U.S. patent number 10,385,717 [Application Number 15/291,650] was granted by the patent office on 2019-08-20 for multi-ply seal.
This patent grant is currently assigned to United Technologies Corporation. The grantee listed for this patent is United Technologies Corporation. Invention is credited to Nathan K. Galle.
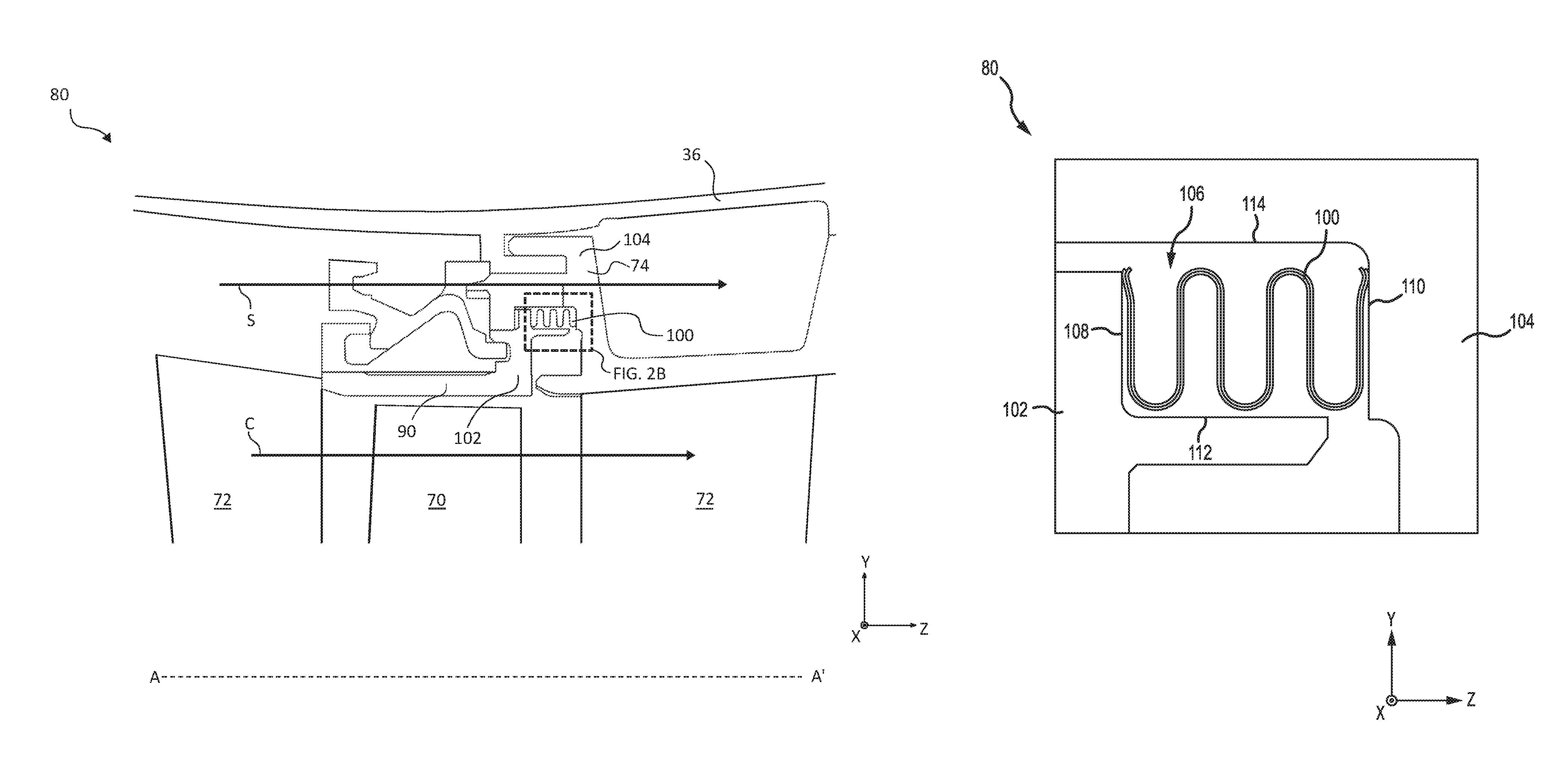




