U.S. patent application number 12/865085 was filed with the patent office on 2010-12-30 for expander-integrated compressor and refrigeration cycle apparatus using the same.
This patent application is currently assigned to PANASONIC CORPORATION. Invention is credited to Hiroshi Hasegawa, Yasufumi Takahashi.
Application Number | 20100326124 12/865085 |
Document ID | / |
Family ID | 40912523 |
Filed Date | 2010-12-30 |





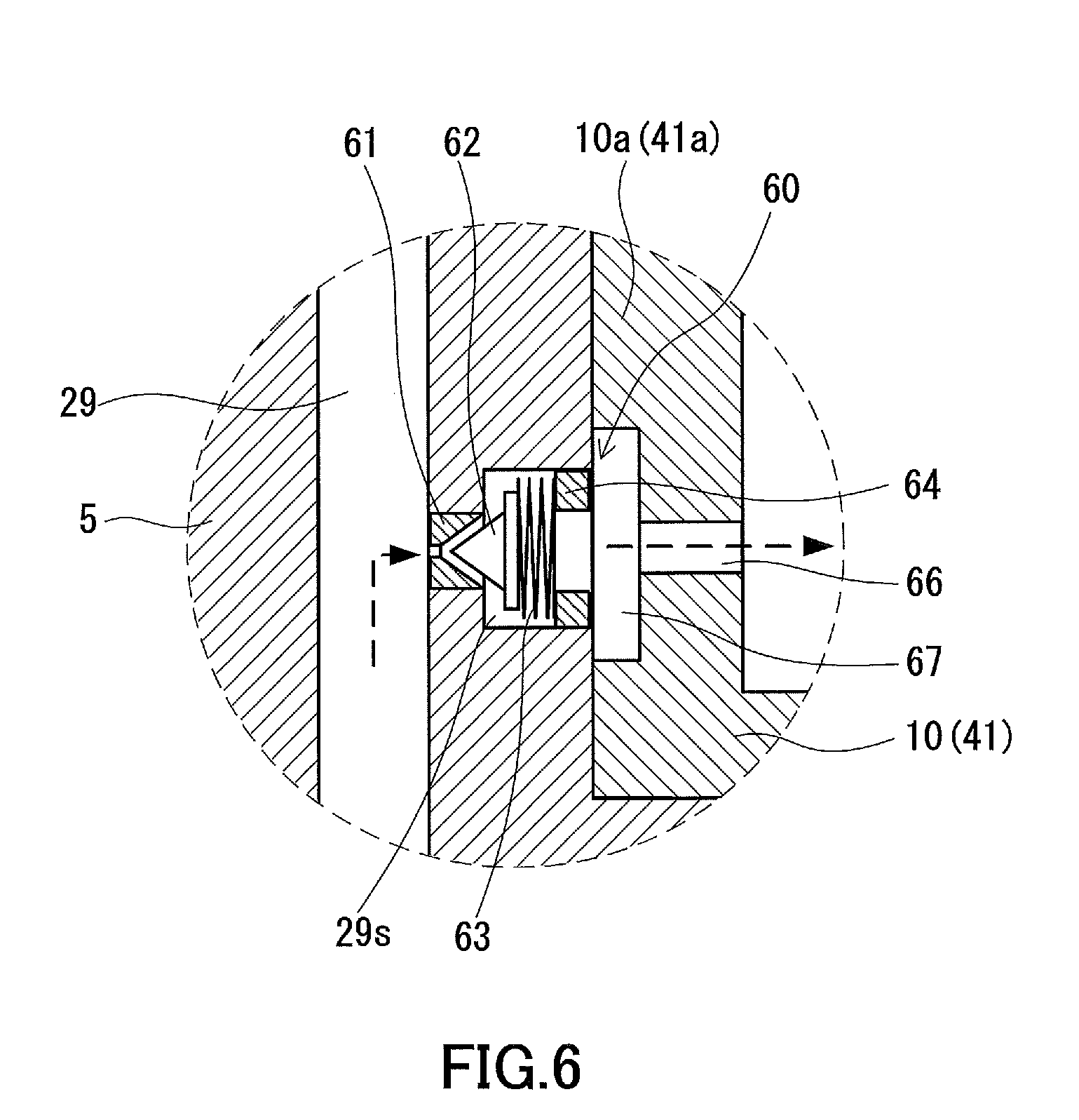





United States Patent
Application |
20100326124 |
Kind Code |
A1 |
Takahashi; Yasufumi ; et
al. |
December 30, 2010 |
EXPANDER-INTEGRATED COMPRESSOR AND REFRIGERATION CYCLE APPARATUS
USING THE SAME
Abstract
An expander-integrated compressor (100A) has a compression
mechanism (2), an expansion mechanism (3), a shaft (5), an oil pump
(6), and an oil supply amount regulating mechanism (30). The
compression mechanism (2) and the expansion mechanism (3) are
coupled to each other by the shaft (5) so that mechanical power can
be transmitted. The compression mechanism (2) and the expansion
mechanism (3) are arrayed vertically in the closed casing (1). The
oil pump (6) is provided at a lower portion of the shaft (5). An
oil supply passage (29) is formed in the shaft (5) so as to extend
in the axis direction. The oil supply amount regulating mechanism
30 controls the amount of the oil to be supplied by the oil pump
(6) to the expansion mechanism (3).
Inventors: |
Takahashi; Yasufumi; (Osaka,
JP) ; Hasegawa; Hiroshi; (Osaka, JP) |
Correspondence
Address: |
HAMRE, SCHUMANN, MUELLER & LARSON P.C.
P.O. BOX 2902
MINNEAPOLIS
MN
55402-0902
US
|
Assignee: |
PANASONIC CORPORATION
Kadoma-shi, Osaka
JP
|
Family ID: |
40912523 |
Appl. No.: |
12/865085 |
Filed: |
January 27, 2009 |
PCT Filed: |
January 27, 2009 |
PCT NO: |
PCT/JP2009/000295 |
371 Date: |
July 28, 2010 |
Current U.S.
