U.S. patent number 10,882,431 [Application Number 16/217,114] was granted by the patent office on 2021-01-05 for road vehicle provided with an electric drive.
This patent grant is currently assigned to FERRARI S.P.A.. The grantee listed for this patent is FERRARI S.p.A.. Invention is credited to Franco Cimatti.





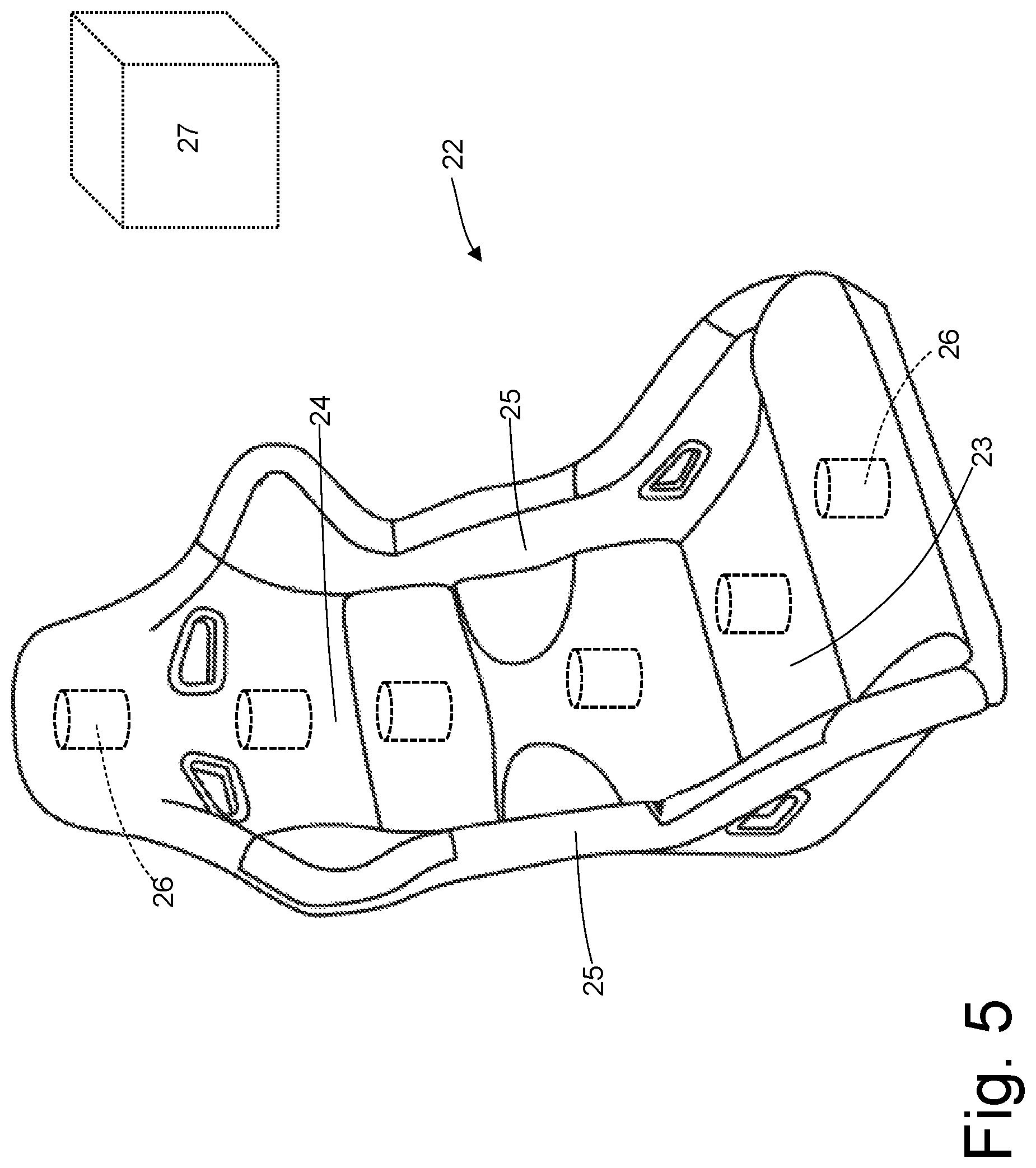


United States Patent |
10,882,431 |
Cimatti |
January 5, 2021 |
Road vehicle provided with an electric drive
Abstract
Road vehicle provided with an electric drive and having: at
least one pair of drive wheels; at least one electric machine; a
mechanical transmission that connects the electric machine to the
drive wheels; a passenger compartment; at least one seat, which is
housed in the passenger compartment and is provided with at least
one mechanical exciter that is designed to generate mechanical
vibrations at variable frequencies and intensities; and a control
unit, which is designed to drive the mechanical exciter using a
driving signal that derives from the noise generated by an internal
combustion thermal engine and based on the speed of rotation of the
electric machine and/or on the speed of rotation of the drive
wheels and/or on the torque generated/absorbed by the electric
machine.
