U.S. patent number 10,996,431 [Application Number 16/523,635] was granted by the patent office on 2021-05-04 for camera module including magnet interacting with both coil for performing focusing function and coil for performing shake compensation function.
This patent grant is currently assigned to LG INNOTEK CO., LTD.. The grantee listed for this patent is LG INNOTEK CO., LTD.. Invention is credited to In Jae Yeo.



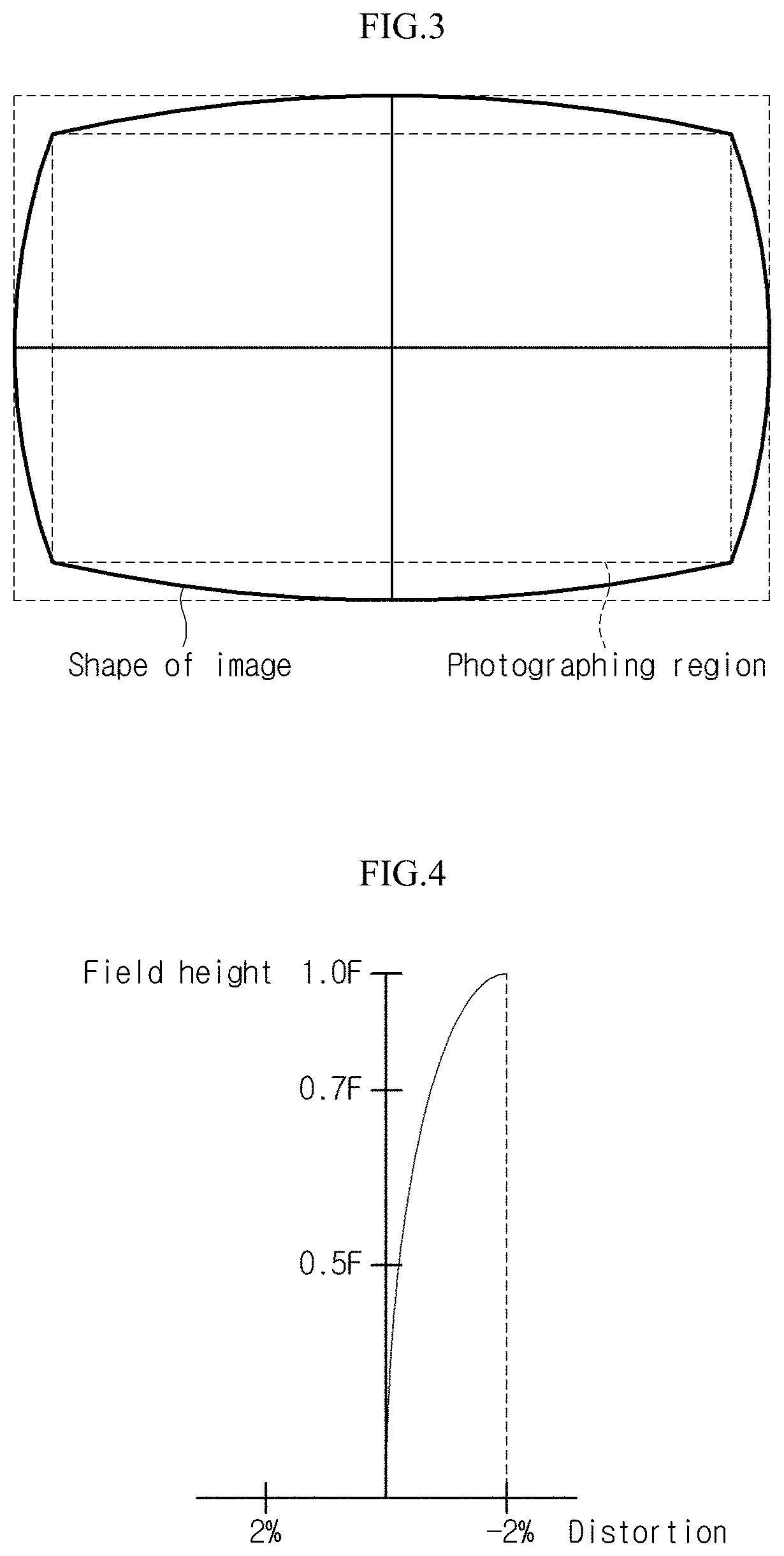


United States Patent |
10,996,431 |
Yeo |
May 4, 2021 |
Camera module including magnet interacting with both coil for
performing focusing function and coil for performing shake
compensation function
Abstract
Disclosed is a camera module. The camera module includes: a lens
barrel disposed in a housing to receive a lens assembly; an elastic
member in at least one of the housing and the lens barrel; a
driving unit moving the lens barrel relative to the housing; and a
sensor unit fixed to the housing.
Inventors: |
Yeo; In Jae (Seoul,
KR) |
Applicant: |
Name |
City |
State |
Country |
Type |
LG INNOTEK CO., LTD. |
Seoul |
N/A |
KR |
|
|
Assignee: |
LG INNOTEK CO., LTD. (Seoul,
KR)
|
Family
ID: |
1000005529993 |
Appl.
