U.S. patent number 10,754,125 [Application Number 15/991,014] was granted by the patent office on 2020-08-25 for imaging lens.
This patent grant is currently assigned to KANTATSU CO., LTD.. The grantee listed for this patent is KANTATSU CO., LTD.. Invention is credited to Masaya Hashimoto, Koji Nitta, Yukio Sekine.



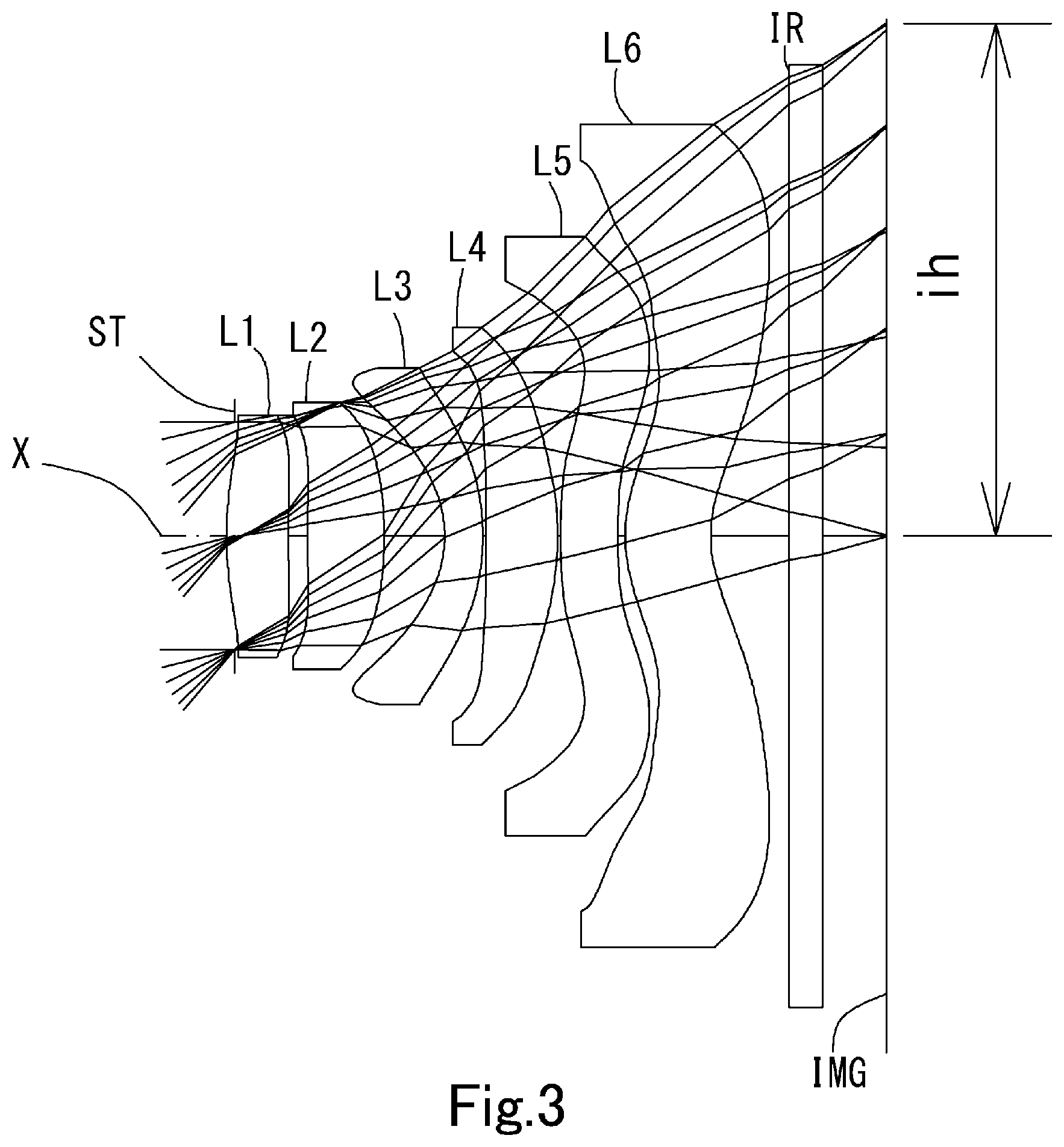







View All Diagrams
United States Patent |
10,754,125 |
Nitta , et al. |
August 25, 2020 |
Imaging lens
Abstract
There is provided an imaging lens with high resolution which
satisfies in well balance the low-profileness and the low F-number
and properly corrects aberrations. An imaging lens comprises a
first lens having positive refractive power, a second lens having
the positive refractive power, a third lens, a fourth lens, a fifth
lens being a double-sided aspheric lens, and a sixth lens being
double-sided aspheric lens and having a concave surface facing the
image side near the optical axis, wherein the image-side surface of
the sixth lens is an aspheric surface changing to the convex
surface at a peripheral area.
Inventors: |
Nitta; Koji (Tokyo,
JP), Sekine; Yukio (Sukagawa, JP),
Hashimoto; Masaya (Sukagawa, JP) |
Applicant: |
Name |
City |
State |
Country |
Type |
KANTATSU CO., LTD. |
Tochigi |
N/A |
JP |
|
|
Assignee: |
KANTATSU CO., LTD. (Yaita-shi,
Tochigi, JP)
|
Family
ID: |
64449270 |
Appl.
No.: |
15/991,014 |
Filed: |
May 29, 2018 |
Prior Publication Data
|
|
|
|
Document
Identifier |
Publication Date |
|
US 20190129137 A1 |
May 2, 2019 |
|
Foreign Application Priority Data
|
|
|
|
|
May 29, 2017 [JP] |
|
|
2017-106027 |
|
Current U.S.
Class: |
1/1 |
Current CPC
Class: |
G02B
13/0045 (20130101); H04N 5/2254 (20130101); G02B
9/60 (20130101); G02B 9/62 (20130101); G02B
13/002 (20130101); G02B 5/005 (20130101); G02B
13/18 (20130101); G02B 3/04 (20130101) |
Current International
Class: |
G02B
13/18 (20060101); G02B 9/62 (20060101); H04N
5/225 (20060101); G02B 9/60 (20060101); G02B
13/00 (20060101); G02B 5/00 (20060101); G02B
3/04 (20060101) |
Field of
Search: |
;359/713,739,740,756,757,759 |
References Cited
[Referenced By]
U.S. Patent Documents
Foreign Patent Documents
|
|
|
|
|
|
|
106997084 |
|
Aug 2017 |
|
CN |
|
2012-155223 |
|
Aug 2012 |
|
JP |
|
2014-059561 |
|
Apr 2014 |
|
JP |
|
2015-158569 |
|
Sep 2015 |
|
JP |
|
2016-14759 |
|
Jan 2016 |
|
JP |
|
2016114803 |
|
Jun 2016 |
|
JP |
|
201704804 |
|
Feb 2017 |
|
TW |
|
201704805 |
|
Feb 2017 |
|
TW |
|
I588526 |
|
Jun 2017 |
|
TW |
|
2014/162779 |
|
Oct 2014 |
|
WO |
|
Primary Examiner: Lester; Evelyn A
Attorney, Agent or Firm: Hamre Schumann, Mueller &
Larson, P.C.
Claims
What is claimed is:
1. An imaging lens comprising in order from an object side to an
image side, a first lens having positive refractive power, a second
lens having the positive refractive power, a third lens, a fourth
lens having a convex surface facing the object side near an optical
axis, a fifth lens being a double-sided aspheric lens, and a sixth
lens being a double-sided aspheric lens and having a concave
surface facing the image side near an optical axis, wherein an
image-side surface of said sixth lens is an aspheric surface
changing to the convex surface at a peripheral area, and below
conditional expressions (1) and (2) are satisfied:
1.5<vd4/vd5<3.6 (1) 0.30<(T3/TTL).times.100<0.85 (2)
where vd4: abbe number at d-ray of a fourth lens, vd5: abbe number
at d-ray of a fifth lens, T3: distance along an optical axis from
an image-side surface of the third lens to an object-side surface
of the fourth lens, and TTL: distance along an optical axis from an
object-side surface of the first lens to an image plane.
2. The imaging lens according to claim 1, wherein a below
conditional expression (3) is satisfied:
0.5<vd1/(vd2+vd3)<1.0 where vd1: abbe number at d-ray of a
first lens, vd2: abbe number at d-ray of a second lens, and vd3:
abbe number at d-ray of a third lens.
3. The imaging lens according to claim 1, wherein said second lens
has a biconvex shape having convex surfaces facing the object side
and the image side near the optical axis.
4. The imaging lens according to claim 1, wherein said second lens
has a meniscus shape having a concave surface facing the object
side near the optical axis.
5. The imaging lens according to claim 1, wherein said fourth lens
has a biconvex shape having convex surfaces facing the object side
and the image side near the optical axis.
6. The imaging lens according to claim 1, wherein said fourth lens
has a meniscus shape having a concave surface facing the object
side near the optical axis.
7. The imaging lens according to claim 1, wherein a below
conditional expression (4) is atisfied: 1.35<f1/f<3.30 (4)
where f1: focal length of the first lens, and f: focal length of
the overall optical system.
8. The imaging lens according to claim 1, wherein a below
conditional expression (5) is satisfied: 0.8<f2/f<3.4 (5)
where f2: focal length of the second lens, and f: focal length of
the overall optical system.
9. The imaging lens according to claim 1, wherein a below
conditional expression (6) is satisfied: -1.70<f3/f<-0.65 (6)
where f3: focal length of the third lens, and f: focal length of
the overall optical system.
10. The imaging lens according to claim 1, wherein a below
conditional expression (7) is satisfied: 0.65<f4/f<2.10 (7)
where f4: focal length of the fourth lens, and f: focal length of
the overall optical system.
