U.S. patent application number 12/823774 was filed with the patent office on 2011-12-29 for compositions and method for use in plugging a well.
Invention is credited to Foy Streetman.
Application Number | 20110315381 12/823774 |
Document ID | / |
Family ID | 45351432 |
Filed Date | 2011-12-29 |



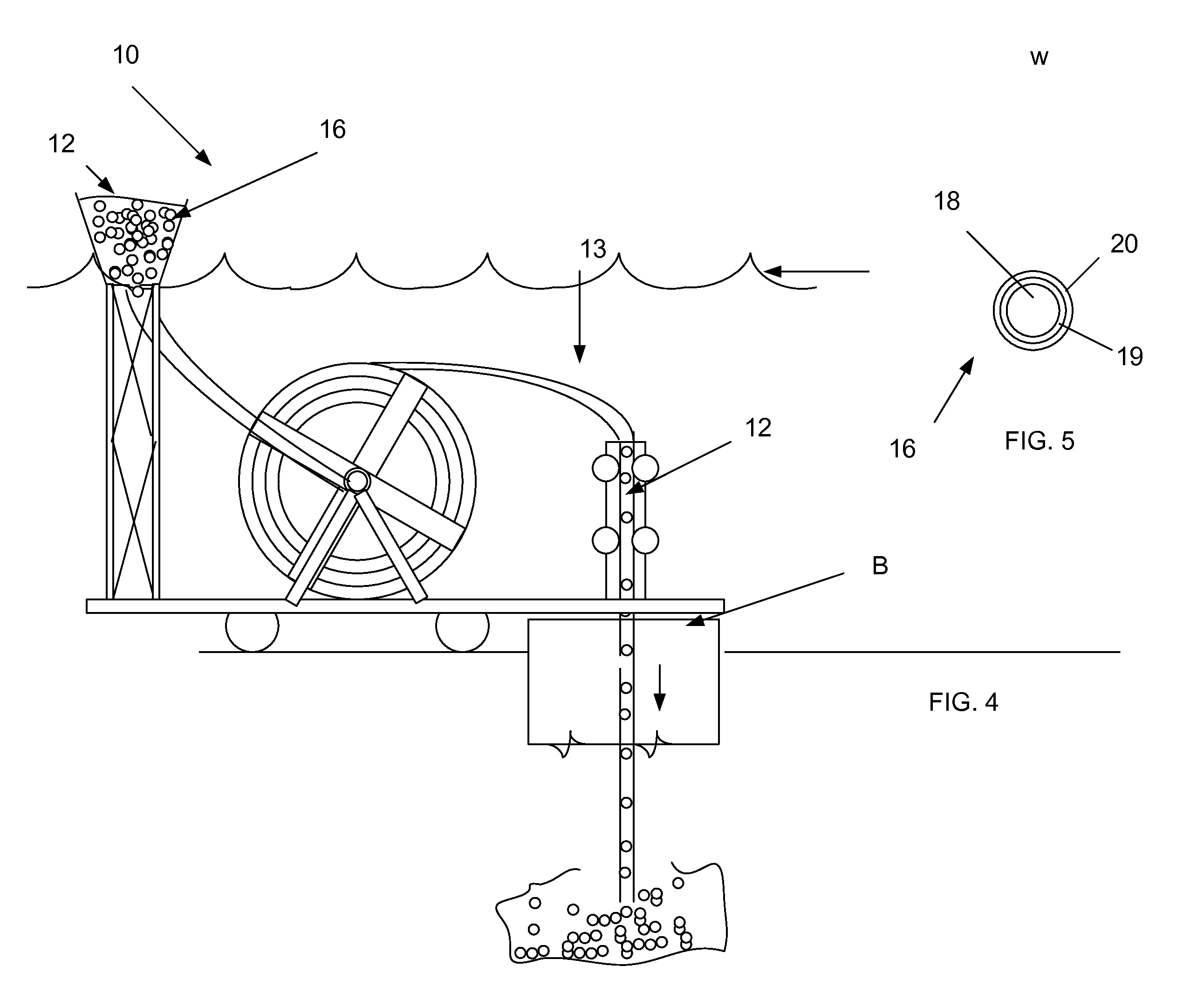

United States Patent
Application |
20110315381 |
Kind Code |
A1 |
Streetman; Foy |
December 29, 2011 |
COMPOSITIONS AND METHOD FOR USE IN PLUGGING A WELL
Abstract
A composition for use in plugging a well includes a mud having a
plurality of plugging members therein, wherein the plugging member
has a density more than about eight times that of water. A method
of providing the composition into the well is also provided.
