U.S. patent number 10,947,884 [Application Number 15/560,684] was granted by the patent office on 2021-03-16 for exhaust purification device and control method for same.
This patent grant is currently assigned to ISUZU MOTORS LIMITED. The grantee listed for this patent is ISUZU MOTORS LIMITED. Invention is credited to Daiji Nagaoka, Teruo Nakada, Takayuki Sakamoto.
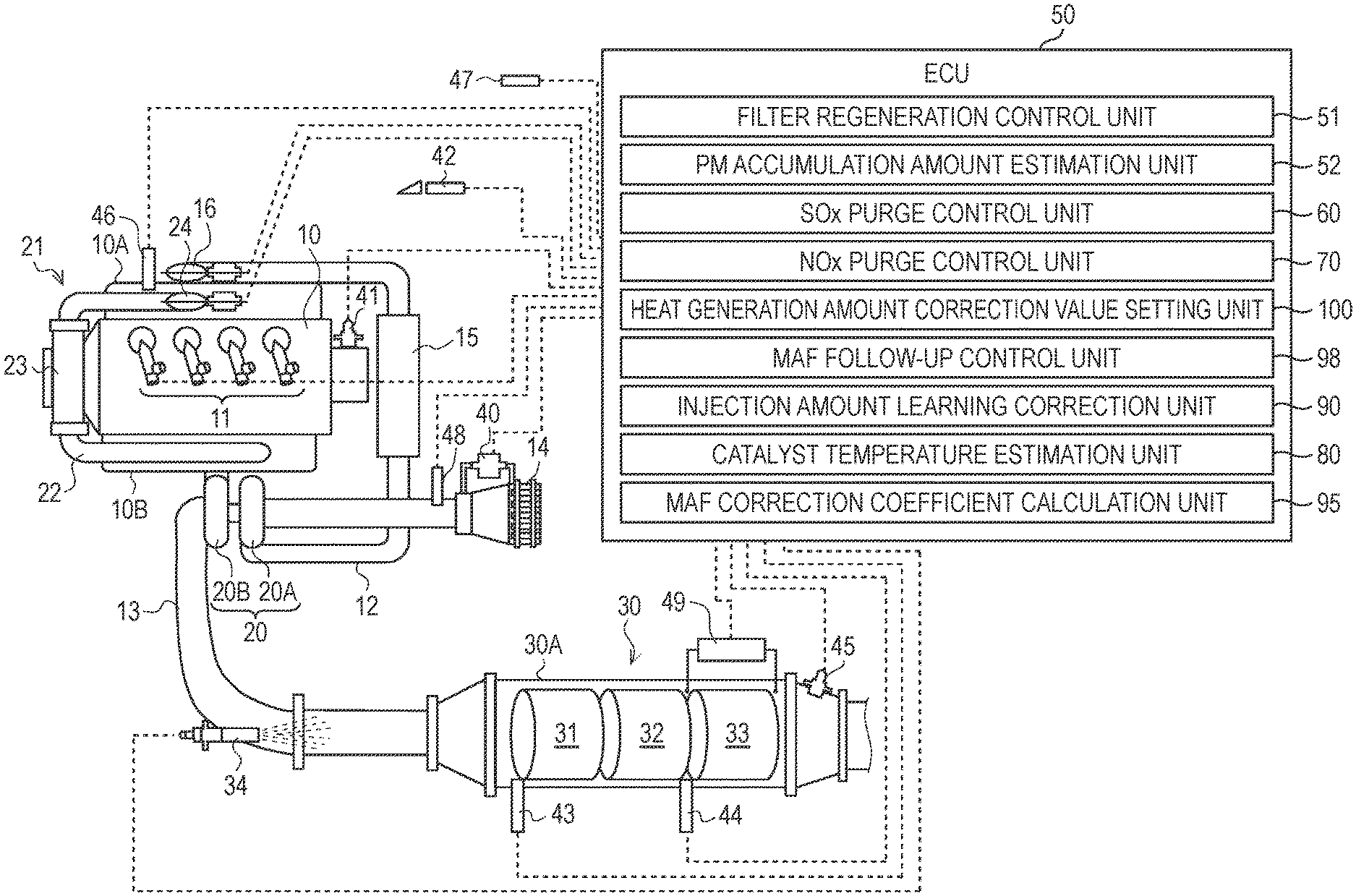










View All Diagrams
United States Patent |
10,947,884 |
Nakada , et al. |
March 16, 2021 |
Exhaust purification device and control method for same
Abstract
The present invention is provided with: a SOx purge control unit
that executes catalyst regeneration processing that maintains the
temperature of a NOx occlusion/reduction catalyst at a prescribed
recovery temperature; a catalyst temperature estimation unit that
estimates catalyst temperature on the basis of the amount of
unburnt fuel contained in exhaust and of a catalyst heat generation
amount; a second exhaust temperature sensor that is arranged
further to an exhaust downstream side than the catalyst and that
detects exhaust temperature; and a heat generation amount
correction value setting unit that, during the execution of the
catalyst regeneration processing, on the basis of an estimated
catalyst temperature estimated by the catalyst temperature
estimation unit and of an actual exhaust temperature detected by
the second exhaust temperature sensor, obtains a heat generation
amount correction value that is used to correct the heat generation
amount of the catalyst.
Inventors: |
Nakada; Teruo (Yokohama,
JP), Sakamoto; Takayuki (Fujisawa, JP),
Nagaoka; Daiji (Kamakura, JP) |
Applicant: |
Name |
City |
State |
Country |
Type |
ISUZU MOTORS LIMITED |
Tokyo |
N/A |
JP |
|
|
Assignee: |
ISUZU MOTORS LIMITED (Tokyo,
JP)
|
Family
ID: |
1000005423910 |
Appl.
No.: |
15/560,684 |
Filed: |
March 23, 2016 |
PCT
Filed: |
March 23, 2016 |
PCT No.: |
PCT/JP2016/059123 |
371(c)(1),(2),(4) Date: |
September 22, 2017 |
PCT
Pub. No.: |
WO2016/152896 |
PCT
Pub. Date: |
September 29, 2016 |
Prior Publication Data
|
|
|
|
Document
Identifier |
Publication Date |
|
US 20180106178 A1 |
Apr 19, 2018 |
|
Foreign Application Priority Data
|
|
|
|
|
Mar 25, 2015 [JP] |
|
|
JP2015-062527 |
|
Current U.S.
Class: |
1/1 |
Current CPC
Class: |
F01N
9/005 (20130101); F01N 9/002 (20130101); F01N
9/00 (20130101); F01N 3/0885 (20130101); F01N
3/0842 (20130101); F01N 3/0814 (20130101); B01D
53/94 (20130101); B01D 53/96 (20130101); F02D
41/04 (20130101); F02D 41/0235 (20130101); F01N
2560/026 (20130101); F01N 2900/1631 (20130101); F01N
2610/03 (20130101); F01N 2560/06 (20130101); F01N
2900/0408 (20130101); F01N 2900/1602 (20130101); F01N
2560/027 (20130101); Y02T 10/40 (20130101); F01N
3/035 (20130101); F01N 3/023 (20130101); F01N
2260/04 (20130101); F01N 2430/06 (20130101); F01N
2900/1404 (20130101) |
Current International
Class: |
F01N
9/00 (20060101); F01N 3/08 (20060101); F02D
41/02 (20060101); B01D 53/94 (20060101); B01D
53/96 (20060101); F02D 41/04 (20060101); F01N
3/035 (20060101); F01N 3/023 (20060101) |
References Cited
[Referenced By]
U.S. Patent Documents
Foreign Patent Documents
|
|
|
|
|
|
|
2578833 |
|
Apr 2013 |
|
EP |
|
2005-133703 |
|
May 2005 |
|
JP |
|
2008-202425 |
|
Sep 2008 |
|
JP |
|
2009-047086 |
|
Mar 2009 |
|
JP |
|
2009517599 |
|
Apr 2009 |
|
JP |
|
2011-99398 |
|
May 2011 |
|
JP |
|
2012-202271 |
|
Oct 2012 |
|
JP |
|
2014-218982 |
|
Nov 2014 |
|
JP |
|
2007063406 |
|
Jun 2007 |
|
WO |
|
Other References
Notification of Reasons for Refusal for related JP App No.
2015-062527 dated Oct. 9, 2018, 8 pgs. cited by applicant .
International Search Report and Written Opinion for PCT App No.
PCT/JP2016/059123 dated Jun. 28, 2016, 9 pgs. cited by applicant
.
Extended European Search Report for related EP App No. 16768799.5
dated Aug. 2, 2018, 7 pgs. cited by applicant.
|
Primary Examiner: Wongwian; Phutthiwat
Assistant Examiner: Tran; Diem T
Attorney, Agent or Firm: Procopio, Cory, Hargreaves &
Savitch LLP
Claims
The invention claimed is:
1. An exhaust purification device comprising: a catalyst provided
in an exhaust system of an internal combustion engine and
configured to generate heat and to purify an exhaust by unburnt
fuel in the exhaust; an exhaust temperature detector that is
arranged at a further exhaust downstream side than the catalyst and
detects an exhaust temperature emitted from the catalyst; a filter
provided in the exhaust system of the internal combustion engine
and configured to trap particulate matters in the exhaust; and an
electronic control unit operated to execute: a catalyst
regeneration processing of recovering a purification capacity of
the catalyst by maintaining a temperature of the catalyst at a
recovery temperature; estimating a temperature of the catalyst on
the basis of an amount of the unburnt fuel contained in the exhaust
and a heat generation amount of the catalyst; a filter regeneration
processing of combusting and removing the particulate matters
accumulated in the filter by maintaining the filter at a combustion
temperature of the particulate matters; obtaining a heat generation
amount correction value, which is used to correct the heat
generation amount of the catalyst, on the basis of the estimated
temperature of the catalyst and an actual exhaust temperature
detected by the exhaust temperature detector during implementation
of the catalyst regeneration processing and during implementation
of the filter regeneration processing; and a pseudo regeneration
processing of maintaining the temperature of the catalyst at a
pseudo regeneration temperature lower than the recovery temperature
of the catalyst and lower than the combustion temperature of the
particulate matters in the filter regeneration processing before at
least one of a first-time catalyst regeneration processing and a
first-time filter regeneration processing is implemented, wherein
an initial value of the heat generation amount correction value is
obtained when the pseudo regeneration processing is over.
2. The exhaust purification device according to claim 1, wherein
the catalyst is a NOx reduction-type catalyst configured to reduce
and purify NOx in the exhaust and to recover from sulfur poisoning
as the catalyst is maintained at a sulfur separation temperature,
and wherein the catalysts regeneration processing implements a
catalyst regeneration control of recovering the NOx reduction-type
catalyst from the sulfur poisoning by increasing an exhaust
temperature of the internal combustion engine to the sulfur
separation temperature.
