U.S. patent application number 15/653088 was filed with the patent office on 2019-01-24 for composite block bearing and method for manufacture.
The applicant listed for this patent is Fenner U.S., Inc.. Invention is credited to Grant Q. Moyer.
Application Number | 20190024705 15/653088 |
Document ID | / |
Family ID | 65018498 |
Filed Date | 2019-01-24 |
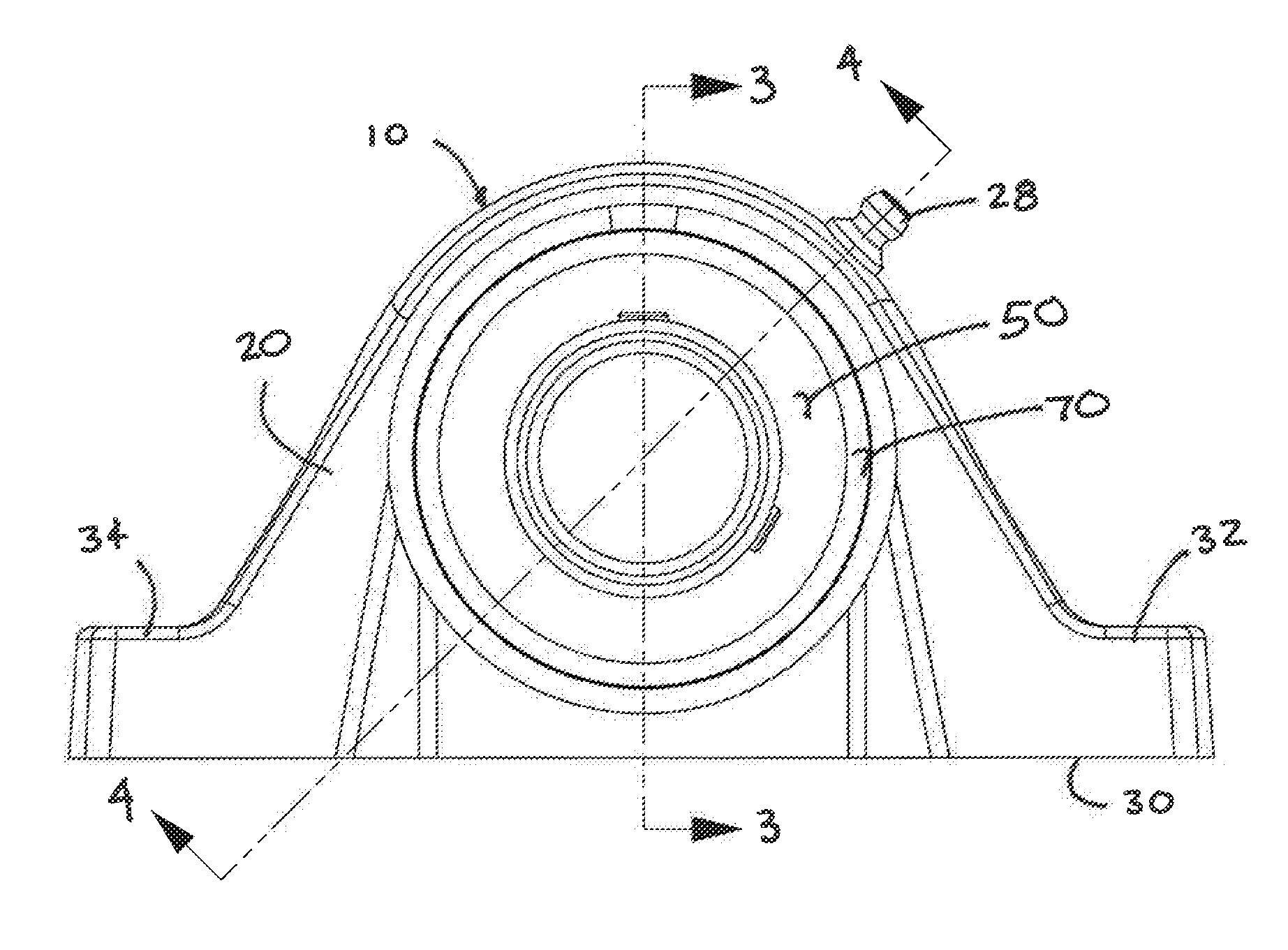
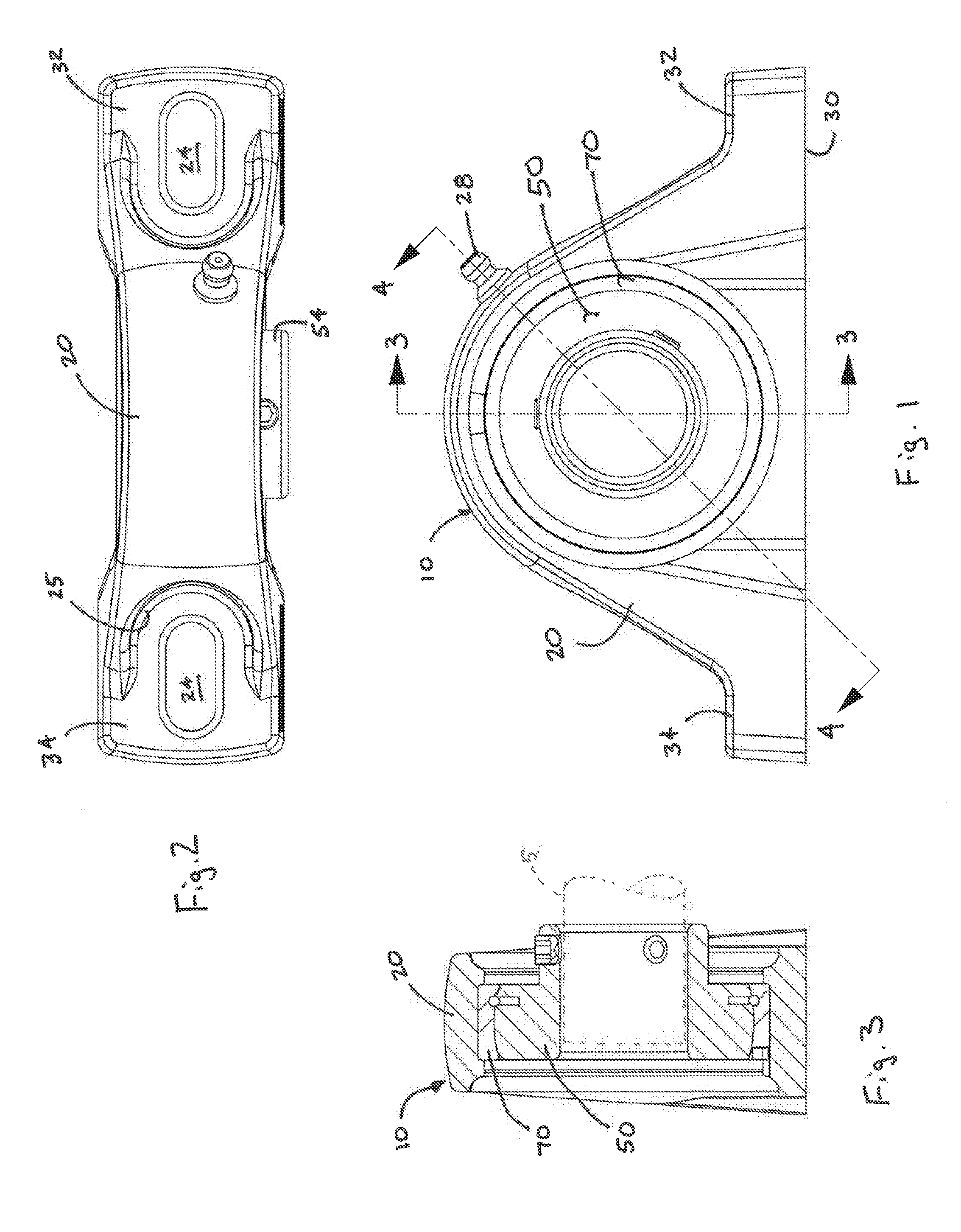

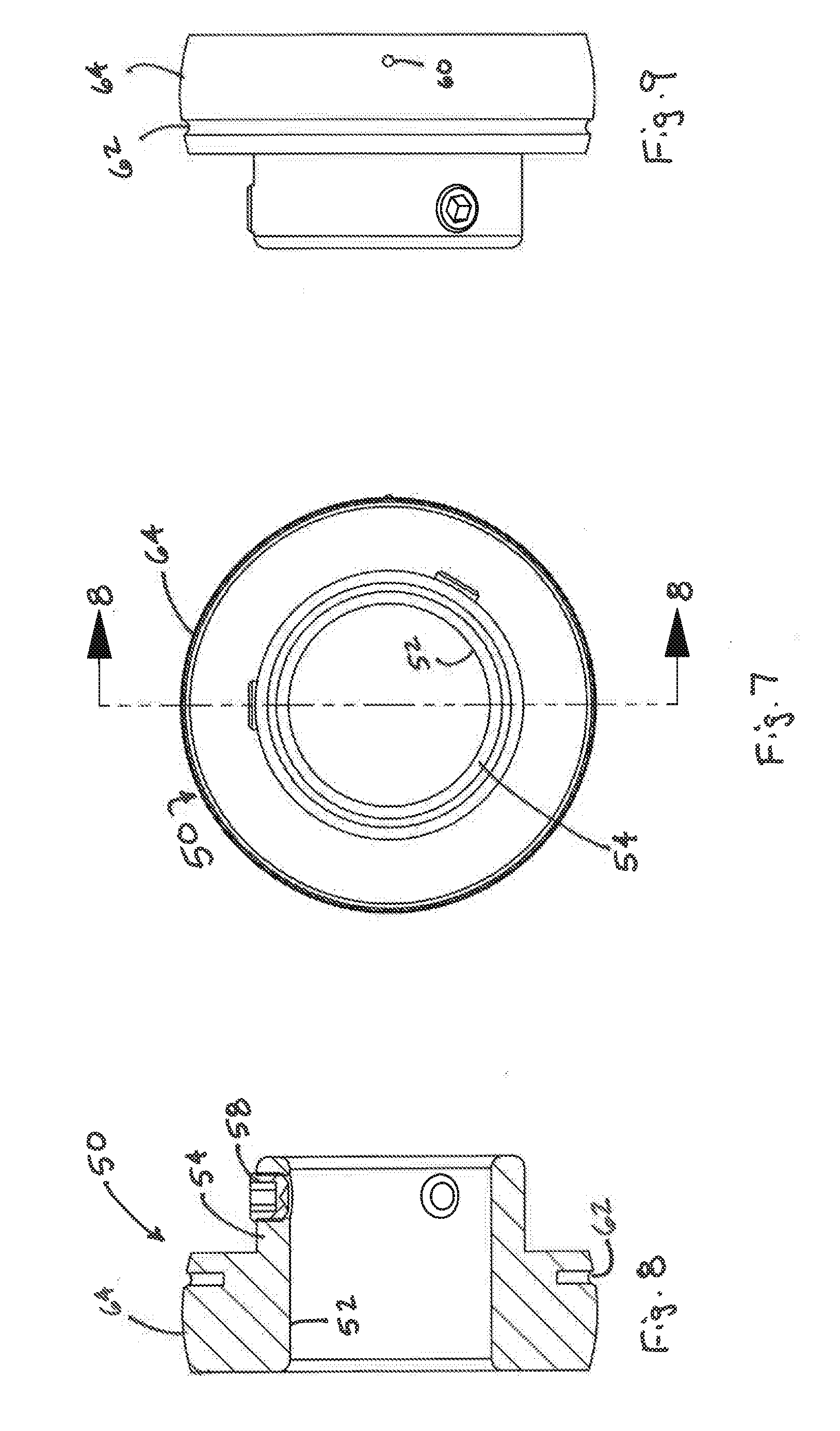
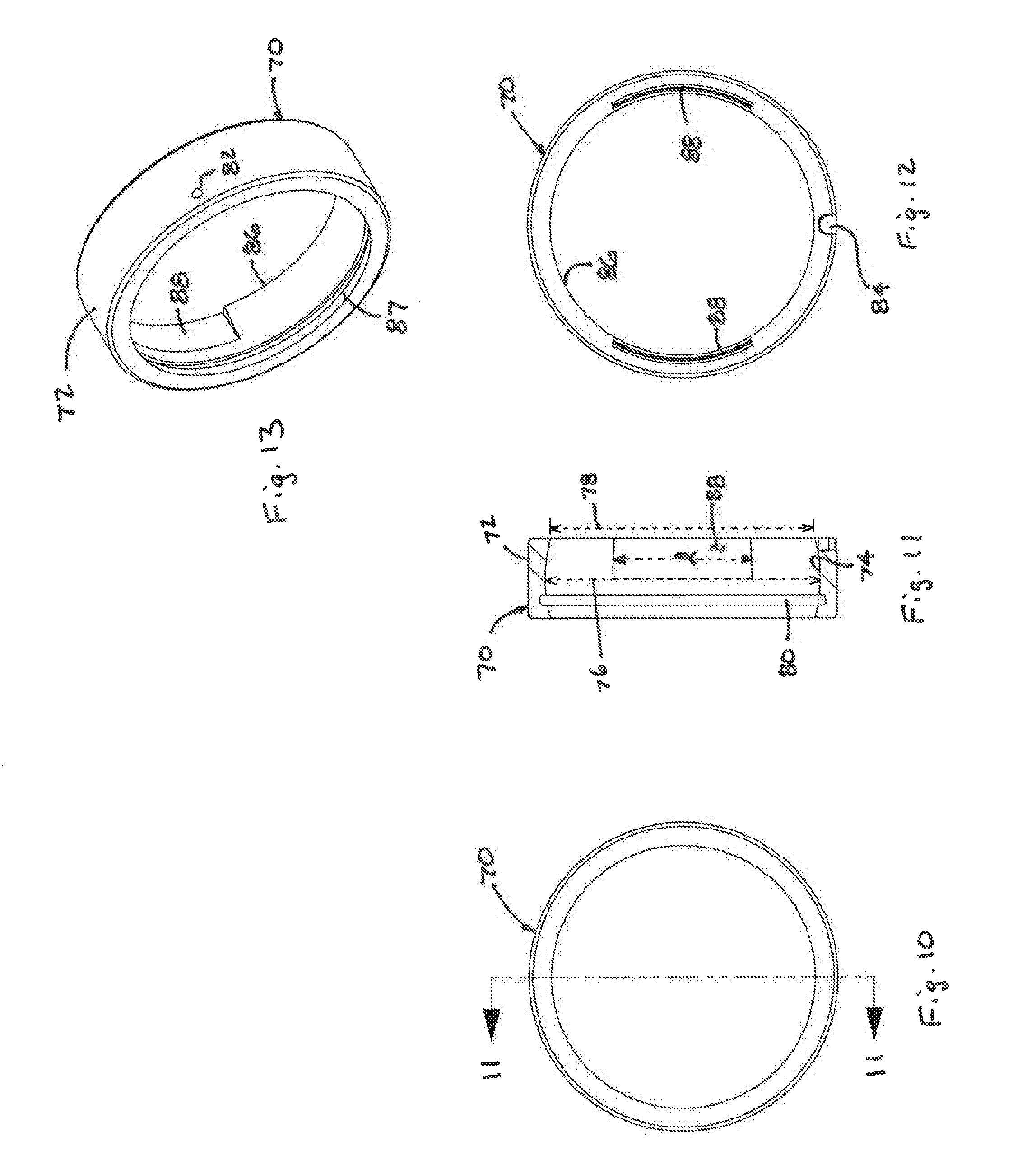
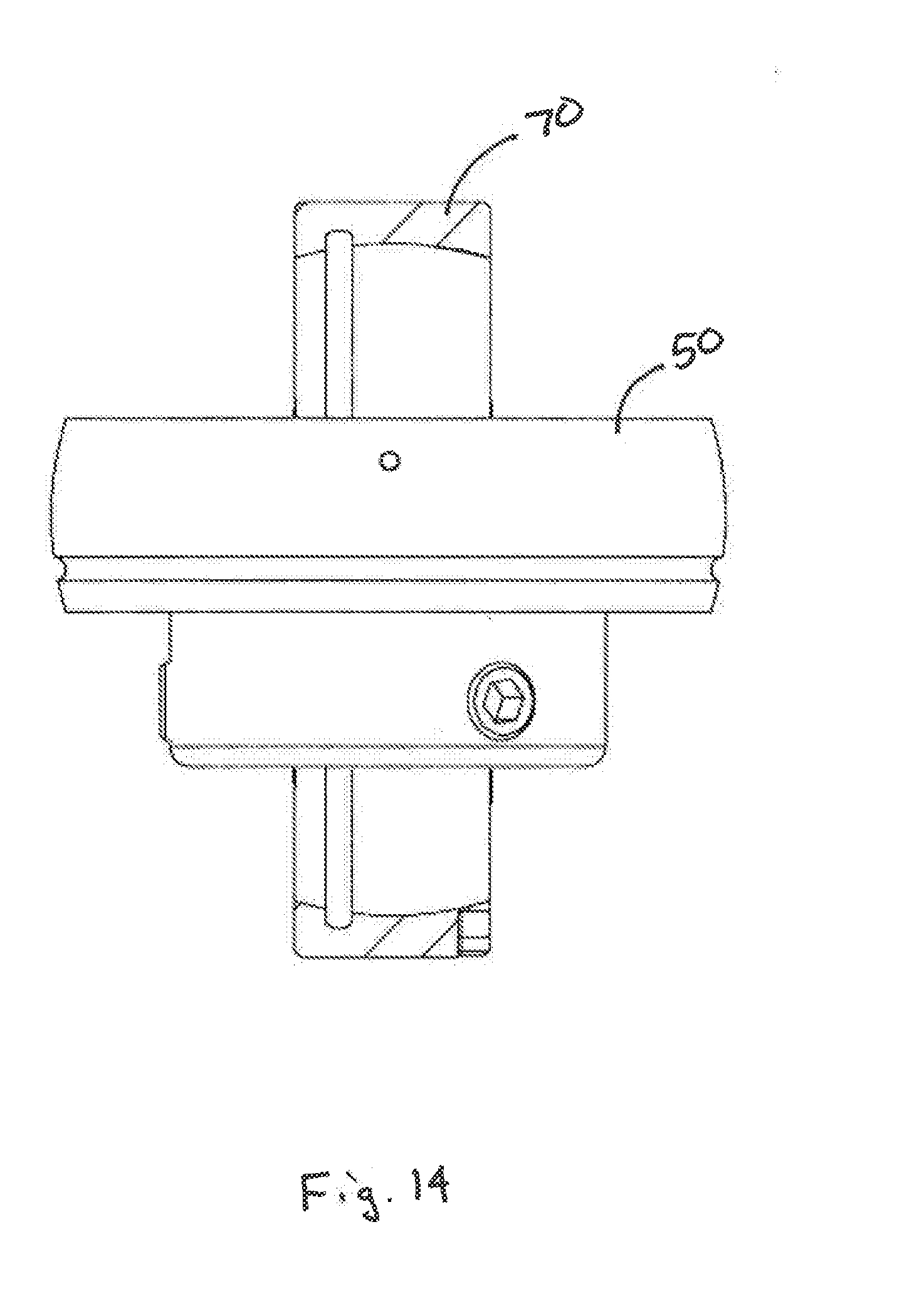
United States Patent
Application |
20190024705 |
Kind Code |
A1 |
Moyer; Grant Q. |
January 24, 2019 |
COMPOSITE BLOCK BEARING AND METHOD FOR MANUFACTURE
Abstract
A bearing assembly and method for making a bearing assembly are
provided. The bearing assembly includes a rotary bearing, a bearing
sleeve and a housing for positioning and retaining the bearing and
the sleeve. The bearing includes a convexly curved exterior surface
and the bearing sleeve includes a concavely curved interior surface
that cooperates with the convexly curve bearing surface. The method
includes the step of forming a bearing sleeve so that it has a
concavely curved interior surface and the step of molding a housing
around the bearing sleeve. The step of molding comprises using a
composite material that comprises a non-metal matrix material and
reinforcing fibers. The method also includes the step of inserting
