, what is needed is a solution based process to
produce charge transport layers using common materials, resulting
in high conductivity thin films. However, in view of the art
considered as a whole at the time the present invention was made,
it was not obvious to those of ordinary skill in the field of this
invention how the shortcomings of the prior art could be
overcome.
[0005] All referenced publications are incorporated herein by
reference in their entirety. Furthermore, where a definition or use
of a term in a reference, which is incorporated by reference
herein, is inconsistent or contrary to the definition of that term
provided herein, the definition of that term provided herein
applies and the definition of that term in the reference does not
apply.
[0006] While certain aspects of conventional technologies have been
discussed to facilitate disclosure of various embodiments,
applicants in no way disclaim these technical aspects, and it is
contemplated that the present disclosure may encompass one or more
of the conventional technical aspects discussed herein.
[0007] The present disclosure may address one or more of the
problems and deficiencies of the prior art discussed above.
However, it is contemplated that various embodiments may prove
useful in addressing other problems and deficiencies in a number of
technical areas. Therefore, the present disclosure should not
necessarily be construed as limited to addressing any of the
particular problems or deficiencies discussed herein.
[0008] In this specification, where a document, act or item of
knowledge is referred to or discussed, this reference or discussion
is not an admission that the document, act or item of knowledge or
any combination thereof was at the priority date, publicly
available, known to the public, part of common general knowledge,
or otherwise constitutes prior art under the applicable statutory
provisions; or is known to be relevant to an attempt to solve any
problem with which this specification is concerned.
BRIEF SUMMARY OF THE INVENTION
[0009] Various embodiments may comprise a method for forming a
charge transport layer of a thin film optoelectronic device. An
organometal halide perovskite precursor may be formed. A substrate
may be coated with the organometal halide perovskite precursor to
form an organometal halide perovskite layer. The organometal halide
perovskite layer may be passivated with a solvent during the
coating step, and the passivated organometal halide perovskite
layer may be annealed.
[0010] Additional embodiments may comprise a method for forming a
charge transport layer of a thin film optoelectronic device. An
organometal halide perovskite precursor may be formed by dissolving
methylammonium chloride (CH.sub.3NH.sub.3Cl) and lead chloride
(PbCl.sub.2) in a mixture of dimethylformamide and
dimethylsulfoxide. A substrate may be coated with the organometal
halide perovskite precursor to form a layer of methylammonium lead
chloride (CH.sub.3NH.sub.3PbCl.sub.3) on the substrate. The
methylammonium lead chloride layer may be passivated by adding a
low polarity organic solvent during the coating step, and the
passivated methylammonium lead chloride layer may be annealed.
[0011] Still further embodiments may comprise an optoelectronic
device. The optoelectronic device may comprise a first charge
transport layer, a photoactive layer, and a second charge transport
layer. One or both of the first and second charge transport layers
may comprise methylammonium lead chloride
(CH.sub.3NH.sub.3PbCl.sub.3) deposited from a mixture of
methylammonium chloride (CH.sub.3NH.sub.3Cl) and lead chloride
(PbCl.sub.2) in a solution of dimethylformamide and
dimethylsulfoxide, passivated with a low polarity organic solvent,
and thermally annealed.
[0012] The long-standing but heretofore unfulfilled need for a
solution based process to produce charge transport layers using
common materials, resulting in highly conductive thin films is now
met by a new, useful, and nonobvious invention.
[0013] These and other important objects, advantages, and features
of the invention will become clear as this disclosure proceeds.
[0014] The invention accordingly comprises the features of
construction, combination of elements, and arrangement of parts
that will be exemplified in the disclosure set forth hereinafter
and the scope of the invention will be indicated in the claims.
BRIEF DESCRIPTION OF THE DRAWINGS
[0015] For a fuller understanding of the invention, reference
should be made to the following detailed description, taken in
connection with the accompanying drawings, in which:
[0016] FIG. 1 is a schematic diagram of a typical multilayer thin
film LED device structure.
[0017] FIG. 2A is a schematic diagram of a portion of thin film LED
device structure with perovskite ETL and HTL layers.
[0018] FIG. 2B is a schematic diagram of a portion of thin film LED
device structure with perovskite ETL and HTL layers.
[0019] FIG. 3 illustrates the band position for two metal halide
perovskite materials.
[0020] FIG. 4A is a top view of an atomic force microscopy image of
CH.sub.3NH.sub.3PbCl.sub.3 thin film prepared by simple spin
casting without solvent passivation, which consists of large
crystals with poor surface coverage and high surface roughness.
[0021] FIG. 4B is 3-D view of the image of FIG. 4A.
