U.S. patent number 10,429,975 [Application Number 15/742,774] was granted by the patent office on 2019-10-01 for touch panel, display device and manufacturing method of touch panel.
This patent grant is currently assigned to BOE TECHNOLOGY GROUP CO., LTD., HEFEI XINSHENG OPTOELECTRONICS TECHNOLOGY CO., LTD.. The grantee listed for this patent is BOE TECHNOLOGY GROUP CO., LTD., HEFEI XINSHENG OPTOELECTRONICS TECHNOLOGY CO., LTD.. Invention is credited to Xiaoyue He, Tsung Chieh Kuo, Qingpu Wang, Jiawei Xu, Lei Zhang.


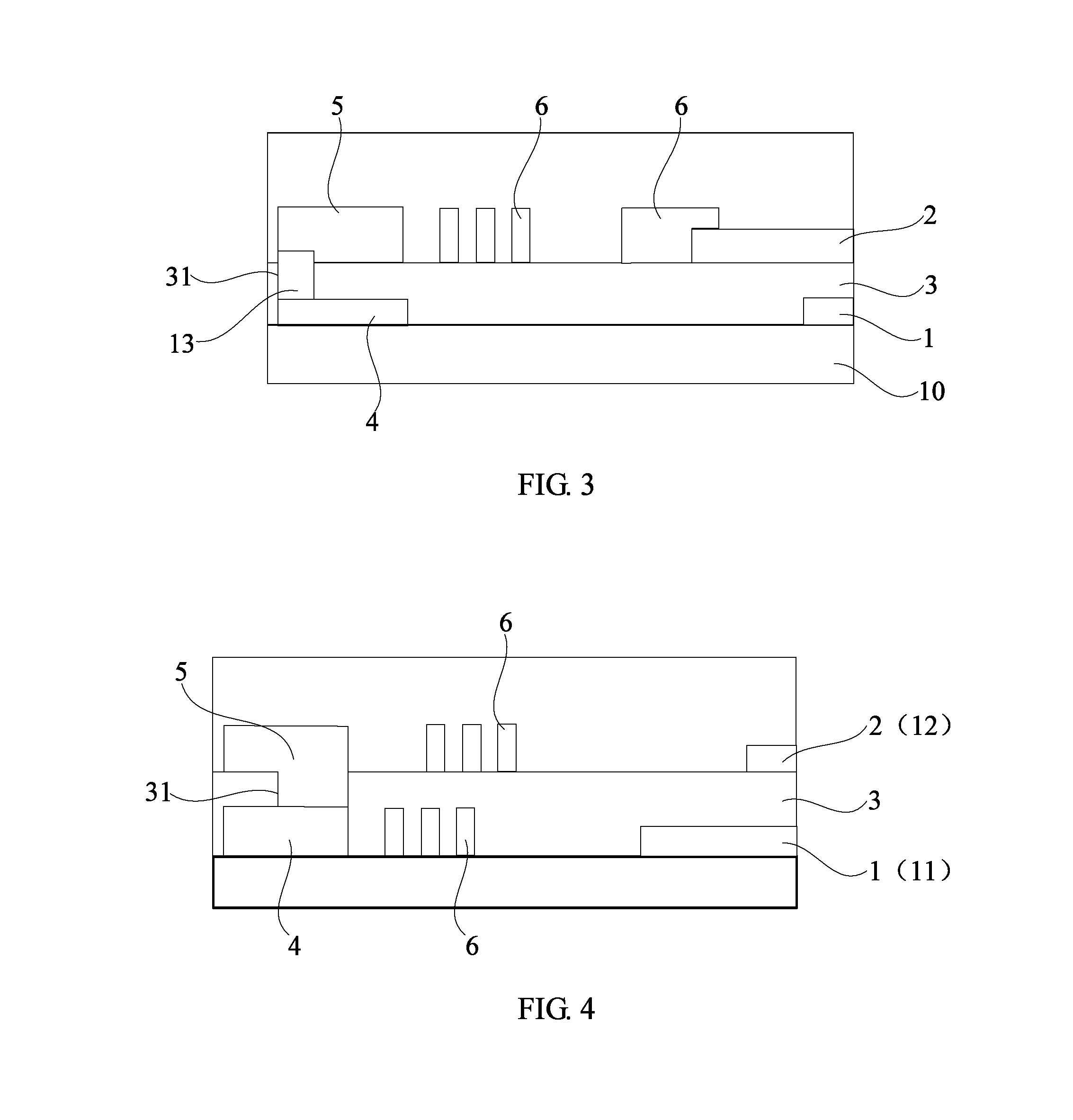

United States Patent |
10,429,975 |
Xu , et al. |
October 1, 2019 |
Touch panel, display device and manufacturing method of touch
panel
Abstract
A touch panel, a display device and a manufacturing method of
the touch panel are provided. The touch panel includes: a first
electrode layer and a second electrode layer configured to sense a
touch; an insulating layer located between the first electrode
layer and the second electrode layer; a first ground wire disposed
on a side of the insulating layer facing the first electrode layer;
and a second ground wire disposed on a side of the insulating layer
facing the second electrode layer. The first ground wire or the
second ground wire is electrically connected with a grounding
terminal. The insulating layer is provided with a ground wire vias
through which the first ground wire and the second ground wire are
electrically connected with each other.