the bearing into the bearing sleeve after the step of molding so
that a convexly shaped curve of the bearing mates with the concave
curve of the bearing sleeve.
Inventors: |
Moyer; Grant Q.;
(Wilmington, NC) |
|
Applicant: |
Name |
City |
State |
Country |
Type |
Fenner U.S., Inc. |
Manheim |
PA |
US |
|
|
Family ID: |
65018498 |
Appl. No.: |
15/653088 |
Filed: |
July 18, 2017 |
Current U.S.
Class: |
1/1 |
Current CPC
Class: |
F16C 43/02 20130101;
F16C 23/045 20130101; F16C 17/02 20130101; F16C 33/04 20130101;
F16C 35/02 20130101 |
International
Class: |
F16C 17/02 20060101
F16C017/02; F16C 33/04 20060101 F16C033/04; F16C 43/02 20060101
F16C043/02 |
Claims
1. A bearing assembly for supporting a rotatable shaft, comprising:
a rotary bearing rotatable about an axis of rotation and having an
inner race and an outer race, wherein the outer race comprises a
convexly curved surface; a bearing sleeve formed of a first
material and circumscribing the rotary bearing, wherein the bearing
sleeve comprises an exterior surface and an interior surface,
wherein the interior surface comprises a concavely curved surface
configured to cooperate with the convexly curved surface of the
rotary bearing to facilitate relative pivoting motion of the rotary
bearing relative to the bearing sleeve about an axis transverse the
axis of rotation of the rotary bearing; a housing formed of a
second material and having an opening configured to receive the
