U.S. patent application number 14/745042 was filed with the patent office on 2015-12-31 for biofilm treatment of composite materials containing mycelium.
The applicant listed for this patent is Matthew James Lucht, Damen Donald Schaak. Invention is credited to Matthew James Lucht, Damen Donald Schaak.
Application Number | 20150376565 14/745042 |
Document ID | / |
Family ID | 54929854 |
Filed Date | 2015-12-31 |
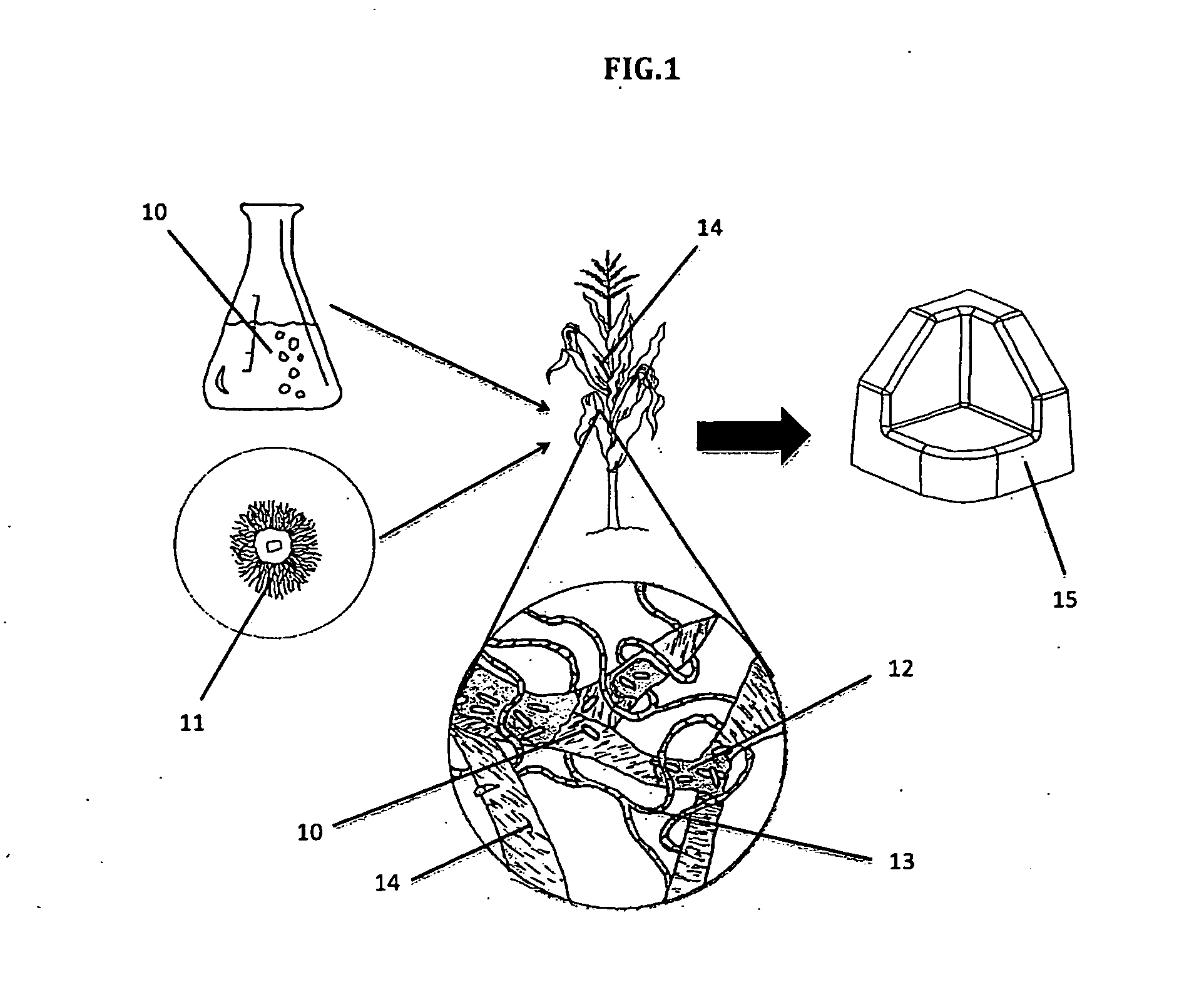


United States Patent
Application |
20150376565 |
Kind Code |
A1 |
Schaak; Damen Donald ; et
al. |
December 31, 2015 |
Biofilm Treatment of Composite Materials Containing Mycelium
Abstract
The process provides a biofilm including and not limited to
cellulose produced by bacteria that can be used as a bio-resin and
as a surface application for myceliated and non-myceliated
biomaterials. In one embodiment, the process comprises the steps of
obtaining an agricultural substrate; and cohabitating a selected
bacteria with a selected fungus in the agricultural substrate for a
period of time to allow the bacteria to grow alongside the fungus
and to excrete a biofilm from the bacteria into the substrate to
provide bio-resin like strengthening compounds to the agricultural
substrate.
