U.S. patent application number 12/310928 was filed with the patent office on 2012-12-27 for compression installation.
Invention is credited to Hans-Gerd Kolscheid, Klaus Peters.
Application Number | 20120324861 12/310928 |
Document ID | / |
Family ID | 38229928 |
Filed Date | 2012-12-27 |
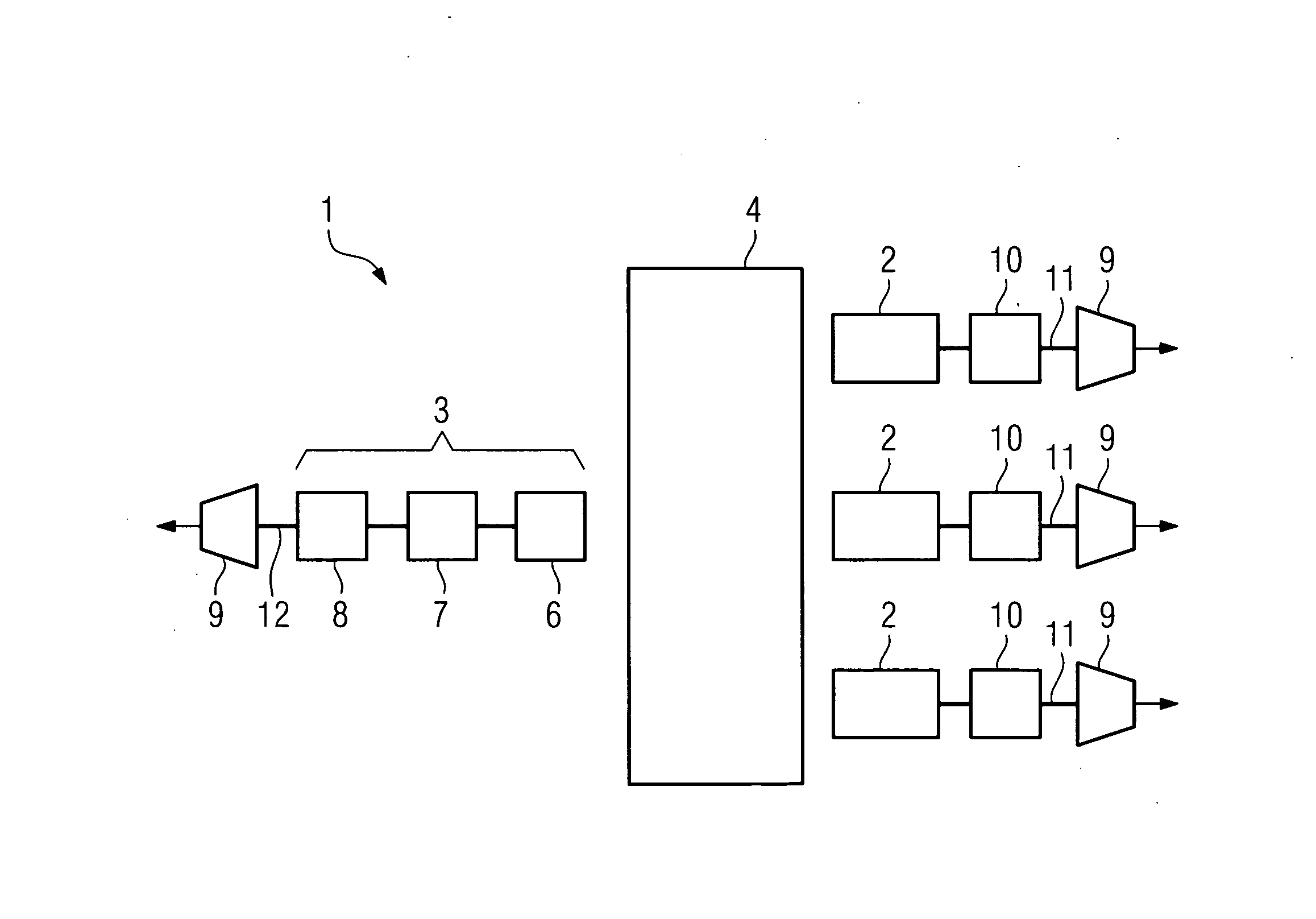
United States Patent
Application |
20120324861 |
Kind Code |
A1 |
Kolscheid; Hans-Gerd ; et
al. |
December 27, 2012 |
Compression Installation
Abstract
A compressor plant with at least one gas turbine having a gas
turbine compressor and with a steam turbine is disclosed, wherein a
steam generation plant which is assigned to the gas turbine is
operated with exhaust gases of the gas turbine, such that the steam
generated in the steam generation plant drives the stream turbine.