No.: |
16/523,635 |
Filed: |
July 26, 2019 |
Prior Publication Data
|
|
|
|
Document
Identifier |
Publication Date |
|
US 20190349504 A1 |
Nov 14, 2019 |
|
Related U.S. Patent Documents
|
|
|
|
|
|
|
Application
Number |
Filing Date |
Patent Number |
Issue Date |
|
|
15827814 |
Nov 30, 2017 |
10412284 |
|
|
|
14411788 |
Jan 2, 2018 |
9860432 |
|
|
|
PCT/KR2013/005777 |
Jun 28, 2013 |
|
|
|
|
Foreign Application Priority Data
|
|
|
|
|
Jun 29, 2012 [KR] |
|
|
10-2012-0071201 |
|
Current U.S.
Class: |
1/1 |
Current CPC
Class: |
G03B
13/34 (20130101); G03B 5/00 (20130101); H04N
5/2257 (20130101); G02B 13/001 (20130101); H04N
5/2254 (20130101); G03B 2205/0046 (20130101); G03B
2205/0007 (20130101); G03B 2205/0053 (20130101) |
Current International
Class: |
G02B
13/00 (20060101); H04N 5/225 (20060101); G03B
13/34 (20210101); G03B 5/00 (20210101) |
References Cited
[Referenced By]
U.S. Patent Documents
Foreign Patent Documents
|
|
|
|
|
|
|
101551500 |
|
Oct 2009 |
|
CN |
|
2001-034971 |
|
Feb 2001 |
|
JP |
|
2005-073130 |
|
Mar 2005 |
|
JP |
|
2008-176185 |
|
Jul 2008 |
|
JP |
|
2011-065140 |
|
Mar 2011 |
|
JP |
|
2011-085666 |
|
Apr 2011 |
|
JP |
|
2011-128583 |
|
Jun 2011 |
|
JP |
|
2011-203283 |
|
Oct 2011 |
|
JP |
|
2011-203476 |
|
Oct 2011 |
|
JP |
|
2011-227427 |
|
Nov 2011 |
|
JP |
|
2011-227428 |
|
Nov 2011 |
|
JP |
|
2011-247909 |
|
Dec 2011 |
|
JP |
|
2011-257448 |
|
Dec 2011 |
|
JP |
|
2012-058762 |
|
Mar 2012 |
|
JP |
|
2012-103376 |
|
May 2012 |
|
JP |
|
2012-150421 |
|
Aug 2012 |
|
JP |
|
2012-238029 |
|
Dec 2012 |
|
JP |
|
2013-024938 |
|
Feb 2013 |
|
JP |
|
10-2006-0002185 |
|
Jan 2006 |
|
KR |
|
10-2006-0130857 |
|
Dec 2006 |
|
KR |
|
10-0742978 |
|
Jul 2007 |
|
KR |
|
10-2007-0101628 |
|
Oct 2007 |
|
KR |
|
10-0918816 |
|
Sep 2009 |
|
KR |
|
10-2009-0131925 |
|
Dec 2009 |
|
KR |
|
10-0952620 |
|
Apr 2010 |
|
KR |
|
10-2010-0048361 |
|
May 2010 |
|
KR |
|
10-0965913 |
|
Jun 2010 |
|
KR |
|
10-2010-0104962 |
|
Sep 2010 |
|
KR |
|
10-1017341 |
|
Feb 2011 |
|
KR |
|
10-2011-0050161 |
|
May 2011 |
|
KR |
|
10-1069619 |
|
Oct 2011 |
|
KR |
|
2011-29822 |
|
Sep 2011 |
|
TW |
|
WO-2011/021559 |
|
Feb 2011 |
|
WO |
|
WO-2011/078614 |
|
Jun 2011 |
|
WO |
|
Other References
Notice of Allowance dated Feb. 4, 2020 in Japanese Application No.
2018-109043. cited by applicant .
International Search Report in International Application No.
PCT/KR2013/005777, filed Jun. 28, 2013. cited by applicant .
Office Action dated May 9, 2017 in Chinese Application No.
201380033866.6. cited by applicant .
Office Action dated May 24, 2017 in Japanese Application No.
2015-520047. cited by applicant .
Notice of Allowance dated Apr. 25, 2019 in U.S. Appl. No.
15/827,814. cited by applicant .
European Search Report dated Mar. 22, 2021 in European Application
No. 20198136.2. cited by applicant.
|
Primary Examiner: Spinks; Antoinette T
Attorney, Agent or Firm: Saliwanchik, Lloyd &
Eisenschenk
Parent Case Text
CROSS-REFERENCE TO RELATED APPLICATIONS
This application is a continuation of U.S. application Ser. No.
15/827,814, filed Nov. 30, 2017; which is a continuation of U.S.
application Ser. No. 14/411,788, filed Dec. 29, 2014, now U.S. Pat.
No. 9,860,432, issued Jan. 2, 2018; which is the U.S. national
stage application of International Patent Application No.
PCT/KR2013/005777, filed Jun. 28, 2013; which claims priority to
Korean Application No. 10-2012-0071201, filed Jun. 29, 2012; all of
which are hereby incorporated by reference in their entirety.