Inventors: |
Cimatti; Franco (Pavullo,
IT) |
Applicant: |
Name |
City |
State |
Country |
Type |
FERRARI S.p.A. |
Modena |
N/A |
IT |
|
|
Assignee: |
FERRARI S.P.A. (Modena,
IT)
|
Family
ID: |
1000005281047 |
Appl.
No.: |
16/217,114 |
Filed: |
December 12, 2018 |
Prior Publication Data
|
|
|
|
Document
Identifier |
Publication Date |
|
US 20190202331 A1 |
Jul 4, 2019 |
|
Foreign Application Priority Data
|
|
|
|
|
Dec 13, 2017 [IT] |
|
|
102017000143862 |
|
Current U.S.
Class: |
1/1 |
Current CPC
Class: |
B60N
2/90 (20180201); B60Q 9/00 (20130101); B60W
50/16 (20130101); B60L 50/00 (20190201); B60K
6/22 (20130101); B60Y 2200/91 (20130101); B60Y
2200/92 (20130101); B60N 2002/981 (20180201); B60L
2250/00 (20130101) |
Current International
Class: |
B60N
2/90 (20180101); B60W 50/16 (20200101); A63F
9/24 (20060101); G05D 19/02 (20060101); B60L
50/00 (20190101); H04B 3/36 (20060101); B60Q
9/00 (20060101); B60K 6/22 (20071001) |
References Cited
[Referenced By]
U.S. Patent Documents
Foreign Patent Documents
Other References
Search Report and Written Opinion for IT Application No.
201700143862 completed Aug. 10, 2018 (7 pages). cited by
applicant.
|
Primary Examiner: Kan; Yuri
Attorney, Agent or Firm: Cantor Colburn LLP
Claims
The invention claimed is:
1. A road vehicle (1) provided with an electric drive (4); the road
vehicle (1) comprises: at least one pair of drive wheels (3); at
least one electric machine (8, 15), which is connected to the drive
wheels (3); a passenger compartment (17); at least one seat (22),
which is housed in the passenger compartment (17) and is provided
with at least one mechanical exciter (26) configured to generate
mechanical vibrations with variable frequency and intensity; and a
control unit (27) configured to drive the at least one mechanical
exciter (26) to generate the mechanical vibrations, wherein the
variable frequency is dependent on a rotational speed of the
electric machine (8; 15) and/or a rotational speed of the drive
wheels (3) and wherein the intensity is dependent on torque
generated and/or absorbed by the electric machine (8; 15).
2. The road vehicle (1) according to claim 1, wherein the frequency
of the mechanical vibrations generated by the at least one
mechanical exciter (26) increases by increasing the rotational
speed of the electric machine (8; 15) and/or the rotational speed
of the drive wheels (3).
3. The road vehicle (1) according to claim 1, wherein the variable
frequency of the mechanical vibrations generated by the at least
one mechanical exciter (26) exclusively depends on the rotational
speed of the electric machine (8; 15) and/or on the rotational
speed of the drive wheels (3).
4. The road vehicle (1) according to claim 1, wherein the variable
frequency of the vibrations generated by the at least one
mechanical exciter (26) further depends on the torque generated
and/or absorbed by the electric machine (8; 15).
5. The road vehicle (1) according to claim 4, wherein the variable
frequency of the mechanical vibrations generated by the at least
one mechanical exciter (26) increases by increasing the torque
generated and/or absorbed by the electric machine (8; 15).
6. The road vehicle (1) according to claim 1, wherein the intensity
of the mechanical vibrations generated by the at least one
mechanical exciter (26) increases by increasing the torque
generated and/or absorbed by the electric machine (8; 15).
