U.S. patent application number 16/048766 was filed with the patent office on 2019-02-21 for energy-saving control method of resonant piezoelectric air pump.
This patent application is currently assigned to Microjet Technology Co., Ltd.. The applicant listed for this patent is Microjet Technology Co., Ltd.. Invention is credited to Shih-Chang CHEN, Chi-Feng HUANG, Wei-Ming LEE, Jia-Yu LIAO, Hao-Jan MOU.
Application Number | 20190055936 16/048766 |
Document ID | / |
Family ID | 63079792 |
Filed Date | 2019-02-21 |
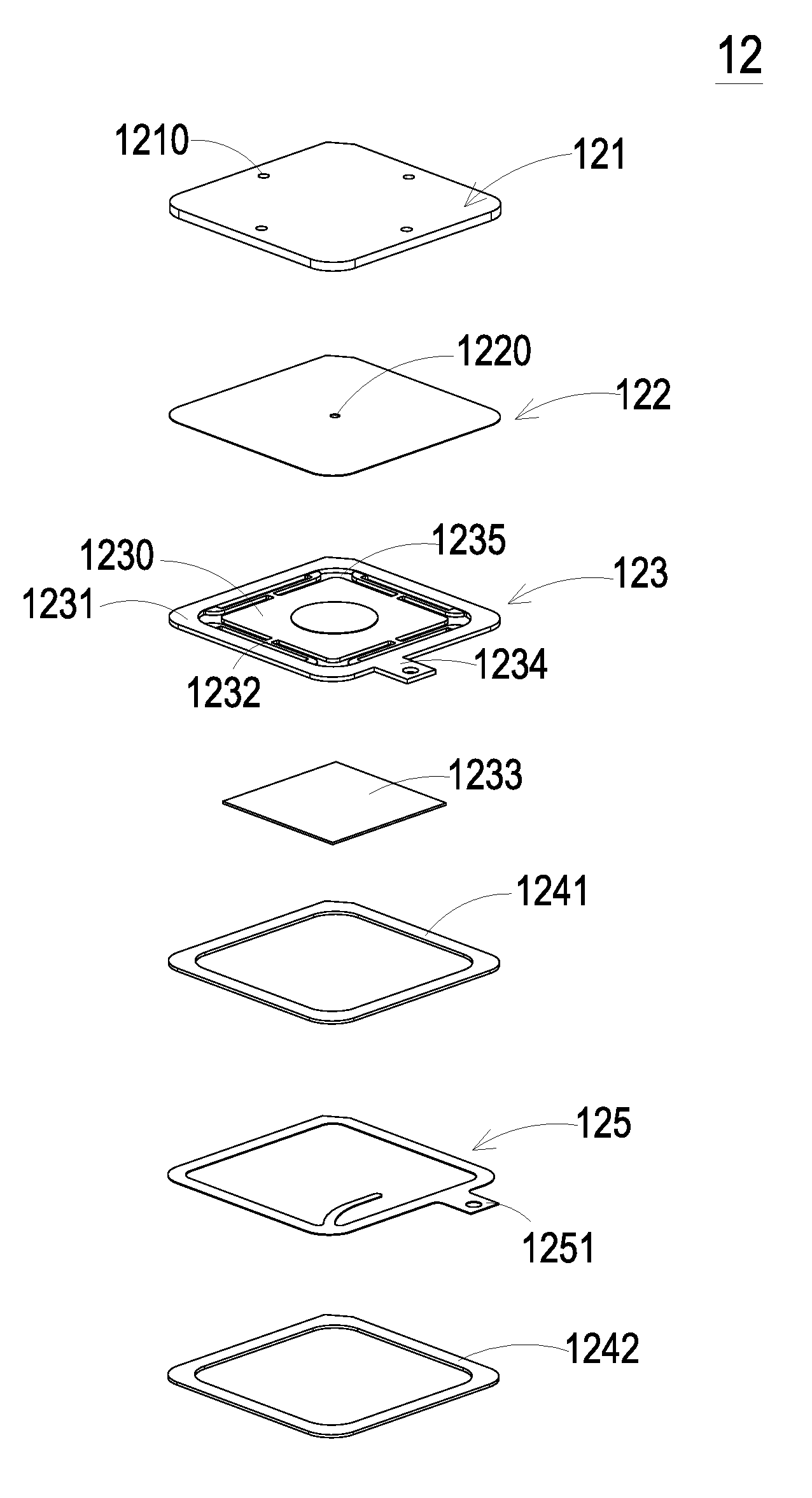
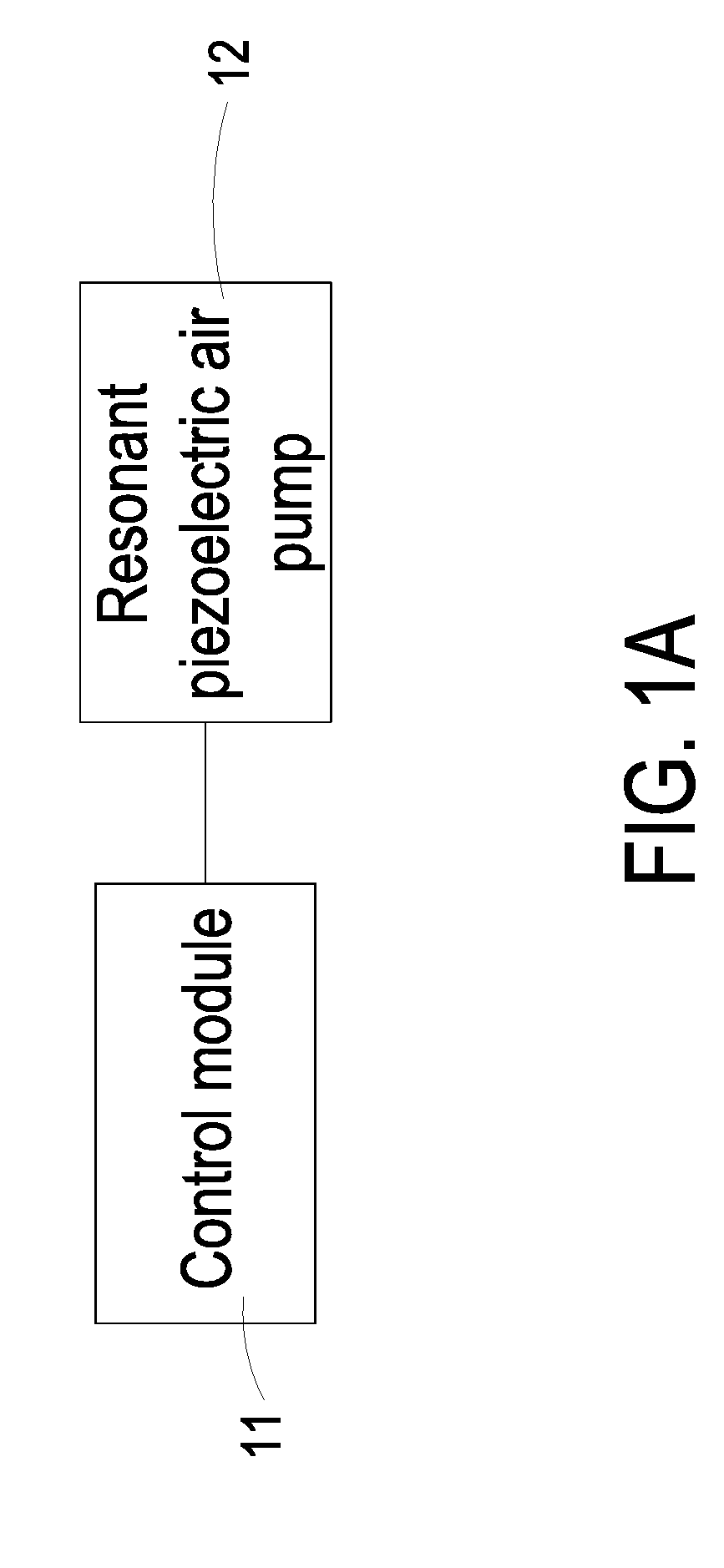
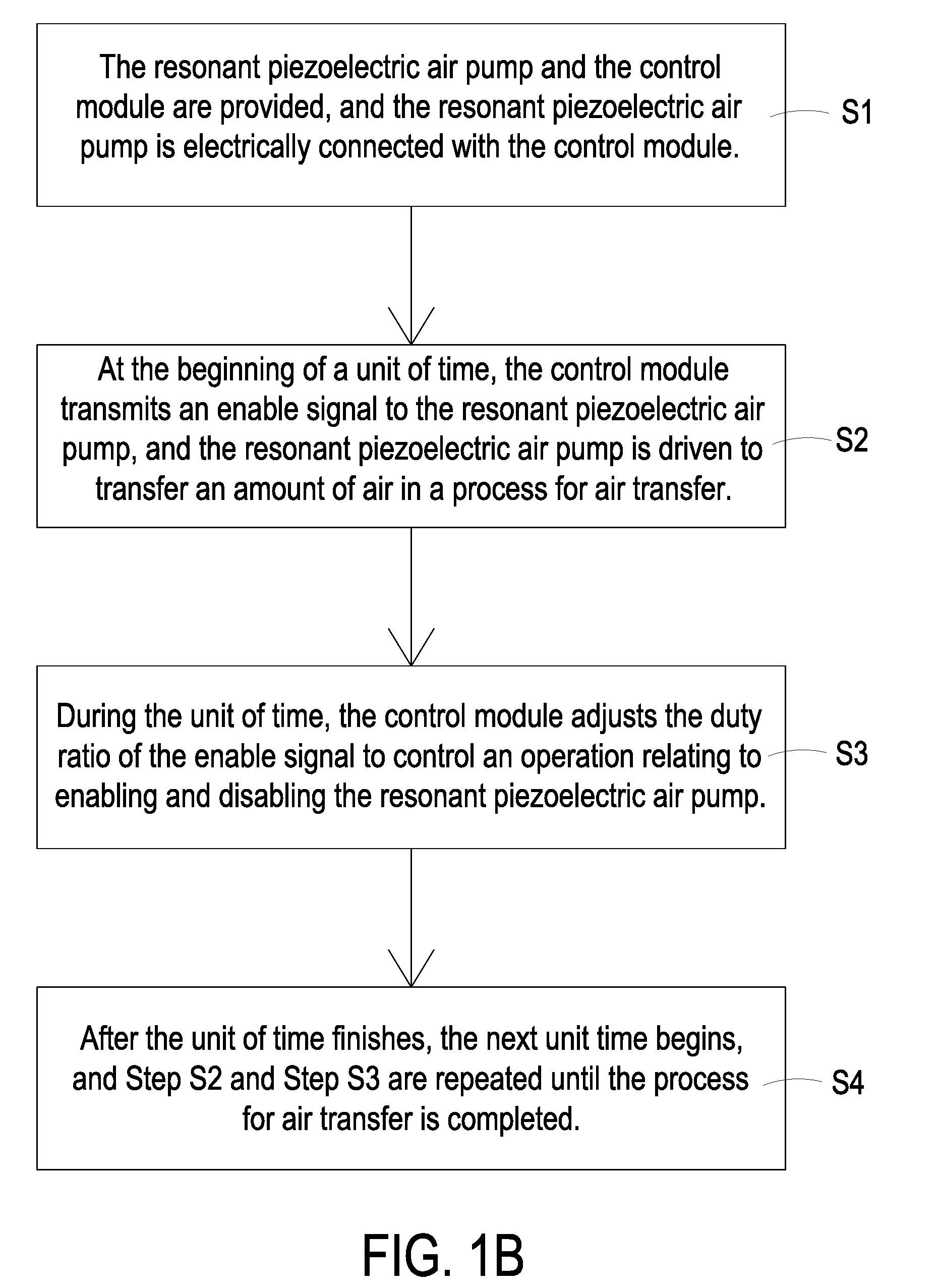




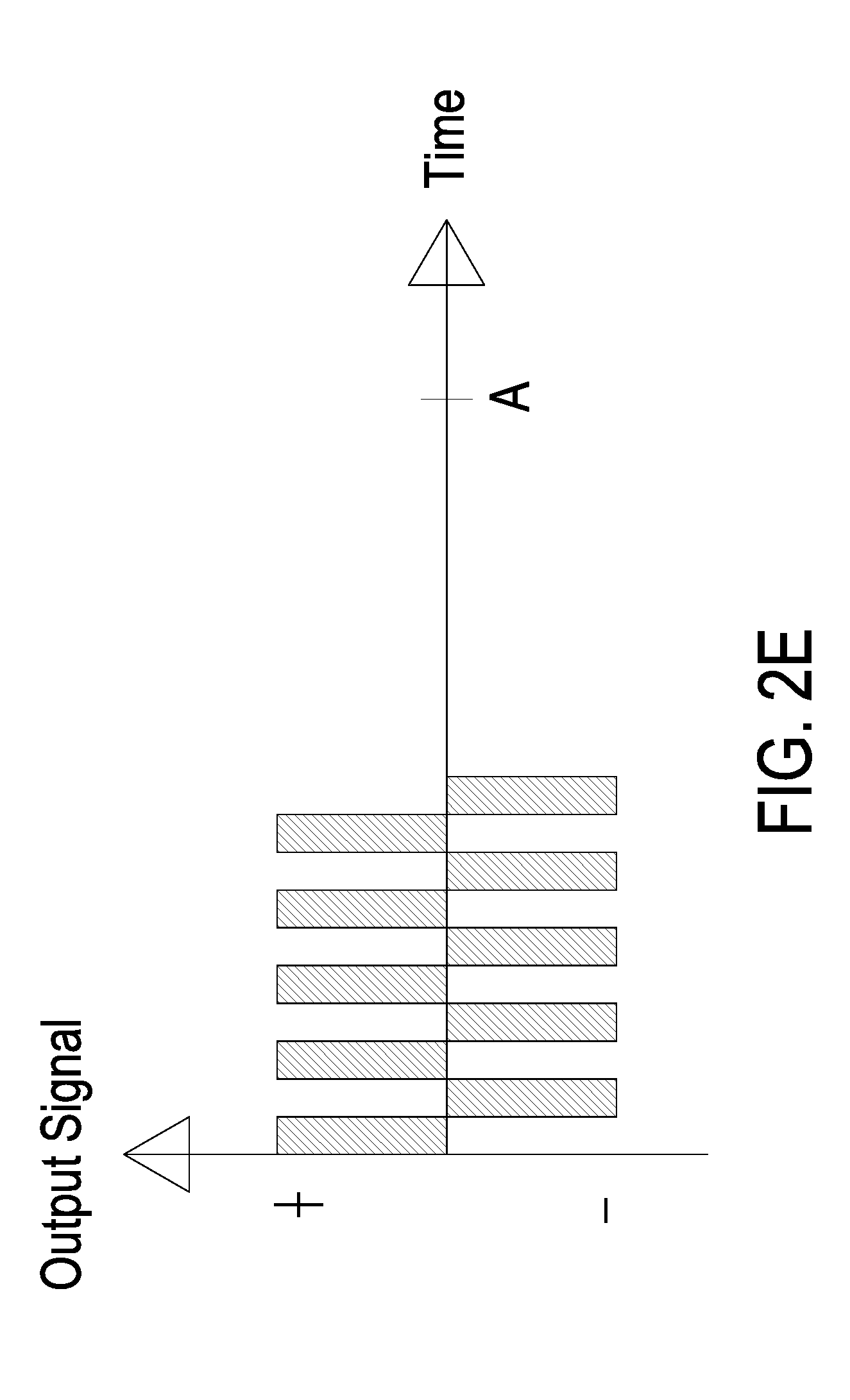

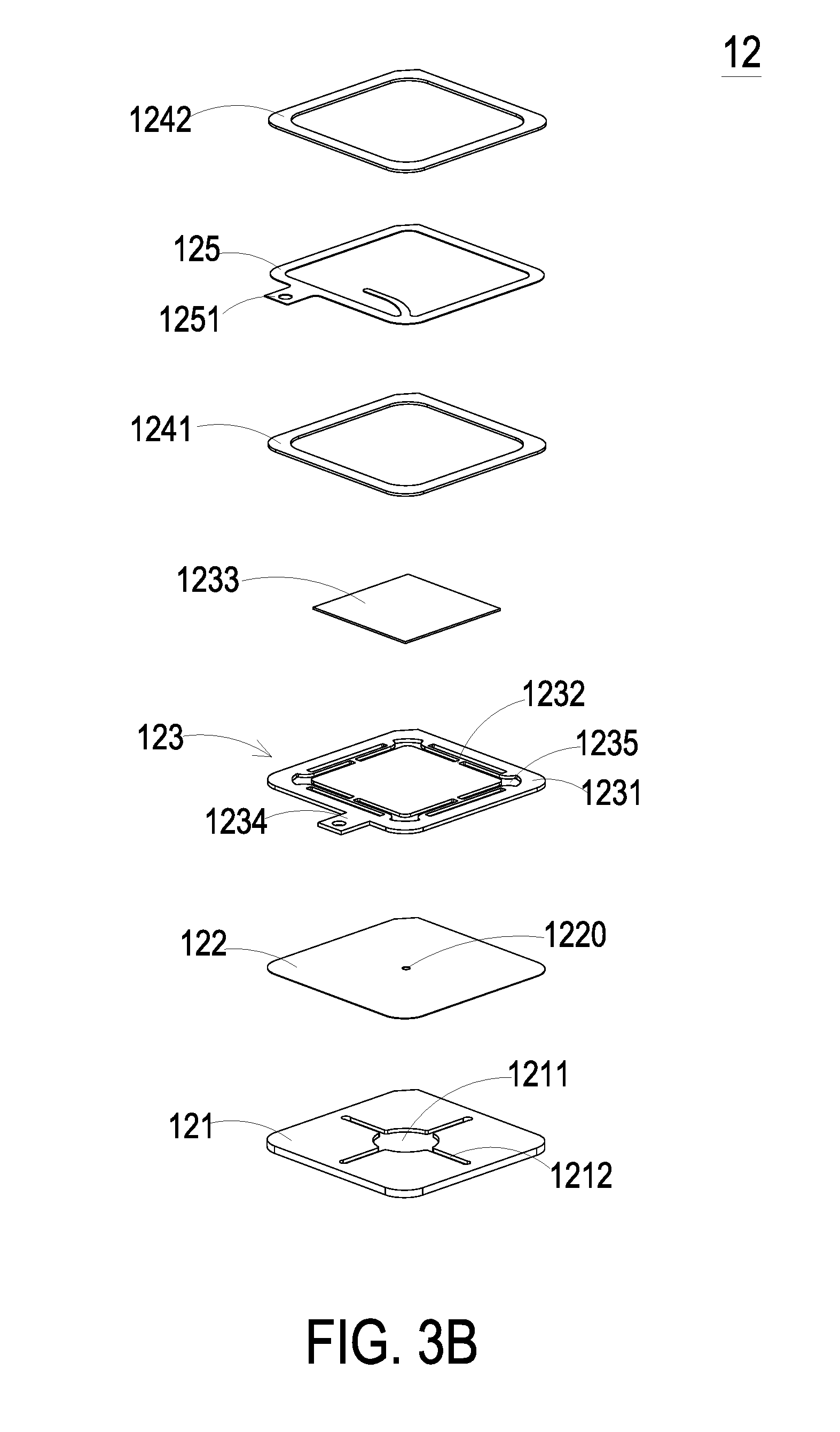
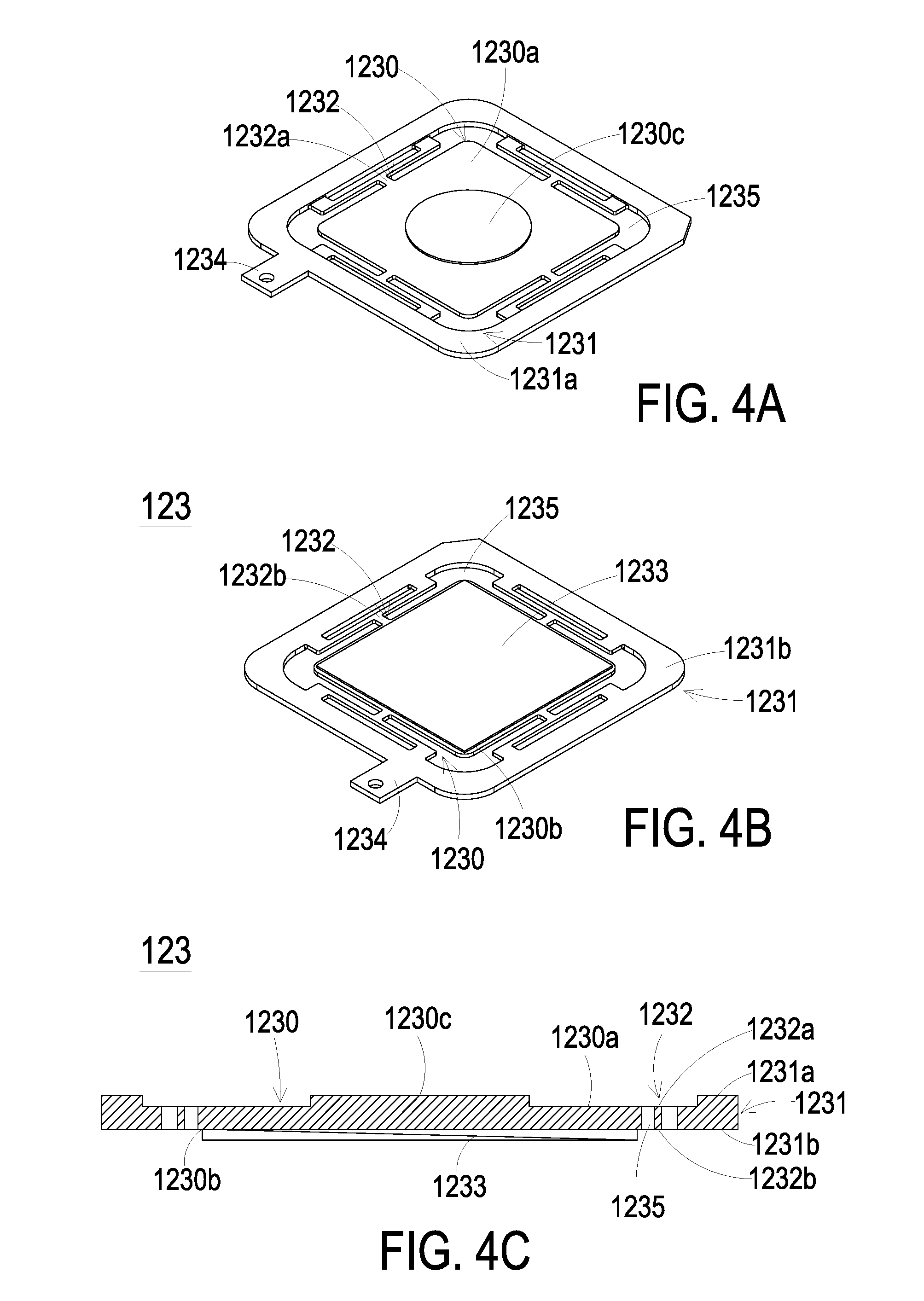
View All Diagrams
United States Patent
Application |
20190055936 |
Kind Code |
A1 |
MOU; Hao-Jan ; et
al. |
February 21, 2019 |
ENERGY-SAVING CONTROL METHOD OF RESONANT PIEZOELECTRIC AIR PUMP
Abstract
An energy-saving control method of a resonant piezoelectric air
pump includes steps of: (a) providing the resonant piezoelectric
air pump and a control module, wherein the resonant piezoelectric
air pump and the control module are electrically connected to each
other; (b) at the beginning of a unit of time, operating the
control module to transmit an enable signal to the resonant
piezoelectric air pump so that the resonant piezoelectric air pump
is driven to transfer an amount of air in a process for air
transfer; (c) during the unit of time, adjusting a duty ratio of
the enable signal by using the control module for enabling or
disabling the resonant piezoelectric air pump; and (d) after
