U.S. patent application number 16/073899 was filed with the patent office on 2019-02-07 for thermally treated metallic materials and related methods.
The applicant listed for this patent is CORNING INCORPORATED. Invention is credited to Dana Craig Bookbinder, Theresa Chang, Jeffrey John Domey, Peter Joseph Lezzi, Richard Orr Maschmeyer, John Christopher Thomas, Kevin Lee Wasson.
Application Number | 20190040491 16/073899 |
Document ID | / |
Family ID | 58213322 |
Filed Date | 2019-02-07 |
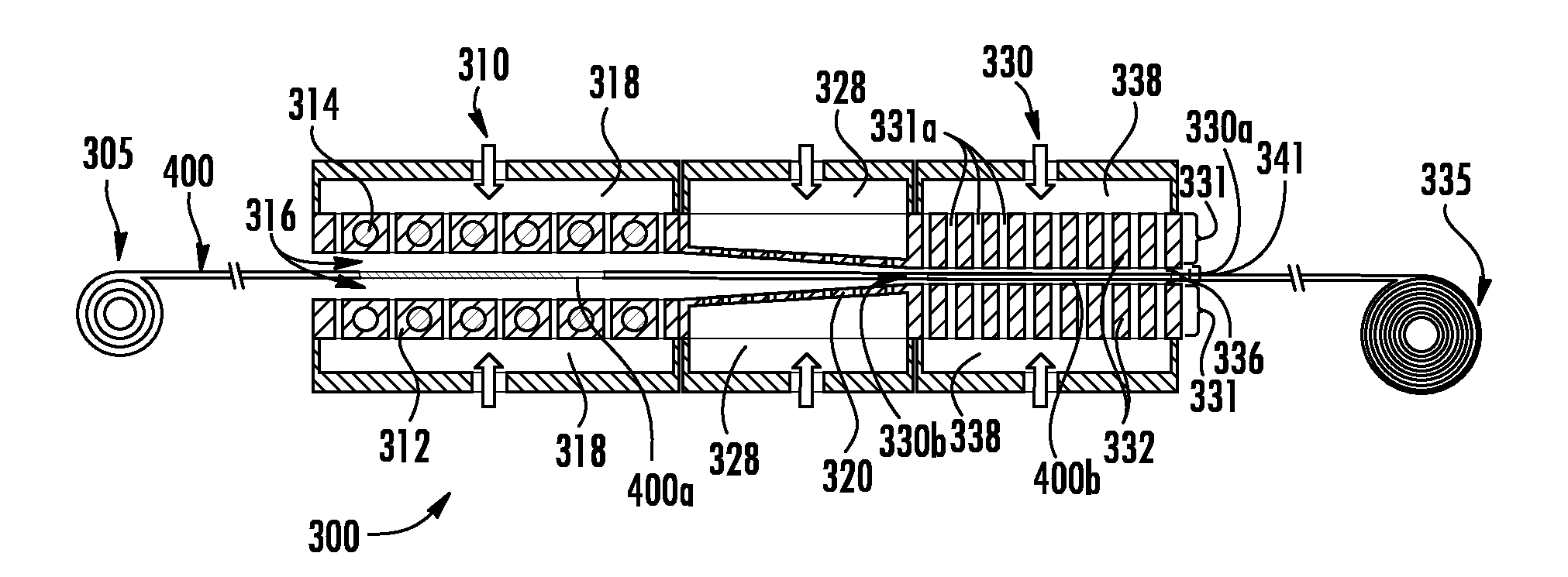
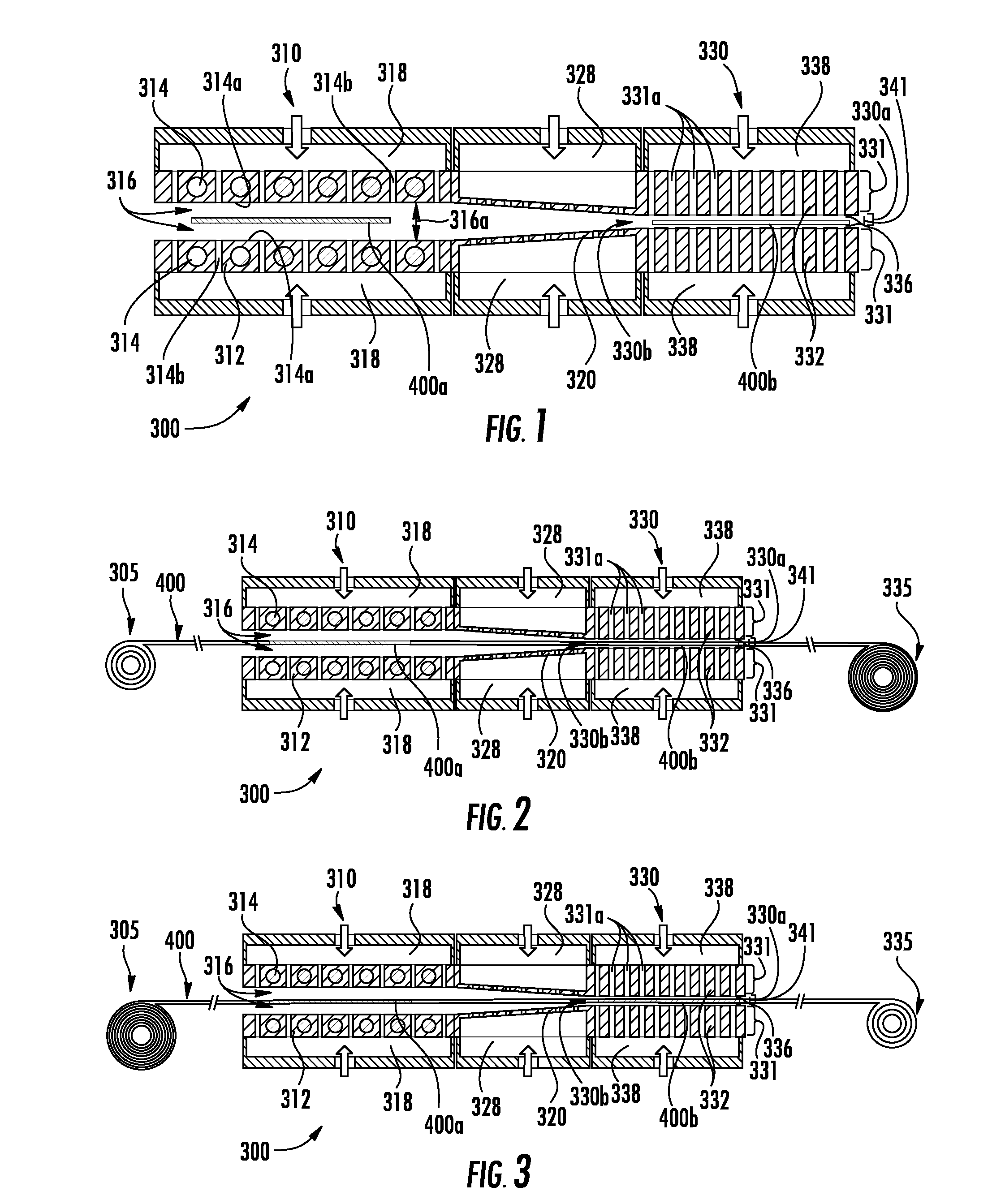
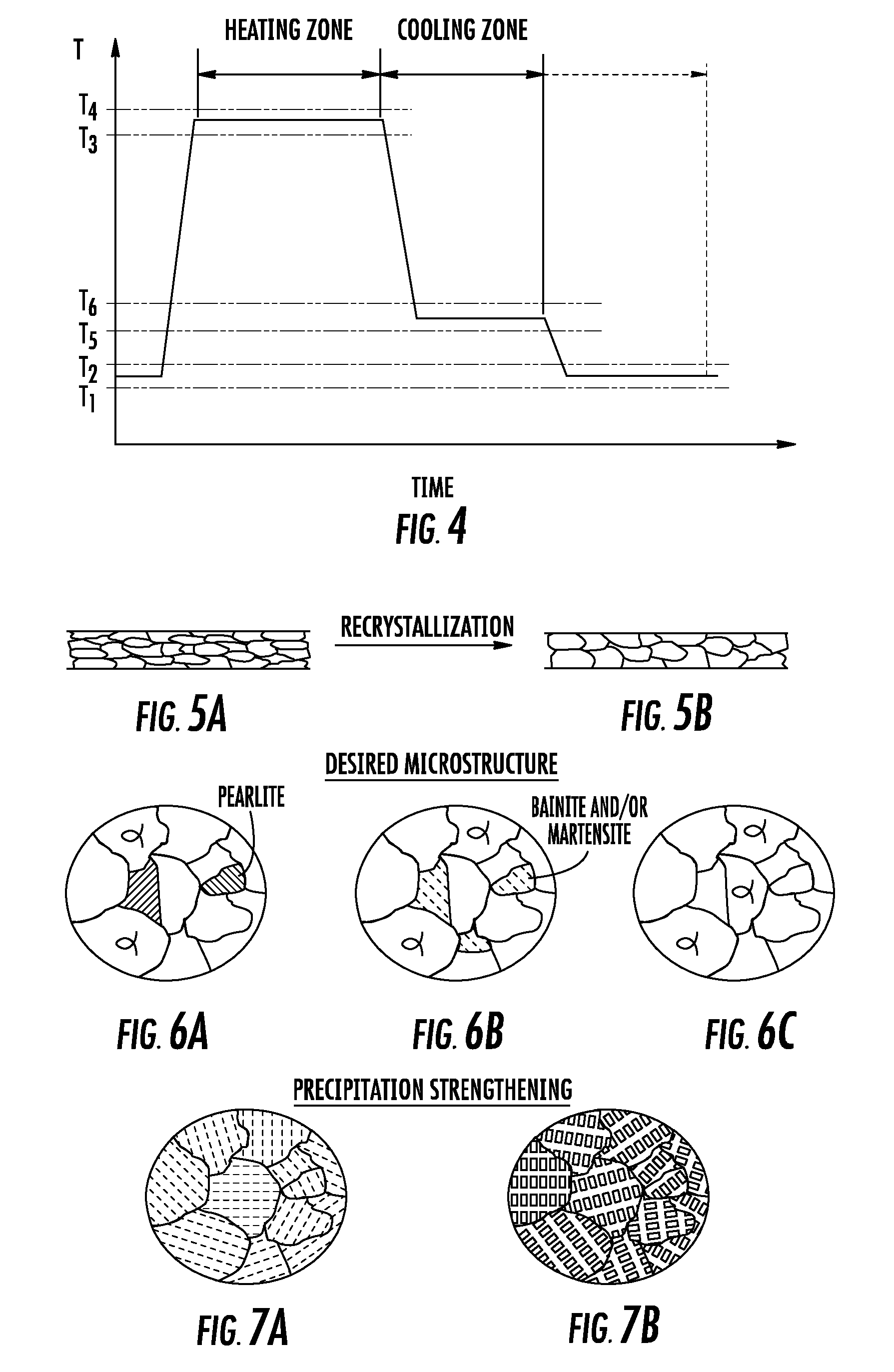
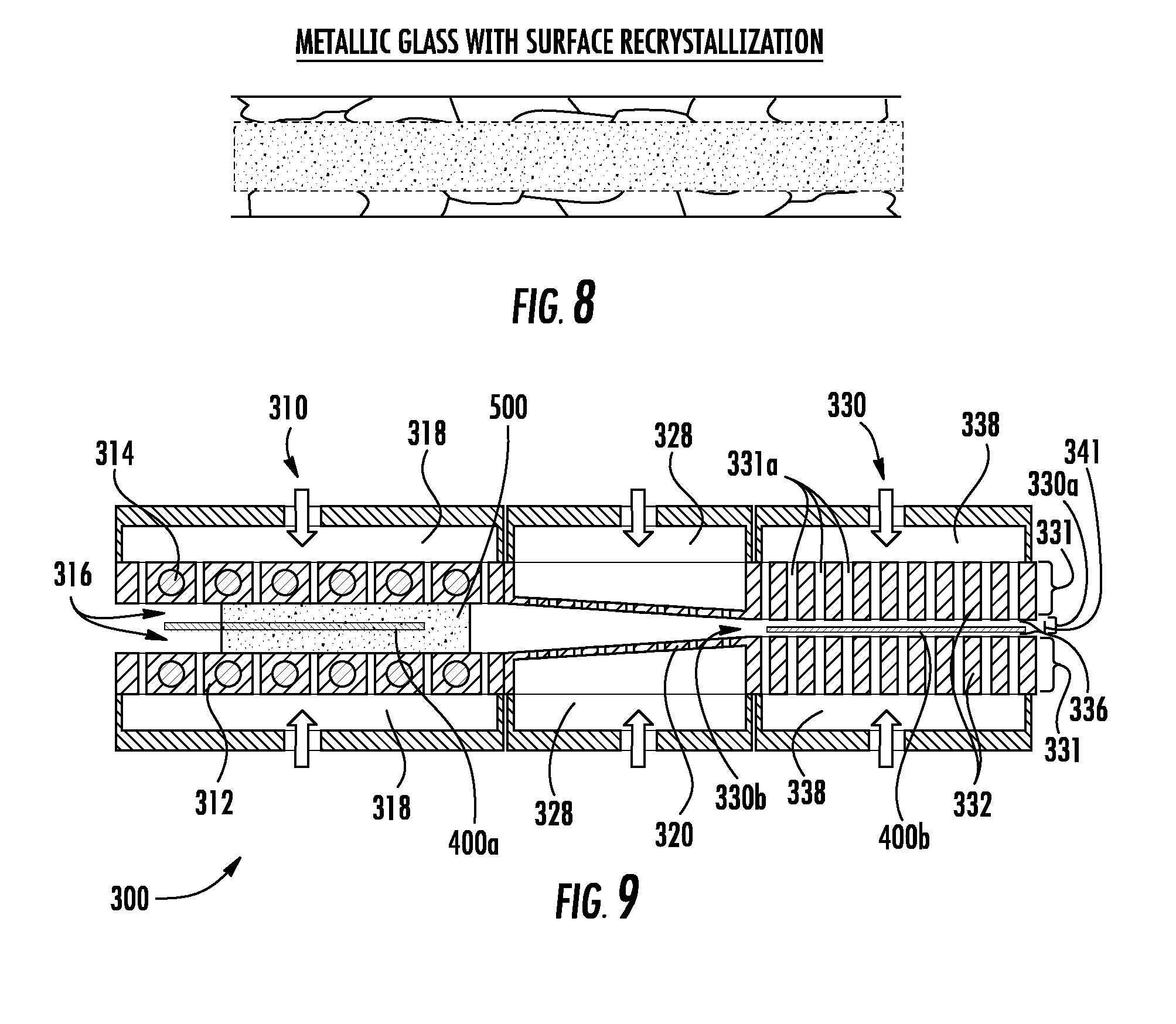
United States Patent
Application |
20190040491 |
Kind Code |
A1 |
Bookbinder; Dana Craig ; et
al. |
February 7, 2019 |
THERMALLY TREATED METALLIC MATERIALS AND RELATED METHODS
Abstract
A thermally treated metal sheet or article as well as processes
and systems for making the thermally treated sheet or article is
provided. The process comprises heating and/or cooling the metal
sheet by non contact thermal conduction for sufficiently long to
provide a desired microstructure and mechanical properties. The
process results in thermally treated metal sheets.
Inventors: |
Bookbinder; Dana Craig;
(Corning, NY) ; Chang; Theresa; (Painted Post,
NY) ; Domey; Jeffrey John; (Elmira, NY) ;
Lezzi; Peter Joseph; (Corning, NY) ; Maschmeyer;
Richard Orr; (Corning, NY) ; Thomas; John
Christopher; (Elmira, NY) ; Wasson; Kevin Lee;
(Elmira, NY) |
|
Applicant: |
Name |
City |
State |
Country |
Type |
CORNING INCORPORATED |
Corning |
NY |
US |
|
|
Family ID: |
58213322 |
Appl. No.: |
16/073899 |
Filed: |
January 27, 2017 |
PCT Filed: |
January 27, 2017 |
PCT NO: |
PCT/US2017/015283 |
371 Date: |
July 30, 2018 |
Related U.S. Patent Documents
|
|
|
|
|
|
Application
Number |
Filing Date |
Patent Number |
|
|
62288695 |
Jan 29, 2016 |
|
|
|
Current U.S.
Class: |
1/1 |
Current CPC
Class: |
C21D 1/613 20130101;
C22C 38/002 20130101; C22F 1/043 20130101; C22C 21/02 20130101;
C22F 1/10 20130101; C21D 1/53 20130101; C21D 9/567 20130101; C21D
2211/002 20130101; C22C 19/07 20130101; C22C 38/44 20130101; C21D
2201/03 20130101; C22F 1/004 20130101; C22C 38/02 20130101; C22F
1/002 20130101; C22F 1/08 20130101; C21D 2211/008 20130101; C22C
38/06 20130101; C22C 19/055 20130101; C22C 38/50 20130101; C21D
9/63 20130101; C22C 38/001 20130101; C22C 38/04 20130101 |
International
Class: |
C21D 9/63 20060101
C21D009/63; C21D 9/567 20060101 C21D009/567; C21D 1/613 20060101
C21D001/613; C21D 1/53 20060101 C21D001/53; C22F 1/043 20060101
C22F001/043; C22F 1/08 20060101 C22F001/08; C22F 1/10 20060101
C22F001/10; C22F 1/00 20060101 C22F001/00 |
Claims
1. A process for thermally treating metallic materials comprising:
heating and/or cooling a metallic article, the article supported
with gas during the heating and/or cooling; wherein the article is
heated by transferring thermal energy from a heat source to the
article across a heating gap between the heat source and the
article such that more than 20% of the thermal energy leaving the
heat source crosses the heating gap and is received by the article;
wherein the article is cooled by transferring thermal energy from
the article to a heat sink across a cooling gap between the article
and the heat sink such that more than 20% of the thermal energy
leaving the article crosses the cooling gap and is received by the
heat sink.
2. The process of claim 1, wherein more than 50% of the thermal
energy leaving the heat source or the article crosses the heating
gap or the cooling gap, respectively, and is received by the
article or the heat sink, respectively.
3. The process of claim 2, wherein the heating gap or the cooling
gap has an average thickness between an outer surface of the heat
source and an adjacent surface of the article or the adjacent
surface of the article and an outer surface of the heat sink that
is less than about 10 mm, 5 mm, 2 mm 1 mm, 800 .mu.m, 600 .mu.m,
400 .mu.m, or 200 .mu.m.
4. The process of claim 3, wherein a heat transfer rate from the
heat source to the article during heating or from the article to
the heat sink during cooling is greater than about 50 kW/m.sup.2,
100 kW/m.sup.2, 150 kW/m.sup.2, 200 kW/m.sup.2, 250 kW/m.sup.2, 300
kW/m.sup.2, 350 kW/m.sup.2, 450 kW/m.sup.2, 550 kW/m.sup.2, 650