Claims
The invention claimed is:
1. A camera module comprising: a housing comprising a first housing
and a second housing disposed under the first housing; a barrel
disposed in the first housing; a first elastic member connecting
the barrel and the first housing; a second elastic member coupled
with the first housing and the second housing; a lens assembly
disposed in the barrel; a first coil disposed on an outer side of
the barrel; a magnet disposed on the first housing; and a second
coil disposed on the second housing, wherein the first coil faces
the magnet in a horizontal direction and the second coil faces a
lower surface of the magnet in a vertical direction such that the
first coil and the second coil share and interact with the magnet,
wherein the lens assembly comprises at least five lenses, wherein a
first lens disposed closest to an object side among the at least
five lenses comprises a positive refractive power and a convex
surface facing the object side, wherein a second lens disposed
second from the object side among the five lenses comprises a
meniscus shape, wherein a third lens disposed third from the object
side among the five lenses comprises a meniscus shape, wherein a
fourth lens disposed fourth from the object side among the five
lenses comprises a meniscus shape, wherein at least one of an
object side surface of the fourth lens and an image side surface of
the fourth lens comprises at least one aspheric inflection point,
wherein a side portion of the first housing is overlapped with a
portion of the second elastic member in the horizontal direction,
wherein the first housing comprises the side portion and an upper
portion extending from an upper end of the side portion in the
horizontal direction, wherein the magnet comprises the lower
surface facing an upper surface of the second coil, an upper
surface facing the upper portion of the first housing, a first side
surface facing the first coil, and a second side surface facing the
side portion of the first housing, wherein the first coil faces the
first side surface of the magnet in the horizontal direction, and
wherein, measured in the vertical direction, a width of the first
side surface of the magnet is greater than a width of a surface of
the first coil facing the first side surface of the magnet.
2. The camera module according to claim 1, comprising an image
sensor disposed under the second housing; and a circuit board on
which the image sensor is mounted, the image sensor electrically
connected to the circuit board.
3. The camera module according to claim 1, wherein the lens
assembly is configured to form an image including a negative
distortion.
4. The camera module according to claim 1, wherein the first coil
and the magnet are configured to perform a focusing function such
that the barrel and the first coil move relative to the first
housing in the vertical direction under operation of the focusing
function, and wherein the magnet and the second coil are configured
to perform a shaking compensation function such that the first
housing and the magnet move relative to the second housing in the
horizontal direction under operation of the shaking compensation
function.
5. The camera module according to claim 4, wherein a distance
between the second coil and the second housing remains constant
under operation of the focusing function and the shaking
compensation function.
6. The camera module according to claim 2, wherein a distance
between the second coil and the image sensor remains constant under
operation of a focusing function and a shaking compensation
function.
7. The camera module according to claim 2, wherein a unit cell of
the image sensor has a length of 2 .mu.m or less or a breadth of 2
.mu.m or less.
8. The camera module according to claim 1, wherein the first coil
is spaced apart from the magnet by a distance in a range of from 50
.mu.m to 1000 .mu.m, and wherein the second coil is spaced apart
from the magnet by a distance in a range of from 50 .mu.m to 1000
.mu.m.
9. The camera module according to claim 1, wherein the second coil
comprises an outer portion, an inner portion, and a central portion
between the outer portion and the inner portion, the central
portion overlapping with the lower surface of the magnet in the
vertical direction, the outer portion extending horizontally from
the central portion to a direction opposite to the barrel, and the
inner portion extending horizontally from the central portion to a
direction to the barrel.
10. The camera module according to claim 9, wherein the outer
portion is disposed between a lower surface of the side portion of
the first housing and the second housing, and wherein the inner
portion is disposed to overlap with the upper portion of the first
housing in the vertical direction and not to overlap with the lower
surface of the magnet in the vertical direction.
11. The camera module according to claim 1, wherein the surface of
the first coil is positioned between the upper surface of the
magnet and the lower surface of the magnet when viewed from the
horizontal direction, and wherein the first coil is positioned
nearer to the lower surface of the magnet than it is to the upper
surface of the magnet, at an initial position of the barrel.
12. The camera module according to claim 1, wherein the second coil
is disposed lower than a bottom surface of the barrel, and wherein
the magnet and the first coil are disposed below the upper portion
of the first housing.
13. The camera module according to claim 1, wherein, measured in
the horizontal direction, a width of the upper portion of the first
housing is greater than a width of the upper surface of the
magnet.
14. The camera module according to claim 1, wherein a distance
between the first side surface of the magnet and the first coil in
the horizontal direction is longer than a distance between the
lower surface of the magnet and the upper surface the second coil
in the vertical direction.
15. The camera module according to claim 1, wherein the magnet
interacts with the first coil to move the barrel and the first coil
relative to the first housing in the vertical direction, and
wherein the second coil interacts with the magnet to move the first
housing and the magnet relative to the second housing in the
horizontal direction.
16. The camera module according to claim 1, wherein the second
elastic member is overlapped with the first elastic member in the
horizontal direction.
17. The camera module according to claim 1, wherein the magnet has
a shape of plate, wherein the first coil is fixed to the outer side
of the barrel, and wherein the second housing supports the second
coil.
18. An information technology (IT) device comprising the camera
module according to claim 1.
Description
TECHNICAL FIELD
The embodiment relates to a camera module.