Inventors: |
Schaak; Damen Donald; (Troy,
NY) ; Lucht; Matthew James; (Troy, NY) |
|
Applicant: |
Name |
City |
State |
Country |
Type |
Schaak; Damen Donald
Lucht; Matthew James |
Troy
Troy |
NY
NY |
US
US |
|
|
Family ID: |
54929854 |
Appl. No.: |
14/745042 |
Filed: |
June 19, 2015 |
Related U.S. Patent Documents
|
|
|
|
|
|
Application
Number |
Filing Date |
Patent Number |
|
|
62017315 |
Jun 26, 2014 |
|
|
|
Current U.S.
Class: |
435/252.4 |
Current CPC
Class: |
C12N 1/20 20130101; C12N
1/14 20130101 |
International
Class: |
C12N 1/20 20060101
C12N001/20; C12N 1/14 20060101 C12N001/14 |
Claims
1. A process comprising the steps of obtaining an agricultural
substrate; and cohabitating a selected bacteria with a selected
fungus in said agricultural substrate for a period of time to allow
said bacteria to grow alongside said fungus and to excrete a
biofilm from said bacteria into said substrate to provide bio-resin
like strengthening compounds to said agricultural substrate.
2. A process as set forth in claim 1 wherein said bacteria is a
Bacillus subtilis species.
3. A process as set forth in claim 2 wherein said fungus is
Ganoderma.
4. A process as set forth in claim 1 wherein said agricultural
substrate is in the form of discrete particles and said fungus
grows a network of interconnected mycelia cells extending through
and around discrete particles of the substrate to bond said
discrete particles together into a self-supporting composite
material.
5. A process of growing a biofilm producing bacteria into a
myceliated substrate comprising the steps of inoculating a Lysogeny
Broth (LB) with one colony of Bacillus subtilis sp. for a period of
time to grow the Bacillus subtilis sp into a culture; passaging the
culture into a LB media and continuing incubation until the culture
reaches mid log phase; co-inoculating an agricultural substrate
with a fungal species and said mid log phase culture using less
than 20% fungal v/v inoculum, and 1 ml of mid log phase bacteria
culture per 6 grams of dry agricultural substrate; and thereafter
incubating the co-inoculated agricultural substrate for a period of
from 2 to 10 days to obtain a self-supporting composite
material.
6. A process as set forth in claim 5 further comprising the steps
of hot pressing the material to bond all components therein.
7. A process as set forth in claim 6 wherein said steps of hot
pressing takes place for a period of 10 minutes at 400.degree. F.
under 350 psi of platen pressure.
8. A process for growing microbial cellulose in vitro for
application to biomaterial surfaces comprising the steps of
inoculating 200 ml of buffered S&H medium with one colony of
microbial cellulose producing bacteria Acetobacter xylinus to form
a culture; incubating said culture at 30.degree. C. for a time
period of from 24 to 96 hours to form a cellulose biofilm thereon;
thereafter harvesting the cellulose biofilm; and applying the
cellulose biofilm to the surface of a biomaterial surface on an
agricultural substrate to form a bio-film like skin thereon.
9. A process as set forth in claim 8 wherein said agricultural
substrate is myceliated with a network of interconnected mycelia
cells extending through and around discrete particles of the
substrate to bond said discrete particles together into a
self-supporting composite material.