kW/m.sup.2, 750 kW/m.sup.2, 1000 kW/m.sup.2, or 1200 kW/m.sup.2 for
the area of the outer surface of the heat source or for the area of
the outer surface of the article, respectively.
5. The process of claim 4, wherein the article is a sheet having a
length, a width and a thickness, wherein the thickness is greater
than about 0.1 mm and less than 2 mm, and at least one of the width
and the length are greater than 5 times the thickness.
6. The process of claim 4, wherein the heating gap or cooling gap
is a gas gap with a gap area, wherein a total flow rate of gas into
the gas gap is greater than zero and less than 2 k/gCp per square
meter of gap area, where k is the thermal conductivity of a gas
within the gas gap evaluated in the direction of heat conduction, g
is the distance between the heated article and the heat sink
surface, and Cp is the specific heat capacity of the gas within the
gas gap.
7. The process of claim 4, wherein the metallic material is
selected from the group consisting of a polycrystalline metallic
material, a single crystal metallic material and a metallic glass
material.
8. The process of claim 4, wherein the metallic material is a
polycrystalline metallic material selected from the group
consisting of a pure metal and an alloy.
9. The process of claim 4 any of claims 1 8, wherein the
polycrystalline metallic material is the alloy selected from the
group consisting of an aluminum alloy, a copper alloy, an iron
alloy and a nickel alloy.
10. The process of claim 9, wherein the alloy is an aluminum alloy
that is heated by the heat source and heating of the aluminum alloy
results in precipitation strengthening of the article.
11. The process of claim 9, wherein the metallic material is a cold
worked aluminum alloy that is heated by the heat source, wherein a
microstructure of the heated cold work aluminum alloy undergoes
recrystallization.
12. The process of claim 9, wherein the metallic material is a
copper alloy that is heated by the heat source and heating of the
copper alloy results in precipitation strengthening of the
article.
13. The process of claim 9, wherein the metallic material is a cold
worked copper alloy that is heated by the heat source, wherein a
microstructure of the heated cold work copper alloy undergoes
recrystallization.
14. The process of claim 9, wherein the metallic material is a cold
worked iron alloy that is heated by the heat source, wherein a
microstructure of the heated cold worked iron alloy undergoes
recrystallization.
15. The process of claim 9, wherein the metallic material is an
iron alloy that is heated by the heat source to an annealing
temperature and cooled by the heat sink at a cooling rate that
provides a microstructure with a desired amount of pearlite.
16. The process of claim 9, wherein the metallic material is an
iron alloy that is heated by the heat source to an appropriate
austenizing temperature for the iron alloy and cooled by the heat
sink at a cooling rate that provides a microstructure with a
desired amount of bainite and/or martensite.
17. The process of claim 16, wherein the cooling rate provides a
microstructure with no pearlite.
18. The process of claim 9, wherein the metallic material is a cold
worked nickel alloy that is heated by the heat source for
recrystallization of the article and cooled by the heat sink for
controlled grain growth of the article after recrystallization.
19. The process of claim 9, wherein the metallic material is a
nickel alloy that is heated by the heat source to an appropriate
aging treatment temperature that provides precipitation
strengthening of the article via precipitation of at least one of
gamma prime precipitates, carbide precipitates, nitride
precipitates and carbonitride precipitates.
20. The process of claim 9, wherein the metallic material is a
metallic glass that is heated such that a surface region of the
article is recrystallized and an inner region is not
recrystallized.
21. The process of claim 1, wherein the heating occurs in a heating
zone configured to chemically alter a surface region of the
article.
22. The process of claim 21, wherein the heating zone is configured
to provide chromizing, carburizing, boriding, nitriding,
aluminizing, silicon izing, and combinations thereof, to the
surface region of the article.
