U.S. patent number 10,850,380 [Application Number 15/146,547] was granted by the patent office on 2020-12-01 for multi-speed power tool with electronic clutch.
This patent grant is currently assigned to Milwaukee Electric Tool Corporation. The grantee listed for this patent is Milwaukee Electric Tool Corporation. Invention is credited to Cole Conrad, Daniel Robert Ertl, Alex Huber, Mark Alan Kubale, Matthew Mergener, Carl Benjamin Westerby, Matthew Wycklendt, Wing Fung Yip.

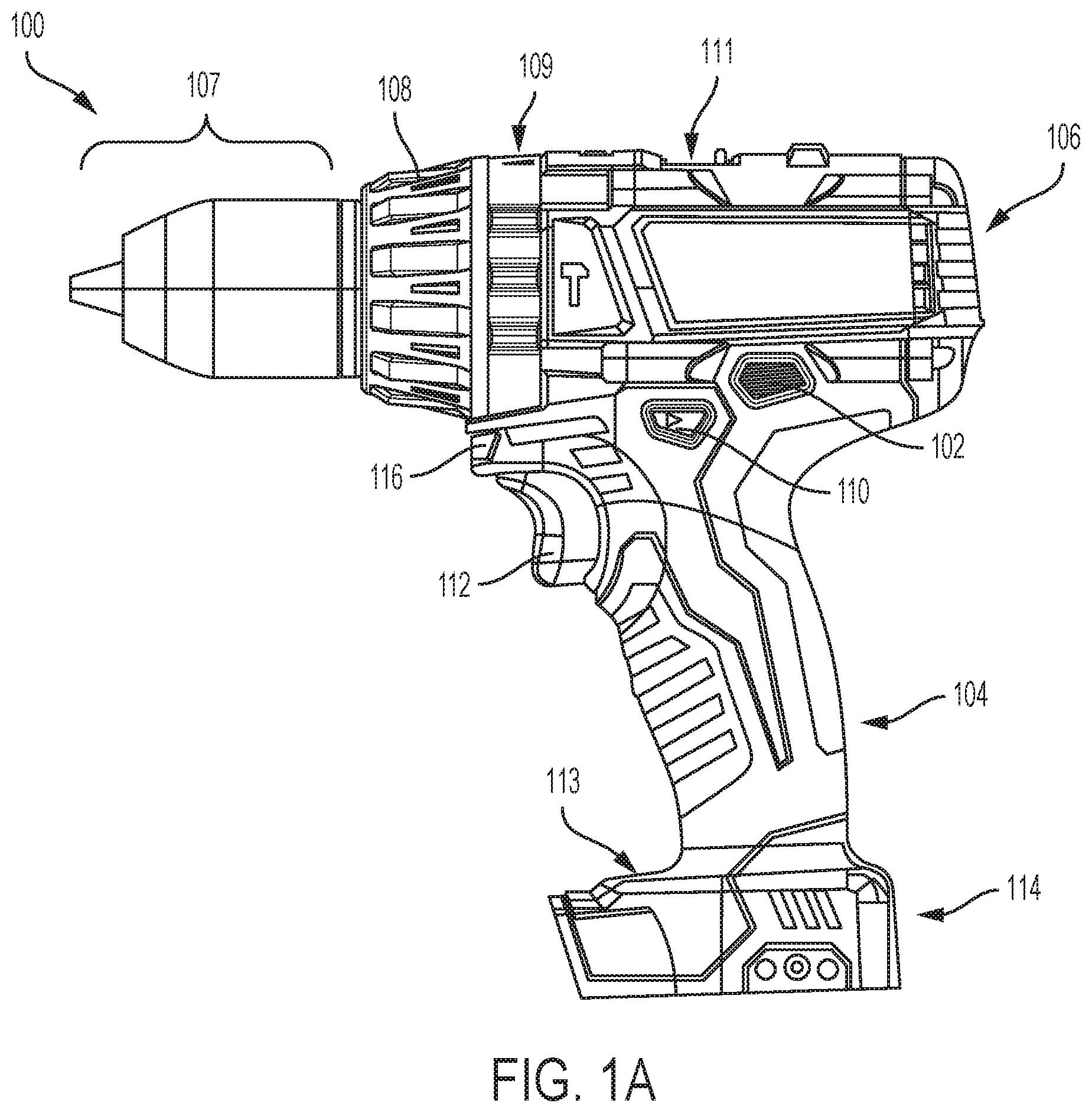
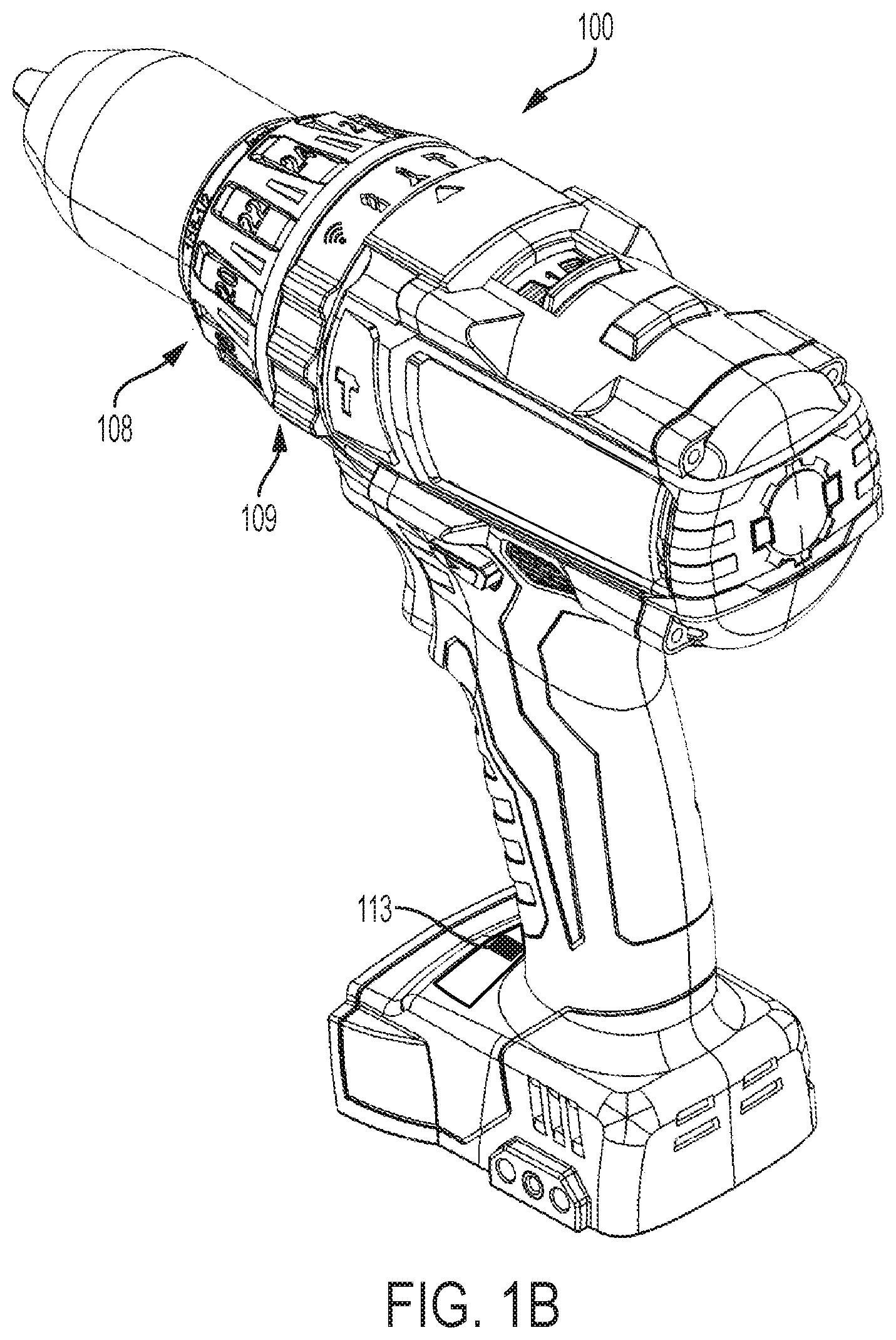

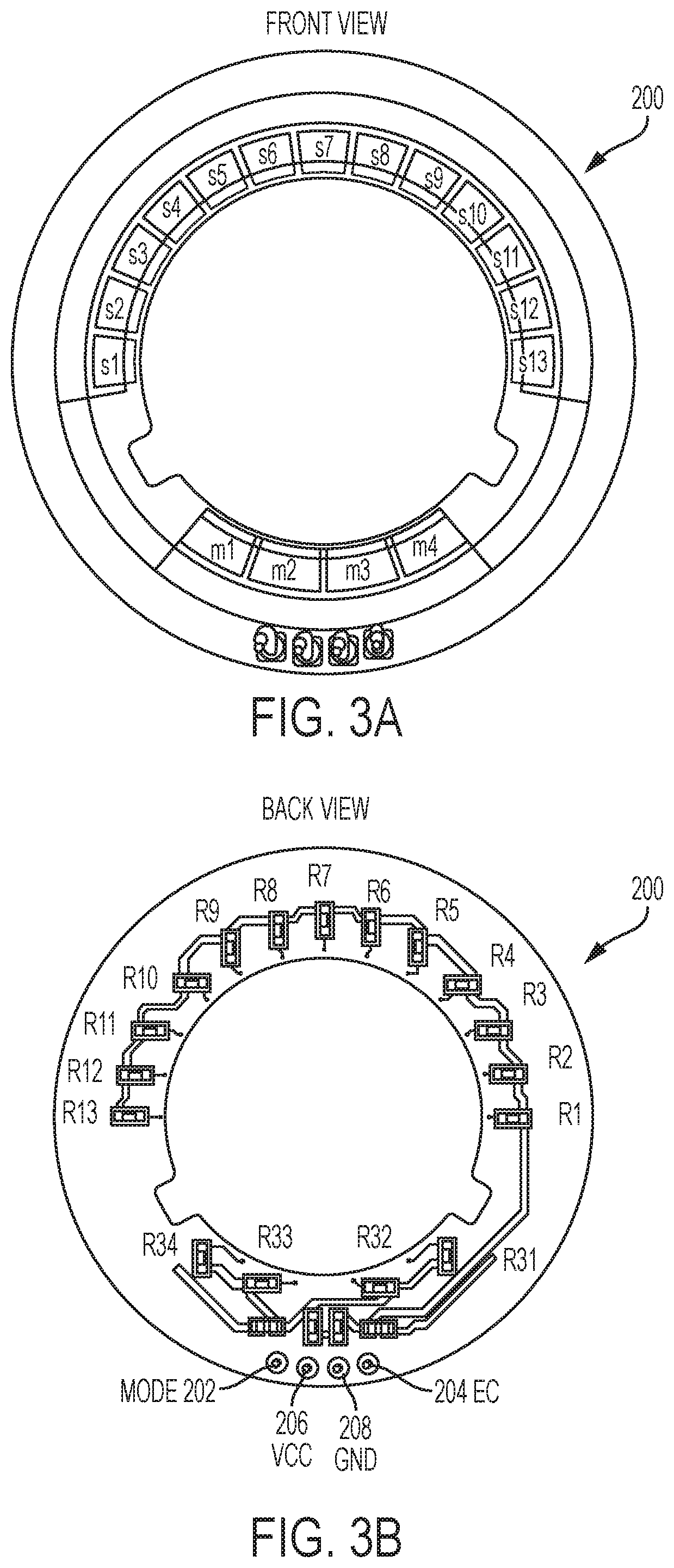






United States Patent |
10,850,380 |
Huber , et al. |
December 1, 2020 |
Multi-speed power tool with electronic clutch
Abstract
A power tool and a method of operating a power tool including a
motor, a clutch collar including a plurality of settings, a
wireless transceiver operable to form a wireless connection with a
remote device, and a processor coupled to the clutch collar and the
wireless transceiver. The processor receives, via the wireless
transceiver, a mapping including a plurality of torque levels
corresponding to the plurality of settings. The processor detects
that the clutch collar is set to a setting of the plurality of
settings. The processor is further determines the torque level for
the setting from the mapping and detects, during the operation of
the power tool, that a torque of the power tool exceeds the torque
level. The processor is also configured to generate an indication
that the torque exceeds the torque level. The indication may
include flashing a light, ratcheting the motor, and stopping the
motor.
Inventors: |
Huber; Alex (Milwaukee, WI),
Westerby; Carl Benjamin (Milwaukee, WI), Ertl; Daniel
Robert (Brookfield, WI), Wycklendt; Matthew (Madison,
WI), Mergener; Matthew (Mequon, WI), Kubale; Mark
Alan (West Bend, WI), Conrad; Cole (Wauwatosa, WI),
Yip; Wing Fung (Kowloon, HK) |
Applicant: |
Name |
City |
State |
Country |
Type |
Milwaukee Electric Tool Corporation |
Brookfield |
WI |
US |
|
|
Assignee: |
Milwaukee Electric Tool
Corporation (Brookfield, WI)
|
Family
ID: |
1000005213192 |
Appl.
No.: |
15/146,547 |
Filed: |
May 4, 2016 |
Prior Publication Data
|
|
|
|
Document
Identifier |
Publication Date |
|
US 20160354888 A1 |
Dec 8, 2016 |
|
Related U.S. Patent Documents
|
|
|
|
|
|
|
Application
Number |
Filing Date |
Patent Number |
Issue Date |
|
|
62180586 |
Jun 16, 2015 |
|
|
|
|
62169671 |
Jun 2, 2015 |
|
|
|
|
Current U.S.
Class: |
1/1 |
Current CPC
Class: |
F16D
48/06 (20130101); B25F 5/001 (20130101); B25D
16/006 (20130101); B25D 16/003 (20130101); F16D
2500/30426 (20130101); F16D 2500/3027 (20130101); F16D
2500/7103 (20130101); F16D 2500/3022 (20130101); F16D
2500/10418 (20130101); B25D 2250/205 (20130101); B25D
2250/165 (20130101); B25D 2250/221 (20130101); F16D