bearing sleeve and the rotary bearing, wherein the housing
comprises a first retainer configured to restrain the bearing
sleeve against displacement relative to the housing; wherein the
second material is non-metallic and is different than the first
material.
2. The bearing assembly of claim 1 wherein the first material
comprises metal.
3. The bearing assembly of claim 1 or two wherein the second
material is a composite material.
4. The bearing assembly of any of claims 14 wherein the second
material comprises a polymer matrix material and reinforcing
fibers.
5. The bearing assembly of any of claims 14 wherein the housing
comprises one or more mounting elements configured to mount the
housing on a machine.
6. (canceled)
7. The bearing assembly of claim 1 wherein the housing comprises a
second retainer configured to restrain the bearing sleeve against
displacement relative to the housing.
8. The bearing assembly of claim 1 wherein the first retainer
comprises a first annular wall formed within the opening of the
housing projecting radially inwardly toward the axis of rotation of
the bearing.
9. (canceled)
10. The bearing assembly of claim 1 wherein the second retainer
comprises a second annular wall formed within the opening of the
housing projecting radially inwardly toward the axis of rotation of
the bearing.
11. (canceled)
12. The bearing assembly of claim 1 wherein the bearing sleeve
comprises a major interior diameter between a first edge and a
second edge of the bearing sleeve and a minor diameter spaced apart
from the major diameter.
13. (canceled)
14. (canceled)
15. The bearing assembly of claim 12 wherein the concave surface of
the bearing sleeve has a diameter of curvature that is at least 50%
of the exterior diameter of the bearing sleeve.
16. The bearing assembly of claim 12 wherein the concave surface of
the bearing sleeve has a diameter of curvature that is less than
95% of the exterior diameter of the bearing sleeve.
17. (canceled)
18. (canceled)
19. The bearing assembly of claim 12 wherein the bearing sleeve
comprises a wall thickness between the exterior diameter and the
major interior diameter, wherein the concave surface of the bearing
sleeve is configured so that the difference between the major
internal diameter and the minor internal diameter of the sleeve
adjacent the edges is less than half the wall thickness of the
bearing sleeve.
20. (canceled)
21. (canceled)
22. The bearing assembly of claim 12 wherein the bearing sleeve
comprises a lip formed adjacent the minor diameter and at least one
recess formed in the lip to facilitate insertion of the bearing
into the bearing sleeve.
23. The bearing assembly of claim 22 wherein the bearing sleeve
comprises a second recess formed in the lip wherein the two
recesses oppose one another forming a slot to facilitate insertion
of the bearing into the bearing sleeve.