23. A process for thermally treating metallic materials comprising:
heating and/or cooling a metallic material article, the article
supported with gas during the heating and/or cooling; wherein the
article is heated by transferring thermal energy from a heat source
to the article across a heating gap between the heat source and the
article such that at least 50% of the thermal energy leaving the
heat source crosses the heating gap and is received by the article;
wherein the article is cooled by transferring thermal energy from
the article to a heat sink across a cooling gap between the article
and the heat sink such that at least 50% of the thermal energy
leaving the article crosses the cooling gap and is received by the
heat sink; wherein the heating gap or the cooling gap has an
average thickness between an outer surface of the heat source and
an adjacent surface of the article or the article and an outer
surface of the heat sink that is less than about 10 mm; wherein a
heat transfer rate from the heat source to the article during
heating or from the article to the heat sink during cooling is
greater than about 1000 kW/m.sup.2.
24. A thermally treated metallic material article comprising: an
article made from a metallic material selected from the group
consisting of an Al-base alloy, a Cu-base alloy, a Ni-base alloy,
an Fe-base alloy and a Ti alloy; the metallic material article
having a microstructure as a result of heating and/or cooling the
metallic material while the metallic material article is supported
with a gas during the heating and/or cooling; the metallic material
article heated by transferring thermal energy from a heat source to
the metallic material article across a heating gap between the heat
source and the metallic material article such that more than 20% of
the thermal energy leaving the heat source crosses the heating gap
and is received by the metallic material article; the metallic
material article cooled by transferring thermal energy from the
metallic material article to a heat sink across a cooling gap
between the metallic material article and the heat sink such that
more than 20% of the thermal energy leaving the metallic material
article crosses the cooling gap and is received by the heat sink;
the microstructure selected from the group consisting of a
solid-solution strengthened microstructure, a precipitation
strengthened microstructure, a ferrite plus pearlite
microstructure, a ferrite plus bainite and/or martensite
microstructure, a ferrite plus retained austenite microstructure
and a ferrite with no pearlite microstructure.
25. The thermally treated metallic material article of claim 24,
wherein the article is made from an Fe-base alloy with a ferrite
plus martensite microstructure with less than 6 vol % bainite and
has a tensile strength of at least 590 MPa, a yield strength of at
least 330 MPa and a total elongation to failure of at least
18%.
26. The thermally treated metallic material article of claim 24,
wherein the article is made from an Al-base alloy with an age
hardened microstructure and an average room temperature tensile
strength of 45,000 psi, an average room temperature yield strength
of 40,000 psi, and an average room temperature elongation to
failure of 12%.
27. The thermally treated metallic material article of claim 24,
wherein the article is made from an Ni-base alloy with an age
hardened microstructure and has an average room temperature tensile
strength of 1335 MPa, an average room temperature yield strength of
910 MPa, and an average room temperature elongation to failure of
26.6%.
Description
[0001] This application claims the benefit of priority under 35
U.S.C. .sctn. 119 of U.S. Provisional Application Ser. No.
62/288,695 filed on Jan. 29, 2016, the content of which is relied
upon and incorporated herein by reference in its entirety.
BACKGROUND
Field
[0002] The disclosure relates generally to thermally treated
metallic materials and to related methods and systems for the
thermal treatment of metals and alloys.
Technical Background
[0003] In the thermal treatment of metallic materials such as pure
metals, alloys, intermetallics and metallic glasses, a variety of
thermal and/or thermomechanical processes are used to provide
desired combinations of microstructure, mechanical properties,
physical properties and/or surface finishes. Particularly, metallic
materials can be thermally treated and/or thermomechanically
treated to produce recrystallization of the metallic material's
microstructure, stress relief of a metallic material article and/or
desired second phase morphology within a host matrix. Such thermal
treatments typically include heating of a metallic material article
to an elevated temperature, holding the metallic material article
at the elevated temperature for a desired length of time and then
cooling the metallic material article. In some processes, a
controlled heating rate employed to heat the metallic component
article to the elevated temperature and/or cooling a controlled
cooling rate to cool the metallic material article is desired.
[0004] Current thermal treatment of metallic material articles,
particularly in commercial thermal treatment processers, use large
heating furnaces, long cooling (runout) tables which require large
amounts energy to provide sufficient heat and cooling liquid to
provide sufficient cooling rates. In addition, rapidly quenching
metallic material articles from the elevated temperature to a
desired lower temperature can be a problematic when attempting to
move metallic material articles from a heated furnace (heating
zone) to a quench station (cooling zone). Accordingly, apparatuses
and methods that provide thermal treatments to metallic material
articles while reducing energy consumption and increasing ease of
movement between heating zones and cooling zones would be
desirable.
SUMMARY
[0005] This disclosure relates, in part, to thermally treated
metallic material articles, and to methods, processes, and systems
that thermally treat metallic material articles. In various
embodiments, the process and method of the current disclosure heats
and/or cools an article formed from a metallic material (article),
the article supported with gas during the heating and/or cooling.
The article is heated by transferring thermal energy from a heat
source to the article across a heating gap between the heat source
and the article such that more than 20% of the thermal energy
leaving the heat source crosses the heating gap and is received by
the article. The article is heated to and held at a desired
elevated temperature for a desired amount of time. Thereafter, the
article is allowed to cool. In embodiments, the article is allowed
to air cool. In other embodiments, the article is cooled by
transferring thermal energy from the article to a heat sink across
a cooling gap between the article and the heat sink such that more
than 20% of the thermal energy leaving the heated article crosses
the cooling gap and is received by the heat sink. In embodiments,
the article is supported with gas during heating and more than half
of the thermal energy leaving the heat source crosses the heating
gap is received by the article. The article can also be supported
with gas during cooling and more than half of the thermal energy
leaving the article crosses the cooling gap is received by the heat
sink. The heating gap or the cooling gap can have an average
thickness between an outer surface of the heat source and the
article or the article and an outer surface of the heat sink
surface, respectively, that is less than 10 millimeters (mm), 5 mm,
2 mm 1 mm, 800 micrometers (.mu.m), 600 .mu.m, 400 .mu.m, or 200
.mu.m. In embodiments, a heat transfer rate from the heat source to
the article during heating, or from the article to the heat sink
during cooling, is greater than 50 kilowatts per square meter
(kW/m.sup.2), greater than 100 kW/m.sup.2, greater than 150
kW/m.sup.2, greater than 200 kW/m.sup.2, greater than 250
kW/m.sup.2, greater than 300 kW/m.sup.2, greater than 350
kW/m.sup.2, greater than 450 kW/m.sup.2, greater than 550
kW/m.sup.2, greater than 650 kW/m.sup.2, greater than 750
kW/m.sup.2, greater than 1000 kW/m.sup.2, or greater than 1200
kW/m.sup.2 for the area of the outer surface of the heat source, or
for the area of the outer surface of the article, respectively.
[0006] The article can be in the form of a sheet, a cylindrical
rod, a hexagonal rod, and the like. When the article is in the form
of a sheet, the article has a length, a width, and a thickness. In
embodiments, the thickness of the sheet is less than 3 mm, less
than 2 mm, less than 1.5 mm, less than 1.0 mm, less than 0.5 mm,
less than about 0.25 mm, less than about 0.1 mm, less than 0.08 mm,
less than 0.06 mm, or less than 0.04 mm. At least one of the width
and the length are greater than five times the thickness of the
sheet. When the article is in the form of a rod, the rod has an
average diameter and a length. In embodiments, the diameter of the
rod is less than 10 mm, less than 9 mm, less than 8 mm, less than 7
mm, less than 6 mm, less than 5 mm, less than 4 mm, less than 3 mm,
less than 2 mm, less than 1 mm, less than 0.8 mm, less than 0.6 mm,
less than 0.4 mm, less than 0.2 mm or less than 0.1 mm.
[0007] The heating gap or cooling gap can be a gas gap with a gap
area and a total mass flow rate of gas into the gas gap is greater
than 0 and less than 2 k/gCp per square meter of gap area where k
is the thermal conductivity of a gas within the gas gap evaluated
in the direction of heat conduction, g is the distance between the
heated article and the heat sink surface, and Cp is the specific
heat capacity of the gas within the gas gap.
[0008] The metallic material can be a pure metal or an alloy and
the pure metal or alloy can be polycrystalline, single crystal, or
metallic glass. The pure metal can be a commercial pure metal such
as commercial pure aluminum (Al), copper (Cu), chromium (Cr),
nickel (Ni), niobium (Nb), iron (Fe), magnesium (Mg), molybdenum
(Mo), silver (Ag), tantalum (Ta), titanium (Ti), tungsten (W)
zirconium (Zr), gold (Au), platinum (Pt) or any other commercially
available pure metal. The alloy can be an Al-base alloy, a Cu-base
alloy, a Cr-base alloy, a Ni-base alloy, a Nb-base alloy, an
Fe-base alloy, a Mg-base alloy, a Mo-base alloy, a Ag-base alloy, a
Ta-base alloy, a Ti-base alloy, a W-base alloy, a Zr-base alloy, a
Au-base alloy or another known alloy.
[0009] In embodiments, the article is made from an Al-base alloy
and the Al-base alloy article is solution heat treated, quenched
and aged in order to provide a precipitation strengthened (also
known as precipitation hardened or age hardened) article with
reduced residual stresses. In addition, the Al-base alloy article
can be subjected cold working and then heated by the heat source
such that recrystallization of the cold worked Al-base alloy
article microstructure occurs. The recrystallized Al-base alloy
article can be controllably cooled to prevent undesired grain
growth of the recrystallized Al-base alloy article
microstructure.
[0010] In embodiments, the article is made from a Cu-base alloy
article and the Cu-base alloy article is solution heat treated,
quenched and aged in order to provide a precipitation strengthened
article with reduced residual stresses. In addition, the Cu-base
alloy article can be subjected cold working and then heated by the
heat source such that recrystallization of the cold worked Cu-base
alloy article microstructure occurs. The recrystallized Cu-base
alloy article can be controllably cooled to prevent undesired grain
growth of the recrystallized Cu-base alloy article
microstructure.
[0011] In embodiments, the article is made from an Fe-base alloy
and the Fe-base alloy article is solution annealed such that the
microstructure of the Fe-base alloy is completely austenite and
then cooled to provide a microstructure with ferrite and a desired
amount of pearlite, including no pearlite. In other embodiments,
the Fe-base alloy article is solution annealed such that the
microstructure of the Fe-base alloy is completely austenite and
then cooled to provide a microstructure with ferrite and a desired
amount of bainite and/or martensite. The solution annealed Fe-base
alloy article can be cooled such retained austenite can be present
in the Fe-base alloy article's microstructure. The Fe-base alloy
article can be subjected cold working and then heated by the heat
source such that recrystallization of the cold worked Fe-base alloy
article microstructure occurs. The recrystallized Fe-base alloy
article can be controllably cooled to prevent undesired grain
growth of the recrystallized Fe-base alloy article
microstructure.
[0012] In embodiments, the article is made from a Ni-base alloy and
the Ni-base alloy article is solution annealed such that the
microstructure of the Ni-base alloy is completely austenitic (face
centered cubic--FCC) and then cooled to provide a microstructure
with desired second phase precipitates. Such second phases
precipitates can include Ni.sub.3Al (gamma prime) precipitates,
carbide precipitates, nitride precipitates and/or carbonitride
precipitates. The Ni-base alloy article can be subjected cold
working and then heated by the heat source such that
recrystallization of the cold worked Ni-base alloy article
microstructure occurs. The recrystallized Ni-base alloy article can
be controllably cooled to prevent undesired grain growth of the
recrystallized Ni-base alloy article microstructure. The article
can be made from other types of alloys and heat treated and cooled
to provide a desired article microstructure. It should be
appreciated that the microstructure of an alloy article is closely
linked to the article's mechanical properties. Accordingly, an
alloy article can be heated treated and cooled to provide a desired
combination of strength and ductility.