7. The road vehicle (1) according to claim 1, wherein the intensity
of the mechanical vibrations generated by the at least one
mechanical exciter (26) exclusively depends on the torque generated
and/or absorbed by the electric machine (8; 15).
8. The road vehicle (1) according to claim 1, wherein the intensity
of the mechanical vibrations generated by the at least one
mechanical exciter (26) further depends on the rotational speed of
the electric machine (8; 15) and/or on the rotational speed of the
drive wheels (3).
9. The road vehicle (1) according to claim 8, wherein the intensity
of the mechanical vibrations generated by the at least one
mechanical exciter (26) increases by increasing the rotational
speed of the electric machine (8; 15) and/or the rotational speed
of the drive wheels (3).
10. The road vehicle (1) according to claim 1, wherein the control
unit (27) is designed to drive the at least one mechanical exciter
(26) using a control signal, which is modulated in frequency based
on the rotational speed of the electric machine (8; 15) and/or on
the rotational speed of the drive wheels (3), and is modulated in
amplitude based on the torque generated and/or absorbed by the
electric machine (8; 15).
11. The road vehicle (1) according to claim 1, wherein the control
unit (27) is configured to drive the at least one mechanical
exciter (26) using a control signal, which derives from a noise
generated by an internal combustion thermal engine.
12. The road vehicle (1) according to claim 11, wherein the control
signal reproduces the noise generated by the internal combustion
thermal engine.
13. The road vehicle (1) according to claim 1, wherein the at least
one seat (22) comprises a plurality of the mechanical exciters (26)
arranged in different positions; and the control unit (27)
differently drives the mechanical exciters (26) based on their
position by differentiating a starting driving signal and/or by
differentiating an amplitude and frequency modulation.
14. The road vehicle (1) according to claim 1, wherein: the at
least one seat (22) comprises a plurality of the mechanical
exciters (26) arranged in different positions; and the plurality of
the mechanical exciters (26) are different from each other, wherein
the mechanical exciters (26) embedded in a seat bottom (23) of the
at least one seat (2) are more powerful and have a lower dynamic
capacity relative to the mechanical exciters (26) embedded in a
seat backrest (24) of the at least one seat (2) having less power
and higher dynamic capacity.
15. The road vehicle (1) according to claim 4, wherein: a majority
part of the variable frequency of the mechanical vibrations
generated by the at least one mechanical exciter (26) depends on
the rotational speed of the electric machine (8; 15) and/or on the
rotational speed of the drive wheels (3); and a minority part of
the variable frequency of the mechanical vibrations generated by
the at least one mechanical exciter (26) depends on the torque
generated and/or absorbed by the electric machine (8; 15).
16. The road vehicle (1) according to claim 4, wherein: 85-95% of
the variable frequency of the mechanical vibrations generated by
the at least one mechanical exciter (26) depends on the rotational
speed of the electric machine (8; 15) and/or on the rotational
speed of the drive wheels (3); and 15-5% of the variable frequency
of the mechanical vibrations generated by the at least one
mechanical exciter (26) depends on the torque generated and/or
absorbed by the electric machine (8; 15).
17. The road vehicle (1) according to claim 8, wherein a majority
part of the intensity of the mechanical vibrations generated by the
at least one mechanical exciter (26) depends on the torque
generated and/or absorbed by the electric machine (8; 15); and a
minority part of the intensity of the mechanical vibrations
generated by the at least one mechanical exciter (26) depends on
the rotational speed of the electric machine (8; 15) and/or on the
rotational speed of the drive wheels (3).
18. The road vehicle (1) according to claim 8, wherein: 70-90% of
the intensity of the mechanical vibrations generated by the at
least one mechanical exciter (26) depends on the torque generated
and/or absorbed by the electric machine (8; 15); and 30-10% of the
intensity of the vibrations generated by the at least one
mechanical exciter (26) depends on the rotational speed of the
electric machine (8; 15) and/or on the rotational speed of the
drive wheels (3).
Description
CROSS-REFERENCE TO RELATED APPLICATIONS
This patent application claims priority from Italian patent
application no. 102017000143862 filed on Dec. 13, 2017, the entire
disclosure of which is incorporated herein by reference.
TECHNICAL FIELD
The present invention relates to a road vehicle provided with an
electric drive.
