U.S. patent application number 16/027924 was filed with the patent office on 2019-01-03 for sulfur nanosponge cathode for lithium-sulfur battery and methods of manufacture thereof.
The applicant listed for this patent is Massachusetts Institute of Technology. Invention is credited to Akihiro KUSHIMA, Ju LI, Junjie NIU, Chao WANG.
Application Number | 20190006663 16/027924 |
Document ID | / |
Family ID | 55631251 |
Filed Date | 2019-01-03 |
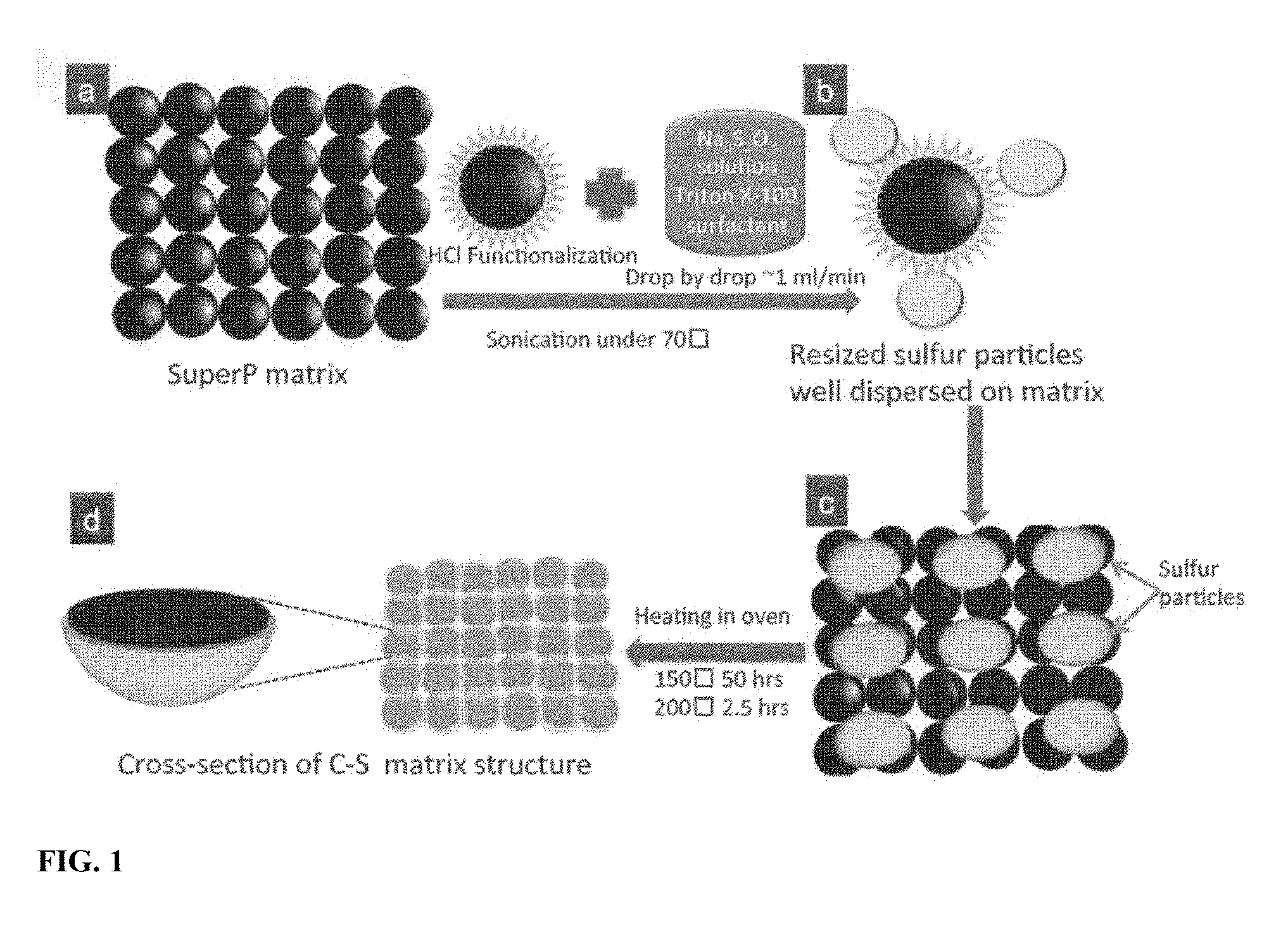


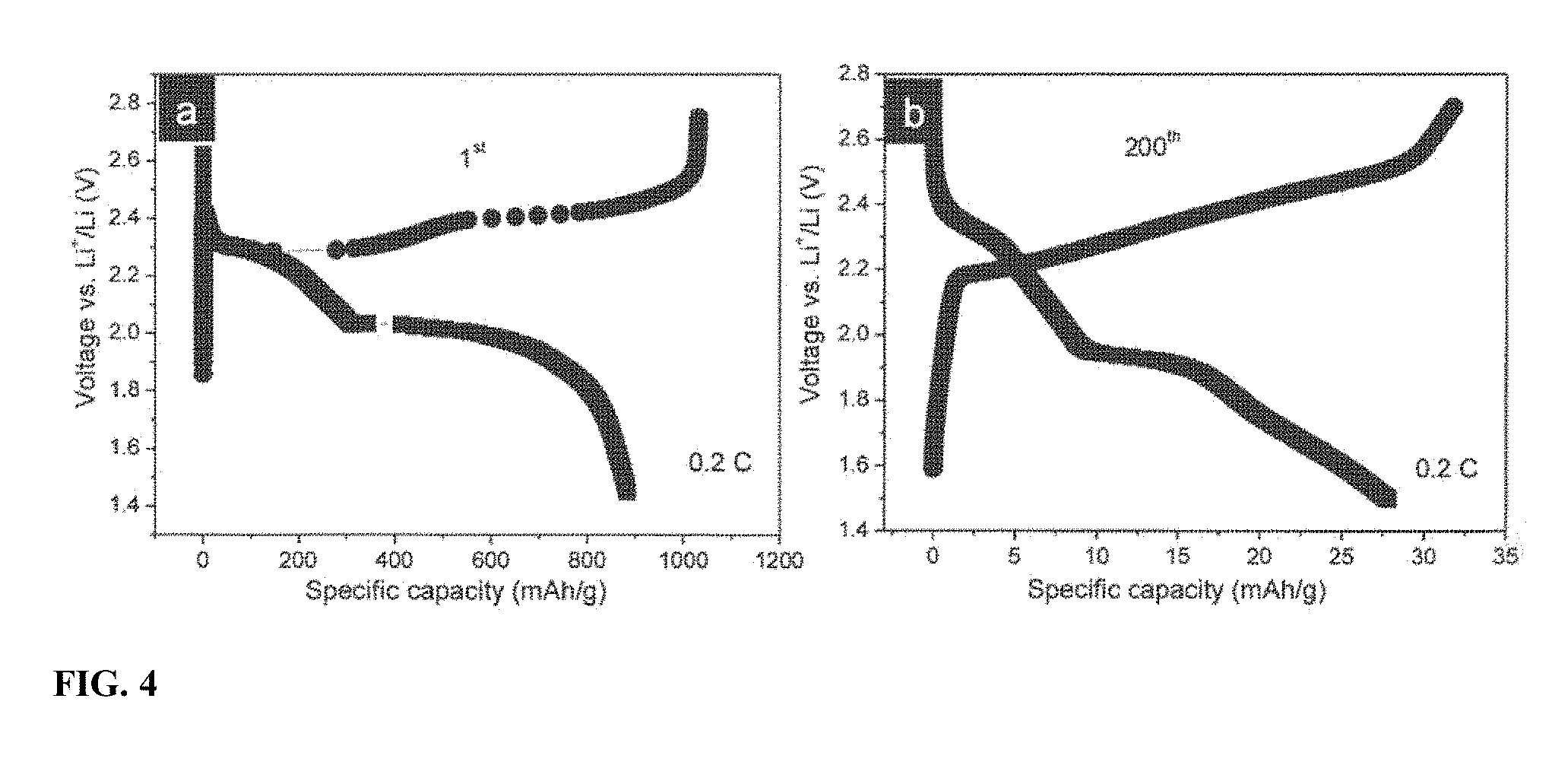

