U.S. patent number 10,930,822 [Application Number 16/251,862] was granted by the patent office on 2021-02-23 for method of manufacturing light emitting device.
This patent grant is currently assigned to NICHIA CORPORATION. The grantee listed for this patent is NICHIA CORPORATION. Invention is credited to Tomoaki Tsuruha, Noritsugu Uchiwa.

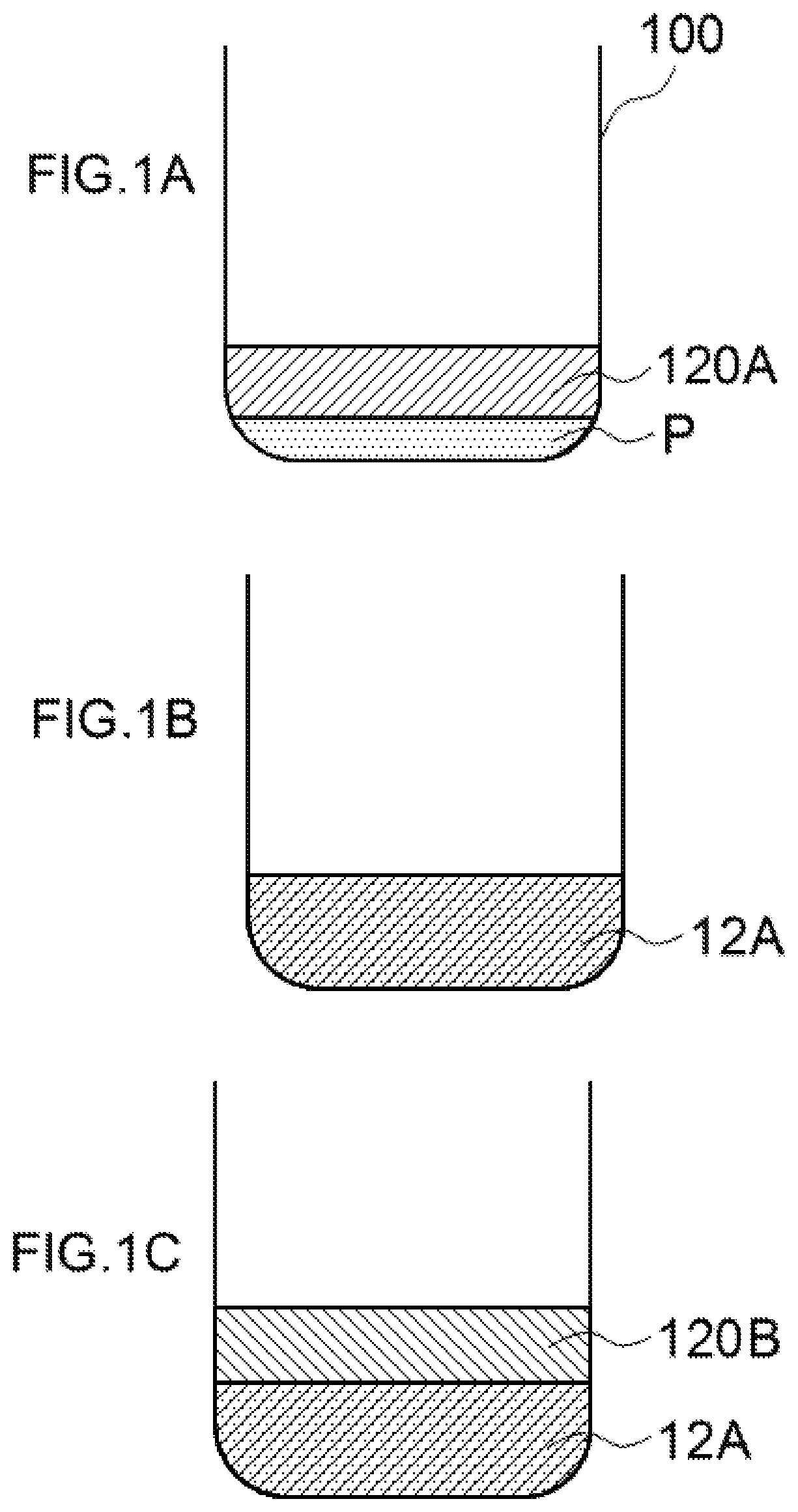
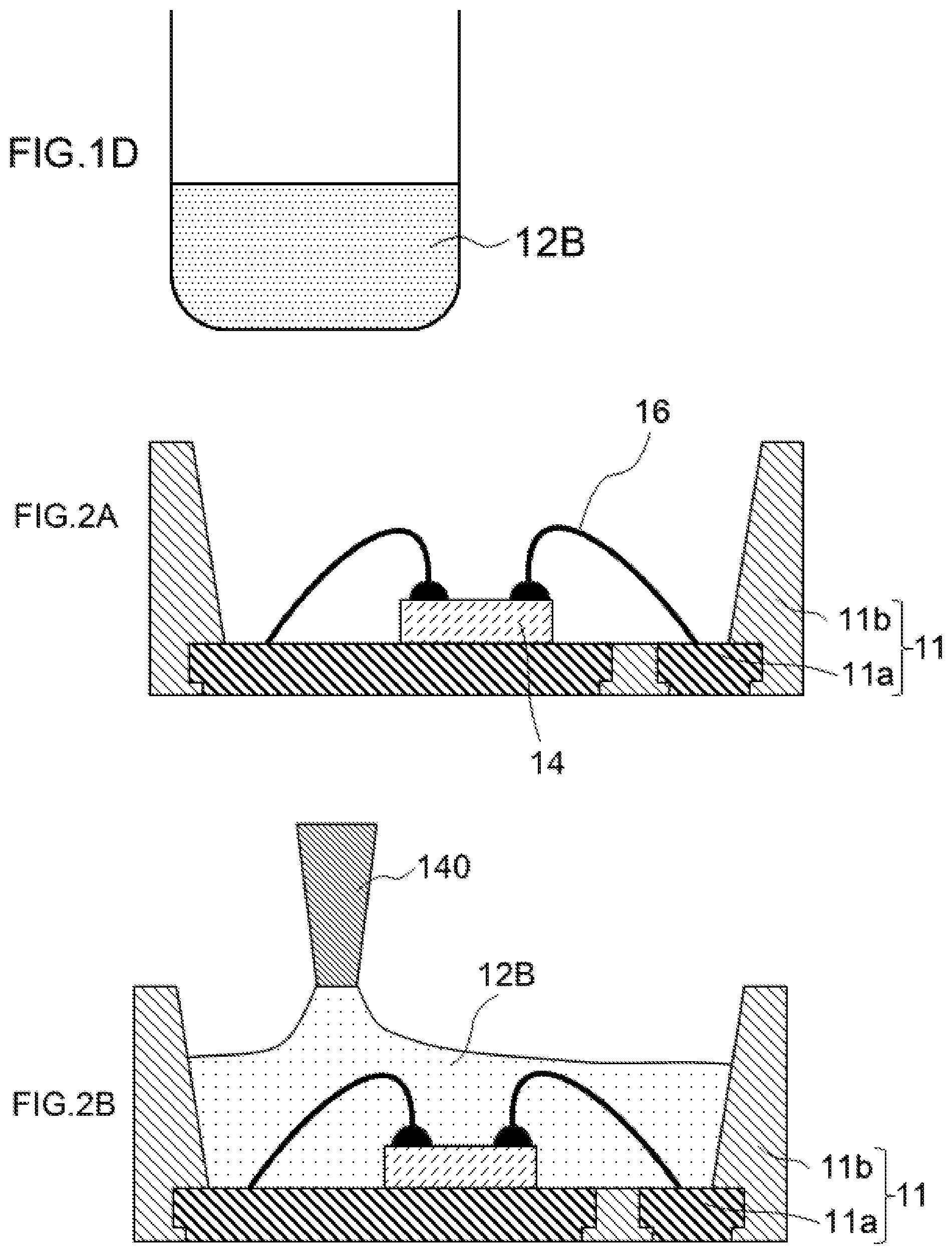
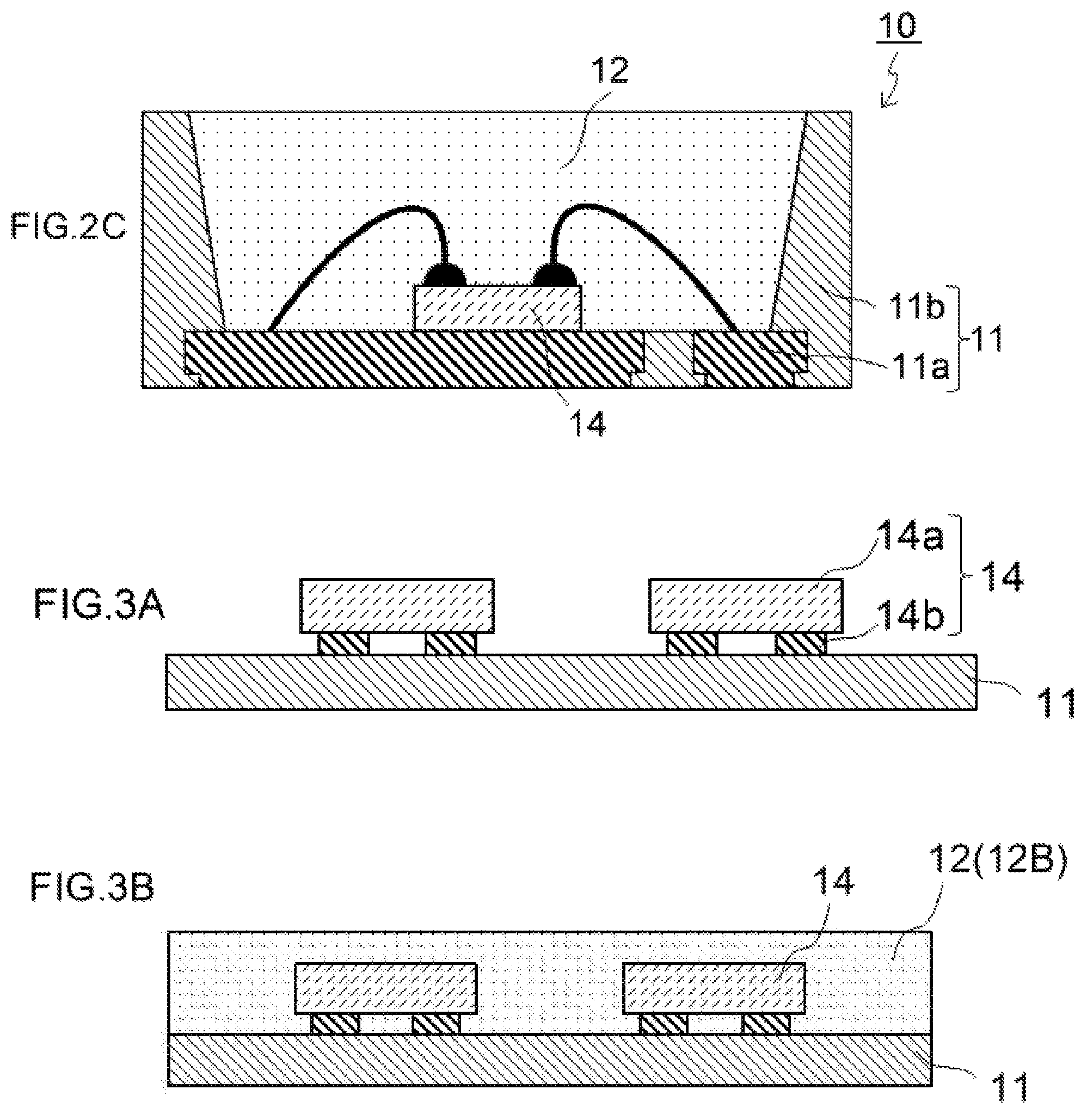