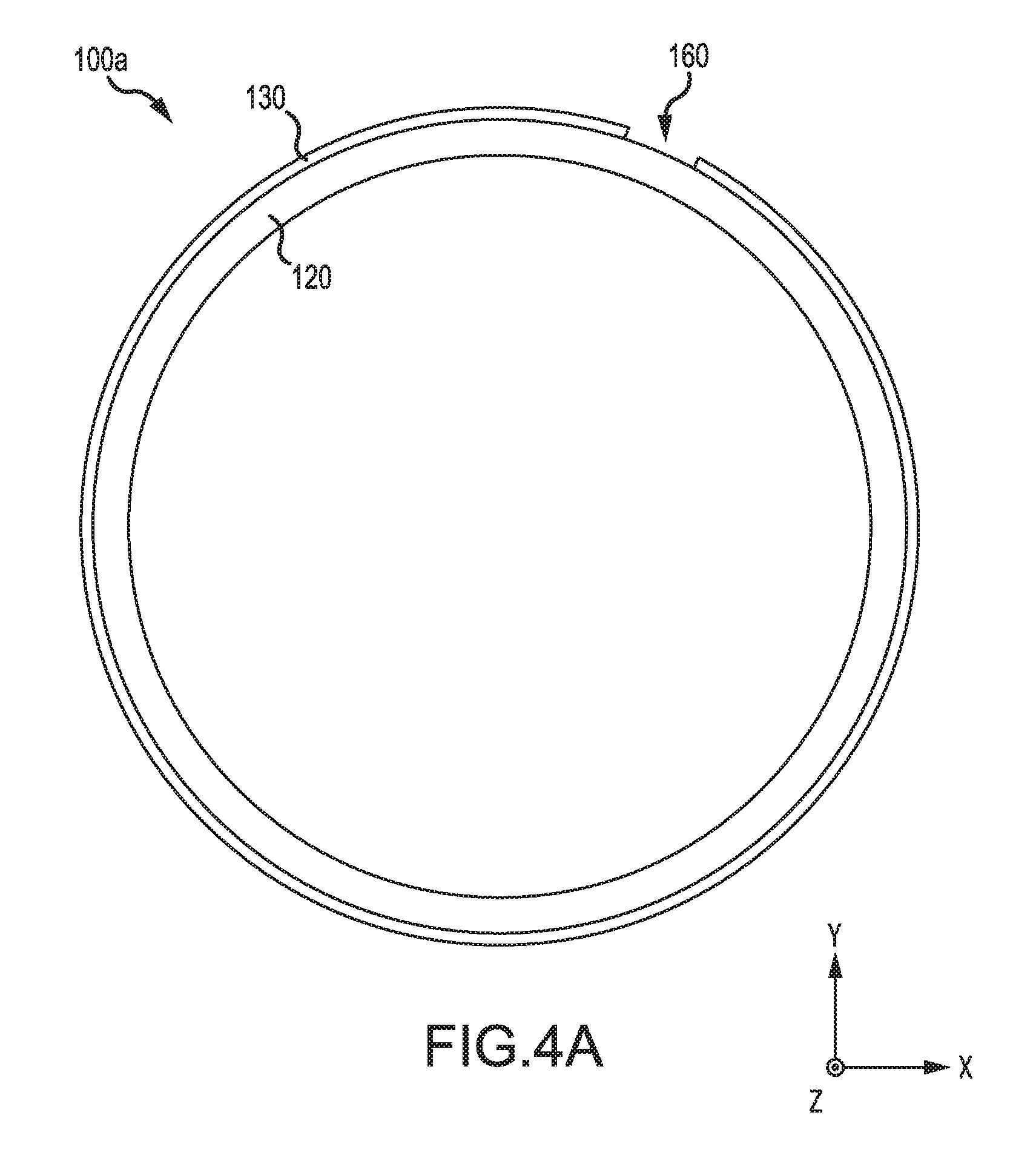
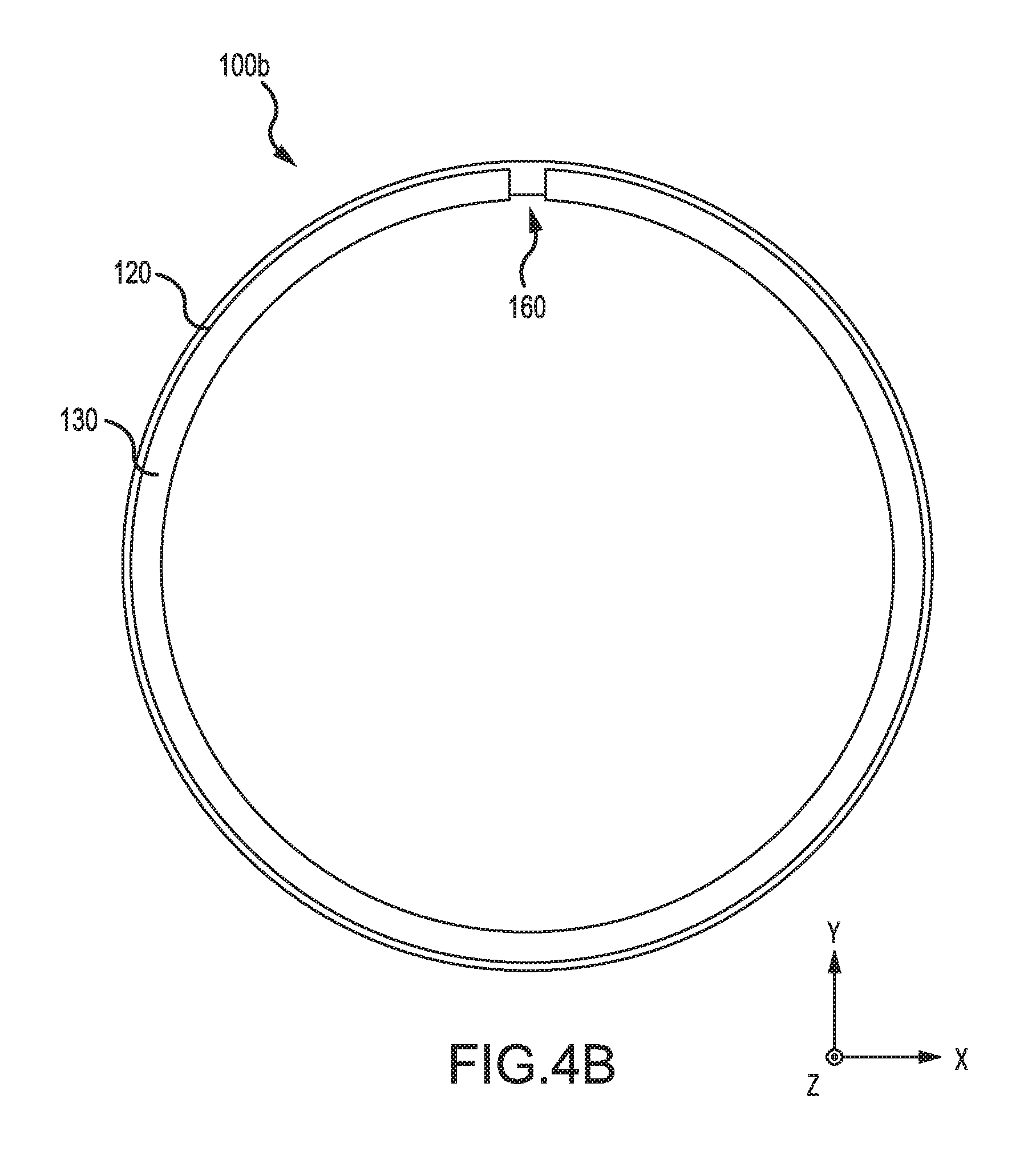
United States Patent |
10,385,717 |
Galle |
August 20, 2019 |
Multi-ply seal
Abstract
A seal may comprise a first ply including an annular shape and a
second ply including a discontinuous annular shape having an axial
split. The second ply may be positioned adjacent to a surface of
the first ply.