Class: |
62/468 ;
62/498 |
Current CPC
Class: |
F04C 23/003 20130101;
F04C 23/008 20130101; F04C 18/356 20130101; F04C 29/025 20130101;
F04C 29/028 20130101 |
Class at
Publication: |
62/468 ;
62/498 |
International
Class: |
F25B 43/00 20060101
F25B043/00; F25B 1/00 20060101 F25B001/00 |
Foreign Application Data
Date |
Code |
Application Number |
Jan 29, 2008 |
JP |
2008-018354 |
Claims
1. An expander-integrated compressor comprising: a rotary-type
compression mechanism for compressing a working fluid; a
rotary-type expansion mechanism for recovering mechanical power
from the working fluid; a shaft coupling the rotary-type
compression mechanism and the rotary-type expansion mechanism so as
to transmit the mechanical power recovered by the rotary-type
expansion mechanism to the rotary-type compression mechanism; a
closed casing accommodating the rotary-type compression mechanism,
the rotary-type expansion mechanism, and the shaft in such a manner
that the rotary-type compression mechanism and the rotary-type
expansion mechanism are arrayed vertically, the closed casing
having a bottom portion utilized as an oil reservoir and an
interior space to be filled with the working fluid having been
compressed; an oil pump provided at a lower portion of the shaft;
an oil supply passage for supplying oil in the oil reservoir to the
rotary-type compression mechanism or the rotary-type expansion
mechanism located in an upper part of the closed casing by the oil
pump, the oil supply passage being formed in the shaft so as to
extend in an axis direction; and an oil supply amount regulating
mechanism, disposed below the rotary-type compression mechanism or
the rotary-type expansion mechanism located in the upper part of
the closed casing and disposed above the rotary-type compression
mechanism or the rotary-type expansion mechanism located in a lower
part of the closed casing, for regulating the amount of the oil to
be supplied through the oil supply passage to the rotary-type
compression mechanism or the rotary-type expansion mechanism
located in the upper part of the closed casing, and wherein: a
branch passage is formed in the shaft, the branch passage branching
in a radial direction from the oil supply passage and opening in an
outer circumferential surface of the shaft; and the oil supply
amount regulating mechanism is provided in the branch passage or
exteriorly of the shaft so that the oil is guided to the interior
space of the closed casing through the branch passage.
2. The expander-integrated compressor according to claim 1, wherein
the oil supplied through the oil supply passage does not flow out
over the rotary-type compression mechanism or the rotary-type
expansion mechanism located in the upper part of the closed
casing.
3. The expander-integrated compressor according to claim 1, wherein
the oil supply passage does not open in an upper end face of the
shaft.
4. The expander-integrated compressor according to claim 1, wherein
the oil supply amount regulating mechanism includes a structure for
preventing the amount of the oil to be supplied to the rotary-type
compression mechanism or the rotary-type expansion mechanism
through the oil supply passage, from increasing correspondingly to
an increase of a rotation speed of the shaft.
5. The expander-integrated compressor according to claim 1, wherein
the oil supply amount regulating mechanism includes an orifice, a
needle valve, or a relief valve.
6. The expander-integrated compressor according to claim 1, further
comprising: a motor, disposed between the rotary-type compression
mechanism and the rotary-type expansion mechanism, for driving the
shaft; and wherein the branch passage is formed in a portion of the
shaft that is between the motor and the rotary-type compression
mechanism or the rotary-type expansion mechanism located in the
lower part of the closed casing.
7. The expander-integrated compressor according to claim 1,
wherein: the rotary-type compression mechanism or the rotary-type
expansion mechanism includes a bearing portion for supporting the
shaft and covering the outer circumferential surface of the shaft
at a location where the branch passage is formed; (i) a chamber in
which the branch passage opens and (ii) an oil discharge passage
for connecting the chamber and the interior space of the closed
casing are formed in the bearing portion; and the oil is guided
from the oil supply passage to the interior space of the closed
casing through the branch passage, the chamber, and the oil
discharge passage.
8. The expander-integrated compressor according to claim 1, wherein
the oil supply amount regulating mechanism includes a valve seat, a
valve body disposed so as to face the valve seat, and a spring for
adjusting a gap between the valve seat and the valve body by
expanding and contracting according to a pressure change of the oil
in the oil supply passage.
9. The expander-integrated compressor according to claim 8, wherein
the shape of the valve body is spherical.
10. The expander-integrated compressor according to claim 7,
wherein the oil supply amount regulating mechanism is provided in
the chamber, in the oil discharge passage, or at an outlet of the
oil discharge passage.
11. The expander-integrated compressor according to claim 1,
wherein the oil pump is a velocity type pump.
12. A refrigeration cycle apparatus comprising: an
expander-integrated compressor according to claim 1; a radiator for
cooling the refrigerant compressed by the rotary-type compression
mechanism of the expander-integrated compressor; and an evaporator
for evaporating the refrigerant expanded by the rotary-type
expansion mechanism of the expander-integrated compressor.
13. (canceled)
Description
TECHNICAL FIELD
[0001] The present invention relates to an expander-integrated
compressor and a refrigeration cycle apparatus using the same.
BACKGROUND ART
[0002] Recently, as natural resource issues and global warming
issues have become ever more serious, much research and development
efforts have been invested in reducing energy consumption of
refrigeration cycle apparatuses, which are used for water heaters
and air conditioners. For example, conventional refrigeration cycle
apparatuses have a mechanism of expanding the refrigerant using an
expansion valve, but there is an attempt to employ a positive
displacement expander in place of the expansion valve in order to
recover the energy of expansion of the refrigerant and utilize it
as auxiliary power for the compressor. By the recovery and
utilization of the expansion energy of the refrigerant, it can be
expected to achieve about a 20% reduction in power usage
theoretically, or about a 10% reduction even with an actual
apparatus. As a fluid machine that achieves such an attempt,
development of a fluid machine (expander-integrated compressor),
such as disclosed in JP 2005-299632 A, is underway at a rapid
pace.
[0003] FIG. 11 is a vertical cross-sectional view illustrating a
typical expander-integrated compressor. An expander-integrated
compressor 200 has a two-stage rotary type compression mechanism
121, a motor 122, a two-stage rotary type expansion mechanism 123,
and a closed casing 120 that accommodates them. The compression
mechanism 121, the motor 122, and the expansion mechanism 123 are
coupled to each other by a shaft 124.
[0004] A bottom part of the closed casing 120 forms an oil
reservoir 125 for holding oil (refrigeration oil). An oil pump 126
is fitted to a lower end portion of the shaft 124 in order to pump
up the oil held in the oil reservoir 125. The oil pumped up by the
oil pump 126 is supplied to the compression mechanism 121 and the
expansion mechanism 123 via an oil supply passage 127 formed in the
shaft 124. Thereby, lubricity and sealing of the sliding parts of
the compression mechanism 121 and the expansion mechanism 123 are
ensured.
