U.S. patent application number 15/184475 was filed with the patent office on 2016-12-29 for temperature control unit for a gaseous or liquid medium.
This patent application is currently assigned to AVL LIST GMBH. The applicant listed for this patent is AVL LIST GMBH. Invention is credited to Michael Buchner, Vedran Burazer.
Application Number | 20160377330 15/184475 |
Document ID | / |
Family ID | 55907745 |
Filed Date | 2016-12-29 |




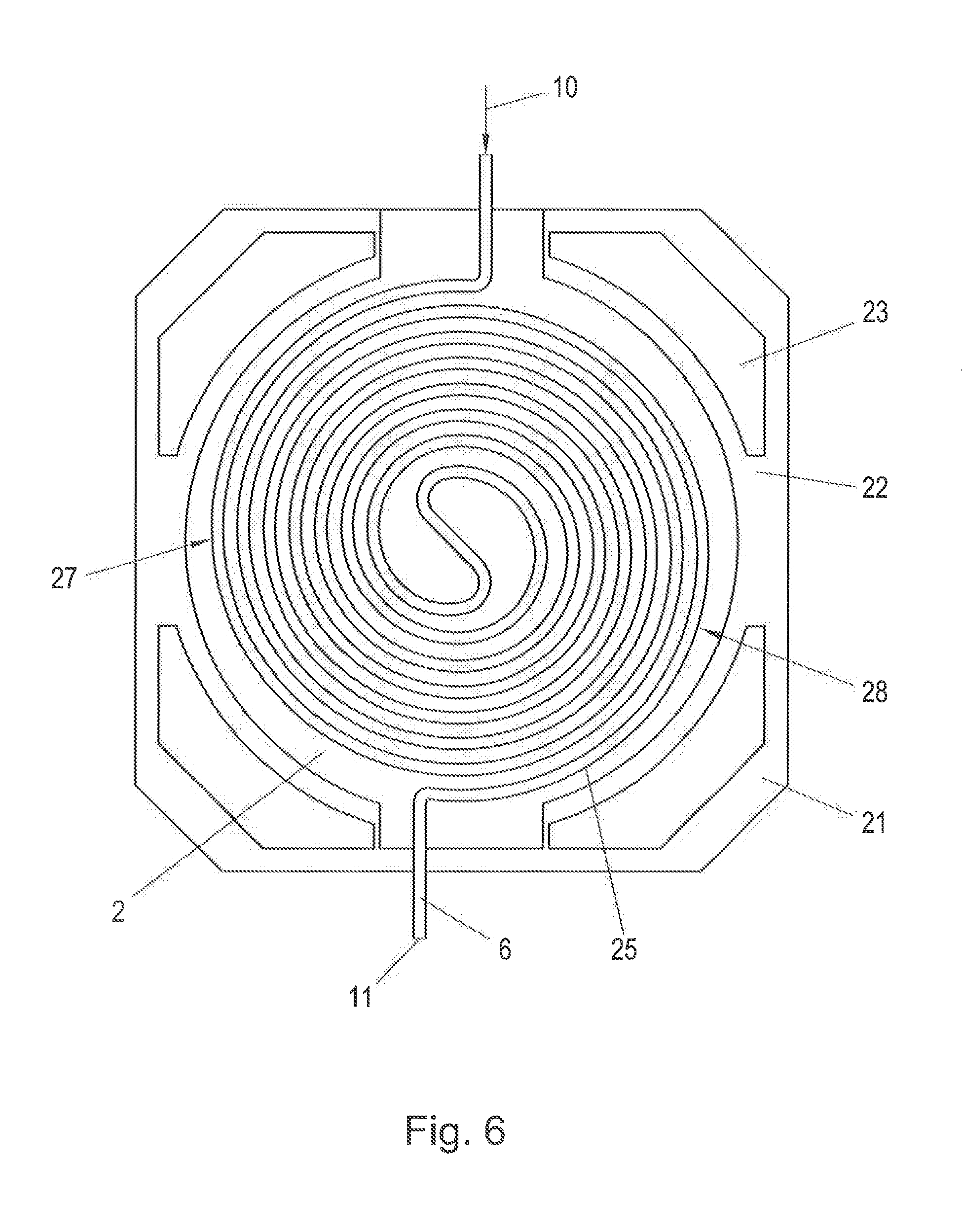

United States Patent
Application |
20160377330 |
Kind Code |
A1 |
Burazer; Vedran ; et
al. |
December 29, 2016 |
Temperature Control Unit for a Gaseous or Liquid Medium
Abstract
For a temperature control unit for gaseous or liquid medium with
a highly dynamic temperature regulation of the medium, the
temperature control unit (1) is designed with a base body (2) and a
cooling body (5) between which are arranged multiple thermoelectric
modules (7) and with a media line (6) in the base body (2), and it
is provided that the mass ratio of the thermal storage mass of the
cooling body (5) to the thermal storage mass of the base body (2)
and the media line (6) arranged therein is in the range of 0.5 to
1, advantageously in the range of 0.7 to 0.8.