[0022] FIG. 5 is a flowchart of an exemplary method for forming a
charge transport layer of a thin film optoelectronic device.
[0023] FIG. 6 is a flowchart of an exemplary method for forming a
charge transport layer of a thin film optoelectronic device.
[0024] FIG. 7 is a schematic diagram of process for producing
CH.sub.3NH.sub.3PbCl.sub.3 thin films by spin coating combined with
solvent passivation and thermal annealing.
[0025] FIG. 8A is a top view of an atomic force microscopy image of
CH.sub.3NH.sub.3PbCl.sub.3 thin film on a glass substrate.
[0026] FIG. 8B is a 3-D view of the image of FIG. 8A.
[0027] FIG. 9 is a graph illustrating spin coating and
chlorobenzene dripping conditions os a solvent passivation
method.
[0028] FIG. 10 is an XRD graph of CH.sub.3NH.sub.3PbCl.sub.3 thin
film of 25 nm on a glass substrate.
[0029] FIG. 11 is a graph of transmittance spectra of
CH.sub.3NH.sub.3PbCl.sub.3 thin film of 25 nm and PEDOT:PSS of 40
nm.
[0030] FIG. 12 is a schematic device structure of an OLED with
CH.sub.3NH.sub.3PbCl.sub.3 thin film HTL.
[0031] FIG. 13 illustrates chemical structures of organic materials
used in OLED devices.
[0032] FIG. 14 is an energy level diagram for component
materials.
[0033] FIG. 15 is a graph of electroluminescence spectrum.
[0034] FIG. 16 is a graph of current density versus voltage, and
brightness versus voltage for green phosphorescent OLEDs with
different HTLs.
[0035] FIG. 17 is a graph of EQE versus current density for green
phosphorescent OLEDs with different HTLs.
[0036] FIG. 18 is a graph of power efficiency versus luminescence
for green phosphorescent OLEDs with different HTLs.
[0037] FIG. 19 is a graph of luminous efficiency versus
luminescence for green phosphorescent OLEDs with different
HTLs.
[0038] FIG. 20 is a graph of impedance spectroscopy Cole-Cole plots
of CH.sub.3NH.sub.3PbCl.sub.3 based OLED.
[0039] FIG. 21 is a graph of impedance spectroscopy Cole-Cole plots
of PEDOT:PSS based OLED.
[0040] FIG. 22 is a graph of current density versus voltage, and
brightness versus voltage for green phosphorescent OLEDs with 20 nm
and 15 nm thickness CH.sub.3NH.sub.3PbCl.sub.3.
[0041] FIG. 23 is a graph of EQE versus current density for green
phosphorescent OLEDs with 20 nm and 15 nm thickness
CH.sub.3NH.sub.3PbCl.sub.3.
[0042] FIG. 24 is a graph of power efficiency versus luminescence
for green phosphorescent OLEDs with 20 nm and 15 nm thickness
CH.sub.3NH.sub.3PbCl.sub.3.
[0043] FIG. 25 is a graph of luminous efficiency versus
luminescence for green phosphorescent OLEDs with 20 nm and 15 nm
thickness CH.sub.3NH.sub.3PbCl.sub.3.
[0044] FIG. 26A is a top view of an atomic force microscopy image
of CH.sub.3NH.sub.3PbCl.sub.3 thin films at 20 nm.
[0045] FIG. 26B is a 3-D view of the image of FIG. 26A.
[0046] FIG. 27A is a top view of an atomic force microscopy image
of CH.sub.3NH.sub.3PbCl.sub.3 thin films at 15 nm.
[0047] FIG. 27B is a 3-D view of the image of FIG. 27A.
DETAILED DESCRIPTION OF THE PREFERRED EMBODIMENT
[0048] In the following detailed description of the preferred
embodiments, reference is made to the accompanying drawings, which
form a part thereof, and within which are shown by way of
illustration specific embodiments by which the present disclosure
may be practiced. It is to be understood that other embodiments may
be utilized and structural changes may be made without departing
from the scope of the invention.
[0049] Typical thin film optoelectronic devices, such as
light-emitting diodes (LEDs) and photovoltaic cells (PVs), may be
configured with a layered structure, with a photoactive (either
light emitting or light harvesting) layer sandwiched between charge
transport layers that contact two electrodes. The charge transport
layers, including hole transporting layer (HTL) and electron
transporting layer (ETL), may play a critical role in determining
the device performance. Materials to produce charge transport
layers may comprise organics, polymers, and metal oxides.