Inventors: |
Xu; Jiawei (Beijing,
CN), Zhang; Lei (Beijing, CN), Kuo; Tsung
Chieh (Beijing, CN), Wang; Qingpu (Beijing,
CN), He; Xiaoyue (Beijing, CN) |
Applicant: |
Name |
City |
State |
Country |
Type |
BOE TECHNOLOGY GROUP CO., LTD.
HEFEI XINSHENG OPTOELECTRONICS TECHNOLOGY CO., LTD. |
Beijing
Hefei, Anhui |
N/A
N/A |
CN
CN |
|
|
Assignee: |
BOE TECHNOLOGY GROUP CO., LTD.
(Beijing, CN)
HEFEI XINSHENG OPTOELECTRONICS TECHNOLOGY CO., LTD. (Hefei,
Anhui, CN)
|
Family
ID: |
57791654 |
Appl.
No.: |
15/742,774 |
Filed: |
July 14, 2017 |
PCT
Filed: |
July 14, 2017 |
PCT No.: |
PCT/CN2017/092972 |
371(c)(1),(2),(4) Date: |
January 08, 2018 |
PCT
Pub. No.: |
WO2018/036301 |
PCT
Pub. Date: |
March 01, 2018 |
Prior Publication Data
|
|
|
|
Document
Identifier |
Publication Date |
|
US 20180373369 A1 |
Dec 27, 2018 |
|
Foreign Application Priority Data
|
|
|
|
|
Aug 25, 2016 [CN] |
|
|
2016 1 0725053 |
|
Current U.S.
Class: |
1/1 |
Current CPC
Class: |
G06F
3/0412 (20130101); G06F 3/044 (20130101); G06F
2203/04111 (20130101); G06F 2203/04107 (20130101); G06F
2203/04112 (20130101) |
Current International
Class: |
G06F
3/041 (20060101); G06F 3/044 (20060101) |
References Cited
[Referenced By]
U.S. Patent Documents
Foreign Patent Documents
|
|
|
|
|
|
|
103677461 |
|
Mar 2014 |
|
CN |
|
104391389 |
|
Mar 2015 |
|
CN |
|
204270269 |
|
Apr 2015 |
|
CN |
|
105824461 |
|
Aug 2016 |
|
CN |
|
106325601 |
|
Jan 2017 |
|
CN |
|
206133506 |
|
Apr 2017 |
|
CN |
|
Other References
International Search Report and Written Opinion dated Oct. 24,
2017; PCT/CN2017/092972. cited by applicant.
|
Primary Examiner: McLoone; Peter D
Claims
What is claimed is:
1. A touch panel, comprising, a first electrode layer and a second
electrode layer configured to sense touch and an insulating layer
located between the first electrode layer and the second electrode
layer; a first ground wire disposed on a side of the insulating
layer facing the first electrode layer, the first ground wire and
the first electrode layer being including same material and
provided in a same layer; and a second ground wire disposed on a
side of the insulating layer facing the second electrode layer, the
second ground wire and the second electrode layer including same
material and provided in a same layer; wherein the first ground
wire or the second ground wire are electrically connected with a
grounding terminal; and the insulating layer is provided with a
ground wire vias through which the first ground wire and the second
ground wire are electrically connected with each other.
2. The touch panel according to claim 1, further comprising, a
display area and a black matrix region surrounding the display
area; wherein the first electrode layer and the second electrode
layer are located in the display area; and the first ground wire
and the second ground wire are disposed along the black matrix
region.
3. The touch panel according to claim 2, wherein the first
electrode layer comprises a lateral touch electrode and a
longitudinal touch electrode; and the second electrode layer
comprises an electrode bridge point configured to bridge the
lateral touch electrode and the longitudinal touch electrode at an
intersection.
4. The touch panel according to claim 3, further comprising, a
metal wiring disposed on the side of the insulating layer facing
the first electrode layer and configured to electrically connect
the lateral touch electrode and the longitudinal touch electrode
with a driving chip.