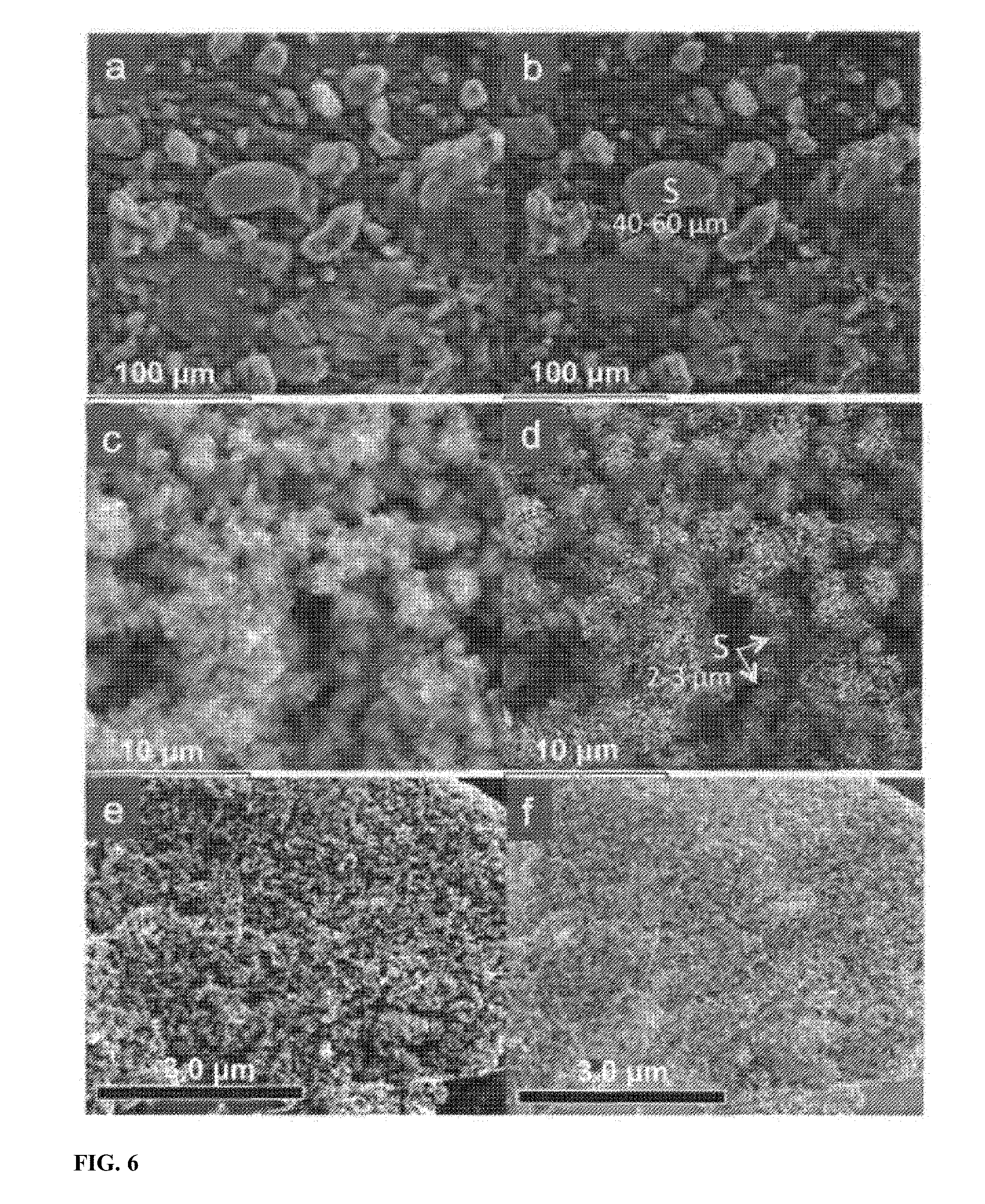



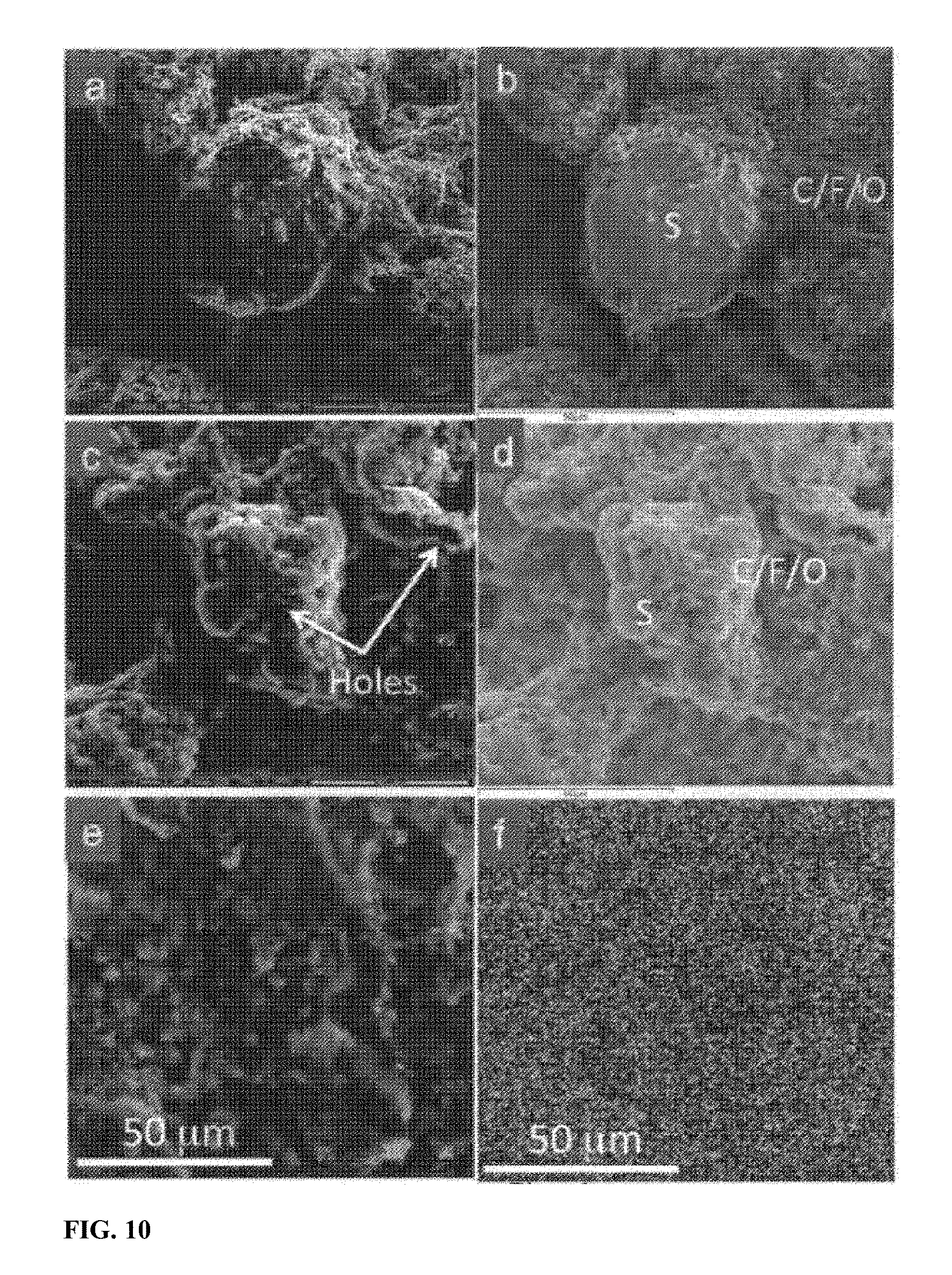
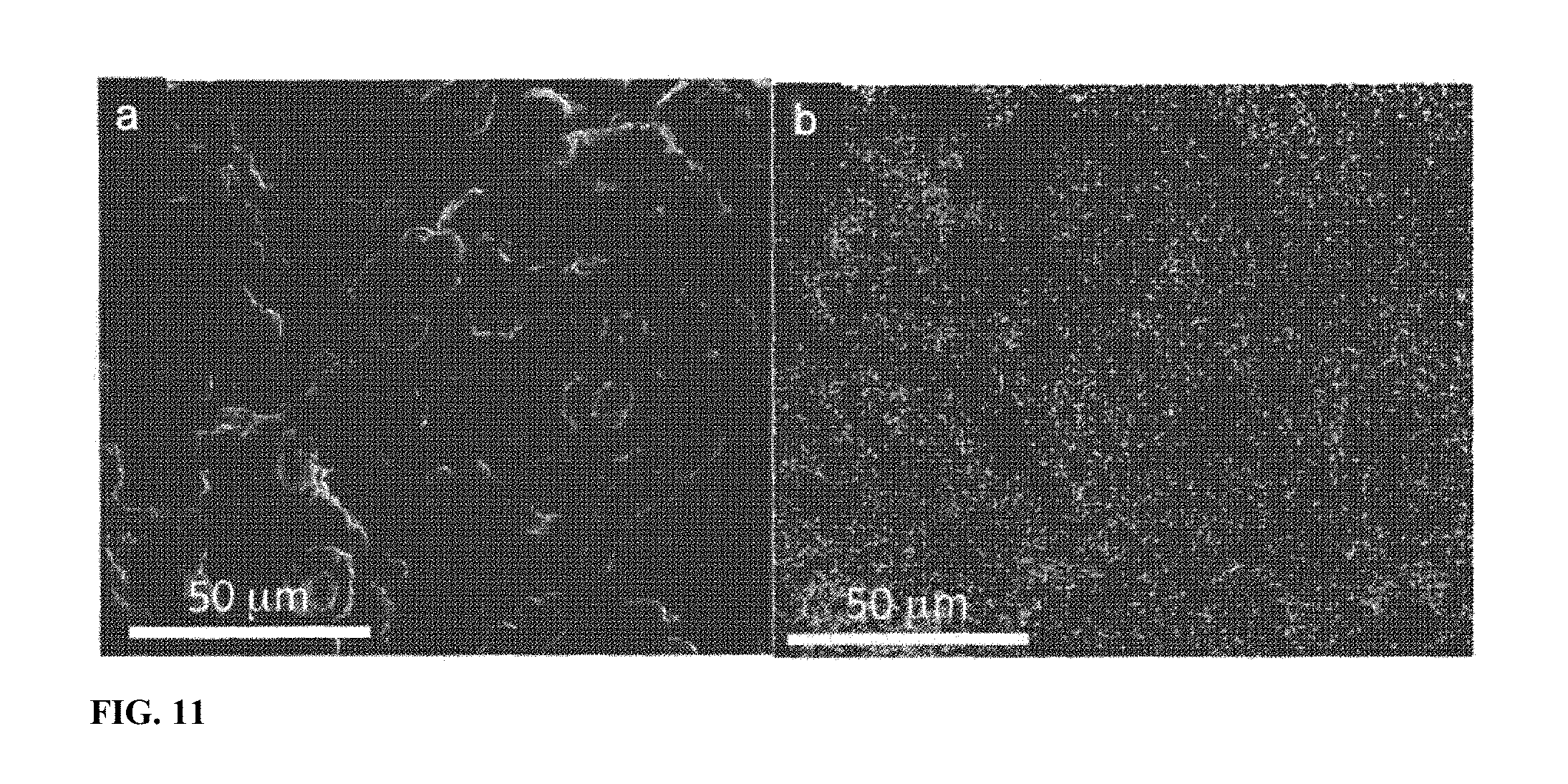
View All Diagrams
United States Patent
Application |
20190006663 |
Kind Code |
A1 |
NIU; Junjie ; et
al. |
January 3, 2019 |
SULFUR NANOSPONGE CATHODE FOR LITHIUM-SULFUR BATTERY AND METHODS OF
MANUFACTURE THEREOF
Abstract
The present invention is directed to lithium-sulfur batteries
exhibiting a high capacity, high cycle life with low production
cost and improved safety.