[0005] An oil return pipe 128 is disposed in an upper part of the
expansion mechanism 123. One end of the oil return pipe 128
communicates with the oil supply passage 127 formed in the shaft
124, while the other end opens below the expansion mechanism 123.
Generally, the oil is supplied excessively in order to ensure the
reliability of the expansion mechanism 123. The excess oil is
returned via the oil return pipe 128 to the oil reservoir 125.
[0006] By disposing both the compression mechanism 121 and the
expansion mechanism 123 in the closed casing 120, there is an
advantage in being able to lubricate both the compression mechanism
121 and the expansion mechanism 123 by the oil held in the oil
reservoir 125.
DISCLOSURE OF THE INVENTION
[0007] In the expander-integrated compressor 200 shown in FIG. 11,
the oil pumped up from the oil reservoir 125 is heated by the
compression mechanism 121 because it passes through the compression
mechanism 121 that is at a high temperature. The oil heated by the
compression mechanism 121 is heated further by the motor 122, and
it reaches the expansion mechanism 123. The oil having reached the
expansion mechanism 123 is cooled by the expansion mechanism 123
that is at a low temperature, and is thereafter discharged below
the expansion mechanism 123 via the oil return pipe 128. The oil
discharged from the expansion mechanism 123 and the oil return pipe
128 is heated again when passing along a side face of the motor 122
and is also heated when passing along a side face of the
compression mechanism 121. The oil then returns to the oil
reservoir 125 of the closed casing 120.
[0008] As described above, the oil circulation between the
compression mechanism 121 and the expansion mechanism 123 causes
heat transfer from the compression mechanism 121 to the expansion
mechanism 123. Such heat transfer lowers the temperature of the
refrigerant discharged from the compression mechanism 121, and
elevates the temperature of the refrigerant discharged from the
expansion mechanism 123. In terms of air conditioners, this means a
decrease of indoor heating capacity during heating, or a decrease
of indoor cooling capacity during cooling.
[0009] It is important to reduce the above-described heat transfer
as much as possible in order to improve cycle efficiency. In
particular, when the system operates at high output power and the
rotation speed of the expander-integrated compressor is
correspondingly high, the amount of the oil supplied by the oil
pump 126, and accordingly the quantity of heat transferred by the
oil, is great.
[0010] The present invention has been accomplished in view of the
foregoing circumstances, and it is an object of the invention to
reduce the heat transfer from the compression mechanism to the
expansion mechanism.
[0011] Accordingly, the present invention provides an
expander-integrated compressor including:
[0012] a compression mechanism for compressing a working fluid;
[0013] an expansion mechanism for recovering mechanical power from
the working fluid;
[0014] a shaft coupling the compression mechanism and the expansion
mechanism so as to transmit the mechanical power recovered by the
expansion mechanism to the compression mechanism;
[0015] a closed casing accommodating the compression mechanism, the
expansion mechanism, and the shaft in such a manner that the
compression mechanism and the expansion mechanism are arrayed
vertically, the closed casing having a bottom portion utilized as
an oil reservoir and an interior space to be filled with the
working fluid having been compressed;
[0016] an oil pump provided at a lower portion of the shaft;
and
[0017] an oil supply passage for supplying oil in the oil reservoir
to the compression mechanism or the expansion mechanism located in
an upper part of the closed casing by the oil pump, the oil supply
passage being formed in the shaft so as to extend in an axis
direction; and
[0018] an oil supply amount regulating mechanism, disposed below
the compression mechanism or the expansion mechanism located in the
upper part of the closed casing, for regulating the amount of the
oil to be supplied to the compression mechanism or the expansion
mechanism located in the upper part of the closed casing through
the oil supply passage.
[0019] In another aspect, the present invention provides a
refrigeration cycle apparatus including:
[0020] an expander-integrated compressor according to the present
invention;
[0021] a radiator for cooling the refrigerant compressed by the
compression mechanism of the expander-integrated compressor;
and
[0022] an evaporator for evaporating refrigerant expanded by the
expansion mechanism of the expander-integrated compressor.
[0023] In yet another aspect, the present invention provides an
expander-integrated compressor including:
[0024] a compression mechanism for compressing a working fluid;
[0025] an expansion mechanism for recovering mechanical power from
the working fluid;
[0026] a shaft coupling the compression mechanism and the expansion
mechanism so as to transmit the mechanical power recovered by the
expansion mechanism to the compression mechanism;
[0027] a closed casing accommodating the compression mechanism, the
expansion mechanism, and the shaft, the closed casing having a
bottom portion utilized as an oil reservoir and an interior space
to be filled with the working fluid having been compressed;
[0028] an oil pump provided at an end portion of the shaft;
[0029] an oil supply passage for supplying oil in the oil reservoir
by the oil pump to the compression mechanism or the expansion
mechanism that is located in a far side, viewed from the oil pump,
with respect to an axis direction of the shaft, the oil supply
passage being formed in the shaft so as to extend in the axis
direction; and
[0030] an oil supply amount regulating mechanism for regulating the
amount of the oil to be supplied to the compression mechanism or
the expansion mechanism through the oil supply passage.
[0031] The above-described expander-integrated compressor of the
present invention is provided with the oil supply amount regulating
mechanism. Therefore, an appropriate amount of oil can be supplied
to the compression mechanism or the expansion mechanism regardless
of the rotation speed of the shaft. As a result, it is possible to
reduce the heat transfer from the compression mechanism to the
expansion mechanism that results from the oil circulation.
BRIEF DESCRIPTION OF THE DRAWINGS
[0032] FIG. 1 is a vertical cross-sectional view illustrating an
expander-integrated compressor according to a first embodiment of
the present invention.
[0033] FIG. 2A is a horizontal cross-sectional view taken along
line IIA-IIA of the expansion mechanism.
[0034] FIG. 2B is a horizontal cross-sectional view taken along
line IIB-IIB of an expansion mechanism.
[0035] FIG. 3 is a partially enlarged view of FIG. 1.
[0036] FIG. 4 is a view illustrating a modified embodiment of an
oil supply amount regulating mechanism.
[0037] FIG. 5 is a vertical cross-sectional view illustrating an
expander-integrated compressor according to a second embodiment of
the present invention.
[0038] FIG. 6 is a partially enlarged view of FIG. 5.
[0039] FIG. 7 is a vertical cross-sectional view illustrating an
expander-integrated compressor according to a third embodiment of
the present invention.