3. A control method of an exhaust purification device comprising a
catalyst provided in an exhaust system of an internal combustion
engine and configured to generate heat and to purify an exhaust by
unburnt fuel in the exhaust, and an exhaust temperature detection
sensor arranged at a further exhaust downstream side than the
catalyst and configured to detect an exhaust temperature emitted
from the catalyst, the method comprising: a catalyst regeneration
processing of recovering a purification capacity of the catalyst by
maintaining a temperature of the catalyst at a recovery
temperature; a catalyst temperature estimation processing of
estimating the temperature of the catalyst on the basis of an
amount of the unburnt fuel contained in the exhaust and a heat
generation amount of the catalyst; an exhaust temperature detection
processing of detecting an exhaust temperature emitted from the
catalyst at a further downstream side than the catalyst; a filter
regeneration processing of combusting and removing particulate
matters accumulated in a filter by maintaining the filter at a
combustion temperature of the particulate matters, the filter
provided in the exhaust system of the internal combustion engine
and configured to trap the particulate matters in the exhaust; a
correction value obtaining processing of obtaining a heat
generation amount correction value, which is used to correct the
heat generation amount of the catalyst, on the basis of an
estimated catalyst temperature estimated by the catalyst
temperature estimation processing and an actual exhaust temperature
detected by the exhaust temperature detection sensor during
implementation of the catalyst regeneration processing and during
implementation of the filter regeneration processing; and
performing a pseudo regeneration processing by maintaining the
temperature of the catalyst at a pseudo regeneration temperature
lower than the recovery temperature of the catalyst and lower than
the combustion temperature of the particulate matters in the filter
regeneration processing before at least one of a first-time
catalyst regeneration processing and a first-time filter
regeneration processing is implemented, wherein the correction
value obtaining processing obtains an initial value of the heat
generation amount correction value when the pseudo regeneration
processing is over.
Description
CROSS-REFERENCE TO RELATED APPLICATIONS
This application is a U.S. National Stage entry of PCT Application
No. PCT/JP2016/059123, filed on Mar. 23, 2016, which claims
priority to Japanese Patent Application No. 2015-062527, filed Mar.
25, 2015, the contents of which are incorporated herein by
reference.
TECHNICAL FIELD
The present invention relates to an exhaust purification device and
a control method thereof.
BACKGROUND ART
In the related art, a NOx-occlusion-reduction-type catalyst has
been known, as catalyst for reducing and purifying nitrogen
compound (NOx) in the exhaust to be emitted from an internal
combustion engine. When the exhaust is in a lean atmosphere, the
NOx-occlusion-reduction-type catalyst occludes NOx contained in the
exhaust, and when the exhaust is in a rich atmosphere, the
NOx-occlusion-reduction-type catalyst detoxifies and releases the
occluded NOx with hydrocarbon contained in the exhaust by reduction
and purification. For this reason, when a NOx occlusion amount of
the catalyst reaches a predetermined amount, it is necessary to
periodically perform NOx purge of enriching the exhaust by post
injection or exhaust pipe injection so as to recover a NOx
occlusion capacity (for example, refer to PTL 1).
Also, sulfur oxide (SOx) contained in the exhaust is occluded in
the NOx-occlusion-reduction-type catalyst. When a SOx occlusion
amount increases, a NOx purification capacity of the
NOx-occlusion-reduction-type catalyst is deteriorated. For this
reason, when the SOx occlusion amount reaches a predetermined
amount (sulfur poisoning), it is necessary to periodically perform
SOx purge of supplying unburnt fuel to an upstream oxidation
catalyst to increase an exhaust temperature to a SOx separation
temperature by post injection or exhaust pipe injection so as to
separate SOx from the NOx-occlusion-reduction-type catalyst for
recovery from the sulfur poisoning (for example, refer to PTL
2).
CITATION LIST
Patent Documents
PTL 1: JP2008-202425A
PTL 2: JP2009-047086A
SUMMARY OF INVENTION
Technical Problem
In general, in the above type of the device, when performing the
NOx purge or SOx purge, an amount of the unburnt fuel corresponding
to a deviation between an estimated temperature and a target
temperature of the NOx-occlusion-reduction-type catalyst is
supplied. When estimating a catalyst temperature, a heat generation
amount of the catalyst is used. However, there is an individual
difference in the heat generation amount of the catalyst. Also, the
heat generation amount of the catalyst gradually decreases due to
aging degradation. In order to secure estimation accuracy of the
catalyst temperature, it is required to obtain the heat generation
amount of the catalyst as correct as possible.
An exhaust purification device and a control method thereof of the
disclosure are to improve estimation accuracy of a catalyst
temperature.
Solution to Problem
An exhaust purification device of the disclosure includes a
catalyst provided in an exhaust system of an internal combustion
engine and configured to generate heat and to purify an exhaust by
unburnt fuel in the exhaust, a catalyst regeneration means for
implementing catalyst regeneration processing of recovering a
purification capacity of the catalyst by maintaining a temperature
of the catalyst at a predetermined recovery temperature, a catalyst
temperature estimation means for estimating a temperature of the
catalyst on the basis of an amount of the unburnt fuel contained in
the exhaust and a heat generation amount of the catalyst, an
exhaust temperature detection means that is arranged at a further
exhaust downstream side than the catalyst and detects an exhaust
temperature emitted from the catalyst, and a correction value
obtaining means for, during implementation of the catalyst
regeneration processing by the catalyst regeneration means,
obtaining a heat generation amount correction value, which is used
to correct the heat generation amount of the catalyst, on the basis
of an estimated catalyst temperature estimated by the catalyst
temperature estimation means and an actual exhaust temperature
detected by the exhaust temperature detection means.
Also, an exhaust purification device of the disclosure is an
exhaust purification device including a catalyst provided in an
exhaust system of an internal combustion engine and configured to
generate heat and to purify an exhaust by unburnt fuel in the
exhaust, an exhaust temperature detection sensor arranged at a
further exhaust downstream side than the catalyst and configured to
detect an exhaust temperature emitted from the catalyst, and a
control unit, wherein the control unit is configured to
execute:
catalyst regeneration processing of recovering a purification
capacity of the catalyst by maintaining a temperature of the
catalyst at a predetermined recovery temperature,
catalyst temperature estimation processing of estimating the
temperature of the catalyst on the basis of an amount of the
unburnt fuel contained in the exhaust and a heat generation amount
of the catalyst, and
correction value obtaining processing of, during implementation of
the catalyst regeneration processing, obtaining a heat generation
amount correction value, which is used to correct the heat
generation amount of the catalyst, on the basis of an estimated
catalyst temperature estimated by the catalyst temperature
estimation processing and an actual exhaust temperature detected by
the exhaust temperature detection sensor.
Also, a control method of an exhaust purification device of the
disclosure is a control method of an exhaust purification device
including a catalyst provided in an exhaust system of an internal
combustion engine and configured to generate heat and to purify the
exhaust by unburnt fuel in exhaust and an exhaust temperature
detection sensor arranged at a further exhaust downstream side than
the catalyst and configured to detect an exhaust temperature
emitted from the catalyst. The method includes:
catalyst regeneration processing of recovering a purification
capacity of the catalyst by maintaining a temperature of the
catalyst at a predetermined recovery temperature,
catalyst temperature estimation processing of estimating the
temperature of the catalyst on the basis of an amount of the
unburnt fuel contained in the exhaust and a heat generation amount
of the catalyst,
exhaust temperature detection processing of detecting an exhaust
temperature emitted from the catalyst at a further downstream side
than the catalyst, and
correction value obtaining processing of, during implementation of
the catalyst regeneration processing, obtaining a heat generation
amount correction value, which is used to correct the heat
generation amount of the catalyst, on the basis of an estimated
catalyst temperature estimated by the catalyst temperature
estimation processing and an actual exhaust temperature detected by
the exhaust temperature detection sensor.
Advantageous Effects of Invention
According to the exhaust purification device and the control method
thereof of the disclosure, it is possible to improve the estimation
accuracy of the catalyst temperature.
BRIEF DESCRIPTION OF DRAWINGS
FIG. 1 is an overall configuration view depicting an exhaust
purification system in accordance with an illustrative
embodiment.
FIG. 2 is a timing chart diagram for illustrating SOx purge control
in accordance with the illustrative embodiment.
FIG. 3 is a block diagram depicting setting processing of an MAF
target value upon SOx purge lean control in accordance with the
illustrative embodiment.
FIG. 4 is a block diagram depicting setting processing of a target
injection amount upon SOx purge rich control in accordance with the
illustrative embodiment.
FIG. 5 is a timing chart diagram for illustrating catalyst
temperature regulation control of SOx purge control in accordance
with the illustrative embodiment.
FIG. 6 is a timing chart diagram for illustrating NOx purge control
in accordance with the illustrative embodiment.
FIG. 7 is a block diagram depicting setting processing of an MAF
target value upon NOx purge lean control in accordance with the
illustrative embodiment.
FIG. 8 is a block diagram depicting setting processing of a target
injection amount upon NOx purge rich control in accordance with the
illustrative embodiment.
FIG. 9A is a block diagram depicting setting processing of a heat
generation amount correction value in accordance with the
illustrative embodiment.
FIG. 9B illustrates temporal change of a catalyst heat generation
amount and an estimated heat generation amount after
correction.
FIG. 10 is a flowchart depicting setting processing of the heat
generation amount correction value in accordance with the
illustrative embodiment.
FIG. 11 is a block diagram depicting injection amount learning
correction processing of an injector in accordance with the
illustrative embodiment.
FIG. 12 is a flowchart depicting learning correction coefficient
calculation processing in accordance with the illustrative
embodiment.
FIG. 13 is a block diagram depicting catalyst temperature
estimation processing in accordance with the illustrative
embodiment.
FIG. 14 is a block diagram depicting setting processing of an MAF
correction coefficient in accordance with the embodiment.
DESCRIPTION OF EMBODIMENTS
Hereinafter, an exhaust purification system in accordance with an
illustrative embodiment of the disclosure will be described with
reference to the accompanying drawings. As shown in FIG. 1, each
cylinder of a Diesel engine (hereinafter, simply referred to as
`engine`) 10 is provided with an in-cylinder injector 11 configured
to directly inject high-pressure fuel accumulated to a common rail
(not shown) into each cylinder. A fuel injection amount and fuel
injection timing of each in-cylinder injector 11 are controlled in
correspondence to instruction signals that are input from an
electronic control unit (hereinafter, referred to as `ECU`) 50.
An intake manifold 10A of the engine 10 is connected with an intake
passage 12 for introducing therein fresh air, and an exhaust
manifold 10B is connected with an exhaust passage 13 for
discharging exhaust to an outside. The intake passage 12 is
provided with an air cleaner 14, an intake air amount sensor
(hereinafter, referred to as `MAF sensor`) 40, an intake
temperature sensor 48, a compressor 20A of a variable capacity-type
supercharger 20, an intercooler 15, an intake throttle valve 16 and
the like, in corresponding order from an intake upstream side. The
exhaust passage 13 is provided with a turbine 20B of the variable
capacity-type supercharger 20, an exhaust after-treatment device 30
and the like, in corresponding order from an exhaust upstream side.
In the meantime, the engine 10 is mounted with an engine revolution
sensor 41, an accelerator opening degree sensor 42, a boost
pressure sensor 46 and an exterior air temperature sensor 47.