Inventors: |
Streetman; Foy; (Chickasha,
OK) |
Family ID: |
45351432 |
Appl. No.: |
12/823774 |
Filed: |
June 25, 2010 |
Current U.S.
Class: |
166/292 ;
523/130 |
Current CPC
Class: |
E21B 33/138 20130101;
E21B 21/003 20130101 |
Class at
Publication: |
166/292 ;
523/130 |
International
Class: |
E21B 33/13 20060101
E21B033/13 |
Claims
1. A composition for use in plugging a well, which includes a mud
having a plurality of plugging members therein, wherein each said
plugging member has a density more than about eight times that of
water.
2. The composition of claim 1, wherein said plugging element
includes an inner core and an outer cover.
3. The composition of claim 2, wherein at least one of said inner
core and said outer cover includes a heavy material having a
density of more than about eight to twenty times that of water.
4. The composition of claim 3, wherein said outer cover includes a
drag reducing material.
5. The composition of claim 3, wherein said outer cover includes a
dissolvable material.
6. The composition of claim 3, wherein said plugging member
includes an expanding polymer.
7. A method for plugging a well, which includes the steps of: (a)
providing a composition including mud having a plurality of
plugging members therein, wherein the plugging member has a density
more has a density more than about eight times that of water; and
(b) providing said composition in sufficient opposing fluid flow to
fluid flow from an uncontrolled well flow such that said plugging
members are enabled to drop by virtue of gravity to a perforation
zone where said plugging members impede well flow from said
perforation zone.
8. The method of claim 7, wherein step (b) is further characterized
to include inserting tubing into said well and delivering said
composition through said tubing.
9. The method of claim 8, wherein said step (b) is further
characterized to provide said tubing in said well to a point
adjacent a perforation in said well.
10. The method of claim 7, wherein said step (a) is further
characterized to provide a stream of mud under pressure through a
conduit and introduce said plugging members into said conduit
through a valve chamber communicably connected to said conduit.
11. The method of claim 10, wherein said valve chamber is
characterized to be include a top valve and a lower valve and
wherein when said lower valve closed, top valve is open to fill
said chamber with said plugging members, then said top valve is
closed and said lower valve is opened to permit said plugging
members to mix with said mud.
12. The method of claim 7, wherein step (b) is further
characterized to include employing a blow out preventer over said
well and delivering said composition through said blow out
preventer.
13. The method of claim 7, wherein said plugging member includes an
inner core and an outer cover.
14. The method of claim 13, wherein at least one of said inner core
and said outer cover includes a heavy material having a density of
more than about eight times that of water.
15. The method of claim 14, wherein said outer cover includes a
drag reducing material.
16. The method of claim 13, wherein said outer cover includes a
dissolvable material.
17. The method of claim 13, wherein said plugging member includes
an expanding polymer.
18. A system for plugging a well, which includes: a tank having a
mud therein; a conduit connected to said tank; a pump operably
connected to cause mud to flow through said conduit; a chamber
operably connected to said conduit and including a top valve and a
lower valve and wherein when said lower valve closed, said top
valve can be open to filled said chamber with plugging members, and
when said top valve is closed said lower valve can be opened to
permit said plugging members to mix with said mud.
19. The system of claim 18, wherein said conduit is operably
disposed to terminate adjacent said a perforation zone of the well.
Description
BACKGROUND OF INVENTION
[0001] 1. Field of Invention
[0002] The present invention relates in general to oil and gas well
remediation. More particularly, the invention relates to
compositions and method for use in plugging a well.
[0003] 2. Prior Art
[0004] In drilling a well, there is created a connection to the oil
and/or gas reservoir and tubing is installed between the reservoir
and the surface. The outer steel casing requires a gas tight seal
between the reservoir and the surface wherein an annulus (the gap
between the casing and the rock/formation) is typically subjected a
cementing (or grouting) operation. This treatment is normally
referred to as Primary Cementing. The main aspects of primary
cementing are to isolate flow between different reservoirs, to
withstand the external and internal pressures acting upon the well
by offering structural reinforcement and to prevent corrosion of
the steel casing by chemically aggressive reservoir fluids.