24. The bearing assembly of claim 23 wherein the outer race of the
bearing has a width and the two recesses each has a length that is
greater than the width of the outer race of the bearing.
25. The bearing assembly of claim 22 wherein the at least one
recess has a width that extends from the edge of the bearing sleeve
to the point of the major internal diameter.
26. The bearing assembly of claim 1 wherein the convex curve
substantially continuously curves across the width of the outer
race of the bearing.
27. The bearing assembly of claim 1 wherein the concave curve of
the bearing sleeve substantially continuously curves across the
width of the bearing sleeve.
28. A method for forming a bearing assembly having a rotatable
bearing having an external surface forming a convex curve and an
internal surface configured to receive a rotatable shaft,
comprising the steps of: forming a bearing sleeve having an
interior surface forming a concave curve; molding a housing around
the bearing sleeve, wherein the step of molding comprises molding a
composite material comprising a polymer and reinforcing material;
inserting the bearing into the bearing sleeve, wherein the step of
inserting so that the convexly shaped curve of the bearing mates
with the concave curve of the bearing sleeve.
29. (canceled)
30. The method of claim 28 wherein the step of molding comprises
insert molding.
31. The method of claim 28 wherein the step of forming the bearing
sleeve comprises the step of forming a plurality of recessing in an
edge of the bearing sleeve.
32. The method of claim 31 wherein bearing sleeve comprises a
central axis and the bearing comprises an axis of rotation, wherein
the step of inserting the bearing comprises the step of orienting
the bearing so that the axis of rotation is transverse the central
axis and inserting the bearing into the recesses.
33. The method of claim 32 wherein the step of inserting the
bearing comprises the step of pivoting the bearing relative to the
bearing sleeve after the step of inserting the bearing into the
recesses.
34. The method of claim 33 wherein the step of pivoting the bearing
comprises pivoting the bearing about an axis transverse the central
axis.
35. The method of claim 28 wherein the step of forming a bearing
sleeve comprises forming the bearing sleeve out of metal.
36. The method of claim 28 wherein the step of inserting the
bearing sleeve comprises inserting the bearing into the sleeve so
that the convex surface of the bearing cooperates with the concave
surface of the bearing sleeve to facilitate pivoting of the bearing
relative to the bearing sleeve to facilitate alignment of the
bearing axis of rotation with the axis of rotation of the
shaft.
37. The method of claim 28 wherein the step of molding comprises
molding a composite material comprising a polymer and reinforcing
fibers.
38. The method of claim 28 wherein the step of inserting the
bearing comprises inserting the bearing before the step of molding
the housing around the bearing sleeve.
Description
FIELD OF THE INVENTION
[0001] The present invention relates to a block bearing assembly
and a method for manufacturing the assembly. The device provides a
bearing support for supporting a rotatable element, such as a
rotatable shaft. In particular, the assembly is a composite
assembly including elements formed of molded materials and elements
formed from metal.
BACKGROUND OF THE INVENTION
[0002] The use of a block bearing for rotationally supporting a
shaft is known in the art. Typically, such assemblies incorporate a
cast iron or other metallic housing, which increases the weight and
cost of such assemblies. Accordingly, there is a need for a block
bearing assembly incorporating a non-metal housing that is easily
fabricated and able to withstand the stresses imposed on a block
bearing assembly.
SUMMARY OF THE INVENTION
[0003] In accordance with the present invention, a bearing assembly
for supporting a rotatable shaft is provided. The bearing assembly
includes a rotary bearing rotatable about an axis of rotation. The
outer surface of the bearing comprises a convexly curved surface.
The bearing assembly also includes a bearing sleeve formed of a
first material and circumscribing the rotary bearing. The bearing
sleeve comprises an exterior surface and an interior surface. The
interior surface comprises a concavely curved surface configured to
cooperate with the convexly curved surface of the rotary bearing to
facilitate relative pivoting motion of the rotary bearing relative
to the bearing sleeve about an axis transverse the axis of rotation
of the rotary bearing. The bearing assembly also includes a housing
formed of a second material. The housing is formed of a second
material that is non-metallic and is different from the first
material. The housing includes an opening configured to receive the
bearing sleeve and the rotary bearing. The housing also includes a
first retainer configured to restrain the bearing sleeve against
displacement relative to the housing. For instance, the first
retainer may be an annular wall formed within the housing.
[0004] According to another aspect, the present invention also
provides a method for forming a bearing assembly that includes a
rotatable bearing that has an external surface forming a convex
curve. The rotatable bearing has an internal surface configured to
receive a rotatable shaft and the method includes the step of
forming a bearing sleeve. The bearing sleeve is formed so that it
has an interior surface forming a concave curve. The method also
includes the step of molding a housing around the bearing sleeve.
The step of molding comprises using a composite material that
comprises a non-metal matrix material and a reinforcing material.
For instance, the reinforcing material may be reinforcing fibers.
The method also includes the step of inserting the bearing into the
bearing sleeve so that the convexly shaped curve of the bearing
mates with the concave curve of the bearing sleeve. The step of
inserting the bearing may occur prior to the step of molding.
BRIEF DESCRIPTION OF THE DRAWINGS
[0005] The foregoing summary, as well as the following detailed
description of the preferred embodiments of the present invention,
will be better understood when read in conjunction with the
appended drawings, in which:
[0006] FIG. 1 is a front elevational view of a pillow block
assembly.
[0007] FIG. 2 is a plan view of the pillow block assembly
illustrated in FIG. 1.
[0008] FIG. 3 is a sectional view of the pillow block assembly
illustrated in FIG. 1, taken along line 3-3.
[0009] FIG. 4 is a sectional view of the pillow block assembly
illustrated in FIG. 1, taken along line 4-4.
[0010] FIG. 5 is an enlarged sectional view of a portion of the
pillow block assembly of FIG. 4 designated 5.
[0011] FIG. 6 is a sectional of a housing of the pillow block
assembly illustrated in FIG. 3.
[0012] FIG. 7 is a front elevational view of a bearing of the
pillow block assembly illustrated in FIG. 1.
[0013] FIG. 8 is a sectional view of the bearing illustrated in
FIG. 7, taken along the line 8-8.