2500/7101 (20130101); F16D 2500/30415 (20130101); F16D
2500/7102 (20130101); F16D 2500/51 (20130101); F16D
2500/7104 (20130101) |
Current International
Class: |
B25F
5/00 (20060101); B25D 16/00 (20060101); F16D
48/06 (20060101) |
Field of
Search: |
;173/2,176 |
References Cited
[Referenced By]
U.S. Patent Documents
Foreign Patent Documents
|
|
|
|
|
|
|
10029132 |
|
Jan 2002 |
|
DE |
|
10309703 |
|
Sep 2004 |
|
DE |
|
202006014606 |
|
Jan 2007 |
|
DE |
|
2147750 |
|
Jan 2010 |
|
EP |
|
2671681 |
|
Dec 2013 |
|
EP |
|
S58181544 |
|
Oct 1983 |
|
JP |
|
2000176850 |
|
Jun 2000 |
|
JP |
|
2004072563 |
|
Mar 2004 |
|
JP |
|
2006123080 |
|
May 2006 |
|
JP |
|
100782593 |
|
Dec 2007 |
|
KR |
|
WO02030624 |
|
Apr 2002 |
|
WO |
|
WO2007090258 |
|
Aug 2007 |
|
WO |
|
WO2013116303 |
|
Aug 2013 |
|
WO |
|
Other References
International Search Report and Written Opinion for Application No.
PCT/US2016/030769 dated Aug. 5, 2016 (11 pages). cited by applicant
.
Bosch Media Service "Power Tools" Bosch Press Release, Mar. 3, 2016
(3 pages). cited by applicant .
Korean Patent Office Action for Application No. 10-2017-7037714
dated Mar. 15, 2019, with English Translation, 15 pages. cited by
applicant .
Korean Patent Office Action for Application No. 10-20177037714,
dated Sep. 26, 2019 (7 pages, English translation included). cited
by applicant .
Korean Patent Office Notice of Allowance for Application No.
10-20177037714, dated Nov. 12, 2019 (7 pages, English translation
included). cited by applicant .
Extended European Search Report for Application No. 16803935.2
dated Dec. 14, 2018, 8 pages. cited by applicant.
|
Primary Examiner: Long; Robert F
Attorney, Agent or Firm: Michael Best & Friedrich
LLP
Parent Case Text
RELATED APPLICATIONS
This application claims priority to U.S. Provisional Patent
Application No. 62/169,671, filed on Jun. 2, 2015, and U.S.
Provisional Patent Application No. 62/180,586, filed on Jun. 16,
2015, the entire contents of which are hereby incorporated by
reference.
Claims
What is claimed is:
1. A power tool comprising: a housing; a motor within the housing;
a clutch collar on the housing including a plurality of settings; a
wireless transceiver operable to form a wireless connection with a
remote device; and a processor coupled to the clutch collar and the
wireless transceiver, the processor configured to: receive, via the
wireless transceiver, a mapping including a plurality of torque
levels corresponding to the plurality of settings, detect that the
clutch collar is set to a setting of the plurality of settings,
determine the torque level for the setting from the mapping,
detect, during operation of the power tool, that a torque of the
power tool exceeds the torque level, and generate an indication
that the torque exceeds the torque level.