11. The imaging lens according to claim 1, wherein a below
conditional expression (8) is satisfied: 1.9<|f6|/f (8) where
f6: focal length of the sixth lens, and f: focal length of the
overall optical system.
12. The imaging lens according to claim 1, wherein said fifth lens
has plane surfaces on both sides near the optical axis.
13. The imaging lens according to claim 1, wherein a below
conditional expression (9) is satisfied: 0.1<D6/.SIGMA.D<0.3
(9) where D6: thickness on the optical axis of the sixth lens, and
.SIGMA.D: total sum of thickness on the optical axis of the first
lens, the second lens, the third lens, the fourth lens, the fifth
lens and the sixth lens.
14. The imaging lens according to claim 1, wherein a below
conditional expression (10) is satisfied:
0.7<.SIGMA.(L1F-L6R)/f<1.6 (10) where .SIGMA.(L1F-L6R):
distance along the optical axis from the object-side surface of the
first lens to the image-side surface of the sixth lens, and f:
focal length of the overall optical system.
15. The imaging lens according to claim 1, wherein a below
conditional expression (11) is satisfied: 0.1<r5/r6<0.7 (11)
where r5: paraxial curvature radius of the object-side surface of
the third lens, and r6: paraxial curvature radius of the image-side
surface of the third lens.
16. The imaging lens according to claim 1, wherein a below
conditional expressions (12) and (13) are satisfied:
0.20<r11/f<0.55 (12) 0.15<r12/f<0.45 (13) where r11:
paraxial curvature radius of the object-side surface of the sixth
lens, r12: paraxial curvature radius of the image-side surface of
the sixth lens, and f: focal length of the overall optical
system.
17. The imaging lens according to claim 1, wherein a below
conditional expression (14) is satisfied: Fno.ltoreq.2.0 (14) where
Fno: F-number.
18. The imaging lens according to claim 1, wherein a below
conditional expression (15) is satisfied: 0.6<f2/f4<2.6 (15)
where f2: focal length of the second lens, and f4: focal length of
the fourth lens.
19. The imaging lens according to claim 1, wherein a below
conditional expression (16) is satisfied: 0.60<T3/T4<1.35
(16) where T3: distance along an optical axis from an image-side
surface of the third lens to an object-side surface of the fourth
lens, and T4: distance along an optical axis from an image-side
surface of the fourth lens to an object-side surface of the fifth
lens.
20. The imaging lens according to claim 1, wherein a below
conditional expression (17) is satisfied:
5<(D5/TTL).times.100<12 (17) where D5: thickness on the
optical axis of the fifth lens, and TTL: distance along an optical
axis from an object-side surface of the first lens to an image
plane.
Description
The present application is based on and claims priority of a
Japanese patent application No. 2017-106027 filed on May 29, 2017,
the entire contents of which are hereby incorporated by
reference.
BACKGROUND OF THE INVENTION
Field of the Invention
The present invention relates to an imaging lens which forms an
image of an object on a solid-state image sensor such as a CCD
sensor or a C-MOS sensor used in an imaging device, and more
particularly to an imaging lens which is built in an imaging device
mounted in an increasingly compact and low-profile smartphone and
mobile phone, an information terminal such as a PDA (Personal
Digital Assistant), a game console, PC and a robot, and moreover, a
home appliance and an automobile with camera function.
Description of the Related Art
In recent years, it becomes common that camera function is mounted
in a home appliance, information terminal equipment, an automobile
and public transportation. Demand of products with the camera
function is more increased, and development of products is being
made accordingly.
The imaging lens mounted in such equipment is required to be
compact and have high-resolution performance. For Example, Patent
Document 1 (JP2012-155223A) and Patent Document 2 (JP2016-114803)
disclose the imaging lens comprising six lenses.
Patent Document 1 discloses an imaging lens comprising, in order
from an object side, a first lens group having positive refractive
power, second lens group having negative refractive power, a third
lens group having the positive refractive power, a fourth lens
group having the negative refractive power, a fifth lens group
having the positive refractive power, and a sixth lens group having
the negative refractive power.
Patent Document 2 discloses an imaging lens comprising, in order
from an object side, a first lens having a convex surface facing
the object side and positive refractive power, a second lens having
negative refractive power, a third lens having the convex surface
facing the object side, a fourth lens having the positive
refractive power, a fifth lens having the negative refractive
power, and a sixth lens having the negative refractive power.
However, in lens configurations disclosed in the above-described
Patent Documents 1 and 2, when low-profileness and low F-number are
to be realized, it is very difficult to correct aberration at a
peripheral area, and excellent optical performance can not be
obtained.
The present invention has been made in view of the above-described
problems, and an object of the present invention is to provide an
imaging lens with high resolution which satisfies in well balance
the low-profileness and the low F-number and excellently corrects
aberrations.
Regarding terms used in the present invention, a convex surface, a
concave surface or a plane surface of lens surfaces implies that a
shape of the lens surface near an optical axis (paraxial portion),
refractive power implies the refractive power near the optical axis
(paraxial portion). The pole point implies an off-axial point on an
aspheric surface at which a tangential plane intersects the optical
axis perpendicularly. The total track length is defined as a
distance along the optical axis from an object-side surface of an
optical element located closest to the object to an image plane,
when thickness of an IR cut filter or a cover glass which may be
arranged between the imaging lens and the image plane is regarded
as an air.
An imaging lens according to the present invention which forms an
image of an object on a solid-state image sensor, comprises in
order from an object side to an image side, a first lens having
positive refractive power, a second lens having the positive
refractive power, a third lens, a fourth lens, a fifth lens being a
double-sided aspheric lens, and a sixth lens being a double-sided
aspheric lens and having a concave surface facing the image side
near the optical axis, wherein the image-side surface of the sixth
lens is an aspheric surface changing to the convex surface at a
peripheral area.
In the above-described configuration, the first lens achieves
low-profileness and wide field of view of the imaging lens by the
positive refractive power. The second lens has the positive
refractive power, achieves the low-profileness and wide field of
view of the imaging lens, and properly corrects astigmatism and
field curvature. The third lens and the fourth lens maintain the
low-profileness and properly correct aberrations such as spherical
aberration, coma aberration, astigmatism and field curvature in
well balance. The fifth lens is the double-sided aspheric lens, and
therefore reduces burden on the sixth lens which corrects the field
curvature and the distortion, and controls light ray incident angle
to the image sensor. The sixth lens maintains the low-profileness
and secures back focus. Furthermore, the sixth lens is the
double-sided aspheric lens, and therefore corrects the field
curvature and the distortion, and controls the light ray incident
angle to the image sensor.
According to the imaging lens of the above-described configuration,
it is preferable that a below conditional expression (1) is
satisfied: 1.5<vd4/vd5<3.6 (1) where
vd4: abbe number at d-ray of a fourth lens, and
vd5: abbe number at d-ray of a fifth lens.
The conditional expression (1) defines relationship between the
abbe numbers at d-ray of the fourth lens and the fifth lens, and is
a condition for properly correcting chromatic aberration of
magnification. By satisfying the conditional expression (1), the
chromatic aberration of magnification is properly corrected.
According to the imaging lens of the above-described configuration,
it is preferable that a below conditional expression (2) is
satisfied: 0.30<(T3/TTL).times.100<0.85 (2) where
T3: distance along an optical axis from an image-side surface of
the third lens to an object-side surface of the fourth lens,
and
TTL: distance along an optical axis from an object-side surface of
the first lens to an image plane.
The conditional expression (2) defines an appropriate scope of the
distance along an optical axis from the image-side surface of the
third lens to the object-side surface of the fourth lens, and is a
condition for achieving the low-profileness and proper aberration
correction. By satisfying the conditional expression (2), total
track length can be shortened, the light ray incident angle to the
fourth lens becomes appropriate, and excessive occurrence of the
spherical aberration, the coma aberration and the distortion is
suppressed.
According to the imaging lens of the above-described configuration,
it is preferable that a below conditional expression (3) is
satisfied: 0.5<vd1/(vd2+vd3)<1.0 (3) where
vd1: abbe number at d-ray of a first lens,
vd2: abbe number at d-ray of a second lens, and
vd3: abbe number at d-ray of a third lens.
The conditional expression (3) defines relationship between the
abbe numbers at d-ray of the first lens, the second lens and the
third lens, and is a condition for properly correcting axial
chromatic aberration. By satisfying the conditional expression (3),
the axial chromatic aberration is more properly corrected.
According to the imaging lens of the above-described configuration,
it is preferable that the second lens has a biconvex shape having
convex surfaces facing the object side and the image side near the
optical axis, or a meniscus shape having a concave surface facing
the object side near the optical axis.
When the second lens has the biconvex shape near the optical axis,
the positive refractive power can be appropriately allocated to the
object-side surface and the image-side surface. Therefore, large
positive refractive power can be provided while suppressing
occurrence of the spherical aberration. As a result, the imaging
lens can achieve further low-profileness and wide field of
view.
On the other hand, when the second lens has the meniscus shape
having a concave surface facing the object side near the optical
axis, the light ray incident angle to the second lens can be
appropriately controlled, and the coma aberration and high-order
spherical aberration are properly corrected.
According to the imaging lens of the above-described configuration,
it is preferable that the fourth lens has the positive refractive
power. Furthermore, a shape of the fourth lens is preferably the
biconvex shape having convex surfaces facing the object side and
the image side near the optical axis, or a meniscus shape having a
concave surface facing the object side near the optical axis.
When the fourth lens has the biconvex shape near the optical axis,
the positive refractive power can be appropriately allocated to the
object-side surface and the image-side surface. Therefore, large
positive refractive power can be provided while suppressing
occurrence of the spherical aberration. As a result, the imaging
lens can achieve further low-profileness and wide field of
view.