10. A process of growing a biofilm in vitro for application within
a biomaterial inoculating 200 ml of LB media with a colony of
biofilm producing bacteria Bacillus subtilis sp. bacteria to form a
culture; incubating said culture at 37.degree. C. until a biofilm
is formed; harvesting the biofilm by one of direct biofilm
extraction and harvesting of the entirety of the culture; mixing
the harvested biofilm into one of a myceliated agricultural
substrate and a non-myceliated agricultural substrate to form a
biomaterial; and hot pressing the biomaterial to fully bond all
components therein.
11. A process of producing a bacterial antimicrobial in situ
comprising the steps of inoculating 100 ml LB media with one colony
of Streptomycin natalensis to form a culture; growing the culture
at 37.degree. C. to mid log phase; co-inoculating 600 g
agricultural substrate with both bacteria and fungi species using
100 ml mid log bacteria culture and <20% fungal inoculum;
incubating the co-inoculated material at room temperature for 6
days; and heating the incubated co-inoculated material to inactive
microbial growth by desiccation.
12. A process as set forth in claim 11 wherein said bacteria is
S.natalensis and said fungi is Ganoderma.
13. A process of producing a bacterial antimicrobial in vitro
comprising the steps of inoculating 100 ml LB media with one colony
of Streptomycin alboniger to form a culture; growing the culture at
37.degree. C. to mid log phase; filtering the Streptomycin
alboniger out of the culture to reduce the culture to spent media
spiked with antimicrobial compounds; adding 100 ml of the
antimicrobial supernatant to 600 g agricultural substrate and
incubating the substrate for 3 hours at room temperature;
inoculating the substrate with <20% fungi (Ganoderma) and
incubate for 6 days at room temperature; and terminating microbial
growth in the incubated substrate by desiccation.
14. A process comprising the steps of obtaining an agricultural
substrate; and inoculating said agricultural substrate with a
selected bacteria grown to mid log phase and incubating the
inoculated agricultural substrate for a period of time to allow
said bacteria to excrete a biofilm from said bacteria into said
substrate to provide bio-resin like strengthening compounds to said
agricultural substrate.
15. A process as set forth in claim 14 wherein said bacteria is
Bacillus subtilis and is inoculated into said agricultural
substrate at a rate of 1 milliliter of bacterial culture to 6 grams
dry of agricultural substrate.
Description
[0001] This invention claims priority of Provisional Patent
Application 62/017,315 filed Jun. 26, 2014.
[0002] This invention relates to a process that provides a biofilm
including and not limited to cellulose produced by bacteria that
can be used as a bio-resin and as a surface application for
myceliated and non-myceliated biomaterials. More particularly, this
invention relates to a biofilm treatment of myceliated
biomaterials.
BACKGROUND OF THE INVENTION
[0003] Biofilms are comprised of excreted protein, DNA, and
polysaccharides that tend to form a complex matrix consisting of
organic and nonorganic materials. These biofilms contain the cells
that produced them providing the cells with a film or slim to live
on. [Karatan, E., Watnick, P. (June 2009). "Signals, Regulatory
Networks, and Materials That Build and Break Bacterial
Biofilms"].
[0004] The production of biofilms can provide bacterium an anchor
or platform to grow from and serve as a protective barrier from the
environment. Polysaccharides typically encapsulate the biofilms
providing a bound matrix of living and nonliving organic matter.
[Hall-Stoodley L, Costerton J W, Stoodley P (February 2004).
"Bacterial biofilms: from the natural environment to infectious
diseases"]
[0005] Biofilms can provide the bacteria a sanctuary from
antibiotics, desiccation, and nutritional stress. Some biofilms
produced from bacteria are composed of single polysaccharides like
microbial cellulose.
[0006] As is known, U.S. patent application Ser. No. 12/001,556,
filed Dec. 12, 2007, describes various techniques for making a
biomaterial composed of a substrate of discrete particles and a
network of interconnected mycelia cells extending through and
around the discrete particles and bonding discrete particles
together.
[0007] It is an object of the invention to provide improvements to
the methods of making biomaterials.
[0008] It is another object of the invention to provide
improvements to the methods of making myceliated biomaterials and
non-myceliated biomaterials.
[0009] It is another object of the invention to utilize bacterial
biofilms to provide biomaterial materials such as described in U.S.
patent application Ser. No. 12/001,556 with an added resin matrix
and surface layer.
