U.S. patent application number 13/576694 was filed with the patent office on 2012-12-27 for valve drive system of internal combustion engine.
Invention is credited to Naoto Hisaminato, Eiichi Kamiyama, Manabu Tateno.
Application Number | 20120325167 13/576694 |
Document ID | / |
Family ID | 44563078 |
Filed Date | 2012-12-27 |
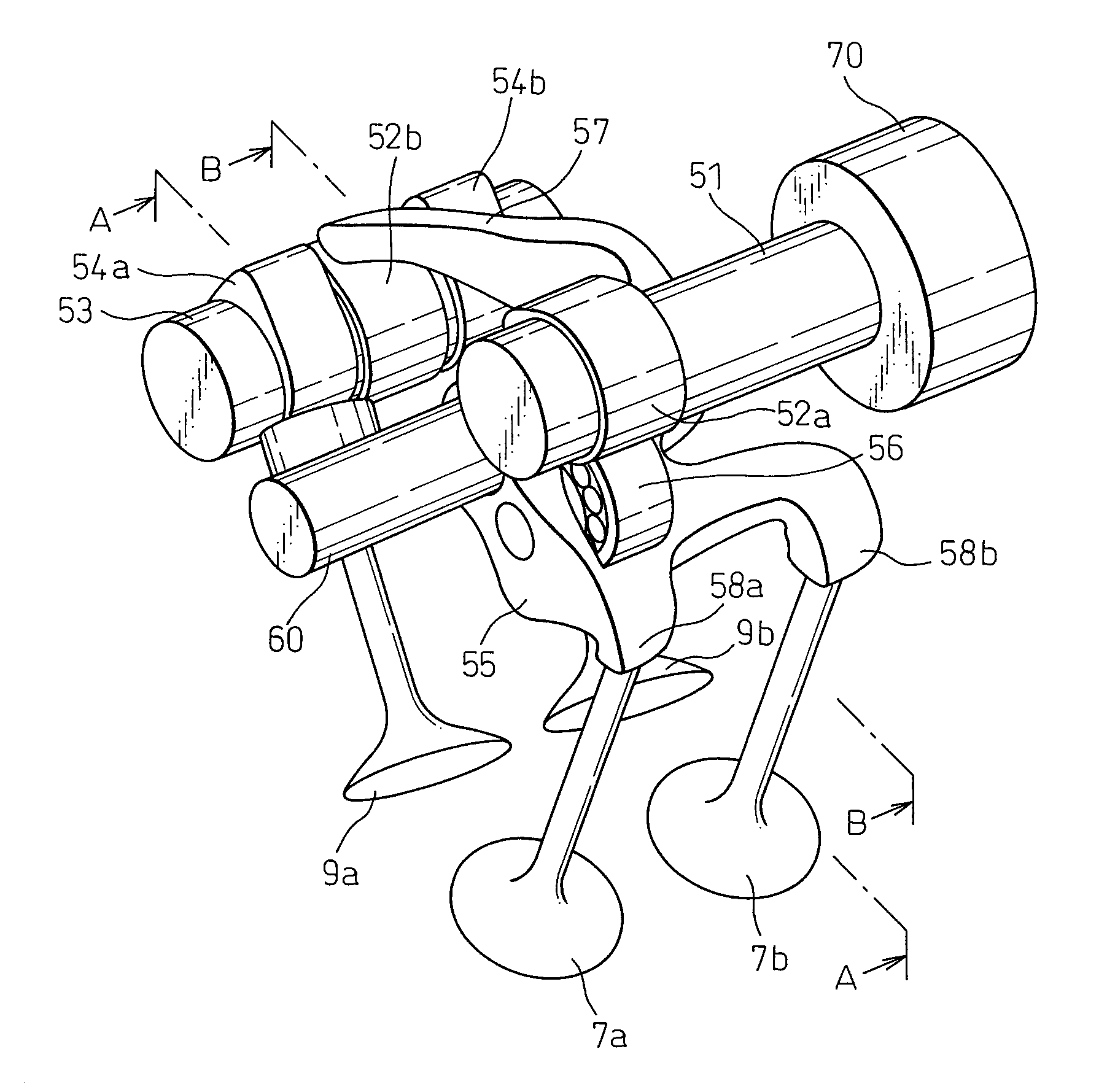

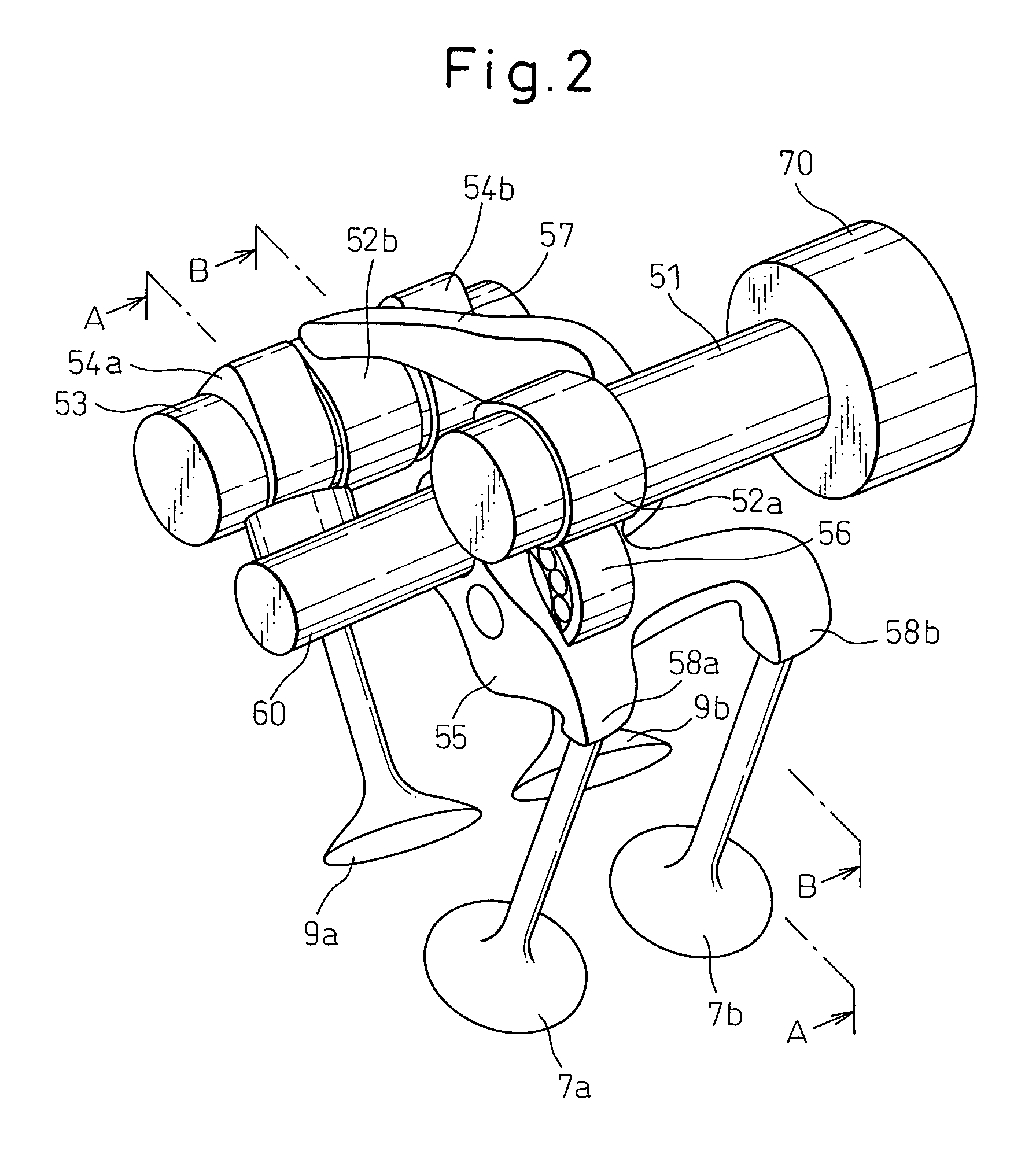








View All Diagrams
United States Patent
Application |
20120325167 |
Kind Code |
A1 |
Kamiyama; Eiichi ; et
al. |
December 27, 2012 |
VALVE DRIVE SYSTEM OF INTERNAL COMBUSTION ENGINE
Abstract
A valve drive system of internal combustion engine which
operates at a high compression ratio cycle, which is provided with
an intake cam 52a and intake cam 52b for operating intake valves
7a, 7b and a variable valve timing device 70 which can offset the
operating timings of the intake valves 7a, 7b by the intake cam 52a
and the operating timings of the intake valves 7a, 7b by the intake
cam 52b from each other. The intake cam 52a and intake cam 52b
include circular parts and cam noses. At least one of the cam nose
of the intake cam 52a and cam nose of the intake cam 52b has a
concentric circular part which is formed in a circular shape
concentric with the circular part.