spending the unit of time, repeating the step (b) and the step (c)
in another unit of time or more units of time thereafter until the
process for air transfer is completed.
Inventors: |
MOU; Hao-Jan; (Hsinchu,
TW) ; CHEN; Shih-Chang; (Hsinchu, TW) ; LIAO;
Jia-Yu; (Hsinchu, TW) ; HUANG; Chi-Feng;
(Hsinchu, TW) ; LEE; Wei-Ming; (Hsinchu,
TW) |
|
Applicant: |
Name |
City |
State |
Country |
Type |
Microjet Technology Co., Ltd. |
Hsinchu |
|
TW |
|
|
Assignee: |
Microjet Technology Co.,
Ltd.
Hsinchu
TW
|
Family ID: |
63079792 |
Appl. No.: |
16/048766 |
Filed: |
July 30, 2018 |
Current U.S.
Class: |
1/1 |
Current CPC
Class: |
H01L 41/0973 20130101;
F04B 45/04 20130101; F04B 49/065 20130101; H01L 23/467 20130101;
F04B 2207/043 20130101; H01L 41/042 20130101; F04B 35/04 20130101;
F04B 49/06 20130101; F04B 17/003 20130101; F04B 45/047
20130101 |
International
Class: |
F04B 49/06 20060101
F04B049/06; F04B 45/047 20060101 F04B045/047 |
Foreign Application Data
Date |
Code |
Application Number |
Aug 21, 2017 |
TW |
106128266 |
Claims
1. An energy-saving control method of a resonant piezoelectric air
pump, comprising steps of: (a) providing the resonant piezoelectric
air pump and a control module, wherein the resonant piezoelectric
air pump and the control module are electrically connected to each
other; (b) at the beginning of a unit of time, operating the
control module to transmit an enable signal to the resonant
piezoelectric air pump so that the resonant piezoelectric air pump
is driven to transfer an amount of air in a process for air
transfer; (c) during the unit of time, adjusting a duty ratio of