2. The power tool of claim 1, further comprising a current sensor
coupled to the processor, wherein the processor is configured to
detect the torque based on a motor current sensed by the current
sensor.
3. The power tool of claim 1, wherein the indication includes at
least one selected from the group consisting of flashing a light,
ratcheting the motor, and stopping the motor.
4. The power tool of claim 1, wherein the indication includes
ratcheting the motor, and an intensity of the ratcheting is set by
the processor based on the torque level.
5. The power tool of claim 1, wherein the mapping includes the
plurality of torque levels corresponding to the plurality of
settings for a first revolution of the clutch collar and a second
plurality of torque levels corresponding to the plurality of
settings for a second revolution of the clutch collar.
6. The power tool of claim 1, further comprising a speed select
switch having a high-speed setting and a low-speed setting, the
speed select switch coupled to the processor, wherein the processor
is further configured to receive the mapping for the high-speed
setting and receive a second mapping for the low-speed setting.
7. The power tool of claim 6, wherein a maximum torque level of the
mapping for the high-speed setting is less than a maximum torque
level of the second mapping for the low-speed setting.
8. The power tool of claim 1, further comprising a speed select
switch having a speed setting, the speed select switch coupled to
the processor, wherein the processor compensates for the speed
setting in detecting the torque of the power tool such that, for
the setting of the plurality of settings of the clutch collar, the
torque of the power tool upon generating the indication is
approximately the same regardless of the speed setting.
9. The power tool of claim 1, wherein the processor is further
configured to: receive, via the wireless transceiver, a request to
enter a fixed torque mode and a fixed torque level; detect, during
a subsequent operation of the power tool, that a subsequent torque
of the power tool exceeds the fixed torque level; and generate a
second indication that the subsequent torque exceeds the fixed
torque level.
10. The power tool of claim 1, wherein the processor is further
configured to: receive, via the wireless transceiver, a request to
enable an anti-kickback feature; set an anti-kickback torque level;
detect, during operation of the power tool, that the torque of the
power tool exceeds the anti-kickback torque level; and stop the
motor when the torque exceeds the anti-kickback torque level.
11. A method of operating a power tool including a housing, a motor
within the housing, a clutch collar on the housing including a
plurality of settings, and an electronic clutch, the method
comprising: receiving, with a processor via a wireless transceiver,
a mapping including a plurality of torque levels corresponding to
the plurality of settings; detecting, with the processor, that the
clutch collar is set to a setting from the plurality of settings;
determining, with the processor, the torque level for the setting
from the mapping; detecting, with the processor, that a torque of
the power tool exceeds the torque level during operation of the
power tool; and generating, with the processor, an indication that
the torque exceeds the torque level.
12. The method of claim 11, wherein detecting the torque includes
detecting a motor current and calculating an estimated torque based
on the motor current.
13. The method of claim 11, wherein the indication includes
ratcheting the motor, and an intensity of the ratcheting varies
with the torque level.
14. The method of claim 11, wherein the mapping includes the
plurality of torque levels corresponding to the plurality of
settings for a first revolution of the clutch collar and a second
plurality of torque levels corresponding to the plurality of
settings for a second revolution of the clutch collar.
15. The method of claim 11, further comprising: receiving, from a
speed select switch, a selection of at least one selected from the
group consisting of a high-speed setting and a low-speed setting,
wherein the mapping corresponds to the high-speed setting; and
receiving, with the processor, a second mapping for the low-speed
setting.
16. The method of claim 15, wherein a maximum torque level of the
mapping for the high-speed setting is less than a maximum torque
level of the second mapping for the low-speed setting.
17. The method of claim 11, receiving, from a speed select switch,
a speed setting; compensating for the speed setting in detecting
the torque of the power tool such that, for the setting of the
plurality of settings of the clutch collar, the torque of the power
tool upon generating the indication is approximately the same
regardless of the speed setting.
18. The method of claim 11, further comprising: receiving, via the
wireless transceiver, a request to enter a fixed torque mode and a
fixed torque level; detecting, during a subsequent operation of the
power tool, that a subsequent torque of the power tool exceeds the
fixed torque level; and generating a second indication that the
subsequent torque exceeds the fixed torque level.
19. The method of claim 11, further comprising: receiving, via the
wireless transceiver, a request to enable an anti-kickback feature;
setting, with the processor, an anti-kickback torque level;
detecting, with the processor during operation of the power tool,
that the torque of the power tool exceeds the anti-kickback torque
level; and stopping, with the processor, the motor when the torque
exceeds the anti-kickback torque level.
20. The method of claim 11, wherein generating the indication
includes at least one selected from the group consisting of
flashing a light, ratcheting the motor, and stopping the motor.
21. A method of operating a power tool including a housing, a motor
within the housing, a clutch collar on the housing including a
plurality of settings, and an electronic clutch, the method
comprising: receiving, with a processor via a wireless transceiver,
a first torque value generated by a remote device based on user
input and wirelessly transmitted by the remote device to the
wireless transceiver; detecting, with the processor, that the
clutch collar is set to a setting of the plurality of settings;
calculating, with the processor, a torque level for the setting
based on the position of the setting among the plurality of
settings and the first torque value; and controlling the motor
based on the torque level.
22. The method of claim 21, wherein controlling the motor based on
the torque level include: detecting, with the processor, that a
torque of the power tool exceeds the torque level during operation
of the power tool; and controlling the motor to one or more of stop
and ratchet.
23. The method of claim 21, further comprising: receiving, with the
processor via the wireless transceiver, a second torque value
generated by the remote device based on the user input, and wherein
calculating the torque level is further based on the second torque
value.
24. The method of claim 23, wherein the first torque value is
indicative of a first torque level for a first setting, the second
torque value is indicative of a second torque level for a second
setting, the method further comprising: associating remaining
settings of the plurality of settings with torque levels between
the first torque level and the second torque level.
25. The method of claim 21, further comprising: providing, by the
external device, a graphical user interface; receiving, by the
external device, an indication of the first torque value and a
second torque value via the graphical user interface, wherein the
first torque value is indicative of a minimum torque level and the
second torque value is indicative of a maximum torque level.
26. The power tool of claim 1, wherein the mapping correlates each
of the plurality of torque levels with a respective one of the
plurality of settings of the clutch collar, and to determine the
torque level for the setting from the mapping, the electronic
processor is configured to select the torque level that is
correlated to the setting by the mapping.
27. The power tool of claim 1, wherein the electronic processor is
further configured to: receive, via the wireless transceiver, a
second mapping including a second plurality of torque levels
corresponding to the plurality of settings of the clutch collar to
provide an updated correlation of the plurality of settings of the
clutch collar to the second plurality of torque levels; detect,
after receiving the second mapping, that the clutch collar is again
set to the setting of the plurality of settings, determine an
updated torque level for the setting from the second mapping,
detect, during further operation of the power tool, that the torque
of the power tool exceeds the updated torque level, and generate a
second indication that the torque exceeds the updated torque level.
Description
FIELD OF THE INVENTION
The present invention relates to an electronic clutch for a power
tool.
SUMMARY
One embodiment provides a power tool including a housing, a motor
within the housing, a clutch collar on the housing including a
plurality of settings, a wireless transceiver operable to form a
wireless connection with a remote device, and a processor coupled
to the clutch collar and the wireless transceiver. The processor is
configured to receive, via the wireless transceiver, a mapping
including a plurality of torque levels corresponding to the
plurality of settings and detect that the clutch collar is set to a
setting of the plurality of settings. The processor is further
configured to determine the torque level for the setting from the
mapping and detect, during the operation of the power tool, that a
torque of the power tool exceeds the torque level. The processor is
also configured to generate an indication that the torque exceeds
the torque level.
Another embodiment provides a method of operating a power tool
including a housing, a motor within the housing, a clutch collar on
the housing including a plurality of settings, and an electronic
clutch. The method includes receiving, with a processor via a
wireless transceiver, a mapping including a plurality of torque
levels corresponding to the plurality of settings and detecting,
with the processor, that the clutch collar is set to a setting from
the plurality of settings. The method also includes determining,
with the processor, the torque level for the setting from the
mapping, and detecting, with the processor, that a torque of the
power tool exceeds the torque level during operation of the power
tool. The method further includes generating, with the processor,
an indication that the torque exceeds the torque level.
Another embodiment provides a method of operating a housing, a
motor within the housing, a clutch collar on the housing including
a plurality of settings, and an electronic clutch. The method
includes receiving, with a processor via a wireless transceiver, a
first torque value generated by a remote device based on user input
and wirelessly transmitted by the remote device to the wireless
transceiver. The method further includes the processor detecting
that the clutch collar is set to a setting of the plurality of
settings. The processor calculates a torque level for the setting
based on the position of the setting among the plurality of
settings and the first torque value. The method further includes
controlling the motor based on the torque level.