In the description of the illustrative embodiment, the MAF sensor
40 configured to measure and detect a mass flow rate (Mass Air
Flow) is used as the sensor configured to measure and detect an
intake air amount (intake flow rate (Suction Air Flow)) of the
engine. However, a flow rate (air flow) sensor different from the
MAF sensor 40 or a means replacing the flow rate sensor can also be
used inasmuch as it can measure and detect the intake flow rate of
the engine.
An EGR (Exhaust Gas Recirculation) device 21 includes an EGR
passage 22 configured to connect the exhaust manifold 10B and the
intake manifold 10A each other, an EGR cooler 23 configured to
cools an EGR gas, and an EGR valve 24 configured to regulate an EGR
amount.
The exhaust after-treatment device 30 includes an oxidation
catalyst 31, a NOx-occlusion-reduction-type catalyst 32 and a
particulate filter (hereinafter, simply referred to as `filter`)
33, which are arranged in a case 30A in corresponding order from
the exhaust upstream side. Also, the exhaust passage 13 positioned
further upstream than the oxidation catalyst 31 is provided with an
exhaust injector 34 configured to inject unburnt fuel (mainly,
hydrocarbon (HC)) into the exhaust passage 13, in response to an
instruction signal input from the ECU 50.
The oxidation catalyst 31 is formed by carrying an oxidation
catalyst component on a surface of a ceramic carrier such as a
honeycomb structure, for example. When the unburnt fuel is supplied
by post injection of the exhaust injector 34 or the in-cylinder
injector 11, the oxidation catalyst 31 oxidizes the same to
increase an exhaust temperature.
The NOx-occlusion-reduction-type catalyst 32 is formed by carrying
alkali metal or the like on a surface of a ceramic carrier such as
a honeycomb structure, for example. The
NOx-occlusion-reduction-type catalyst 32 occludes NOx in the
exhaust when the exhaust air-fuel ratio is in a lean state, and
reduces and purifies the occluded NOx with a reducing agent (HC or
the like) included in the exhaust when the exhaust air-fuel ratio
is in a rich state.
The filter 33 is formed by arranging a plurality of cells, which
are divided by a porous partition wall, along a flowing direction
of the exhaust and alternately plugging upstream and downstream
sides of the cells, for example. The filter 33 is configured to
trap particulate matters (PM) in the exhaust in fine holes or
surfaces of the partition wall, and when an estimated PM
accumulation amount reaches a predetermined amount, so-called
filter forced regeneration of combusting and removing the
accumulated PM is executed. The filter forced regeneration is
performed by supplying the unburnt fuel to the upstream oxidation
catalyst 31 by the exhaust pipe injection or the post injection and
increasing a temperature of the exhaust to be introduced to the
filter 33 to a PM combustion temperature.
A first exhaust temperature sensor 43 is provided further upstream
than the oxidation catalyst 31 and is configured to detect a
temperature of the exhaust to be introduced into the oxidation
catalyst 31. A second exhaust temperature sensor 44 is an example
of the exhaust temperature detection means of the disclosure and is
provided at a further exhaust downstream side than the
NOx-occlusion-reduction-type catalyst 32 and at a further exhaust
upstream side than the filter 33. The second exhaust temperature
sensor 44 is configured to detect a temperature of the exhaust to
be introduced into the filter 33 immediately after emitted from the
NOx-occlusion-reduction-type catalyst 32. In the illustrative
embodiment, since the NOx-occlusion-reduction-type catalyst 32 and
the filter 33 are arranged closely to each other, the exhaust
temperature that is to be detected by the second exhaust
temperature sensor 44 is substantially the same as a temperature of
the NOx-occlusion-reduction-type catalyst 32.
A NOx/lambda sensor 45 is provided further downstream than the
filter 33, and is configured to detect a NOx value and a lambda
value (hereinafter, referred to as `air excess ratio`) of the
exhaust having passed through the NOx-occlusion-reduction-type
catalyst 32.
A differential pressure sensor 49 is a sensor configured to detect
a differential pressure between an upstream side and a downstream
side of the filter 33. A detection signal of the differential
pressure sensor 49 is output to the ECU 50. The differential
pressure sensor 49 and a PM accumulation amount estimation unit 52
(which will be described later) of the ECU 50 are examples of the
accumulation amount estimation means.
The ECU 50 is configured to perform a variety of controls of the
engine 10 and the like and includes a CPU, a ROM, a RAM, an input
port, an output port and the like, which are well known. In order
to perform the diverse controls, the ECU 50 is input with sensor
values of the sensors 40 to 45. Also, the ECU 50 has, as some
functional elements, a filter regeneration control unit 51, a PM
accumulation amount estimation unit 52, a SOx purge control unit
60, a NOx purge control unit 70, a heat generation amount
correction value setting unit 100, an MAF follow-up control unit
98, an injection amount learning correction unit 90, a catalyst
temperature estimation unit 80 and an MAF correction coefficient
calculation unit 95. The functional elements are included in the
ECU 50, which is the integral hardware. However, some of the
functional elements may be provided in separate hardware.
[Filter Regeneration Control]
The filter regeneration control unit 51 is an example of the filter
regeneration means of the disclosure and is configured to implement
filter regeneration processing of combusting and removing PM
accumulated in the filter 33. The filter regeneration control unit
51 sets a filter forced regeneration flag F.sub.DPF to an on-state
(refer to time t.sub.1 in FIG. 2) when an estimated PM accumulation
amount obtained from the PM accumulation amount estimation unit 52
exceeds a predetermined upper limit threshold value. When the
filter forced regeneration flag F.sub.DPF becomes on, an
instruction signal for executing exhaust pipe injection is
transmitted to the exhaust injector 34 or an instruction signal for
executing post injection is transmitted to each in-cylinder
injector 11. Thereby, the exhaust temperature is increased to a PM
combustion temperature (for example, about 550.degree. C.), and the
temperature-increased state is maintained. The filter forced
regeneration flag F.sub.DPF becomes off (refer to time t.sub.2 in
FIG. 2) when the estimated PM accumulation amount is lowered to a
predetermined lower limit threshold value (determination threshold
value) indicative of combustion removal. An injection amount
instruction value (hereinafter, referred to as `filter regeneration
post injection amount instruction value Q.sub.DPF_Post_Trgt`),
which is used when the filter forced regeneration is implemented by
the post injection, is transmitted to the catalyst temperature
estimation unit 80, too, which will be described in detail later,
so as to estimate a catalyst heat generation amount.
[PM Accumulation Amount Estimation]
The PM accumulation amount estimation unit (an example of the
filter accumulation amount estimation means) 52 is configured to
estimate a PM accumulation amount trapped in the filter 33. The PM
accumulation amount estimation unit 52 has a differential pressure
characteristic map (not shown), which is obtained in advance by a
test and the like and indicates a relation between a front-rear
differential pressure of the filter 33 and a PM accumulation
amount. The PM accumulation amount estimation unit is configured to
calculate and estimate a PM accumulation amount trapped in the
filter 33 on the basis of the differential pressure characteristic
map and a level of a detection signal of the differential pressure
sensor 49. In the meantime, the estimation of the PM accumulation
amount in the filter 33 is not limited to the differential pressure
sensor 49, and the other method can also be adopted. For example,
the PM accumulation amount may be estimated on the basis of a
traveling distance of a vehicle and may be detected by an
electrostatic capacitance-type or resistance-type PM sensor.
[SOx Purge Control]
The SOx purge control unit 60 is an example of the catalyst
regeneration means of the disclosure and is configured to implement
catalyst regeneration processing of enriching the exhaust,
increasing the exhaust temperature to a sulfur separation
temperature (for example, about 600.degree. C.), maintaining the
sulfur separation temperature for a predetermined time period and
recovering the NOx-occlusion-reduction-type catalyst 32 from the
SOx poisoning (sulfur poisoning) (hereinafter, the control for
implementing the catalyst regeneration processing is referred to as
`SOx purge control`).
FIG. 2 is a timing chart of the SOx purge control in accordance
with the illustrative embodiment. As shown in FIG. 2, a SOx purge
flag F.sub.SP for starting the SOx purge control becomes on at the
same time when the filter forced regeneration flag F.sub.DPF
becomes off (refer to time t.sub.2 in FIG. 2). Thereby, the control
can be effectively shifted to the SOx purge control from a state
where the exhaust temperature has been increased by the forced
regeneration of the filter 33, so that the fuel consumption can be
effectively reduced.
In the illustrative embodiment, the enriching of the exhaust by the
SOx purge control is implemented by concurrently using SOx purge
lean control of lowering an air excess ratio from a value (for
example, about 1.5) upon normal operation to a first target air
excess ratio (for example, about 1.3) closer to a lean side than a
theoretical air-fuel ratio equivalent value (about 1.0) by air
system control and SOx purge rich control of lowering the air
excess ratio from the first target air excess ratio to a second
target air excess ratio (for example, about 0.9) of a rich side by
injection system control. Hereinafter, the SOx purge lean control
and the SOx purge rich control are described in detail.
[Air System Control of SOx Purge Lean Control]
FIG. 3 is a block diagram depicting setting processing of an MAF
target value MAF.sub.SPL_Trgt upon SOx purge lean control. A first
target air excess ratio setting map 61 is a map that is to be
referred to on the basis of an engine revolution Ne and an
accelerator opening degree Q (a fuel injection amount of the engine
10), and an air excess ratio target value .lamda..sub.SPL_Trgt
(first target air excess ratio) upon SOx purge lean control
corresponding to the engine revolution Ne and the accelerator
opening degree Q is set in advance by a test and the like.
First, the air excess ratio target value .lamda..sub.SPL_Trgt upon
SOx purge lean control is read from the first target air excess
ratio setting map 61, in response to the engine revolution Ne and
the accelerator opening degree Q, which are input signals, and is
then input to an MAF target value calculation unit 62. Also, the
MAF target value calculation unit 62 calculates an MAF target value
MAF.sub.SPL_Trgt upon SOx purge lean control, based on an equation
(1).
MAF.sub.SPL_Trgt=.lamda..sub.SPL_Trgt.times.Q.sub.fnl_corrd.times.Ro.sub.-
Fuel.times.AFR.sub.sto/Maf.sub._corr (1) In the equation (1),
Q.sub.fnl_corrd indicates a learning-corrected fuel injection
amount (the post injection is excluded) (which will be described
later), Ro.sub.Fuel indicates a fuel specific gravity, AFR.sub.sto
indicates a theoretical air-fuel ratio, and Maf.sub._corr indicates
an MAF correction coefficient (which will be described later).
The MAF target value MAF.sub.SPL_Trgt calculated by the MAF target
value calculation unit 62 is input to a ramp processing unit 63
when the SOx purge flag F.sub.SP becomes on (refer to time t.sub.2
in FIG. 2). The ramp processing unit 63 is configured to read a
ramp coefficient from each of ramp coefficient maps 63A, 63B, in
response to the engine revolution Ne and the accelerator opening
degree Q, which are input signals, and to input an MAF target ramp
value MAF.sub.SPL_Trgt_Ramp to which the ramp coefficient is added
to a valve control unit 64.
