U.S. patent application number 15/529695 was filed with the patent office on 2017-12-28 for systems and methods related to the separation wax products from products.
The applicant listed for this patent is SABIC Global Technologies B.V.. Invention is credited to Ali Al-Hammad, Abdullah Turki Al-Jaloud, Saud Al-Khudeer, Thabet Al-Qahtani, Khalid Karim, Shehzada Khurram, Zeeshan Nawaz.
Application Number | 20170369797 15/529695 |
Document ID | / |
Family ID | 54838381 |
Filed Date | 2017-12-28 |
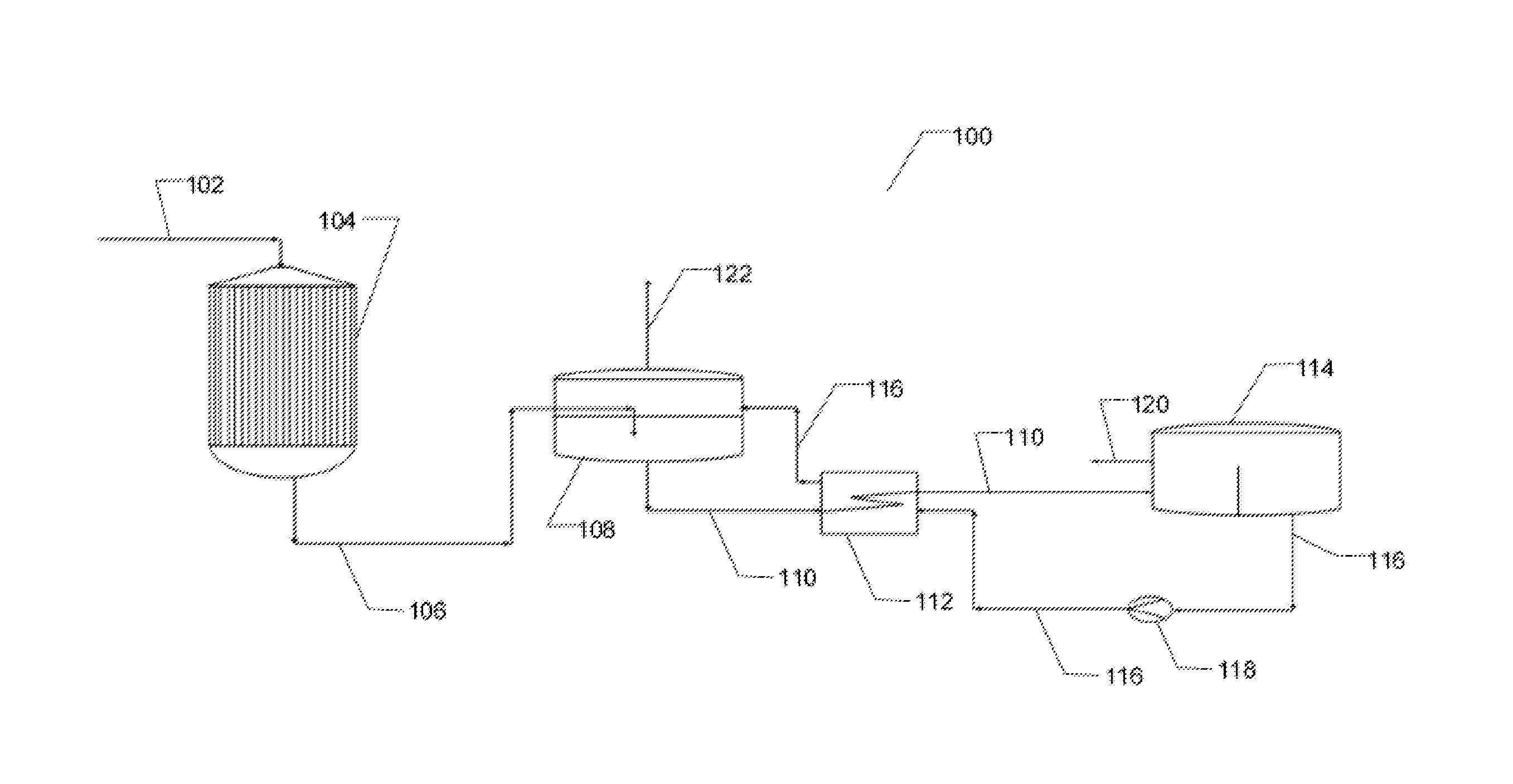
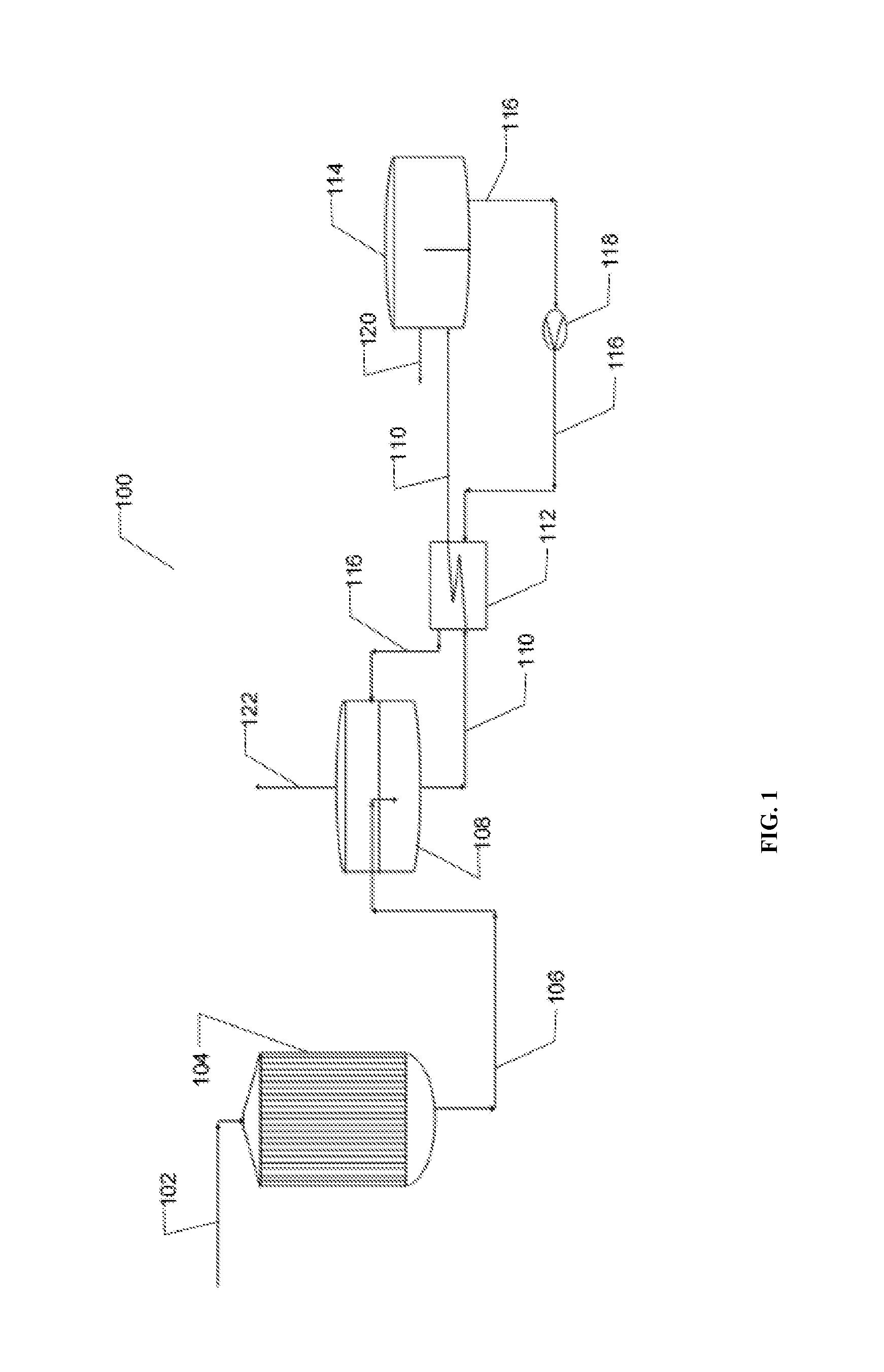
United States Patent
Application |
20170369797 |
Kind Code |
A1 |
Khurram; Shehzada ; et
al. |
December 28, 2017 |
SYSTEMS AND METHODS RELATED TO THE SEPARATION WAX PRODUCTS FROM
PRODUCTS
Abstract
Disclosed herein is a system comprising: a) a separator tank
comprising a first inlet, a second inlet, a first outlet, and a
second outlet, b) a heat exchanger, and c) a holding tank
comprising a third inlet and a third outlet, wherein the separator
tank is in fluid communication with the holding tank via a first
connector and via a second connector, wherein the first connector
is connected to the first outlet of the separator tank and to the
third inlet of the holding tank, wherein the second connector is
connected to the first inlet of the separator tank and to the third
outlet of the holding tank, and wherein the first connector and the
second connector are in communication with the heat exchanger.
Inventors: |
Khurram; Shehzada; (Riyadh,
SA) ; Nawaz; Zeeshan; (Riyadh, SA) ; Karim;
Khalid; (Riyadh, SA) ; Al-Qahtani; Thabet;
(Riyadh, SA) ; Al-Jaloud; Abdullah Turki; (Riyadh,
SA) ; Al-Khudeer; Saud; (Riyadh, SA) ;
Al-Hammad; Ali; (Riyadh, SA) |
|
Applicant: |
Name |
City |
State |
Country |
Type |
SABIC Global Technologies B.V. |
Bergen op Zoom |
|
NL |
|
|
Family ID: |
54838381 |
Appl. No.: |
15/529695 |
Filed: |
November 17, 2015 |
PCT Filed: |
November 17, 2015 |
PCT NO: |
PCT/IB2015/058895 |
371 Date: |
May 25, 2017 |
Related U.S. Patent Documents
