U.S. patent number 10,300,617 [Application Number 15/503,987] was granted by the patent office on 2019-05-28 for cutting tool and manufacturing method.
This patent grant is currently assigned to Fiskars Finland Oy Ab. The grantee listed for this patent is Fiskars Finland Oy Ab. Invention is credited to Heikki Savolainen.


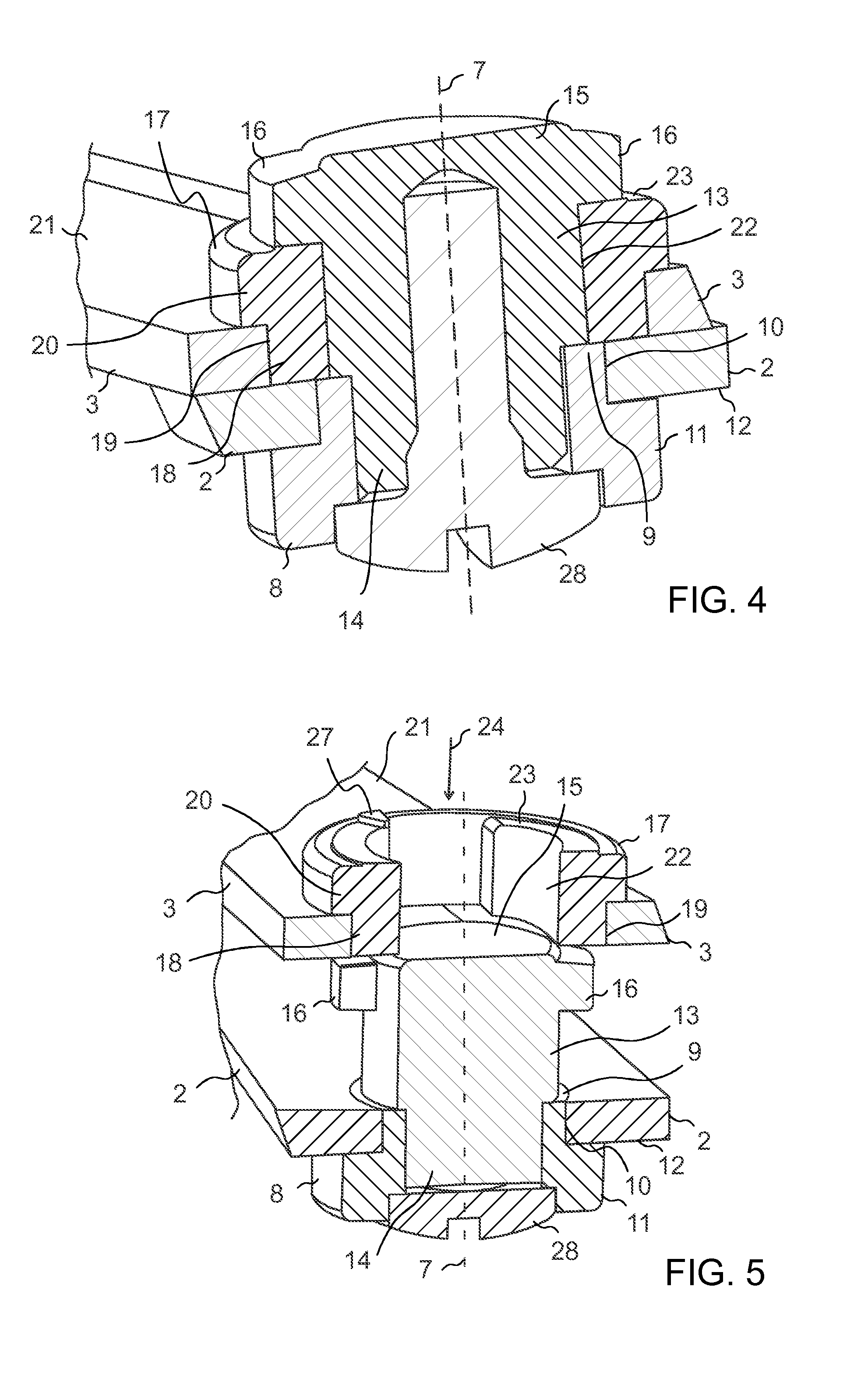
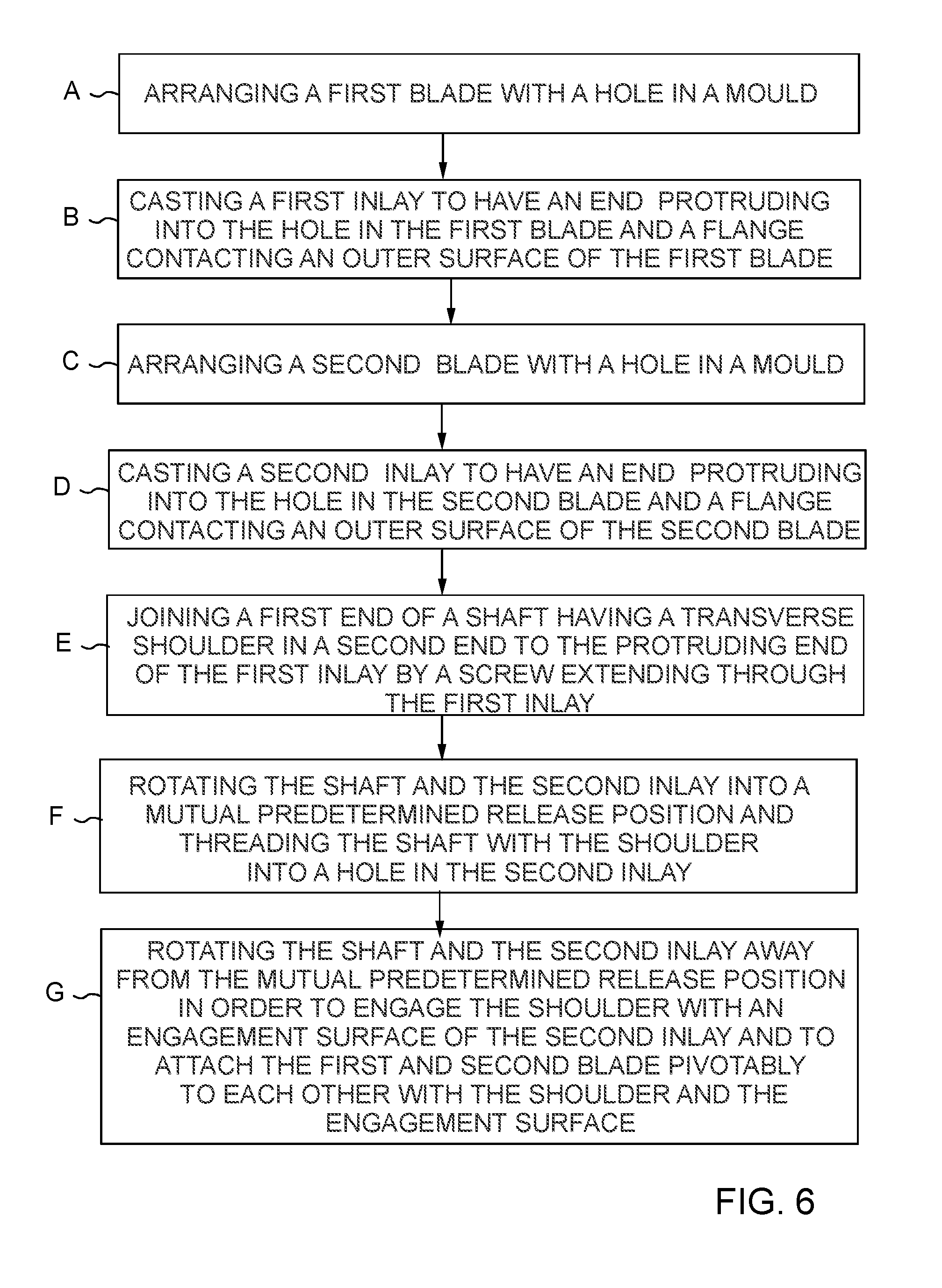
United States Patent |
10,300,617 |
Savolainen |
May 28, 2019 |
Cutting tool and manufacturing method
Abstract
A cutting tool includes first and second blades attached to each
other by a joint, and first and second handles. A first inlay
having a protruding end protrudes into a hole in the first blade. A
shaft has a first end joined to the protruding end of the first
inlay, and has a second end with at least one transverse shoulder.