PRIOR ART
When a road vehicle is driven by a thermal engine, the thermal
engine generates relatively intense noise and vibrations,
essentially due to the bursts (i.e. the violent combustion) inside
the cylinders and to the reciprocating motion (pistons-connecting
rods-cranks). Obviously, the noise and the vibrations are linked to
the speed of rotation of the drive shaft (in commercial and
petrol-fuelled internal combustion engines, the speed of rotation
is normally between 600-900 rpm at the minimum and 6000-9000 rpm in
the most performing engines). The noise and the vibrations
generated by the thermal engine are transmitted (in a more or less
attenuated way) inside the passenger compartment and are therefore
clearly perceived by the occupants of the passenger compartment and
in particular by the driver. Particularly when sporty driving a
high performance road vehicle, the noise and the vibrations
perceived by the driver are an integral part of the driving
experience and contribute to transmitting positive feelings to the
driver. In other words, when a driver drives a high performance
road vehicle in a sporting manner, besides obtaining accelerations
and high speeds, she/he also expects to perceive a certain type of
noise and a certain type of vibrations, whose absence (or strong
attenuation) is therefore negative.
When a road vehicle is driven by an electric machine (working as an
electric engine), the electric machine generates a noise solely due
to the high-speed rotary motion and generates vibrations solely due
to electrical and mechanical imbalances. Obviously, the noise and
the vibrations are linked to the speed of rotation of the electric
machine drive shaft (in commercial electric machines used in the
automotive sector the speed of rotation is normally between 0 rpm
and 16000-20000 rpm). Consequently, in a road vehicle the
vibrations and the noise generated by a thermal engine are very
different from the vibrations and the noise generated by an
electric machine, both in terms of intensity (which is decidedly
lower in the electric machine) and in terms of frequency (generally
much higher in the electric machine). For example, the sound
produced by a thermal engine is perceived by the driver like a
rumble (namely, like a loud and deep noise), whereas the sound
produced by an electric machine is perceived by the driver as an
acute and tenuous hiss (namely, much more similar to an electrical
appliance than to a conventional machine).
In other words, electric road vehicles are characterized by the
replacement of a combustion-driven thermal engine provided with a
reciprocating motion (pistons-connecting rods-cranks) with a rotary
electric engine. The familiar feeling for the users of road
vehicles driven by thermal engines is the presence of
vibro-acoustics linked to the engine orders of the thermal engine
(both as combustion and as oscillating dynamics). The engine orders
are linked to the number of cylinders set in motion by rotation,
and are therefore proportional to the engine speed of rotation.
This familiar feeling is almost completely lacking in electric
drive vehicles due to the absence of combustion, the absence of
alternate motion mechanics, the foreseeable simplification of the
transmission lines and the different (even several times higher)
speeds of rotation of the electric engines. Thus, not only do the
levels change, but also the frequencies of vibro-acoustic
sensations, with the presence of predictably higher frequencies. On
the contrary, in the overall noise of an electric road vehicle, the
part not linked to the powertrain increases: the aerodynamic noise
based on the speed of the road vehicle, the rolling noise of the
wheels on the road and the noise of the devices on board the
vehicle (air conditioning, automatic actuations . . . ).
In case of an electric drive and trying to compensate for the
absence of the usual noise of a thermal engine, it has been
proposed to use speakers installed in the passenger compartment to
artificially generate a sound that can simulate in a more or less
faithful way the noise of a thermal engine. However, the use of the
speakers installed in the passenger compartment to generate a noise
from a thermal engine tends to generate a noise that is perceived
by the driver as not very natural (and therefore unpleasant since
"artificial").
The patent application DE102008040113A1 describes a hybrid-driven
road vehicle, therefore provided with a transmission line
comprising an internal combustion thermal engine and an electric
machine that can operate as an engine. A mechanical exciter is
incorporated in a driver's seat, said exciter being designed to
generate mechanical vibrations and, when the thermal engine is
switched off, being driven based on the status of the transmission
line to indicate when the transmission line is active and therefore
ready to respond to the accelerator command.
The U.S. Pat. No. 5,635,903A describes an electric vehicle provided
with (at least) a loudspeaker arranged inside the passenger
compartment and (at least) a loudspeaker arranged outside the
bodywork. Both speakers are driven to reproduce a sound depending
on a speed of rotation of the wheels, a vehicle advancement speed,
a position of an accelerator control and an ambient noise captured
by a microphone.