|
|
|
|
|
|
Application
Number |
Filing Date |
Patent Number |
|
|
62084644 |
Nov 26, 2014 |
|
|
|
Current U.S.
Class: |
1/1 |
Current CPC
Class: |
C10G 2300/1022 20130101;
C10G 2/33 20130101; C10G 70/06 20130101; C10G 21/14 20130101; C10G
21/00 20130101; C10G 21/16 20130101; C10G 2/341 20130101; C10G
31/06 20130101; C10G 21/06 20130101; C10G 21/08 20130101 |
International
Class: |
C10G 70/06 20060101
C10G070/06; C10G 21/16 20060101 C10G021/16; C10G 31/06 20060101
C10G031/06; C10G 21/14 20060101 C10G021/14; C10G 21/08 20060101
C10G021/08 |
Claims
1. A method comprising the steps of: a) providing a first product
gas stream comprising a first wax product and a first lower
hydrocarbon product, wherein the first gas product has a first
temperature and the first wax product and first lower hydrocarbon
product are in gas form; and b) separating at least a portion of
the first wax product from the first product gas stream by lowering
the first temperature of the first product gas stream by contacting
the first product gas stream with a first separation liquid having
a second temperature, thereby liquefying or solidifying at least a
portion of the first wax product into the first separation liquid,
thereby producing a second product gas stream comprising at least a
portion of the first lower hydrocarbon product.
2. The method of claim 1, wherein the method further comprises the
steps of: c) lowering the second temperature of the first
separation liquid to a third temperature by use of a heat
exchanger; d) transporting the first separation liquid to a holding
tank and allowing the first wax product to float to the surface of
the first separation liquid; and e) removing the first wax product
from the first separation liquid, thereby producing a second
separation liquid.
3. The method of claim 2, wherein the second separation liquid is
recycled back into step b) and is the first separation liquid.
4. The method of claim 1, wherein the first temperature is from
about 230.degree. C. to about 250.degree. C.