5. The touch panel according to claim 2, wherein the first
electrode layer comprises a lateral touch electrode; and the second
electrode layer comprises a longitudinal touch electrode.
6. The touch panel according to claim 1, wherein the first
electrode layer includes a material which is indium tin oxide; and
the second electrode layer includes a material which is indium tin
oxide.
7. The touch panel according to claim 1, wherein the first
electrode layer comprises a lateral touch electrode and a
longitudinal touch electrode; and the second electrode layer
comprises an electrode bridge point configured to bridge the
lateral touch electrode and the longitudinal touch electrode at an
intersection.
8. A display device, comprising a touch panel, wherein the touch
panel comprises, a first electrode layer and a second electrode
layer configured to sense touch and an insulating layer located
between the first electrode layer and the second electrode layer; a
first ground wire disposed on a side of the insulating layer facing
the first electrode layer, the first ground wire and the first
electrode layer being including same material and provided in a
same layer; and a second ground wire disposed on a side of the
insulating layer facing the second electrode layer, the second
ground wire and the second electrode layer including same material
and provided in a same layer; wherein the first ground wire or the
second ground wire are electrically connected with a grounding
terminal; and the insulating layer is provided with a ground wire
vias through which the first ground wire and the second ground wire
are electrically connected with each other.
9. A manufacturing method of a touch panel, comprising: forming a
first electrode layer and a first ground wire by a same material in
a same layer on a substrate; forming an insulating layer on the
first electrode layer and the first ground wire, the insulating
layer being provided with a ground wire vias; and forming a second
electrode layer and a second ground wire on the insulating layer by
a same material in a same layer; wherein the first ground wire or
the second ground wire is electrically connected with a grounding
terminal, and the first ground wire and the second ground wire are
electrically connected with each other through the ground wire vias
of the insulating layer.
10. The manufacturing method of the touch panel according to claim
9, wherein the substrate comprises a display area and a black
matrix region surrounding the display area; wherein the first
electrode layer and the second electrode layer are formed in the
display area; and the first ground wire and the second ground wire
are formed in the black matrix region.
11. The manufacturing method of the touch panel according to claim
10, wherein the first electrode layer comprises a lateral touch
electrode and a longitudinal touch electrode; and the second
electrode layer comprises an electrode bridge point configured to
bridge the lateral touch electrode and the longitudinal touch
electrode at an intersection; the manufacturing method further
comprises: depositing a transparent electrode layer on the
substrate and forming patterns of the lateral touch electrode and
the longitudinal touch electrode by a patterning process;
depositing a metal layer on the substrate and forming patterns of
the first ground wire and the metal wiring by a patterning process,
wherein the metal wiring electrically connects the lateral touch
electrode and the longitudinal touch electrode with a driving chip;
and depositing a transparent electrode layer on the insulating
layer and forming patterns of the electrode bridge point and the
second ground wire by a patterning process.
12. The manufacturing method of the touch panel according to claim
10, wherein the second electrode layer comprises a lateral touch
electrode and a longitudinal touch electrode; the first electrode
layer comprises an electrode bridge point configured to bridge the
lateral touch electrode and the longitudinal touch electrode at an
intersection; the manufacturing method further comprises:
depositing a transparent electrode layer on the substrate and
forming patterns of the electrode bridge point and the first ground
wire by a patterning process; and depositing a transparent
electrode layer on the insulating layer and forming patterns of the
lateral touch electrode and the longitudinal touch electrode by a
patterning process; and depositing a metal layer on the insulating
layer and forming patterns of the second ground wire and the metal
wiring by a patterning process, wherein the metal wiring
electrically connects the lateral touch electrode and the
longitudinal touch electrode with a driving chip.
13. The manufacturing method of the touch panel according to claim
10, wherein the first electrode layer comprises a lateral touch
electrode and the second electrode layer comprises a longitudinal
touch electrode; the manufacturing method further comprises:
depositing a first electrode layer on the substrate and forming
patterns of the lateral touch electrode and the first ground wire
by a patterning process; and depositing a second electrode layer on
the insulating layer and forming patterns of the longitudinal touch
electrode and the second ground wire by a patterning process.
Description
CROSS REFERENCE TO RELATED APPLICATIONS
The present application claims priority of the Chinese patent
application No. 201610725053.9 titled "Touch panel, Display Device
and Manufacturing Method of Touch panel" filed with SIPO on Aug.
25, 2016, which is incorporated herein by reference in its
entirety.
TECHNICAL FIELD
Embodiments of the present disclosure relate to a touch panel, a
display device and a manufacturing method of the touch panel.
BACKGROUND
Touch panels are external input devices applied widely and
increasingly, which implements input by a simple touch by a finger
and allows the man-machine interaction process to be directly
performed, and has features of simple, fast and humanization.
