U.S. patent application number 14/930104 was filed with the patent office on 2016-12-29 for thermoelectric element of vehicle exhaust system.
The applicant listed for this patent is Hyundai Motor Company. Invention is credited to Hong Kil Baek, Jin Woo Kwak, Han Saem Lee, Seung Woo Lee, Tae Won Lee, Su Jung Noh, Kyong Hwa Song.
Application Number | 20160376971 14/930104 |
Document ID | / |
Family ID | 57537234 |
Filed Date | 2016-12-29 |

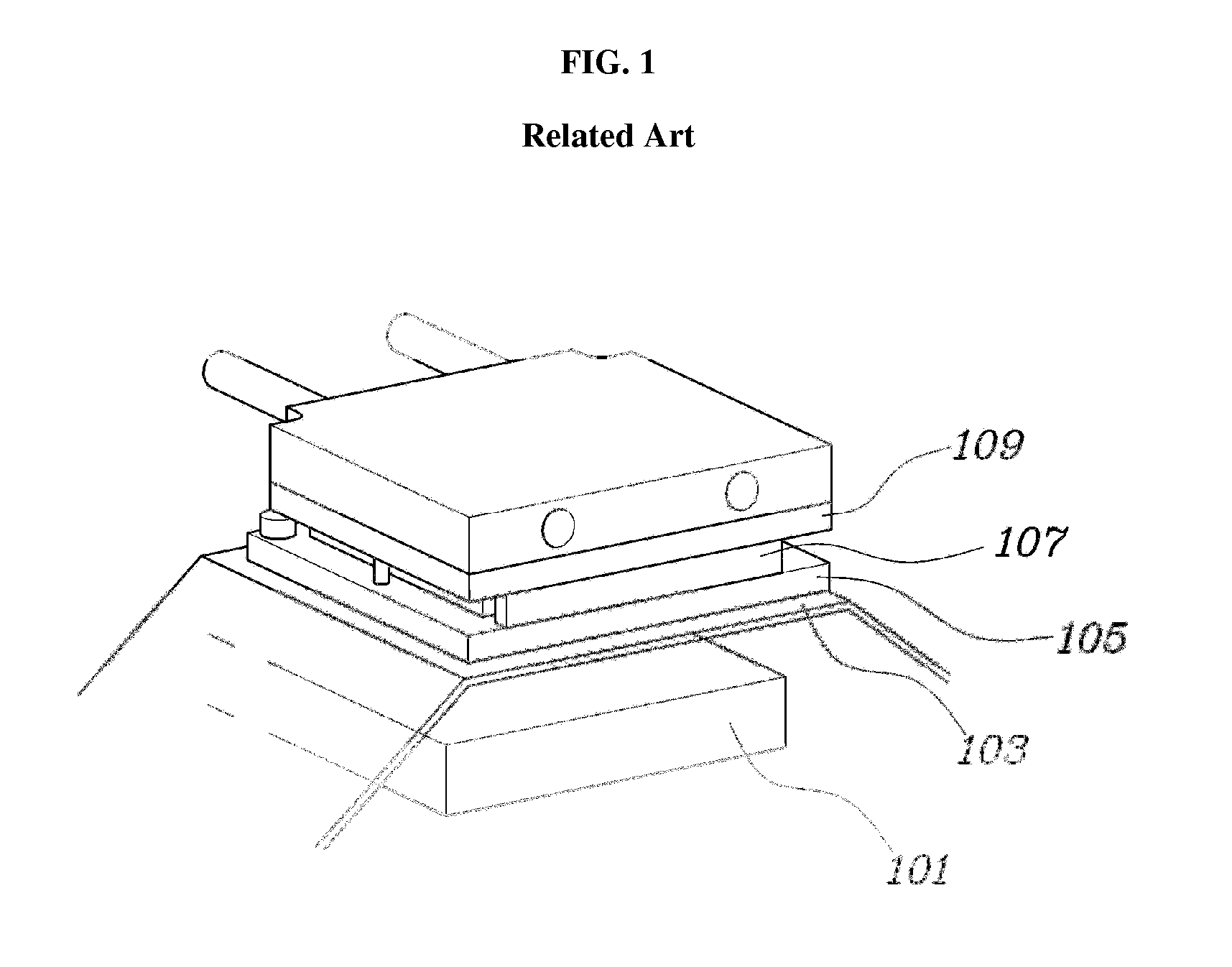
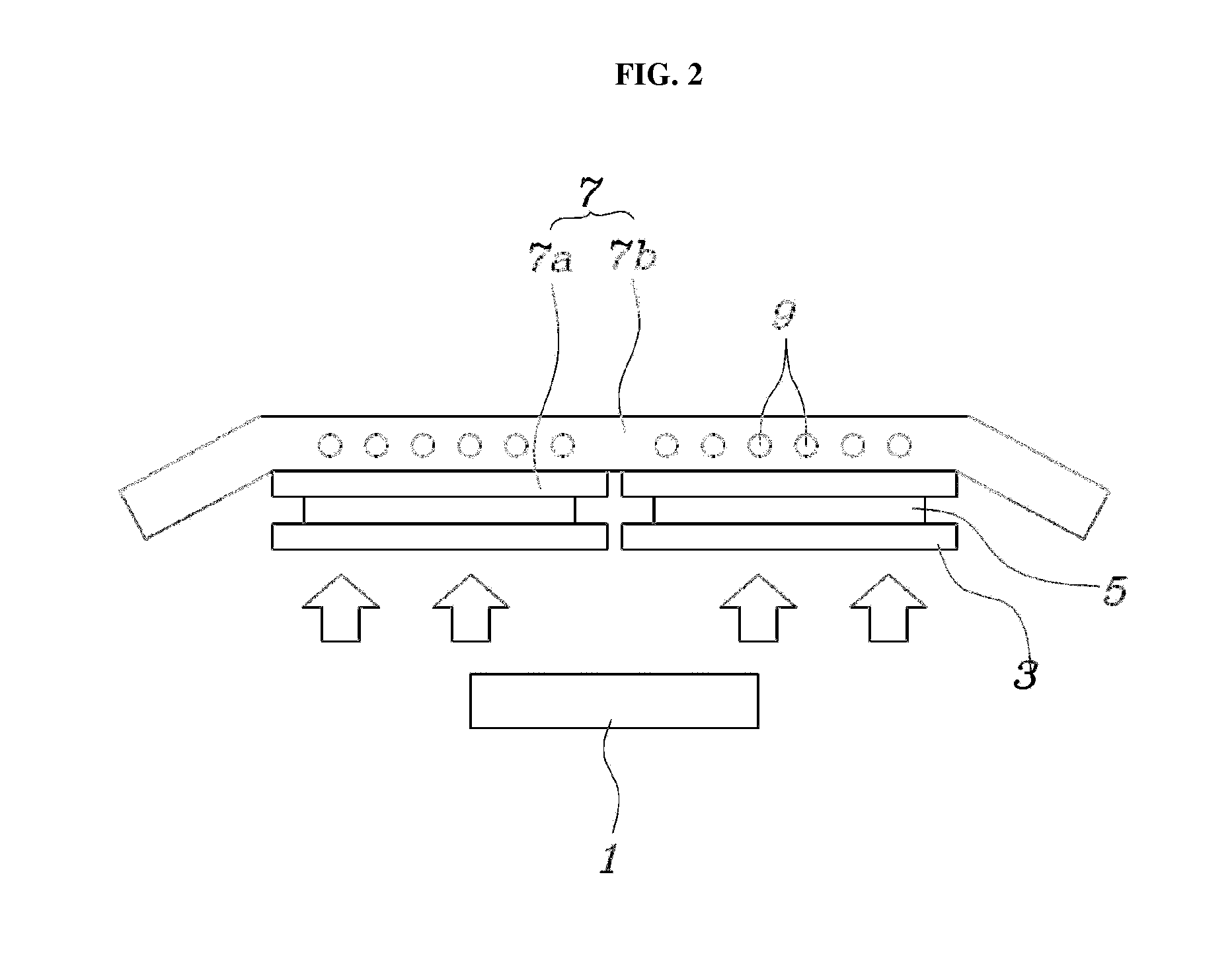
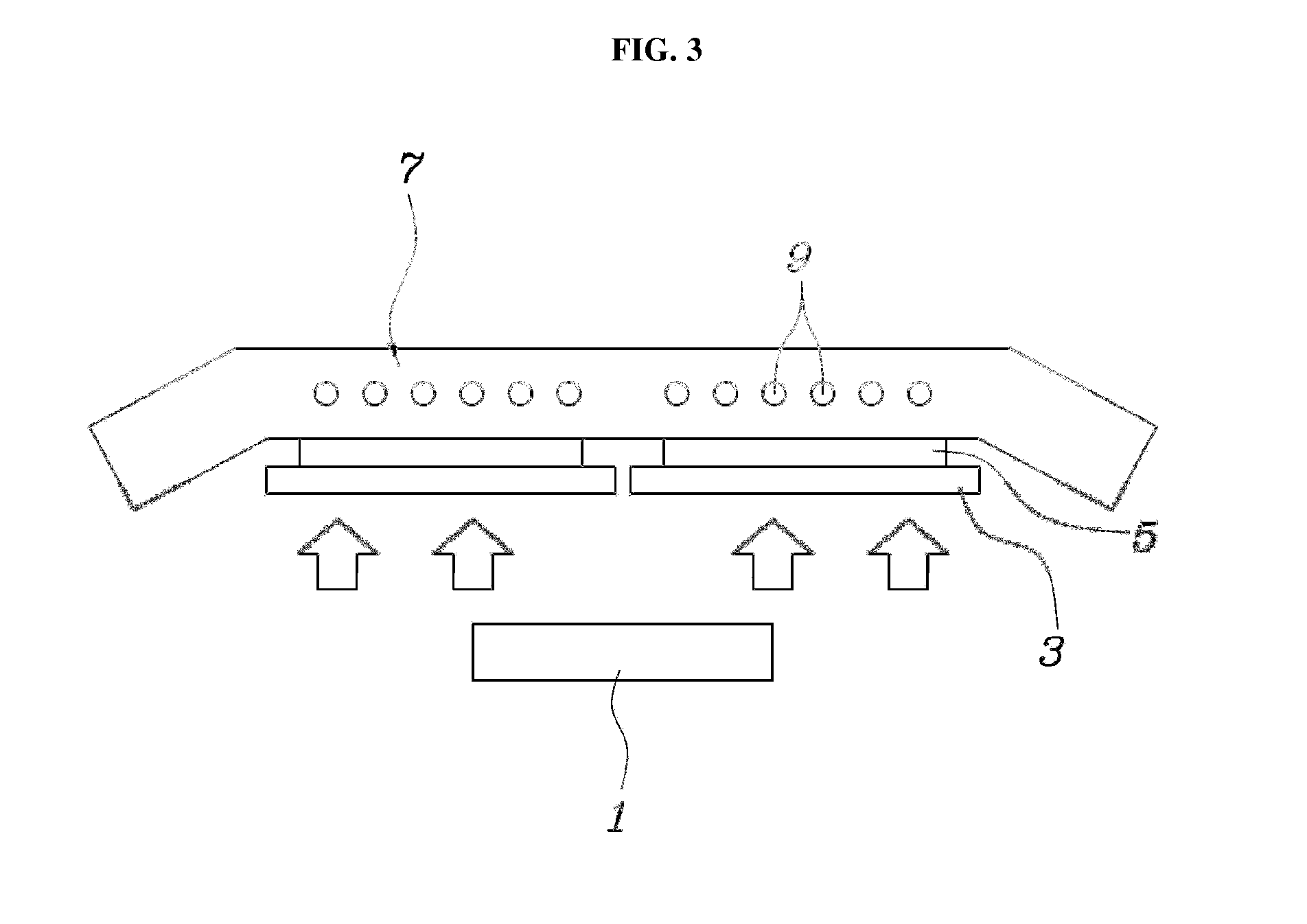
United States Patent
Application |
20160376971 |
Kind Code |
A1 |
Lee; Seung Woo ; et
al. |
December 29, 2016 |
THERMOELECTRIC ELEMENT OF VEHICLE EXHAUST SYSTEM
Abstract
A thermoelectric element of a vehicle exhaust system is
provided, which achieves maximum generation efficiency without
exceeding an endurance limit thereof. The thermoelectric element
includes a thermoelectric module and a heat dissipation plate.