5. The method of claim 1, wherein the second temperature is from
about 160.degree. C. to about 190.degree. C.
6. The method of claim 2, wherein the third temperature is from
about 140.degree. C. to about 145.degree. C.
7.-11. (canceled)
12. The method of claim 1, wherein at least 90% of the first wax
product is separated from the first product gas stream.
13. (canceled)
14. The method of claim 1, wherein the first separation liquid
comprises silicone oil, an ionic liquid, or a glycol, or a
combination thereof.
15. The method of claim 1, wherein the second separation liquid
comprises less than 0.5% of the first wax product.
16. (canceled)
17. The method of claim 1, wherein the separating at least a
portion of the first wax product from the first product gas stream
is performed in a separator tank at a pressure from about 3 bar to
about 12 bar.
18. (canceled)
19. A method comprising the steps of: a) providing a first
separation liquid comprising a first wax product, wherein the first
separation liquid has a second temperature and wherein the first
wax product is in liquid or solid form; b) lowering the second
temperature of the first separation liquid to a third temperature
by use of a heat exchanger; c) transporting the first separation
liquid to a holding tank and allowing the first wax product to
float to the surface of the first separation liquid; and d)
removing the first wax product from the first separation liquid,
thereby producing a second separation liquid.
20. (canceled)
21. The method of claim 19, wherein the second temperature is from
about 160.degree. C. to about 190.degree. C.
22. The method of claim 19, wherein the third temperature is from
about 140.degree. C. to about 145.degree. C.
23. (canceled)
24. The method of claim 19, wherein step a) is performed in a
holding tank, wherein the method further comprises the step of
transporting the first separation liquid comprising the first wax
product from the holding tank to the heat exchanger.
25. (canceled)
26. (canceled)
27. (canceled)
28. The method of claim 19, wherein the method further comprises
the step of transporting the second separation liquid to a heat
exchanger and increasing the temperature of the second separation
liquid to a fourth temperature.
29. (canceled)
30. The method of claim 28, wherein the method further comprises
transporting the second separation liquid having the fourth
temperature to a separator tank.
31. The method of claim 30, wherein the method further comprises
the steps of: e) providing a first product gas stream comprising a
first wax product and a first lower hydrocarbon product, wherein
the first gas product has a first temperature and the first wax
product and first lower hydrocarbon product are in gas form; and f)
separating at least a portion of the first wax product from the
first product gas stream by lowering the first temperature of the
first product gas stream by contacting the first product gas stream
with the second separation liquid having the fourth temperature,
thereby liquefying or solidifying at least a portion of the first
wax product into the second separation, thereby producing a second
product gas stream comprising at least a portion of the first lower
hydrocarbon product.
32.-38. (canceled)
39. A system comprising: a) a separator tank comprising a first
inlet, a second inlet, a first outlet, and a second outlet; b) a
heat exchanger; c) a holding tank comprising a third inlet and a
third outlet, wherein the separator tank is in fluid communication
with the holding tank via a first connector and via a second
connector, wherein the first connector is connected to the first
outlet of the separator tank and to the third inlet of the holding
tank, wherein the second connector is connected to the first inlet
of the separator tank and to the third outlet of the holding tank,
and wherein the first connector and the second connector are in
communication with the heat exchanger.
40. The system of claim 40, wherein the system further comprises a
Fisher-Tropsch reactor comprising a fourth inlet and a fourth
outlet, wherein the separator tank is in fluid communication with
the Fisher-Tropsch via a third connector, wherein the third
connector is connected to the to the fourth outlet of the
Fisher-Tropsch reactor and the second inlet of the separator
tank.
41. The system of claim 40, wherein the system further comprises a
Fisher-Tropsch reactor comprising a fourth inlet and a fourth
outlet, wherein the separator tank is in fluid communication with
the Fisher-Tropsch via a third connector, wherein the third
connector is connected to the to the fourth outlet of the
Fisher-Tropsch reactor and the second inlet of the separator
tank.
42.-47. (canceled)
Description
CROSS-REFERENCE TO RELATED APPLICATIONS
[0001] This application claims the benefit of U.S. Provisional
Application No. 62/084,644, filed Nov. 26, 2014, which application
is incorporated hereby by reference in its entirety.
BACKGROUND
[0002] Syngas (mixtures of hydrogen (H.sub.2)) and carbon monoxide
(CO) can be readily produced from either coal or methane (natural
gas) by methods well known in the art and widely commercially
practiced around the world. A number of well-known industrial
processes use syngas for producing various oxygenated organic
chemicals. The Fischer-Tropsch catalytic process for catalytically
producing hydrocarbons from syngas was initially discovered and
developed in the 1920's, and was used in South Africa for many
years to produce gasoline range hydrocarbons as automotive
fuels.
[0003] The products produced in a Fischer-Tropsch catalytic process
comprise a portion of wax. It is desired to separate the wax from
the hydrocarbons in the products so that the hydrocarbons can be
further processed in downstream processes.
[0004] Accordingly, systems and methods that separate wax from
hydrocarbons are disclosed herein.
SUMMARY OF THE INVENTION
[0005] Disclosed herein is a system comprising: a) a separator tank
comprising a first inlet, a second inlet, a first outlet, and a
second outlet; b) a heat exchanger; and c) a holding tank
comprising a third inlet and a third outlet, wherein the separator
tank is in fluid communication with the holding tank via a first
connector and via a second connector, wherein the first connector
is connected to the first outlet of the separator tank and to the
third inlet of the holding tank, wherein the second connector is
connected to the first inlet of the separator tank and to the third
outlet of the holding tank, and wherein the first connector and the
second connector are in communication with the heat exchanger.
[0006] Also disclosed herein is a method comprising the steps of:
a) providing a first product gas stream comprising a first wax
product and a first lower hydrocarbon product, wherein the first
gas product has a first temperature and the first wax product and
first lower hydrocarbon product are in gas form; and b) separating
at least a portion of the first wax product from the first product
gas stream by lowering the first temperature of the first product
gas stream by contacting the first product gas stream with a first
separation liquid having a second temperature, thereby liquefying
or solidifying at least a portion of the first wax product into the
first separation liquid, thereby producing a second product gas
stream comprising at least a portion of the first lower hydrocarbon
product.