[0005] A poor cementing job can result in migration of reservoir
fluids, even leading to gas migration through micro-annuli in the
well which not only reduces the cost-effectiveness of the well but
may cause a "blow out" resulting in considerable damage. Although
repair jobs ("secondary cementing") are possible (in essence
forcing more cement into the cracks and micro-annuli) they are
costly and do not always lead to the desired results.
[0006] A "blowout" refers to the uncontrolled flow of well fluids
from a well and "fluids" refer to both liquids and gases. Recently,
offshore drilling operations have resulted in a major blow out.
[0007] Production tubing string includes a conduit in the well
structure which contains petroleum fluids under pressure which,
under conditions of a blowout, are uncontrollably escaping from
some point along the vertical development of the conduit.
[0008] In such blow outs, oil leaks into rock formations outside
the well. If the rock is porous, the oil would eventually bubble up
from different spots in the ocean floor. It's important to know how
high up in the well any breach or crack is. The higher it is, the
worse the scenario because the closer it is to potentially porous
rock and the ocean.
[0009] The well leak could be significantly worse than what's been
measured from the end of the pipe. If you only measure the flow
coming out of the end of the well bore, you're missing what is
spurting from the break in the pipe. The clogging of the break is
imperative in order to plug the well and minimize the ecological
disaster.
[0010] In a small crack or break, a relatively small volume of
cement (typically in the order of 100 m) is used to place the plug,
its quality needs to be sufficient as it will serve as a seal for a
very long time. However, in underwater operations, it is difficult
to provide opposing fluid flow and plugging material.
[0011] The customary abandonment operation is very costly,
especially in an off-shore environment, since it typically requires
the use of a workover or drilling rig. It would be very beneficial
if methods were available which could lead to abandonment of wells
without the necessity to remove the production tubing.
[0012] One of the major drawbacks of using traditional cementing
materials such as Class G Cement (e.g. OPC: Ordinary Portland
Cement) in plugging is that such materials cannot achieve a gas
tight seal. In the search for effective cementing materials,
attention has to be paid to the material should be gas-tight (i.e.
withstand a predetermined bar per m), it should have a controllable
setting time so that a range of temperatures and well depths (each
requiring different conditions) can be coped with, it should be
thermally stable up to a predetermined temperature as well as being
chemically stable against reservoir fluids for a very long period
of time and its properties should be such that pumping through
existing oil field equipment can be carried out without many
problems.
[0013] A wide range of non-cement plugging agents have been
attempted which include resins, golf balls, tire bits, for example.
However, such materials have not met with great success.
Compositions consisting essentially of a mixture of slurry of
hydraulic cement (such as Portland cement) and rubber latex have
been used. The use of putty ("mastic") has been disclosed for
producing joints separating zones in wells.
[0014] Still others provide a method for controlling well blow
outs, especially when those located in a body of water and the well
cannot be conventionally controlled using drilling mud. The
environmental hazards, as well as the hazards to personnel, of well
blow outs have become increasingly important, especially where
those blow outs have taken place in ecologically sensitive areas,
such as the coast of the United States. None of the prior methods
proves to be a universal application, and each poses some economic
or technological drawback.
[0015] Some disclose methods and apparatus for producing deep
boreholes in which the borehole is filled at least partially with a
substance which remains in the liquid state and has a density
greater than the mean density of the ground strata being drilled.
Thus, any infiltrations from the formation into the borehole, as
well as drilling debris, naturally move upward to the free surface
of the liquid substance filling the borehole.
[0016] One prior method employs a so called "hot tap" which is a
connection of a fluid-conducting conduit to a second conduit
without the need for decreasing the pressure of the contents of the
second conduit and without any substantial pressure loss or loss of
the contents of the second conduit through the point of connection
with the first conduit. U.S. Pat. No. 3,647,000 employs a method
for capping the uncontrolled flow of oil and gas from petroleum
wells located in a body of water. The method involves the tapping
of a window or access opening into the well casing or tubing
through which the well fluids are flowing below the surface of the
well, crimping the casing or tubing above the point of the tap and
injecting solid plugging bodies which lodge within the constriction
in the production tubing string and form a plug blocking the flow.