There is assigned at least one additional compressor for
compressing a process medium. The compressor is connected directly
to the gas turbine and/or the steam turbine such that the assigned
compressor is driven in each case directly by the gas turbine
and/or the steam turbine.
Inventors: |
Kolscheid; Hans-Gerd;
(Duisburg, DE) ; Peters; Klaus; (Mulheim,
DE) |
Family ID: |
38229928 |
Appl. No.: |
12/310928 |
Filed: |
September 11, 2007 |
PCT Filed: |
September 11, 2007 |
PCT NO: |
PCT/EP2007/059502 |
371 Date: |
December 8, 2009 |
Current U.S.
Class: |
60/39.182 |
Current CPC
Class: |
F25J 1/0283 20130101;
F25J 1/0287 20130101; F25J 1/0022 20130101; F25J 1/0282 20130101;
F25J 1/0289 20130101; F01K 23/064 20130101; F01K 23/10
20130101 |
Class at
Publication: |
60/39.182 |
International
Class: |
F01K 23/10 20060101
F01K023/10 |
Foreign Application Data
Date |
Code |
Application Number |
Sep 15, 2006 |
EP |
06019355.4 |
Claims
1.-8. (canceled)
9. A compression installation comprising: a gas turbine with a gas
turbine compressor; a steam turbine with a steam generating
installation being operated with exhaust gases of the gas turbine
such that the steam generated in the steam generating installation
drives the steam turbine, an additional compressor for compression
of a process medium, the compressor being connected directly to the
gas turbine such that the compressor is respectively driven
directly by the gas turbine; and a starter-helper motor generator
associated to the gas turbine, the starter-helper motor generator
being used both as a helper motor (auxiliary motor) or as a
generator.
10. A compression installation comprising: a gas turbine with a gas
turbine compressor; a steam turbine with a steam generating
installation being operated with exhaust gases of the gas turbine
such that the steam generated in the steam generating installation
drives the steam turbine, an additional compressor for compression
of a process medium, the compressor being connected directly to the
steam turbine such that the compressor is respectively driven
directly by the steam turbine; and a starter-helper motor generator
associated to the gas turbine, the starter-helper motor generator
being used both as a helper motor (auxiliary motor) or as a
generator.
11. A compression installation comprising: a gas turbine with a gas
turbine compressor; a steam turbine with a steam generating
installation being operated with exhaust gases of the gas turbine
such that the steam generated in the steam generating installation
drives the steam turbine, an additional compressor for compression
of a process medium, the compressor being connected directly to the
gas turbine and the steam turbine such that the compressor is
respectively driven directly by the gas turbine and the steam
turbine; and a starter-helper motor generator associated to the gas
turbine, the starter-helper motor generator being used both as a
helper motor (auxiliary motor) or as a generator.
12. The compression installation as claimed in claim 9, wherein the
additional compressor is followed by an electrical process machine
and/or a generator.
13. The compression installation as claimed in claim 10, wherein
the additional compressor is followed by an electrical process
machine and/or a generator.
14. The compression installation as claimed in claim 11, wherein
the additional compressor is followed by an electrical process
machine and/or a generator.