BRIEF DESCRIPTION OF THE DRAWINGS
FIGS. 1A and 1B illustrate a power tool according to some
embodiments.
FIG. 2 illustrates a block diagram of the power tool according to
some embodiments.
FIGS. 3A and 3B illustrate a printed circuit board assembly
associated with the power tool of FIGS. 1A and 1B according to some
embodiments.
FIG. 4 illustrates a circuit diagram of the printed circuit board
assembly of FIGS. 3A and 3B according to some embodiments.
FIG. 5 illustrates a block diagram of a remote device according to
some embodiments.
FIGS. 6A and 6B illustrate a graphical user interface of a remote
device associated with the power tool of FIGS. 1A and 1B according
to some embodiments.
FIG. 7 illustrates a graphical user interface of a remote device
associated with the power tool of FIGS. 1A and 1B according to some
embodiments.
FIG. 8 illustrates a flowchart of a method of operating a power
tool having an electronic clutch according to some embodiments.
DETAILED DESCRIPTION
Before any embodiments of the invention are explained in detail, it
is to be understood that the invention is not limited in its
application to the details of construction and the arrangement of
components set forth in the following description or illustrated in
the following drawings. The invention is capable of other
embodiments and of being practiced or of being carried out in
various ways.
FIGS. 1A-B illustrate a power tool 100 incorporating a brushless
direct current (DC) motor. In a brushless motor power tool, such as
power tool 100, switching elements are selectively enabled and
disabled by control signals from a controller to selectively apply
power from a power source (e.g., battery pack) to drive a brushless
motor. The power tool 100 is a brushless hammer drill having a
housing 102 with a handle portion 104 and motor housing portion
106. The power tool 100 further includes an output unit 107, a
clutch selector ring (or clutch collar) 108, a mode selector ring
109, forward/reverse selector 110, speed select switch 111, trigger
112, a mode selector pushbutton 113, a battery interface 114, and
light 116. The mode selector ring 109 allows a user to select
between a drilling mode, a driving mode, a hammering mode, and an
adaptive mode. When in the adaptive mode, the mode selector
pushbutton 113 may be activated (e.g., pushed) to cycle through
adaptive modes defined by control profiles of the tool 100. The
clutch collar 108 allows a user to select between various clutch
settings, such as settings 1-13 or the even values between 2-26
(i.e., settings 2, 4, 6, 8, . . . 24, 26). Other embodiments
include a clutch collar 108 having fewer or more setting options.
The speed select switch 111 is a two-position switch that slides
between a high speed and a low speed. In some embodiments, the
speed select switch 111 includes additional speed settings (e.g.,
high, medium, and low).
FIG. 2 illustrates a simplified block diagram 120 of the power tool
100, which includes a power source 122, field effect transistors
(FETs) 124, a motor 126, Hall sensors 128, a motor control unit
130, user input 132, and other components 133 (battery pack fuel
gauge, work lights (e.g., light emitting diodes (LEDs), such as the
light 116), a current sensor 135, a voltage sensor 136, and a
wireless transceiver 137). The power source 122 provides DC power
to the various components of the power tool 100 and may be a power
tool battery pack that is rechargeable and uses, for instance,
lithium ion cell technology. In some instances, the power source
122 may receive alternating current (AC) power (e.g., 120V/60 Hz)
from a tool plug that is coupled to a standard wall outlet, and
then filter, condition, and rectify the received power to output DC
power.
Each of the Hall sensors 128 outputs motor feedback information,
such as an indication (e.g., a pulse) when a magnet of the motor's
rotor rotates across the face of that Hall sensor. Based on the
motor feedback information from the Hall sensors 128, the motor
control unit 130 can determine the position, velocity, and
acceleration of the rotor. The motor control unit 130 also receives
user controls from user input 132, such as by depressing the
trigger 112 or shifting the forward/reverse selector 110. In
response to the motor feedback information and user controls, the
motor control unit 130 transmits control signals to control the
FETs 124 to drive the motor 126. By selectively enabling and
disabling the FETs 124, power from the power source 122 is
selectively applied to stator coils of the motor 126 to cause
rotation of a rotor. Although not shown, the motor control unit 130
and other components of the power tool 100 are electrically coupled
to the power source 122 such that the power source 122 provides
power thereto.
The current sensor 135 detects current to the motor, for example,
by detecting current flowing between the power source 122 and the
FETS 124 or between the FETS 124 and the motor 126, and provides an
indication of the current sensed to the motor control unit 130. The
voltage sensor 136 detects voltages of the power tool 100, such as
a voltage level of the power source 122 and a voltage across the
motor 126. The wireless transceiver 137 provides a wireless
connection between the motor control unit 130 and an external
device to enable wireless communication with the external device,
such as a remote device 140.
In some embodiments, the motor control unit 130 includes a memory
and an electronic processor configured to execute instructions
stored on the memory to effect the functionality of the motor
control unit 130 described herein.
The tool 100 includes an electronic clutch, also referred to as an
e-clutch. More particularly, the tool 100 includes an e-clutch
control module 134. The e-clutch control module 134 may be
implemented in hardware, software, or a combination thereof. In the
illustrated embodiment, the e-clutch control module 134 includes
instructions stored on and executed by the motor control unit 130
to implement the e-clutch functionality described herein. The
e-clutch control module 134 takes input from a user from the clutch
collar 108. As will be discussed in more detail below, the clutch
collar 108 provides the user a rotatable selector that provides an
electrical signal indicative of the user selection to the e-clutch
control module 134. The position of the speed select switch 111,
which a user can toggle between two settings (for example, a high
speed setting ("1") and a low speed setting ("2")), is monitored by
the e-clutch control module 134 as well.
The user selection on the clutch collar 108 is translated into a
desired/target torque output level for the tool 100. Then, when the
tool 100 is in operation, the e-clutch control module 134
calculates an output torque of the power tool by taking into
account one or more of a gear ratio, battery current, effect of
speed control or pulse-width-modulation (PWM) on root mean squared
(RMS) current, and changes in motor velocity and acceleration. For
example, the e-clutch control module 134 calculates the output
torque based on a current flowing to the motor 126 as sensed by the
current sensor 135. When the target torque is reached, the motor
control unit 130 generates an indication of reaching the target
torque by one or more of stopping the tool 100 from further
driving, shaking (i.e., ratcheting) the motor 126 to indicate that
the target torque has been reached, and flashing the light 116 to
indicate that the target torque has been reached.
The clutch collar 108 allows the user to select the desired torque
level at which the tool 100 clutches. The clutch collar 108 is able
to rotate continuously and is not limited, for example, to a single
revolution or 360 degrees of rotation. In other words, the clutch
collar 108 is able to be rotated multiple revolutions (i.e., more
than 360 degrees of rotation). The continuous rotation feature
allows the clutch collar 108 to go from a maximum torque setting
(e.g., at a 0 degree rotational position) to the minimum torque
setting (e.g., at a 359 degree rotational position), which are
adjacent, more quickly than if the clutch collar 108 had to rotate
back through the various intervening settings between the maximum
and minimum setting.
In other embodiments, the clutch collar 108 is limited in rotation,
for example, by a rotational stop physically blocking rotation
beyond a certain point (e.g., 180 degrees, 270 degrees, 300
degrees, 360 degrees, 540 degrees, 720 degrees, an amount between
300 and 360 degrees, or another degree amount). As an example, the
clutch collar 108 may include a projection that rotates with the
collar and the motor housing 106 may have a fixed tab (i.e., a
rotational stop). The clutch collar 108 is free to rotate until the
projection abuts the fixed tab. The projection and tab may be
internal (i.e., inside the clutch collar 108 and motor housing 106,
respectively) or external (i.e., on an outside surface of the
clutch collar 108 and the motor housing 106, respectively).
The clutch collar 108 includes a wiper (not shown) that contacts
one of several resistive elements, each associated with a
particular clutch setting. The particular resistive element
contacted by the wiper depends on the rotational position of the
clutch collar 108.