SUMMARY
Embodiments of the present disclosure relates to a touch panel, a
display device, and a manufacturing method of the touch panel.
According to at least one embodiment of the present disclosure, a
touch panel is provided. The touch panel comprises: a first
electrode layer and a second electrode layer configured to sense a
touch and an insulating layer located between the first electrode
layer and the second electrode layer; a first ground wire disposed
on a side of the insulating layer facing the first electrode layer;
and a second ground wire disposed on a side of the insulating layer
facing the second electrode layer. The first ground wire or the
second ground wire is electrically connected with a grounding
terminal; and the insulating layer is provided with a ground wire
vias through which the first ground wire and the second ground wire
are electrically connected with each other.
For example, the touch panel also comprises: a display area and a
black matrix region surrounding the display area. The first
electrode layer and the second electrode layer are located in the
display area; and the first ground wire and the second ground wire
are disposed along the black matrix region.
For example, the first electrode layer comprises a lateral touch
electrode and a longitudinal touch electrode; and the second
electrode layer comprises an electrode bridge point configured to
bridge the lateral touch electrode and the longitudinal touch
electrode at an intersection.
For example, the touch panel also comprises: a metal wiring
disposed on the side of the insulating layer facing the first
electrode layer and configured to electrically connect the lateral
touch electrode and the longitudinal touch electrode with a driving
chip. The first ground wire and the metal wiring are disposed in a
same layer, and the first ground wire includes a material same as
that of the metal wiring.
For example, the second ground wire and the second electrode layer
are disposed in a same layer and the second ground wire includes a
material same as that of the second electrode layer.
For example, the material of the first electrode layer is indium
tin oxide; and the material of the second electrode layer is indium
tin oxide.
For example, the first electrode layer comprises a lateral touch
electrode; and the second electrode layer comprises a longitudinal
touch electrode.
For example, the first ground wire includes a material same as that
of the first electrode layer, and the first ground wire is disposed
in a same layer as the first electrode layer.
For example, the second ground wire includes a material same as
that of the second electrode layer, and the second ground wire and
the second electrode layer are disposed in a same layer.
According to embodiments of the present disclosure, a display
device is provided, comprising the touch panel.
According to embodiments of the present disclosure, a manufacturing
method of a touch panel is provided, comprising: forming a first
electrode layer and a first ground wire on a substrate; forming an
insulating layer on the first electrode layer and the first ground
wire, the insulating layer being provided with a ground wire vias;
and forming a second electrode layer and a second ground wire on
the insulating layer. The first ground wire, or the second ground
wire is electrically connected with a grounding terminal, and the
first ground wire and the second ground wire are electrically
connected with each other through the ground wire vias of the
insulating layer.
For example, the substrate comprises a display area and a black
matrix region surrounding the display area. The first electrode
layer and the second electrode layer are formed in the display
area; and the first ground wire and the second ground wire are
formed in the black matrix region.
For example, the first electrode layer comprises a lateral touch
electrode and a longitudinal touch electrode; and the second
electrode layer comprises an electrode bridge point configured to
bridge the lateral touch electrode and the longitudinal touch
electrode at an intersection. The manufacturing method also
comprises: depositing a transparent electrode layer on the
substrate and forming patterns of the lateral touch electrode and
the longitudinal touch electrode by a patterning process;
depositing a metal layer on the substrate and forming patterns of
the first ground wire and the metal wiring by a patterning process.
The metal wiring electrically connects the lateral touch electrode
and the longitudinal touch electrode with a driving chip. The
manufacturing method also comprises depositing a transparent
electrode layer on the insulating layer and forming patterns of the
electrode bridge point and the second ground wire by a patterning
process.
For example, the second electrode layer comprises a lateral touch
electrode and a longitudinal touch electrode; and the first
electrode layer comprises an electrode bridge point configured to
bridge the lateral touch electrode and the longitudinal touch
electrode at an intersection. The manufacturing method also
comprises: depositing a transparent electrode layer on the
substrate and forming patterns of the electrode bridge point and
the first ground wire by a patterning process. The manufacturing
method also comprises: depositing a transparent electrode layer on
the insulating layer and forming patterns of the lateral touch
electrode and the longitudinal touch electrode by a patterning
process; and depositing a metal layer on the insulating layer and
forming patterns of the second ground wire and the metal wiring by
a patterning process. The metal wiring electrically connects the
lateral touch electrode and the longitudinal touch electrode with a
driving chip.
For example, the first electrode layer comprises a lateral touch
electrode, and the second electrode layer comprises a longitudinal
touch electrode. The manufacturing method also comprises:
depositing a first electrode layer on the substrate and forming
patterns of the lateral touch electrode and the first ground wire
by a patterning process; and depositing a second electrode layer on
the insulating layer and forming patterns of the longitudinal touch
electrode and the second ground wire by a patterning process.