[0007] Also disclosed herein is a method comprising the steps of:
a) providing a first separation liquid comprising a first wax
product, wherein the first separation liquid has a second
temperature and wherein the first wax product is in liquid or solid
form; b) lowering the second temperature of the first separation
liquid to a third temperature by use of a heat exchanger; c)
transporting the first separation liquid to a holding tank and
allowing the first wax product to float to the surface of the first
separation liquid; and d) removing the first wax product from the
first separation liquid, thereby producing a second separation
liquid.
[0008] Also, disclosed herein is a method comprising a) providing a
first product gas stream comprising a first wax product and a first
lower hydrocarbon product, wherein the first gas product has a
first temperature and the first wax product and first lower
hydrocarbon product are in gas form; and b) separating at least a
portion of the first wax product from the first product gas stream
by lowering the first temperature of the first product gas stream
by contacting the first product gas stream with a first separation
liquid having a second temperature, thereby liquefying or
solidifying at least a portion of the first wax product into the
first separation liquid, thereby producing a second product gas
stream comprising at least a portion of the first lower hydrocarbon
product; c) lowering the second temperature of the first separation
liquid to a third temperature by use of a heat exchanger; d)
transporting the first separation liquid to a holding tank and
allowing the first wax product to float to the surface of the first
separation liquid; and e) removing the first wax product from the
first separation liquid, thereby producing a second separation
liquid.
[0009] Additional advantages will be set forth in part in the
description which follows, and in part will be obvious from the
description, or can be learned by practice of the aspects described
below. The advantages described below will be realized and attained
by means of the chemical compositions, methods, and combinations
thereof particularly pointed out in the appended claims. It is to
be understood that both the foregoing general description and the
following detailed description are exemplary and explanatory only
and are not restrictive.
DESCRIPTION OF THE FIGURES
[0010] The accompanying FIGURES, which are incorporated in and
constitute a part of this specification, illustrate several
aspects, and together with the description, serve to explain the
principles of the invention.
[0011] FIG. 1 shows a system disclosed herein.
[0012] Additional advantages of the invention will be set forth in
part in the description that follows, and in part will be obvious
from the description, or can be learned by practice of the
invention. The advantages of the invention will be realized and
attained by means of the elements and combinations particularly
pointed out in the appended claims. It is to be understood that
both the foregoing general description and the following detailed
description are exemplary and explanatory only and are not
restrictive of the invention, as claimed.
DETAILED DESCRIPTION
[0013] Disclosed herein are materials, compounds, compositions, and
components that can be used for, can be used in conjunction with,
can be used in preparation for, or are products of the disclosed
method and compositions. It is to be understood that when
combinations, subsets, interactions, groups, etc. of these
materials are disclosed that while specific reference of each
various individual and collective combinations and permutation of
these compounds cannot be explicitly disclosed, each is
specifically contemplated and described herein. For example, if a
catalyst component is disclosed and discussed, and a number of
alternative solid state forms of that component are discussed, each
and every combination and permutation of the catalyst component and
the solid state forms that are possible are specifically
contemplated unless specifically indicated to the contrary. This
concept applies to all aspects of this disclosure including, but
not limited to, steps in methods of making and using the disclosed
compositions. Thus, if there are a variety of additional steps that
can be performed it is understood that each of these additional
steps can be performed with any specific aspect or combination of
aspects of the disclosed methods, and that each such combination is
specifically contemplated and should be considered disclosed.
1. Definitions
[0014] In this specification and in the claims which follow,
reference will be made to a number of terms which shall be defined
to have the following meanings:
[0015] It must be noted that, as used in the specification and the
appended claims, the singular forms "a," "an" and "the" include
plural referents unless the context clearly dictates otherwise.
Thus, for example, reference to "a hydrocarbon" includes mixtures
of hydrocarbons.
[0016] Ranges can be expressed herein as from one particular value,
and/or to another particular value. When such a range is expressed,
another aspect includes from the one particular value and/or to the
other particular value. Similarly, when values are expressed as
approximations, by use of the antecedent "," it will be understood
that the particular value forms another aspect. It will be further
understood that the endpoints of each of the ranges are significant
both in relation to the other endpoint, and independently of the
other endpoint.
[0017] References in the specification and concluding claims to
parts by weight, of a particular element or component in a
composition or article, denote the weight relationship between the
element or component and any other elements or components in the
composition or article for which a part by weight is expressed.
Thus, in a compound containing 2 parts by weight of component X and
5 parts by weight of component Y, X and Y are present at a weight
ratio of 2:5, and are present in such a ratio regardless of whether
additional components are contained in the compound.
[0018] A weight percent of a component, unless specifically stated
to the contrary, is based on the total weight of the formulation or
composition in which the component is included.
[0019] As used herein, the terms space time yield ("STY") refers to
the tons or kg of product that is produced per unit time per volume
of catalyst.
2. System
[0020] The Fischer-Tropsch catalytic process for producing
hydrocarbons from syngas is known in the art.
[0021] The production of wax, CO.sub.2, CH.sub.4, and heavy
hydrocarbon (C10+) is unwanted in Fischer-Tropsch processes, which
targets the production of light hydrocarbons (C2-C5). Waxes
produced from Fischer-Tropsch processes are typically paraffin
waxes, that is, a mixture of hydrocarbon molecules, wherein each
molecule contains from 20 to 100 carbon atoms. The systems and
methods disclosed herein provide means for separating wax from
other hydrocarbons, such as, for example, light hydrocarbons.
[0022] Isothermal and/or adiabatic fixed bed reactors can be used
to carry out the Fischer-Tropsch process. The isothermal and/or
adiabatic fixed bed reactors are used to convert syngas to
hydrocarbon products, including, olefins, waxes (e.g. paraffins)
and alcohols. The amount of waxes in the hydrocarbon products is
less than 5%. In one aspect, the amount of waxes in the hydrocarbon
products is less than 4%, 3%, 2%, or 1%.