Heavy non-combustible mud is then pumped into the production tubing
through the tapped-in access line until the weight of the injected
mud overcomes the formation pressure, thus terminating well flow.
Neither the nature of the plugging bodies nor the nature of the
heavy mud is specified.
[0017] U.S. Pat. No. 3,926,256 discloses a method for preventing
blow outs in offshore wells. There is an apparatus in which pins
extend into the passage through which oil or gas are flowing, the
uncontrolled flow being stopped by the injection into the
pin-containing region of a sealer material such as balls of rubber
or fiber, natural or synthetic, Fiberglas, aluminum, shredded
Teflon, and the like, followed by a mastic which acts as the
sealing agent.
[0018] U.S. Pat. No. 4,133,383 discloses a method for terminating
formation fluid blow outs by introducing into the formation a low
viscosity fluid which has the property of becoming highly viscous
under the influence of heat.
[0019] It is also known to apply dry ice or liquid nitrogen to the
exterior of the string through which the well is blowing out and
thereby freeze the blowing fluids to form a plug in the string. In
another development, the casing string through which the Ixtox I
well in the Gulf of Mexico was blowing out during the summer of
1979 was treated with some success in an effort to cut down the
flow by pumping in iron and lead balls.
[0020] A major problem with high pressure deep wells is that the
mud and plugging components are not effective for various reasons.
For example, the plugging components cannot descend to a depth
necessary to perform their job in the face of the up-flow. Another
problem is that the material breaks down prior to reaching the
break or desired zone.
[0021] The present invention overcomes the above problems. The
present invention provides for repair and abandonment operations in
the face of high pressure deep wells.
SUMMARY OF INVENTION
[0022] It is an object to plug a well blow out.
[0023] It is another object to provide a composition for use in
plugging a well.
[0024] Accordingly, the instant invention is directed to a
composition and method for use in plugging a well. The invention
provides a heavy metal, such as lead ball or other suitable
geometric shape, which is covered by a highly resilient coating,
such as steel, polymer, or ceramic, which can survive the sheer
force as they fall against a fairly strong flowing stream so they
can aggregate at the bottom of the well or pack into the break.
Over time, a sufficient number of balls delivered would fill up
over the perforations thereby plug the ability of the formations
pressure to push production upward. Thus, this would stop the
flow.
[0025] Such heavy metals and members can include those that can
have the ability to expand and adhere to surfaces they come into
contact with that can be used in conjunction with the balls either
as a coating or embedded into them. Further, the plugging
composition can be equipped with ability to become more stable once
they arrive at the break or bottom of the wellbore. Preferred
geometric designs can include round and or cone shaped as a method
to reduce the drag or tendency of the flow to lift is a very
important feature as well. In the instant invention, a hopper with
a valve can open to deliver the composition which connected
downstream of a pump to the pipe going into the wellbore. The
composition drilling mud can be pumped and the drilling mud will
carry these plugging members (e.g., balls) and keep them suspended
in the thick fluid. The composition is configured as a mechanism to
deliver these balls to the site with sufficient ability to permit
the balls to descend downward. The size and shape and make-up of
the balls and carrier mud fluid are factors which provide necessary
blocking or plugging effect.
[0026] With a direct line "unobstructed" open hole into a well, a
string of coil tubing or small diameter conventional tubing can be
injected into the existing tubing or open wellbore in a sight line.
Optionally, the use of a blowout preventer can be employed to carry
out delivery. The small string tubing would be used to pump down
the plugging members (balls or cones) into the well near the
bottom. A method can be provided to deliver of the plugging members
into a hopper that is connected to the coil tubing just below the
mud pump whereby these balls or comes would be injected into the
stream of mud being pumped down.
BRIEF DESCRIPTION OF THE DRAWINGS
[0027] FIG. 1 is an elevation partially broken away of an exemplary
well installation employed in wells located in water;
[0028] FIG. 2 is a partial elevation partially broken away
illustrating a portion of the well structure of FIG. 1 and the
implementation of one embodiment the invention;
[0029] FIG. 3 illustrates a plugging element of one embodiment of
the invention;
[0030] FIG. 4 is a partial elevation partially broken away
illustrating a portion of the well structure of FIG. 1 and the
implementation of another embodiment the invention;
[0031] FIG. 5 illustrates a plugging element of another embodiment
of the invention; and
[0032] FIG. 6 is a schematic illustrating an embodiment of the
invention.