A second inlay has a protruding end protruding into a hole in the
second blade and a hole receives the second end of the shaft, and
an engaging surface engages with the shoulder of the shaft. The
hole of the second inlay has a shape and width allowing the second
end of the shaft with the shoulder to pass into the hole in a
release position, but prevents the shaft and shoulder from passing
through the hole when the shaft and second inlay are not in the
release position.
Inventors: |
Savolainen; Heikki (Helsinki,
FI) |
Applicant: |
Name |
City |
State |
Country |
Type |
Fiskars Finland Oy Ab |
Helsinki |
N/A |
FI |
|
|
Assignee: |
Fiskars Finland Oy Ab
(Helsinki, FI)
|
Family
ID: |
53520167 |
Appl.
No.: |
15/503,987 |
Filed: |
August 26, 2015 |
PCT
Filed: |
August 26, 2015 |
PCT No.: |
PCT/FI2015/050547 |
371(c)(1),(2),(4) Date: |
February 14, 2017 |
PCT
Pub. No.: |
WO2016/034764 |
PCT
Pub. Date: |
March 10, 2016 |
Prior Publication Data
|
|
|
|
Document
Identifier |
Publication Date |
|
US 20170252932 A1 |
Sep 7, 2017 |
|
Foreign Application Priority Data
|
|
|
|
|
Sep 1, 2014 [FI] |
|
|
20145757 |
|
Current U.S.
Class: |
1/1 |
Current CPC
Class: |
B26B
13/28 (20130101); B26B 13/285 (20130101); B26B
13/04 (20130101) |
Current International
Class: |
B26B
13/04 (20060101); B26B 13/28 (20060101) |
References Cited
[Referenced By]
U.S. Patent Documents
Foreign Patent Documents
|
|
|
|
|
|
|
201394847 |
|
Feb 2010 |
|
CN |
|
201427315 |
|
Mar 2010 |
|
CN |
|
H563467 |
|
Aug 1993 |
|
JP |
|
WO-03/094756 |
|
Nov 2003 |
|
WO |
|
Other References
English-language translation of Chinese Office Action, App. No.
201580046351.9, Fiskars Finland Oy Ab, 9 pages (dated Jan. 10,
2018). cited by applicant .
Canada Office Action Received for Canadian Application No. 2957815,
dated Jul. 23, 2018, 3 pages. cited by applicant .
Finland Office Action, App. No. 20145757, Fiskars Home Oy Ab, 3
pages (dated Apr. 17, 2015). cited by applicant .
International Search Report and Written Opinion, PCT/FI2015/050547,
Fiskars Home Oy Ab, 10 pages (dated Nov. 23, 2015). cited by
applicant.
|
Primary Examiner: Wellington; Andrea L
Assistant Examiner: Ayala; Fernando A
Attorney, Agent or Firm: Foley & Lardner LLP
Claims
The invention claimed is:
1. A cutting tool, comprising: a first and second blade which are
pivotably attached to each other by a joint, and a first and second
handle which are operatively connected to the first and second
blade for moving the first and second blade in relation to each
other around a rotation axis of the joint, wherein the joint
comprises: a first inlay having a protruding end protruding into a
hole in the first blade and a flange contacting an outer surface of
the first blade, a shaft with a first end joined to the protruding
end of the first inlay and with a second end protruding from the
protruding end of the first inlay, the shaft having at least one
transverse shoulder in the second end, and a second inlay having a
protruding end protruding into a hole in the second blade and a
flange contacting an outer surface of the second blade, the second
inlay having a hole receiving the second end of the shaft, and an
engaging surface for engaging with the shoulder of the shaft for
attaching the second end of the shaft to the second inlay, and
wherein the combination of the shape and width of the hole of the
second inlay and the shape and width of the shoulder allow the
second end of the shaft with the shoulder to pass into the hole
while the shaft and second inlay are rotated into a mutual
predetermined release position, but which prevents the shaft and
shoulder from passing through the hole when the shaft and second
inlay are not rotated into the mutual predetermined release
position.