the enable signal by using the control module for enabling or
disabling the resonant piezoelectric air pump; and (d) after
spending the unit of time, repeating the step (b) and the step (c)
in another unit of time or more units of time thereafter until the
process for air transfer is completed.
2. The energy-saving control method of the resonant piezoelectric
air pump according to claim 1, wherein the duty ratio of the enable
signal is between 0.1% and 99%.
3. The energy-saving control method of the resonant piezoelectric
air pump according to claim 2, wherein the duty ratio of the enable
signal is 10%.
4. The energy-saving control method of the resonant piezoelectric
air pump according to claim 2, wherein the duty ratio of the enable
signal is 50%.
5. The energy-saving control method of the resonant piezoelectric
air pump according to claim 2, wherein the unit of time is 1
second.
6. The energy-saving control method of the resonant piezoelectric
air pump according to claim 2, wherein the unit of time is 0.5
seconds.
7. The energy-saving control method of the resonant piezoelectric
air pump according to claim 2, wherein the duty ratio of the enable
signal is 0.1%.
8. The energy-saving control method of the resonant piezoelectric
air pump according to claim 7, wherein a frequency of the enable
signal is between 20 KHz and 28 KHz.
9. The energy-saving control method of the resonant piezoelectric
air pump according to claim 7, wherein the frequency of the enable
signal is 28 KHz.
10. The energy-saving control method of the resonant piezoelectric
air pump according to claim 1, wherein the resonant piezoelectric