The valve control unit 64 is configured to execute feedback control
of narrowing the intake throttle valve 16 towards a close side and
widening the EGR valve 24 towards an open side so that an actual
MAF value MAF.sub.Act input from the MAF sensor 40 becomes the MAF
target ramp value MAF.sub.SPL_Trgt_Ramp.
In this way, in the illustrative embodiment, the MAF target value
MAF.sub.SPL_Trgt is set on the basis of the air excess ratio target
value .lamda..sub.SPL_Trgt, which is to be read from the first
target air excess ratio setting map 61, and the fuel injection
amount of each in-cylinder injector 11, and the air system
operation is controlled in the feedback manner on the basis of the
MAF target value MAF.sub.SPL_Trgt. Thereby, it is possible to
effectively lower the exhaust to a desired air excess ratio
necessary for the SOx purge lean control without providing a lambda
sensor at the upstream side of the NOx-occlusion-reduction-type
catalyst 32 or without using a sensor value of a lambda sensor even
when the lambda sensor is provided at the upstream side of the
NOx-occlusion-reduction-type catalyst 32.
Also, the fuel injection amount Q.sub.fnl_corrd after the learning
correction is used as the fuel injection amount of each in-cylinder
injector 11, so that it is possible to set the MAF target value
MAF.sub.SPL_Trgt in the feed-forward control manner. Therefore, it
is possible to effectively exclude influences such as aging
degradation, characteristic change and individual difference of
each in-cylinder injector 11.
Also, the ramp coefficient, which is to be set in correspondence to
the operating state of the engine 10, is added to the MAF target
value MAF.sub.SPL_Trgt, so that it is possible to effectively
prevent accident fire of the engine 10 due to a rapid change in the
intake air amount, deterioration of drivability due to torque
variation, and the like.
[Setting of Fuel Injection Amount in SOx Purge Rich Control]
FIG. 4 is a block diagram depicting setting processing of a target
injection amount Q.sub.SPR_Trgt (injection amount per unit time) of
the exhaust pipe injection or the post injection upon the SOx purge
rich control. A second target air excess ratio setting map 65 is a
map that is to be referred to on the basis of the engine revolution
Ne and the accelerator opening degree Q, and an air excess ratio
target value .lamda..sub.SPR_Trgt (second target air excess ratio)
upon SOx purge rich control corresponding to the engine revolution
Ne and the accelerator opening degree Q is set in advance by a test
and the like.
First, the air excess ratio target value .lamda..sub.SPR_Trgt upon
SOx purge rich control is read from the second target air excess
ratio setting map 65, in response to the engine revolution Ne and
the accelerator opening degree Q, which are input signals, and is
then input to an injection amount target value calculation unit 66.
Also, the injection amount target value calculation unit 66
calculates a target injection amount instruction value
Q.sub.SPR_Trgt upon SOx purge rich control, based on an equation
(2).
Q.sub.SPR_Trgt=MAF.sub.SPL_Trgt.times.Maf.sub._corr/(.lamda..sub.SPR_Trgt-
.times.Ro.sub.Fuel.times.AFR.sub.sto)-Q.sub.fnl_corrd (2) In the
equation (2), MAF.sub.SPL_Trgt is input from the MAF target value
calculation unit 62, as an MAF target value upon SOx purge lean.
Also, Q.sub.fnl_corrd indicates a learning-corrected fuel injection
amount (the post injection is excluded) before an MAF follow-up
control is applied (which will be described later), Ro.sub.Fuel
indicates a fuel specific gravity, AFR.sub.sto indicates a
theoretical air-fuel ratio, and Maf.sub._corr indicates an MAF
correction coefficient (which will be described later).
The target injection amount instruction value Q.sub.SPR_Trgt
calculated by the injection amount target value calculation unit 66
is transmitted to the exhaust injector 34 or each in-cylinder
injector 11, as an injection instruction signal, when a SOx purge
flag F.sub.SPR (which will be described later) becomes on
(hereinafter, an injection amount instruction value of the post
injection to be transmitted to the in-cylinder injector 11 is
referred to as `SOx purge rich/post injection amount instruction
value Q.sub.SPR_Post_Trgt`). The SOx purge rich/post injection
amount instruction value Q.sub.SPR_Post_Trgt is transmitted to the
catalyst temperature estimation unit 80 (which will be described in
detail later), too, so as to estimate a catalyst heat generation
amount.
In this way, in the illustrative embodiment, the target injection
amount instruction value Q.sub.SPR_Trgt is set on the basis of the
air excess ratio target value .lamda..sub.SPR_Trgt, which is to be
read from the second target air excess ratio setting map 65, and
the fuel injection amount of each in-cylinder injector 11. Thereby,
it is possible to effectively lower the exhaust to a desired air
excess ratio necessary for the SOx purge rich control without
providing a lambda sensor at the upstream side of the
NOx-occlusion-reduction-type catalyst 32 or without using a sensor
value of a lambda sensor even when the lambda sensor is provided at
the upstream side of the NOx-occlusion-reduction-type catalyst
32.
Also, the fuel injection amount Q.sub.fnl_corrd after the learning
correction is used as the fuel injection amount of each in-cylinder
injector 11, so that it is possible to set the target injection
amount instruction value Q.sub.SPR_Trgt in the feed-forward control
manner. Therefore, it is possible to effectively exclude influences
such as aging degradation and characteristic change of each
in-cylinder injector 11.
[Catalyst Temperature Regulation Control in SOx Purge Control]
The exhaust temperature (hereinafter, also referred to as `catalyst
temperature`) to be introduced into the
NOx-occlusion-reduction-type catalyst 32 during the SOx purge
control is controlled by alternately switching on/off states
(rich/lean) of a SOx purge rich flag F.sub.SPR for executing the
exhaust pipe injection or the post injection, as shown at time
t.sub.2 to t.sub.4 in FIG. 2. When the SOx purge rich flag
F.sub.SPR becomes on (F.sub.SPR=1), the catalyst temperature is
increased by the exhaust pipe injection or the post injection
(hereinafter, the corresponding time period is referred to as
`injection time period T.sub.F_INJ`). On the other hand, when the
SOx purge rich flag F.sub.SPR becomes off, the catalyst temperature
is decreased by stop of the exhaust pipe injection or the post
injection (hereinafter, the corresponding time period is referred
to as `interval T.sub.F_INT`).
In the illustrative embodiment, the injection time period
T.sub.F_INJ is set by reading a value corresponding to the engine
revolution Ne and the accelerator opening degree Q from an
injection time period setting map (not shown) prepared in advance
by a test and the like. In the injection time period setting map,
an injection time period, which is required to securely lower the
air excess ratio of the exhaust obtained in advance by a test and
the like to the second target air excess ratio, is set in
correspondence to the operating state of the engine 10.
The interval T.sub.F_INT is set by feedback control when the SOx
purge rich flag F.sub.SPR is switched from the on-state, at which
the catalyst temperature is highest, to the off-state.
Specifically, the interval is processed by PID control consisting
of proportional control of changing an input signal in proportion
to a deviation .DELTA.T between a catalyst target temperature when
the SOx purge rich flag F.sub.SPR becomes off and an estimated
catalyst temperature, integral control of changing an input signal
in proportion to a time integral value of the deviation .DELTA.T
and derivative control of changing an input signal in proportion to
a time derivative value of the deviation .DELTA.T. The catalyst
target temperature is set to a temperature at which SOx can be
separated from the NOx-occlusion-reduction-type catalyst 32, and
the estimated catalyst temperature is set by any one of an
oxidation catalyst temperature, which is appropriately selected by
a reference temperature selection unit 88 (refer to FIG. 13) (which
will be described in detail later)), and a NOx catalyst
temperature.
As shown at time t.sub.1 in FIG. 5, when the SOx purge flag
F.sub.SP becomes on as the filter forced regeneration is ended
(F.sub.DPF=0), the SOx purge rich flag F.sub.SPR becomes on, too,
so that the interval T.sub.F_INT calculated in the feedback manner
upon previous SOx purge control is once reset. That is, at
first-time control immediately after the filter forced
regeneration, the exhaust pipe injection or the post injection is
executed (refer to time t.sub.1 to t.sub.2 in FIG. 5), in
correspondence to the injection time period T.sub.F_INJ_1 set by
the injection time period setting map. In this way, since the SOx
purge control is started from the SOx purge rich control without
performing the SOx purge lean control, the control is rapidly
shifted to the SOx purge control without lowering the exhaust
temperature, which has been increased by the filter forced
regeneration, so that it is possible to reduce the fuel
consumption.
Then, when the SOx purge rich flag F.sub.SPR becomes off as the
injection time period T.sub.F_INJ_1 has elapsed, the SOx purge rich
flag F.sub.SPR is kept at the off-state until an interval
T.sub.F_INT_1 set by the PID control elapses (refer to time t.sub.2
to t.sub.3 in FIG. 5). Also, when the SOx purge rich flag F.sub.SPR
becomes on as the interval T.sub.F_INT_1 has elapsed, the exhaust
pipe injection or the post injection corresponding to an injection
time period T.sub.F_INJ_2 is again executed (refer to time t.sub.3
to t.sub.4 in FIG. 5). Thereafter, the on/off switching of the SOx
purge rich flag F.sub.SPR is repeatedly executed until the SOx
purge flag F.sub.SP becomes off (refer to time t.sub.n in FIG. 5)
by ending determination of the SOx purge control (which will be
described later).
In this way, in the illustrative embodiment, the injection time
period T.sub.F_INJ in which the catalyst temperature is increased
and the air excess ratio is lowered to the second target air excess
ratio is set from the map that is referred to on the basis of the
operating state of the engine 10, and the interval T.sub.F_INT in
which the catalyst temperature is lowered is processed by the PID
control. Thereby, while effectively maintaining the catalyst
temperature during the SOx purge control within a desired
temperature range necessary for the purge, it is possible to
securely lower the air excess ratio to the target excess ratio.
[Ending Determination of SOx Purge Control]
When any one of conditions that (1) the injection amounts of the
exhaust pipe injection or the post injection are cumulated from the
on-state of the SOx purge flag F.sub.SP and the cumulated injection
amount reaches a predetermined upper limit threshold value amount,
(2) the elapse time measured from the start of the SOx purge
control reaches predetermined upper limit threshold value time and
(3) a SOx occlusion amount of the NOx-occlusion-reduction-type
catalyst 32, which is calculated on the basis of a predetermined
model equation including, as input signals, an operating state of
the engine 10, a sensor value of the NOx/lambda sensor 45 and the
like, is lowered to a predetermined threshold value indicative of
SOx removal success is satisfied, the SOx purge flag F.sub.SP is
set to an off-state and the SOx purge control is over (refer to
time t.sub.4 in FIG. 2 and time t.sub.n in FIG. 5).
In this way, in the illustrative embodiment, the upper limits of
the cumulated injection amount and the elapse time are provided
with respect to the ending conditions of the SOx purge control, so
that it is possible to effectively prevent the fuel from being
excessively consumed when the SOx purge is not progressed due to
the decrease in the exhaust temperature and the like.