On the other hand, when the fourth lens has the meniscus shape
having a concave surface facing the object side near the optical
axis, the light ray incident angle to the fourth lens can be
appropriately controlled, and the coma aberration and the
high-order spherical aberration are properly corrected.
According to the imaging lens of the above-described configuration,
it is preferable that a below conditional expression (4) is
satisfied: 1.35<f1/f<3.30 (4) where
f1: focal length of the first lens, and
f: focal length of the overall optical system.
The conditional expression (4) defines the refractive power of the
first lens, and is a condition for achieving the low-profileness
and the proper aberration correction. When a value is below the
upper limit of the conditional expression (4), the positive
refractive power of the first lens becomes appropriate, and the
low-profileness is facilitated. On the other hand, when the value
is above the lower limit of the conditional expression (4), the
high-order spherical aberration and the coma aberration can be
properly corrected.
According to the imaging lens of the above-described configuration,
it is preferable that a below conditional expression (5) is
satisfied: 0.8<f2/f<3.4 (5) where
f2: focal length of the second lens, and
f: focal length of the overall optical system.
The conditional expression (5) defines the refractive power of the
second lens, and is a condition for achieving the low-profileness
and the proper aberration correction. When a value is below the
upper limit of the conditional expression (5), the positive
refractive power of the second lens becomes appropriate, and the
low-profileness is facilitated. On the other hand, when the value
is above the lower limit of the conditional expression (5), the
high-order spherical aberration and the coma aberration can be
properly corrected.
According to the imaging lens of the above-described configuration,
it is preferable that a below conditional expression (6) is
satisfied: -1.70<f3/f<0.65 (6) where
f3: focal length of the third lens, and
f: focal length of the overall optical system.
The conditional expression (6) defines the refractive power of the
third lens, and is a condition for reducing sensitivity to
manufacturing error and for properly correcting the distortion.
When the refractive power of the third lens is not large or small
more than necessary, the sensitivity to manufacturing error can be
reduced and the coma aberration and the distortion at a peripheral
area can be properly corrected.
According to the imaging lens of the above-described configuration,
it is preferable that a below conditional expression (7) is
satisfied: 0.65<f4/f<2.10 (7) where
f4: focal length of the fourth lens, and
f: focal length of the overall optical system.
The conditional expression (7) defines the refractive power of the
fourth lens, and is a condition for achieving the low-profileness
and the proper aberration correction. When a value is below the
upper limit of the conditional expression (7), the positive
refractive power of the fourth lens becomes appropriate, and the
low-profileness can be achieved. On the other hand, when the value
is above the lower limit of the conditional expression (7), the
high-order spherical aberration and the coma aberration can be
properly corrected.
According to the imaging lens of the above-described configuration,
it is preferable that a below conditional expression (8) is
satisfied: 1.9<|f6|/f (8) where
f6: focal length of the sixth lens, and
f: focal length of the overall optical system.
The conditional expression (8) defines the refractive power of the
sixth lens, and is a condition for achieving the low-profileness
and the proper aberration correction. When the value is above the
lower limit of the conditional expression (8), the chromatic
aberration is corrected, the total track length is shortened and
the field curvature can be properly corrected.
According to the imaging lens of the above-described configuration,
it is preferable that the fifth lens has plane surfaces on both
sides near the optical axis, and has no substantial refractive
power near the optical axis.
When the fifth lens has plane surfaces on both side near the
optical axis, and has no substantial refractive power near the
optical axis, the aberrations such as the chromatic aberration of
magnification can be properly corrected without affecting the focal
length of the overall optical system or allocation of the
refractive power of other lenses.
The fifth lens is not limited to a shape having plane surfaces on
the both sides near the optical axis. If effect on the focal length
of the overall optical system or the refractive power of each lens
is suppressed to small, various shapes may be applicable for the
fifth lens, such as a meniscus shape having the convex surface
facing the object side, a biconvex shape having the convex surfaces
facing the object side and the image side, a meniscus shape having
the concave surface facing the object side, a biconcave shape
having the concave surfaces facing the object side and the image
side, a shape having a plane surface facing the object side and a
convex or a concave surface facing the image side, and a shape
having the plane surface facing the image side and the convex or
the concave surface facing the object side.
According to the imaging lens of the above-described configuration,
it is preferable that a below conditional expression (9) is
satisfied: 0.1<D6/.SIGMA.D<0.3 (9) where
D6: thickness on the optical axis of the sixth lens, and
.SIGMA.D: total sum of thickness on the optical axis of the first
lens, the second lens, the third lens, the fourth lens, the fifth
lens and the sixth lens.
The conditional expression (9) defines the thickness on the optical
axis of the sixth lens to the total sum of each thickness on the
optical axis of the first lens to the sixth lens, and is a
condition for achieving improvement of formability and proper
aberration correction. By satisfying the conditional expression
(9), the thickness of the sixth lens becomes appropriate, and
uneven thickness of a center area and a peripheral area of the
sixth lens becomes small. As a result, the formability of the sixth
lens can be improved. Furthermore, by satisfying the conditional
expression (9), the thickness on the optical axis of the first to
the fifth lenses and intervals therebetween can be appropriately
determined, and freedom in the aspheric surface is improved.
Therefore, the proper aberration correction can be made.
According to the imaging lens of the above-described configuration,
it is preferable that a below conditional expression (10) is
satisfied: 0.7<.SIGMA.(L1F-L6R)/f<1.6 (10) where
.SIGMA.(L1F-L6R): distance along the optical axis from the
object-side surface of the first lens to the image-side surface of
the sixth lens, and
f: focal length of the overall optical system.
The conditional expression (10) defines the distance along the
optical axis from the object-side surface of the first lens to the
image-side surface of the sixth lens to the focal length of the
overall optical system, and is a condition for achieving the
low-profileness and proper aberration correction. When a value is
below the upper limit of the conditional expression (10), the back
focus is secured and space for arranging a filter is also secured.
On the other hand, when the value is above the lower limit of the
conditional expression (10), thickness of each lens of which the
imaging lens is comprised is easily secured. Furthermore, each
interval of lenses can be appropriately determined, and therefore
the freedom in the aspheric surface is improved. Therefore, the
proper aberration correction can be made.
According to the imaging lens of the above-described configuration,
it is preferable that a shape of the third lens is a meniscus shape
having the concave surface facing the object side near the optical
axis. Furthermore, it is more preferable that a below conditional
expression (11) is satisfied: 0.1<r5/r6<0.7 (11) where
r5: paraxial curvature radius of the object-side surface of the
third lens, and
r6: paraxial curvature radius of the image-side surface of the
third lens.
The conditional expression (11) defines relationship of the
curvature radii of the object-side surface and the image-side
surface of the third lens, and is a condition for properly
correcting the aberrations. When the shape near the optical axis of
the third lens is the meniscus shape satisfying a scope of the
conditional expression (11), the coma aberration and the
astigmatism can be properly corrected.
According to the imaging lens of the above-described configuration,
it is preferable that below conditional expressions (12) and (13)
are satisfied: 0.20<r11/f<0.55 (12) 0.15<r12/f<0.45
(13) where
r11: paraxial curvature radius of the object-side surface of the
sixth lens,
r12: paraxial curvature radius of the image-side surface of the
sixth lens, and
f: focal length of the overall optical system.
The conditional expressions (12) and (13) define a shape near the
optical axis of the sixth lens, and are conditions for securing the
back focus and achieving the low-profileness. By satisfying the
conditional expressions (12) and (13), appropriate back focus is
secured and the low-profileness can be achived.
According to the imaging lens of the above-described configuration,
it is preferable that a below conditional expression (14) is
satisfied: Fno.ltoreq.2.0 (14) where
Fno: F-number.
The conditional expression (14) defines the F-number. When a value
is below the upper limit of the conditional expression (14),
brightness required for the imaging lens in recent years can be
fully secured, if it is mounted in a portable mobile device, a
monitoring camera, or an onboard camera.
According to the imaging lens of the above-described configuration,
it is preferable that a below conditional expression (15) is
satisfied: 0.6<f2/f4<2.6 (15) where
f2: focal length of the first lens, and
f4: focal length of the fourth lens.
The conditional expression (15) defines an appropriate scope of a
ratio between the refractive power of the second lens and the
refractive power of the fourth lens, and a condition for achieving
the low-profileness and the proper aberration correction. By
satisfying the conditional expression (15), the large refractive
power is appropriately balanced to the second lens and the fourth
lens, the low-profileness and the wide field of view is achieved,
and proper correction of the astigmatism and the field curvature
can be made.
According to the imaging lens of the above-described configuration,
it is preferable that a below conditional expression (16) is
satisfied: 0.60<T3/T4<1.35 (16) where
T3: distance along an optical axis from an image-side surface of
the third lens to an object-side surface of the fourth lens,
and
T4: distance along an optical axis from an image-side surface of
the fourth lens to an object-side surface of the fifth lens.
The conditional expression (16) defines a ratio of an interval
between the third lens and the fourth lens, and an interval between
the fourth lens and the fifth lens, and is a condition for
achieving the low-profileness and the proper aberration correction.
By satisfying the conditional expression (16), difference between
the interval of the third lens and the fourth lens and the interval
of the fourth lens and the fifth lens is suppressed not to be
increased, and the low-profileness is achieved. Furthermore, by
satisfying the conditional expression (16), the fourth lens is
arranged at an optimum position, and aberration correction function
of the lens becomes more effective.
According to the imaging lens of the above-described configuration,
it is preferable that a below conditional expression (17) is
satisfied: 5<(D5/TTL).times.100<12 (17) where
D5: thickness on the optical axis of the fifth lens, and
TTL: distance along an optical axis from an object-side surface of
the first lens to an image plane.
The conditional expression (17) defines an appropriate thickness on
the optical axis of the fifth lens, and is a condition for
maintaining proper formability of the fifth lens and achieving the
low-profileness.