2. The cutting tool according to claim 1, wherein the shaft is
attached to the first blade via the first inlay to rotate with the
first blade around the rotation axis, the second inlay is attached
to the second blade to rotate with the second blade around the
rotation axis, the engagement surface of the second inlay is
inclined in relation to the first inlay such that the shoulder
contacts a part of the engagement surface which is located further
away from the first inlay when the first and second blades are
close to each other than a part of the engagement surface which the
shoulder contacts when the first and second blade are located at a
distance from each other.
3. The cutting tool according to claim 1, wherein the engagement
surface is provided with a preventer contacting the shoulder to
prevent the blades from being further rotated away from each other
around the rotation axis once the shaft and second inlay have
reached the mutual predetermined release position.
4. The cutting tool according to claim 1, wherein the first end of
the shaft is joined to the protruding end of the first inlay with a
screw extending through the first inlay.
5. The cutting tool according to claim 4, wherein the screw extends
through the shaft from the first end of the shaft to the second end
of the shaft.
6. The cutting tool according to claim 1, wherein one or more of
the first inlay, second inlay and shaft are made of plastic.
7. The cutting tool according to claim 1, wherein said cutting tool
is a pair of scissors.
8. A method for manufacturing a joint for a cutting tool,
comprising: arranging a first blade with a hole in a mould, casting
a first inlay to have a protruding end protruding into the hole in
the first blade and a flange contacting an outer surface of the
first blade, arranging a second blade with a hole in a mould,
casting a second inlay to have a protruding end protruding into the
hole in the second blade and a flange contacting an outer surface
of the second blade, joining a first end of a shaft having a
transverse shoulder in a second end to the protruding end of the
first inlay by a screw extending through the first inlay, rotating
the shaft and the second inlay into a mutual predetermined release
position and threading the shaft with the shoulder into a hole in
the second inlay, and rotating the shaft and the second inlay away
from the mutual predetermined release position in order to engage
the shoulder with an engagement surface of the second inlay and to
attach the first and second blade pivotably to each other with the
shoulder and the engagement surface.
Description
CROSS-REFRENCE TO RELATED APPLICATIONS
This application is a U.S. National Stage of PCT/FI2015/050547,
filed Aug. 26, 2015, which claims the benefit of and priority to
Finland Patent Application No. 20145757, filed Sep. 1, 2014, the
entire contents of each of which are incorporated herein by
reference.
BACKGROUND OF THE INVENTION
Field of the Invention
This invention relates to a cutting tool and more particularly to a
joint for a cutting tool. In the following the invention will be
explained by way of example by referring to a pair of scissors. It
should, however, be observed that the invention may be implemented
also in connection with other cutting tools.
Description of Prior Art
Previously there is known a pair of scissors with a joint where the
first blade is provided with a T shaped shaft protruding from the
first blade and where the second blade is provided with a hole
having a shape allowing the T shaped shaft to be threaded through
the hole while the first and second blade are rotated to a
predetermined mutual position. Once the T shaped shaft is threaded
through the hole, the first and second blade are rotated out of the
predetermined mutual position, such that the transverse part of the
T shaped shaft comes into contact with the outer surface of the
second blade and thereby locks the blades to each other.
A problem with the previously known solution is that it is
difficult and expensive to provide the shaft made of metal and the
hole with optimal shapes. Instead the shaft and hole is provided
with sharp corners which makes it relatively difficult the thread
the T shaped shaft through the hole.
Additionally, during use of the scissors the sharp edges of the
shaft and hole cause scratches to appear in the vicinity of the
joint, which eventually wears out the material such that the joint
may not remain sufficiently tight for the entire lifetime of the
pair of scissors. This may lower the performance of the pair of
scissors, as a loose joint allows a gap to occur between the blades
while cutting.
SUMMARY OF THE INVENTION
An object of the present invention is to solve the above mentioned
drawback with a novel cutting tool and manufacturing method as
defined in independent claims 1 and 8.
The use of a first and second inlay arranged in holes provided in
the first and second blade of the cutting tool makes it easier to
shape the surfaces of the joint in an optimal way to facilitate
easy assembly and disassembly of the cutting tool. Additionally,
the inlays and the shaft may easily be manufactured of a material
other than the blades if it is determined that the material of the
blades is not optimal for these parts.
Preferred embodiments of the invention are disclosed in the
dependent claims.
BRIEF DESCRIPTION OF DRAWINGS
In the following the present invention will be described in closer
detail by way of example and with reference to the attached
drawings, in which
FIGS. 1 and 2 illustrate a first embodiment of a cutting tool,
FIG. 3 is an enlargement of the joint in the cutting tool of FIGS.