BACKGROUND ART
Recently, a camera module has been installed in a mobile
communication terminal, an information technology (IT) device, such
as a PDA or an MP3 player, a vehicle, and an endoscope. As the
technology has been developed toward the high-pixel camera module
from the conventional VGA camera equipped with 0.3 mega pixels, the
camera module has been manufactured in a small size with a slim
structure according to targets to which the camera module is
installed. In addition, the camera module has been equipped with
various additional functions, such as auto-focusing or optical zoom
functions, at the low manufacturing cost.
Meanwhile, the camera module manufactured in these days is equipped
with an image sensor module, which is manufactured through a COB
(chip of board) scheme, a COF (chip of flexible) scheme or a CSP
(chip scale package) scheme, and is usually connected to a main
substrate through an electric connection unit, such as a PCB
(printed circuit board) or an FPCB (flexible printed circuit
board).
However, users recently request the camera module, which can be
directly mounted on the main substrate similar to a general passive
element, in such a manner that the manufacturing process for the
camera module can be simplified while reducing the manufacturing
cost.
The camera module is generally manufactured by attaching an image
sensor, such as a CCD or a CMOS, to a substrate through a wire
bonding scheme or a flip chip scheme. An image of a subject is
focused by the image sensor and the focused image is stored as data
in a memory, which is installed inside or outside the camera
module. In addition, the stored data are converted into electric
signals and the electric signals are displayed as images through a
display medium, such as an LCD or a PC monitor provided in a
device.
A camera module according to the related art includes a housing, an
image sensor supported on a bottom of the housing to convert an
image signal received through a lens into an electric signal, a
lens group to focus an image signal of a subject to the image
sensor, and a barrel in which the lens group are stacked. The
housing, the lens group and the barrel are sequentially coupled
with each other.
In addition, an FPCB mounted thereon with chip components, which
are electric components serving as a condenser and a resistor to
drive the image sensor including a CCD or a CMOS, is electrically
connected to the bottom of the housing.
In the camera module having the above structure according to the
related art, in a state that a plurality of circuit components have
been mounted on the FPCB, an ACF (anisotropic conductive film) is
inserted between the substrate and the image sensor, and heat and
pressure are applied thereto in such a manner that the substrate,
the image sensor and the ACF are fixedly bonded and conducted with
each other and an IR cut-off filter is attached to an opposite
side.
In addition, in a state that the barrel provided therein with a
plurality of lens groups is temporally screw-coupled with the
housing, as described above, the assembled PCB used for mounting
devices is fixedly bonded to the bottom of the housing by an
adhesive.
Meanwhile, after the PCB, to which the image sensor is attached,
has been fixedly bonded to the housing coupled with the barrel, a
focus adjustment is carried out with respect to a subject
(resolution chart) located in front of the barrel and spaced apart
from the barrel by a predetermined distance. At this time, the
focus adjustment of the camera module can be achieved between the
lens group and the image sensor while adjusting the vertical
displacement by rotating the barrel screw-coupled with the
housing.
DISCLOSURE
Technical Problem
The embodiment provides a camera module capable of effectively
inhibiting hand-shaking.
Technical Solution
According to the embodiment, there is provided a camera module
including: a lens barrel disposed in a housing to receive a lens
assembly; an elastic member in at least one of the housing and the
lens barrel; a driving unit moving the lens barrel relative to the
housing; and a sensor unit fixed to the housing.
Advantageous Effects
The camera module according to the embodiment can compensate for
hand-shaking by driving the lens barrel with respect to the
housing. That is, the driving unit can compensate for hand-shaking
by moving the lens barrel relative to the housing.
Particularly, the camera module according to the embodiment allows
an image formed on the sensor unit to have a negative distortion by
the lens assembly. Accordingly, when the shaking is compensated for
by moving the lens barrel, an error at an outer peripheral portion
of the image can be minimized.
DESCRIPTION OF DRAWINGS
FIG. 1 is a sectional view showing a camera module according to the
embodiment.
FIG. 2 is a diagram illustrating an optical system including a lens
assembly, an infrared (IR) cut-off filter unit, and a sensor
unit.
FIG. 3 is a diagram illustrating an image incident onto the sensor
unit through the lens assembly.
FIG. 4 is a diagram illustrating distortion in an optical system
including a lens assembly, an IR cut-off filter unit, and a sensor
unit.
FIG. 5 is a diagram illustrating movement of an image due to
hand-shaking and compensation thereof.
FIG. 6 is a sectional view showing a camera module according to
another embodiment.
FIG. 7 is a sectional view showing a camera module according to
another embodiment.
BEST MODE
Mode for Invention
In the description of the embodiments, it will be understood that
when each lens, unit, part, hole, protrusion, groove or layer is
referred to as being "on" or "under" another lens, unit, part,
hole, protrusion, groove or layer, it can be "directly" or
"indirectly" on the other lens, unit, part, hole, protrusion,
groove or layer or one or more intervening layers may also be
present. Such a position has been described with reference to the
drawings. The thickness and size of each layer shown in the
drawings may be exaggerated, omitted or schematically drawn for the
purpose of convenience or clarity. In addition, the size of
elements does not utterly reflect an actual size.