When a value is below the upper limit of the conditional expression
(17), the thickness on the optical axis of the fifth lens is
prevented from being excessively large, and securing an air gap of
the object side and the image side of the fifth lens is
facilitated. Therefore, the low-profileness can be maintained. On
the other hand, when the value is above the lower limit of the
conditional expression (17), the thickness on the optical axis of
the fifth lens is prevented from being excessively small, and the
formability of the lens becomes proper.
Effect of Invention
According to the present invention, there can be provided an
imaging lens with high resolution which satisfies in well balance
the low-profileness and the low F-number, and properly corrects
aberrations.
BRIEF DESCRIPTION OF THE DRAWINGS
FIG. 1 is a schematic view showing a general configuration of an
imaging lens in Example 1 according to the present invention;
FIG. 2 shows spherical aberration, astigmatism, and distortion of
the imaging lens in Example 1 according to the present
invention;
FIG. 3 is a schematic view showing the general configuration of an
imaging lens in Example 2 according to the present invention;
FIG. 4 shows spherical aberration, astigmatism, and distortion of
the imaging lens in Example 2 according to the present
invention;
FIG. 5 is a schematic view showing the general configuration of an
imaging lens in Example 3 according to the present invention;
FIG. 6 shows spherical aberration, astigmatism, and distortion of
the imaging lens in Example 3 according to the present
invention;
FIG. 7 is a schematic view showing the general configuration of an
imaging lens in Example 4 according to the present invention;
FIG. 8 shows spherical aberration, astigmatism, and distortion of
the imaging lens in Example 4 according to the present
invention.
FIG. 9 is a schematic view showing a general configuration of an
imaging lens in Example 5 according to the present invention;
FIG. 10 shows spherical aberration, astigmatism, and distortion of
the imaging lens in Example 5 according to the present
invention;
FIG. 11 is a schematic view showing the general configuration of an
imaging lens in Example 6 according to the present invention;
FIG. 12 shows spherical aberration, astigmatism, and distortion of
the imaging lens in Example 6 according to the present
invention;
FIG. 13 is a schematic view showing the general configuration of an
imaging lens in Example 7 according to the present invention;
and
FIG. 14 shows spherical aberration, astigmatism, and distortion of
the imaging lens in Example 7 according to the present
invention.
DETAILED DESCRIPTION OF THE PREFERRED EMBODIMENT
Hereinafter, the preferred embodiment of the present invention will
be described in detail referring to the accompanying drawings.
FIGS. 1, 3, 5, 7, 9, 11 and 13 are schematic views of the imaging
lenses in Examples 1 to 7 according to the embodiments of the
present invention, respectively.
As shown in FIG. 1, the imaging lens according to the present
embodiments comprises in order from an object side to an image
side, a first lens L1 having positive refractive power, a second
lens L2 having the positive refractive power, a third lens L3, a
fourth lens L4, a fifth lens L5 being a double-sided aspheric lens,
and a sixth lens L6 having a concave surface facing the image side
near the optical axis X. The image-side surface of the sixth lens
L6 is an aspheric surface changing to the convex surface at a
peripheral area.
A filter IR such as an IR cut filter and a cover glass are arranged
between the sixth lens L6 and an image plane IMG. The filter IR is
omissible.
The first lens L1 has the positive refractive power, and occurrence
of aberrations is suppressed by aspheric surfaces on both sides and
low-profileness and wide field of view of the imaging lens are
achieved. The first lens L1 has a meniscus shape having a convex
surface facing the object side near the optical axis X, or a
biconvex shape having convex surfaces facing the object side and
the image side near the optical axis X. In an Example shown in FIG.
1, an Example 2 shown in FIG. 3, an Example 3 shown in FIG. 5, an
Example 5 shown in FIG. 9 and an Example 7 shown in FIG. 13, the
first lens L1 has the meniscus shape having the convex surface
facing the object side near the optical axis X. In this case, a
position of principal point on the image side of the imaging lens
moves toward the object side, and it is advantageous for the
low-profileness. In an Example 4 shown in FIG. 7 and an Example 6
shown in FIG. 11, the first lens L1 has the biconvex shape having
the convex surfaces facing the object side and the image side near
the optical axis X. In this case, the position of principal point
on the image side of the imaging lens moves toward the image side,
and it is advantageous for the wide field of view.
The second lens L2 has the positive refractive power, and
astigmatism and field curvature are properly corrected by aspheric
surfaces on both sides and the low-profileness and the wide field
of view of the imaging lens are achieved. The second lens L2 has
the biconvex shape having the convex surfaces facing the object
side and the image side near the optical axis X, or a meniscus
shape having a concave surface facing the object side near the
optical axis X. In the Example 1 shown in FIG. 1, the Example 2
shown in FIG. 3, the Example 3 shown in FIG. 5, the Example 4 shown
in FIG. 7 and the Example 7 shown in FIG. 13, the second lens L2
has the biconvex shape having the convex surfaces facing the object
side and the image side near the optical axis X. In this case, the
positive refractive power is appropriately allocated to the
object-side surface and the image-side surface. Therefore, large
positive refractive power can be provided while suppressing
occurrence of the spherical aberration. As a result, the imaging
lens can achieve further low-profileness and wide field of view. In
the Example 5 shown in FIG. 9 and the Example 6 shown in FIG. 11,
the second lens L2 has the meniscus shape having a concave surface
facing the object side near the optical axis X. In this case, the
light ray incident angle to the second lens L2 can be appropriately
controlled, and the coma aberration and high-order spherical
aberration are properly corrected.
The third lens L3 has negative refractive power, and the spherical
aberration, the coma aberration, the astigmatism and the chromatic
aberration are properly corrected by the aspheric surfaces on both
sides. A shape of the third lens L3 is the meniscus shape having a
concave surface facing the object side near the optical axis X.
Therefore, the light ray incident angle to the third lens L3 can be
appropriately controlled, and the coma aberration and the
high-order spherical aberration are properly corrected.
The fourth lens L4 has the positive refractive power, and the
astigmatism and the field curvature are properly corrected by the
aspheric surfaces on both sides and the low-profileness and the
wide field of view of the imaging lens are achieved. The fourth
lens L4 has the biconvex shape having the convex surfaces facing
the object side and the image side near the optical axis X, or the
meniscus shape having the concave surface facing the object side
near the optical axis X. In the Example 1 shown in FIG. 1, the
Example 2 shown in FIG. 3, the Example 3 shown in FIG. 5, the
Example 4 shown in FIG. 7, the Example 5 shown in FIG. 9 and the
Example 6 shown in FIG. 11, the fourth lens L4 has the biconvex
shape near the optical axis X. In this case, the positive
refractive power is appropriately allocated to the object-side
surface and the image-side surface. Therefore, the large positive
refractive power can be provided while suppressing occurrence of
the spherical aberration. As a result, the imaging lens can achieve
further low-profileness and wide field of view. In the Example 7
shown in FIG. 13, the fourth lens L4 has the meniscus shape having
the concave surface facing the object side near the optical axis X.
In this case, the light ray incident angle to the fourth lens L4
can be appropriately controlled, and the coma aberration and the
high-order spherical aberration are properly corrected.
The fifth lens L5 reduces burden on the sixth lens L6 which
corrects the field curvature and the distortion and controls light
ray incident angle to the image sensor, and also corrects chromatic
aberration of magnification by the aspheric surfaces on the both
sides. The fifth lens L5 has plane surfaces on both sides near the
optical axis X, and is an aberration correction lens having no
substantial refractive power near the optical axis X. Therefore,
the aberrations can be properly corrected without affecting the
focal length of the overall optical system or allocation of the
refractive power of other lenses. The fifth lens L5 is not limited
to the double-sided plane surface shape near the optical axis X. If
effect on the focal length of the overall optical system or the
refractive power of each lens is suppressed to small, various
shapes may be applicable for the fifth lens L5, such as a meniscus
shape having the convex surface facing the object side, a biconvex
shape having the convex surfaces facing the object side and the
image side, a meniscus shape having the concave surface facing the
object side, a biconcave shape having the concave surfaces facing
the object side and the image side, a shape having a plane surface
facing the object side and a convex or a concave surface facing the
image side, and a shape having the plane surface facing the image
side and the convex or the concave surface facing the object
side.
The sixth lens L6 has the concave surface facing the image side
near the optical axis X and the negative refractive power, and
secures back focus while maintaining the low-profileness. The
refractive power of the sixth lens L6 may be the positive
refractive power as shown in the Example 7 shown in FIG. 13.
Furthermore, correction of the field curvature and the distortion,
and control of light ray incident angle to the image sensor are
made by the aspheric surfaces on the both sides. The image-side
surface of the sixth lens L6 is the aspheric surface having a pole
point and changes to the convex surface at an area apart from the
optical axis X and maintains the convex shape until an edge of an
effective diameter. By applying such aspheric surface, correction
of the field curvature and control of light ray angle to an image
sensor are facilitated.
In the imaging lens according to the present invention, an aperture
stop ST is arranged on the object side of the first lens L1. By
arranging the aperture stop ST closest to the object, a position of
entrance pupil gets away from the image plane, and control of the
light ray incident angle to the image sensor and telecentricity
becomes facilitated.
Regarding the imaging lens according to the present embodiments,
for example as shown in FIG. 1, all lenses of the first lens L1 to
the sixth lens L6 are preferably single lenses which are not
cemented each other. Configuration without the cemented lens can
frequently use the aspheric surfaces, and proper correction of the
aberrations can be realized. Furthermore, workload for cementing is
reduced, and manufacturing in low cost becomes possible.
Regarding the imaging lens according to the present embodiments, a
plastic material is used for all of the lenses, and manufacturing
is facilitated and mass production in a low cost can be realized.