For instance, FIGS. 3A-B illustrate a front side and a back side,
respectively, of a printed circuit board assembly (PCBA) 200
associated with the clutch collar 108, and FIG. 4 illustrates a
circuit diagram 201 of the PCBA 200 coupled to the motor control
unit 130. The PCBA 200 includes a mode pin 202, an e-clutch (EC)
pin 204, a power pin (Vcc) 206, and a ground pin (GND) 208. As
shown in FIG. 5, the mode pin 202 and the e-clutch pin 204 are
coupled to input pins of the motor control unit 130. The PCBA 200
also includes thirteen surface mount resistors, R1-R13, each having
a different resistance value and conductively coupled to a
different one of thirteen wiper connection points (S1-S13) and
being associated with a different one of the thirteen clutch
settings (1-13). When a user rotates the clutch collar 108 and
stops at a particular clutch setting (e.g., 2), the wiper contacts
a conductive PCBA track (e.g., wiper connection point S2) of the
associated resistor (e.g., R2) to complete a circuit including the
e-clutch pin 204. The conductive tracks for the thirteen resistors
are viewable on the front side of the PCBA 200 in FIG. 3A. The
motor control unit 130 and, particularly, the e-clutch control
module 134, receives an electronic signal indicating that the wiper
has contacted the particular resistor (e.g., R2). The e-clutch
control module 134 interprets the signal and determines that the
user has selected a particular setting (e.g., 2). From the user
perspective, the clutch collar has an interface similar to a
mechanical clutch, ensuring that the user will understand how to
use the clutch.
In some embodiments, the ability to continuously rotate the clutch
collar 108 (e.g., multiple revolutions in the clockwise direction,
and the counter-clockwise direction), allows the clutch collar 108
to specify more settings than wiper-resistor positions on the PCBA
200. For instance, when rotating the clutch collar 108 so that the
wiper moves clockwise on the PCBA 200 shown in FIG. 3A (going from
S1 to S2 through S13), if the user continues to rotate the clutch
collar 108 past position S13, eventually the wiper will again
contact position S1. The e-clutch control module 134 determines,
based on outputs from the e-clutch pin 204, that the clutch collar
108 went from position S13 to S1 without going through positions
S12-S2. Thus, this position S1 can be treated as a fourteenth
position (S14). If the clutch collar 108 continues to rotate in the
clockwise direction, each subsequent position is likewise treated
as a new position. For example, S2 would be a fifteenth position
(S15), S3 would be a sixteenth position (S16), and so on. A similar
expansion of positions is provided through rotating the clutch
collar 108 counter clockwise to go directly from position S1 to
S13, without going through intervening positions S2-S12.
Accordingly, the continuously rotating clutch collar 108
essentially allows an infinite number of settings to be indicated,
as a user can continuously rotate in a first direction to
continuously increment the torque setting, and continuously rotate
in the opposition direction to decrement the torque setting. In
turn, the e-clutch control module 134 can provide a maximum and
minimum torque setting (e.g., in software) where, for instance,
further increments from the clutch collar 108 are ignored because
the maximum setting has been reached. Additionally, the increased
number of setting positions allows tuning of a torque setting with
finer granularity. For instance, rather than dividing up the
potential torque settings among thirteen positions, the e-clutch
control module 134 can divide the same range of potential torque
settings among 26, 39, 50, 100, or another number of positions.
The PCBA 200 is further associated with the mode selector ring 109
to allow a user to select between the drilling mode, driving mode,
hammering mode, and adaptive mode. The PCBA 200 includes further
surface mount resistors R31, R32, R33, and R34 on the bottom
portion of the PCBA 200, each resistor being conductively coupled
to a wiper connection point (M1-M4) and being associated with one
of the four modes for selection. Similar to the clutch collar 108,
the mode selector ring 109 includes a wiper that contacts a
resistive element (R31-R34) to complete a circuit and indicate the
mode selection to the motor control unit 130, albeit the signal is
output via the mode pin 202, rather than the e-clutch pin 204.
The position of the speed select switch 111, which a user can
toggle between two settings (e.g., a "1" and "2"), is monitored by
the e-clutch control module 134 as well. A similar resistor, wiper,
and PCBA track setup as described with respect to FIGS. 3A, 3B, and
4 is used to track the position of the speed select switch 111 and,
therefore, the user's selection of the speed setting (gear ratio)
of the tool 100. In some embodiments, the e-clutch control module
134 receives the speed setting and accounts for the gear ratio of
the speed setting such that a consistent output torque for a given
clutch setting is obtained regardless of the of speed setting
selected. In other embodiments, the e-clutch control module 134
applies a different target torque dependent on the speed setting
such that a different output torque is obtained for a given clutch
setting at different speed settings.
In other embodiments, rather than a wiper-resistor ring technique,
different clutch collar selection and mode selection user interface
technology is used, such as inputs using mutual inductive sensing
and capacitive sensing.
The e-clutch control module 134 estimates the output torque of the
tool 100 (torque at the shaft) using a measurement of battery
current. The current sensor 135, or another sensor used to infer
battery current, provides a measurement to the e-clutch control
module 134. For instance, to determine battery current, the current
sensor 135 may be positioned to measure the current along the
connection between the power source 122 and the FETs 124 labeled
"power" in FIG. 2.
The current-torque relationship is fairly linear, and the
relationship depends on a motor constant (e.g., torque per unit
current (k_t)), gear ratio, gear friction, motor speed and other
factors. Determining the output torque of the tool 100 based on
current may be improved by subtracting current that is due to motor
inertia from the measured battery current. The inertia is specific
to the motor used and takes into account the effects of velocity
and acceleration. Taking motor inertia into consideration when
estimating torque assists in preventing inadvertent shutdowns on
startup or due to changes in the trigger position, where the
current-torque relationship can sometimes be non-linear,
unreliable, or both. The current-to-torque calculation may also be
improved by calculating an RMS current based on the measured
battery current, a PWM duty ratio, and motor design
characteristics. This calculation helps maintain a similar torque
output across different PWM duty ratios. The output torque
calculation may also account for the gear ratio of the power tool
100, which is selected by the user via the speed select switch 111.
For example, the output torque calculation includes one or more of
different offsets and constants, which may be empirically
determined, to compensate for the different speed settings (i.e.,
gear ratios) selectable by the speed select switch 111.
The calculated output torque is compared against the threshold
torque level set by the user (e.g., via the clutch collar 108) and
the tool 100 provides feedback when the threshold torque level is
met or exceeded. In some embodiments, because the output torque
calculation takes into consideration and accounts for the gear
ratio indicated by the speed select switch 111, regardless of the
particular speed setting selected, the tool 100 achieves
approximately the same torque output for a particular torque
setting (e.g., "2") selected by the user via the clutch collar 108.
A torque level (or, torque value) that is considered approximately
the same as another torque level may vary by embodiment and may be,
for example, within 2% of the other torque level, within 5% of the
other torque level, or within 10% of the other torque level.
The tool 100 indicates to the user that the desired torque has been
reached by ratcheting the motor and flashing the light 116. By
ratcheting the motor 126, the e-clutch control module 134 simulates
to the user the ratcheting feel and sound of a mechanical clutch.
This technique makes the experience for the user similar to a
mechanical clutch and it is also cost effective because no
additional hardware is needed. The e-clutch control module 134 will
also control the light 116 to blink when the tool 100 has reached
the selected target torque.
The feedback (e.g., ratcheting) intensity is scaled up and down
with the desired output torque to prevent the ratcheting from being
stronger than the target torque, while maximizing or ensuring the
effectiveness of the feedback to the user. The ratcheting of the
motor 126 is implemented by controlling a pulse-width modulated
(PWM) signal generated by the motor control unit 130 to drive the
motor 126 (via the FETS 124) to be output in short bursts. For
instance, the PWM signal generated by the motor control unit 130
cycles between an active state with a non-zero percent duty cycle
for a first time period, and an inactive (off) state with a zero or
near zero percent duty cycle for a second time period. In some
instances, the frequency and duty cycles for the active and
inactive periods of the PWM signal may vary during the course of
ratcheting. The amount of motor ratcheting generated is based on
the target torque selected by the user. More particularly, the
higher the target torque selected (e.g., as indicted by the clutch
collar 108 and determined by the motor control unit 130), the more
motor ratcheting generated by the tool 100 to indicate when the
target torque is reached. Similarly, the lower the target torque
selected, the less motor ratcheting generated by the tool 100 to
indicate when the target torque is reached. Scaling the motor
ratcheting in accordance with the selected target torque level 1)
prevents over-torqueing a fastener from the ratcheting motion
itself, which could occur if the amount of motor ratcheting is too
high; and 2) allows a level of motor ratcheting commensurate with
the driving action so as to be low enough at low torques to not
startle the user and high enough at high torques to be felt and
recognized by the user.
To scale the intensity of the motor ratcheting, the length of time
that the PWM signal is active and not active can be adjusted.
Generally, the longer the active time period, the more intense the
ratcheting effect. Similarly, the duration of the inactive time
period of the PWM signal can be adjusted to increase and decrease
the intensity of the ratcheting feedback. Generally, the longer the
PWM signal is inactive, the less intense the ratcheting feedback.