[0050] The present disclosure may comprise a new type of charge
transport layer based on halide perovskite thin films and methods
for producing these thin films. The charge transport layer may
comprise either a HTL or a ETL, or both in the same device, and may
be used in different types of LEDs (such as organic, quantum dot,
and perovskite emitting layers). Smooth halide perovskite thin
films (with a thickness ranging from a few nanometers to a few
hundred nanometers) may be prepared via either vacuum processing or
facile solution processing, such as spin coat and ink-jet. The
halide perovskite materials may have a general chemical formula of
ABX.sub.3, where A may be a cation such as but not limited to
methylammonium (CH.sub.3NH.sub.3), formamidinium
(NH.sub.2CHNH.sub.2), and cesium (Cs); B is a metal such as but not
limited to lead (Pb), tin (Sn), and germanium (Ge); and X is a
halide ion such as fluoride (F.sup.-), chloride (Cl.sup.-), bromide
(Br.sup.-), iodide (I.sup.-) and astatide (At.sup.-), and mixtures
of these materials. Thin film optoelectronic devices, for example
organic LEDs and organic PVs, may comprise perovskite-based charge
transport layers that exhibit superior device performance over
equivalent devices based on conventional charge transport layers
such as poly(3,4-ethylenedioxythiophene):poly(styrenesulfonate)
(PEDOT:PSS).
[0051] A desired hole transport material should have suitable
energy levels and band gap, as well as high hole conductivity, for
efficient hole injection and transport, and electron and exciton
blocking. mobility. A desired electron transport material should
have suitable energy levels and band gap, as well as high electron
conductivity, for efficient electron injection and transport, and
hole and exciton blocking. Selection of the hole transport material
and the electron transport material may comprise matching
appropriate individual energy levels and band gaps of each of the
materials in order to produce a desire functionality of the
resulting optoelectronic device.
[0052] As far as fabrication methods for HTL and ETL are concerned,
solution processing represents an attractive and economical
approach to replace high vacuum processing for the production of
thin films. Among a variety of solution processable hole transport
materials developed to date, including organic molecules, polymers,
and metal oxides,
poly(3,4-ethylenedioxythiophene):poly(styrenesulfonate) (PEDOT:PSS)
might be the most recognized material with good conductivity, high
transparency, and suitable work function. However, there are many
intrinsic limitations associated with PEDOT:PSS, such as its
acidity and hygroscopic nature that lead to issues of device
stability and degradation, and its lowest unoccupied molecular
orbital (LUMO) energy level and band gap that result in weak
electron blocking and serious exciton quenching. Crosslinkable
organic/polymeric hole transport materials, which may allow for the
formation of a solvent-resistant layer via crosslinking after
solution processing, have been explored for multilayer structured
devices, in particular organic light-emitting diodes (OLEDs).
However, preparation of crosslinkable materials is not
straightforward, which often involves costly multiple steps of
syntheses and purifications. Transition metal oxides, such as
oxides of nickel (NiO.sub.x), molybdenum (MoO.sub.x), tungsten
(WO.sub.x), and vanadium (VO.sub.x), represent another class of
hole transport materials that have been pursued. Solution processed
metal oxide HTLs are mainly obtained by either thermal
decomposition of organic-inorganic hybrid precursors or annealing
of nanoparticles capped with organic solubilizing/stabilizing
groups. Critical issues for solution processed oxide thin films
include defect states due to stoichiometry deviations, residual
--OH groups, and organic residues, which could negatively impact
the device efficiency and stability.
[0053] Earth-abundant organometal halide perovskites have shown
exceptional properties that make them suitable for low-cost
high-performance optoelectronic devices. These properties mainly
include facile low-temperature synthesis and solution
processability, highly tunable direct band gaps across the visible
to infrared regions, and high charge carrier mobilities.
Perovskite-based PVs have been developed with device efficiencies
increasing from about 3% to about 20%. Electrically driven LEDs and
optically pumped lasers have also been demonstrated with these
organic-inorganic hybrid semiconductors. The tunable band gaps,
band positions, and high charge carrier mobilities of these
materials also suggest that they could serve as high performance
solution processable charge transport materials.