Both-side surfaces of all lenses are appropriate aspheric, and the
aberrations are favorably corrected.
The material applied to the lens is not limited to the plastic
material. By using glass material, further high performance may be
aimed. All of surfaces of lenses are preferably formed as aspheric
surfaces, however, spherical surfaces may be adopted which is easy
to manufacture in accordance with required performance.
The imaging lens according to the present embodiments shows
preferable effect by satisfying the below conditional expressions
(1) to (17). 1.5<vd4/vd5<3.6 (1)
0.30<(T3/TTL).times.100<0.85 (2) 0.5<vd1/(vd2+vd3)<1.0
(3) 1.35<f1/f<3.30 (4) 0.8<f2/f<3.4 (5)
-1.70<f3/f<-0.65 (6) 0.65<f4/f<2.10 (7) 1.9<|f6|/f
(8) 0.1<D6/.SIGMA.D<0.3 (9) 0.7<.SIGMA.(L1F-L6R)/f<1.6
(10) 0.1<r5/r6<0.7 (11) 0.20<r11/f<0.55 (12)
0.15<r12/f<0.45 (13) Fno.ltoreq.2.0 (14) 0.6<f2/f4<2.6
(15) 0.60<T3/T4<1.35 (16) 5<(D5/TTL).times.100<12 (17)
where
vd1: abbe number at d-ray of a first lens L1,
vd2: abbe number at d-ray of a second lens L2,
vd3: abbe number at d-ray of a third lens L3,
vd4: abbe number at d-ray of a fourth lens L4,
vd5: abbe number at d-ray of a fifth lens L5,
T3: distance along an optical axis from an image-side surface of
the third lens L3 to an object-side surface of the fourth lens
L4,
T4: distance along an optical axis from an image-side surface of
the fourth lens L4 to an object-side surface of the fifth lens
L5,
TTL: distance along an optical axis from an object-side surface of
the first lens L1 to an image plane,
f: focal length of the overall optical system,
f1: focal length of the first lens L1,
f2: focal length of the second lens L2,
f3: focal length of the third lens L3,
f4: focal length of the fourth lens L4,
f6: focal length of the sixth lens L6,
D5: thickness on the optical axis of the fifth lens L5,
D6: thickness on the optical axis of the sixth lens L6,
.SIGMA.D: total sum of thickness on the optical axis X of the first
lens L1, the second lens L2, the third lens L3, the fourth lens L4,
the fifth lens L5 and the sixth lens L6,
.SIGMA.(L1F-L6R): distance along the optical axis X from the
object-side surface of the first lens L1 to the image-side surface
of the sixth lens L6,
r5: paraxial curvature radius of the object-side surface of the
third lens L3,
r6: paraxial curvature radius of the image-side surface of the
third lens L3,
r11: paraxial curvature radius of the object-side surface of the
sixth lens L6,
r12: paraxial curvature radius of the image-side surface of the
sixth lens L6, and
Fno: F-number.
It is not necessary to satisfy the above all conditional
expressions, and by satisfying the conditional expression
individually, operational advantage corresponding to each
conditional expression can be obtained.
The imaging lens according to the present embodiments shows further
preferable effect by satisfying the below conditional expressions
(1a) to (17a). 1.85<vd4/vd5<3.20 (1a)
0.40<(T3/TTL).times.100<0.75 (2a)
0.60<vd1/(vd2+vd3)<0.85 (3a) 1.65<f1/f<2.90 (4a)
1.00<f2/f<2.95 (5a) -1.5<f3/f<-0.8 (6a)
0.80<f4/f<1.85 (7a) 2.4<|f6|/f<20.0 (8a)
0.14<D6/.SIGMA.D<0.25 (9a) 0.9<.SIGMA.(L1F-L6R)/f<1.4
(10a) 0.13<r5/r6<0.60 (11a) 0.24<r11/f<0.45 (12a)
0.20<r12/f<0.35 (13a) Fno.ltoreq.1.9 (14a)
0.75<f2/f4<2.3 (15a) 0.75<T3/T4<1.20 (16a)
6<(D5/TTL).times.100<10 (17a)
The signs in the above conditional expressions have the same
meanings as those in the paragraph before the preceding
paragraph.
In this embodiment, the aspheric shapes of the surfaces of the
aspheric lens are expressed by Equation 1, where Z denotes an axis
in the optical axis direction, H denotes a height perpendicular to
the optical axis, R denotes a curvature radius, k denotes a conic
constant, and A4, A6, A8, A10, A12, A14, A16, A18 and A20 denote
aspheric surface coefficients.
.times..times..times..times..times..times..times..times..times..times..ti-
mes..times. ##EQU00001##
Next, examples of the imaging lens according to this embodiment
will be explained. In each example, f denotes the focal length of
the overall optical system of the imaging lens, Fno denotes an
F-number, .omega. denotes a half field of view, and ih denotes a
maximum image height. Additionally, i denotes surface number
counted from the object side, r denotes a curvature radius, d
denotes the distance of lenses along the optical axis (surface
distance), Nd denotes a refractive index at d-ray (reference
wavelength), and vd denotes an abbe number at d-ray. As for
aspheric surfaces, an asterisk (*) is added after surface number
i.
EXAMPLE 1
The basic lens data is shown below in Table 1.
TABLE-US-00001 TABLE 1 Example 1 Unit mm f = 2.72 ih = 3.26 Fno =
1.8 TTL = 4.11 .omega.(.degree.) = 50.1 Surface Data Surface
Curvature Surface Refractive Abbe Number i Radius r Distance d
Index Nd Number vd (Object) Infinity Infinity 1 (Stop) Infinity
-0.0510 2* 2.2524 0.4131 1.544 55.86 (vd1) 3* 5.3692 0.1174 4*
6.0879 0.4526 1.535 55.66 (vd2) 5* -2.3793 0.3515 6* -0.7310 0.3300
1.661 20.37 (vd3) 7* -1.4661 0.0260 8* 10.0989 0.3825 1.544 55.86
(vd4) 9* -2.3572 0.0300 10* Infinity 0.3600 1.614 25.58 (vd5) 11*
Infinity 0.0334 12* 1.0843 0.4918 1.535 55.66 (vd6) 13* 0.8614
0.5000 14 Infinity 0.2100 1.517 64.20 15 Infinity 0.4818 Image
Plane Infinity Constituent Lens Data Lens Start Surface Focal
Length 1 2 6.810 2 4 3.259 3 6 -2.686 4 8 3.550 5 10 Infinity 6 12
-33.885 Aspheric Surface Data Second Surface Third Surface Fourth
Surface Fifth Surface Sixth Surface Seventh Surface k -2.331179E+00
0.000000E+00 -1.000000E+00 -9.999999E-01 -1.000000E+00 0.000000E+00
A4 -7.527715E-02 -2.220918E-01 -1.512366E-01 -1.504052E-01
7.168343E-02 -8.029630E-02 A6 2.319407E-02 -8.729089E-02
-2.817847E-01 1.138025E-02 -7.631071E-01 -3.797023E-01 A8
-2.762643E-01 -6.155922E-01 -1.869433E-01 -3.627602E-01
3.243245E+00 2.386234E+00 A10 0.000000E+00 7.070838E-01
-8.875539E-02 -4.029084E-01 -6.825057E+00 -4.836478E+00 A12
0.000000E+00 0.000000E+00 4.416396E-01 2.133227E+00 7.731701E+00
5.042076E+00 A14 0.000000E+00 0.000000E+00 0.000000E+00
-2.637456E+00 -4.665493E+00 -2.735304E+00 A16 0.000000E+00
0.000000E+00 0.000000E+00 1.077927E+00 1.329231E+00 6.183892E-01
A18 0.000000E+00 0.000000E+00 0.000000E+00 0.000000E+00
0.000000E+00 0.000000E+00 A20 0.000000E+00 0.000000E+00
0.000000E+00 0.000000E+00 0.000000E+00 0.000000E+00 Eighth Surface
Ninth Surface Tenth Surface Eleventh Surface Twelfth Surface
Thirteenth Surface k -1.186726E+01 -5.494574E+00 0.000000E+00
0.000000E+00 -1.749347E+00 -6.224194E+00 A4 -5.858264E-01
-1.765618E-01 8.845825E-01 1.230193E+00 -1.898125E-01 -2.683399E-02
A6 1.714607E+00 8.112415E-01 -1.924596E+00 -2.751103E+00
-8.109097E-03 -9.674510E-02 A8 -2.741997E+00 -1.751492E+00
2.291965E+00 3.353928E+00 -1.072885E-01 9.456732E-02 A10
2.709759E+00 2.347716E+00 -1.836641E+00 -2.645794E+00 2.127916E-01
-4.148820E-02 A12 -1.725241E+00 -1.916429E+00 1.045465E+00
1.383599E+00 -1.392192E-01 1.029346E-02 A14 6.799612E-01
9.003401E-01 -4.350007E-01 -4.715054E-01 4.558670E-02 -1.491162E-03
A16 -1.588798E-01 -2.213776E-01 1.248930E-01 9.966130E-02
-8.140478E-03 1.162402E-04 A18 1.837638E-02 2.196511E-02
-2.120587E-02 -1.178062E-02 7.602449E-04 -3.548513E-06 A20
0.000000E+00 0.000000E+00 1.550254E-03 5.927364E-04 -2.916836E-05
-2.250417E-08
The imaging lens in Example 1 satisfies conditional expressions (1)
to (17) as shown in Table 8.
FIG. 2 shows spherical aberration (mm), astigmatism (mm), and
distortion (%) of the imaging lens in Example 1. The spherical
aberration diagram shows the amount of aberration at wavelengths of
F-ray (486 nm), d-ray (588 nm), and C-ray (656 nm). The astigmatism
diagram shows the amount of aberration at d-ray on a sagittal image
surface S and on tangential image surface T, respectively (same as
FIGS. 4, 6, 8, 10, 12 and 14). As shown in FIG. 2, each aberration
is corrected excellently.