air pump comprises: an air inlet plate having at least one inlet,
at least one convergence channel and a central cavity, wherein the
at least one convergence channel spatially corresponds to the at
least one inlet and guides air from the inlet to converge to the
central cavity; a resonance plate having a central aperture,
wherein the central aperture is spatially corresponding to the
central cavity; a piezoelectric actuator having a suspension plate,
an outer frame, a plurality of brackets and a piezoelectric ceramic
plate, wherein the plurality of brackets are connected between the
suspension plate and the outer frame, and the piezoelectric ceramic
plate is attached on a surface of the suspension plate; at least
one insulation plate; and a conducting plate, wherein the air inlet
plate, the resonance plate, the piezoelectric actuator, the at
least one insulation plate and the conducting plate are stacked
sequentially to be assembled together as the resonant piezoelectric
air pump, and a first chamber is defined by a gap between the
resonance plate and the piezoelectric actuator.
11. The energy-saving control method of the resonant piezoelectric
air pump according to claim 10, wherein the step (b) of the
energy-saving control method further comprises a step of: (b1)
vibrating the piezoelectric actuator in a downward direction by
enabling the resonant piezoelectric air pump, wherein the air is
inhaled from the at least one inlet of the air inlet plate,
converged to the central cavity along the at least one convergence
channel and flows in the downward direction into the first chamber
through the central aperture of the resonance plate.