[0014] FIG. 9 is a side elevational view of the bearing illustrated
in FIG. 7.
[0015] FIG. 10 is a front elevational view of a bearing sleeve of
the pillow block assembly illustrated in FIG. 1.
[0016] FIG. 11 is a sectional view of the bearing liner illustrated
in FIG. 10, taken along the line 11-11.
[0017] FIG. 12 is a rearward elevational view of the bearing liner
illustrated in FIG. 10.
[0018] FIG. 13 is a perspective view of the bearing liner
illustrated in FIG. 10.
[0019] FIG. 14 is an enlarged side view of the bearing illustrated
in FIG. 7 partially inserted into the bearing liner illustrated in
FIG. 10.
DETAILED DESCRIPTION OF THE PREFERRED EMBODIMENTS
[0020] Referring to the figures in general and to FIGS. 1-3
specifically, a pillow block assembly is designated generally 10.
The pillow block assembly 10 includes a housing 10 that houses a
bearing 50, which is surrounded by a bearing sleeve 70. The pillow
block assembly 10 is configured to mount the bearing assembly 50 to
support a rotatable shaft 5.
[0021] The housing 20 for the pillow block assembly 10 may be
formed of any of a variety of materials. Frequently, the housing is
formed from a metal, such as cast iron. However, in the present
instance, the housing 20 may be formed of a non-metal material. For
instance, the housing may be formed from a polymeric or a composite
material. Exemplary composite materials include materials that have
a polymeric matrix material with a reinforcement element, such as
glass fibers, glass balls or other reinforcing material. For
example, the composite material may be nylon, such as nylon 6/6,
reinforced with glass fibers, such as 33% glass fill. It should be
understood that these examples do not limit the variety of
materials that can be used to form the housing.
[0022] Referring to FIGS. 1-6, the housing 20 comprises a cavity 22
for receiving the bearing 50 and the bearing sleeve 70. The housing
may have any of a variety of shapes depending upon the application
for the device 10. In the present instance, the housing 20 has a
semi-ovate body with a flat base 30 forming a generally planar
surface. The base 30 provides a mounting surface (i.e. a surface
that will abut the surface onto which the housing will be mounted).
A forward portion of the base 30 projects forwardly forming a
forward mounting pad 32. A rearward portion of the base projects
rearwardly forming a rearward mounting pad 34. Mounting holes 24
extend through the forward and rearward mounting pads 32, 34. The
mounting holes 24 are configured to receive a connector, such as a
bolt, for connecting the device 10 to a machine or other surface.
Additionally, the mounting holes may be elongated to allow
adjustment of the housing relative to the connector. As shown in
FIG. 2, the housing may be recessed 25 adjacent the mounting pads
32, 34 to provide clearance for inserting connectors into the
mounting holes 24.
[0023] Referring now to FIG. 6, the details of the recess 22 in the
housing will be described in greater detail. The recess 22 is
configured to receive the bearing 50 and the bearing sleeve 70 as
discussed further below. The cavity 22 in the housing includes a
through bore that extends through the thickness of the housing.
Although a through bore is illustrated, a stopped bore can be used.
The housing is formed to provide one or more retaining elements to
retain the bearing 50 and the bearing sleeve 70 in the housing. For
instance, in the present instance, the housing may include an
annular groove 38 sized to receive the bearing sleeve 70. A first
annular flange or lip 42 may extend around the interior bore of the
cavity 22 adjacent a forward edge of the groove 38 to provide a
forward retaining wall. Similarly, a second annular flange or lip
44 may extend around the interior bore adjacent the rearward edge
of the groove 38 to provide a rearward retaining wall. In this way,
the interior diameter of the groove 38 is greater than the interior
diameter of the forward and rearward retaining walls 42, 44.
Optionally, the housing may include annular ribs 46, 48 that
project radially inwardly from the surface of the retaining walls
42, 44. The annular ribs are narrower than the width of the
retaining walls 42, 44 and form snap surfaces for snapping covers
over the openings of the cavity 22 to impede the migration of dirt
and debris into the housing, thereby limiting the buildup of
contaminants on the bearing 50.
[0024] The housing 20 may also include an opening or port that
extends from the outer surface of the housing into the interior of
the cavity 22 as illustrated in FIGS. 4 and 5. A grease port 28,
such as a zerk fitting may be mounted into the access port to
facilitate applying lubrication to the bearing as discussed further
below.
[0025] Referring now to FIGS. 7-9, the details of the bearing 50
will be described in greater details. The bearing may be formed of
any of a variety of bearing elements, including but not limited to
ball bearings, roller bearings, needle bearings and plain bearings.
The embodiment illustrated in FIGS. 1-9 incorporates an insert
bearing that includes radial bearings. The interior diameter of the
bearing forms a cylindrical bore configured to receive the outer
diameter of a shaft 5. In the present instance, the interior
diameter is formed by an inner race 52 of the bearing. The exterior
diameter of the bearing forms a convex surface as shown in FIGS.
8-9. In the present instance, the exterior diameter is formed by
the outer race 64 of the bearing. The convex surface is a
substantially continuously curved surface from the major diameter
of the outer race to the edges of the outer race 64. However, as
shown in FIGS. 8 and 9, a circumferential groove 62 may extend
around the exterior surface of the outer race to provide a groove
for the dispersion of lubrication. As shown in FIG. 8, one or more
recesses may extend radially inwardly into the bearing from the
circumferential groove 62.
[0026] The bearing may be configured to be connected to the shaft 5
in any of a variety of ways. In the present instance, the bearing
incorporates a locking mechanism for locking the shaft 5 onto the
bearing. In particular, the inner race 52 of the bearing 50
comprises an extended collar or ring that extends axially (i.e.
parallel to the axis of rotation) to provide a locking hub or stem
54. As shown in FIGS. 8-9 the locking hub 54 extends outwardly from
the edge of the outer race 64. The locking hub 54 may also include
a locking element for releasably locking the locking hub to the
shaft 5. For instance, the locking hub may include one or more set
screws 58.