EXAMPLE 2
The basic lens data is shown below in Table 2.
TABLE-US-00002 TABLE 2 Example 2 Unit mm f = 2.66 ih = 3.26 Fno =
1.8 TTL = 4.09 .omega.(.degree.) = 49.9 Surface Data Surface
Curvature Surface Refractive Abbe Number i Radius r Distance d
Index Nd Number vd (Object) Infinity Infinity 1 (Stop) Infinity
-0.0510 2* 2.2559 0.3923 1.544 55.86 (vd1) 3* 6.3436 0.1209 4*
9.5000 0.4886 1.535 55.66 (vd2) 5* -2.5193 0.3838 6* -0.7424 0.2421
1.661 20.37 (vd3) 7* -1.5132 0.0200 8* 12.0245 0.4556 1.544 55.86
(vd4) 9* -1.9696 0.0200 10* Infinity 0.3635 1.614 25.58 (vd5) 11*
Infinity 0.0451 12* 1.0176 0.5421 1.535 55.66 (vd6) 13* 0.7909
0.5000 14 Infinity 0.2100 1.517 64.20 15 Infinity 0.3742 Image
Plane Infinity Constituent Lens Data Lens Start Surface Focal
Length 1 2 6.222 2 4 3.777 3 6 -2.521 4 8 3.145 5 10 Infinity 6 12
-39.776 Aspheric Surface Data Second Surface Third Surface Fourth
Surface Fifth Surface Sixth Surface Seventh Surface k -2.695462E+00
0.000000E+00 -3.119093E+01 -1.335637E-01 -9.278509E-01 0.000000E+00
A4 -7.527715E-02 -2.220918E-01 -1.512366E-01 -1.504052E-01
7.168343E-02 -8.029630E-02 A6 2.319407E-02 -8.729089E-02
-2.817847E-01 1.138025E-02 -7.631071E-01 -3.797023E-01 A8
-2.762643E-01 -6.155922E-01 -1.869433E-01 -3.627602E-01
3.243245E+00 2.386234E+00 A10 0.000000E+00 7.070838E-01
-8.875539E-02 -4.029084E-01 -6.825057E+00 -4.836478E+00 A12
0.000000E+00 0.000000E+00 4.416396E-01 2.133227E+00 7.731701E+00
5.042076E+00 A14 0.000000E+00 0.000000E+00 0.000000E+00
-2.637456E+00 -4.665493E+00 -2.735304E+00 A16 0.000000E+00
0.000000E+00 0.000000E+00 1.077927E+00 1.329231E+00 6.183892E-01
A18 0.000000E+00 0.000000E+00 0.000000E+00 0.000000E+00
0.000000E+00 0.000000E+00 A20 0.000000E+00 0.000000E+00
0.000000E+00 0.000000E+00 0.000000E+00 0.000000E+00 Eighth Surface
Ninth Surface Tenth Surface Eleventh Surface Twelfth Surface
Thirteenth Surface k 9.780001E+01 -3.361475E+00 0.000000E+00
0.000000E+00 -1.804938E+00 -4.974734E+00 A4 -5.779474E-01
-1.493699E-01 9.373616E-01 1.235279E+00 -1.996052E-01 -2.768815E-02
A6 1.778412E+00 7.726362E-01 -1.985774E+00 -2.741133E+00
-1.225109E-02 -9.625771E-02 A8 -3.077586E+00 -1.755397E+00
2.356057E+00 3.329674E+00 -1.069381E-01 9.673744E-02 A10
3.239769E+00 2.345984E+00 -1.898728E+00 -2.635137E+00 2.133280E-01
-4.256441E-02 A12 -2.138360E+00 -1.914744E+00 1.074841E+00
1.382481E+00 -1.392405E-01 1.040494E-02 A14 7.708789E-01
9.001788E-01 -4.374730E-01 -4.716857E-01 4.556365E-02 -1.474588E-03
A16 -1.003858E-01 -2.228034E-01 1.215196E-01 9.969614E-02
-8.139113E-03 1.151275E-04 A18 -9.792236E-03 2.278357E-02
-1.973163E-02 -1.178015E-02 7.604543E-04 -4.077100E-06 A20
0.000000E+00 0.000000E+00 1.335666E-03 5.924430E-04 -2.917784E-05
2.624107E-08
The imaging lens in Example 2 satisfies conditional expressions (1)
to (17) as shown in Table 8.
FIG. 4 shows spherical aberration (mm), astigmatism (mm), and
distortion (%) of the imaging lens in Example 2. As shown in FIG.
4, each aberration is corrected excellently.
EXAMPLE 3
The basic lens data is shown below in Table 3.
TABLE-US-00003 TABLE 3 Example 3 Unit mm f = 2.59 ih = 3.26 Fno =
1.8 TTL = 3.94 .omega.(.degree.) = 51.2 Surface Data Surface
Curvature Surface Refractive Abbe Number i Radius r Distance d
Index Nd Number vd (Object) Infinity Infinity 1 (Stop) Infinity
-0.0510 2* 2.4369 0.3986 1.544 55.86 (vd1) 3* 9.0000 0.0927 4*
9.6512 0.4716 1.535 55.66 (vd2) 5* -2.5036 0.3223 6* -0.8138 0.2759
1.661 20.37 (vd3) 7* -1.6670 0.0200 8* 7.4351 0.4583 1.544 55.86
(vd4) 9* -1.7587 0.0200 10* Infinity 0.3458 1.614 25.58 (vd5) 11*
Infinity 0.0673 12* 1.0121 0.4133 1.535 55.66 (vd6) 13* 0.6899
0.5000 14 Infinity 0.2100 1.517 64.20 15 Infinity 0.4145 Image
Plane Infinity Constituent Lens Data Lens Start Surface Focal
Length 1 2 6.011 2 4 3.768 3 6 -2.762 4 8 2.660 5 10 Infinity 6 12
-7.325 Aspheric Surface Data Second Surface Third Surface Fourth
Surface Fifth Surface Sixth Surface Seventh Surface k -3.260016E+00
0.000000E+00 -3.782225E+01 -1.826789E+00 -1.081000E+00 0.000000E+00
A4 -7.527715E-02 -2.220918E-01 -1.512366E-01 -1.504052E-01
7.168343E-02 -8.029630E-02 A6 2.319407E-02 -8.729089E-02
-2.817847E-01 1.138025E-02 -7.631071E-01 -3.797023E-01 A8
-2.762643E-01 -6.155922E-01 -1.869433E-01 -3.627602E-01
3.243245E+00 2.386234E+00 A10 0.000000E+00 7.070838E-01
-8.875539E-02 -4.029084E-01 -6.825057E+00 -4.836478E+00 A12
0.000000E+00 0.000000E+00 4.416396E-01 2.133227E+00 7.731701E+00
5.042076E+00 A14 0.000000E+00 0.000000E+00 0.000000E+00
-2.637456E+00 -4.665493E+00 -2.735304E+00 A16 0.000000E+00
0.000000E+00 0.000000E+00 1.077927E+00 1.329231E+00 6.183892E-01
A18 0.000000E+00 0.000000E+00 0.000000E+00 0.000000E+00
0.000000E+00 0.000000E+00 A20 0.000000E+00 0.000000E+00
0.000000E+00 0.000000E+00 0.000000E+00 0.000000E+00 Eighth Surface
Ninth Surface Tenth Surface Eleventh Surface Twelfth Surface
Thirteenth Surface k 3.262137E+01 -6.046067E+00 0.000000E+00
0.000000E+00 -1.761221E+00 -4.174866E+00 A4 -5.161471E-01
-1.232851E-01 8.568401E-01 1.246105E+00 -2.136159E-01 -6.128761E-02
A6 1.553392E+00 7.682042E-01 -1.716235E+00 -2.748763E+00
-4.537272E-03 -8.416284E-02 A8 -2.600186E+00 -1.723019E+00
1.863763E+00 3.331651E+00 -1.109148E-01 9.542871E-02 A10
2.835580E+00 2.275904E+00 -1.443339E+00 -2.638124E+00 2.149159E-01
-4.285154E-02 A12 -2.213846E+00 -1.864006E+00 8.795010E-01
1.384832E+00 -1.394310E-01 1.048277E-02 A14 1.186491E+00
8.995568E-01 -4.454881E-01 -4.721943E-01 4.553733E-02 -1.476898E-03
A16 -3.846535E-01 -2.312642E-01 1.634907E-01 9.966285E-02
-8.137865E-03 1.140672E-04 A18 5.504336E-02 2.441071E-02
-3.454872E-02 -1.175873E-02 7.620464E-04 -3.944055E-06 A20
0.000000E+00 0.000000E+00 3.003970E-03 5.906561E-04 -2.935038E-05
2.110647E-08
The imaging lens in Example 3 satisfies conditional expressions (1)
to (17) as shown in Table 8.
FIG. 6 shows spherical aberration (mm), astigmatism (mm), and
distortion (%) of the imaging lens in Example 3. As shown in FIG.
6, each aberration is corrected excellently.
EXAMPLE 4
The basic lens data is shown below in Table 4.