Inventors: |
Kamiyama; Eiichi;
(Mishima-shi, JP) ; Tateno; Manabu; (Sunto-gun,
JP) ; Hisaminato; Naoto; (Susono-shi, JP) |
Family ID: |
44563078 |
Appl. No.: |
13/576694 |
Filed: |
March 11, 2010 |
PCT Filed: |
March 11, 2010 |
PCT NO: |
PCT/JP2010/054620 |
371 Date: |
August 2, 2012 |
Current U.S.
Class: |
123/90.16 ;
123/90.15 |
Current CPC
Class: |
F01L 13/0005 20130101;
F01L 2305/00 20200501; F01L 1/143 20130101; F01L 1/267 20130101;
Y02T 10/12 20130101; F02D 13/0238 20130101; F01L 1/181 20130101;
F01L 1/08 20130101; F01L 1/3442 20130101; F02D 13/0269 20130101;
F01L 2013/0089 20130101; F01L 1/26 20130101; Y02T 10/142 20130101;
F01L 2001/0537 20130101 |
Class at
Publication: |
123/90.16 ;
123/90.15 |
International
Class: |
F01L 1/34 20060101
F01L001/34 |
Claims
1.-4. (canceled)
5. A valve drive system of an internal combustion engine which can
increase an expansion ratio when fuel burns and a piston is pushed
compared with an actual compression ratio when an air-fuel mixture
which contains fuel is compressed by a piston, the valve drive
system of the internal combustion engine provided with a first
intake cam and a second intake cam which operate intake valves and
a variable valve timing device which changes at least one operating
timing of an operating timing of intake valves by the first intake
cam and an operating timing of intake valves by the second intake
cam, wherein the intake valve is formed to be operated by being
driven by the first intake cam and the second intake cam, the
variable valve timing device is formed so as to be able to offset
the operating timing of the intake valves by the first intake cam
and the operating timing of the intake valves by the second intake
cam, the first intake cam and the second intake cam include
circular parts of substantially circular cross-sectional shapes and
bulging parts which project from the circular parts and which drive
the intake valves, at least one of the bulging part of the first
intake cam and the bulging part of the second intake cam has a
concentric circular part which is formed in a concentric circular
shape with the circular part, and the concentric circular part
holds an amount of movement of the intake valve substantially
constant in a period during which the intake valve is open.
6. A valve drive system of internal combustion engine as set forth
in claim 5, wherein the bulging part of the first intake cam and
the bulging part of the second intake cam have concentric circular
parts, the first intake cam and the second intake cam are formed so
that the amount of movement of the intake valve which is driven by
the concentric circular part of the first intake cam and the amount
of movement of the intake valve which is driven by the concentric
circular part of the second intake cam become substantially the
same, when the operating timing of the intake valves by the first
intake cam and the operating timing of the intake valves by the
second intake cam are different from each other, a time period
where the concentric circular part of the first intake cam opens
the intake valve and a time period where the concentric circular
part of the second intake cam opens the intake valve overlap each
other.
7. A valve drive system of internal combustion engine as set forth
in claim 5, further provided with an operating state detection
device which detects an operating state of the internal combustion
engine, wherein the system detects the operating state of the
internal combustion engine and determines an amount of offset
between the operating timing of the intake valves by the first
intake cam and the operating timing of the intake valves by the
second intake cam in accordance with the operating state of the
internal combustion engine.
8. A valve drive system of internal combustion engine as set forth
in claim 7 in which a first intake valve and second intake valve
are arranged for each cylinder, the valve drive system of internal
combustion engine further provided with a first transmission member
which is interposed between the first intake cam and the first
intake valve and transmits drive force of the first intake cam to
the first intake valve, a second transmission member which is
interposed between the second intake cam and the second intake
valve and transmits drive force of the second intake cam to the
second intake valve, and a coupling device for coupling and
separating the first transmission member and the second
transmission member, wherein the system couples or separates the
first transmission member and the second transmission member in
accordance with the operating state of the internal combustion
engine.
9. A valve drive system of internal combustion engine as set forth
in claim 6, further provided with an operating state detection
device which detects an operating state of the internal combustion
engine, wherein the system detects the operating state of the
internal combustion engine and determines an amount of offset
between the operating timing of the intake valves by the first
intake cam and the operating timing of the intake valves by the
second intake cam in accordance with the operating state of the
internal combustion engine.
10. A valve drive system of internal combustion engine as set forth
in claim 9 in which a first intake valve and second intake valve
are arranged for each cylinder, the valve drive system of internal
combustion engine further provided with a first transmission member
which is interposed between the first intake cam and the first
intake valve and transmits drive force of the first intake cam to
the first intake valve, a second transmission member which is
interposed between the second intake cam and the second intake
valve and transmits drive force of the second intake cam to the
second intake valve, and a coupling device for coupling and
separating the first transmission member and the second
transmission member, wherein the system couples or separates the
first transmission member and the second transmission member in
accordance with the operating state of the internal combustion
engine.
Description
TECHNICAL FIELD
[0001] The present invention relates to a valve drive system of an
internal combustion engine.
BACKGROUND ART
[0002] In the prior art, there is known an internal combustion
engine which increases the expansion ratio at the time the fuel
burns and expands compared with the actual compression ratio at the
time of compression of the mixture of fuel and air. In this
internal combustion engine, it is possible to suppress the abnormal
combustion which occurs if the compression ratio is high while
improving the heat efficiency. For example, it is known that if
shifting the timing for closing an intake valve by a predetermined
amount after a piston reaches bottom dead center, the actual
compression ratio when compressing the air-fuel mixture at the
inside of a cylinder becomes smaller.
[0003] Japanese Patent Publication No. 2004-183510 A1 relates to a
high expansion ratio cycle engine which is provided with a
supercharger and which sets the expansion ratio larger compared
with the compression ratio and discloses to control an operation of
a variable valve timing mechanism so as to advance an opening
timing of an exhaust valve and increase the exhaust blowdown energy
when it is judged that the engine is operating at a low-medium
speed and low load region and the engine is in an acceleration
transition state.
[0004] Japanese Patent Publication No. 6-33714 A1 discloses a valve
drive structure with a variable valve timing mechanism which is
provided with an intake valve or exhaust valve which is provided in
an engine, a low speed-use cam, a high speed-use cam, a main rocker
arm which can be driven by the low speed-use cam and which drives
the valve, and a sub rocker arm which is driven by the high
speed-use cam. It discloses that this valve drive structure is
provided with a mode switching means which switches between a
non-coupled mode where the sub rocker arm is not coupled with the
main rocker arm and a coupled mode where it is coupled.
[0005] Japanese Patent Publication No. 2008-14191 A1 discloses a
variable valve drive system which can continuously change opening
characteristics of a valve, which variable valve drive system is
provided with an input arm which receives input of a drive cam from
a rocking cam arm and a transmission arm which transfers the input
of the drive cam which is received from the input arm to the valve
and is provided with a cam coupling mechanism as a switching means
for executing and stopping a lift operation of a valve.
CITATION LIST
Patent Literature
[0006] PLT 1: Japanese Patent Publication No. 2004-183510 A1 [0007]
PLT 2: Japanese Patent Publication No. 6-33714 A1 [0008] PLT 3:
Japanese Patent Publication No. 2008-14191 A1
SUMMARY OF INVENTION
Technical Problem
[0008] [0009] In the valve drive structure which is disclosed in
the above Japanese Patent Publication No. 6-33714 A1, the low
speed-use cam has a cam profile which gives an operating timing of
the valve corresponding to low speed operation, the high speed-use
cam has a cam profile which gives an operating timing of the valve
corresponding to high speed operation, and either of the high speed
cam and low speed-use cam is selected for use. In this system, the
on-off valve is driven by either the low speed-use cam or high
speed-use cam so there was the problem that the operating timing of
the valve could not be gradually changed. That is, there was the
problem that it was not possible to continuously change the opening
time of the valve.