Inventors: |
NIU; Junjie; (Malden,
MA) ; KUSHIMA; Akihiro; (Arlington, MA) ;
WANG; Chao; (Cambridge, MA) ; LI; Ju; (Weston,
MA) |
|
Applicant: |
Name |
City |
State |
Country |
Type |
Massachusetts Institute of Technology |
Cambridge |
MA |
US |
|
|
Family ID: |
55631251 |
Appl. No.: |
16/027924 |
Filed: |
July 5, 2018 |
Related U.S. Patent Documents
|
|
|
|
|
|
Application
Number |
Filing Date |
Patent Number |
|
|
14853610 |
Sep 14, 2015 |
10033034 |
|
|
16027924 |
|
|
|
|
62049685 |
Sep 12, 2014 |
|
|
|
Current U.S.
Class: |
1/1 |
Current CPC
Class: |
H01M 4/587 20130101;
Y02T 10/70 20130101; H01M 4/386 20130101; H01M 4/366 20130101; H01M
4/624 20130101; H01M 2004/028 20130101; H01M 2300/0028 20130101;
H01M 4/0402 20130101; H01M 2220/20 20130101; H01M 4/625 20130101;
H01M 4/136 20130101; H01M 10/052 20130101; H01M 10/0569 20130101;
H01M 10/0525 20130101; H01M 10/0568 20130101; Y02E 60/10 20130101;
H01M 4/38 20130101; H01M 2220/30 20130101; H01M 4/387 20130101 |
International
Class: |
H01M 4/36 20060101
H01M004/36; H01M 10/052 20100101 H01M010/052; H01M 4/136 20100101
H01M004/136; H01M 4/38 20060101 H01M004/38; H01M 10/0569 20100101
H01M010/0569; H01M 10/0568 20100101 H01M010/0568; H01M 10/0525
20100101 H01M010/0525; H01M 4/04 20060101 H01M004/04; H01M 4/62
20060101 H01M004/62; H01M 4/587 20100101 H01M004/587 |
Goverment Interests
GOVERNMENT SUPPORT
[0002] This invention was made with government support under
Contract No. FA9550-08-1-0325 awarded by the U.S. Air Force and
Contract No. DMR-1120901 awarded by the National Science
Foundation. The government has certain rights in the invention.
Claims
1. A cathode comprising a nanostructured sponge having a
sulfur-covering-carbon structure prepared by a method comprising:
functionalizing the surface of conductive carbon black particles,
thereby forming hydroxyl and/or carboxyl groups on the surface of
the conductive carbon black particles; dispersing a mixture
comprising sulfur particles and at least one surfactant in a matrix
of the functionalized conductive carbon black particles; and
heating the dispersed sulfur particles and functionalized
conductive carbon black particles for a time and to a temperature
above the melting point of sulfur, whereby the sulfur forms a
coating over the functionalized conductive carbon black particles
to form the nanostructured sponge having the sulfur-covering-carbon
structure.
2. The cathode of claim 1, comprising sulfur-carbon clusters
smaller than about 10 .mu.m.
3. A lithium battery comprising an anode, the cathode of claim 1,
and an electrolyte.
4. The lithium battery of claim 3, wherein the anode is selected
from the group consisting of carbon, silicon, silicon/carbon
composite, lithium titanate, and tin cobalt alloy.
5. The lithium battery of claim 3, wherein the electrolyte is
selected from the group consisting of electrolyte containing
lithium salts and combination of linear and cyclic carbonates.
6. A nanostructured sponge cathode comprising: a conductive carbon
black matrix and sulfur, wherein the sulfur is disposed over the
conductive carbon black particles to provide a sulfur-over-carbon
structure.
7. The nanostructured sponge cathode of claim 6, wherein the
particle size of said conductive carbon black particles ranges from
80 nm to 800 nm.
8. The nanostructured sponge cathode of claim 6, wherein the sulfur
is substantially amorphous.
9. The nanostructured sponge cathode of claim 6, further comprising
a conductive polymer.
10. The nanostructured sponge cathode of claim 9, wherein the
conductive polymer comprises polypyrrole.
11. The nanostructured sponge cathode of claim 6, wherein the
amount of sulfur ranges from about 50 to about 70 wt. %.
Description
CROSS-REFERENCE TO RELATED APPLICATION(S)
[0001] This application is a divisional application of U.S.
application Ser. No. 14/853,610, filed Sep. 14, 2015, and entitled
"SULFUR NANOSPONGE CATHODE FOR LITHIUM-SULFUR BATTERY AND METHODS
OF MANUFACTURE THEREOF," which claims the benefit under 35 U.S.C.
.sctn. 119(e) of U.S. Application No. 62/049,685, entitled
"Scalable Synthesis of Sulfur Nanosponge Cathode for Lithium-Sulfur
Battery with Greatly Improved Cyclability," and filed on Sep. 12,
2014, which application is hereby incorporated by reference
herein.
BACKGROUND
[0003] The surging demand for rechargeable batteries in portable
electronics and electric vehicles has stimulated extensive studies
on various lithium-based electrode materials. Sulfur is a
well-researched material that is nontoxic to the environment and
earth-abundant. It can host two lithium ions (Li.sup.+)
non-topotactically, and exhibits a high theoretical capacity of
1675 mAh/g, almost 10 times that of commercially popular transition
metal based intercalating cathode materials, such as LiCoO.sub.2.
In terms of gravimetric energy density, at 2.1 V versus
Li/Li.sup.+, lithium-sulfur (Li--S) batteries possess about 5 times
the energy density compared to those based on LiCoO.sub.2.
[0004] However, sulfur and its insoluble by-product compounds, such
as Li.sub.2S.sub.2 and Li.sub.2S, are poor electronic and ionic
conductors (electronic insulators), which significantly reduces the
effectiveness of Li--S batteries. Furthermore, these deficiencies
necessitate positioning sulfur-based electrodes in constant and
intimate contact with liquid electrolyte to enhance effective
Li.sup.+ conductivity, which otherwise leads to a rapid degradation
of capacity and cycle life. In addition, the capacity of
conventional Li--S batteries rapidly decay with the number of
charge/discharge cycles due to rapid dissolution of soluble lithium
polysulfides Li.sub.2S.sub.x (4.ltoreq.x.ltoreq.8) into interfacial
bulk liquid electrolyte, and/or via volume expansion-induced
mechanical failures within the electrode structures that couple
with and led to degrading electronic conductivity across the
electrode. To retard the loss of S into the electrolyte solution,
many strategies have been proposed and undertaken, such as
modifying the electrolyte to be a poorer solvent for sulfur
species, and engineering a better electrode and operating voltage
of the electrochemical system, as described, for example, in the
articles by Z. Lin, Z. C. Liu, W. J. Fu, N. J. Dudney and C. D.
Liang, in Angewandte Chemie International Edition, 2013, 52,
7460-7463; by E. Peled, Y. Sternberg, A. Gorenshtein and Y. Lavi,
in the Journal of the Electrochemical Society, 1989, 136,
1621-1625; by S. E. Cheon, K. S. Ko, J. H. Cho, S. W. Kim, E. Y.