[0054] The band gap and band position tunability of the halide
perovskite thin films may be derived from controlling the material
structure and composition. As described above, the metal halide
perovskite materials have a general chemical structure of
ABX.sub.3. By changing A, B, and X either independently or
simultaneously, a desired band gap or band position may be
obtained. FIG. 1 schematically illustrates a typical multilayer
thin film LED (organic LED, quantum dot LED, or perovskite LED)
device structure 100. An electroluminescent (EL) layer (light
emitting layer) 105 may be sandwiched between an electron transport
layer (ETL) 110 and a hole transport layer (HTL) 115. The ETL 110
may be further coupled to a cathode 120, and the HTL may be further
coupled to an anode 115. FIGS. 2A and 2B illustrates that either or
both the ETL 110 and the HTL 115 may comprise metal halide
perovskite thin films. In the structure illustrated in FIG. 2A, the
ETL 110 and the HTL 115 may have the same or similar band
positions, while the ETL 110 and the HTL 115 illustrated in FIG. 2B
may have distinctly different band positions. This is further
illustrated for two specific metal halide perovskites in FIG. 3. By
simply varying the halide in the ABX.sub.3 structure, the band
position can be varied from a range of -5.8 eV to -2.9 eV for
CH.sub.3NH.sub.3PbCl.sub.3 to a range of -5.7 eV to -3.4 eV for
CH.sub.3NH.sub.3PbBr.sub.3.
[0055] One of the advantages of the metal halide perovskite thin
film materials is that perovskite has a high charge mobility. For
instance, CH.sub.3NH.sub.3SnI.sub.3 has a hole mobility of 200-300
cm.sup.2V.sup.-1 s.sup.-1. Both CH.sub.3NH.sub.3PbI.sub.3 and
CH.sub.3NH.sub.3PbBr.sub.3 have a hole and electron mobility of
approximately 100 cm.sup.2V.sup.-1 s.sup.-1. The carrier mobility
of CH.sub.3NH.sub.3PbCl.sub.3 is approximately 50 cm.sup.2V.sup.-1
s.sup.-1. The charge mobility of perovskite is higher than organic
semiconductors and comparable to traditional inorganic
semiconductors. Table 1 lists the mobility values for selected
metal halide perovskites.
TABLE-US-00001 TABLE 1 Example Mobility Values for Selected Metal
Halide Perovskites Mobility, cm.sup.2V.sup.-1s.sup.-1 Materials
Electron Hole CH.sub.3NH.sub.3SnI.sub.3 200-300
CH.sub.3NH.sub.3PbI.sub.3 100 100 CH.sub.3NH.sub.3PbBr.sub.3 100
100 CH.sub.3NH.sub.3PbCl.sub.3 50
[0056] In various embodiments, the use of an organometal halide
perovskite-based HTL for highly efficient OLEDs has been
demonstrated for the first time. Methylammonium lead chloride
CH.sub.3NH.sub.3PbCl.sub.3 was chosen in certain embodiments for
its optical and electronic properties suitable for application in
HTL, i.e. transparency in the visible region due to a wide band gap
of about 3.1 eV and high hole conductivity. Although the discussion
hereinafter focuses on the use and subsequent results of thin films
prepared using methylammonium lead chloride, the present disclosure
shall not be considered limited or restricted in any way. One
skilled in the art will recognize, in conjunction with the
teachings of the present disclosure, that any of the compounds or
materials discussed above comprising ABX.sub.3 are within the scope
of the present disclosure.
[0057] By facile spin coating combined with solvent passivation,
essentially pure CH.sub.3NH.sub.3PbCl.sub.3 thin films may be
prepared at low temperature according to various embodiments. The
little-to-no solubility of CH.sub.3NH.sub.3PbCl.sub.3 thin films in
low polarity organic solvents, such as chloroform, chlorobenzene,
and toluene, allows for subsequent solution processing of another
layer on top to form multilayered structures. Phosphorescent OLEDs
based on this solution processed perovskite HTL at a thickness of
25 nm, with a structure of
ITO/CH.sub.3NH.sub.3PbCl.sub.3/PVK:PBD:TPY.sub.2Iracac/BCP/LiF/Al,
showed superior device performance with lower turn-on and operation
voltage, as well as higher brightness, external quantum efficiency,
power efficiency, and luminous efficiency, as compared to a control
device based on a standard PEDOT:PSS HTL. The present disclosure
represents the first time that organometal halide perovskites have
been used as charge transport materials in optoelectronic
devices.
[0058] CH.sub.3NH.sub.3PbCl.sub.3 may be synthesized by reacting
CH.sub.3NH.sub.3Cl with PbCl.sub.2, in the same way as other
methylammonium lead halide perovskites, such as
CH.sub.3NH.sub.3PbI.sub.3 and CH.sub.3NH.sub.3Br.sub.3. However,
preparing high quality essentially pure CH.sub.3NH.sub.3PbCl.sub.3
thin films via solution processing is not as trivial as for
CH.sub.3NH.sub.3PbI.sub.3 and CH.sub.3NH.sub.3bBr.sub.3, due to the
lower solubility of chloride precursors and faster crystallization
kinetics. Simple spin coating a dimethylformamide
(DMF)/dimethylsulfoxide (DMSO) mixed solution of precursors
containing CH.sub.3NH.sub.3Cl and PbCl.sub.2 leads to the formation
of large CH.sub.3NH.sub.3PbCl.sub.3 crystals with poor surface
coverage and extremely high roughness, as shown in FIGS. 4A and 4B.