[0023] Disclosed herein is a system comprising: a) a separator tank
comprising a first inlet, a second inlet, a first outlet, and a
second outlet, b) a heat exchanger, and c) a holding tank
comprising a third inlet and a third outlet, wherein the separator
tank is in fluid communication with the holding tank via a first
connector and via a second connector, wherein the first connector
is connected to the first outlet of the separator tank and to the
third inlet of the holding tank, wherein the second connector is
connected to the first inlet of the separator tank and to the third
outlet of the holding tank, and wherein the first connector and the
second connector are in communication with the heat exchanger.
[0024] In one aspect, the system further comprises a Fisher-Tropsch
reactor comprising a fourth inlet and a fourth outlet, wherein the
separator tank is in fluid communication with the Fisher-Tropsch
via a third connector, wherein the third connector is connected to
the to the fourth outlet of the Fisher-Tropsch reactor and the
second inlet of the separator tank.
[0025] In one aspect, the second connector is in communication with
a pump. The pump facilitates the transfer of purified separation
fluid from the holding tank to the separator tank.
[0026] The heat exchanger serves two purposes. The first purpose is
to lower the temperature of the separation liquid comprising a
first wax product that is being transported from the separator tank
to the holding tank, such lowering the temperature to a second
temperature. The temperature of the separation liquid comprising a
first wax product can be, for example, lowered from about
140.degree. C. to about 145.degree. C. The second purpose is to
increase the temperature of the second separation liquid being
transported from the holding tank to a fourth temperature. The
fourth temperature can be from about 160.degree. C. to about
190.degree. C.
[0027] In one aspect, the third connector is configured to
transport a first product gas stream comprising a first wax product
and a first lower hydrocarbon product from the Fischer-Tropsch
reactor to the separator tank.
[0028] In one aspect, the separator tank is configured to withstand
at least a pressure of above about 12 bar. For example, the
separator tank can be configured to withstand at least a pressure
from about 12 bar to about 20 bar.
[0029] In one aspect, the separator tank is configured to support a
Fischer-Tropsch system on an industrial scale. For example, the
separator tank is configured to hold a volume of a first separation
fluid on an industrial scale. For example, the holding tank can be
configured to hold at least about 1,000 liter of separation fluid.
In another example, the holding tank can be configured to have a
volume from at least about 1,000 liters to about 20,000 liters.
[0030] In one aspect, the first connector is configured to
transport a first wax portion and a first separation liquid from
the separator tank to the holding tank.
[0031] In one aspect, the holding tank is configured to support a
Fischer-Tropsch system on an industrial scale. For example, the
holding tank is configured to hold a volume of a first separation
fluid and a first wax product on an industrial scale. For example,
the holding tank can be configured to hold at least about 1,000
liters of separation fluid and wax. In another example, the holding
tank can be configured to have a volume from at least about 1,000
liters to about 20,000 liter.
[0032] In one aspect, the second connector is configured to
transport a second separation liquid from the holding tank to the
separator tank.
[0033] In one aspect, the separator tank comprises a fifth outlet.
The fifth outlet can be connected to a fifth connector that is
configured to remove a first lower hydrocarbon product from the
separator tank.
[0034] In one aspect, the holding tank comprises a sixth outlet.
The sixth outlet can be connected to a sixth connector that is
configured to remove a first wax product from the holding tank.
[0035] Optionally, in various aspects, the disclosed system can be
operated or configured on an industrial scale. In one aspect, the
system, apparatus, and methods disclosed herein can be configured
to produce a first product gas stream comprising a first wax
product and a first lower hydrocarbon product on an industrial
scale. For example, according to further aspects, the apparatus and
methods can separate a first wax product from a first product gas
stream comprising a first wax product and a first lower hydrocarbon
product in batches on an industrial scale. In a further aspect, the
batch size can comprise any desired industrial-scale batch
size.
[0036] In various aspects, the disclosed system can be operated or
performed on any desired time scale or production schedule that is
commercially practicable. In one aspect, the disclosed system,
apparatus, and methods can produce a quantity of at least 1 ton of
a first product gas stream comprising a first wax product and a
first lower hydrocarbon product in a period of 2 hr or less,
including exemplary quantities of at least about 10 tons within the
period. In a further aspect, the period of time can be 1 hr.
[0037] In one aspect, the disclosed system, apparatus, and methods
can have a STY of at least 0.5/kg/hr of catalyst for the reactors
disclosed herein. For example, the disclosed system, apparatus, and
methods can have a STY of at least 0.7/kg/hr of catalyst for the
reactors disclosed herein. In another example, the disclosed
system, apparatus, and methods can have a STY from 0.5 to 1/kg/hr
of catalyst for the reactors disclosed herein.
[0038] In additional aspects, the components of the disclosed
system and apparatus can be shaped and sized to permit production
of a first product gas stream comprising a first wax product and a
first lower hydrocarbon product on an industrial scale.
[0039] Now referring to FIG. 1, which shows a non-limiting
exemplary aspect of the system disclosed herein. FIG. 1 shows a
system (100). The system (100) has a Fisher-Tropsch reactor (104).
The Fisher-Tropsch reactor (104) has a fourth inlet connected to a
fourth connector (102) and a fourth outlet connected to a third
connector (106). The third connector (106) is connected to the
separator tank (108) via a second inlet on the separator tank
(108). The separator tank (108) has a first outlet connected to a
first connector (110). The first connector (110) is in
communication with heat exchanger (112). The first connector (110)
is connected to the holding tank (114) via a third inlet on the
holding tank (114). The holding tank (114) has a third outlet that
is connected to a second connector (116). The second connector
(116) is in communication with heat exchanger (112). The second
connector (116) can also be in communication with a pump (118). The
second connector (116) is connected to the separator tank (108) via
a first inlet on the separator tank (108). The separator tank (108)
has a fifth outlet connected to a fifth connector (122), which is
configured to remove products from the separator tank (108). The
holding tank (114) can have a sixth outlet connected to a sixth
connector (120), which is configured to remove wax.