[0010] Regarding the valve drive structure which is disclosed in
the above Japanese Patent Publication No. 2004-183510 A1, in the
same way, it uses one cam which has a cam profile which corresponds
to advanced closing of the intake valve and another cam which has a
cam profile which delays the opening time from the one cam so as to
drive the on-off valve. When driving the on-off valve, one of the
cams is used to drive the on-off valve. For this reason, there was
the problem that it was not possible to gradually change the
operating timing of the on-off valve.
[0011] In this regard, in an intake stroke of an internal
combustion engine, loss which is called "intake loss" occurs. This
loss is also called "pumping loss" and corresponds to the energy
loss which occurs when taking in air or an air-fuel mixture to a
combustion chamber. If this loss becomes large, the fuel
consumption amount becomes larger and the output of the internal
combustion engine becomes smaller.
[0012] In the variable valve drive system which is disclosed in the
above Japanese Patent Publication No. 2008-14191 A1, it is
disclosed to variably control the opening characteristics of only
the first valve while making the opening characteristics of the
second valve constant. In this system, it is possible to extend the
time during which at least one of the two valves is open. In this
regard, in this system, the time during which only one of the
valves is open is long, so the intake loss becomes large and
achievement of both an improvement in the fuel consumption amount
and an improvement in the output becomes difficult.
[0013] The present invention has as its object the provision of a
valve drive system of an internal combustion engine with a small
intake loss.
Solution to Problem
[0014] The valve drive system of an internal combustion engine of
the present invention is a valve drive system of an internal
combustion engine which can increase an expansion ratio when fuel
burns and a piston is pushed compared with an actual compression
ratio when an air-fuel mixture which contains fuel is compressed by
a piston, which system is provided with a first intake cam and a
second intake cam which operate intake valves and a variable valve
timing device which changes at least one operating timing of an
operating timing of intake valves by the first intake cam and an
operating timing of intake valves by the second intake cam. The
intake valves are formed to be operated by being driven by the
first intake cam and second intake cam. The variable valve timing
device is formed so as to be able to offset the operating timing of
the intake valves by the first intake cam and the operating timing
of the intake valves by the second intake cam. The first intake cam
and second intake cam include circular parts of substantially
circular cross-sectional shapes and bulging parts which project
from the circular parts and which drive the intake valves. At least
one of the bulging part of the first intake cam and the bulging
part of the second intake cam has a concentric circular part which
is formed in a concentric circular shape with the circular part.
The concentric circular part holds the amount of movement of the
intake valve substantially constant in the period during which the
intake valve is open.
[0015] In the above invention, the bulging part of the first intake
cam and the bulging part of the second intake cam have concentric
circular parts. The first intake cam and second intake cam are
formed so that the amount of movement of the intake valve which is
driven by the concentric circular part of the first intake cam and
the amount of movement of the intake valve which is driven by the
concentric circular part of the second intake cam become
substantially the same. When the operating timing of the intake
valves by the first intake cam and the operating timing of the
intake valves by the second intake cam are different from each
other, the time period where the concentric circular part of the
first intake cam opens the intake valve and the time period where
the concentric circular part of the second intake cam opens the
intake valve preferably overlap each other.
[0016] In the above invention, the system is preferably provided
with an operating state detection device which detects an operating
state of the internal combustion engine, detects the operating
state of the internal combustion engine, and determines the amount
of offset between the operating timing of the intake valves by the
first intake cam and the operating timing of the intake valves by
the second intake cam in accordance with the operating state of the
internal combustion engine.
[0017] In the above invention, the system is preferably a valve
drive system of an internal combustion engine in which a first
intake valve and second intake valve are arranged for each
cylinder, which is provided with a first transmission member which
is interposed between the first intake cam and the first intake
valve and transmits drive force of the first intake cam to the
first intake valve, a second transmission member which is
interposed between the second intake cam and the second intake
valve and transmits drive force of the second intake cam to the
second intake valve, and a coupling device for coupling and
separating the first transmission member and the second
transmission member, and which couples or separates the first
transmission member and the second transmission member in
accordance with the operating state of the internal combustion
engine.
SUMMARY OF INVENTION
[0018] According to the present invention, it is possible to
provide a valve drive system of an internal combustion engine with
a small intake loss.
BRIEF DESCRIPTION OF DRAWINGS
[0019] FIG. 1 is a schematic view of an internal combustion engine
in an Embodiment 1.
[0020] FIG. 2 is a schematic perspective view of a valve drive
system in the Embodiment 1.
[0021] FIG. 3 is a schematic disassembled perspective view of the
valve drive system in the Embodiment 1.
[0022] FIG. 4 is a first schematic cross-sectional view of the
valve drive system in the Embodiment 1.
[0023] FIG. 5 is a second schematic cross-sectional view of the
valve drive system in the Embodiment 1.
[0024] FIG. 6 is a schematic cross-sectional view of an intake cam
of the valve drive system in the Embodiment 1.
[0025] FIG. 7 is a graph of a cam lift of an intake cam in the
Embodiment 1.
[0026] FIG. 8 is a schematic cross-sectional view of a variable
valve timing device which changes an operating timing of intake
valves in the Embodiment 1.
[0027] FIG. 9 is a graph which explains changes in the operating
timing of intake valves in the variable valve timing device in the
Embodiment 1.
[0028] FIG. 10 is a first graph of valve lift when using the valve
drive system in the Embodiment 1 to drive the intake valves.
[0029] FIG. 11 is a second graph of a valve lift when using the
valve drive system in the Embodiment 1 to drive the intake
valves.
[0030] FIG. 12 is a schematic cross-sectional view of an intake cam
of a valve drive system of a comparative example.
[0031] FIG. 13 is a graph of a cam lift of the intake cam of the
valve drive system in the comparative example.
[0032] FIG. 14 is a graph of a valve lift when using the valve
drive system in a first comparative example to drive intake
valves.
[0033] FIG. 15 is a graph of a valve lift when using the valve
drive system in a second comparative example to drive intake
valves.
[0034] FIG. 16 is a schematic disassembled perspective view of a
valve drive system in the Embodiment 2.
[0035] FIG. 17 is a schematic disassembled perspective view of a
part of a rocker arm of the valve drive system in the Embodiment
2.
[0036] FIG. 18 is a first schematic cross-sectional view of a
coupling device which connects one rocker arm and other rocker arm
in the valve drive system in the Embodiment 2.
[0037] FIG. 19 is a second schematic cross-sectional view of a
coupling device which connects one rocker arm and other rocker arm
in the valve drive system in the Embodiment 2.
[0038] FIG. 20 is a graph of the valve lift of intake valves with
one rocker arm and another rocker arm separated in the valve drive
system of the Embodiment 2.
DESCRIPTION OF EMBODIMENTS
Embodiment 1
[0039] Referring to FIG. 1 to FIG. 15, a valve drive system in the
Embodiment 1 of internal combustion engine will be explained. In
the present embodiment, a spark ignition type of ignition internal
combustion engine will be explained as an example. Further, a valve
drive system which drives an intake valve among the on-off valves
will be explained as an example.
[0040] FIG. 1 is a schematic view of an internal combustion engine
in the present embodiment. The internal combustion engine is
provided with an engine body 1. The engine body 1 in the present
embodiment includes a cylinder block 2 and a cylinder head 3. The
cylinder block 2 is formed with hole parts. Inside of each of the
hole parts, a piston 4 is arranged. Pistons 4 are arranged for the
respective cylinders. The spaces which are formed by the top
surfaces of the pistons 4 and the hole parts form combustion
chambers 5.