[0040] FIG. 8 is a partially enlarged view of FIG. 7.
[0041] FIG. 9 is a vertical cross-sectional view illustrating an
expander-integrated compressor according to a fourth embodiment of
the present invention.
[0042] FIG. 10 is a configuration diagram of a refrigeration cycle
apparatus using the expander-integrated compressor.
[0043] FIG. 11 is a vertical cross-sectional view illustrating a
conventional expander-integrated compressor.
BEST MODE FOR CARRYING OUT THE INVENTION
First Embodiment
[0044] FIG. 1 is a vertical cross-sectional view illustrating an
expander-integrated compressor according to a first embodiment of
the present invention. An expander-integrated compressor 100A has a
closed casing 1, a compression mechanism 2, an expansion mechanism
3, a motor 4, a shaft 5, an oil pump 6, and an oil supply amount
regulating mechanism 30. The compression mechanism 2 is disposed in
a lower part of the closed casing 1. The expansion mechanism 3 is
disposed in an upper part of the closed casing 1. The motor 4 is
disposed between the compression mechanism 2 and the expansion
mechanism 3. The compression mechanism 2, the motor 4, and the
expansion mechanism 3 are coupled to each other by the shaft 5 so
that mechanical power can be transmitted. The oil pump 6 is
provided at a lower portion of the shaft 5. The oil supply amount
regulating mechanism 30 is for regulating the amount of the oil to
be supplied to the expansion mechanism 3. In the present
embodiment, a regulating valve (typically a needle valve) is
employed as the oil supply amount regulating mechanism 30.
[0045] The motor 4 drives the shaft 5 to operate the compression
mechanism 2. The expansion mechanism 3 recovers mechanical power
from the expanding working fluid, and supplies the mechanical power
to the shaft 5 to assist the motor 4 to drive the shaft 5. The
working fluid is, for example, a refrigerant such as carbon dioxide
and hydrofluorocarbon.
[0046] In the present embodiment, the arrangement of the
compression mechanism 2, the motor 4, and the expansion mechanism 3
is determined in such a manner that the axis direction of the shaft
5 is in agreement with the vertical direction. However, the
positional relationship between the compression mechanism 2 and the
expansion mechanism 3 may be opposite of that in the present
embodiment. In other words, the compression mechanism 2 may be
disposed in an upper part of the closed casing 1, and the expansion
mechanism 3 may be disposed in a lower part of the closed casing
1.
[0047] The closed casing 1 has an interior space 24 for
accommodating various components. The interior space 24 of the
closed casing 1 is filled with the refrigerant compressed by the
compression mechanism 2. A bottom portion of the closed casing 1 is
utilized as an oil reservoir 25. The oil is used for ensuring
lubrication and sealing on the sliding parts of the compression
mechanism 2 and the expansion mechanism 3. The amount of the oil in
the oil reservoir 25 is controlled so that the oil level is below
the motor 4. This prevents a decrease of the efficiency of the
motor and an increase of the oil discharge amount to the
refrigerant circuit, which result from the agitation of the oil by
the rotor of the motor 4. Since the temperature of the compression
mechanism 2 becomes high during operation of the
expander-integrated compressor 100A, the temperature of the oil
held in the oil reservoir 25 becomes accordingly high.
[0048] The compression mechanism 2 has cylinders 17 and 18, pistons
7 and 8, and bearing members 10 and 11, and it has the same
structure as that of the conventional two-stage rotary compressor.
A suction pipe 13 is connected to the cylinder 17, and a suction
pipe 14 is connected to the cylinder 18. The refrigerant is guided
to compression chambers 19 and 20, formed in the respective
cylinders 17 and 18, through the suction pipes 13 and 14. The
refrigerant compressed in the compression chambers 19 and 20 is
discharged to the interior space 24 of the closed casing 19. A
discharge pipe 15 is connected to the closed casing 1 so that an
opening thereof is located between the motor 4 and the expansion
mechanism 3. The refrigerant discharged to the interior space 24
flows upward through a region surrounding the motor 4. The
refrigerant is then guided through the discharge pipe 15 to a flow
passage outside the closed casing 1. At that time, the refrigerant
and the oil can be separated from each other by a gravitational
force or a centrifugal force.
[0049] In the present embodiment, a rotary-type fluid mechanism is
employed as the compression mechanism 2. The "rotary type" includes
not only a rolling piston type, in which a vane slides along the
outer circumferential surface of a piston, and a sliding vane type,
in which a vane slides along the inner circumferential surface of a
cylinder, but also a swing piston type, in which a piston and a
vane are integrally formed. In addition, the type of the
compression mechanism 2 is not limited to the rotary type. It is
also possible to employ other types of fluid mechanisms, such as a
scroll type, a reciprocating type, and a screw type, as the
compression mechanism 2. The same applies to the later-described
expansion mechanism 3.
[0050] The motor 4 has a stator 21 fixed to the closed casing 1 and
a rotor 22 fixed to the shaft 5. Electric power is supplied to the
motor 4 through a terminal (not shown) disposed at the top of the
closed casing 1.
[0051] An oil supply passage 29 communicating with sliding parts of
the expansion mechanism 3 is formed in the shaft 5 so as to extend
in the axis direction. This is desirable because, when forming the
oil supply passage 29 inside the shaft 5, the problems associated
with an increase in the parts count and parts layout do not arise.
The oil is supplied to sliding parts of the expansion mechanism 3
through the oil supply passage 29.
[0052] In the present embodiment, the oil supply passage 29 does
not open in the upper end face of the shaft 5. In this way, the oil
does not flow out over the expansion mechanism 3, unlike the
conventional example described with reference to FIG. 11. Thereby,
the oil is less easily cooled by the expansion mechanism 3. In
other words, the heat transfer from the compression mechanism 2 to
the expansion mechanism 3 can be reduced more effectively. However,
the oil supply passage 29 may open in the upper end face of the
shaft 5.
[0053] The shaft 5 may be made of a single component, or may be
made by combining (coupling) a plurality of components together.
Specifically, the shaft 5 may include a first shaft on the
compression mechanism 2 side and a second shaft on the expansion
mechanism 3 side. The first shaft and the second shaft may be
coupled directly by fitting them onto each other, or may be coupled
to each other via another component (coupler). When the shaft 5 is
made of a combination of a plurality of components, assembling,
especially alignment between the compression mechanism 2 and the
expansion mechanism 3, becomes easy.