Inventors: |
Galle; Nathan K. (Portland,
OR) |
Applicant: |
Name |
City |
State |
Country |
Type |
United Technologies Corporation |
Farmington |
CT |
US |
|
|
Assignee: |
United Technologies Corporation
(Farmington, CT)
|
Family
ID: |
59974219 |
Appl.
No.: |
15/291,650 |
Filed: |
October 12, 2016 |
Prior Publication Data
|
|
|
|
Document
Identifier |
Publication Date |
|
US 20180100406 A1 |
Apr 12, 2018 |
|
Current U.S.
Class: |
1/1 |
Current CPC
Class: |
F04D
29/164 (20130101); F01D 11/08 (20130101); F16J
15/0887 (20130101); F01D 9/02 (20130101); F04D
29/542 (20130101); F01D 11/005 (20130101); F05D
2300/177 (20130101); F05D 2220/32 (20130101); F05D
2250/75 (20130101); F01D 25/246 (20130101); F05D
2240/11 (20130101); F05D 2250/183 (20130101) |
Current International
Class: |
F01D
11/08 (20060101); F01D 11/00 (20060101); F01D
9/02 (20060101); F04D 29/54 (20060101); F04D
29/16 (20060101); F16J 15/08 (20060101); F01D
25/24 (20060101) |
References Cited
[Referenced By]
U.S. Patent Documents
Foreign Patent Documents
|
|
|
|
|
|
|
2949874 |
|
Dec 2015 |
|
EP |
|
3051071 |
|
Aug 2016 |
|
EP |
|
3211181 |
|
Aug 2017 |
|
EP |
|
3246534 |
|
Nov 2017 |
|
EP |
|
3252275 |
|
Dec 2017 |
|
EP |
|
Other References
Nickel Alloy 600. Datasheet [online]. Aircraft Materials UK, Sep.
2016 [retrieved on Aug. 2, 2018]. Retrieved from the Internet:
<URL:
https://www.aircraftmaterials.com/data/nickel/600.html>. cited
by examiner .
Nickel Superalloy Waspaloy. Datasheet [online]. Aircraft Materials
UK, Sep. 2016 [retrieved on Aug. 2, 2018]. Retrieved from the
Internet: <URL:
https://www.aircraftmaterials.com/data/nickel/waspaloy.html>.
cited by examiner .
Hardness Conversion Chart. Datasheet [online]. Carbide Depot, Inc,
Apr. 2001 [retrieved on Aug. 2, 2018]. Retrieved from the Internet:
<URL: http://www.carbidedepot.com/formulas-hardness.htm>.
cited by examiner .
Nickel Alloy 600. Datasheet [online]. Aircraft Materials UK, Sep.
2016 [retrieved on Aug. 2, 2018]. Retrieved from the Internet:
<URL:
https://www.aircraftmaterials.com/data/nickel/600.html>. (Year:
2016). cited by examiner .
Nickel Superalloy Waspaloy. Datasheet [online]. Aircraft Materials
UK, Sep. 2016 [retrieved on Aug. 2, 2018]. Retrieved from the
Internet: <URL:
https://www.aircraftmaterials.com/data/nickel/waspaloy.html>.
(Year: 2016). cited by examiner .
Hardness Conversion Chart. Datasheet [online]. Carbide Depot, Inc,
Apr. 2001 [retrieved on Aug. 2, 2018]. Retrieved from the Internet:
<URL: http://www.carbidedepot.com/formulas-hardness.htm>.
(Year: 2001). cited by examiner .
European Patent Office, European Search Report dated Feb. 21, 2018
in Application No. 17193438.3-1006. cited by applicant .
Merriam-Webster Incorporated et al: 11 11 Adjacent11 : definition
and synonyms11 1s Collegiateln: 11 Merriam-Webster Dictionary:
Eleventh Edition11 , Jul. 30, 2013 (Jul. 30, 2013),
Merriam-Webster, Incorporated, Springfield, MA , USA, XP055450688,
ISBN: 978-0-87779-807-1 pp. 16-16, * left-hand column, paragraph 10
*. cited by applicant.
|
Primary Examiner: White; Dwayne J
Assistant Examiner: Gillenwaters; Jackson N
Attorney, Agent or Firm: Snell & Wilmer, L.L.P.