[0041] The cylinder head 3 has intake ports 8 as parts of the
engine intake passage which communicate with the combustion
chambers 5. The cylinder head 3 has exhaust ports 10 as parts of
the engine exhaust passage which communicate with the combustion
chambers 5. The engine intake passage is a passage which feed air
or a mixture of fuel and air to the combustion chambers 5. The
engine exhaust passage is a passage for exhausting exhaust gas
which is produced due to combustion of fuel in the combustion
chambers 5. Intake valves 7a are arranged at the ends of the intake
ports 8 and are formed so as to open and close the parts of the
engine intake passage which communicate with the combustion
chambers 5. The exhaust valves 9a are arranged at the ends of the
exhaust ports 10 and are formed so as to open and close the parts
of the engine exhaust passage which are communicated with the
combustion chambers 5. The cylinder head 3 has spark plugs 6
fastened to it as ignition devices. The spark plugs 6 are formed so
as to ignite the fuel in the combustion chambers 5.
[0042] The intake ports 8 are connected through intake runners 11
to a surge tank 12. The intake runners 11 have fuel injectors 13
arranged in them for injecting fuel toward the insides of the
intake ports 8. The fuel injectors 13 are not limited to this. They
may also be arranged to directly inject fuel inside of the
combustion chambers 5. The surge tank 12 is connected through an
intake duct 14 to an air cleaner 15. At the inside of the intake
duct 14, a throttle valve 17 which is driven by an actuator 16 is
arranged. Further, inside of the intake duct 14, an intake air
detector 18 is arranged for detecting the amount of intake air.
[0043] Each fuel injector 13 is connected by a fuel feed pipe 26 to
a fuel tank 22. In the middle of the fuel feed pipe 26, an
electronic control type variable discharge fuel pump 24 is
arranged. In the present embodiment, the fuel tank 22 stores
gasoline. The fuel which is stored in the fuel tank 22 is fed
through the fuel feed pipe 26 to the fuel injectors 13 by being
driven by the fuel pump 24.
[0044] On the other hand, the exhaust ports 10 are connected
through an exhaust manifold 19 to, for example, a catalytic
converter 20 which contains a three-way catalyst. If calling the
ratio of air and fuel (hydrocarbons) of the exhaust gas which is
fed to the engine intake passage, combustion chambers, or engine
exhaust passage the "air-fuel ratio (A/F) of the exhaust gas", an
air-fuel ratio sensor 21 for detecting the air-fuel ratio of the
exhaust gas is arranged inside the engine exhaust passage at the
upstream side of the catalytic converter 20.
[0045] The internal combustion engine in the present embodiment is
provided with a control device. The control device in the present
embodiment includes an electronic control unit 30. The electronic
control unit 30 includes a digital computer. The electronic control
unit 30 is provided with components which are connected with each
other by a bidirectional bus 31 such as a ROM (read only memory)
32, RAM (random access memory) 33, and CPU (microprocessor) 34. The
electronic control unit 30 is provided with an input port 35 and
output port 36 which are connected by the bidirectional bus 31.
[0046] The output signal of the intake air detector 18 and the
output signal of the air-fuel ratio sensor 21 are input through
corresponding AD converters 37 to the input port 35. Further, an
accelerator pedal 40 has a load sensor 41 connected to it for
generating an output voltage which is proportional to the amount of
depression of the accelerator pedal 40. The output signal of the
load sensor 41 is input through the corresponding AD converter 37
to the input port 35. Further, the input port 35 has a crank angle
sensor 42 connected to it which generates an output pulse every
time a crankshaft rotates by for example 30.degree.. From the
output of the crank angle sensor 42, the speed of the engine body 1
can be detected.
[0047] On the other hand, the output port 36 is connected through
corresponding drive circuits 38 to the spark plugs 6, fuel
injectors 13, fuel pump 24, and actuator 16. The electronic control
unit 30 in the present embodiment is formed so as to control fuel
injection and control ignition.
[0048] FIG. 2 shows a schematic perspective view of the valve drive
system of the present embodiment. FIG. 3 shows a schematic
disassembled perspective view of the valve drive system of the
present embodiment. Referring to FIG. 2 and FIG. 3, the internal
combustion engine in the present embodiment is provided with a
plurality of intake valves for each cylinder. Further, it is
provided with a plurality of exhaust valves for each cylinder. In
the present embodiment, two intake valves 7a, 7b and two exhaust
valves 9a, 9b are arranged for each cylinder. The respective intake
valves 7a, 7b and exhaust valves 9a, 9b are biased by not shown
elastic members in a direction in which the valves close.
[0049] The valve drive system is provided with an intake cam 52a as
a first intake cam which is supported by an intake cam shaft 51.
The intake cam 52a is formed so as to rotate together with the
intake cam shaft 51. The intake cam shaft 51 is formed so as to
rotate interlocked with movement of the piston 4 which are arranged
at the inside of the cylinder.
[0050] The valve drive system is provided with a rocker arm 55 as a
transmission member which transmits the drive force of the intake
cams 52a, 52b to the intake valves 7a, 7b. The rocker arm 55 is
supported by a rocker shaft 60. The rocker arm 55 is formed so as
to rock about the center axis of the rocker shaft 60 used as the
support rod. The rocker arm 55 has pushing parts 58a, 58b for
pushing the intake valves 7a, 7b. The pushing parts 58a, 58b at the
present embodiment are arranged right above the intake valves 7a,
7b. The rocker arm 55 includes a roller 56. The roller 56 is
supported by the rocker arm body so as to be able to rotate. The
intake cam 52a contacts the roller 56.
[0051] The valve drive system of the present embodiment has exhaust
cams 54a, 54b for driving the exhaust valves 9a, 9b. The exhaust
cams 54a, 54b have cam noses and are arranged to push the exhaust
valves 9a, 9b. The exhaust cams 54a, 54b are supported by an
exhaust cam shaft 53. The exhaust cams 54a, 54b are formed so as to
integrally rotate with the exhaust cam shaft 53. The exhaust cam
shaft 53 is formed so as to rotate interlocked with the movement of
the piston 4 which is arranged at the inside of the cylinder.
[0052] The valve drive system of the present embodiment is provided
with an intake cam 52b as a second intake cam which drives the
intake valves 7a, 7b. The intake cam 52b in the present embodiment
is supported at the exhaust cam shaft 53. The intake cam 52b is
formed so as to rotate together with the exhaust cam shaft 53.
[0053] The rocker arm 55 in the present embodiment has an extension
part 57 which extends toward the intake cam 52b which is arranged
at the exhaust cam shaft 53. The extension part 57 in the present
embodiment is formed in a rod shape. The extension part 57 contacts
the intake cam 52b at the front end. In the present embodiment, the
extension part 57 pushes against and contacts the upper side of the
intake cam 52b. In this way, at the rocker arm 55 in the present
embodiment, the extension part 57 is formed at one side when the
rocker arm 55 rocks while the pushing parts 58a, 58b and roller 56
are formed at the other side.
[0054] In the present embodiment, a second intake cam constituted
by the intake cam 52b is arranged between the two exhaust cams 54a,
54b, but the invention is not limited to this. The intake cam 52b
may also be arranged in the region at the outside of the two
exhaust cams 54a, 54b.
[0055] Referring to FIG. 2, the valve drive system of the present
embodiment is provided with a variable valve timing device 70 which
changes operating timings of the intake valves 7a, 7b by the intake
cam 52a. The variable valve timing device 70 is formed so as to be
able to change the operating timings of the intake valves with
respect to movement of the piston 4 or crank angle. The variable
valve timing device 70 in the present embodiment is connected to
the intake cam shaft 51. The variable valve timing device 70 in the
present embodiment is formed so as to be able to change the phase
of the intake cam 52a with respect to the crank angle.
[0056] FIG. 4 shows a first schematic cross-sectional view of the
valve drive system of the present embodiment. FIG. 4 is a schematic
cross-sectional view when cut along the line A-A in FIG. 2. FIG. 4
is a schematic cross-sectional view when cut along the intake valve
7a and the exhaust valve 9a.
[0057] In the present embodiment, due to the rotational force of
the crankshaft, the intake cam shaft 51 rotates. Due to the intake
cam shaft 51 rotating, the intake cam 52a rotates. The intake cam
52a has a bulging part constituted by the cam nose 61b. By the cam
nose 61b pushing against the rocker arm 55 through the roller 56,
the rocker arm 55 rocks. By the rocker arm 55 rocking, the pushing
part 58a pushes against the intake valve 7a whereby the intake
valve 7a opens in state. Further, by the rocker arm 55 rocking, the
pushing part 58b pushes against the intake valve 7b whereby the
intake valve 7b opens in state (see FIG. 1 and FIG. 2).