TABLE-US-00004 TABLE 4 Example 4 Unit mm f = 2.47 ih = 3.26 Fno =
1.8 TTL = 3.91 .omega.(.degree.) = 52.5 Surface Data Surface
Curvature Surface Refractive Abbe Number i Radius r Distance d
Index Nd Number vd (Object) Infinity Infinity 1 (Stop) Infinity
0.0300 2* 2.6539 0.4608 1.544 55.86 (vd1) 3* -500.3507 0.1044 4*
100.0701 0.4194 1.535 55.66 (vd2) 5* -2.4843 0.3152 6* -0.7912
0.2001 1.661 20.37 (vd3) 7* -1.6698 0.0200 8* 8.3903 0.5924 1.544
55.86 (vd4) 9* -1.4881 0.0200 10* Infinity 0.3013 1.614 25.58 (vd5)
11* Infinity 0.1237 12* 0.9144 0.4126 1.535 55.66 (vd6) 13* 0.6290
0.5000 14 Infinity 0.2100 1.517 64.20 15 Infinity 0.3059 Image
Plane Infinity Constituent Lens Data Lens Start Surface Focal
Length 1 2 4.852 2 4 4.539 3 6 -2.503 4 8 2.372 5 10 Infinity 6 12
-7.597 Aspheric Surface Data Second Surface Third Surface Fourth
Surface Fifth Surface Sixth Surface Seventh Surface k -2.632580E+00
0.000000E+00 0.000000E+00 -7.917237E+00 -1.045405E+00 0.000000E+00
A4 -7.511897E-02 -2.216251E-01 -1.509188E-01 -1.500892E-01
7.153280E-02 -8.012757E-02 A6 2.311290E-02 -8.698540E-02
-2.807985E-01 1.134042E-02 -7.604364E-01 -3.783734E-01 A8
-2.749116E-01 -6.125782E-01 -1.860280E-01 -3.609841E-01
3.227366E+00 2.374550E+00 A10 0.000000E+00 7.026358E-01
-8.819706E-02 -4.003738E-01 -6.782123E+00 -4.806053E+00 A12
0.000000E+00 0.000000E+00 4.382463E-01 2.116837E+00 7.672297E+00
5.003336E+00 A14 0.000000E+00 0.000000E+00 0.000000E+00
-2.613524E+00 -4.623159E+00 -2.710484E+00 A16 0.000000E+00
0.000000E+00 0.000000E+00 1.066649E+00 1.315324E+00 6.119193E-01
A18 0.000000E+00 0.000000E+00 0.000000E+00 0.000000E+00
0.000000E+00 0.000000E+00 A20 0.000000E+00 0.000000E+00
0.000000E+00 0.000000E+00 0.000000E+00 0.000000E+00 Eighth Surface
Ninth Surface Tenth Surface Eleventh Surface Twelfth Surface
Thirteenth Surface k 4.042719E+01 -3.636609E+00 0.000000E+00
0.000000E+00 -1.929494E+00 -3.388291E+00 A4 -4.933426E-01
-1.337301E-01 9.546355E-01 1.293156E+00 -2.437873E-01 -9.762711E-02
A6 1.439113E+00 7.387064E-01 -1.772673E+00 -2.747973E+00
3.950192E-03 -6.599258E-02 A8 -2.452508E+00 -1.708771E+00
1.904511E+00 3.308634E+00 -1.120200E-01 9.399156E-02 A10
2.779103E+00 2.303112E+00 -1.488840E+00 -2.632469E+00 2.153171E-01
-4.434269E-02 A12 -2.202493E+00 -1.886041E+00 9.071041E-01
1.385081E+00 -1.396150E-01 1.109211E-02 A14 1.141336E+00
9.077591E-01 -4.495010E-01 -4.722948E-01 4.556846E-02 -1.582081E-03
A16 -3.382970E-01 -2.354152E-01 1.624357E-01 9.964229E-02
-8.139940E-03 1.226534E-04 A18 4.202373E-02 2.562746E-02
-3.582932E-02 -1.174936E-02 7.625235E-04 -4.218023E-06 A20
0.000000E+00 0.000000E+00 3.578610E-03 5.893388E-04 -2.941679E-05
2.268033E-08
The imaging lens in Example 4 satisfies conditional expressions (1)
to (17) as shown in Table 8.
FIG. 8 shows spherical aberration (mm), astigmatism (mm), and
distortion (%) of the imaging lens in Example 4. As shown in FIG.
8, each aberration is corrected excellently.
EXAMPLE 5
The basic lens data is shown below in Table 5.
TABLE-US-00005 TABLE 5 Example 5 Unit mm f = 2.49 ih = 3.26 Fno =
1.8 TTL = 3.91 .omega.(.degree.) = 52.1 Surface Data Surface
Curvature Surface Refractive Abbe Number i Radius r Distance d
Index Nd Number vd (Object) Infinity Infinity 1 (Stop) Infinity
-0.0300 2* 2.6123 0.4432 1.544 55.86 (vd1) 3* 59.9999 0.1006 4*
-5999.9940 0.4177 1.535 55.66 (vd2) 5* -2.3939 0.3248 6* -0.7724
0.2050 1.661 20.37 (vd3) 7* -1.6285 0.0200 8* 8.1679 0.5640 1.544
55.86 (vd4) 9* -1.4563 0.0200 10* Infinity 0.2820 1.614 25.58 (vd5)
11* Infinity 0.1322 12* 0.8988 0.3839 1.535 55.66 (vd6) 13* 0.6285
0.5000 14 Infinity 0.2100 1.517 64.20 15 Infinity 0.3734 Image
Plane Infinity Constituent Lens Data Lens Start Surface Focal
Length 1 2 5.004 2 4 4.478 3 6 -2.458 4 8 2.319 5 10 Infinity 6 12
-7.741 Aspheric Surface Data Second Surface Third Surface Fourth
Surface Fifth Surface Sixth Surface Seventh Surface k -3.702824E+00
0.000000E+00 0.000000E+00 -6.448212E+00 -1.080022E+00 0.000000E+00
A4 -7.527738E-02 -2.220925E-01 -1.512371E-01 -1.504057E-01
7.168365E-02 -8.029654E-02 A6 2.319419E-02 -8.729133E-02
-2.817861E-01 1.138030E-02 -7.631109E-01 -3.797042E-01 A8
-2.762662E-01 -6.155966E-01 -1.869446E-01 -3.627628E-01
3.243268E+00 2.386251E+00 A10 0.000000E+00 7.070902E-01
-8.875619E-02 -4.029120E-01 -6.825119E+00 -4.836522E+00 A12
0.000000E+00 0.000000E+00 4.416444E-01 2.133251E+00 7.731786E+00
5.042131E+00 A14 0.000000E+00 0.000000E+00 0.000000E+00
-2.637490E+00 -4.665554E+00 -2.735339E+00 A16 0.000000E+00
0.000000E+00 0.000000E+00 1.077943E+00 1.329251E+00 6.183985E-01
A18 0.000000E+00 0.000000E+00 0.000000E+00 0.000000E+00
0.000000E+00 0.000000E+00 A20 0.000000E+00 0.000000E+00
0.000000E+00 0.000000E+00 0.000000E+00 0.000000E+00 Eighth Surface
Ninth Surface Tenth Surface Eleventh Surface Twelfth Surface
Thirteenth Surface k 3.367314E+01 -3.768192E+00 0.000000E+00
0.000000E+00 -1.948663E+00 -3.298325E+00 A4 -5.004754E-01
-1.192848E-01 9.830686E-01 1.299255E+00 -2.452653E-01 -1.107272E-01
A6 1.469749E+00 7.226936E-01 -1.835626E+00 -2.757331E+00
4.277730E-03 -5.860955E-02 A8 -2.524711E+00 -1.682018E+00
1.989508E+00 3.316366E+00 -1.101479E-01 9.126892E-02 A10
2.871435E+00 2.267117E+00 -1.557904E+00 -2.634591E+00 2.144441E-01
-4.380031E-02 A12 -2.265235E+00 -1.858146E+00 9.354133E-01
1.384890E+00 -1.394668E-01 1.104958E-02 A14 1.163429E+00
8.997934E-01 -4.490824E-01 -4.721300E-01 4.555141E-02 -1.584185E-03
A16 -3.441692E-01 -2.379676E-01 1.579797E-01 9.967033E-02
-8.135783E-03 1.225808E-04 A18 4.340716E-02 2.701494E-02
-3.449233E-02 -1.177166E-02 7.616982E-04 -4.090529E-06 A20
0.000000E+00 0.000000E+00 3.448965E-03 5.920393E-04 -2.935678E-05
1.337399E-08
The imaging lens in Example 5 satisfies conditional expressions (1)
to (17) as shown in Table 8.
FIG. 10 shows spherical aberration (mm), astigmatism (mm), and
distortion (%) of the imaging lens in Example 5. As shown in FIG.
10, each aberration is corrected excellently.
EXAMPLE 6
The basic lens data is shown below in Table 6.