Inventors: |
Burazer; Vedran; (Graz,
AT) ; Buchner; Michael; (Graz, AT) |
|
Applicant: |
Name |
City |
State |
Country |
Type |
AVL LIST GMBH |
GRAZ |
|
AT |
|
|
Assignee: |
AVL LIST GMBH
GRAZ
AT
|
Family ID: |
55907745 |
Appl. No.: |
15/184475 |
Filed: |
June 16, 2016 |
Current U.S.
Class: |
62/3.3 |
Current CPC
Class: |
F25B 2321/0251 20130101;
F25B 2321/0252 20130101; Y02T 10/12 20130101; H01L 35/32 20130101;
Y02T 10/166 20130101; F25B 2321/023 20130101; F25B 21/04
20130101 |
International
Class: |
F25B 21/04 20060101
F25B021/04 |
Foreign Application Data
Date |
Code |
Application Number |
Jun 23, 2015 |
AT |
A 50531/2015 |
Claims
1. A temperature control unit for temperature control of a gaseous
or liquid medium by means of a number of thermoelectric modules,
which are arranged between a base body and a cooling body, and a
media line through which the gaseous or liquid medium flows is
arranged in the base body, wherein the mass ratio of the thermal
storage mass of the cooling body to the thermal storage mass of the
base body and the media line arranged therein is in the range of
0.5 to 1, advantageously in the range of 0.7 to 0.8.
2. The temperature control unit according to claim 1, wherein the
mass ratio is 0.75.
3. The temperature control unit according to claim 1, wherein a
groove into which the media line is pressed is provided in the base
body.
4. The temperature control unit according to claim 3, wherein the
media line is arranged in the base body in the form of a spiral
leading from the outside to the inside.
5. The temperature control unit according to claim 3, wherein the
media line is arranged in the base body in the form of a two-start
spiral in a first spiral start leading from the outside to the
inside and in a second spiral start connected radially at the
inside to the first spiral start leading from the inside to the
outside.
6. The temperature control unit according to claim 5, wherein the
multiple thermoelectric modules are arranged in a plurality of rows
on the base body wherein the module heating power of a
thermoelectric module situated further toward the outside radially
is greater than the module heating power of a thermoelectric module
situated further toward the inside radially.
7. The temperature control unit according to claim 1, wherein the
base body is surrounded by a base body jacket wherein a plurality
of radial connecting webs which are connected to the base body
jacket are arranged over the circumference of the base body.
8. The temperature control unit according to claim 7, wherein the
base body jacket is designed to be partially hollow.
9. The temperature control unit according to claim 1, wherein a
cooling line through which cooling medium for cooling the cooling
body flows as needed is arranged in the cooling body.
10. The temperature control unit according to claim 9, wherein the
cooling line is arranged in the form of a spiral.
11. The temperature control unit according to claim 1, wherein the
media line is arranged in the base body in the form of a spiral
leading from the outside to the inside.
12. The temperature control unit according to claim 1, wherein the
media line is arranged in the base body in the form of a two-start
spiral in a first spiral start leading from the outside to the
inside and in a second spiral start connected radially at the
inside to the first spiral start leading from the inside to the
outside.
13. The temperature control unit according to claim 4, wherein the
multiple thermoelectric modules are arranged in a plurality of rows
on the base body wherein the module heating power of a
thermoelectric module situated further toward the outside radially
is greater than the module heating power of a thermoelectric module
situated further toward the inside radially.
Description
[0001] The present invention relates to a temperature control unit
for temperature control of a gaseous or liquid medium by means of a
number of thermoelectric modules which are arranged between a base
body and a cooling body and a media line through which the gaseous
or liquid medium flows is arranged in the base body.