3. Methods
[0040] The systems disclosed herein can be used in methods to
separate wax, such as, for example, paraffins, from a hydrocarbon
stream comprising light hydrocarbons.
[0041] Disclosed herein is a method comprising the steps of: a)
providing a first product gas stream comprising a first wax product
and a first lower hydrocarbon product, wherein the first gas
product has a first temperature and the first wax product and first
lower hydrocarbon product are in gas form; and b) separating at
least a portion of the first wax product from the first product gas
stream by lowering the first temperature of the first product gas
stream by contacting the first product gas stream with a first
separation liquid having a second temperature, thereby liquefying
or solidifying at least a portion of the first wax product into the
first separation liquid, thereby producing a second product gas
stream comprising at least a portion of the first lower hydrocarbon
product. In one aspect, the method can further comprise the steps
of c) lowering the second temperature of the first separation
liquid to a third temperature by use of a heat exchanger; d)
transporting the first separation liquid to a holding tank and
allowing the first wax product to float to the surface of the first
separation liquid; and e) removing the first wax product from the
first separation liquid, thereby producing a second separation
liquid.
[0042] Also disclosed herein is a method comprising the steps of:
a) providing a first separation liquid comprising a first wax
product, wherein the first separation liquid has a second
temperature and wherein the first wax product is in liquid or solid
form; b) lowering the second temperature of the first separation
liquid to a third temperature by use of a heat exchanger; c)
transporting the first separation liquid to a holding tank and
allowing the first wax product to float to the surface of the first
separation liquid; and d) removing the first wax product from the
first separation liquid, thereby producing a second separation
liquid. In one aspect, the method further comprises the steps of e)
providing a first product gas stream comprising a first wax product
and a first lower hydrocarbon product, wherein the first gas
product has a first temperature and the first wax product and first
lower hydrocarbon product are in gas form; and f) separating at
least a portion of the first wax product from the first product gas
stream by lowering the first temperature of the first product gas
stream by contacting the first product gas stream with the second
separation liquid having the fourth temperature, thereby liquefying
or solidifying at least a portion of the first wax product into the
second separation, thereby producing a second product gas stream
comprising at least a portion of the first lower hydrocarbon
product. In one aspect, the method further comprises the step of
transporting the first separation liquid comprising the first wax
product from the holding tank to the heat exchanger.
[0043] In one aspect, the step of a) providing a first separation
liquid comprising a first wax product, wherein the first separation
liquid has a second temperature and wherein the first wax product
is in liquid or solid form is performed in a holding tank.
[0044] Also, disclosed herein is a method comprising a) providing a
first product gas stream comprising a first wax product and a first
lower hydrocarbon product, wherein the first gas product has a
first temperature and the first wax product and first lower
hydrocarbon product are in gas form; and b) separating at least a
portion of the first wax product from the first product gas stream
by lowering the first temperature of the first product gas stream
by contacting the first product gas stream with a first separation
liquid having a second temperature, thereby liquefying or
solidifying at least a portion of the first wax product into the
first separation liquid, thereby producing a second product gas
stream comprising at least a portion of the first lower hydrocarbon
product; c) lowering the second temperature of the first separation
liquid to a third temperature by use of a heat exchanger; d)
transporting the first separation liquid to a holding tank and
allowing the first wax product to float to the surface of the first
separation liquid; and e) removing the first wax product from the
first separation liquid, thereby producing a second separation
liquid.
[0045] In one aspect, where appropriate, the second separation
liquid can recycled back into step b) and is the first separation
liquid. In one aspect, the recycling of the second separation
liquid is continuous. In one aspect, the first separation liquid
and the second separation liquid being recycled in the separation
tank can have a temperature from about 160.degree. C. to about
190.degree. C.
[0046] In one aspect, the first temperature is from about
230.degree. C. to about 250.degree. C. For example, the first
temperature can be from about 235.degree. C. to about 245.degree.
C.
[0047] In one aspect, the second temperature is from about
160.degree. C. to about 190.degree. C. For example, the second
temperature can be from about 165.degree. C. to about 185.degree.
C., such as, from about 170.degree. C. to about 180.degree. C.
[0048] In one aspect, the third temperature is from about
140.degree. C. to about 145.degree. C. For example, the third
temperature is from about 142.degree. C. to about 144.degree.
C.
[0049] In one aspect, the fourth temperature is from about
160.degree. C. to about 190.degree. C. For example, the fourth
temperature can be from about 165.degree. C. to about 185.degree.
C., such as, from about 170.degree. C. to about 180.degree. C.
[0050] In one aspect, the first product gas stream comprises less
than 5% of the first wax product. For example, the first product
gas stream can comprise less than 3% of the first wax product. In
another example, first product gas stream can comprise less than 2%
of the first wax product. In one aspect, the first product gas
stream comprises from about 1% to about 5% of the first wax
product.
[0051] In one aspect, the second product gas stream comprises less
than 0.5% of the first wax product. For example, the second product
gas stream can comprise less than 0.3% of the first wax product. In
another example, the second product gas stream can comprise less
than 0.1% of the first wax product. In one aspect, the second
product gas stream comprises from about 0.01% to 0.5% of the first
wax product.
[0052] In one aspect, at least 50% of the first wax product is
separated from the first product gas stream. For example, at least
70% of the first wax product is separated from the first product
gas stream. In another example, at least 80% of the first wax
product can be separated from the first product gas stream. In yet
another example, at least 85% of the first wax product can be
separated from the first product gas stream. In another example, at
least 90% of the first wax product can be separated from the first
product gas stream. In another example, at least 95% of the first
wax product can be separated from the first product gas stream. In
another example, at least 97% of the first wax product can be
separated from the first product gas stream. In another example, at
least 99% of the first wax product can be separated from the first
product gas stream.