1 and 2, and
FIGS. 4 and 5 illustrate details of the joint of FIG. 3.
FIG. 6 is a flowchart of a method of manufacturing a joint for a
cutting tool, according to an exemplary embodiment.
DESCRIPTION OF AT LEAST ONE EMBODIMENT
FIGS. 1 and 2 illustrate a first embodiment of a cutting tool 1. In
the illustrated example the cutting tool 1 consists of a pair of
scissors, with a first blade 2 and a second blade 3 attached to
each other by a joint 4. A first handle 5 and a second handle 6 are
operatively connected to the first 2 and second 3 blade for moving
the first 2 and second 3 blade in relation to each other around a
rotation axis 7 of the joint 4.
FIGS. 4 and 5 illustrate details of the joint 4 of FIG. 3. The
joint 4 comprises a first inlay 8 with a protruding end 9
protruding into a hole 10 in the first blade 2. Additionally, the
first inlay comprises a flange 11 contacting an outer surface 12 of
the first blade 2.
A shaft 13 has a first end 14 joined to the protruding end 9 of the
first inlay 8 and a second end 15 protruding from the protruding
end 9 of the first inlay 8. Thus the shaft 13 is arranged as an
extension of the protruding end 9 of the first inlay 8. The shaft
13 is provided with at least one transverse shoulder 16 in the
second end 15. In the drawings it is, however, by way of example
assumed that the second end of the shaft 13 is provided with two
transverse shoulders 16, such that the second end 15 of the shaft
13 is generally T shaped.
A second inlay 17 has a protruding end 18 protruding into a hole 19
in the second blade 3. A flange 20 of the second inlay 17 contacts
an outer surface 21 of the second blade 3. The second inlay 17 has
a hole 22 receiving the second end 15 of the shaft 13. The second
inlay 17 is provided with an engagement surface 23 for engaging
with the shoulders 16 of the shaft 13 for attaching the second end
15 of the shaft 13 to the second inlay 17. In the example of FIGS.
3 to 5, the engagement surface 23 is the outer surface of the
second inlay 17 which faces away from the first blade 2. In the
illustrated example, the hole 22 extends through the entire second
inlay 17, such that the second end 15 of the shaft protrudes
through the entire second inlay 17. This is however, not necessary
in all embodiments, as in some embodiments the hole of the second
inlay need not protrude entirely through the second inlay, but
instead the hole may be implemented as a cavity receiving the
second end of the shaft.
As best seen in FIGS. 3 and 5, the hole 22 of the second inlay 17
has a shape and width allowing the second end 15 of the shaft 13
with the shoulders 16 to pass into the hole 22 while the shaft and
second inlay are rotated into a mutual predetermined release
position. In praxis the illustrated shoulders 16 are at that stage
rotated into a position illustrated by arrows 24, where the
diameter of the hole 22 is large enough to allow the shoulders 16
to pass through the hole 22. However, the shape and width of the
hole 22 prevents the shaft 13 and shoulders 16 from passing through
the hole 22 when the shaft 13 and second inlay 17 are not rotated
into the mutual predetermined release position. For practical
reasons the release position is set in such a way that when the
shaft 13 and second inlay 17 reach the release position, the blades
are in an open position, in other words the first 2 and second 3
blades have been mutually rotated around the rotation axis 7 as
much away from each other as possible.
The shaft 13 is attached to the first blade 2 via the first inlay 8
to rotate together with the first blade 2 around the rotation axis
7. To facilitate this the first inlay 8 needs to be fixed to the
first blade 2 such that it always rotates with the first blade 2.
One alternative to accomplish this is that the hole 10 in the first
blade 2 is not round, but oval or has a corner, for instance, while
the first inlay 8 has a matching shape locking it into the hole 10.
Similarly the second inlay 17 is attached to the second blade 3 to
rotate with the second blade 3 around the rotation axis 7. Also
this may be accomplished by selecting a suitable shape for the hole
19 in the second blade 3 and a matching shape for the second inlay
17. Alternatively, it is possible that the holes 10 and 19 are
circular, in which case the inlays may be non-rotatably attached to
the first and second blade in some other way, such as by use of an
adhesive, for instance.