[NOx Purge Control]
The NOx purge control unit 70 is configured to execute control of
enriching the exhaust, detoxifying and releasing NOx, which is
occluded in the NOx-occlusion-reduction-type catalyst 32, by
reduction and purification, thereby recovering a NOx occlusion
capacity of the NOx-occlusion-reduction-type catalyst 32
(hereinafter, the control is referred to as `NOx purge
control`).
A NOx purge flag F.sub.NP for starting the NOx purge control
becomes on (refer to time t.sub.1 in FIG. 6) when a NOx emission
amount per unit time is estimated from an operating state of the
engine 10 and an estimated cumulative value .SIGMA.NOx obtained by
cumulatively calculating the emission amounts exceeds a
predetermined threshold value. Alternatively, when a NOx conversion
efficiency by the NOx-occlusion-reduction-type catalyst 32 is
calculated from a NOx emission amount of a catalyst upstream side,
which is estimated from the operating state of the engine 10, and a
NOx amount of a catalyst downstream side, which is detected by the
NOx/lambda sensor 45, and the NOx conversion efficiency becomes
below a predetermined determination threshold value, the NOx purge
flag F.sub.NP becomes on.
In the illustrative embodiment, the enriching of the exhaust by the
NOx purge control is implemented by concurrently using NOx purge
lean control of lowering an air excess ratio from a value (for
example, about 1.5) upon normal operation to a third target air
excess ratio (for example, about 1.3) closer to a lean side than a
theoretical air-fuel ratio equivalent value (about 1.0) by air
system control and NOx purge rich control of lowering the air
excess ratio from the third target air excess ratio to a fourth
target air excess ratio (for example, about 0.9) of a rich side by
injection system control. Hereinafter, the NOx purge lean control
and the NOx purge rich control are described in detail.
[Setting of MAF Target Value in NOx Purge Lean Control]
FIG. 7 is a block diagram depicting setting processing of an MAF
target value MAF.sub.NPL_Trgt upon NOx purge lean control. A third
target air excess ratio setting map 71 is a map that is to be
referred to on the basis of an engine revolution Ne and an
accelerator opening degree Q, and an air excess ratio target value
.lamda..sub.NPL_Trgt (third target air excess ratio) upon NOx purge
lean control corresponding to the engine revolution Ne and the
accelerator opening degree Q is set in advance by a test and the
like.
First, the air excess ratio target value .lamda..sub.NPL_Trgt upon
NOx purge lean control is read from the third target air excess
ratio setting map 71, in response to the engine revolution Ne and
the accelerator opening degree Q, which are input signals, and is
then input to an MAF target value calculation unit 72. Also, the
MAF target value calculation unit 72 calculates an MAF target value
MAF.sub.NPL_Trgt upon NOx purge lean control, based on an equation
(3).
MAF.sub.NPL_Trgt=.lamda..sub.NPL_Trgt.times.Q.sub.fnl_corrd.times.Ro.sub.-
Fuel.times.AFR.sub.sto/Maf.sub._corr (3) In the equation (3),
Q.sub.fnl_corrd indicates a learning-corrected fuel injection
amount (the post injection is excluded) (which will be described
later), Ro.sub.Fuel indicates a fuel specific gravity, AFR.sub.sto
indicates a theoretical air-fuel ratio, and Maf.sub._corr indicates
an MAF correction coefficient (which will be described later).
The MAF target value MAF.sub.NPL_Trgt calculated by the MAF target
value calculation unit 72 is input to a ramp processing unit 73
when the NOx purge flag F.sub.NP becomes on (refer to time t.sub.1
in FIG. 6). The ramp processing unit 73 is configured to read a
ramp coefficient from each of ramp coefficient maps 73A, 73B, in
response to the engine revolution Ne and the accelerator opening
degree Q, which are input signals, and to input an MAF target ramp
value MAF.sub.NPL_Trgt_Ramp to which the ramp coefficient is added
to a valve control unit 74.
The valve control unit 74 is configured to execute feedback control
of narrowing the intake throttle valve 16 towards a close side and
widening the EGR valve 24 towards an open side so that an actual
MAF value MAF.sub.Act input from the MAF sensor 40 becomes the MAF
target ramp value MAF.sub.NPL_Trgt_Ramp.
In this way, in the embodiment, the MAF target value
MAF.sub.NPL_Trgt is set on the basis of the air excess ratio target
value .lamda..sub.NPL_Trgt, which is to be read from the first
target air excess ratio setting map 71, and the fuel injection
amount of each in-cylinder injector 11, and the air system
operation is controlled in the feedback manner on the basis of the
MAF target value MAF.sub.NPL_Trgt. Thereby, it is possible to
effectively lower the exhaust to a desired air excess ratio
necessary for the NOx purge lean control without providing a lambda
sensor at an upstream side of the NOx-occlusion-reduction-type
catalyst 32 or without using a sensor value of a lambda sensor even
when the lambda sensor is provided at the upstream side of the
NOx-occlusion-reduction-type catalyst 32.
Also, the fuel injection amount Q.sub.fnl_corrd after the learning
correction is used as the fuel injection amount of each in-cylinder
injector 11, so that it is possible to set the MAF target value
MAF.sub.NPL_Trgt in the feed-forward control manner. Therefore, it
is possible to effectively exclude influences such as aging
degradation and characteristic change of each in-cylinder injector
11.
Also, the ramp coefficient, which is to be set in correspondence to
the operating state of the engine 10, is added to the MAF target
value MAF.sub.NPL_Trgt, so that it is possible to effectively
prevent accident fire of the engine 10 due to a rapid change in the
intake air amount, deterioration of drivability due to torque
variation, and the like.
[Setting of Fuel Injection Amount in NOx Purge Rich Control]
FIG. 8 is a block diagram depicting setting processing of a target
injection amount Q.sub.NPR_Trgt (injection amount per unit time) of
the exhaust pipe injection or the post injection upon NOx purge
rich control. A fourth target air excess ratio setting map 75 is a
map that is to be referred to on the basis of the engine revolution
Ne and the accelerator opening degree Q, and an air excess ratio
target value .lamda..sub.NPR_Trgt (fourth target air excess ratio)
upon NOx purge rich control corresponding to the engine revolution
Ne and the accelerator opening degree Q is set in advance by a test
and the like.
First, the air excess ratio target value .lamda..sub.NPR_Trgt upon
NOx purge rich control is read from the fourth target air excess
ratio setting map 75, in response to the engine revolution Ne and
the accelerator opening degree Q, which are input signals, and is
then input to an injection amount target value calculation unit 76.
Also, the injection amount target value calculation unit 76
calculates a target injection amount instruction value
Q.sub.NPR_Trgt upon NOx purge rich control, based on an equation
(4).
Q.sub.NPR_Trgt=MAF.sub.NPL_Trgt.times.Maf.sub._corr/(.lamda..sub.NPR_Trgt-
.times.Ro.sub.Fuel.times.AFR.sub.sto)-Q.sub.fnl_corrd (4) In the
equation (4), MAF.sub.NPL_Trgt is input from the MAF target value
calculation unit 72, as a NOx purge lean MAF target value. Also,
Q.sub.fnl_corrd indicates a learning-corrected fuel injection
amount (the post injection is excluded) before an MAF follow-up
control is applied, Ro.sub.Fuel indicates a fuel specific gravity,
AFR.sub.sto indicates a theoretical air-fuel ratio, and
Maf.sub._corr indicates an MAF correction coefficient (which will
be described later).
The target injection amount instruction value Q.sub.NPR_Trgt
calculated by the injection amount target value calculation unit 66
is transmitted to the exhaust injector 34 or each in-cylinder
injector 11, as an injection instruction signal, when the NOx purge
flag F.sub.NP becomes on, as shown at time t.sub.1 in FIG. 6
(hereinafter, particularly, an injection amount instruction value
of the post injection to be transmitted to the in-cylinder injector
11 is referred to as `NOx purge rich/post injection amount
instruction value Q.sub.NPR_Post_Trgt`). The NOx purge rich/post
injection amount instruction value Q.sub.NPR_Post_Trgt is
transmitted to the catalyst temperature estimation unit 80, too,
which will be described in detail later, so as to estimate a
catalyst heat generation amount.
In this way, in the illustrative embodiment, the target injection
amount Q.sub.NPR_Trgt is set on the basis of the air excess ratio
target value .lamda..sub.NPR_Trgt, which is to be read from the
fourth target air excess ratio setting map 75, and the fuel
injection amount of each in-cylinder injector 11. Thereby, it is
possible to effectively lower the exhaust to a desired air excess
ratio necessary for the NOx purge rich control without providing a
lambda sensor at the upstream side of the
NOx-occlusion-reduction-type catalyst 32 or without using a sensor
value of a lambda sensor even when the lambda sensor is provided at
the upstream side of the NOx-occlusion-reduction-type catalyst
32.
Also, the fuel injection amount Q.sub.fnl_corrd after the learning
correction is used as the fuel injection amount of each in-cylinder
injector 11, so that it is possible to set the target injection
amount Q.sub.NPR_Trgt in the feed-forward control manner.
Therefore, it is possible to effectively exclude influences such as
aging degradation and characteristic change of each in-cylinder
injector 11.
[Ending Determination of NOx Purge Control]
When any one of conditions that (1) the injection amounts of the
exhaust pipe injection or the post injection are cumulated from the
on-state of the NOx purge flag F.sub.NP and the cumulated injection
amount reaches a predetermined upper limit threshold value amount,
(2) the elapse time measured from the start of the NOx purge
control reaches predetermined upper limit threshold value time and
(3) a NOx occlusion amount of the NOx-occlusion-reduction-type
catalyst 32, which is calculated on the basis of a predetermined
model equation including, as input signals, an operating state of
the engine 10, a sensor value of the NOx/lambda sensor 45 and the
like, is lowered to a predetermined threshold value indicative of
NOx removal success is satisfied, the NOx purge flag F.sub.NP is
set to an off-state and the NOx purge control is over (refer to
time t.sub.2 in FIG. 6).
In this way, in the illustrative embodiment, the upper limits of
the cumulated injection amount and the elapse time are provided
with respect to the ending conditions of the NOx purge control, so
that it is possible to securely prevent the fuel from being
excessively consumed when the NOx purge fails due to the decrease
in the exhaust temperature and the like.
[Setting of Heat Generation Amount Correction Value]
FIG. 9A is a block diagram depicting setting processing of a heat
generation amount correction value. The heat generation amount
correction value setting unit 100 is an example of the correction
value obtaining means of the disclosure, and is configured to
obtain a heat generation amount correction value, which is used to
correct the heat generation amount of the
NOx-occlusion-reduction-type catalyst 32, on the basis of an
estimated catalyst temperature estimated by the catalyst
temperature estimation unit 80 (an example of the catalyst
temperature estimation means) and an actual exhaust temperature
detected by the second exhaust temperature sensor 44 (an example of
the exhaust temperature detection means) during implementation of
the filter regeneration processing by the filter regeneration
control unit 51 (an example of the filter regeneration means) and
during implementation of the catalyst regeneration processing by
the SOx purge control unit 60 (an example of the catalyst
regeneration means).