The Root Mean Square roughness (Rq) was measured at .about.50
nm.
[0059] FIG. 5 is a flowchart of an exemplary method 500 for forming
a charge transport layer of a thin film optoelectronic device. At
step 505, an organometal halide perovskite precursor may be formed.
A substrate may be coated with the organometal halide perovskite
precursor at step 510 to form an organometal halide perovskite
layer. At step 515, the organometal halide perovskite layer may be
passivated with a solvent during the coating step, and the
passivated organometal halide perovskite layer may be annealed at
step 520.
[0060] FIG. 6 is a flowchart of an exemplary method 600 for forming
a charge transport layer of a thin film optoelectronic device. At
step 605, an organometal halide perovskite precursor may be formed
by dissolving methylammonium chloride (CH.sub.3NH.sub.3Cl) and lead
chloride (PbCl.sub.2) in a mixture of dimethylformamide and
dimethylsulfoxide. A substrate may be coated with the organometal
halide perovskite precursor at step 610 to form a layer of
methylammonium lead chloride (CH.sub.3NH.sub.3PbCl.sub.3) on the
substrate. At step 615, the methylammonium lead chloride layer may
be passivated by adding a low polarity organic solvent during the
coating step, and the passivated methylammonium lead chloride layer
may be annealed at step 620.
[0061] A new type of hole transport layer according to various
embodiments based on organometal-halide perovskite for highly
efficient LEDs has been demonstrated. The solvent passivation
approach allowed for the formation of smooth perovskite thin films
with great surface coverage. Solution processed multilayer green
phosphorescent LEDs based on this new perovskite HTL showed
superior performance over devices using conventional PEDOT:PSS HTL,
with lower turn-on (5.2 V vs. 5.9 V) and operating voltages, as
well as higher luminescence (2,400 cd/m.sup.2 vs. 1,400 cd/m.sup.2
at 15V), higher EQE (7.7% vs. 7.0%), higher power efficiency (7.4
lm/w, vs. 6.6 lm/w), and higher luminous efficiency (29.2 cd/A vs.
26.4 cd/A). The improved device performance was primarily
attributed to the wide band gaps, suitable energy levels, and
efficient hole injection and transport. Various embodiments
demonstrate a new pathway toward highly efficient solution
processed multilayer OLEDs, and further establish organic-inorganic
halide perovskites as a new class of semiconductors with highly
desirable characteristics for thin film optoelectronic devices.
EXAMPLES
Example 1
[0062] To prepare smooth CH.sub.3NH.sub.3PbCl.sub.3 thin films with
good surface coverage suitable for optoelectronic devices, a
solvent passivation approach was used. FIG. 7 and FIG. 9 illustrate
the procedure (700 in FIG. 7) for the preparation of essentially
pure CH.sub.3NH.sub.3PbCl.sub.3 thin films according to various
embodiments by spin coating combined with solvent passivation and
thermal annealing. The perovskite precursors contained 0.64 M
CH.sub.3NH.sub.3Cl and 0.4 M PbCl.sub.2 in a solvent mixture of DMF
and DMSO (DMF:DMSO, 7:3, V/V). Spin coating (step 705) was carried
out at 6,000 rpm for 30 seconds. One ml chlorobenzene was quickly
dropped on the thin film at 6 s after the spin coating started
(step 710), forming the CH.sub.3NH.sub.3PbCl.sub.3 thin film (step
715). After solution processing, thermal annealing was performed at
100.degree. C. for 10 mins to remove the solvent residue and ensure
the full conversion of perovskite precursors into
CH.sub.3NH.sub.3PbCl.sub.3 crystals (step 720). FIG. 8A shows the
optical image of the CH.sub.3NH.sub.3PbCl.sub.3 thin film of about
25 nm thickness on a glass substrate, which is almost featureless
with great transparency. The morphology of this perovskite thin
film was characterized by atomic force microscopy (AFM), as shown
in FIG. 8A. The 3-D height view is shown in FIG. 8B. Except few
randomly scattered nanocrystals standing out, the thin film showed
great surface coverage on the glass substrate and good smoothness
with a surface roughness of Rq=7.2 nm.