[0002] For accurate measurement of the fuel consumption by an
internal consumption engine on a test stand, accurate conditioning
of the temperature and pressure of the fuel supplied to the
internal combustion engine is necessary. The fuel consumption is
often measured using a known Coriolis flow sensor. An example of
such a measurement of fuel consumption can be found in US
2014/0123742 A1, which is based on conditioning of liquid fuels. In
that application, the temperature of the fuel is regulated with a
cooling liquid by means of a heat exchanger. Extreme changes in
load cause extreme fluctuations in fuel consumption and in the
media temperature of the return flow (input temperature). However,
such a heat exchanger is sluggish, allowing only gradual changes in
temperature. Thus, the conditioning by means of a heat exchanger
that has been described is not suitable for extreme load
alternations (changes in input temperature). With the current state
of the art, this leads to the result that it is necessary to allow
a settling time after such a load reversal. During this period of
time, the temperature is not stable and a high-precision
measurement is impossible for flow sensors. For operation that is
independent of the changes in input temperature, one option is to
increase the power density of the heat exchanger, but this is not
readily feasible technically and would require a redesign of the
heat exchanger, if it were possible at all. If the power density
remains the same, this would result in a need for a much larger
amount of space. Another possibility might consist of a more
aggressive regulation of the heat exchanger, but this in turn would
mean greater overshooting and undershooting, and, associated with
this, inferior dynamics with respect to possible changes in the
target temperature. However, increasing the size of the heat
exchanger would also be helpful only in the case of liquids. In the
case of gaseous media, a change in flow would immediately cause a
change in pressure and a change in target temperature. The heat
exchanger would therefore have to enable extremely fast changes in
target temperature but this cannot be achieved in practical terms
for a heat exchanger operated with a cooling liquid. To do so, the
available power would have to be further increased at the same
mass, but merely increasing the power would be of no benefit in
this case. However, one remaining alternative is to adjust the
regulator of the heat exchanger more aggressively, although that
would in turn result in even greater undershooting and
overshooting. Rapid and precise temperature control would be
impossible in this way.
[0003] Dynamic temperature regulation by means of a heat exchanger
is also relatively inaccurate, i.e., if a constant temperature is
not to be set. Apart from this, such a heat exchanger would
necessitate additional parts and controllers for operating the heat
exchanger, which would also make the plant more expensive.
[0004] DE 10 2010 046 946 A1 proposes controlling the temperature
of the fuel in a conditioning plant by means of thermoelectric
modules (so-called Peltier elements). Thus, because of the low
storage masses achieved, a highly dynamic temperature regulation is
possible, whereby the fuel can be both heated and cooled. This
apparatus is also aimed specifically at conditioning liquid
fuels.
[0005] There is the additional problem with gaseous fuels such as
natural gas or hydrogen that the gaseous fuel is usually available
or supplied, at a high pressure and consequently must first be
depressurized to a lower pressure, which is required for use as a
fuel in an internal combustion engine. However, when the gaseous
fuel such as natural gas is depressurized, the fuel cools down
drastically, which can be problematic for the downstream component
of the conditioning plant, for example, due to the formation of
condensate and ice on the gas lines or other components in the gas
line. Therefore, the gaseous fuel is usually heated before being
depressurized, so that the desired temperature of the fuel is
achieved by decompression. Because of the fluctuations in pressure
of the gaseous fuel supplied and also because of the dependence of
temperature on the composition of the gaseous fuel after
decompression, which can also vary, the temperature regulation of
the gaseous fuel must be highly dynamic prior to decompression in
order to be able to maintain a constant temperature after
decompression and before the flow measurement. In addition the
required heating power for temperature control of the fuel also
depends greatly on the prevailing flow rate, which also
necessitates a highly dynamic temperature regulation in the case of
rapidly changing flow rates.
[0006] Such a highly dynamic temperature regulation necessitates,
first of all, a regulating method that is capable of carrying out
highly dynamic regulating intervention (in the sense of rapid
changes in temperature), and secondly, a temperature control unit
that is also capable of implementing the highly dynamic control
intervention measures. Consequently, such a temperature control
unit must be capable of implementing the required temperature
changes in the flowing fuel within a very short period of time. In
addition, a high thermal stability is also desired, also if under
some circumstances high demands cannot be made of the dynamics of
the temperature regulation because in certain applications a high
precision and extremely constant regulation is required. These
requirements necessitate a temperature control unit with a high
heating and cooling power, but under some circumstances it may also
be necessary to change rapidly between heating and cooling. Apart
from this, an accurate temperature regulation must also be possible
in order to prevent excessive overregulation of the temperature
(either overheating or undercooling).