BRIEF DESCRIPTION OF THE DRAWINGS
Embodiments of the present disclosure will be described in more
detail below with reference to accompanying drawings to allow an
ordinary skill in the art to more clearly understand embodiments of
the present disclosure, in which:
FIG. 1 is a schematically structural diagram of a touch panel
provided in an embodiment of the present disclosure;
FIG. 2 is a part of a schematically structural view of a touch
panel provided in an embodiment of the present disclosure;
FIG. 3 is a part of a schematically structural view of a touch
panel provided in another embodiment of the present disclosure;
FIG. 4 is a part of a schematically structural view of a touch
panel provided in yet another embodiment of the present disclosure;
and
FIG. 5 is a flow chart of a method for manufacturing a touch panel
provided in an embodiment of the present disclosure.
DETAILED DESCRIPTION
Technical solutions of the embodiments will be described in a
clearly and fully understandable way in connection with the
drawings related to the embodiments of the disclosure. It is
apparent that the described embodiments are just a part but not all
of the embodiments of the disclosure. Based on the described
embodiments herein, those skilled in the art can obtain other
embodiment(s), without any creative work, which shall be within the
scope of the disclosure.
The inventors noticed that the touch panels suffer more and more
the electrostatic (ESD) affect with the extension of application
fields of touch panels and the popularity of large size touch
panels. For example, the touch panels in the art have no effective
protection ways against the generation of the inductive
electrostatic and releasing of electrostatic accumulation during
the manufacturing process, structures, such as sensing electrodes,
and metal wirings in touch panels, are susceptible to poor
electrostatic induction. And the light blocking structure in the
black matrix region in the touch panels in the art consists of
carbon wrapped in resin layer, when electrostatic induction
currents are generated in metal wirings or sensing electrode paths
of the black matrix region, the resin layer of the light blocking
structure tends to be electrically broken down such that the light
blocking structure forms a conducting path, resulting in problems,
such as higher analog-to-digital converter (ADC) on electrical side
edge, and short circuiting between the transmitting electrode and
the receiving electrode (Tx&Rx short).
As shown in FIGS. 1-4, a touch panel provided in an embodiment of
the present disclosure includes a first electrode layer 1 and a
second electrode layer 2 for sensing touch, and an insulating layer
3 located between the first electrode layer 1 and the second
electrode layer 2. The touch panel also includes a first ground
wire 4 disposed on a side of the insulating layer 3 facing the
first electrode layer 1 and a second ground wire 5 disposed on a
side of the insulating layer 3 facing the second electrode layer 2.
The first ground wire 4 is electrically connected with the
grounding terminal and/or the second ground wire 5 is electrically
connected with the grounding terminal. The insulating layer 3 is
provided with a ground wire vias 31 through which the first ground
wire 4 and the second ground wire 5 are electrically connected with
each other.
In the touch panel, the first ground wire 4 and the second ground
wire 5 are respectively disposed in the two layers of electrode
layer (the first electrode layer 1 and the second electrode layer
2) structure for touch sensing, and the first ground wire 4 and/or
the second ground wire 5 are electrically connected with the
grounding terminal. The first ground wire 4 and the second ground
wire 5 can serve as an electrostatic shielding for the two
electrode layers to avoid interference from external charges. In
addition, the first ground wire 4 and the second ground wire 5 can
conduct static electricity generated in the two electrode layers
out in time to avoid poor sensing of touch due to electrostatic
accumulation and releasing. In this way, the touch panel can avoid
poor yield due to electrostatic (ESD).
As shown in FIG. 1, in an exemplary embodiment, the touch panel may
include a display area and a black matrix region surrounding the
display area. The first electrode layer 1 and second electrode
layer 2 are located in the display area, and the first ground wire
4 and second ground wire 5 are arranged along the black matrix
region. For example, the first ground wire 4 and second ground wire
5 may be strip structures extending along the black matrix
region.
The first ground wire 4 and the second ground wire 5 extend along
the black matrix region, that is, the first ground wire 4 and the
second ground wire 5 enclose the first electrode layer 1 and the
second electrode layer 2 such that the first ground wire 4 and the
second ground wire 5 may effectively shield the first electrode
layer 1 and the second electrode layer 2. In this way, it is
possible to effectively avoid interference to the first electrode
layer 1 and the second electrode layer 2 by external charges.