[0063] The formation of highly crystalline and essentially pure
CH.sub.3NH.sub.3PbCl.sub.3 thin films was confirmed by X-ray
diffraction (XRD), as shown in FIG. 10. XRD peaks 15.431.degree.,
31.309.degree., 47.833.degree. are ascribed to (100), (200) and
(300) crystal plane respectively, which are consistent with the
cubic structure of CH.sub.3NH.sub.3PbCl.sub.3 crystal. FIG. 11
shows the transmittance spectra of the perovskite thin film of 25
nm thick. A sharp peak occurred at around 400 nm, which was
attributed to the absorption of CH.sub.3NH.sub.3PbCl.sub.3. In the
visible region, the perovskite thin film showed extremely high
transparency (>95%), which is comparable to that of a 40 nm
thick PEDOT:PSS film. This high transparency in the visible region
allowed the perovskite thin film to be inserted between the light
emitting layer and transparent electrode without affecting the
light extraction of emission in the visible region.
Example 2
[0064] For various embodiments, the performance of
CH.sub.3NH.sub.3PbCl.sub.3 thin films as HTL in green
phosphorescent OLEDs was evaluated. FIG. 12 shows the multilayered
device structure, and the materials chemical structures are shown
in FIG. 13. A 80 nm thick electroluminescent layer (EL) comprised a
guest-host blend with 5 wt % of green phosphorescent emitter
TPY.sub.2Iracac doped in a PVK:PBD (60/40, w/w) host. A 40 nm thick
BCP layer acted as an electron transport and hole/exciton blocking
layer. The metal cathode comprised 1 nm LiF and 100 nm Al. Control
devices without HTL and with a PEDOT:PSS HTL were also fabricated
and tested for comparison. FIG. 14 shows the corresponding energy
level diagram for the multilayer structured devices. The Valence
Band Maximum (VBM) and Conduction Band Minimum (CBM) energy levels
of CH.sub.3NH.sub.3PbCl.sub.3 were reported to be 5.82 eV and 2.94
eV, respectively. The deep VBM energy level of
CH.sub.3NH.sub.3PbCl.sub.3 aligned well with the Highest Occupied
Molecular Orbital (HOMO) of PVK, which could enable efficient
direct hole injection from the perovskite layer into the PVK:PBD
host and/or phosphorescent dopants. FIG. 15 shows the
electroluminescent spectrum for all the phosphorescent devices with
different HTLs. Pure green emission (peak at 523 nm) from the
phosphorescent TPY.sub.2Iracac doped into PVK:PBD was observed,
suggesting that charge recombination primarily occurred in the
emitting layer and there was efficient energy transfer from the
PVK:PBD host to the dopant. No emission from the
CH.sub.3NH.sub.3PbCl.sub.3 layer was observed, which is not
surprising considering its wide band gap and efficient energy
transfer to the emitting layer.
Example 3
[0065] The device characteristics of OLEDs without HTL, with a
PEDOT:PSS HTL, and with a 25 nm CH.sub.3NH.sub.3PbCl.sub.3 thin
film HTL, are presented in FIGS. 16 through 19 in terms of current
density versus voltage (FIG. 16) and brightness versus voltage
(FIG. 17). For external quantum efficiencies, power efficiencies
are presented in FIG. 18 and luminous efficiencies are presented in
FIG. 19. The major device performance values are summarized in
Table 2. As shown in FIG. 16, the device with a
CH.sub.3NH.sub.3PbCl.sub.3 HTL showed much higher current density
than the control devices with a PEDOT:PSS HTL and without HTL,
indicating the superior charge injection and transport from the ITO
anode to the CH.sub.3NH.sub.3PbCl.sub.3 layer and light emitting
layer. A higher brightness is achieved for the device with a
CH.sub.3NH.sub.3PbCl.sub.3 HTL over the PEDOT:PSS based device at
the same operating voltage, as shown in FIG. 17. The turn-on
voltage (@1 cd/m.sup.2) of the CH.sub.3NH.sub.3PbCl.sub.3 based
device is 5.3V, which is lower than 5.9 V of the PEDOTDT:PSS based
device. At 20V, a maximum brightness of 19,400 cd/m.sup.2 is
achieved for the CH.sub.3NH.sub.3PbCl.sub.3 based device, which is
higher than 18,300 cd/m.sup.2 for the PEDOT:PSS device. The device
with a PEDOT:PSS HTL shows a maximum EQE (7%), maximum power
efficiency (6.6 lm/W) and maximum luminous efficiency (26.6 cd/A).