[0027] Referring now to FIGS. 10-13, the details of the bearing
sleeve 70 will be described in greater detail. The bearing sleeve
70 is configured to nest within the housing cavity 22 and
circumscribe the bearing 50. The sleeve 70 may be formed from any
of a variety of materials, including, polymeric, metal or composite
materials. In the present instance, the sleeve can be formed from
any of a variety of metals, such as sintered iron or machined steel
rod. The exterior surface of the outer sleeve is configured to mate
with and/or cooperate with the interior surface of the cavity 22 in
the housing. For instance, in the embodiment illustrated in FIGS.
10-13, the exterior surface of the bearing sleeve is substantially
cylindrical to nest in the annular groove 38 in the housing.
However, the exterior surface of the bearing sleeve 70 may have any
of a variety of shapes and the cavity 22 may be formed to cooperate
with and/or mate with such shapes.
[0028] The bearing sleeve 70 has a diameter and a width; and the
diameter is larger than the width of the sleeve. Further still, the
sleeve diameter may be substantially larger than the width of the
sleeve. For example, the sleeve diameter may be at least 50%
greater than the width of the sleeve. Further, the sleeve diameter
may be at least 100% greater than the width of the sleeve. In some
applications the sleeve may be more than 300% greater than the
width of the sleeve. In this way, the sleeve diameter may be 50% to
300% greater than the width of the sleeve. For example, in an
exemplary embodiment, the sleeve may be approximately 2.3 inches
(approx. 58 mm) in diameter and approximately 5/8 inches (approx.
15 mm) wide.
[0029] The interior surface of the bearing sleeve 70 may be
configured in any of a variety of shapes. For example, the interior
surface of the sleeve 70 may be substantially cylindrical. In the
embodiment illustrated in FIGS. 10-13, the inner surface 74 of the
bearing sleeve 70 is concave. In this way, the interior surface 74
cooperates with and/or mates with the exterior surface of the outer
race 64 of the bearing 50. Specifically, the interior surface 74 of
the bearing sleeve forms a substantially continuously curving
concave surface. The apex of the convex curve is intermediate the
two edges. In this way, the interior diameter of the sleeve 70 has
a major diameter 76 intermediate the sides of the sleeve. In the
embodiment illustrated in FIG. 11, the major diameter 76 is
positioned at the midpoint between the edges of the sleeve so that
the convex surface is substantially mirrored about the midpoint of
the sleeve. The sleeve also comprises a minor diameter 78 adjacent
one or both of the edges of the sleeve. In the embodiment shown in
FIG. 11, since the concave curve is substantially constant about
the midpoint of the sleeve, the inner diameter at each edge of the
sleeve is substantially the same and forms the minor diameter 78 of
the sleeve. Accordingly, the inner diameter of the sleeve adjacent
the edges is less than the inner diameter of the sleeve at a
midpoint of the sleeve, thereby forming a reduced diameter lip at
one or both of the open ends of the sleeve. In FIG. 13 a lip at the
first end of the sleeve is designated 86 and a lip at the opposite
end of the sleeve is designated 87.
[0030] As noted above, the curvature of the concave interior
surface 74 may be a continuously curved surface. The curvature may
be configured so that the diameter of curvature of the concave
surface is at least 50% of the exterior diameter of the sleeve.
Additionally, the diameter of curvature of the concave surface may
be less than approximately 95% of the exterior diameter of the
sleeve. In some applications, the diameter of curvature may be
approximately 90% of the exterior diameter of the sleeve and in
some applications, the diameter of curvature may be approximately
80% of the exterior diameter of the sleeve. Similarly, the
curvature of the concave curve may be configured so that the
difference between the major internal diameter and the minor
internal diameter of the sleeve adjacent the edges is less than
half the wall thickness of the sleeve 70 (where the wall thickness
is the difference between the major diameter and the external
diameter of the sleeve). Similarly, the curvature of the concave
curve may be configured so that the difference between the major
internal diameter and the minor internal diameter is more than 10%
of the wall thickness of the sleeve. Additionally, the curvature of
the concave curve may be configured so that the difference between
the major internal diameter and the minor internal diameter is more
than 20% of the wall thickness of the sleeve.
[0031] Referring against to FIG. 11, the bearing sleeve 70 may also
include an annular groove 80 formed in the interior surface 74.
Additionally, the sleeve 70 may include a fluid passage or port 82
through the thickness of the sleeve, intersecting the groove 80.
The groove 80 and the port 82 form a fluid path for lubrication to
lubricate the bearing 50.
[0032] Referring to FIG. 11-13, the bearing sleeve 70 may also
include one or more recesses or pockets 88 that extend through the
lip 86 at the edge of the sleeve. As discussed further below, the
recesses 88 provide clearance through the lip 86 for inserting the
bearing 50 into the sleeve 70. In the embodiment illustrated in
FIGS. 11-13, the bearing sleeve includes a pair of recesses 88
spaced equidistantly around the circumference of the sleeve so that
the recesses oppose one another as shown in FIG. 12. The recesses
88 have a width that extends from the edge of the sleeve to a point
at or adjacent the major diameter 76 of the sleeve. The length of
each recess 88 (designated "e" in FIG. 12) extends a length at
least as great as the width of the outer race 64 of the bearing.
The depth of the recess tapers from generally flush with the
midpoint of the sleeve (i.e. essentially zero depth) to a maximum
depth at the edge of the sleeve. The maximum depth is approximately
equal to or greater than the difference between the major diameter
76 and the minor diameter 78. In this way, the recesses 88 extend
through the lip 86 of the sleeve.
[0033] Referring to FIGS. 11 and 12, the bearing sleeve 70 may also
include an optional recess 84 formed at one of the edges of the
bearing sleeve. The recess 84 may be used as an alignment element
to align the bearing sleeve in a mold as discussed further
below.
[0034] When configured as discussed above, the device 10 provides a
bearing assembly for providing rotational support for a shaft 5.
The bearing assembly 10 includes a housing 20 having mounting
elements for attaching the bearing assembly to another element,
such as a machine. The housing 20 is formed of a first material and
the bearing 50 is mounted in a sleeve 70 formed of a second
material that is different from the first material. In the present
instance, preferably the first material is a non-metallic material
and preferably the second material is a metallic material.