DESCRIPTION OF THE PREFERRED EMBODIMENT
[0033] Referring now to the drawings, the composition and method of
present invention is generally designated by the numeral 10 and is
for use with deep high pressure wells located in water. It will be
understood however, that the present invention can be employed with
wells located on land.
[0034] A typical well structure is designated by the numeral 4 is
illustrated within a body of water indicated generally at W. The
well structure 4 extends above the top of the surface of the water
W and normally terminates at a well head (not shown) which includes
regulating and control equipment and fittings for conducting the
well fluids to a collection point.
[0035] The structure 4 includes an external conductor pipe 30 which
extends from above the surface of the water W to a point somewhat
below the surface of the water bed indicated generally at S.
Typical intermediate casing string 32 and a producing casing string
34 are carried concentrically within the conductor pipe 30 and
extend to different subterranean points within the well bore.
Concrete 36 is illustrated within the annular space between the
conductor pipe 30 and intermediate casing string 32. A production
tubing string 38 extends through the center of the well structure 4
and is normally the principle conductor employed for conveying the
petroleum fluids from the subterranean formation to the wellhead.
Under normal conditions, with a well structure such as illustrated
in FIG. 1, petroleum fluids in the formation are conducted through
the production tubing string 38. The intermediate and production
casing strings 32 and 34 normally contain little or no pressure and
effluent flow is limited to the production tubing string 38.
[0036] Pressure estimates for deep offshore wells range from 3500
psi to 9500+ps or from 20 MPa to 65 MPa. It is not uncommon for the
well bore diameter to be large for example a foot in diameter. A
blowout requires immediate remediation.
[0037] Plugging the hole can include the use of coiled tubing 13
wherein coiled tubing is run into the hole and pumping the
composition 12 with plugging members 16 enable killing fluid flow.
Coiled tubing can be a conventional continuous length of low-alloy
carbon-steel tubing that can be spooled on a reel and deployed into
a wellbore B for delivering composition 12. One method is to inject
the tubing 13 to near the perforations P. However, if this cannot
be achieved due to debris in the wellbore B, the tubing 13 can be
injected to a depth where it is possible and by creating a large
flow of mud 15 with plugging members 16, the well flow will be
reduced allowing the plugging members 16 to fall from such point to
the bottom of the well.
[0038] Optionally, a blowout preventer 14 which includes a manifold
communicably connected to receive the composition 12 which includes
plugging members 16 of the instant invention can be provided. The
composition 12 includes noncombustible high-density well control
material or "mud" 15 and the plugging members 16, As seen in
section in FIGS. 3 and 5, the plugging members 16 can include a
core 18, such as heavy metal with one or more coating 19 and 20
which can be a friction reduced and or durable coating, such as a
polymer, steel, or ceramic coating.
Sample Density of materials are as follows:
TABLE-US-00001 metal g/cm{circumflex over ( )}3 lb/in{circumflex
over ( )}3 lb/ft{circumflex over ( )}3 lb/gal water 1.00 0.036 62
8.35 aluminum 2.70 0.098 169 22.53 zinc 7.13 0.258 445 59.50 iron
7.87 0.284 491 65.68 copper 8.96 0.324 559 74.78 silver 10.49 0.379
655 87.54 lead 11.36 0.410 709 94.80 mercury 13.55 0.490 846 113.08
gold 19.32 0.698 1206 161.23
[0039] Some material is cost prohibitive in addition to being
malleable while others are less costly, yet malleable and toxic
such as lead and mercury. In order to use these materials, the
material is to be coated with a sufficient coating to permit use
under the rough forces within the well bore, i.e., be pushed down
by the drilling fluids using pump 17, e.g., 20,000 hp.
[0040] To this end, a sufficiently sized plugging member 16 can be
formed of lead for example and then coated with a suitable coating.
One coating for use with the invention can include Molybdenum
Disulfide (MoS2) combined with one of nylon (with the trade name
Nylatron), Teflon, and Vespel. Another self-lubricating composite
coating for high-temperature application includes molybdenum
disulfide and titanium nitride formed by chemical vapor deposition.