[0058] On the other hand, for example, due to the rotational force
of the crankshaft, the exhaust cam shaft 53 rotates. Due to the
exhaust cam shaft 53 rotating, the exhaust cam 54a rotates. By the
cam nose of the exhaust cam 54a pushing against the exhaust valve
9a, the exhaust valve 9a opens in state. In the same way, by the
exhaust cam 54b rotating, the exhaust valve 9b can be opened (see
FIG. 1 and FIG. 2).
[0059] FIG. 5 shows a second schematic cross-sectional view of the
valve drive system of the present embodiment. FIG. 5 is a schematic
cross-sectional view when cut along the line B-B in FIG. 2. FIG. 5
is a schematic cross-sectional view when cut along the part of the
extension part of the rocker arm.
[0060] The intake valves 7a, 7b in the present embodiment are also
driven by the second intake cam constituted by the intake cam 52b.
The extension part 57 abuts against the surface of the intake cam
52b. By the exhaust cam shaft 53 rotating, the intake cam 52b
rotates. The intake cam 52b has a bulging part constituted by the
cam nose 61b. The cam nose 61b of the intake cam 52b pushes against
the extension part 57, whereby the extension part 57 is lifted up.
That is, the rocker arm 55 is rocked. By the extension part 57
being pushed up, the pushing part 58b of the rocker arm 55 is
pushed downward. By the pushing part 58b being pushed downward, the
intake valve 7b is pushed down and opens in state. Further, by the
rocker arm 55 rocking, the pushing part 58a pushes against the
intake valve 7a whereby the intake valve 7a opens in state (see
FIG. 1 and FIG. 2). In this way, due to the action of the intake
cams 52a, 52b, the intake valves 7a, 7b are driven.
[0061] As explained above, the intake valves 7a, 7b in the present
embodiment are driven not only by the first intake cam constituted
by the intake cam 52a but also the second intake cam constituted by
the intake cam 52b. In the valve drive system of the present
embodiment, the intake valves 7a, 7b simultaneously operate to open
and close.
[0062] FIG. 6 shows a schematic cross-sectional view of an intake
cam of the valve drive system of the present embodiment. In FIG. 6,
the first intake cam constituted by the intake cam 52a is taken up
as an example. In the present embodiment, the first intake cam and
the second intake cam are formed so as to become substantially the
same in cross-sectional shapes. The cross-sectional shapes of the
intake cams are not limited to this. The first intake cam and
second intake cam may also be different from each other in
cross-sectional shape.
[0063] The intake cam 52a has a circular part 61a having a
substantially circular shape in cross-sectional shape and a bulging
part constituted by the cam nose 61b which sticks out from the
circular part 61a and drives the intake valves. The circular part
61a of the intake cam 52a is formed into a shape coaxial with the
intake cam shaft 51. Further, the circular part 61a of the intake
cam 52b is formed into a shape coaxial with the exhaust cam shaft
53.
[0064] The cam nose 61b in the present embodiment has a concentric
circular part 61c which is formed in a circular shape concentric
with the circular part 61a. The concentric circular part 61c is
formed at the top surface of the cam nose 61b. The concentric
circular part 61c is included in a concentric circle 101 of the
circular part 61a.
[0065] FIG. 7 shows a graph of a cam lift of an intake cam in the
present embodiment. The abscissa is the rotational angle of the
intake cam. The cam lift corresponds to the amount of movement of
the valves (valve lift). In the graph of FIG. 7, the cam lift is
shown by the solid line, the speed of the cam lift is shown by the
broken line, and the acceleration of the cam lift is shown by the
two-dot chain line. Further, the point of time of half of the time
period during which the cam nose of the intake cam causes a cam
lift is shown by the center line 121 of the one-dot chain line. The
center line 121 corresponds to the point where the cam lift becomes
maximum when, for example, the cam nose does not have a concentric
circular part.
[0066] In the region of the circular part 61a of the intake cam,
the cam lift becomes zero. The cam lift rises along with the
rotational angle of the intake cam 52a in the region of the cam
nose 61b. The cam lift becomes maximum at the concentric circular
part 61c of the cam nose 61b. The region of the concentric circular
part 61c of the cam nose 61b is shown by the arrow 112. At the
region of the concentric circular part 61c, the cam lift becomes
substantially constant. That is, the amount of movement of the
intake valves is maintained substantially constant. Further, in the
region of the concentric circular part 61c, the speed of the cam
lift and the acceleration of the cam lift become zero.
[0067] The region of the lifting part of the cam nose 61b is shown
by the arrow 111. In this region, the cam lift rises and falls.
Along with the rise or fall of the cam lift, the speed and
acceleration of the cam lift change. In this way, the cam nose of
the intake cam in the present embodiment is formed with a
concentric circular part at which the cam lift is maintained
substantially constant.
[0068] Next, the variable valve timing device in the present
embodiment will be explained. The variable valve timing device in
the present embodiment is formed to be able to change the starting
timing of the actual compression action. The variable valve timing
device 70 is connected to the output port 36 of the electronic
control unit 30 and is controlled by the electronic control unit 30
(see FIG. 1).
[0069] FIG. 8 shows a schematic view of the variable valve timing
device in the present embodiment. The variable valve timing device
70 in the present embodiment is attached to an end of the intake
cam shaft 51 (see FIG. 2).
[0070] The variable valve timing device 70 in the present
embodiment is provided with a timing pulley 71 which rotates in the
direction of the arrow 115 by a timing belt which engages with the
crankshaft of the engine body and a cylindrical housing 72 which
rotates together with the timing pulley 71. The variable valve
timing device 70 is provided with a shaft 73 which rotates together
with the intake cam shaft 51 and can rotate relative to the
cylindrical housing 72, a plurality of partition walls 74 which
extend from the inner circumferential surface of the cylindrical
housing 72 to the outer circumferential surface of the shaft 73,
and vanes 75 which extend between the partition walls 74 from the
outer circumferential surface of the shaft 73 to the inner
circumferential surface of the cylindrical housing 72. At the two
sides of the vanes 75, advance-use oil pressure chambers 76 and
retardation-use oil pressure chambers 77 are formed.
[0071] The variable valve timing device includes a feed device
which feeds working oil to the oil pressure chambers 76, 77. The
feed device includes a working oil feed control valve 78. The
working oil feed control valve 78 includes oil pressure ports 79,
80 which are connected to the oil pressure chambers 76, 77, a feed
port 82 of working oil which is discharged from the oil pressure
pump 81, a pair of drain ports 83, 84, and a spool valve 85 which
controls communication and cutoff between the ports 79, 80, 82, 83,
and 84.
[0072] When the phase of the intake cam 52a which is arranged at
the intake cam shaft 51 should be advanced, in FIG. 8, the spool
valve 85 is moved to the right. The working oil which is fed from
the feed port 82 is fed through the oil pressure port 79 to the
advance-use oil pressure chambers 76 while the working oil in the
retardation-use oil pressure chambers 77 is discharged from the
drain port 84. At this time, the shaft 73 is rotated relative to
the cylindrical housing 72 in the direction of the arrow 115.
[0073] As opposed to this, when retarding the phase of the intake
cam 52a which is arranged at the intake cam shaft 51, in FIG. 8,
the spool valve 85 is moved to the left. The working oil which is
fed from the feed port 82 is fed through the oil pressure port 80
to the retardation-use oil pressure chambers 77 while the working
oil in the advance-use oil pressure chambers 76 is discharged from
the drain port 83. At this time, the shaft 73 is rotated relative
to the cylindrical housing 72 in a direction opposite to the arrow
115.
[0074] When the shaft 73 is rotating relative to the cylindrical
housing 72, the spool valve 85 is returned to the neutral position
whereby the rotational operation of the shaft 73 stops. The shaft
73 is held at the position at that time. Therefore, the variable
valve timing device 70 can advance the phase of the intake cam 52a
which is fastened to the intake cam shaft 51 by exactly the desired
amount. Alternatively, it can retard the phase of the intake cam
52a by exactly the desired amount.