12. The energy-saving control method of the resonant piezoelectric
air pump according to claim 11, wherein the step (b) of the
energy-saving control method further comprises a step of: (b2)
vibrating the resonance plate in the downward direction in
resonance with the piezoelectric actuator, wherein the resonance
plate moves away from an original position and attaches to the
suspension plate of the piezoelectric actuator, and the volume of
the first chamber is compressed, thereby pushing the air to move
toward the peripheral regions of the first chamber and flow
downwardly through a vacant space between the brackets of the
piezoelectric actuator.
13. The energy-saving control method of the resonant piezoelectric
air pump according to claim 12, wherein the step (b) of the
energy-saving control method further comprises a step of: (b3)
vibrating the piezoelectric actuator in an upward direction when
the resonance plate returns to the original position, wherein the
volume of the first chamber is compressed which makes the air flow
toward the peripheral regions of the first chamber and the air
outside the resonant piezoelectric air pump is continuously inhaled
from the at least one inlet of the air inlet plate and then
converged to the central cavity.
14. The energy-saving control method of the resonant piezoelectric
air pump according to claim 13, wherein the step (b) of the
energy-saving control method further comprises a step of: (b4)
vibrating the resonance plate in the upward direction in resonance
with the piezoelectric actuator, wherein the air in the central
cavity is introduced into the first chamber through the central
aperture of the resonance plate, and the air moves in the downward
direction and passes through the vacant space between the brackets
of the piezoelectric actuator.
15. The energy-saving control method of the resonant piezoelectric
air pump according to claim 14, wherein the step (b) of the
energy-saving control method further comprises a step of: (b5)
repeating the step (b1), the step (b2), the step (b3) and the step
(b4) for transferring the air continuously.
16. An energy-saving control method of a resonant piezoelectric air
pump, comprising steps of: (a) providing at least one resonant
piezoelectric air pump and at least one control module, wherein the
resonant piezoelectric air pump and the control module are
electrically connected to each other; (b) at the beginning of a
unit of time, operating the control module to transmit at least one
enable signal to the resonant piezoelectric air pump so that the
resonant piezoelectric air pump is driven to transfer an amount of
air in a process for air transfer; (c) during the unit of time,
adjusting a duty ratio of the enable signal by using the control
module for enabling or disabling the resonant piezoelectric air
pump; and (d) after spending the unit of time, repeating the step
(b) and the step (c) in another unit of time or more units of time
thereafter until the process for air transfer is completed.
Description
FIELD OF THE INVENTION
[0001] The present disclosure relates to an energy-saving control
method of a resonant piezoelectric air pump, and more particularly
to an energy-saving control method for driving a resonant
piezoelectric air pump by adjusting a duty ratio.
BACKGROUND OF THE INVENTION
[0002] With the development of science and technology, air transfer
is widely applied in all kinds of electronic devices and medical
equipments, and various effects can be achieved by the air
transfer. In addition, with the miniaturization and thinning
tendency of electronic device and medical equipment, the resonant
piezoelectric air pump or the miniature motor is used more widely
because of its small size.
[0003] In the prior art, the resonant piezoelectric air pump or the
miniature motor is driven to transfer the air in an operation
without interruption, so as to maximize the amount of the
transferred air per unit of time. However, the operation without
interruption consumes a lot of power, and the consumed power under
the operation without interruption can't result in the most
efficient air transfer. Accordingly, there is a need for a solution
that enhances the efficiency of air transfer of the resonant
piezoelectric air pump or the miniature motor and saves energy at
the same time.
[0004] Moreover, during the uninterrupted operation of the resonant
piezoelectric air pump or the miniature motor, the temperature of
the elements therein may be too high. Accordingly, the elements
inside the resonant piezoelectric air pump or the miniature motor
are broken due to the over-high temperature, the efficiency of air
transfer decreases, and the temperature of the outputted air is too
high. Accordingly, it is also important to prevent the temperature
from getting too high during the air transfer of the resonant
piezoelectric air pump or the miniature motor.
[0005] Therefore, there is a need for providing an energy-saving
control method of a resonant piezoelectric air pump for solving the
problems that exists in the prior art relating to inefficient air
transfer, large power consumption and over-high temperature caused
by the operation without interruption.
SUMMARY OF THE INVENTION
[0006] An object of the present disclosure provides an
energy-saving control method of a resonant piezoelectric air pump.
By adjusting the duty ratio for driving the resonant piezoelectric
air pump, the problems that exists in the prior art relating to
inefficient air transfer, large power consumption and over-high
temperature caused by the operation without interruption are
solved.
[0007] In accordance with an aspect of the present disclosure, an
energy-saving control method of a resonant piezoelectric air pump
is provided. The energy-saving control method includes steps of:
(a) providing the resonant piezoelectric air pump and a control
module, wherein the resonant piezoelectric air pump and the control
module are electrically connected to each other; (b) at the
beginning of a unit of time, operating the control module to
transmit an enable signal to the resonant piezoelectric air pump so
that the resonant piezoelectric air pump is driven to transfer an
amount of air in a process for air transfer; (c) during the unit of
time, adjusting duty ratio of the enable signal by using the
control module for enabling or disabling the resonant piezoelectric
air pump; and (d) after spending the unit of time, repeating the
step (b) and the step (c) in another unit of time or more units of
time thereafter until the process for air transfer is
completed.
[0008] In accordance with another aspect of the present disclosure,
an energy-saving control method of a resonant piezoelectric air
pump is provided. The energy-saving control method includes steps
of: (a) providing at least one resonant piezoelectric air pump and
at least one control module, wherein the resonant piezoelectric air
pump and the control module are electrically connected to each
other; (b) at the beginning of at least one unit of time, operating
the control module to transmit at least one enable signal to the
resonant piezoelectric air pump so that the resonant piezoelectric
air pump is driven to transfer an amount of air in a process for
air transfer; (c) during the unit of time, adjusting a duty ratio
of the enable signal by using the control module for enabling or
disabling the resonant piezoelectric air pump; and (d) after
spending the unit of time, repeating the step (b) and the step (c)
in another unit of time or more units of time thereafter until the
process for air transfer is completed.
BRIEF DESCRIPTION OF THE DRAWINGS
[0009] FIG 1A is a schematic view illustrating a resonant
piezoelectric air pump and a control module according to an
embodiment of the present disclosure;
[0010] FIG. 1B is a flowchart illustrating an energy-saving control
method of the resonant piezoelectric air pump according to an
embodiment of the present disclosure;
[0011] FIG. 2A is a schematic graph showing an output signal
driving the resonant piezoelectric air pump at 100% duty ratio
versus time;
[0012] FIG. 2B is a schematic graph showing an output air pressure
of driving the resonant piezoelectric air pump at 100% duty ratio
versus time;
[0013] FIG. 2C is a schematic graph showing an output signal of
driving the resonant piezoelectric air pump at a duty ratio
according to a first embodiment of the present disclosure versus
time;
[0014] FIG. 2D is a schematic graph showing an output air pressure
of driving the resonant piezoelectric air pump at the duty ratio
according to the first embodiment of the present disclosure versus
time;
[0015] FIG. 2E is a schematic graph showing an output signal of
driving the resonant piezoelectric air pump at a duty ratio
according to a second embodiment of the present disclosure versus
time;
[0016] FIG. 3A is a schematic exploded view illustrating a resonant
piezoelectric air pump according to an embodiment of the present
disclosure;
[0017] FIG. 3B is a schematic exploded view illustrating the
resonant piezoelectric air pump of FIG. 3A and taken along another
viewpoint;
[0018] FIG. 4A is a schematic exploded view illustrating the
piezoelectric actuator of FIG. 3A;
[0019] FIG. 4B is a schematic exploded view illustrating the
piezoelectric actuator of FIG. 3A and taken along another
viewpoint;
[0020] FIG. 4C is a schematic cross-sectional view illustrating the
piezoelectric actuator of FIG. 3A; and
[0021] FIGS. 5A to 5E schematically illustrate the actions of the
resonant piezoelectric air pump of FIG. 3A.