The patent application US2002082754A1 describes a hybrid-driven
road vehicle that is therefore provided with a transmission line
comprising an internal combustion thermal engine and an electric
machine that can operate as an engine. According to a possible
embodiment, a mechanical exciter is provided (e.g. arranged in the
steering wheel or in the driver's seat), which is designed to
generate mechanical vibrations and is driven only when the thermal
engine is off and the advancing speed is lower than a predetermined
threshold to indicate to the driver that the electric machine is
active.
DESCRIPTION OF THE INVENTION
The object of the present invention is to provide a road vehicle
equipped with an electric drive, which allows the driver to have
pleasant vibro-acoustic sensations.
According to the present invention, it is provided a road vehicle
with an electric drive as claimed in the appended claims.
The claims describe preferred embodiments of the present invention
forming an integral part of the present disclosure.
BRIEF DESCRIPTION OF THE DRAWINGS
The present invention will now be described with reference to the
annexed drawings showing an example of a non-limiting embodiment,
in which:
FIG. 1 is a schematic and plan view of a hybrid road vehicle
equipped with an electric drive system made in accordance with the
present invention;
FIG. 2 is a schematic and plan view of an alternative embodiment of
the road vehicle of FIG. 1 with an exclusively electric drive;
FIG. 3 is a schematic and lateral view of the road vehicle of FIG.
1;
FIG. 4 is a schematic and perspective view of a driving seat of the
road vehicle of FIG. 1; and
FIGS. 5, 6 and 7 are schematic and perspective views of respective
variants of the driving seat of FIG. 4.
PREFERRED EMBODIMENTS OF THE INVENTION
In FIG. 1, the number 1 indicates as a whole a hybrid-driven road
vehicle provided with two front wheels 2 and two rear drive wheels
3, which receive the driving torque from a hybrid drive system
4.
The hybrid drive system 4 comprises an internal combustion thermal
engine 5, which is arranged in a front position and is provided
with a drive shaft 6, a mechanical transmission 7, which transmits
the driving torque generated by the internal combustion engine 5 to
the rear drive wheels 3, and an electric machine 8 that is
mechanically connected to the mechanical transmission 7 and is
reversible (i.e. it can work both as an electric engine by
absorbing electrical power and generating mechanical power and as
an electric generator by absorbing mechanical power and generating
electrical power).
The mechanical transmission 7 comprises a transmission shaft 9 that
on the one side is angularly integral with the drive shaft 6 and on
the other side is mechanically connected to a double clutch gearbox
10, which is arranged in the rear position and transmits the motion
to the rear drive wheels 3 by means of two axle shafts
(half-shafts) 11, which receive the motion from a differential 12.
The electric machine 8 is mechanically connected to the gearbox 10
and in particular is angularly integral with a primary shaft of the
gearbox 10. With regard to how to connect the electric machine 8 to
the double clutch gearbox 10, for example, please refer to the
patent application EP2325034A1.
FIG. 2 shows an alternative embodiment of the road vehicle 1, in
which the drive system 4 instead of being hybrid is purely
electric. In particular, the electric drive system 4 is arranged in
the rear position and comprises two reversible electric machines
15, each of which is angularly integral with a corresponding rear
drive wheel 3 (namely a corresponding axle shaft 11 of a rear drive
wheel 3) by interposing a mechanical transmission 16 having its own
(generally non-unitary) transmission ratio. In the embodiment shown
in FIG. 2, the electric drive system 4 comprises two independent
electric machines 15 to apply to the two rear drive wheels 3
differentiated driving torques (thus allowing the use of the
"torque vectoring" control) and to avoid the use of a differential.
According to a different embodiment not shown, the electric drive
system 4 comprises a single electric machine 15 and a single
mechanical transmission 16 provided with a differential from which
the two axle shafts 11 depart. As shown in FIG. 3, the road vehicle
1 comprises a passenger compartment 17 frontally limited by a
dashboard 18, which is arranged beneath a windshield 19. The
dashboard 18 supports an instrument panel 20, which is arranged in
front of the driver, immediately behind a steering wheel 21. A
driving seat 22 is arranged inside the passenger compartment, said
seat being arranged in front of the dashboard 18 (and therefore in
front of the steering wheel 21).