Chin and H. T. Kim, in the Journal of the Electrochemical Society,
2003, 150, A800-A805; by L. X. Yuan, J. K. Feng, X. P. Ai, Y. L.
Cao, S. L. Chen and H. X. Yang, in Electrochemistry Communications,
2006, 8, 610-614; by J. H. Shin and E. J. Cairns, in the Journal of
Power Sources, 2008, 177, 537-545; by Z. W. Seh, W. Li, J. J. Cha,
G. Zheng, Y. Yang, M. T. McDowell, P.-C. Hsu and Y. Cui, in Nature
Communications, 2013, 4, 6; by J. Wang, S. Y. Chew, Z. W. Zhao, S.
Ashraf, D. Wexler, J. Chen, S. H. Ng, S. L. Chou and H. K. Liu, in
Carbon, 2008, 46, 229-235; and by Y. S. Su, Y. Z. Fu, T. Cochell
and A. Manthiram, in Nature Communications, 2013, 4, 2985.
`Solvent-in-Salt` electrolytes with ultrahigh salt concentration
can also be used to achieve a high-energy rechargeable battery, for
example as described in the articles by L. M. Suo, Y. S. Hu, H. Li,
M. Armand and L. Q. Chen, in Nature Communications, 2013, 4; and by
Y. Sun, L. Zhao, H. L. Pan, X. Lu, L. Gu, Y. S. Hu, H. Li, M.
Armand, Y. Ikuhara, L. Q. Chen and X. J. Huang, in Nature
Communications, 2013, 4. Strategies for inhibiting undesirable
polysulfide dissolution reactions via modifying the charging
condition were developed to obtain improved cycle life (>500
cycles), and additives like graphene, mesoporous carbon, and
conductive polymers were exploited to facilitate efficient electron
conduction, as described in the articles by H. L. Wang, Y. Yang, Y.
Y. Liang, J. T. Robinson, Y. G. Li, A. Jackson, Y. Cui and H. J.
Dai, in Nano Letters, 2011, 11, 2644-2647; by M. K. Song, Y. G.
Zhang and E. J. Cairns, in Nano Letters, 2013, 13, 5891-5899; by N.
Jayaprakash, J. Shen, S. S. Moganty, A. Corona and L. A. Archer, in
Angewandte Chemie International Edition, 2011, 50, 5904-5908; by Y.
Z. Fu and A. Manthiram, in the Royal Society of Chemistry Advances,
2012, 2, 5927-5929; by X. Liang, Y. Liu, Z. Y. Wen, L. Z. Huang, X.
Y. Wang and H. Zhang, in the Journal of Power Sources, 2011, 196,
6951-6955; by H. K. Song and G. T. R. Palmore, in Advanced
Materials, 2006, 18, 1764; by J. L. Wang, J. Yang, J. Y. Xie and N.
X. Xu, in Advanced Materials, 2002, 14, 963; and by Y. Yao, N. Liu,
M. T. McDowell, M. Pasta and Y. Cui, in Energy & Environmental
Science, 2012, 5, 7927. By encapsulating sulfur in TiO.sub.2
nanoshells with pre-existing void, the .about.80% volume expansion
of sulfur in lithiation can be accommodated and this yolk-shell
structure can also restrict the intermediate polysulfides to reside
within the structure, so the battery could run over 1000 cycles
with good capacity retention, as described in Z. W. Seh, W. Li, J.
J. Cha, G. Zheng, Y. Yang, M. T. McDowell, P.-C. Hsu and Y. Cui, in
Nature Communications, 2013, 4, 6. However, although recent
technological progress has been made in Li--S battery performance
according to G. Y. Zheng, Y. Yang, J. J. Cha, S. S. Hong and Y.
Cui, in Nano Letters, 2011, 11, 4462-4467, manufacturing such
improved Li--S battery system at mass-production levels, employing
a scalable and cost-effective synthesis is still yet to be
demonstrated, until the present invention.
SUMMARY
[0005] In some embodiments described herein, a method of
manufacturing is disclosed comprising functionalizing the surface
of conductive carbon black particles, thereby forming hydroxyl
and/or carboxyl groups on the surface of the conductive carbon
black particles, dispersing a mixture comprising sulfur particles,
and at least one surfactant in a matrix of the functionalized
conductive carbon black particles, and heating the dispersed sulfur
particles and functionalized conductive carbon black particles for
a time and to a temperature above the melting point of sulfur,
whereby the sulfur forms a coating over the functionalized
conductive carbon black particles to form a nanostructured sponge
having a sulfur-covering-carbon structure. In another embodiment,
the method of functionalizing comprises contacting the conductive
carbon black particles with acid. In another embodiment, the sulfur
particles are formed in-situ in the functionalized conductive
carbon black by reducing a water-soluble sulfur-containing
compound. In another embodiment, heating is at a temperature
ranging from about 150 to about 200.degree. C. In another
embodiment, the sulfur coating is no thicker than 1 micron. In
another embodiment, the method of heating is carried out for a time
ranging from about 2 to about 50 hours. In another embodiment, the
conductive carbon black particles have a BET surface area ranging
from about 40 m.sup.2/g to about 80 m.sup.2/g. In another
embodiment, the method of dispersing comprises agitating in an
aqueous solution, conductive carbon black particles, an acid, a
surfactant and thiosulfate, whereby the thiosulfate forms sulfur
particles and the conductive carbon black particles are surface
functionalized in situ. In other embodiments, the method further
comprises isolating and drying the mixture of functionalized
conductive carbon black particles and sulfur particles. In another
embodiment, a cathode comprises a nanostructured sponge having a
sulfur-covering-carbon structure prepared by the methods disclosed
herein. In some embodiments, a lithium battery comprises an anode,
the cathode as prepared by the methods described herein, and an
electrolyte. In another embodiment, the lithium battery contains an
anode selected from the group consisting of carbon (graphite,
graphene, hard carbon, mesoporous carbon, etc. and any combination
thereof), silicon, silicon/carbon composite, lithium titanate (LTO,
Li.sub.4Ti.sub.5O.sub.12, etc.), and tin cobalt alloy. In another
embodiment, the lithium battery contains an electrolyte selected
from the group consisting of electrolyte containing lithium salts
(e.g., LiPF.sub.6, LiBF.sub.4 or LiClO.sub.4) and combinations of
linear and cyclic carbonates (e.g., ethylene carbonate, dimethyl
carbonate or poly(oxyethylene)).
[0006] In some other embodiments, a nanostructured sponge cathode
is disclosed which comprises a conductive carbon black matrix and
sulfur, wherein the sulfur is disposed over the conductive carbon
black particles to provide a sulfur-over-carbon structure. In
another embodiment, the nanostructured sponge cathode contains the
particle size of said conductive carbon black particles ranges from
80 nm to 800 nm. In another embodiment, the sulfur of the
nanostructured sponge cathode is substantially amorphous. In
another embodiment, the nanostructured sponge cathode comprises a
conductive polymer. In another embodiment, the nanostructured
sponge cathode includes the conductive polymer comprising
polypyrrole. In another embodiment, the nanostructured sponge
cathode contains sulfur whose amount ranges from about 50 wt. % to
about 70 wt. %. In another embodiment, the nanostructured sponge
cathode comprises sulfur-carbon clusters smaller than about 10
.mu.m.
BRIEF DESCRIPTION OF THE DRAWINGS
[0007] The skilled artisan will understand that the drawings
primarily are for illustrative purposes and are not intended to
limit the scope of the inventive subject matter described herein.
The drawings are not necessarily to scale; in some instances,
various aspects of the inventive subject matter disclosed herein
may be shown exaggerated or enlarged in the drawings to facilitate
an understanding of different features. In the drawings, like
reference characters generally refer to like features (e.g.,
functionally similar and/or structurally similar elements). All
documents disclosed herein are incorporated by reference in the
entirety for all purposes.
[0008] FIG. 1 is a schematic of manufacturing process flow for
in-situ synthesis of sulfur nanosponge (SULFUN) cathode matrix.
[0009] FIG. 2 shows discharge voltage profiles of SULFUN (a)
treated at 200.degree. C. with 2.5 hours with a charge rate of 0.2
C; cycling performance of commercial pure sulfur, mortar milled S/C
mixture, and SULFUN treated at 200.degree. C. for 2.5 hours (b);
and at 150.degree. C. for 50 hours (c) at a charge rate of 0.2
C.
[0010] FIG. 3 Comparable cycling performance of the pure sulfur and
SULFUN matrix treated at 200.degree. C. for 2.5 hours at a rate of
0.2 C. The inset is the enlarged cycling profile. This sample was
synthesized using the complete method as in FIG. 2b.
[0011] FIG. 4 Charge/discharge voltage profiles of the mortar
milled S/C mixture coin cells after cycling at 0.2 C. The 1.sup.st
a) and the 200.sup.th b) cycles.