[0054] The expansion mechanism 3 has a first cylinder 42, a second
cylinder 44 having an inner diameter larger than the inner diameter
of the first cylinder 42, an intermediate plate 43 partitioning the
first cylinder 42 and the second cylinder 44. The first cylinder 42
and the second cylinder 44 are disposed concentrically with each
other. As illustrated in FIGS. 2A and 2B, the expansion mechanism 3
further has a first piston 46, a first vane 48, a first spring 50,
a second piston 47, a second vane 49, and a second spring 51.
[0055] As illustrated in FIG. 2A, the first piston 46 is fitted
with an eccentric portion 5c of the shaft 5, and it performs
eccentric rotational motion in the first cylinder 42. The first
vane 48 is retained reciprocably in a vane groove 42a formed in the
first cylinder 42. One end of the first vane 48 is in contact with
the first piston 46. The first spring 50 is in contact with the
other end of the first vane 48, and biases the first vane 48 toward
the first piston 46.
[0056] As illustrated in FIG. 2B, the second piston 47 is fitted
with an eccentric portion 5d of the shaft 5, and it performs
eccentric rotational motion in the second cylinder 44. The second
vane 49 is retained reciprocably in a vane groove 44a formed in the
second cylinder 44. One end of the second vane 49 is in contact
with the second piston 47. The second spring 51 is in contact with
the other end of the second vane 49, and biases the second vane 49
toward the second piston 47.
[0057] The expansion mechanism 3 further has a bearing member 45
and a bearing member 41. The bearing member 41 is fitted to the
closed casing 1 with no clearance between them. The components such
as the cylinders and the intermediate plate are fixed to the closed
casing 1 via the bearing member 41. The bearing member 41 and the
intermediate plate 43 sandwiches the first cylinder 42 from the top
and bottom, and the intermediate plate 43 and the bearing member 45
sandwiches the second cylinder 44 from the top and bottom.
Sandwiching the bearing member 45, the intermediate plate 43, and
the bearing member 41 forms working chambers 55 and 56 in the first
cylinder 42 and the second cylinder 44, respectively.
[0058] As illustrated in FIG. 2A, a suction-side working chamber
55a (first suction-side space) and a discharge-side working chamber
55b (first discharge-side space) are formed inside the first
cylinder 42. The working chamber 55a and the working chamber 55b
are partitioned by the first piston 46 and the first vane 48. As
illustrated in FIG. 2B, a suction-side working chamber 56a (second
suction-side space) and a discharge-side working chamber 56b
(second discharge-side space) are formed inside the second cylinder
44. The working chamber 56a and the working chamber 56b are
partitioned by the second piston 47 and the second vane 49. The
total volumetric capacity of the two working chambers 56a and 56b
in the second cylinder 44 is greater than the total volumetric
capacity of the two working chambers 55a and 55b in the first
cylinder 42. The discharge-side working chamber 55b of the first
cylinder 42 and the suction-side working chamber 56a of the second
cylinder 44 are brought into communication with each other through
a through hole 43a formed in the intermediate plate 43, so that
they can function as a single working chamber (an expansion
chamber).
[0059] The method for making the total volumetric capacity of the
working chambers 56a and 56b greater than the total volumetric
capacity of the working chambers 55a and 55b is not limited to the
method of varying the inner diameters of the first cylinder 42 and
the second cylinder 44. It is also possible to employ the method of
appropriately setting the thicknesses of the cylinders 42 and 44 or
the outer diameters of the pistons 46 and 47.
[0060] The expansion mechanism 3 further has a suction pipe 52
serving as a suction passage for directly drawing the refrigerant
that has not yet been expanded from a flow passage external to the
closed casing 1, and a discharge pipe 53 serving as a discharge
passage for directly discharging the refrigerant that has been
expanded to a flow passage external to the closed casing 1.
Specifically, the suction pipe 52 is directly inserted in the first
cylinder 42 so that the refrigerant can be guided from the flow
passage external to the closed casing 1 to the working chamber 55
of the first cylinder 42. The discharge pipe 53 is directly
inserted in the second cylinder 44 so that the refrigerant can be
guided from the working chamber 56 of the second cylinder 44 to the
flow passage external to the closed casing 1. The suction pipe 52
may be inserted in the bearing member 41, and the discharge pipe 53
may be inserted in the bearing member 45.
[0061] The refrigerant that has not yet been expanded passes
through the suction pipe 52 and flows into the working chamber 55a
of the first cylinder 42. The working fluid having flowed into the
working chamber 55a of the first cylinder 42 moves to the working
chamber 55b in association with rotation of the shaft 5, and it
expands and reduces its pressure in the expansion chamber formed by
the working chamber 55b, the through hole 43a, and the working
chamber 56a, while rotating the shaft 5. The refrigerant having
expanded is guided to the outside of the closed casing 1 through
the working chamber 56b and the discharge pipe 53.
[0062] The location at which the oil pump 6 is provided is a lower
portion of the shaft 5. Specifically, the oil pump 6 is disposed in
the oil supply passage 29 in a lower portion of the shaft 5.
Disposing the oil pump 6 in the oil supply passage 29 eliminates
the need to provide an oil supply pipe separately.
[0063] The oil pump 6 is operated by the mechanical power supplied
from the shaft 5. In the present embodiment, a velocity type pump
(turbine pump) is employed as the oil pump 6. Specifically, the oil
pump 6 has a pump blade 6a and a blade stopper 6b. The pump blade
6a is fixed to the shaft 5 by the blade stopper 6b. Rotation of the
pump blade 6a together with the shaft 5 causes the oil to be pumped
upward. Generally, the rotation speed of the oil pump 6 is equal to
the rotation speed of the shaft 5. Therefore, as the rotation speed
of the shaft 5 increases, the delivery capacity and delivery
pressure of the oil pump 6 increases accordingly. However, since
the effectiveness of the oil supply amount regulating mechanism 30
increases as the delivery pressure of the oil pump 6 increases, the
amount of the oil to be supplied to the expansion mechanism 3 is
not proportional to the rotation speed of the shaft 5.
[0064] The type of the oil pump is not limited to the velocity type
pump, and a positive displacement pump may be used. Examples of the
positive displacement pump include a rotary type oil pump and a
TROCHOID pump (registered trademark of Nippon Oil Pump Co., Ltd.).
However, the velocity type pump is better suited for the oil supply
amount regulating mechanism 30 in the present embodiment than the
positive displacement pump. The reason is that no oil escape route
is provided in the present embodiment, as it is provided in the
later-described second and third embodiments.