Claims
What is claimed is:
1. A seal, comprising: a first ply having a circumferentially
continuous annular shape; a second ply having a circumferentially
discontinuous annular shape including an axial split, the second
ply positioned directly adjacent to at least one of an inner
diameter surface or an outer diameter surface of the first ply; and
a third ply positioned adjacent to at least one of the first ply or
the second ply, the third ply having a circumferentially
discontinuous annular shape.
2. The seal of claim 1, wherein the first ply and the second ply
comprise a "W" seal.
3. The seal of claim 2, wherein the second ply is nested within the
first ply with an inner diameter surface of the second ply in
contact with the outer diameter surface of the firstply.
4. The seal of claim 1, wherein the first ply comprises a first
sheet metal and the second ply comprises a second sheet metal.
5. The seal of claim 1, wherein the first ply is comprised of a
first material and the second ply is comprised of a second
material, and wherein at least one of the first material or the
second material comprises a nickel-based alloy.
6. The seal of claim 5, wherein the first material and the second
material comprise the same material.
7. An engine section of a gas turbine engine, comprising: a first
engine component; a second engine component disposed adjacent to
the first engine component; and a seal disposed between the first
engine component and the second engine component, the seal
comprising: a first ply having a circumferentially continuous
annular shape, a second ply having a circumferentially
discontinuous annular shape including an axial split, the second
ply positioned directly adjacent to at least one of an inner
diameter surface or an outer diameter surface of the first ply; and
a third ply positioned adjacent to at least one of the first ply or
the second ply, the third ply having a circumferentially
discontinuous annular shape.
8. The engine section of claim 7, wherein the first ply and the
second ply comprise a "W" seal.
9. The engine section of claim 8, wherein the second ply is nested
within the first ply with an inner diameter surface of the second
ply in contact with the outer diameter surface of the first
ply.
10. The engine section of claim 7, wherein the second ply is
mechanically loaded against the at least one of an inner diameter
surface or an outer diameter surface of the first ply.
11. The engine section of claim 7, wherein the first ply is
comprised of a first material and the second ply is comprised of a
second material, and wherein at least one of the first material or
the second material comprises a nickel-based alloy.
12. The engine section of claim 11, wherein the first material and
the second material comprise the same material.
13. The engine section of claim 11, wherein the second material has
a greaterwear resistance than the first material.
14. The engine section of claim 7, wherein the first ply comprises
a first sheet metal and the second ply comprises a second sheet
metal.
15. A gas turbine engine, comprising: an engine section comprising
at least one of a compressor section or a turbine section, the
engine section comprising: a blade outer air seal, a vane adjacent
to the blade outer air seal, and a seal disposed between the blade
outer air seal and the vane, the seal comprising: a first ply
having a circumferentially continuous annular shape; a second ply
having a circumferentially discontinuous annular shape including an
axial split, the second ply positioned directly adjacent to at
least one of an inner diameter surface or an outer diameter surface
of the first ply; and a third ply positioned adjacent to at least
one of the first ply or the second ply, the third ply having a
circumferentially discontinuous annular shape.
16. The gas turbine engine of claim 15, wherein the first ply and
the second ply comprise a "W" seal.
17. The gas turbine engine of claim 16, wherein the second ply is
nested within the first ply with an inner diameter surface of the
second ply in contact with the outer diameter surface of the first
ply.
18. The gas turbine engine of claim 17, wherein the second ply is
mechanically loaded against the outer diameter surface of the first
ply.
19. The gas turbine engine of claim 15, wherein the first ply is
comprised of a first material and the second ply is comprised of a
second material and wherein at least one of the first material or
the second material comprises a nickel-based alloy.
Description
FIELD
The present disclosure relates to seals and, more specifically, to
seals for gas turbine engines.
BACKGROUND
A gas turbine engine typically includes a fan section, a compressor
section, a combustor section, and a turbine section. Air moves into
the engine through the fan section. Airfoil arrays in the
compressor section rotate to compress the air, which is then mixed
with fuel and combusted in the combustor section. The products of
combustion are expanded to rotatably drive airfoil arrays in the
turbine section. Rotating the airfoil arrays in the turbine section
drives rotation of the fan and compressor sections. The compressor
section and turbine section each have multiple stages of blades
that rotate about a central axis and multiple stages of vanes that
are stationary relative to the central axis.
Gas turbine engines may have various gas-flow streams that may be
kept separate from one another. The gas-flow streams may be
separated by various components. The internal engine environment is
exposed to temperature and pressure extremes and other harsh
environmental conditions, which may affect the integrity of the
components separating different gas-flow streams. Higher pressure
gaspath air may tend to leak between airfoil arrays into lower
pressure gaspaths. Seals may be included between the components to
minimize leakage. Seal degradation may contribute to loss of
performance and/or efficiency of the gas turbine engine.
SUMMARY
A seal for gas turbine engine is described herein, in accordance
with various embodiments. A seal may comprise a first ply having an
annular shape and a second ply including a second ply having a
circumferentially discontinuous annular shape including an axial
split. The second ply may be positioned directly adjacent to at
least one of an inner diameter surface or an outer diameter surface
of the first ply.
In various embodiments, the first ply and the second ply comprise a
"W" seal. The second ply may be nested within the first ply with an
inner diameter surface of the second ply in contact with the
surface of the first ply. A third ply may be positioned adjacent to
at least one of the first ply or the second ply. The third ply may
have a circumferentially discontinuous annular shape. The first ply
may comprise a first sheet metal and the second ply may comprise a
second sheet metal. The first ply may be comprised of a first
material and the second ply may be comprised of a second material.
At least one of the first material or the second material may
comprise a nickel-based alloy. The first material and the second
material may comprise the same material.