DETAILED DESCRIPTION OF THE PREFERRED EMBODIMENT
[0022] The present invention will now be described more
specifically with reference to the following embodiments. It is to
be noted that the following descriptions of preferred embodiments
of this invention are presented herein for purpose of illustration
and description only. It is not intended to be exhaustive or to be
limited to the precise form disclosed.
[0023] Please refer to FIGS. 1A and 1B. The present disclosure
provides an energy-saving control method of a resonant
piezoelectric air pump including at least one resonant
piezoelectric air pump 12, at least one control module 11, at least
one unit of time and at least one enable signal. The number of the
resonant piezoelectric air pump 12, the control module 11, the unit
of time and the enable signal is exemplified by one for each in the
following embodiments but not limited thereto. It is noted that
each of the resonant piezoelectric air pump 12, the control module
11, the unit of time and the enable signal can also be provided in
plural numbers.
[0024] The resonant piezoelectric air pump 12 is a resonance-type
piezoelectric air pump for air transfer. The resonant piezoelectric
air pump 12 can be applied in all kinds of electronic devices and
medical equipments, such as notebook computer, smart phone, smart
watch, tablet computer and so on, but not limited thereto. FIG 1A
is a schematic view illustrating a resonant piezoelectric air pump
and a control module according to an embodiment of the present
disclosure. As shown in FIG. 1A, the resonant piezoelectric air
pump 12 is electrically connected to the control module 11. The
control module 11 is configured to enable or disable the resonant
piezoelectric air pump 12, but not limited thereto. In this
embodiment, the control module 11 is connected to a power source
(not shown) for providing a driving power to the control module 11.
The control module 11 determines whether the driving power is
transmitted to the resonant piezoelectric air pump 12, so as to
control the on/off operations of the resonant piezoelectric air
pump 12.
[0025] Please refer to FIGS. 1A and 1B. FIG. 1B is a flowchart
illustrating an energy-saving control method of the resonant
piezoelectric air pump according to an embodiment of the present
disclosure. The energy-saving control method of the resonant
piezoelectric air pump achieves energy-saving and efficient air
transfer by adjusting the ratio of the enable signal of the
resonant piezoelectric air pump 12 in a unit of time (i.e., duty
ratio). As shown in FIGS. 1A and 1B, firstly, the resonant
piezoelectric air pump 12 and the control module 11 are provided
(Step S1). In this embodiment, the resonant piezoelectric air pump
12 is electrically connected to the control module 11, and the
control module 11 is configured to enable or disable the resonant
piezoelectric air pump 12, but not limited thereto. The detailed
structure of the resonant piezoelectric air pump 12 will be further
described as follows.
[0026] Then, at the beginning of a unit of time, the control module
11 transmits an enable signal to the resonant piezoelectric air
pump 12, and the resonant piezoelectric air pump 12 is driven to
transfer an amount of air in a process for air transfer (Step S2).
In this embodiment, the unit of time is a time interval between two
neighboring starting moments of the resonant piezoelectric air pump
12 when being enabled. In other words, from the moment when the
resonant piezoelectric air pump 12 is enabled to the moment when
the resonant piezoelectric air pump 12 is enabled again
subsequently, the time interval therebetween refers to a single
unit of time. Preferably but not exclusively, the unit of time has
a specific value, which may be varied according to the practical
requirements.
[0027] During the unit of time, the control module 11 adjusts the
duty ratio of the enable signal to control an operation relating to
enabling and disabling the resonant piezoelectric air pump 12 until
the unit of time ends (Step S3). Namely, the control module 11
adjusts the duty ratio of the enable signal, so as to enable or
disable the resonant piezoelectric air pump 12 within the unit of
time according to the enable signal. Finally, after the unit of
time finishes, the next unit of time begins, and Step S2 and Step
S3 are repeated in each unit of time subsequently until the process
for air transfer is completed (Step S4).
[0028] Please refer to FIGS. 2A and 2B. FIG. 2A is a schematic
graph showing an output signal of driving the resonant
piezoelectric air pump at 100% duty ratio versus time, and FIG. 2B
is a schematic graph showing an output air pressure of driving the
resonant piezoelectric air pump at 100% duty ratio versus time. As
shown in FIG. 2A, the resonant piezoelectric air pump 12 keeps
operating without interruption within the unit of time A. That is,
the resonant piezoelectric air pump 12 is driven at 100% duty
ratio. As shown in FIG. 2B, the resonant piezoelectric air pump 12
driven at 100% duty ratio reaches a specific output air pressure X
after five units of time A. The equation for calculating the power
consumption (i.e., calculating the shadow area in FIG. 2B) is
P.sub.100%=X*5A*100%. That is, the power consumption P.sub.100% is
equal to 5XA.
[0029] Please refer to FIGS. 2C and 2D. FIG. 2C is a schematic
graph showing an output signal of driving the resonant
piezoelectric air pump at a duty ratio according to a first
embodiment of the present disclosure versus time, and FIG. 2D is a
schematic graph showing an output air pressure of driving the
resonant piezoelectric air pump at the duty ratio according to the
first embodiment of the present disclosure versus time. As shown in
FIG. 2C, the resonant piezoelectric air pump 12 according to the
first embodiment of the present disclosure starts to operate at the
beginning of the unit of time A, and receives the enable signal
only during 10% of the unit of time A. That is, the duty ratio of
the enable signal for driving the resonant piezoelectric air pump
12 is 10%. However, the duty ratio of the enable signal is not
limited thereto, and it may be varied according to the practical
requirements. As shown in FIG. 2D, the resonant piezoelectric air
pump 12 driven at 10% duty ratio reaches the specific output air
pressure X after seven units of time A. The equation for
calculating the power consumption (i.e., calculating the shadow
area in FIG. 2D) is P.sub.10%=X*7A*10%. That is, the power
consumption P.sub.10% is equal to 0.7XA.
[0030] Please refer to FIGS. 2A, 2B, 2C and 2D. As described above,
the resonant piezoelectric air pump 12 driven at 100% duty ratio
allows the air pressure to accumulate and reach the specific output
air pressure X rapidly. However, the resonant piezoelectric air
pump 12 consumes a large amount of power (P.sub.100%=5XA) in terms
of 100% duty ratio. Compared with 100% duty ratio described above,
the resonant piezoelectric air pump 12 at 10% duty ratio takes a
longer time to reach the specific output air pressure X. However,
the power consumption of the resonant piezoelectric air pump 12
driven at 10% duty ratio (P.sub.10%=0.7XA) is much smaller than the
power consumption of the resonant piezoelectric air pump 12 driven
at 100% duty ratio (P.sub.100%=5XA). Moreover, during the
intermittent operation of the resonant piezoelectric air pump 12
driven at 10% duty ratio, unnecessary power consumption is reduced.