According to what shown in FIG. 4, the driving seat 22 comprises a
seat bottom 23, which is substantially horizontal and on which the
driver rests her/his legs, and a seat backrest 24, which is
substantially vertical, ends with an (integrated) headrest and on
which the driver rests her/his back. According to a preferred (but
not limiting) embodiment, the driving seat 22 comprises two
containment sides 25, which may be more or less accentuated and
hold the driver sideways inside the driving seat 22. The two
containment sides 25 normally develop both at the seat bottom 23
and at the seat backrest 24.
Mechanical exciters 26 (also called shakers) are embedded inside
the driving seat 22 and are designed to generate mechanical
vibrations with a variable frequency and intensity. As shown in the
various embodiments of FIGS. 4-7, the number and the arrangement of
the mechanical exciters 26 inside the driving seat 22 vary
depending on the desired result and on the desired expense. The
minimum configuration provides a single mechanical exciter 26
embedded in the driving seat 22 (generally near the headrest).
A control unit 27 is provided, which is designed to drive the
mechanical exciters 26 by using a (previously stored) driving
signal, which derives from the noise generated by an internal
combustion thermal engine. For example, the driving signal could
reproduce more or less faithfully the noise generated by an
internal combustion engine or it could be a reprocessing of the
noise generated by an internal combustion thermal engine that
retains only some traits of the original noise.
The driving signal is modulated (changed) in frequency and
amplitude based on the speed of rotation of the electric machine 8
or 15, and/or on the speed of rotation of the rear drive wheels 3
(i.e. the forward speed of the road vehicle 1, which is directly
proportional to the speed of rotation of the rear drive wheels 3),
and/or of the torque generated/absorbed by the electric machine 8
or 15. When there are two (or more) independent electric machines
15, only one of the electric machines 15 (namely a "master"
electric machine 15) can be considered, or it can be considered an
average of the electric machines 15 (i.e. it is considered an
average speed of rotation of the electric machines 15 and an
average generated/absorbed torque of the electric machines 15).
Please note that the speed of rotation of the electric machine 8 or
15 can be completely equivalent to the speed of rotation of the
rear drive wheels 3 (when the mechanical transmission ratio between
the shaft of the electric machine 8 or 15 and the rear drive wheels
3 is stable). In this case, only the speed of rotation of the
electric machine 8 or 15 is considered, or only the speed of
rotation of the rear drive wheels 3 is considered. Alternatively,
the speed of rotation of the electric machine 8 or 15 may be
different from the speed of rotation of the rear drive wheels 3
(when the mechanical transmission ratio between the shaft of the
electric machine 8 or 15 and the rear drive wheels 3 is variable).
In this case it is possible to consider only the speed of rotation
of the electric machine 8 or 15, only the speed of rotation of the
rear drive wheels 3, both the speed of rotation of the electric
machine 8 or 15 and the speed of rotation of the rear drive wheels
3, an average (possibly weighted) of the speed of rotation of the
electric machine 8 or 15 and of the speed of rotation of the rear
drive wheels 3.
The control unit 27 is designed to drive the mechanical exciters 26
so that the mechanical exciters 26 generate vibrations having a
frequency depending on the speed of rotation of the electric
machine 8 or 15 and/or on the speed of rotation of the rear drive
wheels 3. In other words, the control unit 27 modulates (varies) in
frequency the driving signal based on the speed of rotation of the
electric machine 8 or 15 and/or the speed of rotation of the rear
drive wheels 3. In this case, the frequency of the vibrations
generated by the mechanical exciters 26 increases by increasing the
speed of rotation of the electric machine 8 or 15 and/or the speed
of rotation of the rear drive wheels 3. In particular, the increase
may be normal (the frequency of the vibrations generated by the
mechanical exciters 26 is greater than or equal to the increase in
the speed of rotation of the electric machine 8 or 15 and/or of the
speed of rotation of the rear wheels 3), or the increase can be
tight (the frequency of the vibrations generated by the mechanical
exciters 26 is strictly higher by increasing the speed of rotation
of the electric machine 8 or 15 and/or the speed of rotation of the
rear drive wheels 3).
According to a possible embodiment, the frequency of the vibrations
generated by the mechanical exciters 26 depends only on the speed
of rotation of the electric machine 8 or 15 and/or on the speed of
rotation of the rear drive wheels 3 (i.e. the frequency of the
vibrations generated by the mechanical exciters 26 does not depend
on the torque generated/absorbed by the electric machine 8 or
15).