Furthermore, the first ground wire 4 and the second ground wire 5
may conduct static electricity generated around the first electrode
layer 1 and the second electrode layer 2 out in time, which can
effectively avoid electrostatic accumulation and effectively avoid
poor sensing of touch due to electrostatic discharge. In addition,
the first ground wire 4 and the second ground wire 5 are disposed
along the black matrix region, so that they are not likely to
contact and short with the first electrode layer 1 and the second
electrode layer 2, and will not affect the display area due to
light blocking, for example.
In embodiment I, as shown in FIGS. 1 and 2, the touch panel may be
an OGS (One Glass Solution) structure. For example, in the touch
panel of the present embodiment, the first electrode layer 1 may
include a lateral touch electrode 11 and a longitudinal touch
electrode 12; and the second electrode layer 2 may include an
electrode bridge point 21 configured to bridge the lateral touch
electrode 11 and the longitudinal touch electrode 12 at their
intersection. As shown in FIG. 1, the electrode bridge point 21 may
be a bridging structure disposed at the intersection and configured
to connect the longitudinal touch electrode 12.
As shown in FIG. 1 and FIG. 2, in an example, in the touch panel,
both of materials of the first electrode layer 1 and the second
electrode layer 2 are a transparent electrode material. For
example, both the first electrode layer 1 and the second electrode
layer 2 are an indium tin oxide (ITO) material layer.
As shown in FIG. 1 and FIG. 2, in an example, the touch panel may
also include a metal wiring 6 disposed on a side of the insulating
layer 3 facing the first electrode layer 1 and configured to
electrically connect the lateral touch electrode 11 and the
longitudinal touch electrode 12 with the driving chip 7.
As shown in FIG. 2, for example, the first ground wire 4 may be
disposed in the same layer as the metal wiring 6, and the material
of the first ground wire 4 may be the same as that of the metal
wiring 6. The first ground wire 4 and the metal wiring 6 may be
prepared in a same patterning process, which can simplify the
manufacturing process of the touch panel.
As shown in FIG. 1, for example, the first ground wire 4 may be
electrically connected with the driving chip 7, so as to be
electrically connected with the grounding terminal.
As shown in FIG. 2, in an example, the second ground wire 5 may be
disposed in a same layer as the second electrode layer 2, and the
material of the second ground wire 5 may also be the same as that
of the second electrode layer 2. The second ground wire 5 and the
second electrode layer 2 may be prepared in a same patterning
process, and the manufacturing process of the touch panel can be
simplified.
In the embodiment II, as shown in FIG. 4, in the touch panel of the
present embodiment, the first electrode layer 1 may include a
lateral touch electrode 11; and the second electrode layer 2 may
include a longitudinal touch electrode 12.
As shown in FIG. 4, in an example, the touch panel may be a metal
mesh structure. For example, both of the materials of the first
electrode layer 1 and the second electrode layer 2 are a metal, and
the lateral touch electrode 11 and the longitudinal touch electrode
12 are metal mesh electrodes.
As shown in FIG. 4, in an example, the material of the first ground
wire 4 may be the same as that of the first electrode layer 1, and
the first ground wire 4 may be disposed in the same layer as the
first electrode layer 1. The first ground wire 4 and the first
electrode layer 1 may be prepared in a same patterning process, and
the manufacturing process of the touch panel can be simplified.
For example, the material of the second ground wire 5 may be the
same as that of the second electrode layer 2, and the second ground
wire 5 may be disposed in a same layer as the second electrode
layer 2. The second ground wire 5 and the second electrode layer 2
may be prepared in a same patterning process, and the manufacturing
process of the touch panel can be simplified.
As shown in FIG. 4, in another example, both of the materials of
the first electrode layer 1 and the second electrode layer 2 may be
a transparent electrode material. For example, both the lateral
touch electrode 11 and the longitudinal touch electrode 12 may be
an ITO electrode.
As shown in FIG. 4, in an example, the material of the first ground
wire 4 may the same as that of the metal wiring of the lateral
touch electrode 11 and disposed in a same layer as the metal
wiring. The material of the second ground wire 5 may be the same as
that of the metal wiring of the longitudinal touch electrode and
disposed in a same layer as the metal wiring.
For example, in the lateral touch electrode 11 and the longitudinal
touch electrode 12 in the various embodiments, it is possible that
the lateral touch electrode 11 is the transmitting electrode, and
the longitudinal touch electrode 12 is the sensing electrode; or
the lateral touch electrode 11 is the sensing electrode and the
longitudinal touch electrode 12 is the transmitting electrode.
An embodiment of the present disclosure also provides a display
device that includes the touch panel in any one of the embodiments.
The touch panel in the display device in the embodiment of the
present disclosure may avoid defectiveness due to electrostatic
(ESD) effect, in this way, the display device in the embodiment of
the present disclosure has better touch sensing performance and
higher reliability.