[0013] The process can include heating of the metallic material
article in a heating zone configured to chemically alter a surface
region of the article. For example, the heating zone can include
chemical vapor deposition (CVD) equipment and/or plasma deposition
equipment that can chemically alter the surface region of the
article. The surface region of the article can be chemically
altered such as by coating with, impregnation and/or diffusion of
elements such as nitrogen (nitriding), boron (boriding), carbon
(carburizing), and combinations thereof.
[0014] Additional features and advantages will be set forth in the
detailed description that follows, and, in part, will be readily
apparent to those skilled in the art from the description or
recognized by practicing the embodiments as described in the
written description and claims hereof, as well as the appended
drawings.
[0015] It is to be understood that both the foregoing general
description and the following detailed description are merely
exemplary, and are intended to provide an overview or framework to
understand the nature and character of the claims.
[0016] The accompanying drawings are included to provide a further
understanding and are incorporated in and constitute a part of this
specification. The drawings illustrate one or more embodiments, and
together with the description serve to explain principles and the
operation of the various embodiments.
BRIEF DESCRIPTION OF THE DRAWINGS
[0017] FIG. 1 is a diagrammatic cross-section of a thin metallic
material sheet being cooled by conduction more than by convection
using an inventive thermal treatment system according to an
exemplary embodiment;
[0018] FIG. 2 is a diagrammatic cross-sectional diagram of metallic
material thin sheet being heated and cooled by conduction more than
by convection in a continuous manner using an inventive thermal
treatment system according to an exemplary embodiment;
[0019] FIG. 3 is a diagrammatic cross-sectional diagram of metallic
material thin sheet being heated and cooled by conduction more than
by convection in a continuous manner according to an exemplary
embodiment;
[0020] FIG. 4 is a graph showing temperature versus time for
heating and cooling of metallic material thin sheet according to
embodiments disclosed in the present disclosure;
[0021] FIG. 5A is a schematic cross-section of a cold worked
metallic material thin sheet before recrystallization;
[0022] FIG. 5B is a schematic cross-section of the metallic
material thin sheet of FIG. 4A after recrystallization;
[0023] FIG. 6A is a schematic illustration of an iron alloy having
a desired amount of pearlite and produced according to an exemplary
embodiment;
[0024] FIG. 6B is a schematic illustration of an iron alloy
microstructure with a desired amount of bainite and martensite
produced according to an exemplary embodiment;
[0025] FIG. 6C is a schematic illustration of an iron alloy
microstructure having no pearlite;
[0026] FIG. 7A is a schematic illustration of an aluminum alloy
microstructure having been precipitation strengthened according to
an exemplary embodiment;
[0027] FIG. 7B is a schematic illustration of a nickel alloy
microstructure having been precipitation strengthened according to
an exemplary embodiment;
[0028] FIG. 8 is a schematic cross-section of a metallic glass thin
sheet with surface regions having a recrystallized microstructure
in an inner region with a glass microstructure produced according
to an exemplary embodiment; and
[0029] FIG. 9 is a schematic cross-sectional diagram of an
apparatus configured to chemically alter a surface region of a
metallic material thin sheet article according to an exemplary
embodiment.
DETAILED DESCRIPTION
[0030] Applicant has recognized a need for improvements in thermal
treatment of metallic materials, both in methods and systems for
thermally treating metallic materials and the resulting thermally
treated metallic materials themselves. For example, thin sheets of
metallic materials are useful for a number of applications,
including use in heat exchangers, aerospace applications, cookware,
cutlery, heat treating equipment, alternative energy components,
and building materials. Metallic materials, the term herein
including pure metals, alloys, intermetallics, and metallic
glasses, can be processed to have a wide range of microstructures
and mechanical properties. Metallic materials, particularly alloys,
can provide high strength and excellent ductility compared to
ceramics and glasses. In addition, metallic materials are typically
electrically conductive and are used in electrical
applications.
[0031] Traditional thermal treatment of metallic materials
typically includes placing a metallic material article (article) in
a furnace at an elevated temperature for a given amount of time and
then removing the article form the furnace and cooled. In the event
that the article has been subjected to cold working, the thermal
treatment of the article can result in recrystallization of the
article's microstructure. The thermal treatment of the article can
also reduce residual stress within the article without
recrystallization of the article's microstructure. When the article
is made from a metal or alloy that has a high temperature phase and
a different low temperature phase, e.g. iron or steel with an
austenitic high temperature phase (.gamma.) and a ferritic low
temperature phase (.alpha.) thermal treatment of the article can
provide an article microstructure with the ferritic low temperature
phase and additional metastable phases. In addition, heating and
controlled cooling of the article can provide a desired density and
spatial location of the one or more metastable phases. However,
traditional thermal treatment of articles typically involves large
furnaces that use significant amounts of energy for heating.
Additionally, such furnaces may provide a reducing atmosphere for
thermal treatment of the articles and this use large amounts of
reducing gases such as hydrogen gas.
[0032] Therefore, a need exists for systems and methods for
thermally treating articles that significantly reduce energy and/or
reducing gas requirements. Specifically, processes and systems
discussed herein thermally treat articles with a reduced energy
consumption of at least 50% compared to traditional thermal
treating systems. When a reducing gas is used during thermal
treatment of a given type of classification of articles, the
methods and systems described herein reduce the amount of reducing
gas needed by more than 50% compared to traditional thermal
treating systems.
[0033] The processes and systems described herein thermally treat
an article by heating and/or cooling the article while it is
supported with gas. In some embodiments the gas can be a moving
and, in further embodiments, capable of moving the article. The
article can be heated by transferring thermal energy from a heat
source to the article across a heating gap between the heat source
and the article such that more than 20% of the thermal energy
leaving the heat source crosses the heating gap and can be received
by the article. Also, the article can be cooled by transferring
thermal energy from the article to a heat sink across a cooling gap
between the article and the heat sink such that more than 20% of
the thermal energy leaving the article crosses the cooling gap and
can be received by the heat sink. In embodiments, more than 50% of
the thermal energy leaving the heat source or the article crosses
the heating gap or the cooling gap, respectively, and can be
received by the article component or the heat sink, respectively.
The heating gap or the cooling gap can have an average thickness
between an outer surface of the heat source and the article or
between the article and an outer surface of the heat sink that can
be less than 200 microns, less than 180 microns, less than 160
microns, less than 140 microns, less than 120 microns, less than
100 microns, less than 80 microns, less than 60 microns, less than
40 microns or less than 20 microns. A heat transfer rate from the
heat source to the article during heating or from the article to
the heat sink during cooling can be greater than 50 kilowatts per
square meter (kW/m.sup.2), greater than 100 kW/m.sup.2, greater
than 150 kW/m.sup.2, greater than 200 kW/m.sup.2, greater than 250
kW/m.sup.2, greater than 300 kW/m.sup.2, greater than 350
kW/m.sup.2, greater than 450 kW/m.sup.2, greater than 550
kW/m.sup.2, greater than 650 kW/m.sup.2, greater than 750
kW/m.sup.2, greater than 1000 kW/m.sup.2, or greater than 1200
kW/m.sup.2 for the area of the outer surface of the heat source, or
for the area of the outer surface of the article, respectively.
[0034] The article can be in the form of a sheet, a cylindrical
rod, a hexagonal rod, and the like. When the article is in the form
of a sheet, the article has a length, a width, and a thickness. In
embodiments, the thickness of the sheet can be less than 3 mm, less
than 2 mm, less than 1.5 mm, less than 1.0 mm, less than 0.5 mm,
less than about 0.25 mm, less than about 0.1 mm, less than 0.08 mm,
less than 0.06 mm, or less than 0.04 mm. At least one of the width
and the length are greater than five times the thickness of the
sheet. When the article is in the form of a rod, the rod has an
average diameter and a length. In embodiments, the diameter of the
rod can be less than 10 mm, less than 9 mm, less than 8 mm, less
than 7 mm, less than 6 mm, less than 5 mm, less than 4 mm, less
than 3 mm, less than 2 mm, less than 1 mm, less than 0.8 mm, less
than 0.6 mm, less than 0.4 mm, less than 0.2 mm or less than 0.1
mm.
[0035] The heating gap or cooling gap can be a gas gap with a gap
area and the total mass flow rate of gas into the gas gap can be
greater than zero and less than 2 k/gCp per square meter of gap
area, where k is the thermal conductivity of a gas within the gas
gap evaluated in the direction of heat conduction, g is the
distance between the heat source and the article or between the
article and the heat sink surface, and Cp is the specific heat
capacity of the gas within the gas gap.
[0036] The metallic material can be a pure metal or an alloy and
the pure metal or alloy can be polycrystalline, single crystal, or
metallic glass. The pure metal can be a commercial pure metal such
as commercial pure aluminum (Al), copper (Cu), chromium (Cr),
nickel (Ni), niobium (Nb), iron (Fe), magnesium (Mg), molybdenum
(Mo), silver (Ag), tantalum (Ta), titanium (Ti), tungsten (W)
zirconium (Zr), gold (Au), platinum (Pt) or any other commercially
available pure metal. The alloy can be an Al-base alloy, a Cu-base
alloy, a Cr-base alloy, a Ni-base alloy, a Nb-base alloy, an
Fe-base alloy, a Mg-base alloy, a Mo-base alloy, a Ag-base alloy, a
Ta-base alloy, a Ti-base alloy, a W-base alloy, a Zr-base alloy, a
Au-base alloy or another known alloy.
[0037] In embodiments, the article can be made from an Al-base
alloy and the Al-base alloy article can be solution heat treated
and quenched in order to provide a precipitation strengthened (also
known as precipitation hardened or age hardened) article with
reduced residual stresses. In addition, the Al-base alloy article
can be subjected cold working and then heated by the heat source
such that recrystallization of the cold worked Al-base alloy
article microstructure occurs. The recrystallized Al-base alloy
article can be controllably cooled to prevent undesired grain
growth of the recrystallized Al-base alloy article
microstructure.
[0038] In embodiments, the article can be made from a Cu-base alloy
article and the Cu-base alloy article can be solution heat treated,
quenched and aged in order to provide a precipitation strengthened
article with reduced residual stresses. In addition, the Cu-base
alloy article can be subjected cold working and then heated by the
heat source such that recrystallization of the cold worked Cu-base
alloy article microstructure occurs. The recrystallized Cu-base
alloy article can be controllably cooled to prevent undesired grain
growth of the recrystallized Cu-base alloy article
microstructure.
[0039] In embodiments, the article can be made from an Fe-base
alloy and the Fe-base alloy article can be solution annealed such
that the microstructure of the Fe-base alloy can be completely
austenite and then cooled to provide a microstructure with ferrite
and a desired amount of pearlite, including no pearlite. In other
embodiments, the Fe-base alloy article can be solution annealed
such that the microstructure of the Fe-base alloy can be completely
austenite and then cooled to provide a microstructure with ferrite
and a desired amount of bainite and/or martensite. The solution
annealed Fe-base alloy article can be cooled such retained
austenite can be present in the Fe-base alloy article's
microstructure. The Fe-base alloy article can be subjected cold
working and then heated by the heat source such that
recrystallization of the cold worked Fe-base alloy article
microstructure occurs. The recrystallized Fe-base alloy article can
be controllably cooled to prevent undesired grain growth of the
recrystallized Fe-base alloy article microstructure. For the
purposes of the present disclosure, the term "solution annealed"
refers to a thermal treatment that produces a solid solution of
alloy elements in a high temperature matrix phase. It should be
appreciated that the high temperature matrix phase can be the same
phase as a low temperature matrix phase, e.g. face centered cubic
(FCC) austenite for Ni-base alloys, or can be a different phase
from the low temperature phase, e.g. FCC austenite versus BCC
ferrite for Fe-base alloys.