[0007] DE 10 2010 046 946 A1 gives the indication that for a highly
dynamic temperature regulation, small thermal storage masses of the
temperature control unit are advantageous.
[0008] U.S. Pat. No. 6,502,405 B1 discloses a heat exchanger
element with Peltier elements for heating or cooling fuel in a
vehicle. The heat exchanger element consists of a thermal
conduction block in which a fuel line is installed in a meandering
layout and which is insulated thermally on a first side. Peltier
elements, which are thermally connected to a cooling body, are
located on the second side of the thermal conduction block. The
cooling body is typically designed with a large surface area and a
small storage mass in order to maximize the heat dissipation
capacity. In addition, a fan is also provided on the cooling body
in order to further increase the capacity for dissipation of heat.
Thus, the heat exchanger element of U.S. Pat. No. 6,502,405 B1 is
also designed for a low thermal storage mass in order to be able to
rapidly dissipate the heat to the surroundings via the cooling
body. Due to the meandering layout of the fuel line in a heat
exchanger element, however, there is also an uneven heating of the
fuel, which makes the temperature regulation more difficult because
all of the Peltier elements are controlled with the same power
supply voltage. The uneven heating results in a higher temperature
difference between the emission temperature of the medium and the
surface of the Peltier elements, which in turn leads to a lower
maximum emission temperature of the medium because the Peltier
elements cannot be heated indefinitely. Or there is a lower maximum
flow rate at a predetermined target emission temperature. Apart
from this, more thermal energy is stored in the heat conducting
block due to the greater temperature difference. This thermal
energy must be dissipated again when there is a change in the
target temperature, but that in turn makes the heat exchanger
element more sluggish. For a more uniform heating of the fuel, the
individual Peltier elements would either have to be coordinated
with one another, i.e., different Peltier elements provided along
the fuel line, or the Peltier elements would have to be supplied
and regulated individually. However, both options would be very
complicated and therefore a disadvantage.
[0009] However, the problems described above can basically occur
with any gaseous or liquid medium whose temperature is to be
regulated in a temperature control unit, not just with fuels.
[0010] Against the background of this prior art, it is an object of
the present invention to provide a temperature control unit for a
gaseous or liquid medium which permits a particularly highly
dynamic and accurate temperature regulation of the medium.
[0011] This object is achieved according to the invention by
selecting the mass ratio of the thermal storage mass of the cooling
body to the thermal storage mass of the base body and the media
line arranged therein to be in the range of 0.5 to 1,
advantageously in the range of 0.7 to 0.8, and most especially
advantageously to be 0.75.
[0012] It has been found that for a highly dynamic temperature
regulation of a medium by means of a temperature control unit
according to the preamble of claim 1, in particular when a rapid
and repeated change in direction of heat flow is necessary, it is a
disadvantage for the storage mass to be too low, as suggested by
the state of the art. It has surprisingly been found that a certain
mass ratio between the mass of the cooling body and the mass of the
base body together with the media line arranged therein is
advantageous for the regulation of temperature. The reason for this
is apparently the fact that due to the greater mass of the cooling
body, a thermal storage mass is formed and therefore thermal energy
is not released to the environment too rapidly. This stored energy
can then optionally be used for support in heating the fuel, so
that the temperature control can be achieved more rapidly and with
a greater precision.
[0013] A compact design of the temperature control unit is obtained
when a groove into which the media line is pressed is provided in
the base body.
[0014] For a very efficient temperature control, it is advantageous
if the media line in the base body is arranged in a spiral pattern
from the outside to the inside. Due to this arrangement of the
media line in the base body in the form of a single-start spiral, a
particularly uniform and efficient temperature control of the
medium can be achieved. Due to the spiral shape, the temperature
control unit may be designed very compactly because the spiral
passes can be arranged close to one another. Therefore, a
thermoelectric module may also cover multiple spiral passes, which
improve the efficiency of the temperature control unit and the
uniformity in heating. This makes it possible to achieve a
particularly highly dynamic and accurate and stable temperature
regulation of the medium.
[0015] Efficient temperature control is additionally supported when
the multiple thermoelectric modules are arranged in multiple rows
on the base body aligned around the periphery, wherein the module
heating power of a thermoelectric module situated further toward
the outside radially is greater than the module heating power of a
thermoelectric module situated further toward the inside radially.