TABLE-US-00006 TABLE 6 Example 6 Unit mm f = 2.50 ih = 3.26 Fno =
1.8 TTL = 3.92 .omega.(.degree.) = 52.3 Surface Data Surface
Curvature Surface Refractive Abbe Number i Radius r Distance d
Index Nd Number vd (Object) Infinity Infinity 1 (Stop) Infinity
-0.0300 2* 2.6952 0.4499 1.544 55.86 (vd1) 3* -500.0000 0.0992 4*
-236.5491 0.4213 1.535 55.66 (vd2) 5* -2.4152 0.3264 6* -0.7681
0.2000 1.661 20.37 (vd3) 7* -1.6067 0.0200 8* 7.8466 0.5631 1.544
55.86 (vd4) 9* -1.4775 0.0200 10* Infinity 0.2889 1.614 25.58 (vd5)
11* Infinity 0.1274 12* 0.9109 0.3914 1.535 55.66 (vd6) 13* 0.6369
0.5000 14 Infinity 0.2100 1.517 64.20 15 Infinity 0.3697 Image
Plane Infinity Constituent Lens Data Lens Start Surface Focal
Length 1 2 4.927 2 4 4.560 3 6 -2.461 4 8 2.334 5 10 Infinity 6 12
-7.879 Aspheric Surface Data Second Surface Third Surface Fourth
Surface Fifth Surface Sixth Surface Seventh Surface k -4.497389E+00
0.000000E+00 0.000000E+00 -6.219467E+00 -1.064692E+00 0.000000E+00
A4 -7.527715E-02 -2.220918E-01 -1.512366E-01 -1.504052E-01
7.168343E-02 -8.029630E-02 A6 2.319407E-02 -8.729089E-02
-2.817847E-01 1.138025E-02 -7.631071E-01 -3.797023E-01 A8
-2.762643E-01 -6.155922E-01 -1.869433E-01 -3.627602E-01
3.243245E+00 2.386234E+00 A10 0.000000E+00 7.070838E-01
-8.875539E-02 -4.029084E-01 -6.825057E+00 -4.836478E+00 A12
0.000000E+00 0.000000E+00 4.416396E-01 2.133227E+00 7.731701E+00
5.042076E+00 A14 0.000000E+00 0.000000E+00 0.000000E+00
-2.637456E+00 -4.665493E+00 -2.735304E+00 A16 0.000000E+00
0.000000E+00 0.000000E+00 1.077927E+00 1.329231E+00 6.183892E-01
A18 0.000000E+00 0.000000E+00 0.000000E+00 0.000000E+00
0.000000E+00 0.000000E+00 A20 0.000000E+00 0.000000E+00
0.000000E+00 0.000000E+00 0.000000E+00 0.000000E+00 Eighth Surface
Ninth Surface Tenth Surface Twelfth Surface Eleventh Surface
Thirteenth Surface k 3.360683E+01 -3.721259E+00 0.000000E+00
0.000000E+00 -1.879843E+00 -3.336148E+00 A4 -5.054708E-01
-1.270644E-01 9.605790E-01 1.288821E+00 -2.477514E-01 -1.049799E-01
A6 1.483371E+00 7.519021E-01 -1.791143E+00 -2.753188E+00
5.308238E-03 -6.111112E-02 A8 -2.528776E+00 -1.705370E+00
1.923993E+00 3.316318E+00 -1.109453E-01 9.174578E-02 A10
2.872815E+00 2.277352E+00 -1.501562E+00 -2.635934E+00 2.145576E-01
-4.378499E-02 A12 -2.285687E+00 -1.864225E+00 9.104191E-01
1.385387E+00 -1.394541E-01 1.103457E-02 A14 1.185696E+00
8.981698E-01 -4.468369E-01 -4.721497E-01 4.555319E-02 -1.582184E-03
A16 -3.492906E-01 -2.325064E-01 1.593117E-01 9.963342E-02
-8.136690E-03 1.219252E-04 A18 4.255337E-02 2.514587E-02
-3.468565E-02 -1.175503E-02 7.617190E-04 -3.933179E-06 A20
0.000000E+00 0.000000E+00 3.449503E-03 5.896842E-04 -2.935663E-05
1.801413E-09
The imaging lens in Example 6 satisfies conditional expressions (1)
to (17) as shown in Table 8.
FIG. 12 shows spherical aberration (mm), astigmatism (mm), and
distortion (%) of the imaging lens in Example 6. As shown in FIG.
12, each aberration is corrected excellently.
EXAMPLE 7
The basic lens data is shown below in Table 7.
TABLE-US-00007 TABLE 7 Example 7 Unit mm f = 2.81 ih = 3.26 Fno =
1.8 TTL = 4.25 .omega.(.degree.) = 50.0 Surface Data Surface
Curvature Surface Refractive Abbe Number i Radius r Distance d
Index Nd Number vd (Object) Infinity Infinity 1 (Stop) Infinity
-0.0325 2* 2.6482 0.4779 1.544 55.86 (vd1) 3* 21.3167 0.2448 4*
4.4669 0.4057 1.535 55.66 (vd2) 5* -26.3020 0.2268 6* -2.0213
0.3000 1.661 20.37 (vd3) 7* -13.4597 0.0208 8* -10.3341 0.4783
1.544 55.86 (vd4) 9* -2.0235 0.0200 10* Infinity 0.3600 1.661 20.37
(vd5) 11* Infinity 0.0264 12* 0.7824 0.4857 1.535 55.66 (vd6) 13*
0.6782 0.5000 14 Infinity 0.2100 1.517 64.20 15 Infinity 0.5669
Image Plane Infinity Constituent Lens Data Lens Start Surface Focal
Length 1 2 5.506 2 4 7.173 3 6 -3.638 4 8 4.531 5 10 Infinity 6 12
15.253 Aspheric Surface Data Second Surface Third Surface Fourth
Surface Fifth Surface Sixth Surface Seventh Surface k 2.472955E+00
0.000000E+00 -1.000000E+00 -9.999999E-01 -1.000000E+00 0.000000E+00
A4 -9.148951E-02 -1.626906E-01 -1.643676E-01 -1.499051E-01
-5.784550E-01 -- 2.334739E-02 A6 -1.003969E-02 -1.270262E-01
-1.405476E-02 -8.795773E-03 1.580392E+00 -2.640383E-02 A8
-1.175108E-01 6.505164E-02 -4.758153E-01 -5.995714E-01
-4.789919E+00 -1.621203E+00 A10 0.000000E+00 -2.950093E-02
3.913980E-01 6.759232E-01 9.854858E+00 4.023703E+00 A12
0.000000E+00 0.000000E+00 0.000000E+00 -1.271616E-01 -1.118269E+01
-3.926083E+00 A14 0.000000E+00 0.000000E+00 0.000000E+00
2.139518E-02 6.626144E+00 1.752123E+00 A16 0.000000E+00
0.000000E+00 0.000000E+00 -3.626468E-02 -1.604280E+00 -2.944286E-01
A18 0.000000E+00 0.000000E+00 0.000000E+00 0.000000E+00
0.000000E+00 0.000000E+00 A20 0.000000E+00 0.000000E+00
0.000000E+00 0.000000E+00 0.000000E+00 0.000000E+00 Eighth Surface
Ninth Surface Tenth Surface Eleventh Surface Twelfth Surface
Thirteenth Surface k -1.232784E+01 -3.360798E+01 0.000000E+00
0.000000E+00 -2.148448E+00 -2.508419E+00 A4 6.137630E-01
-2.488437E-01 7.583641E-01 5.726725E-01 -2.862441E-01 -2.262405E-01
A6 -1.040908E+00 1.208180E+00 -1.191706E+00 -7.104699E-01
4.475700E-02 1.007643E-01 A8 8.735916E-01 -1.912512E+00
1.064228E+00 4.208414E-01 1.595003E-02 -2.624835E-02 A10
-4.017928E-01 1.470622E+00 -6.563438E-01 -1.561038E-01
-5.046308E-03 3.943571E-03 A12 8.951159E-02 -6.019950E-01
2.467789E-01 3.653295E-02 2.044365E-04 -3.099407E-04 A14
-2.211894E-03 1.267435E-01 -4.839913E-02 -4.788211E-03 5.760857E-05
7.457861E-06 A16 -2.863722E-03 -1.088079E-02 3.723050E-03
2.605478E-04 -4.902575E-06 2.946515E-07 A18 0.000000E+00
0.000000E+00 0.000000E+00 0.000000E+00 0.000000E+00 0.000000E+00
A20 0.000000E+00 0.000000E+00 0.000000E+00 0.000000E+00
0.000000E+00 0.000000E+00
The imaging lens in Example 7 satisfies conditional expressions (1)
to (17) as shown in Table 8.
FIG. 14 shows spherical aberration (mm), astigmatism (mm), and
distortion (%) of the imaging lens in Example 7. As shown in FIG.
14, each aberration is corrected excellently.
In table 8, values of conditional expressions (1) to (17) related
to the Examples 1 to 7 are shown.
TABLE-US-00008 TABLE 8 Conditional Expression Example 1 Example 2
Example 3 Example 4 Example 5 Example 6 Example 7 (1) vd4 /vd5 2.18
2.18 2.18 2.18 2.18 2.18 2.74 (2) (T3/TTL)*100 0.63 0.49 0.51 0.51
0.51 0.51 0.49 (3) vd1/(vd2 + vd3) 0.73 0.73 0.73 0.73 0.73 0.73
0.73 (4) f1/f 2.51 2.34 2.32 1.97 2.01 1.97 1.96 (5) f2/f 1.20 1.42
1.45 1.84 1.79 1.82 2.56 (6) f3/f -0.99 -0.95 -1.07 -1.01 -0.99
-0.98 -1.30 (7) f4/f 1.31 1.18 1.03 0.96 0.93 0.93 1.61 (8) |f6|/f
12.47 14.96 2.83 3.08 3.10 3.15 5.43 (9) D6/.SIGMA.D 0.20 0.22 0.17
0.17 0.17 0.17 0.19 (10) .SIGMA.(L1F - L6R)/f 1.10 1.16 1.11 1.20
1.16 1.16 1.09 (11) r5/r 6 0.50 0.49 0.49 0.47 0.47 0.48 0.15 (12)
r11/f 0.40 0.38 0.39 0.37 0.36 0.36 0.28 (13) r12/f 0.32 0.30 0.27
0.25 0.25 0.25 0.24 (14) Fno 1.80 1.80 1.80 1.80 1.80 1.80 1.80
(15) f2/f4 0.92 1.20 1.42 1.91 1.93 1.95 1.58 (16) T3/T4 0.87 1.00
1.00 1.00 1.00 1.00 1.04 (17) (D5/TTL)*100 8.76 8.89 8.78 7.70 7.22
7.38 8.47
When the imaging lens according to the present invention is adopted
to a product with the camera function, there is realized
contribution to the low-profileness and the low F-number of the
camera and also high performance thereof.
DESCRIPTION OF REFERENCE NUMERALS
ST: aperture stop,
L1: first lens,
L2: second lens,
L3: third lens,
L4: fourth lens,
L5: fifth lens,
L6: sixth lens,
IMG: image plane,
IR: filter, and
ih: maximum image height.
* * * * *