[0040] In embodiments, the article can be made from a Ni-base alloy
and the Ni-base alloy article can be solution annealed such that
the microstructure of the Ni-base alloy can be completely
austenitic (face centered cubic--FCC) and then cooled to provide a
microstructure with desired second phase precipitates. Such second
phases precipitates can include Ni.sub.3Al (gamma prime)
precipitates, carbide precipitates, nitride precipitates and/or
carbonitride precipitates. The Ni-base alloy article can be
subjected cold working and then heated by the heat source such that
recrystallization of the cold worked Ni-base alloy article
microstructure occurs. The recrystallized Ni-base alloy article can
be controllably cooled to prevent undesired grain growth of the
recrystallized Ni-base alloy article microstructure. The article
can be made from other types of alloys and heat treated and cooled
to provide a desired article microstructure. It should be
appreciated that the microstructure of an alloy article can be
closely linked to the article's mechanical properties. Accordingly,
an alloy article can be heated treated and cooled to provide a
desired combination of strength and ductility.
[0041] The process can include heating of the metallic material
article in a heating zone configured to chemically alter a surface
region of the article. For example, the heating zone can include
chemical vapor deposition (CVD) equipment and/or plasma deposition
equipment that can chemically alter the surface region of the
article. The surface region of the article can be chemically
altered such as by coating with, impregnation and/or diffusion of
elements such as nitrogen (nitriding), boron (boriding), carbon
(carburizing), and combinations thereof.
[0042] By way of example, FIG. 1 shows an exemplary embodiment of a
metal thermal treatment system 300 according to this disclosure.
FIG. 1 shows a schematic cross-sectional diagram of the system 300,
in which an article (sheet) can be heated via conduction of heat
from a heat source to the article and cooled via conduction of heat
from the article, through a gas into a conductive heat sink. The
metal thermal treatment system 300 includes a hot zone 310, a cold
zone 330, and a transition gas bearing 320. Transition gas bearing
320 moves or directs the article (e.g., metallic material sheet
(sheet) 400a) from the hot zone 310 to the cold zone 330 such that
no contact or substantially no contact occurs between the sheet and
the bearings. The hot zone 310 has gas bearings 312 each fed from a
hot zone plenum 318, and the bearings 312 have heat sources 314
inserted into holes through the bearings 312, which serve to heat
the hot zone gas bearings 312 to a desired thermal treatment
process temperature. The heat sources 314 can be electrically
resistive heat sources or induction heating heat sources. In
embodiments, the heat sources 314 may have an outer surfaces 314a
that face the channel 316 and the outer surfaces 314a may provide
infrared heating. A sheet (hot zone) 400a can be kept between the
hot zone gas bearings 312 for a duration long enough to bring it to
a desired thermal treatment temperature (e.g., a stress relief
temperature, a solution annealing temperature, a high temperature
phase annealing temperature, an age hardening temperature,
etc.).
[0043] In some embodiments, heating the article in the hot zone may
be done predominantly via conduction of heat from a heat sink
through a thin gas barrier. The conductive heating processes used
in the hot zone can be similar to, but the reverse of the cooling
processes described herein (e.g., pushing heat into the article).
As shown in FIG. 1, the hot zone 310 includes the one or more heat
sources 314 disposed adjacent to the channel 316. Where two heat
sources are utilized, such heat sources may be disposed on opposite
sides of the channel 316, facing each other across a channel gap
316a between the outer surfaces 314a. In some embodiments, the heat
sources include a plurality of apertures 314b which form part of
the gas bearing 312, and the outer surfaces 314a of the hot gas
bearings 312 of the hot zone 310 serve as the two heat source
surfaces. Due to the low gas flow rate within channel 316 and the
small size that can be provided for the channel gap 316a, sheet
400a can be heated within hot zone 310 primarily by conduction of
heat from the heat sources 314 across the channel gap 316a and into
the sheet 400a, without the sheet 400a touching the heat source
outer surfaces 314a.
[0044] In some embodiments, the heat sources and/or the surfaces
thereof may be segmented. In some embodiments, the heat sources may
be porous, and in such embodiments, the apertures through which the
gas for gas bearings 312 can be delivered are the pores of the
porous heat sinks. The plurality of apertures 314b, a gas source
and the channel gap 316a may be in fluid communication. In some
embodiments, the gas flows through the apertures 314b to form gas
cushions, layers or bearings in the channel gap 316a. The gas
cushions of some embodiments prevent the sheet 400a from contacting
the heat source 314 surfaces. The gas also serves as the gas
through which the sheet 400a can be heated by conduction more than
by convection.
[0045] In some embodiments, the gas flowed through the apertures
314b heats the heat sources 314. In some embodiments, the gas
flowed through the apertures both facilitates heat conduction, from
the heat source 314, across the gap 316a, into the sheet 400a, and
also heats the heat sources 314. In some instances, a separate gas
or liquid may be used to heat the heat sources 314. For instance,
the heat sources 314 may include passages (not shown), for flowing
a heating gas or liquid therethrough to heat the heat sources 314.
The passages can be enclosed.
[0046] Where two heat sources are used (i.e., a first heat source
and the second heat source), one or more gas sources may be used to
provide a gas to the channel gap 316a. The gas sources may include
the same gas as one another or different gases. The channel gap
316a may, therefore, include one gas, a mixture of gases from
different gas sources, or the same gas source. Exemplary gases
include air, nitrogen, carbon dioxide, helium or other noble gases,
hydrogen and various combinations thereof. The gas may be described
by its thermal conductivity when it enters the channel 316 just
before it begins to conductively heat the sheet 400a. In some
instances, the gas may have a thermal conductivity of about (e.g.,
plus or minus 1%) 0.02 W/(mK) or greater, about 0.025 W/(mK) or
greater, about 0.03 W/(mK) or greater, about 0.035 W/(mK) or
greater, about 0.04 W/(mK) or greater, about 0.045 W/(mK) or
greater, about 0.05 W/(mK) or greater, about 0.06 W/(mK) or
greater, about 0.07 W/(mK) or greater, about 0.08 W/(mK) or
greater, about 0.09 W/(mK) or greater, about 0.1 W/(mK) or greater,
about 0.15 W/(mK) or greater, or about 0.2 W/(mK) or greater).
[0047] The processes and systems described herein allow for high
heat transfer rates which, as discussed above, allow for rapid and
controlled heating within sheet, and allow for rapid, localized and
controlled heating of outer surface regions of thin sheet. Using
air as the gas, with gaps between the sheet and the heat sinks,
heat transfer rates as high as 50 kilowatts per square meter
(kW/m.sup.2), greater than 100 kW/m.sup.2, greater than 150
kW/m.sup.2, greater than 200 kW/m.sup.2, greater than 250
kW/m.sup.2, greater than 300 kW/m.sup.2, greater than 350
kW/m.sup.2, greater than 450 kW/m.sup.2, greater than 550
kW/m.sup.2, greater than 650 kW/m.sup.2, greater than 750
kW/m.sup.2, greater than 1000 kW/m.sup.2, or greater than 1200
kW/m.sup.2 or more are possible through conduction alone. Using
helium or hydrogen, heat transfer rates of 5000 kW/m.sup.2 or more
can be achieved. Accordingly, the cold zone 330 can provide cooling
rates that equate to furnace cooling, air cooling and/or water
quenching (1000-4000 kW/m.sup.2) of articles thermally treated in
the thermal treatment system 300.
[0048] In some embodiments, gaps 316a, between the hot zone gas
bearings 312 and the sheet 400a, may be relatively large, on the
order of 0.05'' (1.27 mm) to 0.125'' (3.175 mm) or greater, since
the sheet 400a may be heated up relatively slowly and thermal
radiation from the hot gas bearings 312 into the sheet 400a can be
adequate for this purpose. In other embodiments, hot zone gap size
may be as small as 150 microns per side or 500 microns per side.
Smaller gaps may be advantageous, in some embodiments, because they
enable the bearings to have better "stiffness"--i.e., ability to
centralize the sheet and therefore flatten it while it is in its
softened state. In some embodiments, the process may re-form the
sheets flattening them--in the initial heating step, for example
via the pressure supplied by the gas bearings 312. In some
embodiments, the top and bottom hot zone bearings may be on
actuators, allowing for changing the gap width in a continuous
manner or, alternatively, allowing the sheet to be brought into the
hot zone when the gap is large and then compressing the gap to
flatten the sheet while it is still soft.
[0049] Process temperatures in the hot and/or cool zone are
dependent on a number of factors, including sheet composition,
sheet thickness, sheet properties (CTE, etc.), and desired level of
thermal treatment (e.g. stress reliving, solution annealing, etc.).
Generally, the starting process temperature may be any value
between the ambient temperature and the melting point of the sheet.
For low carbon steel, for example, system 300 heats the sheet 400a
to a temperature between about (e.g., plus or minus 1%) 780 to
about 820.degree. C. For age-hardenable aluminum alloys, for
example, system 300 heats the sheet to a solution anneal
temperature of about 530.degree. C., an annealing temperature of
about 410.degree. C. and/or an aging precipitation heat treatment
temperature of about 175.degree. C. For solution strengthened
nickel alloys, for example, system 300 heats the sheet to a
solution anneal temperature of about 1150.degree. C. For
age-hardenable nickel alloys, for example, system 300 heats the
sheet to a solution anneal temperature of about 1080.degree. C., to
a first age-hardening treatment temperature of about 995.degree.
C., to a second age-hardening treatment temperature of about
845.degree. C. and to a third age-hardening treatment temperature
of about 760.degree. C. Between the first age-hardening treatment
temperature to the a second age-hardening treatment temperature,
and from the a second age-hardening treatment temperature to the
third age-hardening treatment temperature, the sheet can be cooled
at one or more desired cooling rates such that furnace cooling, air
cooling, water quenching, or some cooling rate between cooling
rates associate with furnace cooling, air cooling or water
quenching, can be provided to the sheet. Furthermore, the sheet can
be moved back and forth between the hot zone 310 and the cold zone
330 in order to provide desired heating and cooling cycles for the
sheet.
[0050] The sheet 400a can be heated to its desired starting thermal
treatment temperature (e.g., a solution anneal temperature), and it
can then moved from the hot zone 310 to the cold zone 330 for
controlled cooling using any suitable means. In some embodiments,
moving the sheet 400a from the hot zone 310 to the cold zone 330
may be accomplished by, for example (1) tilting the entire assembly
such that gravity acting on the sheet forces it to move to the cold
zone, (2) blocking off the gas flow from the leftmost exit of the
hot zone 310 (the sides are enclosed in this embodiment), thereby
forcing all of the gas emanating from all of the gas bearings to
exit from the rightmost exit of the cold zone, causing fluid forces
to be exerted on the sheet 400a and causing it to move to the cold
zone 330, or (3) by a combination of (1) and (2)).
[0051] The transition gas bearings 320 may be supplied with gas by
transition bearing plenums 328. The solid material thickness behind
the surfaces of the transition gas bearings 320 may be thin, of low
thermal mass and/or low thermal conductivity, allowing for reduced
heat conduction from the hot zone 310 to the cold zone 330. The
transition gas bearings 320 may serve as a thermal break or
transition between the two zones 310 and 330 and may serve to
transition from the larger gaps 316a of the hot zone down to small
gaps 336 of the cold zone 330. Further, the low thermal mass and/or
low thermal conductivity of transition gas bearings 320 limit(s)
the amount of heat transfer and therefore cooling experienced by
sheet 400a while passing past transition gas bearings 320.