FIG. 1 is a diagram showing a camera module according to the
embodiment. FIG. 2 is a diagram illustrating an optical system
including a lens assembly, an IR cut-off filter unit, and a sensor
unit. FIG. 3 is a diagram illustrating an image incident onto the
sensor unit through the lens assembly. FIG. 4 is a diagram
illustrating distortion in an optical system including a lens
assembly, an IR cut-off filter unit, and a sensor unit. FIG. 5 is a
diagram illustrating movement of an image due to hand-shaking and
compensation thereof.
Referring to FIGS. 1 to 5, the camera module according to the
embodiment includes a lens barrel 100, a lens assembly 200, a first
elastic member 310, a second elastic member 320, a first housing
410, a second housing 420, an IR cut-off filter unit 500 and a
sensor unit 600, a circuit board 800, and driving units 710, 720,
730, and 740.
The lens barrel 100 receives the lens assembly 200 therein. The
lens barrel 100 has a receiving groove for receiving the lens
assembly 200. The receiving groove may have a shape corresponding
to a shape of the lens assembly 200.
The lens barrel 100 may have a rectangular shape or a cylindrical
shape. That is, the outer portion of the lens barrel 100 may have a
rectangular shape or a circular shape.
The lens barrel 100 may be connected with the first housing 410. In
detail, the lens barrel 100 is connected to the first housing 410
through the first elastic member 310. That is, the lens barrel 100
may be movably connected to the first housing 410 by the first
elastic member 310.
In addition, the lens barrel 100 includes a light incident groove,
which is open upward (toward an object). The light incident groove
exposes the lens assembly 200. An image is incident into the lens
assembly 200 through the light incident groove.
The lens assembly 200 is disposed in the lens barrel 100. In
detail, the lens assembly 200 is disposed in the receiving groove.
The lens assembly 200 is inserted into the receiving groove. In
more detail, the outer portion of the lens assembly 200 may have a
circular shape. In more detail, the outer portion of the lens
assembly 200 may have a circular shape when viewed from the top. In
addition, the lens assembly 200 may have a rectangular shape when
viewed from the top.
The lens assembly 200 includes a plurality of lenses 210, 220, 230,
and 240. For instance, the lens assembly 200 may include a first
lens 210, a second lens 220, a third lens 230 and a fourth lens
240. The third lens 230, the second lens 220, and the first lens
210 may be sequentially laminated.
Further, a first spacer and a second spacer may be interposed among
the lenses 210, 220, 230, and 240. The lenses 210, 220, 230, and
240 are spaced apart from each other through the first spacer and
the second spacer.
Although it has been described that the lens assembly 200 includes
four lenses, the embodiment is not limited thereto. That is, the
lens assembly 200 may include one to three lenses or at least five
lenses.
Referring to FIG. 2, the lens assembly 200, the IR cut-off filter
unit 500, and the sensor unit 600 constitute the optical
system.
The first lens 210, the second lens 220, the third lens 230, and
the fourth lens 240 may be sequentially disposed from the object
side to the image side. In order to acquire an image of a subject,
light corresponding to image information of the subject is incident
to the sensor unit 600 by passing through the first lens 210, the
second lens 220, the third lens 230, the fourth lens 240, and the
IR cut-off filter unit 500.
The first lens 210 may have positive (+) refractive power, the
second lens 220 may have negative (-) refractive power, the third
lens 230 may have the positive (+) refractive power, and the fourth
lens 240 may have the negative (-) refractive power. Further, the
first lens 210, the second lens 220, the third lens 230, and the
fourth lens 240 may include glass or plastic.
The first lens 210 has a convex surface at the object side R1
thereof, and the first lens 210 has a convex, concave, flat surface
at the image side R2 thereof. Further, the first lens 210 may have
an aspherical or spherical surface at the object side R1 thereof.
Preferably, the first lens 210 has double-convex surfaces in the
vicinity of an optical axis.
A curvature of the image side R2 of the first lens 210 may satisfy
the following equation 1. 0.ltoreq.R<0.01 Equation 1
In detail, the curvature of the image side R2 of the first lens 210
may satisfy the following equation 7. 0.ltoreq.R<0.001 Equation
7
In more detail, the curvature of the image side R2 of the first
lens 210 may be zero (0).
That is, the image side R2 of the first lens 210 may have a very
small curvature. The image side R2 of the first lens 210 may
include the flat surface. The image side R2 of the first lens 210
may have the flat surface or a curved surface similar to the flat
surface. The image side R2 of the first lens 210 is similar to the
flat surface so that tolerance of a small optical system according
to the embodiment may be reduced.
The second lens 220 may have a meniscus shape. The second lens 220
may have a concave surface at the object side R1 thereof and the
second lens 220 may have a concave surface at the image side R4
thereof. That is, the second lens 220 may have double-concave
shapes. In addition, the second lens 220 may have a spherical or
aspherical surface at the object side R3 and the image side R4
thereof. It is preferable that the second lens 220 has a meniscus
shape where a concave surface is directed to the object side.
The third lens 230 has a convex surface at the image side thereof
in the vicinity of the optical axis and has positive power. For
example, the third lens 230 may have a concave surface at the
object side thereof in the vicinity of the optical axis.
The third lens 230 may have a concave surface at the object side
thereof and have a convex surface at the image side R6 thereof. In
addition, the third lens 230 may have a spherical or aspherical
surface at the object side R5 and the image side R6 thereof.