For instance, to increase the intensity of the ratcheting, the time
period that the PWM signal is active is increased, the time period
that the PWM signal is inactive is decreased, or both.
The particular threshold torque level used by the tool 100 varies
depending on the selected mode of the tool 100. When in the
drilling mode and the hammering mode, as selected via the mode
selector ring 109, the tool 100 generally does not implement
threshold torque levels as described above. When in the driving
mode, the e-clutch control module 134 uses the default threshold
torque level setting assigned to the currently selected torque
setting indicated by the rotational position of the clutch collar
108. The e-clutch control module 134 may include a mapping of
default threshold torque levels corresponding to the settings of
the clutch collar 108. When in the adaptive mode, as indicated by
the mode selector ring 109 based on a user selection, the tool 100
may operate implement threshold torque levels as described above.
The threshold torque levels may be set through wireless
communications between the power tool 100 and the remote device
140, as described in further detail below.
FIG. 5 illustrates a block diagram of the remote device 140. The
remote device 140 may be, for example, a smart phone, laptop,
tablet, desktop, or other computing device. The remote device 140
includes a memory 145, an electronic processor 150, a touchscreen
display 155, and a wireless transceiver 160 coupled by a bus 165.
The memory 145 stores instructions, including those for a graphical
user interface, that are executed by the electronic processor 150
to perform the processing functions of the remote device 140
described herein. The touchscreen display 155 displays information
for a user and receives input from a user. The touchscreen display
155 is one example of a user interface and, in some embodiments
further or alternative user interface elements are included in the
remote device 140, such as pushbuttons, speakers, keyboards, and
the like. The electronic processor 150 is operable to execute
instructions of the memory 145 to generate a graphical user
interface (GUI) on the touchscreen display 155, such as the GUIs
250 and 300 described in further detail below. The wireless
transceiver 160 is configured to form a wireless communication link
with the wireless transceiver 137 of the power tool 100 (FIG. 2) to
enable the electronic processor 150 to communicate with the motor
control unit 130 (and the e-clutch control module 134 thereof) of
the power tool 100. The wireless transceivers 137, 160 may use the
Bluetooth.RTM. communication protocol, Wi-Fi.RTM. communication
protocol, or another wireless protocol.
FIGS. 6A and 6B illustrate a GUI 250 generated by the remote device
140 and configured to receive user input specifying a control
provide (e.g., a custom drive control profile), and to generate and
transmit to the motor control unit 130 the custom drive control
profile to configure operation of the power tool 100. The power
tool 100 and, in particular, the motor control unit 130, may store
multiple control profiles, which may be provided and updated by the
remote device 140. A control profile includes various tool
operating parameters used by the motor control unit 130 to control
the power tool 100. When in the adaptive mode, as indicated by the
mode selector ring 109, the motor control unit 130 may cycle
through and select the particular control profile to employ for
operation of the power tool 100 in response to depressions of the
mode selector pushbutton 113 by a user. For example, the power tool
100 may include four control profiles at a given moment, and each
time the mode selector pushbutton 113 is depressed, the selected
control profile used by the motor control unit 130 to control the
power tool changes (e.g., from profile one, to profile two, to
control profile three, to profile four, back to profile one, and so
on). In other embodiments, more or less control profiles are stored
on the power tool 100, or only a single control profile is stored
on the power tool 100.
The GUI 250 is operable to receive a user selection of the
adjustable mode or the fixed mode via a clutch ring settings
selector 255 (see, e.g., FIGS. 6A and 6B). For the fixed mode, a
set-up screen of which is shown in FIG. 6B, the remote device 140
receives a user selection, via a slider 260 or text box 265, of a
particular fixed torque level (e.g., 75 in-lbs.) or a particular
percentage of available torque (e.g., 75% (of maximum available
torque)). The selected fixed torque level, along with an indication
of the fixed torque mode, is part of a custom drive control profile
that is then wirelessly communicated to the tool 100 and, more
particularly, to the e-clutch control module 134. This selected
torque level is then used by the e-clutch control module 134 as the
torque threshold for the tool 100, regardless of the position of
the clutch collar 108.
Alternatively, the power tool 100 may receive a custom drive
control profile from the remote device 140 indicating that the tool
100 is to operate in the adjustable mode. In the adjustable mode, a
set-up screen of which is shown in FIG. 6A, the torque threshold
used by the e-clutch control module 134 is the torque level
assigned to the currently selected torque setting indicated by the
rotational position of the clutch collar 108. Initially, the torque
levels assigned to the various torque settings of the clutch collar
108 are the default torque levels that are also used in the driving
mode. However, via the remote device 140, the user can assign new
torque levels to the various settings available to be selected by
the clutch collar 108, over-writing or being used in place of the
default torque levels. The GUI 250 receives the user assignment of
torque levels to settings of the clutch collar 108 (a mapping), and
provides the mapping via the wireless transceiver 160 to the
e-clutch control module 134 as part of a control profile. The
e-clutch control module 134 may store the mapping to a memory of
the motor control unit 130.
In an example mapping generation by the GUI 250, the user is able
to assign a maximum and minimum torque level (via the slider 260 or
text boxes 265) that can be selected via the clutch collar 108,
such that the lowest torque setting of the clutch collar 108 is
assigned the minimum torque level selected and the highest torque
setting of the clutch collar 108 is assigned the maximum torque
level selected. The remaining intermediate torque settings are then
assigned a proportional torque level between the minimum and
maximum torque levels. For instance, assuming thirteen torque
settings (1-13) on the clutch collar 108 and a user selecting a
minimum torque level of 50 inch-pounds (in.-lbs.) and a maximum
torque level of 110 in.-lbs., the remote device 140 will assign the
following torque levels to the tool 100, in some embodiments:
TABLE-US-00001 TABLE I Torque Setting Torque level Torque level
(Clutch Collar Position) (in-lbs.) (% of maximum torque) 1 50 29% 2
55 32% 3 60 35% 4 65 38% 5 70 41% 6 75 44% 7 80 47% 8 85 50% 9 90
53% 10 95 56% 11 100 59% 12 105 62% 13 110 65%
These assigned values assume a linear scale between minimum and
maximum values. However, in some instances, non-linear scales are
used, such as an exponential scale. In some embodiments, the GUI
250 may receive a selection of the scale to apply via user input.
The maximum and minimum selected torque levels can also be
expressed as a percentage of the maximum torque available. For
instance, the right column of the above table illustrates the
torque levels expressed as a percentage. Furthermore, as noted
above with respect to the continuously rotating feature of the
clutch collar 108, more or fewer than 13 torque setting positions
are assigned a torque level in some embodiments. For instance, each
increment or decrement of the position of the clutch collar 108 can
increment or decrement, respectively, the torque level by 1 in-lb
(or by 1% of maximum torque) until the maximum or minimum torque
levels are reached.
The GUI 250 further includes a speed setting selector 270 to select
between a high speed mapping and a low speed mapping. In other
words, the GUI 250 is operable to receive torque levels for a first
mapping when the high speed mapping is selected via the speed
setting selector 270, and to receive torque levels for a second
mapping when the low speed mapping is selected via the speed
setting selector 270. The remote device 140 is further operable to
generate and provide to the motor control unit 130 a profile
including the first mapping applicable when the power tool is in
the high speed setting and the second mapping applicable when the
power tool is in the low speed setting (selected via the speed
select switch 111).
In some embodiments, the profile provided to the power tool 100
based on user input received by the GUI 250 may indicate that, in
one of the speed settings (e.g., the high speed setting), the power
tool 100 is in the adjustable mode and, in the other of the speed
settings (e.g., the low speed setting), the power tool is in the
fixed mode. For example, with the low speed mapping selected on the
GUI 250 via the speed setting selector 270, the GUI 250 may receive
a selection of the adjustable mode via the clutch ring settings
selector 255. Further, with the high speed mapping selected on the
GUI 250 via the speed setting selector 270, the GUI 250 may receive
a selection of the fixed mode via the clutch ring settings selector
255. The remote device 140 then generates a profile including a
first mapping and the adjustable mode for the low speed setting and
a fixed torque level and the fixed mode indication for the high
speed setting. Accordingly, a user is operable to cycle the power
tool 100, by moving the speed select switch 111, between an
adjustable mode whereby the user may specify a torque level via the
clutch collar 108 and a fixed mode whereby the torque level is
fixed (based on input via the GUI 250).
The profile generated by the remote device 140 and provided to the
power tool 100 based on the GUI 250 may further include a maximum
speed for the motor 126 (one for each of the high and low speed
setting), a trigger ramp up parameter indicating a pace at which
the motor 126 should ramp up to a desired speed, a work light
duration indicating how long to keep the light 116 enabled (e.g.,
after the trigger 112 is pressed or released), and a work light
brightness level.