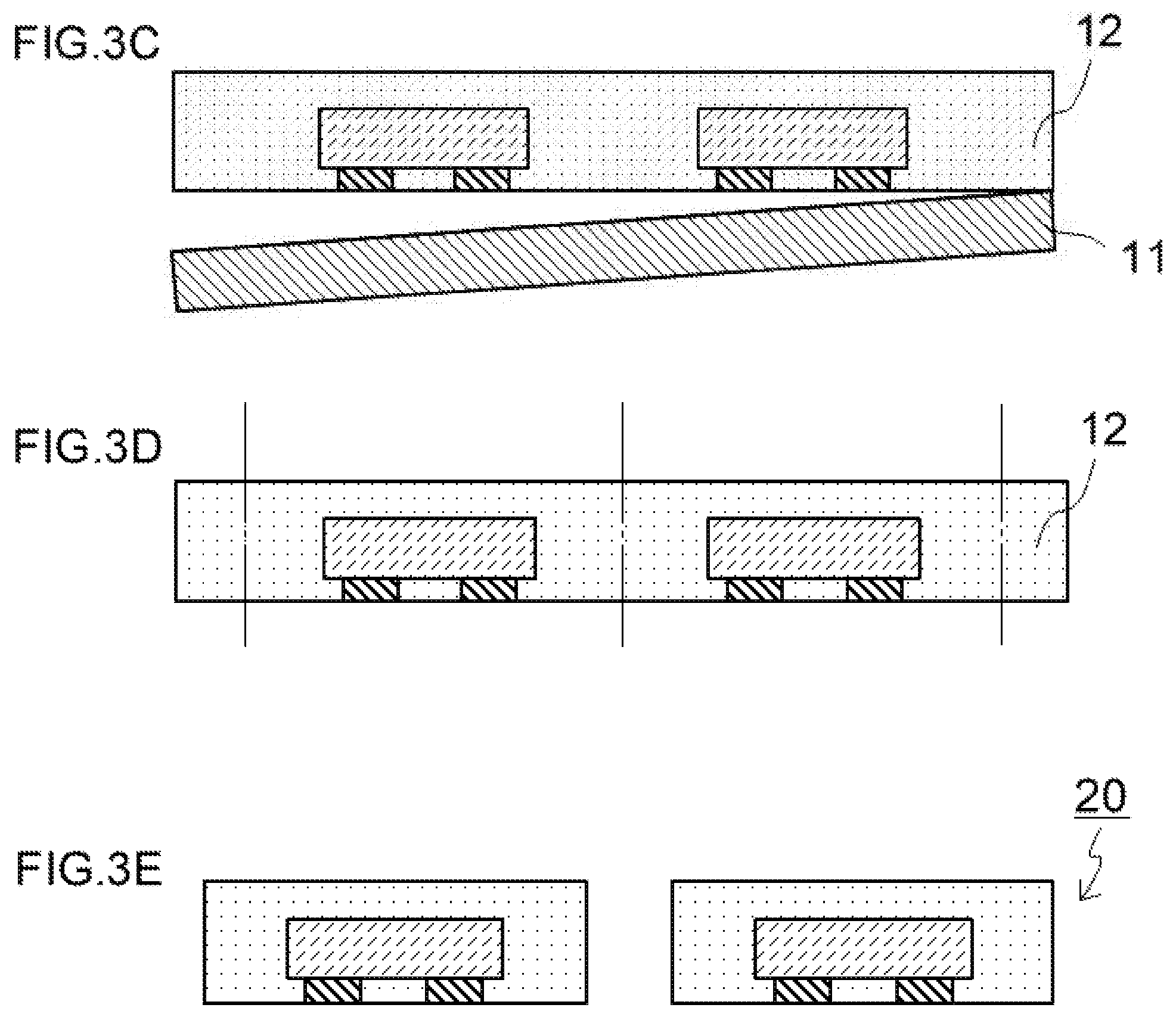
United States Patent |
10,930,822 |
Tsuruha , et al. |
February 23, 2021 |
Method of manufacturing light emitting device
Abstract
A method of manufacturing a light emitting device includes:
providing particles of a fluorescent material; providing a
substrate having a light emitting element mounted thereon;
providing a first resin solution and a second resin solution that
are two components of a two-component type curable resin; mixing
the particles of the fluorescent material in the first resin
solution to obtain a first suspension; allowing the first
suspension to stand; mixing the second resin solution with the
first suspension to obtain a second suspension after the allowing
of the first suspension to stand; and applying the second
suspension on the light emitting element and curing the second
suspension to obtain a sealing member.