Also, the over-high temperature, damage to elements or even
reduction in service life of elements, all of which are caused by
the continuous operation of the resonant piezoelectric air pump 12,
can be avoided. Therefore, the effects of saving energy and
efficient air transfer are achieved.
[0031] Please refer to FIG. 2E. FIG. 2E is a schematic graph
showing an output signal of driving the resonant piezoelectric air
pump at a duty ratio according to a second embodiment of the
present disclosure versus time. The resonant piezoelectric air pump
12 according to the second embodiment of the present disclosure
starts to operate at the beginning of the unit of time A, and
receives the enable signal only during 50% of the unit of time A.
That is, the duty ratio of the enable signal for driving the
resonant piezoelectric air pump 12 is 50%. However, the duty ratio
of the enable signal is not limited thereto, and it may be varied
according to the practical requirements. In some embodiments, the
duty ratio of the enable signal for driving the resonant
piezoelectric air pump 12 can be any value between 0.1% and 99%,
but is not limited thereto.
[0032] Please refer to FIGS. 3A and 3B. FIG. 3A is a schematic
exploded view illustrating a resonant piezoelectric air pump
according to an embodiment of the present disclosure, and FIG. 3B
is a schematic exploded view illustrating the resonant
piezoelectric air pump of FIG. 3A and taken along another
viewpoint. The resonant piezoelectric air pump 12 includes an air
inlet plate 121, a resonance plate 122, a piezoelectric actuator
123, a first insulation plate 1241, a conducting plate 125 and a
second insulation plate 1242. The air inlet plate 121, the
resonance plate 122, the piezoelectric actuator 123, the first
insulation plate 1241, the conducting plate 125 and the second
insulation plate 1242 are stacked on each other sequentially to be
assembled together as the resonant piezoelectric air pump 12. In
this embodiment, preferably but not exclusively, the piezoelectric
actuator 123 is assembled from a suspension plate 1230 and a
piezoelectric ceramic plate 1233 and is disposed spatially
corresponding to the resonance plate 122. The air is fed from at
least one inlet 1210 of the air inlet plate 121 into the resonant
piezoelectric air pump 12 and passes through plural pressure
chambers by enabling the piezoelectric actuator 123, so as to
transfer an amount of air in a process for air transfer.
[0033] As shown in FIG. 3A, the air inlet plate 121 of the resonant
piezoelectric air pump 12 has at least one inlet 1210. Preferably
but not exclusively, the air inlet plate 121 has four inlets 1210,
and the number of the inlet 1210 may be varied according to the
practical requirements. In response to the action of the
atmospheric pressure, the air can be introduced into the resonant
piezoelectric air pump 12 through the at least one inlet 1210. As
shown in FIG. 3B, a central cavity 1211 and at least one
convergence channel 1212 are formed on a bottom surface of the air
inlet plate 121, and the bottom surface is opposite to the inlets
1210. In this embodiment, the number of the at least one
convergence channel 1212 is four, but not limited thereto. The four
convergence channels 1212 are disposed spatially corresponding to
the four inlets 1210 on the top surface of the air inlet plate 121
respectively, such that the air entered from the inlet 1210 would
be guided along the convergence channels 1212 to the central cavity
1211 and transferred downwardly. Consequently, the air can be
transferred by the resonant piezoelectric air pump 12. In this
embodiment, the at least one inlet 1210, the at least one
convergence channel 1212 and the central cavity 1211 of the air
inlet plate 121 are integrally formed from a single structure. The
central cavity 1211 is a convergence chamber for temporarily
storing the air. In some embodiments, the air inlet plate 131 may
be, for example, made of stainless steel. Moreover, the depth of
the convergence chamber defined by the central cavity 1211 is equal
to the depth of the at least one convergence channel 1212.
[0034] In this embodiment, the resonance plate 122 is made of a
flexible material, but not limited thereto. The resonance plate 122
includes a central aperture 1220 disposed corresponding to the
central cavity 1211 on the bottom surface of the air inlet plate
121 for allowing the air to be transferred downwardly. In other
embodiments, the resonance plate 122 may be made of copper.
[0035] Please refer to FIGS. 4A, 4B and 4C. FIG. 4A is a schematic
exploded view illustrating the piezoelectric actuator of FIG. 3A,
FIG. 4B is a schematic exploded view illustrating the piezoelectric
actuator of FIG. 3A and taken along another viewpoint, and FIG. 4C
is a schematic cross-sectional view illustrating the piezoelectric
actuator of FIG. 3A. The piezoelectric actuator 123 includes a
suspension plate 1230, an outer frame 1231, a plurality of brackets
1232 and a piezoelectric ceramic plate 1233. The piezoelectric
ceramic plate 1233 is attached on a bottom surface 1230b of the
suspension plate 1230. The plural brackets 1232 are connected
between the suspension plate 1230 and the outer frame 1231. While
in each bracket 1232, two ends of the bracket 1232 are connected to
the outer frame 1231, and another end of the bracket 1232 is
connected to the suspension plate 1230. A plurality of vacant
spaces 1235 are formed among the bracket 1232, the suspension plate
1230 and the outer frame 1231 so that the air can go through the
vacant spaces 1235. The disposing way and type of the suspension
plate 1230, the outer frame 1231 and the brackets 1232 and the
number of the brackets 1232 may be varied according to the
practical requirements. Moreover, a conducting pin 1234 is
protruded outwardly from the outer frame 1231 so as to be
electrically connected to an external circuit (not shown).
[0036] The suspension plate 1230 has a bulge 1230c that makes the
suspension plate 1230 a stepped structure. The bulge 1230c is
formed on a top surface 1230a of the suspension plate 1230. The
bulge 1230c is for example but not limited to a circular convex
structure. As shown in FIGS. 4A, 4B and 4C, a top surface of the
bulge 1230c of the suspension plate 1230 is coplanar with a top
surface 1231a of the outer frame 1231, while the top surface 1230a
of the suspension plate 1230 is coplanar with a top surface 1232a
of the bracket 1232. Moreover, there is a drop of specified amount
from the bulge 1230c of the suspension plate 1230 (or the top
surface 1231a of the outer frame 1231) to the top surface 1230a of
the suspension plate 1230 (or the top surface 1232a of the bracket
1232). With regard to the bottom surface 1230b of the suspension
plate 1230, as shown in FIGS. 4B and 4C, the bottom surface 1230b,
a bottom surface 1231b of the outer frame 1231 and a bottom surface
1232b of the bracket 1232 are coplanar with each other. The
piezoelectric ceramic plate 1233 is attached on the bottom surface
1230b of the suspension plate 1230. In some embodiments, the
suspension plate 1230, the plural brackets 1232 and the outer frame
1231 are integrally formed from a metal plate (e.g., a stainless
steel plate).