A heat generation amount HG.sub.LNT of the
NOx-occlusion-reduction-type catalyst 32 can be defined by an
equation (5). [Mathematical Formula 1]
H.sub.GLNT=.intg.T.sub.LNTC.sub.LNTM.sub.LNT (5)
In the equation (5), T.sub.LNT indicates a temperature of the
NOx-occlusion-reduction-type catalyst 32 but is substantially the
same as an actual exhaust temperature, which is to be detected by
the second exhaust temperature sensor 44, in the illustrative
embodiment, as described above. Also, C.sub.LNT indicates a thermal
capacity of the NOx-occlusion-reduction-type catalyst 32, and
M.sub.LNT indicates a weight of the NOx-occlusion-reduction-type
catalyst 32. Since C.sub.LNT and M.sub.LNT are fixed values, a heat
generation amount ratio HG.sub.ratio, which is a ratio of a
detected value and an estimated value of the
NOx-occlusion-reduction-type catalyst 32, can be defined by an
equation (6).
.times..times..times..times..intg..times..times..times..intg..times..time-
s..times. ##EQU00001##
In the equation (6), .intg.Temp.sub._DPF_est indicates an estimated
catalyst temperature of the NOx-occlusion-reduction-type catalyst
32 obtained by the catalyst temperature estimation unit 80 (NOx
catalyst temperature estimation unit 87B). Also,
.intg.Temp.sub._DPF_act indicates an exhaust temperature detected
by the second exhaust temperature sensor 44.
The heat generation amount correction value setting unit 100 (a
heat generation amount correction value calculation unit 101) is
configured to obtain a heat generation amount correction value
HG.sub.corr by calculating integral values of the heat generation
amount ratio HG.sub.ratio during implementation of the filter
regeneration processing by the filter regeneration control unit 51
(the filter regeneration means) and during implementation of the
catalyst regeneration processing by the SOx purge control unit 60
(the catalyst regeneration means). For this reason, the heat
generation amount correction value calculation unit 101 is input
with the SOx purge flag F.sub.SP, the filter forced regeneration
flag F.sub.DPF, and the detection signal from the second exhaust
temperature sensor 44.
Also, the heat generation amount correction value setting unit 100
(the pseudo regeneration means) is configured to perform pseudo
regeneration processing by maintaining a temperature of the
NOx-occlusion-reduction-type catalyst 32 at a pseudo regeneration
temperature lower than a sulfur separation temperature (the
recovery temperature) and a PM combustion temperature (a catalyst
temperature in the filter regeneration processing) before at least
one of first-time catalyst regeneration processing and first-time
filter regeneration processing is implemented. In the illustrative
embodiment, the pseudo regeneration processing is performed on
condition that an estimated PM accumulation amount obtained from
the PM accumulation amount estimation unit 52 reaches 40% to 60% of
the filter regeneration threshold value. In the below, setting
processing of the heat generation amount correction value that is
to be performed by the heat generation amount correction value
setting unit 100 is described with reference to a flowchart of FIG.
10.
In step S100, it is determined whether the filter regeneration
processing has not been implemented yet. In general, since the
first-time SOx purge control is performed later than the first-time
filter regeneration processing, the filter regeneration processing
is set as a determination target, in the illustrative embodiment.
It is determined whether the filter regeneration processing has not
been implemented yet on the basis of a determination flag
F.sub.DPF_FST, for example. The determination flag F.sub.SP_FST is
set to an off-state (F.sub.DPF_FST=0) upon factory shipment, and is
set to an on-state (F.sub.DPF_FST=1) when the first-time filter
regeneration processing is implemented. When the
NOx-occlusion-reduction-type catalyst 32 is repaired or replaced,
the determination flag F.sub.DPF_FST is reset to the off-state
(F.sub.DPF_FST=0).
When it is determined that the filter regeneration processing has
not been implemented (F.sub.DPF_FST=0) (Y in S100), it is
determined in step S110 whether the PM accumulation amount is equal
to or greater than an initial accumulation amount threshold value
(40% to 60% of the filter regeneration threshold value). When the
PM accumulation amount is equal to or greater than the initial
accumulation amount threshold value (Y in S110), processing of step
S120 is executed, and when the PM accumulation amount is less than
the initial accumulation amount threshold value (N in S110),
processing of step 100 is executed.
In step 120, processing of the pseudo filter regeneration is
started. In the illustrative embodiment, the heat generation amount
correction value setting unit 100 outputs the injection instruction
signal to the exhaust injector 34 or the in-cylinder injector 11,
thereby increasing an unburnt fuel concentration in the exhaust. In
the pseudo filter regeneration, the unburnt fuel injection is
controlled so that the temperature is to be a pseudo regeneration
temperature (about 500.degree. C.) lower than the exhaust
temperature (about 550.degree. C.) upon the filter forced
regeneration and the sulfur separation temperature (about
600.degree. C.) upon the SOx purge.
During the implementation (N in S140) of the pseudo filter
regeneration processing, the heat generation amount correction
value setting unit 100 obtains the actual exhaust temperature from
the second exhaust temperature sensor 44 and the estimated catalyst
temperature from the catalyst temperature estimation unit 80
(S130).
When the pseudo filter regeneration processing is over (Y in S140),
the heat generation amount correction value setting unit 100
calculates an initial correction value (S150). As described above,
for calculation of the initial correction value, the heat
generation amount ratio HG.sub.ratio of the equation (6) is used.
However, the calculation of the heat generation amount ratio
HG.sub.ratio is performed from temperature rising timings of the
actual exhaust temperature and the estimated catalyst temperature
until the actual exhaust temperature and the estimated catalyst
temperature are lowered to a level equivalent to an inlet
temperature of the oxidation catalyst 31 (a detected temperature of
the first exhaust temperature sensor 43) after the pseudo filter
regeneration processing is over. The calculated initial correction
value HG.sub.corr_ini (an example of the initial value of the heat
generation amount correction value) is output to the catalyst
temperature estimation unit 80 (NOx catalyst heat generation amount
estimation unit 86B), so that it is used to estimate the heat
generation amount and to estimate the NOx catalyst temperature in
the NOx-occlusion-reduction-type catalyst 32.
When it is determined in step S100 that the filter regeneration
processing has been already implemented (F.sub.DPF_FST=1) (N in
S100), processing of step S160 is performed. In step S160, it is
determined whether the filter forced regeneration flag F.sub.DPF is
on (F.sub.DPF=1) or not. Here, when it is determined that the
filter forced regeneration flag F.sub.DPF is on (Y in S160), the
processing proceeds to step 180. Also, when it is determined that
the filter forced regeneration flag F.sub.DPF is off (F.sub.DPF=0)
(N in S160), the processing proceeds to step 170. In step S170, it
is determined whether the SOx purge flag F.sub.SP is on
(F.sub.SP=1). Here, when it is determined that the SOx purge flag
F.sub.SP is on (Y in S170), the processing proceeds to step 180.
Also, when it is determined that the SOx purge flag F.sub.SP is off
(F.sub.SP=0) (N in S170), the processing proceeds to step S100. In
summary, in steps S160 and S170, it is determined whether the
filter forced regeneration flag F.sub.DPF or the SOx purge flag
F.sub.SP is on or not, and when at least one flag is on, the
processing of step S180 is performed.
In step S180, like step S130, the actual exhaust temperature from
the second exhaust temperature sensor 44 and the estimated catalyst
temperature from the catalyst temperature estimation unit 80 are
obtained. This temperature obtaining processing is continuously
performed until both the filter forced regeneration flag F.sub.DPF
and the SOx purge flag F.sub.SP become off (F.sub.DPF=0,
F.sub.SP=0) (S190, S200). When both the flags become off, the
processing proceeds to step S210.
In step S210, a temporal correction value HG.sub.corr_sfo is
calculated. Here, the calculation processing is performed on the
basis of the heat generation amount ratio HG.sub.ratio, like the
processing of step 150. The calculated temporal correction value
HG.sub.corr_sfo is output to the catalyst temperature estimation
unit 80 (NOx catalyst heat generation amount estimation unit 86B),
so that it is used to estimate the heat generation amount and to
estimate the NOx catalyst temperature.
In this way, in the illustrative embodiment, since the heat
generation amount correction value of the
NOx-occlusion-reduction-type catalyst 32 is obtained during the
implementation of the filter regeneration processing by the filter
regeneration control unit 51 and during the implementation of the
catalyst regeneration processing by the SOx purge control unit 60,
it is possible to secure the sufficient heating time period so as
to obtain the heat generation amount ratio. Thereby, when there is
a difference between the heat generation amount of the
NOx-occlusion-reduction-type catalyst 32 and the estimated heat
generation amount of the catalyst temperature estimation unit 80
(NOx catalyst heat generation amount estimation unit 86B), it is
possible to correctly obtain the difference. As a result, like the
estimated heat generation amount HG.sub._corr after the correction,
which is shown in FIG. 9B, it is possible to accurately obtain the
catalyst heat generation amount HG.sub._act that gradually
decreases over time and to increase the estimation accuracy of the
catalyst temperature.
Also, in the illustrative embodiment, since the pseudo regeneration
processing is performed before the first-time filter regeneration
processing or SOx purge processing, it is possible to securely
prevent the temperature of the NOx-occlusion-reduction-type
catalyst 32 from excessively increasing. Also, in the first-time
filter regeneration processing or SOx purge processing, it is
possible to perform the estimation processing with higher
precision, as compared to a case where the initial heat generation
amount HG.sub._cal shown in FIG. 9B is used.
[MAF Follow-Up Control]
The MAF follow-up control unit 77 is configured to execute control
(referred to as `MAF follow-up control`) of correcting a fuel
injection timing and a fuel injection amount of each in-cylinder
injector 11 in correspondence to MAF change (1) for a switching
time period from a lean state of normal operation to a rich state
by the SOx purge control or the NOx purge control and (2) for a
switching time period from the rich state by the SOx purge control
or the NOx purge control to the lean state of normal operation.
[Injection Amount Learning Correction]
As shown in FIG. 11, the injection amount learning correction unit
90 includes a learning correction coefficient calculation unit 91
and an injection amount correction unit 92.
The learning correction coefficient calculation unit 91 is
configured to calculate a learning correction coefficient
F.sub.Corr of the fuel injection amount, based on an error
.DELTA..lamda. between an actual lambda value .lamda..sub.Act,
which is to be detected by the NOx/lambda sensor 45 upon lean
operation of the engine 10, and an estimated lambda value
.lamda..sub.Est. When the exhaust is in the lean state, an HC
concentration in the exhaust is very small, so that a change in
exhaust lambda value due to an oxidation reaction of HC in the
oxidation catalyst 31 is negligible small. For this reason, it is
thought that the actual lambda value .lamda..sub.Act in the
exhaust, which passes through the oxidation catalyst 31 and is
detected by the downstream-side NOx/lambda sensor 45, coincides
with the estimated lambda value .lamda..sub.Est in the exhaust
emitted from the engine 10. For this reason, when the error
.DELTA..lamda. occurs between the actual lambda value
.lamda..sub.Act and the estimated lambda value .lamda..sub.Est, it
can be assumed that the error is caused due to a difference between
an instructed injection amount to each in-cylinder injector 11 and
an actual injection amount. In the below, learning correction
coefficient calculation processing, which is to be performed using
the error .DELTA..lamda. by the learning correction coefficient
calculation unit 91, is described with reference to a flowchart of
FIG. 12.