Inventors: |
Tsuruha; Tomoaki (Anan,
JP), Uchiwa; Noritsugu (Tokushima, JP) |
Applicant: |
Name |
City |
State |
Country |
Type |
NICHIA CORPORATION |
Anan |
N/A |
JP |
|
|
Assignee: |
NICHIA CORPORATION (Anan,
JP)
|
Family
ID: |
59896586 |
Appl.
No.: |
16/251,862 |
Filed: |
January 18, 2019 |
Prior Publication Data
|
|
|
|
Document
Identifier |
Publication Date |
|
US 20190157518 A1 |
May 23, 2019 |
|
Related U.S. Patent Documents
|
|
|
|
|
|
|
Application
Number |
Filing Date |
Patent Number |
Issue Date |
|
|
15466959 |
Mar 23, 2017 |
10224465 |
|
|
|
Foreign Application Priority Data
|
|
|
|
|
Mar 24, 2016 [JP] |
|
|
2016-059655 |
|
Current U.S.
Class: |
1/1 |
Current CPC
Class: |
H01L
33/56 (20130101); H01L 33/502 (20130101); H01L
33/486 (20130101); H01L 33/507 (20130101); H01L
33/54 (20130101); H01L 2933/0041 (20130101); H01L
2224/48257 (20130101); H01L 2224/96 (20130101); H01L
2933/0033 (20130101); H01L 2224/48465 (20130101); H01L
2224/48091 (20130101); H01L 2924/181 (20130101); H01L
2933/005 (20130101); H01L 2224/48247 (20130101); H01L
33/501 (20130101); H01L 2224/48091 (20130101); H01L
2924/00014 (20130101); H01L 2924/181 (20130101); H01L
2924/00012 (20130101); H01L 2224/48465 (20130101); H01L
2224/48247 (20130101); H01L 2924/00 (20130101) |
Current International
Class: |
H01L
33/50 (20100101); H01L 33/56 (20100101); H01L
33/48 (20100101); H01L 33/54 (20100101) |
References Cited
[Referenced By]
U.S. Patent Documents
Foreign Patent Documents
|
|
|
|
|
|
|
101336258 |
|
Dec 2008 |
|
CN |
|
102504640 |
|
Jun 2012 |
|
CN |
|
103232802 |
|
Aug 2013 |
|
CN |
|
103289547 |
|
May 2016 |
|
CN |
|
109181478 |
|
Jan 2019 |
|
CN |
|
2006-321966 |
|
Nov 2006 |
|
JP |
|
2007-157798 |
|
Jun 2007 |
|
JP |
|
2008-088399 |
|
Apr 2008 |
|
JP |
|
2009-280763 |
|
Dec 2009 |
|
JP |
|
2014-056896 |
|
Mar 2014 |
|
JP |
|
2014-165225 |
|
Sep 2014 |
|
JP |
|
2015-042705 |
|
Mar 2015 |
|
JP |
|
2015-063619 |
|
Apr 2015 |
|
JP |
|
2011-125463 |
|
Oct 2011 |
|
WO |
|
2015-068513 |
|
May 2015 |
|
WO |
|
Other References
Non Final Office Action of the US continuation U.S. Appl. No.
15/466,959, dated Oct. 20, 2017. cited by applicant .
Final Office Action of the US continuation U.S. Appl. No.
15/466,959, dated May 14, 2018. cited by applicant .
Advisory Action of the US continuation U.S. Appl. No. 15/466,959,
dated Sep. 11, 2018. cited by applicant .
Notice of Allowance of the US continuation U.S. Appl. No.
15/466,959, dated Oct. 25, 2018. cited by applicant.
|
Primary Examiner: Nguyen; Sophia T
Attorney, Agent or Firm: Global IP Counselors, LLP
Parent Case Text
CROSS-REFERENCE TO RELATED PATENT APPLICATION
This application is a continuation application of U.S. patent
application Ser. No. 15/466,959 filed on Mar. 23, 2017. The present
application claims priority to Japanese Patent Application No.
2016-059655, filed on Mar. 24, 2016. The entire disclosures of U.S.
patent application Ser. No. 15/466,959 and Japanese Patent
Application No. 2016-059655 are hereby incorporated herein by
reference.
Claims
What is claimed is:
1. A method of manufacturing a light emitting device comprising:
providing particles of a fluorescent material; providing a
substrate having a light emitting element mounted thereon, the
light emitting element including a pair of electrodes; providing a
first resin solution and a second resin solution that are two
components of a two-component type curable resin, the second resin
solution containing a curing agent of the two-component type
curable resin; mixing the particles of the fluorescent material in
the first resin solution at a first agitation speed for a first
period of time to obtain a first suspension; allowing the first
suspension to stand; mixing the second resin solution with the
first suspension at a second agitation speed that is lower than the
first agitation speed for a second period of time that is shorter
than the first period of time to obtain a second suspension after
the allowing of the first suspension to stand; applying the second
suspension on the light emitting element so that the second
suspension covers the light emitting element including a region
between the electrodes, and curing the second suspension to obtain
a sealing member; and cutting the sealing member.
2. The method of manufacturing a light emitting device according to
claim 1, wherein the particles of the fluorescent material have an
average particle size in a range of 3 .mu.m to 30 .mu.m.