An engine section of a gas turbine engine is also provided. The
engine section may comprise a first engine component and a second
engine component disposed adjacent to the first engine component. A
seal disposed between the first engine component and the second
engine component. The seal may comprise a first ply having an
annular shape. The seal may further comprise a second ply having
circumferentially discontinuous annular shape including an axial
split. The second ply may be positioned directly adjacent to at
least one of an inner diameter surface or an outer diameter surface
of the first ply.
In various embodiments, the first ply and the second ply comprise a
"W" seal. The second ply may be nested within the first ply with an
inner diameter surface of the second ply in contact with the
surface of the first ply. The second ply may be mechanically loaded
against the surface of the first ply. The first ply may be
comprised of a first material and the second ply may be comprised
of a second material. The first material and the second material
may comprise the same material. At least one of the first material
or the second material may comprise a nickel-based alloy. The
second material may have a greater wear resistance than the first
material. The first ply may comprise a first sheet metal and the
second ply may comprise a second sheet metal.
A gas turbine engine is also provided. The gas turbine engine may
comprise an engine section comprising at least one of a compressor
section or a turbine section. The engine section may comprise a
blade outer air seal and a vane adjacent to the blade outer air
seal. A seal may be disposed between the blade outer air seal and
the vane. The seal may comprise a first ply having an annular
shape. The seal may further comprise a second ply having
circumferentially discontinuous annular shape including an axial
split. The second ply may be positioned directly adjacent to at
least one of an inner diameter surface or an outer diameter surface
of the first ply.
In various embodiments, the first ply and the second ply comprise a
"W" seal. The second ply may be nested within the first ply with an
inner diameter surface of the second ply in contact with the
surface of the first ply. The second ply may be mechanically loaded
against the surface of the first ply. The first ply may be
comprised of a first material and the second ply may be comprised
of a second material. At least one of the first material or the
second material may comprise a nickel-based alloy.
The foregoing features and elements may be combined in various
combinations without exclusivity, unless expressly indicated
otherwise. These features and elements as well as the operation
thereof will become more apparent in light of the following
description and the accompanying drawings. It should be understood,
however, the following description and drawings are intended to be
exemplary in nature and non-limiting.
BRIEF DESCRIPTION OF THE DRAWINGS
The subject matter of the present disclosure is particularly
pointed out and distinctly claimed in the concluding portion of the
specification. A more complete understanding of the present
disclosure, however, may best be obtained by referring to the
detailed description and claims when considered in connection with
the figures, wherein like numerals denote like elements.
FIG. 1 illustrates a schematic cross-section of a gas turbine
engine, in accordance with various embodiments;
FIG. 2A illustrates a schematic cross-section of an engine section
of the gas turbine engine of FIG. 1, in accordance with various
embodiments;
FIG. 2B illustrate an enlarged view of the engine section with a
seal between engine components, in accordance with various
embodiments;
FIGS. 3A and 3B illustrate a cross-sectional view of seal
configurations, in accordance with various embodiments; and
FIGS. 4A and 4B illustrate an axial view of seal configurations, in
accordance with various embodiments.
DETAILED DESCRIPTION
All ranges and ratio limits disclosed herein may be combined. It is
to be understood that unless specifically stated otherwise,
references to "a," "an," and/or "the" may include one or more than
one and that reference to an item in the singular may also include
the item in the plural.
The detailed description of various embodiments herein makes
reference to the accompanying drawings, which show various
embodiments by way of illustration. While these various embodiments
are described in sufficient detail to enable those skilled in the
art to practice the disclosure, it should be understood that other
embodiments may be realized and that logical, chemical, and
mechanical changes may be made without departing from the spirit
and scope of the disclosure. Thus, the detailed description herein
is presented for purposes of illustration only and not of
limitation. For example, the steps recited in any of the method or
process descriptions may be executed in any order and are not
necessarily limited to the order presented. Furthermore, any
reference to singular includes plural embodiments, and any
reference to more than one component or step may include a singular
embodiment or step. Also, any reference to attached, fixed,
connected, or the like may include permanent, removable, temporary,
partial, full, and/or any other possible attachment option.
Additionally, any reference to without contact (or similar phrases)
may also include reduced contact or minimal contact. Cross hatching
lines may be used throughout the figures to denote different parts
but not necessarily to denote the same or different materials.
As used herein, "aft" refers to the direction associated with the
tail (e.g., the back end) of an aircraft, or generally, to the
direction of exhaust of the gas turbine engine. As used herein,
"forward" refers to the direction associated with the nose (e.g.,
the front end) of an aircraft, or generally, to the direction of
flight or motion.
As used herein, "distal" refers to the direction radially outward,
or generally, away from the axis of rotation of a turbine engine.
As used herein, "proximal" refers to a direction radially inward,
or generally, towards the axis of rotation of a turbine engine.
In various embodiments and with reference to FIG. 1, a gas turbine
engine 20 is provided. Gas turbine engine 20 may be a two-spool
turbofan that generally incorporates a fan section 22, a compressor
section 24, a combustor section 26 and a turbine section 28.
Alternative engines may include, for example, an augmentor section
among other systems or features. In operation, fan section 22 can
drive coolant (e.g., air) along a bypass flow-path B while
compressor section 24 can drive coolant along a core flow-path C
for compression and communication into combustor section 26 then
expansion through turbine section 28. Although depicted as a
turbofan gas turbine engine 20 herein, it should be understood that
the concepts described herein are not limited to use with turbofans
as the teachings may be applied to other types of turbine engines
including three-spool architectures.