Other silicon based ceramics including silicon nitride and silicon
carbide can be used their high temperature strength and relative
corrosion resistance.
[0041] The concept is to provide a sufficient resistant force with
the blowout preventer to permit the coated pellets to drop to the
well blocking point. The coating 19 and/or 20 permits the normally
mechanically weak, but heavy material to survive a mile long
journey under very high pressure in 1200 gpm within a rigid pipe.
The coating 19 or 20 can be a drag reducing material such as a
hydrophobic coating, such as Wearlon Super F-6M.TM. available from
Industrial Coating Systems in China. It is also contemplated that
one of the coating 19 or 20 can include a well treating agent.
Optionally the coating 19 or 20 can include a dissolvable material,
such as a soluble polymer, which can house the heavy substance or
adhesive substance such that once reaching the bottom of the well
or perforation P, it can dissolve and permit the heavy material to
block the perforation P. Still another option is to provide coating
with water-activated urethanes which expand, i.e., as water absorbs
into the urethane polymers.
[0042] As generally seen in FIG. 6, it is envisioned that a mud 15
can be pumped via a pump 17 using coiled tubing 13. The mud 15 can
include drilling fluids can be water-based muds (which can be
dispersed and non-dispersed), non-aqueous muds, usually called
oil-based mud, and gaseous drilling fluid, in which a wide range of
gases can be used or synthetic mud.
[0043] Intersecting the tubing 13 is a chamber 29 which includes a
top valve 21A and a lower valve 21 B. With valve 21B closed, Valve
21A is open to fill the chamber 29. Then with valve 21A closed,
valve 21B can be open to permit the plugging members 16 to mix with
the mud 15. The plugging members 16 can preferably be formed in a
variety of sizes to permit restrictions to form and plugging of the
well.
[0044] Formation F pushes into well at perforations P where
production is coming into well bore B. The plugging members 16 by
virtue of their weight and coating structure are enabled to flow to
a point whereby they can form a restriction in the well, i.e.,
enable them to fall into the bottom of the well adjacent the
perforation P and can aid in blocking the flow.
[0045] In another aspect of the present invention, upon occurrence
of a blowout, blowout preventer 14 can be operably disposed over
well bore B. In most wells located in bodies of water in the ocean
or in waters such as the Gulf of Mexico, the vertical distance
between the water surface and the bed S provides ample working room
and overhead protection.
[0046] Referring to FIG. 2, once so positioned, the blowout
preventer 14 is actuated to cause the flow of mud composition 12
which includes plugging members 16 which by virtue of their weight
and coating structure are enabled to flow to a point whereby they
can form a restriction in the well. These plugging members 16
migrate through a fluid current to form the restriction.
[0047] When the plug P has terminated or substantially terminated,
conventional mud can then introduced into the tubing string 38 at a
pressure which is sufficient to overcome the formation pressure and
displace the petroleum fluids from the production tubing string 38.
The mud 15 flows down hole into the production string 38 until the
weight of the inserted mud is sufficient to overcome the formation
pressure. Thereafter, the well bore B may be closed and the well
may be abandoned or repaired as desired.
[0048] It will be appreciated that the method of the present
invention encompasses the steps of inserting plugging materials of
the instant invention into a conduit at a point whereby there is a
sufficient opposing current created to permit the free fall of the
plugging members 16 causing a plug to form internally of the
conduit or at the formation zone F. The particular apparatus
employed in forming the restriction or in forming the upstream
access point for introduction of plugging materials is conventional
and improved equipment and techniques for effecting these steps is
anticipated and may form the subject matter of future patent
applications.
[0049] It will be understood that other suitable means may be
employed for supplying the plugging members 16 and mud composition
12. If desired, however, other suitable subsurface equipment may be
employed for the same purpose.
[0050] The plugging members 16 are denser than the petroleum
effluents. It will be understood, that the method of the present
invention is readily capable of use with plugging members 16 of a
suitable density provided with a coating 19 and or 20 which is
preferably non-toxic and able to withstand the rigors of the harsh
well environment. The flow of composition 12 must be strong enough
to permit the plugging members 16 to reach the desired zone or
break point.
[0051] The foregoing disclosure and description of the invention is
illustrative and explanatory thereof and various changes in the
procedures as well as in the details of the described method may be
made within the scope of the appended claims without departing from
the spirit of the invention.
* * * * *