In this way, the temperature of the medium flowing in from the
outside can be regulated in the region of the higher heating power
on the outside radially, which permits rapid and marked changes in
temperature. The modules are then preferably coordinated with one
another so that the temperature spread is minimal at the maximum
flow rate between the module surface and the emission temperature
of the medium. It has been found that this is the case when all the
modules are at approximately the same surface temperature. Due to
the peripheral arrangement, the thermoelectric modules within one
row are naturally almost at the same temperature. Only the
different rows would have to be balanced in this regard, which is a
significant simplification in contrast to a meandering arrangement
of the media line, because it is no longer necessary for all the
thermoelectric modules to be balanced for the same result to be
achieved (minimum temperature spread).
[0016] Furthermore, the module heating power can be optimally
adapted to the conditions and modules having a lower module heating
power can be installed on the inside radially.
[0017] To concentrate the thermal energy in the base body and to
prevent an excessive drain of thermal energy, the base body is
advantageously surrounded by a base body jacket wherein a plurality
of radial connecting webs which are connected to the base body
jacket are arranged over the circumference of the base body. This
also increases the efficiency of the temperature control unit. This
can be further improved if the base body jacket is designed to be
partially hollow because this achieves even better thermal
insulation between the base body and the surroundings.
[0018] It may be advantageous to arrange a cooling line in the
cooling body through which cooling medium for cooling the cooling
body flows as needed in order to be able to dissipate heat from the
cooling body more rapidly. This may be useful in particular in the
case of gases without a pronounced Joule-Thomson effect or with
liquid media because in these cases, frequent reversal of polarity
of the thermal modules may be necessary. The cooling line is then
advantageously again arranged in a spiral.
[0019] The present invention is explained in greater detail below
with reference to FIGS. 1 to 7, which illustrate advantageous
embodiments of the invention as an example, schematically and
without restriction, in which:
[0020] FIG. 1 shows a perspective view of the temperature control
unit according to the invention,
[0021] FIG. 2 shows a view of a temperature control unit with the
cooling body removed,
[0022] FIGS. 3 and 4 show views of the base body of a temperature
control unit,
[0023] FIG. 5 shows a view of the media line in the temperature
control unit,
[0024] FIG. 6 shows another advantageous arrangement of the media
line in the base body, and
[0025] FIG. 7 shows a temperature control unit with a cooling line
in the cooling body.
[0026] FIG. 1 shows a perspective view of the temperature control
unit 1 according to the invention. The temperature control unit 1
consists of a base body 2 on which any fastening elements 3 may be
provided for fastening the temperature control unit 1 such as, for
example, feet in the exemplary embodiment shown here. On a first
side of the base body 2, a thermal insulation element 4 is arranged
and a cooling body 5 is arranged on the opposite second side. A
media line 6 passes through the temperature control unit 1; a
gaseous or liquid medium such as a fuel whose temperature is
controlled at a desired level in the temperature control unit 1
flows through this media line 6. The media line 6 therefore has an
input connection 10 and an output connection 11, so that the
direction of flow of the medium through the temperature control
unit 1 is defined (indicated by arrows in FIG. 1).
[0027] FIG. 2 shows the temperature control unit 1 with the cooling
body 5 removed. A number of thermoelectric modules (Peltier
elements) 7, which are arranged on the base body 2, can be seen
therein. A thermoelectric module 7 is known to be a semiconductor
element, which is arranged between a first heating surface 9a
(facing the base body 2 here, but not visible in FIG. 2) and a
second heating surface 9b (facing the cooling body 5 here).
Depending on the polarity of the electric voltage supplied to the
semiconductor element, either the first heating surface 9a is
hotter than the second heating surface 9b or vice versa. Since the
design and function of such thermoelectric modules 7 are
sufficiently well known and such thermoelectric modules 7 are
available commercially in various power classes, they will not be
discussed in greater detail here.
[0028] Thus, depending on the polarity of the power supply voltage,
which is supplied via terminals 8, for example, it is possible to
provide both heating and cooling with such a thermoelectric module
7. "Heating" here means that heat is supplied to the base body 2,
and "cooling" means that heat is withdrawn from the base body 2.
The heat flow between the base body 2 and the cooling body 5 can
thus be influenced with the thermoelectric modules 7.
[0029] The thermoelectric modules 7 are in thermodynamic contact
with the base body 2 via a first heating surface 9a (not visible in
FIG. 2) directly or indirectly (for example, via a heat transfer
element to improve the thermal conduction). The cooling body 5 is
arranged on the second heating surface 9b of the thermoelectric
module and is in thermally conducting contact either directly or
indirectly with the second hating surface 9b. A cooling body 5 and
the base body 2 are not arranged next to one another in order to
prevent direct thermally conducting contact between the cooling
body 5 and base body 2 (as can be seen in FIG. 1).