[0053] In one aspect, the first product gas stream comprises from
about 50% to about 99% of the first lower hydrocarbon product. For
example, the first product gas stream can comprise from about 50%
to about 90% of the first lower hydrocarbon product. In another
example, the first product gas stream can comprise from about 60%
to about 80% of the first lower hydrocarbon product.
[0054] In one aspect, the first hydrocarbon product comprises C2-C5
hydrocarbons.
[0055] In one aspect, the first separation liquid comprises
silicone oil, an ionic liquid, or a glycol, or a combination
thereof. For example, the first separation liquid can comprise
silicone oil. In another example, the first separation liquid can
comprise an ionic liquid, such as ioniq liquids of silver and
copper salts, such as for example, silver tetrafluoroborate. In yet
another example, the first separation liquid can comprise a glycol.
The glycol can be a mono, di, or tri glycol compounds. Non-limiting
examples of suitable glycols include ethylene glycol, propylene
glycol, and 1,3, butanediol. The first separation liquid can be
selected to be a liquid that is inert to the first product gas
stream and has a boiling point above that of the temperature, such
as about 160.degree. C. to about 190.degree. C., during operating
pressure conditions of the separator tank. The operating pressure
of the separator tank can be from about 3 bar to about 12 bar.
[0056] In one aspect, the second separation liquid comprises less
than 0.5% of the first wax product. For example, the second
separation liquid can comprise less than 0.3% of the first wax
product. In another example, the second separation liquid can
comprise less than 0.1% of the first wax product. In another
example, the second separation liquid can comprise less than 0.05%
of the first wax product. In one aspect, the second separation
liquid comprises from about 0.01% to 0.5% of the first wax
product.
[0057] In one aspect, the second separation liquid is substantially
identical to the first separation liquid. For example, the second
separation can be the first separation liquid.
[0058] In one aspect, the separating at least a portion of the
first wax product from the first product gas stream is performed in
a separator tank at a pressure from about 3 bar to about 12 bar.
For example, the separating at least a portion of the first wax
product from the first product gas stream is performed in a
separator tank at a pressure from about 5 bar to about 10 bar.
[0059] In one aspect, the first product gas stream comprises less
than 10% of C6+ hydrocarbons. For example, the first product gas
stream comprises less than 8% of C6+ hydrocarbons. In another
aspect, the first product gas stream comprises less than 5% of C6+
hydrocarbons. In yet another aspect, the first product gas stream
comprises from about 1% to about 10% of C6+ hydrocarbons.
[0060] In one aspect, the first wax product is in solid form when
separated from the first gas product stream. In another aspect, the
first wax product is in liquid form when separated from the first
gas product stream.
[0061] In one aspect, the step of removing the first wax product
from the first separation liquid comprises scrapping or skimming
the first wax product from the first separation liquid.
[0062] In one aspect, the method further comprises transporting the
second separation liquid having the fourth temperature to a
separator tank.
4. Aspects
[0063] In view of the described catalyst and catalyst compositions
and methods and variations thereof, herein below are described
certain more particularly described aspects of the inventions.
These particularly recited aspects should not however be
interpreted to have any limiting effect on any different claims
containing different or more general teachings described herein, or
that the "particular" aspects are somehow limited in some way other
than the inherent meanings of the language and formulas literally
used therein.
[0064] Aspect 1: A method comprising the steps of: a) providing a
first product gas stream comprising a first wax product and a first
lower hydrocarbon product, wherein the first gas product has a
first temperature and the first wax product and first lower
hydrocarbon product are in gas form; and b) separating at least a
portion of the first wax product from the first product gas stream
by lowering the first temperature of the first product gas stream
by contacting the first product gas stream with a first separation
liquid having a second temperature, thereby liquefying or
solidifying at least a portion of the first wax product into the
first separation liquid, thereby producing a second product gas
stream comprising at least a portion of the first lower hydrocarbon
product.
[0065] Aspect 2: The method of aspect 1, wherein the method further
comprises the steps of: c) lowering the second temperature of the
first separation liquid to a third temperature by use of a heat
exchanger; d) transporting the first separation liquid to a holding
tank and allowing the first wax product to float to the surface of
the first separation liquid; and e) removing the first wax product
from the first separation liquid, thereby producing a second
separation liquid.
[0066] Aspect 3: The method of aspect 2, wherein the second
separation liquid is recycled back into step b) and is the first
separation liquid.
[0067] Aspect 4: The method of any one of aspects 1-3, wherein the
first temperature is from about 230.degree. C. to about 250.degree.
C.
[0068] Aspect 5: The method of any one of aspects 1-4, wherein the
second temperature is from about 160.degree. C. to about
190.degree. C.
[0069] Aspect 6: The method of any one of aspects 2-5, wherein the
third temperature is from about 140.degree. C. to about 145.degree.
C.
[0070] Aspect 7: The method of any one of aspects 1-6, wherein the
first product gas stream comprising less than 5% of the first wax
product.
[0071] Aspect 8: The method of any one of aspects 1-7, wherein the
second product gas stream comprising less than 0.5% of the first
wax product.
[0072] Aspect 9: The method of any one of aspects 1-7, wherein the
first product gas stream comprising from about 50% to about 99.5%
of the first lower hydrocarbon product.
[0073] Aspect 10: The method of any one of aspects 1-9, wherein at
least 50% of the first wax product is separated from the first
product gas stream.
[0074] Aspect 11: The method of any one of aspects 1-9, wherein at
least 80% of the first wax product is separated from the first
product gas stream.
[0075] Aspect 12: The method of any one of aspects 1-9, wherein at
least 90% of the first wax product is separated from the first
product gas stream.
[0076] Aspect 13: The method of any one of aspects 1-12, wherein
the first hydrocarbon product comprises C2-C5 hydrocarbons.
[0077] Aspect 14: The method of any one of aspects 1-12, wherein
the first separation liquid comprises silicone oil, an ionic
liquid, or a glycol, or a combination thereof.
[0078] Aspect 15: The method of any one of aspects 1-14, wherein
the second separation liquid comprises less than 0.5% of the first
wax product.