[0010] Briefly, the invention provides a process by which biofilms
including and not limited to cellulose produced by bacteria can be
used as a bio-resin and as a surface application for myceliated and
non-myceliated biomaterials.
[0011] In particular, the process comprises the steps of obtaining
an agricultural substrate; and cohabitating a selected bacteria
with a selected fungus in the agricultural substrate for a period
of time to allow the bacteria to grow alongside the fungus and to
excrete a biofilm from the bacteria into the substrate to provide
bio-resin like strengthening compounds to the agricultural
substrate.
[0012] In accordance with the techniques described in U.S. patent
application Ser. No. 12/001,556, the fungus grows a network of
interconnected mycelia cells extending through and around discrete
particles of the substrate to bond the discrete particles together
into a self-supporting composite material.
[0013] In one embodiment, the bacteria will be cohabitated with a
selected fungus in agricultural substrates (AS), e.g. corn stalks.
During this cohabitation period, the bacteria will grow alongside
the fungal strains and excrete biofilms into the substrate
providing bio-resin like strengthening compounds to the
self-supporting composite material.
[0014] In another embodiment, the bacteria may be grown in vitro,
thus producing a biofilm, which would then be harvested and applied
to the AS at various stages of the growth process and in some
instances encapsulating the material in a biofilm like skin. These
in vitro applications would be applied to both the internal and
external surfaces of the biomaterials. Some bacterial strains will
be genetically engineered to optimize biofilm quality, excretion
levels, and induction. In this embodiment, the biofilm may be
applied to myceliated substrates, i.e. a substrate wherein the
fungus grows a network of interconnected mycelia cells extending
through and around discrete particles of the substrate, or the
biofilm may be applied to non-myceliated substrates.
[0015] Utilizing genetic engineering techniques, inducible
controlling sequences may be inserted into the bacterial genome to
regulate biofilm production and various other biofilm components.
Inducible gene expression will be regulated by photoreceptors,
temperature signaling, small molecules, constitutively expressed
promoters, or through knocking out genes.
[0016] Agricultural substrates are vulnerable to unwanted microbial
bio burden that can cause the growing material to become
contaminated. These contaminated materials fail to grow properly
thus reducing product yields and performance. Here, the
antimicrobial properties of some bacteria species are to be
harnessed. Both bacteria and fungi species will be cohabitated
together in the selected agricultural substrates (e.g. corn
stalks). In this particular application, the bacteria will excrete
antimicrobial compounds that reduce the competition between
unwanted microbes and the selected fungal species. This strategy
will enhance the ability of the fungus to resist external bio
burden commonly growing throughout the selected agricultural
substrates. Molecular genetic techniques are also utilized to
reprogram the bacteria strains to overexpress antimicrobials both
in vitro, and in situ.
[0017] These and other objects of the invention will become more
apparent from the following detailed description taken in
conjunction with the accompanying drawings wherein:
[0018] FIG. 1 illustrates a schematic of the steps of a process in
accordance with the invention;
[0019] FIG. 2 illustrates photoimages of a flask containing a
biofilm produced in vitro in accordance with the invention; and
[0020] FIG. 3 illustrates a view of a microbial cellulose film
being harvested from a dish in accordance with the invention.
[0021] Referring to FIG. 1, in accordance with one embodiment of
the process of the invention, a liquid medium of a bacteria culture
(a Bacillus subtilis species) is first prepared, for example, in a
flask 10, along with the preparation of fungal mycelium, for
example, on an agar plate 11.
[0022] Thereafter the bacteria culture and fungal mycelium are
applied to an agricultural substrate, for example, corn stalks.
[0023] As illustrated, during incubation of the agricultural
substrate, the bacteria produces a biofilm (bioresin) 12 while the
fungal mycelium grows hyphae 13 that grow to form a network of
interconnected mycelia cells extending through and around discrete
particles 14 of the agricultural substrate to bond the discrete
particles together into a self-supporting composite material, i.e.
the finished product 15.
[0024] As indicted, the finished product 15 is a biomaterial, i.e.
a molded block, that can be used for protective packaging.
[0025] FIG. 1 represents the ability of a fungus and bacteria
strains to cohabitate.