An embodiment of the present disclosure also provides a
manufacturing method for a touch panel, as shown in FIG. 5 in
conjunction with FIGS. 1-4, which includes steps of: step S101,
forming a first electrode layer 1 and a first ground wire 4 on a
substrate 10; step S102, forming an insulating layer 3 on the first
electrode layer 1 and the first ground wire 4, the insulating layer
3 being provided with a ground wire vias 31; and step S103, forming
a second electrode layer 2 and a second ground wire 5 on the
insulating layer 3.
The first ground wire 4 is electrically connected with the
grounding terminal; or the second ground wire 5 is electrically
connected with the grounding terminal; or the first ground wire 4
and the second ground wire 5 are electrically connected through the
ground wire vias 31 of the insulating layer 3.
In the touch panel formed by the manufacturing method, the first
ground wire 4 and the second ground wire 5 are disposed in the two
layers of the electrode layer (the first electrode layer 1 and the
second electrode layer 2) structure for touch sensing,
respectively, and the first ground wire 4 and the second ground
wire 5 are both electrically connected with the grounding terminal.
In this way, the first ground wire 4 and the second ground wire 5
may serve as an electrostatic shield for the two electrode layers
to avoid interference from external charges. In addition, the first
ground wire 4 and the second ground wire 5 may conduct static
electricity generated in the two electrode layers out in time to
avoid poor touch sensing due to electrostatic accumulation and
releasing. In this way, the touch panel may avoid defectiveness due
to electrostatic (ESD) effect.
Referring to FIG. 1, in an example, the touch panel may include a
display area and a black matrix region surrounding the display
area. The first electrode layer 1 and the second electrode layer 2
are located in the display area. The first ground wire 4 and the
second ground wire 5 are disposed along the black matrix region.
For example, the first ground wire 4 and second ground wire 5 can
be strip structures extending along the black matrix region.
The first ground wire 4 and the second ground wire 5 extend along
the black matrix region, that is, the first ground wire 4 and the
second ground wire 5 enclose the first electrode layer 1 and the
second electrode layer 2, such that the first ground wire 4 and the
second ground wire 5 may effectively shield the first electrode
layer 1 and the second electrode layer 2 in which way it is
possible to effectively avoid interference with the first electrode
layer 1 and the second electrode layer 2 by external charges.
Furthermore, the first ground wire 4 and the second ground wire 5
may conduct static electricity generated around the first electrode
layer 1 and the second electrode layer 2 out in time, which
effectively avoid electrostatic accumulation and may effectively
avoid poor sensing of touch due to electrostatic discharge. In
addition, the first ground wire 4 and the second ground wire 5 are
disposed along the black matrix region, in this way, they are not
likely to contact and short with the first electrode layer 1 and
the second electrode layer 2, and will not affect the display area
due to light blocking, for example.
In embodiment I, as shown in FIGS. 1 and 2, in the touch panel
formed by the manufacturing method of the present embodiment, the
first electrode layer 1 includes a lateral touch electrode 11 and a
longitudinal touch electrode 12; and the second electrode layer 2
includes an electrode bridge point 21 configured to bridge the
lateral touch electrode 11 and the longitudinal touch electrode 12
at the intersection. As shown in FIG. 1, the electrode bridge point
12 may be a bridging structure disposed at the intersection and
configured to connect the longitudinal touch electrodes 12.
As shown in FIGS. 1, 2 and 5, in an example, in the manufacturing
method of the touch panel, step S101, namely the step of forming
the first electrode layer 1 and the first ground wire 4 on the
substrate 10 may comprise: for example, depositing a transparent
electrode layer, such as ITO layer, on the substrate 10, and
forming patterns of the lateral touch electrode 11 and the
longitudinal touch electrode 12 by a patterning process; and
depositing a metal layer on the substrate 10, and forming patterns
of the first ground wire 4 and the metal wiring 6 by a patterning
process. The metal wiring 6 electrically connects the lateral touch
electrode 11 and the longitudinal touch electrode 12 with the
driving chip 7, respectively.
For example, the first ground wire 4 is electrically connected with
the driving chip 7, which realizes the electrical connection with
the grounding terminal.
The step S102, namely the step of forming the second electrode
layer 2 and the second ground wire 5 on the insulating layer 10 may
include: for example, depositing a transparent electrode layer,
such as ITO layer, on the insulating layer 3, and forming patterns
of the electrode bridge point 21 and the second ground wire 5 by a
patterning process.