[0065] The oil supply amount regulating mechanism 30 includes a
structure for preventing the amount of the oil to be supplied to
the expansion mechanism 3 through the oil supply passage 29 from
increasing correspondingly to an increase of the rotation speed of
the shaft 5. As described previously, it is important to reduce the
heat transfer from the compression mechanism 2 to the expansion
mechanism 3 resulting from the oil circulation as much as possible,
in order to improve the efficiency of a refrigeration cycle
apparatus (see FIG. 10) using the expander-integrated compressor
100A. When the rotation speed of the shaft 5 increases, the
delivery capacity and delivery pressure of the oil pump 6 tend to
increase. However, excessive supply of the oil is prevented by the
workings of the oil supply amount regulating mechanism 30. In some
cases, the oil supply amount to the expansion mechanism 3 can be
maintained at almost a constant level regardless of the rotation
speed of the shaft 5. As a result, it is possible to reduce the
heat transfer from the compression mechanism 2 to the expansion
mechanism 3 that results from the oil circulation.
[0066] In the present embodiment, the oil supply amount regulating
mechanism 30 is provided in the oil supply passage 29. For this
reason, it is unnecessary to provide a dedicated space for the oil
supply amount regulating mechanism 30. The location at which the
oil supply amount regulating mechanism 30 should be provided may be
below the expansion mechanism 3, which is located in the upper part
of the closed casing 1. Typically, the oil supply amount regulating
mechanism 30 is provided between the working chamber 20 of the
compression mechanism 2 and the motor 4 with respect to the axis
direction of the shaft 5.
[0067] FIG. 3 is a partially enlarged view of FIG. 1. As
illustrated in FIG. 3, the oil supply amount regulating mechanism
30 has a valve seat 31, a needle 32 (valve body), a spring 33, and
a needle stopper 34. The valve seat 31 has an orifice shape whose
inner diameter decreases toward the expansion mechanism 3. The
needle 32 is disposed so as to face the valve seat 31. The needle
32 has a leading end portion in a circular conic shape. The spring
33 is disposed between the valve seat 31 and the needle 32 so that
a gap through which the oil can flow is formed between the valve
seat 31 and the needle 32. The spring 33 expands and contracts
according to a pressure change of the oil in the oil supply passage
29, so that the gap between the valve seat 31 and the needle 32 can
be adjusted. The needle stopper 34 for defining the range of motion
of the needle 32 is disposed opposite the valve seat 31 across the
needle 32. The valve seat 31 or the needle stopper 34 may be formed
by a portion of the shaft 5.
[0068] With the oil supply amount regulating mechanism 30, the oil
to be supplied to the expansion mechanism 3 flows through the oil
supply passage 29 and hits the back face of the needle 32.
Thereafter, the oil passes through the surrounding region of the
needle 32 and flows toward the valve seat 31. The oil hitting the
back face of the needle 32 presses the needle 32 toward the valve
seat 31 with a force corresponding to the flow rate of the oil. The
needle 32 is pushed back with a force in proportion to the
displacement of the spring 33. Specifically, the area of the gap
between the valve seat 31 and the needle 32 (the cross-sectional
area of the gap) changes according to the flow rate of the oil.
While the oil feeding capability of the oil pump 6 becomes higher
in proportional to an increase of the rotation speed of the shaft
5, the resistance to the oil flow increases because the gap between
the valve seat 31 and the needle 32 narrows. As a result, the
amount of the oil to be supplied is restricted (optimized).
[0069] Even when the shaft 5 revolves at a high speed, an
unnecessarily great amount of the oil is not supplied to the
expansion mechanism 3 because of the workings of the oil supply
amount regulating mechanism 30. In other words, an appropriate
amount of the oil can be supplied to the expansion mechanism 3. As
a result, it is possible to reduce the heat transfer from the
compression mechanism 2 to the expansion mechanism 3 that results
from the oil circulation. Moreover, since excess oil is not
supplied to the expansion mechanism 3, it is possible to prevent
the working fluid from mixing with a large amount of the oil in the
expansion mechanism 3. Thus, it is possible to prevent a
considerable decrease in heat exchange efficiency resulting from
the excess oil flowing into an evaporator 102 (see FIG. 10). As
illustrated in FIG. 4, the effect of optimizing the oil supply
amount can be obtained by providing only the valve seat 31 in the
oil supply passage 29. That is, by merely providing an orifice in
the oil supply passage 29, the oil can be prevented from being
excessively supplied to the expansion mechanism 3 because the
pressure loss at the orifice increases proportionally to an
increase of the oil flow rate.
[0070] In the present embodiment, the oil of the oil supply passage
29 is supplied only to the expansion mechanism 3. However, the oil
of the oil supply passage 29 may also be supplied to the
compression mechanism 2.
Second Embodiment
[0071] FIG. 5 is a vertical cross-sectional view illustrating an
expander-integrated compressor according to a second embodiment of
the present invention. As illustrated in FIG. 5, a main difference
between an expander-integrated compressor 100B of the present
embodiment and the expander-integrated compressor 100A of the first
embodiment is in the oil supply amount regulating mechanism. The
same parts as those in the embodiment shown in FIG. 1 will be
designated by the same reference numerals, and the descriptions
thereof will be omitted.
[0072] FIG. 6 is a partially enlarged view of FIG. 5. In the
present embodiment, a branch passage 29s branching in a radial
direction from the oil supply passage 29 and opening in an outer
circumferential surface of the shaft 5 is formed in the shaft 5. An
oil supply amount regulating mechanism 60 is provided in the branch
passage 29s. In this way, mounting of the oil supply amount
regulating mechanism 60 is possible from the outside of the shaft
5, so assembling is easier than that in the first embodiment.
Moreover, this is suitable also in the case where the oil pump is a
positive displacement pump because the branch passage 29s behaves
as an oil escape route.
[0073] As illustrated in FIG. 6, the oil supply amount regulating
mechanism 60 has a valve seat 61, a needle 62, a spring 63, and a
needle stopper 64. The valve seat 61 has an orifice shape whose
inner diameter decreases toward the oil supply passage 29. The
valve seat 61 is disposed at a portion of the branch passage 29s
that faces the oil supply passage 29. The needle 62 in a circular
conic shape is disposed so as to face the valve seat 61. The needle
62 is displaceable in a direction toward the valve seat 61 and a
direction away from the valve seat 61 (radial directions of the
shaft 5). The needle stopper 64 is disposed at a portion of the
branch passage 29s that faces an outside of the shaft 5. The needle
stopper 64 defines the range of motion of the needle 62. The spring
63 is disposed between the needle 62 and the needle stopper 64.