[0012] FIG. 5 Charge/discharge voltage profiles of the SULFUN coin
cells after cycling at 0.2 C. Samples annealed at 200.degree. C.
a-b) and at 150.degree. C. c-d).
[0013] FIG. 6 are SEM images and the corresponding
Energy-dispersive X-ray spectroscopy (EDS) mappings. SEM
morphologies of the milled S/C mixture (a), before (c) and after
(e) annealed at 200.degree. C. with 2.5 hours. (b), (d), and (f)
are sulfur and carbon mappings of the areas shown in (a), (c), and
(e), respectively.
[0014] FIG. 7 SEM imaging of as-synthesized pure sulfur without
carbon a), SULFUN matrix treated at 150.degree. C. for 50 hours b),
and 200.degree. C. for 2.5 hours c). Scale bar is 1 .mu.m.
[0015] FIG. 8 EDS maps and electron microscopy images of the SULFUN
matrix. a) SEM morphology of the matrix annealed at 150.degree. C.
with 50 hours. Carbon b) and sulfur c) mappings of the area shown
in a). d) Sulfur and carbon mapping of as-received SULFUN matrix
before heating. TEM imaging of the SULFUN before e) and after f)
heating at 200.degree. C. with 2.5 hours. Scale bar in e) and f): 5
.mu.m.
[0016] FIG. 9 TGA profiles and DTA curves recorded in argon with a
heating rate of 10.degree. C. min.sup.-1, for SULFUN matrices
treated at 150.degree. C. with 50 hours a) and 200.degree. C. with
2.5 hours b), respectively.
[0017] FIG. 10 shows morphological evolution of commercial sulfur
particle and SULFUN during charge/discharge. SEM morphologies of
the commercial sulfur mixture with Super P and binder before (a)
and after two cycles (c). (b) and (d) are EDS Element maps of the
areas shown in (a) and (c), respectively. (e) shows SEM morphology
of the electrode made of SULFUN annealed at 200.degree. C. for 2.5
hours after two cycles with corresponding sulfur elemental maps
(f).
[0018] FIG. 11 SEM image and EDS maps of the commercial cathode
electrode after running two cycles. a) SEM morphology of the
electrode. b) The corresponding sulfur element map.
[0019] FIG. 12 shows cross-section images of the electrode after
two charge/discharge cycles. SEM images and the corresponding EDS
elemental maps of the cross-section of the electrode made of
commercial sulfur (a) and SULFUN (b). The elemental map data
indicate that the electrolyte was suppressed by the SULFUN surface
instead of the commercial sulfur.
[0020] FIG. 13 SEM image and the corresponding EDS element map of
the cross-section of the electrode made of SULFUN after
charging/discharging two cycles (different sample with FIG. 5b).
The dashed white shows the boundary between the newly formed carbon
layer and the electrode film.
[0021] FIG. 14 shows a schematic illustration of reaction mechanism
during charging and discharging. (a) illustrates that a sulfur
particle generates holes and cracks due to the anisotropic
reaction. Commercial sulfur particle shows a much larger
Scontact/Vs ratio (b) compared to the compact SULFUN matrix (c),
which greatly delays the loss of sulfur during electrochemical
reaction.
[0022] FIG. 15 Illustration of the reaction mechanism during the
charging and discharging. a) The commercial sulfur particle
exhibits more pathways of lithium polysulfide/electrolyte contact,
while b), the generated carbon-rich layer reduces the solid
(matrix)/liquid (electrolyte) interface thus prevents the major
loss of active material sulfur.
[0023] FIG. 16 shows electrochemical cycling performance of
modified SULFUN coin-cell batteries at (a) C-rate of 0.2 and (b)
C-rate of 2.0. (a) also shows Coulombic efficiency at 0.2
C-rate.
[0024] FIG. 17 shows XRD patterns of raw sulfur, annealed
sulfur-carbon matrices, and the SULFUN matrix after 7
charge/discharge cycles ending in charging.
[0025] FIG. 18 SEM images and energy-dispersive X-ray spectroscopy
(EDS) maps of the sulfur-carbon matrix. (a) SEM morphology of the
sulfur-carbon matrix before annealing at 200.degree. C. for 2.5
hours. (b) Sulfur and carbon EDS map of area shown in (a). (c) SEM
morphology of the sulfur-carbon matrix after annealing at
200.degree. C. for 2.5 hours. (d)-(f) Sulfur and carbon EDS map of
area shown in (c).
[0026] FIG. 19 EDS maps and TEM images of the sulfur-carbon matrix.
(a) SEM morphology of the matrix annealed at 150.degree. C. for 50
hours. (b) carbon map of the area shown in (a). (c) sulfur map of
the area shown in (a). (d) sulfur and carbon map of as-receive
sulfur-carbon matrix before heating. (e) TEM image of the
sulfur-carbon matrix before heating at 200.degree. C. for 2.5
hours. (f) TEM image of the sulfur-carbon matrix after heating at
200.degree. C. for 2.5 hours. Scale bar in (e) and (f) is 5
.mu.m.
DETAILED DESCRIPTION
[0027] The description provided herein describes a method of
production with novel processing steps described in detail, as well
as novel sulfur containing cathodes, and Li batteries comprising
such cathodes. The various embodiments provide a cheap and simple
approach to manufacture sulfur-based electrodes with carbon
additives for high-capacity lithium ion batteries with long cycle
life. All documents disclosed herein are incorporated by reference
in their entirety for all purposes.
[0028] In various embodiments, the present invention comprises
liquid-based, low-cost and reliable synthetic methods for
lithium-sulfur composite cathodes containing an open network of
conductive carbon black nanoparticles (Cnet), infused with sulfur
(Snet) to form sponge-like networks (Cnet+Snet). Without limitation
to a specific mechanism, it is believed that Snet has open access
to the outside, allowing liquid electrolyte to infiltrate and
impart Snet Li.sup.+ conductivity. During lithiation, Cnet
accommodates the volume expansion of Snet without substantially
losing electrical contact due to the interconnected nature of the
network. During delithiation, the carbon nanoparticles flocculate
on the outer surface of the composite due to depletion of sulfur by
polysulfide dissolution, to form a passivation layer that still
allows Li.sup.+ exchange, but preferentially slows down the loss of
sulfur into the bulk electrolyte liquid. By using an extra carbon
deposition layer to provide a carbonaceous passivation layer,
improved performance is provided, i.e., about 400 mAh/g of
discharge specific capacity after 250 cycles under a high C-rate
2.0. A 763 mAh/g discharge specific capacity for this sulfur
nanosponge cathode (abbreviated as "SULFUN") was obtained after 100
cycles under a C-rate of 0.2. 520 mAh/g and 290 mAh/g discharge
capacities were attained after 300 and 500 cycles,
respectively.
[0029] As described in some embodiments, commercially available
Conductive Carbon Blacks (such as Super P.RTM.) are used in a
facile wet-chemistry method to synthesize a sulfur-carbon
nanosponge. One of the purposes is to enhance cyclability by using
the evolving microstructure of sulfur-carbon nanosponge during
lithiation and delithiation process to help delay the loss of
active sulfur ions. This approach utilizes cheap carbon black as
the base matrix to construct a sulfur-covering-carbon sponge,
instead of utilizing the traditional carbon-wrapping-sulfur
geometry. Even though sulfur is not coated over the carbon in the
beginning prior to first lithiation, the nanosponge structure of
the composite synthesized using the described method can reduce
sulfur loss during cycling.
[0030] To construct a well-blended matrix, a three-step process was
developed: 1) Conductive Carbon Blacks such as Super P.RTM. were
first functionalized by an acid such as hydrochloric acid, as shown
in FIG. 1a. The carbon nanoparticles of .about.70 nm in diameter
adhere to each other, forming a percolating electrical network
(Cnet, FIG. 1a); 2) The in-situ formed small sulfur particles
surrounded with surfactants were dispersed in the solution with
Super P using a redox reaction (e.g., disproportionation of
thiosulfate under acidic conditions) under agitation, such as
ultrasonic or mechanical agitation (FIG. 1b-c); The ultrasonic
agitation breaks apart carbon particle agglomerations, enabling
in-situ formation of small sulfur-carbon clusters (2-4 .mu.m), as
shown in FIG. 6c-d. For comparison, a well-mixed S/C composite
prepared via mortar milling without sonication displays separate,
flat sulfur flakes with much larger sizes of 40-60 .mu.m (FIG. 6b).
3) With heating at an annealing temperature of 150.degree. C. or
200.degree. C., the distributed sulfur was melted and deeply
infiltrated into the framework and spread across the carbon
surface, to form a sulfur-covering-carbon configuration, which is
the other percolating network (Snet) (FIGS. 1d and 6e-f). Cnet and
Snet interpenetrate each other and are in intimate contact, forming
a nanostructured sponge which we call SULFUN. During
lithiation/delithiation, the sponge-like structure of Cnet has the
ability to "breath" to accommodate .about.80% volume expansion of
Snet without losing electrical contact, according to the porosity
calculation SULFUN has a different initial topology (Cnet+Snet,
with both initially open to the outside) from the known
carbon-wrapping-sulfur approach where the intent is to completely
encapsulate and isolate the sulfur.