Process Steps for Growing Biofilms Grown In Situ:
[0026] a. Inoculate the media that has specificity to the bacteria
being cultured with one colony of bacteria. Grow the bacterial
culture until the culture reaches mid log phase. [0027] In this
step, the bacteria strain was inoculated into lysogeny broth (LB)
and grown to optimal cell density. The quantities of the LB medium
are dependent on the bacterial strain used and the quantity of
agricultural substrate the LB is inoculated into. For Bacillus
subtilis (bacteria strain), the agricultural substrate was
inoculated at 1:6 (1 milliliter of bacterial culture: 6 grams dry
agricultural substrate). [0028] b. Add bacterial culture grown to
mid log phase to either myceliated or non-myceliated agricultural
substrate (AS). If preparing "myceliated AS", co-inoculate the AS
with the bacteria culture and one of the selected fungal species.
If "non-myceliated AS" is prepared, the AS will only be inoculated
with the bacterial culture. The biofilm produced by the bacteria
will be the sole microbial bioresin in the substrate. [0029] In
this step, the agricultural substrate was simultaneously inoculated
with both Ganoderma (fungus) and a Bacillus subtilis species
(bacteria) [0030] c. Incubate the biomaterial until the AS is fully
colonized with the added bacteria and/or fungal mycelium. [0031] In
this step, the biomaterial was incubated for 6 days [0032] d.
Terminate growth of materials by method of desiccation. [0033] In
this step, the biomaterial was dried to terminate microbial growth.
[0034] Referring to FIG. 2, wherein like reference characters
indicate like parts as above, a process for producing a bacterial
biofilm in vitro employs a flask 15, into which a biofilm excreting
bacteria 16 is placed.
Process Steps for Growing Biofilms Grown In Vitro:
[0034] [0035] a. Inoculate medium with bacteria (as above) [0036]
b. Incubate culture at optimal conditions for the desired time
[0037] c. Harvest the biofilm (17) [0038] d. Apply the biofilm to
the myceliated or non-myceliated substrate [0039] e. Either
continue to grow out materials or terminate growth.
Applications
I. Bacterial Biofilms Produced In Situ.
[0039] [0040] a. As a means of binding together discrete
lignocellulose particles (both as a sole microbial component and in
combination with other bacteria and fungi). Growing the
biofilm-producing bacteria directly into the myceliated and
non-myceliated biomaterial (in situ) to provide the cohabitated
substrate with the addition of a biofilm that will act as both a
resin for strength and particle bonding. [0041] b. As a surface
application for altering physical properties and aesthetics. Once
the material has finished growing, the biofilm will have been
excreted throughout the material (internal and external surfaces).
The extent to which the biofilm coats the external surfaces of the
finished material is dependent on the bacteria species used during
cohabitation and the resultant biofilm produced. [0042] c. As a
nutrition source for cohabitating fungi. The organic material
accumulated throughout the production of the biofilm may also
become a source of nutrition for other bacteria and fungal species
growing in the substrate.
II. Bacterial Biofilms Produced In Vitro.
[0042] [0043] a. As a means of binding together discrete
lignocellulose particles (both as a sole microbial component, and
in combination with other bacteria and fungi). [0044] b. As a
surface application for altering physical properties and
aesthetics. [0045] c. As a nutrition source for cohabitating fungi.
The organic material accumulated throughout the production of the
biofilm may also become a source of nutrition for other bacteria
and fungal species growing in the substrate.
III. Genetically Engineered Biofilm Producing Bacteria Strains
[0045] [0046] a. Genetically modified biofilm dependent genes will
allow for optimal levels of biofilm production. This will be done
through bacterial controlling sequences specifically engineered for
our species of bacteria and their associated biofilms. [0047] b.
Provide the capability to induce biofilm production at selected
time points during material growth. This will be done through
bacterial controlling sequences, which will be regulated through
photoreceptors, temperature signaling, small molecules or
constitutive promoters.
IV. Bacterial Antimicrobials Produced In Situ
[0047] [0048] a. As a means to cohabitate both fungi and bacteria
species together with the purpose of reducing the background bio
burden residing in our agricultural substrates throughout the
materials growth process.
V. Bacterial Antimicrobials Produced In Vitro
[0048] [0049] a. Culture antimicrobial producing bacteria in vitro
(liquid media). Use the antimicrobial spiked culture as a bio
burden treatment to agricultural substrates.