[0035] The bearing 50 is mounted within the sleeve 70 so that
annular groove 80 in the sleeve aligns with and/or overlies the
circumferential groove 62 of the bearing 50. Additionally, the
grease port 82 in the bearing sleeve 70 aligns with the zerk
fitting 28 in the housing so that grease can injected into the
bearing through the zerk fitting, which then flows through the
lubrication groove 80 in the sleeve and the lubrication groove 62
in the bearing.
[0036] The bearing 50 is mounted within the bearing sleeve 70 so
that the exterior surface of the bearing is moveable relative to
the interior surface of the sleeve 70. In particular, preferably
the bearing 50 is pivotable relative to the sleeve 70 about an axis
that is transverse the axis of rotation of the shaft 5 and the
bearing. More specifically, as illustrated in FIG. 3 the shaft 5 is
supported by the bearing such that the axis of rotation of the
shaft and the axis of rotation of the bearing are parallel to the
planar base 30. However due to alignment issues, the shaft may be
disposed at an angle relative to the planar base 30. With the shaft
skewed relative to the planar base, the axis of rotation of the
bearing may be skewed relative to the shaft. Accordingly, the
bearing 50 may pivot relative to the sleeve 70 to align the shaft
axis with the axis of rotation of the bearing. For instance, the
bearing 50 may pivot clockwise or counter-clockwise relative to
FIG. 3 (about an axis normal to the plane of FIG. 3).
[0037] In the foregoing discussion, the bearing assembly 10 is
described as being connected to and rotationally supporting a first
end of a shaft 5. It should be understood that a second bearing
assembly 10 may be provided at the second end of the shaft to
rotationally support the second end of the shaft so that the shaft
is supported between opposing bearing assemblies 10. Alternatively,
one end of the shaft 5 may be supported by the bearing assembly 10
and the second end of the shaft may be support by a different
assembly. For instance, the second end of the shaft may be driven
by a drive element.
Method of Manufacture
[0038] As noted above, the bearing assembly 10 may comprise a
housing formed of a non-metal material. Accordingly, the following
method describes a method for producing the bearing assembly 10
with a non-metal housing. It should be understood that the bearing
assembly may be formed in a variety of processes and is not limited
to fabrication according to the following methodology.
[0039] A method for producing the bearing assembly 10 includes the
step of forming the housing 20 by molding the housing 20. For
instance, the housing may be formed by molding, such as injection
molding. Prior to molding the housing, the bearing sleeve 70 is
inserted into the mold so that the housing is molded around the
bearing sleeve. In this way, the housing is formed so that the
bearing sleeve is substantially fixedly connected with the housing.
In particular, the housing is insert molded so that the bearing
sleeve is captured in the annular groove 38 in the cavity 22
between the forward and rearward retaining flanges 42, 44.
Accordingly, the retaining flanges 42, 44 act as stops to prevent
axial displacement of the bearing sleeve relative to the
housing.
[0040] Additionally, as noted previously, the housing 20 may
include a grease nipple, such as a zerk fitting 28. The zerk
fitting 28 may also be inserted into the mold prior to forming the
housing. Additionally, the bearing sleeve may include an alignment
element to properly orient the bearing sleeve relative to the
housing. Specifically, the alignment recess 84 may be aligned with
an alignment tab in the mold so that the grease port 82 in the
sleeve is aligned with the zerk fitting 28. In this way, the
housing is formed around the zerk fitting and the bearing sleeve to
provide a continuous fluid path from the fitting into the interior
of the bearing sleeve. Alternatively, the mold may be formed so
that an access port is provided through the housing and the zerk
fitting may be connected to the housing after the step of molding
the housing. Further still, the access port may be machined into
the housing after the housing is molded.
[0041] Referring to FIGS. 12 and 14, before the housing 20 is
formed around the bearing sleeve 70, the bearing 50 is mounted into
the bearing sleeve. The minor diameter 78 of the bearing sleeve is
smaller than the exterior diameter of the bearing 50 at the apex of
the convex outer surface of the outer race 64. Accordingly, the
bearing 50 is not pressed directly into the sleeve (i.e. such that
the axis of rotation of the bearing is aligned with the central
axis of the sleeve). Instead, the edge of the bearing is aligned
with the recesses 88 in the side of the bearing sleeve 70.
Specifically, the bearing 50 is oriented so that the diameter of
the bearing is parallel with or aligned with the opening that
extends from the first recess 88 to the opposing recess. In this
orientation, the bearing 50 is disposed so that the axis of
rotation of the bearing is transverse the central axis of the
sleeve (which is parallel to the axis of the shaft 5 shown in FIG.
3). In this orientation, the bearing 50 is inserted into the sleeve
70 until the major exterior diameter of the bearing is at or
adjacent the major interior diameter 76 in the sleeve. In the
present instance, the major diameter of the bearing 50 is at the
midpoint of the exterior surface of the bearing, so that the
bearing is inserted into the sleeve until half of the bearing is in
the sleeve as shown in FIG. 14. The bearing is then rotated
clockwise from the perspective of FIG. 14 to mount the bearing into
the sleeve.
[0042] It will be recognized by those skilled in the art that
changes or modifications can be made to the above-described
embodiments without departing from the broad inventive concept of
the invention. For instance, in the foregoing description the
assembly is illustrated and described as a pillow block bearing. In
a pillow block bearing the axis of rotation of the bearing (i.e.
the axis of rotation of the shaft mounted in the bearing) is in a
plane parallel to the plane of the mounting surface for the housing
of the pillow block bearing. In contrast, a flange assembly, a
bearing block assembly and a take up block assembly each
incorporates a housing with a bearing mounted within the housing
configured to be mounted in a plane that may not be parallel to the
axis of rotation of the bearing. Accordingly, the invention is not
limited to pillow block bearings and instead includes various
bearing assemblies regardless of the angle of the mounting plane of
the housing relative to the axis of rotation of the shaft.
Additionally, in the foregoing description the bearing is described
as being assembled into the bearing sleeve prior to forming the
housing. However, it should be understood that the bearing sleeve
may be insert molded into the housing and then the bearing may be
assembled into the sleeve after the housing is formed around the
sleeve. It should therefore be understood that this invention is
not limited to the particular embodiments described herein but is
intended to include all changes and modifications that are within
the scope and spirit of the invention as set forth in the following
claims.
* * * * *