In-Situ Synthesis of Sulfur-Carbon Sponge Matrix
[0031] Details of the in-situ synthesis of Sulfur-Carbon sponge
matrix are as follows. In one embodiment 70 wt % (according to the
approximate loading in the final S--C matrix) Conductive Carbon
Blacks (Super C65, Timical) was first treated in a solution mixed
with 20 ml hydrochloric acid (1 N volumetric solution, Avantor
Performance Materials, Inc.) under stirring on a hot plate
(Super-Nuova, Thermo Scientific) for 2 hours at 70.degree. C. Then
100 ml deionized water was added. Meanwhile, sodium thiosulfate
(anhydrous, 99%, Alfa Aesar) was dissolved in 150 ml deionized
water with surfactant Triton X-100 (1% in deionized water, Alfa
Aesar).sup.17. Then, the sodium thiosulfate solution was added into
the Conductive Carbon Blacks solution with a dropping speed of
.about.1 mL/min under an ultrasonic agitation (Symphony, VWR
Ultrasonic Cleaner) at a constant temperature of 70.degree. C. The
reacted sample was centrifuged (IEC HN-SII Centrifuge, Damon/IEC
Division) and dried at 60.degree. C. in an oven (Symphony, VWR).
Finally, the dried mixture was annealed at temperatures of
150.degree. C. for 50 hours ("low-temperature") or 200.degree. C.
for 2.5 hours ("high-temperature") in air, respectively. The
collected samples were stored for coin cell assembly and battery
performance test.
[0032] It will be recognized by the skilled artisan that a variety
of commercially available conductive carbon blacks, in suitable
amounts, can be employed, such as Akzo Nobel's Ketjenblack family
of carbon blacks or Cabot Corporation's LITX.TM. family of carbon
blacks. In addition, other mineral acids such as sulfuric, nitric,
etc. could be employed.
[0033] For comparison, 80 wt % commercial sulfur (Sulfur powder,
99.5%, Alfa Aesar), 10 wt % Super P and 10 wt % binder were
uniformly milled for 30 minutes in a mortar. After the milling, the
mixture was applied to make a slurry on Al foil and then the final
coin cell was assembled using a same protocol.
Characterizations of Morphology, Chemical Composition, and
Structure
[0034] SEM: The surface morphologies were evaluated using a
FEI/Philips XL30 FEG Environmental Scanning Electron Microscope
(ESEM) and JEOL 6320 Field-Emission High-Resolution SEM at 5-10 kV
incident energy. The carbon-sulfur elemental mapping was obtained
through energy-dispersive spectroscopy microanalysis using an INCA
EDS detector at 20 kV acceleration voltage.
[0035] TEM: The in-situ formed sulfur and S--C sponge treated at
different annealing temperatures were characterized by transmission
electron microscopy (TEM) using a JEOL JEM-2010F at an accelerating
voltage of 200 kV. The TEM sample was dispersed on a lacy carbon
film supported on a copper grid to acquire the images. In order to
reduce electron-beam damage, a low magnification with weak beam
intensity was applied when the images were captured.
[0036] TGA: Thermal gravimetric analysis (TGA, SEIKO SSC/5200
TG/DTA220 thermal analysis station) and differential scanning
calorimetry curves were recorded in argon as working gas. The
temperature program was set to be isothermal at 50.degree. C. for
10 min and heated up to 650.degree. C. with a heating rate of
10.degree. C. min'.
[0037] Battery performance of SULFUN was measured via coin cells,
which were assembled inside a glove box. SULFUN was used as the
cathode while a Li foil served as the anode, in an electrolyte of
1.0 M lithium bis-trifluoromethanesulfonylimide (LiTFSI) in
1,3-dioxolane (DOL) and 1,2-dimethoxyethane (DME) (DOL:DME=1:1 in
volume). Because the Snet is initially open to the outside, the
LiTFSI+DOL+DME liquid electrolyte wets and infiltrates Snet in the
initial lithiation, dissolving some sulfur and forming some soluble
lithium polysulfides. The "wet" Snet then has some significant
Li.sup.+ conductivity that percolates within Cnet.
[0038] FIG. 2a depicts an initial discharge specific capacity of
.about.1100 mAh/g at a 0.2 C rate (C rate is calculated based on
the theoretical capacity 1675 mAh/g of sulfur). Two main plateaus
appear in the discharging window of 2.5 to 1.5 V (FIG. 2a). The
first plateau (I) centering at .about.2.3 V corresponds to the
sequential reduction of sulfur (S.sub.8) to high-order polysulfides
Li.sub.2S.sub.X (4.ltoreq.X.ltoreq.8). During the complex
reactions, a series of soluble lithium polysulfides are generated.
As illustrated in the discharge curve, this plateau is quite short,
which only presents a minor capacity of .about.165 mAh/g (about 15%
of the overall 1100 mAh/g). Then there is a short transition (II),
which contributes a small portion .about.146 mAh/g (.about.13%) as
well. A big plateau (III) is located at .about.2.06 V, which is
attributed to the continuous conversion of Li.sub.2S.sub.X
(4.ltoreq.X.ltoreq.8) to low order Li.sub.2S.sub.2 and Li.sub.2S.
In this last step, sulfur is reduced to the final state of
insoluble Li.sub.2S, as described by C. Barchasz, F. Molton, C.
Duboc, J. C. Lepretre, S. Patoux and F. Alloin in Analytical
Chemistry, 2012, 84, 3973-3980. The dominance of this reaction is
evidenced by the long plateau which constitutes a major portion
(.about.64%) of the total capacity. Although the insoluble sulfides
can increase the volume and the electrical resistance, plenty of
interlinked carbon nanoparticles maintain good electron conduction
paths to ensure uninterrupted lithiation/delithiation. In other
words, Cnet is mechanically robust enough and has nano-pore-like
configuration (Specific surface area: >70 m.sup.2/g) with
flexibility that it can accommodate the .about.80% volume change of
Snet by unfolding, while maintaining good electrical conductivity
and contact with Snet. Otherwise the cycling performance would
degrade very rapidly, which was indeed the case historically.
[0039] Shown in FIG. 2b is the cycling capability of SULFUN cathode
annealed at 200.degree. C. With a charging/discharging rate of 0.2
C, a specific discharge capacity as high as .about.763 mAh/g was
retained after running 100 cycles. After 300 cycles, a .about.520
mAh/g capacity was still retained, which implies less than 0.2%
decay for each cycle (FIG. 2b). The capacity was maintained at a
high level of .about.290 mAh/g even at the 500.sup.th cycle. A
long-cyclability coin cell made of the same matrix is shown in FIG.
3, demonstrating reproducibility. Because of the multi-step
procedure during material synthesis and battery assembly, a minor
variation in performance inevitably exists. The 150.degree. C.
annealed sample displays a better cycling behavior, as evidenced in
FIG. 2c. After being subjected to extremely long cycling such as
1500 cycles, the discharge capacity is still as high as 158 mAh/g
(FIG. 2c). It is noted that after running 1100 cycles, the capacity
shows almost no significant drop (FIG. 2c inset). A comparison of
battery performance using the disclosed methods and compositions
with the literature is shown in Table 1.
TABLE-US-00001 TABLE 1 The battery performance of different Li--S
battery systems. 1.sup.st Reversible Discharge Discharge Charge
Degradation Capacity Capacity Rate Total Cycle Rate Per Sulfur
Approach (mAh/g) (mAh/g) (mA/g) Number Cycle Loading Ref. SULFUN
1000-1400 520 (300.sup.th, 335 >500 0.24% (0.2 C) 65 wt %
Current 0.2 C) (0.2 C) 0.36% (2 C) (2 mg/cm.sup.2) work 290
(500.sup.th, 3350 (2 C) 0.2 C) 400 (250.sup.th, 2 C) S--TiO.sub.2
yolk-shell 1,030 690 836 (C/2) 1,000 0.033% 53 wt %, 1
nanocomposite 0.4-0.6 mg/cm.sup.2 Solvent-in-salt electrolyte 1,041
770 335 (C/5) 100 0.26% 48 wt % 2 Ordered mesoporous C--S 1,070 700
1675 (1C) 100 0.35% 57 wt % 3 Double-shelled C--S 1,020 690 167
(C/10) 100 0.32% 45 wt % 4 composite Porous hollow C--S 1,071 974
836 (C/2) 100 0.09% 65 wt % 5 composite Hollow CNF-encapsulated S
~1,400 730 836 (C/2) 150 0.48% ~1.0 mg/cm.sup.2 6 Amphiphilic
surface- 828 ~660 836 (C/2) 300 0.07% ~1.0 mg/cm.sup.2 7 modified
hollow CNF-S Ultrasound-assisted S--C 1,195 836 230 100 0.30% 29 wt
% 8 with fluorinated ether S molecules in a C/CNT 1,670 1,142 167.5
(C/10) 200 0.16% 32 wt % 9 matrix Li--S with interlayers with 1,483
600 and 1000 335 (C/5) >300 0.0011% 70 wt % 10 modified recharge
setting (600 mAh/g) (600 mAh/g) >200 0.0027% (1000 mAh/g) (1000
mAh/g) 1. Z. W. Seh, W. Li, J. J. Cha, G. Zheng, Y. Yang, M. T.