According to an alternative embodiment, the frequency of the
vibrations generated by the mechanical exciters 26 depends both on
the speed of rotation of the electric machine 8 or 15 and/or on the
speed of rotation of the rear drive wheels 3 and on the torque
generated/absorbed by the electric machine 8 or 15. In this case,
the dependence of the frequency of the vibrations generated by the
mechanical exciters 26 on the torque generated/absorbed by the
electric machine 8 or 15 is modest and provides that the frequency
of the vibrations generated by the mechanical exciters 26 increases
by increasing the torque generated/absorbed by the electric machine
8 or 15. In particular, the frequency of the vibrations generated
by the mechanical exciters 26 depends for the most part (85-95%) on
the speed of rotation of the electric machine 8 or 15 and/or on the
speed of rotation of the rear drive wheels 3 and depends to a
minimum extent (15-5%) on the torque generated/absorbed by the
electric machine 8 or 15.
The control unit 27 is designed to drive the mechanical exciters 26
so that the mechanical exciters 26 generate vibrations having an
intensity dependent on the torque generated/absorbed by the
electric machine 8 or 15. In other words, the control unit 27
modulates (varies) in amplitude the driving signal based on the
torque generated/absorbed by the electric machine 8 or 15. In this
case, the intensity of the vibrations generated by the mechanical
exciters 26 increases by increasing the torque generated/absorbed
by the electric machine 8 or 15. In particular, the increase can be
normal (the intensity of the vibrations generated by the mechanical
exciters 26 is greater than or equal to the increase of the torque
generated/absorbed by the electric machine 8 or 15), or the
increase can be tight (the intensity of the vibrations generated by
the mechanical exciters 26 is strictly higher by increasing the
torque generated/absorbed by the electric machine 8 or 15).
According to a possible embodiment, the intensity of the vibrations
generated by the mechanical exciters 26 depends only on the torque
generated/absorbed by the electric machine 8 or 15 (i.e. the
intensity of the vibrations generated by the mechanical exciters 26
does not depend on the speed of rotation of the electric machine 8
or 15 and/or on the speed of rotation of the rear drive wheels
3).
According to an alternative embodiment, the intensity of the
vibrations generated by the mechanical exciters 26 depends both on
the torque generated/absorbed by the electric machine 8 or 15 and
on the speed of rotation of the electric machine 8 or 15 and/or on
the speed of rotation of the rear drive wheels 3. In this case, the
dependence of the intensity of the vibrations on the speed of
rotation of the electric machine 8 or 15 and/or on the speed of
rotation of the rear drive wheels 3 is modest and provides that the
intensity of the vibrations generated by the mechanical exciters 26
increases by increasing the speed of rotation of the electric
machine 8 or 15 and/or the speed of rotation of the rear drive
wheels 3. In particular, the intensity of the vibrations generated
by the mechanical exciters 26 depends for the most part (70-90%) on
the torque generated/absorbed by the electric machine 8 or 15 and
depends to a minimum extent (30-10%) on the speed of rotation of
the electric machine 8 or 15 and/or on the speed of rotation of the
rear drive wheels 3. According to a possible embodiment, the
control unit 27 stores a mathematical map (namely a numeric
matrix), which at the input receives the speed of rotation of the
electric machine 8 or 15 and/or the speed of rotation of the rear
drive wheels 3 and the torque generated/absorbed by the electric
machine 8 or 15 (this value is generally marked to distinguish the
generated torque from the absorbed torque) and at the output
provides a pair of multiplier coefficients (potentially greater
than, equal to or smaller than one), which allow modulating
(varying) the frequency and the intensity the driving signal,
respectively.
In the embodiment described above, the control unit 27 drives all
the mechanical exciters 26 in exactly the same way (i.e. by using
the same starting driving signal with the same amplitude and
frequency modulation). According to a different embodiment, the
control unit 27 drives differently the mechanical exciters 26 based
on their position (e.g. the mechanical exciters 26 of the seat
backrest 24 are driven differently with respect to the mechanical
exciters 26 of the seat bottom 23, or the mechanical exciters 26 at
the headrest are driven differently from the other mechanical
exciters 26 of the seat backrest 24). The control unit 27 can
differentiate the driving of the mechanical exciters 26 by
differentiating the starting driving signal and/or by
differentiating the amplitude and frequency modulation.