In the illustrated example the engagement surface 23 is inclined in
relation to the first inlay 8 such that the shoulders 16 contact
parts 25 of the engagement surface 23 which is are located further
away from the first inlay 8, when the first 2 and second 3 blades
are close to teach other (the position illustrated in FIGS. 1 to
3), than parts 26 of the engagement surface 23 which the shoulders
16 contact when the first 2 and second blade 3 are located at a
distance from each other (not illustrated in the Figures). An
advantage obtained with such an inclined engagement surface 23 is
that the joint is relatively loose in the beginning of a cutting
action (when the blades are mutually rotated away from each other).
However, as the blades move closer to each other, the shoulders 16
move closer to the parts 25 of the engagement surface which is
located furthest away from the first inlay 8. Due to this the
tension in the joint becomes higher at the end of the cutting
action, such that the blades 2 and 3 are pressed with a maximum
force towards each other at the end of the cutting movement. This
prevents the occurrence of a gap between the blades 2 and 3 at the
end of the cutting movement, which is important for the cutting
tool 1, such as a pair of scissors, in order for the cutting tool
to work as efficiently as possible.
From FIG. 3 it can be seen that the engagement surface 23 is
provided with a preventer 27 in the form of a protrusion protruding
outwards from the engagement surface 23. This preventer comes into
contact with one of the shoulders 16 once the shaft is rotated
counterclockwise in FIG. 3 into the release position. This improves
the user friendliness, as it is very easy for the user to know when
the release position has been reached, as further mutual rotation
is not possible due to the preventer.
In the illustrated example it is by way of example assumed that the
shaft 13 is joined to the first inlay 8 with a screw 28, such as a
steel screw, extending through the first inlay 8. Such a screw
makes it possible for the user to adjust the tension of the joint
4. Additionally, the screw 28 may extend substantially through the
entire shaft 13 in which case the screw 28 strengthens the shaft
13. In praxis the upper end of the screw 28 in FIG. 4 may be
visible through the upper surface of the shaft 13, or alternatively
not visible as in FIG. 4, but with the end of the screw in close
vicinity to the upper surface of the shaft. In both cases the screw
28 extends substantially through the entire shaft 13.
It should, however, be observed that the use of a screw is not
necessary in all embodiments. One possible alternative is to
manufacture the shaft 13 and first inlay 8 to consist of one single
part only. In that case the material of the combined shaft and
first inlay joins the first end 14 of the shaft to the protruding
end 9 of the first inlay 8.
One or more of the first inlay 8, the second inlay 17 and the shaft
13 may be manufactured of plastic. One alternative is to utilize
glass fiber reinforced polyamide. In that case the joint 4 for the
cutting tool may be manufactured as follows:
The first blade 2 of steel, for instance, is provided with a hole
at the location of the pivot 4, and arranged in a mould. The first
inlay 8 is casted in the mould with an injection-molding process,
for instance. The second blade 3, of steel, for instance, is
provided with a hole at the location of the pivot 4, and arranged
in a mould. The second inlay 17 is casted in the mould with an
injection-molding process for instance.
The shaft 13 may also be cast with an injection-molding process,
after which the first end 14 of the shaft 13 may be attached to the
first inlay 8 with a screw 28.
The shaft 13 and the second inlay 17 are rotated into a mutual
predetermined release position, where the shaft with the shoulder
16 is threaded through the hole 22 in the second inlay 17. Finally,
the shaft 13 and the second inlay 17 are rotated away from the
mutual predetermined release position such that the shoulder 16
engages with the engagement surface 23 of the second inlay 17 and
locks the first 2 and second 3 blade to each other via the shoulder
16 and the engagement surface 23.
An advantage obtained by manufacturing the parts of the joint in a
mould by injection-molding, for instance, is that it is easier to
manufacture the parts exactly according to desired tolerances, and
the edges of the parts may easily and without additional work
phases or costs be rounded which makes it easier to assemble joint.
The parts may thereby be manufactured in such shapes and dimensions
and of such materials that the material wear during use of the
cutting tool may be minimized.
It is to be understood that the above description and the
accompanying figures are only intended to illustrate the present
invention. It will be obvious to a person skilled in the art that
the invention can be varied and modified without departing from the
scope of the invention.
* * * * *