15. The compression installation as claimed in claim 9, wherein the
additional compressor associated with the gas turbine and the gas
turbine have a common shaft.
16. The compression installation as claimed in claim 10, wherein
the additional compressor is associated with the steam turbine and
the steam turbine have a common shaft.
17. The compression installation as claimed in claim 9, wherein
both the gas turbine and the steam turbine each have an additional
compressor respectively connected directly to the gas turbine and
the steam turbine such that the respectively connected compressors
are respectively driven directly by the gas turbine and the steam
turbine.
18. The compression installation as claimed in claim 10, wherein
both the gas turbine and the steam turbine each have an additional
compressor respectively connected directly to the gas turbine and
the steam turbine such that the respectively connected compressors
are respectively driven directly by the gas turbine and the steam
turbine.
19. The compression installation as claimed in claim 11, wherein
both the gas turbine and the steam turbine each have an additional
compressor respectively connected directly to the gas turbine and
the steam turbine such that the respectively connected compressors
are respectively driven directly by the gas turbine and the steam
turbine.
20. The compression installation as claimed in claim 17, wherein
the additional compressor which is respectively associated with the
gas turbine and the steam turbine is used as a compressor in a gas
liquefaction installation.
21. The compression installation as claimed in claim 18, wherein
the additional compressor which is respectively associated with the
gas turbine and the steam turbine is used as a compressor in a gas
liquefaction installation.
22. The compression installation as claimed in claim 19, wherein
the additional compressor which is respectively associated with the
gas turbine and the steam turbine is used as a compressor in a gas
liquefaction installation.
23. The compression installation as claimed in claim 9, wherein the
gas turbine has a plurality of additional compressors which are
driven directly by the gas turbine.
24. The compression installation as claimed in claim 10, wherein
the steam turbine has a plurality of additional compressors driven
directly by the steam turbine.
25. The compression installation as claimed in claim 11, wherein
the gas turbine and the steam turbine each have a plurality of
additional compressors driven directly by the gas turbine and the
steam turbine.
26. The compression installation as claimed in claim 9, wherein the
steam generating installation is in the form of a waste-heat
boiler.
27. The compression installation as claimed in claim 10, wherein
the steam generating installation is in the form of a waste-heat
boiler.
28. The compression installation as claimed in claim 11, wherein
the steam generating installation is in the form of a waste-heat
boiler.
Description
CROSS REFERENCE TO RELATED APPLICATIONS
[0001] This application is the US National Stage of International
Application No. PCT/EP2007/059502 filed Sep. 11, 2007 and claims
the benefit thereof. The International Application claims the
benefits of European Patent application No. 06019355.4 EP filed
Sep. 15, 2006, both of the applications are incorporated by
reference herein in their entirety.
FIELD OF INVENTION
[0002] The invention relates to a compression installation, in
particular for gas liquefaction, having at least one gas turbine
which comprises a gas turbine compressor, and having a steam
turbine with a steam generating installation, which is associated
with the gas turbine, being operated with exhaust gases from the
gas turbine, such that the steam which is generated in the steam
generating installation drives the steam turbine, with the
combination of the gas turbine and the steam turbine having at
least one additional associated compressor for compression of a
process medium, which compressor is connected directly to the gas
turbine and/or to the steam turbine such that the associated
compressor can respectively be driven directly by the gas turbine
and/or the steam turbine.
BACKGROUND OF INVENTION
[0003] It is known for either gas turbines or steam turbines to be
used, for example, to generate electricity for electrical drive
machines or electric motors for driving compressors. The known
prior art has the disadvantage that the overall efficiency of the
installations is restricted to the capabilities of the individual
process. In this case, the efficiencies of gas turbines are about
40%, those of steam turbines are about 45%, and those of electrical
process machines (for example electric motors) are about 98%.