[0030] The base body 2 is illustrated in detail in FIGS. 3 and 4,
which show the different views of the base body 2. FIG. 3 shows the
side of the base body 2 on which the thermoelectric modules 7 are
arranged. The base body 2 is made essentially of a base plate 20,
which is surrounded along its circumference by a base body jacket
21. The base body jacket 21 is connected to the base plate 20 by
radial connecting webs 22, wherein the connecting webs 22 are
arranged so they are distributed around the circumference of the
base plate 20. In the circumferential direction between the
connecting webs 22, cavities 23 are formed, functioning as thermal
insulation between the base plate 2 and the base body jacket 21.
The heat flow from the base plate 20 into the base body jacket 21
is greatly reduced by the connecting webs 22 and the hollow spaces
23. Therefore, the heat introduced by the thermoelectric modules 7
into the base plate 20 remains concentrated there and flows only to
a minor extent through the base body jacket 21 to the surroundings.
This at the same time also achieves the goal that the base body
jacket 21 and thus the temperature control unit 1 are not heated
too greatly on the outside and that parasitic heat flows, which
would reduce the power and dynamics of the conditioning, are
minimized as much as possible.
[0031] The base body jacket 21 may additionally be designed to be
hollow, in that peripheral slots 24 are incorporated into the base
body jacket 21, also forming cavities for additional thermal
insulation.
[0032] FIG. 4 shows the other side of the base body 2, where it can
be seen that a groove 25, preferably a spiral groove into which the
media line 6 is pressed in the assembled state, is formed on the
backside of the base plate 20. The groove 25 here forms a
single-start flat spiral (Archimedean spiral, logarithmic spiral)
in the base body 2. The media line 6 is preferably guided in a
spiral pattern from the outside to the inside, emerging from the
temperature control unit 1 in the inner central region of the base
plate 20, wherein the media line 6 is deflected, preferably by
approx. 90.degree., out of the plane of the spiral on its exit from
the unit in order to allow the media line 6 to easily emerge from
the temperature control unit 1. Fundamentally, however, any other
type of guidance of the media line 6 in the base body 20 is also
conceivable.
[0033] The use of a media line 6 in the form of a single-start
spiral is very complex from the standpoint of manufacturing
technology because in this case the media line 6 extends in all
three dimensions.
[0034] In an alternative embodiment, the media line 6 is arranged
on the base body 2 in the form of a two-start planar spiral (also
known as Fermat's parabolic spiral), as described with reference to
FIG. 6. Again, a suitably shaped groove 25 to receive the media
line 6 may be formed in the base body 2 for this purpose. The
medium is supplied in a spiral pattern in the media line 6 from the
outside radially to the inside centrally via a first spiral pass
27. On the inside centrally the first spiral pass 27 is connected
to a second spiral pass 28 through which the medium is carried in
the media line 6 from the inside radially to the outside radially
in a spiral pattern. A first spiral pass 27 and a second spiral
pass 28 are always situated radially side-by-side due to the
two-start design of the groove 25. The medium is thus supplied on
the outside radially through the input connection 10 and removed on
the outside radially via the output connection 11. The two-start
spiral has the advantage that the media line 6 need not be
deflected out of the plane of the spiral, which is simple in terms
of the manufacturing technology. The two-start spiral, however, has
the disadvantage that the inflowing medium cools the medium flowing
out, so somewhat more power is needed and the resulting heating
achieved is less uniform. The temperature spread is therefore
greater but the thermoelectric modules of one row will all still be
at approximately the same temperature, in the case of coordinated
modules.
[0035] The single-start or two-start spiral need not absolutely be
designed as a circular spiral but instead may also have other
shapes such as rectangular, square, etc. Due to the spiral shape
the temperature control unit 1 may have a very compact design
because the spiral passes can be arranged close to one another.
Therefore, a great many running meters of medial line 6 can be
accommodated in a small space, which increases the available
surface for temperature control of the medium flowing through the
media line 6.
[0036] To be able to implement a dense packing of the media line 6,
bending radii must not come below minimum bending radii stipulated
whilst shaping of the media line 6. A meandering layout of the
media line would be a disadvantage in this regard because the
required bending radii for a dense packing are considerably smaller
than those with a spiral layout. With increasing pressure demands
with regard to the media line 6, the minimum bending radius usually
also increases because of the required increase in wall thickness.