3. The method of manufacturing a light emitting device according to
claim 1, wherein the particles of the fluorescent material is mixed
in the first resin solution with an amount in a range of 10 mass %
to 80 mass % with respect to the first suspension.
4. The method of manufacturing a light emitting device according to
claim 1, wherein the fluorescent material is a manganese-activated
potassium fluosilicate-based fluorescent material.
5. The method of manufacturing a light emitting device according to
claim 4, wherein the particles of the fluorescent material have an
average particle size in a range of 3 .mu.m to 30 .mu.m.
6. The method of manufacturing a light emitting device according to
claim 5, wherein the particles of the fluorescent material is mixed
in the first resin solution with an amount in a range of 10 mass %
to 80 mass % with respect to the first suspension.
7. The method of manufacturing a light emitting device according to
claim 3, wherein the fluorescent material is a manganese-activated
potassium fluosilicate-based fluorescent material.
8. The method of manufacturing a light emitting device according to
claim 1, wherein the allowing of the first suspension to stand is
in a range from 12 hours to 36 hours.
9. The method of manufacturing a light emitting device according to
claim 1, wherein the providing of the substrate includes providing
the substrate having the light emitting element and an additional
light emitting element mounted thereon, the applying of the second
suspension includes applying the second suspension on the light
emitting element and the additional light emitting element, and the
cutting of the sealing member includes cutting the sealing member
between the light emitting element and the additional light
emitting element.
Description
BACKGROUND
1. Technical Field
The present disclosure is related to a method of manufacturing a
light emitting device.
2. Description of Related Art
The light emitting devices such as a light emitting diode (LED)
employing a semiconductor light emitting element (hereinafter may
also be referred to as "light emitting element") include those
provided with a fluorescent material to convert light emitted from
the light emitting element to light of different wavelength.
In manufacturing such light emitting devices, a liquid preparation
of a mixture of particles of a fluorescent material and a liquid
resin may be disposed on a light emitting element by potting and
cured. For the resin, a two-component type curable resin
composition using a main agent and a curing agent (such as
described in Japanese Unexamined Patent Application Publication No.
2015-63619, Japanese Unexamined Patent Application Publication No.
2014-56896, etc.) may be employed.
SUMMARY
However, obtaining of a homogeneous mixture may depend on the type
and/or the mixing ratio of the liquid resin and the fluorescent
material. This can result in unevenness in the emission color of
the light emitting device.
A method of manufacturing a light emitting device according to one
embodiment of the present disclosure includes: providing particles
of a fluorescent material; providing a substrate having a light
emitting element mounted thereon; providing a first resin solution
and a second resin solution that are two components of a
two-component type curable resin; mixing the particles of the
fluorescent material in the first resin solution to obtain a first
suspension; allowing the first suspension to stand; mixing the
second resin solution to the first suspension to obtain a second
suspension after the allowing to stand the first suspension; and
applying the second suspension on the light emitting element and
curing the second suspension to obtain a sealing member.
According to the method described above, the fluorescent material
can be mixed substantially uniformly, thereby preventing unevenness
in the emission color of a light emitting device.
BRIEF DESCRIPTION OF THE DRAWINGS
FIGS. 1A to 1D are schematic cross-sectional views illustrative of
a method of manufacturing a light emitting device of one embodiment
of the present invention.
FIGS. 2A to 2C are schematic cross-sectional views illustrative of
a method of manufacturing a light emitting device of one embodiment
of the present invention.
FIGS. 3A to 3E are schematic cross-sectional views illustrative of
a method of manufacturing a light emitting device of one embodiment
of the present invention.
DETAILED DESCRIPTION OF EMBODIMENTS
Preferred embodiments of the present invention will be described
below with reference to the accompanying drawings. The preferred
embodiments are intended as illustrative of a light emitting device
and a method of manufacturing the light emitting device to give a
concrete form to technical ideas of the present invention, and the
scope of the invention is not limited to those described below.
A method of manufacturing a light emitting device according to
certain embodiments of the present invention includes, providing
particles of a fluorescent material, providing a substrate having a
light emitting element mounted thereon, providing a first resin
solution and a second resin solution that are two components of a
two-component type curable resin, mixing the fluorescent material
in the first resin solution to obtain a first suspension, mixing
the second resin solution to the first suspension to obtain a
second suspension, and applying the second suspension on the light
emitting element and curing the second suspension to obtain a
sealing member.
The respective steps will be described below.
Providing Fluorescent Material
Particles of a fluorescent material are provided. The fluorescent
material is provided in particles with an average particle size in
a range of, for example, about 3 .mu.m to about 30 .mu.m, and the
shapes of the particles are approximately spherical or irregular.
The average particle size can be represented by D.sub.50. The
average particle size of the fluorescent material can be measured
by using, for example, a laser diffraction scattering method or an
image analysis method (i.e., a scanning electron microscopy (SEM),
a transmission electron microscopy (TEM)). Measuring of particle
size with a laser diffraction scattering method can be carried out
by using, for example, a SALD Series particle size analyzer (for
example, SALD-3100) manufactured by Shimadzu Corporation. An image
analysis method may be performed in compliance with JIS
Z8827-1:2008.