[0075] FIG. 9 shows a graph when changing the operating timing of
intake valves by the variable valve timing device of the present
embodiment. This graph shows the state of using the single intake
cam to which the variable valve timing device is connected to drive
the intake valves. The abscissa is the crank angle, while the
ordinate is the amount of movement of the valves constituted by the
valve lift.
[0076] By driving the variable valve timing device, as shown by the
arrow 114, it is possible to change the operating timing of the
intake valves which is shown by the solid line to the operating
timing of the intake valves which is shown by the broken line. The
solid line shows the state where the variable valve timing device
advances the phase of the intake cam the most, while the broken
line shows the state where it retards the phase of the intake cam
the most. The opening timing of the intake valves can be freely set
between the range which is shown by the solid line and the range
which is shown by the broken line. The closing timing of the intake
valves can also be set to any crank angle within the range which is
shown by the reference sign C.
[0077] Note that, the variable valve timing device is not limited
to the above embodiment. It is possible to employ any device which
can change the operating timing of the valves.
[0078] The internal combustion engine in the present embodiment can
retard the timing for closing the intake valves to thereby increase
the expansion ratio at the time when the fuel burns and pushes the
piston over the actual compression ratio when the air-fuel mixture
which contains fuel is compressed by the piston. That is, the
internal combustion engine of the present embodiment can burn fuel
by an Atkinson cycle or other high expansion ratio cycle.
[0079] The variable called the "normal compression ratio" is
determined by the structure of the internal combustion engine. The
normal compression ratio is determined by the volume of the
combustion chamber and stroke volume of the piston when the piston
reaches top dead center. This compression ratio is also called the
"mechanical compression ratio". The mechanical compression ratio of
the internal combustion engine, if referring to the volume of the
combustion chamber when the piston reaches top dead center as
simply the "volume of the combustion chamber", is shown by
(compression ratio)=(volume of combustion chamber+stroke volume of
piston)/(volume of combustion chamber).
[0080] The internal combustion engine in the present embodiment can
delay the timing for closing the intake valves so as to reduce the
volume when the combustion chamber is closed in the compression
stroke. No compression action is performed while the intake valves
are opened, so the actual compression ratio can be made smaller.
That is, it is possible to reduce the actual compression ratio from
the mechanical compression ratio. Here, the actual compression
ratio can be shown by (actual compression ratio)=(volume of
combustion chamber+stroke volume of piston from position where
intake valves close to top dead center)/(volume of combustion
chamber).
[0081] On the other hand, the expansion ratio when the fuel burns
and expands becomes equal to the mechanical compression ratio. By
performing high expansion rate control which retards the timing of
closing the intake valves in an internal combustion engine with a
high mechanical compression ratio in this way, it is possible to
keep the pressure of the combustion chamber from becoming overly
high and abnormal combustion from occurring. Further, it is
possible to increase the expansion ratio so as to improve the heat
efficiency. Furthermore, it is possible to reduce the intake loss
so as to enable increase of the opening degree of the throttle
valve.
[0082] Referring to FIG. 2 and FIG. 3, the variable valve timing
device 70 in the present embodiment is formed so as to be able to
change the phase of the first intake cam constituted by the intake
cam 52a. As opposed to this, the second intake cam constituted by
the intake cam 52b is formed so as to rotate by a constant phase
with respect to the movement of the piston or crank angle. The
rocker arm 55 in the present embodiment is formed to transmit the
drive force of the intake cam 52a and the drive force of the intake
cam 52b to the intake valves 7a, 7b. The valve drive system of the
present embodiment can offset the operating timings of the intake
valves 7a, 7b by the action of the intake cam 52a and the operating
timings of the intake valves 7a, 7b by the action of the intake cam
52b. Further, the operating timings of the intake valves 7a, 7b due
to the action of the intake cam 52a can be continuously gradually
changed.
[0083] The valve drive system of the present embodiment is provided
with an operating state detection device which detects an operating
state of the internal combustion engine and is formed so as to
change the phase of the intake cam 52a in accordance with the
operating state which is detected by the operating state detection
device. That is, it is formed so as to determine the amount of
offset of the operating timing of the intake valves by the intake
cam 52a and the operating timing of the intake valves by the intake
cam 52b.
[0084] Referring to FIG. 1, the operating state detection device in
the present embodiment can detect the load of the internal
combustion engine. The load of the internal combustion engine can,
for example, be estimated from the output of the load sensor 41
which detects the amount of depression of the accelerator pedal 40.
Alternatively, it can be estimated from the opening degree of the
throttle valve 17 etc. Further, the operating state detection
device in the present embodiment can detect the engine speed of the
internal combustion engine. The engine speed can be detected by the
output of the crank angle sensor 42.
[0085] FIG. 10 shows a graph which explains the drive states of the
exhaust valves and intake valves when the internal combustion
engine of the present embodiment is performing first operational
control. The abscissa shows the crank angle, while the ordinate
shows the valve lift. In the example which is shown in FIG. 10, the
exhaust valves open in the range of crank angle from slightly
before bottom dead center (BDC) of the piston to substantially top
dead center (TDC).
[0086] The first operational control in the present embodiment is
used in the case where the load of the engine body is large and the
engine speed is low. In the first operational control, the variable
valve timing device is used to control the phase of the intake cam
52a and the phase of the intake cam 52b to become substantially the
same. For this reason, the change in the valve lifts of the intake
valves 7a, 7b becomes substantially the same as the case of being
driven by a single intake cam.
[0087] In the intake stroke, the intake valves are made to open
when the piston is substantially at top dead center in position,
while the intake valves are made to close when the piston is
substantially at bottom dead center in position. The two intake
valves 7a, 7b are driven by a single rocker arm 55, so the two
intake valves 7a, 7b substantially simultaneously open and close.
When the load of the internal combustion engine is large and the
engine speed is low, closing the intake valves faster enables a
larger amount of air-fuel mixture or air to be taken in. For this
reason, in the first operational control, control is performed to
match the phases of the two intake cams 52a, 52b and close the
intake valves early.
[0088] FIG. 11 is a graph which explains the drive states of the
exhaust valves and intake valves when the internal combustion
engine of the present embodiment is performing second operational
control. The drive state of the exhaust valves is similar to the
first operational control in the present embodiment. In the second
operational control, high expansion ratio control is performed for
retarding the timing for closing the intake valves. High expansion
ratio control can be performed in all regions of the engine speed
at the time of a low load.
[0089] In the second operational control of the present embodiment,
due to the variable valve timing device, the phase of the intake
cam 52a is retarded from the phase of the intake cam 52b. Control
is performed for retarding the operating timing of the intake
valves 7a, 7b which are driven by the intake cam 52a. For this
reason, the intake valves 7a, 7b are driven by the intake cam 52b
when starting to open, then are driven by the intake cam 52a. The
timing for closing the intake valves 7a, 7b can be retarded. Due to
this control, it is possible to reduce the actual compression ratio
at the cylinder, while maintaining the state of a large expansion
ratio. As a result, it is possible to increase the expansion ratio
over the actual compression ratio.
[0090] Next, in third operational control in the present
embodiment, when the phase of the intake cam 52a is retarded from
the phase of the intake cam 52b, for example, the phase of the
intake cam 52a, which is smaller than the second operational
control, is retarded. The third operational control can be employed
when the internal combustion engine is in an operating state of a
high load and a high engine speed. When the engine speed is high,
it is possible to close the intake valves slower so as to use the
inertia of the air and take in a larger amount of air-fuel mixture
or air inside of the combustion chamber. For this reason, in the
high load and high speed region, control may be performed to retard
the phase of the intake cam 52a. Control may be performed to retard
the operating timing of the intake valves 7a, 7b which are driven
by the intake cam 52a.
[0091] The internal combustion engine in the present embodiment can
detect the operating state by the operating state detection device
and gradually change the operational control. Alternatively, it is
possible to detect the operating state and determine the amount of
offset of the operating timing of the intake valves according to
the action of the first intake cam and the operating timing of the
intake valves according to the action of the second intake cam
corresponding to the operating state. Due to this control, it is
possible to operate by the optimal amount of offset corresponding
to the operating state of the internal combustion engine. For this
reason, it is possible to reduce the intake loss while suppressing
the amount of fuel consumption and improving the output.