[0037] Please refer to FIGS. 3A and 3B. The resonant piezoelectric
air pump 12 has the first insulation plate 1241, the conducting
plate 125 and the second insulation plate 1242, which are stacked
on each other sequentially and located under the piezoelectric
actuator 123. The profiles of the first insulation plate 1241, the
conducting plate 125 and the second insulation plate 1242
substantially match the profile of the outer frame 1231 of the
piezoelectric actuator 123. The first insulation plate 1241 and the
second insulation plate 1242 are made of insulating materials (e.g.
plastic material) for providing insulating efficacy. The conducting
plate 125 is made of an electrically conductive material (e.g. a
metallic material) for providing electrically conducting efficacy.
Moreover, the conducting plate 125 has a conducting pin 1251 so as
to be electrically connected to an external circuit (not
shown).
[0038] Please refer to FIGS. 3A, 3B, 5A, 5B, 5C, 5D and 5E. FIGS.
5A to 5E schematically illustrate the actions of the resonant
piezoelectric air pump of FIG. 3A. As shown in FIG. 5A, the air
inlet plate 121, the resonance plate 122, the piezoelectric
actuator 123, the first insulation plate 1241, the conducting plate
125 and the second insulation plate 1242 of the resonant
piezoelectric air pump 12 are stacked on each other sequentially.
Moreover, there is a gap g0 between the resonance plate 122 and the
outer frame 1231 of the piezoelectric actuator 123, which is formed
and maintained by a filler (e.g. a conductive adhesive) inserted
therein in this embodiment. The gap g0 ensures the proper distance
between the resonance plate 122 and the bulge 1230c of the
suspension plate 1230 of the piezoelectric actuator 123, so that
the air can be transferred quickly, the contact interference is
reduced and the generated noise is largely reduced. In some
embodiments, the height of the outer frame 1231 of the
piezoelectric actuator 123 is increased, so that the gap is formed
between the resonance plate 122 and the piezoelectric actuator
123.
[0039] As shown in FIGS. 5A to 5E, after the air inlet plate 121,
the resonance plate 122 and the piezoelectric actuator 123 are
combined together, the convergence chamber for converging the air
is further defined by the central aperture 1220 of the resonance
plate 122 and the central cavity 1211 of the air inlet plate 121
collaboratively. Moreover, a first chamber 1221 is formed between
the resonance plate 122 and the piezoelectric actuator 123 for
temporarily storing the air. Through the central aperture 1220 of
the resonance plate 122, the first chamber 1221 is in communication
with the convergence chamber formed within the central cavity 1211
on the bottom surface of the air inlet plate 121. The air in the
peripheral regions of the first chamber 1221 can be discharged
through the vacant space 1235 between the brackets 1232 of the
piezoelectric actuator 123.
[0040] In this embodiment, when the resonant piezoelectric air pump
12 is enabled, the piezoelectric actuator 123 vibrates along a
vertical direction in a reciprocating manner by using the bracket
1232 as a fulcrum. As shown in FIG. 5B, when the piezoelectric
actuator 123 vibrates downwardly in response to the applied
voltage, the air is fed from the at least one inlet 1210 of the air
inlet plate 121 and converged to the central cavity 1211 along the
at least one convergence channel 1212 on the bottom surface of the
air inlet plate 121. Then, the air is transferred through the
central aperture 1220 of the resonance plate 122 which is disposed
corresponding to the central cavity 1211, and introduced downwardly
into the first chamber 1221. Afterwards, being driven by the
vibration of the piezoelectric actuator 123, the resonance plate
122 is in resonance with the piezoelectric actuator 123 and thus
the resonance plate 122 also vibrates vertically in a reciprocating
manner.
[0041] As shown in FIG. 5C, when the resonance plate 122 vibrates
downwardly, the resonance plate 122 moves down to contact and
attach on the bulge 1230c of the suspension plate 1230 of the
piezoelectric actuator 123. Owing to the deformation of the
resonance plate 122 described above, a middle communication space
of the first chamber 1221 is closed, and the volume of the first
chamber 1221 is compressed. Under this circumstance, the pressure
gradient occurs to push the air in the first chamber 1221 moving
toward peripheral regions of the first chamber 1221 and flowing
downwardly through the vacant space 1235 of the piezoelectric
actuator 123.
[0042] FIG. 5D shows that the resonance plate 122 returns to its
original position. The piezoelectric actuator 123 driven by the
applied voltage vibrates upwardly with a displacement d. In that
case, the volume of the first chamber 1221 is continuously
compressed to generate the pressure gradient which makes the air in
the first chamber 1221 continuously pushed toward peripheral
regions. Meanwhile, the external ambient air is continuously fed
into the at least one inlet 1210 of the air inlet plate 121, and
transferred to the convergence chamber formed within the central
cavity 1211.
[0043] Then, as shown FIG. 5E, influenced by the upward motion of
the piezoelectric actuator 123, the resonance plate 122 moves
upwardly in resonance with the piezoelectric actuator 123.
Consequently, the air is introduced into the first chamber 1221
through the central aperture 1220 of the resonance plate 122, moves
downwardly and discharged from the resonant piezoelectric air pump
12 through the vacant space 1235 between the brackets 1232 of the
piezoelectric actuator 123. Consequently, a pressure gradient is
generated in the designed fluid channels of the resonant
piezoelectric air pump 12 to facilitate the air to flow at a high
speed. Moreover, since there is an impedance difference between the
feeding direction and the exiting direction, the air can be
transferred from the inlet side to the outlet side. Even if a gas
pressure exists at the outlet side, the resonant piezoelectric air
pump 12 still has the capability of pushing the air to the fluid
channels as well as achieving the silent efficacy. In some
embodiments, the vibration frequency of the vertical reciprocation
of the resonance plate 122 is equal to the vibration frequency of
the piezoelectric actuator 123. That is, the resonance plate 122
and the piezoelectric actuator 123 move upwardly or downwardly at
the same time. In fact, the vibration frequencies thereof can be
varied according to the practical requirements, but not limited to
the actions shown in the embodiments of the present disclosure.
[0044] In addition, the unit of time described above is for example
but not limited to 1 second. Moreover, the frequency of the enable
signal is between 20 KHz and 28 KHz. The frequency of the enable
signal is exemplified by 28 KHz and further described below. When
the duty ratio is 100%, the enable signal drives the piezoelectric
actuator 123 to operate 28000 times per second. When the duty ratio
is 10%, the enable signal drives the piezoelectric actuator 123 to
operate 2800 times per second. When the duty ratio is 0.1%, the
enable signal drives the piezoelectric actuator 123 to operate 28
times per second. In other embodiments, the unit of time may be 0.5
seconds but not limited thereto.
[0045] From the above descriptions, the present disclosure provides
an energy-saving control method of a resonant piezoelectric air
pump. By the control module, the duty ratio of the enable signal
for driving the resonant piezoelectric air pump is adjusted, thus
the power consumption is reduced. Moreover, the over-high
temperature, damage to elements or even reduction in service life
of elements, all of which are caused by the continuous operation of
the resonant piezoelectric air pump, can be avoided. Therefore, the
effects of saving energy and efficient air transfer are
achieved.
[0046] While the disclosure has been described in terms of what is
presently considered to be the most practical and preferred
embodiments, it is to be understood that the invention needs not be
limited to the disclosed embodiment. On the contrary, it is
intended to cover various modifications and similar arrangements
included within the spirit and scope of the appended claims which
are to be accorded with the broadest interpretation so as to
encompass all such modifications and similar structures.
* * * * *