Gas turbine engine 20 may generally comprise a low speed spool 30
and a high speed spool 32 mounted for rotation about an engine
central longitudinal axis A-A' relative to an engine static
structure 36 or engine case via several bearing systems 38, 38-1,
and 38-2. Engine central longitudinal axis A-A' is oriented in the
z direction on the provided xyz axis. It should be understood that
various bearing systems 38 at various locations may alternatively
or additionally be provided, including for example, bearing system
38, bearing system 38-1, and bearing system 38-2.
Low speed spool 30 may generally comprise an inner shaft 40 that
interconnects a fan 42, a low pressure compressor 44 and a low
pressure turbine 46. Inner shaft 40 may be connected to fan 42
through a geared architecture 48 that can drive fan 42 at a lower
speed than low speed spool 30. Geared architecture 48 may comprise
a gear assembly 60 enclosed within a gear housing 62. Gear assembly
60 couples inner shaft 40 to a rotating fan structure. High speed
spool 32 may comprise an outer shaft 50 that interconnects a high
pressure compressor 52 and high pressure turbine 54. A combustor 56
may be located between high pressure compressor 52 and high
pressure turbine 54. A mid-turbine frame 57 of engine static
structure 36 may be located generally between high pressure turbine
54 and low pressure turbine 46. Mid-turbine frame 57 may support
one or more bearing systems 38 in turbine section 28. Inner shaft
40 and outer shaft 50 may be concentric and rotate via bearing
systems 38 about the engine central longitudinal axis A-A', which
is collinear with their longitudinal axes. As used herein, a "high
pressure" compressor or turbine experiences a higher pressure than
a corresponding "low pressure" compressor or turbine.
The core airflow C may be compressed by low pressure compressor 44
then high pressure compressor 52, mixed and burned with fuel in
combustor 56, then expanded over high pressure turbine 54 and low
pressure turbine 46. Turbines 46, 54 rotationally drive the
respective low speed spool 30 and high speed spool 32 in response
to the expansion.
Gas turbine engine 20 may be, for example, a high-bypass ratio
geared aircraft engine. In various embodiments, the bypass ratio of
gas turbine engine 20 may be greater than about six (6). In various
embodiments, the bypass ratio of gas turbine engine 20 may be
greater than ten (10). In various embodiments, geared architecture
48 may be an epicyclic gear train, such as a star gear system (sun
gear in meshing engagement with a plurality of star gears supported
by a carrier and in meshing engagement with a ring gear) or other
gear system. Geared architecture 48 may have a gear reduction ratio
of greater than about 2.3 and low pressure turbine 46 may have a
pressure ratio that is greater than about five (5). In various
embodiments, the bypass ratio of gas turbine engine 20 is greater
than about ten (10:1). In various embodiments, the diameter of fan
42 may be significantly larger than that of the low pressure
compressor 44, and the low pressure turbine 46 may have a pressure
ratio that is greater than about five (5:1). Low pressure turbine
46 pressure ratio may be measured prior to inlet of low pressure
turbine 46 as related to the pressure at the outlet of low pressure
turbine 46 prior to an exhaust nozzle. It should be understood,
however, that the above parameters are exemplary of various
embodiments of a suitable geared architecture engine and that the
present disclosure contemplates other gas turbine engines including
direct drive turbofans. A gas turbine engine may comprise an
industrial gas turbine (IGT) or a geared aircraft engine, such as a
geared turbofan, or non-geared aircraft engine, such as a turbofan,
or may comprise any gas turbine engine as desired.
Referring now to FIG. 1 and to FIG. 2A, according to various
embodiments, each of low pressure compressor 44, high pressure
compressor 52, low pressure turbine 46, and high pressure turbine
54 in gas turbine engine 20 may comprise one or more stages or sets
of rotating blades ("rotors blades") and one or more stages or sets
of stationary vanes ("stator vanes") axially interspersed with the
associated blade stages but non-rotating about engine central
longitudinal axis A-A'. Each compressor stage and turbine stage may
comprise multiple interspersed stages of blades 70 and vanes 72.
The blades 70 rotate about engine central longitudinal axis A-A',
while the vanes 72 remain stationary about engine central
longitudinal axis A-A'. For example, FIG. 2A schematically shows,
by example, a portion of an engine section 80, which is illustrated
as a turbine section 28 of gas turbine engine 20.
With reference to FIG. 2A, a portion of engine section 80 is
illustrated, in accordance with various embodiments. Engine section
80 may include a circumferential array of blades 70 configured to
rotate about engine central longitudinal axis A-A'. Upstream
(forward) and downstream (aft) of blade 70 is a circumferential
arrays of vanes 72 configured to guide core airflow C flow through
the engine section 80. Vane 72 may include an outer diameter
platform 74 coupled to engine case structure 36. Outer diameter
platform 74 may be coupled to or integral with vane 72.