Arrangement of the heat dissipation plate directly exposes one side
to the exhaust system and the opposite side contacts the
thermoelectric module. Furthermore, the thermoelectric element
includes a cooling unit having interior cooling channels and
disposed on the other side of the thermoelectric module.
Inventors: |
Lee; Seung Woo; (Seoul,
KR) ; Song; Kyong Hwa; (Seoul, KR) ; Baek;
Hong Kil; (Seoul, KR) ; Kwak; Jin Woo;
(Gyeongsan, KR) ; Noh; Su Jung; (Seoul, KR)
; Lee; Tae Won; (Incheon, KR) ; Lee; Han Saem;
(Seoul, KR) |
|
Applicant: |
Name |
City |
State |
Country |
Type |
Hyundai Motor Company |
Seoul |
|
KR |
|
|
Family ID: |
57537234 |
Appl. No.: |
14/930104 |
Filed: |
November 2, 2015 |
Current U.S.
Class: |
60/320 |
Current CPC
Class: |
Y02T 10/12 20130101;
F01N 5/025 20130101; Y02T 10/16 20130101; H01L 35/30 20130101 |
International
Class: |
F01N 5/02 20060101
F01N005/02 |
Foreign Application Data
Date |
Code |
Application Number |
Jun 26, 2015 |
KR |
10-2015-0091356 |
Claims
1. A thermoelectric element of a vehicle exhaust system comprising:
a thermoelectric module; a heat dissipation plate exposed to the
exhaust system at a first side thereof while contacting a first
side of the thermoelectric module at a second side; and a cooling
unit disposed on a second side of the thermoelectric module and
including a cooling channels within an interior.
2. The thermoelectric element according to claim 1, wherein the
cooling unit includes: a cooling plate having a first side disposed
at, on the second side of the thermoelectric module; and a cooling
system disposed on a second side of the cooling plate and having
the cooling channels disposed within the interior, to allow cooling
water to flow therethrough.
3. The thermoelectric element according to claim 2, wherein the
cooling plate and the cooling system are formed separately formed,
and are coupled to one another.
4. The thermoelectric element according to claim 1, wherein the
cooling unit has an integrated structure.
5. The thermoelectric element according to claim 1, wherein the
heat dissipation plate is spaced apart from an adjacent surface of
the exhaust system by a predetermined distance.
6. The thermoelectric element according to claim 1, wherein the
heat dissipation plate obstructs a high temperature from the
vehicle exhaust system from being directly applied to the
thermoelectric element.
7. A vehicle having the thermoelectric element of claim 1.
Description
CROSS-REFERENCE TO RELATED APPLICATION
[0001] This application claims the priority benefit of Korean
Patent Application No. 10-2015-0091356, filed on Jun. 26, 2015, in
the Korean Intellectual Property Office, the disclosure of which is
incorporated herein by reference.
BACKGROUND
[0002] 1. Field of the Invention
[0003] The present invention relates to a thermoelectric element
installed within a vehicle exhaust system, and more particularly to
a thermoelectric element capable of achieving maximum generation
efficiency without exceeding an endurance limit.
[0004] 2. Description of the Related Art
[0005] Generally, technology for mounting a thermoelectric element
on a surface of a heat protector or a muffler installed at the side
of an exhaust system within a vehicle converts exhaust heat into
electrical energy for driving of electric components disposed
within the vehicle. As shown in FIG. 1 a thermoelectric element is
installed proximate to an exhaust system. Referring to FIG. 1, a
heat shield plate 103 is installed separated from an exhaust system
101 to prevent engine parts from being damaged by exhaust heat. A
heat dissipation plate 105 is disposed at a surface (e.g.,
adjacent) of the heat shield plate 103. A thermoelectric module 107
is positioned between the heat dissipation plate 105 and a cooling
plate 109.
[0006] Typically, in such an arrangement of the thermoelectric
element, exhaust heat absorbed by the heat dissipation plate is
shielded by the heat shield plate and limits absorption of exhaust
heat. For example, it may be difficult to achieve maximum
generation efficiency since a heat dissipation temperature that
enables the thermoelectric element may be difficult to maintain.
Furthermore, a minimal temperature difference (e.g., .DELTA.T)
between the heat dissipation plate and the cooling plate may reduce
the generation amount.