[0052] Once the sheet 400a (hot zone) moves into the cold zone 330
and into the channel 330a, the sheet 400b (cold zone) can be
stopped from exiting the right side exit by a mechanical stop or
any other suitable blocking mechanism, shown as stop gate 341. Once
the sheet 400b cools sufficiently, the stop gate 341 may be moved,
unblocking cold zone channel 330a, and then the sheet 400b may be
removed from the system 300. If desired, the sheet 400b may be left
in the cold zone 330 until somewhere near room temperature or below
before removal.
[0053] As noted above, within hot zone 310, sheet 400a can be
heated to a desired temperature and the cold zone 330 includes a
channel 330a for receiving heated sheet 400a through an opening
330b, conveying the sheet 400a into the cold zone 330, and cooling
the sheet 400b in the cold zone 330. In one or more embodiments,
the channel 330a includes a conveyance system that may include gas
bearings, roller wheels, conveyor belt, or other means to
physically transport the sheet through the cold zone. As shown in
FIG. 1, cold zone 330 includes gas bearings 332 which are fed
plenums 338 that are separate from hot zone plenums 318 and
transition bearing plenums 328.
[0054] As shown in FIG. 1, the cold zone 330 includes one or more
heat sinks 331 disposed adjacent to the channel 330a. Where two
heat sinks are utilized, such heat sinks may be disposed on
opposite sides of the channel 330a, facing each other across a
channel gap 330a. In some embodiments, the heat sinks include a
plurality of apertures 331a which form part of the gas bearing 332,
and the surfaces of the cold gas bearings 332 of the cold zone 330
serve as the two heat sink surfaces. Due to the low gas flow rate
within channel 330a and the small size of channel gap 330a, sheet
400b can be cooled within cold zone 330 primarily by conduction of
heat from the sheet 400b across the gap and into the solid heat
sinks 331, without the sheet 400b touching the heat sink
surfaces.
[0055] In some embodiments, the heat sinks and/or the surfaces
thereof may be segmented. As noted above, in some embodiments, the
heat sinks may be porous, and in such embodiments, the apertures
through which the gas for gas bearings 332 can be delivered are the
pores of the porous heat sinks. The plurality of apertures 332b, a
gas source and the channel gap 330a may be in fluid communication.
In some embodiments, the gas flows through the apertures 331a to
form gas cushions, layers or bearings in the channel gap 330a. The
gas cushions of some embodiments prevent the sheet 400b from
contacting the heat sink 331 surfaces. The gas also serves as the
gas through which the sheet 400b can be cooled by conduction more
than by convection.
[0056] In some embodiments, the gas flowed through the apertures
331a cools the heat sinks. In some embodiments, the gas flowed
through the apertures both facilitates heat conduction, from the
sheet, across the gap, into the heat sinks, and also cools the heat
sinks 331. In some instances, a separate gas or liquid may be used
to cool the heat sinks 331. For instance, the heat sinks 331 may
include passages 334, for flowing a cooling gas or liquid
therethrough to cool the heat sinks 331. The passages 334 can be
enclosed.
[0057] Where two heat sinks are used (i.e., a first heat sink and
the second heat sink), one or more gas sources may be used to
provide a gas to the channel gap 330a. The gas sources may include
the same gas as one another or different gases. The channel gap
330a may, therefore, include one gas, a mixture of gases from
different gas sources, or the same gas source. Exemplary gases
include air, nitrogen, carbon dioxide, helium or other noble gases,
hydrogen and various combinations thereof. In embodiments, the gas
can be hydrogen and the thermal treatment system 300 serves as a
bright anneal furnace, i.e. a furnace that anneals the sheet in a
reducing environment which prevents oxidation of the sheet surface
and reduces most oxides present on the sheet surface, thereby
providing an annealed sheet with a "bright" surface. The quick
transfer of the sheet 400a from the hot zone 310 to the cold zone
330 can provide a rapid cooling rate, e.g. equivalent to water
quenching, to the sheet 400b. It should be appreciated that such a
"water quench" type of cooling provides cooling rates currently not
available for current bright anneal furnaces.
[0058] The gas may be described by its thermal conductivity when it
enters the channel 330a just before it begins to conductively cool
the sheet 400b. In some instances, the gas may have a thermal
conductivity of about (e.g., plus or minus 1%) 0.02 W/(mK) or
greater, about 0.025 W/(mK) or greater, about 0.03 W/(mK) or
greater, about 0.035 W/(mK) or greater, about 0.04 W/(mK) or
greater, about 0.045 W/(mK) or greater, about 0.05 W/(mK) or
greater, about 0.06 W/(mK) or greater, about 0.07 W/(mK) or
greater, about 0.08 W/(mK) or greater, about 0.09 W/(mK) or
greater, about 0.1 W/(mK) or greater, about 0.15 W/(mK) or greater,
or about 0.2 W/(mK) or greater).
[0059] The processes and systems described herein allow for high
heat transfer rates which, as discussed above, allow for a
strengthening degree of temperature differential to form within
even a very thin sheet. Using air as the gas, with gaps between the
sheet and the heat sinks, heat transfer rates as high as 50, 100,
150, 200, 250, 300 350, 450, 550, 650, 750, 1000, and 1200
kW/m.sup.2 or more are possible through conduction alone. Using
helium or hydrogen, heat transfer rates of 5000 kW/m.sup.2 or more
can be achieved.
[0060] The heat sinks 331 of one or more embodiments may be
stationary or may be movable to modify the thickness of the channel
gap 330a. The thickness of the sheet 400b may be in a range from
about 0.4 times the thickness to about 0.6 times the thickness of
channel gap 300a, which is defined as the distance between the
opposing surfaces of the heat sinks 331 (e.g., upper and lower
surface of heat sinks 331 in the arrangement of FIG. 1). In some
instances, the channel gap can be configured to have a thickness
sufficient such that the heated sheet can be cooled by conduction
more than by convection.
[0061] In some embodiments, the channel gap in the hot zone 310
and/or the cold zone 330 may have a thickness such that when sheet
400a or 400b is being conveyed through or located within the
channel 316a or 330a, the distance between the major surfaces of
the sheet 400a or 400b and the heat source surface or heat sink
surface (e.g., the gap size discussed above) can be about (e.g.,
plus or minus 1%) 100 .mu.m or greater (e.g., in the range from
about 100 .mu.m to about 200 .mu.m, from about 100 .mu.m to about
190 .mu.m, from about 100 .mu.m to about 180 .mu.m, from about 100
.mu.m to about 170 .mu.m, from about 100 .mu.m to about 160 .mu.m,
from about 100 .mu.m to about 150 .mu.m, from about 110 .mu.m to
about 200 .mu.m, from about 120 .mu.m to about 200 .mu.m, from
about 130 .mu.m to about 200 .mu.m, or from about 140 .mu.m to
about 200 .mu.m). In some embodiments, the channel gap may have a
thickness such that when sheet 400a or 400b is being conveyed
through the channel 316 or 330a, the distance between the sheet and
the heat source surface or heat sink surface (the gap or gaps 316a
or 330a) can be about (e.g., plus or minus 1%) 100 .mu.m or less
(e.g., in the range from about 10 .mu.m to about 100 .mu.m, from
about 20 .mu.m to about 100 .mu.m, from about 30 .mu.m to about 100
.mu.m, from about 40 .mu.m to about 100 .mu.m, from about 10 .mu.m
to about 90 .mu.m, from about 10 .mu.m to about 80 .mu.m, from
about 10 .mu.m to about 70 .mu.m, from about 10 .mu.m to about 60
.mu.m, or from about 10 .mu.m to about 50 .mu.m). The total
thickness of the channel gap 316a or 330a can be dependent on the
thickness of the sheet 400a or 400b, but can be generally
characterized as 2 times the distance between the heat source
surface or heat sink surface and the sheet, plus the thickness of
the sheet. In some embodiments, the distance or gaps 316a or 330a
between the sheet and the heat sources or heat sinks may not be
equal. In such embodiments, the total thickness of the channel gap
316a or 330a may be characterized as the sum of the distances
between the sheet and each heat source surface or the sheet and
each heat sink surface, plus the thickness of the sheet.
[0062] In some instances, the total thickness of the channel gap
316a or 330a may be less than about (e.g., plus or minus 1%) 2500
.mu.m (e.g., in the range from about 120 .mu.m to about 2500 .mu.m,
about 150 .mu.m to about 2500 .mu.m, about 200 .mu.m to about 2500
.mu.m, about 300 .mu.m to about 2500 .mu.m, about 400 .mu.m to
about 2500 .mu.m, about 500 .mu.m to about 2500 .mu.m, about 600
.mu.m to about 2500 .mu.m, about 700 .mu.m to about 2500 .mu.m,
about 800 .mu.m to about 2500 .mu.m, about 900 .mu.m to about 2500
.mu.m, about 1000 .mu.m to about 2500 .mu.m, about 120 .mu.m to
about 2250 .mu.m, about 120 .mu.m to about 2000 .mu.m, about 120
.mu.m to about 1800 .mu.m, about 120 .mu.m to about 1600 .mu.m,
about 120 .mu.m to about 1500 .mu.m, about 120 .mu.m to about 1400
.mu.m, about 120 .mu.m to about 1300 .mu.m, about 120 .mu.m to
about 1200 .mu.m, or about 120 .mu.m to about 1000 .mu.m). In some
instances, the total thickness of the channel gap may be about 2500
.mu.m or more (e.g., in the range from about 2500 .mu.m to about
10,000 .mu.m, about 2500 .mu.m to about 9,000 .mu.m, about 2500
.mu.m to about 8,000 .mu.m, about 2500 .mu.m to about 7,000 .mu.m,
about 2500 .mu.m to about 6,000 .mu.m, about 2500 .mu.m to about
5,000 .mu.m, about 2500 .mu.m to about 4,000 .mu.m, about 2750
.mu.m to about 10,000 .mu.m, about 3000 .mu.m to about 10,000
.mu.m, about 3500 .mu.m to about 10,000 .mu.m, about 4000 .mu.m to
about 10,000 .mu.m, about 4500 .mu.m to about 10,000 .mu.m, or
about 5000 .mu.m to about 10,000 .mu.m).
[0063] The apertures 331a in the heat sink 331 may be positioned to
be perpendicular to the heat sink surface or may be positioned at
an angle of 20 degrees or less, such as about (e.g., plus or minus
1%) 15 degrees or less, about 10 degrees or less or about 5 degrees
or less) from perpendicular to the heat sink surface.
[0064] In some embodiments, the material behind the heat sink (cold
gas bearing 332) surfaces can be any suitable material having high
heat transfer rates, including metals (e.g., stainless steel,
copper, aluminum), ceramics, carbon, etc. This material may be
relatively thick compared to the material behind the surfaces of
the transition gas bearings 320, as shown in FIG. 1, such that heat
sink can easily accept relatively large amounts of thermal energy.
In an exemplary embodiment, the material of the heat sinks 331 can
be stainless steel.
[0065] Referring to FIG. 2, the metal thermal treatment system 300
shown in FIG. 1 can processes metal sheet in a continuous manner.
The thermal treatment system 300 is similar to the thermal
treatment system 300 shown in FIG. 1 except a sheet 400 can be
continuous processed through the thermal treatment system 300 by
supplying a sheet 400 to the thermal treatment system 300 from a
feed roll 305 and after exiting the thermal treatment system 300
coiling the thermal treated sheet 400 into an exit roll 335. As the
sheet 400 enters the hot zone 310 it can be heated as discussed
above with respect to sheet 400a. The sheet 400 continues to pass
through the transition gas bearing 320 and into the cold zone 330
where it cooled as discussed above with respect to sheet 400b. It
should be appreciated that the speed of the sheet 400 through the
thermal treatment system 300, the heating rate of the sheet 400 in
the hot zone 310, the thermal treatment temperature of the sheet
400 in the hot zone 310, the cooling rate of the sheet 400 in the
cold zone 330 are designed and implemented to provide a thermally
treated metallic material sheet with desired a desired
microstructure and mechanical properties.