[0074] A bearing member 10 has a bearing portion 10a that supports
the shaft 5. The bearing portion 10a covers an outer
circumferential surface of the shaft 5 at a location where the
branch passage 29s is formed. A circular chamber 67 is formed in an
inner circumferential surface of the bearing portion 10a. The
branch passage 29s opens toward the chamber 67. An oil discharge
passage 66 for connecting the chamber 67 and the interior space 24
of the closed casing 1 is further formed in the bearing portion 10a
so as to penetrate through the bearing portion 10a in a radial
direction. By the branch passage 29s, the chamber 67, and the oil
discharge passage 66, the oil can flow from the oil supply passage
29 to the interior space 24 of the closed casing 1.
[0075] When the internal pressure of the oil supply passage 29 is
lower than a predetermined pressure, the oil supply amount
regulating mechanism 60 is brought to a closed state. The closed
state refers to a state in which the branch passage 29s is closed
by the needle 62 being fitted into the valve seat 61. In the closed
state, the oil cannot flow through the branch passage 29s. On the
other hand, when the rotation speed of the shaft 5 increases and
the internal pressure of the oil supply passage 29 thereby becomes
higher than a predetermined pressure, the oil supply amount
regulating mechanism 60 is brought to an open state. The open state
refers to a state in which the needle 62 is detached from the valve
seat 61 so that a gap is formed between the valve seat 61 and the
needle 62. In the open state, the oil can flow through the branch
passage 29s.
[0076] When the internal pressure of the oil supply passage 29
becomes higher than the predetermined pressure, the oil enters the
branch passage 29s through the valve seat 61 while displacing the
needle 62. The force of the oil that displaces the needle 62 is
proportional to the internal pressure of the oil supply passage 29.
On the condition that the outward load that is applied to the
needle 62 by the oil in the oil supply passage 29 and the like
(more specifically, the pressure of the oil and the centrifugal
force) exceeds the force by which the spring 63 pushes the needle
62 when the oil supply amount regulating mechanism 60 is in the
closed state, the oil supply amount regulating mechanism 60
switches from the closed state to the open state.
[0077] In other words, when the rotation speed of the shaft 5
increases and the oil is fed into the oil supply passage 29 in an
amount greater than is necessary, the increase of the internal
pressure of the oil supply passage 29 brings the oil supply amount
regulating mechanism 60 into the open state. When the oil supply
amount regulating mechanism 60 is brought into the open state, part
of the oil flowing through the oil supply passage 29 is guided to
the outside of the shaft 5 through the branch passage 29s. The oil
having flowed out of the shaft 5 is discharged to the interior
space 24 of the closed casing 1 through the chamber 67 and the oil
discharge passage 66 formed in the bearing portion 10a of the
bearing member 10. As a result, the amount of the oil to be
supplied to the expansion mechanism 3 is optimized. Thus, in the
present embodiment, the oil supply amount regulating mechanism 60
is constructed by a relief valve.
[0078] In addition, in the present embodiment, the oil is allowed
to escape to the outside of the shaft 5 through the branch passage
29s. For this reason, when the oil supply amount regulating
mechanism 60 is brought into the open state, a difference in the
flow rate of the oil in the oil supply passage 29 arises between
the positions before and after the oil supply amount regulating
mechanism 60. Specifically, the flow rate is high between the oil
supply amount regulating mechanism 60 and the oil pump 6, and the
flow rate is low between the expansion mechanism 3 and the oil
supply amount regulating mechanism 60. It is preferable that the
portion at which the flow rate of the oil is high be farther away
from the expansion mechanism 3, from the view point of reducing the
heat transfer from the compression mechanism 2 to the expansion
mechanism 3 that results from the oil circulation. Therefore, it is
desirable that the branch passage 29s be formed in a portion of the
shaft 5 that is between the motor 4 and the compression mechanism
2.
Third Embodiment
[0079] FIG. 7 is a vertical cross-sectional view illustrating an
expander-integrated compressor according to a third embodiment of
the present invention. As illustrated in FIG. 7, a main difference
between an expander-integrated compressor 100C of the present
embodiment and the expander-integrated compressor 100A of the first
embodiment is in the oil supply amount regulating mechanism.
[0080] FIG. 8 is a partially enlarged view of FIG. 7. In the
present embodiment, a branch passage 29t branching in a radial
direction from the oil supply passage 29 and opening in an outer
circumferential surface of the shaft 5 is formed in the shaft 5. An
oil supply amount regulating mechanism 70 is provided exteriorly of
the shaft so that the oil is guided to the interior space 24 of the
closed casing 1 through the branch passage 29t. Since the oil
supply amount regulating mechanism 70 is provided exteriorly of the
shaft 5, a larger space than is available in the preceding two
embodiments can be ensured for the oil supply amount regulating
mechanism 70.
[0081] The present embodiment is similar to the second embodiment
in the respect that the branch passage 29t is formed in the shaft 5
as an oil escape route. On the other hand, the present embodiment
is different from the second embodiment in the respect that the oil
supply amount regulating mechanism 70 does not rotate together with
the shaft 5. This is suitable also in the case where the oil pump
is a positive displacement pump because the branch passage 29t
behaves as an oil escape route.
[0082] As illustrated in FIG. 8, in the present embodiment, the oil
supply amount regulating mechanism 70 is provided inside the
bearing member 10. The bearing member 10 has the bearing portion
10a that supports the shaft 5. The bearing portion 10a covers an
outer circumferential surface of the shaft 5 at a location where
the branch passage 29t is formed. A circular chamber 77 is formed
in an inner circumferential surface of the bearing portion 10a. The
branch passage 29t opens toward the chamber 77. An oil discharge
passage 76 is further formed in the bearing portion 10a, as a
passage for connecting the chamber 77 and the interior space 24 of
the closed casing 1. The oil supply amount regulating mechanism 70
is provided in the oil discharge passage 76.
[0083] The oil supply amount regulating mechanism 70 has a valve
seat 71, a valve body 72, a spring 73, and a valve body stopper 74.