These device performance values are comparable to previous results
for devices based on PEDOT:PSS with solution processed light
emitting layers containing PVK, PBD, and TPY.sub.2Iracac. In
contrast, the device with a CH.sub.3NH.sub.3PbCl.sub.3 HTL shows
enhanced maximum EQE (7.7%), maximum power efficiency (7.4 lm/W)
and maximum luminous efficiency (29.2 cd/A). As compared to the
device without HTL, the CH.sub.3NH.sub.3PbCl.sub.3 based OLED shows
two fold higher EQE, power efficiency, and luminous efficiency,
which clearly confirmed the hole injection/transport functionality
of the solution processed CH.sub.3NH.sub.3PbCl.sub.3 layer.
TABLE-US-00002 TABLE 2 Device Characteristics of OLEDs with
Different HTLs HTL No HTL PEDOT:PSS CH.sub.3CH.sub.3PbCl.sub.3
Turn-on Voltage 7.4 5.9 5.3 (1 cd/m.sup.2), V Max. Brightness 6,100
18,300 19,400 (@20 V), cd/m.sup.2 Max. EQE, % 3.8 7.0 7.7 Max.
Power Efficiency, 2.9 6.6 7.4 lm/W Max. Luminous Efficiency, 14.7
26.6 29.2 cd/A
Example 4
[0066] To further confirm the enhanced hole injection and transport
with the introduction of a CH.sub.3NH.sub.3PbCl.sub.3 layer,
impedance spectroscopy measurements were performed on the
fabricated devices. Much lower impedance is observed for the device
with a CH.sub.3NH.sub.3PbCl.sub.3 HTL as shown in FIG. 20 than the
control device with a PEDOT:PSS HTL as shown in FIG. 21, suggesting
the reduction of a barrier for the hole injection, consistent with
the lowered driving voltage for the device. OLEDs with
CH.sub.3NH.sub.3PbCl.sub.3 HTLs at different thicknesses of 20 nm
and 15 nm have also been fabricated, which showed slightly lower
device performance in FIGS. 22 through 25 as compared to the
results presented in FIGS. 16 through 19. This could be attributed
to the inferior thin film morphology and surface coverage as shown
in the AFM images of FIGS. 26A and 26B (20 nm) and FIGS. 27A and
27B (15 nm), which could lead to less efficient hole injection and
transport.
Experimental
[0067] Materials and Equipment.
[0068] PEDOT:PSS (Clevios.TM. P VP AI 4083) was purchased from
Heraeus. CH.sub.3NH.sub.3Cl, PbCl.sub.2, PVK, PBD, BCP, LiF, and Al
were purchased from Sigma-Aldrich and used as received.
TPY.sub.2Iracac was synthesized in-house according to the report
procedure. Pre-patterned ITO-coated glass substrates (20
.OMEGA./sq) were purchased from the Thin Film Devices Inc.
[0069] Thin film optical absorption and transparency were measured
in a CARY 5000 UV-Vis-NIR spectrophotometer. The thickness of thin
films was determined by a Dektak 150 profilometer. Atomic force
microscopy (AFM) images were taken with a Bruker Icon scanning
probe microscope in tapping-mode.
[0070] X-Ray Diffraction was performed using a custom built Huber
4-circle diffractometer with graphite monochromator and analyzer in
non-dispersive diffraction geometry, coupled to a Rigaku rotating
anode generator producing CuK.alpha. radiation.
[0071] Preparations of Perovskite Thin Films.
[0072] CH.sub.3NH.sub.3Cl and PbCl.sub.2 were dissolved in DMF:DMSO
mixed solutions (DMF:DMSO,7/3,V/V) at concentrations of 0.64 M and
0.4 M respectively. The CH.sub.3NH.sub.3PbCl.sub.3 precursor
solution was prepared by mixing the CH.sub.3NH.sub.3Cl and
PbCl.sub.2 solutions by 1 to 1 volume ratio. DMSO was used to
enhance the solubility of CH.sub.3NH.sub.3PbCl.sub.3. The mixed
solution passed though a syringe filter before it was spin cast on
substrates at 6,000 rpm for 30 s. One ml chlorobenzene was quickly
dropped at 6 s during spin coating. Thermal annealing was performed
right after spin casting at 100.degree. C. for 10 mins to remove
the solvent residue and fully convert the precursors into
CH.sub.3NH.sub.3PbCl.sub.3 thin films. CH.sub.3NH.sub.3PbCl.sub.3
thin films at 20 nm and 10 nm thick were also prepared by using the
same method with 0.4 M CH.sub.3NH.sub.3Cl+0.25 M PbCl.sub.2, and
0.24 M CH.sub.3NH.sub.3Cl+0.15 M PbCl.sub.2, respectively.
[0073] Phosphorescent OLEDs Fabrication and Testing.