[0066] Referring now to FIGS. 1-3, FIG. 3 illustrates the use of
another treatment system 300 to thermally treat the sheet 400 after
it has been thermally treated by the thermal treatment system 300
in FIG. 2. Particularly, the thermal treatment system 300 in FIG. 2
thermally treats the sheet 400 through a first heating and cooling
thermal treatment cycle and the thermal treatment system 300 in
FIG. 3 thermally treats the sheet 400 through a second heating and
cooling thermal treatment cycle. The sheet 400 from feed roll 305
in the thermal treatment system 300 in FIG. 2 can be fed into the
heating zone 310 and thermally treated as discussed above in
reference to sheet 400a in FIGS. 1-2. The sheet 400 moves from the
hot zone 310, through the transition gas bearings 320 and into the
cold zone 330 where it can be thermally treated as discussed above
in reference to sheet 400b in FIGS. 1-2. As the thermally treated
sheet 400 exits the cold zone 330 it can be coiled into the exit
roll 335 for the thermal treatment system 300 in FIG. 2. Between
the feed roll 305 and the exit roll 335 of the thermal treatment
system 300 in FIG. 2, the sheet 400 can be subjected to a first
heating and cooling thermal treatment cycle. Exit roll 335 of the
thermal treatment system 300 in FIG. 2 can be then used as feed
roll 305 for the thermal treatment system 300 in FIG. 3. Similar to
the thermal treatment system 300 in FIG. 2, the thermally treated
sheet 400 from the thermal treatment system 300 in FIG. 2, which
can be the feed roll 305 for the thermal treatment system 300 in
FIG. 3, can be subjected to another (second) heating and cooling
thermal treatment cycle. It should be appreciated that more than
two thermal treatment systems as disclosed herein can be used to
thermally treat metallic material articles and thus provide more
than two heating and cooling thermal treatment cycles.
[0067] Referring now to FIGS. 1-4, FIG. 4 illustrates a time versus
temperature graph for sheet passing through the metal thermal
treatment system 300 in FIG. 1 or 2, or passing through one of the
thermal treatments systems in FIG. 3. In embodiments, and as shown
in FIG. 4, the sheet 400 has a temperature between T1-T2 (e.g.,
ambient temperature) before entering the hot zone 310 of the
thermal treatment system 300, at which time the sheet 400a can be
heated to a heat treatment temperature (e.g. a solution anneal
temperature) between T3-T4 in the heat zone 310. The sheet 400a can
be held at the heat treatment temperature between T3-T4 for a
predetermined amount of time and then passed through the transition
gas bearings 320 into the cold zone 330 where cooling of the sheet
400b to a temperature between T5-T6 at a predetermined and desired
cooling rate occurs. Thereafter, the sheet 400b can be removed from
the cold zone 330 and allowed to further cool to the temperature
between T1-T2 (e.g., ambient temperature). In the alternative, the
sheet 400b can be cooled and held at the temperature between T5-T6
in the cold zone 330, and then cooled and held to the temperature
between T1-T2 in the cold zone 330, before the sheet 400b exits the
cold zone 330. The cooling rate for the sheet 400b cooled from the
temperature between T3-T4 to the temperature between T5-T6 may or
may not be the same as the cooling rate for the sheet 400b cooled
from the temperature between T5-T6 to the temperature between
T1-T2.
[0068] FIGS. 5A and 5B illustrate recrystallization of an article
that has been subjected to work hardening (also known as strain
hardening and cold working). The article has been subjected to
plastic deformation and exhibits a work hardened microstructure
(e.g. grains elongated in the direction of the plastic deformation
process) in FIG. 5A. After being heated to a desired a
recrystallization temperature in the hot zone 310 for a desired
amount of time, recrystallization of the microstructure occurs as
illustrated ion FIG. 5B. Also, cooling of the article in the cold
zone 330 controls grain growth, i.e. prevents excessive grain
growth after recrystallization. Such recrystallization of articles
can be provided by the thermal treatments system 300 for a variety
of metallic materials, including but not limited to commercial pure
metals such as commercial pure Al, Cu, Cr, Ni, Nb, Fe, Mg, Mo, Ag,
Ta, Ti, W, Zr, Au, Pt or any other commercially available pure
metal, and alloys such as Al-base alloys, Cu-base alloys, Cr-base
alloys, Ni-base alloys, Nb alloys, Fe-base alloys, Mg alloys, Mo
alloys, Ag alloys, Ta alloys, Ti alloys, W alloys, Zr alloys, Au
alloys or other known alloys.
[0069] FIGS. 6A-6C illustrate exemplary microstructures of articles
that have been processed through the thermal treatment system 300.
For example, steel sheet can be thermally treated in the thermal
treatment system 300 such that a ferrite matrix with a desired
amount of pearlite can be provided as illustrated in FIG. 5A. In
the alternative, steel sheet can be thermally treated such that a
ferrite matrix with a desired amount of bainite and/or martensite
can be provided as illustrated in FIG. 5B. Also, steel sheet can be
thermally treated such that a ferrite matrix free of pearlite and
other second phases can be provided as illustrated in FIG. 5C.
[0070] Referring now to FIG. 6A, an exemplary microstructure of an
Al-base alloy having been thermally treated by the metal thermal
treatment system 300 is shown. The thermal treatment system 300 has
heated and cooled the Al-base alloy such that precipitates known as
"GP zones" have been precipitated throughout the alloy
microstructure and provided age hardening of the material. FIG. 6B
illustrates an exemplary microstructure of a nickel alloy that has
been processed through the metal thermal treatment system 300 such
that gamma prime precipitates have been precipitated throughout the
alloy microstructure and provided precipitation strengthening of
the material.
[0071] Referring now to FIG. 8, a representative microstructure of
a metallic glass having been processed through the metal thermal
treatment system 300 illustrates surface regions of the metallic
glass thin sheet having been recrystallized while an inner region
remains with an amorphous or glass morphology. Such thermal
treatment provides an article with surfaces that are resistant to
crack initiation and propagation and an interior with increased
tensile strength and elastic strain limit.
[0072] Referring now to FIG. 9, in embodiments, the thermal
treatment system 300 chemically alters surface regions of articles
that pass therethrough. Particularly, a gaseous atmosphere 500 with
one or more chemical elements (e.g. Cr, C, B, N, Al, Si, etc.) to
be deposited onto the sheet 400a is shown. While FIG. 9 illustrates
the gaseous atmosphere 500 on both sides of the sheet 400a, in
embodiments, the thermal treatment system 300 can provide the
gaseous atmosphere 500 primarily to only one side of the sheet
400a. Once the one or more chemical elements in the gaseous
atmosphere 500 are deposited onto the surface of the sheet 400a,
the one or more chemical elements can diffuse into surface regions
of the sheet 400a and thereby alloy with the sheet 400a to provide
a chemically altered surface. In the alternative, the one or more
chemical elements deposited onto the surface of the sheet 400a can
remain at the surface and thereby provide a chemically altered
surface. The gaseous atmosphere 500 can be provided or generated
using a chemical vapor deposition (CVD) process, a plasma
deposition process, etc. In embodiments, the gaseous atmosphere 500
assists in supporting the sheet 400a such that the sheet 400a does
not come into physical contact with the heat sources 314. The
thermal treatment system 300 with the gaseous atmosphere 500 can
chromize a surface region of the sheet 400a (chromizing), carburize
a surface region of the sheet 400a (carburizing), boride a surface
region of the sheet 400a (boriding), nitride a surface region of
the sheet 400a (nitriding), aluminize a surface region of the sheet
400a (aluminizing), siliconize a surface region of the sheet 400a
(siliconizing) and combinations thereof.
EXAMPLES
[0073] Apparatus setup--As detailed above, the apparatus comprises
three zones--a hot zone, a transition zone, and a cold zone. The
gaps between the top and bottom thermal bearings in the hot zone
and cold zone are set to desired spacings. Gas flow rates in the
hot zone, transition zone, and quench zone are set to ensure
centering of the article on the gas-bearing. The hot zone can be
pre-heated to a desired temperature T.sub.o where the article will
be held a predetermined and desired amount of time before being
transferred to the cold zone and cooled. The temperature T.sub.0 is
determined by metallic material of the article being thermally
treated and the specific thermal treatment being performed on the
article. The time to equilibration is dependent at least on the
thickness of the article. For example, for sheets of approximately
1.1 mm or less, equilibration occurs in approximately 10 seconds.
For 3 mm sheets, equilibration occurs in approximately 10 seconds
to 30 seconds. For thicker sheets, up to approximately 6 mm, the
equilibration time may be on the order of 60 seconds. Once the
article has equilibrated to T.sub.0, it can be held at T.sub.o for
a desired amount of time and then transferred through the
transition zone on gas bearings and into the cooling or quench
zone. The article cools at a desired cooling rate to a temperature
below T.sub.o (T.sub.L)and may or may not be held in the cold zone
at T.sub.L for an extended period of time before exiting the cold
zone. The article can be maintained in the cold zone for any period
of time from 1 second, 10 seconds, 1 minute, several minutes, 1
hour, several hours or more, depending on the thermal treatment
desired and/or the desired temperature of the article at
removal.
[0074] A variety of different alloys can be thermally treated with
the thermal treatment system disclosed herein. Examples of such
alloys and microstructures and mechanical properties that can be
obtained are provided.
Aluminum Alloys
Example 1
[0075] A 6061 wrought aluminum sheet having a chemical composition
in weight percent of 0.15 Mn, 0.4-0.8 Si, 0.15-0.35 Cr, 0.15-0.4
Cu, 0.7 Fe, 0.25 Zn, 0.8-1.2 Mg, 0.15 Ti, with the remainder being
Al and other incidental impurities was provided as thin sheet
having a thickness of 1 mm. The thin sheet was annealed in the hot
zone at 775.degree. F. for 2 hours followed by controlled cooling
at 50.degree. F. per hour down to 500.degree. F., followed by air
cooling. The material was subjected to an age hardening heat
treatment at 350.degree. F. for 8 hours followed by air cooling in
order to produce the T6 temper. Mechanical properties of the 6061
aluminum sheet with the T6 temper showed an average tensile
strength of 45,000 psi, yield strength of 40,000 psi, shear
strength of 31,000 psi, elongation to failure of 12%, and a Brinell
hardness of 95.
Steel Alloys
Example 2
[0076] A cold rolled steel alloy sheet having a thickness of 0.5 mm
and a chemical composition within the range and weight percent of
0.085-0.11 C, 1.4-2.0 Mn, 0.09-0.21 Mo, 0.02-0.05 Al, 0.16-0.5 Si,
0.13-0.5 Cr, 0.016 max Ti, 0.06 max Ni, 0.003 max S, 0.015 max P,
0.006 max N, and with the balance being iron and incidental metal
impurities can be processed through the metal thermal treatment
system 300 and subjected to an intercritical annealing in the hot
zone at temperatures between 760-800.degree. C. Thereafter, the
intercritically annealed steel alloy sheet can be rapidly cooled to
a temperature of less than 450.degree. C. in the cold zone. The
rapidly cooled sheet has a ferrite-martensite microstructure with
less than 6 volume percent bainite, a 0.2% yield strength of at
least 330 MPa, a tensile strength of at least 590 MPa, a total
elongation to failure of at least 18%, and a uniform elongation of
at least 10%.