Therefore, a meandering layout has a particularly negative effect
when there are high pressure demands, as in the present case.
[0037] FIG. 5 shows the thermal insulation element 4 with the media
line 6, which is advantageously a spiral-shaped single-start line
that is pressed into the base body 20 in the assembled state. Due
to the thermal insulation element 4 this achieves the result that
the heat introduced by the thermoelectric modules 7 into the base
plate 20 remains concentrated there and is not discharged to the
surroundings via the end face of the temperature control unit
1.
[0038] The thermoelectric modules 7 are preferably adapted in the
form of a circle and/or adapted to the spiral form and arranged in
multiple rows (that is at various radial distances) on the base
plate 20 (FIG. 2). Therefore, more thermoelectric modules 7 may be
arranged on the outside radially because of the resulting larger
circumference. The inflowing medium is thus thermally regulated in
the outer radial region where the heating power is higher, which
permits marked and rapid changes in temperature. It is also
advantageous if a thermoelectric module 7 which is arranged farther
toward the inside radially has a lower module heating power than a
thermoelectric module 7 arranged farther to the outside radially.
Since the media line 6 is preferably guided to the inside in a
single-start spiral, fewer and weaker (in the sense of less module
heating power) thermoelectric modules on the inside radially are
sufficient for temperature control on the medium. Thus, the
temperature control of the medium can also be optimized by the
arrangement and choice of the module heating power of the
individual thermoelectric modules 7 and a very uniform heating of
the medium can be achieved.
[0039] If an electric power supply voltage is applied to a
thermoelectric module 7, then as is known one of the heating
surfaces 9a, 9b of the thermoelectric module 7 is cooled off while
at the same time the opposing heating surface 9a, 9b is heated. The
maximum temperature spread between the heating surfaces 9a, 9b
depends on the operating temperature (temperature on the warmer
heating surface) of the thermoelectric module 7. The higher the
operating temperature, the higher the maximum achievable
temperature spread between the cold and hot heating surfaces 9a,
9b. Therefore, with the available thermoelectric modules 7,
temperatures of up to 200.degree. C. can be achieved on the hot
heating surface, with the cold heating surface not exceeding
100.degree. C. A highly dynamic regulation of the temperature is
made possible by simply reversing the polarity of the power supply
voltage. This regulation is supported in the temperature control
unit 1 according to the invention, in that the cooling body 5 is
used as a buffer storage in heating operation, i.e., when the
medium in the media line 6 is to be heated. Therefore the thermal
storage mass, however, should not be designed to be as small as
possible as is suggested in the prior art, but instead a certain
storage mass is desired in order to achieve this.
[0040] It has been found to be advantageous if the mass ratio of
the thermal storage mass of the cooling body 5 to the thermal
storage mass of the base body 2 and the media line 6 arranged
therein is selected to be in the range of 0.5 to 1, advantageously
0.7 to 0.8. A most especially advantageous temperature regulability
of the temperature control unit 1 was achieved at a mass ratio in
the range of 0.75 and/or at a mass ratio of 0.75. A tested
temperature control unit 1, for example, had a thermal storage mass
of the cooling body 5 of 5.4 kg and a thermal storage mass of the
base body 2 and the media line 6 arranged therein of 7.2 kg, which
yields a mass ratio of 0.75.
[0041] In one embodiment as shown in FIG. 3 or FIG. 6, in which the
base body jacket 21 is thermally separated from the base body 2 by
means of cavities 23, the mass of the base body jacket 21 is not
counted with the thermal storage mass of the base body. Likewise,
the insulation element 4 is not part of the thermal storage mass of
the base body 2.