However, in the case of electrical process machines and electric
motors, it must be remembered that the current which they require
must be provided from a gas process (gas turbine), a steam process
(steam turbine) or by a combination of the two processes. The
efficiency for electricity generation is in this case at most 60%,
with modern technology. Furthermore, complicated circuit technology
is required in order to transmit the electrical power that is
generated to the electrical process machine or to the electric
motor. Furthermore, transmission losses in a system which has to
convert the electrical energy in a frequency converter from one
frequency range to another are likewise not negligible. The
transmission losses may, for example, be up to about 5%.
[0004] The electrical process machines or the electric motors drive
a compressor, for example, which can be used, for example, as a
compressor for a gas liquefaction installation. A gas liquefaction
installation such as this is known, for example, as an LNG
(liquefied natural gas) installation. In this case, natural gas is
cooled down to about -160.degree. C. In the process, the natural
gas becomes liquid and is (with a smaller volume) then also easier
to transport (normally in special transport apparatuses). In this
case, the object of the compressors is to compress working media,
normally working gases, which can absorb heat when subsequently
expanded. This heat is taken from the natural gas in the so-called
"cold box" of the LNG installation, and the natural gas is cooled
down in this way. The working medium or working gas is in this case
repeatedly compressed and expanded in a circuit.
[0005] The compressors are normally driven by the abovementioned
electric motor, thus resulting in considerable (transmission)
losses here since the power to be generated for the electric motor
is generated either by the gas process or the steam process since
the electric motor has to drive the compressor.
[0006] DE 21 02 770, U.S. Pat. No. 4,321,790 and WO 2005/024188 A2
each disclose combined gas and steam turbine installations which
are also intended for driving a compressor. The described
installations have significant efficiency losses, particularly
during fluctuating operation.
SUMMARY OF INVENTION
[0007] An object of the invention is to improve a compression
installation of the type mentioned initially, using simple means,
such that the efficiency is improved and hazardous emissions are
reduced at the same time.
[0008] According to the invention, the object is achieved by a
compression installation as claimed in the claims.
[0009] Gas turbines and steam turbines are advantageously used
separately to drive the at least one compressor directly, that is
to say without the interposition of an electrical process machine
or an electric motor. This leads to an efficiency improvement since
the power is transmitted both from the gas turbine and from the
steam turbine to the respectively associated at least one
compressor by direct means, thus avoiding conversion losses such as
those which occur in the generation of electrical power and the
driving of compressors by means of electrical process machines or
electric motors. However, at the same time, this also results in a
reduction in hazardous emissions such as CO.sub.2 emissions, which
is particularly advantageous with regard to commercial factors and
the acquisition of emission rights. This is because, when fewer
emissions are emitted, fewer emission rights must be acquired as
well.
[0010] This becomes even more advantageous if the exhaust gas from
the gas turbine can be used to fire a steam generating
installation, preferably a waste-heat boiler, which in turn
produces the steam required for the steam turbine. To this extent
it is expedient for the gas turbine and the steam turbine to be
combined with one another to form a gas and steam process. A
plurality of gas turbines may, of course, be connected to one
waste-heat boiler, in which case each gas turbine can also
respectively drive at least one compressor in an expedient manner.
The steam turbine may have a high-pressure part, a medium-pressure
part and/or a low-pressure part, with a steam turbine preferably
being provided that has all three pressure parts mentioned above.
In this case, by way of example, the steam is first of all passed
from the waste-heat boiler into the high-pressure part, from there
into the medium-pressure part and finally into the low-pressure
part, downstream from which the at least one compressor is
arranged. The arrangement of the compressor downstream from the
low-pressure part is, of course, not restricted to this
arrangement. It is possible, for example, for the compressor to be
arranged between the turbine elements or on the high-pressure
side.
[0011] In order to further improve efficiency, it is advantageous
if the at least one gas turbine and/or the steam turbine has or
have a plurality of respectively associated compressors which are
connected in series or in parallel with the at least one
compressor.
[0012] It is feasible for the at least one compressor to be
followed by a generator or an electrical process machine, or an
electric motor, in order, for example, to drive other machines.