Examples of such a fluorescent material include an oxide-based
fluorescent material, a sulfide-based fluorescent material, and a
nitride-based fluorescent material. For example, in the case where
a gallium nitride based light emitting element to emit blue light
is used as the light emitting element, fluorescent materials that
can absorb blue light and emit light of different color may be
employed. Specific examples thereof include, YAG-based fluorescent
materials and LAG-based fluorescent materials to emit yellow to
green light, and SiAlON-based fluorescent materials
(.beta.-sialon-based fluorescent materials) and SGS-based
fluorescent materials to emit green light, and SCASN-based
fluorescent materials and CASN-based fluorescent materials,
manganese-activated potassium fluosilicate-based fluorescent
materials (KSF-based fluorescent materials: K.sub.2SiF.sub.6:Mn),
sulfide-based fluorescent materials to emit red light, and those
fluorescent materials are used singly or in combination.
Providing Substrate Having Light Emitting Element Mounted
Thereon
A substrate 11 having a light emitting element 14 mounted thereon,
as illustrated in FIG. 2A, is provided. In this step, a
commercially available substrate having a plurality of light
emitting elements mounted thereon may be provided, or a substrate
having a plurality of light emitting elements mounted thereon may
be provided through separately providing a substrate and a
plurality of light emitting elements and mounting the plurality of
light emitting elements on the substrate. Note that, for example,
in the description given with reference to FIG. 2A, a substrate
having a single light emitting element mounted thereon is
illustrated, but in typical manufacturing, a plurality of light
emitting elements is mounted on a single substrate. In other words,
a plurality of light emitting devices is collectively fabricated on
a single substrate, and through singulating, such a collective of
the light emitting devices are cut into individual light emitting
devices.
The light emitting element 14 includes a semiconductor layer and
electrodes. The semiconductor layer includes, for example, a p-type
semiconductor layer, a light emitting layer, and an n-type
semiconductor layer. The light emitting element 14 may further
include an element substrate. Further, positive and negative
electrodes are provided.
For the semiconductor layer, nitride-based compound semiconductors
such as In.sub.XAl.sub.YGa.sub.1-X-YN (0.ltoreq.X, 0.ltoreq.Y,
X+Y<1) can be suitably used. Those nitride-based semiconductor
layers may respectively have a single-layer structure, or a layered
structure made of layers of different compositions and thickness,
or a superlattice structure. Particularly, it is preferable that
the light emitting layer has a single quantum well structure or a
multiquantum well structure, in which thin layers each can produce
quantum effect are layered.
The positive and negative electrodes of the light emitting element
are arranged at a same surface side of the semiconductor layer. The
positive and negative electrodes may have either a single layer
structure or a layered structure, configured to be ohmically
connected (that is, linear or approximately linear current-voltage
characteristics is exhibited), to the p-type semiconductor layer
and the n-type semiconductor layer respectively.
The substrate 11 is a member on which the light emitting element 14
can be mounted, and which can serve as a base when a sealing member
to be described further below is disposed. For the substrate,
either a member configured to serve as a part of the light emitting
device, or a member that to be removed after disposing the sealing
member can be used.
For the substrate configured to serve as a part of the light
emitting device, for example as shown in FIG. 2A to 2C, a substrate
11 provided with a recess to mount the light emitting element 14
therein can be employed. The substrate 11 includes an insulating
base member 11b and electrically conductive portions 11a configured
to serve as the electrodes. For the base member, a resin, ceramic,
glass epoxy resin, or the like, can be used. When a resin is used
for the base member, the substrate may be a resin package molded
integrally with the leads so that portions of the leads are
contained in the resin package. When the base member is made of
ceramic, the substrate may be a ceramic package of a calcined
product of layered material of green sheets and metal thin films.
Such a substrate may have a flat-plate-like shape or a shape
provided with a recess to mount the light emitting element
therein.
For the substrate, a substrate that to be removed after disposing
the sealing member, that is, a substrate used only in the
manufacturing can also be used. For example, as shown in FIG. 3A,
the substrate 11 having a flat plate-like shape (or a sheet-like
shape) can be used. The substrate 11 can be any member on which the
light emitting element 14 can be mounted, as shown in FIG. 3A.
Also, the substrate 11 can be made of an appropriate material on
which the second mixture solution 12b can be disposed, and can be
resistant to heating temperature applied during curing the second
mixture solution to form the sealing member 12, as shown in FIG.
3B. Further, in this case, the substrate 11 is removed from the
sealing member 12 and the light emitting elements 14 as shown in
FIG. 3C, so that the substrate 11 is preferably a member that can
be easily removed. Removing of the substrate 11 can be carried out
by, for example, mechanical peeling or dissolving in a solvent. For
such a substrate 11, ceramics or the like can be employed.
Providing the substrate and the light emitting elements as
described above and mounting the light emitting elements on the
substrate with the use of a bonding member, the substrate having
the light emitting elements mounted thereon can be provided. For
the bonding member, an electrically conductive joining member or an
electrically insulating joining member can be used. Also, the light
emitting elements can be mounted either in a face-up manner or in a
flip-chip manner. When the substrate has adhesive characteristics
(for example, a wafer sheet), a separate joining member is not
needed. When a face-up mounting is employed, the electrically
conductive members of the substrate and the electrodes of each of
the light emitting elements may be electrically connected via
wires, respectively.
Providing First Resin Solution and Second Resin Solution
A first resin solution and a second resin solution that are
components of two-component type curable resin composition are
provided. When mixed, the first resin solution and the second resin
solution chemically react to form a cured product.