In various embodiments, engine section 80 may include stationary
annular fluid seals, referred to as a blade outer air seal (BOAS)
assembly, circumscribing the blades 70 and defining a radially
outward boundary of core airflow path C. A BOAS assembly may
include one or more BOAS segments 90 circumferentially arranged to
form an annular ring about engine central longitudinal axis A-A'
radially outward of blades 70. BOAS segments 90 may be disposed
axially adjacent with respect to vanes 72. During engine operation,
vanes 72 and BOAS segments 90 are subjected to different thermal
loads and environmental conditions. Cooling air may be provided to
BOAS segment 90 and vanes 72 to enable operation of the turbine
during exposure to hot combustion gasses produced within the
combustion area, as described above. Pressurized air may be
diverted from other engine sections as a secondary airflow S and
used to cool components within engine section 80. A BOAS segment 90
and vanes 72 may define an inner diameter boundary of secondary
airflow S, and engine case structure 36 may define an outer
diameter boundary of secondary airflow S. Secondary airflow S may
have a higher pressure than core airflow C. A difference in
pressure of secondary airflow S may typically be about 100 to 200
pounds per square inch (psi), or 689 to 1379 kilopascals (kPa),
greater than core airflow C, producing a tendency for secondary
airflow S to leak into core airflow C. One or more seals 100 may
therefore be incorporated between stages of BOAS segment 90 and
vanes 72 to reduce leakage of cooling air from secondary airflow S
into core airflow C. Seal 100 may comprise an annular seal disposed
between BOAS segment 90 and vane 72.
With reference to FIG. 2B, a portion of an engine section 80 having
a seal 100 is shown, in accordance with various embodiments. Seal
100 may be disposed between adjacent engine components, such as a
first engine component 102 and a second engine component 104. The
first engine component 102 and second engine component 104 may
comprise any stationary or rotating engine component. For example,
the first engine component 102 may include a BOAS segment 90 and
the second engine component 104 may include a vane 72 or outer
diameter platform 74 (see FIG. 2A). First engine component 102 and
second engine component 104 may be define a cavity 106
therebetween.
In various embodiments, at least a portion of seal 100 may include
a continuous annular ring extending circumferentially within cavity
106 around of engine section 80. Cavity 106 may expand and contract
(axially and/or radially) in response to the thermal and/or
mechanical environment of engine section 80. With a continuous ring
portion, seal 100 provides a hoop stiffness, which may reduce the
loading of seal 100 against a surface 112 at the inner diameter of
seal 100 or against a surface 114 at the outer diameter of seal
100. Seal 100 may be disposed within cavity 106 and may generally
be free-floating within cavity 106. Seal 100 may be a "W" seal
(e.g. a seal having a "W"-shaped cross-section or that form a "W"
shape). A "W" seal may be flexible enough axially to expand and
seal against the walls of first engine component 102 and a second
engine component. Seal 100 may be biased outwardly along engine
central longitudinal axis A-A' to contact aft surface 108 of first
engine component 102 and forward surface 110 of second engine
component 104. The "W" shape may enable seal 100 to compress and
extend as first engine component 102 moves relative to second
engine component 104 in response to thermally driven deformations
and pressure loads. Thus, seal 100 prevents or reduces leakage
airflow passing through cavity 106.
With reference to FIG. 3A, a cross-section of seal 100 is shown, in
accordance with various embodiments. Seal 100 may include two or
more layers or plies of material, such as first ply 120 and second
ply 130. Second ply 130 may be positioned directly adjacent to
first ply 120 and may be generally in contact with first ply 120.
In various embodiments, second ply 130 may be nested within first
ply 120 and at least a portion of first ply 120 may be in contact
with second ply 130. An inner diameter surface 132 of second ply
130 may be in contact with an outer diameter surface 124 of first
ply 120. Seal 100 may include a full hoop portion that extends
circumferentially within engine section 80. In various embodiments,
first ply 120 may be a full hoop and second ply 130 may be a split
hoop. As a split hoop, second ply 130 may be easily coupled with
first ply 120. Second ply 130 may be mechanically loaded against an
outer diameter surface 124 of first ply 120. In various
embodiments, second ply 130 may be positioned with an outer
diameter surface 134 of second ply 130 directly adjacent to an
inner diameter surface 122 of first ply 120. In various
embodiments, seal 100 comprises one or more layers or plies in
addition to first ply 120 and second ply 130, such as a third ply
150 as illustrated, for example, by seal 152 in FIG. 3B. First ply
120 may be formed as a separate component from second ply 130 and
as a separate component from additional plies, such as third ply
150. Seal 100 may be subsequently assembled by positioning second
ply 130 adjacent to and nested with first ply 120.
With reference to FIG. 3B, a cross-section of seal 152 is shown, in
accordance with various embodiments. Seal 152 may include multiple
layers or plies of material, such as first ply 120, second ply 130
and third ply 150. Third ply 150 may be positioned directly
adjacent to at least one of first ply 120 and second ply 130. Third
ply 150 may have a circumferentially discontinuous annular
shape.
With reference to FIGS. 3A and 3B, multi-ply seals 100, 152 may
include various quantities of plies. Although discussed in terms of
seal 100 having two plies, it will be understood that the present
disclosure is applicable to seals having additional plies. In
various embodiments, the plies, such as first ply 120 and second
ply 130 of seal 100 and/or third ply 150 of seal 152, may be
manufactured from sheet metal, such as titanium, titanium-based
alloy, nickel, nickel-based alloy, aluminum, aluminum-based alloy,
steel, stainless steel or other materials, which may be formed and
folded into a serpentine shape including one or more legs 140
defined by one or more bends 142. For example, seal 100 may have a
shape that resembles a "W." First ply 120 may be manufactured
separately from second ply 130. First ply 120 may comprise a first
portion of a sheet metal and second ply 130 may comprise a second
portion of a sheet metal, wherein the first portion of the sheet
metal and the second portion of the sheet metal are separate
portions of sheet metal. First ply 120 may have a first thickness
T1 and second ply 130 may have a second thickness T2. Each of first
thickness T1 and second thickness T2 may be between 0.001 inch
(0.0254 millimeters (mm)) and 0.01 inch (0.254 mm), between 0.003
inch (0.076 mm) and 0.010 inch (0.254 mm), and more specifically,
between 0.003 inch (0.076 mm) and 0.006 inch (0.15 mm).