[0007] For example, when .DELTA.T enabling the thermoelectric
element to achieve maximum generation efficiency is within a range
of about 180 to 230.degree. C., the temperature of heat dissipated
from the heat dissipation plate (e.g., hot-side temperature) is in
a range of about 150 to 200.degree. C. even though the temperature
of exhaust gas is approximately as high as 700.degree. C. or
greater. Accordingly, .DELTA.T is in a range of about 100 to
150.degree. C. and, as such, securing .DELTA.T capable of realizing
maximum generation efficiency is limited. Thus, degradation of
generation efficiency may occur.
[0008] Further, when the thermoelectric element is mounted directly
(e.g. coupled to) on a surface of the exhaust system in order to
remedy the above-mentioned problems, heat is directly applied to
the thermoelectric element. In particular, the thermoelectric
element may surpass a temperature exceeding a limit temperature,
above which the thermoelectric element is no longer durable (e.g.,
functional). In this case, durability (e.g., functionality) of the
thermoelectric element may be degraded.
[0009] The above matters disclosed in this section are merely for
enhancement of understanding of the general background of the
invention and should not be taken as an acknowledgement or any form
of suggestion that the matters form the related art already known
to a person skilled in the art.
SUMMARY
[0010] The present invention provides a thermoelectric element of a
vehicle exhaust system, for achieving maximum generation efficiency
without exceeding an endurance limit thereof. An exemplary
embodiment provides a thermoelectric element of a vehicle exhaust
system that may include a thermoelectric module, a heat dissipation
plate that may be arranged to be directly exposed to the exhaust
system at a first side (e.g., one) side and may contact (e.g.,
abut) a first side (e.g., one) side of the thermoelectric module at
the second side (e.g., other) side of the heat dissipation plate.
Further, a cooling unit may be disposed on the second (e.g., other)
side of the thermoelectric module and may include cooling channels
disposed on the interior thereof.
[0011] In some exemplary embodiments, the cooling unit may include
a cooling plate coupled, at a first side, opposite to (e.g., on the
other side of, opposing) the thermoelectric module, and a cooling
system coupled to a second side (e.g., opposite side other side) of
the cooling plate. The cooling channels may be disposed within the
interior of the cooling plate, to allow cooling water to flow
therethrough. In another exemplary embodiment, the cooling plate
and the cooling system may be formed separately, and may be coupled
to (e.g., interfaced with, assembled together) each other. The
cooling unit may have an integrated structure. The heat dissipation
plate may be separated (e.g., spaced apart) from a facing (e.g.,
opposing) surface of the exhaust system by a predetermined
distance.
[0012] The present exemplary embodiment provides the following
effects through the above-described configurations. For example, it
may be possible to increase the temperature of heat dissipated from
the heat dissipation plate to an allowable maximum temperature for
the thermoelectric element which may be used, in place of the
existing heat shield plate. The cooling unit may be spaced apart
from the exhaust system and the heat dissipation plate may be
disposed between the exhaust system and the cooling unit. Namely,
the radiant heat of the exhaust system, typically lost by the heat
shield plate in conventional systems may be reduced. Additionally,
the temperature difference between the heat dissipation plate and
the cooling plate may be increased and, the maximum generation
efficiency of the thermoelectric element may be achieved.
Furthermore, a reduction in manufacturing costs may be achieved by
omitting the heat shield plate from the exhaust system.
[0013] Moreover, in some exemplary embodiments an amount of exhaust
heat absorbed by the heat dissipation plate may be increased. For
example, the thermoelectric element may be prevented (e.g.,
obstructed) from directly contacting the surface of the exhaust
system. Accordingly, the thermoelectric element may be inhibited
(e.g., prevented) from exceeding a high-temperature endurance limit
and, the thermoelectric element may secure the desired
high-temperature endurance.
BRIEF DESCRIPTION OF THE DRAWINGS
[0014] The above and other objects, features and other advantages
of the present disclosure will be apparent from the following
detailed description taken in conjunction with the accompanying
drawings.
[0015] FIG. 1 is an exemplary view illustrating a thermoelectric
element installed at a vehicle exhaust system in accordance with
related art;
[0016] FIG. 2 is an exemplary view illustrating an arrangement of a
thermoelectric element at a vehicle exhaust system in accordance
with one exemplary embodiment of the present invention; and
[0017] FIG. 3 is an exemplary view illustrating an arrangement of a
thermoelectric element at a vehicle exhaust system in accordance
with another exemplary embodiment of the present invention.