The first resin solution is a main agent of the two-component type
curable resin and has light-transmissive properties and
light-resisting properties. Specific examples of the resin used for
the first resin solution include a silicone resin, a modified
silicone resin, an epoxy resin, a modified epoxy resin, and an
acrylic resin. The examples also include a silicone resin, an epoxy
resin, a urea resin, a fluororesin, and a hybrid resin that
contains at least one of those resins.
The second resin solution contains a curing agent of the
two-component type curable resin. Specific examples of the resin
used for the second resin solution include a silicone resin, a
modified silicone resin, an epoxy resin, a modified epoxy resin,
and an acrylic resin. The examples also include a silicone resin,
an epoxy resin, a urea resin, a fluororesin, and a hybrid resin
that contains at least one of those resins.
Providing First Suspension
The first resin solution and particles of a fluorescent material
are mixed to provide a first suspension. The fluorescent material
can be mixed in a range of about 10 mass % to about 80 mass % with
respect to the first suspension.
As shown in FIG. 1A, the first resin solution 120A and the
fluorescent material particles P are placed in a mixing vessel 100
equipped with an agitator and are agitated. At this time, the first
resin solution 120A may be placed in the mixing vessel 100 and
feeding the fluorescent material particles P into the mixing vessel
100 while agitating the first resin solution 120A, or both the
first resin solution 120A and the fluorescent material particles
may be placed in the mixing vessel 100 and then agitated. In
addition to the fluorescent material particles P, a light diffusing
material or the like may be mixed.
The agitation is preferably carried out at a temperature in a range
of about 20.degree. C., to about 50.degree. C. The agitation may be
carried out by centrifugal agitation, vacuum centrifugal agitation,
manual agitation, etc. When centrifugal agitation is employed, for
example, a rotation speed in a range of 400 rpm to 1200 rpm with
respect to about 150 ml of the first suspension may be applied. The
agitating time in a range of 1 minute to 20 minutes may be
applied.
The first suspension 12A obtained by the agitation contains the
fluorescent material dispersed in the first resin solution, as
shown in FIG. 1B. The first suspension 12A is then allowed to stand
for 12 hours to 36 hours, at an appropriate temperature between
about 10.degree. C. and about 30.degree. C. The first suspension
12A may be allowed to stand in the mixing vessel or in another
vessel. The length of time of the standing can be appropriately
determined according to the composition, quantity of the resin, the
ratio of the fluorescent material, or the like.
Mixing of the fluorescent material only in the first resin solution
can facilitate uniform mixing of the fluorescent material in the
entire resin. This is considered as below. When the first resin
solution and the second solution are mixed before mixing the
fluorescent material, curing reaction may be initiated in a portion
of the mixed resin that may create a portion of different
characteristics to which a uniform mixing of the fluorescent
material may be difficult to obtain. However, when the fluorescent
material is mixed only in the first resin solution, in other words,
when the fluorescent material is mixed in a uniform resin, uniform
dispersion of the fluorescent material in the first resin solution
can be obtained, which in turn can facilitate uniform mixing of the
fluorescent material in the entire resin.
Providing Second Suspension
The first suspension and the second resin solution are mixed to
obtain a second suspension.
As shown in FIG. 1C, the second resin solution 120B is placed in
the mixing vessel 100 that contains the first suspension 12A. The
second resin solution 120B may be placed while agitating the first
suspension 12A, or the second solution 120B may be placed in the
first suspension 12A then start agitating.
The agitation is preferably carried out at a temperature in a range
of about 20.degree. C., to about 50.degree. C. The agitation may be
carried out by centrifugal agitation, vacuum centrifugal agitation,
manual agitation, etc. Mixing of the first resin solution and the
second resin solution initiates a chemical reaction, so that the
agitation time of the second suspension is preferably shorter than
the agitation time of the first suspension. When centrifugal
agitation is employed, for example, a rotation speed in a range of
400 rpm to 1200 rpm with respect to about 250 ml of the second
suspension may be applied. The agitation time in a range of 1
minute to 20 minutes may be applied. The second suspension 12B thus
obtained is transferred from the mixing vessel to a dispenser of a
molding machine.
Disposing Second Suspension to Cover Light Emitting Element and
Curing Second Suspension
As shown in FIG. 2B, a nozzle 140 of a dispenser is positioned over
the light emitting element 14 mounted on the substrate 11, and the
second suspension 12B is discharged through the nozzle 140 to carry
out potting. The amount of the second suspension 12B applied by the
potting is sufficient to enclose the entire of the light emitting
element 14, and when a wire is employed, to also enclose the
wire.
In the case shown in FIG. 2B, a recess is defined in the substrate
11, so that the substrate member 128 is applied by potting in the
recess. But in the case as shown in FIG. 3B, when the substrate 11
is not provided with a recess, the second suspension 12B can be
disposed by printing, compression molding, transfer molding, or the
like.
Subsequently, the second suspension 12B is cured by heating. Thus,
a sealing member 12 covering the light emitting element 14 mounted
on the substrate 11 can be obtained. The substrate 11 will be cut
to be singulated into a plurality of light emitting devices 10 in
which variation in the chromaticity is reduced.
In the case as shown in FIG. 3E, where each of the light emitting
devices 20 does not have the substrate, after removing the
substrate 11 as shown in FIG. 3A, the sealing member 12 is cut as
shown in FIG. 3D to singulate the light emitting devices 20 as
shown in FIG. 3E. In such a light emitting devices 20 that does not
have the substrate, the electrodes 14 of the light emitting element
14 can be exposed from the sealing member 12 so as to serve as the
electrodes of the light emitting device 20. To obtain this
configuration, as shown in FIG. 3A, the light emitting elements 14
are preferably mounted on the substrate 11 respectively with the
semiconductor layer 14a side facing upward and the electrodes 14b
and the substrate 11 are facing each other.