According to a possible embodiment, all the mechanical exciters 26
are identical. Alternatively, the mechanical exciters 26 could be
different: for example, the mechanical exciters 26 embedded in the
seat bottom 23 may be more powerful and have a lower dynamic
capacity, while the mechanical exciters 26 embedded in the seat
backrest 24 (particularly near the headrest) may be less powerful
and have a greater dynamic capacity.
According to a possible embodiment, the control unit 27 could have
stored several different starting signals (more or less sporty)
which can, for example, be selected according to the driver's
preferences (e.g. expressed through the so-called "manettino",
which allows the driver to set the road vehicle 1 for a relaxed
driving, for a sporty driving, for a racing driving, for driving in
the wet, for driving on icy surfaces . . . ). Analogously, also the
amplitude and frequency modulation of the starting driving signal
could be varied based on the driver's preferences (e.g. expressed
through the so-called "manettino").
In the embodiment described above, only the driving seat 22 is
provided with mechanical exciters 26. According to other perfectly
equivalent embodiments, the mechanical exciters 26 are also present
in the passenger seats (possibly in a smaller number if compared to
the driving seat 22).
By way of example, each mechanical exciter 26 is of the
electrodynamic type and comprises a fixed ferromagnetic armature
provided with at least one permanent magnet, which generates a
constant magnetic field, and a coil (optionally coupled to a mobile
ferromagnetic armature), which is axially floating through special
linear guides, is immersed in the constant magnetic field, is
integral with a vibrating mass (which can be formed by the mobile
ferromagnetic armature) and can be flown through by an alternating
current (namely variable over time). By varying the frequency and
the intensity of the voltage applied to the coil (i.e. by varying
the frequency and the intensity of the electric current that passes
through the coil), also the frequency and the stroke of the
oscillating movement of the coil vary (and therefore of the
vibrating mass that is integral with the coil), and then the
frequency and intensity of the vibrations generated by the
mechanical exciters 26 vary.
In an electrodynamic mechanical exciter 26 the upper frequency
limit is determined by the natural frequency of the coil and is of
the order of some kHz (3-6 kHz). Moreover, an electrodynamic
mechanical exciter 26 normally has a bad behaviour at frequencies
lower than 5-10 Hz. These frequency limits are not problematic in
this application, in which the vibrations to be generated by the
mechanical exciters 26 generally have a frequency between 20-40 Hz
and 2-3 kHz.
Please note that in particular situations (for example in an
emergency) the mechanical exciters 26 embedded in the driving seat
22 can be used not to generate a pleasant vibro-acoustic sensation,
but to provide the driver with a tactile sensation that calls the
driver's attention. For example, the mechanical exciters 26
embedded in the driving seat 22 can be used when the driver shows a
tendency to fall asleep, in the event of a possible/potential
impact against an obstacle placed in front of the vehicle and in
the event of overstepping the stripe that delimits the edge of the
carriageway.
The embodiments described herein can be combined without departing
from the scope of protection of the present invention.
The road vehicle 1 described above has numerous advantages. First,
the road vehicle 1 described above allows locating the
vibro-acoustic sensation generated by the mechanical exciters 26 in
very close proximity to the users, since it concentrates the
mechanical exciters 26 on the driving seat 22. This allows limiting
the total number of mechanical exciters 26 and reaching the users
in a direct way.
Moreover, the road vehicle 1 described above provides quite a
natural reproduction of the vibro-acoustic sensation of a thermal
engine, providing the users with a very pleasant and not too
invasive experience. In other words, the vibro-acoustic sensation
produced by the mechanical exciters 26 embedded in the driving seat
22 corresponds to the driver's wishes/expectations.
Finally, the road vehicle 1 described above is easy to manufacture,
since a normal driving seat 22 offers a large usable space to
easily embed the mechanical exciters 26.
LIST OF REFERENCE NUMBERS OF THE FIGURES
1 road vehicle 2 front wheels 3 rear wheels 4 drive system 5 engine
6 drive shaft 7 transmission 8 electric machine 9 transmission
shaft 10 mechanical gearbox 11 axle shafts 12 differential 13
electronic power converter 14 accumulation system 15 electric
machine 16 mechanical transmission 17 passenger compartment 18
dashboard 19 windshield 20 instrument panel 21 steering wheel 22
driving seat 23 seat bottom 24 seat backrest 25 containment sides
26 mechanical exciter 27 control unit
* * * * *