[0092] For example, when the engine speed of the internal
combustion engine is low and the load of the internal combustion
engine shifts from a low load to a high load, it is possible to
gradually shift from the above second operational control to first
operational control. Alternatively, for example, if the internal
combustion engine is under high load, when the engine speed
gradually rises, it is possible to gradually shift from the first
operational control to the third operational control.
[0093] The operating state which is detected by the operating state
detection device is not limited to the engine speed and load. It is
possible to employ any variable which affects the combustion state
of the fuel.
[0094] The internal combustion engine in the present embodiment can
reduce the intake loss since it extends the period during which
both intake valves are open. Here the valve drive system of a
comparative example of the present embodiment will be used as an
example for the explanation.
[0095] FIG. 12 shows a schematic cross-sectional view of an intake
cam of a comparative example. The intake cam 52a of the comparative
example has a circular part 61a and a cam nose 61b. The cam nose
61b does not have a concentric circular part and is formed to have
an approximately mountain shape in cross-sectional shape. The
region which is shown by the arrow 111 corresponds to the region of
the lifting part where the cam lift changes.
[0096] FIG. 13 shows a graph which explains the relationship
between a rotational angle and cam lift of an intake cam of a
comparative example. The cam lift increases steadily until the
vertex of the cam nose 61b and steadily decreases after the vertex
of the cam nose 61b. The speed of the cam lift and the acceleration
of the cam lift fluctuate. In particular, the speed of the cam lift
is constantly changing.
[0097] FIG. 14 shows a graph which explains the operation of intake
valves of a valve drive system of a first comparative example. The
valve drive system of the first comparative example is provided
with two intake cams and two intake valves. For the two intake
cams, intake cams of the comparative example are used. Further, the
valve drive system of the first comparative example is formed so
that one intake cam drives one intake valve, while the other intake
cam drives the other intake valve independently. That is, the two
intake valves are respectively independently driven by the intake
cams.
[0098] The graph of FIG. 14 is a graph of the amounts of movement
of the intake valves when using the variable valve timing device to
delay the phase of the first intake cam from the phase of the
second intake cam. In the valve drive system of the first
comparative example, one cam drives one intake valve, so the period
in which at least one of the two intake valves 7a, 7b is opened
becomes longer. In this regard, the period in which one valve is
opened and the other valve is closed becomes longer, while the
period in which the two valves are simultaneously open becomes
shorter. As opposed to this, the valve drive system of the present
embodiment, referring to FIG. 11, can extend the periods in which
the two intake valves are opened. As a result, the intake loss can
be reduced and the heat efficiency can be improved.
[0099] In particular, in high expansion ratio control, even at the
end of the period in which the intake valves are opened, it is
preferable that a plurality of intake valves be open. In high
expansion ratio control, to retard the timing of closing the intake
valves, part of the air-fuel mixture which flows into the
combustion chamber is discharged into the intake port while the
piston rises. In this case as well, by a plurality of intake valves
opening, the force of raising the piston can be reduced and the
loss can be decreased.
[0100] FIG. 15 shows a graph which explains the operation of the
intake valves of the valve drive system of a second comparative
example. The valve drive system of the second comparative example
replaces the intake cams of the valve drive system of the present
embodiment with the intake cams of the comparative example. That
is, the two intake valves 7a, 7b are driven by a single rocker arm
55. In the valve drive system of the second comparative example, a
difference arises in the coupling part of the drive of the intake
valve by the second intake cam and the drive of the intake valve by
the first intake cam. During the period which an intake valve is
moving in the closing direction due to the action of the second
intake cam, an intake valve is rapidly turning to the open
direction due to the action of the first intake cam. In the system
of the second comparative example, at this time, sometimes shock
occurs in the operation of the intake valves. Further, noise is
liable to be generated and the operation of the intake valves is
liable to become unstable.
[0101] Referring to FIG. 11, as opposed to this, the valve drive
system of the present embodiment is formed so that when the intake
cams are out of phase from each other, at any phase differences,
the period in which the concentric circular part of the first
intake cam opens the intake valve and the period in which the
concentric circular part of the second intake cam opens the intake
valve overlap with each other. Due to this configuration, when the
lifts of the intake valves become maximum, the valve lifts of the
intake valves can be kept substantially constant. For this reason,
it is possible to suppress shock when driving the intake
valves.
[0102] Further, in the present embodiment, by making the phase of
the first intake cam deviate to the maximum extent from the phase
of the second intake cam, the amount of offset of the operating
timing of the first intake valve with respect to the operating
timing of the second intake valve becomes maximum. In this case as
well, the valve drive system of the present embodiment is formed so
that the period during which an intake valve is opened by the
concentric circular part of the first intake cam and the period
during which an intake valve is opened by the concentric circular
part of the second intake cam overlap. By employing this
constitution, even when the above amount of offset becomes the
maximum, it is possible to maintain the maximum value of the lift
of the intake valves substantially constant and suppress shock
given to the intake valves. Alternatively, no matter by what amount
of offset the operating timing of the first intake valve is
shifted, it is possible to maintain the maximum value of the lift
of the intake valve substantially constant.
[0103] In the present embodiment, two intake valves are arranged
for one cylinder, but the invention is not limited to this. A
single intake valve is also possible. Further, in the present
embodiment, two intake cams drive the intake valves, but the
invention is not limited to this. A plurality of intake cams may be
arranged for one cylinder.
[0104] Furthermore, in the present embodiment, the system is formed
so that the variable valve timing device is connected to the first
intake cam, the phase of the first intake cam is variable, and the
operating timing of the first intake valve is shifted, but the
invention is not limited to this. It is sufficient that at least
one of the first intake cam and second intake cam have the variable
valve timing device connected to it. Alternatively, the internal
combustion engine may be formed so that operating timing of the
intake valves by the first intake cam and the operating timing by
the second intake cam can be offset from each other.
[0105] Further, in the present embodiment, the first intake cam is
arranged at the intake cam shaft, and the second intake cam is
arranged at the exhaust cam shaft, but the invention is not limited
to this. The first intake cam and second intake cam can be arranged
at any shaft which they rotate interlocked with the movement of the
piston in the cylinder. Further, the valve drive system is not
limited to an embodiment where the intake cams drive the intake
valves through the rocker arms and other transmission members and
may be formed so that the intake cams directly drive the intake
valves.
[0106] Further, in the present embodiment, concentric circular
parts are formed at both the bulging part of the first intake cam
and the bulging part of the second intake cam, but the invention is
not limited to this. It is sufficient that a concentric circular
part be formed at least at one of the intake cams.
Embodiment 2
[0107] Referring to FIG. 16 to FIG. 20, a valve drive system of an
internal combustion engine in the Embodiment 2 will be explained.
The valve drive system of the present embodiment differs from the
Embodiment 1 in the structure of the transmission member, as
constituted by the rocker arm, which transmits the drive force of
the intake cam to the intake valves.
[0108] FIG. 16 shows a schematic disassembled perspective view of
the valve drive system of the present embodiment. The valve drive
system of the present embodiment is provided with a first
transmission member constituted by a rocker arm 55a and with a
second transmission member constituted by a rocker arm 55b. The
rocker arm 55a and the rocker arm 55b are formed to be able to
independently rock about the rocker shaft 60 as the center of
rocking. The first intake cam constituted by the intake cam 52a and
the second intake cam constituted by the intake cam 52b in the
present embodiment are formed to have cross-sectional shapes which
have circular parts and bulging parts and to have bulging parts
which have concentric circular parts.
[0109] The rocker arm 55a includes a roller 56 and a pushing part
58a. The rocker arm 55b includes an extension part 57 and a pushing
part 58b. The intake cam 52a is fastened to the intake cam shaft
51. The intake cam shaft 51 has a not shown variable valve timing
device connected to it.
[0110] The intake cam 52a pushes against the rocker arm 55a through
the roller 56. The rocker arm 55a pushes against the intake valve
7a, whereby the intake valve 7a can be opened. On the other hand,
the intake cam 52b which is attached to the exhaust cam shaft 53
pushes against the rocker arm 55b, whereby the rocker arm 55b is
made to rock. When the rocker arm 55b rocks, it pushes against the
intake valve 7b whereby the intake valve 7b can be opened.