The substrate 11 having a flat plate-like shape as shown in FIG. 3A
may not be removed but is used as a constituting component of the
light emitting device. In such a case, as shown in FIG. 3B, the
sealing member 12 can be disposed to cover all the plurality of
light emitting elements 14, then, both the substrate 11 and the
sealing member 12 are cut to obtain the individual light emitting
devices.
EXAMPLES
Hereinafter, examples according to the embodiments of the present
invention will be described in detail. Needless to say, the present
invention is not limited only to the examples described below.
Example 1
A method of manufacturing a light emitting device will be described
illustrating a side-view type light emitting device having a
lateral width of 4.0 mm, a longitudinal width of 3.6 mm, and a
thickness of 2.05 mm. FIGS. 2A to 2C illustrate manufacturing steps
according to Example 1.
For the particles of a fluorescent material, a KSF-based
fluorescent material (K.sub.2SiF.sub.6:Mn) having an average
particle size of 20 .mu.m is provided. For the first resin
solution, a main agent (silicone resin) of the two-component type
curable resin is provided. For the second resin solution, a curing
agent (silicone resin) of the two-component type curable resin is
provided.
For the agitating machine, a centrifugal mixer (Model AR-500
manufactured by Thinky Corporation) equipped with a 500 ml mixing
vessel is provided. The first resin solution 50 ml and a KSF-based
fluorescent material 50 g (e.g., 50 mass % with respect to the
first suspension) are placed in the mixing vessel, and agitated in
the centrifugal mixer. Agitation speed is 1000 rpm and agitation
time is 3 minutes. The first suspension obtained by the agitation
is allowed to stand in the mixing vessel for about 18 hours.
Then, 50 ml of the second resin solution is placed in the mixing
vessel containing the first suspension described above, and
centrifugal agitation is carried out. Agitation speed is 600 rpm
and mixing time is 1 minute.
The second suspension obtained by agitation can be used in situ,
but preferably filtered before use. Filtration can be carried out
by, for example, using a filter having 212 .mu.m openings and
vacuum filtration.
Further, deaeration is preferably performed. For example, a
centrifugal vacuum deaeration mixer (Model ARV-310 manufactured by
Thinky Corporation) may be used. Agitation is performed at a
rotational speed of 600 rpm and an agitation time of 3 minutes. The
second suspension thus obtained is filled in the dispenser equipped
with a nozzle.
As shown in FIG. 2A, a substrate 11 having a light emitting element
14 mounted thereon is provided. For the light emitting element 14,
a light emitting element 14 having a nitride semiconductor layer
and a main emission peak wavelength of 445 nm is provided. For the
substrate 11, a resin package that includes a substrate 11 having
leads 11a and a molded resin member 11b is provided. Note that, in
manufacturing, a plurality of resin packages is collectively formed
and treated. The leads 11a are respectively a portion of a lead
frame that is formed by, for example, patterning a copper plate
having a thickness of 0.25 mm, a width of 200 mm and a length of 47
mm into a predetermined shape and applying a plating of silver
etc., on the surface thereof. A single lead frame is provided with
40 columns and 8 rows of the molded resin members 11b. Each read
package that includes a single molded resin member 11b and
corresponding leads corresponds to a single light emitting
device.
The resin package defines a recess of 3.4 mm in lateral width, 3.6
mm in longitudinal width, and 0.35 mm in depth. A surface of 1.13
mm in lateral width and 2.215 mm in longitudinal width defines the
bottom surface of the recess. A plurality of leads 11a configured
to serve positive and negative electrodes are exposed at the bottom
surface of the recess and the light emitting element 14 is mounted
on the exposed portions of the corresponding leads 11a. The molded
resin member 11b defines lateral surfaces of the recess. The molded
resin member 11b is exposed between the leads at the bottom surface
of the recess.
The leads 11a and the light emitting element 14 are bonded by a
bonding member. An upper surface of the light emitting element 14
is provided with p- and n-electrodes. The p- and n-electrodes are
respectively electrically connected to corresponding leads 11a via
wires 16.
As shown in FIG. 2B, a second suspension 12B is discharged through
the nozzle 140, potting over the light emitting element 14 mounted
on the substrate 11. Then, the substrate with the plurality of
packages is placed in a heating device and heated at 150.degree.
C., for 4 hours. Thus, the second suspension 12B in each recess is
cured to form the sealing member 12. Subsequently, the substrate is
cut to obtain each of a plurality of light emitting devices 10
shown in FIG. 2C.
Variations in chromaticity among 320 light emitting devices 10
obtained from a single substrate were about 20% less in x-values
and about 10% less in y-values, compared to that of the light
emitting devices obtained by using a suspension provided by mixing
the first resin solution and the second resin solution, then the
fluorescent material is mixed in the suspension.
The light emitting device according to the present invention can be
used for various kinds of light sources, such as illumination light
sources, light sources for various kinds of indicators, light
sources for automobile use, light sources for displays, back light
sources for liquid crystal displays, light sources for sensors, and
signals.
It is to be understood that although the present disclosure has
been described with regard to preferred embodiments thereof,
various other embodiments and variants may occur to those skilled
in the art, which are within the scope and spirit of the
disclosure, and such other embodiments and variants are intended to
be covered by the following claims.
* * * * *