McDowell, P.-C. Hsu and Y. Cui, in Nature Communications, 2013, 4,
6 2. L. M. Suo, Y. S. Hu, H. Li, M. Armand and L. Q. Chen, in
Nature Communications, 2013, 4 3. J. Schuster, G. He, B
Mandlemeier, T. Yim, K. T. Lee, T. Bein and L. F. Nazar, Angew.
Chem.-Int. Edit., 2012, 51, 3591-3595. 4. C. F. Zhang, H. B. Wu, C.
Z. Yuan, Z. P. Guo and X. W. Lou, Angew. Chem.-Int. Edit., 2012,
51, 9592-9595. 5. N. Jayaprakash, J. Shen, S. S. Moganty, A. Corona
and L. A. Archer, in Angewandte Chemie International Edition, 2011,
50, 5904-5908. 6. G. Y. Zheng, Y. Yang, J. J. Cha, S. S. Hong and
Y. Cui, in Nano Letters, 2011, 11, 4462-4467. 7. G. Y. Zheng, Q. F.
Zhang, J. J. Cha, Y. Yang, W. Y. Li, Z. W. She and Y. Cui, Nano
Lett, 2013, 13, 1265-1270. 8. W. Weng, V. G. Pol, and K. Amine, Adv
Mater, 2013, 25, 1608-1615. 9. A. Manthiram, Y. Z. Fu and Y. S. Su,
Accounts Chem. Res., 2013, 46, 1125-1134 10. Y. S. Su, Y. Z. Fu, T.
Cochell and A. Manthiram, in Nature Communications, 2013, 4,
2985.
[0040] For microstructural comparison, coin cells made of
commercial pure sulfur and mortar-milled S/C mixture cathodes were
also tested, as shown in FIGS. 2b and 3. For the pure sulfur, the
capacity drastically decreased from .about.856 mAh/g to less than
200 mAh/g after only 15 cycles. The battery almost died after 29
cycles. As for the mortar-milled S/C mixture, the capacity dropped
to less than 300 mAh/g after 100 cycles and almost down to zero at
the 200.sup.th cycle (FIG. 2b). The two plateaus from the
charge/discharge voltage profile almost disappeared after 200
cycles (FIG. 4) while they were still observed apparently even
after 1500 cycles in SULFUN (FIG. 5). It was further observed that
in the coin cell assembly with the SULFUN cathode, adding a trace
of conductive polymer polypyrrole (PPy) in the SULFUN/binder/Super
P slurry acts as a network to restrain the dissolution of
intermediate products. It will not impair Li.sup.+/e.sup.-
transport due to the relatively high electric conductivity (0.005
Scm.sup.-1) of PPy, and appears to trap both polysulfides and
possibly detached sulfur particles without raising resistance,
which can further reduces the rate at which the capacity of the
cell decreases.
[0041] The atomic structure and evolution of sulfur inside SULFUN
was investigated. As shown in FIG. 17, the X-ray diffraction
pattern (XRD) of the as-received raw sulfur indicates an
orthorhombic structure. After annealing, a monoclinic crystalline
structure was stabilized. A totally amorphous structure of sulfur
was found upon the completion of 7 cycles (ending in charging) of
the SULFUN cathode.
[0042] The morphology of sulfur was characterized by electron
microscopy. As shown in FIG. 7a, the as-fabricated sulfur without
carbon host has a particle size ranging 5-10 .mu.m. The commercial
sulfur after mortar milling has a particle size ranging 40-60 .mu.m
(FIG. 6a-b). However, during SULFUN fabrication step 2), the size
of sulfur particles dispersed on the carbon matrix surface becomes
smaller (FIGS. 6c-d and 8d-e/19d-e), corresponding to sulfur
particle sizes of 2-4 .mu.m, which is about 50% less than the
particles size of free-standing sulfur in FIG. 7a and much smaller
than the commercial pure (FIG. 10a) and mortar-milled (FIG. 6a-b)
sulfur. The sulfur was dispersed rather uniformly on the carbon
surface, as illustrated from the energy-dispersive X-ray
spectroscopy (EDS) mapping in FIGS. 6d and 8d/19d. In contrast to
the separate sulfur particles after milling (FIG. 6a-b), the
ball-like S/C cluster with decreased sizes ensures a sufficient
contact, leading to a high ion/electron conductivity (FIG. 6c-d).
In order to further reduce the microstructural length scale and
form a compact nanoscale S--C network, the sulfur was subsequently
melted during SULFUN fabrication step 3 at 150.degree. C. or
200.degree. C. Under this temperature, like a water filtering
sponge, the fluidic sulfur permeated inside the carbon sponge (FIG.
1d). As displayed in FIGS. 6e-f and FIGS. 7b-c, after heating the
sulfur almost cannot be isolated from the Cnet any more. TEM images
of the 200.degree. C. treated sample also exhibits a uniform
composition (FIGS. 8f and 19f). Elemental mapping of local areas
clearly shows a proportional distribution of sulfur and carbon
(FIGS. 3d-f and 7a-c/19a-c). These data imply that Snet has been
interfused with the nanostructured Cnet, with improved adhesion
between sulfur and carbon, providing a fast pathway for
ion/electron transport. According to the estimated volume of the
matrix, the gravimetric loading of sulfur is about 70 wt %.
Quantitative thermal-gravimetric analysis (TGA) reveals the final
loading of sulfur in SULFUN was 62 and 65 wt % after heat treatment
at 150 and 200.degree. C., respectively. (FIG. 9).
[0043] The initial size of sulfur particles plays a critical role
on the imbibition process and the later cyclability of the
resulting electrochemical cell. To obtain a homogenous cathode,
well-dispersed sulfur particles with a small size are significant.
In the present method, carbon black first underwent acid treatment
in hydrochloric acid to create functional hydroxyl/carboxyl groups.
In parallel, the added surfactant groups surrounded the fresh
sulfur particles to prevent Ostwald ripening. The surfactant also
helped to disperse the sulfur particles more efficiently in the
matrix. Then, a very important step is the slow redox reaction, in
which e.g. sodium thiosulfate solution was added into the
functionalized carbon suspension slowly, drop by drop, with
vigorous agitation. As a result, sulfur with a reduced particle
size uniformly spread over a wide area of the carbon surface was
provided, and which was subsequently melted and spread further by
annealing at 150.degree. C. for 50 hours or at 200.degree. C. for
2.5 hours (FIG. 6c-d). In contrast, the particle size of commercial
ground and pure sulfur possesses is 40-60 .mu.m (FIGS. 6a-b and
10a-b).
[0044] Next, we investigated the morphological evolution of the
electrode surface during lithiation/delithiation. As can be seen
from FIG. 10a, the surface of the original commercial sulfur is
quite smooth. A clear boundary between sulfur and other materials
like carbon and binder is observed via elemental mapping (FIG.
10b). However after only two cycles, several holes with size 2-4
.mu.m were observed in the sulfur particles, which by then were
already severely deformed and shrunk, indicating a fast loss of the
active sulfur (FIG. 10c-d and FIG. 11). The sulfur particles were
dramatically deformed and broke into small particles which were
dispersed among the surface inhomogeneously (FIG. 11). In contrast,
the surface of the SULFUN electrode is still smooth after the
cycling, as shown in FIG. 10e. The elemental sulfur map indicates a
homogeneous distribution (FIG. 100. From analysis of the
cross-section of the pure sulfur electrode, 0 and F which can only
be precipitated out from the electrolyte was found to be dispersed
across the whole electrode film (.about.40 .mu.m, FIG. 12a),
indicating deep invasion of the liquid electrolyte and corrosion of
the sulfur. However, the 0 and F elements were highly concentrated
at the top surface (1-2 .mu.m) with the SULFUN electrode (FIGS. 12b
and 13), indicating liquid electrolyte invasion and corrosion were
probably repelled from the inside matrix. The corrosion reaction is
believed to be heterogeneous and anisotropic, as illustrated in
FIGS. 14a and 15a. Some locations will be more heavily corroded and
consequently generate holes/cracks, causing the whole particle to
split (FIG. 14a). The electrode surface composed of pure or milled
sulfur displays a larger solid-liquid interface Scontact to the
liquid electrolyte but with a smaller volume of sulfur Vs (FIG. 14b
and FIG. 15a). In this case, the liquid electrolyte can easily
permeate into the electrode (FIG. 12a), which also creates a path
to carry away the soluble polysulfides. However, the compactly
nanostructured SULFUN exposes only a very small area of naked
sulfur to the liquid electrolyte (FIGS. 14c and 15b) limiting the
sulfur dissolution, even when the intermediate lithium polysulfides
are formed inside. Here a possible mechanism is suggested. Because
the Snet is initially open to the outside, the LiTFSI+DOL+DME
liquid electrolyte wets and infiltrates Snet in the initial
lithiation, dissolving some sulfur and forming some soluble lithium
polysulfides. The "wet" Snet then has some significant Li.sup.+
conductivity that percolates within Cnet. However, once the
embedded sulfur on the top is dispersed, the carbon nanoparticles
remaining (tens to hundreds nanometers, as shown in FIGS. 12b and
13) concentrates to form a dense carbon-rich layer as a passivation
layer against corrosion, which serves like a sieve to selectively
block larger molecules such as the electrolyte and polysulfide
while allowing small charged species (L.sup.+/e.sup.-) to pass
through (FIGS. 14c and 15).