[0074] ITO-coated glass substrates were cleaned by successive
sonication in soap solution, deionized water, acetone, and
isopropanol for 15 min at 40.degree. C. and UV ozone cleaned for 20
min. For the device with PEDOT:PSS as HTL, PEDOT:PSS was spun-cast
onto the cleaned ITO coated glass substrate at a spin speed of
3,000 rpm for 45 s and baked at 140.degree. C. for 20 mins to
obtain a 40 nm thick thin film. For the devices with
CH.sub.3NH.sub.3PbCl.sub.3 based HTLs, the films were prepared by
the method mentioned above. After the deposition of HTL, a solution
of 13 mg/mL PVK:PBD (60/40 w/w) containing 5 wt % of
TPY.sub.2Iracac in chloroform was spin coated on the top at 4,000
rpm for 30 s. The thickness was about 80 nm. A 40 nm thick layer of
BCP was then deposited at a rate of 1.0 .ANG./s under high vacuum
conditions (<3.times.10.sup.-6 Torr). After the deposition of
BCP, the chamber was vented, and a shadow mask with a 2 mm wide
stripe was placed onto the substrates perpendicular to the ITO
stripes. 1 nm LiF and 100 nm Al were deposited at a rate of 0.02
.ANG./s and 4 .ANG./s, respectively. OLEDs were formed at the
2.times.2 mm squares where the ITO (anode) and Al (cathode) stripes
intersect.
[0075] The devices were tested in air within 30 mins after
fabrication. The electrical and optical intensity characteristics
of the devices were measured with a Keithly 4200
sourcemeter/multimeter coupled to a FDS 1010 Si photodiode (Thor
Labs). Only light emitted from the front face of the device was
collected and used in subsequent efficiency calculations. The
electroluminescence (EL) spectra were measured on a HORIBA iHR320
spectrofluorimeter, equipped with a HORIBA Synapse CCD detection
system. The emission was found to be uniform throughout the area of
each device.
[0076] Impedance Spectroscopy Study.
[0077] The Impedance Spectroscopy measurements were performed on
the fabricated devices using a Gamry Interface 1000. DC voltage was
fixed at 8V. For the AC voltage, the amplitude of the test signal
was 100 mV. The range of measurement frequency was set from 100 Hz
to 1 MHz. From the Cole-Cole plot in FIGS. 15 and 16, the bulk
resistance Rb2 of the PEDOT:PSS based device was determined at
about 827.times.10.sup.3 ohm. As compared to the control device,
the bulk resistance Ra2 of CH.sub.3NH.sub.3PbCl.sub.3 based device
dramatically decreased to 18.times.10.sup.3 ohm, which proved that
the CH.sub.3NH.sub.3PbCl.sub.3 based device had a much higher
conductivity and lower driving voltage. The results were consistent
with the higher current density in CH.sub.3NH.sub.3PbCl.sub.3 based
device than PEDOT:PSS device.
[0078] The advantages set forth above, and those made apparent from
the foregoing description, are efficiently attained. Since certain
changes may be made in the above construction without departing
from the scope of the present disclosure, it is intended that all
matters contained in the foregoing description or shown in the
accompanying drawings shall be interpreted as illustrative and not
in a limiting sense.
[0079] It is also to be understood that the following claims are
intended to cover all of the generic and specific features of the
present disclosure herein described, and all statements of the
scope of the present disclosure that, as a matter of language,
might be said to fall therebetween.
Glossary of Claim Terms
[0080] Anneal: A process, typically thermal, used to further a
chemical reaction and evaporate volatile components.
[0081] Charge transport layer: A layer, such as a hole transporting
layer or an electron transporting layer, in an optoelectronic
device that allows for the movement of electrons within the device
in response to an electric current of exposure to a light
source.
[0082] Light emitting: A device or material that emits visible
light when subjected to an electric current.
[0083] Light harvesting: A device or material that absorbs energy
from radiant light and produces an electrical current.
[0084] Low polarity organic solvent: an organic (carbon based)
solvent with a relatively low dielectric constants (ranging from
about 5 to 20).
[0085] Organometal halide: A compound containing at least one bond
between a carbon atom of an organic compound and a metal and that
also contains a halide ion.
[0086] Passivate: A chemical modification of a surface.
[0087] Perovskite: A class of compounds with the same type of
crystal structure as calcium titanium oxide (CaTiO.sub.3) with the
oxygen in the face centers.
[0088] Photoactive layer: The layer of an optoelectronic device
that absorbs or emits light.
[0089] Thin film optoelectronic device: An optoelectronic device
utilizing one or more layers of material ranging in thickness from
fractions of a nanometer to several micrometers.
* * * * *