In step S300, it is determined whether the engine 10 is in a lean
operating state, based on the engine revolution Ne and the
accelerator opening degree Q. When it is determined that the engine
is in the lean operating state, the learning correction coefficient
calculation unit proceeds to step S310 so as to start learning
correction coefficient calculation.
In step S310, a learning value F.sub.CorrAdpt is calculated
(F.sub.CorrAdpt=(.lamda..sub.Est-.lamda..sub.Act).times.K.sub.1.times.K.s-
ub.2) by multiplying the error .DELTA..lamda., which is obtained by
subtracting the actual lambda value .lamda..sub.Act detected at the
NOx/lambda sensor 45 from the estimated lambda value
.lamda..sub.Est, by a learning value gain K.sub.1 and a correction
sensitivity coefficient K.sub.2. The estimated lambda value
.lamda..sub.Est is estimated and calculated from the operating
state of the engine 10 corresponding to the engine revolution Ne
and the accelerator opening degree Q. Also, the correction
sensitivity coefficient K.sub.2 is read from a correction
sensitivity coefficient map 91A shown in FIG. 11, in response to
the actual lambda value .lamda..sub.Act detected at the NOx/lambda
sensor 45, which is an input signal.
In step S320, it is determined whether an absolute value
|F.sub.CorrAdpt| of the learning value F.sub.CorrAdpt is within a
range of a predetermined correction limit value A. When it is
determined that the absolute value |F.sub.CorrAdpt| exceeds the
correction limit value A, the control returns and this learning is
stopped.
In step S330, it is determined whether a learning prohibition flag
F.sub.Pro is off. As the learning prohibition flag F.sub.Pro, for
example, a transient operation of the engine 10, the SOx purge
control (F.sub.SP=1) and the like are exemplified. The reason is
that when the corresponding conditions are satisfied, the error
.DELTA..lamda. increases due to a change in the actual lambda value
.lamda..sub.Act, so that the correct learning cannot be performed.
Regarding the determination as to whether the engine 10 is in the
transient operation, based on a temporal change amount of the
actual lambda value .lamda..sub.Act detected at the NOx/lambda
sensor 45, when the temporal change amount is greater than a
predetermined threshold value, it may be determined that the engine
is in the transient operation.
In step S340, a learning value map 91B (refer to FIG. 11), which is
referred to on the basis of the engine revolution Ne and the
accelerator opening degree Q, is updated to the learning value
F.sub.CorrAdpt calculated in step S310. More specifically, in the
learning value map 91B, a plurality of learning regions divided in
correspondence to the engine revolution Ne and the accelerator
opening degree Q is set. The learning regions are preferably set to
be narrower as use frequencies thereof are higher and to be wider
as use frequencies thereof are lower. Thereby, the learning
accuracy is improved in the region of which use frequency is high
and it is possible to effectively prevent the non-learning in the
region of which use frequency is low.
In step S350, in response to the engine revolution Ne and the
accelerator opening degree Q, which are input signals, "1" is added
to the learning value read from the learning value map 91B, so that
a learning correction coefficient F.sub.Corr is calculated
(F.sub.Corr=1+F.sub.CorrAdpt). The learning correction coefficient
F.sub.Corr is input to the injection amount correction unit 92
shown in FIG. 11.
The injection amount correction unit 92 multiplies respective basic
injection amounts of pilot injection Q.sub.Pilot, pre-injection
Q.sub.Pre, main injection Q.sub.Main, after-injection Q.sub.After
and post injection Q.sub.Post by the learning correction
coefficient F.sub.Corr, thereby correcting the fuel injection
amounts.
In this way, the fuel injection amount to each in-cylinder injector
11 is corrected by the learning value corresponding to the error
.DELTA..lamda. between the estimated lambda value .lamda..sub.Est
and the actual lambda value .lamda..sub.Act, so that it is possible
to effectively exclude the non-uniformity such as aging
degradation, characteristic change, individual difference and the
like of each in-cylinder injector 11.
[Catalyst Temperature Estimation]
FIG. 13 is a block diagram depicting estimation processing of the
oxidation catalyst temperature and the NOx catalyst temperature,
which is to be performed by the catalyst temperature estimation
unit 80. The catalyst temperature estimation unit 80 is an example
of the catalyst temperature estimation means of the disclosure, and
is configured to estimate the catalyst temperature, based on an
amount of the unburnt fuel contained in the exhaust and the heat
generation amount of the oxidation catalyst 31 or the
NOx-occlusion-reduction-type catalyst 32.
A lean-time HC map 81A is a map that is to be referred to on the
basis of the operating state of the engine 10, and a HC amount
(hereinafter, referred to as `lean-time HC emission amount`) to be
emitted from the engine 10 upon the lean operation is set therein
in advance by a test and the like. When the filter forced
regeneration flag F.sub.DPF, the SOx purge flag F.sub.SP and the
NOx purge flag F.sub.NP are all off (F.sub.DPF=0, F.sub.SP=0,
F.sub.NP=0), the lean-time HC emission amount read from the
lean-time HC map 81A on the basis of the engine revolution Ne and
the accelerator opening degree Q is transmitted to each of the heat
generation amount estimation units 86A, 86B.
A lean-time CO map 81B is a map that is to be referred to on the
basis of the operating state of the engine 10, and a CO amount
(hereinafter, referred to as `lean-time CO emission amount`) to be
emitted from the engine 10 upon the lean operation is set therein
in advance by a test and the like. When the filter forced
regeneration flag F.sub.DPF, the SOx purge flag F.sub.SP and the
NOx purge flag F.sub.NP are all off (F.sub.DPF=0, F.sub.SP=0,
F.sub.NP=0), the lean-time CO emission amount read from the
lean-time CO map 81B on the basis of the engine revolution Ne and
the accelerator opening degree Q is transmitted to the oxidation
catalyst heat generation amount estimation unit 86A and the NOx
catalyst heat generation amount estimation unit 86B.
A filter forced regeneration-time HC map 82A is a map that is to be
referred to on the basis of the operating state of the engine 10,
and a HC amount (hereinafter, referred to as `filter
regeneration-time HC emission amount`) to be emitted from the
engine 10 upon implementation of the filter forced regeneration
control is set therein in advance by a test and the like. When the
filter forced regeneration flag F.sub.DPF is on (F.sub.DPF=1), the
filter regeneration-time HC emission amount read from the filter
forced regeneration-time HC map 82A on the basis of the engine
revolution Ne and the accelerator opening degree Q is multiplied by
a predetermined correction coefficient corresponding to the
operating state of the engine 10, which is then transmitted to the
oxidation catalyst heat generation amount estimation unit 86A and
the NOx catalyst heat generation amount estimation unit 86B.
A filter forced regeneration-time CO map 82B is a map that is to be
referred to on the basis of the operating state of the engine 10,
and a CO amount (hereinafter, referred to as `filter
regeneration-time CO emission amount`) to be emitted from the
engine 10 upon implementation of the filter forced regeneration
control is set therein in advance by a test and the like. When the
filter forced regeneration flag F.sub.DPF is on (F.sub.DPF=1), the
filter regeneration-time CO emission amount read from the filter
forced regeneration-time CO map 82B on the basis of the engine
revolution Ne and the accelerator opening degree Q is multiplied by
a predetermined correction coefficient corresponding to the
operating state of the engine 10, which is then transmitted to the
oxidation catalyst heat generation amount estimation unit 86A and
the NOx catalyst heat generation amount estimation unit 86B.
A NOx purge-time HC map 83A is a map that is to be referred to on
the basis of the operating state of the engine 10, and a HC amount
(hereinafter, referred to as `NOx purge-time HC emission amount`)
to be emitted from the engine 10 upon implementation of the NOx
purge control is set therein in advance by a test and the like.
When the NOx purge flag F.sub.NP is on (F.sub.NP=1), the NOx
purge-time HC emission amount read from the NOx purge-time HC map
83A on the basis of the engine revolution Ne and the accelerator
opening degree Q is multiplied by a predetermined correction
coefficient corresponding to the operating state of the engine 10,
which is then transmitted to the oxidation catalyst heat generation
amount estimation unit 86A and the NOx catalyst heat generation
amount estimation unit 86B.
A NOx purge-time CO map 83B is a map that is to be referred to on
the basis of the operating state of the engine 10, and a CO amount
(hereinafter, referred to as `NOx purge-time CO emission amount`)
to be emitted from the engine 10 upon implementation of the NOx
purge control is set therein in advance by a test and the like.
When the NOx purge flag F.sub.NP is on (F.sub.NP=1), the NOx
purge-time CO emission amount read from the NOx purge-time CO map
83B on the basis of the engine revolution Ne and the accelerator
opening degree Q is multiplied by a predetermined correction
coefficient corresponding to the operating state of the engine 10,
which is then transmitted to the oxidation catalyst heat generation
amount estimation unit 86A and the NOx catalyst heat generation
amount estimation unit 86B.
A SOx purge-time HC map 84A is a map that is to be referred to on
the basis of the operating state of the engine 10, and a HC amount
(hereinafter, referred to as `SOx purge-time HC emission amount`)
to be emitted from the engine 10 upon implementation of the SOx
purge control is set therein in advance by a test and the like.
When the SOx purge flag F.sub.SP is on (F.sub.SP=1), the SOx
purge-time HC emission amount read from the SOx purge-time HC map
84A on the basis of the engine revolution Ne and the accelerator
opening degree Q is multiplied by a predetermined correction
coefficient corresponding to the operating state of the engine 10,
which is then transmitted to the oxidation catalyst heat generation
amount estimation unit 86A and the NOx catalyst heat generation
amount estimation unit 86B.
A SOx purge-time CO map 84B is a map that is to be referred to on
the basis of the operating state of the engine 10, and a CO amount
(hereinafter, referred to as `SOx purge-time CO emission amount`)
to be emitted from the engine 10 upon implementation of the SOx
purge control is set therein in advance by a test and the like.
When the SOx purge flag F.sub.SP is on (F.sub.SP=1), the SOx
purge-time CO emission amount read from the SOx purge-time CO map
84B on the basis of the engine revolution Ne and the accelerator
opening degree Q is multiplied by a predetermined correction
coefficient corresponding to the operating state of the engine 10,
which is then transmitted to the oxidation catalyst heat generation
amount estimation unit 86A and the NOx catalyst heat generation
amount estimation unit 86B.
The post injection amount instruction value correction unit 85
implements post injection amount instruction value correction of
correcting a post injection amount instruction value, which is used
to estimate the catalyst heat generation amount, by the learning
correction coefficient input from the learning correction
coefficient calculation unit 91 when the SOx purge rich control,
the NOx purge rich control or the filter forced regeneration
control is implemented by the post injection.