The focus length of the third lens 230 may satisfy the following
equation 2. 0.5<f3/F<1.0 Equation 2
In Equation 2, f3 represents an effective focal distance of the
third lens 230, and F represents a whole focus distance of a small
optical system according to the embodiment.
In detail, the focus length of the third lens 230 may satisfy the
following equation 4. 0.6<f3/F<0.9 Equation 4
The fourth lens 240 may have a meniscus shape. The fourth lens 240
may have a convex surface at an object side R7 thereof and the
fourth lens 240 may have a concave surface at an image side R8
thereof. In addition, the fourth lens 240 may have an aspherical
surface at the object side R7 and the image side R8 thereof.
Further, the fourth lens 240 includes at least one aspheric
inflection point.
In this case, the at least one aspheric inflection point may be
formed on the object side R7 of the fourth lens 240. In addition,
the at least one aspheric inflection point CP may be formed on the
image side R8 of the fourth lens 240. The aspheric inflection point
of the fourth lens 240 may adjust the maximum radiation angle of a
main light incident into the light receiving device 70.
The focus length of the fourth lens 240 may satisfy the following
equation 3. -10<f4/F<-0.5 Equation 3
In Equation 3, f4 represents an effective focal distance of the
fourth lens 240, and F represents a whole focus distance of a small
optical system according to the embodiment.
In detail, the focus length of the third lens 230 may satisfy the
following equation 5. -1<f4/F<-0.5 Equation 5
If the light receiving device 70 serving as an imaging surface R14
is a charge coupled device (CCD) or a complementary metal oxide
semiconductor (CMOS), an angle to ensure the quantity of light
exists with respect to each pixel. If a different angle is used in
the pixel, the quantity of light is not ensured, a shading
phenomenon in which an outer portion of the image is darkened.
Therefore, the maximum of incident angle of the main ray is
adjusted by forming the aspheric inflection point at the image side
R8 of the fourth lens 240 facing the image side, thereby inhibiting
the outer portion of the image screen from being darkened.
The small optical system may satisfy the following Equation 6.
1<ttl/F<1.3 Equation 6
In Equation 6, ttl represents a distance between the object side of
the first lens 210 and the image side thereof, and F represents the
whole effective focus length.
When the optical system of the embodiment is designed as described
above, the optical system may have a negative distortion. That is,
as shown in FIGS. 3 and 4, the optical system may the negative
distortion.
For example, when a field height is in the range of 0 F to 1.0 F in
the optical system, a distortion of an image of the sensor unit 600
may be in the range of -2% to 0%.
In detail, when the field height is in the range of 0.7 F to 1.0 F
in the optical system, the distortion of an image of the sensor
unit 600 may be in the range of 0% to -2%.
In addition, when the field height is in the range of 0 F to 1.0 F
in the optical system, the distortion of an image of the sensor
unit 600 may be in the range of -2% to -5%.
In detail, when the field height is in the range of 0.7 F to 1.0 F
in the optical system, the distortion of an image of the sensor
unit 600 may be in the range of -2% to -5%.
The first elastic member 310 is disposed in the first housing 410.
The first elastic member 310 is fixed to the first housing 410.
Further, the first elastic member 310 is fixed to the lens barrel
100. The first elastic member 310 movably fixes the lens barrel 100
to the first housing 410.
The first elastic member 310 may include a spring. In detail, the
first elastic member 310 may include a leaf spring.
The first housing 410 receives the lens barrel 100. The first
housing 410 is connected to the lens barrel 100 through the first
elastic member 310.
The first housing 410 may include plastic or metal. The first
housing 410 may have a rectangular container shape.
The second housing 420 receives the first housing 410. That is, the
first housing 410 is disposed in the second housing 420. The first
housing 410 is connected to the second housing 420 by the second
elastic member 320.
The first housing 410 is movably fixed in the second housing 420 by
the second elastic member 320. The first housing 410 may float in
the second housing 420.
The second housing 420 is fixed to the circuit board 800. The
second housing 420 may be coupled with the circuit board 800. The
second housing 420 may include plastic or metal.
The second elastic member 320 is connected to the first housing 410
and the second housing 420. The second elastic member 320 movably
fixes the first housing 410 to the second housing 420. The second
elastic member 320 may include a spring. In detail, the second
elastic member 320 may include a leaf spring.
The IR cut-off filter unit 500 is disposed in the second housing
420. The IR cut-off filter unit 500 is fixed to the circuit board
800 and may be fixed to the second housing 420. The IR cut-off
filter unit 500 filters an incident IR. The IR cut-off filter unit
500 may filter light having an excessively long wavelength
introduced into the sensor unit 600.
The IR cut-off filter unit 500 may be formed by alternately
depositing titanium oxide and silicon oxide on optical glass. In
order to cut-off the IR, thicknesses of the titanium oxide and the
silicon oxide may be suitable adjusted.
The sensor unit 600 is received in the second housing 420. The
sensor unit 600 includes a CCD image sensor and a CMOS image
sensor. In addition, the sensor unit 600 further includes the
circuit board 800 connected to the image sensor. The sensor unit
600 converts an incident image into an electrical signal.
The sensor unit 600 is fixed to the circuit board 800. The sensor
unit 600 may be mounted on the circuit board 800. The sensor unit
600 is electrically connected to the circuit board 800.