[0045] An additional carbon layer with tens of microns thickness
was coated on the SULFUN surface. FIG. 16 shows the cycling
performance and coulombic efficiency of the modified SULFUN battery
at different charge/discharge rates. As can be seen from FIG. 16a,
an initial >1300 mAh/g capacity was achieved and then was
maintained at a value of .about.1100 mAh/g until 60 cycles,
accompanying with the coulombic efficiency >98%. Under the 10
times faster charging/discharging (2.0 C), a special discharge
capacity of .about.400 mAh/g was still attained after 250 cycles
(FIG. 16b). This high rate capability indicates the extra carbon
can act as a passivation layer to reduce the "shuttling effect", as
the in-situ formed carbon-rich passivation layer on SULFUN surface,
leading to a long battery life.
[0046] To better understand the microstructure of the samples, FIG.
17 shows XRD patterns of raw sulfur, annealed sulfur-carbon
matrices, and the SULFUN matrix after 7 charge/discharge cycles
ending in charging. In addition, FIG. 18 shows SEM images and
energy-dispersive X-ray spectroscopy (EDS) maps of the
sulfur-carbon matrix: (a) SEM morphology of the sulfur-carbon
matrix before annealing at 200.degree. C. for 2.5 hours. (b) Sulfur
and carbon EDS map of area shown in (a). (c) SEM morphology of the
sulfur-carbon matrix after annealing at 200.degree. C. for 2.5
hours. (d)-(f) Sulfur and carbon EDS map of area shown in (c).
[0047] Additional micrographs are shown in FIG. 19, which includes
EDS maps and TEM images of the sulfur-carbon matrix: (a) SEM
morphology of the matrix annealed at 150.degree. C. for 50 hours.
(b) carbon map of the area shown in (a). (c) sulfur map of the area
shown in (a). (d) sulfur and carbon map of as-receive sulfur-carbon
matrix before heating. (e) TEM image of the sulfur-carbon matrix
before heating at 200.degree. C. for 2.5 hours. (f) TEM image of
the sulfur-carbon matrix after heating at 200.degree. C. for 2.5
hours. Scsle bar in (e) and (f) is 5 .mu.m.
[0048] To better understand the selective permeation effect, the
size dependence of the molecule/ion on the solubility and diffusion
coefficient inside the Super-P can be calculated. The mass
transport flux is proportional to the product of the solubility and
the diffusion coefficient in carbon black, as
J .about. k B T 6 .pi. M 1 / 2 a exp ( - Q k B T ) , ( 1 )
##EQU00001##
[0049] where k.sub.B is the Boltzmann constant, T is temperature, M
and a are the mass and the average radius of the molecule/particle,
respectively. Q is the effective activation energy, combining both
insertion energy and migration energy barrier. When a molecule/ion
in the liquid electrolyte is inserted into and diffuses inside the
passivation layer, both interfacial and elastic energies contribute
to Q:
Q .apprxeq. F surface + F elastic = 4 .pi. a 2 .gamma. + 24 .pi. a
3 .mu. K 2 3 K + 4 .mu. , ( 2 ) ##EQU00002##
[0050] where .gamma. is the interfacial energy, K, .mu. and
.epsilon. are the bulk modulus, shear modulus and dilatational
misfit strain, respectively. For small particles such as single
lithium ion, molecular sulfur/polysulfide ion, or even electrolyte,
F.sub.surface>>F.sub.elastic, and eq. (2) becomes
Q.apprxeq.S.gamma.. Here, S is the surface area. The average
surface energy of SuperP is .about.100 mJ/m.sup.2 and the surface
area of Li ion, small sulfur molecules S.sub.4 and S.sub.8 can be
estimated using lithium ion radius of 1.34 .ANG. and the bond
length values of various small sulfur molecules. Thus, from eq. (1)
and (2) the ratio of permeation fluxes J(X) (X=Li, S.sub.4,
S.sub.8) as J(Li): J(S.sub.4): J(S.sub.8)=1:10.sup.-3:10.sup.-8 is
obtained, showing the permeation of the S.sub.8 cluster is eight
orders of magnitude slower than Li. The upshot of the above rough
estimation is that a pure carbon layer (blocking the invasion of
the liquid electrolyte into Snet) can selectively allow
L.sup.+/e.sup.- to easily get in, but prevent the larger
polysulfides Li.sub.2S.sub.X (4.ltoreq.X.ltoreq.8) from getting in
or out, thus slowing down the shuttling effect and act as a
passivating molecular sieve. Also, the fine-meshed Cnet will
probably restrain and block much smaller sulfur particles from
breaking off Snet mechanically and convecting into the liquid, even
with a certain degree of heterogeneous corrosion. In other words,
the SULFUN nanocomposite can better facilitate stress relaxation
and enhance flaw tolerance, which may be a generic behavior of
nano-scale electrode materials.
[0051] In conclusion, the in-situ synthesized sulfur-carbon
nanosponge using Conductive Carbon Blacks as a host greatly slowed
down the loss of sulfur, hereby displaying a better cycling
performance while maintaining a high capacity. The suggested
passivation layer or extra carbon layers can prevent the decay of
capacity by limiting the transport of the larger polysulfides
Li.sub.2S.sub.X (4.ltoreq.X.ltoreq.8) without slowing down
L.sup.+/e.sup.-. This "defense-in-depth" strategy is distinct from
the complete encapsulation or the "defense-in-perimeter" strategy
most researchers have employed. The improved coin-cell scale
performance discussed herein indicates that the polysulfides
shuttling effect is ameliorable through nanostructural design and
engineering. The high capacity, long cyclability, cheap raw
materials and simple preparation make the SULFUN cathode material
suitable for industrial scale production.
Characterization of Battery Performance
[0052] Battery behavior of the synthesized material was performed
via a coin cell. Typically, a CR2032 coin cell (MTI) with a lithium
foil as counter/reference electrode was assembled in an
argon-filled glove box (LABmaster SP, MBraun) with both O.sub.2 and
H.sub.2O concentrations lower than 0.1 ppm. Celgard 2400 was used
as the separator. For liquid electrolyte, 1.0 M lithium
bis-trifluoromethanesulfonylimide in 1,3-dioxolane and
1,2-dimethoxyethane (volume ratio 1:1, Novolyte) was employed,
although the skilled artisan will recognize that other electrolytes
such as those containing lithium salts (e.g., LiPF.sub.6,
LiBF.sub.4 or LiClO.sub.4) and combination of linear and cyclic
carbonates (e.g., ethylene carbonate, dimethyl carbonate or
poly(oxyethylene)) can also suitably be employed. Certain relevant
battery performance characteristics were tested without additives
except the rate data shown in FIG. 7. A hydraulic crimping machine
(MSK-110, MTI) was employed to close the cell. To make a slurry,
the active material of sulfur-Super P sponge, or pure sulfur
synthesized using a same method but without carbon, or milled
sulfur/carbon mixture was blended with 10 wt % Super C65 (Timical),
10 wt % poly (vinylidene fluoride) binder (MTI), and a small amount
of polypyrrole solution (polypyrrole doped, 5 wt % dispersion in
H.sub.2O, conductivity of dried cast film: >0.0005 S/cm,
Sigma-Aldrich) dissolved in N-methylpyrrolidone (MTI). The sulfur
loading was designed to be 1.0 mg/cm.sup.2 for 150.degree. C.
sample and 2.0 mg/cm.sup.2 for 200.degree. C. sample, respectively.
The mixture was sonicated until a homogeneous slurry was formed.
Then the slurry was coated onto an aluminum foil current collector.
After drying 2 hours at 90.degree. C. in an oven, the sample was
cut out to serve as a cathode.
[0053] For the high-rate charge/discharge test, an additional layer
which is composed of carbon/binder was coated on the top of the
dried slurry made of SULFUN. In a typical experiment, the melted
sulfur/carbon mixture with 10 wt % SuperP and 10 wt % poly
(vinylidene fluoride) binder was first coated on the aluminum foil,
as described above. After the first slurry was almost dried, the
secondary slurry composed of SuperP (80 wt %) and binder (20 wt %)
with a loading of .about.2.0 mg/cm.sup.2 was coated on the surface.
Then the sample was dried overnight at 65.degree. C. in an oven for
battery assembling.
[0054] The packed coin cell was galvanostatically
charged/discharged in a fixed voltage window between 1.4 and
2.5/2.8 V on a 12-channel Arbin Instruments BT2000 battery tester
at room temperature. The cycling capability was recorded at a
charging/discharging rate of 0.2 C and 2.0 C, respectively. The
specific capacities were calculated based on the sulfur loading
corrected by the TGA test.
* * * * *