[0111] FIG. 17 is a schematic perspective view of the time when
disassembling the part of the rocker arm of the valve drive system
of the present embodiment. FIG. 18 shows a first schematic
cross-sectional view when cutting a rocker arm and a rocker shaft
for making the rocker arm rock.
[0112] Referring to FIG. 17 and FIG. 18, the valve drive system of
the present embodiment includes a coupling device which couples and
separates the rocker arm 55a and the rocker arm 55b. The coupling
device in the present embodiment includes a lock pin 63 for
coupling the rocker arm 55a and the rocker arm 55b so as to
integrally rock. The coupling device in the present embodiment
includes a slider 62 which pushes against the lock pin 63 and a
return spring 64 which biases the lock pin 63 and slider 62.
[0113] The rocker arm 55a is formed with a hole part 65a. The
rocker arm 55b is formed with a hole part 65b. The hole parts 65a,
65b are formed at the surfaces of the rocker arms 55a, 55b facing
each other. The hole parts 65a, 65b are formed so that the lock pin
63 and slider 62 can move inside. The hole parts 65a, 65b are
formed to correspond to the outer shapes of the lock pin 63 and
slider 62.
[0114] The hole part 65a and hole part 65b are formed so as to
communicate with each other when the rocker arms 55a, 55b are
arranged at predetermined rocking positions. The hole parts 65a,
65b in the present embodiment are formed so as to match in position
and communicate with each other when the rocker arm 55a abuts
against the circular part 61a of the intake cam 52a and further the
rocker arm 55b abuts against the circular part 61a of the intake
cam 52b.
[0115] The slider 62, lock pin 63, and return spring 64 are
arranged inside of the hole parts 65a, 65b. The return spring 64
pushes the lock pin 63 toward the inlet of the oil path 63 through
the slider 62.
[0116] Inside of the rocker shaft 60 and rocker arm 55a, an oil
path 67 is formed. The valve drive system of the present embodiment
is provided with a working oil feed device which feeds a working
oil to the oil path 67. The working oil feed device is formed so as
to be able to feed pressured working oil. The oil path 67 is formed
passing though the inside of the rocker shaft 60 and rocker arm 55a
and feeding working oil to the hole part 65a. The working oil feed
device in the present embodiment includes an oil pressure control
valve 68 which is connected to the oil path 67. The oil pressure
control valve 68 is formed to be able to adjust the pressure of the
working oil which is fed to the hole part 65a. The working oil feed
device in the present embodiment is controlled by the electronic
control unit 30 (see FIG. 1).
[0117] FIG. 18 shows the state when due to control of the oil
pressure control valve 68, the pressure of the working oil which is
fed to the hole part 65a is low. In this state, the lock pin 63, as
shown by the arrow 113, is pushed against by the elastic force of
the return spring 64. The interface between the slider 62 and the
lock pin 63 matches with the gap which is formed between the rocker
arm 55a and the rocker arm 55b. The rocker arm 55a and the rocker
arm 55b are not coupled with each other in this state. For this
reason, the rocker arm 55a and the rocker arm 55b can rock
independently without affecting each other.
[0118] FIG. 19 shows a second schematic cross-sectional view when
cutting a rocker arm and a rocker shaft for making the rocker arm
rock. By opening the oil pressure control valve 68, it is possible
to feed high pressure working oil through the oil path 67 to the
hole part 65a. The biasing force due to the pressure of the working
oil which is fed to the hole part 65a becomes larger than the
biasing force due to the return spring 64, so the slider 62 and
lock pin 63 move toward the inside of the hole part 65b. At the
clearance part between the rocker arm 55a and the rocker arm 55b,
the lock pin 63 is arranged. The rocker arm 55a and the rocker arm
55b are coupled with each other. The rocker arm 55a and the rocker
arm 55b rock together.
[0119] In this way, the valve drive system of the present
embodiment can drive the rocker arm 55a and the rocker arm 55b
independently from each other or drive them together. By raising
the pressure of the working oil which is fed to the coupling device
and making the rocker arm 55a and rocker arm 55b integrated, the
system becomes similar to the valve drive system which is provided
with one rocker arm in the Embodiment 1 and a similar function can
be exhibited.
[0120] Referring to FIG. 18, the valve drive system of the present
embodiment can lower the pressure of the working oil which is fed
to the coupling device so as to make the rocker arm 55a and the
rocker arm 55b independently rock. In the operating state where the
load of the internal combustion engine is small, sometimes the fuel
is not stably burned in the combustion chamber 5. For example, when
the air-fuel mixture which is fed to the inside of the combustion
chamber 5 is small, sometimes the fuel does not stably burn. In
such a case, control is performed to independently drive the rocker
arm 55a and rocker arm 55b of the valve drive system. Furthermore,
control is performed which offsets the operating timing of the
intake valve 7a and the operating timing of the intake valve 7b
from each other by the variable valve timing device.
[0121] Referring to FIG. 16 and FIG. 18, by separating the rocker
arm 55a and the rocker arm 55b, the first intake valve constituted
as the intake valve 7a is operated by the action of the first
intake cam constituted by the intake cam 52a, while the second
intake valve constituted as the intake valve 7b is operated by the
action of the second intake cam constituted as the intake cam
52b.
[0122] FIG. 20 shows a graph of the valve lift of the intake valves
in operational control in the present embodiment. FIG. 20 shows a
graph of the lift of the intake valves when operating in a state
with the two rocker arms 55a, 55b separated and the operating
timings of the two intake valves shifted from each other. The valve
lift of the second intake valve constituted by the intake valve 7b
is shown by the straight line, while the valve lift of the first
intake valve constituted by the intake valve 7a is shown by the
one-dot chain line. In the operational control which is shown in
FIG. 20, the phase difference of the intake cam 52b and the intake
cam 52a is made maximum. That is, the amount of offset of the
operating timings of the intake valves is made maximum. The valve
drive system of the present embodiment is formed so that even if
the amount of offset is made the maximum, the period where the
second intake valve is opened by the concentric circular part of
the second intake cam and period where the first intake valve is
opened by the concentric circular part of the first intake cam
overlap with each other.
[0123] Due to the action of the second intake cam constituted by
the intake cam 52b, the second intake valve constituted by the
intake valve 7b starts to be driven. After this, due to the action
of the first intake cam constituted by the intake cam 52a, the
first intake valve constituted by the intake valve 7a is driven. In
the present embodiment, one valve opens, then the other valve
opens, so it is possible to form a flow of air-fuel mixture in the
circumferential direction of the combustion chamber. That is, it is
possible to form a swirl flow. For this reason, the air-fuel
mixture can be sufficiently mixed inside of the combustion chamber.
Even when the air or air-fuel mixture which flows into the
combustion chamber is small, stable combustion is possible.
Further, in the valve drive system of the present embodiment as
well, a concentric circular part is formed at the bulging part of
the intake cam, so it is possible to lengthen the period during
which the two valves are open and possible to reduce the intake
loss.
[0124] The coupling device in the present embodiment includes an
oil path which feeds oil, a return spring, and a lock pin, but the
invention is not limited to this. For the coupling device, any
configuration may be employed so long as integrally coupling and
separating a plurality of rocker arms.
[0125] The rest of the configuration, action, and effects are
similar to those of the Embodiment 1, so the explanations will not
be repeated here.
[0126] The above embodiments may be suitably combined. In the above
figures, the same or corresponding parts are assigned the same
reference signs. Note that, the above embodiments are illustrative
and do not limit the invention. The embodiments include changes
within the scope of the claims.
REFERENCE SIGNS LIST
[0127] 1 engine body [0128] 5 combustion chamber [0129] 6 spark
plug [0130] 7a, 7b intake valve [0131] 17 throttle valve [0132] 18
intake air detector [0133] 30 electronic control unit [0134] 40
accelerator pedal [0135] 41 load sensor [0136] 42 crank angle
sensor [0137] 51 intake cam shaft [0138] 52a, 52b intake cam [0139]
55, 55a, 55b rocker arm [0140] 57 extension part [0141] 58a, 58b
pushing part [0142] 60 rocker shaft [0143] 61a circular part [0144]
61b cam nose [0145] 61c concentric circular part [0146] 62 slider
[0147] 63 lock pin [0148] 64 return spring [0149] 67 oil path
[0150] 70 variable valve timing device
* * * * *