VI. Genetically Engineered Antimicrobial Producing Bacteria
[0049] [0050] a. Through genetic modifications, reprogram the
cohabitating bacteria to express or overexpress antimicrobials in
both in vitro and in situ paradigms.
[0051] The following are specific examples of the process for
making a biofilm.
Example 1
Grow Biofilm-Producing Bacteria into Myceliated Substrate
[0052] a. Inoculate 25 ml Lysogeny Broth (LB) with one colony of
Bacillus subtilis sp. (bacteria), grow overnight at 37.degree. C.
[0053] a. Passage the culture (1:10) into 250 ml LB media, and
continue incubation until the culture reaches mid log phase. [0054]
b. Co-inoculate the AS with both fungal and bacterial species using
<20% fungal v/v inoculum, and 1 ml of log phase bacteria culture
per 6 grams of dry AS. [0055] c. Incubate the co-inoculated AS for
2-10 days. [0056] d. Hot press the material (10 minutes at
400.degree. F., held under 350 psi of platen pressure.) to bond all
components if applicable to material performance. [0057] e.
Terminate growth of material
Example 2
Grow Microbial Cellulose in Vitro and Apply to Biomaterial
Surfaces
[0057] [0058] a. Inoculate 200 ml of a common liquid medium used to
culture bacteria, such as a buffered S&H medium, with one
colony of microbial cellulose producing bacteria Acetobacter
xylinus. [0059] b. Incubate culture at 30.degree. C. for 24-96
hours to form a biofilm thereon. [0060] c. Harvest the cellulose
biofilm 17 (FIG. 3) [0061] d. Apply the cellulose to the surface of
partially or fully myceliated AS thereby forming a bio-film like
skin. [0062] e. Allow the biomaterial to grow into the cellulose if
further biofilm integration is required for material performance.
[0063] f. Terminate growth of material
Example 3
Grow Microbial Biofilm In Vitro and Apply within Biomaterials
[0063] [0064] a. Inoculate 200 ml of LB media with colony of
biofilm producing bacteria Bacillus subtilis sp. bacteria [0065] b.
Incubate culture at 37.degree. C. until the biofilm has reached
optimal qualities and quantities (24-96 hours) [0066] c. Harvest
the biofilm by either direct biofilm extraction (FIG. 3), or for
other biofilms that remain homogenous in the media, the entirety of
the culture will be harvested. [0067] d. Mix the harvested biofilm
into myceliated or non-myceliated AS. [0068] e. Hot press the
material to fully bond all components. [0069] f. Terminate the
growth of material.
Example 4
Bacterial Antimicrobials Produced In Situ
[0069] [0070] a. Inoculate 100 ml LB media with one colony of
Streptomycin natalensis. Grow culture at 37.degree. C. to mid log
phase. [0071] b. Co-inoculate 600 g AS with both bacteria
(S.natalensis) and fungi (Ganoderma) species using 100 ml mid log
bacteria culture, and <20% fungal inoculum. [0072] c. Incubate
co-inoculated material at room temperature for 6 days. [0073] d.
Heat inactive microbial growth by desiccation. [0074] e. Material
will have enhanced resistance to bio burden throughout the
incubation process resulting in limited loss of product due to
contaminated material.
Example 5
Bacterial Antimicrobials Produced In Vitro
[0074] [0075] a. Inoculate 100 ml LB media with one colony of
Streptomycin alboniger. Grow culture at 37.degree. C. to mid log
phase. [0076] b. Filter the bacteria out of the culture using 0.2
um filters thus reducing the culture to spent media spiked with
antimicrobial compounds (may also retain the bacteria if
co-habitation of the antimicrobial producing bacteria and fungus is
needed in next steps). [0077] c. Add 100 ml of the antimicrobial
supernatant to 600 g AS, and incubate the treated AS for 3 hours at
room temperature. [0078] d. Inoculate the treated AS with <20%
Fungi (Ganoderma), and incubate for 6 days at room temperature.
[0079] e. Terminate all microbial growth by desiccation.
[0080] In all of the processes described above, the inoculated
agricultural substrates may be placed in molds of predetermined
shape in order to produce products having a shape corresponding to
the shape of the interior of the mold.
[0081] The invention thus provides a process of making a bacterial
biofilm that can be used as a bio-resin and as a surface
application for myceliated and non-myceliated biomaterials.
* * * * *