[0013] It is advantageous if the at least one compressor which is
associated with the gas turbine, and the gas turbine, have a common
shaft, as a result of which the efficiency is further improved. Two
separate shaft parts of the respective component can, of course,
also be provided, which are connected to one another by suitable
means. Even when a plurality of compressors is connected in series,
one common shaft may be provided. The at least one compressor which
is associated with the steam turbine, and the steam turbine, may,
of course, also have a common shaft, in which case, of course,
separate shaft parts, as mentioned above, are also possible.
[0014] The respective compressor which is driven directly by the
gas turbine or the steam turbine may, for example, be used as
compressor in a gas liquefaction installation, for example an LNG
installation.
BRIEF DESCRIPTION OF THE DRAWING
[0015] Further advantageous refinements of the invention are
disclosed in the dependent claims and in the following FIGURE
description. In the FIGURE, the single
[0016] FIG. 1 shows an outline illustration of a compression
installation.
DETAILED DESCRIPTION OF INVENTION
[0017] FIG. 1 shows a compression installation 1 which has at least
one gas turbine 2 and one steam turbine 3. By way of example, three
gas turbines 2 are provided in the illustrated exemplary
embodiment.
[0018] The exhaust gases from the gas turbine 2 fire a steam
generating installation 4, which is in the form of a waste-heat
boiler. The steam which is generated in the steam generating
installation 4 is supplied to the steam turbine 3, and drives
it.
[0019] The illustrated gas turbines 2 have an associated
starter-helper motor generator (SHMG) 10. This starter-helper motor
generator (SHMG) 10 can be used both as helper motor (auxiliary
motor) and as a generator. The starter should be understood as
meaning that the motor--in a similar manner to that in the case of
a car engine--represents the starter, and ensures that the gas
turbine is brought to a rotation speed such that the gas turbine is
able to drive the shaft train on its own.
[0020] In the compression installation 1 illustrated by way of
example in FIG. 1, the gas process (gas turbine 2) and the steam
process (steam turbine 3) are combined to form a gas and steam
process.
[0021] According to the illustrated exemplary embodiment, the steam
turbine 3 has a high-pressure part 6, a medium-pressure part 7 and
a low-pressure part 8.
[0022] Both the at least one gas turbine 2 and the steam turbine 3
each have at least one associated compressor 9. The respective
compressors 9 are respectively connected directly to the at least
one gas turbine 2 and the steam turbine 3, with the at least one
compressor 9 which is associated with the steam turbine 3 being
arranged downstream from the low-pressure part 8 of the steam
turbine 3. The compressors 9 which are respectively associated with
the at least one gas turbine 2 and the steam turbine 3 are
respectively driven directly by the gas turbine 2 and the steam
turbine 3, without the interposition of an electrical process
machine or an electric motor, in which case, in fact, the
starter-helper motor generator (SHMG) 10 can be associated with the
gas turbines.
[0023] The exemplary embodiment shown in FIG. 1 does not show that
one or more compressors 9 may be followed by an electrical process
machine or an electric motor, and/or a generator. The positioning
of the compressor 9 in the shaft trains is, of course, not intended
to be restricted to the disclosed position, but can be made
variable.
[0024] It is possible for the at least one compressor 9 which is
associated with the gas turbine 2, and the at least one gas turbine
2, to have a common shaft (line 11). Furthermore, the at least one
compressor 9 which is associated with the steam turbine 3, or its
low-pressure part 8, and the steam turbine 3, or the low-pressure
part 8, may have a common shaft 12.
[0025] By way of example, the respective compressor 9 can compress
a working medium or a working gas such that the working medium can
absorb heat when it is subsequently expanded. For example, it is
feasible for the working medium which is compressed in the
respective compressor 9 to be supplied to a gas liquefaction
installation, for example, an LNG installation (liquefied natural
gas), in order to cool down natural gas.
* * * * *