The oil discharge passage 76 includes a portion having a T-shaped
cross-sectional shape along the flow direction of the oil. The
valve seat 71 is disposed in the T-shaped portion. The valve body
72 in a spherical shape is disposed so as to face the valve seat
71. The valve body stopper 74 is disposed opposite the valve seat
71 across the valve body 72. The valve body stopper 74 defines the
range of motion of the valve body 72. The spring 73 is disposed
between the valve body 72 and the valve body stopper 74. It should
be noted that the structure of the oil supply amount regulating
mechanism 70 may be the same as that in the second embodiment.
[0084] When the internal pressure of the oil supply passage 29 is
lower than a predetermined pressure, the oil supply amount
regulating mechanism 70 is brought to a closed state. The closed
state refers to a state in which the oil discharge passage 76 is
closed by the valve body 72 being fitted into the valve seat 71. In
the closed state, the oil cannot flow through the oil discharge
passage 76. On the other hand, when the rotation speed of the shaft
5 increases and the internal pressure of the oil supply passage 29
thereby becomes higher than the predetermined pressure, the oil
supply amount regulating mechanism 70 is brought to an open state.
The open state refers to a state in which the valve body 72 is
detached from the valve seat 71 so that a gap is formed between the
valve seat 71 and the valve body 72. In the open state, the oil can
flow through the oil discharge passage 76.
[0085] When the internal pressure of the oil supply passage 29
becomes higher than the predetermined pressure, the oil displaces
the valve body 72, causing the oil discharge passage 76 to open.
The force of the oil that displaces the valve body 72 is
proportional to the internal pressure of the oil supply passage 29.
On the condition that the load that is applied to the valve body 72
by the oil in the oil supply passage 29 exceeds the force by which
the spring 73 pushes the needle 72 when the oil supply amount
regulating mechanism 70 is in the closed state, the oil supply
amount regulating mechanism 70 switches from the closed state to
the open state.
[0086] In other words, when the rotation speed of the shaft 5
increases and the oil is fed into the oil supply passage 29 in an
amount greater than is necessary, the increase of the internal
pressure of the oil supply passage 29 brings the oil supply amount
regulating mechanism 70 into the open state. When the oil supply
amount regulating mechanism 70 is brought into the open state, part
of the oil flowing through the oil supply passage 29 is guided to
the outside of the shaft 5 through the branch passage 29t. The oil
having flowed out of the shaft 5 is discharged to the interior
space 24 of the closed casing 1 through the chamber 77 and the oil
discharge passage 76 each formed in the bearing portion 10a of the
bearing member 10. As a result, the amount of the oil to be
supplied to the expansion mechanism 3 is optimized. Thus, in the
present embodiment as well, the oil supply amount regulating
mechanism 70 is constructed by a relief valve.
[0087] It should be noted that the oil supply amount regulating
mechanism 70 may be disposed at an outlet of the oil discharge
passage 76, or may be disposed in the chamber 77.
[0088] In the present embodiment as well, the oil is allowed to
escape to the outside of the shaft 5 through the branch passage
29t. Therefore, it is desirable that the branch passage 29t be
formed in a portion of the shaft 5 that is between the motor 4 and
the compression mechanism 2, which is located in the lower part of
the closed casing 1.
Fourth Embodiment
[0089] In an expander-integrated compressor 100D of the present
embodiment, the axis direction of the shaft 5 is parallel to the
horizontal direction, as illustrated in FIG. 9. The oil reservoir
25 is formed along the longitudinal direction of the closed casing
1. A partition wall 27 is provided between the expansion mechanism
3 and the motor 4. The partition wall 27 divides the interior space
24 into a space on the expansion mechanism 3 side and a space on
the compression mechanism 2 side. The motor 4 is disposed also in
the space on the compression mechanism 2 side. This partition wall
27 also has the function to reduce the heat transfer from the
compression mechanism 2 and the motor 4 to the expansion mechanism
3. The partition wall 27 has a passage 27h allowing the oil to flow
therethrough.
[0090] A positive displacement-type the oil pump 26 is provided at
an end portion of the shaft 5. The oil pump 26, the expansion
mechanism 3, the motor 4, and the compression mechanism 2 are
arrayed in that order along the axis direction of the shaft 5. The
oil supply amount regulating mechanism 60 is the same one as
described with reference to FIG. 6 in the third embodiment. A
nozzle 26k of the oil pump 26 extends toward the oil reservoir 25
so that it can draw the oil in the oil reservoir 25. The oil drawn
by the oil pump 26 is supplied through the oil supply passage 29 to
the compression mechanism 2 located in the far side, viewed from
the oil pump 26, with respect to the axis direction the shaft 5. In
the present embodiment, the oil from the oil pump 26 is also
supplied to the expansion mechanism 3, which is located on the near
side, viewed from the oil pump 26. The oil discharged from the oil
supply passage 29 through the oil supply amount regulating
mechanism 60 returns to the space on the expansion mechanism 3
side.
[0091] As in the foregoing embodiments, the oil supply amount
regulating mechanism 60 prevents excessive supply of the oil.
Thereby, the heat transfer from the compression mechanism 2 to the
expansion mechanism 3 is suppressed. In the embodiment shown in
FIG. 9, the oil pump 26 is provided in the expansion mechanism 3
side. However, it is possible to provide the oil pump 26 in the
compression mechanism 2 side. It is also possible to provide the
oil supply amount regulating mechanism 30 (first embodiment) or the
oil supply amount regulating mechanism 70 (third embodiment), in
place of the oil supply amount regulating mechanism 60.
INDUSTRIAL APPLICABILITY
[0092] The expander-integrated compressor according to the present
invention may be suitably applied to, for example, refrigeration
cycle apparatuses (heat pumps) for air conditioners, water heaters,
driers, or refrigerator-freezers. As illustrated in FIG. 10, a
refrigeration cycle apparatus 110 includes: an expander-integrated
compressor 100A (, 100B, 100C, or 100D); a radiator 101 for cooling
the refrigerant compressed by the compression mechanism 2; and an
evaporator 114 for evaporating the refrigerant expanded by the
expansion mechanism 3. The compression mechanism 2, the radiator
101, the expansion mechanism 3, and the evaporator 102 are
connected by pipes, to form a refrigerant circuit.
[0093] For example, when refrigeration cycle apparatus 110 is
applied to an air conditioner, it is possible to prevent a decrease
in heating capacity caused by a decreased discharge temperature of
the compression mechanism 2 during heating operation, and a
decrease in cooling capacity caused by an increased discharge
temperature of the expansion mechanism 3 during cooling operation,
by reducing the heat transfer from the compression mechanism 2 to
the expansion mechanism 3. As a result, the coefficient of
performance of the air conditioner is improved.
* * * * *