In the manufacturing method of the touch panel in the present
embodiment, the first ground wire 4, and metal wirings 6 of the
sensing electrodes (the lateral touch electrode 11 and the
longitudinal touch electrode 12) are formed by a same patterning
process; and the second ground wire 5, and the second electrode
layer 2 are formed by a same patterning process. In this way, no
additional process steps need to be added for the preparing process
of the first ground wire 4 and the second ground wire 5. In this
way, the manufacturing process of the manufacturing method of the
touch panel is simplified.
In embodiment 11, as shown in FIGS. 1 and 3, in the touch panel
formed by the manufacturing method of the present embodiment, the
second electrode layer 2 includes a lateral touch electrode 11 and
a longitudinal touch electrode 12; and the first electrode layer 1
includes an electrode bridge point 21 configured to bridge the
lateral touch electrode 11 and the longitudinal touch electrode 12
at the intersection.
As shown in FIGS. 1, 3 and 5, in an example, in the manufacturing
method of the touch panel of the present embodiment, step S101,
namely the step of forming the first electrode layer 1 and the
first ground wire 4 on the substrate 10 may comprise: for example,
depositing a transparent electrode layer, such as ITO layer, on the
substrate 10, and forming patterns of the electrode bridge point 21
and the first ground wire 4 by a patterning process.
The step S102, namely the step of forming the second electrode
layer 2 and the second ground wire 5 on the insulating layer 3 may
include: for example, depositing a transparent electrode layer,
such as ITO layer, on the insulating layer 3, and forming patterns
of the lateral touch electrode 11 and the longitudinal touch
electrode 12 by a patterning process; and depositing a metal layer
on the insulating layer 3, and forming patterns of the second
ground wire 5 and the metal wiring 6 by a patterning process. The
metal wiring 6 electrically connects the lateral touch electrode 11
and the longitudinal touch electrode 12 with the driving chip
7.
For example, the second ground wire 5 is electrically connected
with the driving chip 7, which realizes the electrical connection
with the grounding terminal.
For example, as shown in FIG. 3, the process of patterning the
transparent electrode layer to form patterns of the lateral touch
electrodes 11 and the longitudinal touch electrodes 12 may
simultaneously form the lapping section 13 in the ground wire vias
31 of the insulating layer 3. The lapping section 13 is
electrically connected with the first ground wire 4 through the
ground wire vias 31. In this way, it is possible to implement the
electrical connection between the first ground wire 4 and the
second ground wire 5 by connecting the second ground wire 5 on the
insulating layer 3 with the lapping section 13.
In the manufacturing method of the touch panel in the present
embodiment, the first ground wire 4 and the first electrode layer 1
are formed by a same patterning process, and the second ground wire
5 and metal wirings 6 of the sensing electrodes (the lateral touch
electrode 11 and the longitudinal touch electrode 12) are formed by
a same patterning process. In this way, no additional process steps
need to be added for the preparing process of the first ground wire
4 and the second ground wire 5. The manufacturing process of the
manufacturing method of the touch panel is simplified.
In embodiment III, as shown in FIGS. 4 and 5, in the touch panel
formed by the manufacturing method of the present embodiment, the
first electrode layer 1 includes a lateral touch electrode 11; and
the second electrode layer 2 includes a longitudinal touch
electrode 12.
As shown in FIGS. 4 and 5, in an example, in the manufacturing
method of the touch panel, step S101, namely the step of forming
the first electrode layer 1 and the first ground wire 4 on the
substrate 10 may comprise: for example, depositing an electrode
layer on the substrate 10, and forming patterns of the lateral
touch electrode 11 and the first ground wire 4 by a patterning
process. For example, the electrode layer may be a metal layer. For
example, the lateral touch electrode 11 is a metal mesh electrode.
The electrode layer may also be a transparent electrode layer. For
example, the lateral touch electrode 11 may be an ITO
electrode.
The step S102, namely the step of forming the second electrode
layer 2 and the second ground wire 5 on the insulating layer 3 may
include: for example, depositing an electrode layer on the
insulating layer 3, and forming patterns of the longitudinal touch
electrode 12 and the second ground wire 5 by a patterning process.
For example, the electrode layer may be a metal layer. For example,
the longitudinal touch electrode 12 is a metal mesh electrode. The
electrode layer may be a transparent electrode layer. For example,
the longitudinal touch electrode 12 may be an ITO electrode.
It is to be noted that the embodiments are only illustrations of
the touch panel manufacturing method of the embodiment of the
present disclosure, and the manufacturing method of the embodiments
of the present disclosure is not limited to the embodiments.
The described above are only exemplary embodiments of the present
disclosure, and the present disclosure is not intended to be
limited thereto. For one of ordinary skill in the art, various
changes and alternations may be readily contemplated without
departing from the technical scope of the present disclosure, and
all of these changes and alternations shall fall within the scope
of the present disclosure.
* * * * *