More specifically, when the SOx purge rich flag F.sub.SPR becomes
on and the SOx purge rich control is implemented by the post
injection, a corrected post injection amount instruction value
Q.sub.SPR_Post_Corr (=Q.sub.SPR_Post_Trgt.times.F.sub.Corr), which
is obtained by multiplying the SOx purge rich/post injection amount
instruction value Q.sub.SPR_Post_Trgt input from the injection
amount target value calculation unit 66 (the SOx purge control unit
60) by the learning correction coefficient F.sub.Corr, is
transmitted to the oxidation catalyst heat generation amount
estimation unit 86A and the NOx catalyst heat generation amount
estimation unit 86B.
Also, when the NOx purge rich flag F.sub.NPR becomes on and the NOx
purge rich control is implemented by the post injection, a
corrected post injection amount instruction value
Q.sub.NPR_Post_Corr (=Q.sub.NPR_Post_Trgt.times.FCorr), which is
obtained by multiplying the NOx purge rich/post injection amount
instruction value Q.sub.NPR_Post_Trgt input from the injection
amount target value calculation unit 76 (NOx purge control unit 70)
by the learning correction coefficient F.sub.Corr, is transmitted
to the oxidation catalyst heat generation amount estimation unit
86A and the NOx catalyst heat generation amount estimation unit
86B.
Also, when the filter forced regeneration flag F.sub.DPF becomes on
and the filter forced regeneration control is implemented by the
post injection, a corrected post injection amount instruction value
Q.sub.DPF_Post_Corr (=Q.sub.DPF_Post_Trgt.times.F.sub.Corr), which
is obtained by multiplying the filter regeneration post injection
amount instruction value Q.sub.DPF_Post_Trgt input from the filter
regeneration control unit 51 by the learning correction coefficient
F.sub.Corr, is transmitted to the oxidation catalyst heat
generation amount estimation unit 86A and the NOx catalyst heat
generation amount estimation unit 86B.
The oxidation catalyst heat generation amount estimation unit 86A
is configured to estimate a HC/CO heat generation amount
(hereinafter, referred to as `oxidation catalyst HC/CO heat
generation amount`) in the oxidation catalyst 31, based on the
HC/CO emission amounts, which are input from the respective maps
81A to 84B in correspondence to the on and off states of the SOx
purge flag F.sub.SP, the NOx purge flag F.sub.NP and the filter
forced regeneration flag F.sub.DPF, the corrected post injection
amount instruction value, which is input from the post injection
amount instruction value correction unit 85 in correspondence to
selection of the exhaust pipe injection and the post injection, and
the like. The oxidation catalyst HC/CO heat generation amount is
estimated and calculated on the basis of a model equation
including, as input values, the HC/CO emission amount and the
corrected post injection amount instruction value, and a map, for
example.
The NOx catalyst heat generation amount estimation unit 86B is
configured to estimate a HC/CO heat generation amount (hereinafter,
referred to as `NOx catalyst HC/CO heat generation amount`) in the
NOx-occlusion-reduction-type catalyst 32, based on the HC/CO
emission amounts, which are input from the respective maps 81A to
84B in correspondence to the on and off states of the SOx purge
flag F.sub.SP, the NOx purge flag F.sub.NP and the filter forced
regeneration flag F.sub.DPF, the corrected post injection amount
instruction value, which is input from the post injection amount
instruction value correction unit 85 in correspondence to selection
of the exhaust pipe injection and the post injection, and the like.
The NOx catalyst HC/CO heat generation amount is estimated and
calculated on the basis of a model equation including, as input
values, the HC/CO emission amount and the corrected post injection
amount instruction value, and a map, for example. In the estimation
and calculation, the lowering of the heat generation amount due to
aging degradation of the NOx-occlusion-reduction-type catalyst 32
is corrected by referring to the heat generation amount correction
value set by the heat generation amount correction value setting
unit 100. Thereby, it is possible to increase the accuracy of the
HC/CO heat generation amount to be estimated and calculated.
The oxidation catalyst temperature estimation unit 87A is
configured to estimate and calculate the catalyst temperature of
the oxidation catalyst 31, based on a model equation including, as
input values, the oxidation catalyst inlet temperature detected by
the first exhaust temperature sensor 43, the oxidation catalyst
HC/CO heat generation amount input from the oxidation catalyst heat
generation amount estimation unit 86A, the sensor value of the MAP
sensor 40, a heat radiation amount to the exterior air, which is
estimated from the sensor value of the exterior air temperature
sensor 47 or the intake temperature sensor 48, and the like, and a
map.
The NOx catalyst temperature estimation unit 87B is configured to
estimate and calculate the catalyst temperature of the
NOx-occlusion-reduction-type catalyst 32, based on a model equation
including, as input values, the oxidation catalyst temperature
(hereinafter, referred to as `NOx catalyst inlet temperature`)
input from the oxidation catalyst temperature estimation unit 87A,
the NOx catalyst HC/CO heat generation amount input from the NOx
catalyst heat generation amount estimation unit 86B, a heat
radiation amount to the exterior air, which is estimated from the
sensor value of the exterior air temperature sensor 47 or the
intake temperature sensor 48, and the like, and a map.
As described in detail above, in the illustrative embodiment, when
the SOx purge control, the NOx purge control and the filter forced
regeneration control are implemented by the post injection, the
corrected post injection amount instruction value in which the
learning correction value is reflected is used to estimate and
calculate the heat generation amounts of the oxidation catalyst 31
and the NOx-occlusion-reduction-type catalyst 32. Thereby, it is
possible to calculate the catalyst heat generation amount with high
precision, considering the influences such as aging degradation of
the in-cylinder injector 11. Therefore, it is possible to securely
improve the temperature estimation accuracy of the oxidation
catalyst 31 and the NOx-occlusion-reduction-type catalyst 32.
Also, the HC/CO maps 81A to 84B are appropriately switched, in
correspondence to the respective operating states such as the
normal lean operation, the filter forced regeneration, the SOx
purge and the NOx purge in which the HC/CO emission amounts are
different, so that it is possible to accurately calculate the HC/CO
heat generation amount in the catalyst corresponding to the
operating states. Therefore, it is possible to effectively improve
the temperature estimation accuracy of the oxidation catalyst 31
and the NOx-occlusion-reduction-type catalyst 32.
[FB Control Reference Temperature Selection]
The reference temperature selection unit 88 shown in FIG. 13 is
configured to select a reference temperature that is used for the
temperature feedback control of the filter forced regeneration and
SOx purge.
In the exhaust purification system including the oxidation catalyst
31 and the NOx-occlusion-reduction-type catalyst 32, the HC/CO heat
generation amounts are different in the respective catalysts 31,
32, in correspondence to heat generation characteristics and the
like of the catalysts. For this reason, as the reference
temperature of the temperature feedback control, it is preferably
to select a temperature of the catalyst having a greater heat
generation amount, from a standpoint of improving
controllability.
The reference temperature selection unit 88 is configured to select
a temperature of the catalyst, which has a greater heat generation
amount estimated from the operating state of the engine 10, of the
oxidation catalyst temperature and the NOx catalyst temperature,
and to transmit the selected catalyst temperature to the filter
regeneration control unit 51, the SOx purge control unit 60, the
NOx purge control unit 70 and the heat generation amount correction
value setting unit 100, as the reference temperature of the
temperature feedback control
More specifically, during the filter forced regeneration in which
an oxygen concentration in the exhaust is relatively high and the
HC/CO heat generation amount of the oxidation catalyst 31
increases, the oxidation catalyst temperature that is input from
the oxidation catalyst temperature estimation unit 87A is selected
as the reference temperature of the temperature feedback control.
On the other hand, during the SOx purge rich control or the NOx
purge rich control in which the HC/CO heat generation amount of the
NOx-occlusion-reduction-type catalyst 32 increases due to reduction
of the oxygen concentration in the exhaust, the NOx catalyst
temperature that is input from the NOx catalyst temperature
estimation unit 87B is selected as the reference temperature of the
temperature feedback control.
In this way, in the illustrative embodiment, the temperature of the
catalyst having a greater HC/CO heat generation amount is selected
as the reference temperature of the temperature feedback control,
so that it is possible to effectively improve the
controllability.
[MAF Correction Coefficient]
The MAF correction coefficient calculation unit 95 is configured to
calculate an MAF correction coefficient Maf.sub._corr, which is to
be used for the setting of the MAF target value MAF.sub.SPL_Trgt
and the target injection amount Q.sub.SPR_Trgt upon the SOx purge
control.
In the illustrative embodiment, the fuel injection amount of each
in-cylinder injector 11 is corrected on the basis of the error
.DELTA..lamda. between the actual lambda value .lamda..sub.Act
detected at the NOx/lambda sensor 45 and the estimated lambda value
.lamda..sub.Est. However, since the lambda is a ratio of air and
fuel, it cannot be said that the error .DELTA..lamda. is
necessarily caused due to the difference between the instructed
injection amount to each in-cylinder injector 11 and the actual
injection amount. That is, the error .DELTA..lamda. of the lambda
may be influenced not only by each in-cylinder injector 11 but also
an error of the MAF sensor 40.
FIG. 14 is a block diagram depicting setting processing of the MAF
correction coefficient Maf.sub._corr, which is to be performed by
the MAF correction coefficient calculation unit 95. A correction
coefficient setting map 96 is a map that is to be referred to on
the basis of the engine revolution Ne and the accelerator opening
degree Q, and an MAF correction coefficient Maf.sub._corr
indicative of a sensor characteristic of the MAP sensor 40
corresponding to the engine revolution Ne and the accelerator
opening degree Q is set in advance by a test and the like.
The MAF correction coefficient calculation unit 95 is configured to
read the MAF correction coefficient Maf.sub._corr from the
correction coefficient setting map 96, in response to the engine
revolution Ne and the accelerator opening degree Q, which are input
signals, and to transmit the MAF correction coefficient
Maf.sub._corr to the MAF target value calculation unit 62 and the
injection amount target value calculation unit 66. Thereby, it is
possible to effectively reflect the sensor characteristics of the
MAF sensor 40 when setting the MAF target value MAF.sub.SPL_Trgt
and the target injection amount Q.sub.SPR_Trgt upon the SOx purge
control.
[Others]
In the meantime, the present invention is not limited to the above
illustrative embodiment and can be implemented with being
appropriately modified without departing from the gist of the
present invention.
For example, in the above illustrative embodiment, the
NOx-occlusion-reduction-type catalyst 32 has been exemplified as
the catalyst configured to purify the exhaust. However, the present
invention can also be implemented for the other catalysts
configured to heat generate and to purify the exhaust by the supply
of the unburnt fuel.
The subject application is based on a Japanese Patent Application
No. 2015-062527 filed on Mar. 25, 2015, the entire contents of
which are incorporated herein by reference.
INDUSTRIAL APPLICABILITY
The present invention has the effect of increasing the estimation
accuracy of the catalyst temperature and is useful for the exhaust
purification device and the like.
DESCRIPTION OF REFERENCE NUMERALS AND SIGNS
10: engine 11: in-cylinder injector 12: intake passage 13: exhaust
passage 16: intake throttle valve 24: EGR valve 31: oxidation
catalyst 32: NOx-occlusion-reduction-type catalyst 33: filter 34:
exhaust injector 40: MAP sensor 45: NOx/lambda sensor 50: ECU
* * * * *