A photographing region of the sensor unit 600 may have the size of
2.5 mm.times.4.0 mm. Further, a unit cell of the sensor unit 600
may have length and breadth of 2 .mu.m or less.
The circuit board 800 may cover a bottom of the second housing 420.
The circuit board 800 is coupled with the second housing 420. The
circuit board 800 may include a printed circuit board (PCB). The
circuit board 800 may be electrically connected to the sensor unit
600. The circuit board 800 may apply a signal for driving the
sensor unit 600. Further, the circuit board 800 may receive a
signal from the sensor unit 600.
The sensor unit 600 is mounted on the circuit board 800. In detail,
the sensor unit 600 may be fixed to the circuit board 800. That is,
the sensor unit 600 may be fixed to the second housing 420 through
the circuit board 800.
Further, the circuit board 800 may be electrically connected to the
driving units 710, 720, 730, and 740. That is, a signal for driving
the driving units 710, 720, 730, and 740 may be applied to the
driving units 710, 720, 730, and 740 through the circuit board
800.
The driving units 710, 720, 730, and 740 drive the lens barrel 100
with respect to the first housing 410. The driving units 710, 720,
730, and 740 drive the first housing 410 with respect to the second
housing 420.
The driving units 710, 720, 730, and 740 may move the lens barrel
100 and the first housing 410 by a magnetic force. The driving
units 710, 720, 730, and 740 may include a first driving unit 710,
a second driving unit 720, a third driving unit 730, and a fourth
driving unit 740. The driving units 710, 720, 730, and 740 may move
the lens barrel relative to the housing 400 by a magnetic force. In
this case, the magnetic force may be applied to a direction
inclined with respect to the optical axis OA of the lens assembly
200.
The first driving unit 710 is attached to the lens barrel 100. The
first driving unit 710 may be fixed to the lens barrel 100. The
first driving unit 710 may be disposed at an outer side of the lens
barrel 100.
The first driving unit 710 may include a coil. The first driving
unit 710 may receive a driving signal through the circuit board
800. The first driving unit 710 may generate a magnetic field
according to an electrical signal.
The first driving unit 710 may apply an attractive force or a
repulsive force to the second driving unit 720 in a direction
inclined with respect to a reference horizontal plane. In this
case, the first driving unit 710 may apply the magnetic force to
the second driving unit 720 at an angle of about +20.degree. to
about +70.degree. with respect to the reference horizontal plane.
In detail, the first driving unit 710 may apply the magnetic force
to the second driving unit 720 at an angle of about +30.degree. to
about +50.degree. with respect to the reference horizontal plane
R.
The second driving unit 720 is attached to the first housing 410.
In detail, the second driving unit 720 may be fixed to the first
housing 410. In more detail, the second driving unit 720 may be
fixed to an inner side of the first housing 410.
The second driving unit 720 includes a magnetic material. The
second driving unit 720 may have a plate shape. That is, the second
driving unit 720 may be prepared as a plate magnet.
The first driving unit 710 is close to the second driving unit 720.
The first driving unit 710 may be spaced apart from the second
driving unit 720 by a very small distance. The distance between the
first driving unit 710 and the second driving unit 720 may be in
the range of about 50 .mu.m to about 1000 .mu.m. The first driving
unit 710 may face the second driving unit 720. Accordingly, a
magnetic field may be generated between the first driving unit 710
and the second driving unit 720.
The first driving unit 710 and the second driving unit 720 move the
lens barrel 100 relative to the first housing 410. In detail, the
first driving 710 and the second driving unit 720 may move the lens
barrel 100 relative to the first housing 410 in an optical-axis
direction of the lens assembly 200.
The third driving unit 730 is attached to the first housing 410. In
detail, the third driving unit 730 may be fixed to the first
housing 410. In more detail, the third driving unit 730 may be
fixed to an outer side of the first housing 410.
The third driving unit 730 includes a magnetic material. The third
driving unit 730 may have a plate shape. That is, the third driving
unit 730 may be prepared as a plate magnet.
The fourth driving unit 740 is attached to the second housing 420.
In detail, the fourth driving unit 740 may be fixed to the second
housing 420. In more detail, the fourth driving unit 740 may be
fixed to an inner side of the second housing 420.
The fourth driving unit 740 may include a coil. The fourth driving
unit 740 may receive a driving signal through the circuit board
800. The fourth driving unit 740 may generates a magnetic field
according to an electrical signal.
The third driving unit 730 is close to the fourth driving unit 740.
The third driving unit 730 may be spaced apart from the fourth
driving unit 740 by a very small distance. The distance between the
third driving unit 730 and the fourth driving unit 740 may be in
the range of about 50 .mu.m to about 1000 .mu.m. The third driving
unit 730 may face the fourth driving unit 740. Accordingly, a
magnetic force may be generated between the third driving unit 730
and the fourth driving unit 740.
The third driving unit 730 and the fourth driving unit 740 move the
first housing 410 relative to the second housing 420. In detail,
the third driving 730 and the fourth driving unit 740 may move the
first housing 410 relative to the second housing 420 in a
horizontal direction with respect to an optical axis of the lens
assembly 200.
As a result, the driving units 710, 720, 730, and 740 may move the
lens assembly 200 relative to the sensor unit 600 in the optical
axis direction and in a direction horizontal to the optical
axis.