[0079] Aspect 16: The method of any one of aspects 1-15, wherein
the second separation liquid is substantially identical to the
first separation liquid.
[0080] Aspect 17: The method of any one of aspects 1-16, wherein
the separating at least a portion of the first wax product from the
first product gas stream is performed in a separator tank at a
pressure from about 3 bar to about 12 bar.
[0081] Aspect 18: The method of any one of aspects 1-18, wherein
the first product gas stream comprises less than 10% of C10+
hydrocarbons.
[0082] Aspect 19: A method comprising the steps of: a) providing a
first separation liquid comprising a first wax product, wherein the
first separation liquid has a second temperature and wherein the
first wax product is in liquid or solid form; b) lowering the
second temperature of the first separation liquid to a third
temperature by use of a heat exchanger; c) transporting the first
separation liquid to a holding tank and allowing the first wax
product to float to the surface of the first separation liquid; and
d) removing the first wax product from the first separation liquid,
thereby producing a second separation liquid.
[0083] Aspect 20: The method of aspect 19, wherein the first
separation liquid comprises at least 10% of the first wax
product.
[0084] Aspect 21: The method of aspects 19 or 20, wherein the
second temperature is from about 160.degree. C. to about
190.degree. C.
[0085] Aspect 22: The method of any one of aspects 19-21, wherein
the third temperature is from about 140.degree. C. to about
145.degree. C.
[0086] Aspect 23: The method of any one of aspects 19-22, wherein
step a) is performed in a holding tank.
[0087] Aspect 24: The method of aspect 23, wherein the method
further comprises the step of transporting the first separation
liquid comprising the first wax product from the holding tank to
the heat exchanger.
[0088] Aspect 25: The method of any one of aspects 19-24, wherein
the first wax product is in solid form.
[0089] Aspect 26: The method of any one of aspects 19-25, wherein
removing the first wax product from the first separation liquid
comprises scrapping or skimming the first wax product from the
first separation liquid.
[0090] Aspect 27: The method of any one of aspects 19-26, wherein
the second separation liquid comprises less than 0.5% of the first
wax product.
[0091] Aspect 28: The method of any one of aspects 19-27, wherein
the method further comprises the step of transporting the second
separation liquid to a heat exchanger and increasing the
temperature of the second separation liquid to a fourth
temperature.
[0092] Aspect 29: The method of aspect 28, wherein the fourth
temperature is from about 160.degree. C. to about 190.degree.
C.
[0093] Aspect 30: The method of aspects 28 or 29, wherein the
method further comprises transporting the second separation liquid
having the fourth temperature to a separator tank.
[0094] Aspect 31: The method of aspect 30, wherein the method
further comprises the steps of: e) providing a first product gas
stream comprising a first wax product and a first lower hydrocarbon
product, wherein the first gas product has a first temperature and
the first wax product and first lower hydrocarbon product are in
gas form; and f) separating at least a portion of the first wax
product from the first product gas stream by lowering the first
temperature of the first product gas stream by contacting the first
product gas stream with the second separation liquid having the
fourth temperature, thereby liquefying or solidifying at least a
portion of the first wax product into the second separation,
thereby producing a second product gas stream comprising at least a
portion of the first lower hydrocarbon product.
[0095] Aspect 32: The method of aspect 31, wherein the first
product gas stream comprising less than 5% of the first wax
product.
[0096] Aspect 33: The method of aspects 31 or 32, wherein the
second product gas stream comprising less than 0.5% of the first
wax product.
[0097] Aspect 34: The method of any one of aspects 31-33, wherein
the first product gas stream comprising from about 50% to about
99.5% of the first lower hydrocarbon product.
[0098] Aspect 35: The method of any one of aspects 31-34, wherein
at least 50% of the first wax product is separated from the first
product gas stream.
[0099] Aspect 36: The method of any one of aspects 31-35, wherein
at least 80% of the first wax product is separated from the first
product gas stream.
[0100] Aspect 37: The method of any one of aspects 31-36, wherein
at least 90% of the first wax product is separated from the first
product gas stream.
[0101] Aspect 38: The method of any one of aspects 31-37, wherein
the first hydrocarbon product comprises C2-C5 hydrocarbons.
[0102] Aspect 39: The method of any one of aspects 19-38, wherein
the first separation liquid comprises silicon oil, an ionic liquid,
or a glycol, or a combination thereof.
[0103] Aspect 40: A system comprising: a) a separator tank
comprising a first inlet, a second inlet, a first outlet, and a
second outlet; b) a heat exchanger; c) a holding tank comprising a
third inlet and a third outlet, wherein the separator tank is in
fluid communication with the holding tank via a first connector and
via a second connector, wherein the first connector is connected to
the first outlet of the separator tank and to the third inlet of
the holding tank, wherein the second connector is connected to the
first inlet of the separator tank and to the third outlet of the
holding tank, and wherein the first connector and the second
connector are in communication with the heat exchanger.
[0104] Aspect 41: The system of aspect 40, wherein the system
further comprises a Fisher-Tropsch reactor comprising a fourth
inlet and a fourth outlet, wherein the separator tank is in fluid
communication with the Fisher-Tropsch via a third connector,
wherein the third connector is connected to the to the fourth
outlet of the Fisher-Tropsch reactor and the second inlet of the
separator tank.
[0105] Aspect 42: The system of aspect 40 or 41, wherein separator
tank is configured to withstand pressure above 15 bar.
[0106] Aspect 43: The system of any one of aspect 40-42, wherein
the holding tank is configured to hold at least 1,000 liters of
separation fluid.
[0107] Aspect 44: The system of any one of aspect 40-43, wherein
the separator tank is configured to hold at least 1,000 liters of
separation fluid.
[0108] Aspect 45: The system of any one of aspect 40-44, wherein
the second connector is in communication with a pump.
[0109] Aspect 46: The system of any one of aspect 40-45, wherein
the separator tank comprises a fifth outlet.
[0110] Aspect 47: The system of any one of aspect 40-46, wherein
the holding tank comprises a sixth outlet.
* * * * *