Cobalt and Nickel Solid-Solution-Strengthened Alloys
[0077] Although Co-base and Ni-base solid-solution strengthened
alloys employ second phase precipitates such as Cr-carbides,
W-carbides, etc., to assist in high temperature strengthening of
the material, the primary strengthening mechanism can be the
addition and alloying of various elements within the Co or Ni
matrix to provide "solid solution strengthening."
Example 3
[0078] One Co-base and two Ni-base solid-solution strengthened
alloys having the following nominal chemical compositions (wt %)
can be processed through the metal thermal treatment system
300.
[0079] Cobalt Alloy (C1): 10 Ni, 20 Cr, 15 W, 3 max Fe 1.5 Mn, 0.4
max Si, 0.10 C with the balance Co (approximately 51 et %) and
incidental impurities (commercially available as HAYNES.RTM. 25
alloy).
[0080] First Nickel Alloy (N1): 22 Cr, 14 W, 2 Mo, 3 max Fe, 5 max
Co, 0.5 Mn, 0.4 Si, 0.3 Al, 0.10 C, 0.02 La, 0.015 max B, with the
balance Ni (approximately 57 wt %) and incidental impurities
(commercially available as HAYNES.RTM. 230.RTM. alloy).
[0081] Second Nickel Alloy (N2): 22 Cr 18 Fe 9 Mo 1.5 Co 0.6 W 0.10
C 1 max Mn 1 max Si 0.008 B with the balance Ni (approximately 47
wt %) and incidental impurities (commercially available as
HAYNES.RTM. Hastelloy.RTM. X alloy).
[0082] Typical solution annealing temperatures provided by the
thermal treatment system 300 for the C1 and N1-N2 alloys are shown
in Table 1 below. Such solid-solution-strengthened alloys are
typically supplied in the solution annealed condition with
microstructures of primary carbides dispersed in a single phase
matrix. The microstructure can be free of primary carbides at grain
boundaries and provides an optimum combination for room temperature
fabricability and elevated temperature properties once the material
can be put into service. Heat treatments performed at temperatures
below the solution heat treating temperature range provided by the
thermal treatment system 300 are known as mill annealing or stress
relief thermal treatments (see Table 1 below). Mill annealing
treatments are employed for restoring formed, partially fabricated,
or otherwise as-worked alloy material to a condition where
additional deformation or welding of the material can be performed.
Such treatments may also be used to produce structures in finished
raw materials which are optimum for specific forming operations.
For example, mill annealing thermal treatments provided by the
thermal treatment system 300 can be used to produce a
microstructure with a fine grain size for deep drawing
applications. Mill annealing of the solid-solution-strengthened
alloys by the thermal treatment system 300 can also be used to
relief stress and yet avoid article distortion that can occur at
full solution annealing temperatures. However, it should be
appreciated that the gas bearings of the thermal treatment system
300 support the solid-solution-strengthened alloys during annealing
and thus can actually impose and ensure a final shape is maintained
during the higher temperature solution annealing thermal
treatments. Use of a mill annealing heat treatment typically
results in precipitation of secondary carbides on grain boundaries
of material originally supplied in the solution-annealed condition,
and will not normally restore the material to the as-received
condition.
TABLE-US-00001 TABLE 1 Typical Solution Annealing Minimum Mill
Annealing Temperatures (.degree. C.) Temperature (.degree. C.) Co
alloy 1175-1230 1120 Fe-base alloy 1165-1190 1035 Ni1 alloy
1165-1245 1120 Ni2 alloy 1165-1190 1010
[0083] When the solid-solution-strengthened are in the cold or
warm-worked condition, i.e. after cold working of the material,
application of a mill anneal or solution heat thermal treatment by
the thermal treatment system 300 typically alters the
microstructure of the article. The amount of prior cold work in the
article influences the resulting microstructure and mechanical
properties of the article. The results for several combinations of
prior cold work and annealing temperature upon the microstructure
response for sheet of the alloys noted above are shown below in
Table 2.
TABLE-US-00002 TABLE 2 Amount Anneal Resulting ASTM Grain Size** of
Cold Temperature* Co Fe Ni1 Ni2 Work % (.degree. C.) alloy alloy
alloy alloy 0 None 31/2-4 5-6 5-6 4-5 10 1010 N/A NR N/A NR 1065 NR
NR NR NR 1120 NR 5-51/2 NFR 5-7 1175 4-41/2 5-51/2 4-7 N/A 1230
3-41/2 N/A 61/2-7 N/A 15 1065 7 N/A N/A N/A 1120 6-7 N/A N/A N/A
1175 5-7 N/A N/A N/A 1230 3-41/2 N/A N/A N/A 20 1010 N/A NR N/A NFR
1065 7-8 NR NFR NFR 1120 7-8 71/2-81/2 8-81/2 7-8 1175 41/2-7
6-61/2 71/2-8 N/A 1230 21/2-41/2 N/A 7-71/2 N/A 25 1065 71/2-8 N/A
N/A N/A 1120 71/2-8 N/A N/A N/A 1175 4 N/A N/A N/A 1230 31/2 N/A
N/A N/A 30 1010 N/A NFR N/A NFR 1065 N/A 71/2-91/2 8-9 8-10 1120
N/A 7-71/2 9-10 71/2-91/2 1175 N/A 41/2-61/2 81/2-9 N/A 1230 N/A
N/A 6-7 N/A 40 1010 N/A 71/2-91/2 N/A 8-9 1065 N/A 8-91/2 91/2-10
8-10 1120 N/A 7-9 9-10 91/2-10 1175 N/A 41/2-61/2 81/2-9 N/A 1230
N/A N/A 4-7 N/A 50 1010 N/A 9-10 N/A 81/2-10 1065 N/A 81/2-10 9-10
81/2-10 1120 N/A 8-91/2 9-10 81/2-10 1175 N/A 51/2-6 9-91/2 N/A
1230 N/A N/A 51/2-61/2 N/A
[0084] Currently available commercial annealing furnaces for such
alloys have temperature tolerances of +/-15.degree. C. with
tolerances of +/-10.degree. C. obtainable with specialized
equipment. However with the very small gap between the heat sources
and the metallic material article in the thermal treatment system
300, temperature tolerances can be maintained within +/-8.degree.
C., and, in some embodiments, between +/-6.degree. C., +/-4.degree.
C., +/-3.degree. C., +/-2.degree. C., or +/-1.degree. C. at
annealing temperatures up to 1200.degree. C. Accordingly, greater
temperature control provides increased microstructure and
mechanical property control of articles thermally treated with
embodiments of the thermal treatment system disclosed herein.
Nickel Age-Hardenable Alloys
Example 4
[0085] Two Ni-base age-hardenable (also known as precipitation
hardenable or precipitation strengthenable) alloys having the
following nominal chemical compositions (wt %) can be processed
through the metal thermal treatment system 300.
[0086] First Ni-base age-hardenable alloy (NiAH1): 13.5 Co, 2 max
Fe, 19 Cr, 4.3 Mo, 1.5 Al, 3 Ti, 0.08 C, 0.1 max Mn, 0.15 max Si,
0.006 B, 0.1 Cu, 0.05 Zr, with balance Ni (approximately 58 wt %)
and incidental impurities (commercially available as HAYNES.RTM.
Waspaloy alloy).
[0087] Second Ni-base age-hardenable alloy (NiAH2): 16 Cr, 8 Fe,
2.5 Ti, 1 Nb, 0.8 Al, 1 max Co, 0.35 max Mn, 0.35 max Sai, 0.08 max
C, with balance Ni (approximately 70 wt %) and incidental
impurities (commercially available as INCONEL.RTM. X-750 alloy and
HAYNES.RTM. X-750 alloy).
[0088] Ni-base age-hardenable alloys derive most of their strength
from thermal treatments that result in a range of second phase
precipitates in the microstructure. The predominant precipitate is
Ni.sub.3Al (gamma prime). Thermal treatment of such alloys to
provide the precipitation hardened microstructure requires a number
of heating and cooling steps. For example, a typical heat treatment
for the NiAH1 alloy to provide the precipitation hardened
microstructure includes solution annealing the material at
1080.degree. C. for 30 minutes followed by a water quench. Then the
material is subjected to a first precipitation thermal treatment at
995.degree. C. for 2 hours followed by air cooling to room
temperature, then a second precipitation thermal treatment at
845.degree. C. for 4 hours followed by air cooling to room
temperature, and then a third precipitation thermal treatment at
760.degree. C. for 16 hours followed air cooling to room
temperature. The resulting precipitation hardened microstructure
for the NiAH1 provides excellent mechanical properties up to
temperatures approximately 700.degree. C. as shown in Table 3
(tensile test properties) and Table 4 (stress-rupture properties)
below.
TABLE-US-00003 TABLE 3 Ultimate Test Tensile Strength 0.2% Yield
Elongation in Temperature (.degree. C.) (MPa) Strength (MPa) 51 mm
(%) ROOM 1335 910 26.6 650 1195 770 20.8 760 970 770 12.0 870 545
415 12.0 980 220 135 19.4 1095 83 41 36.8
TABLE-US-00004 TABLE 4 Approximate Initial Stress in Test
Temperature MPa to Produce Rupture in: (.degree. C.) 10 Hours 100
Hours 1000 Hours 600 -- -- 660 650 -- 635 550 705 615 515 395 760
495 365 240 815 345 220 130 870 215 125 68 925 120 66 --
[0089] For another example, a typical heat treatment for the NiAH2
alloy to provide the precipitation hardened microstructure includes
solution annealing the material at 1040.degree. C. followed by a
first precipitation thermal treatment at 730.degree. C. for 8 hours
followed by furnace cooling to a second precipitation thermal
treatment at 620.degree. C. for 8 hours followed by air cooling to
room temperature. The resulting precipitation hardened
microstructure for the NiAH2 provides excellent mechanical
properties up to temperatures approximately 700.degree. C. as shown
in Tables 5 and 6 below.
TABLE-US-00005 TABLE 5 Ultimate Test Tensile Strength 0.2% Yield
Elongation in Temperature (.degree. C.) (MPa) Strength (MPa) 51 mm
(%) ROOM 1325 975 23.6 540 1120 860 22.2 650 990 835 5.8 760 650
635 2.5 870 360 295 8.0 980 115 63 42.0
TABLE-US-00006 TABLE 6 Approximate Initial Stress in Test
Temperature MPa to Produce Rupture in: (.degree. C.) 10 Hours 100
Hours 1000 Hours 600 825 585 490 650 550 455 345 705 420 310 200
760 285 180 105 815 165 97 51 870 86 46 -- 925 45 -- --
[0090] Other aspects and advantages will be apparent from a review
of the specification as a whole, the appended claims and Appendix
A.
[0091] The construction and arrangements of the metallic materials
as shown in the various exemplary embodiments, are illustrative
only. Although only a few embodiments have been described in detail
in this disclosure, many modifications are possible (e.g.,
variations in sizes, dimensions, structures, shapes, and
proportions of the various elements, values of parameters, mounting
arrangements, use of materials, orientations) without materially
departing from the novel teachings and advantages of the subject
matter described herein. Some elements shown as integrally formed
may be constructed of multiple parts or elements, the position of
elements may be reversed or otherwise varied, and the nature or
number of discrete elements or positions may be altered or varied.
The order or sequence of any process, logical algorithm, or method
steps may be varied or re-sequenced according to alternative
embodiments. Other substitutions, modifications, changes and
omissions may also be made in the design, operating conditions and
arrangement of the various exemplary embodiments without departing
from the scope of the present inventive technology.
* * * * *