DETAILED DESCRIPTION
[0018] Advantages and features of the invention and methods of
accomplishing the same may be understood more readily by reference
to the following detailed descriptions of exemplary embodiments and
the accompanying drawings. While the invention will be described in
conjunction with exemplary embodiments, it will be understood that
present description is not intended to limit the invention to those
exemplary embodiments. On the contrary, the invention is intended
to cover not only the exemplary embodiments, but also various
alternatives, modifications, equivalents and other embodiments,
which may be included within the spirit and scope of the invention
as defined by the appended claims.
[0019] It is understood that the term "vehicle" or "vehicular" or
other similar term as used herein is inclusive of motor vehicles in
general such as passenger automobiles including sports utility
vehicles (SUV), buses, trucks, various commercial vehicles,
watercraft including a variety of boats and ships, aircraft, and
the like, and includes hybrid vehicles, electric vehicles, plug-in
hybrid electric vehicles, hydrogen-powered vehicles and other
alternative fuel vehicles (e.g. fuels derived from resources other
than petroleum). As referred to herein, a hybrid vehicle is a
vehicle that has two or more sources of power, for example both
gasoline-powered and electric-powered vehicles.
[0020] The terminology used herein is for the purpose of describing
particular embodiments only and is not intended to be limiting of
the invention. As used herein, the singular forms "a", "an" and
"the" are intended to include the plural forms as well, unless the
context clearly indicates otherwise. It will be further understood
that the terms "comprises" and/or "comprising," when used in this
specification, specify the presence of stated features, integers,
steps, operations, elements, and/or components, but do not preclude
the presence or addition of one or more other features, integers,
steps, operations, elements, components, and/or groups thereof. As
used herein, the term "and/or" includes any and all combinations of
one or more of the associated listed items. For example, in order
to make the description of the present invention clear, unrelated
parts are not shown and, the thicknesses of layers and regions are
exaggerated for clarity. Further, when it is stated that a layer is
"on" another layer or substrate, the layer may be directly on
another layer or substrate or a third layer may be disposed
therebetween.
[0021] Unless specifically stated or obvious from context, as used
herein, the term "about" is understood as within a range of normal
tolerance in the art, for example within 2 standard deviations of
the mean. "About" can be understood as within 10%, 9%, 8%, 7%, 6%,
5%, 4%, 3%, 2%, 1%, 0.5%, 0.1%, 0.05%, or 0.01% of the stated
value. Unless otherwise clear from the context, all numerical
values provided herein are modified by the term "about."
[0022] Reference will now be made in detail to the exemplary
embodiments of the present invention, examples of which are
illustrated in the accompanying drawings. Wherever possible, the
same reference numbers will be used throughout the drawings to
refer to the same or like parts.
[0023] Referring to FIGS. 2 and 3, a thermoelectric element of a
vehicle exhaust system according to an exemplary embodiment is
illustrated. The thermoelectric element may include a heat
dissipation plate 3 and a cooling unit 7. Hereinafter, the
thermoelectric element of the exemplary embodiment will be
described in detail with reference to FIGS. 2 and 3. The heat
dissipation plate 3 may be arranged to directly face (e.g.,
positioned opposite to) an exhaust system 1 at a first side (e.g.,
one side) thereof. A thermoelectric module 5 may be disposed, at a
second side (e.g., one side) of the exhaust system, on the second
side (e.g., opposite side) of the heat dissipation plate 3. In
particular, the exhaust system 1 may be a part (e.g., a portion) of
the vehicle exhaust system that may emit high exhaust heat, for
example, an exhaust manifold a muffler or the like.