[0042] At a constant heating demand of the temperature control unit
1, i.e., at a constant power supply voltage of the thermoelectric
module 7, a stable temperature spread is established on the
thermoelectric modules 7. As soon as less thermal energy and/or
heat for temperature control of the medium is/are needed, the power
supply voltage to the thermoelectric modules 7 is reduced so that
the temperature spread also becomes lower. The temperature on the
heating surface 9a of the thermoelectric module 7, which is in
contact with the base plate 20, therefore drops. At the same time,
the temperature on the opposite heating surface 9b rises. Thus
there is a temperature gradient between the heating surface 9b and
the cooling body, which is adjacent to it so that heat flows into
the cooling body 5 and is not dissipated to the surroundings
immediately because of the thermal storage mass of the cooling body
5, but instead is stored temporarily (at least for a limited period
of time). This temporarily stored thermal energy is available to
the temperature regulation and/or temperature control unit 1 as
support when more thermal energy is again needed for temperature
control of the medium. In this case, the power supply voltage would
be raised again so that the temperature spread on the
thermoelectric modules 7 would increase again. The temperature on
the heating surface 9b with which the cooling body 5 is in contact
would thus drop in comparison with the temperature of the cooling
body 5. This results in an inverted temperature gradient, thus
resulting in thermal energy (heat), which is stored in the cooling
body 5, then flowing into the base body 2 and thus supporting the
thermoelectric modules 7. Because of the thermal storage mass of
the cooling body 5, it is possible for the temperature control unit
1 to respond very rapidly and accurately to load alternations
and/or changes in temperature, and the typical excess temperature
control is can be prevented to the greatest extent. However, this
requires the thermal storage mass of the cooling body 5 to be not
too large or too small in comparison with the thermal storage mass
of the base body 2 and the media line 6 arranged therein.
[0043] The total surface area of the cooling body 5 should be
designed as a function of the operating temperature to be expected,
so that the heat stored in the cooling body 5 is not released too
rapidly to the surface but instead remains stored in the cooling
body 5 for a sufficient period of time. The surface is therefore
not to be dimensioned to be as large as possible and optimized for
the dissipation of heat, as it would be in a traditional cooling
body, but on the contrary, it is to be dimensioned so that the heat
remains stored in the cooling body 5.
[0044] Complete thermal insulation of the cooling body 5 from the
surroundings would also be a disadvantage because in the case of
frequent reversals of polarity, the temperature in the cooling body
5 might escalate.
[0045] For various media, the material of the media line 6 and the
heating power of the thermoelectric module 7 may optionally be
adapted. However, the general basic principle with the cooling body
5 as a storage mass for support of the temperature control unit 1
remains unaffected.
[0046] For certain gaseous media such as natural gas, there is a
great cooling in accordance with the Joule-Thomson effect due to
the required depressurization. With these gases the temperature
control unit 1 must usually only preheat the gaseous medium.
Cooling of these gases by the temperature control unit 1 is usually
not necessary. Therefore, it is normally also sufficient for these
applications to work only with the temperature spread of the
thermoelectric module 7. Reversal of the polarity to switch from
heating to cooling is rather not necessary.
[0047] Other gaseous media such as hydrogen do not have this
pronounced effect of extreme cooling due to the required
depressurization. On the contrary, there may even be a heating due
to depressurization. In temperature control of liquid media, often
no depressurization is necessary because the liquid medium is
already at the correct pressure.
[0048] In the case of gases without a pronounced Joule-Thomson
effect or with liquid media, the temperature control unit 1
therefore must often switch between heating and cooling the gaseous
medium in order to keep the temperature constant as a function of
the pressure and the flow rate. In particular in the case of
cooling, however, it may happen that because of the lower surface
area of the cooling body 5, the heat formed, in particular the
waste heat of the thermoelectric modules 7, cannot be dissipated
rapidly enough. Therefore, when using temperature control unit 1
with such gaseous or liquid media, provisions may also be taken to
additionally cool the cooling body 5 as needed. Therefore, a
cooling line 12 may be introduced into the cooling body 5. The
cooling liquid is sent through this line for the additional cooling
of the cooling body 5. Such a design is indicated in FIG. 7. The
cooling line 12 may again be arranged in the cooling body 5 in the
form of a single-start or two-start spiral as described above with
respect to the media line 6. Therefore, the cooling body 5 may also
be designed in multiple parts in order to be able to introduce the
cooling line 12. However, other embodiments of the cooling line 12
are of course also conceivable.
[0049] In the exemplary embodiment shown in FIG. 7, grooves 31 are
cut into a cooling body base body 30, for example by milling, in
order to form the cooling line 12. The grooves 31 are preferably
cut in the form of spirals as described above. The cooling body
base body 30 with the grooves 31 is covered with a cooling body
cover 32 in order to form the cooling body 5.
[0050] If a separate line is used as cooling line 12 in the cooling
body 5 (like the media line 6 in the base body), then the cooling
line 12 would also be part of the thermal storage mass of the
cooling body 5.
[0051] To be able to connect the cooling line 12 in the cooling
body 5, a cooling medium supply connection 34 and a cooling medium
removal connection 33 may be provided on the cooling body. The
cooling medium is preferably supplied from the inside and removed
centrally on the outside.
* * * * *