Seal 100 may include a metal, such as titanium, titanium-based
alloy, nickel, nickel-based alloy, aluminum, aluminum-based alloy,
steel, or stainless steel, or other materials. First ply 120 may
include a first material and second ply 130 may include a second
material. In various embodiments, first ply 120 may include the
same material as second ply 130 and, in various embodiments, first
ply 120 may include a different material than second ply 130. For
example, first ply 120 may include a material having a lower
coefficient of thermal expansion (CTE) relative to a material of
second ply 130. The materials of first ply 120 and second ply 130
may be configured according to the operating conditions of the
surrounding environment. For example, in engine section 80 (see
FIG. 2A), first ply 120 having a full hoop configuration may
comprise the inner diameter of seal 100 and may include a material
capable of withstanding higher temperatures relative to second ply
130. Second ply 130 having a split hoop configuration may comprise
an outer diameter of seal 100 and may include a material having
greater wear resistance, strength, and/or spring stiffness. Thus,
the materials of first ply 120 and second ply 130 may be selected
to optimize the sealing effectiveness and wear resistance of seal
100.
With reference to FIGS. 4A and 4B, a front axial view of seal
configurations are shown in accordance with various embodiments. In
various embodiments, seal 100 may be annular or ring shaped. First
ply 120 may be circumferentially continuous, and second ply 130 may
be split, or circumferentially discontinuous. Stated differently,
first ply 120 may include an annular shape, and second ply may
include a circumferentially discontinuous annular shape having an
axial split, shown by opening 160. FIG. 4A shows a configuration of
seal 100a with second ply 130 disposed at an outer diameter of
first ply 120. Second ply 130 may be bias fit onto the outer
diameter surface of first ply 120. FIG. 4B shows a configuration of
seal 100b with second ply 130 disposed at an inner diameter of
first ply 120. Second ply 130 may be bias fit onto the inner
diameter surface of first ply 120. Second ply 130 may be a split
ring, an expanding ring, an interlocking split ring, or the like.
In various embodiments, second ply 130 may be a discontinuous ring,
which is split at an opening 160. Opening 160 may be defined by an
axial split in second ply 130 extending from a first axial end 136
to a second axial end 138 of second ply 130 (see FIG. 3A). Opening
160 may extend completely through second ply 130 and may allow
second ply 130 to expand and contract. Opening 160 may provide for
ease of installation onto first ply 120 and may provide for a bias
fit or snap fit. As a full hoop, first ply 120 provides support for
second ply 130. Thus, seal 100 may be installed within an engine
section that does not have a platform or a radial surface (for
example, surface 112 in FIG. 2B) for supporting a seal.
Returning to FIG. 2B, seal 100 may include a full hoop portion,
first ply 120, and a split hoop portion, second ply 130. By loading
second ply 130 against first ply 120, which has a hoop stiffness,
first ply 120 provides structural support for seal 100. Thus, first
ply 120 and second ply 130 may not load radially inward or radially
outward against an engine component, thereby reducing contact of
the inner diameter and outer diameter of seal 100 with surfaces
112, 114. Reducing such contact results in less wear to seal 100,
and thus, extends the operational life of seal 100.
Benefits and other advantages have been described herein with
regard to specific embodiments. Furthermore, the connecting lines
shown in the various figures contained herein are intended to
represent exemplary functional relationships and/or physical
couplings between the various elements. It should be noted that
many alternative or additional functional relationships or physical
connections may be present in a practical system. However, the
benefits, advantages, and any elements that may cause any benefit
or advantage to occur or become more pronounced are not to be
construed as critical, required, or essential features or elements
of the disclosure. The scope of the disclosure is accordingly to be
limited by nothing other than the appended claims, in which
reference to an element in the singular is not intended to mean
"one and only one" unless explicitly so stated, but rather "one or
more." Moreover, where a phrase similar to "at least one of A, B,
or C" is used in the claims, it is intended that the phrase be
interpreted to mean that A alone may be present in an embodiment, B
alone may be present in an embodiment, C alone may be present in an
embodiment, or that any combination of the elements A, B and C may
be present in a single embodiment; for example, A and B, A and C, B
and C, or A and B and C.
Systems, methods and apparatus are provided herein. In the detailed
description herein, references to "various embodiments", "one
embodiment", "an embodiment", "an example embodiment", etc.,
indicate that the embodiment described may include a particular
feature, structure, or characteristic, but every embodiment may not
necessarily include the particular feature, structure, or
characteristic. Moreover, such phrases are not necessarily
referring to the same embodiment. Further, when a particular
feature, structure, or characteristic is described in connection
with an embodiment, it is submitted that it is within the knowledge
of one skilled in the art to affect such feature, structure, or
characteristic in connection with other embodiments whether or not
explicitly described. After reading the description, it will be
apparent to one skilled in the relevant art(s) how to implement the
disclosure in alternative embodiments.
Furthermore, no element, component, or method step in the present
disclosure is intended to be dedicated to the public regardless of
whether the element, component, or method step is explicitly
recited in the claims. No claim element is intended to invoke 35
U.S.C. 112(f) unless the element is expressly recited using the
phrase "means for." As used herein, the terms "comprises",
"comprising", or any other variation thereof, are intended to cover
a non-exclusive inclusion, such that a process, method, article, or
apparatus that comprises a list of elements does not include only
those elements but may include other elements not expressly listed
or inherent to such process, method, article, or apparatus.
* * * * *
References