[0024] For example, the thermoelectric module 5 may be disposed, at
the other side (e.g., an opposite side) of the exhaust system, on
the other side of the heat dissipation plate 3 and the surfaces may
contact (e.g., interface with one another). The exhaust heat may be
absorbed by the heat dissipation plate 3 and may be transferred
(e.g., transmitted) to the thermoelectric module 5. In particular,
the heat dissipation plate 3 may be separated (e.g., spaced apart)
from an opposing surface (e.g., a facing surface) of the exhaust
system 1 by a predetermined distance. For example, it may be
possible to prevent (e.g., obstruct) high temperature from the
exhaust system 1 from being directly applied to the thermoelectric
element. Accordingly, the thermoelectric element may be prevented
from exceeding a high-temperature endurance limit. Further, the
cooling unit 7 may be disposed on the opposite side (e.g., other
side) of the thermoelectric module 5. Cooling channels 9 may be
disposed within the interior of the thermoelectric module 5. The
cooling unit 7 may include a cooling plate 7a and a cooling system
7b.
[0025] Referring to FIG. 2, the cooling plate 7a may be disposed,
at a first side (e.g., one side) thereof, on the opposite side
(e.g., other side) of the thermoelectric module 5 in a surface
contact manner. The cooling system 7b may be disposed on the
opposite side (e.g., other side) of the cooling plate 7a and the
surfaces may contact (e.g., interface with one another, coupled to
one another) one another. A plurality of cooling channels 9 may be
installed within the interior of the cooling system 7b, to
facilitate cooling water to flow through the cooling system 7b.
Additionally, the cooling system 7b may have a block shape or the
like. In other words, the cooling plate 7a and cooling system 7b
may be formed separately formed and, as such, may be assembled to
allow the surfaces to contact (e.g., interface, coupled to) one
another.
[0026] In particular, the cooling system 7b may be formed to have a
greater size than the size of the heat dissipation plate 3 and
thermoelectric module 5. For example, the cooling system 7b may
include lateral and longitudinal dimensions that may cover one
surface of the exhaust system 1 that faces the cooling system 7b
and, may function as the heat shield plate. Additionally, it may be
possible to avoid damage to components proximate to the exhaust
system 1 caused by exhaust heat, through the cooling system 7b.
[0027] Alternatively, the cooling unit 7 of the exemplary
embodiments may include an integrated structure disposed on the
opposite (e.g., other) side of the thermoelectric module 5.
Referring to FIG. 3, the cooling unit 7 may have a structure in
which the cooling plate 7a and cooling system 7b may be integrated.
For example, the integrated structure may perform both the function
of the cooling plate 7a and the function of the cooling system 7b.
In other words, a plurality of cooling channels 9, through which
cooling water flows, may be installed within the interior of the
cooling unit 7. In particular, the cooling unit 7 may have a
greater size than those of the heat dissipation plate 3 and
thermoelectric module 5. For example, the cooling unit 7 may
include lateral and longitudinal dimensions that may cover one
surface of the exhaust system 1 adjacent to (e.g., facing) the
cooling unit 7 and, may function as the heat shield plate.
Additionally, it may be possible to prevent damage to components
proximate to the exhaust system 1 caused by exhaust heat, via the
cooling unit 7.
[0028] In some exemplary embodiments, the temperature of heat
dissipated from the heat dissipation plate 3 may be increased to an
allowable maximum temperature for the thermoelectric element. For
example, in place of the existing heat shield plate, the cooling
unit 7 may be separated from (e.g., spaced apart) from the exhaust
system 1 when the heat dissipation plate 3 is disposed between the
exhaust system 1 and the cooling unit 7. Accordingly, the radiant
heat of the exhaust system 1, typically lost by the heat shield
plate in conventional cases may be reduced. Additionally, the
temperature difference between the heat dissipation plate 3 and the
cooling plate 7a may be increased and the maximum generation
efficiency of the thermoelectric element may be achieved.
Accordingly, a reduction in manufacturing costs may be achieved by
removing the heat shield plate from the exhaust system 1.
[0029] Furthermore, an amount of exhaust heat absorbed by the heat
dissipation plate 3 may be increased when the thermoelectric
element may be prevented from directly contacting the surface of
the exhaust system 1. Accordingly, the thermoelectric element may
be prevented from exceeding a high-temperature endurance limit
thereof and, as such, the thermoelectric element may achieve the
desired high-temperature endurance.
[0030] While this invention has been described in connection with
what is presently considered to be exemplary embodiments on the
contrary, it is intended to cover various modifications and
equivalent arrangements without departing from the scope and spirit
of the invention as disclosed in the accompanying claims. In
addition, it is to be considered that all of these modifications
and alterations fall within the scope of the present invention
* * * * *