For example, when the subject is horizontally moved due to shaking,
the first housing 410 may be tilted or horizontally moved by the
third driving unit 730 and the fourth driving unit 740.
Accordingly, a relative horizontal location between the lens
assembly 200 and the sensor 600 may be adjusted.
Further, a focus length between the lens assembly 200 and the
sensor unit 600 may be adjusted by the first driving unit 710 and
the second driving unit 720.
Particularly, since the optical system has a negative distortion,
movement of an image according to shaking in a horizontal direction
is minimized, and accordingly, a compensation error may be
reduced.
That is, as shown in FIG. 5, in the camera module according to the
embodiment, when an image is moved in the sensor unit 600 due to
shaking, the driving units 710, 720, 730, and 740 move the lens
barrel 100 in a direction opposite to a moving direction of the
image. For example, the driving units 710, 720, 730, and 740 move
the image to the initial position by horizontally moving or tilting
the lens barrel 100.
In this case, since the optical system has a negative distortion,
an error of an image according to movement of the lens barrel 100
may be minimized in an outer peripheral portion of the image.
That is, the optical system of the camera module according to the
embodiment has the negative distortion, so it is possible to
inhibit the movement distance of the image from being increased due
to the shaking as the image is located away from the optical
axis.
Particularly, the camera module according to the embodiment can
minimize image shaking at an outer peripheral portion of the
photographing region and maximize a shaking correction effect.
FIG. 6 is a diagram showing a camera module according to another
embodiment. The embodiment will be described by making reference to
the above description of the camera module. The description of the
previous embodiment with respect to the camera module may be
incorporated in the description of the embodiment except for the
modifications.
Referring to FIG. 6, the first housing 410 may be omitted from the
camera module according to the embodiment. Further, a second
housing 420 may be directly connected to the lens barrel 100
through an elastic member. In this case, the elastic member may
connect the lens barrel 110 to the second housing 420 in a
direction inclined with respect to an optical axis of the lens
assembly 200.
Further, a first driving unit 710 is attached to the lens barrel
110. The first driving unit 710 may include a magnetic
material.
In addition, a fourth driving unit 740 is attached to an inner side
of the second housing 420. The fourth driving unit 740 may include
a coil.
A fifth driving unit 750 is attached onto the circuit board 800. In
detail, the fifth driving unit 750 may be interposed between the
first driving unit 710 and the circuit board 800. The fifth driving
unit 750 may include a coil.
Further, the fourth driving unit 740 and the fifth driving unit 750
may be electrically to the circuit board 800.
The lens barrel 100 may be driven in a horizontal direction
perpendicular to the optical axis by a magnetic force between the
first driving unit 710 and the fourth driving unit 740. Moreover,
the lens barrel 100 may be driven in the optical axis direction by
a magnetic force between the first driving unit 710 and the fifth
driving unit 750.
That is, the lens barrel 100 may be driven in the horizontal
direction by the first driving unit 710 and the fourth driving unit
740. Further, the lens barrel 100 may be driven in the optical axis
direction by the first driving unit 710 and the fifth driving unit
750.
The camera module according to the embodiment may correct shaking
and adjust automatic focus by a simple structure.
FIG. 7 is a diagram showing a camera module according to another
embodiment. The embodiment will be described by making reference to
the above description of the camera module. The description of the
previous embodiment with respect to the camera module may be
incorporated in the description of the embodiment except for the
modifications.
Referring to FIG. 7, in the camera module according to the
embodiment, a third driving unit 730 is omitted and a fourth
driving unit 740 may be close to the second driving unit 720. In
detail, the fourth driving unit 740 may be interposed between the
second driving unit 720 and the circuit board 800.
Accordingly, the first housing 410 may be relatively moved
according to an attractive force or a repulsive force between the
second driving unit 720 and the fourth driving unit 740. In detail,
the lens barrel 100 may be driven according to the attractive force
or the repulsive force between the first driving unit 710 and the
second driving unit 720, and the first housing 410 may be driven
according to a magnetic force between the second driving unit 720
and the fourth driving unit 740. That is, the first driving unit
710 may share the second driving unit 720 with the fourth driving
unit 740
Therefore, the camera module according to the embodiment may have
reduced number of components and have the simple structure by
omitting the third driving unit 730.
Any reference in this specification to "one embodiment," "an
embodiment," "example embodiment," etc., means that a particular
feature, structure, or characteristic described in connection with
the embodiment is included in at least one embodiment of the
invention. The appearances of such phrases in various places in the
specification are not necessarily all referring to the same
embodiment. Further, when a particular feature, structure, or
characteristic is described in connection with any embodiment, it
is submitted that it is within the purview of one skilled in the
art to affect such feature, structure, or characteristic in
connection with other ones of the embodiments.
Although embodiments have been described with reference to a number
of illustrative embodiments thereof, it should be understood that
numerous other modifications and embodiments can be devised by
those skilled in the art that will fall within the spirit and scope
of the principles of this disclosure. More particularly, various
variations and modifications are possible in the component parts
and/or arrangements of the subject combination arrangement within
the scope of the disclosure, the drawings and the appended claims.
In addition to variations and modifications in the component parts
and/or arrangements, alternative uses will also be apparent to
those skilled in the art.
* * * * *