Using the e-clutch control module 134, clutch collar 108, and
remote device 140, rather than a traditional mechanical clutch,
allows for more sophisticated mappings of torque control. A
mechanical input (clutch collar 108) provides the user with a
mechanical input mechanism on the tool 100 that is coupled with
programmable electronic control to provide greater tool
customization, intelligence, and usability. The ability to remap
the torque settings selectable by the clutch collar 108 results in
a tool 100 having an extended user interface, where the indications
that are provided by the mechanical input are programmable and are
not fixed. For instance, torque setting "2" is not fixed to
indicate 55 in-lbs. (or another value) of torque. Rather, via the
remote device 140, the meaning of a particular output signal from
the mechanical input can be remapped by the user to indicate
something different to the motor control unit 130 and e-clutch
control module 134. The particular indication from the mechanical
input, specified through the mapping, is then used to control the
motor in a certain predetermined manner. This extended user
interface provided by the remote device 140 provides extended
functionality and customization of the tool 100, which has limited
surface real estate for additional user interface components.
In some embodiments, the e-clutch control module 134 limits the
maximum allowable torque setting to be that which is allowable
according to applicable laws, rules, or regulations for a driving
tool without a side handle. In some embodiments, the e-clutch
control module 134 receives an input regarding whether a side
handle is present on the tool and limits the maximum allowable
torque setting based on the input. More particularly, when the
e-clutch control module 134 determines that the side handle is not
present, the maximum allowable torque setting is limited to that
which is permitted according to applicable laws, rules, or
regulations. When the e-clutch control module 134 determines that
the side handle is present, the maximum torque setting allowable is
permitted to be higher than when the side handle is not present.
The higher maximum torque setting may again be limited by
applicable laws, rules, or regulations for a driving tool with a
side handle.
In some embodiments, a switch on the tool 100 allows a user to
indicate to the e-clutch control module 134 whether a side handle
is present. The switch may be similar in function and structure to
the speed select switch 111, may be a push button, or another
electro-mechanical input device that provides an output to the
e-clutch control module 134 indicative of whether a side handle is
present. In another embodiment, attaching the side handle to the
tool itself actuates a switch that provides an indication to the
e-clutch control module 134 of the presence of the side handle, and
removal of the handle provides an indication to the e-clutch
control module 134 that that the side handle has been removed. In
another embodiment, the GUI of the remote device 140 includes an
input (e.g., radio buttons or two-position slider) enabling a user
to select or toggle between a side handle on indication and a side
handle off indication. This selection is then communicated to the
e-clutch control module 134 and used as described above to set the
maximum allowable torque setting.
As noted above, the tool includes a speed selector switch 111
allowing the user to select between two gear ratios, which results
in a different output speed range. Generally, a high gear ratio
allows for higher maximum speed, but lower maximum torque, while a
low gear ratio allows for a higher maximum torque, but lower
maximum speed. In tools with traditional mechanical clutches, the
maximum torque allowable is typically limited to a maximum torque
to be provided in the high gear ratio (high speed) mode. As a
result, while the low gear ratio mode would allow for a higher
maximum torque absent the mechanical clutch, the mechanical clutch
limits the maximum torque allowable in the low gear ratio (low
speed) mode to the maximum torque to be provided in the high gear
ratio mode. As such, the higher torques of the low gear ratio mode
remain unavailable in a clutching mode. In contrast, the tool 100
includes an e-clutch rather than a mechanical clutch. The
configurability of the e-clutch control module 134 removes the
torque limit imposed by the higher gear ratio to be able to take
advantage of the extra torque levels available by the low gear
ratio.
Accordingly, in some embodiments, the e-clutch control module 134
allows a user to specify a higher torque level for the low speed
mode than is selectable for the high speed mode. For instance, in
FIGS. 6A-B, the low speed mode is selected and the maximum torque
allowed is approximately 175 in-lbs., which is the same maximum
torque allowed in the high speed mode. However, in some
embodiments, the tool 100 can achieve a higher torque output while
in the low speed mode. Accordingly, in some embodiments, the
maximum selectable torque level is a first value (e.g., 175
in-lbs.) when in the high speed mode; but, in the low speed mode,
the maximum selectable torque level is a greater value (e.g., 300
in-lbs. or 1000 in-lbs.).
In some embodiments, the e-clutch control module 134 allows a user
to individually provide a torque level for each setting of the
clutch collar 108. A GUI of the remote device 140 may include a
text box, slider, or other input mechanism, for each setting of the
clutch collar 108 to enable a user to enter a custom torque level
for each clutch collar setting. For example, the user may enter 200
in-lbs for setting 1, 150 in-lbs for setting 2, and 700 in-lbs for
setting 3. In other embodiments, the GUI of the remote device 140
may receive, from a user, custom values for a subset of the
settings, and a range for the other settings. For instance, for a
clutch collar 108 having thirteen settings (e.g. 1-13), the GUI may
receive custom torque levels for settings the three settings (e.g.,
1-3), and a range for the remaining settings (e.g., 4-13) defined
by a maximum value and a minimum value. The remote device 140 may,
in turn, divide the range among the remaining settings (e.g.,
4-13), similar to as described above with respect to Table I.
In some embodiments, the e-clutch control module 134 receives via a
GUI of the remote device 140 different ranges for different subsets
of the settings of the clutch collar 108. For example, the GUI may
provide a mapping of torque levels to the e-clutch control module
134, based on received user input, specifying a first range of
torques for a first group of settings (e.g., 1-5) of the clutch
collar and a second range of torques for a second group of settings
(e.g., 6-13) of the clutch collar, the ranges each defined by
maximum and minimum torque levels similar to as described
above.
FIG. 7 illustrates another graphical user interface, GIU 300,
generated by the remote device 140 and used to configure the tool
100. The GUI 300 is configured to receive user input specifying a
custom drill control profile, which is then transmitted by the
remote device 140 to the power tool 100 to configure operation of
the power tool 100. The GUI 300 is similar to the GUI 250 of FIGS.
6A-B, but includes different features, including an anti-kickback
feature block 301. More particularly, the GUI 300 includes an
anti-kickback toggle 302 that has an enable and a disable position,
selectable by the user. For instance, as illustrated in FIG. 7, the
anti-kickback toggle 302 is in the enabled position, but is
switched to the disabled position by swiping to the left on the GUI
300 (e.g., on a touch screen of the remote device 140). When
enabled, the user is operable to set the sensitivity of the
anti-kickback feature by setting a torque shutoff level (i.e., an
anti-kickback torque level). In the illustrated example, the user
may adjust the torque shutoff level between level 1 and level 10 by
sliding the slider 304. The GUI 300 also includes a torque shutoff
level indicator 306 indicating the currently selected torque
shutoff setting, which is set to level 3 in FIG. 7. After the
remote device 140 receives the user settings of the custom drill
profile via GUI 300, the remote device 140 transmits the profile
(configuration data) to the power tool 100 wirelessly or via a
wired connection, which is received by the motor control unit 130.
As previously described, the mode selector pushbutton 113 may be
pressed to cycle through profiles of the tool 100 and to select the
custom drill control profile having the anti-kickback feature
enabled.
In operation, while the power tool 100 is performing a drilling
operation with the anti-kickback feature is enabled, the e-clutch
control module 134 monitors the battery current to the motor 126
using the current sensor 135, as described above. The e-clutch
control module 134 also determines a current threshold based on the
selected torque shutoff setting (e.g., using a look up table
mapping each torque shutoff setting to a current value). When the
e-clutch control module 134 determines that the battery current
level reaches the current threshold, the motor control unit 130
ceases driving the motor 126 to bring the motor 126 to a quick
stop. Thus, the motor control unit 130 infers that a kickback
situation is occurring based on an increase in motor torque, which
is inferred via battery current, and shuts down the motor 126.
When the anti-kickback toggle 302 is disabled, and the remote
device 140 communicates the custom drill profile configuration data
to the power tool with the disabled feature status, the power tool
100 proceeds without a torque shutoff as described.
As illustrated in FIG. 7, other tool operation parameters may be
specified via the GUI 300. For example, the GUI 300 is operable to
receive a maximum speed for the motor 126 (for both the high and
low speed setting), a trigger ramp up parameter indicating a pace
at which the motor 126 should ramp up to a desired speed, a work
light duration indicating how long to keep the light 116 enabled
(e.g., after the trigger 112 is pressed or released), and a work
light brightness level. The GUI 300, in turn, generates a custom
drill control profile including the specified parameters, which is
transmitted to the motor control unit 130. The profile may be
stored in a memory of the motor control unit 130. The motor control
unit 130, in turn, controls the power tool 100 in accordance with
the parameters specified by the custom drill control profile.
FIG. 8 illustrates a flowchart of a method 700 of operating a power
tool 100 having an electronic clutch. The method 700 includes
receiving a mapping for the clutch collar 108 (at step 710). For
example, the mapping may be part of a profile generated by the
remote device 140 in response to user inputs received by the GUI
250 (FIGS. 6A and 6B). The profile may also include an indication
of a mode specified via the GUI 250, such as an adjustable mode or
a fixed mode. The mapping indicates or assigns a torque level for
each of the plurality of positions (that is, plurality of settings)
of the clutch collar 108. The motor control unit 130 receives and
stores the mapping from the remote device 140 via the wireless
transceiver 137. A processor of the motor control unit 130 may
store the mapping in a memory of the motor control unit 130.
In some embodiments, as described above, the mapping includes
torque levels for two or more revolutions of the clutch collar 108.
For example, the mapping may include torque levels corresponding to
a plurality of settings for a first revolution of the clutch collar
and a second plurality of torque levels corresponding to the
plurality of settings for a second revolution of the clutch collar.
Assuming that the clutch collar 108 includes thirteen settings for
one revolution of the clutch collar 108, this mapping may include
twenty-six torque levels, one for each setting (or, position) of
the clutch collar 108 over two revolutions. In some embodiments,
torque levels for more than two revolutions of settings of the
clutch collar are provided. In some embodiments, the mapping
specifies a maximum torque level, and minimum torque level, and an
increment/decrement level indicating the change in target torque
levels between settings of the clutch collar 108.
At step 720, the motor control unit 130 detects the clutch collar
108 position selected by the user of the power tool 100. As
described above with respect to FIGS. 3A, 3B, and 4, the user may
rotate the clutch collar 108 to select a particular torque level.
At step 730, the motor control unit 130 determines the torque level
for the position of clutch collar 108 selected by the user. The
motor control unit 130 determines this torque level based on the
mapping received at step 710. As described above, in some
embodiments, the remote device 140 may transmit a profile to the
power tool 100 including a user-specified fixed torque level. In
these embodiments, the motor control unit determines the torque
level to be the fixed torque level received from the remote device
140, which may occur by the motor control unit 130 ignoring the
position of the clutch collar 108, ignoring the speed setting, or
assigning the fixed torque level to each of the positions of the
clutch collar 108 such that the fixed torque level is selected
regardless of the position of the clutch collar 108.
At step 740, the motor control unit 130 detects a torque of the
power tool 100. The motor control unit 130 detects the torque, for
example, based on motor current. For example, the current sensor
135 senses the current flowing to the motor 126 and provides a
signal indicative of the current to the motor control unit 130. The
motor control unit 130 may use techniques described above to
determine the torque based on the signal received from the current
sensor 135.
At step 750, the motor control unit 130 determines whether the
toque of the power tool 100 exceeds the torque level determined at
step 730. In some embodiments, this determination may involve a
comparison of torque levels (e.g., in inch-pounds or
Newton-meters), and, in other embodiments, the determination may
involve a comparison of current values indicative of a torque
(e.g., in Amperes). When the torque detected in step 740 exceeds
the torque level determined at step 730, the motor control unit 130
generates an indication (at step 760). The indication includes, for
example, flashing the light 116, ratcheting the motor 126, and/or
stopping the motor 126. In other words, in response to determining
that the detected torque of the power tool exceeds the torque
level, the motor control unit 130 may stop the motor 126 to provide
the indication, for instance, by ceasing the sending of driving
signals to the FETs 124 or by controlling the FETs 124 to actively
brake the motor 124. In some embodiments, the motor control unit
130 may ratchet the motor 126 to provide the indication in step
750. In some embodiments, the motor control unit 130 may control
the light 116 to flash to provide the indication. In yet further
embodiments, the motor control unit 130 generates the indication by
using a combination of flashing the light 116, ratcheting the motor
126, and stopping the motor 126. For example, the control unit 130
may flash the light 116 and ratchet the motor 126 for a first
period of time, and then stop the motor 126. The method 700 repeats
steps 740 and 750 until the torque exceeds the torque level
determined in step 730, until a new position of the clutch collar
108 is selected, or until the trigger 112 is released.
In some embodiments, the mapping received in step 710 includes a
first mapping for a high speed setting and a second mapping for a
low speed setting. When the power tool 100 is in the high speed
setting, indicated by the speed select switch 111, the first
mapping is used by the e-clutch control module 134 (e.g., in step
730 for determining the torque level). However, when the power tool
is in the low speed setting, indicated by the speed select switch
111, the second mapping is used by the e-clutch control module 134.
Accordingly, the clutch collar 108 may indicate different desired
torque levels at same rotational position depending on the position
for the speed select switch 111. In some embodiments, the maximum
torque level of the first mapping is less than the maximum torque
level of the second mapping.
In some embodiments, the method includes receiving, from a speed
select switch, a speed setting. The method further includes
compensating for the speed setting in detecting the torque of the
power tool in step 740 or in calculating the torque level in step
730 to provide similar performance regardless of the speed setting.
For example, through the compensation, the torque of the power tool
upon generating the indication in step 750 for a particular setting
of the clutch collar 108 is approximately the same regardless of
the speed setting.
In some embodiments, the method 700 includes a further step of
receiving, via the wireless transceiver, a request to enter a fixed
torque mode and a fixed torque level. The request and the fixed
torque level may be provided by the remote device 140 as part of a
control profile generated based on user input on the GUI 250. In a
subsequent operation of the power tool, the e-clutch control module
134 detects, during a subsequent operation of the power tool, that
a subsequent torque of the power tool exceeds the fixed torque
level. The subsequent torque of the power tool is detected similar
to the torque detection of step 740. The motor control unit 130
then generates a second indication that the subsequent torque
exceeds the fixed torque level. The second indication is generated
similar to the indication of step 760, and may include one or more
of stopping the motor 126, ratcheting the motor 126, and flashing
the light 116.
In some embodiments, the mapping received in step 710 includes a
first torque value generated by the remote device 140 based on user
input, for example, received via the GUI 250. The motor control
unit 130 uses the first torque value and calculates, in advance or
as needed, torque levels for the plurality of settings. For
example, in step 730, the motor control unit 130 calculates a
torque level for the clutch collar setting detected in step 720
based on the position of the clutch collar setting among the
plurality of settings and the first torque value. The first torque
value may indicate a maximum torque level or a minimum torque
level. Taking, for example, the first torque value as indicative of
a minimum torque level, the motor control unit 130 may calculate
the torque level of the setting by assuming a particular torque
increment and incrementing the minimum torque level by the number
of settings that the clutch collar setting is above the minimum
clutch collar setting. Alternatively, the motor control unit 130
may use a default maximum torque level in combination with the
received minimum torque level and calculate the torque level for
the clutch collar setting to be a value proportional or
corresponding to the position of the clutch setting among the
plurality of settings. For example, a clutch collar setting of six
out of thirteen possible settings would result in a torque level
that is greater than the mid-point between the minimum and maximum
torque levels, assuming a linear scale, and a clutch collar setting
of five out of thirteen settings would result in a torque level
that is below the mid-point. The motor control unit proceeds to
control the motor based on the calculated torque level. For
example, the motor control unit 130 proceeds to execute steps 740,
750, and 760, in some embodiments, and uses the calculated torque
level in the determination of step 750.
In some embodiments, in step 710, a first torque value and a second
torque value are received, and calculating the torque level is
further based on the second torque value. In some examples, the
first torque value is indicative of a minimum torque level and the
second torque value is indicative of a maximum torque level.
Similar to as described immediately above, the motor control unit
130 uses the first torque value and the second torque value to
calculate, in advance or as needed, torque levels for the plurality
of settings. In some examples, the first torque value is indicative
of a first torque level for a first setting, the second torque
value is indicative of a second torque level for a second setting,
the method further includes associating remaining settings of the
plurality of settings with torque levels between the first torque
level and the second torque level.
Although the flow chart of FIG. 8 is illustrated and described as
steps performed in a serial manner, one or more blocks of the
method 700 may be executed in parallel or in a different order than
described. Further, the processor of the motor control unit 130 may
execute instructions to implement the steps and functions of the
method 700 attributable to the motor control unit 130.
Although the tool 100 is described as a hammer drill, in some
embodiments, the tool 100 is a standard, non-hammering
drill/driver, or another drill/driving tool, such as an angle
driver or an impact driver.
Thus, the invention provides, among other things, a power tool
having a configurable electronic clutch and methods of configuring
an electronic clutch. Various features and advantages of the
invention are set forth in the following claims.
* * * * *